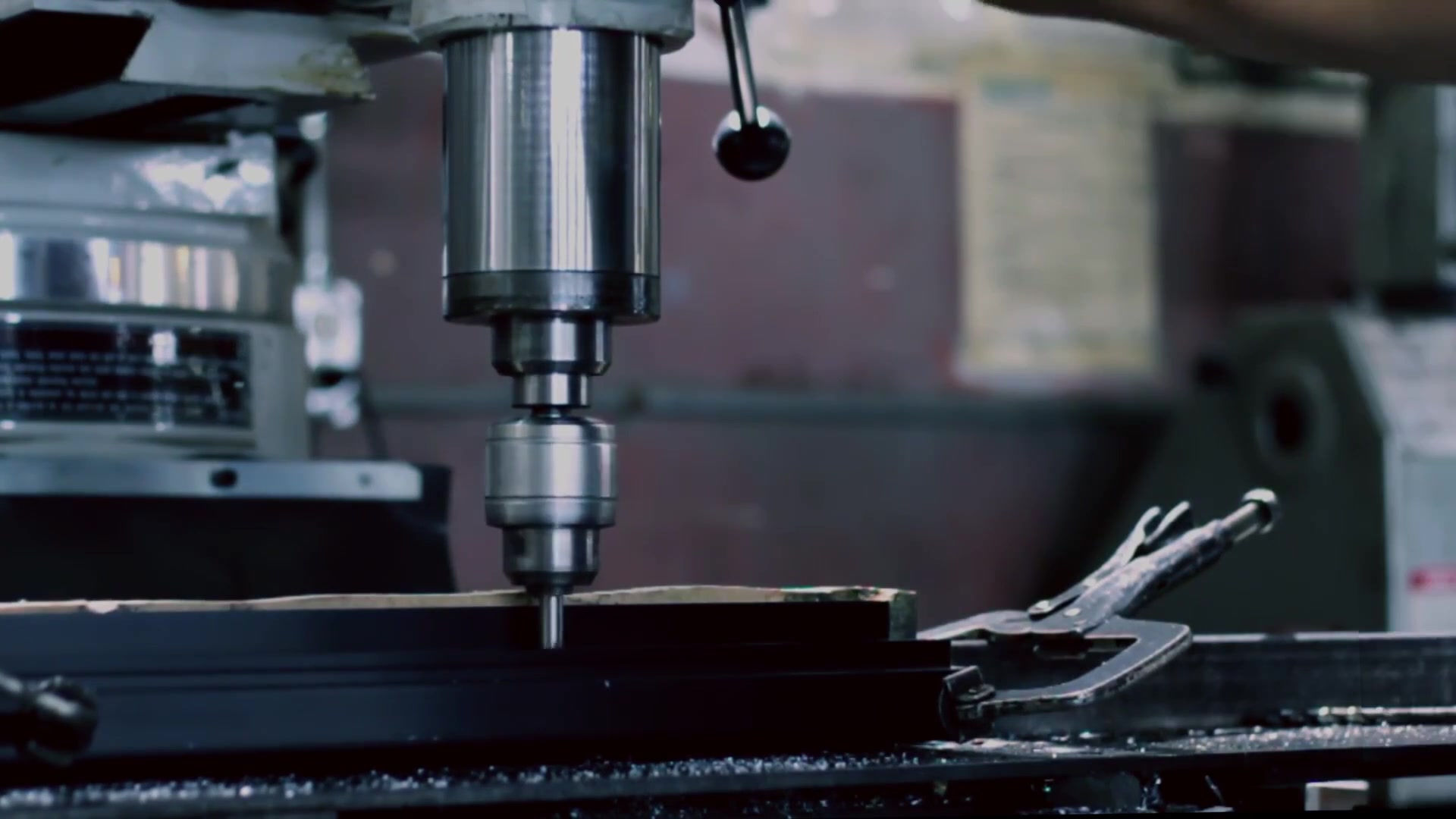
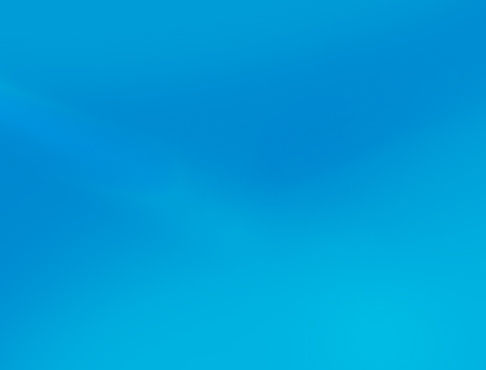
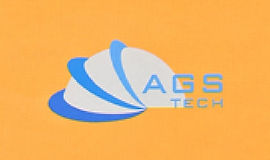
Produsen Kustom Global, Integrator, Konsolidator, Mitra Outsourcing untuk Berbagai Produk & Layanan.
Kami adalah sumber satu atap Anda untuk manufaktur, fabrikasi, teknik, konsolidasi, integrasi, outsourcing produk & layanan yang diproduksi khusus dan siap pakai.
Choose your Language
-
Manufaktur Kustom
-
Manufaktur Kontrak Domestik & Global
-
Pengalihdayaan Manufaktur
-
Pengadaan Domestik & Global
-
Consolidation
-
Integrasi Teknik
-
Layanan Rekayasa
Jenis manufaktur kaca yang kami tawarkan adalah kaca kontainer, glass blowing, glass fiber & tubing & rod, barang pecah belah domestik dan industri, lampu dan bohlam, cetakan kaca presisi, komponen dan rakitan optik, kaca datar & lembaran & pelampung. Kami melakukan pembentukan tangan serta pembentukan mesin.
Proses manufaktur keramik teknis populer kami adalah die pressing, isostatic pressing, hot isostatic pressing, hot pressing, slip casting, tape casting, ekstrusi, injection moulding, green machining, sintering atau firing, diamond grinding, hermetic assemblies.
Kami menyarankan Anda mengklik di sini untuk
UNDUH Ilustrasi Skema Proses Pembentukan dan Pembentukan Kaca oleh AGS-TECH Inc.
UNDUH Ilustrasi Skema Proses Manufaktur Keramik Teknis kami oleh AGS-TECH Inc.
File yang dapat diunduh dengan foto dan sketsa ini akan membantu Anda lebih memahami informasi yang kami berikan kepada Anda di bawah ini.
• INDUSTRI KACA KONTAINER: Kami memiliki jalur TEKAN DAN tiup otomatis serta tiupan dan tiup untuk manufaktur. Dalam proses pukulan dan pukulan kami menjatuhkan gumpalan ke dalam cetakan kosong dan membentuk leher dengan menerapkan pukulan udara terkompresi dari atas. Segera setelah ini, udara terkompresi dihembuskan untuk kedua kalinya dari arah lain melalui leher wadah untuk membentuk bentuk awal botol. Pra-bentuk ini kemudian dipindahkan ke cetakan yang sebenarnya, dipanaskan kembali untuk melunakkan dan udara terkompresi diterapkan untuk memberikan pra-bentuk bentuk wadah akhir. Lebih eksplisit, itu ditekan dan didorong ke dinding rongga cetakan pukulan untuk mengambil bentuk yang diinginkan. Akhirnya, wadah kaca yang diproduksi dipindahkan ke oven anil untuk pemanasan ulang berikutnya dan penghilangan tekanan yang dihasilkan selama pencetakan dan didinginkan dengan cara yang terkontrol. Pada metode press and blow, lelehan gob dimasukkan ke dalam cetakan parison (blank mould) dan dipress ke dalam bentuk parison (blank form). Kosong kemudian dipindahkan ke cetakan tiup dan ditiup mirip dengan proses yang dijelaskan di atas di bawah "Proses Tiup dan Tiup". Langkah-langkah selanjutnya seperti anil dan penghilang stres serupa atau sama.
• GLASS BLOWING : Kami telah memproduksi produk kaca menggunakan hand blowing konvensional serta menggunakan udara terkompresi dengan peralatan otomatis. Untuk beberapa pesanan peniupan konvensional diperlukan, seperti proyek yang melibatkan karya seni kaca, atau proyek yang membutuhkan lebih sedikit suku cadang dengan toleransi longgar, proyek prototyping / demo….dll. Meniup kaca konvensional melibatkan pencelupan pipa logam berongga ke dalam panci kaca cair dan memutar pipa untuk mengumpulkan sejumlah bahan kaca. Kaca yang terkumpul pada ujung pipa digulung pada besi pipih, dibentuk sesuai keinginan, memanjang, dipanaskan kembali dan ditiupkan udara. Saat siap, itu dimasukkan ke dalam cetakan dan udara ditiup. Rongga cetakan basah untuk menghindari kontak kaca dengan logam. Film air bertindak seperti bantalan di antara mereka. Peniupan manual adalah proses lambat padat karya dan hanya cocok untuk pembuatan prototipe atau barang bernilai tinggi, tidak cocok untuk pesanan volume tinggi per potong yang murah.
• MANUFAKTUR PERANGKAT GELAS DOMESTIK & INDUSTRI : Menggunakan berbagai jenis bahan kaca berbagai macam barang pecah belah sedang diproduksi. Beberapa gelas tahan panas dan cocok untuk peralatan gelas laboratorium sedangkan beberapa gelas cukup baik untuk menahan mesin pencuci piring berkali-kali dan cocok untuk membuat produk dalam negeri. Menggunakan mesin Westlake, puluhan ribu gelas minum diproduksi per hari. Untuk menyederhanakan, gelas cair dikumpulkan dengan vakum dan dimasukkan ke dalam cetakan untuk membuat bentuk awal. Kemudian udara ditiupkan ke dalam cetakan, ini dipindahkan ke cetakan lain dan udara ditiup lagi dan kaca mengambil bentuk akhirnya. Seperti di tiup tangan, cetakan ini tetap basah dengan air. Peregangan lebih lanjut adalah bagian dari operasi finishing di mana leher sedang dibentuk. Kelebihan kaca terbakar. Setelah itu proses pemanasan ulang dan pendinginan terkontrol yang dijelaskan di atas berikut ini.
• TABUNG KACA & PEMBENTUKAN BATANG : Proses utama yang kami gunakan untuk pembuatan tabung kaca adalah proses DANNER dan VELLO. Dalam Proses Danner, kaca dari tungku mengalir dan jatuh pada lengan miring yang terbuat dari bahan tahan api. Selongsong dibawa pada poros berongga atau sumpitan yang berputar. Kaca kemudian dililitkan di sekitar selongsong dan membentuk lapisan halus yang mengalir di selongsong dan di atas ujung poros. Dalam hal pembentukan tabung, udara dihembuskan melalui sumpitan dengan ujung berongga, dan dalam hal pembentukan batang, kami menggunakan ujung padat pada poros. Tabung atau batang kemudian ditarik di atas rol pembawa. Dimensi seperti ketebalan dinding dan diameter tabung kaca disesuaikan dengan nilai yang diinginkan dengan mengatur diameter selongsong dan tekanan udara tiup ke nilai yang diinginkan, menyesuaikan suhu, laju aliran kaca, dan kecepatan menggambar. Proses pembuatan tabung gelas Vello di sisi lain melibatkan kaca yang bergerak keluar tungku dan masuk ke mangkuk dengan mandrel atau bel berongga. Gelas kemudian melewati ruang udara antara mandrel dan mangkuk dan mengambil bentuk tabung. Setelah itu bergerak di atas rol ke mesin gambar dan didinginkan. Pada akhir pemotongan garis pendingin dan pemrosesan akhir berlangsung. Dimensi tabung dapat disesuaikan seperti pada proses Danner. Saat membandingkan proses Danner dengan Vello, kita dapat mengatakan bahwa proses Vello lebih cocok untuk produksi jumlah besar sedangkan proses Danner mungkin lebih cocok untuk pesanan tabung volume kecil yang presisi.
• PROCESSING OF SHEET & FLAT & FLOAT GLASS : Kami memiliki sejumlah besar kaca lembaran dengan ketebalan mulai dari ketebalan submilimeter hingga beberapa sentimeter. Kacamata datar kami hampir memiliki kesempurnaan optik. Kami menawarkan kaca dengan coating khusus seperti optical coating, dimana teknik chemical vapor deposition digunakan untuk melapisi coating seperti antireflection atau mirror coating. Juga lapisan konduktif transparan yang umum. Juga tersedia pelapis hidrofobik atau hidrofilik pada kaca, dan pelapis yang membuat kaca dapat membersihkan sendiri. Kaca tempered, antipeluru dan kaca laminasi adalah barang populer lainnya. Kami memotong kaca menjadi bentuk yang diinginkan dengan toleransi yang diinginkan. Operasi sekunder lainnya seperti melengkung atau membengkokkan kaca datar tersedia.
• PRECISION GLASS MOLDING : Kami menggunakan teknik ini sebagian besar untuk membuat komponen optik presisi tanpa memerlukan teknik yang lebih mahal dan memakan waktu seperti penggilingan, pemolesan dan pemolesan. Teknik ini tidak selalu cukup untuk membuat yang terbaik dari optik terbaik, tetapi dalam beberapa kasus seperti produk konsumen, kamera digital, optik medis, ini bisa menjadi pilihan bagus yang lebih murah untuk produksi volume tinggi. Juga memiliki keunggulan dibandingkan teknik pembentukan kaca lainnya di mana geometri kompleks diperlukan, seperti dalam kasus aspheres. Proses dasar melibatkan pemuatan sisi bawah cetakan kami dengan kaca kosong, evakuasi ruang proses untuk menghilangkan oksigen, dekat penutupan cetakan, pemanasan cepat dan isotermal mati dan kaca dengan cahaya inframerah, penutupan lebih lanjut dari bagian cetakan untuk menekan kaca yang dilunakkan secara perlahan dengan cara yang terkontrol hingga ketebalan yang diinginkan, dan akhirnya mendinginkan kaca dan mengisi ruangan dengan nitrogen dan mengeluarkan produk. Kontrol suhu yang tepat, jarak penutupan cetakan, kekuatan penutupan cetakan, pencocokan koefisien ekspansi cetakan dan bahan kaca adalah kunci dalam proses ini.
• INDUSTRI KOMPONEN DAN RAKITAN OPTIK KACA : Selain pencetakan kaca presisi, ada sejumlah proses berharga yang kami gunakan untuk membuat komponen dan rakitan optik berkualitas tinggi untuk aplikasi yang menuntut. Grinding, lapping dan polishing kaca optik kelas dalam bubur abrasif khusus halus adalah seni dan ilmu untuk membuat lensa optik, prisma, flat dan banyak lagi. Permukaan datar, bergelombang, halus dan permukaan optik bebas cacat membutuhkan banyak pengalaman dengan proses tersebut. Perubahan kecil dalam lingkungan dapat mengakibatkan produk di luar spesifikasi dan menghentikan jalur produksi. Ada kasus di mana satu sapuan pada permukaan optik dengan kain bersih dapat membuat produk memenuhi spesifikasi atau gagal dalam pengujian. Beberapa bahan kaca yang populer digunakan adalah fused silica, quartz, BK7. Juga perakitan komponen tersebut membutuhkan pengalaman khusus. Terkadang lem khusus digunakan. Namun, terkadang teknik yang disebut kontak optik adalah pilihan terbaik dan tidak melibatkan bahan di antara kacamata optik yang terpasang. Ini terdiri dari permukaan datar yang bersentuhan secara fisik untuk menempel satu sama lain tanpa lem. Dalam beberapa kasus spacer mekanis, batang atau bola kaca presisi, klem atau komponen logam mesin digunakan untuk merakit komponen optik pada jarak tertentu dan dengan orientasi geometris tertentu satu sama lain. Mari kita periksa beberapa teknik populer kami untuk membuat optik kelas atas.
GRINDING & LAPPING & POLISHING : Bentuk kasar komponen optik diperoleh dengan menggiling blanko kaca. Setelah itu pemolesan dan pemolesan dilakukan dengan memutar dan menggosok permukaan kasar komponen optik terhadap alat dengan bentuk permukaan yang diinginkan. Bubur dengan partikel abrasif kecil dan cairan dituangkan di antara optik dan alat pembentuk. Ukuran partikel abrasif dalam bubur tersebut dapat dipilih sesuai dengan tingkat kerataan yang diinginkan. Penyimpangan permukaan optik kritis dari bentuk yang diinginkan dinyatakan dalam panjang gelombang cahaya yang digunakan. Optik presisi tinggi kami memiliki toleransi sepersepuluh dari panjang gelombang (Panjang Gelombang/10) atau bahkan lebih ketat. Selain profil permukaan, permukaan kritis dipindai dan dievaluasi untuk fitur dan cacat permukaan lainnya seperti dimensi, goresan, keripik, lubang, bintik... dll. Kontrol ketat terhadap kondisi lingkungan di lantai manufaktur optik dan metrologi ekstensif serta persyaratan pengujian dengan peralatan canggih menjadikan ini cabang industri yang menantang.
• PROSES SEKUNDER DALAM MANUFAKTUR KACA: Sekali lagi, kami hanya dibatasi oleh imajinasi Anda ketika datang ke proses sekunder dan finishing kaca. Berikut kami daftarkan beberapa di antaranya:
-Pelapis pada kaca (optik, listrik, tribologi, termal, fungsional, mekanik...). Sebagai contoh kita dapat mengubah sifat permukaan kaca sehingga misalnya memantulkan panas sehingga membuat interior bangunan tetap dingin, atau membuat satu sisi menyerap inframerah menggunakan nanoteknologi. Ini membantu menjaga bagian dalam gedung tetap hangat karena lapisan permukaan terluar kaca akan menyerap radiasi infra merah di dalam gedung dan memancarkannya kembali ke bagian dalam.
-Etsa pada kaca
-Pelabelan Keramik Terapan (ACL)
-Ukiran
- Pemolesan api
-Pemolesan kimia
-Pewarnaan
MANUFAKTUR KERAMIK TEKNIS
• DIE PRESSING : Terdiri dari pemadatan uniaksial serbuk granular yang dikurung dalam cetakan
• HOT PRESSING : Mirip dengan die pressing tetapi dengan penambahan suhu untuk meningkatkan densifikasi. Bubuk atau bentuk awal yang dipadatkan ditempatkan ke dalam cetakan grafit dan tekanan uniaksial diterapkan sementara cetakan disimpan pada suhu tinggi seperti 2000 C. Suhu dapat berbeda tergantung pada jenis bubuk keramik yang diproses. Untuk bentuk dan geometri yang rumit, pemrosesan selanjutnya seperti penggilingan berlian mungkin diperlukan.
• ISOSTATIC PRESSING : Granular powder atau die-pressed compacts ditempatkan dalam wadah kedap udara dan kemudian ke dalam bejana bertekanan tertutup dengan cairan di dalamnya. Setelah itu dipadatkan dengan meningkatkan tekanan bejana tekan. Cairan di dalam bejana mentransfer gaya tekanan secara merata ke seluruh luas permukaan wadah kedap udara. Dengan demikian, material dipadatkan secara seragam dan mengambil bentuk wadahnya yang fleksibel serta profil dan fitur internalnya.
• HOT ISOSTATIC PRESSING : Mirip dengan isostatic pressing, tetapi selain tekanan atmosfer gas, kita sinter compact pada suhu tinggi. Pengepresan isostatik panas menghasilkan densifikasi tambahan dan peningkatan kekuatan.
• SLIP CASTING / DRAIN CASTING : Kami mengisi cetakan dengan suspensi partikel keramik berukuran mikrometer dan cairan pembawa. Campuran ini disebut "slip". Cetakan memiliki pori-pori dan oleh karena itu cairan dalam campuran disaring ke dalam cetakan. Akibatnya, gips terbentuk pada permukaan bagian dalam cetakan. Setelah sintering, bagian-bagian dapat dikeluarkan dari cetakan.
• TAPE CASTING : Kami memproduksi kaset keramik dengan menuangkan bubur keramik ke permukaan pembawa yang bergerak datar. Bubur mengandung bubuk keramik yang dicampur dengan bahan kimia lain untuk tujuan mengikat dan membawa. Saat pelarut menguap, lembaran keramik yang padat dan fleksibel tertinggal yang dapat dipotong atau digulung sesuai keinginan.
• PEMBENTUKAN EKSTRUSI : Seperti dalam proses ekstrusi lainnya, campuran lembut bubuk keramik dengan pengikat dan bahan kimia lainnya dilewatkan melalui cetakan untuk mendapatkan bentuk penampang dan kemudian dipotong pada panjang yang diinginkan. Proses ini dilakukan dengan campuran keramik dingin atau panas.
• MOLDING INJEKSI TEKANAN RENDAH : Kami menyiapkan campuran bubuk keramik dengan pengikat dan pelarut dan memanaskannya ke suhu yang dapat dengan mudah ditekan dan dipaksakan ke dalam rongga alat. Setelah siklus pencetakan selesai, bagian tersebut dikeluarkan dan bahan kimia pengikat dibakar. Menggunakan cetakan injeksi, kami dapat memperoleh bagian yang rumit dengan volume tinggi secara ekonomis. Lubang yang merupakan pecahan kecil dari milimeter pada dinding setebal 10mm dimungkinkan, ulir dimungkinkan tanpa pemesinan lain, toleransi seketat +/- 0,5% dimungkinkan dan bahkan lebih rendah saat suku cadang dikerjakan , ketebalan dinding dalam urutan 0,5 mm hingga panjang 12,5 mm dimungkinkan serta ketebalan dinding 6,5 mm hingga panjang 150 mm.
• MESIN HIJAU : Dengan menggunakan alat pemesinan logam yang sama, kami dapat mengerjakan bahan keramik yang ditekan dengan mesin saat masih lunak seperti kapur. Toleransi +/- 1% dimungkinkan. Untuk toleransi yang lebih baik, kami menggunakan penggilingan berlian.
• SINTERING atau FIRING : Sintering memungkinkan densifikasi penuh. Penyusutan yang signifikan terjadi pada bagian kompak hijau, tetapi ini bukan masalah besar karena kami memperhitungkan perubahan dimensi ini ketika kami merancang bagian dan perkakas. Partikel bubuk terikat bersama dan porositas yang disebabkan oleh proses pemadatan dihilangkan sebagian besar.
• DIAMOND GRINDING : Bahan terkeras di dunia "berlian" digunakan untuk menggiling bahan keras seperti keramik dan bagian presisi diperoleh. Toleransi dalam kisaran mikrometer dan permukaan yang sangat halus sedang dicapai. Karena biayanya, kami hanya mempertimbangkan teknik ini ketika kami benar-benar membutuhkannya.
• RAKITAN HERMETIS adalah mereka yang secara praktis tidak memungkinkan pertukaran materi, padatan, cairan atau gas antara antarmuka. Penyegelan hermetis kedap udara. Misalnya selungkup elektronik kedap udara adalah mereka yang menjaga isi interior sensitif dari perangkat yang dikemas tidak terluka oleh kelembaban, kontaminan atau gas. Tidak ada yang 100% hermetis, tetapi ketika kita berbicara tentang hermetisitas yang kami maksudkan secara praktis, bahwa ada hermetisitas sejauh tingkat kebocoran sangat rendah sehingga perangkat aman dalam kondisi lingkungan normal untuk waktu yang sangat lama. Rakitan kedap udara kami terdiri dari komponen logam, kaca dan keramik, logam-keramik, keramik-logam-keramik, logam-keramik-logam, logam ke logam, logam-kaca, logam-kaca-logam, kaca-logam-kaca, kaca- logam dan kaca ke kaca dan semua kombinasi ikatan logam-kaca-keramik lainnya. Misalnya, kami dapat melapisi komponen keramik dengan logam sehingga dapat merekat dengan kuat ke komponen lain dalam perakitan dan memiliki kemampuan penyegelan yang sangat baik. Kami memiliki pengetahuan tentang melapisi serat optik atau feedthrough dengan logam dan menyolder atau mematrinya ke selungkup, sehingga tidak ada gas yang lewat atau bocor ke dalam selungkup. Oleh karena itu mereka digunakan untuk pembuatan selungkup elektronik untuk merangkum perangkat sensitif dan melindunginya dari atmosfer luar. Selain karakteristik penyegelannya yang sangat baik, sifat lain seperti koefisien ekspansi termal, ketahanan deformasi, sifat non-outgassing, masa pakai yang sangat lama, sifat nonkonduktif, sifat insulasi termal, sifat antistatik...dll. menjadikan material kaca dan keramik sebagai pilihan untuk aplikasi tertentu. Informasi tentang fasilitas kami yang memproduksi fitting keramik ke logam, penyegelan kedap udara, feedthrough vakum, komponen kontrol vakum dan cairan tinggi dan ultratinggi dapat ditemukan di sini:Brosur Pabrik Komponen Hermetik