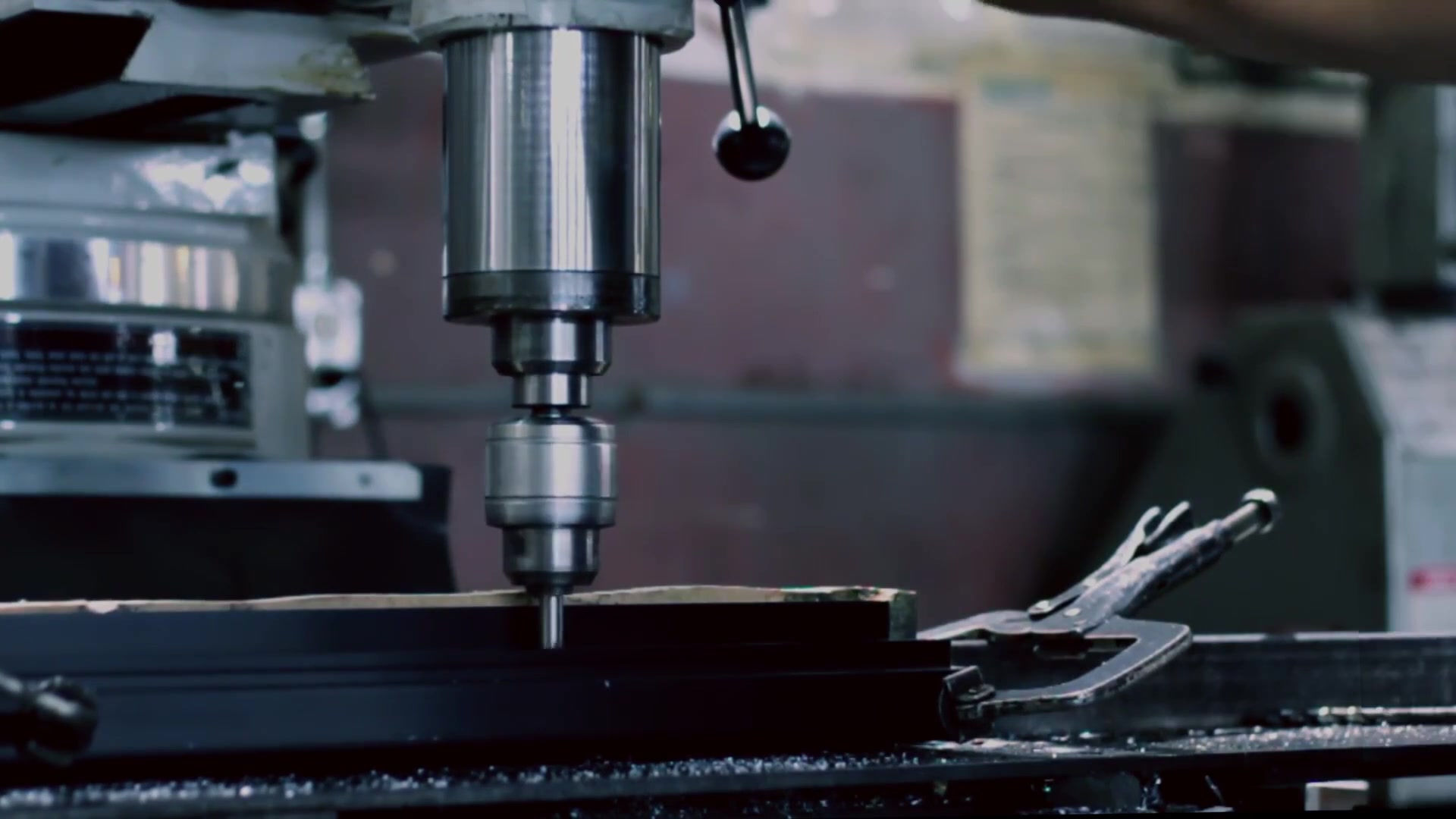
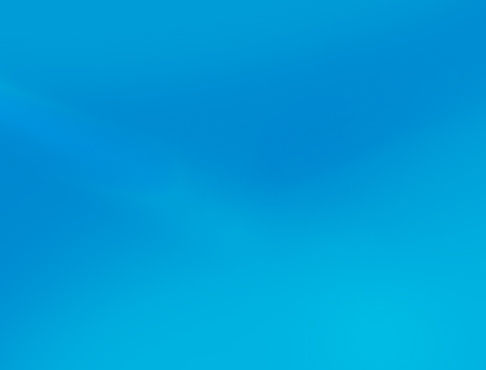
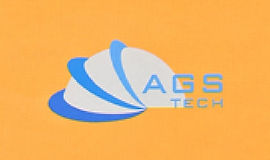
Maailmanlaajuinen räätälöity valmistaja, integraattori, yhdistäjä, ulkoistuskumppani laajalle valikoimalle tuotteita ja palveluita.
Olemme keskitetty lähde räätälöityjen ja valmiiden tuotteiden ja palvelujen valmistukseen, valmistukseen, suunnitteluun, konsolidointiin, integrointiin ja ulkoistamiseen.
Valitse kielesi
-
Räätälöity valmistus
-
Kotimainen ja kansainvälinen sopimusvalmistus
-
Valmistuksen ulkoistaminen
-
Kotimaiset ja maailmanlaajuiset hankinnat
-
Consolidation
-
Tekninen integrointi
-
Suunnittelupalvelut
LASERLEIKKAUS is a HIGH-ENERGY-BEAM MANUFACTURING_cc71f58d_hiGH-ENERGY-BEAM MANUFACTURING_cc. In LASER BEAM MACHINING (LBM), laserlähde kohdistaa optisen energian työkappaleen pintaan. Laserleikkaus ohjaa suuritehoisen laserin erittäin fokusoidun ja tiheän tehon tietokoneella leikattavaan materiaaliin. Kohdennettu materiaali joko sulaa, palaa, höyrystyy pois tai puhalletaan pois kaasusuihkun vaikutuksesta hallitusti, jolloin jäljelle jää laadukas pintakäsittely. Teolliset laserleikkurimme soveltuvat tasaisten levymateriaalien sekä rakenne- ja putkimateriaalien, metallisten ja ei-metallisten työkappaleiden leikkaamiseen. Lasersäteen työstö- ja leikkausprosesseissa ei yleensä tarvita tyhjiötä. Laserleikkauksessa ja -valmistuksessa käytetään useita lasertyyppejä. Pulssi- tai jatkuva aalto CO2 LASER soveltuu leikkaamiseen, poraukseen ja kaivertamiseen. The NEODYMIUM (Nd) and neodymium yttrium-aluminum-garnet (Nd-YAG) LASERS are identical tyyliltään ja eroavat vain sovelluksista. Neodyymi-Nd:tä käytetään poraamiseen ja missä tarvitaan paljon energiaa mutta vähän toistoa. Toisaalta Nd-YAG-laseria käytetään siellä, missä tarvitaan erittäin suurta tehoa sekä poraukseen ja kaivertamiseen. Sekä CO2- että Nd/Nd-YAG-lasereita voidaan käyttää LASERHITSAUKSEN. Muita valmistuksessa käyttämiämme lasereita ovat Nd:GLASS, RUBY ja EXCIMER. Laser Beam Machiningissa (LBM) seuraavat parametrit ovat tärkeitä: Työkappaleen pinnan heijastavuus ja lämmönjohtavuus sekä sen ominaislämpö ja piilevä sulamis- ja haihtumislämpö. Laser Beam Machining (LBM) -prosessin tehokkuus kasvaa näiden parametrien pienentyessä. Leikkaussyvyys voidaan ilmaista seuraavasti:
t ~ P / (vxd)
Tämä tarkoittaa, että leikkaussyvyys "t" on verrannollinen tehonsyöttöön P ja kääntäen verrannollinen leikkausnopeuteen v ja lasersäteen pisteen halkaisijaan d. LBM:llä valmistettu pinta on yleensä karkea ja siinä on lämpövaikutusalue.
HIILIDIOKSIDI (CO2) LASERLEIKKAUS ja TYÖSTÖ: DC-viritetyt CO2-laserit pumpataan johtamalla virtaa kaasuseoksen läpi, kun taas RF-viritetyt CO2-laserit käyttävät viritykseen radiotaajuista energiaa. RF-menetelmä on suhteellisen uusi ja siitä on tullut suositumpi. DC-mallit vaativat elektrodeja ontelon sisällä, ja siksi niissä voi olla elektrodien eroosiota ja elektrodimateriaalin pinnoitusta optiikassa. Päinvastoin, RF-resonaattoreissa on ulkoiset elektrodit, joten ne eivät ole alttiita näille ongelmille. Käytämme CO2-lasereita monien materiaalien, kuten teräksen, alumiinin, ruostumattoman teräksen, titaanin ja muovien teolliseen leikkaamiseen.
YAG-LASERLEIKKAUS and MACHINING: Käytämme YAG-lasereita metallien leikkaamiseen ja värjäykseen. Lasergeneraattori ja ulkoinen optiikka vaativat jäähdytystä. Hukkalämpö syntyy ja siirtyy jäähdytysnesteen vaikutuksesta tai suoraan ilmaan. Vesi on yleinen jäähdytysneste, jota yleensä kierrätetään jäähdyttimen tai lämmönsiirtojärjestelmän kautta.
EXCIMER LASER LEIKKAUS ja TYÖSTÖ: Excimer laser on eräänlainen laser, jonka aallonpituudet ovat ultraviolettialueella. Tarkka aallonpituus riippuu käytetyistä molekyyleistä. Esimerkiksi seuraavat aallonpituudet liittyvät suluissa esitettyihin molekyyleihin: 193 nm (ArF), 248 nm (KrF), 308 nm (XeCl), 353 nm (XeF). Jotkut eksimeerilaserit ovat viritettävissä. Excimer-lasereilla on se houkutteleva ominaisuus, että niillä voidaan poistaa erittäin hienoja kerroksia pintamateriaalia lähes ilman kuumennusta tai muuttamista materiaaliin. Siksi eksimeerilaserit soveltuvat hyvin orgaanisten materiaalien, kuten joidenkin polymeerien ja muovien, tarkkuuteen mikrotyöstöön.
KAASUTUVINEN LASERLEIKKAUS: Joskus käytämme lasersäteitä yhdessä kaasuvirran, kuten hapen, typen tai argonin, kanssa ohuiden levymateriaalien leikkaamiseen. Tämä tehdään käyttämällä a LASER-BEAM TORCHia. Ruostumattomasta teräksestä ja alumiinista käytämme korkeapaineista inerttikaasuavusteista laserleikkausta typellä. Tämä johtaa oksidivapaisiin reunoihin hitsattavuuden parantamiseksi. Nämä kaasuvirrat puhaltavat myös sulan ja höyrystyneen materiaalin pois työkappaleen pinnoilta.
Mallissa a LASER MICROJET CUTTING meillä on vesisuihkuohjattu beaser, jossa pulssipainettu lasersuihku on kytketty vesisuihkuksi. Käytämme sitä laserleikkaukseen samalla kun käytämme vesisuihkua ohjaamaan lasersädettä, kuten optista kuitua. Lasermikrosuihkun etuja ovat, että vesi poistaa myös roskat ja jäähdyttää materiaalia, se on nopeampi kuin perinteinen "kuiva" laserleikkaus korkeammalla kuutionopeudella, yhdensuuntaisella uurrella ja monisuuntaisella leikkauskyvyllä.
Käytämme laserleikkauksessa erilaisia menetelmiä. Joitakin menetelmiä ovat höyrystys, sulatus ja puhallus, sulapuhallus ja -poltto, lämpöjännityshalkeilu, piirustus, kylmäleikkaus ja poltto, stabiloitu laserleikkaus.
- Höyrystysleikkaus: Kohdistettu palkki lämmittää materiaalin pinnan kiehumispisteeseensä ja muodostaa reiän. Reikä lisää äkillistä imukykyä ja syventää reikää nopeasti. Kun reikä syvenee ja materiaali kiehuu, syntyvä höyry syövyttää sulat seinät puhaltaen materiaalia ulos ja laajentaen reikää entisestään. Tällä menetelmällä leikataan yleensä sulamattomia materiaaleja, kuten puuta, hiiltä ja kertamuovia.
- Sula- ja puhallusleikkaus: Käytämme korkeapainekaasua puhaltamaan sulaa materiaalia leikkausalueelta, mikä vähentää tarvittavaa tehoa. Materiaali kuumennetaan sulamispisteeseensä ja sitten kaasusuihku puhaltaa sulan materiaalin ulos urasta. Tämä eliminoi tarpeen nostaa materiaalin lämpötilaa enempää. Leikkaamme metalleja tällä tekniikalla.
- Lämpöjännityshalkeilu: Hauraat materiaalit ovat herkkiä lämpömurtumille. Säde kohdistuu pintaan aiheuttaen paikallista kuumenemista ja lämpölaajenemista. Tämä johtaa halkeamaan, jota voidaan sitten ohjata siirtämällä palkkia. Käytämme tätä tekniikkaa lasinleikkauksessa.
- Piikiekkojen varkain pilkkominen: Mikroelektroniikkasirujen erottaminen piikiekoista suoritetaan salaamalla paloitteluprosessilla käyttämällä pulssillista Nd:YAG-laseria, 1064 nm:n aallonpituus soveltuu hyvin piin elektroniseen kaistaväliin (1,11 eV tai 1117 nm). Tämä on suosittu puolijohdelaitteiden valmistuksessa.
- Reaktiivinen leikkaus: Tätä tekniikkaa kutsutaan myös liekkileikkaukseksi, ja se voidaan muistuttaa happipolttimen leikkaamista, mutta sytytyslähteenä on lasersäde. Käytämme tätä yli 1 mm:n paksuisten hiiliterästen ja jopa erittäin paksujen teräslevyjen leikkaamiseen pienellä laserteholla.
PULSSILASERS tarjoavat meille suuren tehon energiapurskeen lyhyeksi ajaksi ja ovat erittäin tehokkaita joissakin laserleikkausprosesseissa, kuten lävistyksessä, tai kun tarvitaan hyvin pieniä reikiä tai erittäin alhaisia leikkausnopeuksia. Jos sen sijaan käytettäisiin jatkuvaa lasersädettä, lämpö voisi saavuttaa pisteen, jossa koko työstettävä kappale sulaa. Lasereillamme on kyky pulssia tai leikata CW:tä (Continuous Wave) NC (numeerinen ohjaus) ohjelmaohjauksella. Käytämme DOUBLE PULSE LASERS emitting sarjaa pulssipareja parantaaksemme materiaalin poistonopeutta ja reiän laatua. Ensimmäinen pulssi poistaa materiaalia pinnalta ja toinen pulssi estää ulostyönnettyä materiaalia lukkiutumasta reiän tai leikkauksen sivuun.
Toleranssit ja pintakäsittely laserleikkauksessa ja koneistuksessa ovat erinomaisia. Nykyaikaisten laserleikkureiden paikannustarkkuus on noin 10 mikrometriä ja toistettavuus 5 mikrometriä. Vakiokarheus Rz kasvaa levyn paksuuden myötä, mutta pienenee lasertehon ja leikkausnopeuden myötä. Laserleikkaus- ja koneistusprosessit pystyvät saavuttamaan läheiset toleranssit, usein 0,001 tuuman (0,025 mm) tarkkuudella. Osageometria ja koneidemme mekaaniset ominaisuudet on optimoitu parhaan toleranssin saavuttamiseksi. Laserleikkauksella saatavat pintakäsittelyt voivat vaihdella välillä 0,003–0,006 mm. Yleensä saamme helposti aikaan halkaisijaltaan 0,025 mm olevia reikiä, ja jopa 0,005 mm reikiä ja reiän syvyys-halkaisijasuhde 50:1 on valmistettu eri materiaaleista. Yksinkertaisimmat ja tavallisimmat laserleikkurimme leikkaavat hiiliteräsmetallia 0,020–0,5 tuuman (0,51–13 mm) paksuudelta ja voivat olla jopa kolmekymmentä kertaa nopeampaa kuin tavallinen sahaus.
Lasersädetyöstöä käytetään laajalti metallien, ei-metallien ja komposiittimateriaalien poraamiseen ja leikkaamiseen. Laserleikkauksen etuja mekaaniseen leikkaukseen verrattuna ovat helpompi työskentely, puhtaus ja työkappaleen likaantumisen vähentäminen (koska perinteisessä jyrsinnässä tai sorvauksessa ei ole leikkaussärmää, joka voi kontaminoitua materiaalin vaikutuksesta tai saastuttaa materiaalin, ts. Komposiittimateriaalien hankaava luonne voi tehdä niistä vaikean koneistamisen perinteisillä menetelmillä, mutta helpoksi lasertyöstöllä. Koska lasersäde ei kulu prosessin aikana, saatava tarkkuus voi olla parempi. Koska laserjärjestelmissä on pieni lämpövaikutusalue, on myös pienempi mahdollisuus vääntyä leikattava materiaali. Joillekin materiaaleille laserleikkaus voi olla ainoa vaihtoehto. Lasersäteen leikkausprosessit ovat joustavia, ja kuituoptisen säteen toimitus, yksinkertainen kiinnitys, lyhyet asennusajat, kolmiulotteisten CNC-järjestelmien saatavuus mahdollistavat laserleikkauksen ja koneistuksen kilpailla menestyksekkäästi muiden ohutlevyjen valmistusprosessien, kuten lävistyksen, kanssa. Tästä huolimatta lasertekniikkaa voidaan joskus yhdistää mekaanisten valmistustekniikoiden kanssa yleisen tehokkuuden parantamiseksi.
Metallilevyjen laserleikkauksella on se etu plasmaleikkaukseen verrattuna, että se on tarkempi ja kuluttaa vähemmän energiaa, mutta useimmat teollisuuslaserit eivät pysty leikkaamaan suurempia metallipaksuuksia kuin plasma. Suuremmilla tehoilla, kuten 6000 watilla, toimivat laserit lähestyvät plasmakoneita niiden kyvyssä leikata paksuja materiaaleja. Näiden 6000 watin laserleikkureiden pääomakustannukset ovat kuitenkin paljon korkeammat kuin plasmaleikkauskoneiden, jotka pystyvät leikkaamaan paksuja materiaaleja, kuten teräslevyä.
Laserleikkauksessa ja koneistuksessa on myös haittoja. Laserleikkaus vaatii suurta virrankulutusta. Teollisuuden lasertehokkuus voi vaihdella 5 %:sta 15 %:iin. Minkä tahansa laserin virrankulutus ja hyötysuhde vaihtelevat lähtötehon ja toimintaparametrien mukaan. Tämä riippuu laserin tyypistä ja siitä, kuinka hyvin laser sopii käsillä olevaan työhön. Tiettyyn tehtävään tarvittava laserleikkaustehon määrä riippuu materiaalityypistä, paksuudesta, käytetystä prosessista (reaktiivinen/inertti) ja halutusta leikkausnopeudesta. Laserleikkauksen ja koneistuksen maksimituotantonopeutta rajoittavat useat tekijät, kuten laserin teho, prosessityyppi (joko reaktiivinen tai inertti), materiaalin ominaisuudet ja paksuus.
In LASER ABLATION poistamme materiaalia kiinteältä pinnalta säteilyttämällä sitä lasersäteellä. Pienellä laservuolla materiaali kuumenee absorboidun laserenergian vaikutuksesta ja haihtuu tai sublimoituu. Suurella laservuolla materiaali muunnetaan tyypillisesti plasmaksi. Tehokas laserit puhdistavat suuren paikan yhdellä pulssilla. Pienitehoiset laserit käyttävät monia pieniä pulsseja, jotka voidaan skannata alueen poikki. Laserablaatiossa materiaali poistetaan pulssilaserilla tai jatkuvan aallon lasersäteellä, jos laserin intensiteetti on riittävän korkea. Pulssilaserit voivat porata erittäin pieniä, syviä reikiä erittäin kovien materiaalien läpi. Erittäin lyhyet laserpulssit poistavat materiaalia niin nopeasti, että ympäröivä materiaali imee hyvin vähän lämpöä, joten laserporausta voidaan tehdä herkille tai lämpöherkille materiaaleille. Pinnoitteet voivat absorboida laserenergiaa selektiivisesti, joten CO2- ja Nd:YAG-pulssilasereita voidaan käyttää pintojen puhdistamiseen, maalin ja pinnoitteen poistamiseen tai pintojen valmisteluun maalausta varten ilman, että alla oleva pinta vahingoittuu.
We use LASER ENGRAVING and LASER MARKING to engrave or mark an object. Nämä kaksi tekniikkaa ovat itse asiassa laajimmin käytetyt sovellukset. Musteita ei käytetä, eikä siinä ole työkalunpäitä, jotka koskettavat kaiverrettua pintaa ja kuluvat, kuten perinteisissä mekaanisissa kaiverrus- ja merkintämenetelmissä. Erityisesti laserkaiverrukseen ja -merkintään suunniteltuja materiaaleja ovat laserherkät polymeerit ja erikoisuudet metalliseokset. Vaikka lasermerkintä- ja kaiverruslaitteet ovat suhteellisen kalliimpia vaihtoehtoihin, kuten rei'ityksiin, pinsseihin, kynsiin, etsausleimoihin jne. verrattuna, niistä on tullut yhä suositumpia tarkkuutensa, toistettavuutensa, joustavuutensa, automaation helppouden ja online-sovelluksen ansiosta. monenlaisissa valmistusympäristöissä.
Lopuksi käytämme lasersäteitä useisiin muihin valmistustoimintoihin:
- LASERHITSAUS
- LASERLÄMPÖKÄSITTELY: Metallien ja keramiikan pienimuotoinen lämpökäsittely niiden pintamekaanisten ja tribologisten ominaisuuksien muokkaamiseksi.
- LASER PINTAKÄSITTELY / MUOKKAUS: Lasereita käytetään pintojen puhdistamiseen, funktionaalisten ryhmien lisäämiseen, pintojen muokkaamiseen pyrittäessä parantamaan tarttuvuutta ennen pinnoitus- tai liitosprosesseja.