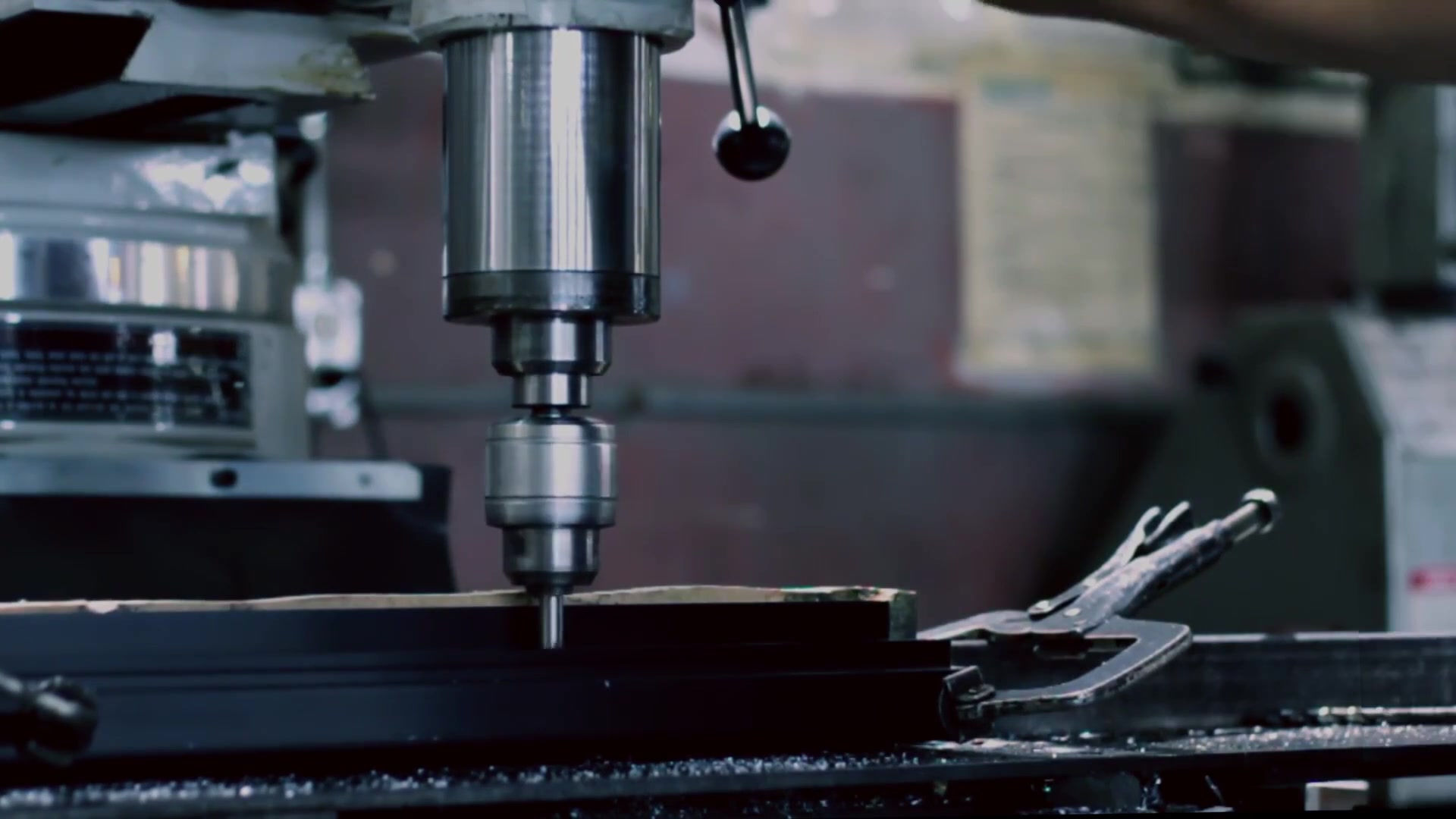
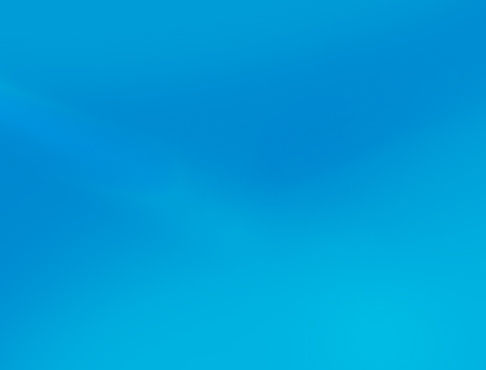
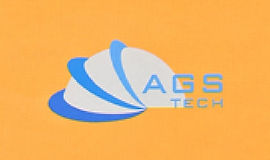
Hilberînerê Xwerû ya Gloverî, Integrator, Hevkar, Hevkarê Derveyî Ji bo Cûreyek Berfireh a Hilber û Karûbaran.
Em ji bo çêkirin, çêkirin, endezyarî, yekbûn, yekbûn, derxistina hilber û karûbarên xwerû yên çêkirî û yên li derveyî refê çavkaniya weya yek-rawest in. Ger hûn bixwazin, em di heman demê de etîketa taybet / spî hilberên we bi navê marqeya we nîşan didin.
Zimanê xwe hilbijêre
Hilberîna Xweser a Parçe, Pêkhatî, Meclîs, Berhemên Qediyayî, Makîne û Amûrên Pîşesaziyê
Hilberîna Peymana Navxweyî û Gerdûnî
Manufacturing Outsourcing
Kirîna Navxweyî, Gerdûnî ya Berhemên Pîşesazî
Etîketkirina taybet / Spî Hilberên xwe bi navê marqeya xwe nîşankirin
Karûbarên Dîtina Hilber & Cihgirtin
Sêwirana gerdûnî û Hevkariya Kanal
Endezyariya Entegrasyonê
Xizmetên Endezyariyê
Hevgirtina Gerdûnî, Warehousing, Logistics
Encamên Lêgerînê
164 results found with an empty search
- Gear Cutting & Shaping Tools , USA , AGS-TECH Inc.
AGS-TECH, Inc. is a supplier of Gear Cutting & Shaping Tools, including Gear Hobbing Cutters, Gear Hobs, Gear Shaper Cutters, Gear Shaving Cutters. We also manufacture and supply gear cutting and shaping tools according to your specific designs and customized needs. Amûrên Çêkirina Çêkirina Gear Ji kerema xwe ji bo dakêşana broşûra têkildar, li ser amûrên birrîn û şekildana kelûpelên şîn ên balkêş ên li jêr bikirtînin. Vana amûrên qutkirin û şekilkirina kelûpelên bêserûber in, lê ger bixwazin em li gorî nexşe û taybetmendiyên we jî çêdikin. Gear Hobbing Cutters (Gear Hobs) Gear Shaper Cutters Gear Shaving Cutters Biha: Bi model û hêjmara fermanê ve girêdayî ye. Bila ji me re hilbera berjewendiya we ji bo binavkirinê nas bikin. Ji ber ku em cûrbecûr amûrên birrîn û şekildana gemarê bi pîvan, sepan û materyalên cihêreng hildigirin; ne mimkûn e ku meriv wan li vir rêz bike. Heke hûn nebawer in, em ji we re teşwîq dikin ku bi me re têkilî daynin da ku em diyar bikin ka kîjan hilber ji we re çêtirîn e. Ji kerema xwe ji me re agahdar bikin: - Serlêdana te - Pola materyalê tê xwestin - Dimensions - Pêdiviyên qedandinê - Pêdiviyên pakkirinê - Pêdiviyên etîketkirinê - Hejmara her ferman û daxwaziya salane VIRÊ bikirtînin da ku kapasîteyên me yên teknîkî û rêbernameya referansê dakêşin ji bo birîna taybetmendî, sondajê, rijandin, çêkirin, şikilandin, pîvazkirina amûrên ku di bijîjkî, diranan, amûrên rast, mêtina metal, çêkirina mirinê û sepanên din ên pîşesaziyê de têne bikar anîn. CLICK Product Finder-Locator Service Li vir bikirtînin da ku biçin Menuya Amûrên Birîn, Xalkirin, Xirkirin, Lapkirin, Paqijkirin, Diçandin û Teşekirin. Ref. Kod: oicasxingwanggongju
- Masonry Cutting Shaping Tools, USA, AGS-TECH Inc.
High quality Masonry Cutting and Shaping Tools including universal drills, glass tile drill bits, chisel, hammer drill bits, masonry drill bits, TCT core drills, diamond core drills, SDS chuck adapter, and more. Amûrên Cutting & Shaping Masonry Masonry is work done using stone, brick, or concrete. Therefore, masonry cutting, shaping tools refer to all kinds of blades, drills, drill bits, chisels.....etc. used to work on materials such as stones, bricks and concrete. Please click on the products of interest below to download related brochure. (Put the mouse on name of product and click on it). We do have a wide spectrum of masonry cutting & shaping tools suitable for almost any application. There is a wide variety of masonry cutting & shaping tools with different dimensions, applications and material; it is impossible to present them all here. If you cannot find or if you are not sure which masonry cutting and shaping tools will meet your expectations and requirements, email or call us so we can determine which product is the best fit for you. When contacting us, please try to provide us as much detail as possible such as your application, dimensions, material grade if you know, finishing requirements, packaging & labeling requirements and of course quantity of your planned order. Universal Drills New!! Glass Tile Drill Bits Chisel Cold Chisel & Punch Hammer Drill Bits (SDS) Masonry Drill Bits TCT Core Drills Diamond Core Drills SDS Chuck Adapter Private Label Abrasives (We can put your company name, logo, brand on these. In other words we offer you private label) Private Label Abrasives Ordering Instructions Guide Private Label Drill Bits (We can private label these drill bits with your company name and logo) Private Label Hand Tools for Every Industry This catalog contains some masonry cutting and shaping tools. We can private label these hand tools if you wish. In other words, we can put your company name, brand and label on them. This way you can promote your brand by reselling these to your customers. Private Label Power Tool Accessories This brochure includes some masonry cutting and shaping tools. We can private label these hand tools if you wish. In other words, we can put your company name, brand and label on them. This way you can promote your brand by reselling these to your customers. Private Label Power Tools for Every Industry This catalog contains some masonry cutting and shaping tools. We can private label these hand tools if you wish. In other words, we can put your company name, brand and label on them. This way you can promote your brand by reselling these to your customers. Private Label Taps - Cutting Tools (We can private label these drill bits with your company name and logo) VIRÊ bikirtînin da ku kapasîteyên me yên teknîkî û rêbernameya referansê dakêşin ji bo birîna taybetmendî, sondajê, rijandin, çêkirin, şikilandin, pîvazkirina amûrên ku di bijîjkî, diranan, amûrên rast, mêtina metal, çêkirina mirinê û sepanên din ên pîşesaziyê de têne bikar anîn. CLICK Product Finder-Locator Service Li vir bikirtînin da ku biçin Menuya Amûrên Birîn, Xalkirin, Xirkirin, Lapkirin, Paqijkirin, Diçandin û Teşekirin. Ref. Kod: OICASOSTAR
- Engineering Integration , USA , AGS-TECH Inc.
AGS-TECH, Inc. is globally recognized for its wide range of engineering integration, mechanical & optical & electronic & software integration capabilities. Yekbûna Endezyariyê - Yekbûna Mekanîk & Optîkî & Elektronîk & Nermalava Em ne tenê pêkhateyên takekesî çêdikin. Em di heman demê de INTEGRATION ENDEZZERÎ - Yekbûna Mekanîk & Optîkî & Elektronîkî û Nermalavê, Civîn û Testkirin peyda dikin. Bi gotinek din, em dikarin hêman û perçeyên we çêkin û dikarin wan binecivînin an jî wan di hilberên bêkêmasî de bicivînin. Digel vê yekê em dikarin hardware bi nermalavê û firmware re yek bikin, ceribandin û kalîteyê li ser hilberên we bikin, em dikarin wekî ku amade ne ku ji xerîdarên xwe re bifroşin etîket bikin, pakkirin û bişînin. Cûreyên karûbarên entegrasyonê yên endezyariyê ku em bi salan e ku ji xerîdarên xwe re pêşkêş dikin ev in: - Yekbûn û komkirina endezyarî ya pêkhateyên mekanîkî yên ji metal, alloy, plastîk û elastomer (lasoman) hatine çêkirin. Nimûneyên hilberên ku me hilberandine meclîsên pêlav, hilgir û kelûpelan, çîp û alavên ku ji hêla me ve ji bo serîlêdanên taybetî têne çêkirin in. - Yekbûn û komkirina endezyarî ya pêkhateyên elektrîkî û elektronîkî yên wekî panelên çerxa çapkirî, meclîsên têl û kabloyan, çîpên germê, xanî û pakêta hilberê. Mînakên tîpîk dabînkirina hêzê ne ku me ji bo xerîdarên xwe çêdikir. - Yekbûn û berhevkirina endezyariya pêkhateyên optîkî bi pêkhateyên mekanîkî, elektrîkî û elektronîkî. Mînakên tîpîk cîhazên hestiyar ên optîkî, amûrên ceribandina optîkî ne. - Yekbûna endezyarî ya hardware optîk, elektronîkî û mekanîkî bi nermalavê re. Robotên cihêreng û pergalên xweseriyê yên ku me ji bo xerîdarên xwe çêkirine ji vê komê re mînak in. Em dikarin kodê binivîsin û pergalên weya bicîbûyî, robot û alavên otomasyonê bername bikin an heke we kodek nivîsandî hebe, em dikarin wê bi pergala weya nû re yek bikin, xelet bikin, biguhezînin û koda we hîn çêtir bikin. Ji bo hin projeyan, me bi serfirazî nermalava ji-raftê an kodek belaş berdest di nav pergalên xerîdarên xwe de yek kiriye. Ji bo BERNAMEYA HEVKARÎYA DESIGN a me broşurê dakêşin Heke hûn bi piranî li şûna kapasîteyên çêkirinê bi kapasîteyên me yên endezyar û lêkolîn û pêşkeftinê re eleqedar in, wê hingê em we vedixwînin ku hûn biçin serdana malpera meya endezyariyê http://www.ags-engineering.com CLICK Product Finder-Locator Service RÛPERA BERÊ
- Pneumatic Reservoirs, Hydraulic Reservoir, Vacuum Chambers, Tanks
Pneumatic Reservoirs, Hydraulic Reservoir, Vacuum Chambers, Tanks, High Vacuum Chamber, Hydraulics & Pneumatics System Components Manufacturing at AGS-TECH Inc. Reservoir & Odeyên ji bo Hîdraulîk & Pneumatîk & Vacuum New designs of hydraulic and pneumatic systems require smaller and smaller RESERVOIRS than the traditional ones. We specialize in reservoirs that will meet your industrial needs and standards and are as compact as possible. High vacuum is expensive, and therefore the smallest VACUUM CHAMBERS that will fulfill your needs are the most appealing in most cases. We specialize in modular vacuum chambers and equipment and can offer you solutions on an ongoing basis as your business grows. HYDRAULIC & PNEUMATIC RESERVOIRS: Fluid power systems require air or liquid to transmit energy. Pneumatic systems use the air as the source for reservoirs. A compressor takes in atmospheric air, compresses it and then stores it in a receiver tank. A receiver tank is similar to a hydraulic system’s accumulator. A receiver tank stores energy for future use similar to a hydraulic accumulator. This is possible because air is a gas and is compressible. At the end of the work cycle the air is simply returned to the atmosphere. Hydraulic systems, on the other hand, need a finite amount of liquid fluid that must be stored and reused continually as the circuit works. Reservoirs are therefore part of almost any hydraulic circuit. Hydraulic reservoirs or tanks may be part of the machine framework or a separate stand-alone unit. The design and application of reservoirs is very important. The efficiency of a well-designed hydraulic circuit can be greatly reduced by poor reservoir design. Hydraulic reservoirs do much more than just providing a place to store fluid. FUNCTIONS OF PNEUMATIC & HYDRAULIC RESERVOIRS: In addition to holding in reserve enough fluid to supply a system's varying needs, a reservoir provides: -A large surface area for transferring heat from the fluid to the surrounding environment. -Sufficient volume to let returning fluid slow down from a high velocity. This allows heavier contaminants to settle down and facilitates air escape. Air space above the fluid can accept air that bubbles out of the fluid. Users get access to remove used fluid and contaminants from the system and can add new fluid. -A physical barrier separating fluid entering the reservoir from fluid entering the pump suction line. -Space for hot-fluid expansion, gravity drain-back from a system during shutdown, and storage of large volumes needed intermittently during peak periods of operation -In some cases, a convenient surface to mount other system components and components. COMPONENTS OF RESERVOIRS: The filler-breather cap should include a filter media to block contaminants as the fluid level lowers and rises during a cycle. If the cap is used for filling, it should have a filter screen in its neck to catch large particles. It is best to pre-filter any fluid entering reservoirs. The drain plug is removed and tank emptied when the fluid needs to be changed. At this time, the clean-out covers should be removed to provide access to clean out all stubborn residue, rust, and flaking that may have accumulated in the reservoir. The clean-out covers and internal baffle are assembled together, with some brackets to keep the baffle upright. Rubber gaskets seal the clean-out covers to prevent leaks. If the system is seriously contaminated, one must flush all pipes and actuators while changing the tank fluid. This can be done by disconnecting the return line and placing its end in a drum, then cycling the machine. Sight glasses on reservoirs make it easy to visually check fluid levels. Calibrated sight gauges provide even more accuracy. Some sight gauges include a fluid-temperature gauge. The return line should be located in the same end of the reservoir as the inlet line and on the opposite side of the baffle. Return lines should terminate below fluid level to reduce turbulence and aeration in reservoirs. The open end of the return line should be cut at 45 degrees to eliminate the chances of stopping flow if it gets pushed to the bottom. Alternatively the opening can be pointed toward the side wall to get the maximum heat-transfer surface contact possible. In cases where hydraulic reservoirs are part of the machine base or body, it may not be possible to incorporate some of these features. Reservoirs are occasionally pressurized because pressurized reservoirs provide the positive inlet pressure required by some pumps, usually in line piston types. Also pressurized reservoirs force fluid into a cylinder through an undersized pre-fill valve. This may require pressures between 5 and 25 psi and one cannot use conventional rectangular reservoirs. Pressurizing reservoirs keeps out contaminates. If the reservoir always has a positive pressure in it there is no way for atmospheric air with its contaminants to enter. Pressure for this application is very low, between 0.1 to 1.0 psi, and may be acceptable even in rectangular model reservoirs. In a hydraulic circuit, wasted horsepower needs to be calculated in order to determine heat generation. In highly efficient circuits the wasted horsepower could be low enough to use the reservoirs cooling capacities to keep maximum operating temperatures below 130 F. If heat generation is slightly higher than what standard reservoirs can handle, it may be best to oversize the reservoirs rather than adding heat exchangers. Oversized reservoirs are less expensive than heat exchangers; and avoid the cost of installing water lines. Most industrial hydraulic units operate in warm indoor environments and therefore low temperatures are not a problem. For circuits that see temperatures below 65 to 70 F., some sort of fluid heater is recommended. The most common reservoir heater is an electric-powered immersion type unit. These reservoir heaters consist of resistive wires in a steel housing with a mounting option. Integral thermostatic control is available. Another way to electrically heat reservoirs is with a mat that has heating elements like electric blankets. This type heaters require no ports in the reservoirs for insertion. They evenly heat the fluid during times of low or no fluid circulation. Heat can be introduced through a heat exchanger by using hot water or steam The exchanger becomes a temperature controller when it also uses cooling water to take away heat when needed. Temperature controllers are not a common option in most climates because the majority of industrial applications operate in controlled environments. Always consider first if there is any way to reduce or eliminate unnecessarily generated heat, so it does not have to be paid for twice. It is costly to produce the unused heat and it is also expensive to get rid of it after it enters the system. Heat exchangers are costly, the water running through them is not free, and maintenance of this cooling system can be high. Components such as flow controls, sequence valves, reducing valves, and undersized directional control valves can add heat to any circuit and should be carefully thought about when designing. After calculating wasted horsepower, review catalogs that include charts for given size heat exchangers showing the amount of horsepower and/or BTU they can remove at different flows, oil temperatures, and ambient air temperatures. Some systems use a water-cooled heat exchanger in the summer and an air-cooled one in the winter. Such arrangements eliminate plant heating in summer weather and save on heating costs in the winter. SIZING OF RESERVOIRS: The volume of a reservoir is a very important consideration . A rule of thumb for sizing a hydraulic reservoir is that its volume should equal three times the rated output of the system's fixed-displacement pump or mean flow rate of its variable-displacement pump. As an example, a system using a 10 gpm pump should have a 30 gal reservoir. This is nevertheless only a guideline for initial sizing. Due to modern day system technology, design objectives have changed for economic reasons, such as space saving, minimizing oil usage, and overall system cost reductions. Regardless of whether you choose to follow the traditional rule of thumb or follow the trend toward smaller reservoirs, be aware of parameters that may influence the reservoir size required. As an example, some circuit components such as large accumulators or cylinders may involve large volumes of fluid. Therefore, larger reservoirs may be needed so that fluid level does not drop below the pump inlet regardless of pump flow. Systems exposed to high ambient temperatures also require larger reservoirs unless they incorporate heat exchangers. Be sure to consider the substantial heat that can be generated within a hydraulic system. This heat is generated when the hydraulic system produces more power than is consumed by the load. The size of reservoirs, therefore, is determined primarily by the combination of highest fluid temperature and highest ambient temperature. All other factors being equal, the smaller the temperature difference between the two temperatures, the larger the surface area and hence the volume needed to dissipate heat from fluid to the surrounding environment. If the ambient temperature exceeds the fluid temperature, a heat exchanger will be needed to cool the fluid. For applications where space conservation is important, heat exchangers can reduce reservoir size and cost significantly. If reservoirs are not full at all times, they may not be dissipating heat through their full surface area. Reservoirs should contain at least 10% additional space of fluid capacity. This allows for thermal expansion of the fluid and gravity drain-back during shutdown, yet still provides a free fluid surface for deaeration. Maximum fluid capacity of reservoirs are marked permanently on their top plate. Smaller reservoirs are lighter, more compact, and less expensive to manufacture and maintain than one of traditional size and they are environmentally more friendly by reducing the total amount of fluid that can leak from a system. However specifying smaller reservoirs for a system must be accompanied by modifications that compensate for the lower volumes of fluid contained in the reservoirs. Smaller reservoirs have less surface area for heat transfer, and therefore heat exchangers may be necessary to maintain fluid temperatures within requirements. Also, in smaller reservoirs contaminants will not have as much opportunity for settling, so high-capacity filters will be required to trap contaminants. Traditional reservoirs provide the opportunity for air to escape from fluid before it is drawn into the pump inlet. Providing too small reservoirs could result in aerated fluid being drawn into the pump. This could damage the pump. When specifying a small reservoir, consider installing a flow diffuser, which reduces the velocity of return fluid, and helps prevent foaming and agitation, thus reducing potential pump cavitation from flow disturbances at the inlet. Another method you can use is to install a screen at an angle in the reservoirs. The screen collects small bubbles, which join with others to form large bubbles that rise to the fluid's surface. Nevertheless the most efficient and economical method to prevent aerated fluid from being drawn into the pump is to prevent aeration of fluid in the first place by paying careful attention to fluid flow paths, velocities, and pressures when designing a hydraulic system. VACUUM CHAMBERS: While it is sufficient to manufacture most of our hydraulic and pneumatic reservoirs by sheet metal forming due to the relatively low pressures involved, some or even most of our vacuum chambers are machined from metals. Very low pressure vacuum systems must endure high external pressures from the atmosphere and cannot be made of sheet metals, plastic moulds or other fabrication techniques that reservoirs are made of. Therefore vacuum chambers are relatively more expensive than reservoirs in most cases. Also sealing of vacuum chambers is a greater challenge as compared to reservoirs in most cases because gas leaks into the chamber is hard to control. Even minute amounts of air leak into some vacuum chambers can be disastrous while most pneumatic and hydraulic reservoirs can tolerate some leakage easily. AGS-TECH is a specialist in high and ultra high vacuum chambers and equipment. We provide our clients the highest quality in engineering and fabrication of high vacuum and ultra high vacuum chambers and equipment. Excellence is assured through control of the entire process from; CAD design, fabrication, leak-testing, UHV cleaning and bake-out with RGA scan when required. We do provide off the shelf catalogue items, as well as work closely with clients to provide custom vacuum equipment and chambers. Vacuum Chambers can be manufactured in Stainless steel 304L/ 316L & 316LN or machined from Aluminum. High vacuum can accommodate small vacuum housings as well as large vacuum chambers with several meters of dimensions. We offer fully integrated vacuum systems-manufactured to your specifications, or designed & built to your requirements. Our vacuum chamber manufacturing lines deploy TIG welding and extensive machine shop facilities with 3, 4 & 5 axis machining to process hard to machine refractory material such as tantalum, molybdenum to high temperature ceramics such as boron and macor. In addition to these complex chambers we are always ready to consider your requests for smaller vacuum reservoirs. Reservoirs and canisters for both low and high vacuum can be designed and supplied. As we are the most diverse custom manufacturer, engineering integrator, consolidator and outsourcing partner; you can contact us for any of your standard as well as complicated new projects involving reservoirs and chambers for hydraulics, pneumatics and vacuum applications. We can design reservoirs and chambers for you or use your existing designs and turn them into products. In any case, getting our opinion on hydraulic and pneumatic reservoirs and vacuum chambers and accessories for your projects will only be to your benefit. - Hydraulic Reservoirs with Private Label (We can put your company name as the brand and your company logo on these. This way you can market your brand name when selling or using these) CLICK Product Finder-Locator Service RÛPERA BERÊ
- Service and Repair Kits for Pneumatics Hydraulics and Vacuum Systems
Service and Repair Kits for Pneumatics Hydraulics and Vacuum Systems - Replacement Parts - Refurbishing Rebuilding Pneumatic Hydraulic and Vacuum Equipment Kîtên Xizmet û Tamîrkirinê ji bo Pneumatîk & Hîdraulîk û Vacuum We make your pneumatic, hydraulic and vacuum equipment and systems last longer, operate more efficiently and more economically, by supplying you the most reliable and high quality service & repair kits and products. Our service and repair kits are easy to be used by experienced technical staff. We offer original service and repair kits, generic brand name kits and custom designed and manufactured service and repair kits. Custom service & repair kits are produced, assembled and packaged according to your needs and if desired we can include instruction materials inside. Besides service and repair kits, we offer other products and services: REPLACEMENT PARTS SERVICE and REPAIR KITS for PUMPS SERVICE and REPAIR KITS FOR PNEUMATIC and HYDRAULIC RESERVOIRS FILTER SERVICE & REPAIR KITS PNEUMATIC CYLINDER SERVICE and REPAIR KITS HYDRAULIC CYLINDER SERVICE and REPAIR KITS SERVICE and REPAIR KITS FOR DISTRIBUTION COMPONENTS SERVICE and REPAIR KITS for VACUUM SYSTEMS and LINES REBUILD & REFURBISH KITS CUSTOM MANUFACTURED & OFF-SHELF FILTER ELEMENTS CUSTOM CNC MACHINED and OFF-SHELF SEALS & O-RINGS MOLDED RUBBER and CUSTOM MACHINED PARTS SERVICE and REPAIR KITS for PNEUMATIC & HYDRAULIC and VACUUM TOOLS Here is what we can offer you: - Supply you ORIGINAL service and repair kits, original replacement components and products of some well known pneumatic, hydraulic and vacuum system manufacturers for the list prices or lower. - Supply you GENERIC BRAND NAME service and repair kits, replacement components and products of some well known pneumatic, hydraulic and vacuum system manufacturers for lower prices. Even though lower in price as compared to original kits, our generic brand name service and repair kits are at least as reliable and good in quality as the originals. - REFURBISH & REBUILD your existing systems to make them at least of the same quality as original or even better. - DESIGN and CUSTOM MANUFACTURE service and repair kits, replacement components and pneumatic, hydraulic and vacuum system products for competitive prices and highest quality to make you more competitive in the global markets. CLICK ON BLUE HIGHLIGHTED TEXT TO DOWNLOAD CATALOGS: - Private Label Gauges, Filters, Regulators, Temperature Instruments (We private label these with your brand name and logo if you wish) - Private Label Pneumatic Compressed Air Hoses Fittings (We private label these with your brand name and logo if you wish) - Private Label Pneumatic Couplings, Plugs and Nipples (We private label these with your brand name and logo if you wish) Please note that even though our service and repair kits are easy to use, we strongly recommend that you have professional staff that handles your equipment. The service and repair kits can turn out to be of no use or you may even damage your equipment in case the kits are not used professionally by experienced personnel. Pneumatic, hydraulic and vacuum equipment requires professional handling, and instructions included in our service and repair kits alone may not be sufficient for an inexperienced person to understand and use them. In situations where you cannot afford the cost or production downtime caused by shipping your equipment to us for service and repair, or if you do not need or choose to have our technicians come to your site we will be glad to help you over the phone or teleconferencing system, but you may still need a local professional to carry out the instructions, unless your system is simple enough for anyone to fix. All components in our service and repair kits have industry standard warranties and you are assured full satisfaction or money back guarantee. For details on warranty and other issues related to our service and repair kits, please contact our professional service staff at +1-505-550-6501 / +1-505-565-5102 or email: technicalsupport@agstech.net CLICK Product Finder-Locator Service RÛPERA BERÊ
- Seals, Fittings, Connections, Adaptors, Flanges, Pneumatics Hydraulics
Seals - Fittings - Connections - Adaptors - Flanges for Pneumatics Hydraulics and Vacuum - AGS-TECH Inc. Mohr & Têkilî & Girêdan & Girêdan & Adapter & Flange & Hevgirêdanên Lezgîn Vital components in pneumatic, hydraulic and vacuum systems are SEALS, FITTINGS, CONNECTIONS, ADAPTERS, QUICK COUPLINGS, CLAMPS, FLANGES. Depending on the application environment, standards requirements, and geometry of the application area there are a wide spectrum of these products readily available from our stock. On the other hand, for customers with special needs and requirements we are custom manufacturing seals, fittings, connections, adaptors, clamps and flanges for every possible pneumatics, hydraulics and vacuum application. If components within hydraulic systems never needed to be removed, we could simply braze or weld connections. However, it is inevitable that connections must be broken to allow servicing and replacing, so removable fittings and connections are a necessity for hydraulic, pneumatic and vacuum systems. Fittings seal fluids within hydraulic systems by one of two techniques: ALL-METAL FITTINGS rely on metal-to-metal contact, while O-RING TYPE FITTINGS rely on compressing an elastomeric seal. In both cases, tightening threads between mating halves of the fitting or between fitting and component forces two mating surfaces come together to form a high-pressure seal. ALL-METAL FITTINGS: Threads on pipe fittings are tapered and rely on the stress generated by forcing the tapered threads of the male half of the fittings into the female half of fittings. Pipe threads are prone to leakage because they are torque-sensitive. Over-tightening all-metal fittings distorts the threads too much and creates a path for leakage around the fittings threads. Pipe threads on all-metal fittings are also prone to loosening when exposed to vibration and wide temperature fluctuations. Pipe threads on fittings are tapered, and therefore repeated assembly and disassembly of the fittings aggravate the leakage problems by distorting the threads. Flare-type fittings are superior to pipe fittings and likely will remain the design of choice used in hydraulic systems. Tightening the nut draws the fittings into the flared end of the tubing, resulting in a positive seal between the flared tube face and the fitting body. The 37 degree flare fittings are designed for use with thin-wall to medium-thickness tubing in systems with operating pressures up to 3,000 psi and temperatures from -65 to 400 F. Because thick-wall tubing is difficult to form to produce the flare, it is not recommended for use with flare fittings. It is more compact than most other fittings and can easily be adapted to metric tubing. It is readily available and one of the most economical. The flareless fittings, gradually are gaining wider acceptance, because they require minimal tube preparation. Flareless fittings handle average fluid working pressures up to 3,000 psi and are more tolerant of vibration than other types of all-metal fittings. Tightening the fitting's nut onto the body draws a ferrule into the body. This compresses the ferrule around the tube, causing the ferrule to contact, then penetrate the outer circumference of the tube, creating a positive seal. Flareless fittings need to be used with medium or thick-walled tubing. O-RING TYPE FITTINGS: Fittings using O-rings for leak-tight connections continue to gain acceptance by equipment designers. Three basic types are available: SAE straight-thread O-ring boss fittings, face seal or flat-face O-ring (FFOR) fittings, and O-ring flange fittings. The choice between O-ring boss and FFOR fittings usually depends on such factors as fitting location, wrench clearance…etc. Flange connections generally are used with tubing that have an outer diameter greater than 7/8-inch or for applications involving extremely high pressures. O-ring boss fittings seat an O-ring between threads and wrench flats around the outer diameter (OD) of the male half of the connector. A leak-tight seal is formed against a machined seat on the female port. There are two groups of O-ring boss fittings: adjustable and non-adjustable fittings. Non-adjustable or non-orientable O-ring boss fittings include plugs and connectors. These are simply screwed into a port, and no alignment is needed. Adjustable fittings on the other hand, such as elbows and tees, need to be oriented in a specific direction. The basic design difference between the two types of O-ring boss fittings is that plugs and connectors have no locknuts and require no back-up washer to effectively seal a joint. They depend on their flanged annular area to push the O-ring into the port's tapered seal cavity and squeeze the O-ring for sealing the connection. On the other hand, adjustable fittings are screwed into the mating member, oriented in the required direction, and locked in place when a locknut is tightened. Tightening the locknut also forces a captive backup washer onto the O-ring, which forms the leak-tight seal. Assembly is always predictable, technicians need only make sure that the backup washer is firmly seated on the port's spot face surface when the assembly is completed and that it is tightened properly. The FFOR fittings form a seal between a flat and finished surface on the female half and an O-ring held in a recessed circular groove in the male half. Turning a captive threaded nut on the female half draws the two halves together while compressing the O-ring. Fittings with O-ring seals offer some advantages over metal-to-metal fittings. All-metal fittings are more susceptible to leakage because they must be tightened to within a higher, yet narrower torque range. This makes it easier to strip threads or crack or distort fitting components, which prevents proper sealing. The rubber-to-metal seal in O-ring fittings does not distort any metal parts and provides a feel on our fingers when the connection is tight. All-metal fittings tighten more gradually, so technicians may find it more difficult detecting when a connection is tight enough but not too tight. Disadvantages are that O-ring fittings are more expensive than all-metal fittings, and care must be exercised during installation to ensure that the O-ring doesn't fall out or get damaged when the assemblies are connected. In addition, O-rings are not interchangeable among all couplings. Selecting the wrong O-ring or reusing one that has been deformed or damaged can result in leakage in fittings. Once an O-ring has been used in a fitting, it is not reusable, even though it may appear free of distortions. FLANGES: We offer flanges individually or as a complete set for a number of applications in a range of sizes and types. Stock is kept of Flanges, Counter-flanges, 90 degree flanges, Split flanges, Threaded flanges. Fittings for tubing larger than 1-in. OD have to be tightened with large hexnuts which requires a large wrench to apply sufficient torque to tighten the fittings properly. To install such large fittings, the necessary space needs to be given to workers to swing large wrenches. Worker strength and fatigue could also affect proper assembly. Wrench extensions may be needed for some workers to exert an applicable amount of torque. Split-flange fittings are available so that they overcome these problems. Split-flange fittings use an O-ring to seal a joint and contain pressurized fluid. An elastomeric O-ring sits in a groove on a flange and mates with a flat surface on a port - an arrangement similar to the FFOR fitting. The O-ring flange is attached to the port using four mounting bolts that tighten down onto flange clamps. This eliminates the need for large wrenches when connecting large-diameter components. When installing flange connections, it is important to apply even torque on the four flange bolts to avoid creating a gap through which the O-ring can extrude under high pressure. A split-flange fitting consists generally of four elements: a flanged head connected permanently (generally welded or brazed) to the tube, an O-ring that fits into a groove machined into the end face of the flange, and two mating clamp halves with appropriate bolts to connect the split-flange assembly to a mating surface. The clamp halves do not actually contact the mating surfaces. A critical operation during assembly of a split-flange fitting to its mating surface is to make sure that the four fastening bolts are tightened gradually and evenly in a cross pattern. CLAMPS: A variety of clamping solutions for hose and tube are available, with either a profiled or smooth inner surface in a wide range of sizes. All necessary components can be supplied according to the specific application including, Clamp jaws, Bolts, Stacking bolts, Weld plates, Top plates, Rail. Our hydraulic and pneumatic clamps enable a more efficient installation, resulting in a clean pipe layout, with effective vibration and noise reduction. AGS-TECH hydraulic and pneumatic clamping products ensure repeatability of clamping and consistent clamping forces to avoid part movement and tool breakage. We stock a wide variety of clamping components (inch and metric-based), precision 7 MPa (70 bar) hydraulic clamping systems and professional-grade pneumatic work-holding devices. Our hydraulic clamping products are rated up to 5,000 psi operating pressure that can securely clamp parts in many applications ranging from automotive to welding, and from consumer to industrial markets. Our selection of pneumatic clamping systems provide air-operated holding for high-production environments and applications that require consistent clamping forces. Pneumatic clamps are used for holding and fixturing in assembly, machining, plastics manufacturing, automation and welding applications. We can help you determine work-holding solutions based on your part size, amount of clamp forces needed and other factors. As the World’s most diverse custom manufacturer, outsourcing partner and engineering integrator, we can design and manufacture custom pneumatic and hydraulic clamps for you. ADAPTERS: AGS-TECH offers adapters that provide leak free solutions. Adapters include hydraulic, pneumatic & instrumentation. Our adapters are manufactured to meet or exceed the industrial standards requirements of SAE, ISO, DIN, DOT and JIS. A wide range of adapter styles are available including: Swivel Adapters, Steel and Stainless Steel Pipe Adapters and Industrial Fittings, Brass Pipe Adapters, Brass and Plastic Industrial Fittings, High Purity and Process Adapters, Angled Flare Adapters. QUICK COUPLINGS: We offer quick connect / disconnect couplings for hydraulic, pneumatic and medical applications. Quick disconnect couplings are used to connect and disconnect hydraulic or pneumatic lines quickly and easily without using any tools. Various models are available: Non spill and double-shut-off quick couplings, Connect under pressure quick couplings, Thermoplastic quick couplings, Test port quick couplings, agricultural quick couplings,….and more. SEALS: Hydraulic and pneumatic seals are designed for the reciprocating motion which is common in hydraulic and pneumatic applications, such as cylinders. Hydraulic and pneumatic seals include Piston seals, Rod seals, U-cups, Vee, Cup, W, Piston, Flange packings. Hydraulic seals are designed for high-pressure dynamic applications such as hydraulic cylinders. Pneumatic seals are used in pneumatic cylinders and valves and are usually designed for lower operating pressures compared to hydraulic seals. Pneumatic applications demand however higher operating speeds and lower friction seals compared to hydraulic applications. Seals may be used for rotary and reciprocating motion. Some hydraulic seals and pneumatic seals are composite and are two-or multi-part manufactured as an integral unit. A typical composite seal consists of an integral PTFE ring and an elastomer ring, providing the properties of an elastomeric ring with a rigid, low friction (PTFE) working face. Our seals can have a variety of different cross sections. Common sealing orientation and directions for hydraulic and pneumatic seals include 1.) Rod Seals which are radial seals. The seal is press-fit into a housing bore with the sealing lip contacting the shaft. Also referred to as a shaft seal. 2.) Piston seals which are radial seals. The seal is fit onto a shaft with the sealing lip contacting the housing bore. V-rings are considered external lip seals, 3.) Symmetric seals are symmetrical and work equally well as a rod or piston seal, 4.) An axial seal seals axially against a housing or machine component. Sealing direction is relevant to hydraulic and pneumatic seals used in applications with axial motion, such as cylinders and pistons. The action can be single or double. Single acting, or unidirectional seals, offer an effective seal in one axial direction only, whereas double acting, or bi-directional seals, are effective when sealing in both directions. In order to seal in both directions for a reciprocating motion, more than one seal must be used. Features for hydraulic and pneumatic seals include spring loaded, integral wiper, and split seal. Some important dimensions to consider when you specify hydraulic and pneumatic seals are: • Shaft outer diameter or seal inner diameter • Housing bore diameter or seal outer diameter • Axial cross section or thickness • Radial cross section Important service limit parameters to consider when purchasing seals are: • Maximum operating speed • Maximum operating pressure • Vacuum rating • Operation temperature Popular material choices for rubber sealing elements for hydraulics and pneumatics include: • Ethylene Acrylic • EDPM Rubber • Fluoroelastomer and Fluorosilicone • Nitrile • Nylon or Polyamide • Polychloroprene • Polyoxymethylene • Polytetrafluoroethylene (PTFE) • Polyurethane / Urethane • Natural Rubber Some seal material choices are: • Sintered Bronze • Stainless Steel • Cast Iron • Felt • Leather Standards related to seals are: BS 6241 - Specifications for dimensions of housing for hydraulic seals incorporating bearing rings for reciprocating applications ISO 7632 - Road vehicles - elastomeric seals GOST 14896 - Rubber U-packing seals for hydraulic devices You can download relevant product brochures from the links below: Pneumatic Fittings Pneumatic Air Tubing Connectors Adapters Couplings Splitters and Accessories Private Label Pneumatic Compressed Air Hoses Fittings (We private label these with your brand name and logo if you wish) Private Label Pneumatic Quick Couplings, Plugs and Nipples (We private label these with your brand name and logo if you wish) Information on our facility producing ceramic to metal fittings, hermetic sealing, vacuum feedthroughs, high and ultrahigh vacuum and fluid control components can be found here: Fluid Control Factory Brochure CLICK Product Finder-Locator Service RÛPERA BERÊ
- Specialty Cutting Tools , USA , AGS-TECH Inc.
We offer specialty cutting tools to cut and process special and extraordinary materials and products. They include honing tools, hone, hones, precision dicing tools for cutting semiconductors, glass and more. Amûrên Cutting Specialty Please click on the Specialty Cutting Tools of interest below to download the relevant brochure. Honing Tools, Hone, Hones Precision Dicing Tools for Semiconductors, Glass and More Private Label Abrasives (We can put your company name, logo, brand on these. In other words we offer you private label) Private Label Abrasives Ordering Instructions Guide Private Label Hand Tools for Every Industry This catalog contains some specialty cutting tools. We can private label these hand tools if you wish. In other words, we can put your company name, brand and label on them. This way you can promote your brand by reselling these to your customers. Private Label Power Tool Accessories - Drill Bits - Cutting Grinding Polishing Disks - Hole Saws - Jig Saw Blades....etc. We can private label these hand tools if you wish. In other words, we can put your company name, brand and label on them. This way you can promote your brand by reselling these to your customers. Private Label Power Tools for Every Industry This catalog contains some specialty cutting tools. We can private label these hand tools if you wish. In other words, we can put your company name, brand and label on them. This way you can promote your brand by reselling these to your customers. Private Label Taps - Cutting Tools (We can private label these drill bits with your company name and logo) Prices depend on model and quantity of order. Besides the off-the-shelf products in our brochures above, we do manufacture and supply custom specialty cutting tools. In other words, if you have a design and blueprint, send it to us and we can manufacture them according to your design. Since we carry a wide variety of specialty cutting and shaping tools with different dimensions, applications and material; it is impossible to list them here. We encourage you to get in touch with us so we can determine which product is the best fit for you. When contacting us, please inform us about: - Your application - Material grade - Dimensions - Finishing requirements - Packaging requirements - Labeling requirements - Quantity requested per order & per year VIRÊ bikirtînin da ku kapasîteyên me yên teknîkî û rêbernameya referansê dakêşin ji bo birîna taybetmendî, sondajê, rijandin, çêkirin, şikilandin, pîvazkirina amûrên ku di bijîjkî, diranan, amûrên rast, mêtina metal, çêkirina mirinê û sepanên din ên pîşesaziyê de têne bikar anîn. CLICK Product Finder-Locator Service Li vir bikirtînin da ku biçin Menuya Amûrên Birîn, Xalkirin, Xirkirin, Lapkirin, Paqijkirin, Diçandin û Teşekirin. Ref. Kod: oicaszhengzhouhongtuo, oicaslzqtool
- Gears and Gear Drives, Gear Assembly, Spur Gears, Rack & Pinion
Gears and Gear Drives, Gear Assembly, Spur Gears, Rack & Pinion & Bevel Gears, Miter, Worms, Machine Elements Manufacturing at AGS-TECH Inc. Gears & Gear Drive Meclîsa AGS-TECH Inc. offers you power transmission components including GEARS & GEAR DRIVES. Gears transmit motion, rotating or reciprocating, from one machine part to another. Where necessary, gears reduce or increase the revolutions of the shafts. Basically gears are rolling cylindrical or conic-shaped components with teeth on their contact surfaces to ensure positive motion. Please note that gears are the most durable and rugged of all mechanical drives. Most heavy-duty machine drives and automobiles, transportation vehicles preferably use gears rather than belts or chains. We have many kinds of gears. - SPUR GEARS: These gears connect parallel shafts. Spur gear proportions and teeth shape are standardized. Gear drives need to be operated under a variety of conditions and therefore it is very difficult to determine the best gear set for a particular application. The easiest is to select from stocked standard gears with an adequate load rating. Approximate power ratings for spur gears of various sizes (number of teeth) at several operating speeds (revolutions/minute) are available in our catalogs. For gears with sizes and speeds not listed, ratings can be estimated from values shown on special tables and graphs. Service class and factor for spur gears is also a factor in the selection process. - RACK GEARS: These gears convert spur gears motion to reciprocating or linear motion. A rack gear is a straight bar with teeth that engage the teeth on a spur gear. The specifications for the teeth of the rack gear are given in the same manner as for spur gears, because rack gears can be imagined as spur gears having an infinite pitch diameter. Basically, all circular dimensions of spur gears become linear fir rack gears. - BEVEL GEARS (MITER GEARS and else): These gears connect shafts whose axes intersect. The axes of bevel gears may intersect at an angle, but the most common angle is 90 degrees. The teeth of bevel gears are the same shape as spur gear teeth, but taper toward the cone apex. Miter gears are bevel gears having the same diametral pitch or module, pressure angle and number of teeth. - WORMS and WORM GEARS: These gears connect shafts whose axes do not intersect. Worm gears are used to transmit power between two shafts that are at right angles to each other and are nonintersecting. Teeth on the worm gear are curved to conform with the teeth on the worm. The lead angle on worms should be between 25 and 45 degrees to be efficient in power transmission. Multi-thread worms with one to eight threads are used. - PINION GEARS: The smaller of the two gears is called pinion gear. Often a gear and pinion are made of different materials for better efficiency and durability. The pinion gear is made of a stronger material because the teeth on the pinion gear come into contact more times than the teeth on the other gear. We have standard catalog items as well the capability to manufacture gears according to your request and specifications. We also offer gear design, assembly and manufacturing. Gear design is very complicated because designers need to be dealing with problems such as strength, wear and material selection. The majority of our gears are made of cast iron, steel, brass, bronze or plastic. We have five levels of tutorial for gears, please read them in the given order. If you are not familiar with gears and gear drives, these tutorials below will help you in designing your product. If you prefer, we can also assist you in choosing the right gears for your design. Click on highlighted text below to download the relevant product catalog: - Introductory guide for gears - Basic guide for gears - Guide for practical use of gears - Introduction to gears - Technical reference guide for gears To help you compare applicable standards related to gears in different parts of the World, here you can download: Equivalency Tables for Standards of Raw Material and Gear Precision Grade Once more, we would like to repeat that in order to purchase gears from us, you do not need to have a particular part number, size of gear….etc handy. You do not need to be an expert in gears and gear drives. All you need is really to provide us as much information as possible regarding your application, dimensional limitations where the gears need to be installed, maybe photos of your system…and we will help you. We use computer software packages for the integrated design and manufacture of generalized gear pairs. These gear pairs include cylindrical, bevel, skew-axis, worm and worm wheel, along with non-circular gear pairs. The software we use is based on mathematical relations that differ from established standards and practice. This enables the following features: • any face width • any gear ratio (linear & nonlinear) • any number of teeth • any spiral angle • any shaft center distance • any shaft angle • any tooth profile. These mathematical relations seamlessly encompass different gear types to design and manufacture gear pairs. Here are some of our off-shelf gear and gear drive brochures and catalogs. Click on colored text to download: - Gears - Worm Gears - Worms and Gear Racks - Slewing Drives - Slewing Rings (some have internal or external gears) - Worm Gear Speed Reducers - WP Model - Worm Gear Speed Reducers - NMRV Model - T-Type Spiral Bevel Gear Redirector - Worm Gear Screw Jacks Reference Code: OICASKHK CLICK Product Finder-Locator Service RÛPERA BERÊ
- Hydraulic Pipe Cutters - Vacuum Lifters - Vacuum Manipulators
Pneumatic Hydraulic & Vacuum Tools, Air Tool, Hydraulic Powered Tools, Air Screwdrivers, Air Drills, Pneumatic Nail Guns, Air Die Grinders,Hydraulic Pipe Cutter Amûrên ji bo Hîdraulîk & Pneumatîk & Vacuum We also supply widely used industrial tools for pneumatic, hydraulic and vacuum systems. PNEUMATIC TOOLS (also called AIR TOOLS or AIR-POWERED TOOLS or PNEUMATIC-POWERED TOOLS are types of power tools driven by compressed air, supplied by air compressors. Pneumatic tools can also be driven by compressed carbon dioxide (CO2) stored in small cylinders allowing portability and use where no compressed air lines are available. Pneumatic tools are safer to run and easier to maintain than electric power tool equivalents. Pneumatic tools also have a higher power-to-weight ratio, allowing a smaller, lighter tool to accomplish the same task. General grade pneumatic tools with short life span are generally less expensive. Both disposable as well as industrial grade pneumatic tools with long life span are available. Generally speaking, pneumatic tools are cheaper than the equivalent electric-powered tools. Air tools are becoming more and more popular in the DIY (Do it yourself) market. HYDRAULIC-POWERED TOOLS on the other hand are generally more powerful tools used for applications that require higher pressures and forces. Liquids are much much less compressible than gases and that is the reason why hydraulic powered tools are able to supply such large forces. INDUSTRIAL VACUUM TOOLS offered are mostly manipulators, grippers, holders, lifters used in handling, moving, removing parts and components in industrial settings. Vacuum is also used in packaging to remove air from inside packages to extend the shelf life of products and protect them from moisture, air and early corrosion and decay. We supply both off-shelf and custom manufactured pneumatic, hydraulic and vacuum tools. Here is a list of some common tools: AIR SCREWDRIVERS, ROUTERS AIR RATCHET AIR & HYDRAULIC DRILLS PNEUMATIC NAIL GUN AIR & HYDRAULIC HAMMERS RIVETER & RIVETING HAMMER AIR GUNS and NOZZLES SANDBLASTER AIRBRUSH PAINT SPRAYER AIR CAULK GUNS AIR DIE GRINDERS AIR SANDER AIR BEVELERS AIR CUT-OFF TOOLS SWIVEL CONNECTORS AIR KNIVES PNEUMATIC SLIDES AIR CANNONS AIR AMPLIFIERS AIR CONVEYORS HYDRAULIC & PNEUMATIC TORQUE WRENCH HYDRAULIC PRESSES HYDRAULIC PIPE CUTTERS HYDRAULIC PULLER HYDRAULIC BOLTING TOOLS HYDRAULIC WORKHOLDING DEVICES VACUUM MANIPULATORS and GRIPPERS VACUUM LIFTERS VACUUM PACKAGING TOOLS CUSTOM SPECIALTY TOOLS Click links below to download our relevant brochures: - Air Tool Kits - Air Tools Accessories and Special Industrial Pneumatic Tools - Air Nailers and Staplers - Air Spray Guns - Air Brushes - Air Guns, Hoses, Connectors, Splitters and Accessories - DIY Air Tools - DIY Air Tools Assortment & Wet Air Tools - Oil-Less Mini Air Compressors - Private Label Pneumatic Air Blow Guns (We can put your company name, brand, logo, label on these if you wish) - Private Label Pneumatic Compressed Air Tools (We can put your company name, brand, logo, label on these if you wish) - Professional Air Tools Part-1 - Professional Air Tools Part-2 - Professional Air Tools Part-3 - Professional Air Tools Assortment CLICK Product Finder-Locator Service RÛPERA BERÊ
- Mechanical Seals, Induction Cap Sealing, Adhesive Sealant, Bung
Mechanical Seals, Induction Cap Sealing, Adhesive Sealant, Bung - Diaphragm Ferrofluidic Seal, Flange Gasket, O-Ring - Piston Ring, Hydrostatic, Labyrint Seal Çêkirina Mohrên Mekanîkî A MECHANICAL SEAL is a device which helps join systems or mechanisms together by preventing leakage, containing pressure, or excluding contamination. Mechanical seals can vary in their construction from a simple-O-Ring to complicated assembled structures containing lubricants inside labyrinth shaped canals and self-aligning functionality. Many types of mechanical seals are available. Some of our mechanical seals are available from stock and can be ordered by catalog part number, and on the other hand custom manufacturing option of mechanical seals is available for our customers. So we can design and manufacture mechanical seals specially for your application. The effectiveness of a seal is dependent on adhesion in the case of sealants and compression in the case of gaskets. Major MECHANICAL SEAL TYPES we offer are: Induction sealing or cap sealing, Adhesive sealant, Bridgman seal, a piston sealing mechanism that creates a high pressure reservoir from a lower pressure source, Bung, Coating, Compression seal fitting, Diaphragm seal, Ferrofluidic seal, Gasket or Mechanical Packing, Flange gasket, O-ring, V-ring, U-cup, Wedge, Bellows, D-ring, Delta rings, T-rings, Lobed ring, O-ring boss seal, Piston ring, Glass-ceramic-to-metal seals, Hose coupling, various types of hose couplings, Hermetic seal, Hydrostatic seal, Hydrodynamic seal, Labyrinth seal, a seal which creates a tortuous path for the liquid to flow through, Lid (container), Rotating face mechanical seal, Face seal, Plug, Radial shaft seal, Trap (siphon trap), Stuffing Box, Gland Assembly (mechanical packing), Split Mechanical Seal, Wiper seal, Dry gas seal, Exitex seal, Radial seal, Felt radial seal, Radial positive-contact seals, Clearance seals, Split-ring seal, Axial mechanical seal, End face seals, Molded packings, Lip-type and squeeze type packing, Static seals and sealants, Flat nonmetallic gaskets, Metallic gaskets, Exclusion seals (wiper, scraper, axial and boot seals) Our stocked mechanical seals include famous brands including Timken, AGS-TECH as well as other quality brands. Below you can click and download catalogues of some of the most popular seals. Please tell us the catalogue number/model number and the quantity you would like to order and we will offer you the best prices and lead times along with offers for alternative brands similar in quality. We can supply original brand name as well as generic brand name mechanical seals. TIMKEN SEALS: - Download Timken Large Bore Industrial Seal Catalog Small Bore Bonded Seal Catalog - NSC Info Section NSC Manufacturers NSC Numeric & Metric NSC Numerical Lists NSC Oil Seals 410027- 9Y9895 NSC O Rings Oil Seals up to 410005 NSC Size Section MATERIALS USED IN MECHANICAL SEALS: All our mechanical seals are assembled from the finest materials. The type of lubricant and the mean operating temperature generally govern the choice of elastomer to be used for the mechanical seal compound. Nitrile rubber compounds are among the most widely used sealing materials because temperatures seldom exceed 220 F (105 C). Nitrile rubber has good wear characteristics, easy to mold and inexpensive sealing materials used in seals. For some seals special oil resistant silicone compounds are preferred. For high end applications fluoroelastomer compounds such as Viton are used in seals because they have a long life at very high temperatures in almost any lubricant. Seals incorporating fluoroelastomers are higher in cost however. At low temperatures fluoroelastomers get stiff but not brittle. CLICK Product Finder-Locator Service RÛPERA BERÊ
- Fasteners and Rigging Hardware Manufacturing , USA , AGS-TECH Inc.
AGS-TECH, Inc. is a global manufacturer of fasteners and rigging hardware including shackles, eye bolt and nut, turnbuckles, wire rope clip, hooks, load binder, steel and synthetic plastic wires, cables and ropes, traditional ropes from manila, polyhemp, sisal, cotton, link chains, steel chain and more. Fasteners, Rigging Hardware Manufacturing For information on our manufacturing capabilities of fasteners, you may visit our dedicated page by clicking here: Go to Fasteners Page However, if you are looking for Rigging Hardware, then continue reading and scroll down this page please. Rigging Hardware Rigging hardware is an essential component in any hoisting, lifting, fastening system involving ropes, belts, chains...etc. The quality, strength, durability, lifetime and overall reliability of rigging hardware can be a bottleneck, a limiting factor if the right product of high quality is not chosen for your systems, no matter how good the other components are. You can think of it like a chain, where a single damaged chain link can potentially cause failure of the entire chain. Our rigging hardware products include many items such as cable gliders, clevises, fittings, hooks, shackles, snap hooks, connecting links, swivels, grab links, wire rope clips and much more. Prices of fasteners and rigging hardware components depend on product, model and quantity of your order. It also depends on whether you need an off-the-shelf product or need us to custom manufacture the fasteners and rigging hardware components to your specifications, drawings and needs. Since we carry a wide variety of fasteners and rigging hardware with different dimensions, applications, material grade and coating; in case you can't find a suitable product below in one of our catalogs, we encourage you to email or call us so we can determine which product is the best fit for you. When contacting us, please make sure to provide us some of the following key information: - Application for the fasteners or rigging hardware product - Material grade needed for your fasteners & rigging hardware components - Dimensions - Finish - Packaging requirements - Labeling requirements - Quantity per order / Yearly demand Please download our relevant product brochures by clicking on the colored links below: Standard Rigging Hardware - Shackles Standard Rigging Hardware - Eye Bolt and Nut Standard Rigging Hardware - Turnbuckles Standard Rigging Hardware - Wire Rope Clip Standard Rigging Hardware - Hooks Standard Rigging Hardware - Load Binder Standard Rigging Hardware - New Products Standard Rigging Hardware - Stainless Steel Standard Rigging Hardware - Steel Wires - Steel Wire Ropes and Cables Standard Rigging Hardware - Synthetic Plastic Ropes Standard Rigging Hardware - Traditional-Ropes-Manila-Polyhemp-Sisal-Cotton LINK CHAINS have torus shaped links. They are used in bicycle locks, as locking chains, sometimes as pulling & hoisting chains and similar applications. Here is our downloadable product brochure for off-the-shelf link chains: Link Chains - Steel Chains - International Chains - Stainless Steel Chains and Accessories CLICK Product Finder-Locator Service RÛPERA BERÊ
- Photochemical Machining, PCM, Photo Etching, Chemical Milling,Blankin
Photochemical Machining - PCM - Photo Etching - Chemical Milling - Blanking - Wet Etching - CM - Sheet Metal Components Machining Kîmyewî & Blanking Photochemical CHEMICAL MACHINING (CM) technique is based on the fact that some chemicals attack metals and etch them. This results in removal of small layers of material from surfaces. We use reagents and etchants such as acids and alkaline solutions to remove material from surfaces. The hardness of the material is not a factor for etching. AGS-TECH Inc. frequently uses chemical machining for engraving metals, manufacturing printed-circuit boards and deburring of produced parts. Chemical machining is well suited for shallow removal up to 12 mm on large flat or curved surfaces, and CHEMICAL BLANKING of thin sheets. The chemical machining (CM) method involves low tooling and equipment costs and is advantageous over other ADVANCED MACHINING PROCESSES for low production runs. Typical material removal rates or cutting speeds in chemical machining are around 0.025 – 0.1 mm/min. Using CHEMICAL MILLING, we produce shallow cavities on sheets, plates, forgings and extrusions, either to meet design requirements or for reduction of weight in parts. The chemical milling technique can be used on a variety of metals. In our manufacturing processes, we deploy removable layers of maskants to control the selective attack by the chemical reagent on different areas of the workpiece surfaces. In microelectronic industry the chemical milling is widely used to fabricate miniature devices on chips and the technique is referred to as WET ETCHING. Some surface damage may result from chemical milling due to preferential etching and intergranular attack by the chemicals involved. This may result in deterioration of surfaces and roughening. One has to be careful prior to deciding to use chemical milling on metal castings, welded and brazed structures because uneven material removal may occur because the filler metal or the structural material may machine preferentially. In metal castings uneven surfaces may be obtained due to porosity and non-uniformity of the structure. CHEMICAL BLANKING: We use this method to produce features that penetrate through the thickness of the material, having the material removed by chemical dissolution. This method is an alternative to stamping technique we use in sheet metal manufacturing. Also in burr-free etching of printed-circuit boards (PCB) we deploy chemical blanking. PHOTOCHEMICAL BLANKING & PHOTOCHEMICAL MACHINING (PCM): Photochemical blanking is also known as PHOTOETCHING or PHOTO ETCHING, and is a modified version of chemical milling. Material is removed from flat thin sheets using photographic techniques and complex burr-free, stress-free shapes are blanked. Using photochemical blanking we manufacture fine and thin metal screens, printed-circuit cards, electric-motor laminations, flat precision springs. The photochemical blanking technique offers us the advantage of producing small parts, fragile parts without the need to manufacture difficult and expensive blanking dies that are used in traditional sheet metal manufacturing. Photochemical blanking does require skilled personnel, but the tooling costs are low, the process is easily automated and feasibility is high for medium to high volume production. Some disadvantages exist as is the case in every manufacturing process: Environmental concerns due to chemicals and safety concerns due to volatile liquids being used. Photochemical machining also known as PHOTOCHEMICAL MILLING, is the process of fabricating sheet metal components using a photoresist and etchants to corrosively machine away selected areas. Using photo etching we produce highly complex parts with fine details economically. The photochemical milling process is for us an economical alternative to stamping, punching, laser and water jet cutting for thin gauge precision parts. The photochemical milling process is useful for prototyping and allows for easy and quick changes when there is a change in design. It is an ideal technique for research & development. Phototooling is fast and inexpensive to produce. Most phototools cost less than $ 500 and can be produced within two days. Dimensional tolerances are well met with no burrs, no stress and sharp edges. We can start manufacturing a part within hours after receiving your drawing. We can use PCM on most commercially available metals and alloys such as include aluminium, brass, beryllium-copper, copper, molybdenum, inconel, manganese, nickel, silver, steel, stainless steel, zinc and titanium with thicknesses of 0.0005 to 0.080 in (0.013 to 2.0 mm). Phototools are exposed only to light and therefore do not wear out. Due to the cost of hard tooling for stamping and fine blanking, significant volume is required to justify the expense, which is not the case in PCM. We start the PCM process by printing the shape of the part onto optically clear and dimensionally stable photographic film. The phototool consists of two sheets of this film showing negative images of the parts meaning that the area that will become the parts is clear and all of the areas to be etched are black. We register the two sheets optically and mechanically to form the top and bottom halves of the tool. We cut the metal sheets to size, clean and then laminate on both sides with a UV-sensitive photoresist. We place the coated metal between the two sheets of the phototool and a vacuum is drawn to ensure intimate contact between the phototools and the metal plate. We then expose the plate to UV light that allows the areas of resist that are in the clear sections of the film to be hardened. After exposure we wash away the unexposed resist of the plate, leaving the areas to be etched unprotected. Our etching lines have driven-wheel conveyors to move the plates and arrays of spray nozzles above and below the plates. The etchant is typically an aqueous solution of acid such as ferric chloride, that is heated and directed under pressure to both sides of the plate. The etchant reacts with the unprotected metal and corrodes it away. After neutralizing and rinsing, we remove the remaining resist and the sheet of parts is cleaned and dried. Applications of photochemical machining include fine screens and meshes, apertures, masks, battery grids, sensors, springs, pressure membranes, flexible heating elements, RF and microwave circuits and components, semiconductor leadframes, motor and transformer laminations, metal gaskets and seals, shields and retainers, electrical contacts, EMI/RFI shields, washers. Some parts, such as semiconductor leadframes, are very complex and fragile that, despite volumes in the millions of pieces, they can only be produced by photo etching. The accuracy achievable with the chemical etching process offers us tolerances starting at +/-0.010mm depending on the material type and thickness. Features can be positioned with accuracies around +-5 microns. In PCM, the most economical way is to plan the largest sheet size possible consistent with the size and dimensional tolerances of the part. The more parts per sheet are produced the lower the unit labor cost per part. Material thickness affects costs and is proportional to the length of time to etch through. Most alloys etch at rates between 0.0005–0.001 in (0.013–0.025 mm) of depth per minute per side. In general, for steel, copper or aluminum workpieces with thicknesses up to 0.020 in (0.51 mm), part costs will be roughly $0.15–0.20 per square inch. As the geometry of the part becomes more complex, photochemical machining gains greater economic advantage over sequential processes such as CNC punching, laser or water-jet cutting, and electrical discharge machining. Contact us today with your project and let us provide you our ideas and suggestions. CLICK Product Finder-Locator Service RÛPERA BERÊ