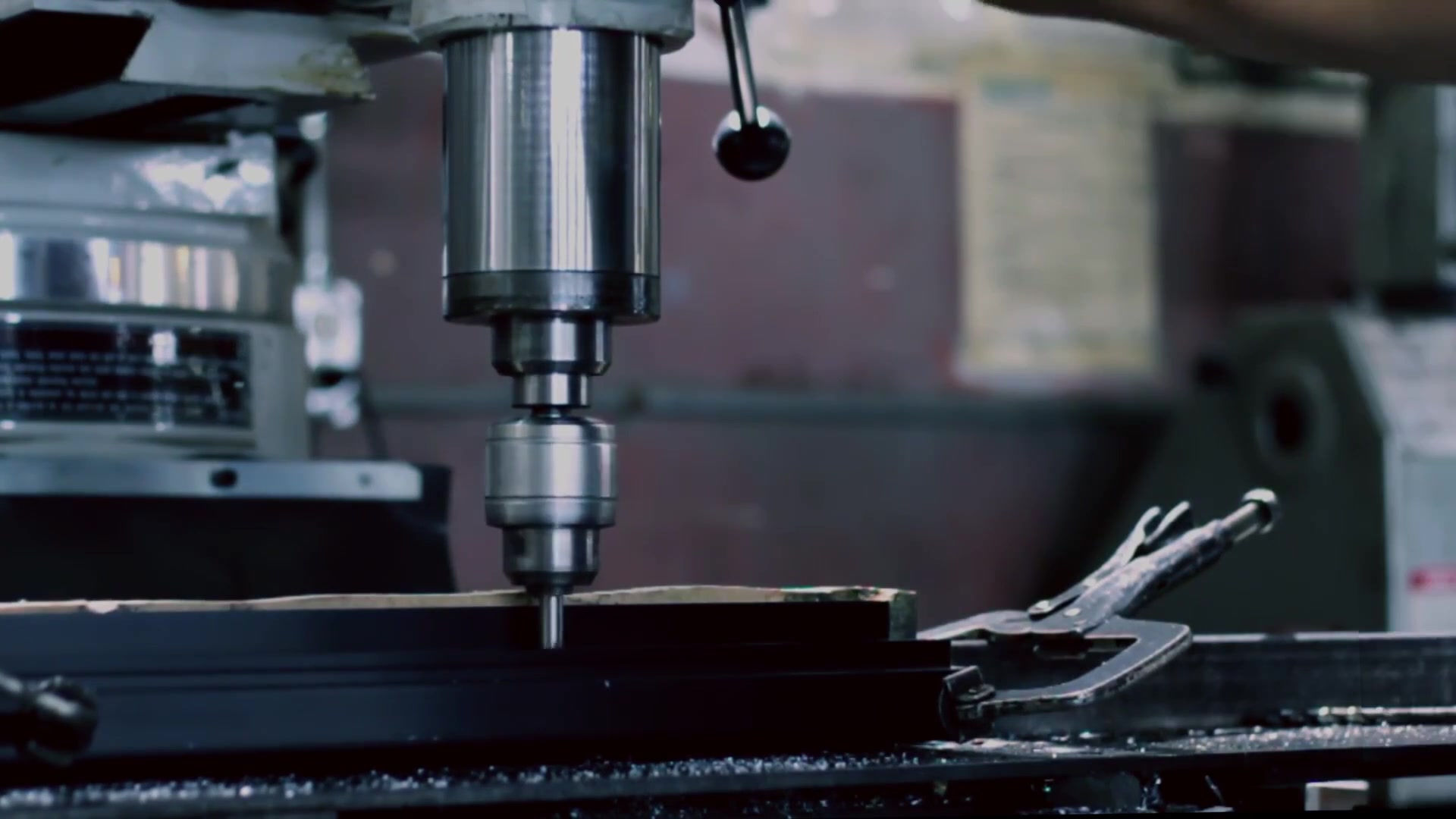
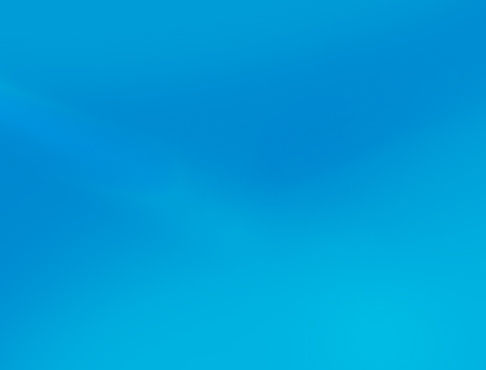
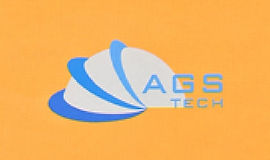
Maailmanlaajuinen räätälöity valmistaja, integraattori, yhdistäjä, ulkoistuskumppani laajalle valikoimalle tuotteita ja palveluita.
Olemme keskitetty lähde räätälöityjen ja valmiiden tuotteiden ja palvelujen valmistukseen, valmistukseen, suunnitteluun, konsolidointiin, integrointiin ja ulkoistamiseen.
Valitse kielesi
-
Räätälöity valmistus
-
Kotimainen ja kansainvälinen sopimusvalmistus
-
Valmistuksen ulkoistaminen
-
Kotimaiset ja maailmanlaajuiset hankinnat
-
Consolidation
-
Tekninen integrointi
-
Suunnittelupalvelut
Räätälöidyt valu- ja koneistustekniikkamme ovat kulutus- ja ei-kuluvat valut, rauta- ja ei-rautametallivalut, hiekka-, muotti-, keskipako-, jatkuva-, keraaminen muotti, investointi, kadonnut vaahto, lähes verkkomuoto, pysyvä muotti (painovoimavalu), kipsi muotit (kipsivalu) ja vaippavalut, koneistetut osat, jotka valmistetaan jyrsinnällä ja sorvauksella tavanomaisilla sekä CNC-laitteilla, sveitsiläinen koneistus korkean suorituskyvyn halpoja pieniä tarkkuusosia varten, ruuvityöstö kiinnikkeille, ei-perinteinen koneistus. Muista, että metallien ja metalliseosten lisäksi koneistamme myös keraamisia, lasi- ja muovikomponentteja joissain tapauksissa, kun muotin valmistus ei ole houkuttelevaa tai vaihtoehto. Polymeerimateriaalien työstö vaatii erikoiskokemusta, joka meillä on, koska muovit ja kumi asettavat haasteeseen pehmeyden, jäykkyyden jne. vuoksi. Katso lisätietoja keramiikan ja lasin koneistamisesta sivultamme Ei-perinteinen valmistus. AGS-TECH Inc. valmistaa ja toimittaa sekä kevyitä että raskaita valukappaleita. Olemme toimittaneet metallivaluja ja koneistettuja osia kattiloihin, lämmönvaihtimiin, autoihin, mikromoottoreihin, tuuliturbiineihin, elintarvikepakkauslaitteisiin ja muihin. Suosittelemme, että napsautat tätä LATAA AGS-TECH Inc:n kaaviomaiset kuvaukset koneistus- ja valuprosesseista.
Tämä auttaa sinua ymmärtämään paremmin alla tarjoamamme tiedot. Katsotaanpa joitain tarjoamistamme erilaisista tekniikoista yksityiskohtaisesti:
• KÄYTETTÄVÄN MUOTTIEN VALU: Tämä laaja luokka viittaa menetelmiin, joissa käytetään väliaikaisia ja kertakäyttöisiä muotteja. Esimerkkejä ovat hiekka, kipsi, kuori, investointi (kutsutaan myös kadonneeksi vahaksi) ja kipsivalu.
• HIEKAN VALU: Prosessi, jossa hiekkaa käytetään muottimateriaalina. Hyvin vanha menetelmä ja edelleen erittäin suosittu siinä määrin, että suurin osa valmistetuista metallivaluista on valmistettu tällä tekniikalla. Alhaiset kustannukset jopa pienillä tuotantomäärillä. Soveltuu pienten ja suurten osien valmistukseen. Tekniikalla voidaan valmistaa osia muutamassa päivässä tai viikossa hyvin pienin investoinnein. Kostea hiekka liimataan yhteen käyttämällä savea, sideaineita tai erikoisöljyjä. Hiekka sisältyy yleensä muottilaatikoihin ja ontelo- ja porttijärjestelmät luodaan tiivistämällä hiekkaa mallien ympärille. Prosessit ovat:
1.) Mallin asettaminen hiekkaan muotin valmistamiseksi
2.) Mallin ja hiekan liittäminen porttijärjestelmään
3.) Mallin poistaminen
4.) Muotin ontelon täyttö sulalla metallilla
5.) Metallin jäähdytys
6.) Hiekkamuotin rikkominen ja valukappaleen poistaminen
• KIPSIMUOTTIVALUN : Hiekan sijasta muottimateriaalina käytetään kipsiä. Lyhyet tuotannon läpimenoajat kuten hiekkavalu ja edullinen. Hyvät mittatoleranssit ja pintakäsittely. Sen suurin haitta on, että sitä voidaan käyttää vain alhaisen sulamispisteen metallien, kuten alumiinin ja sinkin, kanssa.
• SHELL MUOTTAVALU: Samanlainen kuin hiekkavalu. Muotin onkalo saadaan karkaistulla hiekkakuorella ja lämpökovettuvalla hartsisideaineella hiekalla täytetyn pullon sijaan kuten hiekkavaluprosessissa. Melkein mikä tahansa hiekkavalattavaksi sopiva metalli voidaan valaa kuorivalulla. Prosessi voidaan tiivistää seuraavasti:
1.) Kuorimuotin valmistus. Käytetty hiekka on paljon pienempää raekokoa verrattuna hiekkavalussa käytettävään hiekkaan. Hieno hiekka sekoitetaan lämpökovettuvan hartsin kanssa. Metallikuvio on päällystetty irrotusaineella kuoren poistamisen helpottamiseksi. Tämän jälkeen metallikuvio kuumennetaan ja hiekkaseos huokotetaan tai puhalletaan kuumavalukuvion päälle. Kuvion pintaan muodostuu ohut kuori. Tämän kuoren paksuutta voidaan säätää vaihtelemalla aikaa, jonka hiekkahartsiseos on kosketuksissa metallikuvion kanssa. Irtonainen hiekka poistetaan sitten kuoren peittämän kuvion jälkeen.
2.) Seuraavaksi kuori ja kuvio kuumennetaan uunissa niin, että kuori kovettuu. Kun kovettuminen on valmis, kuori irrotetaan kuviosta käyttämällä kuvioon sisäänrakennettuja tappeja.
3.) Kaksi tällaista kuorta kootaan yhteen liimaamalla tai puristamalla, ja ne muodostavat täydellisen muotin. Nyt vaippamuotti työnnetään säiliöön, jossa se on tuettu hiekalla tai metallikuulilla valuprosessin aikana.
4.) Nyt kuuma metalli voidaan kaataa kuori muottiin.
Vaippavalun etuja ovat tuotteet, joissa on erittäin hyvä pintakäsittely, mahdollisuus valmistaa monimutkaisia osia suurella mittatarkkuudella, prosessi on helppo automatisoida, taloudellinen suuriin tuotantomääriin.
Haittapuolena on, että muotit edellyttävät hyvää ilmanvaihtoa kaasujen vuoksi, joita syntyy sulan metallin kosketuksessa sideainekemikaaliin, lämpökovettuvat hartsit ja metallikuviot ovat kalliita. Metallikuvioiden hinnasta johtuen tekniikka ei välttämättä sovellu pieniin tuotantomääriin.
• INVESTOINNUSVALUN (tunnetaan myös nimellä LOST-WAX CASTING): Myös hyvin vanha tekniikka ja soveltuu laadukkaiden osien valmistukseen suurella tarkkuudella, toistettavuudella, monipuolisuudella ja eheydellä monista metalleista, tulenkestävistä materiaaleista ja erityisistä korkean suorituskyvyn metalliseoksista. Voidaan valmistaa niin pieniä kuin suuriakin osia. Kallis prosessi verrattuna joihinkin muihin menetelmiin, mutta suuri etu on mahdollisuus valmistaa osia, joilla on lähes verkkomuoto, monimutkaiset ääriviivat ja yksityiskohdat. Joten kustannuksia kompensoi jossain tapauksissa uudelleentyöstön ja koneistuksen poistaminen. Vaikka vaihteluita voi olla, tässä on yhteenveto yleisestä sijoitusprosessista:
1.) Alkuperäisen mestarikuvion luominen vahasta tai muovista. Jokainen valu tarvitsee yhden kuvion, koska ne tuhoutuvat prosessissa. Myös muottia, josta kuvioita valmistetaan, tarvitaan ja useimmiten muotti valetaan tai koneistetaan. Koska muottia ei tarvitse avata, voidaan saavuttaa monimutkaisia valukappaleita, monia vahakuvioita voidaan yhdistää kuten puun oksia ja kaataa yhteen, mikä mahdollistaa useiden osien valmistamisen yhdestä metallin tai metalliseoksen kaatamisesta.
2.) Seuraavaksi kuvio kastetaan tai kaadetaan tulenkestävällä lietteellä, joka koostuu erittäin hienorakeisesta piidioksidista, vedestä ja sideaineista. Tämä johtaa keraamiseen kerrokseen kuvion pinnalle. Kuvion tulenkestävä pinnoite jätetään kuivumaan ja kovettumaan. Tästä vaiheesta tulee nimi investointivalu: Tulenkestävä liete sijoitetaan vahakuvion päälle.
3.) Tässä vaiheessa kovettunut keraaminen muotti käännetään ylösalaisin ja kuumennetaan niin, että vaha sulaa ja valuu ulos muotista. Jäljelle jätetään onkalo metallivalua varten.
4.) Kun vaha on poistunut, keraaminen muotti kuumennetaan vielä korkeampaan lämpötilaan, mikä johtaa muotin vahvistumiseen.
5.) Metallivalu kaadetaan kuumaan muottiin täyttäen kaikki monimutkaiset osat.
6.) Valun annetaan jähmettyä
7.) Lopuksi keraaminen muotti rikotaan ja valmistetut osat leikataan puusta.
Tässä on linkki Investment Casting Plant -esitteeseen
• HAISUUSKUVIOINNIN VALU: Prosessissa käytetään kuviota, joka on valmistettu materiaalista, kuten polystyreenivaahdosta, joka haihtuu, kun kuumaa sulaa metallia kaadetaan muottiin. Tätä prosessia on kahta tyyppiä: LOST FOAM CASTING, jossa käytetään sitomatonta hiekkaa, ja FULL MOLD CASTING, jossa käytetään sidottua hiekkaa. Tässä ovat yleiset prosessin vaiheet:
1.) Valmista kuvio materiaalista, kuten polystyreenistä. Kun valmistetaan suuria määriä, kuvio muovataan. Jos osalla on monimutkainen muoto, useita tällaisen vaahtomateriaalin osia on ehkä liitettävä yhteen kuvion muodostamiseksi. Usein pinnoitamme kuvion tulenkestävällä seoksella hyvän pinnan viimeistelyn aikaansaamiseksi.
2.) Kuvio laitetaan sitten muovaushiekkaan.
3.) Sula metalli kaadetaan muottiin haihduttamalla vaahtomuovikuvio eli polystyreeni useimmissa tapauksissa sen virratessa muotin ontelon läpi.
4.) Sula metalli jätetään hiekkamuottiin kovettumaan.
5.) Kun se on kovettunut, poistamme valukappaleen.
Joissakin tapauksissa valmistamamme tuote vaatii ytimen kuviossa. Haihdutusvalussa ydintä ei tarvitse asettaa ja kiinnittää muottipesään. Tekniikka soveltuu erittäin monimutkaisten geometrioiden valmistukseen, se on helposti automatisoitavissa suuria volyymeja varten, eikä valuosassa ole jakolinjoja. Perusprosessi on yksinkertainen ja taloudellinen toteuttaa. Suuren volyymin tuotannossa, koska kuvioiden valmistamiseksi polystyreenistä tarvitaan muotti tai muotti, tämä voi olla jonkin verran kallista.
• EI LAAJENNETTUVA MUOTTIEN VALU: Tämä laaja luokka viittaa menetelmiin, joissa muottia ei tarvitse uudistaa jokaisen tuotantosyklin jälkeen. Esimerkkejä ovat kesto-, paine-, jatkuva- ja keskipakovalu. Toistettavuus saavutetaan ja osat voidaan luonnehtia LÄHELLÄ VERKKOMUOKSI.
• PYSYVÄ MUOTTAVALU: Metallista valmistettuja uudelleenkäytettäviä muotteja käytetään useisiin valuihin. Pysyvää muottia voidaan yleensä käyttää kymmeniä tuhansia kertoja ennen kuin se kuluu loppuun. Muotin täyttämiseen käytetään yleensä painovoimaa, kaasun painetta tai tyhjiötä. Muotit (kutsutaan myös suulakkeiksi) on yleensä valmistettu raudasta, teräksestä, keraamisesta tai muista metalleista. Yleinen prosessi on:
1.) Kone ja luo muotti. On tavallista työstää muotti kahdesta metallikappaleesta, jotka sopivat yhteen ja voidaan avata ja sulkea. Sekä osien ominaisuudet että porttijärjestelmä koneistetaan yleensä valumuottiin.
2.) Sisäiset muotin pinnat on päällystetty lietteellä, joka sisältää tulenkestäviä materiaaleja. Tämä auttaa säätelemään lämmön virtausta ja toimii voiteluaineena, joka helpottaa valuosan irrottamista.
3.) Seuraavaksi pysyvät muotin puolikkaat suljetaan ja muotti kuumennetaan.
4.) Sula metalli kaadetaan muottiin ja annetaan rauhassa jähmettyä.
5.) Ennen kuin paljon jäähtymistä tapahtuu, poistamme osan pysyvästä muotista ejektoreilla, kun muotin puolikkaat avataan.
Käytämme usein pysyvää muottivalua matalan sulamispisteen metalleille, kuten sinkille ja alumiinille. Teräsvaluissa käytämme muottimateriaalina grafiittia. Joskus saamme monimutkaisia geometrioita käyttämällä kestäviä muotteja sisältäviä ytimiä. Tämän tekniikan etuja ovat valut, joilla on hyvät mekaaniset ominaisuudet, jotka saadaan nopealla jäähdytyksellä, ominaisuuksien tasaisuus, hyvä tarkkuus ja pinnan viimeistely, alhaiset hylkäysnopeudet, mahdollisuus automatisoida prosessi ja tuottaa suuria määriä taloudellisesti. Haittoja ovat korkeat alkuasennuskustannukset, jotka tekevät siitä sopimattomaksi pienikokoisiin toimintoihin, ja valmistettujen osien koon rajoitukset.
• SULAVALUS: Muotti työstetään ja sula metalli työnnetään korkealla paineella muotin onteloihin. Sekä ei-rautametallien että rautametallien painevalut ovat mahdollisia. Prosessi soveltuu suurten määrien tuotantosarjoihin pienistä ja keskikokoisista osista, joissa on yksityiskohdat, erittäin ohuet seinät, mittojen tasaisuus ja hyvä pintakäsittely. AGS-TECH Inc. pystyy valmistamaan tällä tekniikalla jopa 0,5 mm:n seinämän paksuuksia. Kuten pysyvässä muottivalussa, muotin tulee koostua kahdesta puolikkaasta, jotka voivat avautua ja sulkeutua valmistetun osan poistamiseksi. Painevalumuotissa voi olla useita onteloita, jotta voidaan tuottaa useita valukappaleita kullakin syklillä. Painevalumuotit ovat erittäin raskaita ja paljon suurempia kuin niiden valmistamat osat, joten myös kalliita. Korjaamme ja vaihdamme kuluneet muotit asiakkaillemme maksutta niin kauan kuin he tilaavat osansa meiltä. Suulakkeillamme on pitkä käyttöikä useiden satojen tuhansien syklien alueella.
Tässä on yksinkertaistetun prosessin perusvaiheet:
1.) Muotin valmistus yleensä teräksestä
2.) Muotti asennettu painevalukoneeseen
3.) Mäntä pakottaa sulan metallin virtaamaan suulakkeen onteloissa täyttäen monimutkaiset piirteet ja ohuet seinät
4.) Kun muotti on täytetty sulalla metallilla, valukappaleen annetaan kovettua paineen alaisena
5.) Muotti avataan ja valu poistetaan ejektorin tappien avulla.
6.) Nyt tyhjät suuttimet voidellaan uudelleen ja ne kiinnitetään seuraavaa sykliä varten.
Painevalussa käytämme usein puristusmuovausta, jossa lisäämme muottiin lisäosan ja valetaan metalli sen ympärille. Kiinteytymisen jälkeen näistä osista tulee osa valutuotetta. Painevalun etuja ovat osien hyvät mekaaniset ominaisuudet, monimutkaisten ominaisuuksien mahdollisuus, hienot yksityiskohdat ja hyvä pintakäsittely, korkeat tuotantonopeudet, helppo automatisointi. Haitat ovat: Ei kovin sopiva pieneen tilavuuteen korkeiden muotti- ja laitekustannusten vuoksi, valaettavien muotojen rajoitukset, pienet pyöreät jäljet valuosissa, jotka johtuvat ejektorin tappien kosketuksesta, ohut metallin välähdys irtoamislinjasta, tarve suuttimen välisen jakolinjan tuuletusaukkojen osalta tarve pitää muotin lämpötilat alhaisina käyttämällä veden kiertoa.
• KESKIPAKOVALUN : Sula metalli kaadetaan pyörivän muotin keskelle pyörimisakselin kohdalta. Keskipakovoimat heittävät metallin reunaa kohti ja sen annetaan jähmettyä muotin pyöriessä. Voidaan käyttää sekä vaaka- että pystyakselin kiertoa. Osat, joissa on pyöreä sisäpinta, sekä muita ei-pyöreitä muotoja voidaan valaa. Prosessi voidaan tiivistää seuraavasti:
1.) Sula metalli kaadetaan keskipakomuottiin. Sitten metalli pakotetaan ulkoseiniin muotin pyörimisen vuoksi.
2.) Kun muotti pyörii, metallivalu kovettuu
Keskipakovalu on sopiva tekniikka onttojen sylinterimäisten osien, kuten putkien, valmistukseen, ei tarvita putkia, nousuputkia ja porttielementtejä, hyvä pinnan viimeistely ja yksityiskohtaiset ominaisuudet, ei kutistumisongelmia, mahdollisuus valmistaa pitkiä putkia, joilla on erittäin suuri halkaisija, korkea tuotantokapasiteetti .
• JATKUVA VALU ( STRAND CASTING ): Käytetään jatkuvan metallin valumiseen. Periaatteessa sula metalli valetaan muotin kaksiulotteiseen profiiliin, mutta sen pituus on määrittelemätön. Uutta sulaa metallia syötetään jatkuvasti muottiin, kun valu kulkee alaspäin pituuden kasvaessa ajan myötä. Metallit, kuten kupari, teräs ja alumiini, valetaan pitkiksi säikeiksi jatkuvalla valuprosessilla. Prosessilla voi olla useita konfiguraatioita, mutta yleinen voidaan yksinkertaistaa seuraavasti:
1.) Sula metalli kaadetaan korkealla muotin yläpuolella olevaan astiaan hyvin lasketuilla määrillä ja virtausnopeuksilla ja virtaa vesijäähdytetyn muotin läpi. Muottiin kaadettu metallivalu jähmettyy muotin pohjalle sijoitetuksi starttitankoon. Tämä aloitustanko antaa teloille jotain tarttua aluksi.
2.) Rullat kantavat pitkää metallinauhaa tasaisella nopeudella. Telat muuttavat myös metallisäikeen virtaussuuntaa pystysuorasta vaakasuoraan.
3.) Kun jatkuva valu on kulkenut tietyn vaakamatkan, valun mukana liikkuva taskulamppu tai saha leikkaa sen nopeasti haluttuihin pituuksiin.
Jatkuva valuprosessi voidaan integroida ROLLING PROCESSiin, jossa jatkuvasti valettu metalli voidaan syöttää suoraan valssaamolle I-palkkien, T-palkkien jne. valmistamiseksi. Jatkuva valu tuottaa yhtenäiset ominaisuudet koko tuotteelle, sillä on korkea jähmettymisnopeus, se alentaa kustannuksia erittäin alhaisen materiaalihäviön vuoksi, tarjoaa prosessin, jossa metallin kuormaus, kaataminen, jähmettyminen, leikkaus ja valun poisto tapahtuvat jatkuvassa toiminnassa ja tuloksena on korkea tuottavuus ja korkea laatu. Tärkeä näkökohta on kuitenkin korkea alkuinvestointi, asennuskustannukset ja tilantarve.
• TYÖSTÖPALVELUT: Tarjoamme kolmen, neljän ja viiden akselin koneistusta. Käyttämämme työstöprosesseja ovat SORVAUS, JYRSINTÄ, PORAUS, PORAUS, AVENEMINEN, HÖYLÄYS, SAHAUS, HIOMAUS, LIPOTUS, KIOLTO ja EI-PERINTEINEN TYÖSTÖ, jota käsitellään tarkemmin verkkosivustomme eri valikoissa. Käytämme suurimmassa osassa tuotannostamme CNC-koneita. Kuitenkin joihinkin operaatioihin perinteiset tekniikat sopivat paremmin ja siksi luotamme myös niihin. Koneistuskykymme saavuttavat korkeimman mahdollisen tason ja jotkin vaativimmat osat valmistetaan AS9100-sertifioidussa tehtaassa. Suihkumoottorien siivet vaativat erittäin erikoistuneen valmistuskokemuksen ja oikean laitteiston. Ilmailuteollisuudella on erittäin tiukat standardit. Jotkut komponentit, joilla on monimutkainen geometrinen rakenne, on helpoimmin valmistaa viisiakselisella työstyksellä, jota löytyy vain joistakin koneistuslaitoksista, mukaan lukien meidän. Ilmailu-sertifioidulla tehtaallamme on tarvittava kokemus ilmailuteollisuuden laajan dokumentointivaatimuksen mukaisesti.
KORVAUStoiminnoissa työkappaletta pyöritetään ja liikutetaan leikkaustyökalua vasten. Tätä prosessia varten käytetään konetta nimeltä sorvi.
JYRSINTÄ koneessa, jota kutsutaan jyrsintäkoneeksi, on pyörivä työkalu, joka tuo leikkuureunat vasten työkappaletta.
PORAUStoiminnot sisältävät pyörivän leikkurin, jossa on leikkuureunat, jotka muodostavat reikiä joutuessaan kosketuksiin työkappaleen kanssa. Yleensä käytetään poranpuristimia, sorveja tai myllyjä.
PORAUSoperaatioissa työkalu, jossa on yksi taivutettu teräväkärkinen kärki, siirretään pyörivän työkappaleen karkeaan reikään, mikä suurentaa hieman reikää ja parantaa tarkkuutta. Sitä käytetään hienoja viimeistelytarkoituksiin.
AVENNUS tarkoittaa hammastettua työkalua materiaalin poistamiseksi työkappaleesta yhdellä avennuksella (hammastyökalu). Lineaarisessa avennuksessa avennin kulkee lineaarisesti työkappaleen pintaa vasten leikkauksen aikaansaamiseksi, kun taas kiertoavennuksen yhteydessä avennin pyöritetään ja puristetaan työkappaleeseen akselisymmetrisen muodon leikkaamiseksi.
SWISS TYPE MACHINING on yksi arvokkaista tekniikoistamme, joita käytämme pienten erittäin tarkkojen osien suuren volyymin valmistukseen. Sveitsiläisen sorvin avulla sorvaamme pieniä, monimutkaisia, tarkkoja osia edullisesti. Toisin kuin perinteiset sorvit, joissa työkappale pidetään paikallaan ja työkalu liikkuu, sveitsiläisissä sorvauskeskuksissa työkappaleen annetaan liikkua Z-akselilla ja työkalu on paikallaan. Sveitsin tyyppisessä koneistuksessa tankovarasto pidetään koneessa ja viedään eteenpäin z-akselin ohjausholkin kautta, jolloin vain koneistettava osa tulee näkyviin. Näin varmistetaan tiukka pito ja tarkkuus on erittäin korkea. Jännitteisten työkalujen saatavuus tarjoaa mahdollisuuden jyrsimiseen ja poraamiseen materiaalin edetessä ohjausholkista. Sveitsin tyyppisten laitteiden Y-akseli tarjoaa täyden jyrsintäkyvyn ja säästää huomattavasti valmistusaikaa. Lisäksi koneissamme on porat ja poraustyökalut, jotka toimivat osalla, kun sitä pidetään alakarassa. Swiss-Type-työstökykymme antaa meille täysin automatisoidun täydellisen koneistuksen yhdessä työvaiheessa.
Koneistus on yksi AGS-TECH Inc:n liiketoiminnan suurimmista segmenteistä. Käytämme sitä joko ensisijaisena tai toissijaisena toimenpiteenä osan valun tai suulakepuristamisen jälkeen, jotta kaikki piirustusvaatimukset täyttyvät.
• PINNAN VIIMEISTELYPALVELUT: Tarjoamme laajan valikoiman pintakäsittelyjä ja pintakäsittelyjä, kuten pintakäsittelyä tarttuvuuden parantamiseksi, ohuen oksidikerroksen levittämistä pinnoitteen tarttuvuuden parantamiseksi, hiekkapuhallus, kemiallinen kalvo, anodisointi, nitraus, jauhemaalaus, ruiskupinnoitus , erilaisia edistyneitä metallointi- ja pinnoitustekniikoita, mukaan lukien sputterointi, elektronisuihku, haihdutus, pinnoitus, kovat pinnoitteet, kuten timantin kaltainen hiili (DLC) tai titaanipinnoite poraus- ja leikkaustyökaluihin.
• TUOTTEIDEN MERKINTÄ- JA MERKINNÄT PALVELUT: Monet asiakkaamme tarvitsevat merkintöjä ja etiketöintejä, lasermerkintöjä ja kaiverruksia metalliosiin. Jos sinulla on tällainen tarve, keskustelemme siitä, mikä vaihtoehto on sinulle paras.
Tässä on joitain yleisesti käytettyjä metallivalutuotteita. Koska nämä ovat valmiita, voit säästää muottikustannuksissa, jos jokin näistä sopii tarpeisiisi:
NAPSAUTA TÄSTÄ LATAAksesi AGS-Electronicsin 11-sarjan painevaletut alumiinilaatikot