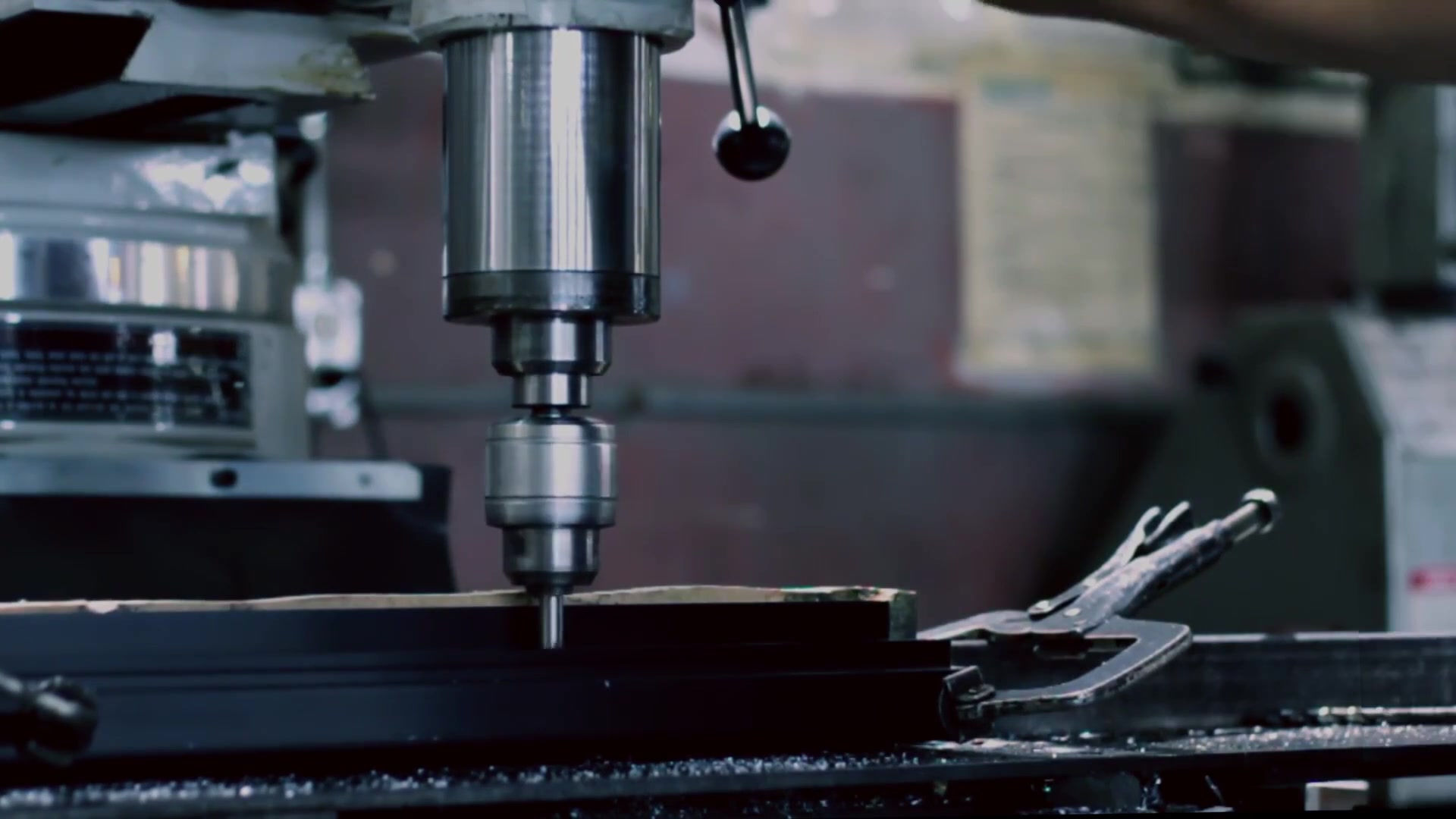
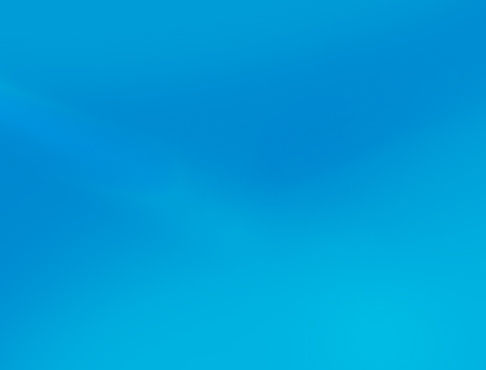
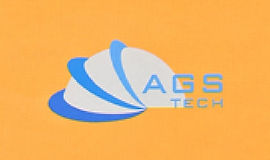
Глобален прилагоден производител, интегратор, консолидатор, партнер за аутсорсинг за широк спектар на производи и услуги.
Ние сме ваш единствен извор за производство, изработка, инженерство, консолидација, интеграција, аутсорсинг на нарачано произведени и производи и услуги кои не се на полица. Ние, исто така, приватна етикета / бела етикета на вашите производи со името на вашиот бренд ако сакате.
Изберете го вашиот јазик
Прилагодено производство на делови, компоненти, склопови, готови производи, машини и индустриска опрема
Домашно и глобално договорно производство
Производство Аутсорсинг
Домашни, глобални набавки на индустриски производи
Приватно означување / Бело означување на вашите производи со вашето име на бренд
Услуги за пронаоѓање и лоцирање производи
Глобален дизајн и партнерство за канали
Инженерска интеграција
Инженерски услуги
Глобална консолидација, складирање, логистика
Search Results
164 results found with an empty search
- Functional Decorative Coatings - Thin Film - Thick Films - AR Coating
Functional & Decorative Coatings, Thin Film, Thick Films, Antireflective and Reflective Mirror Coating - AGS-TECH Inc. Функционални облоги / Декоративни премази / Тенок филм / Дебел филм A COATING is a covering that is applied to the surface of an object. Coatings can be in the form of THIN FILM (less than 1 micron thick) or THICK FILM (over 1 micron thick). Based on the purpose of applying the coating we can offer you DECORATIVE COATINGS and/or FUNCTIONAL COATINGS, or both. Sometimes we apply functional coatings to change the surface properties of the substrate, such as adhesion, wettability, corrosion resistance, or wear resistance. In some other cases such as in semiconductor device fabrication, we apply the functional coatings to add a completely new property such as magnetization or electrical conductivity which become an essential part of the finished product. Our most popular FUNCTIONAL COATINGS are: Adhesive Coatings: Examples are adhesive tape, iron-on fabric. Other functional adhesive coatings are applied to change the adhesion properties, such as non-stick PTFE coated cooking pans, primers that encourage subsequent coatings to adhere well. Tribological Coatings: These functional coatings relate to the principles of friction, lubrication and wear. Any product where one material slides or rubs over another is affected by complex tribological interactions. Products like hip implants and other artificial prosthesis are lubricated in certain ways whereas other products are unlubricated as in high temperature sliding components where conventional lubricants can not be used. The formation of compacted oxide layers have been proven to protect against wear of such sliding mechanical parts. Tribological functional coatings have huge benefits in industry, minimizing wear of machine elements, minimizing wear and tolerance deviations in manufacturing tools such as dies and moulds, minimizing power requirements and making machinery and equipment more energy efficient. Optical Coatings: Examples are Anti-reflective (AR) coatings, reflective coatings for mirrors, UV- absorbent coatings for protection of eyes or for increasing the life of the substrate, tinting used in some colored lighting, tinted glazing and sunglasses. Catalytic Coatings such as applied on self-cleaning glass. Light-Sensitive Coatings used to make products such as photographic films Protective Coatings: Paints can be considered protecting the products besides being decorative in purpose. Hard anti-scratch coatings on plastics and other materials are one of our most widely used functional coatings to reduce scratching, improve wear resistance, …etc. Anti-corrosion coatings such as plating are also very popular. Other protective functional coatings are put on waterproof fabric and paper, antimicrobial surface coatings on surgical tools and implants. Hydrophilic / Hydrophobic Coatings: Wetting (hydrophilic) and unwetting (hydrophobic) functional thin and thick films are important in applications where water absorption is either desired or undesired. Using advanced technology we can alter your product surfaces, to make them either easily wettable or unwettable. Typical applications are in textiles, dressings, leather boots, pharmaceutical or surgical products. Hydrophilic nature refers to a physical property of a molecule that can transiently bond with water (H2O) through hydrogen bonding. This is thermodynamically favorable, and makes these molecules soluble not only in water, but also in other polar solvents. Hydrophilic and hydrophobic molecules are also known as polar molecules and nonpolar molecules, respectively. Magnetic Coatings: These functional coatings add magnetic properties such as is the case for magnetic floppy disks, cassettes, magnetic stripes, magnetooptic storage, inductive recording media, magnetoresist sensors, and thin-film heads on products. Magnetic thin films are sheets of magnetic material with thicknesses of a few micrometers or less, used primarily in the electronics industry. Magnetic thin films can be single-crystal, polycrystalline, amorphous, or multilayered functional coatings in the arrangement of their atoms. Both ferro- and ferrimagnetic films are used. The ferromagnetic functional coatings are usually transition-metal-based alloys. For example, permalloy is a nickel-iron alloy. The ferrimagnetic functional coatings, such as garnets or the amorphous films, contain transition metals such as iron or cobalt and rare earths and the ferrimagnetic properties are advantageous in magnetooptic applications where a low overall magnetic moment can be achieved without a significant change in the Curie temperature. Some sensor elements function on the principle of change in electrical properties, such as the electrical resistance, with a magnetic field. In semiconductor technology, the magnetoresist head used in disk storage technology functions with this principle. Very large magnetoresist signals (giant magnetoresistance) are observed in magnetic multilayers and composites containing a magnetic and nonmagnetic material. Electrical or Electronic Coatings: These functional coatings add electrical or electronic properties such as conductivity to manufacture products such as resistors, insulation properties such as in the case of magnet wire coatings used in transformers. DECORATIVE COATINGS: When we speak of decorative coatings the options are only limited by your imagination. Both thick and thin film type coatings have been successfully engineered and applied in the past to our customers products. Regardless of the difficulty in the geometric shape and material of the substrate and application conditions, we are always capable to formulate the chemistry, physical aspects such as exact Pantone code of color and application method for your desired decorative coatings. Complex patterns involving shapes or different colors are also possible. We can make your plastic polymer parts look metallic. We can color anodize extrusions with various patterns and it won’t even look anodized. We can mirror coat an oddly-shaped part. Furthermore decorative coatings can be formulated that will also act as functional coatings at the same time. Any of the below mentioned thin and thick film deposition techniques used for functional coatings can be deployed for decorative coatings. Here are some of our popular decorative coatings: - PVD Thin Film Decorative Coatings - Electroplated Decorative Coatings - CVD and PECVD Thin Film Decorative Coatings - Thermal Evaporation Decorative Coatings - Roll-to-Roll Decorative Coating - E-Beam Oxide Interference Decorative Coatings - Ion Plating - Cathodic Arc Evaporation for Decorative Coatings - PVD + Photolithography, Heavy Gold Plating on PVD - Aerosol Coatings for Glass Coloring - Anti-tarnish Coating - Decorative Copper-Nickel-Chrome Systems - Decorative Powder Coating - Decorative Painting, Custom Tailored Paint Formulations using Pigments, Fillers, Colloidal Silica Dispersant...etc. If you contact us with your requirements for decorative coatings, we can provide you our expert opinion. We have advanced tools such as color readers, color comparators….etc. to guarantee consistent quality of your coatings. THIN and THICK FILM COATING PROCESSES: Here are the most widely used of our techniques. Electro-Plating / Chemical Plating (hard chromium, chemical nickel) Electroplating is the process of plating one metal onto another by hydrolysis, for decorative purposes, corrosion prevention of a metal or other purposes. Electroplating lets us use inexpensive metals such as steel or zinc or plastics for the bulk of the product and then apply different metals on the outside in the form of a film for better appearance, protection, and for other properties desired for the product. Electroless plating, also known as chemical plating, is a non-galvanic plating method that involves several simultaneous reactions in an aqueous solution, which occur without the use of external electrical power. The reaction is accomplished when hydrogen is released by a reducing agent and oxidized, thus producing a negative charge on the surface of the part. Advantages of these thin and thick films are good corrosion resistance, low processing temperature, possibility to deposit in bore holes, slots… etc. Disadvantages are the limited selection of coating materials, relatively soft nature of the coatings, environmentally polluting treatment baths that are needed including chemicals such as cyanide, heavy metals, fluorides, oils, limited accuracy of surface replication. Diffusion Processes (Nitriding, nitrocarburization, boronizing, phosphating, etc.) In heat treatment furnaces, the diffused elements usually originate from gases reacting at high temperatures with the metal surfaces. This can be a pure thermal and chemical reaction as a consequence of the thermal dissociation of the gases. In some cases, diffused elements originate from solids. The advantages of these thermochemical coating processes are good corrosion resistance, good reproducibility. The disadvantages of these are being relatively soft coatings, limited selection of base material (which must be suitable for nitriding), long processing times, environmental and health hazards involved, requirement of post-treatment. CVD (Chemical Vapor Deposition) CVD is a chemical process used to produce high quality, high-performance, solid coatings. The process produces thin films too. In a typical CVD, the substrates are exposed to one or more volatile precursors, that react and/or decompose on the substrate surface to produce the desired thin film. Advantages of these thin & thick films are their high wear resistance, potential to economically produce thicker coatings, suitability for bore holes, slots ….etc. Disadvantages of CVD processes are their high processing temperatures, difficulty or impossibility of coatings with multiple metals (such as TiAlN), rounding of edges, use of environmentally hazardous chemicals. PACVD / PECVD (Plasma-Assisted Chemical Vapor Deposition) PACVD is also called PECVD standing for Plasma Enhanced CVD. Whereas in a PVD coating process the thin & thick film materials are evaporated from a solid form, in PECVD the coating results from a gas phase. Precursor gasses are cracked in the plasma to become available for the coating. Advantages of this thin and thick film deposition technique is that significantly lower process temperatures are possible as compared to CVD, precise coatings are deposited. Disadvantages of PACVD are that it has only limited suitability for bore holes, slots etc. PVD (Physical Vapor Deposition) PVD processes are a variety of purely physical vacuum deposition methods used to deposit thin films by the condensation of a vaporized form of the desired film material onto workpiece surfaces. Sputtering and evaporative coatings are examples of PVD. Advantages are that no environmentally damaging materials and emissions are produced, a large variety of coatings can be produced, coating temperatures are below the final heat treatment temperature of most steels, precisely reproducible thin coatings, high wear resistance, low frictional coefficient. Disadvantages are bore holes, slots ...etc. can only be coated down to a depth equal to the diameter or width of the opening, corrosion resistant only under certain conditions, and for obtaining uniform film thicknesses, parts must be rotated during deposition. The adhesion of functional and decorative coatings are substrate dependent. Furthermore, the lifetime of thin and thick film coatings depends on environmental parameters such as humidity, temperature...etc. Therefore, before considering a functional or decorative coating, contact us for our opinion. We can choose the most suitable coating materials and coating technique that fits your substrates and application and deposit them under the strictest quality standards. Contact AGS-TECH Inc. for details of thin and thick film deposition capabilities. Do you need design assistance ? Do you need prototypes ? Do you need mass manufacturing ? We are here to help you. Click on blue colored text below to download product catalogs and brochures: - Private Label Nano Surface Protection Car Care Products We can label these products with your name and logo if you wish - Private Label Nano Surface Industrial Products We can label these products with your name and logo if you wish - Private Label Nano Surface Protection Marine Products We can label these products with your name and logo if you wish - Private Label Nano Surface Protection Products We can label these products with your name and logo if you wish КЛИКНЕТЕ Услуга за пронаоѓање на производи-локатор ПРЕТХОДНА СТРАНИЦА
- Adhesive Bonding - Adhesives - Sealing - Fastening - Joining
Adhesive Bonding - Adhesives - Sealing - Fastening - Joining Nonmetallic Materials - Optical Contacting - UV Bonding - Specialty Glue - Epoxy - Custom Assembly Лепливо врзување и запечатување и прилагодено механичко прицврстување и склопување Among our other most valuable JOINING techniques are ADHESIVE BONDING, MECHANICAL FASTENING and ASSEMBLY, JOINING NONMETALLIC MATERIALS. We dedicate this section to these joining and assembly techniques because of their importance in our manufacturing operations and the extensive content related to them. ADHESIVE BONDING: Did you know that there are specialized epoxies that can be used for almost hermetic level sealing ? Depending on the level of sealing you require, we will choose or formulate a sealant for you. Also do you know that some sealants can be heat cured whereas others require only a UV light to be cured ? If you explain us your application, we can formulate the right epoxy for you. You may require something that is bubble free or something that matches the thermal coefficient of expansion of your mating parts. We have it all ! Contact us and explain your application. We will then choose the most suitable material for you or custom formulate a solution for your challenge. Our materials come with inspection reports, material data sheets and certification. We are capable to assemble your components very economically and ship you completed and quality inspected products. Adhesives are available to us in various forms such as liquids, solutions, pastes, emulsions, powder, tape and films. We use three basic types of adhesives for our joining processes: -Natural Adhesives -Inorganic Adhesives -Synthetic Organic Adhesives For load-bearing applications in manufacturing and fabrication we use adhesives with high cohesive strength, and they are mostly synthetic organic adhesives, which may be thermoplastics or thermosetting polymers. Synthetic organic adhesives are our most important category and can be classified as: Chemically Reactive Adhesives: Popular examples are silicones, polyurethanes, epoxies, phenolics, polyimides, anaerobics like Loctite. Pressure Sensitive Adhesives: Common examples are natural rubber, nitrile rubber, polyacrylates, butyl rubber. Hot Melt Adhesives: Examples are thermoplastics like ethylene-vinyl-acetate copolymers, polyamides, polyester, polyolefins. Reactive Hot Melt Adhesives: They have a thermoset portion based on urethane’s chemistry. Evaporative / Diffusion Adhesives: Popular ones are vinyls, acrylics, phenolics, polyurethanes, synthetic and natural rubbers. Film and Tape Type Adhesives: Examples are nylon-epoxies, elastomer-epoxies, nitrile-phenolics, polyimides. Delayed Tack Adhesives: These include polyvinyl acetates, polystyrenes, polyamides. Electrically and Thermally Conductive Adhesives: Popular examples are epoxies, polyurethanes, silicones, polyimides. According to their chemistries adhesives we use in manufacturing can be classified as: - Epoxy based adhesive systems: High strength and high temperature endurance as high as 473 Kelvin are characteristic of these. Bonding agents in sand mold castings are this type. - Acrylics: These are suitable for applications that involve contaminated dirty surfaces. - Anaerobic adhesive systems: Curing by oxygen deprivation. Hard and brittle bonds. - Cyanoacrylate: Thin bond lines with setting times under 1 minute. - Urethanes: We use them as popular sealants with high toughness and flexibility. - Silicones: Well known for their resistance against moisture and solvents, high impact and peel strength. Relatively long curing times of up to a few days. To optimize the properties in adhesive bonding, we may combine several adhesives. Examples are epoxy-silicon, nitrile-phenolic combined adhesive systems. Polyimides and polybenzimidazoles are used in high-temperature applications. Adhesive joints withstand shear, compressive, and tensile forces pretty well but they may easily fail when subjected to peeling forces. Therefore, in adhesive bonding, we must consider the application and design the joint accordingly. Surface preparation is also of critical importance in adhesive bonding. We clean, treat and modify surfaces to increase the strength and reliability of interfaces in adhesive bonding. Using special primers, wet and dry etching techniques such as plasma cleaning are among our common methods. An adhesion promoting layer such as a thin oxide may improve adhesion in some applications. Increasing surface roughness may also be beneficial prior to adhesive bonding but needs to be well controlled and not exaggerated because excessive roughness can result in trapping of air and therefore a weaker adhesively bonded interface. We use nondestructive methods for testing the quality and strength of our products after adhesive bonding operations. Our techniques include methods such as acoustic impact, IR detection, ultrasonic testing. Advantages of adhesive bonding are: -Adhesive bonding can provide structural strength, sealing and insulation function, suppression of vibration and noise. -Adhesive bonding can eliminate localized stresses at the interface by eliminating the need for joining using fasteners or welding. -Generally no holes are needed for adhesive bonding, and therefore external appearance of components is unaffected. -Thin and fragile parts can be adhesively joined without damage and without significant increase in weight. -Adhesive joining can be used to bond parts made of very different materials with significantly different sizes. -Adhesive bonding can be used on heat sensitive components safely due to low temperatures involved. However some disadvantages do exist for adhesive bonding and our customers should consider these prior to finalizing their designs of joints: -Service temperatures are relatively low for adhesively joint components -Adhesive bonding may require long bonding and curing times. -Surface preparation is needed in adhesive bonding. -Especially for large structures it may be difficult to test adhesively bonded joints nondestructively. -Adhesive bonding may pose reliability concerns in the long term due to degradation, stress corrosion, dissolution….and the like. One of our outstanding products is ELECTRICALLY CONDUCTIVE ADHESIVE, which can replace lead-based solders. Fillers such as silver, aluminum, copper, gold make these pastes conductive. Fillers can be in the form of flakes, particles or polymeric particles coated with thin films of silver or gold. Fillers can also improve thermal conductivity besides electrical. Let us continue with our other joining processes used in manufacturing products. MECHANICAL FASTENING and ASSEMBLY: Mechanical fastening offers us ease of manufacturing, ease of assembly and disassembly, ease of transportation, ease of parts replacement, maintenance and repair, ease in design of movable and adjustable products, lower cost. For fastening we use: Threaded Fasteners: Bolts, screws and nuts are examples of these. Depending on your application, we can provide you specially designed nuts and lock washers for dampening vibration. Riveting: Rivets are among our most common methods of permanent mechanical joining and assembly processes. Rivets are placed in holes and their ends are deformed by upsetting. We perform assembly using riveting at room temperature as well as at high temperatures. Stitching / Stapling / Clinching: These assembly operations are widely used in manufacturing and are basically the same as is used on papers and cardboards. Both metallic and nonmetallic materials can be joined and assembled quickly without need to predrill holes. Seaming: An inexpensive fast joining technique we use widely in manufacturing of containers and metal cans. It is based on folding two thin pieces of material together. Even airtight and watertight seams are possible, especially if seaming is performed jointly with using sealants and adhesives. Crimping: Crimping is a joining method where we do not use fasteners. Electrical or fiber optic connectors are sometimes installed using crimping. In high volume manufacturing, crimping is an indispensible technique for fast joining and assembly of both flat and tubular components. Snap-in Fasteners: Snap fits are also an economical joining technique in assembly and manufacturing. They permit quick assembly and disassembly of components and are a good fit for household products, toys, furniture among others. Shrink and Press Fits: Another mechanical assembly technique, namely shrink fitting is based on the principle of differential thermal expansion and contraction of two components, whereas in press fitting one component is forced over another resulting in good joint strength. We use shrink fitting widely in the assembly and manufacturing of cable harness, and mounting gears and cams on shafts. JOINING NONMETALLIC MATERIALS: Thermoplastics can be heated and melted at the interfaces to be joined and by applying pressure adhesive joining can be accomplished by fusion. Alternatively thermoplastic fillers of the same type may be used for the joining process. Joining of some polymers such as polyethylene may be difficult due to oxidation. In such cases, an inert shielding gas like nitrogen may be used against oxidation. Both external as well as internal heat sources can be used in adhesive joining of polymers. Examples of external sources we commonly use in adhesive joining of thermoplastics are hot air or gases, IR radiation, heated tools, lasers, resistive electrical heating elements. Some of our internal heat sources are ultrasonic welding and friction welding. In some assembly and manufacturing applications we use adhesives for bonding polymers. Some polymers such as PTFE (Teflon) or PE (Polyethylene) have low surface energies and therefore a primer is first applied prior to completing the adhesive bonding process with a suitable adhesive. Another popular technique in joining is the “Clearweld Process” where a toner is first applied to the polymer interfaces. A laser is then directed at the interface, but it does not heat the polymer, but does heat the toner. This makes it possible to heat only well-defined interfaces resulting in localized welds. Other alternative joining techniques in the assembly of thermoplastics are using fasteners, self-tapping screws, integrated snap-fasteners. An exotic technique in manufacturing and assembly operations is embedding tiny micron-sized particles into the polymer and using high-frequency electromagnetic field to inductively heat and melt it at the interfaces to be joined. Thermoset materials on the other hand, do not soften or melt with increasing temperatures. Therefore, adhesive joining of thermoset plastics are usually carried out using threaded or other molded-in inserts, mechanical fasteners and solvent bonding. Regarding joining and assembly operations involving glass and ceramics in our manufacturing plants, here are a few common observations: In cases where a ceramic or glass have to be joined with difficult-to-bond materials, the ceramic or glass materials are frequently coated with a metal that bonds itself easily to them, and then joined to the difficult-to-bond material. When ceramic or glass has a thin metal coating it can be more readily brazed to metals. Ceramics are sometimes joined and assembled together during their shaping process while still hot, soft and tacky. Carbides can be more easily brazed to metals if they have as their matrix material a metal binder such as cobalt or nickel-molybdenum alloy. We braze carbide cutting tools to steel toolholders. Glasses bond well to each other and metals when hot and soft. Information on our facility producing ceramic to metal fittings, hermetic sealing, vacuum feedthroughs, high and ultrahigh vacuum and fluid control components can be found here: Brazing Factory Brochure Private Label Epoxy Solutions for Construction, Electrical, Industrial Assembly (Download brochure by clicking on blue text. We can put your name, label, logo on these epoxies if you wish) КЛИКНЕТЕ Услуга за пронаоѓање на производи-локатор ПРЕТХОДНА СТРАНИЦА
- PCB, PCBA, Printed Circuit Board Assembly, Surface Mount Assembly, SMA
PCB - PCBA - Printed Circuit Board Assembly - Rigid Flexible Multilayer - Surface Mount Assembly - SMA - AGS-TECH Inc. PCB & PCBA Производство и склопување We offer: PCB: Printed Circuit Board PCBA: Printed Circuit Board Assembly • Printed Circuit Board Assemblies of all types (PCB, rigid, flexible and multilayer) • Substrates or complete PCBA assembly depending on your needs. • Thru-Hole and Surface Mount Assembly (SMA) Please send us your Gerber files, BOM, component specifications. We can either assemble your PCBs and PCBA's using your exact components specified, or we can offer you our matching alternatives. We are experienced shipping PCBs and PCBAs and will make sure to package them in antistatic bags to avoid electrostatic damage. PCBs intended for extreme environments often have a conformal coating, which is applied by dipping or spraying after the components have been soldered. The coat prevents corrosion and leakage currents or shorting due to condensation. Our conformal coats are usually dips of dilute solutions of silicone rubber, polyurethane, acrylic, or epoxy. Some are engineering plastics sputtered onto the PCB in a vacuum chamber. Safety Standard UL 796 covers component safety requirements for printed wiring boards for use as components in devices or appliances. Our tests analyze characteristics such as flammability, maximum operating temperature, electrical tracking, heat deflection, and direct support of live electrical parts. The PCB boards may use organic or inorganic base materials in a single or multilayer, rigid or flexible form. Circuitry construction may include etched, die stamped, precut, flush press, additive, and plated conductor techniques. Printed-component parts may be used. The suitability of the pattern parameters, temperature and maximum solder limits shall be determined in accordance with the applicable end-product construction and requirements. Don't wait, call us for more information, design assistance, prototypes and mass production. If you need, we will take care of all the labeling, packaging, shipping, import & customs, storage and delivery. Below you can download our relevant brochures and catalogs for PCB and PCBA assembly: General process capabilities & tolerances for rigid PCB manufacturing General process capabilities & tolerances for aluminum PCB manufacturing General process capabilities & tolerances for flexible and rigid-flexible PCB manufacturing General PCB Fabrication Processes General process summary of Printed Circuit Board Assembly PCBA manufacturing Overview of Printed Circuit Boards Manufacturing Plant Some more brochures of our products we can use in your PCB and PCBA assembly projects: To download our catalog for off-shelf interconnect components & hardware such as quick-fit terminals, USB plugs & sockets, micro pins & jacks and more, please CLICK HERE Terminal Blocks and Connectors Terminal Blocks General Catalogue Standard heat sinks Extruded heat sinks Easy Click heat sinks a perfect product for PCB assemblies Super Power heat sinks for medium - high power electronic systems Heat sinks with Super Fins LCD modules Receptacles-Power Entry-Connectors Catalogue Dowload brochure for our DESIGN PARTNERSHIP PROGRAM If you are interested in our engineering and research & development capabilities instead of manufacturing operations and capabilities, then we invite you to visit our engineering site http://www.ags-engineering.com КЛИКНЕТЕ Услуга за пронаоѓање на производи-локатор ПРЕТХОДНА СТРАНИЦА
- Composite Stereo Microscopes, Metallurgical Microscope, Fiberscope
Composite Stereo Microscopes - Metallurgical Microscope - Fiberscope - Borescope - SADT -AGS-TECH Inc - New Mexico - USA Микроскоп, фиберскоп, борескоп, машини за мерење на видот, проектори за профили We supply MICROSCOPES, FIBERSCOPES, BORESCOPES, VISION MEASURING MACHINES, PROFILE PROJECTORS from manufacturers like SADT, SINOAGE, SINOWON for industrial applications. There are a large number of microscopes based on the physical principle used to produce an image and based on their area of application. The type of instruments we supply are OPTICAL MICROSCOPES (COMPOUND / STEREO TYPES), and METALLURGICAL MICROSCOPES. You can purchase brand new as well as refurbished or used equipment from us. Browse through our catalogs below and let us know the brand and model number and we will provide you our offers: HAIDA Color Assessment Cabinet SADT-SINOAGE Brand Metrology and Test Equipment Catalog In this catalog you will find some high quality metallurgical microscopes and inverted microscopes. SINOWON Instant Vision Measuring System SINOWON Profile Projector SINOWON Toolmakers Microscope SINOWON Vision Measuring Machine SINOWON Video Microscope We offer both FLEXIBLE and RIGID FIBERSCOPE and BORESCOPE models and they are primarily used for NONDESTRUCTIVE TESTING in confined spaces, like crevices in some concrete structures and aircraft engines. Both of these optical instruments are used for visual inspection. There are however differences between fiberscopes and borescopes: One of them is the flexibility aspect. Fiberscopes are made of flexible optic fibers and have a viewing lens attached to their head. The operator can turn the lens after insertion of the fiberscope into a crevice. This increases the operator’s view. To the contrary, borescopes are generally rigid and allow the user to view only straight ahead or at right angles. Another difference is the light source. A fiberscope does transmit light down its optical fibers to illuminate the observation area. On the other hand, a borescope has mirrors and lenses so light can be bounced from between mirrors to illuminate the observation area. Lastly, the clarity is different. Whereas fiberscopes are limited to a range of 6 to 8 inches, borescopes can provide a wider and clearer view as compared to fiberscopes. OPTICAL MICROSCOPES : These optical instruments use visible light (or UV light in the case of fluorescence microscopy) to produce an image. Optical lenses are used to refract the light. The first microscopes that were invented were optical. Optical microscopes can be further subdivided into several categories. We focus our attention to two of them: 1.) COMPOUND MICROSCOPE : These microscopes are composed of two lens systems, an objective and an ocular (eye piece). The maximum useful magnification is about 1000x. 2.) STEREO MICROSCOPE (also known as DISSECTING MICROSCOPE): These microscopes magnify to about maximum 100x and supply a 3D view of the specimen. They are useful for observing opaque objects. METALLURGICAL MICROSCOPES : Our downloadable SADT catalog with the link above does contain metallurgical and inverted metallographic microscopes. So please see our catalog for product details. In order to acquire a basic understanding about these types of microscopes, please go to our page COATING SURFACE TEST INSTRUMENTS. FIBERSCOPES : Fiberscopes incorporate fiber optic bundles, consisting of numerous fiber optic cables. Fiber optic cables are made of optically pure glass and are as thin as a human’s hair. The main components to a fiber optic cable are: Core, which is the center made of high purity glass, cladding which is he outer material surrounding the core that prevents light from leaking and finally buffer which is the protective plastic coating. Generally there are two different fiber optic bundles in a fiberscope: The first one is the illumination bundle which is designed to carry light from the source to the eyepiece and the second one is the imaging bundle designed to carry an image from the lens to the eyepiece. A typical fiberscope is made up of the following components: -Eyepiece: This is the part from where we observe the image. It magnifies the image carried by the imaging bundle for easy viewing. -Imaging Bundle: A strand of flexible glass fibers transmitting the images to the eyepiece. -Distal Lens: A combination of multiple micro lenses that take images and focus them into the small imaging bundle. -Illumination System: A Fiber optic light guide that sends light from the source to the target area (eyepiece) -Articulation System: The system providing the user the ability to control the movement of the bending section of the fiberscope that is directly attached to the distal lens. -Fiberscope Body: The control section designed to help one hand operation. -Insertion Tube: This flexible and durable tube protects the fiber optic bundle and articulation cables. -Bending Section – The most flexible part of the fiberscope connecting the insertion tube to the distal viewing section. -Distal Section: ending location for both the illumination and imaging fiber bundle. BORESCOPES / BOROSCOPES : A borescope is an optical device consisting of a rigid or flexible tube with an eyepiece on one end, and an objective lens on the other end linked together by a light transmitting optical system in between. Optical fibers surrounding the system are generally used for illuminating the object to be viewed. An internal image of the illuminated object is formed by the objective lens, magnified by the eyepiece and presented to the viewer's eye. Many modern borescopes can be fitted with imaging and video devices. Borescopes are used similar to fiberscopes for visual inspection where the area to be inspected is inaccessible by other means. Borescopes are considered nondestructive test instruments for viewing and examining defects and imperfections. The areas of application is only limited by your imagination. The term FLEXIBLE BORESCOPE is sometimes used interchangeably with the term fiberscope. One disadvantage for flexible borescopes originates from pixelation and pixel crosstalk due to the fiber image guide. Image quality varies widely among different models of flexible borescopes depending on the number of fibers and construction used in the fiber image guide. High end borescopes offer a visual grid on image captures that aids in evaluating the size of the area under inspection. For flexible borescopes, articulation mechanism components, range of articulation, field of view and angles of view of the objective lens are also important. Fiber content in the flexible relay is also critical to provide the highest possible resolution. Minimal quantity is 10,000 pixels while the best images are obtained with higher numbers of fibers in the 15,000 to 22,000 pixels range for the larger diameter borescopes. The ability to control the light at the end of the insertion tube allows the user to make adjustments that can significantly improve the clarity of images taken. On the other hand, RIGID BORESCOPES generally provide a superior image and lower cost compared to a flexible borescope. The shortcoming of rigid borescopes is the limitation that access to what is to be viewed must be in a straight line. Therefore, rigid borescopes have a limited area of application. For similar-quality instruments, the largest rigid borescope that will fit the hole gives the best image. A VIDEO BORESCOPE is similar to the flexible borescope but uses a miniature video camera at the end of the flexible tube. The end of the insertion tube includes a light which makes it possible to capture video or still images deep within the area of investigation. The ability of video borescopes to capture video and still images for later inspection is very useful. Viewing position can be changed via a joystick control and displayed on the screen mounted on its handle. Because the complex optical waveguide is replaced with an inexpensive electrical cable, video borescopes can be much less costly and potentially offer better resolution. Some borescopes offer USB cable connection. For details and other similar equipment, please visit our equipment website: http://www.sourceindustrialsupply.com КЛИКНЕТЕ Услуга за пронаоѓање на производи-локатор ПРЕТХОДНА СТРАНИЦА
- Industrial & Specialty & Functional Textiles, Hydrophobic - Hydrophillic Textile Materials, Flame Resistant, Antibasterial, Antifungal, Antistatic Fabrics, Filtering Cloths, Biocompatible Fabric
Industrial & Specialty & Functional Textiles, Hydrophobic - Hydrophillic Textile Materials, Flame Resistant Textiles, Antibasterial, Antifungal, Antistatic, UC Protective Fabrics, Filtering Clothes, Textiles for Surgery, Biocompatible Fabric Индустриски и специјализирани и функционални текстил Of interest to us are only specialty & functional textiles and fabrics and products made thereof that serve a particular application. These are engineering textiles of outstanding value, also sometimes referred to as technical textiles and fabrics. Woven as well as non-woven fabrics and cloths are available for numerous applications. Below is a list of some major types of industrial & specialty & functional textiles that are within our product development and manufacturing scope. We are willing to work with you on designing, developing and manufacturing your products made of: Hydrophobic (water repellant) & hydrophilic (water absorbing) textile materials Textiles and fabrics of extraordinary strength, durability and resistance to severe environmental conditions (such as bulletproof, high heat resistant, low-temperature resistant, flame resistant, inert or resistant against corrosive fluids and gases, resisting mildew formation….) Antibacterial & Antifungal textiles and fabrics UV protective Electrically conductive & non-conductive textiles and fabrics Antistatic fabrics for ESD control….etc. Textiles and fabrics with special optical properties and effects (fluorescent…etc.) Textiles, fabrics and cloths with special filtering capabilities, filter manufacturing Industrial textiles such as duct fabrics, interlinings, reinforcement, transmission belts, reinforcements for rubber (conveyer belts, print blankets, cords), textiles for tapes and abrasives. Textiles for the automotive industry (hoses, belts, airbags, interlinings, tires) Textiles for construction, building and infrastructure products (concrete cloth, geomembranes, and fabric innerduct) Composite multi-functional textiles having different layers or components for different functions. Textiles made by activated carbon infusion on polyester fibers to provide cotton hand feel, odor release, moisture management and UV protection features. Textiles made from shape memory polymers Textiles for surgery and surgical implants, biocompatible fabrics Please note that we engineer, design and manufacture products to your needs and specifications. We can either manufacture products according to your specifications or, If desired, we can help you in choosing the right materials and designing the product. You can click on the blue highlighted text below and download these brochures. We can label these products with your name and logo if you wish: - Private Label Cleanroom Consumables and Apparel - Private Label Nano Surface Protection Car Care Products - Private Label Nano Surface Protection Industrial Products - Private Label Nano Surface Protection Marine Products - Private Label Nano Surface Protection Products ПРЕТХОДНА СТРАНИЦА
- Brazing, Soldering, Welding, Joining Processes, Assembly Services
Brazing - Soldering - Welding - Joining Processes - Assembly Services - Subassemblies - Assemblies - Custom Manufacturing - AGS-TECH Inc. - NM - USA Лемење и лемење и заварување Among the many JOINING techniques we deploy in manufacturing, special emphasis is given to WELDING, BRAZING, SOLDERING, ADHESIVE BONDING and CUSTOM MECHANICAL ASSEMBLY because these techniques are widely used in applications like manufacturing of hermetic assemblies, high-tech product manufacturing and specialized sealing. Here we will concentrate on the more specialized aspects of these joining techniques as they are related to manufacturing of advanced products and assemblies. FUSION WELDING: We use heat to melt and coalesce materials. Heat is supplied by electricity or high-energy beams. The types of fusion welding we deploy are OXYFUEL GAS WELDING, ARC WELDING, HIGH-ENERGY-BEAM WELDING. SOLID-STATE WELDING: We join parts without melting and fusion. Our solid-state welding methods are COLD, ULTRASONIC, RESISTANCE, FRICTION, EXPLOSION WELDING and DIFFUSION BONDING. BRAZING & SOLDERING: They use filler metals and give us the advantage of working at lower temperatures than in welding, thus less structural damage to products. Information on our brazing facility producing ceramic to metal fittings, hermetic sealing, vacuum feedthroughs, high and ultrahigh vacuum and fluid control components can be found here: Brazing Factory Brochure Brazing Machines (We private label these with your brand name and logo if you wish. This way you can promote your brand name when you resell these machines to your customers) ADHESIVE BONDING: Because of the diversity of adhesives used in industry and also diversity of applications, we have a dedicated page for this. To go to our page about adhesive bonding, please click here. CUSTOM MECHANICAL ASSEMBLY: We use a variety of fasteners such as bolts, screws, nuts, rivets. Our fasteners are not limited to standard off-shelf fasteners. We design, develop and manufacture specialty fasteners that are made from nonstandard materials so they can meet requirements for special applications. Sometimes electrical or heat non-conductivity is desired whereas sometimes conductivity. For some special applications, a customer may want special fasteners that cannot be removed without destroying the product. There are endless ideas and applications. We have it all for you, if not off-shelf we can quickly develop it. To go to our page on mechanical assembly, please click here . Let us examine our various joining techniques in more details. OXYFUEL GAS WELDING (OFW): We use a fuel gas mixed with oxygen to produce the welding flame. When we use acetylene as the fuel and oxygen, we call it oxyacetylene gas welding. Two chemical reactions occur in the oxyfuel gas combustion process: C2H2 + O2 ------» 2CO + H2 + Heat 2CO + H2 + 1.5 O2--------» 2 CO2 + H2O + Heat The first reaction dissociates the acetylene into carbon monoxide and hydrogen while producing about 33% of the total heat generated. The second process above represents further combustion of the hydrogen and carbon monoxide while producing about 67% of the total heat. Temperatures in the flame are between 1533 to 3573 Kelvin. The oxygen percentage in the gas mixture is important. If the oxygen content is more than half, the flame becomes an oxidizing agent. This is undesirable for some metals but desirable for others. An example when oxidizing flame is desirable is copper-based alloys because it forms a passivation layer over the metal. On the other hand, when the oxygen content is reduced, full combustion is not possible and the flame becomes a reducing (carburizing) flame. The temperatures in a reducing flame are lower and therefore it is suitable for processes like soldering and brazing. Other gases are also potential fuels, but they have some disadvantages over acetylene. Occasionally we supply filler metals to the weld zone in the form of filler rods or wire. Some of them are coated with flux to retard oxidation of surfaces and thus protecting the molten metal. An additional benefit the flux gives us is the removal of oxides and other substances from the weld zone. This leads to stronger bonding. A variation of the oxyfuel gas welding is the PRESSURE GAS WELDING, where the two components are heated at their interface using oxyacetylene gas torch and once the interface starts to melt, the torch is withdrawn and an axial force is applied to press the two parts together until the interface is solidified. ARC WELDING: We use electrical energy to produce an arc between the electrode tip and parts to be welded. The power supply can be AC or DC while the electrodes are either consumable or nonconsumable. Heat transfer in arc welding can be expressed by the following equation: H / l = e x V I / v Here H is the heat input, l is the weld length, V and I are the voltage and current applied, v is the welding speed and e is the process efficiency. The higher the efficiency “e” the more beneficially the available energy is used to melt the material. The heat input can also be expressed as : H = u x (Volume) = u x A x l Here u is the specific energy for melting, A the cross section of the weld and l the weld length. From the two equations above we can obtain: v = e x V I / u A A variation of arc welding is the SHIELDED METAL ARC WELDING (SMAW) which constitutes about 50% of all industrial and maintenance welding processes. ELECTRIC ARC WELDING (STICK WELDING) is performed by touching the tip of a coated electrode to the workpiece and quickly withdrawing it to a distance sufficient to maintain the arc. We call this process also stick-welding because the electrodes are thin and long sticks. During the welding process, the tip of the electrode melts along with its coating and the base metal in the vicinity of the arc. A mixture of the base metal, electrode metal and substances from the electrode coating solidify in the weld area. The coating of the electrode deoxidizes and provides a shielding gas in the weld region, thus protecting it from the oxygen in the environment. Therefore the process is referred to as shielded metal arc welding. We use currents between 50 and 300 Amperes and power levels generally less than 10 kW for optimum weld performance. Also of importance is the polarity of the DC current (direction of current flow). Straight polarity where the workpiece is positive and the electrode is negative is preferred in welding of sheet metals because of its shallow penetration and also for joints with very wide gaps. When we have reverse polarity, i.e. the electrode is positive and workpiece negative we can achieve deeper weld penetrations. With AC current, since we have pulsating arcs, we can weld thick sections using large diameter electrodes and maximum currents. The SMAW welding method is suitable for workpiece thicknesses of 3 to 19 mm and even more using multiple-pass techniques. The slag formed on top of the weld needs to be removed using a wire brush, so that there is no corrosion and failure at the weld area. This of course adds to the cost of shielded metal arc welding. Nevertheless the SMAW is the most popular welding technique in industry and repair work. SUBMERGED ARC WELDING (SAW): In this process we shield the weld arc using granular flux materials like lime, silica, calcium floride, manganese oxide….etc. The granular flux is fed into the weld zone by gravity flow through a nozzle. The flux covering the molten weld zone significantly protects from sparks, fumes, UV radiation….etc and acts as a thermal insulator, thus letting heat penetrate deep into workpiece. The unfused flux is recovered, treated and reused. A coil of bare is used as electrode and fed through a tube to the area of weld. We use currents between 300 and 2000 Amperes. The submerged arc welding (SAW) process is limited to horizontal and flat positions and circular welds if rotation of the circular structure (such as pipes) is possible during welding. Speeds can reach 5 m/min. The SAW process is suitable for thick plates and results in high-quality, tough, ductile and uniform welds. The productivity, that is the amount of weld material deposited per hour is 4 to 10 times the amount as compared to the SMAW process. Another arc welding process, namely the GAS METAL ARC WELDING (GMAW) or alternatively referred to as METAL INERT GAS WELDING (MIG) is based on the weld area being shielded by external sources of gases like helium, argon, carbon dioxide….etc. There may be additional deoxidizers present in the electrode metal. Consumable wire is fed through a nozzle into the weld zone. Fabrication involving bot ferrous as well as nonferrous metals is carried out using gas metal arc welding (GMAW). Welding productivity is about 2 times that of the SMAW process. Automated welding equipment is being used. Metal is transferred in one of three ways in this process: “Spray Transfer” involves transfer of several hundred small metal droplets per second from electrode to the weld area. In “Globular Transfer” on the other hand, carbon dioxide rich gases are used and globules of molten metal are propelled by the electric arc. Welding currents are high and weld penetration deeper, welding speed greater than in spray transfer. Thus the globular transfer is better for welding heavier sections. Finally, in the “Short Circuiting” method, the electrode tip touches the molten weld pool, short circuiting it as metal at rates over 50 droplets/second is transferred in individual droplets. Low currents and voltages are used along with thinner wire. Powers used are about 2 kW and temperatures relatively low, making this method suitable for thin sheets less than 6mm thickness. Another variation the FLUX-CORED ARC WELDING (FCAW) process is similar to gas metal arc welding, except that the electrode is a tube filled with flux. The advantages of using cored-flux electrodes is that they produce more stable arcs, give us the opportunity to improve properties of weld metals, less brittle and flexible nature of its flux as compared to SMAW welding, improved welding contours. Self-shielded cored electrodes contain materials that shield the weld zone against the atmosphere. We use about 20 kW power. Like the GMAW process, the FCAW process also offers the opportunity to automate processes for continuous welding, and it is economical. Different weld metal chemistries can be developed by adding various alloys to the flux core. In ELECTROGAS WELDING (EGW) we weld the pieces placed edge to edge. It is sometimes also called BUTT WELDING. Weld metal is put into a weld cavity between two pieces to be joined. The space is enclosed by two water-cooled dams to keep the molten slag from pouring out. The dams are moved up by mechanical drives. When workpiece can be rotated, we can use the electrogas welding technique for circumferential welding of pipes too. Electrodes are fed through a conduit to keep a continuous arc. Currents can be around 400Amperes or 750 Amperes and power levels around 20 kW. Inert gases originating from either a flux-cored electrode or external source provide shielding. We use the electrogas welding (EGW) for metals such as steels, titanium….etc with thicknesses from 12mm to 75mm. The technique is a good fit for large structures. Yet, in another technique called ELECTROSLAG WELDING (ESW) the arc is ignited between the electrode and the bottom of the workpiece and flux is added. When molten slag reaches the electrode tip, the arc is extinguished. Energy is continuously supplied through the electrical resistance of the molten slag. We can weld plates with thicknesses between 50 mm and 900 mm and even higher. Currents are around 600 Ampere while voltages are between 40 – 50 V. The welding speeds are around 12 to 36 mm/min. Applications are similar to electrogas welding. One of our nonconsumable electrode processes, the GAS TUNGSTEN ARC WELDING (GTAW) also known as TUNGSTEN INERT GAS WELDING (TIG) involves the supply of a filler metal by a wire. For closely-fit joints sometimes we do not use the filler metal. In the TIG process we do not use flux, but use argon and helium for shielding. Tungsten has a high melting point and is not consumed in the TIG welding process, therefore constant current as well as arc gaps can be maintained. Power levels are between 8 to 20 kW and currents at either 200 Ampere (DC) or 500 Ampere (AC). For aluminum and magnesium we use AC current for its oxide cleaning function. To avoid contamination of the tungsten electrode, we avoid its contact with molten metals. Gas Tungsten Arc Welding (GTAW) is especially useful for welding thin metals. GTAW welds are of very high quality with good surface finish. Due to the higher cost of hydrogen gas, a less frequently used technique is ATOMIC HYDROGEN WELDING (AHW), where we generate an arc between two tungsten electrodes in a shielding atmosphere of flowing hydrogen gas. The AHW is also a nonconsumable electrode welding process. The diatomic hydrogen gas H2 breaks down into its atomic form near the welding arc where temperatures are over 6273 Kelvin. While breaking down, it absorbs large amount of heat from the arc. When the hydrogen atoms strike the weld zone which is a relatively cold surface, they recombine into diatomic form and release the stored heat. Energy can be varied by changing the workpiece to arc distance. In another nonconsumable electrode process, PLASMA ARC WELDING (PAW) we have a concentrated plasma arc directed toward the weld zone. The temperatures reach 33,273 Kelvin in PAW. A nearly equal number of electrons and ions make up the plasma gas. A low-current pilot arc initiates the plasma which is between the tungsten electrode and orifice. Operating currents are generally around 100 Amperes. A filler metal may be fed. In plasma arc welding, shielding is accomplished by an outer shielding ring and using gases such as argon and helium. In plasma arc welding, the arc may be between the electrode and workpiece or between the electrode and nozzle. This welding technique has the advantages over other methods of higher energy concentration, deeper and narrower welding capability, better arc stability, higher welding speeds up to 1 meter/min, less thermal distortion. We generally use plasma arc welding for thicknesses less than 6 mm and sometimes up to 20 mm for aluminum and titanium. HIGH-ENERGY-BEAM WELDING: Another type of fusion welding method with electron-beam welding (EBW) and laser welding (LBW) as two variants. These techniques are of particular value for our high-tech products manufacturing work. In electron-beam welding, high speed electrons strike the workpiece and their kinetic energy is converted to heat. The narrow beam of electrons travel easily in the vacuum chamber. Generally we use high vacuum in e-beam welding. Plates as thick as 150 mm can be welded. No shielding gases, flux or filler material is needed. Elecron beam guns have 100 kW capacities. Deep and narrow welds with high aspect ratios up to 30 and small heat-affected zones are possible. Welding speeds can reach 12 m/min. In laser-beam welding we use high-power lasers as the source of heat. Laser beams as small as 10 microns with high density enable deep penetration into the workpiece. Depth-to-width ratios as much as 10 is possible with laser-beam welding. We use both pulsed as well as continuous wave lasers, with the former in applications for thin materials and the latter mostly for thick workpieces up to about 25 mm. Power levels are up to 100 kW. The laser beam welding is not well suited for optically very reflective materials. Gases may also be used in the welding process. The laser beam welding method is well fit for automation & high volume manufacturing and can offer welding speeds between 2.5 m/min and 80 m/min. One major advantage this welding technique offers is access to areas where other techniques cannot be used. Laser beams can easily travel to such difficult regions. No vacuum as in electron-beam welding is needed. Welds with good quality & strength, low shrinkage, low distortion, low porosity can be obtained with laser beam welding. Laser beams can be easily manipulated and shaped using fiber optic cables. The technique is thus well suitable for welding of precision hermetic assemblies, electronic packages…etc. Let us look at our SOLID STATE WELDING techniques. COLD WELDING (CW) is a process where pressure instead of heat is applied using dies or rolls to the parts that are mated. In cold welding, at least one of the mating parts needs to be ductile. Best results are obtained with two similar materials. If the two metals to be joined with cold welding are dissimilar, we may get weak and brittle joints. The cold welding method is well suited for soft, ductile and small workpieces such as electrical connections, heat sensitive container edges, bimetallic strips for thermostats…etc. One variation of cold welding is roll bonding (or roll welding), where the pressure is applied through a pair of rolls. Sometimes we perform roll welding at elevated temperatures for better interfacial strength. Another solid state welding process we use is the ULTRASONIC WELDING (USW), where the workpieces are subjected to a static normal force and oscillating shearing stresses. The oscillating shearing stresses are applied through the tip of a transducer. Ultrasonic welding deploys oscillations with frequencies from 10 to 75 kHz. In some applications such as seam welding, we use a rotating welding disk as the tip. Shearing stresses applied to the workpieces cause small plastic deformations, break up oxide layers, contaminants and lead to solid state bonding. Temperatures involved in ultrasonic welding are way below melting point temperatures for metals and no fusion takes place. We frequently use the ultrasonic welding (USW) process for nonmetallic materials like plastics. In thermoplastics, the temperatures do reach melting points however. Another popular technique, in FRICTION WELDING (FRW) the heat is generated through friction at the interface of the workpieces to be joined. In friction welding we keep one of the workpieces stationary while the other workpiece is held in a fixture and rotated at a constant speed. The workpieces are then brought into contact under an axial force. The surface speed of rotation in friction welding may reach 900m/min in some cases. After sufficient interfacial contact, the rotating workpiece is brought to a sudden stop and the axial force is increased. The weld zone is generally a narrow region. The friction welding technique can be used to join solid and tubular parts made of a variety of materials. Some flash may develop at the interface in FRW, but this flash can be removed by secondary machining or grinding. Variations of the friction welding process exist. For example “inertia friction welding” involves a flywheel whose rotational kinetic energy is used to weld the parts. The weld is complete when the flywheel comes to a stop. The rotating mass can be varied and thus the rotational kinetic energy. Another variation is “linear friction welding”, where linear reciprocating motion is imposed on at least one of the components to be joined. In linear friction welding parts do not have to be circular, they can be rectangular, square or of other shape. Frequencies can be in the tens of Hz, amplitudes in the millimeters range and pressures in the tens or hundreds of MPa. Finally “friction stir welding” is somewhat different than the other two explained above. Whereas in inertia friction welding and linear friction welding heating of interfaces is achieved through friction by rubbing two contacting surfaces, in the friction stir welding method a third body is rubbed against the two surfaces to be joined. A rotating tool of 5 to 6 mm diameter is brought into contact with the joint. The temperatures can increase to values between 503 to 533 Kelvin. Heating, mixing and stirring of the material in the joint takes place. We use the friction stir welding on a variety of materials including aluminum, plastics and composites. Welds are uniform and quality is high with minimum pores. No fumes or spatter are produced in friction stir welding and the process is well automated. RESISTANCE WELDING (RW): The heat required for welding is produced by the electrical resistance between the two workpieces to be joined. No flux, shielding gases or consumable electrodes are used in resistance welding. Joule heating takes place in resistance welding and can be expressed as: H = (Square I) x R x t x K H is heat generated in joules (watt-seconds), I current in Amperes, R resistance in Ohms, t is the time in seconds the current flows through. The factor K is less than 1 and represents the fraction of energy that is not lost through radiation and conduction. Currents in resistance welding processes can reach levels as high as 100,000 A but voltages are typically 0.5 to 10 Volts. Electrodes are typically made of copper alloys. Both similar and dissimilar materials can be joined by resistance welding. Several variations exist for this process: “Resistance spot welding” involves two opposing round electrodes contacting the surfaces of the lap joint of the two sheets. Pressure is applied until current is turned off. The weld nugget is generally up to 10 mm in diameter. Resistance spot welding leaves slightly discolored indentation marks at weld spots. Spot welding is our most popular resistance welding technique. Various electrode shapes are used in spot welding in order to reach difficult areas. Our spot welding equipment is CNC controlled and has multiple electrodes that can be used simultaneously. Another variation “resistance seam welding” is carried out with wheel or roller electrodes that produce continuous spot welds whenever the current reaches a sufficiently high level in the AC power cycle. Joints produced by resistance seam welding are liquid and gas tight. Welding speeds of about 1.5 m/min are normal for thin sheets. One may apply intermittent currents so that spot welds are produced at desired intervals along the seam. In “resistance projection welding” we emboss one or more projections (dimples) on one of the workpiece surfaces to be welded. These projections may be round or oval. High localized temperatures are reached at these embossed spots that come into contact with the mating part. Electrodes exert pressure to compress these projections. Electrodes in resistance projection welding have flat tips and are water cooled copper alloys. The advantage of resistance projection welding is our ability to a number of welds in one stroke, thus the extended electrode life, capability to weld sheets of various thicknesses, capability to weld nuts and bolts to sheets. Disadvantage of resistance projection welding is the added cost of embossing the dimples. Yet another technique, in “flash welding” heat is generated from the arc at the ends of the two workpieces as they begin to make contact. This method may also alternatively considered arc welding. The temperature at the interface rises, and material softens. An axial force is applied and a weld is formed at the softened region. After the flash welding is complete, the joint can be machined for improved appearance. Weld quality obtained by flash welding is good. Power levels are 10 to 1500 kW. Flash welding is suitable for edge-to-edge joining of similar or dissimilar metals up to 75 mm diameter and sheets between 0.2 mm to 25 mm thickness. “Stud arc welding” is very similar to flash welding. The stud such as a bolt or threaded rod serves as one electrode while being joined to a workpiece such as a plate. To concentrate the generated heat, prevent oxidation and retain the molten metal in the weld zone, a disposable ceramic ring is placed around the joint. Finally “percussion welding” another resistance welding process, utilizes a capacitor to supply the electrical energy. In percussion welding the power is discharged within milliseconds of time very quickly developing high localized heat at the joint. We use percussion welding widely in the electronics manufacturing industry where heating of sensitive electronic components in the vicinity of the joint has to be avoided. A technique called EXPLOSION WELDING involves detonation of a layer of explosive that is put over one of the workpieces to be joined. The very high pressure exerted on the workpiece produces a turbulent and wavy interface and mechanical interlocking takes place. Bond strengths in explosive welding are very high. Explosion welding is a good method for cladding of plates with dissimilar metals. After cladding, the plates may be rolled into thinner sections. Sometimes we use explosion welding for expanding tubes so that they get sealed tightly against the plate. Our last method within the domain of solid state joining is DIFFUSION BONDING or DIFFUSION WELDING (DFW) in which a good joint is achieved mainly by diffusion of atoms across the interface. Some plastic deformation at the interface also contributes to the welding. Temperatures involved are around 0.5 Tm where Tm is melting temperature of the metal. Bond strength in diffusion welding depends on pressure, temperature, contact time and cleanliness of contacting surfaces. Sometimes we use filler metals at the interface. Heat and pressure are required in diffusion bonding and are supplied by electrical resistance or furnace and dead weights, press or else. Similar and dissimilar metals can be joined with diffusion welding. The process is relatively slow due to the time it takes for atoms to migrate. DFW can be automated and is widely used in the fabrication of complex parts for the aerospace, electronics, medical industries. Products manufactured include orthopedic implants, sensors, aerospace structural members. Diffusion bonding can be combined with SUPERPLASTIC FORMING to fabricate complex sheet metal structures. Selected locations on sheets are first diffusion bonded and then the unbonded regions are expanded into a mold using air pressure. Aerospace structures with high stiffness-to-weight ratios are manufactured using this combination of methods. The diffusion welding / superplastic forming combined process reduces the number of parts required by eliminating the need for fasteners, results in low-stress highly accurate parts economically and with short lead times. BRAZING: The brazing and soldering techniques involve lower temperatures than those required for welding. Brazing temperatures are higher than soldering temperatures however. In brazing a filler metal is placed between the surfaces to be joined and temperatures are raised to the melting temperature of the filler material above 723 Kelvin but below the melting temperatures of the workpieces. The molten metal fills the closely fitting space between workpieces. Cooling and subsequent solidification of the filer metal results in strong joints. In braze welding the filler metal is deposited at the joint. Considerably more filler metal is used in braze welding compared to brazing. Oxyacetylene torch with oxidizing flame is used to deposit the filler metal in braze welding. Due to lower temperatures in brazing, problems at heat affected zones such as warping and residual stresses are less. The smaller the clearance gap in brazing the higher is the shear strength of the joint. Maximum tensile strength however is achieved at an optimum gap (a peak value). Below and above this optimum value, the tensile strength in brazing decreases. Typical clearances in brazing can be between 0.025 and 0.2 mm. We use a variety of brazing materials with different shapes such as performs, powder, rings, wire, strip…..etc. and can manufacture these performs specially for your design or product geometry. We do also determine the content of the brazing materials according to your base materials and application. We frequently use fluxes in brazing operations to remove unwanted oxide layers and prevent oxidation. To avoid subsequent corrosion, fluxes are generally removed after the joining operation. AGS-TECH Inc. uses various brazing methods, including: - Torch Brazing - Furnace Brazing - Induction Brazing - Resistance Brazing - Dip Brazing - Infrared Brazing - Diffusion Brazing - High Energy Beam Our most common examples of brazed joints are made of dissimilar metals with good strength such as carbide drill bits, inserts, optoelectronic hermetic packages, seals. SOLDERING : This is one of our most frequently used techniques where the solder (filler metal) fills the joint as in brazing between closely fitting components. Our solders have melting points below 723 Kelvin. We deploy both manual and automated soldering in manufacturing operations. Compared to brazing, soldering temperatures are lower. Soldering is not very suitable for high-temperature or high-strength applications. We use lead-free solders as well as tin-lead, tin-zinc, lead-silver, cadmium-silver, zinc-aluminum alloys besides others for soldering. Both noncorrosive resin-based as well as inorganic acids and salts are used as flux in soldering. We use special fluxes to solder metals with low solderability. In applications where we have to solder ceramic materials, glass or graphite, we first plate the parts with a suitable metal for increased solderability. Our popular soldering techniques are: -Reflow or Paste Soldering -Wave Soldering -Furnace Soldering -Torch Soldering -Induction Soldering -Iron Soldering -Resistance Soldering -Dip soldering -Ultrasonic Soldering -Infrared Soldering Ultrasonic soldering offers us a unique advantage whereby the need for fluxes is eliminated due to ultrasonic cavitation effect which removes oxide films from the surfaces being joined. Reflow and Wave soldering are our industrially outstanding techniques for high volume manufacturing in electronics and therefore worth explaining in greater detail. In reflow soldering, we use semisolid pastes that include solder-metal particles. The paste is placed onto the joint using a screening or stenciling process. In printed circuit boards (PCB) we frequently use this technique. When electrical components are placed onto these pads from paste, the surface tension keeps the surface-mount packages aligned. After placing the components, we heat the assembly in a furnace so the reflow soldering takes place. During this process, the solvents in the paste evaporate, the flux in the paste is activated, the components are preheated, the solder particles are melted and wet the joint, and finally the PCB assembly is cooled slowly. Our second popular technique for high volume production of PCB boards, namely wave soldering relias on the fact that molten solders wet metal surfaces and form good bonds only when the metal is preheated. A standing laminar wave of molten solder is first generated by a pump and the preheated and prefluxed PCBs are conveyed over the wave. The solder wets only exposed metal surfaces but does not wet the IC polymer packages nor the polymer-coated circuit boards. A high-velocity of hot water jet blows excess solder from the joint and prevents bridging between adjacent leads. In wave soldering of surface-mount packages we first adhesively bond them to the circuit board before soldering. Again screening and stenciling is used but this time for epoxy. After the components are placed in their correct locations, the epoxy is cured, the boards are inverted and wave soldering takes place. КЛИКНЕТЕ Услуга за пронаоѓање на производи-локатор ПРЕТХОДНА СТРАНИЦА
- Electromagnetic Components Manufacturing and Assembly, Selenoid
Electromagnetic Components Manufacturing and Assembly, Selenoid, Electromagnet, Transformer, Electric Motor, Generator, Meters, Indicators, Scales,Electric Fans Соленоиди и електромагнетни компоненти и склопови Како прилагоден производител и инженерски интегратор, AGS-TECH може да ви ги обезбеди следните ЕЛЕКТРОМАГНЕТНИ КОМПОНЕНТИ И СКЛОПИ: • Склопови на селеноид, електромагнет, трансформатор, електромотор и генератор • Електромагнетни броила, индикатори, ваги специјално произведени за да одговараат на вашиот уред за мерење. • Електромагнетни сензори и склопови на актуатор • Електрични вентилатори и ладилници со различна големина за електронски уреди и индустриски апликации • Други сложени електромагнетни системи склопување Кликнете овде за да ја преземете брошурата на нашите Панелни метри - OICASCHINT Брошура за меки ферити - јадра - тороиди - производи за сузбивање на EMI - RFID транспондери и додатоци Преземете ја брошурата за нашата ПРОГРАМА ЗА ПАРТНЕРСТВО ЗА ДИЗАЈН Ако сте најмногу заинтересирани за нашите инженерски и истражувачки и развојни способности наместо производствените способности, тогаш ве покануваме да ја посетите нашата инженерска страница http://www.ags-engineering.com КЛИКНЕТЕ Услуга за пронаоѓање на производи-локатор ПРЕТХОДНА СТРАНИЦА
- Glass Cutting Shaping Tools , USA , AGS-TECH Inc.
Glass Cutting Shaping Tools offered by AGS-TECH, Inc. We supply high quality diamond wheel series, diamond wheel for solar glass, diamond wheel for CNC machine, peripheral diamond wheel, cup & bowl shape diamond wheels, resin wheel series, polishing wheel series, felt wheel, stone wheel, coating removal wheel... Алатки за обликување на сечење стакло Please click on the Glass Cutting and Shaping Tools of interest below to download related brochure. Diamond Wheel Series Diamond Wheel for Solar Glass Diamond Wheel for CNC Machine Peripheral Diamond Wheel Cup & Bowl Shape Diamond Wheel Resin Wheel Series Polishing Wheel Series 10S Polishing Wheel Felt Wheel Stone Wheel Coating Removal Wheel BD Polishing Wheel BK Polishing Wheel 9R Ploshing Wheel Polishing Material series Cerium Oxide Series Glass Drill Series Glass Tool Series Other Glass Tools Glass Plier Glass Suction & Lifter Grinding Tool Power Tool UV,Testing Tool Sandblast Fittings Series Machine Fittings Series Cutting Discs Glass Cutters Ungrouped Price of our glass cutting shaping tools depends on model and quantity of order. If you would like us to design and/or manufacture glass cutting and shaping tools specifically for you, please either provide us detailed blueprints, or ask us for help. We will then design, prototype and manufacture them specially for you. Since we carry a wide variety of glass cutting, drilling, grinding, polishing and shaping products with different dimensions, applications and material; it is impossible to list them here. We encourage you to email or call us so we can determine which product is the best fit for you. When contacting us, please inform us about: - Intended application - Material grade preferred - Dimensions - Finishing requirements - Packaging requirements - Labeling requirements - Quantity of your planned order & estimated yearly demand Private Label Auto Glass Repair and Replacement Systems We can private label these hand tools if you wish. In other words, we can put your company name, brand and label on them. This way you can promote your brand by reselling these to your customers. Private Label Hand Tools for Every Industry This catalog contains a few glass cutting and shaping tools. We can private label these hand tools if you wish. In other words, we can put your company name, brand and label on them. This way you can promote your brand by reselling these to your customers. Private Label Power Tool Accessories This brochure includes some glass cutting and shaping tools. We can private label these hand tools if you wish. In other words, we can put your company name, brand and label on them. This way you can promote your brand by reselling these to your customers. Private Label Power Tools for Every Industry This catalog contains some glass cutting and shaping tools. We can private label these hand tools if you wish. In other words, we can put your company name, brand and label on them. This way you can promote your brand by reselling these to your customers. КЛИКНЕТЕ ТУКА за да ги преземете нашите технички способности и референтниот водич за специјализирани алатки за сечење, дупчење, мелење, обликување, обликување, полирање што се користат во медицински, стоматолошки, прецизни инструменти, печат на метал, обликување матрица и други индустриски апликации. КЛИКНЕТЕ Услуга за пронаоѓање на производи-локатор Кликнете овде за да отидете во менито Алатки за сечење, дупчење, брусење, преклопување, полирање, коцки и обликување Уп. Шифра: OICASANHUA
- Hardness Tester - Rockwell - Brinell - Vickers - Leeb - Microhardness
Hardness Tester - Rockwell - Brinell - Vickers - Leeb - Microhardness - Universal - AGS-TECH Inc. - New Mexico - USA Тестери за цврстина AGS-TECH Inc. stocks a comprehensive range of hardness testers including ROCKWELL, BRINELL, VICKERS, LEEB, KNOOP, MICROHARDNESS TESTERS, UNIVERSAL HARDNESS TESTER, PORTABLE HARDNESS TESTING INSTRUMENTS, optical systems and software for measurement, data acquisition and analysis, test blocks, indenters, anvils and related accessories. Some of the brand name hardness testers we sell are BUEHLER, ELCOMETER, MITECH, SADT, SINOAGE, SINOWON ..... You can purchase brand new, refurbished or used equipment from us. Simply choose the product from the following catalogs and provide us the brand name and model of your choice: BUEHLER Hardness Testing Catalog ELCOMETER Inspection Equipment Catalog (does offer Physical Test Equipment , Concrete Inspection Equipment, Concrete Test Hammers , Hardness & Scratch Resistance Testers ) MITECH MH600 P ortable Hardness Tester MITECH Hardness Testers P roduct Comparison Table MITUTOYO Hardness Testing Machines SADT-SINOAGE B rand M etrology and T est E quipment Catalog SINOWON Rockwell Hardness Tester SINOWON Portable Ultrasonic Hardness Tester One of the most common tests for assessing the mechanical properties of materials is the hardness test. Hardness of a material is its resistance to permanent indentation. One may also say hardness is a material’s resistance to scratching and to wear. There are several techniques to measure the hardness of materials using various geometries and materials. The measurement results are not absolute, they are more of a relative comparative indicator, because the results depend on the shape of the indenter and the applied load. Our portable hardness testers can generally run any hardness test listed above. They can be configured for particular geometric features and materials such as hole interiors, gear teeth…etc. Let us briefly go over the various hardness test methods. BRINELL TEST : In this test, a steel or tungsten carbide ball with 10 mm diameter is pressed against a surface with a load of 500, 1500 or 3000 Kg force. Brinell hardness number is the ratio of the load to the curved area of indentation. A Brinell test leaves behind different types of impressions on the surface depending on the tested material’s condition. For example, on annealed materials a rounded profile is left behind whereas on cold-worked materials we observe a sharp profile. Tungsten carbide indenter balls are recommended for Brinell hardness numbers higher than 500. For harder workpiece materials a 1500 Kg or 3000 Kg load is recommended so that the impressions left behind are sufficiently large for accurate measurement. Because of the fact that impressions made by the same indenter at different loads are not geometrically similar, the Brinell hardness number depends on the load used. Therefore one should always note the load employed on the test results. Brinell test is well suited for materials between low to medium hardness. ROCKWELL TEST : In this test the depth of penetration is measured. The indenter is pressed on the surface initially with a minor load and then a major load. The difference in the penetration debth is a measure of hardness. Several Rockwell hardness scales exist employing different loads, indenter materials and geometries. The Rockwell hardness number is read directly from a dial on the testing machine. For example, if the hardness number is 55 using the C scale, it is written as 55 HRC. VICKERS TEST : Sometimes also referred to as the DIAMOND PYRAMID HARDNESS TEST, it uses a pyramid-shaped diamond indenter with loads ranging from 1 to 120 Kg. The Vickers hardness number is given by HV=1.854P / square L. The L here is the diagonal length of the diamond pyramid. The Vickers test gives basically the same hardness number regardless of the load. The Vickers test is suitable for testing materials with a wide range of hardness including very hard materials. KNOOP TEST : In this test, we use a diamond indenter in the shape of an elongated pyramid and loads between 25g to 5 Kg. The Knoop hardness number is given as HK=14.2P / square L. Here the letter L is the length of the elongated diagonal. The size of indentations in Knoop tests is relatively small, in the range of 0.01 to 0.10 mm. Due to this small number surface preparation for the material is very important. Test results should cite the load applied because the hardness number obtained depends on the applied load. Because light loads are used, the Knoop test is considered a MICROHARDNESS TEST. The Knoop test is therefore suitable for very small, thin specimens, brittle materials such as gemstones, glass and carbides, and even for measuring the hardness of individual grains in a metal. LEEB HARDNESS TEST : It is based on rebound technique measuring the Leeb hardness. It is an easy and industrially popular method. This portable method is mostly used for testing sufficiently large workpieces above 1 kg. An impact body with a hard metal test tip is propelled by spring force against the workpiece surface. When the impact body hits the workpiece, surface deformation takes place which will result in loss of kinetic energy. Velocity measurements reveal this loss in kinetic energy. When the impact body passes coil at a precise distance from the surface, a signal voltage is induced during the impact and rebound phases of the test. These voltages are proportional to the velocity. Using electronic signal processing one gets the Leeb hardness value from display. Our PORTABLE HARDNESS TESTERS from SADT / HARTIP HARDNESS TESTER SADT HARTIP2000/HARTIP2000 D&DL : This is an innovative portable Leeb hardness tester with newly patented technology, which makes HARTIP 2000 a universal angle (UA) impact direction hardness tester. There is no need to set up impact direction when taking measurements at any angle. Therefore, HARTIP 2000 offers a linear accuracy compared to the angle compensating method. HARTIP 2000 is also a cost saving hardness tester and has many other features. The HARTIP2000 DL is equipped with SADT unique D and DL 2-in-1 probe. SADT HARTIP1800 Plus/1800 Plus D&DL : This device is an advanced state-of-the-art palm sized metal hardness tester with many new features. Using a patented technology, SADT HARTIP1800 Plus is a new generation product. It has a high accuracy of +/-2 HL (or 0.3% @HL800) with high contract OLED display and wide environmental temperature range (-40ºC~60ºC). Apart from huge memories in 400 blocks with 360k data, HARTIP1800 Plus can download measured data to PC and printout to mini-printer by USB port and wirelessly with internal blue-tooth module. The battery can be charged simply from USB port. It has a customer re-calibration and statics function. HARTIP 1800 plus D&DL is equipped with two-in-one probe. With unique two-in-one probe, HARTIP1800plus D&DL can convert between probe D and probe DL simply by changing impact body. It’s more economical than buying them individually. It has the same configuration with HARTIP1800 plus except two-in-one probe. SADT HARTIP1800 Basic/1800 Basic D&DL : This is a basic model for HARTIP1800plus. With most of core functions of HARTIP1800 plus and a lower price, HARTIP1800 Basic is a good choice for the customer with limited budget. HARTIP1800 Basic also can be equipped with our unique D/DL two-in-one impact device. SADT HARTIP 3000 : This is an advanced hand-held digital metal hardness tester with high accuracy, wide measurement range and ease of operation. It is suitable for testing the hardness of all metals especially on site for large structural and assembled components, which are widely used in the power, petrochemical, aerospace, automotive and machine building industries. SADT HARTIP1500/HARTIP1000 : This is an integrated handheld metal hardness tester that combines impact device (probe) and processor into one unit. The size is much smaller than the standard impact device, which allows HARTIP 1500/1000 to meet not only normal measurement conditions, but also can take measurements at narrow spaces. HARTIP 1500/1000 is suitable for testing the hardness of almost all ferrous and nonferrous materials. With its new technology, its accuracy is improved to a higher level than the standard type. HARTIP 1500/1000 is one of the most economic hardness testers in its class. BRINELL HARDNESS READING AUTOMATIC MEASURING SYSTEM / SADT HB SCALER : HB Scaler is an optical measuring system which can automatically measure the size of indentation from Brinell hardness tester and gives the Brinell hardness readings. All values and indentation images can be saved in PC. With the software, all values can be processed and printed out as a report. Our BENCH HARDNESS TESTER products from SADT are: SADT HR-150A ROCKWELL HARDNESS TESTER : The manually operated HR-150A Rockwell hardness tester is known for its perfection and ease of operation. This machine uses the standard preliminary test force of 10kgf and main loads of 60/100/150 kilograms while conforming to the international Rockwell standard. After each test, the HR-150A shows the Rockwell B or Rockwell C hardness value directly on the dial indicator. The preliminary test force has to be applied manually, followed by applying the main load by means of the lever at the right side of the hardness tester. After unloading, the dial indicates the requested hardness value directly with high accuracy and repeatability. SADT HR-150DT MOTORIZED ROCKWELL HARDNESS TESTER : This series of hardness testers are recognized for their accuracy and ease of operation, function entirely conforming to the international Rockwell standard. Depending on the combination of indenter type and applied total test force, a unique symbol is given to each Rockwell scale. HR-150DT and HRM-45DT feature both specific Rockwell scales of HRC and HRB on a dial. The appropriate force should be adjusted manually, using the dial on the right side of the machine. After application of the preliminary force, the HR150DT and HRM-45DT will proceed with a fullly automated testing: loading, waiting, unloading, and at the end will display the hardness. SADT HRS-150 DIGITAL ROCKWELL HARDNESS TESTER : The HRS-150 digital Rockwell hardness tester is designed for ease of use and safety of operation. It conforms with the international Rockwell standard. Depending on the combination of indenter type and applied total test force, a unique symbol is given to each Rockwell scale. The HRS-150 will automatically show your selection of a specific Rockwell scale on the LCD display, and will indicate which load is being used. The integrated autobrake mechanism allows the preliminary test force to be applied manually without the possibility of an error. After application of the preliminary force, the HRS-150 will proceed with a fully automatic test: loading, dwell time, unloading, and computation of the hardness value and its display. Connected to the included printer through an RS232 output, it’s possible to print out all results. Our BENCH TYPE SUPERFICIAL ROCKWELL HARDNESS TESTER products from SADT are: SADT HRM-45DT MOTORIZED SUPERFICIAL ROCKWELL HARDNESS TESTER : This series hardness testers are recognized for their accuracy and ease of operation, perform entirely conforming to the international Rockwell standard. Depending on the combination of indenter type and applied total test force, a unique symbol is given to each Rockwell scale. HR-150DT and HRM-45DT feature both of the specific Rockwell scales HRC and HRB on a dial. The appropriate force should be adjusted manually, using the dial on the right side of the machine. After application of the preliminary force, the HR150DT and HRM-45DT will proceed with a fullly automatic test process: loading, dwelling, unloading, and at the end will display the hardness. SADT HRMS-45 SUPERFICIAL ROCKWELL HARDNESS TESTER : HRMS-45 Digital Superficial Rockwell Hardness Tester is a novel product integrating advanced mechanical and electronic technologies. The dual display of LCD and LED digital diodes, make it an upgraded product version of the standard type superficial Rockwell tester. It measures the hardness of ferrous, nonferrous metals and hard materials, carburized and nitrided layers, and other chemically treated layers. It is also used for the measurement of hardness of thin pieces. SADT XHR-150 PLASTIC ROCKWELL HARDNESS TESTER : XHR-150 plastics Rockwell hardness tester adopts a motorized testing method, testing force can be loaded, kept at dwelling and unloaded automatically. Human error is minimized and easy to operate. It is used to measure hard plastics, hard rubbers, aluminum, tin, copper, soft steel, synthetic resins, tribologic materials, etc. Our BENCH TYPE VICKERS HARDNESS TESTER products from SADT are: SADT HVS-10/50 LOW LOAD VICKERS HARDNESS TESTER : This low load Vicker’s hardness tester with digital display is a new hi-tech product integrating mechanical and photoelectrical technologies. As a substitute for traditional small-load Vicker’s hardness testers, it features an easy operation and good reliability, which is specially designed for testing small, thin samples or parts after surface coating. Suitable for research institutes, industrial labs and QC departments, this is an ideal hardness testing instrument for research and measurement purposes. It offers integration of computer programming technology, high resolution optical measuring system and photoelectrical technique, soft key input, light source adjustment, selectable testing model, conversion tables, pressure-holding time, file number input and data saving functions. It has a big LCD screen to display the test model, test pressure, indention length, hardness values, pressure holding time and the numbers of tests. Offers also date recording, test results recording and data processing, printing output function, through an RS232 interface. SADT HV-10/50 LOW LOAD VICKERS HARDNESS TESTER : These low load Vickers hardness testers are new hi-tech products integrating mechanical and photoelectrical technologies. These testers are specially designed for testing small and thin samples and parts after surface coating. Suitable for research institutes, industrial labs and QC departments. Key features and functions are microcomputer control, adjustment of light source via soft keys, adjustment of pressure holding time and LED/LCD display, its unique measurement conversion device and unique micro eyepiece one-time measurement readout device that ensures easy use and high accuracy. SADT HV-30 VICKERS HARDNESS TESTER : The HV-30 model Vickers hardness tester is specially designed for testing small, thin samples and parts after surface coating. Suitable for research institutes, factory labs and QC departments, these are ideal hardness testing instruments for research and test purposes. Key features and functions are micro computer control, automatic loading and unloading mechanism, adjustment of lighting source via hardware, adjustment of pressure holding time (0~30s), unique measurement conversion device and unique micro eyepiece one-time measurement readout device, ensuring easy use and high accuracy. Our BENCH TYPE MICRO HARDNESS TESTER products from SADT are: SADT HV-1000 MICRO HARDNESS TESTER / HVS-1000 DIGITAL MICRO HARDNESS TESTER : This product is especially well suited for high precision hardness testing of small and thin samples such as sheet, foil, coatings, ceramic products and hardened layers. To ensure a satisfactory indentation, the HV1000 / HVS1000 features automatic loading and unloading operations, a very accurate loading mechanism and a robust lever system. The micro-computer controlled system ensures an absolutely precise hardness measurement with adjustable dwell time. SADT DHV-1000 MICRO HARDNESS TESTER / DHV-1000Z DIGITAL VICKERS HARDNESS TESTER : These micro Vickers hardness testers made with a unique and precise design are able to produce a clearer indentation and hence a more accurate measurement. By means of a 20 × lens and a 40 × lens the instrument has a wider measurement field and a broader application range. Equipped with a digital microscope, on its LCD screen it shows the measuring methods, the test force, the indentation length, the hardness value, the dwell time of the test force as well as the number of the measurements. In addition, it is equipped with an interface linked to a digital camera and a CCD video camera. This tester is widely used for measuring ferrous metals, non-ferrous metals, IC thin sections, coatings, glass, ceramics, precious stones, quench hardened layers and more. SADT DXHV-1000 DIGITAL MICRO HARDNESS TESTER : These micro Vickers hardness testers made with a unique and precise are able to produce a clearer indentation and hence more accurate measurements. By means of a 20 × lens and a 40 × lens the tester has a wider measurement field and a broader application range. With an automatically turning device ( the automatically turning turret ), the operation has become easier; and with a threaded interface, it can be linked to a digital camera and a CCD video camera. First the device lets the LCD touch screen to be used, thus allowing the operation to be more human controlled. The device has capabilities such as direct reading of the measurements, the easy change of the hardness scales, the saving of the data, the printing and the connection with the RS232 interface. This tester is widely used for measuring ferrous metals, non-ferrous metals, IC thin sections, coatings, glass, ceramics, precious stones; thin plastic sections, quench hardened layers and more. Our BENCH TYPE BRINELL HARDNESS TESTER / MULTI-PURPOSE HARDNESS TESTER products from SADT are: SADT HD9-45 SUPERFICIAL ROCKWELL & VICKERS OPTICAL HARDNESS TESTER : This device serves the purpose of measuring the hardness of ferrous, nonferrous metals, hard metals, carburized and nitrided layers and chemically treated layers and thin pieces. SADT HBRVU-187.5 BRINELL ROCKWELL & VICKERS OPTICAL HARDNESS TESTER : This instrument is used for determining the Brinell, Rockwell and Vickers hardness of ferrous, nonferrous metals, hard metals, carburized layers and chemically treated layers. It can be used in plants, scientific & research institutes, laboratories and colleges. SADT HBRV-187.5 BRINELL ROCKWELL & VICKERS HARDNESS TESTER (NOT OPTICAL) : This instrument is used for determining the Brinell, Rockwell and Vickers hardness of ferrous, non-ferrous metals, hard metals, carburized layers and chemically treated layers. It can be used in factories, scientific & research institutes, laboratories and colleges. It’s not an optical type hardness tester. SADT HBE-3000A BRINELL HARDNESS TESTER : This automatic Brinell hardness tester features a wide measurement range up to 3000 Kgf with a high accuracy conforming to DIN 51225/1 standard. During the automatic test cycle the applied force will be controlled by a closed loop system guaranteeing a constant force on the work piece, conforming to DIN 50351 standard. The HBE-3000A comes completely with a reading microscope with enlargement factor 20X and a micrometer resolution of 0.005 mm. SADT HBS-3000 DIGITAL BRINELL HARDNESS TESTER : This digital Brinell hardness tester is a new generation state-of-the-art device. It can be used to determine the Brinell hardness of ferrous and non-ferrous metals. The tester offers electronic auto loading, computer software programming, high power optical measurement, photosensor and other features. Each operational process and test result can be displayed on its large LCD screen. The test results can be printed. Device is suitable for manufacturing environments, colleges and scientific institutions. SADT MHB-3000 DIGITAL ELECTRONIC BRINELL HARDNESS TESTER : This instrument is an integrated product combining optical, mechanical and electronic techniques, adopting a precise mechanical structure and computer controlled closed-circuit system. The instrument loads and unloads the testing force with its motor. Using a 0.5% accuracy compression sensor to feedback the information and the CPU to control, the instrument compensates automatically for the varying testing forces. Equipped with a digital micro eyepiece on the instrument, the length of indentation can be measured directly. All testing data such as the test method, the test force value, the length of test indentation, the hardness value and the dwell time of testing force can be shown on the LCD screen. There is no need to input the value of the diagonal length for the indentation and no need to look up the hardness value from the hardness table. Therefore the read data is more accurate and operation of this instrument is easier. For details and other similar equipment, please visit our equipment website: http://www.sourceindustrialsupply.com КЛИКНЕТЕ Услуга за пронаоѓање на производи-локатор PREVIOUS PAGE
- Ultrasonic Machining, Ultrasonic Impact Grinding, Custom Manufacturing
Ultrasonic Machining, Ultrasonic Impact Grinding, Rotary Ultrasonic Machining, Non-Conventional Machining, Custom Manufacturing - AGS-TECH Inc. New Mexico, USA Ултразвучна обработка и ротациона ултразвучна обработка и мелење со ултразвучно влијание Another popular NON-CONVENTIONAL MACHINING technique we frequently use is ULTRASONIC MACHINING (UM), also widely known as ULTRASONIC IMPACT GRINDING, where material is removed from a workpiece surface by microchipping and erosion with abrasive particles using a vibrating tool oscillating at ultrasonic frequencies, aided by an abrasive slurry that flows freely between the workpiece and the tool. It differs from most other conventional machining operations because very little heat is produced. The tip of the ultrasonic machining tool is called a “sonotrode” which vibrates at amplitudes of 0.05 to 0.125 mm and frequencies around 20 kHz. The vibrations of the tip transmit high velocities to fine abrasive grains between the tool and the surface of the workpiece. The tool never contacts the workpiece and therefore the grinding pressure is rarely more than 2 pounds. This working principle makes this operation perfect for machining extremely hard and brittle materials, such as glass, sapphire, ruby, diamond, and ceramics. The abrasive grains are located within a water slurry with a concentration between 20 to 60% by volume. The slurry also acts as the carrier of the debris away from the cutting / machining region. We use as abrasive grains mostly boron carbide, aluminum oxide and silicon carbide with grain sizes ranging from 100 for roughing processes to 1000 for our finishing processes. The ultrasonic-machining (UM) technique is best suited for hard and brittle materials like ceramics and glass, carbides, precious stones, hardened steels. The surface finish of ultrasonic machining depends upon the hardness of the workpiece/tool and the average diameter of the abrasive grains used. The tool tip is generally a low-carbon steel, nickel and soft steels attached to a transducer through the toolholder. The ultrasonic-machining process utilizes the plastic deformation of metal for the tool and the brittleness of the workpiece. The tool vibrates and pushes down on the abrasive slurry containing grains until the grains impact the brittle workpiece. During this operation, the workpiece is broken down while the tool bends very slightly. Using fine abrasives, we can achieve dimensional tolerances of 0.0125 mm and even better with ultrasonic-machining (UM). Machining time depends upon the frequency at which the tool is vibrating, the grain size and hardness, and the viscosity of the slurry fluid. The less viscous the slurry fluid, the faster it can carry away used abrasive. Grain size must be equal or greater than the hardness of the workpiece. As an example we can machine multiple aligned holes 0.4 mm in diameter on a 1.2 mm wide glass strip with ultrasonic machining. Let us get a little bit into the physics of the ultrasonic machining process. Microchipping in ultrasonic machining is possible thanks to the high stresses produced by particles striking the solid surface. Contact times between particles and surfaces are very short and in the order of 10 to 100 microseconds. The contact time can be expressed as: to = 5r/Co x (Co/v) exp 1/5 Here r is the radius of the spherical particle, Co is the elastic wave velocity in the workpiece (Co = sqroot E/d) and v is the velocity that the particle hits the surface with. The force a particle exerts on the surface is obtained from the rate of change of momentum: F = d(mv)/dt Here m is the grain mass. The average force of the particles (grains) hitting and rebounding from the surface is: Favg = 2mv / to Here to is the contact time. When numbers are plugged into this expression, we see that even though the parts are very small, since the contact area is also very small, the forces and thus the stresses exerted are significantly high to cause microchipping and erosion. ROTARY ULTRASONIC MACHINING (RUM): This method is a variation of ultrasonic machining, where we replace the abrasive slurry with a tool that has metal-bonded diamond abrasives that have been either impregnated or electroplated on the tool surface. The tool is rotated and ultrasonically vibrated. We press the workpiece at constant pressure against the rotating and vibrating tool. The rotary ultrasonic machining process gives us capabilities such as producing deep holes in hard materials at high material removal rates. Since we deploy a number of conventional and non-conventional manufacturing techniques, we can be of help to you whenever you have questions about a particular product and the fastest and most economical way of manufacturing & fabricating it. КЛИКНЕТЕ Услуга за пронаоѓање на производи-локатор ПРЕТХОДНА СТРАНИЦА
- Automation and Intelligent Systems, Artificial Intelligence, AI, IoT
Automation and Intelligent Systems, Artificial Intelligence, AI, Embedded Systems, Internet of Things, IoT, Industrial Control Systems, Automatic Control, Janz Автоматизација и интелигентни системи AUTOMATION also referred to as AUTOMATIC CONTROL, is the use of various CONTROL SYSTEMS for operating equipment such as factory machines, heat treating and curing ovens, telecommunication equipment, …etc. with minimal or reduced human intervention. Automation is achieved by using various means including mechanical, hydraulic, pneumatic, electrical, electronic and computers in combination. An INTELLIGENT SYSTEM on the other hand is a machine with an embedded, Internet-connected computer that has the capability to gather and analyze data and communicate with other systems. Intelligent systems require security, connectivity, ability to adapt according to current data, capability for remote monitoring and management. EMBEDDED SYSTEMS are powerful and capable of complex processing and data analysis usually specialized for tasks relevant to the host machine. Intelligent systems are all around in our daily lives. Examples are traffic lights, smart meters, transportation systems and equipment, digital signage. Some brand name products we sell are ATOP TECHNOLOGIES, JANZ TEC, KORENIX, ICP DAS, DFI-ITOX. AGS-TECH Inc. offers you products that you can readily purchase from stock and integrate into your automation or intelligent system as well as custom products designed specifically for your application. As the most diverse ENGINEERING INTEGRATION provider we pride ourselves with our capability to provide a solution for almost any automation or intelligent system needs. Besides products, we are here for your consulting and engineering needs. CLICK ON BLUE COLORED TEXT BELOW TO DOWNLOAD OUR PRODUCT BROCHURES AND CATALOGS: - ATOP TECHNOLOGIES compact product brochure - ATOP Technologies Product List 2021) - Barcode and Fixed Mount Scanners - RFID Products - Mobile Computers - Micro Kiosks OEM Technology (We private label these with your brand name and logo if you wish) - Barcode Scanners (We private label these with your brand name and logo if you wish) - Catalog for Vandal-Proof IP65/IP67/IP68 Keyboards, Keypads, Pointing Devices, ATM Pinpads, Medical & Military Keyboards and other similar Rugged Computer Peripherals - DFI-ITOX brand embedded single board computers brochure - Fixed Industrial Scanners (We private label these with your brand name and logo if you wish) - ICP DAS brand industrial communication and networking products brochure - ICP DAS brand Industrial Touch Pad brochure - ICP DAS brand machine automation brochure - ICP DAS brand PACs Embedded Controllers & DAQ brochure - ICP DAS brand PCI Boards and IO Cards - ICP DAS brand Remote IO Modules and IO Expansion Units brochure - JANZ TEC brand compact product brochure - Kiosk Systems (We private label these with your brand name and logo if you wish) - Kiosk Systems Accessories Guide (We private label these with your brand name and logo if you wish) - KORENIX brand compact product brochure - Mobile Computers for Enterprises (We private label these with your brand name and logo if you wish) - Printers for Barcode Scanners and Mobile Computers (We private label these with your brand name and logo if you wish) - RFID Readers - Scanners - Encoders - Printers (We private label these with your brand name and logo if you wish) Dowload brochure for our DESIGN PARTNERSHIP PROGRAM Industrial control systems are computer-based systems to monitor and control industrial processes. Some of our INDUSTRIAL CONTROL SYSTEMS (ICS) are: - Supervisory Control and Data Acquisition (SCADA) Systems : These systems operate with coded signals over communication channels to provide control of remote equipment, generally using one communication channel per remote station. The control systems may be combined with data acquisition systems by adding the use of coded signals over communication channels to acquire information about the status of the remote equipment for display or for recording functions. SCADA systems are different from other ICS systems by being large-scale processes that can include multiple sites over large distances. SCADA systems can control industrial processes such as manufacturing and fabrication, infrastructure processes such as transport of oil & gas, electric power transmission, and facility-based processes such as monitoring & control of heating, ventilation, air conditioning systems. - Distributed Control Systems (DCS) : A type of automated control system that is distributed throughout a machine to provide instructions to different parts of the machine. Contrary to having a centrally located device controlling all machines, in distributed control systems each section of a machine has its own computer that controls the operation. DCS systems are commonly used in manufacturing equipment, utilizing input and output protocols to control the machine. Distributed Control Systems typically use custom designed processors as controllers. Both proprietary interconnections as well as standard communications protocols are used for communication. Input and output modules are the component parts of a DCS. Input and output signals may be either analog or digital. Buses connect the processor and modules through multiplexers and demultiplexers. They also connect the distributed controllers with the central controller and to the Human–machine interface. DCS are frequently used in: -Petrochemical and chemical plants -Power plant systems, boilers, nuclear power plants -Environmental control systems -Water management systems -Metal manufacturing plants - Programmable Logic Controllers (PLC) : A Programmable Logic Controller is a small computer with a built-in operating system made primarily to control machinery. PLCs operating systems are specialized to handle incoming events in real time. Programmable Logic Controllers can be programmed. A program is written for the PLC which turns on and off outputs based on input conditions and the internal program. PLCs have input lines where sensors are connected to notify events (such as temperature being above/below a certain level, liquid level reached,… etc.), and output lines to signal any reaction to the incoming events (such as start the engine, open or close a specific valve,… etc.). Once a PLC is programmed, it can run repeatedly as needed. PLCs are found inside of machines in industrial environments and can run automatic machines for many years with little human intervention. They are designed for harsh environments. Programmable Logic Controllers are used extensively in process-based industries, they are computer-based solid-state devices that control industrial equipment and processes. Even though PLCs can control system components used in SCADA and DCS systems, they are often the primary components in smaller control systems. CLICK Product Finder-Locator Service ПРЕТХОДНА СТРАНИЦА
- Industrial Workstations, Industrial Computer, Micro Computers,AGS-TECH
Industrial Workstations - Industrial Computer - Micro Computers - AGS-TECH Inc. - NM - USA Индустриски работни станици и микро компјутери A WORKSTATION is a high-end MICROCOMPUTER designed and used for technical or scientific applications. The intention is that they are used by one person at a time, and are commonly connected to a local area network (LAN) and run multi-user operating systems. The term workstation has also been used by many to refer to a mainframe computer terminal or a PC connected to a network. In the past, workstations had offered higher performance than desktop computers, especially with respect to CPU and graphics, memory capacity and multitasking capability. Workstations are optimized for the visualization and manipulation of different types of complex data such as 3D mechanical design, engineering simulation (such as computational fluid dynamics), animation and rendering of images, mathematical plots…etc. Consoles consist at least of a high resolution display, a keyboard and a mouse, but may also offer multiple displays, graphics tablets, 3D mice (devices for manipulation and navigation of 3D objects and scenes), etc. Workstations are the first segment of the computer market to present advanced accessories and collaboration tools. Catalog for Vandal-Proof IP65/IP67/IP68 Keyboards, Keypads, Pointing Devices, ATM Pinpads, Medical & Military Keyboards and other similar Rugged Computer Peripherals To choose a suitable Industrial Workstation for your project, please go to our industrial computer store by CLICKING HERE. We offer both off-the-shelf as well as CUSTOM DESIGNED AND MANUFACTURED INDUSTRIAL WORKSTATIONS for industrial use. For mission critical applications we design and manufacture your industrial workstations according to your specific needs. We discuss your needs and requirements and provide you feedback and design proposals prior to building your computer system. We select one of a variety of rugged enclosures and determine the right computing horsepower that meets your needs. Industrial workstations can be supplied with active and passive PCI Bus backplanes that can be configured to support your ISA cards. Our spectrum covers from small 2 – 4 slot benchtop systems up to 2U, 4U or higher rackmount systems. We offer NEMA / IP RATED FULLY ENCLOSEDworkstations. Our industrial workstations outperform similar competitors systems in terms of the quality standards they meet, reliability, durability, long term use and are used in a variety of industries including the military, navy, marine, petroleum & gas, industrial processing, medical, pharmaceutical, transportation and logistics, semiconductor manufacturing. They are designed to be used in a wide variety of environmental conditions and industrial applications that require additional protection from dirt, dust, rain, sprayed water and other circumstances where corrosive materials such as salt water or caustic substances can be present. Our heavy-duty, ruggedly-built LCD computers and workstations are an ideal and dependable solution for use in poultry, fish or beef processing facilities where total wash-down with disinfectants occurs repeatedly, or in petrochemical refineries and offshore drilling platforms for oil & natural gas. Our NEMA 4X (IP66) models are gasket sealed and constructed from 316 stainless steel. Each system is engineered and assembled according to a completely sealed design using top quality 316 stainless steel for the outer enclosure and high-tech components inside each rugged PC. They come equipped with industrial grade bright TFT displays and resistive analog industrial touch-screens. Here we list some of the features of our popular industrial workstations: - Water and dust proof, corrosion resistant. Integrated with water proof keyboards - Rugged enclosed workstation, rugged motherboards - NEMA 4 (IP65) or NEMA 4X (IP66) environmental protection - Flexibility and options in mounting. Mounting types such as pedestal, bulkhead…etc. - Direct or KVM cabling to host - Powered by Intel Dual-Core or Atom processors - SATA fast access disk drive or solid state media - Windows or Linux operating systems - Expandability - Extended operational temperatures - Depending on customer preferences, input connectors can be located on the bottom, side or rear. - Models available in 15.0”, 17” & 19.0” - Superior sunlight readability - Integrated purge system for C1D1 applications as well as non-purged C1D2 designs - UL, CE, FC, RoHS, MET compliances Dowload brochure for our DESIGN PARTNERSHIP PROGRAM КЛИКНЕТЕ Услуга за пронаоѓање на производи-локатор ПРЕТХОДНА СТРАНИЦА