
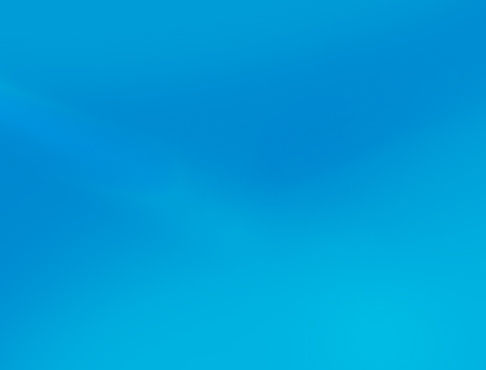
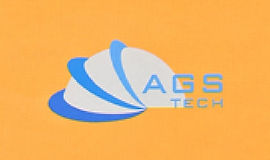
Produsen Kustom Global, Integrator, Konsolidator, Mitra Outsourcing untuk Berbagai Produk & Layanan.
Kami adalah sumber satu atap Anda untuk manufaktur, fabrikasi, teknik, konsolidasi, integrasi, outsourcing produk & layanan yang diproduksi khusus dan siap pakai.
Choose your Language
-
Manufaktur Kustom
-
Manufaktur Kontrak Domestik & Global
-
Pengalihdayaan Manufaktur
-
Pengadaan Domestik & Global
-
Consolidation
-
Integrasi Teknik
-
Layanan Rekayasa
Kami menggabungkan, merakit, dan mengencangkan suku cadang produksi Anda dan mengubahnya menjadi produk jadi atau setengah jadi menggunakan WELDING, BRAZING, SOLDERING, SINTERING, ADHESIVE BONDING, FASTENING, PRESS FITTING. Beberapa proses pengelasan kami yang paling populer adalah busur, gas oxyfuel, resistensi, proyeksi, jahitan, kesal, perkusi, solid state, berkas elektron, laser, termit, pengelasan induksi. Proses mematri populer kami adalah obor, induksi, tungku dan mematri dip. Metode penyolderan kami adalah besi, hot plate, oven, induksi, celup, gelombang, reflow, dan penyolderan ultrasonik. Untuk ikatan perekat kami sering menggunakan termoplastik dan pengaturan termo, epoksi, fenolat, poliuretan, paduan perekat serta beberapa bahan kimia dan pita lainnya. Akhirnya proses pengikatan kami terdiri dari pemakuan, pengencangan, mur dan baut, riveting, clinching, pinning, stitching & stapel dan press fitting.
• PENGELASAN : Pengelasan melibatkan penyambungan material dengan melelehkan benda kerja dan memasukkan material pengisi, yang juga bergabung dengan kolam las cair. Saat area mendingin, kami mendapatkan sambungan yang kuat. Tekanan diterapkan dalam beberapa kasus. Berlawanan dengan pengelasan, operasi mematri dan menyolder hanya melibatkan peleburan material dengan titik leleh yang lebih rendah di antara benda kerja, dan benda kerja tidak meleleh. Kami menyarankan Anda mengklik di sini untukUNDUH Ilustrasi Skema Proses Pengelasan kami oleh AGS-TECH Inc.
Ini akan membantu Anda lebih memahami informasi yang kami berikan kepada Anda di bawah ini.
Dalam PENGELASAN BUSUR, kami menggunakan catu daya dan elektroda untuk membuat busur listrik yang melelehkan logam. Titik las dilindungi oleh gas pelindung atau uap atau bahan lainnya. Proses ini populer untuk pengelasan suku cadang otomotif dan struktur baja. Dalam pengelasan busur logam terlindung (SMAW) atau juga dikenal sebagai pengelasan tongkat, tongkat elektroda didekatkan dengan bahan dasar dan busur listrik dihasilkan di antara mereka. Batang elektroda meleleh dan bertindak sebagai bahan pengisi. Elektroda juga mengandung fluks yang bertindak sebagai lapisan terak dan mengeluarkan uap yang bertindak sebagai gas pelindung. Ini melindungi area las dari kontaminasi lingkungan. Tidak ada pengisi lain yang digunakan. Kerugian dari proses ini adalah kelambatannya, perlu sering mengganti elektroda, kebutuhan untuk mengikis sisa terak yang berasal dari fluks. Sejumlah logam seperti besi, baja, nikel, aluminium, tembaga ... dll. Dapat dilas. Keuntungannya adalah alatnya yang murah dan kemudahan penggunaan. Pengelasan busur logam gas (GMAW) juga dikenal sebagai gas inert logam (MIG), kami memiliki pengisian terus menerus dari pengisi kawat elektroda habis pakai dan gas inert atau sebagian inert yang mengalir di sekitar kawat terhadap pencemaran lingkungan di wilayah las. Baja, aluminium dan logam non-ferrous lainnya dapat dilas. Keunggulan MIG adalah kecepatan pengelasan yang tinggi dan kualitas yang baik. Kekurangannya adalah peralatannya yang rumit dan tantangan yang dihadapi di lingkungan luar yang berangin karena kita harus menjaga kestabilan gas pelindung di sekitar area pengelasan. Variasi dari GMAW adalah pengelasan busur inti fluks (FCAW) yang terdiri dari tabung logam halus yang diisi dengan bahan fluks. Terkadang fluks di dalam tabung cukup untuk perlindungan dari kontaminasi lingkungan. Pengelasan Busur Terendam (SAW) secara luas merupakan proses otomatis, melibatkan pengumpanan kawat terus menerus dan busur yang dipukul di bawah lapisan penutup fluks. Tingkat produksi dan kualitas tinggi, terak las mudah lepas, dan kami memiliki lingkungan kerja yang bebas asap rokok. Kekurangannya hanya bisa digunakan untuk mengelas parts pada posisi tertentu. Dalam las busur tungsten gas (GTAW) atau las gas tungsten-inert (TIG) kami menggunakan elektroda Tungsten bersama dengan pengisi terpisah dan gas inert atau dekat inert. Seperti kita ketahui Tungsten memiliki titik leleh yang tinggi dan merupakan logam yang sangat cocok untuk suhu yang sangat tinggi. Tungsten di TIG tidak dikonsumsi bertentangan dengan metode lain yang dijelaskan di atas. Teknik pengelasan yang lambat tapi berkualitas tinggi yang menguntungkan dibandingkan teknik lain dalam pengelasan bahan tipis. Cocok untuk banyak logam. Pengelasan busur plasma serupa tetapi menggunakan gas plasma untuk membuat busur. Busur dalam pengelasan busur plasma relatif lebih terkonsentrasi dibandingkan dengan GTAW dan dapat digunakan untuk rentang ketebalan logam yang lebih luas pada kecepatan yang jauh lebih tinggi. Pengelasan busur GTAW dan plasma dapat diterapkan pada bahan yang kurang lebih sama.
OXY-FUEL / OXYFUEL WELDING disebut juga oxyacetylene welding, oxy welding, gas welding dilakukan dengan menggunakan bahan bakar gas dan oksigen untuk pengelasan. Karena tidak ada tenaga listrik yang digunakan, alat ini portabel dan dapat digunakan di tempat yang tidak ada listrik. Dengan menggunakan obor las, kami memanaskan potongan dan bahan pengisi untuk menghasilkan kumpulan logam cair bersama. Berbagai bahan bakar dapat digunakan seperti asetilena, bensin, hidrogen, propana, butana…dll. Dalam pengelasan oxy-fuel kami menggunakan dua wadah, satu untuk bahan bakar dan yang lainnya untuk oksigen. Oksigen mengoksidasi bahan bakar (membakarnya).
RESISTANCE WELDING: Jenis pengelasan ini memanfaatkan pemanasan joule dan panas dihasilkan di lokasi di mana arus listrik diterapkan untuk waktu tertentu. Arus tinggi dilewatkan melalui logam. Kolam logam cair terbentuk di lokasi ini. Metode pengelasan resistansi populer karena efisiensinya, sedikit potensi polusi. Namun kerugiannya adalah biaya peralatan yang relatif signifikan dan keterbatasan yang melekat pada benda kerja yang relatif tipis. SPOT WELDING adalah salah satu jenis utama dari pengelasan resistansi. Di sini kita menggabungkan dua atau lebih lembaran atau benda kerja yang tumpang tindih dengan menggunakan dua elektroda tembaga untuk menjepit lembaran bersama-sama dan melewatkan arus tinggi melaluinya. Bahan antara elektroda tembaga memanas dan kolam cair dihasilkan di lokasi itu. Arus kemudian dihentikan dan ujung elektroda tembaga mendinginkan lokasi las karena elektroda didinginkan dengan air. Menerapkan jumlah panas yang tepat ke bahan dan ketebalan yang tepat adalah kunci untuk teknik ini, karena jika diterapkan secara salah sambungan akan menjadi lemah. Pengelasan titik memiliki keuntungan karena tidak menyebabkan deformasi yang signifikan pada benda kerja, efisiensi energi, kemudahan otomatisasi dan tingkat produksi yang luar biasa, dan tidak memerlukan pengisi apa pun. Kerugiannya adalah karena pengelasan terjadi di titik-titik daripada membentuk jahitan yang terus menerus, kekuatan keseluruhan bisa relatif lebih rendah dibandingkan dengan metode pengelasan lainnya. SEAM WELDING di sisi lain menghasilkan lasan pada permukaan faying dari bahan serupa. Jahitannya bisa berupa sambungan pantat atau tumpang tindih. Pengelasan jahitan dimulai dari satu ujung dan bergerak secara progresif ke ujung lainnya. Metode ini juga menggunakan dua elektroda dari tembaga untuk memberikan tekanan dan arus ke daerah las. Elektroda berbentuk cakram berputar dengan kontak konstan di sepanjang garis jahitan dan membuat lasan kontinu. Di sini juga, elektroda didinginkan oleh air. Lasannya sangat kuat dan dapat diandalkan. Metode lain adalah teknik las proyeksi, flash dan kesal.
PENGELASAN SOLID-STATE sedikit berbeda dari metode sebelumnya yang dijelaskan di atas. Penggabungan terjadi pada suhu di bawah suhu leleh logam bergabung dan tanpa menggunakan pengisi logam. Tekanan dapat digunakan dalam beberapa proses. Berbagai metode adalah COEXTRUSION WELDING di mana logam yang berbeda diekstrusi melalui die yang sama, COLD PRESSURE WELDING di mana kita menggabungkan paduan lunak di bawah titik lelehnya, DIFFUSION WELDING teknik tanpa garis las yang terlihat, EXPLOSION WELDING untuk menyambung bahan yang berbeda, misalnya paduan tahan korosi ke struktur baja, ELECTROMAGNETIC PULSE WELDING di mana kami mempercepat tabung dan lembaran dengan gaya elektromagnetik, FORGE WELDING yang terdiri dari memanaskan logam hingga suhu tinggi dan memalunya bersama-sama, FRICTION WELDING di mana dengan pengelasan gesekan yang cukup dilakukan, FRICTION STIR WELDING yang melibatkan putaran non- alat habis pakai yang melintasi garis sambungan, PENGELASAN TEKANAN PANAS di mana kami menekan logam bersama-sama pada suhu tinggi di bawah suhu leleh dalam vakum atau gas inert, PENGELASAN TEKANAN ISOSTATIK PANAS sebuah proses di mana kami menerapkan tekanan menggunakan gas inert di dalam bejana, ROLL WELDING di mana kami bergabung bahan yang berbeda dengan memaksa mereka antara dua roda berputar, ULTRASONIC WELDING di mana lembaran logam atau plastik tipis dilas menggunakan energi getaran frekuensi tinggi.
Proses pengelasan kami yang lain adalah ELECTRON BEAM WELDING dengan penetrasi yang dalam dan proses yang cepat tetapi menjadi metode yang mahal kami menganggapnya untuk kasus-kasus khusus, ELECTROSLAG WELDING metode yang cocok untuk pelat tebal dan benda kerja baja saja, INDUCTION WELDING di mana kami menggunakan induksi elektromagnetik dan memanaskan benda kerja konduktif atau feromagnetik kami, LASER BEAM WELDING juga dengan penetrasi yang dalam dan pemrosesan yang cepat tetapi metode yang mahal, LASER HYBRID WELDING yang menggabungkan BBLR dengan GMAW di kepala las yang sama dan mampu menjembatani kesenjangan 2 mm antara pelat, PERKUSI LAS yang melibatkan pelepasan listrik diikuti dengan penempaan bahan dengan tekanan yang diberikan, PENGELASAN TERMIT yang melibatkan reaksi eksotermik antara aluminium dan serbuk oksida besi., PENGELASAN ELEKTROGAS dengan elektroda habis pakai dan digunakan hanya dengan baja dalam posisi vertikal, dan akhirnya PENGELASAN STUD ARC untuk menyambung stud ke dasar bahan dengan panas dan tekanan.
Kami menyarankan Anda mengklik di sini untukUNDUH Ilustrasi Skema Proses Pematrian, Penyolderan, dan Pengikatan Perekat kami oleh AGS-TECH Inc
Ini akan membantu Anda lebih memahami informasi yang kami berikan kepada Anda di bawah ini.
• BRAZING : Kami menggabungkan dua atau lebih logam dengan memanaskan logam pengisi di antara keduanya di atas titik lelehnya dan menggunakan aksi kapiler untuk menyebar. Prosesnya mirip dengan penyolderan tetapi suhu yang dibutuhkan untuk melelehkan pengisi lebih tinggi dalam mematri. Seperti dalam pengelasan, fluks melindungi bahan pengisi dari kontaminasi atmosfer. Setelah pendinginan, benda kerja disatukan. Proses ini melibatkan langkah-langkah kunci berikut: Kesesuaian dan jarak bebas yang baik, pembersihan bahan dasar yang tepat, pemasangan yang tepat, pemilihan fluks dan atmosfer yang tepat, pemanasan rakitan dan akhirnya pembersihan rakitan brazing. Beberapa proses mematri kami adalah TORCH BRAZING, metode populer yang dilakukan secara manual atau otomatis. Sangat cocok untuk pesanan produksi volume rendah dan kasus khusus. Panas diterapkan menggunakan api gas di dekat sambungan yang dibrazing. FURNACE BRAZING membutuhkan lebih sedikit keterampilan operator dan merupakan proses semi-otomatis yang cocok untuk produksi massal industri. Baik kontrol suhu dan kontrol atmosfer di tungku adalah keuntungan dari teknik ini, karena yang pertama memungkinkan kita untuk mengontrol siklus panas dan menghilangkan pemanasan lokal seperti halnya dalam pematrian obor, dan yang terakhir melindungi bagian dari oksidasi. Dengan menggunakan jigging, kami mampu menekan biaya produksi seminimal mungkin. Kerugiannya adalah konsumsi daya yang tinggi, biaya peralatan dan pertimbangan desain yang lebih menantang. VACUUM BRAZING berlangsung di tungku vakum. Keseragaman suhu dipertahankan dan kami memperoleh sambungan yang bebas fluks dan sangat bersih dengan tegangan sisa yang sangat kecil. Perlakuan panas dapat terjadi selama pematrian vakum, karena tegangan sisa rendah yang ada selama siklus pemanasan dan pendinginan yang lambat. Kerugian utama adalah biayanya yang tinggi karena pembuatan lingkungan vakum adalah proses yang mahal. Namun teknik lain DIP BRAZING bergabung dengan bagian-bagian yang dipasang di mana senyawa mematri diterapkan pada permukaan kawin. Setelah itu bagian-bagian yang diperbaiki fixtured dicelupkan ke dalam rendaman garam cair seperti Sodium Chloride (garam meja) yang bertindak sebagai media perpindahan panas dan fluks. Udara dikeluarkan dan oleh karena itu tidak terjadi pembentukan oksida. Dalam INDUCTION BRAZING kami menggabungkan material dengan logam pengisi yang memiliki titik leleh lebih rendah dari bahan dasarnya. Arus bolak-balik dari kumparan induksi menciptakan medan elektromagnetik yang menginduksi pemanasan induksi pada sebagian besar bahan magnet besi. Metode ini menyediakan pemanasan selektif, sambungan yang baik dengan pengisi hanya mengalir di area yang diinginkan, sedikit oksidasi karena tidak ada nyala api dan pendinginan cepat, pemanasan cepat, konsistensi dan kesesuaian untuk pembuatan volume tinggi. Untuk mempercepat proses kami dan untuk memastikan konsistensi, kami sering menggunakan bentuk awal. Informasi tentang fasilitas mematri kami yang memproduksi fitting keramik ke logam, penyegelan kedap udara, feedthrough vakum, komponen kontrol vakum dan cairan tinggi dan ultratinggi dapat ditemukan di sini: Brosur Pabrik Brazing
• SOLDERING : Dalam penyolderan benda kerja tidak meleleh, melainkan logam pengisi yang titik leburnya lebih rendah dari bagian penyambung yang mengalir ke dalam sambungan. Logam pengisi dalam penyolderan meleleh pada suhu yang lebih rendah daripada di mematri. Kami menggunakan paduan bebas timah untuk menyolder dan memiliki kepatuhan RoHS dan untuk aplikasi dan persyaratan yang berbeda, kami memiliki paduan yang berbeda dan sesuai seperti paduan perak. Solder menawarkan kita sambungan yang kedap gas dan cair. Pada SOFT SOLDERING, filler metal kami memiliki titik leleh di bawah 400 Celcius, sedangkan pada SILVER SOLDERING dan BRAZING kami membutuhkan suhu yang lebih tinggi. Solder lunak menggunakan suhu yang lebih rendah tetapi tidak menghasilkan sambungan yang kuat untuk aplikasi yang menuntut pada suhu tinggi. Penyolderan perak di sisi lain, membutuhkan suhu tinggi yang disediakan oleh obor dan memberi kita sambungan kuat yang cocok untuk aplikasi suhu tinggi. Mematri membutuhkan suhu tertinggi dan biasanya menggunakan obor. Karena sambungan mematri sangat kuat, sambungan ini merupakan kandidat yang baik untuk memperbaiki benda besi yang berat. Di lini produksi kami, kami menggunakan penyolderan tangan manual serta jalur solder otomatis. INDUCTION SOLDERING menggunakan arus AC frekuensi tinggi dalam kumparan tembaga untuk memfasilitasi pemanasan induksi. Arus diinduksi di bagian yang disolder dan sebagai akibatnya panas dihasilkan pada resistansi tinggi joint. Panas ini melelehkan logam pengisi. Fluks juga digunakan. Penyolderan induksi adalah metode yang baik untuk menyolder silinder dan pipa dalam proses berkelanjutan dengan melilitkan gulungan di sekelilingnya. Menyolder beberapa bahan seperti grafit dan keramik lebih sulit karena memerlukan pelapisan benda kerja dengan logam yang sesuai sebelum disolder. Ini memfasilitasi ikatan antarmuka. Kami melakukan solder bahan tersebut terutama untuk aplikasi kemasan kedap udara. Kami memproduksi papan sirkuit cetak (PCB) kami dalam volume tinggi sebagian besar menggunakan SOLDER GELOMBANG. Hanya untuk jumlah kecil tujuan prototyping kami menggunakan solder tangan menggunakan besi solder. Kami menggunakan penyolderan gelombang untuk rakitan PCB lubang-lubang dan pemasangan permukaan (PCBA). Lem sementara membuat komponen tetap menempel pada papan sirkuit dan rakitan ditempatkan pada konveyor dan bergerak melalui peralatan yang berisi solder cair. Pertama PCB difluks dan kemudian memasuki zona pemanasan awal. Solder cair berada dalam panci dan memiliki pola gelombang berdiri di permukaannya. Ketika PCB bergerak di atas gelombang ini, gelombang ini menyentuh bagian bawah PCB dan menempel pada bantalan solder. Solder tetap pada pin dan bantalan saja dan tidak pada PCB itu sendiri. Gelombang di solder cair harus dikontrol dengan baik sehingga tidak ada percikan dan puncak gelombang tidak menyentuh dan mencemari area papan yang tidak diinginkan. Dalam REFLOW SOLDERING, kami menggunakan pasta solder lengket untuk menempelkan komponen elektronik ke papan sementara. Kemudian papan dimasukkan melalui oven reflow dengan kontrol suhu. Di sini solder meleleh dan menghubungkan komponen secara permanen. Kami menggunakan teknik ini baik untuk komponen pemasangan di permukaan maupun untuk komponen lubang tembus. Kontrol suhu yang tepat dan penyesuaian suhu oven sangat penting untuk menghindari kerusakan komponen elektronik di papan dengan memanaskannya di atas batas suhu maksimumnya. Dalam proses penyolderan reflow, kami sebenarnya memiliki beberapa daerah atau tahapan masing-masing dengan profil termal yang berbeda, seperti langkah pemanasan awal, langkah perendaman termal, langkah reflow dan pendinginan. Langkah-langkah yang berbeda ini sangat penting untuk penyolderan reflow bebas kerusakan dari rakitan papan sirkuit tercetak (PCBA). ULTRASONIC SOLDERING adalah teknik lain yang sering digunakan dengan kemampuan unik- Dapat digunakan untuk menyolder bahan kaca, keramik, dan non-logam. Misalnya panel fotovoltaik yang non-logam membutuhkan elektroda yang dapat ditempelkan menggunakan teknik ini. Dalam penyolderan ultrasonik, kami menggunakan ujung penyolderan berpemanas yang juga memancarkan getaran ultrasonik. Getaran ini menghasilkan gelembung kavitasi pada antarmuka substrat dengan bahan solder cair. Energi ledakan kavitasi memodifikasi permukaan oksida dan menghilangkan kotoran dan oksida. Selama waktu ini lapisan paduan juga terbentuk. Solder pada permukaan ikatan menggabungkan oksigen dan memungkinkan pembentukan ikatan bersama yang kuat antara kaca dan solder. DIP SOLDERING dapat dianggap sebagai versi penyolderan gelombang yang lebih sederhana yang hanya cocok untuk produksi skala kecil. Fluks pembersihan pertama diterapkan seperti pada proses lainnya. PCB dengan komponen terpasang dicelupkan secara manual atau semi-otomatis ke dalam tangki yang berisi solder cair. Solder cair menempel pada area logam terbuka yang tidak dilindungi oleh topeng solder di papan. Peralatannya sederhana dan murah.
• ADHESIVE BONDING : Ini adalah teknik populer lainnya yang sering kita gunakan dan melibatkan ikatan permukaan menggunakan lem, epoksi, bahan plastik atau bahan kimia lainnya. Ikatan dilakukan dengan menguapkan pelarut, dengan pengawetan panas, dengan pengawetan sinar UV, dengan pengawetan tekanan atau menunggu waktu tertentu. Berbagai lem berkinerja tinggi digunakan di lini produksi kami. Dengan aplikasi dan proses pengawetan yang direkayasa dengan benar, ikatan perekat dapat menghasilkan ikatan tegangan yang sangat rendah yang kuat dan andal. Ikatan perekat dapat menjadi pelindung yang baik terhadap faktor lingkungan seperti kelembaban, kontaminan, korosif, getaran ... dll. Keuntungan dari ikatan perekat adalah: mereka dapat diterapkan pada bahan yang sulit untuk disolder, dilas atau dibraze. Juga dapat lebih disukai untuk bahan peka panas yang akan rusak oleh pengelasan atau proses suhu tinggi lainnya. Keuntungan lain dari perekat adalah mereka dapat diterapkan pada permukaan berbentuk tidak beraturan dan meningkatkan berat perakitan dengan jumlah yang sangat kecil jika dibandingkan dengan metode lain. Juga perubahan dimensi di bagian sangat minim. Beberapa lem memiliki sifat pencocokan indeks dan dapat digunakan di antara komponen optik tanpa mengurangi kekuatan sinyal cahaya atau optik secara signifikan. Kerugian di sisi lain adalah waktu curing yang lebih lama yang dapat memperlambat jalur manufaktur, persyaratan pemasangan, persyaratan persiapan permukaan dan kesulitan untuk membongkar saat pengerjaan ulang diperlukan. Sebagian besar operasi ikatan perekat kami melibatkan langkah-langkah berikut:
-Perawatan permukaan: Prosedur pembersihan khusus seperti pembersihan air deionisasi, pembersihan alkohol, pembersihan plasma atau korona adalah umum. Setelah dibersihkan, kami dapat menerapkan promotor adhesi ke permukaan untuk memastikan sambungan terbaik.
-Perbaikan Bagian: Baik untuk aplikasi perekat maupun untuk pengawetan, kami merancang dan menggunakan perlengkapan khusus.
-Aplikasi Perekat: Kami terkadang menggunakan manual, dan terkadang tergantung pada kasus sistem otomatis seperti robotika, motor servo, aktuator linier untuk mengirimkan perekat ke lokasi yang tepat dan kami menggunakan dispenser untuk mengirimkannya pada volume dan kuantitas yang tepat.
-Curing: Tergantung pada perekatnya, kami dapat menggunakan pengeringan dan curing sederhana serta curing di bawah lampu UV yang bertindak sebagai katalis atau curing panas dalam oven atau menggunakan elemen pemanas resistif yang dipasang pada jig dan fixture.
Kami menyarankan Anda mengklik di sini untukUNDUH Ilustrasi Skema Proses Pengencangan kami oleh AGS-TECH Inc.
Ini akan membantu Anda lebih memahami informasi yang kami berikan kepada Anda di bawah ini.
• PROSES PENGIKAT : Proses penyambungan mekanis kami terbagi dalam dua kategori utama: PENGIKAT dan SAMBUNGAN INTEGRAL. Contoh pengencang yang kami gunakan adalah sekrup, pin, mur, baut, paku keling. Contoh sambungan integral yang kami gunakan adalah snap and shrink fit, jahitan, crimps. Dengan menggunakan berbagai metode pengikatan, kami memastikan sambungan mekanis kami kuat dan andal selama bertahun-tahun digunakan. SEKRUP dan BAUT adalah beberapa pengencang yang paling umum digunakan untuk menyatukan dan memposisikan objek. Sekrup dan baut kami memenuhi standar ASME. Berbagai jenis sekrup dan baut dikerahkan termasuk sekrup tutup hex dan baut hex, sekrup dan baut lag, sekrup ujung ganda, sekrup dowel, sekrup mata, sekrup cermin, sekrup lembaran logam, sekrup penyesuaian halus, sekrup pengeboran sendiri dan sekrup self-tapping , setel sekrup, sekrup dengan ring built-in,…dan banyak lagi. Kami memiliki berbagai tipe kepala sekrup seperti countersunk, dome, round, flanged head dan berbagai tipe screw drive seperti slot, phillips, square, hex socket. RIVET di sisi lain adalah pengikat mekanis permanen yang terdiri dari poros silinder halus dan kepala di satu sisi. Setelah penyisipan, ujung paku keling yang lain berubah bentuk dan diameternya diperluas sehingga tetap di tempatnya. Dengan kata lain, sebelum pemasangan paku keling memiliki satu kepala dan setelah pemasangan memiliki dua kepala. Kami memasang berbagai jenis paku keling tergantung pada aplikasi, kekuatan, aksesibilitas dan biaya seperti paku keling padat/bulat, struktural, semi-tubular, blind, oscar, drive, flush, friction-lock, paku keling self-piercing. Riveting dapat lebih disukai dalam kasus di mana deformasi panas dan perubahan sifat material karena panas pengelasan perlu dihindari. Riveting juga menawarkan bobot yang ringan dan terutama kekuatan dan daya tahan yang baik terhadap gaya geser. Terhadap beban tarik namun sekrup, mur dan baut mungkin lebih cocok. Dalam proses CLINCHING kami menggunakan punch dan die khusus untuk membentuk interlock mekanis antara lembaran logam yang disambung. Pukulan mendorong lapisan lembaran logam ke dalam rongga mati dan menghasilkan pembentukan sambungan permanen. Tidak ada pemanasan dan pendinginan tidak diperlukan dalam clinching dan itu adalah proses kerja dingin. Ini adalah proses ekonomis yang dapat menggantikan pengelasan titik dalam beberapa kasus. Dalam PINNING kami menggunakan pin yang merupakan elemen mesin yang digunakan untuk mengamankan posisi bagian-bagian mesin relatif satu sama lain. Jenis utama adalah clevis pins, cotter pin, spring pin, dowel pins, and split pin. Dalam STAPLING kami menggunakan stapler dan staples yang merupakan pengencang bercabang dua yang digunakan untuk menyambung atau mengikat bahan. Stapel memiliki keuntungan sebagai berikut: Ekonomis, sederhana dan cepat digunakan, mahkota staples dapat digunakan untuk menjembatani material yang disambung, Mahkota staples dapat memfasilitasi menjembatani bagian seperti kabel dan mengikatnya ke permukaan tanpa melubangi atau merusak, penghapusan relatif mudah. PRESS FITTING dilakukan dengan mendorong bagian-bagian bersama-sama dan gesekan di antara mereka mengikat bagian-bagian itu. Bagian press fit yang terdiri dari poros berukuran besar dan lubang berukuran kecil umumnya dirakit dengan salah satu dari dua metode: Baik dengan menerapkan gaya atau memanfaatkan ekspansi termal atau kontraksi bagian. Ketika fitting press dibuat dengan menerapkan gaya, kita bisa menggunakan press hidrolik atau press yang dioperasikan dengan tangan. Di sisi lain, saat pemasangan tekan dibuat dengan ekspansi termal, kami memanaskan bagian yang membungkus dan merakitnya ke tempatnya saat panas. Ketika mereka mendingin, mereka berkontraksi dan kembali ke dimensi normal mereka. Ini menghasilkan kecocokan pers yang baik. Kami menyebutnya sebagai alternatif SHRINK-FITTING. Cara lain untuk melakukan ini adalah dengan mendinginkan bagian yang diselimuti sebelum perakitan dan kemudian menggesernya ke bagian kawinnya. Saat rakitan memanas, mereka mengembang dan kami mendapatkan kecocokan yang ketat. Metode terakhir ini mungkin lebih disukai dalam kasus di mana pemanasan menimbulkan risiko perubahan sifat material. Pendinginan lebih aman dalam kasus tersebut.
Komponen dan Rakitan Pneumatik & Hidrolik
• Katup, komponen hidrolik dan pneumatik seperti O-ring, washer, seal, gasket, ring, shim.
Karena katup dan komponen pneumatik memiliki variasi yang besar, kami tidak dapat mencantumkan semuanya di sini. Tergantung pada lingkungan fisik dan kimia aplikasi Anda, kami memiliki produk khusus untuk Anda. Harap sebutkan aplikasi, jenis komponen, spesifikasi, kondisi lingkungan seperti tekanan, suhu, cairan atau gas yang akan bersentuhan dengan katup dan komponen pneumatik Anda kepada kami; dan kami akan memilih produk yang paling cocok untuk Anda atau memproduksinya khusus untuk aplikasi Anda.