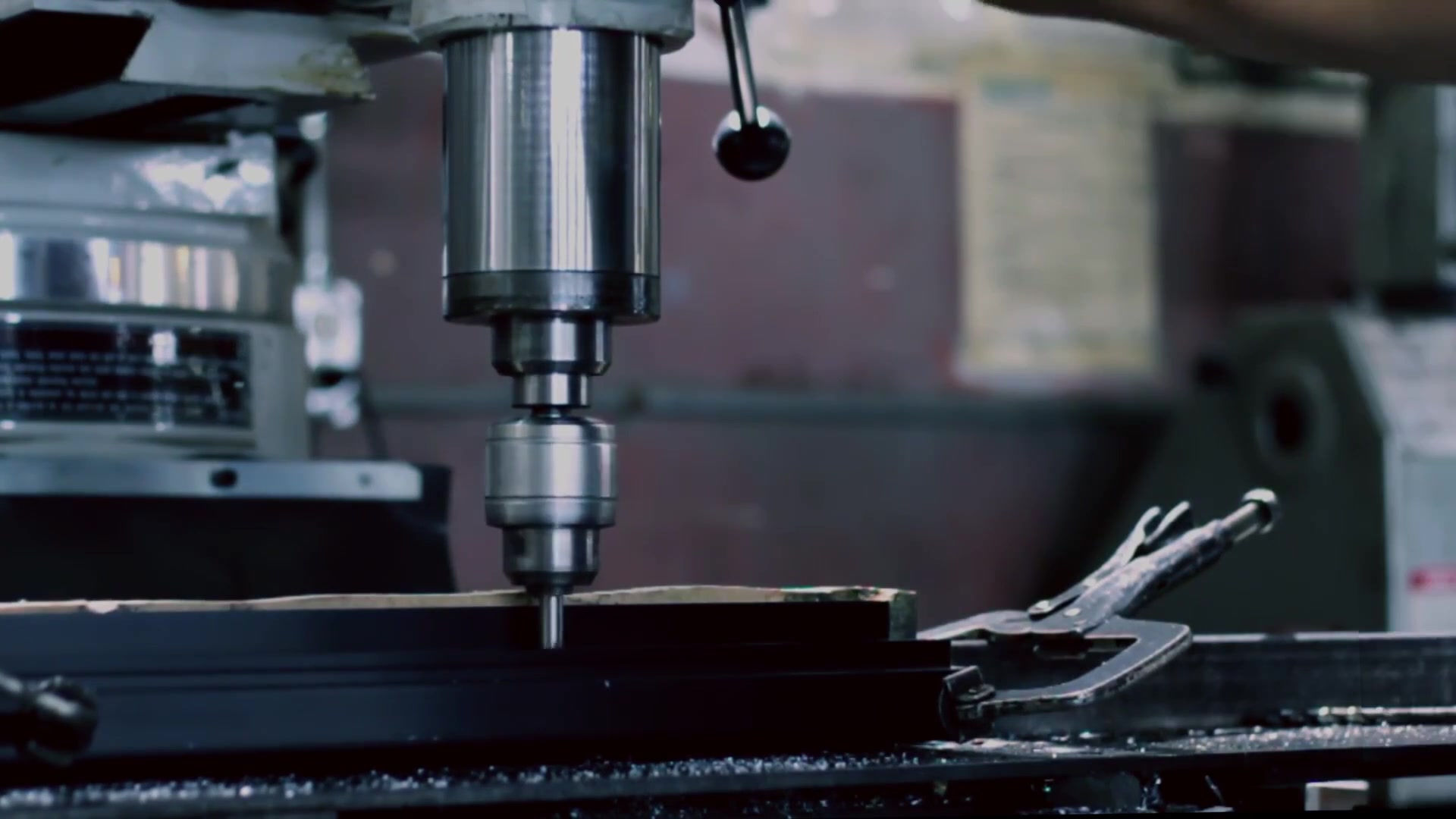
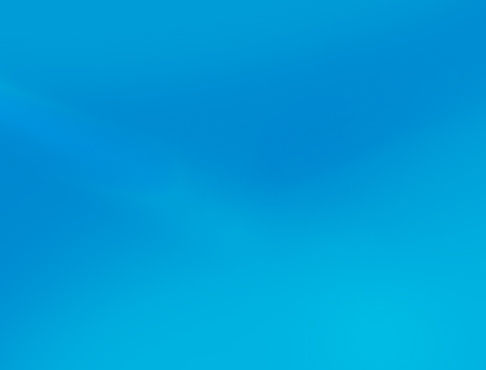
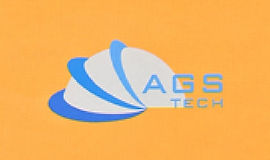
Produsen Custom Global, Integrator, Consolidator, Mitra Outsourcing kanggo Macem-macem Produk & Layanan.
Kita minangka sumber siji-mandeg kanggo manufaktur, fabrikasi, teknik, konsolidasi, integrasi, outsourcing produk & layanan sing digawe khusus lan ora kasedhiya. Kita uga label pribadi / label putih produk sampeyan kanthi jeneng merek yen sampeyan pengin.
Pilih Basa sampeyan
Manufaktur Custom Parts, Komponen, Rakitan, Produk Rampung, Mesin lan Peralatan Industri
Manufaktur Kontrak Domestik & Global
Outsourcing Produksi
Domestik, Pengadaan Global Produk Industri
Labeling pribadi / Label Putih Produk sampeyan nganggo Jeneng merek sampeyan
Product Finding & Locating Services
Desain Global lan Kemitraan Saluran
Integrasi Teknik
Layanan Teknik
Konsolidasi Global, Gudang, Logistik
Search Results
164 results found with an empty search
- Ultrasonic Machining, Ultrasonic Impact Grinding, Custom Manufacturing
Ultrasonic Machining, Ultrasonic Impact Grinding, Rotary Ultrasonic Machining, Non-Conventional Machining, Custom Manufacturing - AGS-TECH Inc. New Mexico, USA Mesin Ultrasonik & Rotary Mesin Ultrasonik & Penggilingan Dampak Ultrasonik Another popular NON-CONVENTIONAL MACHINING technique we frequently use is ULTRASONIC MACHINING (UM), also widely known as ULTRASONIC IMPACT GRINDING, where material is removed from a workpiece surface by microchipping and erosion with abrasive particles using a vibrating tool oscillating at ultrasonic frequencies, aided by an abrasive slurry that flows freely between the workpiece and the tool. It differs from most other conventional machining operations because very little heat is produced. The tip of the ultrasonic machining tool is called a “sonotrode” which vibrates at amplitudes of 0.05 to 0.125 mm and frequencies around 20 kHz. The vibrations of the tip transmit high velocities to fine abrasive grains between the tool and the surface of the workpiece. The tool never contacts the workpiece and therefore the grinding pressure is rarely more than 2 pounds. This working principle makes this operation perfect for machining extremely hard and brittle materials, such as glass, sapphire, ruby, diamond, and ceramics. The abrasive grains are located within a water slurry with a concentration between 20 to 60% by volume. The slurry also acts as the carrier of the debris away from the cutting / machining region. We use as abrasive grains mostly boron carbide, aluminum oxide and silicon carbide with grain sizes ranging from 100 for roughing processes to 1000 for our finishing processes. The ultrasonic-machining (UM) technique is best suited for hard and brittle materials like ceramics and glass, carbides, precious stones, hardened steels. The surface finish of ultrasonic machining depends upon the hardness of the workpiece/tool and the average diameter of the abrasive grains used. The tool tip is generally a low-carbon steel, nickel and soft steels attached to a transducer through the toolholder. The ultrasonic-machining process utilizes the plastic deformation of metal for the tool and the brittleness of the workpiece. The tool vibrates and pushes down on the abrasive slurry containing grains until the grains impact the brittle workpiece. During this operation, the workpiece is broken down while the tool bends very slightly. Using fine abrasives, we can achieve dimensional tolerances of 0.0125 mm and even better with ultrasonic-machining (UM). Machining time depends upon the frequency at which the tool is vibrating, the grain size and hardness, and the viscosity of the slurry fluid. The less viscous the slurry fluid, the faster it can carry away used abrasive. Grain size must be equal or greater than the hardness of the workpiece. As an example we can machine multiple aligned holes 0.4 mm in diameter on a 1.2 mm wide glass strip with ultrasonic machining. Let us get a little bit into the physics of the ultrasonic machining process. Microchipping in ultrasonic machining is possible thanks to the high stresses produced by particles striking the solid surface. Contact times between particles and surfaces are very short and in the order of 10 to 100 microseconds. The contact time can be expressed as: to = 5r/Co x (Co/v) exp 1/5 Here r is the radius of the spherical particle, Co is the elastic wave velocity in the workpiece (Co = sqroot E/d) and v is the velocity that the particle hits the surface with. The force a particle exerts on the surface is obtained from the rate of change of momentum: F = d(mv)/dt Here m is the grain mass. The average force of the particles (grains) hitting and rebounding from the surface is: Favg = 2mv / to Here to is the contact time. When numbers are plugged into this expression, we see that even though the parts are very small, since the contact area is also very small, the forces and thus the stresses exerted are significantly high to cause microchipping and erosion. ROTARY ULTRASONIC MACHINING (RUM): This method is a variation of ultrasonic machining, where we replace the abrasive slurry with a tool that has metal-bonded diamond abrasives that have been either impregnated or electroplated on the tool surface. The tool is rotated and ultrasonically vibrated. We press the workpiece at constant pressure against the rotating and vibrating tool. The rotary ultrasonic machining process gives us capabilities such as producing deep holes in hard materials at high material removal rates. Since we deploy a number of conventional and non-conventional manufacturing techniques, we can be of help to you whenever you have questions about a particular product and the fastest and most economical way of manufacturing & fabricating it. KLIK Product Finder-Locator Service PAGE sadurunge
- Electronic Testers, Electrical Properties Testing, Oscilloscope, Pulse
Electronic Testers - Electrical Test Equipment - Electrical Properties Testing - Oscilloscope - Signal Generator - Function Generator - Pulse Generator - Frequency Synthesizer - Multimeter Alat Uji Listrik & Elektronik With the term ELECTRONIC TESTER we refer to test equipment that is used primarily for testing, inspection and analysis of electrical and electronic components and systems. We offer the most popular ones in the industry: POWER SUPPLIES & SIGNAL GENERATING DEVICES: POWER SUPPLY, SIGNAL GENERATOR, FREQUENCY SYNTHESIZER, FUNCTION GENERATOR, DIGITAL PATTERN GENERATOR, PULSE GENERATOR, SIGNAL INJECTOR METERS: DIGITAL MULTIMETERS, LCR METER, EMF METER, CAPACITANCE METER, BRIDGE INSTRUMENT, CLAMP METER, GAUSSMETER / TESLAMETER/ MAGNETOMETER, GROUND RESISTANCE METER ANALYZERS: OSCILLOSCOPES, LOGIC ANALYZER, SPECTRUM ANALYZER, PROTOCOL ANALYZER, VECTOR SIGNAL ANALYZER, TIME-DOMAIN REFLECTOMETER, SEMICONDUCTOR CURVE TRACER, NETWORK ANALYZER, PHASE ROTATION TESTER, FREQUENCY COUNTER You can purchase brand new, refurbished or used test equipment from us at the most competitive discounted prices. Simply choose the product from the downloadable catalogs and let us know the product name, product code and relevant information and we will send you our quote. Download by clicking on highlighted text: ANRITSU Electronic Measuring Instruments FLUKE Test Tools Catalog KEYSIGHT Basic Automotive Test Products KEYSIGHT Basic Instruments KEYSIGHT Bench and Power Products KEYSIGHT Network Analyzer Products KEYSIGHT Signal Generation Solutions KEYSIGHT Smart Bench Essentials Series Products KEYSIGHT High-Volume Traffic Generator Products KEYSIGHT Layer 4-7 Network Test Products KEYSIGHT Layer 2-3 Network Test Products KEYSIGHT Distribution Products Catalog MEGGER Low Voltage Test Tools Catalog MICROWAVE Flexible Cable Assembly MICROWAVE and MILIMETER WAVE Test Accessories Brochure (Cable assemblies, VNA Test Assemblies, Mechanical Calibration Kits, RF Coaxial Adapters, Test Port Adapters, DC Blocks, NMD Connectors....etc.) Private Label Hand Tools for Every Industry (This catalog contains a few electrical & electronic test instruments. We can private label these hand tools if you wish. In other words, we can put your company name, brand and label on them. This way you can promote your brand by reselling these to your customers.) ROHDE SCHWARZ Benchtop Power Supplies Ideal for labs and system racks, galvanic isolation, floating channels, constant voltage or current modes, protection functions, parallel and serial operation, low ripple/noise, remote sensing option ROHDE SCHWARZ Test Equipment Catalog (Oscilloscopes, Power Supplies, Signal Generators, Handheld Analyzers, Spectrum Analyzers, Vector Network Analyzers, Meters & Counters) TEKTRONIX Product Catalog for Test and Measurement Solutions VANDAL-PROOF IP65/IP67/IP68 Keyboards, Keypads, Pointing Devices, ATM Pinpads, Medical & Military Keyboards and other similar Rugged Computer Peripherals For details and other similar equipment, please visit our equipment website: http://www.sourceindustrialsupply.com Let us briefly go over some of these equipment in everyday use throughout the industry: The electrical power supplies we supply for metrology purposes are discrete, benchtop and stand-alone devices. The ADJUSTABLE REGULATED ELECTRICAL POWER SUPPLIES are some of the most popular ones, because their output values can be adjusted and their output voltage or current is maintained constant even if there are variations in input voltage or load current. ISOLATED POWER SUPPLIES have power outputs that are electrically independent of their power inputs. Depending on their power conversion method, there are LINEAR and SWITCHING POWER SUPPLIES. The linear power supplies process the input power directly with all their active power conversion components working in the linear regions, whereas the switching power supplies have components working predominantly in non-linear modes (such as transistors) and convert power to AC or DC pulses before processing. Switching power supplies are generally more efficient than linear supplies because they lose less power due to shorter times their components spend in the linear operating regions. Depending on application, a DC or AC power is used. Other popular devices are PROGRAMMABLE POWER SUPPLIES, where voltage, current or frequency can be remotely controlled through an analog input or digital interface such as an RS232 or GPIB. Many of them have an integral microcomputer to monitor and control the operations. Such instruments are essential for automated testing purposes. Some electronic power supplies use current limiting instead of cutting off power when overloaded. Electronic limiting is commonly used on lab bench type instruments. SIGNAL GENERATORS are another widely used instruments in lab and industry, generating repeating or non-repeating analog or digital signals. Alternatively they are also called FUNCTION GENERATORS, DIGITAL PATTERN GENERATORS or FREQUENCY GENERATORS. Function generators generate simple repetitive waveforms such as sine waves, step pulses, square & triangular and arbitrary waveforms. With Arbitrary waveform generators the user can generate arbitrary waveforms, within published limits of frequency range, accuracy, and output level. Unlike function generators, which are limited to a simple set of waveforms, an arbitrary waveform generator allows the user to specify a source waveform in a variety of different ways. RF and MICROWAVE SIGNAL GENERATORS are used for testing components, receivers and systems in applications such as cellular communications, WiFi, GPS, broadcasting, satellite communications and radars. RF signal generators generally work between a few kHz to 6 GHz, while microwave signal generators operate within a much wider frequency range, from less than 1 MHz to at least 20 GHz and even up to hundreds of GHz ranges using special hardware. RF and microwave signal generators can be classified further as analog or vector signal generators. AUDIO-FREQUENCY SIGNAL GENERATORS generate signals in the audio-frequency range and above. They have electronic lab applications checking of the frequency response of audio equipment. VECTOR SIGNAL GENERATORS, sometimes also referred to as DIGITAL SIGNAL GENERATORS are capable of generating digitally-modulated radio signals. Vector signal generators can generate signals based on industry standards such as GSM, W-CDMA (UMTS) and Wi-Fi (IEEE 802.11). LOGIC SIGNAL GENERATORS are also called DIGITAL PATTERN GENERATOR. These generators produce logic types of signals, that is logic 1s and 0s in the form of conventional voltage levels. Logic signal generators are used as stimulus sources for functional validation & testing of digital integrated circuits and embedded systems. The devices mentioned above are for general-purpose use. There are however many other signal generators designed for custom specific applications. A SIGNAL INJECTOR is a very useful and quick troubleshooting tool for signal tracing in a circuit. Technicians can determine the faulty stage of a device such as a radio receiver very quickly. The signal injector can be applied to the speaker output, and if the signal is audible one can move to the preceding stage of the circuit. In this case an audio amplifier, and if the injected signal is heard again one can move the signal injection up the stages of the circuit until the signal is no longer audible. This will serve the purpose of locating the location of the problem. A MULTIMETER is an electronic measuring instrument combining several measurement functions in one unit. Generally, multimeters measure voltage, current, and resistance. Both digital and analog version are available. We offer portable hand-held multimeter units as well as laboratory-grade models with certified calibration. Modern multimeters can measure many parameters such as: Voltage (both AC / DC), in volts, Current (both AC / DC), in amperes, Resistance in ohms. Additionally, some multimeters measure: Capacitance in farads, Conductance in siemens, Decibels, Duty cycle as a percentage, Frequency in hertz, Inductance in henries, Temperature in degrees Celsius or Fahrenheit, using a temperature test probe. Some multimeters also include: Continuity tester; sounds when a circuit conducts, Diodes (measuring forward drop of diode junctions), Transistors (measuring current gain and other parameters), battery checking function, light level measuring function, acidity & Alkalinity (pH) measuring function and relative humidity measuring function. Modern multimeters are often digital. Modern digital multimeters often have an embedded computer to make them very powerful tools in metrology and testing. They include features such as:: •Auto-ranging, which selects the correct range for the quantity under test so that the most significant digits are shown. •Auto-polarity for direct-current readings, shows if the applied voltage is positive or negative. •Sample and hold, which will latch the most recent reading for examination after the instrument is removed from the circuit under test. •Current-limited tests for voltage drop across semiconductor junctions. Even though not a replacement for a transistor tester, this feature of digital multimeters facilitates testing diodes and transistors. •A bar graph representation of the quantity under test for better visualization of fast changes in measured values. •A low-bandwidth oscilloscope. •Automotive circuit testers with tests for automotive timing and dwell signals. •Data acquisition feature to record maximum and minimum readings over a given period, and to take a number of samples at fixed intervals. •A combined LCR meter. Some multimeters can be interfaced with computers, while some can store measurements and upload them to a computer. Yet another very useful tool, an LCR METER is a metrology instrument for measuring the inductance (L), capacitance (C), and resistance (R) of a component. The impedance is measured internally and converted for display to the corresponding capacitance or inductance value. Readings will be reasonably accurate if the capacitor or inductor under test does not have a significant resistive component of impedance. Advanced LCR meters measure true inductance and capacitance, and also the equivalent series resistance of capacitors and the Q factor of inductive components. The device under test is subjected to an AC voltage source and the meter measures the voltage across and the current through the tested device. From the ratio of voltage to current the meter can determine the impedance. The phase angle between the voltage and current is also measured in some instruments. In combination with the impedance, the equivalent capacitance or inductance, and resistance, of the device tested can be calculated and displayed. LCR meters have selectable test frequencies of 100 Hz, 120 Hz, 1 kHz, 10 kHz, and 100 kHz. Benchtop LCR meters typically have selectable test frequencies of more than 100 kHz. They often include possibilities to superimpose a DC voltage or current on the AC measuring signal. While some meters offer the possibility to externally supply these DC voltages or currents other devices supply them internally. An EMF METER is a test & metrology instrument for measuring electromagnetic fields (EMF). Majority of them measure the electromagnetic radiation flux density (DC fields) or the change in an electromagnetic field over time (AC fields). There are single axis and tri-axis instrument versions. Single axis meters cost less than tri-axis meters, but take longer to complete a test because the meter only measures one dimension of the field. Single axis EMF meters have to be tilted and turned on all three axes to complete a measurement. On the other hand, tri-axis meters measure all three axes simultaneously, but are more expensive. An EMF meter can measure AC electromagnetic fields, which emanate from sources such as electrical wiring, while GAUSSMETERS / TESLAMETERS or MAGNETOMETERS measure DC fields emitted from sources where direct current is present. The majority of EMF meters are calibrated to measure 50 and 60 Hz alternating fields corresponding to the frequency of US and European mains electricity. There are other meters which can measure fields alternating at as low as 20 Hz. EMF measurements can be broadband across a wide range of frequencies or frequency selective monitoring only the frequency range of interest. A CAPACITANCE METER is a test equipment used to measure capacitance of mostly discrete capacitors. Some meters display the capacitance only, whereas others also display leakage, equivalent series resistance, and inductance. Higher end test instruments use techniques such as inserting the capacitor-under-test into a bridge circuit. By varying the values of the other legs in the bridge so as to bring the bridge into balance, the value of the unknown capacitor is determined. This method ensures greater precision. The bridge may also be capable to measure series resistance and inductance. Capacitors over a range from picofarads to farads may be measured. Bridge circuits do not measure leakage current, but a DC bias voltage can be applied and the leakage measured directly. Many BRIDGE INSTRUMENTS can be connected to computers and data exchange be made to download readings or to control the bridge externally. Such bridge instruments aso offer go / no go testing for automation of tests in a fast paced production & quality control environment. Yet, another test instrument, a CLAMP METER is an electrical tester combining a voltmeter with a clamp type current meter. Most modern versions of clamp meters are digital. Modern clamp meters have most of the basic functions of a Digital Multimeter, but with the added feature of a current transformer built into the product. When you clamp the instrument’s “jaws” around a conductor carrying a large ac current, that current is coupled through the jaws, similar to the iron core of a power transformer, and into a secondary winding which is connected across the shunt of the meter’s input, the principle of operation resembling much that of a transformer. A much smaller current is delivered to the meter’s input due to the ratio of the number of secondary windings to the number of primary windings wrapped around the core. The primary is represented by the one conductor around which the jaws are clamped. If the secondary has 1000 windings, then the secondary current is 1/1000 the current flowing in the primary, or in this case the conductor being measured. Thus, 1 amp of current in the conductor being measured would produce 0.001 amps of current at the input of the meter. With clamp meters much larger currents can be easily measured by increasing the number of turns in the secondary winding. As with most of our test equipment, advanced clamp meters offer logging capability. GROUND RESISTANCE TESTERS are used for testing the earth electrodes and the soil resistivity. The instrument requirements depend on the range of applications. Modern clamp-on ground testing instruments simplify ground loop testing and enable non-intrusive leakage current measurements. Among the ANALYZERS we sell are OSCILLOSCOPES without doubt one of the most widely used equipment. An oscilloscope, also called an OSCILLOGRAPH, is a type of electronic test instrument that allows observation of constantly varying signal voltages as a two-dimensional plot of one or more signals as a function of time. Non-electrical signals like sound and vibration can also be converted to voltages and displayed on oscilloscopes. Oscilloscopes are used to observe the change of an electrical signal over time, the voltage and time describe a shape which is continuously graphed against a calibrated scale. Observation and analysis of the waveform reveals us properties such as amplitude, frequency, time interval, rise time, and distortion. Oscilloscopes can be adjusted so that repetitive signals can be observed as a continuous shape on the screen. Many oscilloscopes have storage function that allows single events to be captured by the instrument and displayed for a relatively long time. This allows us to observe events too fast to be directly perceptible. Modern oscilloscopes are lightweight, compact and portable instruments. There are also miniature battery-powered instruments for field service applications. Laboratory grade oscilloscopes are generally bench-top devices. There is a vast variety of probes and input cables for use with oscilloscopes. Please contact us in case you need advice about which one to use in your application. Oscilloscopes with two vertical inputs are called dual-trace oscilloscopes. Using a single-beam CRT, they multiplex the inputs, usually switching between them fast enough to display two traces apparently at once. There are also oscilloscopes with more traces; four inputs are common among these. Some multi-trace oscilloscopes use the external trigger input as an optional vertical input, and some have third and fourth channels with only minimal controls. Modern oscilloscopes have several inputs for voltages, and thus can be used to plot one varying voltage versus another. This is used for example for graphing I-V curves (current versus voltage characteristics) for components such as diodes. For high frequencies and with fast digital signals the bandwidth of the vertical amplifiers and sampling rate must be high enough. For-general purpose use a bandwidth of at least 100 MHz is usually sufficient. A much lower bandwidth is sufficient for audio-frequency applications only. Useful range of sweeping is from one second to 100 nanoseconds, with appropriate triggering and sweep delay. A well-designed, stable, trigger circuit is required for a steady display. The quality of the trigger circuit is key for good oscilloscopes. Another key selection criteria is the sample memory depth and sample rate. Basic level modern DSOs now have 1MB or more of sample memory per channel. Often this sample memory is shared between channels, and can sometimes only be fully available at lower sample rates. At the highest sample rates the memory may be limited to a few 10's of KB. Any modern ''real-time'' sample rate DSO will have typically 5-10 times the input bandwidth in sample rate. So a 100 MHz bandwidth DSO would have 500 Ms/s - 1 Gs/s sample rate. Greatly increased sample rates have largely eliminated the display of incorrect signals that was sometimes present in the first generation of digital scopes. Most modern oscilloscopes provide one or more external interfaces or buses such as GPIB, Ethernet, serial port, and USB to allow remote instrument control by external software. Here is a list of different oscilloscope types: CATHODE RAY OSCILLOSCOPE DUAL-BEAM OSCILLOSCOPE ANALOG STORAGE OSCILLOSCOPE DIGITAL OSCILLOSCOPES MIXED-SIGNAL OSCILLOSCOPES HANDHELD OSCILLOSCOPES PC-BASED OSCILLOSCOPES A LOGIC ANALYZER is an instrument that captures and displays multiple signals from a digital system or digital circuit. A logic analyzer may convert the captured data into timing diagrams, protocol decodes, state machine traces, assembly language. Logic Analyzers have advanced triggering capabilities, and are useful when the user needs to see the timing relationships between many signals in a digital system. MODULAR LOGIC ANALYZERS consist of both a chassis or mainframe and logic analyzer modules. The chassis or mainframe contains the display, controls, control computer, and multiple slots into which the data-capturing hardware is installed. Each module has a specific number of channels, and multiple modules can be combined to obtain a very high channel count. The ability to combine multiple modules to obtain a high channel count and the generally higher performance of modular logic analyzers makes them more expensive. For the very high end modular logic analyzers, the users may need to provide their own host PC or purchase an embedded controller compatible with the system. PORTABLE LOGIC ANALYZERS integrate everything into a single package, with options installed at the factory. They generally have lower performance than modular ones, but are economical metrology tools for general purpose debugging. In PC-BASED LOGIC ANALYZERS, the hardware connects to a computer through a USB or Ethernet connection and relays the captured signals to the software on the computer. These devices are generally much smaller and less expensive because they make use of a personal computer’s existing keyboard, display and CPU. Logic analyzers can be triggered on a complicated sequence of digital events, then capture large amounts of digital data from the systems under test. Today specialized connectors are in use. The evolution of logic analyzer probes has led to a common footprint that multiple vendors support, which provides added freedom to end users: Connectorless technology offered as several vendor-specific trade names such as Compression Probing; Soft Touch; D-Max is being used. These probes provide a durable, reliable mechanical and electrical connection between the probe and the circuit board. A SPECTRUM ANALYZER measures the magnitude of an input signal versus frequency within the full frequency range of the instrument. The primary use is to measure the power of the spectrum of signals. There are optical and acoustical spectrum analyzers as well, but here we will discuss only electronic analyzers that measure and analyze electrical input signals. The spectra obtained from electrical signals provides us information about frequency, power, harmonics, bandwidth…etc. The frequency is displayed on the horizonal axis and the signal amplitude on the vertical. Spectrum analyzers are widely used in the electronics industry for the analyses of the frequency spectrum of radio frequency, RF and audio signals. Looking at the spectrum of a signal we are able to reveal elements of the signal, and the performance of the circuit producing them. Spectrum analyzers are able to make a large variety of measurements. Looking at the methods used to obtain the spectrum of a signal we can categorize the spectrum analyzer types. - A SWEPT-TUNED SPECTRUM ANALYZER uses a superheterodyne receiver to down-convert a portion of the input signal spectrum (using a voltage-controlled oscillator and a mixer) to the center frequency of a band-pass filter. With a superheterodyne architecture, the voltage-controlled oscillator is swept through a range of frequencies, taking advantage of the full frequency range of the instrument. Swept-tuned spectrum analyzers are descended from radio receivers. Therefore swept-tuned analyzers are either tuned-filter analyzers (analogous to a TRF radio) or superheterodyne analyzers. In fact, in their simplest form, you could think of a swept-tuned spectrum analyzer as a frequency-selective voltmeter with a frequency range that is tuned (swept) automatically. It is essentially a frequency-selective, peak-responding voltmeter calibrated to display the rms value of a sine wave. The spectrum analyzer can show the individual frequency components that make up a complex signal. However it does not provide phase information, only magnitude information. Modern swept-tuned analyzers (superheterodyne analyzers, in particular) are precision devices that can make a wide variety of measurements. However, they are primarily used to measure steady-state, or repetitive, signals because they can't evaluate all frequencies in a given span simultaneously. The ability to evaluate all frequencies simultaneously is possible with only the real-time analyzers. - REAL-TIME SPECTRUM ANALYZERS: A FFT SPECTRUM ANALYZER computes the discrete Fourier transform (DFT), a mathematical process that transforms a waveform into the components of its frequency spectrum, of the input signal. The Fourier or FFT spectrum analyzer is another real-time spectrum analyzer implementation. The Fourier analyzer uses digital signal processing to sample the input signal and convert it to the frequency domain. This conversion is done using the Fast Fourier Transform (FFT). The FFT is an implementation of the Discrete Fourier Transform, the math algorithm used for transforming data from the time domain to the frequency domain. Another type of real-time spectrum analyzers, namely the PARALLEL FILTER ANALYZERS combine several bandpass filters, each with a different bandpass frequency. Each filter remains connected to the input at all times. After an initial settling time, the parallel-filter analyzer can instantaneously detect and display all signals within the analyzer's measurement range. Therefore, the parallel-filter analyzer provides real-time signal analysis. Parallel-filter analyzer is fast, it measures transient and time-variant signals. However, the frequency resolution of a parallel-filter analyzer is much lower than most swept-tuned analyzers, because the resolution is determined by the width of the bandpass filters. To get fine resolution over a large frequency range, you would need many many individual filters, making it costly and complex. This is why most parallel-filter analyzers, except the simplest ones in the market are expensive. - VECTOR SIGNAL ANALYSIS (VSA) : In the past, swept-tuned and superheterodyne spectrum analyzers covered wide frequency ranges from audio, thru microwave, to millimeter frequencies. In addition, digital signal processing (DSP) intensive fast Fourier transform (FFT) analyzers provided high-resolution spectrum and network analysis, but were limited to low frequencies due to the limits of analog-to-digital conversion and signal processing technologies. Today's wide-bandwidth, vector-modulated, time-varying signals benefit greatly from the capabilities of FFT analysis and other DSP techniques. Vector signal analyzers combine superheterodyne technology with high speed ADC's and other DSP technologies to offer fast high-resolution spectrum measurements, demodulation, and advanced time-domain analysis. The VSA is especially useful for characterizing complex signals such as burst, transient, or modulated signals used in communications, video, broadcast, sonar and ultrasound imaging applications. According to form factors, spectrum analyzers are grouped as benchtop, portable, handheld and networked. Benchtop models are useful for applications where the spectrum analyzer can be plugged into AC power,such as in a lab environment or manufacturing area. Bench top spectrum analyzers generally offer better performance and specifications than the portable or handheld versions. However they are generally heavier and have several fans for cooling. Some BENCHTOP SPECTRUM ANALYZERS offer optional battery packs, allowing them to be used away from a mains outlet. Those are referred to as a PORTABLE SPECTRUM ANALYZERS. Portable models are useful for applications where the spectrum analyzer needs to be taken outside to make measurements or carried while in use. A good portable spectrum analyzer is expected to offer optional battery-powered operation to allow the user to work in places without power outlets, a clearly viewable display to allow the screen to be read in bright sunlight, darkness or dusty conditions, light weight. HANDHELD SPECTRUM ANALYZERS are useful for applications where the spectrum analyzer needs to be very light and small. Handheld analyzers offer a limited capability as compared to larger systems. Advantages of handheld spectrum analyzers are however their very low power consumption, battery-powered operation while in the field to allow the user to move freely outside, very small size & light weight. Finally, NETWORKED SPECTRUM ANALYZERS do not include a display and they are designed to enable a new class of geographically-distributed spectrum monitoring and analysis applications. The key attribute is the ability to connect the analyzer to a network and monitor such devices across a network. While many spectrum analyzers have an Ethernet port for control, they typically lack efficient data transfer mechanisms and are too bulky and/or expensive to be deployed in such a distributed manner. The distributed nature of such devices enable geo-location of transmitters, spectrum monitoring for dynamic spectrum access and many other such applications. These devices are able to synchronize data captures across a network of analyzers and enable Network-efficient data transfer for a low cost. A PROTOCOL ANALYZER is a tool incorporating hardware and/or software used to capture and analyze signals and data traffic over a communication channel. Protocol analyzers are mostly used for measuring performance and troubleshooting. They connect to the network to calculate key performance indicators to monitor the network and speed-up troubleshooting activities. A NETWORK PROTOCOL ANALYZER is a vital part of a network administrator's toolkit. Network protocol analysis is used to monitor the health of network communications. To find out why a network device is functioning in a certain way, administrators use a protocol analyzer to sniff the traffic and expose the data and protocols that pass along the wire. Network protocol analyzers are used to - Troubleshoot hard-to-solve problems - Detect and identify malicious software / malware. Work with an Intrusion Detection System or a honeypot. - Gather information, such as baseline traffic patterns and network-utilization metrics - Identify unused protocols so that you can remove them from the network - Generate traffic for penetration testing - Eavesdrop on traffic (e.g., locate unauthorized Instant Messaging traffic or wireless Access Points) A TIME-DOMAIN REFLECTOMETER (TDR) is an instrument that uses time-domain reflectometry to characterize and locate faults in metallic cables such as twisted pair wires and coaxial cables, connectors, printed circuit boards,….etc. Time-Domain Reflectometers measure reflections along a conductor. In order to measure them, the TDR transmits an incident signal onto the conductor and looks at its reflections. If the conductor is of a uniform impedance and is properly terminated, then there will be no reflections and the remaining incident signal will be absorbed at the far end by the termination. However, if there is an impedance variation somewhere, then some of the incident signal will be reflected back to the source. The reflections will have the same shape as the incident signal, but their sign and magnitude depend on the change in impedance level. If there is a step increase in the impedance, then the reflection will have the same sign as the incident signal and if there is a step decrease in impedance, the reflection will have the opposite sign. The reflections are measured at the output/input of the Time-Domain Reflectometer and displayed as a function of time. Alternatively, the display can show the transmission and reflections as a function of cable length because the speed of signal propagation is almost constant for a given transmission medium. TDRs can be used to analyze cable impedances and lengths, connector and splice losses and locations. TDR impedance measurements provide designers the opportunity to perform signal integrity analysis of system interconnects and accurately predict the digital system performance. TDR measurements are widely used in board characterization work. A circuit board designer can determine the characteristic impedances of board traces, compute accurate models for board components, and predict board performance more accurately. There are many other areas of application for time-domain reflectometers. A SEMICONDUCTOR CURVE TRACER is a test equipment used to analyze the characteristics of discrete semiconductor devices such as diodes, transistors, and thyristors. The instrument is based on oscilloscope, but contains also voltage and current sources that can be used to stimulate the device under test. A swept voltage is applied to two terminals of the device under test, and the amount of current that the device permits to flow at each voltage is measured. A graph called V-I (voltage versus current) is displayed on the oscilloscope screen. Configuration includes the maximum voltage applied, the polarity of the voltage applied (including the automatic application of both positive and negative polarities), and the resistance inserted in series with the device. For two terminal devices like diodes, this is sufficient to fully characterize the device. The curve tracer can display all of the interesting parameters such as the diode's forward voltage, reverse leakage current, reverse breakdown voltage,…etc. Three-terminal devices such as transistors and FETs also use a connection to the control terminal of the device being tested such as the Base or Gate terminal. For transistors and other current based devices, the base or other control terminal current is stepped. For field effect transistors (FETs), a stepped voltage is used instead of a stepped current. By sweeping the voltage through the configured range of main terminal voltages, for each voltage step of the control signal, a group of V-I curves is generated automatically. This group of curves makes it very easy to determine the gain of a transistor, or the trigger voltage of a thyristor or TRIAC. Modern semiconductor curve tracers offer many attractive features such as intuitive Windows based user interfaces, I-V, C-V and pulse generation, and pulse I-V, application libraries included for every technology…etc. PHASE ROTATION TESTER / INDICATOR: These are compact and rugged test instruments to identify phase sequence on three-phase systems and open/de-energized phases. They are ideal for installing rotating machinery, motors and for checking generator output. Among the applications are the identification of proper phase sequences, detection of missing wire phases, determination of proper connections for rotating machinery, detection of live circuits. A FREQUENCY COUNTER is a test instrument that is used for measuring frequency. Frequency counters generally use a counter which accumulates the number of events occurring within a specific period of time. If the event to be counted is in electronic form, simple interfacing to the instrument is all that is needed. Signals of higher complexity may need some conditioning to make them suitable for counting. Most frequency counters have some form of amplifier, filtering and shaping circuitry at the input. Digital signal processing, sensitivity control and hysteresis are other techniques to improve performance. Other types of periodic events that are not inherently electronic in nature will need to be converted using transducers. RF frequency counters operate on the same principles as lower frequency counters. They have more range before overflow. For very high microwave frequencies, many designs use a high-speed prescaler to bring the signal frequency down to a point where normal digital circuitry can operate. Microwave frequency counters can measure frequencies up to almost 100 GHz. Above these high frequencies the signal to be measured is combined in a mixer with the signal from a local oscillator, producing a signal at the difference frequency, which is low enough for direct measurement. Popular interfaces on frequency counters are RS232, USB, GPIB and Ethernet similar to other modern instruments. In addition to sending measurement results, a counter can notify the user when user-defined measurement limits are exceeded. For details and other similar equipment, please visit our equipment website: http://www.sourceindustrialsupply.com CLICK Product Finder-Locator Service PAGE sadurunge
- Thickness Gauges, Ultrasonic Flaw Detector, Nondestructive Measurement
Thickness Gauges - Ultrasonic - Flaw Detector - Nondestructive Measurement of Thickness & Flaws from AGS-TECH Inc. - USA Ketebalan lan Cacat Gauges & Detektor AGS-TECH Inc. offers ULTRASONIC FLAW DETECTORS and a number of different THICKNESS GAUGES with different principles of operation. One of the popular types are the ULTRASONIC THICKNESS GAUGES ( also referred to as UTM ) which are measuring instruments for the NON-DESTRUCTIVE TESTING & investigation of a material's thickness using ultrasonic waves. Another type is HALL EFFECT THICKNESS GAUGE ( also referred to as MAGNETIC BOTTLE THICKNESS GAUGE ). The Hall Effect thickness gauges offer the advantage of accuracy not being affected by the shape of samples. A third common type of NON-DESTRUCTIVE TESTING ( NDT ) instruments are EDDY CURRENT THICKNESS GAUGES. Eddy-current-type thickness gauges are electronic instruments that measure variations in impedance of an eddy-current inducing coil caused by coating thickness variations. They can only be used if the electrical conductivity of the coating differs significantly from that of the substrate. Yet a classical type of instruments are the DIGITAL THICKNESS GAUGES. They come in a variety of forms and capabilities. Most of them are relatively inexpensive instruments that rely on contacting two opposing surfaces of the specimen to measure thickness. Some of the brand name thickness gauges and ultrasonic flaw detectors we sell are SADT, SINOAGE and MITECH. ELCOMETER Inspection Equipment (material and corrosion thickness measurement, flaw detection instruments available) MITECH Multimode U ltrasonic T hickness G auges MT180 and MT190, please CLICK HERE MITECH P roduct C omparison T able for Flaw Detectors please click here. MITECH Ultrasonic F law D etector MODEL MFD620C please click here. Private Label Hand Tools for Every Industry (This catalog contains a few thickness gauges. We can private label these hand tools if you wish. In other words, we can put your company name, brand and label on them. This way you can promote your brand by reselling these to your customers.) SADT-SINOAGE Ultrasonic Thickness Gauges, please CLICK HERE. SADT-SINOAGE Brand Metrology and Test Equipment, please CLICK HERE. ULTRASONIC THICKNESS GAUGES : What makes ultrasonic measurements so attractive is their ability to gauge thickness without a need for accessing both sides of the test specimen. Various versions of these instruments such as ultrasonic coating thickness gauge, paint thickness gauge and digital thickness gauge are commercially available. A variety of materials including metals, ceramics, glasses and plastics can be tested. The instrument measures the amount of time it takes sound waves to traverse from the transducer through the material to the back end of the part and then the time which the reflection takes to get back to the transducer. From the time measured, the instrument calculates the thickness based on the speed of sound through the specimen. The transducer sensors are generally piezoelectric or EMAT. Thickness gauges with both a predetermined frequency as well as some with tunable frequencies are available. The tunable ones allow inspection of a wider range of materials. Typical ultrasonic thickness gauge frequencies are 5 mHz. Our thickness gauges offer the capability to save data and to output it to data logging devices. Ultrasonic thickness gauges are non-destructive testers, they do not require access to both sides of the test specimens, some models can be used on coatings and linings, accuracies less than 0.1mm can be obtained, easy to use on the field and no need for lab environment. Some disadvantages are the requirement of calibration for each material, need for good contact with the material which sometimes requires special coupling gels or petroleum jelly to be used at the device/sample contact interface. Popular application areas of portable ultrasonic thickness gauges are shipbuilding, construction industries, pipelines and pipe manufacturing, container and tank manufacturing....etc. The technicians can easily remove dirt and corrosion from the surfaces and then apply the coupling gel and press the probe against the metal to measure thickness. Hall Effect gages measure total wall thicknesses only, while ultrasonic gages are capable to measure individual layers in multilayer plastic products. In HALL EFFECT THICKNESS GAUGES the measurement accuracy will not be affected by the shape of samples. These devices are based on the theory of Hall Effect. For testing, the steel ball is placed on one side of the sample and the probe on the other side. The Hall Effect sensor on the probe measures the distance from the probe tip to the steel ball. The calculator will display the real thickness readings. As you can imagine, this non-destructive test method offers quick measurement for spot thickness on area where accurate measurement of corners, small radii, or complex shapes are required. In nondestructive testing, Hall Effect gages employ a probe containing a strong permanent magnet and a Hall semiconductor connected to a voltage measurement circuit. If a ferromagnetic target such as a steel ball of known mass is placed in the magnetic field, it bends the field, and this changes the voltage across the Hall sensor. As the target is moved away from the magnet, the magnetic field and hence the Hall voltage, change in a predictable manner. Plotting these changes, an instrument can generate a calibration curve that compares the measured Hall voltage to the distance of the target from the probe. The information entered into the instrument during the calibration allows the gage to establish a lookup table, in effect plotting a curve of voltage changes. During measurements, the gage checks the measured values against the lookup table and displays thickness on a digital screen. Users only need to key in known values during calibration and let the gage do the comparing and calculating. The calibration process is automatic. Advanced equipment versions offer display of the real time thickness readings and automatically captures the minimum thickness. Hall Effect thickness gauges are widely used in plastic packaging industry with rapid measurement ability, up to 16 times per second and accuracies of about ±1%. They can store thousands of thickness readings in memory. Resolutions of 0.01 mm or 0.001 mm (equivalent to 0.001” or 0.0001”) are possible. EDDY CURRENT TYPE THICKNESS GAUGES are electronic instruments that measure variations in impedance of an eddy-current inducing coil caused by coating thickness variations. They can only be used if the electrical conductivity of the coating differs significantly from that of the substrate. Eddy current techniques can be used for a number of dimensional measurements. The ability to make rapid measurements without the need for couplant or, in some cases even without the need for surface contact, makes eddy current techniques very useful. The type of measurements that can be made include thickness of thin metal sheet and foil, and of metallic coatings on metallic and nonmetallic substrate, cross-sectional dimensions of cylindrical tubes and rods, thickness of nonmetallic coatings on metallic substrates. One application where the eddy current technique is commonly used to measure material thickness is in the detection and characterization of corrosion damage & thinning on the skins of aircraft. Eddy current testing can be used to do spot checks or scanners can be used to inspect small areas. Eddy current inspection has an advantage over ultrasound in this application because no mechanical coupling is required to get the energy into the structure. Therefore, in multi-layered areas of the structure like lap splices, eddy current can often determine if corrosion thinning is present in buried layers. Eddy current inspection has an advantage over radiography for this application because only single sided access is required to perform the inspection. To get a piece of radiographic film on the back side of the aircraft skin might require uninstalling interior furnishings, panels, and insulation which could be very costly and damaging. Eddy current techniques are also used to measure the thickness of hot sheet, strip and foil in rolling mills. An important application of tube-wall thickness measurement is the detection and assessment of external and internal corrosion. Internal probes must be used when the external surfaces are not accessible, such as when testing pipes that are buried or supported by brackets. Success has been achieved in measuring thickness variations in ferromagnetic metal pipes with the remote field technique. Dimensions of cylindrical tubes and rods can be measured with either outer diameter coils or internal axial coils, whichever is appropriate. The relationship between change in impedance and change in diameter is fairly constant, with the exception at very low frequencies. Eddy current techniques can determine thickness changes down to about three percent of the skin thickness. It is also possible to measure the thicknesses of thin layers of metal on metallic substrates, provided the two metals have widely differing electrical conductivities. A frequency must be selected such that there is complete eddy current penetration of the layer, but not of the substrate itself. The method has also been used successfully for measuring thickness of very thin protective coatings of ferromagnetic metals (such as chromium and nickel) on non-ferromagnetic metal bases. On the other hand, the thickness of nonmetallic coatings on metal substrates can be determined simply from the effect of liftoff on impedance. This method is used for measuring the thickness of paint and plastic coatings. The coating serves as a spacer between the probe and the conductive surface. As the distance between the probe and the conductive base metal increases, the eddy current field strength decreases because less of the probe's magnetic field can interact with the base metal. Thicknesses between 0.5 and 25 µm can be measured with an accuracy between 10% for lower values and 4% for higher values. DIGITAL THICKNESS GAUGES : They rely on contacting two opposing surfaces of the specimen to measure thickness. Most digital thickness gauges are switchable from metric reading to inch reading. They are limited in their capabilities because proper contacting is needed to make accurate measurements. They are also more prone to operator error due to variations from user to user’s specimen handling differences as well as the wide differences in specimen properties such as hardness, elasticity….etc. They may be however sufficient for some applications and their prices are lower compared to the other types of thickness testers. The MITUTOYO brand is well recognized for its digital thickness gauges. Our PORTABLE ULTRASONIC THICKNESS GAUGES from SADT are: SADT Models SA40 / SA40EZ / SA50 : SA40 / SA40EZ are the miniaturized ultrasonic thickness gauges that can measure wall thickness and velocity. These intelligent gauges are designed to measure the thickness of both metallic and nonmetallic materials such as steel, aluminum, copper, brass, silver and etc. These versatile models can easily be equipped with the low & high frequency probes, high temperature probe for demanding application environments. The SA50 ultrasonic thickness meter is micro-processor controlled and is based on the ultrasonic measurement principle. It is capable of measuring the thickness and acoustic speed of ultrasound transmitted through various materials. The SA50 is designed to measure the thickness of standard metal materials and metal materials covered with coating. Download our SADT product brochure from above link to see differences in measuring range, resolution, accuracy, memory capacity, ….etc between these three models. SADT Models ST5900 / ST5900+ : These instruments are the miniaturized ultrasonic thickness gauges that can measure wall thicknesses. The ST5900 has a fixed velocity of 5900 m/s, which is used only for measuring the wall thickness of steel. On the other hand, the model ST5900+ is capable to adjust velocity between 1000~9990m/s so that it can measure the thickness of both metallic and nonmetallic materials like steel, aluminum, brass, silver,…. etc. For details on various probes please download product brochure from the above link. Our PORTABLE ULTRASONIC THICKNESS GAUGES from MITECH are: Multi-Mode Ultrasonic Thickness Gauge MITECH MT180 / MT190 : These are multi-mode ultrasonic thickness gauges based on the same operating principles as SONAR. The instrument is capable of measuring the thickness of various materials with accuracies as high as 0.1/0.01 millimeters. The multi-mode feature of the gauge allows the user to toggle between pulse-echo mode (flaw and pit detection), and echo-echo mode (filtering paint or coating thickness). Multi-mode: Pulse-Echo mode and Echo-Echo mode. The MITECH MT180 / MT190 models are capable of performing measurements on a wide range of materials, including metals, plastic, ceramics, composites, epoxies, glass and other ultrasonic wave conducting materials. Various transducer models are available for special applications such as coarse grain materials and high temperature environments. The instruments offer Probe-Zero function, Sound-Velocity-Calibration function, Two-Point Calibration function, Single Point Mode and Scan Mode. The MITECH MT180 / MT190 models are capable of seven measurement readings per second in the single point mode, and sixteen per second in the scan mode. They have coupling status indicator, option for Metric/Imperial unit selection, battery information indicator for the remaining capacity of the battery, auto sleep and auto power off function to conserve battery life, optional software to process the memory data on the PC. For details on various probes and transducers please download product brochure from the above link. ULTRASONIC FLAW DETECTORS : Modern versions are small, portable, microprocessor-based instruments suitable for plant and field use. High frequency sound waves are used to detect hidden cracks, porosity, voids, flaws and discontinuities in solids such as ceramic, plastic, metal, alloys…etc. These ultrasonic waves reflect from or transmit through such flaws in the material or product in predictable ways and produce distinctive echo patterns. Ultrasonic flaw detectors are nondestructive test instruments (NDT testing). They are popular in testing of welded structures, structural materials, manufacturing materials. The majority of ultrasonic flaw detectors operate at frequencies between 500,000 and 10,000,000 cycles per second (500 KHz to 10 MHz), far beyond the audible frequencies our ears can detect. In ultrasonic flaw detection, generally the lower limit of detection for a small flaw is one-half wavelength and anything smaller than that will be invisible to the test instrument. The expression summarizing a sound wave is: Wavelength = Speed of Sound / Frequency Sound waves in solids exhibit various modes of propagation: - A longitudinal or compression wave is characterized by particle motion in the same direction as wave propagation. In other words the waves travel as a result of compressions and rarefactions in the medium. - A shear / transverse wave exhibits particle motion perpendicular to the direction of wave propagation. - A surface or Rayleigh wave has an elliptical particle motion and travels across the surface of a material, penetrating to a depth of approximately one wavelength. Seismic waves in earthquakes are also Rayleigh waves. - A plate or Lamb wave is a complex mode of vibration observed in thin plates where material thickness is less than one wavelength and the wave fills the entire cross-section of the medium. Sound waves may be converted from one form to another. When sound travels through a material and encounters a boundary of another material, a portion of the energy will be reflected back and a portion transmitted through. The amount of energy reflected, or reflection coefficient, is related to the relative acoustic impedance of the two materials. Acoustic impedance in turn is a material property defined as density multiplied by the speed of sound in a given material. For two materials, the reflection coefficient as a percentage of incident energy pressure is: R = (Z2 - Z1) / (Z2 + Z1) R = reflection coefficient (e.g. percentage of energy reflected) Z1 = acoustic impedance of first material Z2 = acoustic impedance of second material In ultrasonic flaw detection, the reflection coefficient approaches 100% for metal / air boundaries, which can be interpreted as all of the sound energy being reflected from a crack or discontinuity in the path of the wave. This makes ultrasonic flaw detection possible. When it comes to reflection and refraction of sound waves, the situation is similar to that of light waves. Sound energy at ultrasonic frequencies is highly directional and the sound beams used for flaw detection are well defined. When sound reflects off a boundary, the angle of reflection equals the angle of incidence. A sound beam that hits a surface at perpendicular incidence will reflect straight back. Sound waves that are transmitted from one material to another bend in accordance to Snell's Law of refraction. Sound waves hitting a boundary at an angle will be bent according to the formula: Sin Ø1/Sin Ø2 = V1/V2 Ø1 = Incident angle in first material Ø2= Refracted angle in second material V1 = Velocity of sound in the first material V2 = Velocity of sound in the second material Transducers of ultrasonic flaw detectors have an active element made of a piezoelectric material. When this element is vibrated by an incoming sound wave, it generates an electrical pulse. When it is excited by a high voltage electrical pulse, it vibrates across a specific spectrum of frequencies and generates sound waves. Because sound energy at ultrasonic frequencies does not travel efficiently through gasses, a thin layer of coupling gel is used between the transducer and the test piece. Ultrasonic transducers used in flaw detection applications are: - Contact Transducers: These are used in direct contact with the test piece. They send sound energy perpendicular to the surface and are typically used for locating voids, porosity, cracks, delaminations parallel to the outside surface of a part, as well as for measuring thickness. - Angle Beam Transducers: They are used in conjunction with plastic or epoxy wedges (angle beams) to introduce shear waves or longitudinal waves into a test piece at a designated angle with respect to the surface. They are popular in weld inspection. - Delay Line Transducers: These incorporate a short plastic waveguide or delay line between the active element and the test piece. They are used to improve near surface resolution. They are suitable for high temperature testing, where the delay line protects the active element from thermal damage. - Immersion Transducers: These are designed to couple sound energy into the test piece through a water column or water bath. They are used in automated scanning applications and also in situations where a sharply focused beam is needed for improved flaw resolution. - Dual Element Transducers: These utilize separate transmitter and receiver elements in a single assembly. They are often used in applications involving rough surfaces, coarse grained materials, detection of pitting or porosity. Ultrasonic flaw detectors generate and display an ultrasonic waveform interpreted with the aid of analysis software, to locate flaws in materials and finished products. Modern devices include an ultrasonic pulse emitter & receiver, hardware and software for signal capture and analysis, a waveform display, and a data logging module. Digital signal processing is used for stability and precision. The pulse emitter & receiver section provides an excitation pulse to drive the transducer, and amplification and filtering for the returning echoes. Pulse amplitude, shape, and damping can be controlled to optimize transducer performance, and receiver gain and bandwidth can be adjusted to optimize signal-to-noise ratios. Advanced version flaw detectors capture a waveform digitally and then perform various measurement and analysis on it. A clock or timer is used to synchronize transducer pulses and provide distance calibration. Signal processing generates a waveform display that shows signal amplitude versus time on a calibrated scale, digital processing algorithms incorporate distance & amplitude correction and trigonometric calculations for angled sound paths. Alarm gates monitor signal levels at selected points in the wave train and flag echoes from flaws. Screens with multicolor displays are calibrated in units of depth or distance. Internal data loggers record full waveform and setup information associated with each test, information like echo amplitude, depth or distance readings, presence or absence of alarm conditions. Ultrasonic flaw detection is basically a comparative technique. Using appropriate reference standards along with a knowledge of sound wave propagation and generally accepted test procedures, a trained operator identifies specific echo patterns corresponding to the echo response from good parts and from representative flaws. The echo pattern from a tested material or product may then be compared to the patterns from these calibration standards to determine its condition. An echo that precedes the backwall echo implies the presence of a laminar crack or void. Analysis of the reflected echo reveals the depth, size, and shape of the structure. In some cases testing is performed in a through transmission mode. In such a case the sound energy travels between two transducers placed on opposite sides of the test piece. If a large flaw is present in the sound path, the beam will be blocked and the sound will not reach the receiver. Cracks and flaws perpendicular to the surface of a test piece, or tilted with respect to that surface, are usually invisible with straight beam test techniques because of their orientation with respect to the sound beam. In such cases which are common in welded structures, angle beam techniques are used, employing either common angle beam transducer assemblies or immersion transducers aligned so as to direct sound energy into the test piece at a selected angle. As the angle of an incident longitudinal wave with respect to a surface increases, an increasing portion of the sound energy is converted to a shear wave in the second material. If the angle is high enough, all of the energy in the second material will be in the form of shear waves. The energy transfer is more efficient at the incident angles that generate shear waves in steel and similar materials. In addition, the minimum flaw size resolution is improved through the use of shear waves, since at a given frequency, the wavelength of a shear wave is approximately 60% the wavelength of a comparable longitudinal wave. The angled sound beam is highly sensitive to cracks perpendicular to the far surface of the test piece and, after bouncing off the far side it is highly sensitive to cracks perpendicular to the coupling surface. Our ultrasonic flaw detectors from SADT / SINOAGE are: Ultrasonic Flaw Detector SADT SUD10 and SUD20 : SUD10 is a portable, microprocessor-based instrument used widely in manufacturing plants and in the field. SADT SUD10, is a smart digital device with new EL display technology. SUD10 offers almost all functions of a professional nondestructive test instrument. The SADT SUD20 model has the same functions as SUD10, but is smaller and lighter. Here are some features of these devices: -High-speed capture and very low noise -DAC, AVG, B Scan -Solid metal housing (IP65) -Automated video of test process and play -High contrast viewing of the waveform at bright, direct sunlight as well as complete darkness. Easy reading from all angles. -Powerful PC software & data can be exported to Excel -Automated calibration of transducer Zero, Offset and/or Velocity -Automated gain, peak hold and peak memory functions -Automated display of precise flaw location (Depth d, level p, distance s, amplitude, sz dB, Ø) -Automated switch for three gauges (Depth d, level p, distance s) -Ten independent setup functions, any criteria can be input freely, can work in the field without test block -Big memory of 300 A graph and 30000 thickness values -A&B Scan -RS232/USB port, communication with PC is easy -The embedded software can be updated online -Li battery, continuous working time of up to 8 hours -Display freezing function -Automatic echo degree -Angles and K-value -Lock and unlock function of system parameters -Dormancy and screen savers -Electronic clock calendar -Two gates setting and alarm indication For details download our SADT / SINOAGE brochure from the link above. Some of our ultrasonic detectors from MITECH are: MFD620C Portable Ultrasonic Flaw Detector with hi-resolution color TFT LCD display. The background color and the wave color can be selectable according to the environment. LCD brightness can be manually set. Continue working for over 8 hours with high performance lithium-ion battery module (with large capacity lithium-ion battery option), easy to be dismantled and the battery module can be charged independently outside the device. It is light and portable, easily to be taken by one hand; easy operation; superior reliability guarantees long lifetime. Range: 0~6000mm (at steel velocity); range selectable in fixed steps or continuously variable. Pulser: Spike excitation with low, middle and high choices of the pulse energy. Pulse Repetition Rate: manually adjustable from 10 to 1000 Hz. Pulse width: Adjustable in a certain range to match different probes. Damping: 200, 300, 400, 500, 600 selectable to meet different resolution and sensitivity needs. Probe working mode: Single element, dual element and through transmission; Receiver: Real-time sampling at 160MHz high speed, enough to record the defect information. Rectification: Positive half wave, negative half wave, full wave, and RF : DB Step: 0dB, 0.1 dB, 2dB, 6dB step value as well as auto-gain mode Alarm: Alarm with sound and light Memory: Total 1000 configuration channels, all instrument operating parameters plus DAC/AVG curve can be stored; stored configuration data can be easily previewed and recalled for quick, repeatable instrument setup. Total 1000 datasets store all instrument operating parameters plus A-scan. All the configuration channels and datasets can be transferred to PC via USB port. Functions: Peak Hold: Automatically searches the peak wave inside the gate and holds it on the display. Equivalent diameter calculation: find out the peak echo and calculate its equivalent diameter. Continuous Record: Record the display continuously and save it to the memory inside the instrument. Defect Localization: Localize the defect position, including the distance, the depth and its plane projection distance. Defect Sizing: Calculate the defect size Defect Evaluation: Evaluate the defect by echo envelope. DAC: Distance Amplitude Correction AVG: Distance Gain Size curve function Crack measure: Measure and calculate the crack depth B-Scan: Display the cross-section of the test block. Real-Time Clock: Real time clock for tracking the time. Communication: USB2.0 high-speed communication port For details and other similar equipment, please visit our equipment website: http://www.sourceindustrialsupply.com KLIK Product Finder-Locator Service PAGE sadurunge
- Mesomanufacturing,Mesoscale Manufacturing,Miniature Device Fabrication
Mesomanufacturing - Mesoscale Manufacturing - Miniature Device Fabrication - Tiny Motors - AGS-TECH Inc. - New Mexico Manufaktur Mesoscale / Mesomanufacturing With conventional production techniques we produce “macroscale” structures that are relatively large and visible to the naked eye. With MESOMANUFACTURING however we produce components for miniature devices. Mesomanufacturing is also referred to as MESOSCALE MANUFACTURING or MESO-MACHINING. Mesomanufacturing overlaps both macro and micromanufacturing. Examples of mesomanufacturing are hearing aides, stents, very small motors. The first approach in mesomanufacturing is to scale macromanufacturing processes down. For example a tiny lathe with dimensions in the few dozen millimeters and a motor of 1.5W weighing 100 grams is a good example of mesomanufacturing where downscaling has taken place. The second approach is to scale micromanufacturing processes up. As an example LIGA processes can be upscaled and enter the realm of mesomanufacturing. Our mesomanufacturing processes are bridging the gap between silicon-based MEMS processes and conventional miniature machining. Mesoscale processes can fabricate two and three-dimensional parts having micron size features in traditional materials such as stainless steels, ceramics, and glass. Mesomanufacturing processes that are currently available to us include, focused ion beam (FIB) sputtering, micro-milling, micro-turning, excimer laser ablation, femto-second laser ablation, and micro electro-discharge (EDM) machining. These mesoscale processes employ subtractive machining technologies (i.e., material removal), whereas the LIGA process, is an additive mesoscale process. Mesomanufacturing processes have different capabilities and performance specifications. Machining performance specifications of interest include minimum feature size, feature tolerance, feature location accuracy, surface finish, and material removal rate (MRR). We have the capability of mesomanufacturing electro-mechanical components that require mesoscale parts. The mesoscale parts fabricated by subtractive mesomanufacturing processes have unique tribological properties because of the variety of materials and the surface conditions produced by the different mesomanufacturing processes. These subtractive mesoscale machining technologies bring us concerns related to cleanliness, assembly, and tribology. Cleanliness is vital in mesomanufacturing because mesoscale dirt and debris particle size created during the meso-machining process can be comparable to mesoscale features. Mesoscale milling and turning can create chips and burrs that can block holes. Surface morphology and surface finish conditions vary greatly depending on the mesomanufacturing method. Mesoscale parts are difficult to handle and align which makes assembly a challenge which most of our competitors are unable to overcome. Our yield rates in mesomanufacturing is far higher than our competitors which gives us the advantage of being able to offer better prices. MESOSCALE MACHINING PROCESSES: Our major mesomanufacturing techniques are Focused Ion Beam (FIB), Micro-milling, & Micro-turning, laser meso-machining, Micro-EDM (electro-discharge machining) Mesomanufacturing using focused Ion Beam (FIB), Micro-milling, & Micro-turning: The FIB sputters material from a workpiece by Gallium ion beam bombardment. The workpiece is mounted to a set of precision stages and is placed in a vacuum chamber underneath the source of Gallium. The translation and rotation stages in the vacuum chamber make various locations on the work piece available to the beam of Gallium ions for FIB mesomanufacturing. A tunable electric field scans the beam to cover a pre-defined projected area. A high voltage potential causes a source of Gallium ions to accelerate and collide with the work piece. The collisions strip away atoms from the work piece. The result of the FIB meso-machining process can be the creation of a near vertical facets. Some FIBs available to us have beam diameters as small as 5 nanometers, making the FIB a mesoscale and even microscale capable machine. We mount micro-milling tools on high precision milling machines to machine channels in aluminum. Using FIB we can fabricate micro-turning tools which can then be used on a lathe to fabricate finely threaded rods. In other words, FIB can be used to machine hard tooling besides directly meso-machining features onto the end work piece. The slow material removal rate has rendered the FIB as impractical for directly machining large features. The hard tools, however, can remove material at an impressive rate and are durable enough for several hours of machining time. Nevertheless, the FIB is practical for directly meso-machining complex three dimensional shapes that do not require a substantial material removal rate. Length of exposure and angle of incidence can greatly affect the geometry of directly machined features. Laser Mesomanufacturing: Excimer lasers are used for mesomanufacturing. The excimer laser machines material by pulsing it with nanosecond pulses of ultraviolet light. The work piece is mounted to precision translational stages. A controller coordinates the motion of the work piece relative to the stationary UV laser beam and coordinates the firing of the pulses. A mask projection technique can be used to define meso-machining geometries. The mask is inserted into the expanded part of the beam where the laser fluence is too low to ablate the mask. The mask geometry is de-magnified through the lens and projected onto the work piece. This approach can be used for machining multiple holes (arrays) simultaneously. Our excimer and YAG lasers can be used to machine polymers, ceramics, glass and metals having feature sizes as small as 12 microns. Good coupling between the UV wavelength (248 nm) and the workpiece in laser mesomanufacturing / meso-machining results in vertical channel walls. A cleaner laser meso-machining approach is to use a Ti-sapphire femtosecond laser. The detectable debris from such mesomanufacturing processes are nano-sized particles. Deep one micron-size features can be microfabricated using the femtosecond laser. The femtosecond laser ablation process is unique in that it breaks atomic bonds instead of thermally ablating material. The femtosecond laser meso-machining / micromachining process has a special place in mesomanufacturing because it is cleaner, micron capable, and it is not material specific. Mesomanufacturing using Micro-EDM (electro-discharge machining): Electro-discharge machining removes material through a spark erosion process. Our micro-EDM machines can produce features as small as 25 microns. For the sinker and the wire micro-EDM machine, the two major considerations for determining feature size are the electrode size and the over-bum gap. Electrodes little over 10 microns in diameter and over-bum as little as a few microns are being used. Creating an electrode having a complex geometry for the sinker EDM machine requires know-how. Both graphite and copper are popular as electrode materials. One approach to fabricating a complicated sinker EDM electrode for a mesoscale part is to use the LIGA process. Copper, as the electrode material, can be plated into LIGA molds. The copper LIGA electrode can then be mounted onto the sinker EDM machine for mesomanufacturing a part in a different material such as stainless steel or kovar. No one mesomanufacturing process is sufficient for all operations. Some mesoscale processes are more wide reaching than others, but each process has its niche. Most of the time we require a variety of materials to optimize performance of mechanical components and are comfortable with traditional materials such as stainless steel because these materials have a long history and have been very well characterized through the years. Mesomanufacturing processes allow us to use traditional materials. Subtractive mesoscale machining technologies expand our material base. Galling may be an-issue with some material combinations in mesomanufacturing. Each particular mesoscale machining process uniquely affects the surface roughness and morphology. Micro-milling and micro-turning may generate burrs and particles that can cause mechanical problems. Micro-EDM may leave a recast layer that can have particular wear and friction characteristics. Friction effects between mesoscale parts may have limited points of contact and are not accurately modeled by surface contact models. Some mesoscale machining technologies, such as micro-EDM, are fairly mature, as opposed to others, such as femtosecond laser meso-machining, which still require additional development. KLIK Product Finder-Locator Service PAGE sadurunge
- Electronic Components, Diodes, Transistors, Thermoelectric Cooler, TEC
Electronic Components, Diodes, Transistors - Resistors, Thermoelectric Cooler, Heating Elements, Capacitors, Inductors, Driver, Device Sockets and Adapters Komponen lan Majelis Listrik & Elektronik As a custom manufacturer and engineering integrator, AGS-TECH can supply you the following ELECTRONIC COMPONENTS and ASSEMBLIES: • Active and passive electronic components, devices, subassemblies and finished products. We can either use the electronic components in our catalogs and brochures listed below or use your prefered manufacturers components in your electronic products assembly. Some of the electronic components and assembly can be custom tailored according to your needs and requirements. If your order quantities justify, we can have the manufacturing plant produce according to your specifications. You can scroll down and download our brochures of interest by clicking on highlighted text: Antenna Brochure for 5G - LTE 4G - LPWA 3G - 2G - GPS - GNSS - WLAN - BT - Combo - ISM Chip resistors Chip resistors product line Custom Specialized Cable Assemblies Brochure for Lighting, Touch Technology, Industrial Electronics, Security, White Goods, Aerospace, Military, Telecom, Medical & Sterilizable, Renewable Energy...etc. Diodes and rectifiers Disc capacitors catalog High frequency devices product line (Band Pass Filters, Low Pass Filters, IPD, CPL, Balanced Filter, Diplexer, Balun, Chip Antenna...etc.) Microwave Flexible Cable Assembly Microwave and Milimeter Wave Test Accessories Brochure (Cable assemblies, VNA Test Assemblies, Mechanical Calibration Kits, RF Coaxial Adapters, Test Port Adapters, DC Blocks, NMD Connectors....etc.) Microwave Waveguides - Coaxial Components - Milimeterwave Antennas (Straight Waveguide, Waveguide Bend, Waveguide to Coaxial Adapter, Directional Couplers, Waveguide Tee, Circulators, Isolators......etc.) Multilayer ceramic capacitors MLCC catalog Multilayer ceramic capacitors MLCC product line Off-shelf interconnect components and hardware Precision RF Adapter s Catalog (Coax RF, Microwave, mmWave Adapters such as SMA, SSMA, SMP, BNC, Type-N, 3.5 mm.....etc) RF Components Brochure for Coaxial Fixed Attenuators, Coaxial Terminations, DC Blocks, Coax Adapters, Waveguide Components, Power Dividers, RF Connectors, RF Tools. RF devices and high frequency inductors (Multilayer Ceramic Capacitors, Chip-Resistor, Disc Capacitors, RF & HF Inductor Varistors & SMD-Varistors, Chip Antenna, Filters, Coupler) RF and Microwave Components (Broadband 90/180 Degree Hybrid and Coupler, Broadband Power Divider, Filter, RF switch, Broadband Amplifier, Broadband Frequency Synthesizer) RF Product Overview Chart (RF Antenna, Multilayer Ceramic Filter, Multilayer Ceramic Balun, Ceramic Diplexer) Soft Ferrites - Cores - Toroids - EMI Suppression Products - RFID Transponders and Accessories Brochure Terminal Blocks and Connectors Terminal Blocks General Catalogue Receptacles-Power Entry-Connectors Catalogue Vandal-Proof IP65/IP67/IP68 Keyboards, Keypads, Pointing Devices, ATM Pinpads, Medical & Military Keyboards and other similar Rugged Computer Peripherals Varistors Varistors product overview Yaren Model MOSFET - SCR - FRD - Voltage Control Devices - Bipolar Transistors Zeasset Model Electrolytic Capacitors • Other electronic components and assembly we have been providing are pressure sensors, temperature sensors, conductivity sensors, proximity sensors, humidity sensors, speed sensor, shock sensor, chemical sensor, inclination sensor, load cell, strain gauges. To download related catalogs and brochures of these, please click on colored text: Coding system for off-shelf strain gauges Digital Temperature Transmitter UTI2 Digital Temperature Transmitter UTI6 Din Rail Mounted Temperature Transmitters UTB11 Electronic Temperature Switch UTS2 Explosive Proof Temperature Transmitter UTB4 Integrated Temperature Transmitter UTB8 Intelligent Temperature Transmitter UTI5 Load cells, weight sensors, load gauges, transducers and transmitters Pressure sensors, pressure gauges, transducers and transmitters Process Automation Solutions (We private label these with your brand name and logo if you wish) Proximity sensors Sensors & Analytical Measurement Systems for Liquid Analysis (We private label these with your brand name and logo if you wish) Sensors & Analytical Measurement Systems for Optical OEM Applications in Liquid Analysis (We private label these with your brand name and logo if you wish) Sensors & Analytical Measurement Systems for pH Testing (We private label these with your brand name and logo if you wish) Smart Temperature Transmitter UTB-101 Sockets and accessories of proximity sensors Strain Gauges for Stress Analysis Temperature Humidity Transmitters Temperature Pressure Integration Transmitter UTB5 Thermal Resistor Temperature Transducer UTC1 (-50~+600 C) Thermal Resistor Temperature Transducer UTC2 (-40~+200 C) Wireless Digital Temperature Gauge UTI7 • Chip level micrometer scale tiny Microelectromechanical Systems (MEMS) based devices such as micropumps, micromirrors, micromotors, microfluidic devices. • Integrated Circuits (IC) • Switching elements, switch, relay, contactor, circuit breaker Contactors with UL and CE Certification NC1100111-1042532 Contactors with UL and CE Certification NC2100111-1044422 Contactors with UL and CE Certifications NC6100111-1040002 Definite Purpose Contactor with UL and CE Certifications NCK3100111-1052422 Electronic Overload Relay with UL and CE Certification NRE8100111-1143132 Miniature Circuit Breakers with UL and CE Certification NB1100111-1114242 Miniature Power Relay with UL and CE Certification JQX-10F100111-1153432 Miniature Power Relay with UL and CE Certifications JQX-13F100111-1154072 Miniature Power Relay with UL and CE Certification JTX100111-1155122 Miniature Power Relay with UL and CE Certification MK100111-1155402 Miniature Power Relay with UL and CE Certification NJX-13FW100111-1152352 Push button and rotary switches & control boxes Sub-Miniature Power Relay with UL and CE Certification JQC-3F100111-1153132 Thermal Overload Relay with UL and CE Certification NR2100111-1144062 • Electric fans and coolers for installation in electronic and industrial devices • Heating elements, thermoelectric coolers (TEC) Easy Click heat sinks Extruded heat sinks Heat sinks with Super Fins Standard heat sinks Super cooling plates Super Power heat sinks for medium - high power electronic systems Waterless cooling plates • We supply Electronic Enclosures for protection of your electronic components and assembly. Besides these off-shelf electronic enclosures, we do custom injection mold and thermoform electronic enclosures that fit your technical drawings. Please download from links below: Economic 17 Series Hand Held Enclosures Tibox Model Enclosures and Cabinets 01 Series Instrument Case System-I 02 Series Plastic and Aluminum Instrument Case Systems II 03 Series Plastic and Steel Enclosures 05 Series Instrument Case System-V 08 Series Plastic Cases 10 Series Sealed Plastic Enclosures 11 Series Die-cast Aluminium Boxes 14 Series PLC Enclosures 15 Series Modular Plastic Enclosures 16 Series DIN rail module enclosures 18 Series Special Plastic Enclosures 19 Series Desktop Enclosures 20 Series Wall-Mounting Enclosures 21 Series Card Reader Enclosures 24 Series DIN Plastic Enclosures 31 Series Potting and Power Supply Enclosures 37 Series Plastic Equipment Cases • Telecommunication and datacommunication products, lasers, receivers, transceivers, transponders, modulators, amplifiers. CATV products such as CAT3, CAT5, CAT5e, CAT6, CAT7 cables, CATV splitters. • Laser components and assembly • Acoustic components and assemblies, recording electronics - These catalogs contain only some brands we sell. We also have generic brand names and other brands with similar good quality for you to choose from. Dowload brochure for our DESIGN PARTNERSHIP PROGRAM - Contact us for your special electronic assembly requests. We integrate various components & products and manufacture complex assemblies. We can either design it for you or assemble according to your design. Reference Code: OICASANLY KLIK Product Finder-Locator Service PAGE sadurunge
- Solar Power Modules, Rigid, Flexible Panels, Thin Film, Monocrystaline
Solar Power Modules - Rigid - Flexible Panels - Thin Film - Monocrystalline - Polycrystalline - Solar Connector available from AGS-TECH Inc. Manufaktur lan Majelis Sistem Tenaga Surya Kustomisasi Kita nyedhiyakake: • Sel & panel tenaga surya, piranti tenaga solar lan rakitan khusus kanggo nggawe energi alternatif. Sel tenaga surya bisa dadi solusi sing paling apik kanggo peralatan sing mandhiri sing ana ing wilayah sing adoh kanthi nguwasani peralatan utawa piranti sampeyan. Ngilangi pangopènan dhuwur amarga panggantos baterei, ngilangi kebutuhan kanggo nginstal kabel listrik kanggo nyambungake peralatan menyang saluran listrik utama bisa menehi dorongan marketing gedhe kanggo produk sampeyan. Coba pikirake nalika sampeyan ngrancang peralatan sing mapan ing wilayah sing adoh. Kajaba iku, tenaga surya bisa ngirit dhuwit kanthi nyuda katergantungan ing energi listrik sing dituku. Elinga, sel energi surya bisa fleksibel utawa kaku. Riset janji isih ditindakake babagan sel surya semprotan. Energi sing diasilake dening piranti solar umume disimpen ing baterei utawa digunakake langsung sawise generasi. Kita bisa nyedhiyakake sel surya, panel, baterei solar, inverter, konektor energi surya, rakitan kabel, kabeh kit tenaga surya kanggo proyek sampeyan. Kita uga bisa nulungi sampeyan sajrone tahap desain piranti solar sampeyan. Kanthi milih komponen sing tepat, jinis sel surya sing tepat lan bisa uga nggunakake lensa optik, prisma ... etc. kita bisa nggedhekake jumlah daya kui dening sel solar. Ngoptimalake tenaga surya yen lumahing kasedhiya ing piranti diwatesi bisa dadi tantangan. Kita duwe keahlian sing tepat lan alat desain optik kanggo entuk iki. Unduh brosur kanggo PROGRAM KEMITRAAN DESIGN Priksa manawa kanggo ndownload katalog komponen listrik & elektronik lengkap kanggo produk sing ora ana ing rak kanthi KLIK KINI . Katalog iki duwe produk kayata konektor solar, baterei, konverter lan liya-liyane kanggo proyek sing ana gandhengane karo solar. Yen sampeyan ora bisa nemokake iku ana, hubungi kita lan kita bakal ngirim informasi apa kita wis kasedhiya. Yen sampeyan seneng banget karo produk lan sistem energi alternatif sing bisa dianyari domestik utawa sarana skala gedhe, kalebu sistem solar, mula sampeyan ngajak sampeyan ngunjungi situs energi http://www.ags-energy.com KLIK Product Finder-Locator Service PAGE sadurunge
- Electron Beam Machining, EBM, E-Beam Machining & Cutting & Boring
Electron Beam Machining, EBM, E-Beam Machining & Cutting & Boring, Custom Manufacturing of Parts - AGS-TECH Inc. - NM - USA EBM Machining & Electron Beam Machining In ELECTRON-BEAM MACHINING (EBM) we have high-velocity electrons concentrated into a narrow beam which are directed toward the work piece, creating heat and vaporizing the material. Thus EBM is a kind of HIGH-ENERGY-BEAM MACHINING technique. Electron-Beam Machining (EBM) can be used for very accurate cutting or boring of a variety of metals. Surface finish is better and kerf width is narrower in comparison to other thermal-cutting processes. The electron beams in EBM-Machining equipment are generated in an electron beam gun. The applications of Electron-Beam Machining are similar to those of Laser-Beam Machining, except that EBM requires a good vacuum. Thus these two processes are classified as electro-optical-thermal processes. The workpiece to be machined with EBM process is located under the electron beam and is kept under vacuum. The electron beam guns in our EBM machines are also provided with illumination systems and telescopes for alignment of the beam with the workpiece. Workpiece is mounted on a CNC table so that holes of any shape can be machined using the CNC control and beam deflection functionality of the gun. To achieve the fast evaporation of the material, the planar density of the power in the beam must be as high as possible. Values up to 10exp7 W/mm2 can be achieved at the spot of impact. The electrons transfer their kinetic energy into heat in a very small area, and the material impacted by the beam is evaporated in a very short time. The molten material at the top of the front, is expelled from the cutting zone by the high vapor pressure at the lower parts. EBM equipment is built similarly to electron beam welding machines. Electron-beam machines usually utilize voltages in the range of 50 to 200 kV to accelerate electrons to about 50 to 80% of the speed of light (200,000 km/s). Magnetic lenses whose function is based on Lorentz forces are used to focus the electron beam to the surface of the workpiece. With the help of a computer, the electromagnetic deflection system positions the beam as needed so holes of any shape can be drilled. In other words, the magnetic lenses in Electron-Beam-Machining equipment shape the beam and reduce the divergence. Apertures on the other hand allow only the convergent electrons to pass and capture the divergent low energy electrons from the fringes. The aperture and the magnetic lenses in EBM-Machines thus improve the quality of the electron beam. The gun in EBM is used in pulsed mode. Holes can be drilled in thin sheets using a single pulse. However for thicker plates, multiple pulses would be needed. Switching pulse durations of as low as 50 microseconds to as long as 15 miliseconds are generally used. To minimize electron collisions with air molecules resulting in scattering and keep contamination to a minimum, vacuum is used in EBM. Vacuum is difficult and expensive to produce. Especially obtaining good vacuum within large volumes and chambers is very demanding. Therefore EBM is best suited for small parts that fit into reasonably sized compact vacuum chambers. The level of vacuum within the EBM’s gun is in the order of 10EXP(-4) to 10EXP(-6) Torr. The interaction of the electron beam with the work piece produces X-rays which pose health hazard, and therefore well trained personnel should operate EBM equipment. Generally speaking, EBM-Machining is used for cutting holes as small as 0.001 inch (0.025 millimetre) in diameter and slots as narrow as 0.001 inch in materials up to 0.250 inch (6.25 millimetres) thick. Characteristic length is the diameter over which the beam is active. Electron beam in EBM may have a characteristic length of tens of microns to mm depending on degree of focusing of the beam. Generally, the high-energy focused electron beam is made to impinge on the workpiece with a spot size of 10 – 100 microns. EBM can provide holes of diameters in the range of 100 microns to 2 mm with a depth up to 15 mm, i.e., with a depth/diameter ratio of around 10. In case of defocused electron beams, power densities would drop as low as 1 Watt/mm2. However in case of focused beams the power densities could be increased to tens of kW/mm2. As a comparison, laser beams can be focused over a spot size of 10 – 100 microns with a power density as high as 1 MW/mm2. Electrical discharge typically provides the highest power densities with smaller spot sizes. Beam current is directly related to the number of electrons available in the beam. Beam current in Electron-Beam-Machining can be as low as 200 microamperes to 1 ampere. Increasing the EBM’s beam current and/or pulse duration directly increases the energy per pulse. We use high-energy pulses in excess of 100 J/pulse to machine larger holes on thicker plates. Under normal conditions, EBM-machining offers us the advantage of burr-free products. The process parameters directly affecting the machining characteristics in Electron-Beam-Machining are: • Acceleration voltage • Beam current • Pulse duration • Energy per pulse • Power per pulse • Lens current • Spot size • Power density Some fancy structures can also be obtained using Electron-Beam-Machining. Holes can be tapered along the depth or barrel shaped. By focusing the beam below the surface, reverse tapers can be obtained. A wide range of materials like steel, stainless steel, titanium and nickel super-alloys, aluminum, plastics, ceramics can be machined using e-beam-machining. There could be thermal damages associated with EBM. However, the heat-affected zone is narrow due to short pulse durations in EBM. The heat-affected zones are generally around 20 to 30 microns. Some materials such as aluminum and titanium alloys are more readily machined compared to steel. Furthermore EBM-machining does not involve cutting forces on the work pieces. This enables machining of fragile and brittle materials by EBM without any significant clamping or attaching as is the case in mechanical machining techniques. Holes can also be drilled at very shallow angles like 20 to 30 degrees. The advantages of Electron-Beam-Machining: EBM provides very high drilling rates when small holes with high aspect ratio are drilled. EBM can machine almost any material regardless of its mechanical properties. No mechanical cutting forces are involved, thus work clamping, holding and fixturing costs are ignorable, and fragile/brittle materials can be processed without problems. Heat affected zones in EBM are small because of shorte pulses. EBM is able of providing any shape of holes with accuracy by using electromagnetic coils to deflect electron beams and the CNC table. The disadvantages of Electron-Beam-Machining: Equipment is expensive and operating and maintaining vacuum systems requires specialized technicians. EBM requires significant vacuum pump down periods for attaining required low pressures. Even though heat affected zone is small in EBM, the recast layer formation occurs frequently. Our many years of experience and know-how helps us to take advantage of this valuable equipment in our manufacturing environment. KLIK Product Finder-Locator Service PAGE sadurunge
- Tanks and Containers, USA, AGS-TECH Inc.
AGS-TECH offers off-shelf and custom manufactured tanks and containers of various sizes. We supply wire mesh cage containers, stainless, aluminum and metal tanks and containers, IBC tanks, plastic and polymer containers, fiberglass tanks, collapsible tanks. Tank lan Wadhah We supply chemical, powder, liquid and gas storage containers and tanks made from inert polymers, stainless steel....etc. We have foldable, rolling containers, stackable containers, collapsible containers, containers with other useful functionalities finding applications in many industries such as construction, food, pharmaceuticals, chemical, petrochemical....etc. Tell us about your application and we will recommend you the most suitable container. Large volume stainless steel or other material containers are custom made to order and according to your specifications. Smaller containers are generally available off-the-shelf and also custom manufactured if your quantities justify. If quantities are significant, we can blow or rotation mould plastic containers & tanks according to your specifications. Here are the main types of our tanks and containers: Wire Mesh Cage Containers We have a variety of Wire Mesh Cage Containers in stock and can also custom manufacture them according to your specifications and needs. Our Wire Mesh Cage Containers include products such as: Stackable Cage Pallets Foldable Wire Mesh Roll Containers Foldable Wire Mesh Containers All our wire mesh cage containers are made of highest quality stainless or mild steel materials and the non-stainless versions are coated against corrosion and decay generally using zinc, hot dip or powder coating. Color of finish is generally zinc: white or yellow; or powder coated according to your request. Our wire mesh cage containers are assembled under strict quality control procedures and tested for mechanical impact, weight carrying capacity, durability, strength and long term reliability. Our wire mesh cage containers conform to international quality standards as well as US and international transportation industry standards. Wire mesh cage containers are generally used as storage boxes & bins, storage carts, transportation carts..etc. When choosing a wire mesh cage container, please consider important parameters such as loading capacity, weight of the container itself, dimensions of the grid, exterior and interior dimensions, whether you need a container that folds flat for space-saving shipping and storage, and please also consider how many of a particular container can be loaded in a 20 foot or 40 foot shipping container. The bottom line is wire mesh cage containers are long lasting, economical and environmentally friendly alternative to disposable packaging. Below are downloadable brochures of our wire mesh container products. - Wire Mesh Container Quote Design Form (please click to download, fill out and email us) Stainless and Metal Tanks & Containers Our stainless and other metal tanks and containers are ideal for storing creams and fluids. They are ideal for the cosmetics, pharmaceutical and food & beverage industries and others. They comply with European, American and international guidelines. Our stainless and metal tanks are easy to clean. These containers have steady basis and can be sanitized with no retention area. We can fit our stainless and metal tanks and containers with all types of accessories, such as integration of a washing head. Our containers are pressurizable. They are easily adaptable to your plant and workplace. Working pressures of our containers vary, so make sure to compare the specifications to your needs. Our aluminum containers and tanks are also very popular in the industry. Some models are mobile with wheels, others are stackable. We have powder, granules and pellets storage tanks that are UN approved for transportation of hazardous products. We are capable to custom design and fabricate stainless and metal tanks according to your needs and specifications. Inner and outer dimensions, wall thicknesses of our stainless and metal tanks & containers can be varied according to your requirements. Stainless and Aluminum Tanks & Containers Stackable Tanks and Containers Wheeled Tanks and Containers IBC & GRV Tanks Powder, Granules and Pellets Storage Tanks Custom Designed and Fabricated Tanks and Containers Please click links below to download our brochures for Stainless and Metal Tanks & Containers: IBC Tanks and Containers Plastic and Polymer Tanks & Containers AGS-TECH supplies tanks & containers from a vast variety of plastic and polymer materials. We encourage you to contact us with your request and specify the following so we can quote you the most appropriate product. - Application - Material grade - Dimensions - Finish - Packaging requirements - Quantity For example FDA approved food grade plastic materials are important for some containers storing beverages, grains, fruit juice....etc. On the other hand, if you need plastic and polymer tanks and containers to store chemicals or pharmaceuticals, the inertness of the plastic material against the content is of utmost importance. Contact us for our opinion on materials. You can also order off-shelf plastic and polymer tanks & containers from our brochures below. Please click on the links below to download our brochures for plastic and polymer tanks and containers: IBC Tanks and Containers Fiberglass Tanks & Containers We offer tanks & containers made of fiberglass materials. Our fiberglass tanks and containers meet US & internationally accepted standards for storage tank construction. Fiberglass tanks & containers are fabricated with contact molded laminates conforming to ASTM 4097 and filament wound laminates conforming to ASTM 3299. Special resins used in fiberglass tanks fabrication are chosen based upon customer information regarding concentration, temperature, and corrosive behavior of the product being stored. FDA approved as well as fire retardant resins are available for special applications. We encourage you to contact us with your request and specify the following so we can quote you the most appropriate fiberglass tank and container. - Application - Material expectations & specifications - Dimensions - Finish - Packaging requirements - Quantity needed We will happily give you our opinion. You can also order off-shelf fiberglass tanks & containers from our brochures below. If none of the fiberglass tanks and containers in our off-shelf portfolio satisfies you, please let us know and we can consider custom manufacturing according to your needs. Collapsible Tanks & Containers Collapsible water tanks and containers are your best choice to store liquid in applications where plastic barrels and other containers are too small or impractical. Also when you need large amounts of water or liquid quickly without constructing a concrete or metal tank, our collapsible tanks and containers are ideal. As the name implies, collapsible tanks and containers, are collapsible, meaning that you can shrink them after use, roll and make them very compact and small in volume, easy to store and transport when empty. They are reusable. We can supply you any size and model and according to your specifications. General Features of our Collapsible Tanks and Containers: - Color: Blue, orange, grey, dark green, black,.....etc. - Material: PVC - Capacity: Generally between 200 to 30000 liters - Light weight, easy operation. - Minimum packing size, easy for transportation and storage. - No contamination of water - High strength of coated fabric, adhesion up to 60 lb/in. - High strength of the seams is assured with the high frequency melt and sealed with the same polyurethane as the tank body, so the tanks have excellent ability preventing air leakage and its very safe for water. Applications for Collapsible Tanks and Containers: · Temporary Storage · Rainwater Collection · Residential and Public Storage of Water · Defense Water Storage Applications · Water Treatment · Emergency Storage and Relief · Irrigation · Construction companies choose PVC water tanks to test bridge maximum load · Fire fighting We also accept OEM orders. Custom labeling, packaging and logo printing is available. PAGE sadurunge
- Coating Thickness Gauge, Surface Roughness Tester, Nondestructive Test
Coating Thickness Gauge - Surface Roughness Tester - Nondestructive Testing - SADT - Mitech - AGS-TECH Inc. - NM - USA Instrumen Uji Lapisan Lumahing Among our test instruments for coating and surface evaluation are COATING THICKNESS METERS, SURFACE ROUGHNESS TESTERS, GLOSS METERS, COLOR READERS, COLOR DIFFERENCE METER, METALLURGICAL MICROSCOPES, INVERTED METALLOGRAPHIC MICROSCOPE. Our main focus is on NON-DESTRUCTIVE TEST METHODS. We carry high quality brands such as ELCOMETER, SADT-SINOAGE and MITECH. A large percentage of all surfaces around us are coated. Coatings serve many purposes including good appearance, protection and giving products certain desired functionality such as water repelling, enhanced friction, wear and abrasion resistance….etc. Therefore it is of vital importance to be capable to measure, test and evaluate the properties and quality of coatings and surfaces of products. Coatings can be broadly categorized into two main groups if thicknesses are taken into consideration: THICK FILM and THIN FILM COATINGS. Please click on highlighted text below to download respective catalogs. You can procure brand new, or refurbished and used surface coating test instruments from us. Simply indicate the brand name, model number and we will provide you the most competitive quote. AMETEK-LLOYD Instruments Materials Testing (does include also Peeling, Adhesion Test Instruments...etc.) ELCOMETER Inspection Equipment (many coating inspection instruments available) HAIDA Color Assessment Cabinet MI TECH Coating Thickness Gauge Model MCT200 catalog. SADT-SINOAGE Brand Metrology and Test Equipment catalog download. In this catalog you will find some of these instruments for the evaluation of surfaces and coatings. Some of the instruments and techniques used for such purposes are: COATING THICKNESS METER : Different types of coatings require different types of coating testers. A basic understanding of the various techniques is thus essential for the user to choose the right equipment. In the Magnetic Induction Method of coating thickness measurement we measure nonmagnetic coatings over ferrous substrates and magnetic coatings over nonmagnetic substrates. The probe is positioned on the sample and the linear distance between the probe tip that contacts the surface and the base substrate is measured. Inside the measurement probe is a coil that generates a changing magnetic field. When the probe is placed on the sample, the magnetic flux density of this field is altered by the thickness of a magnetic coating or the presence of a magnetic substrate. The change in magnetic inductance is measured by a secondary coil on the probe. The output of the secondary coil is transferred to a microprocessor, where it’s shown as a coating thickness measurement on the digital display. This quick test is suitable for liquid or powder coatings, platings such as chrome, zinc, cadmium or phosphate over steel or iron substrates. Coatings such as paint or powder thicker than 0.1 mm are suitable for this method. The magnetic induction method is not well suited for nickel over steel coatings because of nickel’s partial magnetic property. Phase-sensitive Eddy current method is more suitable for these coatings. Another type of coating where the magnetic induction method is prone to failure is zinc galvanized steel. The probe will read a thickness equal to the total thickness. Newer model instruments are capable of self-calibration by detecting the substrate material through the coating. This is of course very helpful when a bare substrate is not available or when the substrate material is unknown. Cheaper equipment versions require however calibration of the instrument on a bare and uncoated substrate. The Eddy Current Method of coating thickness measurement measures nonconductive coatings on nonferrous conductive substrates, nonferrous conductive coatings on nonconductive substrates and some nonferrous metal coatings on nonferrous metals. It is similar to the magnetic inductive method previously mentioned containing a coil and similar probes. The coil in the Eddy current method has the dual function of excitation and measurement. This probe coil is driven by a high-frequency oscillator to generate an alternating high-frequency field. When placed near a metallic conductor, eddy currents are generated in the conductor. Impedance change takes place in the probe coil. The distance between the probe coil and the conductive substrate material determines the amount of impedance change, which can be measured, correlated to a coating thickness and displayed in the form of a digital reading. Applications include liquid or powder coating on aluminum and nonmagnetic stainless steel, and anodize over aluminum. This method’s reliability depends on the part’s geometry and the coating’s thickness. The substrate needs to be known prior to taking readings. Eddy current probes shouldn’t be used for measuring nonmagnetic coatings over magnetic substrates such as steel and nickel over aluminum substrates. If users must measure coatings over magnetic or nonferrous conductive substrates they will be best served with a dual magnetic induction/Eddy current gage that automatically recognizes the substrate. A third method, called the Coulometric method of coating thickness measurement, is a destructive testing method that has many important functions. Measuring the duplex nickel coatings in the automotive industry is one of it major applications. In the coulometric method, the weight of an area of known size on a metallic coating is determined through localized anodic stripping of the coating. The mass-per-unit area of the coating thickness is then calculated. This measurement on the coating is made using an electrolysis cell, which is filled with an electrolyte specifically selected to strip the particular coating. A constant current runs through the test cell, and since the coating material serves as the anode, it gets deplated. The current density and the surface area are constant, and thus the coating thickness is proportional to the time it takes to strip and take off the coating. This method is very useful for measuring electrically conductive coatings on a conductive substrate. The Coulometric method can also be used for determining the coating thickness of multiple layers on a sample. For example, the thickness of nickel and copper can be measured on a part with a top coating of nickel and an intermediate copper coating on a steel substrate. Another example of a multilayer coating is chrome over nickel over copper on top of a plastic substrate. Coulometric test method is popular in electroplating plants with a small number of random samples. Yet a fourth method is the Beta Backscatter Method for measuring coating thicknesses. A beta-emitting isotope irradiates a test sample with beta particles. A beam of beta particles is directed through an aperture onto the coated component, and a proportion of these particles are backscattered as expected from the coating through the aperture to penetrate the thin window of a Geiger Muller tube. The gas in the Geiger Muller tube ionizes, causing a momentary discharge across the tube electrodes. The discharge which is in the form of a pulse is counted and translated to a coating thickness. Materials with high atomic numbers backscatter the beta particles more. For a sample with copper as a substrate and a gold coating of 40 microns thick, the beta particles are scattered by both the substrate and the coating material. If the gold coating thickness increases, the backscatter rate also increases. The change in the rate of particles scattered is therefore a measure of the coating thickness. Applications that are suitable for the beta backscatter method are those where the atomic number of the coating and substrate differ by 20 percent. These include gold, silver or tin on electronic components, coatings on machine tools, decorative platings on plumbing fixtures, vapor-deposited coatings on electronic components, ceramics and glass, organic coatings such as oil or lubricant over metals. The beta backscatter method is useful for thicker coatings and for substrate & coating combinations where magnetic induction or Eddy current methods won’t work. Changes in alloys affect the beta backscatter method, and different isotopes and multiple calibrations might be required to compensate. An example would be tin/lead over copper, or tin over phosphorous/bronze well known in printed circuit boards and contact pins, and in these cases the changes in alloys would be better measured with the more expensive X-ray fluorescence method. The X-ray fluorescence method for measuring coating thickness is a noncontact method that allows the measurement of very thin multilayer alloy coatings on small and complex parts. Parts are exposed to X-radiation. A collimator focuses the X-rays onto an exactly defined area of the test specimen. This X-radiation causes characteristic X-ray emission (i.e., fluorescence) from both the coating and the substrate materials of the test specimen. This characteristic X-ray emission is detected with an energy dispersive detector. Using the appropriate electronics, it’s possible to register only the X-ray emission from the coating material or substrate. It’s also possible to selectively detect a specific coating when intermediate layers are present. This technique is widely used on printed circuit boards, jewelry and optical components. The X-ray fluorescence is not suitable for organic coatings. The measured coating’s thickness should not exceed 0.5-0.8 mils. However, unlike the beta backscatter method, X-ray fluorescence can measure coatings with similar atomic numbers (for example nickel over copper). As previously mentioned, different alloys affect an instrument’s calibration. Analyzing base material and coating’s thickness are critical for ensuring precision readings. Todays systems and software programs reduce the need for multiple calibrations without sacrificing quality. Finally it is worth mentioning that there are gages that can operate in several of the above mentioned modes. Some have detachable probes for flexibility in use. Many of these modern instruments do offer statistical analysis capabilities for process control and minimal calibration requirements even if used on differently shaped surfaces or different materials. SURFACE ROUGHNESS TESTERS : Surface roughness is quantified by the deviations in the direction of the normal vector of a surface from its ideal form. If these deviations are large, the surface is considered rough; if they are small, the surface is considered smooth. Commercially available instruments called SURFACE PROFILOMETERS are used to measure and record surface roughness. One of the commonly used instruments features a diamond stylus traveling along a straight line over the surface. The recording instruments are able to compensate for any surface waviness and indicate only roughness. Surface roughness can be observed through a.) Interferometry and b.) Optical microscopy, scanning-electron microscopy, laser or atomic-force microscopy (AFM). Microscopy techniques are especially useful for imaging very smooth surfaces for which features cannot be captured by less sensitive instruments. Stereoscopic photographs are useful for 3D views of surfaces and can be used to measure surface roughness. 3D surface measurements can be performed by three methods. Light from an optical-interference microscope shines against a reflective surface and records the interference fringes resulting from the incident and reflected waves. Laser profilometers are used to measure surfaces through either interferometric techniques or by moving an objective lens to maintain a constant focal length over a surface. The motion of the lens is then a measure of the surface. Lastly, the third method, namely the atomic-force microscope, is used for measuring extremely smooth surfaces on the atomic scale. In other words with this equipment even atoms on the surface can be distinguished. This sophisticated and relatively expensive equipment scans areas of less than 100 micron square on specimen surfaces. GLOSS METERS, COLOR READERS, COLOR DIFFERENCE METER : A GLOSSMETERmeasures the specular reflection gloss of a surface. A measure of gloss is obtained by projecting a light beam with fixed intensity and angle onto a surface and measuring the reflected amount at an equal but opposite angle. Glossmeters are used on a variety of materials such as paint, ceramics, paper, metal and plastic product surfaces. Measuring gloss can serve companies in assuring quality of their products. Good manufacturing practices require consistency in processes and this includes consistent surface finish and appearance. Gloss measurements are carried out at a number of different geometries. This depends on the surface material. For example metals have high levels of reflection and therefore the angular dependence is less as compared to non-metals such as coatings and plastics where angular dependence is higher due to diffuse scattering and absorption. Illumination source and observation reception angles configuration allows measurement over a small range of the overall reflection angle. The measurement results of a glossmeter are related to the amount of reflected light from a black glass standard with a defined refractive index. The ratio of the reflected light to the incident light for the test specimen, compared to the ratio for the gloss standard, is recorded as gloss units (GU). Measurement angle refers to the angle between the incident and reflected light. Three measurement angles (20°, 60°, and 85°) are used for the majority of industrial coatings. The angle is selected based on the anticipated gloss range and the following actions are taken depending on the measurement: Gloss Range..........60° Value.......Action High Gloss............>70 GU..........If measurement exceeds 70 GU, change test setup to 20° to optimize measurement accuracy. Medium Gloss........10 - 70 GU Low Gloss.............<10 GU..........If measurement is less than 10 GU, change test setup to 85° to optimize measurement accuracy. Three types of instruments are available commercially: 60° single angle instruments, a double-angle type that combines 20° and 60° and a triple-angle type that combines 20°, 60° and 85°. Two additional angles are used for other materials, the angle of 45° is specified for the measurement of ceramics, films, textiles and anodized aluminum, while the measurement angle 75° is specified for paper and printed materials. A COLOR READER or also referred to as COLORIMETER is a device that measures the absorbance of particular wavelengths of light by a specific solution. Colorimeters are most commonly used to determine the concentration of a known solute in a given solution by the application of the Beer-Lambert law, which states that the concentration of a solute is proportional to the absorbance. Our portable color readers can also be used on plastic, painting, platings, textiles, printing, dye making, food such as butter, french fries, coffee, baked products and tomatoes….etc. They can be used by amateurs who don’t have professional knowledge on colors. Since there are many types of color readers, the applications are endless. In quality control they are used mainly to insure samples fall within color tolerances set by the user. To give you an example, there are handheld tomato colorimeters which use an USDA approved index to measure and grade the color of processed tomato products. Yet another example are handheld coffee colorimeters specifically designed to measure the color of whole green beans, roasted beans, and roasted coffee using industry standard measurements. Our COLOR DIFFERENCE METERS display directly color difference by E*ab, L*a*b, CIE_L*a*b, CIE_L*c*h. Standard deviation is within E*ab0.2 They work on any color and testing takes only seconds of time. METALLURGICAL MICROSCOPES and INVERTED METALLOGRAPHIC MICROSCOPE : Metallurgical microscope is usually an optical microscope, but differs from others in the method of the specimen illumination. Metals are opaque substances and therefore they must be illuminated by frontal lighting. Therefore the source of light is located within the microscope tube. Installed in the tube is a plain glass reflector. Typical magnifications of metallurgical microscopes are in the x50 – x1000 range. Bright field illumination is used for producing images with bright background and dark non-flat structure features such as pores, edges and etched grain boundaries. Dark field illumination is used for producing images with dark background and bright non-flat structure features such as pores, edges, and etched grain boundaries. Polarized light is used for viewing metals with non-cubic crystalline structure such as magnesium, alpha-titanium and zinc, responding to cross-polarized light. Polarized light is produced by a polarizer which is located before the illuminator and analyzer and placed before the eyepiece. A Nomarsky prism is used for differential interference contrast system which makes it possible to observe features not visible in bright field. INVERTED METALLOGRAPHIC MICROSCOPES have their light source and condenser on the top, above the stage pointing down, while the objectives and turret are below the stage pointing up. Inverted microscopes are useful for observing features at the bottom of a large container under more natural conditions than on a glass slide, as is the case with a conventional microscope. Inverted microscopes are used in metallurgical applications where polished samples can be placed on top of the stage and viewed from underneath using reflecting objectives and also in micromanipulation applications where space above the specimen is required for manipulator mechanisms and the microtools they hold. Here is a brief summary of some of our test instruments for the evaluation of surfaces and coatings. You can download details of these from the product catalog links provided above. Surface Roughness Tester SADT RoughScan : This is a portable, battery-powered instrument for checking surface roughness with the measured values displayed on a digital readout. The instrument is easy to use and can be used in the lab, manufacturing environments, in shops, and wherever surface roughness testing is required. SADT GT SERIES Gloss Meters : GT series gloss meters are designed and manufactured according to international standards ISO2813, ASTMD523 and DIN67530. The technical parameters conform to JJG696-2002. The GT45 gloss meter is especially designed for measuring plastic films and ceramics, small areas and curved surfaces. SADT GMS/GM60 SERIES Gloss Meters : These glossmeters are designed and manufactured according to international standards ISO2813, ISO7668, ASTM D523, ASTM D2457. The technical parameters also conform to JJG696-2002. Our GM Series gloss meters are well suited to measure painting, coating, plastic, ceramics, leather products, paper, printed materials, floor coverings…etc. It has an appealing and user friendly design, three - angle gloss data is displayed simultaneously, large memory for measurement data, latest bluetooth function and removable memory card to transmit data conveniently, special gloss software to analyze data output, low battery and memory-full indicator. Through Internal bluetooth module and USB interface, GM gloss meters can transfer data to PC or exported to printer via printing interface. Using optional SD cards memory can be extended as much as needed. Precise Color Reader SADT SC 80 : This color reader is mostly used on plastics, paintings,, platings, textiles & costumes, printed products and in the dye manufacturing industries. It is capable to perform color analysis. The 2.4” color screen and portable design offers comfortable use. Three kinds of light sources for user selection, SCI and SCE mode switch and metamerism analysis satisfy your test needs under different work conditions. Tolerance setting, auto -judge color difference values and color deviation functions make you determine the color easily even if you don’t have any professional knowledge on colors. Using professional color analysis software users can perform the color data analysis and observe color differences on the output diagrams. Optional mini printer enables users to print out the color data on site. Portable Color Difference Meter SADT SC 20 : This portable color difference meter is widely used in quality control of plastic and printing products. It is used to capture color efficiently and accurately. Easy to operate, displays color difference by E*ab, L*a*b, CIE_L*a*b, CIE_L*c*h., standard deviation within E*ab0.2, it can be connected to computer through the USB expansion interface for inspection by software. Metallurgical Microscope SADT SM500 : It is a self-contained portable metallurgical microscope ideally suited for metallographic evaluation of metals in laboratory or in situ. Portable design and unique magnetic stand, the SM500 can be attached directly against the surface of ferrous metals at any angle, flatness, curvature and surface complexity for non-destructive examination. The SADT SM500 can also be used with digital camera or CCD image processing system to download metallurgical images to PC for data transfer, analysis, storage and printout. It is basically a portable metallurgical laboratory, with on-site sample preparation, microscope, camera and no need for AC power supply in the field. Natural colors without the need for changing light by dimming the LED lighting provides the best image observed at any time. This instrument has optional accessories including additional stand for small samples, digital camera adapter with eyepiece, CCD with interface, eyepiece 5x/10x/15x/16x, objective 4x/5x/20x/25x/40x/100x, mini grinder, electrolytic polisher, a set of wheel heads, polishing cloth wheel, replica film, filter (green, blue, yellow), bulb. Portable Metallurgraphic Microscope SADT Model SM-3 : This instrument offers a special magnetic base, fixing the unit firmly on the work pieces, it is suitable for large-scale roll test and direct observation, no cutting and sampling needed, LED lighting, uniform color temperature, no heating, forward / backward and left / right moving mechanism, convenient for adjustment of the inspection point, adapter for connecting digital cameras and observing the recordings directly on PC. Optional accessories are similar to the SADT SM500 model. For details, please download product catalog from the link above. Metallurgical Microscope SADT Model XJP-6A : This metalloscope can be easily used in factories, schools, scientific research institutions for identifying and analyzing the microstructure of all kinds of metals and alloys. It is the ideal tool for testing metal materials, verifying the quality of castings and analyzing metallographic structure of the metalized materials. Inverted Metallographic Microscope SADT Model SM400 : The design makes possible inspecting grains of metallurgical samples. Easy installation at the production line and easy to carry. The SM400 is suitable for colleges and factories. An adapter for attaching digital camera to the trinocular tube is also available. This mode needs MI of the metallographic image printing with fixed sizes. We have a selection of CCD adapters for computer print-out with standard magnification and over 60% observation view. Inverted Metallographic Microscope SADT Model SD300M : Infinite focusing optics provides high resolution images. Long distance viewing objective, 20 mm wide field of view, three -plate mechanical stage accepting almost any sample size, heavy loads and allowing nondestructive microscope examination of large components. The three-plate structure provides the microscope stability and durability. The optics provides high NA and long viewing distance, delivering bright, high-resolution images. The new optical coating of SD300M is dust and damp proof. For details and other similar equipment, please visit our equipment website: http://www.sourceindustrialsupply.com KLIK Product Finder-Locator Service PAGE sadurunge
- Brazing, Soldering, Welding, Joining Processes, Assembly Services
Brazing - Soldering - Welding - Joining Processes - Assembly Services - Subassemblies - Assemblies - Custom Manufacturing - AGS-TECH Inc. - NM - USA Brazing & Soldering & Welding Among the many JOINING techniques we deploy in manufacturing, special emphasis is given to WELDING, BRAZING, SOLDERING, ADHESIVE BONDING and CUSTOM MECHANICAL ASSEMBLY because these techniques are widely used in applications like manufacturing of hermetic assemblies, high-tech product manufacturing and specialized sealing. Here we will concentrate on the more specialized aspects of these joining techniques as they are related to manufacturing of advanced products and assemblies. FUSION WELDING: We use heat to melt and coalesce materials. Heat is supplied by electricity or high-energy beams. The types of fusion welding we deploy are OXYFUEL GAS WELDING, ARC WELDING, HIGH-ENERGY-BEAM WELDING. SOLID-STATE WELDING: We join parts without melting and fusion. Our solid-state welding methods are COLD, ULTRASONIC, RESISTANCE, FRICTION, EXPLOSION WELDING and DIFFUSION BONDING. BRAZING & SOLDERING: They use filler metals and give us the advantage of working at lower temperatures than in welding, thus less structural damage to products. Information on our brazing facility producing ceramic to metal fittings, hermetic sealing, vacuum feedthroughs, high and ultrahigh vacuum and fluid control components can be found here: Brazing Factory Brochure Brazing Machines (We private label these with your brand name and logo if you wish. This way you can promote your brand name when you resell these machines to your customers) ADHESIVE BONDING: Because of the diversity of adhesives used in industry and also diversity of applications, we have a dedicated page for this. To go to our page about adhesive bonding, please click here. CUSTOM MECHANICAL ASSEMBLY: We use a variety of fasteners such as bolts, screws, nuts, rivets. Our fasteners are not limited to standard off-shelf fasteners. We design, develop and manufacture specialty fasteners that are made from nonstandard materials so they can meet requirements for special applications. Sometimes electrical or heat non-conductivity is desired whereas sometimes conductivity. For some special applications, a customer may want special fasteners that cannot be removed without destroying the product. There are endless ideas and applications. We have it all for you, if not off-shelf we can quickly develop it. To go to our page on mechanical assembly, please click here . Let us examine our various joining techniques in more details. OXYFUEL GAS WELDING (OFW): We use a fuel gas mixed with oxygen to produce the welding flame. When we use acetylene as the fuel and oxygen, we call it oxyacetylene gas welding. Two chemical reactions occur in the oxyfuel gas combustion process: C2H2 + O2 ------» 2CO + H2 + Heat 2CO + H2 + 1.5 O2--------» 2 CO2 + H2O + Heat The first reaction dissociates the acetylene into carbon monoxide and hydrogen while producing about 33% of the total heat generated. The second process above represents further combustion of the hydrogen and carbon monoxide while producing about 67% of the total heat. Temperatures in the flame are between 1533 to 3573 Kelvin. The oxygen percentage in the gas mixture is important. If the oxygen content is more than half, the flame becomes an oxidizing agent. This is undesirable for some metals but desirable for others. An example when oxidizing flame is desirable is copper-based alloys because it forms a passivation layer over the metal. On the other hand, when the oxygen content is reduced, full combustion is not possible and the flame becomes a reducing (carburizing) flame. The temperatures in a reducing flame are lower and therefore it is suitable for processes like soldering and brazing. Other gases are also potential fuels, but they have some disadvantages over acetylene. Occasionally we supply filler metals to the weld zone in the form of filler rods or wire. Some of them are coated with flux to retard oxidation of surfaces and thus protecting the molten metal. An additional benefit the flux gives us is the removal of oxides and other substances from the weld zone. This leads to stronger bonding. A variation of the oxyfuel gas welding is the PRESSURE GAS WELDING, where the two components are heated at their interface using oxyacetylene gas torch and once the interface starts to melt, the torch is withdrawn and an axial force is applied to press the two parts together until the interface is solidified. ARC WELDING: We use electrical energy to produce an arc between the electrode tip and parts to be welded. The power supply can be AC or DC while the electrodes are either consumable or nonconsumable. Heat transfer in arc welding can be expressed by the following equation: H / l = e x V I / v Here H is the heat input, l is the weld length, V and I are the voltage and current applied, v is the welding speed and e is the process efficiency. The higher the efficiency “e” the more beneficially the available energy is used to melt the material. The heat input can also be expressed as : H = u x (Volume) = u x A x l Here u is the specific energy for melting, A the cross section of the weld and l the weld length. From the two equations above we can obtain: v = e x V I / u A A variation of arc welding is the SHIELDED METAL ARC WELDING (SMAW) which constitutes about 50% of all industrial and maintenance welding processes. ELECTRIC ARC WELDING (STICK WELDING) is performed by touching the tip of a coated electrode to the workpiece and quickly withdrawing it to a distance sufficient to maintain the arc. We call this process also stick-welding because the electrodes are thin and long sticks. During the welding process, the tip of the electrode melts along with its coating and the base metal in the vicinity of the arc. A mixture of the base metal, electrode metal and substances from the electrode coating solidify in the weld area. The coating of the electrode deoxidizes and provides a shielding gas in the weld region, thus protecting it from the oxygen in the environment. Therefore the process is referred to as shielded metal arc welding. We use currents between 50 and 300 Amperes and power levels generally less than 10 kW for optimum weld performance. Also of importance is the polarity of the DC current (direction of current flow). Straight polarity where the workpiece is positive and the electrode is negative is preferred in welding of sheet metals because of its shallow penetration and also for joints with very wide gaps. When we have reverse polarity, i.e. the electrode is positive and workpiece negative we can achieve deeper weld penetrations. With AC current, since we have pulsating arcs, we can weld thick sections using large diameter electrodes and maximum currents. The SMAW welding method is suitable for workpiece thicknesses of 3 to 19 mm and even more using multiple-pass techniques. The slag formed on top of the weld needs to be removed using a wire brush, so that there is no corrosion and failure at the weld area. This of course adds to the cost of shielded metal arc welding. Nevertheless the SMAW is the most popular welding technique in industry and repair work. SUBMERGED ARC WELDING (SAW): In this process we shield the weld arc using granular flux materials like lime, silica, calcium floride, manganese oxide….etc. The granular flux is fed into the weld zone by gravity flow through a nozzle. The flux covering the molten weld zone significantly protects from sparks, fumes, UV radiation….etc and acts as a thermal insulator, thus letting heat penetrate deep into workpiece. The unfused flux is recovered, treated and reused. A coil of bare is used as electrode and fed through a tube to the area of weld. We use currents between 300 and 2000 Amperes. The submerged arc welding (SAW) process is limited to horizontal and flat positions and circular welds if rotation of the circular structure (such as pipes) is possible during welding. Speeds can reach 5 m/min. The SAW process is suitable for thick plates and results in high-quality, tough, ductile and uniform welds. The productivity, that is the amount of weld material deposited per hour is 4 to 10 times the amount as compared to the SMAW process. Another arc welding process, namely the GAS METAL ARC WELDING (GMAW) or alternatively referred to as METAL INERT GAS WELDING (MIG) is based on the weld area being shielded by external sources of gases like helium, argon, carbon dioxide….etc. There may be additional deoxidizers present in the electrode metal. Consumable wire is fed through a nozzle into the weld zone. Fabrication involving bot ferrous as well as nonferrous metals is carried out using gas metal arc welding (GMAW). Welding productivity is about 2 times that of the SMAW process. Automated welding equipment is being used. Metal is transferred in one of three ways in this process: “Spray Transfer” involves transfer of several hundred small metal droplets per second from electrode to the weld area. In “Globular Transfer” on the other hand, carbon dioxide rich gases are used and globules of molten metal are propelled by the electric arc. Welding currents are high and weld penetration deeper, welding speed greater than in spray transfer. Thus the globular transfer is better for welding heavier sections. Finally, in the “Short Circuiting” method, the electrode tip touches the molten weld pool, short circuiting it as metal at rates over 50 droplets/second is transferred in individual droplets. Low currents and voltages are used along with thinner wire. Powers used are about 2 kW and temperatures relatively low, making this method suitable for thin sheets less than 6mm thickness. Another variation the FLUX-CORED ARC WELDING (FCAW) process is similar to gas metal arc welding, except that the electrode is a tube filled with flux. The advantages of using cored-flux electrodes is that they produce more stable arcs, give us the opportunity to improve properties of weld metals, less brittle and flexible nature of its flux as compared to SMAW welding, improved welding contours. Self-shielded cored electrodes contain materials that shield the weld zone against the atmosphere. We use about 20 kW power. Like the GMAW process, the FCAW process also offers the opportunity to automate processes for continuous welding, and it is economical. Different weld metal chemistries can be developed by adding various alloys to the flux core. In ELECTROGAS WELDING (EGW) we weld the pieces placed edge to edge. It is sometimes also called BUTT WELDING. Weld metal is put into a weld cavity between two pieces to be joined. The space is enclosed by two water-cooled dams to keep the molten slag from pouring out. The dams are moved up by mechanical drives. When workpiece can be rotated, we can use the electrogas welding technique for circumferential welding of pipes too. Electrodes are fed through a conduit to keep a continuous arc. Currents can be around 400Amperes or 750 Amperes and power levels around 20 kW. Inert gases originating from either a flux-cored electrode or external source provide shielding. We use the electrogas welding (EGW) for metals such as steels, titanium….etc with thicknesses from 12mm to 75mm. The technique is a good fit for large structures. Yet, in another technique called ELECTROSLAG WELDING (ESW) the arc is ignited between the electrode and the bottom of the workpiece and flux is added. When molten slag reaches the electrode tip, the arc is extinguished. Energy is continuously supplied through the electrical resistance of the molten slag. We can weld plates with thicknesses between 50 mm and 900 mm and even higher. Currents are around 600 Ampere while voltages are between 40 – 50 V. The welding speeds are around 12 to 36 mm/min. Applications are similar to electrogas welding. One of our nonconsumable electrode processes, the GAS TUNGSTEN ARC WELDING (GTAW) also known as TUNGSTEN INERT GAS WELDING (TIG) involves the supply of a filler metal by a wire. For closely-fit joints sometimes we do not use the filler metal. In the TIG process we do not use flux, but use argon and helium for shielding. Tungsten has a high melting point and is not consumed in the TIG welding process, therefore constant current as well as arc gaps can be maintained. Power levels are between 8 to 20 kW and currents at either 200 Ampere (DC) or 500 Ampere (AC). For aluminum and magnesium we use AC current for its oxide cleaning function. To avoid contamination of the tungsten electrode, we avoid its contact with molten metals. Gas Tungsten Arc Welding (GTAW) is especially useful for welding thin metals. GTAW welds are of very high quality with good surface finish. Due to the higher cost of hydrogen gas, a less frequently used technique is ATOMIC HYDROGEN WELDING (AHW), where we generate an arc between two tungsten electrodes in a shielding atmosphere of flowing hydrogen gas. The AHW is also a nonconsumable electrode welding process. The diatomic hydrogen gas H2 breaks down into its atomic form near the welding arc where temperatures are over 6273 Kelvin. While breaking down, it absorbs large amount of heat from the arc. When the hydrogen atoms strike the weld zone which is a relatively cold surface, they recombine into diatomic form and release the stored heat. Energy can be varied by changing the workpiece to arc distance. In another nonconsumable electrode process, PLASMA ARC WELDING (PAW) we have a concentrated plasma arc directed toward the weld zone. The temperatures reach 33,273 Kelvin in PAW. A nearly equal number of electrons and ions make up the plasma gas. A low-current pilot arc initiates the plasma which is between the tungsten electrode and orifice. Operating currents are generally around 100 Amperes. A filler metal may be fed. In plasma arc welding, shielding is accomplished by an outer shielding ring and using gases such as argon and helium. In plasma arc welding, the arc may be between the electrode and workpiece or between the electrode and nozzle. This welding technique has the advantages over other methods of higher energy concentration, deeper and narrower welding capability, better arc stability, higher welding speeds up to 1 meter/min, less thermal distortion. We generally use plasma arc welding for thicknesses less than 6 mm and sometimes up to 20 mm for aluminum and titanium. HIGH-ENERGY-BEAM WELDING: Another type of fusion welding method with electron-beam welding (EBW) and laser welding (LBW) as two variants. These techniques are of particular value for our high-tech products manufacturing work. In electron-beam welding, high speed electrons strike the workpiece and their kinetic energy is converted to heat. The narrow beam of electrons travel easily in the vacuum chamber. Generally we use high vacuum in e-beam welding. Plates as thick as 150 mm can be welded. No shielding gases, flux or filler material is needed. Elecron beam guns have 100 kW capacities. Deep and narrow welds with high aspect ratios up to 30 and small heat-affected zones are possible. Welding speeds can reach 12 m/min. In laser-beam welding we use high-power lasers as the source of heat. Laser beams as small as 10 microns with high density enable deep penetration into the workpiece. Depth-to-width ratios as much as 10 is possible with laser-beam welding. We use both pulsed as well as continuous wave lasers, with the former in applications for thin materials and the latter mostly for thick workpieces up to about 25 mm. Power levels are up to 100 kW. The laser beam welding is not well suited for optically very reflective materials. Gases may also be used in the welding process. The laser beam welding method is well fit for automation & high volume manufacturing and can offer welding speeds between 2.5 m/min and 80 m/min. One major advantage this welding technique offers is access to areas where other techniques cannot be used. Laser beams can easily travel to such difficult regions. No vacuum as in electron-beam welding is needed. Welds with good quality & strength, low shrinkage, low distortion, low porosity can be obtained with laser beam welding. Laser beams can be easily manipulated and shaped using fiber optic cables. The technique is thus well suitable for welding of precision hermetic assemblies, electronic packages…etc. Let us look at our SOLID STATE WELDING techniques. COLD WELDING (CW) is a process where pressure instead of heat is applied using dies or rolls to the parts that are mated. In cold welding, at least one of the mating parts needs to be ductile. Best results are obtained with two similar materials. If the two metals to be joined with cold welding are dissimilar, we may get weak and brittle joints. The cold welding method is well suited for soft, ductile and small workpieces such as electrical connections, heat sensitive container edges, bimetallic strips for thermostats…etc. One variation of cold welding is roll bonding (or roll welding), where the pressure is applied through a pair of rolls. Sometimes we perform roll welding at elevated temperatures for better interfacial strength. Another solid state welding process we use is the ULTRASONIC WELDING (USW), where the workpieces are subjected to a static normal force and oscillating shearing stresses. The oscillating shearing stresses are applied through the tip of a transducer. Ultrasonic welding deploys oscillations with frequencies from 10 to 75 kHz. In some applications such as seam welding, we use a rotating welding disk as the tip. Shearing stresses applied to the workpieces cause small plastic deformations, break up oxide layers, contaminants and lead to solid state bonding. Temperatures involved in ultrasonic welding are way below melting point temperatures for metals and no fusion takes place. We frequently use the ultrasonic welding (USW) process for nonmetallic materials like plastics. In thermoplastics, the temperatures do reach melting points however. Another popular technique, in FRICTION WELDING (FRW) the heat is generated through friction at the interface of the workpieces to be joined. In friction welding we keep one of the workpieces stationary while the other workpiece is held in a fixture and rotated at a constant speed. The workpieces are then brought into contact under an axial force. The surface speed of rotation in friction welding may reach 900m/min in some cases. After sufficient interfacial contact, the rotating workpiece is brought to a sudden stop and the axial force is increased. The weld zone is generally a narrow region. The friction welding technique can be used to join solid and tubular parts made of a variety of materials. Some flash may develop at the interface in FRW, but this flash can be removed by secondary machining or grinding. Variations of the friction welding process exist. For example “inertia friction welding” involves a flywheel whose rotational kinetic energy is used to weld the parts. The weld is complete when the flywheel comes to a stop. The rotating mass can be varied and thus the rotational kinetic energy. Another variation is “linear friction welding”, where linear reciprocating motion is imposed on at least one of the components to be joined. In linear friction welding parts do not have to be circular, they can be rectangular, square or of other shape. Frequencies can be in the tens of Hz, amplitudes in the millimeters range and pressures in the tens or hundreds of MPa. Finally “friction stir welding” is somewhat different than the other two explained above. Whereas in inertia friction welding and linear friction welding heating of interfaces is achieved through friction by rubbing two contacting surfaces, in the friction stir welding method a third body is rubbed against the two surfaces to be joined. A rotating tool of 5 to 6 mm diameter is brought into contact with the joint. The temperatures can increase to values between 503 to 533 Kelvin. Heating, mixing and stirring of the material in the joint takes place. We use the friction stir welding on a variety of materials including aluminum, plastics and composites. Welds are uniform and quality is high with minimum pores. No fumes or spatter are produced in friction stir welding and the process is well automated. RESISTANCE WELDING (RW): The heat required for welding is produced by the electrical resistance between the two workpieces to be joined. No flux, shielding gases or consumable electrodes are used in resistance welding. Joule heating takes place in resistance welding and can be expressed as: H = (Square I) x R x t x K H is heat generated in joules (watt-seconds), I current in Amperes, R resistance in Ohms, t is the time in seconds the current flows through. The factor K is less than 1 and represents the fraction of energy that is not lost through radiation and conduction. Currents in resistance welding processes can reach levels as high as 100,000 A but voltages are typically 0.5 to 10 Volts. Electrodes are typically made of copper alloys. Both similar and dissimilar materials can be joined by resistance welding. Several variations exist for this process: “Resistance spot welding” involves two opposing round electrodes contacting the surfaces of the lap joint of the two sheets. Pressure is applied until current is turned off. The weld nugget is generally up to 10 mm in diameter. Resistance spot welding leaves slightly discolored indentation marks at weld spots. Spot welding is our most popular resistance welding technique. Various electrode shapes are used in spot welding in order to reach difficult areas. Our spot welding equipment is CNC controlled and has multiple electrodes that can be used simultaneously. Another variation “resistance seam welding” is carried out with wheel or roller electrodes that produce continuous spot welds whenever the current reaches a sufficiently high level in the AC power cycle. Joints produced by resistance seam welding are liquid and gas tight. Welding speeds of about 1.5 m/min are normal for thin sheets. One may apply intermittent currents so that spot welds are produced at desired intervals along the seam. In “resistance projection welding” we emboss one or more projections (dimples) on one of the workpiece surfaces to be welded. These projections may be round or oval. High localized temperatures are reached at these embossed spots that come into contact with the mating part. Electrodes exert pressure to compress these projections. Electrodes in resistance projection welding have flat tips and are water cooled copper alloys. The advantage of resistance projection welding is our ability to a number of welds in one stroke, thus the extended electrode life, capability to weld sheets of various thicknesses, capability to weld nuts and bolts to sheets. Disadvantage of resistance projection welding is the added cost of embossing the dimples. Yet another technique, in “flash welding” heat is generated from the arc at the ends of the two workpieces as they begin to make contact. This method may also alternatively considered arc welding. The temperature at the interface rises, and material softens. An axial force is applied and a weld is formed at the softened region. After the flash welding is complete, the joint can be machined for improved appearance. Weld quality obtained by flash welding is good. Power levels are 10 to 1500 kW. Flash welding is suitable for edge-to-edge joining of similar or dissimilar metals up to 75 mm diameter and sheets between 0.2 mm to 25 mm thickness. “Stud arc welding” is very similar to flash welding. The stud such as a bolt or threaded rod serves as one electrode while being joined to a workpiece such as a plate. To concentrate the generated heat, prevent oxidation and retain the molten metal in the weld zone, a disposable ceramic ring is placed around the joint. Finally “percussion welding” another resistance welding process, utilizes a capacitor to supply the electrical energy. In percussion welding the power is discharged within milliseconds of time very quickly developing high localized heat at the joint. We use percussion welding widely in the electronics manufacturing industry where heating of sensitive electronic components in the vicinity of the joint has to be avoided. A technique called EXPLOSION WELDING involves detonation of a layer of explosive that is put over one of the workpieces to be joined. The very high pressure exerted on the workpiece produces a turbulent and wavy interface and mechanical interlocking takes place. Bond strengths in explosive welding are very high. Explosion welding is a good method for cladding of plates with dissimilar metals. After cladding, the plates may be rolled into thinner sections. Sometimes we use explosion welding for expanding tubes so that they get sealed tightly against the plate. Our last method within the domain of solid state joining is DIFFUSION BONDING or DIFFUSION WELDING (DFW) in which a good joint is achieved mainly by diffusion of atoms across the interface. Some plastic deformation at the interface also contributes to the welding. Temperatures involved are around 0.5 Tm where Tm is melting temperature of the metal. Bond strength in diffusion welding depends on pressure, temperature, contact time and cleanliness of contacting surfaces. Sometimes we use filler metals at the interface. Heat and pressure are required in diffusion bonding and are supplied by electrical resistance or furnace and dead weights, press or else. Similar and dissimilar metals can be joined with diffusion welding. The process is relatively slow due to the time it takes for atoms to migrate. DFW can be automated and is widely used in the fabrication of complex parts for the aerospace, electronics, medical industries. Products manufactured include orthopedic implants, sensors, aerospace structural members. Diffusion bonding can be combined with SUPERPLASTIC FORMING to fabricate complex sheet metal structures. Selected locations on sheets are first diffusion bonded and then the unbonded regions are expanded into a mold using air pressure. Aerospace structures with high stiffness-to-weight ratios are manufactured using this combination of methods. The diffusion welding / superplastic forming combined process reduces the number of parts required by eliminating the need for fasteners, results in low-stress highly accurate parts economically and with short lead times. BRAZING: The brazing and soldering techniques involve lower temperatures than those required for welding. Brazing temperatures are higher than soldering temperatures however. In brazing a filler metal is placed between the surfaces to be joined and temperatures are raised to the melting temperature of the filler material above 723 Kelvin but below the melting temperatures of the workpieces. The molten metal fills the closely fitting space between workpieces. Cooling and subsequent solidification of the filer metal results in strong joints. In braze welding the filler metal is deposited at the joint. Considerably more filler metal is used in braze welding compared to brazing. Oxyacetylene torch with oxidizing flame is used to deposit the filler metal in braze welding. Due to lower temperatures in brazing, problems at heat affected zones such as warping and residual stresses are less. The smaller the clearance gap in brazing the higher is the shear strength of the joint. Maximum tensile strength however is achieved at an optimum gap (a peak value). Below and above this optimum value, the tensile strength in brazing decreases. Typical clearances in brazing can be between 0.025 and 0.2 mm. We use a variety of brazing materials with different shapes such as performs, powder, rings, wire, strip…..etc. and can manufacture these performs specially for your design or product geometry. We do also determine the content of the brazing materials according to your base materials and application. We frequently use fluxes in brazing operations to remove unwanted oxide layers and prevent oxidation. To avoid subsequent corrosion, fluxes are generally removed after the joining operation. AGS-TECH Inc. uses various brazing methods, including: - Torch Brazing - Furnace Brazing - Induction Brazing - Resistance Brazing - Dip Brazing - Infrared Brazing - Diffusion Brazing - High Energy Beam Our most common examples of brazed joints are made of dissimilar metals with good strength such as carbide drill bits, inserts, optoelectronic hermetic packages, seals. SOLDERING : This is one of our most frequently used techniques where the solder (filler metal) fills the joint as in brazing between closely fitting components. Our solders have melting points below 723 Kelvin. We deploy both manual and automated soldering in manufacturing operations. Compared to brazing, soldering temperatures are lower. Soldering is not very suitable for high-temperature or high-strength applications. We use lead-free solders as well as tin-lead, tin-zinc, lead-silver, cadmium-silver, zinc-aluminum alloys besides others for soldering. Both noncorrosive resin-based as well as inorganic acids and salts are used as flux in soldering. We use special fluxes to solder metals with low solderability. In applications where we have to solder ceramic materials, glass or graphite, we first plate the parts with a suitable metal for increased solderability. Our popular soldering techniques are: -Reflow or Paste Soldering -Wave Soldering -Furnace Soldering -Torch Soldering -Induction Soldering -Iron Soldering -Resistance Soldering -Dip soldering -Ultrasonic Soldering -Infrared Soldering Ultrasonic soldering offers us a unique advantage whereby the need for fluxes is eliminated due to ultrasonic cavitation effect which removes oxide films from the surfaces being joined. Reflow and Wave soldering are our industrially outstanding techniques for high volume manufacturing in electronics and therefore worth explaining in greater detail. In reflow soldering, we use semisolid pastes that include solder-metal particles. The paste is placed onto the joint using a screening or stenciling process. In printed circuit boards (PCB) we frequently use this technique. When electrical components are placed onto these pads from paste, the surface tension keeps the surface-mount packages aligned. After placing the components, we heat the assembly in a furnace so the reflow soldering takes place. During this process, the solvents in the paste evaporate, the flux in the paste is activated, the components are preheated, the solder particles are melted and wet the joint, and finally the PCB assembly is cooled slowly. Our second popular technique for high volume production of PCB boards, namely wave soldering relias on the fact that molten solders wet metal surfaces and form good bonds only when the metal is preheated. A standing laminar wave of molten solder is first generated by a pump and the preheated and prefluxed PCBs are conveyed over the wave. The solder wets only exposed metal surfaces but does not wet the IC polymer packages nor the polymer-coated circuit boards. A high-velocity of hot water jet blows excess solder from the joint and prevents bridging between adjacent leads. In wave soldering of surface-mount packages we first adhesively bond them to the circuit board before soldering. Again screening and stenciling is used but this time for epoxy. After the components are placed in their correct locations, the epoxy is cured, the boards are inverted and wave soldering takes place. KLIK Product Finder-Locator Service PAGE sadurunge
- Computer Storage Devices, Disk Array, NAS Array, Storage Area Network
Computer Storage Devices - Disk Array - NAS Array - Storage Area Network - SAN - Utility Storage Arrays - AGS-TECH Inc. Piranti Panyimpenan, Array Disk lan Sistem Panyimpenan, SAN, NAS A STORAGE DEVICE or also known as STORAGE MEDIUM is any computing hardware that is used for storing, porting and extracting data files and objects. Storage devices can hold and store information temporarily as well as permanently. They can be internal or external to a computer, to a server or to any similar computing device. Our focus is on DISK ARRAY which is a hardware element that contains a large group of hard disk drives (HDDs). Disk arrrays may contain several disk drive trays and have architectures improving speed and increasing data protection. A storage controller runs the system, which coordinates activity within the unit. Disk arrays are the backbone of modern storage networking environments. A disk array is a DISK STORAGE SYSTEM which contains multiple disk drives and is differentiated from a disk enclosure, in that an array has cache memory and advanced functionality such as RAID and virtualization. RAID stands for Redundant Array of Inexpensive (or Independent) Disks and employs two or more drives to improve performance and fault tolerance. RAID enables the storage of data in multiple places to protect the data against corruption and to serve it to users faster. Click on the blue highlighted text to download catalogs and brochures: Private Label Flash Storage for Embedded Industrial Applications (We can put your name, logo, brand on these.........) To choose a suitable Industrial Grade Storage Device for your project, please go to our industrial computer store by CLICKING HERE. Dowload brochure for our DESIGN PARTNERSHIP PROGRAM Components of a typical disk array include: - Disk array controllers - Cache memories - Disk enclosures - Power supplies Generally disk arrays provide increased availability, resiliency and maintainability by using additional, redundant components such as controllers, power supplies, fans, etc., to the degree that all single points of failure are eliminated from the design. These components are most of the time hot-swappable. Typically, disk arrays are divided into categories: NETWORK ATTACHED STORAGE (NAS) ARRAYS : NAS is a dedicated file storage device that provides local-area network (LAN) users with centralized, consolidated disk storage through a standard Ethernet connection. Each NAS device is connected to the LAN as an independent network device and assigned an IP address. Its main advantage is that network storage is not limited to the storage capacity of a computing device or the number of disks in a local server. NAS products can generally hold enough disks to support RAID, and multiple NAS appliances can be attached to the network for storage expansion. STORAGE AREA NETWORK (SAN) ARRAYS : They contain one or more disk arrays that function as the repository for the data which is moved in and out of the SAN. Storage arrays connect to the fabric layer with cables running from the devices in the fabric layer to the GBICs in the ports on the array. There are mainly two types of storage area network arrays, namely modular SAN arrays and monolithic SAN arrays. Both of them use built-in computer memory to speed up and cache access to slow disk drives. The two types use memory cache differently. Monolithic arrays generally have more cache memory compared to modular arrays. 1.) MODULAR SAN ARRAYS : These have fewer port connections, they store less data and connect to fewer servers compared to monolithic SAN arrays. They make it possible for the user such as small companies to start small with a few disk drives and to increase the number as storage needs grow. They have shelves for holding disk drives. If connected to only a few servers, modular SAN arrays can be very fast and offer companies a flexibility. Modular SAN arrays fit into standard 19” racks. They generally use two controllers with separate cache memory in each and mirror the cache between the controllers to prevent data loss. 2.) MONOLITHIC SAN ARRAYS : These are big collections of disk drives in data centers. They can store much more data compared to modular SAN arrays and generally connect to mainframes. Monolithic SAN arrays have many controllers that can share direct access to fast global memory cache. Monolithic arrays generally have more physical ports to connect to storage area networks. Thus more servers can use the array. Typically monolithic arrays are more valuable and have superior built-in redundancy and reliability. UTILITY STORAGE ARRAYS : In utility storage service model, a provider offers storage capacity to individuals or organizations on a pay-per-use basis. This service model is also referred to as storage on demand. This facilitates efficient use of resources and reduces cost. This can be more cost effective to companies by eliminating the need to purchase, manage and maintain infrastructures that meet peak requirements which may be beyond the needed capacity limits. STORAGE VIRTUALIZATION : This uses virtualization to enable better functionality and more advanced features in computer data storage systems. Storage virtualization is the apparent pooling of data from several same-type or different types of storage devices into what appears to be a single device managed from a central console. It helps storage administrators perform backup, archiving and recovery more easily and faster by overcoming the complexity of a storage area network (SAN). This can be achieved by implementing virtualization with software applications or using hardware and software hybrid appliances. KLIK Product Finder-Locator Service PAGE sadurunge
- Camera Systems & Components, Optic Scanner, Optical Readers, CCD
Camera Systems - Components - Optic Scanner - Optical Readers - Imaging System - CCD - Optomechanical Systems - IR Cameras Manufaktur & Majelis Sistem Kamera Kustomisasi AGS-TECH offers: • Camera systems, camera components and custom camera assemblies • Custom designed and manufactured optical scanners, readers, optical security product assemblies. • Precision optical, opto-mechanical and electro-optical assemblies integrating imaging and nonimaging optics, LED lighting, fiber optics and CCD cameras • Among the products our optical engineers have developed are: - Omni-directional periscope and camera for surveillance and security applications. 360 x 60º field of view high resolution image, no stitching required. - Inner cavity wide angle video camera - Super slim 0.6 mm diameter flexible video endoscope. All medical video couplers fit over standard endoscope eyepieces and are completely sealed and soakable. For our medical endoscope and camera systems, please visit: http://www.agsmedical.com - Video camera and coupler for semi-rigid endoscope - Eye-Q Videoprobe. Non-contact zoom videoprobe for coordinate measuring machines. - Optical spectrograph & IR imaging system (OSIRIS) for ODIN satellite. Our engineers worked on the flight unit assembly, alignment, integration and test. - Wind imaging interferometer (WINDII) for NASA upper atmosphere research satellite (UARS). Our engineers worked on consulting on assembly, integration and test. WINDII performance and operational lifetime far exceeded the design goals and requirements. Depending on your application, we will determine what dimensions, pixel count, resolution, wavelength sensitivity your camera application requires. We can build systems for you suitable for infrared, visible and other wavelengths. Contact us today to find out more. Dowload brochure for our DESIGN PARTNERSHIP PROGRAM Developing a customized camera system can take relatively longer lead times and cost more as compared to ready-to-use systems. Therefore please click on the blue links below to check whether any of our ready-to-use products fit your application: Barcode and Fixed Mount Scanners - RFID Products - Mobile Computers - Micro Kiosks OEM Technology (We private label these with your brand name and logo if you wish) Barcode Scanners (We private label these with your brand name and logo if you wish) Fixed Industrial Scanners (We private label these with your brand name and logo if you wish) Hikrobot Machine Vision Products Hikrobot Smart Machine Vision Products Hikrobot Machine Vision Standard Products Hikvision Logistic Vision Solutions Private Label Medical Endoscopes and Visualization Systems (We can put your company name and logo on these) Also make sure to download our comprehensive electric & electronic components catalog for off-shelf products by CLICKING HERE. KLIK Product Finder-Locator Service PREVIOUS PAGE