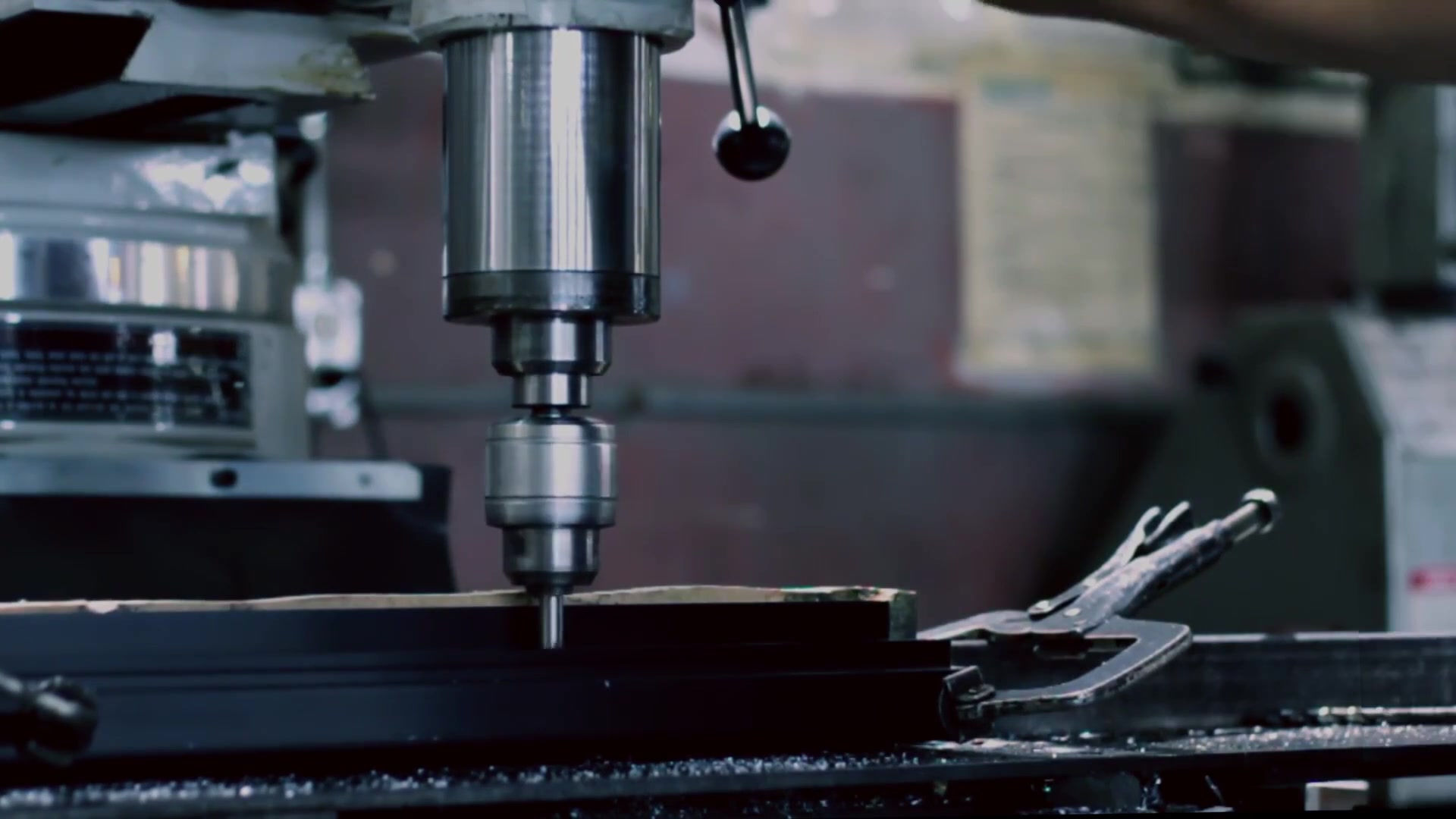
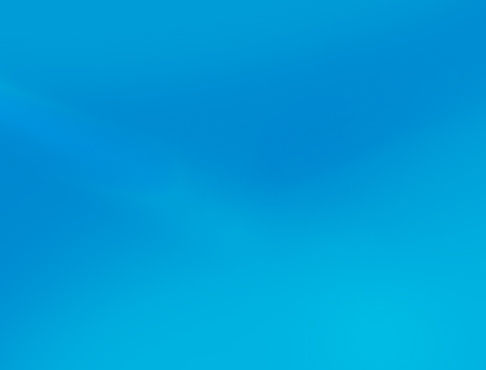
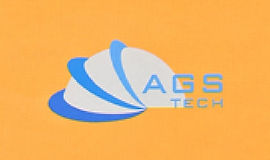
Produttore globale personalizzato, integratore, consolidatore, partner di outsourcing per un'ampia varietà di prodotti e servizi.
Siamo la tua fonte unica per la produzione, la fabbricazione, l'ingegnerizzazione, il consolidamento, l'integrazione, l'esternalizzazione di prodotti e servizi personalizzati e off-shelf.
Choose your Language
-
Produzione su misura
-
Produzione a contratto nazionale e globale
-
Esternalizzazione della produzione
-
Appalti nazionali e globali
-
Consolidamento
-
Integrazione ingegneristica
-
Servizi di ingegneria
Tra le molte tecniche di GIUNZIONE che impieghiamo nella produzione, viene data particolare enfasi a SALDATURA, BRASATURA, SALDATURA, INCOLLAGGIO ADESIVI E ASSEMBLAGGIO MECCANICO PERSONALIZZATO perché queste tecniche sono ampiamente utilizzate in applicazioni come la produzione di assemblaggi ermetici, la produzione di prodotti ad alta tecnologia e la sigillatura specializzata. Qui ci concentreremo sugli aspetti più specializzati di queste tecniche di giunzione in quanto sono legate alla produzione di prodotti e assemblaggi avanzati.
SALDATURA A FUSIONE: Usiamo il calore per fondere e fondere i materiali. Il calore è fornito da elettricità o travi ad alta energia. I tipi di saldatura per fusione che impieghiamo sono SALDATURA A GAS OXYFUEL, SALDATURA AD ARCO, SALDATURA A FASCIO AD ALTA ENERGIA.
SALDATURA A STATO SOLIDO: Uniamo le parti senza fusione e fusione. I nostri metodi di saldatura allo stato solido sono FREDDO, ULTRASUONI, RESISTENZA, FRICTION, EXPLOSION WELDING e DIFFUSION BONDING.
BRASATURA E SALDATURA: Usano metalli d'apporto e ci danno il vantaggio di lavorare a temperature più basse rispetto alla saldatura, quindi meno danni strutturali ai prodotti. Informazioni sul nostro impianto di brasatura che produce raccordi da ceramica a metallo, tenuta ermetica, passanti per il vuoto, componenti per il controllo dei fluidi e per alto e ultra alto vuoto sono disponibili qui:Brochure della fabbrica di brasatura
INCOLLAGGIO ADESIVI: A causa della diversità degli adesivi utilizzati nell'industria e anche della diversità delle applicazioni, abbiamo una pagina dedicata a questo. Per andare alla nostra pagina sull'incollaggio, fare clic qui.
MONTAGGIO MECCANICO PERSONALIZZATO: Utilizziamo una varietà di elementi di fissaggio come bulloni, viti, dadi, rivetti. I nostri elementi di fissaggio non si limitano agli elementi di fissaggio standard standard. Progettiamo, sviluppiamo e produciamo elementi di fissaggio speciali realizzati con materiali non standard in modo che possano soddisfare i requisiti per applicazioni speciali. A volte si desidera la non conduttività elettrica o termica mentre a volte si desidera la conduttività. Per alcune applicazioni speciali, un cliente potrebbe desiderare elementi di fissaggio speciali che non possono essere rimossi senza distruggere il prodotto. Ci sono infinite idee e applicazioni. Abbiamo tutto per te, se non off-shelf possiamo svilupparlo rapidamente. Per andare alla nostra pagina sull'assemblaggio meccanico, fare clic qui. Esaminiamo le nostre varie tecniche di giunzione in modo più dettagliato.
SALDATURA A GAS OXYFUEL (OFW): Utilizziamo un gas combustibile miscelato con ossigeno per produrre la fiamma di saldatura. Quando usiamo l'acetilene come combustibile e ossigeno, lo chiamiamo saldatura a gas ossiacetilenico. Nel processo di combustione del gas ossicombustibile si verificano due reazioni chimiche:
C2H2 + O2 ------» 2CO + H2 + Riscald
2CO + H2 + 1,5 O2--------» 2 CO2 + H2O + Calore
La prima reazione dissocia l'acetilene in monossido di carbonio e idrogeno producendo circa il 33% del calore totale generato. Il secondo processo sopra rappresenta un'ulteriore combustione dell'idrogeno e del monossido di carbonio mentre produce circa il 67% del calore totale. Le temperature nella fiamma sono comprese tra 1533 e 3573 Kelvin. La percentuale di ossigeno nella miscela di gas è importante. Se il contenuto di ossigeno è superiore alla metà, la fiamma diventa un agente ossidante. Questo è indesiderabile per alcuni metalli ma desiderabile per altri. Un esempio quando la fiamma ossidante è desiderabile sono le leghe a base di rame perché forma uno strato di passivazione sul metallo. Quando invece si riduce il contenuto di ossigeno, non è possibile la combustione completa e la fiamma diventa una fiamma riducente (carburante). Le temperature in una fiamma riducente sono più basse e quindi è adatto per processi come la saldatura e la brasatura. Anche altri gas sono potenziali combustibili, ma presentano alcuni svantaggi rispetto all'acetilene. Occasionalmente forniamo metalli d'apporto alla zona di saldatura sotto forma di barre di apporto o filo. Alcuni di essi sono rivestiti con fondente per ritardare l'ossidazione delle superfici e proteggere così il metallo fuso. Un ulteriore vantaggio che il flusso ci offre è la rimozione di ossidi e altre sostanze dalla zona di saldatura. Questo porta a un legame più forte. Una variante della saldatura a gas ossicombustibile è la SALDATURA A GAS A PRESSIONE, in cui i due componenti vengono riscaldati alla loro interfaccia utilizzando una torcia a gas ossiacetilenico e una volta che l'interfaccia inizia a fondere, la torcia viene estratta e viene applicata una forza assiale per premere insieme le due parti fino a quando l'interfaccia non si è solidificata.
SALDATURA AD ARCO: Usiamo energia elettrica per produrre un arco tra la punta dell'elettrodo e le parti da saldare. L'alimentazione può essere AC o DC mentre gli elettrodi sono consumabili o non consumabili. Il trasferimento di calore nella saldatura ad arco può essere espresso dalla seguente equazione:
H / l = ex VI / v
Qui H è l'apporto termico, l è la lunghezza della saldatura, V e I sono la tensione e la corrente applicate, v è la velocità di saldatura ed e è l'efficienza del processo. Maggiore è l'efficienza "e", più vantaggiosamente viene utilizzata l'energia disponibile per fondere il materiale. La portata termica può anche essere espressa come:
H = ux (Volume) = ux A xl
Qui u è l'energia specifica per la fusione, A la sezione trasversale della saldatura e l la lunghezza della saldatura. Dalle due equazioni precedenti possiamo ottenere:
v = ex VI / u A
Una variante della saldatura ad arco è la SALDATURA AD ARCO METALLICO SHIELDED (SMAW) che costituisce circa il 50% di tutti i processi di saldatura industriale e di manutenzione. LA SALDATURA AD ARCO ELETTRICO (SALDATURA A STICK) viene eseguita toccando la punta di un elettrodo rivestito sul pezzo e ritirandolo rapidamente a una distanza sufficiente a mantenere l'arco. Chiamiamo questo processo anche saldatura a bastoncino perché gli elettrodi sono bastoncini sottili e lunghi. Durante il processo di saldatura, la punta dell'elettrodo fonde insieme al suo rivestimento e al metallo base in prossimità dell'arco. Una miscela di metallo di base, metallo dell'elettrodo e sostanze del rivestimento dell'elettrodo si solidifica nell'area di saldatura. Il rivestimento dell'elettrodo si disossida e fornisce un gas di protezione nella zona di saldatura, proteggendolo così dall'ossigeno nell'ambiente. Pertanto il processo è indicato come saldatura ad arco metallico schermato. Utilizziamo correnti comprese tra 50 e 300 Ampere e livelli di potenza generalmente inferiori a 10 kW per prestazioni di saldatura ottimali. Importante è anche la polarità della corrente continua (direzione del flusso di corrente). La polarità rettilinea in cui il pezzo è positivo e l'elettrodo è negativo è preferita nella saldatura di lamiere a causa della sua penetrazione ridotta e anche per giunti con giochi molto ampi. Quando abbiamo la polarità inversa, cioè l'elettrodo è positivo e il pezzo negativo, possiamo ottenere penetrazioni di saldatura più profonde. Con la corrente alternata, poiché disponiamo di archi pulsanti, possiamo saldare sezioni spesse utilizzando elettrodi di grande diametro e correnti massime. Il metodo di saldatura SMAW è adatto per spessori di pezzi da 3 a 19 mm e anche più utilizzando tecniche a più passate. La scoria formata sopra la saldatura deve essere rimossa utilizzando una spazzola metallica, in modo che non vi siano corrosione e rotture nell'area di saldatura. Questo ovviamente si aggiunge al costo della saldatura ad arco metallico schermato. Tuttavia, la SMAW è la tecnica di saldatura più popolare nell'industria e nei lavori di riparazione.
SALDATURA AD ARCO SOMMERSO (SEGA): In questo processo proteggiamo l'arco di saldatura utilizzando materiali a flusso granulare come calce, silice, floruro di calcio, ossido di manganese….ecc. Il flusso granulare viene immesso nella zona di saldatura per gravità attraverso un ugello. Il flusso che ricopre la zona di saldatura fusa protegge in modo significativo da scintille, fumi, radiazioni UV, ecc. e funge da isolante termico, permettendo così al calore di penetrare in profondità nel pezzo. Il flusso non fuso viene recuperato, trattato e riutilizzato. Una bobina di nudo viene utilizzata come elettrodo e alimentata attraverso un tubo all'area di saldatura. Usiamo correnti comprese tra 300 e 2000 Ampere. Il processo di saldatura ad arco sommerso (SAW) è limitato alle posizioni orizzontali e piatte e alle saldature circolari se è possibile la rotazione della struttura circolare (come i tubi) durante la saldatura. Le velocità possono raggiungere i 5 m/min. Il processo SAW è adatto per lamiere spesse e consente saldature di alta qualità, tenaci, duttili e uniformi. La produttività, ovvero la quantità di materiale di saldatura depositato all'ora, è da 4 a 10 volte la quantità rispetto al processo SMAW.
Un altro processo di saldatura ad arco, vale a dire il GAS METAL ARC WELDING (GMAW) o in alternativa denominato METAL INERT GAS WELDING (MIG) si basa sull'area di saldatura protetta da fonti esterne di gas come elio, argon, anidride carbonica ... ecc. Potrebbero essere presenti ulteriori disossidanti nel metallo dell'elettrodo. Il filo di consumo viene alimentato attraverso un ugello nella zona di saldatura. La fabbricazione che coinvolge metalli sia ferrosi che non ferrosi viene eseguita utilizzando la saldatura ad arco di metalli gassosi (GMAW). La produttività della saldatura è circa 2 volte quella del processo SMAW. Vengono utilizzate apparecchiature di saldatura automatizzate. Il metallo viene trasferito in uno dei tre modi seguenti in questo processo: "Trasferimento spray" comporta il trasferimento di diverse centinaia di piccole goccioline di metallo al secondo dall'elettrodo all'area di saldatura. Nel "trasferimento globulare", invece, vengono utilizzati gas ricchi di anidride carbonica e globuli di metallo fuso vengono spinti dall'arco elettrico. Le correnti di saldatura sono elevate e la penetrazione della saldatura è più profonda, la velocità di saldatura è maggiore rispetto al trasferimento a spruzzo. Pertanto il trasferimento globulare è migliore per la saldatura di sezioni più pesanti. Infine, nel metodo "Cortocircuito", la punta dell'elettrodo tocca il bagno di saldatura fuso, cortocircuitandolo mentre il metallo a velocità superiori a 50 goccioline/secondo viene trasferito in singole goccioline. Vengono utilizzate basse correnti e tensioni insieme a un filo più sottile. Le potenze utilizzate sono di circa 2 kW e le temperature relativamente basse, rendendo questo metodo adatto per lamiere sottili di spessore inferiore a 6 mm.
Un'altra variazione del processo di SALDATURA AD ARCO FLUX-CORED (FCAW) è simile alla saldatura ad arco di metallo gas, tranne per il fatto che l'elettrodo è un tubo riempito di flusso. I vantaggi dell'utilizzo di elettrodi a flusso animato sono che producono archi più stabili, ci danno l'opportunità di migliorare le proprietà dei metalli di saldatura, la natura meno fragile e flessibile del suo flusso rispetto alla saldatura SMAW, i contorni di saldatura migliorati. Gli elettrodi animati autoprotetti contengono materiali che schermano la zona di saldatura dall'atmosfera. Usiamo circa 20 kW di potenza. Come il processo GMAW, anche il processo FCAW offre l'opportunità di automatizzare i processi per la saldatura continua ed è economico. È possibile sviluppare diverse sostanze chimiche dei metalli di saldatura aggiungendo varie leghe al nucleo di flusso.
In ELECTROGAS WELDING (EGW) saldiamo i pezzi posizionati da bordo a bordo. A volte è anche chiamata SALDATURA DI TESTA. Il metallo di saldatura viene inserito in una cavità di saldatura tra due pezzi da unire. Lo spazio è racchiuso da due dighe raffreddate ad acqua per evitare che le scorie fuse fuoriescano. Le dighe vengono sollevate da azionamenti meccanici. Quando il pezzo può essere ruotato, possiamo utilizzare la tecnica della saldatura a elettrogas anche per la saldatura circonferenziale dei tubi. Gli elettrodi vengono alimentati attraverso un condotto per mantenere un arco continuo. Le correnti possono essere di circa 400 Ampere o 750 Ampere e livelli di potenza di circa 20 kW. I gas inerti provenienti da un elettrodo animato o da una sorgente esterna forniscono schermatura. Utilizziamo la saldatura a elettrogas (EGW) per metalli come acciai, titanio….ecc con spessori da 12mm a 75mm. La tecnica è adatta per grandi strutture.
Tuttavia, in un'altra tecnica chiamata SALDATURA A ELETTROSLAG (ESW) l'arco si accende tra l'elettrodo e la parte inferiore del pezzo e viene aggiunto il flusso. Quando la scoria fusa raggiunge la punta dell'elettrodo, l'arco si spegne. L'energia viene continuamente fornita attraverso la resistenza elettrica delle scorie fuse. Possiamo saldare lamiere con spessori compresi tra 50 mm e 900 mm e anche superiori. Le correnti sono di circa 600 Ampere mentre le tensioni sono comprese tra 40 e 50 V. Le velocità di saldatura sono di circa 12-36 mm/min. Le applicazioni sono simili alla saldatura a elettrogas.
Uno dei nostri processi con elettrodi non consumabili, la SALDATURA AD ARCO DI TUNGSTENO CON GAS (GTAW), nota anche come SALDATURA CON GAS INERTE DI TUNGSTENO (TIG), prevede la fornitura di un metallo d'apporto mediante un filo. Per giunti ravvicinati a volte non utilizziamo il metallo d'apporto. Nel processo TIG non utilizziamo il flusso, ma utilizziamo argon ed elio per la schermatura. Il tungsteno ha un alto punto di fusione e non viene consumato nel processo di saldatura TIG, quindi è possibile mantenere una corrente costante e spazi vuoti dell'arco. I livelli di potenza sono compresi tra 8 e 20 kW e le correnti a 200 Ampere (CC) o 500 Ampere (CA). Per l'alluminio e il magnesio utilizziamo la corrente alternata per la sua funzione di pulizia dell'ossido. Per evitare la contaminazione dell'elettrodo di tungsteno, evitiamo il suo contatto con metalli fusi. La saldatura ad arco di tungsteno a gas (GTAW) è particolarmente utile per la saldatura di metalli sottili. Le saldature GTAW sono di altissima qualità con una buona finitura superficiale.
A causa del costo più elevato dell'idrogeno gassoso, una tecnica meno utilizzata è la SALDATURA A IDROGENO ATOMICO (AHW), in cui generiamo un arco tra due elettrodi di tungsteno in un'atmosfera schermante di gas idrogeno che scorre. L'AHW è anche un processo di saldatura ad elettrodo non consumabile. L'idrogeno biatomico H2 si scompone nella sua forma atomica vicino all'arco di saldatura dove le temperature sono superiori a 6273 Kelvin. Mentre si rompe, assorbe una grande quantità di calore dall'arco. Quando gli atomi di idrogeno colpiscono la zona di saldatura che è una superficie relativamente fredda, si ricombinano in forma biatomica e rilasciano il calore immagazzinato. L'energia può essere variata cambiando il pezzo in lavorazione alla distanza dell'arco.
In un altro processo con elettrodi non consumabili, PLASMA ARC WELDING (PAW) abbiamo un arco plasma concentrato diretto verso la zona di saldatura. Le temperature raggiungono i 33.273 Kelvin in PAW. Un numero quasi uguale di elettroni e ioni costituisce il gas plasma. Un arco pilota a bassa corrente avvia il plasma che si trova tra l'elettrodo di tungsteno e l'orifizio. Le correnti di esercizio sono generalmente di circa 100 Ampere. Può essere alimentato un metallo d'apporto. Nella saldatura ad arco al plasma, la schermatura è ottenuta mediante un anello di schermatura esterno e utilizzando gas come argon ed elio. Nella saldatura ad arco al plasma, l'arco può trovarsi tra l'elettrodo e il pezzo o tra l'elettrodo e l'ugello. Questa tecnica di saldatura presenta i vantaggi rispetto ad altri metodi di maggiore concentrazione di energia, capacità di saldatura più profonda e più stretta, migliore stabilità dell'arco, velocità di saldatura più elevate fino a 1 metro/min, minore distorsione termica. Generalmente utilizziamo la saldatura ad arco plasma per spessori inferiori a 6 mm e talvolta fino a 20 mm per alluminio e titanio.
SALDATURA A FASCIO AD ALTA ENERGIA: Un altro tipo di metodo di saldatura per fusione con saldatura a fascio di elettroni (EBW) e saldatura laser (LBW) in due varianti. Queste tecniche sono di particolare valore per il nostro lavoro di produzione di prodotti high-tech. Nella saldatura a fascio di elettroni, gli elettroni ad alta velocità colpiscono il pezzo e la loro energia cinetica viene convertita in calore. Lo stretto fascio di elettroni viaggia facilmente nella camera a vuoto. Generalmente utilizziamo l'alto vuoto nella saldatura a fascio elettronico. È possibile saldare piastre spesse fino a 150 mm. Non sono necessari gas di protezione, flusso o materiale di riempimento. I cannoni a raggi Elecron hanno una capacità di 100 kW. Sono possibili saldature profonde e strette con proporzioni elevate fino a 30 e piccole zone soggette a calore. Le velocità di saldatura possono raggiungere i 12 m/min. Nella saldatura a raggio laser utilizziamo laser ad alta potenza come fonte di calore. Raggi laser di soli 10 micron ad alta densità consentono una penetrazione profonda nel pezzo. Con la saldatura a raggio laser è possibile ottenere rapporti profondità-larghezza fino a 10. Utilizziamo sia laser pulsati che a onda continua, con il primo in applicazioni per materiali sottili e il secondo principalmente per pezzi spessi fino a circa 25 mm. I livelli di potenza sono fino a 100 kW. La saldatura a raggio laser non è adatta per materiali otticamente molto riflettenti. I gas possono essere utilizzati anche nel processo di saldatura. Il metodo di saldatura a raggio laser è adatto per l'automazione e la produzione ad alto volume e può offrire velocità di saldatura comprese tra 2,5 m/min e 80 m/min. Uno dei principali vantaggi offerti da questa tecnica di saldatura è l'accesso ad aree in cui non è possibile utilizzare altre tecniche. I raggi laser possono viaggiare facilmente in regioni così difficili. Non è necessario il vuoto come nella saldatura a fascio di elettroni. Saldature con buona qualità e resistenza, basso ritiro, bassa distorsione, bassa porosità possono essere ottenute con saldatura a raggio laser. I raggi laser possono essere facilmente manipolati e modellati utilizzando cavi in fibra ottica. La tecnica è quindi adatta per la saldatura di assiemi ermetici di precisione, pacchetti elettronici... ecc.
Diamo un'occhiata alle nostre tecniche di SALDATURA A STATO SOLIDO. La SALDATURA A FREDDO (CW) è un processo in cui la pressione invece del calore viene applicata utilizzando stampi o rulli alle parti accoppiate. Nella saldatura a freddo, almeno una delle parti di accoppiamento deve essere duttile. I migliori risultati si ottengono con due materiali simili. Se i due metalli da unire con la saldatura a freddo sono dissimili si possono ottenere giunzioni deboli e fragili. Il metodo di saldatura a freddo è adatto per pezzi morbidi, duttili e di piccole dimensioni come collegamenti elettrici, bordi di contenitori termosensibili, nastri bimetallici per termostati... ecc. Una variante della saldatura a freddo è la saldatura a rulli (o saldatura a rulli), in cui la pressione viene applicata attraverso una coppia di rulli. A volte eseguiamo la saldatura a rulli a temperature elevate per una migliore resistenza interfacciale.
Un altro processo di saldatura allo stato solido che utilizziamo è la SALDATURA A ULTRASUONI (USW), in cui i pezzi sono sottoposti a una forza normale statica ea sollecitazioni di taglio oscillanti. Le sollecitazioni di taglio oscillanti vengono applicate attraverso la punta di un trasduttore. La saldatura ad ultrasuoni distribuisce oscillazioni con frequenze da 10 a 75 kHz. In alcune applicazioni come la saldatura continua, utilizziamo un disco di saldatura rotante come punta. Le sollecitazioni di taglio applicate ai pezzi provocano piccole deformazioni plastiche, rompono gli strati di ossido, contaminanti e portano al legame allo stato solido. Le temperature coinvolte nella saldatura ad ultrasuoni sono molto al di sotto delle temperature del punto di fusione per i metalli e non avviene alcuna fusione. Usiamo spesso il processo di saldatura a ultrasuoni (USW) per materiali non metallici come la plastica. Nei termoplastici, tuttavia, le temperature raggiungono i punti di fusione.
Un'altra tecnica popolare, nella SALDATURA PER FRICTION (FRW) il calore viene generato attraverso l'attrito all'interfaccia dei pezzi da unire. Nella saldatura ad attrito teniamo fermo uno dei pezzi mentre l'altro viene trattenuto in un'attrezzatura e ruotato a velocità costante. I pezzi vengono quindi portati in contatto sotto una forza assiale. La velocità di rotazione superficiale nella saldatura ad attrito può raggiungere in alcuni casi i 900 m/min. Dopo un sufficiente contatto interfacciale, il pezzo in rotazione viene arrestato improvvisamente e la forza assiale viene aumentata. La zona di saldatura è generalmente una regione stretta. La tecnica della saldatura ad attrito può essere utilizzata per unire parti solide e tubolari in diversi materiali. È possibile che si sviluppi un bagliore sull'interfaccia in FRW, ma questo lampo può essere rimosso mediante lavorazione secondaria o rettifica. Esistono variazioni del processo di saldatura per attrito. Ad esempio la “saldatura ad attrito inerziale” prevede un volano la cui energia cinetica rotazionale viene utilizzata per saldare le parti. La saldatura è completa quando il volano si ferma. La massa rotante può essere variata e quindi l'energia cinetica di rotazione. Un'altra variante è la "saldatura ad attrito lineare", in cui viene imposto un movimento alternativo lineare su almeno uno dei componenti da unire. Nella saldatura ad attrito lineare le parti non devono essere circolari, possono essere rettangolari, quadrate o di altra forma. Le frequenze possono essere nell'ordine delle decine di Hz, le ampiezze nell'intervallo dei millimetri e le pressioni nell'ordine delle decine o centinaia di MPa. Infine, la "saldatura per attrito e agitazione" è in qualche modo diversa dalle altre due spiegate sopra. Mentre nella saldatura ad attrito inerziale e nella saldatura ad attrito lineare il riscaldamento delle interfacce è ottenuto mediante attrito sfregando due superfici di contatto, nel metodo di saldatura ad attrito con agitazione un terzo corpo viene strofinato contro le due superfici da unire. Un utensile rotante di diametro compreso tra 5 e 6 mm viene portato a contatto con il giunto. Le temperature possono aumentare fino a valori compresi tra 503 e 533 Kelvin. Ha luogo il riscaldamento, la miscelazione e l'agitazione del materiale nel giunto. Usiamo la saldatura ad attrito su una varietà di materiali tra cui alluminio, plastica e compositi. Le saldature sono uniformi e la qualità è elevata con pori minimi. Nella saldatura ad agitazione ad attrito non vengono prodotti fumi o schizzi e il processo è ben automatizzato.
SALDATURA A RESISTENZA (RW): Il calore necessario per la saldatura è prodotto dalla resistenza elettrica tra i due pezzi da unire. Nella saldatura a resistenza non vengono utilizzati flussi, gas di protezione o elettrodi consumabili. Il riscaldamento Joule avviene nella saldatura a resistenza e può essere espresso come:
H = (Quadrato I) x R xtx K
H è il calore generato in joule (watt-secondi), I la corrente in Ampere, R la resistenza in Ohm, t è il tempo in secondi in cui scorre la corrente. Il fattore K è minore di 1 e rappresenta la frazione di energia che non viene persa per irraggiamento e conduzione. Le correnti nei processi di saldatura a resistenza possono raggiungere livelli fino a 100.000 A, ma le tensioni sono in genere comprese tra 0,5 e 10 Volt. Gli elettrodi sono in genere realizzati in leghe di rame. Sia materiali simili che dissimili possono essere uniti mediante saldatura a resistenza. Esistono diverse varianti per questo processo: la "saldatura a punti di resistenza" prevede due elettrodi tondi opposti che entrano in contatto con le superfici della giunzione sovrapposta delle due lamiere. La pressione viene applicata fino allo spegnimento della corrente. La pepita di saldatura ha generalmente un diametro fino a 10 mm. La saldatura a punti a resistenza lascia segni di indentazione leggermente scoloriti nei punti di saldatura. La saldatura a punti è la nostra tecnica di saldatura a resistenza più popolare. Nella saldatura a punti vengono utilizzate varie forme di elettrodi per raggiungere aree difficili. La nostra attrezzatura per la saldatura a punti è controllata da CNC e dispone di più elettrodi che possono essere utilizzati contemporaneamente. Un'altra variante di "saldatura a resistenza continua" viene eseguita con elettrodi a ruota oa rullo che producono punti di saldatura continui ogni volta che la corrente raggiunge un livello sufficientemente alto nel ciclo di alimentazione CA. I giunti prodotti dalla saldatura a resistenza sono a tenuta di liquidi e gas. Velocità di saldatura di circa 1,5 m/min sono normali per lamiere sottili. Si possono applicare correnti intermittenti in modo da produrre punti di saldatura agli intervalli desiderati lungo la giunzione. Nella “saldatura a proiezione di resistenza” goffriamo una o più sporgenze (fossette) su una delle superfici del pezzo da saldare. Queste proiezioni possono essere rotonde o ovali. In questi punti goffrati che entrano in contatto con la parte di accoppiamento si raggiungono alte temperature localizzate. Gli elettrodi esercitano una pressione per comprimere queste proiezioni. Gli elettrodi nella saldatura a proiezione di resistenza hanno punte piatte e sono leghe di rame raffreddate ad acqua. Il vantaggio della saldatura a proiezione di resistenza è la nostra capacità di eseguire più saldature in una sola passata, quindi la maggiore durata dell'elettrodo, la capacità di saldare lamiere di vari spessori, la capacità di saldare dadi e bulloni alle lamiere. Lo svantaggio della saldatura a proiezione di resistenza è il costo aggiuntivo della goffratura delle fossette. Ancora un'altra tecnica, nella "saldatura flash", il calore viene generato dall'arco alle estremità dei due pezzi quando iniziano a entrare in contatto. Questo metodo può anche essere considerato in alternativa la saldatura ad arco. La temperatura all'interfaccia aumenta e il materiale si ammorbidisce. Viene applicata una forza assiale e si forma una saldatura nella regione ammorbidita. Dopo che la saldatura flash è completa, il giunto può essere lavorato per un aspetto migliore. La qualità della saldatura ottenuta mediante saldatura flash è buona. I livelli di potenza sono da 10 a 1500 kW. La saldatura flash è adatta per la giunzione da bordo a bordo di metalli simili o dissimili fino a 75 mm di diametro e lamiere con uno spessore compreso tra 0,2 mm e 25 mm. La "saldatura ad arco di perno" è molto simile alla saldatura flash. Il prigioniero come un bullone o un'asta filettata funge da elettrodo mentre viene unito a un pezzo come una piastra. Per concentrare il calore generato, prevenire l'ossidazione e trattenere il metallo fuso nella zona di saldatura, attorno al giunto viene posizionato un anello in ceramica monouso. Infine la “saldatura a percussione” un altro processo di saldatura a resistenza, utilizza un condensatore per fornire l'energia elettrica. Nella saldatura a percussione la potenza viene scaricata in pochi millisecondi di tempo sviluppando un elevato calore localizzato al giunto. Utilizziamo ampiamente la saldatura a percussione nell'industria manifatturiera elettronica, dove è necessario evitare il riscaldamento di componenti elettronici sensibili in prossimità del giunto.
Una tecnica chiamata EXPLOSION WELDING prevede la detonazione di uno strato di esplosivo che viene posto su uno dei pezzi da unire. L'altissima pressione esercitata sul pezzo produce un'interfaccia turbolenta e ondulata e si verifica un incastro meccanico. Le forze di adesione nella saldatura esplosiva sono molto elevate. La saldatura per esplosione è un buon metodo per il rivestimento di lastre con metalli diversi. Dopo il rivestimento, le lastre possono essere laminate in sezioni più sottili. A volte utilizziamo la saldatura a esplosione per espandere i tubi in modo che vengano sigillati saldamente contro la piastra.
Il nostro ultimo metodo nell'ambito della giunzione allo stato solido è DIFFUSION BONDING o DIFFUSION WELDING (DFW) in cui una buona giunzione si ottiene principalmente mediante la diffusione di atomi attraverso l'interfaccia. Anche una certa deformazione plastica all'interfaccia contribuisce alla saldatura. Le temperature coinvolte sono di circa 0,5 Tm dove Tm è la temperatura di fusione del metallo. La forza di adesione nella saldatura a diffusione dipende da pressione, temperatura, tempo di contatto e pulizia delle superfici di contatto. A volte utilizziamo metalli d'apporto nell'interfaccia. Il calore e la pressione sono richiesti nel legame per diffusione e sono forniti da resistenza elettrica o forno e pesi morti, pressa o altro. Metalli simili e dissimili possono essere uniti con saldatura a diffusione. Il processo è relativamente lento a causa del tempo impiegato dagli atomi per migrare. DFW può essere automatizzato ed è ampiamente utilizzato nella fabbricazione di parti complesse per l'industria aerospaziale, elettronica e medica. I prodotti fabbricati includono impianti ortopedici, sensori, elementi strutturali aerospaziali. L'incollaggio per diffusione può essere combinato con SUPERPLASTIC FORMING per realizzare strutture complesse in lamiera. Posizioni selezionate sui fogli vengono prima incollate per diffusione e quindi le regioni non legate vengono espanse in uno stampo usando la pressione dell'aria. Le strutture aerospaziali con un elevato rapporto rigidità/peso vengono prodotte utilizzando questa combinazione di metodi. Il processo combinato di saldatura a diffusione/formatura superplastica riduce il numero di parti richieste eliminando la necessità di elementi di fissaggio, produce parti a bassa sollecitazione altamente accurate in modo economico e con tempi di consegna brevi.
BRASATURA: Le tecniche di brasatura e saldatura prevedono temperature inferiori a quelle richieste per la saldatura. Tuttavia, le temperature di brasatura sono superiori a quelle di saldatura. Nella brasatura un metallo d'apporto viene posizionato tra le superfici da unire e le temperature vengono portate alla temperatura di fusione del materiale d'apporto superiore a 723 Kelvin ma al di sotto delle temperature di fusione dei pezzi. Il metallo fuso riempie lo spazio a stretto contatto tra i pezzi. Il raffreddamento e la successiva solidificazione del metallo di limatura danno luogo a giunzioni forti. Nella saldobrasatura il metallo d'apporto si deposita sul giunto. Nella saldobrasatura viene utilizzato molto più metallo d'apporto rispetto alla brasatura. La torcia ossiacetilenica con fiamma ossidante viene utilizzata per depositare il metallo d'apporto nella saldobrasatura. A causa delle temperature più basse durante la brasatura, i problemi nelle zone colpite dal calore come la deformazione e le sollecitazioni residue sono minori. Minore è lo spazio libero nella brasatura, maggiore è la resistenza al taglio del giunto. La massima resistenza alla trazione viene tuttavia raggiunta con un gioco ottimale (un valore di picco). Al di sotto e al di sopra di questo valore ottimale, la resistenza alla trazione nella brasatura diminuisce. I giochi tipici nella brasatura possono essere compresi tra 0,025 e 0,2 mm. Utilizziamo una varietà di materiali per brasatura con forme diverse come pezzi, polvere, anelli, filo, nastro…..ecc. e può produrre queste prestazioni appositamente per il tuo design o la geometria del prodotto. Determiniamo anche il contenuto dei materiali di brasatura in base ai materiali di base e all'applicazione. Utilizziamo frequentemente flussi nelle operazioni di brasatura per rimuovere strati di ossido indesiderati e prevenire l'ossidazione. Per evitare la successiva corrosione, i flussi vengono generalmente rimossi dopo l'operazione di giunzione. AGS-TECH Inc. utilizza vari metodi di brasatura, tra cui:
- Brasatura a torcia
- Brasatura a forno
- Brasatura ad induzione
- Brasatura a resistenza
- Brasatura ad immersione
- Brasatura a infrarossi
- Brasatura a diffusione
- Fascio ad alta energia
I nostri esempi più comuni di giunti brasati sono realizzati con metalli dissimili con una buona resistenza come punte in metallo duro, inserti, pacchetti ermetici optoelettronici, guarnizioni.
SALDATURA : Questa è una delle nostre tecniche più utilizzate in cui la saldatura (metallo d'apporto) riempie il giunto come nella brasatura tra componenti strettamente aderenti. Le nostre saldature hanno punti di fusione inferiori a 723 Kelvin. Distribuiamo sia la saldatura manuale che automatizzata nelle operazioni di produzione. Rispetto alla brasatura, le temperature di saldatura sono inferiori. La saldatura non è molto adatta per applicazioni ad alta temperatura o ad alta resistenza. Utilizziamo saldature senza piombo e leghe stagno-piombo, stagno-zinco, piombo-argento, cadmio-argento, zinco-alluminio oltre ad altre leghe per la saldatura. Sia gli acidi e i sali a base di resine non corrosivi che quelli inorganici vengono utilizzati come disossidante nella saldatura. Utilizziamo flussi speciali per saldare metalli con bassa saldabilità. Nelle applicazioni in cui dobbiamo saldare materiali ceramici, vetro o grafite, placcamo prima le parti con un metallo adatto per una maggiore saldabilità. Le nostre tecniche di saldatura popolari sono:
-Riflusso o incollare la saldatura
- Saldatura ad onda
- Saldatura a forno
- Saldatura a torcia
-Saldatura ad induzione
- Saldatura a ferro
-Saldatura a resistenza
- Saldatura a immersione
- Saldatura ad ultrasuoni
- Saldatura a infrarossi
La saldatura a ultrasuoni ci offre un vantaggio unico per cui la necessità di flussi viene eliminata grazie all'effetto di cavitazione ultrasonica che rimuove i film di ossido dalle superfici da unire. La saldatura a rifusione e a onda sono le nostre tecniche eccezionali a livello industriale per la produzione di grandi volumi nell'elettronica e quindi vale la pena spiegarle in modo più dettagliato. Nella saldatura a rifusione, utilizziamo paste semisolide che includono particelle di metallo saldato. La pasta viene posizionata sul giunto utilizzando un processo di retinatura o stencil. Nei circuiti stampati (PCB) utilizziamo frequentemente questa tecnica. Quando i componenti elettrici vengono posizionati su questi pad dalla pasta, la tensione superficiale mantiene allineati i pacchetti a montaggio superficiale. Dopo aver posizionato i componenti, riscaldiamo l'assieme in un forno in modo che avvenga la saldatura a rifusione. Durante questo processo, i solventi nella pasta evaporano, il flusso nella pasta viene attivato, i componenti vengono preriscaldati, le particelle di saldatura vengono sciolte e bagnano il giunto e infine l'assieme PCB viene raffreddato lentamente. La nostra seconda tecnica popolare per la produzione ad alto volume di schede PCB, vale a dire la saldatura ad onda, si basa sul fatto che le saldature fuse bagnano le superfici metalliche e formano buoni legami solo quando il metallo è preriscaldato. Un'onda laminare stazionaria di saldatura fusa viene prima generata da una pompa e i PCB preriscaldati e preflussi vengono convogliati sull'onda. La saldatura bagna solo le superfici metalliche esposte ma non bagna i pacchetti polimerici IC né i circuiti stampati rivestiti in polimero. Un getto di acqua calda ad alta velocità espelle la saldatura in eccesso dal giunto e impedisce la formazione di ponti tra i conduttori adiacenti. Nella saldatura ad onda di pacchetti a montaggio superficiale, li leghiamo prima adesivamente al circuito stampato prima di saldare. Anche in questo caso viene utilizzata la schermatura e lo stencil, ma questa volta per la resina epossidica. Dopo che i componenti sono stati posizionati nelle posizioni corrette, la resina epossidica viene polimerizzata, le schede vengono invertite e viene eseguita la saldatura ad onda.