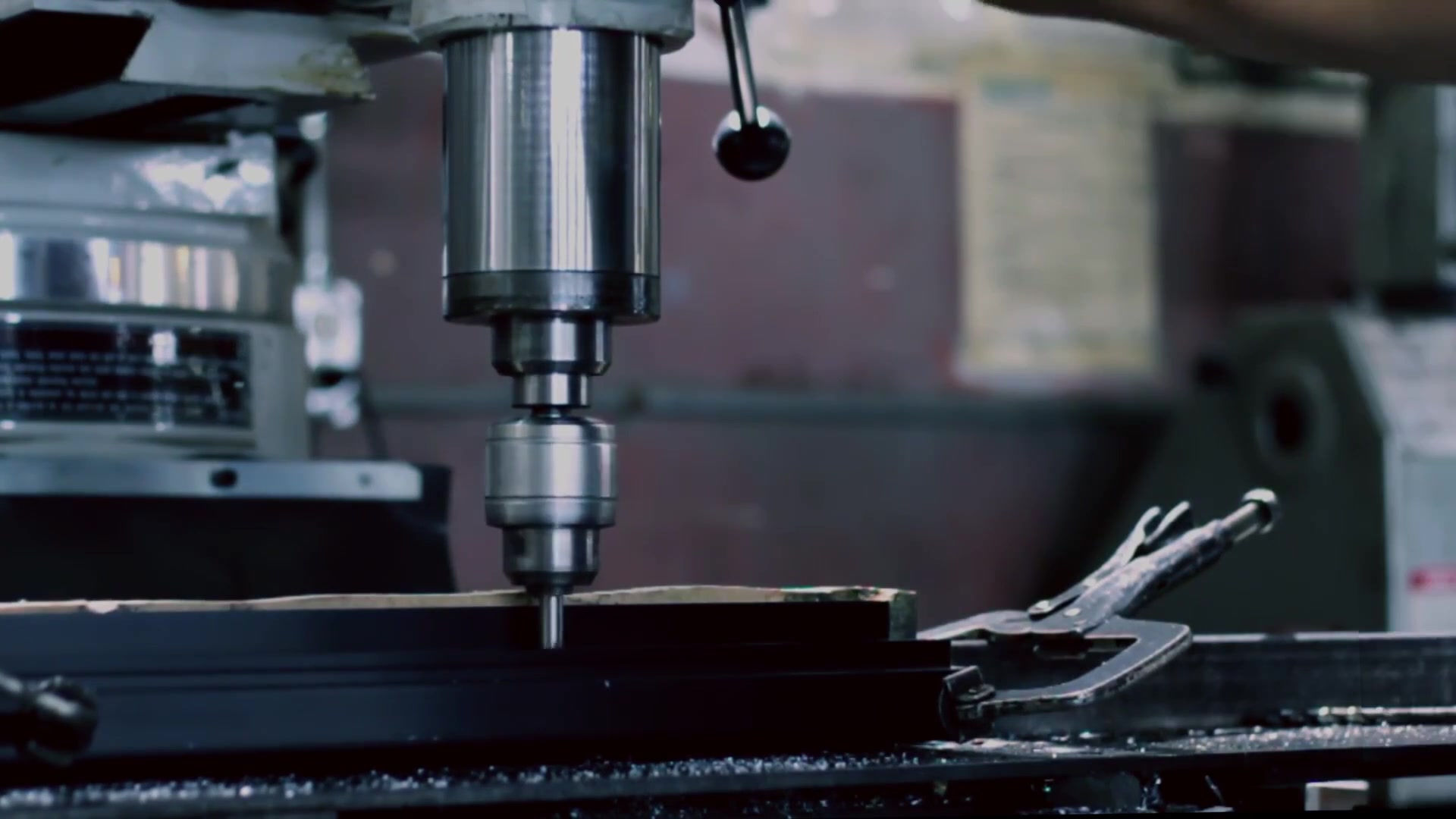
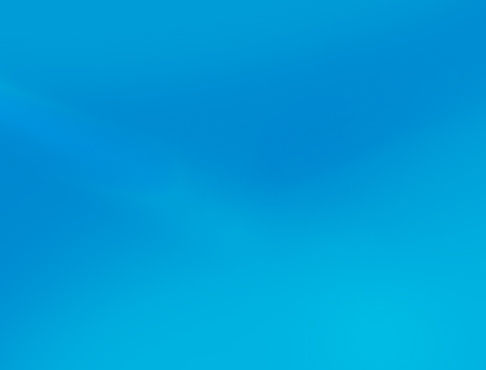
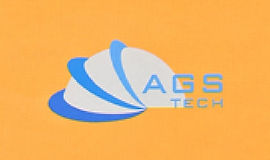
Produsen Custom Global, Integrator, Consolidator, Mitra Outsourcing kanggo Macem-macem Produk & Layanan.
Kita minangka sumber siji-mandeg kanggo manufaktur, fabrikasi, teknik, konsolidasi, integrasi, outsourcing produk & layanan sing digawe khusus lan ora kasedhiya. Kita uga label pribadi / label putih produk sampeyan kanthi jeneng merek yen sampeyan pengin.
Pilih Basa sampeyan
Manufaktur Custom Parts, Komponen, Rakitan, Produk Rampung, Mesin lan Peralatan Industri
Manufaktur Kontrak Domestik & Global
Outsourcing Produksi
Domestik, Pengadaan Global Produk Industri
Labeling pribadi / Label Putih Produk sampeyan nganggo Jeneng merek sampeyan
Product Finding & Locating Services
Desain Global lan Kemitraan Saluran
Integrasi Teknik
Layanan Teknik
Konsolidasi Global, Gudang, Logistik
Search Results
164 results found with an empty search
- Pneumatic and Hydraulic Actuators - Accumulators - AGS-TECH Inc. - NM
Pneumatic and Hydraulic Actuators - Accumulators - AGS-TECH Inc. - NM Aktuator Akumulator AGS-TECH is a leading manufacturer and supplier of PNEUMATIC and HYDRAULIC ACTUATORS for assembly, packaging, robotics, and industrial automation. Our actuators are known for performance, flexibility, and extremely long life, and welcome the challenge of many different types of operating environments. We also supply HYDRAULIC ACCUMULATORS which are devices in which potential energy is stored in the form of a compressed gas or spring, or by a raised weight to be used to exert a force against a relatively incompressible fluid. Our fast delivery of pneumatic and hydraulic actuators and accumulators will reduce your inventory costs and keep your production schedule on track. ACTUATORS: An actuator is a type of motor responsible for moving or controlling a mechanism or system. Actuators are operated by a source of energy. Hydraulic actuators are operated by hydraulic fluid pressure, and pneumatic actuators are operated by pneumatic pressure, and convert that energy into motion. Actuators are mechanisms by which a control system acts upon an environment. The control system may be a fixed mechanical or electronic system, a software-based system, a person, or any other input. Hydraulic actuators consist of cylinder or fluid motor that uses hydraulic power to facilitate mechanical operation. The mechanical motion may give an output in terms of linear, rotary or oscillatory motion. Since liquids are nearly impossible to compress, hydraulic actuators can exert considerable forces. Hydraulic actuators may have however limited acceleration. The actuator’s hydraulic cylinder consists of a hollow cylindrical tube along which a piston can slide. In single acting hydraulic actuators the fluid pressure is applied to just one side of the piston. The piston can move in only one direction, and a spring is generally used to give the piston a return stroke. Double acting actuators are used when pressure is applied on each side of the piston; any difference in pressure between the two sides of the piston moves the piston to one side or the other. Pneumatic actuators convert energy formed by vacuum or compressed air at high pressure into either linear or rotary motion. Pneumatic actuators enable large forces to be produced from relatively small pressure changes. These forces are often used with valves to move diaphragms to affect the flow of liquid through the valve. Pneumatic energy is desirable because it can respond quickly in starting and stopping as the power source does not need to be stored in reserve for operation. Industrial applications of actuators include automation, logic and sequence control, holding fixtures, and high-power motion control. Automotive applications of actuators on the other hand include power steering, power brakes, hydraulic brakes, and ventilation controls. Aerospace applications of actuators include flight-control systems, steering-control systems, air conditioning, and brake-control systems. COMPARING PNEUMATIC and HYDRAULIC ACTUATORS: Pneumatic linear actuators consist of a piston inside a hollow cylinder. Pressure from an external compressor or manual pump moves the piston inside the cylinder. As pressure is increased, the actuator’s cylinder moves along the axis of the piston, creating a linear force. The piston returns to its original position by either a spring-back force or fluid being supplied to the other side of the piston. Hydraulic linear actuators function similar to pneumatic actuators, but an incompressible liquid from a pump rather than pressurized air moves the cylinder. The benefits of pneumatic actuators come from their simplicity. The majority of pneumatic aluminum actuators have a maximum pressure rating of 150 psi with bore sizes ranging from 1/2 to 8 in., which can be converted into approximately 30 to 7,500 lb. of force. Steel pneumatic actuators on the other hand have a maximum pressure rating of 250 psi with bore sizes ranging from 1/2 to 14 in., and generate forces ranging from 50 to 38,465 lb. Pneumatic actuators generate precise linear motion by providing accuracies such as 0.1 inches and repeatabilities within .001 inches. Typical applications of pneumatic actuators are areas of extreme temperatures such as -40 F to 250 F. Using air, pneumatic actuators avoid using hazardous materials. Pneumatic actuators meet explosion protection and machine safety requirements because they create no magnetic interference due to their lack of motors. The cost of pneumatic actuators is low compared to hydraulic actuators. Pneumatic actuators are also lightweight, require minimal maintenance, and have durable components. On the other hand there are disadvantages of pneumatic actuators: Pressure losses and air’s compressibility make pneumatics less efficient than other linear-motion methods. Operations at lower pressures will have lower forces and slower speeds. A compressor must run continuously and apply pressure even if nothing is moving. To be efficient, pneumatic actuators must be sized for a specific job and cannot be used for other applications. Accurate control and efficiency requires proportional regulators and valves, which is costly and complex. Even though the air is easily available, it can be contaminated by oil or lubrication, leading to downtime and maintenance. Compressed air is a consumable that needs to be purchased. Hydraulic actuators on the other hand are rugged and suited for high-force applications. They can produce forces 25 times greater than pneumatic actuators of equal size and operate with pressures of up to 4,000 psi. Hydraulic motors have high horsepower-to-weight ratios by 1 to 2 hp/lb greater than a pneumatic motor. Hydraulic actuators can hold force and torque constant without the pump supplying more fluid or pressure, because fluids are incompressible. Hydraulic actuators can have their pumps and motors located a considerable distance away with still minimal power losses. However hydraulics will leak fluid and result in less efficiency. Hydraulic fluid leaks lead to cleanliness problems and potential damage to surrounding components and areas. Hydraulic actuators require many companion parts, such as fluid reservoirs, motors, pumps, release valves, and heat exchangers, noise-reduction equipment. As a result hydraulic linear motion systems are large and difficult to accommodate. ACCUMULATORS: These are used in fluid power systems to accumulate energy and to smooth out pulsations. Hydraulic system that utilize accumulators can use smaller fluid pumps because accumulators store energy from the pump during low demand periods. This energy is available for instantaneous use, released upon demand at a rate many times greater than could be supplied by the pump alone. Accumulators can also act as surge or pulsation absorbers by cushioning hydraulic hammers, reducing shocks caused by rapid operation or sudden starting and stopping of power cylinders in a hydraulic circuit. There are four major types of accumulators: 1.) The weight loaded piston type accumulators, 2.) Diaphragm type accumulators, 3.) Spring type accumulators and the 4.) Hydropneumatic piston type accumulators. The weight loaded type is much larger and heavier for its capacity than modern piston and bladder types. Both the weight loaded type, and mechanical spring type are very seldom used today. The hydro-pneumatic type accumulators use a gas as a spring cushion in conjunction with a hydraulic fluid, the gas and fluid being separated by a thin diaphragm or a piston. Accumulators have the following functions: -Energy Storage -Absorbing Pulsations -Cushioning Operating Shocks -Supplementing Pump Delivery -Maintaining Pressure -Acting as Dispensers Hydro-pneumatic accumulators incorporate a gas in conjunction with a hydraulic fluid. The fluid has little dynamic power storage capability. However, the relative incompressibility of a hydraulic fluid makes it ideal for fluid power systems and provides quick response to power demand. The gas, on the other hand, a partner to the hydraulic fluid in the accumulator, can be compressed to high pressures and low volumes. Potential energy is stored in the compressed gas to be released when needed. In the piston type accumulators the energy in the compressed gas exerts pressure against the piston separating the gas and the hydraulic fluid. The piston in turn forces the fluid from the cylinder into the system and to the location where useful work needs to be accomplished. In most fluid power applications, pumps are used to generate the required power to be used or stored in a hydraulic system, and pumps deliver this power in a pulsating flow. The piston pump, as commonly used for higher pressures produces pulsations detrimental to a high pressure system. An accumulator properly located in the system will substantially cushion these pressure variations. In many fluid power applications the driven member of the hydraulic system stops suddenly, creating a pressure wave which is sent back through the system. This shock wave can develop peak pressures several times greater than normal working pressures and can be the source of system failure or disturbing noise. The gas cushioning effect in an accumulator will minimize these shock waves. An example of this application is the absorption of shock caused by suddenly stopping the loading bucket on a hydraulic front end loader. An accumulator, capable of storing power, can supplement the fluid pump in delivering power to the system. The pump stores potential energy in the accumulator during idle periods of the work cycle, and the accumulator transfers this reserve power back to the system when the cycle requires emergency or peak power. This enables a system to utilize smaller pumps, resulting in cost and power savings. Pressure changes are observed in hydraulic systems when the liquid is subjected to rising or falling temperatures. Also, there may be pressure drops due to leakage of hydraulic fluids. Accumulators compensate for such pressure changes by delivering or receiving a small amount of hydraulic liquid. In the event the main power source should fail or be stopped, accumulators would act as auxiliary power sources, maintaining pressure in the system. Lastly, accumulators mcan be used to dispense fluids under pressure, such as lubricating oils. Please click on highlighted text below to download our product brochures for actuators and accumulators: - Pneumatic Cylinders - YC Series Hydraulic Cyclinder - Accumulators from AGS-TECH Inc KLIK Product Finder-Locator Service PAGE sadurunge
- Electrochemical Machining and Grinding - ECM - Reverse Electroplating
Electrochemical Machining and Grinding - ECM - Reverse Electroplating - Custom Machining - AGS-TECH Inc. - NM - USA ECM Machining, Electrochemical Machining, Grinding Some of the valuable NON-CONVENTIONAL MANUFACTURING processes AGS-TECH Inc offers are ELECTROCHEMICAL MACHINING (ECM), SHAPED-TUBE ELECTROLYTIC MACHINING (STEM), PULSED ELECTROCHEMICAL MACHINING (PECM), ELECTROCHEMICAL GRINDING (ECG), HYBRID MACHINING PROCESSES. ELECTROCHEMICAL MACHINING (ECM) is a non-conventional manufacturing technique where metal is removed by an electrochemical process. ECM is typically a mass production technique, used for machining extremely hard materials and materials that are difficult to machine using the conventional manufacturing methods. Electrochemical-machining systems we use for production are numerically controlled machining centers with high production rates, flexibility, perfect control of dimensional tolerances. Electrochemical machining is capable of cutting small and odd-shaped angles, intricate contours or cavities in hard and exotic metals like titanium aluminides, Inconel, Waspaloy, and high nickel, cobalt, and rhenium alloys. Both external and internal geometries can be machined. Modifications of the electrochemical machining process are used for operations like turning, facing, slotting, trepanning, profiling where the electrode becomes the cutting tool. The metal removal rate is only a function of ion exchange rate and is not affected by the strength, hardness or toughness of the workpiece. Unfortunately the method of electrochemical machining (ECM) is limited to electrically conductive materials. Another important point to consider deploying the ECM technique is to compare the mechanical properties of the produced parts with those produced by other machining methods. ECM removes material instead of adding it and therefore is sometimes referred to as ''reverse electroplating''. It resembles in some ways to electrical discharge machining (EDM) in that a high current is passed between an electrode and the part, through an electrolytic material removal process having a negatively charged electrode (cathode), a conductive fluid (electrolyte), and a conductive workpiece (anode). The electrolyte acts as the current carrier and is a highly conductive inorganic salt solution like sodium chloride mixed and dissolved in water or sodium nitrate. The advantage of ECM is that there is no tool wear. The ECM cutting tool is guided along the desired path close to the work but without touching the piece. Unlike EDM, however, no sparks are created. High metal removal rates and mirror surface finishes are possible with ECM, with no thermal or mechanical stresses being transferred to the part. ECM does not cause any thermal damage to the part and since there are no tool forces there is no distortion to the part and no tool wear, as would be the case with typical machining operations. In electrochemical machining cavity produced is the female mating image of the tool. In the ECM process, a cathode tool is moved into an anode workpiece. The shaped tool is generally made of copper, brass, bronze or stainless steel. The pressurized electrolyte is pumped at a high rate at a set temperature through the passages in the tool to the area being cut. The feed rate is the same as the rate of ''liquification'' of the material, and the electrolyte movement in the tool-workpiece gap washes metal ions away from the workpiece anode before they have a chance to plate onto the cathode tool. The gap between the tool and the workpiece varies between 80-800 micrometers and the DC power supply in the range 5 – 25 V maintains current densities between 1.5 – 8 A/mm2 of active machined surface. As electrons cross the gap, material from the workpiece is dissolved, as the tool forms the desired shape in the workpiece. The electrolytic fluid carries away the metal hydroxide formed during this process. Commercial electrochemical machines with current capacities between 5A and 40,000A are available. The material removal rate in electrochemical machining can be expressed as: MRR = C x I x n Here MRR=mm3/min, I=current in amperes, n=current efficiency, C=a material constant in mm3/A-min. The constant C depends on valence for pure materials. The higher the valence, the lower is its value. For most metals it is in between 1 and 2. If Ao denotes the uniform cross-sectional area being electrochemically machined in mm2, the feed rate f in mm/min can be expressed as: F = MRR / Ao Feed rate f is the speed the electrode is penetrating the workpiece. In the past there were problems of poor dimensional accuracy and environmentally polluting waste from electrochemical machining operations. These have largely been overcome. Some of the applications of electrochemical machining of high-strength materials are: - Die-Sinking operations. Die-sinking is machining forging – die cavities. - Drilling a jet engine turbine blades, jet-engine parts and nozzles. - Multiple small holes drilling. The electrochemical machining process leaves a burr-free surface. - Steam turbine blades can be machined within close limits. - For deburring of surfaces. In deburring, ECM removes metal projections left from the machining processes and so dulls sharp edges. Electrochemical machining process is fast and often more convenient than the conventional methods of deburring by hand or non-traditional machining processes. SHAPED-TUBE ELECTROLYTIC MACHINING (STEM) is a version of electrochemical machining process we use for drilling small diameter deep holes. A titanium tube is used as the tool which is coated with an electrically insulating resin to prevent the removal of material from other regions like the lateral faces of the hole and tube. We can drill hole sizes of 0.5 mm with depth-to-diameter ratios of 300:1 PULSED ELECTROCHEMICAL MACHINING (PECM): We use very high pulsed current densities in the order of 100 A/cm2. By using pulsed currents we eliminate the need for high electrolyte flow rates which poses limitations for the ECM method in mold and die fabrication. Pulsed electrochemical machining improves fatigue life and eliminates the recast layer left by the electrical discharge machining (EDM) technique on mold and die surfaces. In ELECTROCHEMICAL GRINDING (ECG) we combine the conventional grinding operation with electrochemical machining. The grinding wheel is a rotating cathode with abrasive particles of diamond or aluminum oxide that are metal bonded. The current densities range between 1 and 3 A/mm2. Similar to ECM, an electrolyte such as sodium nitrate flows and the metal removal in electrochemical grinding is dominated by the electrolytic action. Less than 5% of metal removal is by abrasive action of the wheel. The ECG technique is well suited for carbides and high-strength alloys, but not so much of a fit for die-sinking or mould making because the grinder may not easily access deep cavities. The material removal rate in electrochemical grinding can be expressed as: MRR = G I / d F Here MRR is in mm3/min, G is mass in grams, I is current in amperes, d is density in g/mm3 and F is Faraday’s constant (96,485 Coulombs/mole). The speed of penetration of the grinding wheel into workpiece can be expressed as: Vs = (G / d F) x (E / g Kp) x K Here Vs is in mm3/min, E is cell voltage in volts, g is wheel to workpiece gap in mm, Kp is coefficient of loss and K is electrolyte conductivity. The advantage of the electrochemical grinding method over conventional grinding is less wheel wear because less than 5% of the metal removal is by abrasive action of the wheel. There are similarities between EDM and ECM: 1. The tool and workpiece are separated by a very small gap without a contact in between them. 2. Both tool and material must be conductors of electricity. 3. Both techniques need high capital investment. Modern CNC machines are used 4. Both methods consume lots of electric power. 5. A conductive fluid is used as a medium between the tool and the work piece for ECM and a dielectric fluid for EDM. 6. The tool is fed continuously towards the workpiece to maintain a constant gap between them (EDM may incorporate intermittent or cyclic, typically partial, tool withdrawal). HYBRID MACHINING PROCESSES: We frequently take advantage of the benefits of hybrid machining processes where two or more different processes such as ECM, EDM….etc. are used in combination. This gives us the opportunity to overcome the shortcomings of one process by the other, and benefit from the advantages of each process. KLIK Product Finder-Locator Service PREVIOUS PAGE
- Holography - Holographic Glass Grating - AGS-TECH Inc. - New Mexico
Holography - Holographic Glass Grating - AGS-TECH Inc. - New Mexico - USA Produk Holographic lan Sistem Manufaktur Kita nyedhiyakake stok sing ana ing rak uga PRODUK HOLOGRAFI sing dirancang lan diprodhuksi khusus, kalebu: • Tampilan Hologram 180, 270, 360 Derajat/ Proyeksi Visual Berbasis Holografi • Self-adhesive 360 Degree Hologram Tampilan • Film Window 3D kanggo Iklan Tampilan • Full HD Hologram Showcase & Holographic Tampilan 3D Pyramid Kanggo Iklan Holografi • Tampilan Holographic 3D Holocube Kanggo Iklan Holografi • Sistem Proyeksi Holografik 3D • Layar Holographic Layar 3D Mesh • Film Proyeksi Mburi / Film Proyeksi Ngarep (by roll) • Tampilan Tutul Interaktif • Layar Proyeksi Mlengkung: Layar Proyeksi Mlengkung minangka produk sing disesuaikan kanggo saben pelanggan. Kita nggawe layar mlengkung, layar kanggo layar simulator 3D aktif lan pasif lan tampilan simulasi. • Produk optik holografik kayata keamanan tahan panas lan stiker keaslian produk (cetak khusus miturut panjaluk pelanggan) • Gratings Kaca Holographic kanggo aplikasi ornamental utawa ilustrasi & pendidikan. Kanggo ngerteni babagan kemampuan teknik & riset & pangembangan, kita ngajak sampeyan ngunjungi situs teknik http://www.ags-engineering.com KLIK Product Finder-Locator Service PAGE sadurunge
- Fiber Optic Test Instruments, Optical Fiber Testing, OTDR, Loss Meter
Fiber Optic Test Instruments - Optical Fiber Testing - OTDR - Loss Meter - Fiber Cleaver - from AGS-TECH Inc. - NM - USA Instrumen Tes Serat Optik AGS-TECH Inc. offers the following FIBER OPTIC TEST and METROLOGY INSTRUMENTS : - OPTICAL FIBER SPLICER & FUSION SPLICER & FIBER CLEAVER - OTDR & OPTICAL TIME DOMAIN REFLECTOMETER - AUDIO FIBER CABLE DETECTOR - AUDIO FIBER CABLE DETECTOR - OPTICAL POWER METER - LASER SOURCE - VISUAL FAULT LOCATOR - PON POWER METER - FIBER IDENTIFIER - OPTICAL LOSS TESTER - OPTICAL TALK SET - OPTICAL VARIABLE ATTENUATOR - INSERTION / RETURN LOSS TESTER - E1 BER TESTER - FTTH TOOLS You can download our product catalogs and brochures below to choose a suitable fiber optic test equipment for your needs or you may tell us what you need and we will match something suitable for you. We do have in stock brand new as well as refurbished or used but still very good fiber optic instruments. All our equipment is under warranty. Please download our related brochures and catalogs by clicking the colored text below: ANRITSU Electronic Measuring Instruments EXFO Optical Testing Solutions for Manufacturing and R&D EXFO Data Center Solution Guide EXFO Remote Fiber Testing and Monitoring EXFO Test Solutions for Submarine Networks EXFO Quick Guide to Testing FTTH EXFO Fiber Deep and Remote PHY Test Solutions EXFO OTDR and iOLM Selection Guide EXFO Spectral Testing of Active Systems EXFO Network Equipment Manufacturers End-to End Solutions EXFO Expert-Level Field Test Solutions EXFO Mobile Backhaul End to End Network Assessment EXFO High-Speed Product Portfolio EXFO 40G Testing Solutions TRIBRER Handheld Optical Fiber Instruments and Tools You can purchase brand new, refurbished or used equipment from us at the most competitive discounted prices. Simply choose the product from the downloadable catalogs and let us know the product name, product code and relevant information and we will send you our best quote. What distinguishes AGS-TECH Inc. from other suppliers is our wide spectrum of ENGINEERING INTEGRATION and CUSTOM MANUFACTURING capabilities. Therefore, please let us know if you need a custom jig, a custom automation system designed specifically for your fiber optic testing needs. We can modify existing equipment or integrate various components to build a turn-key solution to your engineering needs. It will be our pleasure to briefly summarize and provide information about the main concepts in the realm of FIBER OPTIC TESTING. FIBER STRIPPING & CLEAVING & SPLICING : There are two major types of splicing, FUSION SPLICING and MECHANICAL SPLICING. In industry and high volume manufacturing, fusion splicing is the most widely used technique as it provides for the lowest loss and least reflectance, as well as providing the strongest and most reliable fiber joints. Fusion splicing machines can splice a single fiber or a ribbon of multiple fibers at one time. Most single mode splices are fusion type. Mechanical splicing on the other hand is mostly used for temporary restoration and mostly for multimode splicing. Fusion splicing requires higher capital expenses as compared to mechanical splicing because it requires a fusion splicer. Consistent low loss splices can only be achieved using proper techniques and keeping equipment in good condition. Cleanliness is vital. FIBER STRIPPERS should be kept clean and in good condition and be replaced when nicked or worn. FIBER CLEAVERS are also vital for good splices as one has to have good cleaves on both fibers. Fusion splicers need proper maintenance and fusing parameters need to be set for the fibers being spliced. OTDR & OPTICAL TIME DOMAIN REFLECTOMETER : This instrument is used to test the performance of new fiber optic links and detect problems with existing fiber links. OTDR traces are graphical signatures of a fiber's attenuation along its length. The optical time domain reflectometer (OTDR) injects an optical pulse into one end of the fiber and analyzes the returning backscattered and reflected signal. A technician at one end of the fiber span can measure and localize attenuation, event loss, reflectance, and optical return loss. Examining non-uniformities in the OTDR trace we can evaluate the performance of the link components such as cables, connectors and splices as well as the quality of the installation. Such fiber tests assure us that the workmanship and quality of the installation meet the design and warranty specifications. OTDR traces help characterize individual events that can often be invisible when conducting only loss/length testing. Only with a complete fiber certification, installers can fully understand the quality of a fiber installation. OTDRs are also used for testing and maintaining fiber plant performance. OTDR allows us to see more details impacted by the cabling installation. OTDR maps the cabling and can illustrate termination quality, location of faults. An OTDR provides advanced diagnostics to isolate a point of failure that may hinder network performance. OTDRs allow discovery of problems or potential problems along the length of a channel that may affect long term reliability. OTDRs characterize features such as attenuation uniformity and attenuation rate, segment length, location and insertion loss of connectors and splices, and other events such as sharp bends that may have been incurred during installation of cables. An OTDR detects, locates, and measures events on fiber links and requires access to only one end of the fiber. Here is a summary of what a typical OTDR can measure: Attenuation (also known as fiber loss): Expressed in dB or dB/km, attenuation represents the loss or the rate of loss between two points along the fiber span. Event Loss: The difference in the optical power level before and after an event, expressed in dB. Reflectance: The ratio of reflected power to incident power of an event, expressed as a negative dB value. Optical Return Loss (ORL): The ratio of the reflected power to the incident power from a fiber optic link or system, expressed as a positive dB value. OPTICAL POWER METERS : These meters measure average optical power out of an optical fiber. Removable connector adapters are used in optical power meters so that various models of fiber optic connectors can be used. Semiconductor detectors inside power meters have sensitivities that vary with the wavelength of light. Therefore they are calibrated at typical fiber optic wavelengths such as 850, 1300 and 1550 nm. Plastic Optical Fiber or POF meters on the other hand are calibrated at 650 and 850 nm. Power meters are sometimes calibrated to read in dB (Decibel) referenced to one miliwatt of optical power. Some power meters however are calibrated in relative dB scale, which is well suited for loss measurements because the reference value may be set to “0 dB” on the output of the test source. Rare but occasionally lab meters measure in linear units such as miliwatts, nanowatts….etc. Power meters cover a very broad dynamic range 60 dB. However most optical power and loss measurements are made in the range 0 dBm to (-50 dBm). Special power meters with higher power ranges of up to +20 dBm are used for testing fiber amplifiers and analog CATV systems. Such higher power levels are needed to assure the proper functioning of such commercial systems. Some laboratory type meters on the other hand can measure at very low power levels down to (-70 dBm) or even lower, because in research and development engineers frequently have to deal with weak signals. Continuous wave (CW) test sources are used frequently for loss measurements. Power meters measure the time average of the optical power instead of the peak power. Fiber optic power meters should be recalibrated frequently by labs with NIST traceable calibration systems. Regardless of price, all power meters have similar inaccuracies typically in the neighborhood of +/-5%. This uncertainty is caused by the variability in coupling efficiency at the adapters/connectors, reflections at polished connector ferrules, unknown source wavelengths, nonlinearities in electronic signal conditioning circuitry of the meters and detector noise at low signal levels. FIBER OPTIC TEST SOURCE / LASER SOURCE : An operator needs a test source as well as a FO power meter in order to make measurements of optical loss or attenuation in fibers, cables and connectors. The test source must be chosen for compatibility with the type of fiber in use and the wavelength desired for performing the test. Sources are either LED's or lasers similar to those used as transmitters in actual fiber optic systems. LED's are generally used for testing multimode fiber and lasers for singlemode fibers. For some tests such as measuring spectral attenuation of fiber, a variable wavelength source is used, which is usually a tungsten lamp with a monochromator to vary the output wavelength. OPTICAL LOSS TEST SETS : Sometimes also refered to as ATTENUATION METERS, these are instruments made of fiber optic power meters and sources which are used to measure the loss of fibers, connectors and connectorized cables. Some optical loss test sets have individual source outputs and meters like a separate power meter and test source, and have two wavelengths from one source output (MM: 850/1300 or SM:1310/1550) Some of them offer bidirectional testing on a single fiber and some have two bidirectional ports. The combination instrument which contains both a meter and a source may be less convenient than an individual source and power meter. This is the case when the ends of the fiber and cable are usually separated by long distances, which would require two optical loss test sets instead of one source and one meter. Some instruments also have a single port for bidirectional measurements. VISUAL FAULT LOCATOR : These are simple instruments that inject visible wavelength light into the system and one can visually trace the fiber from transmitter to receiver to insure correct orientation and continuity. Some visual fault locators have powerful visible light sources such as a HeNe laser or visible diode laser and therefore high loss points can be made visible. Most applications center around short cables such as used in telecommunication central offices to connect to the fiber optic trunk cables. Since the visual fault locator covers the range where OTDRs are not useful, it is complementary instrument to the OTDR in cable troubleshooting. Systems with powerful light sources will work on buffered fiber and jacketed single fiber cable if the jacket is not opaque to the visible light. The yellow jacket of singlemode fibers and orange jacket of multimode fibers will usually pass the visible light. With most multifiber cables this instrument cannot be used. Many cable breaks, macrobending losses caused by kinks in the fiber, bad splices….. can be detected visually with these instruments. These instruments have a short range, typically 3-5 km, due to high attenuation of visible wavelengths in fibers. FIBER IDENTIFIER : Fiber Optic technicians need to identify a fiber in a splice closure or at a patch panel. If one carefully bends a singlemode fiber enough to cause loss, the light that couples out can also be detected by a large area detector. This technique is used in fiber identifiers to detect a signal in the fiber at transmission wavelengths. A fiber identifier generally functions as a receiver, is able to discriminate between no signal, a high speed signal and a 2 kHz tone. By specifically looking for a 2 kHz signal from a test source that is coupled into the fiber, the instrument can identify a specific fiber in a large multifiber cable. This is essential in fast and speedy splicing and restoration processes. Fiber identifiers can be used with buffered fibers and jacketed single fiber cables. FIBER OPTIC TALKSET : Optical talk sets are useful for fiber installation and testing. They transmit voice over fiber optic cables that are installed and allow the technician splicing or testing the fiber to communicate effectively. Talksets are even more useful when walkie-talkies and telephones are not available in remote locations where splicing is being done and in buildings with thick walls where radio waves will not penetrate through. Talksets are most effectively used by setting up the talksets on one fiber and leaving them in operation while testing or splicing work is done. This way there will always be a communications link between the work crews and will facilitate deciding which fibers to work with next. The continuous communications capability will minimize misunderstandings, mistakes and will speed up the process. Talksets include those for networking multi-party communications, especially helpful in restorations, and system talksets for use as intercoms in installed systems. Combination testers and talksets are also available commercially. To this date, unfortunately different manufacturers' talksets can not communicate with each other. VARIABLE OPTICAL ATTENUATOR : Variable Optical Attenuators allow the technician to manually vary the attenuation of the signal in the fiber as it is transmitted through the device. VOAs can be used to balance the signal strengths in fiber circuits or to balance an optical signal when evaluating the dynamic range of the measurement system. Optical attenuators are commonly used in fiber optic communications to test power level margins by temporarily adding a calibrated amount of signal loss, or installed permanently to properly match transmitter and receiver levels. There are fixed, step-wise variable, and continuously variable VOAs commercially available. Variable optical test attenuators generally use a variable neutral density filter. This offers the advantages of being stable, wavelength insensitive, mode insensitive, and a large dynamic range. A VOA may be either manually or motor controlled. Motor control provides users a distinct productivity advantage, since commonly used test sequences can be run automatically. The most accurate variable attenuators have thousands of calibration points, resulting in excellent overall accuracy. INSERTION / RETURN LOSS TESTER : In fiber optics, Insertion Loss is the loss of signal power resulting from the insertion of a device in a transmission line or optical fiber and is usually expressed in decibels (dB). If the power transmitted to the load before insertion is PT and the power received by the load after insertion is PR, then the insertion loss in dB is given by: IL = 10 log10(PT/PR) Optical Return Loss is the ratio of the light reflected back from a device under test, Pout, to the light launched into that device, Pin, usually expressed as a negative number in dB. RL = 10 log10(Pout/Pin) Loss may be caused by reflections and scattering along the fiber network due to contributors such as dirty connectors, broken optical fibers, poor connector mating. Commercial optical return loss (RL) & insertion loss (IL) testers are high performance loss test stations that are designed specially for optical fibre testing, lab testing and passive components production. Some integrate three different tests modes in one test station, working as a stable laser source, optical power meter and a return loss meter. The RL and IL measurements are displayed on two separate LCD screens, whilst in return loss test model, the unit will automatically and synchronously set the same wavelength for the light source and power meter. These instruments come complete with FC, SC, ST and universal adaptors. E1 BER TESTER : Bit error rate (BER) tests allow technicians to test cables and diagnose signal problems in the field. One can configure individual T1 channel groups to run an independent BER test, set one local serial port to Bit error rate test (BERT) mode while the remaining local serial ports continue to transmit and receive normal traffic. The BER test checks communication between the local and the remote ports. When running a BER test, the system expects to receive the same pattern that it is transmitting. If traffic is not being transmitted or received, technicians create a back-to-back loopback BER test on the link or in the network, and send out a predictable stream to ensure that they receive the same data that was transmitted. To determine whether the remote serial port returns the BERT pattern unchanged, technicians must manually enable network loopback at the remote serial port while they configure a BERT pattern to be used in the test at specified time intervals on the local serial port. Later they can display and analyze the total number of error bits transmitted and the total number of bits received on the link. Error statistics can be retrieved anytime during the BER test. AGS-TECH Inc. offers E1 BER (Bit Error Rate) testers that are compact, multi-functional and handheld instruments, specially designed for R&D, production, installation and maintenance of SDH, PDH, PCM, and DATA protocol conversion. They feature self-check and keyboard testing, extensive error and alarm generation, detection and indication. Our testers provide smart menu navigation and have a large color LCD screen allowing test results to be displayed clearly. Test results can be downloaded and printed using product software included in the package. E1 BER Testers are ideal devices for fast problem resolution, E1 PCM line access, maintenance and acceptance testing. FTTH – FIBER TO THE HOME TOOLS : Among the tools we offer are single and multihole fiber strippers, fiber tubing cutter, wire stripper, Kevlar cutter, fiber cable slitter, single fiber protection sleeve, fiber microscope, fiber connector cleaner, connector heating oven, crimping tool, pen type fiber cutter, ribbon fiber buff stripper, FTTH tool bag, portable fiber optic polishing machine. If you haven't found something that fits your needs and would like to search further for other similar equipment, please visit our equipment website: http://www.sourceindustrialsupply.com KLIK Product Finder-Locator Service PREVIOUS PAGE
- Plasma Machining, HF Plasma Cutting, Plasma Gouging, CNC, Arc Welding
Plasma Machining - HF Plasma Cutting - Plasma Gouging - CNC - Plasma Arc Welding - PAW - GTAW - AGS-TECH Inc. - New Mexico Plasma Machining & Cutting We use the PLASMA CUTTING and PLASMA MACHINING processes to cut and machine steel, aluminum, metals and other materials of different thicknesses using a plasma torch. In plasma-cutting (also sometimes called PLASMA-ARC CUTTING), an inert gas or compressed air is blown at high speed out of a nozzle and simultaneously an electrical arc is formed through that gas from the nozzle to the surface being cut, turning a portion of that gas to plasma. To simplify, plasma can be described as the fourth state of matter. The three states of matter are solid, liquid and gas. For a common example, water, these three states are ice, water and steam. The difference between these states relates to their energy levels. When we add energy in the form of heat to ice, it melts and forms water. When we add more energy, the water vaporizes in the form of steam. By adding more energy to steam these gases become ionized. This ionization process causes the gas to become electrically conductive. We call this electrically conductive, ionized gas a “plasma”. The plasma is very hot and melts the metal being cut and at the same time blowing the molten metal away from the cut. We use plasma for cutting thin and thick, ferrous and nonferrous materials alike. Our hand-held torches can usually cut up to 2 inches thick steel plate, and our stronger computer-controlled torches can cut steel up to 6 inches thick. Plasma cutters produce a very hot and localized cone to cut with, and are therefore very suitable for cutting metal sheets in curved and angled shapes. The temperatures generated in plasma-arc cutting are very high and around 9673 Kelvin in the oxygen plasma torch. This offers us a fast process, small kerf width, and good surface finish. In our systems using tungsten electrodes, the plasma is inert, formed using either argon, argon-H2 or nitrogen gases. However, we also use sometimes oxidizing gases, such as air or oxygen, and in those systems the electrode is copper with hafnium. The advantage of an air plasma torch is that it uses air instead of expensive gases, thus potentially reducing overall cost of machining . Our HF-TYPE PLASMA CUTTING machines use a high-frequency, high-voltage spark to ionize the air through the torch head and initiate arcs. Our HF plasma cutters do not require the torch to be in contact with the workpiece material at the start, and are suitable for applications involving COMPUTER NUMERICAL CONTROL (CNC) cutting. Other manufacturers are using primitive machines that require tip contact with the parent metal to start and then the gap separation occurs. These more primitive plasma cutters are more susceptible to contact tip and shield damage at starting. Our PILOT-ARC TYPE PLASMA machines use a two step process for producing plasma, without the need for initial contact. In the first step, a high-voltage, low current circuit is used to initialize a very small high-intensity spark within the torch body, generating a small pocket of plasma gas. This is called the pilot arc. The pilot arc has a return electrical path built into the torch head. The pilot arc is maintained and preserved until it is brought into proximity of the workpiece. There the pilot arc ignites the main plasma cutting arc. Plasma arcs are extremely hot and are in the range of 25,000 °C = 45,000 °F. A more traditional method we also deploy is OXYFUEL-GAS CUTTING (OFC) where we use a torch as in welding. The operation is used in cutting of steel, cast iron and cast steel. The principle of cutting in oxyfuel-gas cutting is based on oxidation, burning and melting of the steel. Kerf widths in oxyfuel-gas cutting are in the neighborhood of 1.5 to 10mm. The plasma arc process has been seen as an alternative to the oxy-fuel process. The plasma-arc process differs from the oxy-fuel process in that it operates by using the arc to melt the metal whereas in the oxy-fuel process, the oxygen oxidizes the metal and the heat from the exothermic reaction melts the metal. Therefore, unlike the oxy-fuel process, the plasma-process can be applied for cutting metals which form refractory oxides such as stainless steel, aluminium, and non-ferrous alloys. PLASMA GOUGING a similar process to plasma cutting, is typically performed with the same equipment as plasma cutting. Instead of cutting the material, plasma gouging uses a different torch configuration. The torch nozzle and gas diffuser is usually different, and a longer torch-to-workpiece distance is maintained for blowing away metal. Plasma gouging can be used in various applications, including removing a weld for rework. Some of our plasma cutters are built in to the CNC table. CNC tables have a computer to control the torch head to produce clean sharp cuts. Our modern CNC plasma equipment is capable of multi-axis cutting of thick materials and allowing opportunities for complex welding seams that are not possible otherwise. Our plasma-arc cutters are highly automated through the use of programmable controls. For thinner materials, we prefer laser cutting to plasma cutting, mostly because of our laser cutter's superior hole-cutting abilities. We also deploy vertical CNC plasma cutting machines, offering us a smaller footprint, increased flexibility, better safety and faster operation. The quality of the plasma cut edge is similar to that achieved with the oxy-fuel cutting processes. However, because the plasma process cuts by melting, a characteristic feature is the greater degree of melting towards the top of the metal resulting in top edge rounding, poor edge squareness or a bevel on the cut edge. We use new models of plasma torches with a smaller nozzle and a thinner plasma arc to improve arc constriction to produce more uniform heating at the top and bottom of the cut. This allows us to obtain near-laser precision on plasma cut and machined edges. Our HIGH TOLERANCE PLASMA ARC CUTTING (HTPAC) systems operate with a highly constricted plasma. Focusing of the plasma is achieved by forcing the oxygen generated plasma to swirl as it enters the plasma orifice and a secondary flow of gas is injected downstream of the plasma nozzle. We have a separate magnetic field surrounding the arc. This stabilises the plasma jet by maintaining the rotation induced by the swirling gas. By combining precision CNC control with these smaller and thinner torches we are capable to produce parts that require little or no finishing. Material removal rates in plasma-machining are much higher than in the Electric-Discharge-Machining (EDM) and Laser-Beam-Machining (LBM) processes, and parts can be machined with good reproducibility. PLASMA ARC WELDING (PAW) is a process similar to gas tungsten arc welding (GTAW). The electric arc is formed between an electrode generally made of sintered tungsten and the workpiece. The key difference from GTAW is that in PAW, by positioning the electrode within the body of the torch, the plasma arc can be separated from the shielding gas envelope. The plasma is then forced through a fine-bore copper nozzle which constricts the arc and the plasma exiting the orifice at high velocities and temperatures approaching 20,000 °C. Plasma arc welding is an advancement over the GTAW process. The PAW welding process uses a non-consumable tungsten electrode and an arc constricted through a fine-bore copper nozzle. PAW can be used to join all metals and alloys that are weldable with GTAW. Several basic PAW process variations are possible by varying the current, plasma gas flow rate, and the orifice diameter, including: Micro-plasma (< 15 Amperes) Melt-in mode (15–400 Amperes) Keyhole mode (>100 Amperes) In plasma arc welding (PAW) we obtain a greater energy concentration as compared to GTAW. Deep and narrow penetration is achievable, with a maximum depth of 12 to 18 mm (0.47 to 0.71 in) depending on the material. Greater arc stability allows a much longer arc length (stand-off), and much greater tolerance to arc length changes. As a disadvantage however, PAW requires relatively expensive and complex equipment as compared to GTAW. Also the torch maintenance is critical and more challenging. Other disadvantages of PAW are: Welding procedures tend to be more complex and less tolerant to variations in fit-up, etc. Operator skill required is a little more than for GTAW. Orifice replacement is necessary. KLIK Product Finder-Locator Service PAGE sadurunge
- Micromanufacturing, Surface & Bulk Micromachining, Microscale, MEMS
Micromanufacturing - Surface & Bulk Micromachining - Microscale Manufacturing - MEMS - Accelerometers - AGS-TECH Inc. Manufaktur Mikro / Micromanufacturing / Micromachining / MEMS MICROMANUFACTURING, MICROSCALE MANUFACTURING, MICROFABRICATION or MICROMACHINING refers to our processes suitable for making tiny devices and products in the micron or microns of dimensions. Sometimes the overall dimensions of a micromanufactured product may be larger, but we still use this term to refer to the principles and processes that are involved. We use the micromanufacturing approach to make the following types of devices: Microelectronic Devices: Typical examples are semiconductor chips that function based on electrical & electronic principles. Micromechanical Devices: These are products that are purely mechanical in nature such as very small gears and hinges. Microelectromechanical Devices: We use micromanufacturing techniques to combine mechanical, electrical and electronic elements at very small length scales. Most of our sensors are in this category. Microelectromechanical Systems (MEMS): These microelectromechanical devices also incorporate an integrated electrical system in one product. Our popular commercial products in this category are MEMS accelerometers, air-bag sensors and digital micromirror devices. Depending on the product to be fabricated, we deploy one of the following major micromanufacturing methods: BULK MICROMACHINING: This is a relatively older method which uses orientation-dependent etches on single-crystal silicon. The bulk micromachining approach is based on etching down into a surface, and stopping on certain crystal faces, doped regions, and etchable films to form the required structure. Typical products we are capable of micromanufacturing using bulk micromachining technique are: - Tiny cantilevers - V-groves in silicon for alignment and fixation of optical fibers. SURFACE MICROMACHINING: Unfortunately bulk micromachining is restricted to single-crystal materials, since polycrystalline materials will not machine at different rates in different directions using wet etchants. Therefore surface micromachining stands out as an alternative to bulk micromachining. A spacer or sacrificial layer such as phosphosilicate glass is deposited using CVD process onto a silicon substrate. Generally speaking, structural thin film layers of polysilicon, metal, metal alloys, dielectrics are deposited onto the spacer layer. Using dry etching techniques, the structural thin film layers are patterned and wet etching is used to remove the sacrificial layer, thereby resulting in free-standing structures such as cantilevers. Also possible is using combinations of bulk and surface micromachining techniques for turning some designs into products. Typical products suitable for micromanufacturing using a combination of the above two techniques: - Submilimetric size microlamps (in the order of 0.1 mm size) - Pressure sensors - Micropumps - Micromotors - Actuators - Micro-fluid-flow devices Sometimes, in order to obtain high vertical structures, micromanufacturing is performed on large flat structures horizontally and then the structures are rotated or folded into an upright position using techniques such as centrifuging or microassembly with probes. Yet very tall structures can be obtained in single crystal silicon using silicon fusion bonding and deep reactive ion etching. Deep Reactive Ion Etching (DRIE) micromanufacturing process is carried out on two separate wafers, then aligned and fusion bonded to produce very tall structures that would otherwise be impossible. LIGA MICROMANUFACTURING PROCESSES: The LIGA process combines X-ray lithography, electrodeposition, molding and generally involves the following steps: 1. A few hundreds of microns thick polymethylmetacrylate (PMMA) resist layer is deposited onto the primary substrate. 2. The PMMA is developed using collimated X-rays. 3. Metal is electrodeposited onto the primary substrate. 4. PMMA is stripped and a freestanding metal structure remains. 5. We use the remaining metal structure as a mould and perform injection molding of plastics. If you analyze the basic five steps above, using the LIGA micromanufacturing / micromachining techniques we can obtain: - Freestanding metal structures - Injection molded plastic structures - Using injection molded structure as a blank we can investment cast metal parts or slip-cast ceramic parts. The LIGA micromanufacturing / micromachining processes are time consuming and expensive. However LIGA micromachining produces these submicron precision molds which can be used to replicate the desired structures with distinct advantages. LIGA micromanufacturing can be used for example to fabricate very strong miniature magnets from rare-earth powders. The rare-earth powders are mixed with an epoxy binder and pressed to the PMMA mold, cured under high pressure, magnetized under strong magnetic fields and finally the PMMA is dissolved leaving behind the tiny strong rare-earth magnets which are one of the wonders of micromanufacturing / micromachining. We are also capable to develop multilevel MEMS micromanufacturing / micromachining techniques through wafer-scale diffusion bonding. Basically we can have overhanging geometries within MEMS devices, using a batch diffusion bonding and release procedure. For example we prepare two PMMA patterned and electroformed layers with the PMMA subsequently released. Next, the wafers are aligned face to face with guide pins and press fit together in a hot press. The sacrificial layer on one of the substrates is etched away which results in one of the layers bonded to the other. Other non-LIGA based micromanufacturing techniques are also available to us for the fabrication of various complex multilayer structures. SOLID FREEFORM MICROFABRICATION PROCESSES: Additive micromanufacturing is used for rapid prototyping. Complex 3D structures can be obtained by this micromachining method and no material removal takes place. Microstereolithography process uses liquid thermosetting polymers, photoinitiator and a highly focused laser source to a diameter as small as 1 micron and layer thicknesses of about 10 microns. This micromanufacturing technique is however limited to production of nonconducting polymer structures. Another micromanufacturing method, namely “instant masking” or also known as “electrochemical fabrication” or EFAB involves the production of an elastomeric mask using photolithography. The mask is then pressed against the substrate in an electrodeposition bath so that the elastomer conforms to substrate and excludes plating solution in contact areas. Areas that are not masked are electrodeposited as the mirror image of the mask. Using a sacrificial filler, complex 3D shapes are microfabricated. This “instant masking” micromanufacturing / micromachining method makes it also possible to produce overhangs, arches…etc. KLIK Product Finder-Locator Service PAGE sadurunge
- Glass Cutting Shaping Tools , USA , AGS-TECH Inc.
Glass Cutting Shaping Tools offered by AGS-TECH, Inc. We supply high quality diamond wheel series, diamond wheel for solar glass, diamond wheel for CNC machine, peripheral diamond wheel, cup & bowl shape diamond wheels, resin wheel series, polishing wheel series, felt wheel, stone wheel, coating removal wheel... Alat Pemotong Kaca Please click on the Glass Cutting and Shaping Tools of interest below to download related brochure. Diamond Wheel Series Diamond Wheel for Solar Glass Diamond Wheel for CNC Machine Peripheral Diamond Wheel Cup & Bowl Shape Diamond Wheel Resin Wheel Series Polishing Wheel Series 10S Polishing Wheel Felt Wheel Stone Wheel Coating Removal Wheel BD Polishing Wheel BK Polishing Wheel 9R Ploshing Wheel Polishing Material series Cerium Oxide Series Glass Drill Series Glass Tool Series Other Glass Tools Glass Plier Glass Suction & Lifter Grinding Tool Power Tool UV,Testing Tool Sandblast Fittings Series Machine Fittings Series Cutting Discs Glass Cutters Ungrouped Price of our glass cutting shaping tools depends on model and quantity of order. If you would like us to design and/or manufacture glass cutting and shaping tools specifically for you, please either provide us detailed blueprints, or ask us for help. We will then design, prototype and manufacture them specially for you. Since we carry a wide variety of glass cutting, drilling, grinding, polishing and shaping products with different dimensions, applications and material; it is impossible to list them here. We encourage you to email or call us so we can determine which product is the best fit for you. When contacting us, please inform us about: - Intended application - Material grade preferred - Dimensions - Finishing requirements - Packaging requirements - Labeling requirements - Quantity of your planned order & estimated yearly demand Private Label Auto Glass Repair and Replacement Systems We can private label these hand tools if you wish. In other words, we can put your company name, brand and label on them. This way you can promote your brand by reselling these to your customers. Private Label Hand Tools for Every Industry This catalog contains a few glass cutting and shaping tools. We can private label these hand tools if you wish. In other words, we can put your company name, brand and label on them. This way you can promote your brand by reselling these to your customers. Private Label Power Tool Accessories This brochure includes some glass cutting and shaping tools. We can private label these hand tools if you wish. In other words, we can put your company name, brand and label on them. This way you can promote your brand by reselling these to your customers. Private Label Power Tools for Every Industry This catalog contains some glass cutting and shaping tools. We can private label these hand tools if you wish. In other words, we can put your company name, brand and label on them. This way you can promote your brand by reselling these to your customers. KLIK kene kanggo ngundhuh kemampuan teknis lan pandhuan referensi kanggo nglereni, ngebur, grinding, mbentuk, mbentuk, alat polishing sing digunakake ing medis, dental, instrumentasi presisi, stamping logam, die forming lan aplikasi industri liyane. KLIK Product Finder-Locator Service Klik kene kanggo pindhah menyang Cut, Drilling, Grinding, Lapping, Polishing, Dicing lan Shaping Tools Menu Ref. Kode: OICASANHUA
- Surface Treatment and Modification - Surface Engineering - Hardening
Surface Treatment and Modification - Surface Engineering - Hardening - Plasma - Laser - Ion Implantation - Electron Beam Processing at AGS-TECH Pangobatan lumahing lan Modifikasi Surfaces cover everything. The appeal and functions material surfaces provide us are of utmost importance. Therefore SURFACE TREATMENT and SURFACE MODIFICATION are among our everyday industrial operations. Surface treatment & modification leads to enhanced surface properties and can be performed either as a final finishing operation or prior to a coating or joining operation. The processes of surface treatments and modification (also referred to as SURFACE ENGINEERING), tailor the surfaces of materials and products to: - Control friction and wear - Improve corrosion resistance - Enhance adhesion of subsequent coatings or joined parts - Change physical properties conductivity, resistivity, surface energy and reflection - Change chemical properties of surfaces by introducing functional groups - Change dimensions - Change the appearance, e.g., color, roughness…etc. - Clean and / or disinfect the surfaces Using surface treatment and modification, the functions and service lives of materials can be improved. Our common surface treatment and modification methods can be divided into two major categories: Surface Treatment and Modification That Covers Surfaces: Organic Coatings: The organic coatings apply paints, cements, laminates, fused powders and lubricants on the surfaces of materials. Inorganic Coatings: Our popular inorganic coatings are electroplating, autocatalytic plating (electroless platings), conversion coatings, thermal sprays, hot dipping, hardfacing, furnace fusing, thin film coatings such as SiO2, SiN on metal, glass, ceramics,….etc. Surface treatment and modification involving coatings is explained in detail under the related submenu, please click here Functional Coatings / Decorative Coatings / Thin Film / Thick Film Surface Treatment and Modification That Alters Surfaces: Here on this page we will concentrate on these. Not all of the surface treatment and modification techniques we describe below are on the micro or nano-scale, but we will nevertheless mention about them briefly since the basic objectives and methods are similar to significant extent to those that are on the micromanufacturing scale. Hardening: Selective surface hardening by laser, flame, induction and electron beam. High Energy Treatments: Some of our high energy treatments include ion implantation, laser glazing & fusion, and electron beam treatment. Thin Diffusion Treatments: Thin diffusion processes include ferritic-nitrocarburizing, boronizing, other high temperature reaction processes such as TiC, VC. Heavy Diffusion Treatments: Our heavy diffusion processes include carburizing, nitriding, and carbonitriding. Special Surface Treatments: Special treatments such as cryogenic, magnetic, and sonic treatments affect both the surfaces and the bulk materials. The selective hardening processes can be carried out by flame, induction, electron beam, laser beam. Large substrates are deep hardened using flame hardening. Induction hardening on the other hand is used for small parts. Laser and electron beam hardening are sometimes not distinguished from those in hardfacings or high-energy treatments. These surface treatment and modification processes are applicable only to steels that have sufficient carbon and alloy content to allow quench hardening. Cast irons, carbon steels, tool steels, and alloy steels are suitable for this surface treatment and modification method. Dimensions of parts are not significantly altered by these hardening surface treatments. Depth of hardening can vary from 250 microns to the whole section depth. However, in the whole section case, the section must be thin, less than 25 mm (1 in), or small, since the hardening processes require a rapid cooling of materials, sometimes within a second. This is difficult to achieve in large workpieces, and therefore in large sections, only the surfaces can be hardened. As a popular surface treatment and modification process we harden springs, knife blades, and surgical blades among many other products. High-energy processes are relatively new surface treatment and modification methods. Properties of surfaces are changed without changing the dimensions. Our popular high-energy surface treatment processes are electron beam treatment, ion implantation, and laser beam treatment. Electron Beam Treatment: Electron beam surface treatment alters the surface properties by rapid heating and rapid cooling — in the order of 10Exp6 Centigrade/sec (10exp6 Fahrenheit/sec) in a very shallow region around 100 microns near the material surface. Electron beam treatment can also be used in hardfacing to produce surface alloys. Ion Implantation: This surface treatment and modification method uses electron beam or plasma to convert gas atoms to ions with sufficient energy, and implant/insert the ions into atomic lattice of the substrate, accelerated by magnetic coils in a vacuum chamber. Vacuum makes it easier for ions to move freely in the chamber. The mismatch between implanted ions and the surface of the metal creates atomic defects that hardens the surface. Laser Beam Treatment: Like the electron beam surface treatment and modification, laser beam treatment alters the surface properties by rapid heating and rapid cooling in a very shallow region near the surface. This surface treatment & modification method can also be used in hardfacing to produce surface alloys. A know-how in Implant dosages and treatment parameters makes it possible for us to use these high energy surface treatment techniques in our fabrication plants. Thin Diffusion Surface Treatments: Ferritic nitrocarburizing is a case hardening process that diffuses nitrogen and carbon into ferrous metals at sub-critical temperatures. The processing temperature is usually at 565 Centigrade (1049 Fahrenheit). At this temperature steels and other ferrous alloys are still in a ferritic phase, which is advantageous compared to other case hardening processes that occur in the austenitic phase. The process is used to improve: •scuffing resistance •fatigue properties •corrosion resistance Very little shape distortion occurs during the hardening process thanks to the low processing temperatures. Boronizing, is the process where boron is introduced to a metal or alloy. It is a surface hardening and modification process by which boron atoms are diffused into the surface of a metal component. As a result the surface contains metal borides, such as iron borides and nickel borides. In their pure state these borides have extremely high hardness and wear resistance. Boronized metal parts are extremely wear resistant and will often last up to five times longer than components treated with conventional heat treatments such as hardening, carburizing, nitriding, nitrocarburizing or induction hardening. Heavy Diffusion Surface Treatment and Modification: If the carbon content is low (less than 0.25% for example) then we can increase the carbon content of the surface for hardening. The part can be either heat-treated by quenching in a liquid or cooled in still air depending on the properties desired. This method will only allow local hardening on the surface, but not in the core. This is sometimes very desirable because it allows for a hard surface with good wear properties as in gears, but has a tough inner core that will perform well under impact loading. In one of the surface treatment and modification techniques, namely Carburizing we add carbon to the surface. We expose the part to a Carbon rich atmosphere at an elevated temperature and allow diffusion to transfer the Carbon atoms into the steel. Diffusion will happen only if the steel has low carbon content, because diffusion works on the differential of the concentrations principle. Pack Carburizing: Parts are packed in a high carbon medium such as carbon powder and heated in a furnace for 12 to 72 hours at 900 Centigrade (1652 Fahrenheit). At these temperatures CO gas is produced which is a strong reducing agent. The reduction reaction occurs on the surface of the steel releasing carbon. The carbon is then diffused into the surface thanks to the high temperature. The Carbon on the surface is 0.7% to 1.2% depending on process conditions. The hardness achieved is 60 - 65 RC. The depth of the carburized case ranges from about 0.1 mm up to 1.5 mm. Pack carburizing requires good control of temperature uniformity and consistency in heating. Gas Carburizing: In this variant of surface treatment, Carbon Monoxide (CO) gas is supplied to a heated furnace and the reduction reaction of deposition of carbon takes place on the surface of the parts. This process overcomes most of the problems of pack carburizing. One concern however is the safe containment of the CO gas. Liquid Carburizing: The steel parts are immersed in a molten carbon rich bath. Nitriding is a surface treatment and modification process involving diffusion of Nitrogen into the surface of steel. Nitrogen forms Nitrides with elements such as Aluminum, Chromium, and Molybdenum. The parts are heat-treated and tempered before nitriding. The parts are then cleaned and heated in a furnace in an atmosphere of dissociated Ammonia (containing N and H) for 10 to 40 hours at 500-625 Centigrade (932 - 1157 Fahrenheit). Nitrogen diffuses into the steel and forms nitride alloys. This penetrates to a depth of up to 0.65 mm. The case is very hard and distortion is low. Since the case is thin, surface grinding is not recommended and therefore nitriding surface treatment may not be an option for surfaces with very smooth finishing requirements. Carbonitriding surface treatment and modification process is most suitable for low carbon alloy steels. In the carbonitriding process, both Carbon and Nitrogen are diffused into the surface. The parts are heated in an atmosphere of a hydrocarbon (such as methane or propane) mixed with Ammonia (NH3). Simply put, the process is a mix of Carburizing and Nitriding. Carbonitriding surface treatment is performed at temperatures of 760 - 870 Centigrade (1400 - 1598 Fahrenheit), It is then quenched in a natural gas (Oxygen free) atmosphere. The carbonitriding process is not suitable for high precision parts due to the distortions that are inherent. The hardness achieved is similar to carburizing (60 - 65 RC) but not as high as Nitriding (70 RC). The case depth is between 0.1 and 0.75 mm. The case is rich in Nitrides as well as Martensite. Subsequent tempering is needed to reduce brittleness. Special surface treatment and modification processes are in the early stages of development and their effectiveness is as yet unproven. They are: Cryogenic Treatment: Generally applied on hardened steels, slowly cool down the substrate to about -166 Centigrade (-300 Fahrenheit) to increase the density of the material and thus increase the wear resistance and dimension stability. Vibration Treatment: These intend to relieve thermal stress built-up in heat treatments through vibrations and increase the wear life. Magnetic Treatment: These intend to alter the line-up of atoms in materials through magnetic fields and hopefully improve the wear life. The effectiveness of these special surface treatment and modification techniques still remains to be proven. Also these three techniques above affect the bulk material besides surfaces. Please download our catalogs and brochures by clicking on the blue colored text below: - Private Label Nano Surface Protection Car Care Products We can label these products with your name and logo if you wish - Private Label Nano Surface Protection Industrial Products We can label these products with your name and logo if you wish - Private Label Nano Surface Protection Marine Products We can label these products with your name and logo if you wish - Private Label Nano Surface Protection Products We can label these products with your name and logo if you wish KLIK Product Finder-Locator Service PAGE sadurunge
- Display, Touchscreen, Monitors, LED, OLED, LCD, PDP, HMD, VFD, ELD
Display - Touchscreen - Monitors - LED - OLED - LCD - PDP - HMD - VFD - ELD - SED - Flat Panel Displays - AGS-TECH Inc. Tampilan & Layar Demek & Monitor Pabrikan lan Perakitan We offer: • Custom displays including LED, OLED, LCD, PDP, VFD, ELD, SED, HMD, Laser TV, flat panel display of required dimensions and electro-optic specifications. Please click on highlighted text to download relevant brochures for our display, touchscreen, and monitor products. - Catalog for Vandal-Proof IP65/IP67/IP68 Keyboards, Keypads, Pointing Devices, ATM Pinpads, Medical & Military Keyboards and other similar Rugged Computer Peripherals - Kiosk Systems (We private label these with your brand name and logo if you wish) - Kiosk Systems Accessories Guide (We private label these with your brand name and logo if you wish) - LED display panels - LCD modules - Mobile Computers for Enterprises (We private label these with your brand name and logo if you wish) - Process Automation Solutions (This brochure includes some industrial display products. We private label these with your brand name and logo if you wish) Download our brochure for TRu Multi-Touch Monitors. This monitor product line consists of a range of desktop, open frame, slim line and large format multi-touch displays - from 15” to 70''. Built for quality, responsiveness, visual appeal, and durability, TRu Multi-Touch Monitors complement any multi-touch interactive solution. Click here for pricing If you would like to have LCD modules specially designed & manufactured according to your requirements, please fill out and email us: Custom design form for LCD modules If you would like to have LCD panels specially designed & manufactured according to your requirements, please fill out and email us: Custom design form for LCD panels • Custom touchscreen ( such as iPod ) • Among the custom products our engineers have developed are: - A contrast measuring station for liquid crystal displays. - A computerized centering station for television projection lenses Panels / Displays are electronic screens used to view data and / or graphics and are available in a variety of sizes and technologies. Here are the meanings of abbreviated terms related to display, touchscreen and monitor devices: LED: Light Emitting Diode LCD: Liquid Crystal Display PDP: Plasma Display Panel VFD: Vacuum Fluorescent Display OLED: Organic Light Emitting Diode ELD: Electroluminescent Display SED: Surface-conduction Electron-emitter Display HMD: Head Mounted Display A significant benefit of OLED display over liquid crystal display (LCD) is that OLED does not require a backlight to function. Therefore OLED display draws far less power and, when powered from a battery, can operate longer as compared to LCD. Because there is no need for a backlight, an OLED display can be much thinner than an LCD panel. However, degradation of OLED materials has limited their use as display, touchscreen and monitor. ELD works by exciting atoms by passing an electric current through them, and causing ELD to emit photons. By varying the material being excited, the colour of the emitted light can be changed. ELD is constructed using flat, opaque electrode strips running parallel to each other, covered by a layer of electroluminescent material, followed by another layer of electrodes, running perpendicular to the bottom layer. The top layer must be transparent in order to let light go through and escape. At each intersection, the material lights, thereby creating a pixel. ELDs are sometimes used as backlights in LCDs. They are also useful for creating soft ambient light, and for low-colour, high-contrast screens. A surface-conduction electron-emitter display (SED) is a flat panel display technology that uses surface conduction electron emitters for each individual display pixel. The surface conduction emitter emits electrons that excite a phosphor coating on the display panel, similar to cathode ray tube (CRT) televisions. In other words, SEDs use tiny cathode ray tubes behind every single pixel instead of one tube for the whole display, and can combine the slim form factor of LCDs and plasma displays with the superior viewing angles, contrast, black levels, color definition and pixel response time of CRTs. It is also widely claimed that SEDs consume less power than LCD displays. A head-mounted display or Helmet mounted display, both abbreviated 'HMD', is a display device, worn on the head or as part of a helmet, that has a small display optic in front of one or each eye. A typical HMD has either one or two small displays with lenses and semi-transparent mirrors embedded in a helmet, eye-glasses or visor. The display units are small and may include CRT, LCDs, Liquid Crystal on Silicon, or OLED. Sometimes multiple micro-displays are deployed to increase total resolution and field of view. HMDs differ in whether they can display just a computer generated image (CGI), show live images from the real world or a combination of both. Most HMDs display only a computer-generated image, sometimes referred to as a virtual image. Some HMDs allow superimposing a CGI upon a real-world view. This is sometimes referred to as augmented reality or mixed reality. Combining real-world view with CGI can be done by projecting the CGI through a partially reflective mirror and viewing the real world directly. For partially reflective mirrors, check our page on Passive Optical Components. This method is often called Optical See-Through. Combining real-world view with CGI can also be done electronically by accepting video from a camera and mixing it electronically with CGI. This method is often called Video See-Through. Major HMD applications include military, governmental (fire, police, etc.) and civilian/commercial (medicine, video gaming, sports, etc.). Military, police and firefighters use HMDs to display tactical information such as maps or thermal imaging data while viewing the real scene. HMDs are integrated into the cockpits of modern helicopters and fighter aircraft. They are fully integrated with the pilot's flying helmet and may include protective visors, night vision devices and displays of other symbols and information. Engineers and scientists use HMDs to provide stereoscopic views of CAD (Computer Aided Design) schematics. These systems are also used in the maintenance of complex systems, as they can give a technician an effectively ''x-ray vision'' by combining computer graphics such as system diagrams and imagery with the technician's natural vision. There are also applications in surgery, wherein a combination of radiographic data (CAT scans and MRI imaging) is combined with the surgeon's natural view of the operation. Examples of lower cost HMD devices can be seen with 3D games and entertainment applications. Such systems allow 'virtual' opponents to peek from real windows as a player moves about. Other interesting developments in display, touchscreen and monitor technologies AGS-TECH is interested are: Laser TV: Laser illumination technology remained too costly to be used in commercially viable consumer products and too poor in performance to replace lamps except in some rare ultra-high-end projectors. More recently however, companies demonstrated their laser illumination source for projection displays and a prototype rear-projection ''laser TV''. The first commercial Laser TV and subsequently others have been unveiled. First audiences who were shown reference clips from popular movies reported that they were blown away by a Laser TV's hitherto unseen color-display prowess. Some people even describe it as being too intense to the point of seeming artificial. Some other future display technologies will likely include carbon nanotubes and nanocrystal displays using quantum dots to make vibrant and flexible screens. As always, if you provide us details of your requirement and application, we can design and custom manufacture displays, touchscreens and monitors for you. Click here to download brochure of our Panel Meters - OICASCHINT Dowload brochure for our DESIGN PARTNERSHIP PROGRAM More information on our engineering work can be found on: http://www.ags-engineering.com KLIK Product Finder-Locator Service PREVIOUS PAGE
- Mesh & Wire, USA, AGS-TECH Inc.
We supply wire and wire mesh, galvanized wires, metal wire, black annealed wire, wire mesh filters, wire cloth, perforated metal mesh, wire mesh fence and panels, conveyor belt mesh, wire mesh containers and customized wire mesh products to your specifications. Jaring & Kawat We supply wire and mesh products, including galvanized iron wires, PVC coated iron binding wires, wire mesh, wire net, fencing wires, conveyor belt mesh, perforated metal mesh. Besides our off-the-shelf wire mesh products we do custom manufacture mesh and metal wire products according to your specifications and needs. We cut to desired size, label and package according to customer requirements. Please click on submenus below to read more about a specific wire & mesh product. Galvanized Wires & Metal Wires These wires are used in numerous applications throughout industry. For example galvanized iron wires are frequently used for binding and attachment purposes, as ropes of considerable tensile strength. These metal wires can be hot dip galvanized and have metallic appearance or they can be PVC coated and be colored. Barbed wires have various razor types and are used for keeping intruders outside of restricted areas. Various wire gauges are available from stock. Long wires come in coils. If quantities justify, we may be able to manufacture them at your desired lengths and coil dimensions. Custom labeling and packaging of our Galvanized Wires, Metal Wires, Barbed Wire is possible. Download brochures: - Metal Wires - Galvanized - Black Annealed Wire Mesh Filters These are mostly made of thin stainless steel wire mesh and widely used in industry as filters for filtering liquids, dusts, powders...etc. Wire mesh filters have thicknesses in the few milimeters range. AGS-TECH has achieved manufacturing wire mesh with wire diameters less than 1 mm for electromagnetic shielding of military naval illumination systems. We manufacture wire mesh filters with dimensions according to customer specifications. Square, round and oval are commonly used geometries. Wire diameters and mesh count of our filters can be chosen by you. We cut them to size and frame the edges so the filter mesh does not get distorted or damaged. Our wire mesh filters possess high strainability, long lifespan, strong and reliable edges. Some usage areas of our wire mesh filters are chemical industry, pharmaceutical industry, brewage, beverage, electromagnetic shielding, automotive industry, mechanical applications, etc. - Wire Mesh and Cloth Brochure (includes wire mesh filters) Perforated Metal Mesh Our perforated metal mesh sheets are produced from galvanized steel, low carbon steel, stainless steel, copper plates, nickel plates or as requested by you, the customer. Various hole shapes and patterns can be stamped as you wish. Our perforated metal mesh offers smoothness, perfect surface flatness, strength and durability and is suitable for many applications. By supplying perforated metal mesh we have fulfilled the needs of many industries and applications including indoor sound insulation, silencer manufacturing, mining, medicine, food processing, ventilation, agricultural storage, mechanical protection and more. Call us today. We will happily cut, stamp, bend, fabricate your perforated metal mesh according to your specifications and needs. - Wire Mesh and Cloth Brochure (includes perforated metal mesh) Wire Mesh Fence & Panels & Reinforcement Wire mesh is widely used in construction, landscaping, home improvement, gardening, road building...etc., with popular applications of wire mesh as fence and reinforcement panels in construction. See our downloadable brochures below to choose your preferred model of mesh opening, wire gauge, color and finish. All of our wire mesh fence & panels and reinforcement products are compliant with international industry standards. A variety of wire mesh fence structures are available from stock. - Wire Mesh and Cloth Brochure (includes information on our fence & panels and reinforcement) Conveyor Belt Mesh Our Conveyor Belt Mesh are generally made of reinforced mesh stainless steel wire, stainless iron wire, nichrome wire, bullet wire. Applications of conveyor belt mesh are as filter and as conveyer belt for use in chemical industry, petroleum, metallurgy, food industry, pharmaceuticals, glass industry, delivery of parts within a plant or facility..., etc. Weave Style of most conveyor belt mesh is pre-bending to spring and then insertion of wire. Wire diameters are generally: 0.8-2.5mm Wire thicknesses are generally: 5-13.2mm Common colors are generally: Silver Generally width is between 0.4m-3m and lengths are between 0.5 - 100 m Conveyor belt mesh is heat resistant Chain type, width and length of conveyor belt mesh are among the customizable parameters. - Wire Mesh and Cloth Brochure (includes general information on our capabilities) Customized Wire Mesh Products (such as Cable Trays, Stirrup....etc.) From wire mesh and perforated metal mesh we can manufacture a variety of custom products such as cable trays, stirrers, Faraday cages & EM shielding structures, wire baskets and trays, architectural objects, objects of art, steel wire mesh gloves used in the meat industry for protection against injuries...etc. Our customized wire mesh, perforated metals, and expanded metals can be cut to size and flattened for your desired application. Flattened wire mesh is commonly used as machine guards, ventilation screens, burner screens, security screens, liquid drainage screens, ceiling panels and many other applications. We can create customized perforated metals with hole shapes and sizes to meet your project and product requirements. Perforated metals are versatile in their use. We can also provide coated wire mesh. Coatings can improve durability of your customized wire mesh products and also provide a rust resistant barrier. Custom wire mesh coatings available include Powder Coating, Electro-Polishing, Hot-Dipped Galvanizing, Nylon, Painting, Aluminizing, Electro-Galvanizing, PVC, Kevlar,...etc. Whether woven from wire as customized wire mesh, or stamped & punched and flattened from sheet metal as perforated sheets, contact AGS-TECH for your customized product requirements. - Wire Mesh and Cloth Brochure (includes plenty of information on our customized wire mesh production capabilities) - Wire Mesh Cable Trays and Baskets Brochure (besides the products in this brochure you can get customized cable trays according to your specifications) - Wire Mesh Container Quote Design Form (please click to download, fill out and email us) PAGE sadurunge
- Test Equipment for Furniture Testing
Test Equipment for Furniture Testing, Sofa Durability Tester, Chair Base Static Tester, Chair Drop Impact Tester, Mattress Firmness Tester Peralatan Test kanggo Testing Furnitur Specialized Test Equipment for Testing of Furniture are used for testing furniture products such as chairs, table, sofas, mattress....etc., for checking their quality, endurance, functionality, reliability, safety, compliance to domestic and international standards....etc. Our specialized test equipment can be either: - CUSTOM DESIGNED and MANUFACTURED SPECIALIZED TEST EQUIPMENT for FURNITURE TESTING or - OFF-SHELF SPECIALIZED TEST EQUIPMENT for FURNITURE TESTING Custom designed specialized testing equipment is designed and developed by us for our customers specific needs, taking into consideration our customers specific requirements, their markets, their legal responsibilities...etc. We work with you hand in hand to accomplish what you need and want. Our engineers design, prototype and get your approval prior to manufacturing your test machines. On the other hand, our off-shelf specialized test equipment for testing of furniture are already designed and manufactured systems that can be purchased quickly from us and used. If you let us know what you need, we will be happy to guide you and propose you ready systems that can help achieve your goals. Our off-shelf specialized test equipment for testing of furniture can be downloaded from the colored links below: HAIDA Bifma Furnitures Testing Machine HAIDA Chair Arm and Leg Tester HAIDA Chair Base Static Tester HAIDA Chair Caster Durability Tester HAIDA Chair Drop Impact Tester HAIDA Chair and Foam Testing Machine HAIDA Chair Seating and Back Durability HAIDA Chair Strength Tester HAIDA Chair Swivel Tester Catalog Download HAIDA Chair Universal Test Machine HAIDA Color Assessment Cabinet HAIDA Foam Pounding Fatigue Tester HAIDA Furniture Universal Test Machine HAIDA Mattress Cornell Tester HAIDA Mattress Firmness Tester HAIDA Mattress Rollator Durability Tester HAIDA Mattress Rollator Durability Tester-2 HAIDA Sofa Durability Tester HD-F769 HAIDA Sofa Durability Tester HD-F761 HAIDA Sofa Iron Frame Fatigue Tester HAIDA Universal Test Field for Tables Chairs Kanggo peralatan liyane sing padha, bukak situs web peralatan kita: http://www.sourceindustrialsupply.com KLIK Product Finder-Locator Service PREVIOUS PAGE
- Thermal Infrared Test Equipment, Thermal Camera, Differential Scanning
Thermal Infrared Test Equipment, Thermal Camera, Differential Scanning Calorimeter, Thermo Gravimetric Analyzer, Thermo Mechanical Analyzer, Dynamic Mechanical Peralatan Tes Termal & IR KLIK Product Finder-Locator Service Among the many THERMAL ANALYSIS EQUIPMENT, we focus our attention to the popular ones in industry, namely the DIFFERENTIAL SCANNING CALORIMETRY ( DSC ), THERMO-GRAVIMETRIC ANALYSIS ( TGA ), THERMO-MECHANICAL ANALYSIS ( TMA ), DILATOMETRY,DYNAMIC MECHANICAL ANALYSIS ( DMA ), DIFFERENTIAL THERMAL ANALYSIS ( DTA). Our INFRARED TEST EQUIPMENT involves THERMAL IMAGING INSTRUMENTS, INFRARED THERMOGRAPHERS, INFRARED CAMERAS. Some applications for our thermal imaging instruments are Electrical and Mechanical System Inspection, Electronic Component Inspection, Corrosion Damage and Metal Thinning, Flaw Detection. Please download catalogs from colored links below and let us know your prefered brand and model number of the product. You can purchase brand new or refurbished / used Thermal & IR Test Equipment from us: FLUKE Test Tools Catalog (includes Thermal Imagers, Thermometers) HAIDA Color Assessment Cabinet Private Label Hand Tools for Every Industry (This catalog contains a few thermal & IR test instruments. We can private label these hand tools if you wish. In other words, we can put your company name, brand and label on them. This way you can promote your brand by reselling these to your customers.) DIFFERENTIAL SCANNING CALORIMETERS (DSC) : A technique in which the difference in the amount of heat required to increase the temperature of a sample and reference is measured as a function of temperature. Both the sample and reference are maintained at nearly the same temperature throughout the experiment. The temperature program for a DSC analysis is established so that the sample holder temperature increases linearly as a function of time. The reference sample has a well-defined heat capacity over the range of temperatures to be scanned. DSC experiments provide as a result a curve of heat flux versus temperature or versus time. Differential scanning calorimeters are frequently used to study what happens to polymers when they're heated. The thermal transitions of a polymer can be studied using this technique. Thermal transitions are changes that take place in a polymer when they are heated. The melting of a crystalline polymer is an example. The glass transition is also a thermal transition. DSC thermal analysis is carried out for determining Thermal Phase Changes, Thermal Glass Transition Temperature (Tg), Crystalline Melt Temperatures, Endothermic Effects, Exothermic Effects, Thermal Stabilities, Thermal Formulation Stabilities, Oxidative Stabilities, Transition Phenomena, Solid State Structures. DSC analysis determines the Tg Glass Transition Temperature, temperature at which amorphous polymers or an amorphous part of a crystalline polymer go from a hard brittle state to a soft rubbery state, melting point, temperature at which a crystalline polymer melts, Hm Energy Absorbed (joules/gram), amount of energy a sample absorbs when melting, Tc Crystallization Point, temperature at which a polymer crystallizes upon heating or cooling, Hc Energy Released (joules/gram), amount of energy a sample releases when crystallizing. Differential Scanning Calorimeters can be used to determine the thermal properties of plastics, adhesives, sealants, metal alloys, pharmaceutical materials, waxes, foods, oils and lubricants and catalysts….etc. DIFFERENTIAL THERMAL ANALYZERS (DTA): An alternative technique to DSC. In this technique it is the heat flow to the sample and reference that remains the same instead of the temperature. When the sample and reference are heated identically, phase changes and other thermal processes cause a difference in temperature between the sample and reference. DSC measures the energy required to keep both the reference and the sample at the same temperature whereas DTA measures the difference in temperature between the sample and the reference when they are both put under the same heat. So they are similar techniques. THERMOMECHANICAL ANALYZER (TMA) : The TMA reveals the change in the dimensions of a sample as a function of temperature. One can regard TMA as a very sensitive micrometer. The TMA is a device that allows precise measurements of position and can be calibrated against known standards. A temperature control system consisting of a furnace, heat sink and a thermocouple surrounds the samples. Quartz, invar or ceramic fixtures hold the samples during tests. TMA measurements record changes caused by changes in the free volume of a polymer. Changes in free volume are volumetric changes in the polymer caused by the absorption or release of heat associated with that change; the loss of stiffness; increased flow; or by the change in relaxation time. The free volume of a polymer is known to be related to viscoelasticity, aging, penetration by solvents, and impact properties. The glass transition temperature Tg in a polymer corresponds to the expansion of the free volume allowing greater chain mobility above this transition. Seen as an inflection or bending in the thermal expansion curve, this change in the TMA can be seen to cover a range of temperatures. The glass transition temperature Tg is calculated by an agreed upon method. Perfect agreement is not immediately witnessed in the value of the Tg when comparing different methods, however if we carefully examine the agreed upon methods in determining the Tg values then we understand that there is actually good agreement. Besides its absolute value, the width of the Tg is also an indicator of changes in the material. TMA is a relatively simple technique to carry out. TMA is often used for measuring Tg of materials such as highly cross-linked thermoset polymers for which the Differential Scanning Calorimeter (DSC) is difficult to use. In addition to Tg, the coefficient of thermal expansion (CTE) is obtained from thermomechanical analysis. The CTE is calculated from the linear sections of the TMA curves. Another useful result the TMA can provide us is finding out the orientation of crystals or fibers. Composite materials may have three distinct thermal expansion coefficients in the x, y and z directions. By recording the CTE in x, y and z directions one may understand in which direction fibers or crystals are predominantly oriented. To measure the bulk expansion of the material a technique called DILATOMETRY can be used. The sample is immersed in a fluid such as silicon oil or Al2O3 powder in the dilatometer, run thru the temperature cycle and the expansions in all directions are converted to a vertical movement, which is measured by the TMA. Modern thermomechanical analyzers make this easy for users. If a pure liquid is used, the dilatometer is filled with that liquid instead of the silicon oil or alumina oxide. Using diamond TMA the users can run stress strain curves, stress relaxation experiments, creep-recovery and dynamic mechanical temperature scans. The TMA is an indispensible test equipment for industry and research. THERMOGRAVIMETRIC ANALYZERS ( TGA ) : Thermogravimetric Analysis is a technique where the mass of a substance or specimen is monitored as a function of temperature or time. The sample specimen is subjected to a controlled temperature program in a controlled atmosphere. The TGA measures a sample’s weight as it is heated or cooled in its furnace. A TGA instrument consists of a sample pan that is supported by a precision balance. That pan resides in a furnace and is heated or cooled during the test. The mass of the sample is monitored during the test. Sample environment is purged with an inert or a reactive gas. Thermogravimetric analyzers can quantify loss of water, solvent, plasticizer, decarboxylation, pyrolysis, oxidation, decomposition, weight % filler material, and weight % ash. Depending on the case, information may be obtained upon heating or cooling. A typical TGA thermal curve is displayed from left to right. If the TGA thermal curve descends, it indicates a weight loss. Modern TGAs are capable of conducting isothermal experiments. Sometimes the user may want to use a reactive sample purge gases, such as oxygen. When using oxygen as a purge gas user may want to switch gases from nitrogen to oxygen during the experiment. This technique is frequently used to identify the percent carbon in a material. Thermogravimetric analyzer can be used to compare two similar products, as a quality control tool to ensure products meet their material specifications, to ensure products meet safety standards, to determine carbon content, identifying counterfeit products, to identify safe operating temperatures in various gases, to enhance product formulation processes, to reverse engineer a product. Finally it is worth mentioning that combinations of a TGA with a GC/MS are available. GC is short for Gas Chromatography and MS is short for Mass Spectrometry. DYNAMIC MECHANICAL ANALYZER ( DMA) : This is a technique where a small sinusoidal deformation is applied to a sample of known geometry in a cyclic manner. The materials response to stress, temperature, frequency and other values is then studied. The sample can be subjected to a controlled stress or a controlled strain. For a known stress, the sample will deform a certain amount, depending on its stiffness. DMA measures stiffness and damping, these are reported as modulus and tan delta. Because we are applying a sinusoidal force, we can express the modulus as an in-phase component (the storage modulus), and an out of phase component (the loss modulus). The storage modulus, either E’ or G’, is the measure of the sample’s elastic behavior. The ratio of the loss to the storage is the tan delta and is called damping. It is considered a measure of the energy dissipation of a material. Damping varies with the state of the material, its temperature, and with the frequency. DMA is sometimes called DMTA standing for DYNAMIC MECHANICAL THERMAL ANALYZER. Thermomechanical Analysis applies a constant static force to a material and records the material dimensional changes as temperature or time varies. The DMA on the other hand, applies an oscillatory force at a set frequency to the sample and reports changes in stiffness and damping. DMA data provides us modulus information whereas the TMA data gives us the coefficient of thermal expansion. Both techniques detect transitions, but DMA is much more sensitive. Modulus values change with temperature and transitions in materials can be seen as changes in the E’ or tan delta curves. This includes glass transition, melting and other transitions that occur in the glassy or rubbery plateau which are indicators of subtle changes in the material. THERMAL IMAGING INSTRUMENTS, INFRARED THERMOGRAPHERS, INFRARED CAMERAS : These are devices that form an image using infrared radiation. Standard everyday cameras form images using visible light in the 450–750 nanometer wavelength range. Infrared cameras however operate in the infrared wavelength range as long as 14,000 nm. Generally, the higher an object's temperature, the more infrared radiation is emitted as black-body radiation. Infrared cameras work even in total darkness. Images from most infrared cameras have a single color channel because the cameras generally use an image sensor that does not distinguish different wavelengths of infrared radiation. To differentiate wavelengths color image sensors require a complex construction. In some test instruments these monochromatic images are displayed in pseudo-color, where changes in color are used rather than changes in intensity to display changes in the signal. The brightest (warmest) parts of images are customarily colored white, intermediate temperatures are colored red and yellow, and the dimmest (coolest) parts are colored black. A scale is generally shown next to a false color image to relate colors to temperatures. Thermal cameras have resolutions considerably lower than that of optical cameras, with values in the neighborhood of 160 x 120 or 320 x 240 pixels. More expensive infrared cameras can achieve a resolution of 1280 x 1024 pixels. There are two main categories of thermographic cameras: COOLED INFRARED IMAGE DETECTOR SYSTEMS and UNCOOLED INFRARED IMAGE DETECTOR SYSTEMS. Cooled thermographic cameras have detectors contained in a vacuum-sealed case and are cryogenically cooled. The cooling is necessary for the operation of the semiconductor materials used. Without cooling, these sensors would be flooded by their own radiation. Cooled infrared cameras are however expensive. Cooling requires much energy and is time-consuming, requiring several minutes of cooling time prior to working. Although the cooling apparatus is bulky and expensive, cooled infrared cameras offer users superior image quality compared to uncooled cameras. The better sensitivity of cooled cameras allows the use of lenses with higher focal length. Bottled nitrogen gas can be used for cooling. Uncooled thermal cameras use sensors operating at ambient temperature, or sensors stabilized at a temperature close to ambient using temperature control elements. Uncooled infrared sensors are not cooled to low temperatures and therefore do not require bulky and expensive cryogenic coolers. Their resolution and image quality however is lower as compared to cooled detectors. Thermographic cameras offer many opportunities. Overheating spots is power lines can be located and repaired. Electric circuitry can be observed and unusually hot spots can indicate problems such as short circuit. These cameras are also widely used in buildings and energy systems to locate places where there is significant heat loss so that better heat insulation can be considered at those points. Thermal imaging instruments serve as non-destructive test equipment. For details and other similar equipment, please visit our equipment website: http://www.sourceindustrialsupply.com PAGE sadurunge