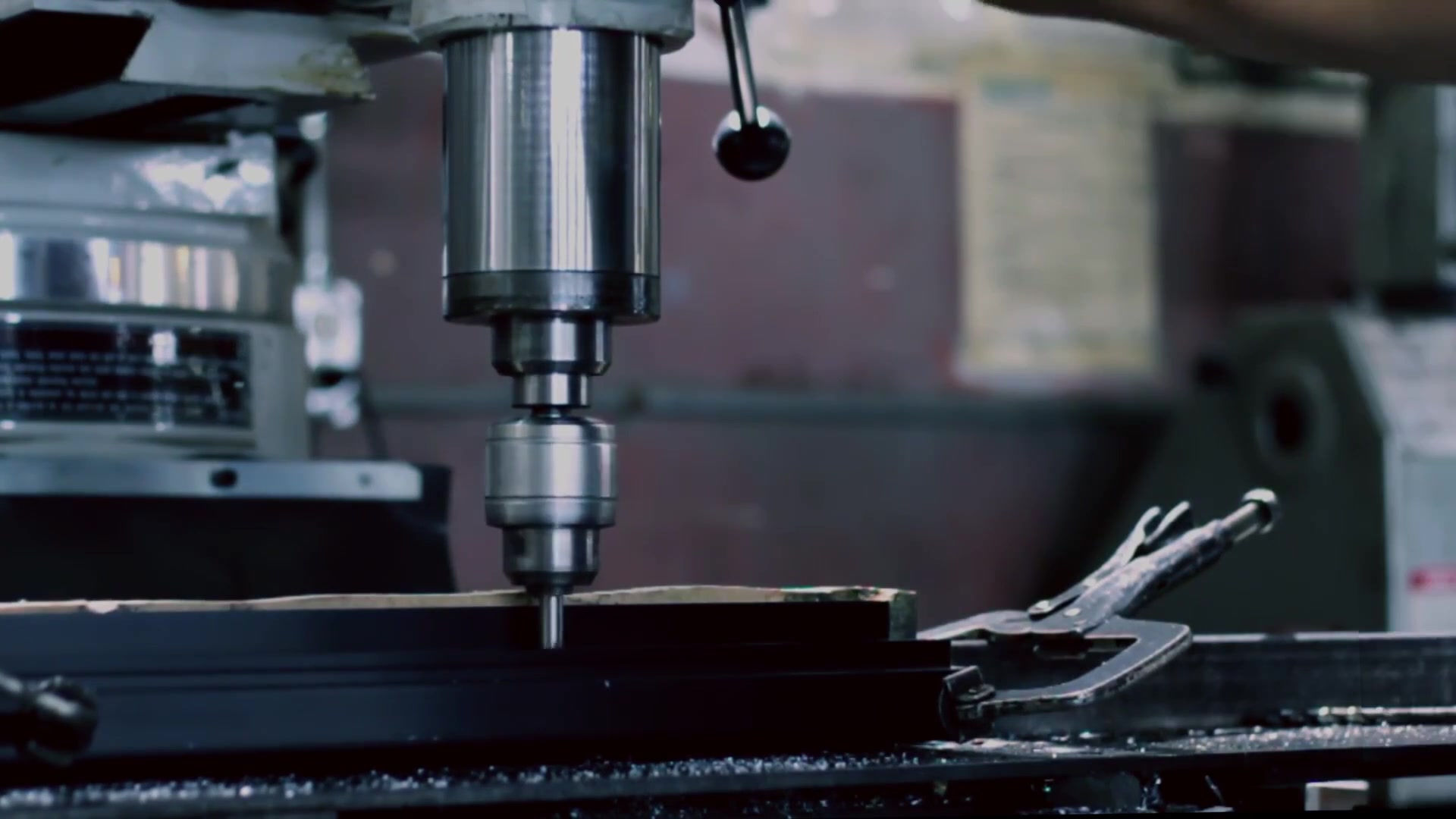
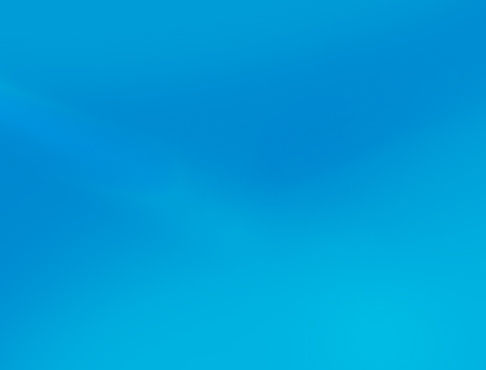
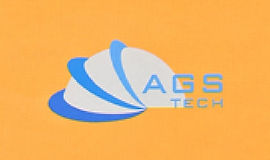
다양한 제품 및 서비스를 위한 글로벌 맞춤형 제조업체, 통합업체, 통합업체, 아웃소싱 파트너.
우리는 맞춤형 제조 및 기성 제품 및 서비스의 제조, 제조, 엔지니어링, 통합, 통합, 아웃소싱을 위한 원스톱 소스입니다.
Choose your Language
-
맞춤형 제조
-
국내 및 글로벌 계약 제조
-
제조 아웃소싱
-
국내 및 글로벌 조달
-
통합
-
엔지니어링 통합
-
엔지니어링 서비스
WELDING, BRAZING, SOLDERING, SINTERING, ADHESIVE BONDING, FASTENING, PRESS FITTING을 사용하여 제조 부품을 결합, 조립 및 고정하고 완제품 또는 반제품으로 변환합니다. 가장 널리 사용되는 용접 공정 중 일부는 아크, 산소 연료 가스, 저항, 투영, 이음매, 업셋, 충격, 고체 상태, 전자빔, 레이저, 써밋, 유도 용접입니다. 우리의 인기 있는 브레이징 공정은 토치, 인덕션, 퍼니스 및 딥 브레이징입니다. 우리의 납땜 방법은 철, 핫 플레이트, 오븐, 인덕션, 딥, 웨이브, 리플로 및 초음파 납땜입니다. 접착 결합을 위해 우리는 열가소성 수지 및 열경화성, 에폭시, 페놀, 폴리우레탄, 접착 합금 및 기타 화학 물질 및 테이프를 자주 사용합니다. 마지막으로 우리의 고정 프로세스는 못 박기, 나사 고정, 너트와 볼트, 리벳 팅, 클린칭, 고정, 스티칭 및 스테이플링 및 압입으로 구성됩니다.
• WELDING : 용접은 가공물을 녹이고 용가재를 도입하여 재료를 접합하는 것으로 용융된 용접 풀도 합류합니다. 해당 지역이 식으면 강한 관절을 얻습니다. 경우에 따라 압력이 가해집니다. 용접과 달리 브레이징 및 솔더링 작업은 공작물 사이의 융점이 낮은 재료의 용융만 포함하며 공작물은 용융되지 않습니다. 여기를 클릭하는 것이 좋습니다.AGS-TECH Inc.의 용접 공정 개략도를 다운로드하십시오.
이렇게 하면 아래에서 제공하는 정보를 더 잘 이해하는 데 도움이 됩니다.
아크 용접에서는 전원 공급 장치와 전극을 사용하여 금속을 녹이는 전기 아크를 생성합니다. 용접점은 차폐 가스, 증기 또는 기타 재료로 보호됩니다. 이 공정은 자동차 부품 및 철강 구조물 용접에 널리 사용됩니다. shelded metal arc welding(SMAW) 또는 스틱 용접이라고도 하는 용접에서 전극 스틱을 모재에 가까이 가져오고 전극 스틱 사이에 전기 아크가 생성됩니다. 전극봉이 녹아서 충전재 역할을 합니다. 전극은 또한 슬래그 층으로 작용하고 차폐 가스로 작용하는 증기를 방출하는 플럭스를 포함합니다. 이는 환경 오염으로부터 용접 영역을 보호합니다. 다른 필러는 사용되지 않습니다. 이 공정의 단점은 속도가 느리고 전극을 자주 교체해야 하며 플럭스에서 발생하는 잔류 슬래그를 제거해야 한다는 것입니다. 철, 강철, 니켈, 알루미늄, 구리 등의 여러 금속. 용접할 수 있습니다. 장점은 저렴한 도구와 사용 용이성입니다. 금속 불활성 가스(MIG)라고도 하는 가스 금속 아크 용접(GMAW)은 용접 영역의 환경 오염에 대해 와이어 주위를 흐르는 불활성 또는 부분적으로 불활성 가스와 소모성 전극 와이어 필러를 지속적으로 공급합니다. 강철, 알루미늄 및 기타 비철금속을 용접할 수 있습니다. MIG의 장점은 높은 용접 속도와 우수한 품질입니다. 단점은 용접 영역 주변의 차폐 가스를 안정적으로 유지해야 하기 때문에 바람이 많이 부는 실외 환경에서 직면하는 복잡한 장비와 문제입니다. GMAW의 변형은 플럭스 재료로 채워진 미세한 금속 튜브로 구성된 플럭스 코어드 아크 용접(FCAW)입니다. 때로는 튜브 내부의 플럭스가 환경 오염으로부터 보호하기에 충분합니다. 서브머지드 아크 용접(SAW)은 광범위하게 자동화된 프로세스로, 연속 와이어 공급 및 플럭스 커버 층 아래에서 발생하는 아크를 포함합니다. 생산율과 품질이 높고 용접 슬래그가 쉽게 떨어져 나가며 연기가 나지 않는 작업 환경을 갖추고 있습니다. 단점은 특정 위치에서 parts를 용접하는 데에만 사용할 수 있다는 것입니다. 가스 텅스텐 아크 용접(GTAW) 또는 텅스텐-비활성 가스 용접(TIG)에서 우리는 별도의 필러 및 불활성 또는 거의 불활성 가스와 함께 텅스텐 전극을 사용합니다. 우리가 알고 있듯이 텅스텐은 융점이 높으며 매우 높은 온도에 매우 적합한 금속입니다. TIG의 텅스텐은 위에서 설명한 다른 방법과 달리 소비되지 않습니다. 얇은 재료의 용접에서 다른 기술에 비해 느리지만 고품질의 용접 기술입니다. 많은 금속에 적합합니다. 플라즈마 아크 용접은 유사하지만 플라즈마 가스를 사용하여 아크를 생성합니다. 플라즈마 아크 용접의 아크는 GTAW에 비해 상대적으로 더 집중되어 있으며 훨씬 빠른 속도로 더 넓은 범위의 금속 두께에 사용할 수 있습니다. GTAW 및 플라즈마 아크 용접은 다소 동일한 재료에 적용될 수 있습니다.
OXY-FUEL / OXYFUEL WELDING 옥시아세틸렌 용접이라고도 하며, 산소 용접, 가스 용접은 용접용 가스 연료와 산소를 사용하여 수행됩니다. 전력을 사용하지 않기 때문에 휴대용으로 전기가 없는 곳에서도 사용할 수 있습니다. 용접 토치를 사용하여 조각과 충전재를 가열하여 공유 용융 금속 풀을 생성합니다. 아세틸렌, 가솔린, 수소, 프로판, 부탄 등 다양한 연료를 사용할 수 있습니다. 순산소 용접에서 우리는 두 개의 용기를 사용합니다. 하나는 연료용이고 다른 하나는 산소용입니다. 산소는 연료를 산화시킵니다(연소).
RESISTANCE WELDING: joule heating을 이용하여 전류가 인가되는 위치에서 일정 시간 열을 발생시키는 용접 방식입니다. 높은 전류가 금속을 통과합니다. 이 위치에서 용융 금속 풀이 형성됩니다. 저항 용접 방법은 효율성과 오염 가능성이 적기 때문에 널리 사용됩니다. 그러나 단점은 장비 비용이 상대적으로 중요하고 상대적으로 얇은 공작물에 대한 고유한 한계입니다. 스폿 용접은 저항 용접의 주요 유형 중 하나입니다. 여기서 우리는 두 개 이상의 구리 전극을 사용하여 두 개 이상의 겹치는 시트 또는 공작물을 결합하여 시트를 함께 고정하고 높은 전류를 통과시킵니다. 구리 전극 사이의 물질이 가열되고 그 위치에 용융 풀이 생성됩니다. 그런 다음 전류가 멈추고 전극이 수냉식이므로 구리 전극 팁이 용접 위치를 냉각시킵니다. 올바른 재료와 두께에 적절한 양의 열을 가하는 것이 이 기술의 핵심입니다. 잘못 적용하면 접합부가 약해지기 때문입니다. 스폿 용접은 공작물에 큰 변형을 일으키지 않고 에너지 효율이 높고 자동화가 쉽고 생산 속도가 우수하며 필러가 필요하지 않은 장점이 있습니다. 단점은 용접이 연속적인 이음매를 형성하지 않고 스폿에서 이루어지기 때문에 전체 강도가 다른 용접 방법에 비해 상대적으로 낮을 수 있다는 것입니다. 반면에 SEAM WELDING은 유사한 재료의 접합 표면에서 용접을 생성합니다. 솔기는 맞대기 또는 겹침 조인트가 될 수 있습니다. 심 용접은 한쪽 끝에서 시작하여 다른 쪽 끝으로 점진적으로 이동합니다. 이 방법은 또한 두 개의 구리 전극을 사용하여 용접 영역에 압력과 전류를 가합니다. 디스크 모양의 전극은 솔기 라인을 따라 일정한 접촉으로 회전하고 연속 용접을 합니다. 여기에서도 전극은 물로 냉각됩니다. 용접은 매우 강력하고 신뢰할 수 있습니다. 다른 방법으로는 프로젝션, 플래시 및 업셋 용접 기술이 있습니다.
SOLID-STATE WELDING은 위에서 설명한 이전 방법과 약간 다릅니다. 유착은 금속 충전재를 사용하지 않고 결합된 금속의 용융 온도보다 낮은 온도에서 발생합니다. 일부 공정에서는 압력이 사용될 수 있습니다. 다양한 방법으로는 이종 금속을 동일한 다이를 통해 압출하는 공압출 용접, 융점 이하의 연질 합금을 접합하는 냉압 용접, 용접선이 보이지 않는 확산 용접, 내식성 합금과 같은 이종 재료를 구조에 접합하는 폭발 용접이 있습니다. 강, 강관과 판재를 전자기력으로 가속하는 ELECTROMAGNETIC PULSE WELDING, 금속을 고온으로 가열하여 함께 망치질하는 FORGE WELDING, 충분한 마찰로 용접하는 FRICTION WELDING, 회전하지 않고 회전하는 FRICTION STIR WELDING 접합선을 가로지르는 소모품 도구, 진공 또는 불활성 가스에서 용융 온도 이하의 고온에서 금속을 함께 누르는 HOT PRESSURE WELDING, 용기 내부의 불활성 가스를 사용하여 압력을 가하는 공정 HOT ISOSTATIC PRESSURE WELDING, 접합하는 ROLL WELDING 서로 다른 재료를 강제로 두 개의 회전 바퀴, 고주파 진동 에너지를 사용하여 얇은 금속 또는 플라스틱 시트를 용접하는 ULTRASONIC WELDING.
다른 용접 공정으로는 깊은 용입과 빠른 가공을 하는 ELECTRON BEAM WELDING이지만 특수한 경우에는 고가라고 생각하는 ELECTROSLAG WELDING, 두꺼운 후판과 철재에만 적합한 ELECTROSLAG WELDING, 전자기 유도를 사용하는 INDUCTION WELDING 등이 있습니다. 우리의 전기 전도성 또는 강자성 공작물을 가열, 깊은 침투와 빠른 처리 그러나 고가의 방법을 사용하는 LASER BEAM WELDING, 동일한 용접 헤드에서 LBW와 GMAW를 결합하고 플레이트 사이의 2mm 간격을 연결할 수 있는 LASER HYBRID WELDING, PERCUSSION WELDING 방전 후 압력을 가하여 재료를 단조하는 방법, 알루미늄과 산화철 분말 사이의 발열 반응을 포함하는 THERMIT WELDING, 소모성 전극을 사용하고 수직 위치에 강철만 사용하는 ELECTROGAS WELDING, 마지막으로 스터드를 베이스에 접합하기 위한 STUD ARC WELDING이 포함됩니다. 열과 압력이 있는 재료.
여기를 클릭하는 것이 좋습니다.AGS-TECH Inc의 브레이징, 납땜 및 접착 본딩 공정의 개략도를 다운로드하십시오.
이렇게 하면 아래에서 제공하는 정보를 더 잘 이해하는 데 도움이 됩니다.
• BRAZING : 두 개 이상의 금속을 융점 이상으로 가열하고 모세관 현상을 이용하여 두 개 이상의 금속을 접합합니다. 이 공정은 납땜과 유사하지만 충전재를 녹이는 데 관련된 온도는 납땜에서 더 높습니다. 용접과 마찬가지로 플럭스는 대기 오염으로부터 충전재를 보호합니다. 냉각 후 공작물이 함께 결합됩니다. 이 프로세스에는 다음과 같은 주요 단계가 포함됩니다. 적절한 맞춤 및 간극, 기본 재료의 적절한 세척, 적절한 고정, 적절한 플럭스 및 분위기 선택, 어셈블리 가열 및 최종적으로 납땜 어셈블리의 세척. 당사의 일부 납땜 공정은 수동 또는 자동 방식으로 수행되는 인기 있는 방법인 TORCH BRAZING입니다. 소량 생산 주문 및 특수 케이스에 적합합니다. 납땜되는 접합부 근처에 가스 화염을 사용하여 열이 가해집니다. Furnace BRAZING은 작업자의 기술이 덜 필요하고 산업용 대량 생산에 적합한 반자동 공정입니다. 퍼니스의 온도 제어와 분위기 제어는 모두 이 기술의 장점입니다. 전자는 토치 브레이징의 경우처럼 열 사이클을 제어하고 국부 가열을 제거할 수 있고 후자는 부품을 산화로부터 보호하기 때문입니다. 지깅을 사용하여 제조 비용을 최소화할 수 있습니다. 단점은 높은 전력 소비, 장비 비용 및 더 까다로운 설계 고려 사항입니다. VACUUM BRAZING은 진공 용광로에서 이루어집니다. 온도 균일성이 유지되고 잔류 응력이 거의 없는 플럭스가 없고 매우 깨끗한 조인트를 얻을 수 있습니다. 열처리는 느린 가열 및 냉각 주기 동안 존재하는 낮은 잔류 응력 때문에 진공 브레이징 중에 발생할 수 있습니다. 가장 큰 단점은 진공 환경을 만드는 데 비용이 많이 들기 때문에 비용이 많이 든다는 것입니다. 또 다른 기술 DIP BRAZING은 접합면에 브레이징 화합물이 적용되는 고정 부품을 결합합니다. 그 후 fixtured 부품을 열 전달 매체 및 플럭스로 작용하는 염화나트륨(식염)과 같은 용융염 욕조에 담근다. 공기가 배제되어 산화물 형성이 일어나지 않습니다. 인덕션 브레이징에서는 모재보다 융점이 낮은 용가재로 재료를 접합합니다. 유도 코일의 교류는 대부분 철 자성 재료에 유도 가열을 유도하는 전자기장을 생성합니다. 이 방법은 선택적인 가열, 충전제가 원하는 영역에만 흐르는 양호한 접합부, 화염이 존재하지 않고 냉각이 빠르기 때문에 산화가 적음, 빠른 가열, 일관성 및 대량 제조에 대한 적합성을 제공합니다. 공정 속도를 높이고 일관성을 보장하기 위해 우리는 프리폼을 자주 사용합니다. 세라믹-금속 피팅, 밀폐 밀봉, 진공 피드스루, 고진공 및 초고진공 및 유체 제어 부품을 생산하는 당사의 브레이징 시설에 대한 정보는 여기에서 확인할 수 있습니다._cc781905-5cde-3194-bb3b-136d_브레이징 공장 브로셔
• SOLDERING : 솔더링에서는 가공물이 녹는 것이 아니라 접합부로 흘러 들어가는 접합부보다 융점이 낮은 용가재가 있습니다. 납땜에서 용가재는 납땜보다 낮은 온도에서 녹습니다. 우리는 납땜을 위해 무연 합금을 사용하고 RoHS를 준수하며 다양한 애플리케이션 및 요구 사항에 대해 은 합금과 같은 다양하고 적합한 합금을 보유하고 있습니다. 납땜은 기체 및 액체가 새지 않는 접합부를 제공합니다. SOFT SOLDERING에서 우리의 용가재는 섭씨 400도 미만의 융점을 갖는 반면 SILVER SOLDERING 및 BRAZING에서는 더 높은 온도가 필요합니다. 소프트 솔더링은 더 낮은 온도를 사용하지만 고온에서 까다로운 애플리케이션을 위한 강한 접합을 생성하지 않습니다. 반면에 은 납땜은 토치에 의해 제공되는 고온이 필요하고 고온 응용 분야에 적합한 강한 접합부를 제공합니다. 브레이징에는 가장 높은 온도가 필요하며 일반적으로 토치가 사용됩니다. 브레이징 조인트는 매우 강하기 때문에 무거운 철 물체를 수리하기에 좋은 후보입니다. 우리의 제조 라인에서는 수동 수동 납땜과 자동 납땜 라인을 모두 사용합니다. INDUCTION SOLDERING은 유도 가열을 촉진하기 위해 구리 코일에서 고주파 AC 전류를 사용합니다. 납땜 부분에 전류가 유도되어 고저항 joint에서 열이 발생합니다. 이 열은 용가재를 녹입니다. 플럭스도 사용됩니다. 유도 납땜은 코일을 감아 연속 공정으로 실린더와 파이프를 납땜하는 좋은 방법입니다. 흑연 및 세라믹과 같은 일부 재료를 납땜하는 것은 납땜 전에 적절한 금속으로 공작물을 도금해야 하기 때문에 더 어렵습니다. 이것은 계면 결합을 용이하게 합니다. 우리는 특히 밀폐 포장 응용 분야를 위해 이러한 재료를 납땜합니다. 우리는 주로 WAVE SOLDERING을 사용하여 인쇄 회로 기판(PCB)을 대량 생산합니다. 소량의 프로토 타이핑 목적으로만 우리는 납땜 인두를 사용하여 손 납땜을 사용합니다. 우리는 스루홀과 표면 실장 PCB 어셈블리(PCBA) 모두에 웨이브 솔더링을 사용합니다. 임시 접착제는 부품이 회로 기판에 부착된 상태를 유지하고 어셈블리가 컨베이어에 배치되고 용융 땜납이 포함된 장비를 통해 이동합니다. 먼저 PCB가 플럭스화된 다음 예열 영역으로 들어갑니다. 용융 땜납은 팬에 있고 표면에 정상파 패턴이 있습니다. PCB가 이 파동 위로 이동할 때 이 파동이 PCB 바닥에 닿아 납땜 패드에 달라붙습니다. 솔더는 핀과 패드에만 남아 있고 PCB 자체에는 남아 있지 않습니다. 용융 땜납의 파도는 튀지 않고 파도 꼭대기가 보드의 원하지 않는 부분을 만지거나 오염시키지 않도록 잘 제어되어야 합니다. REFLOW SOLDERING에서는 점착성 솔더 페이스트를 사용하여 전자 부품을 보드에 임시로 부착합니다. 그런 다음 보드는 온도 조절 기능이 있는 리플로 오븐을 통과합니다. 여기에서 땜납이 녹고 구성 요소를 영구적으로 연결합니다. 우리는 이 기술을 표면 실장 부품과 관통 구멍 부품 모두에 사용합니다. 적절한 온도 제어 및 오븐 온도 조정은 기판의 전자 부품이 최대 온도 한계 이상으로 과열되어 파손되는 것을 방지하는 데 필수적입니다. 리플 로우 솔더링 과정에서 실제로 예열 단계, 열 흡수 단계, 리플 로우 및 냉각 단계와 같은 뚜렷한 열 프로파일을 가진 여러 영역 또는 단계가 있습니다. 이러한 다양한 단계는 PCBA(인쇄 회로 기판 어셈블리)의 손상 없는 리플로 납땜에 필수적입니다. ULTRASONIC SOLDERING은 독특한 기능을 가진 자주 사용되는 또 다른 기술입니다. 유리, 세라믹 및 비금속 재료를 납땜하는 데 사용할 수 있습니다. 예를 들어 비금속인 광전지 패널에는 이 기술을 사용하여 부착할 수 있는 전극이 필요합니다. 초음파 납땜에서는 초음파 진동도 방출하는 가열된 납땜 팁을 배치합니다. 이러한 진동은 기판과 용융 솔더 재료의 계면에서 캐비테이션 거품을 생성합니다. 캐비테이션의 파열 에너지는 산화물 표면을 수정하고 먼지와 산화물을 제거합니다. 이 시간 동안 합금 층이 또한 형성됩니다. 결합 표면의 땜납은 산소를 포함하고 유리와 땜납 사이에 강한 공유 결합을 형성할 수 있습니다. DIP SOLDERING은 소규모 생산에만 적합한 웨이브 솔더링의 간단한 버전으로 간주될 수 있습니다. 첫 번째 세척 플럭스는 다른 공정과 마찬가지로 적용됩니다. 부품이 장착된 PCB는 수동 또는 반자동 방식으로 용융 땜납이 들어 있는 탱크에 담근다. 녹은 솔더는 기판의 솔더 마스크로 보호되지 않은 노출된 금속 영역에 달라붙습니다. 장비가 간단하고 저렴합니다.
• ADHESIVE BONDING : 이것은 우리가 자주 사용하는 또 다른 대중적인 기술이며 접착제, 에폭시, 플라스틱 에이전트 또는 기타 화학 물질을 사용하여 표면을 접착하는 것과 관련됩니다. 결합은 용매 증발, 열 경화, UV 광 경화, 압력 경화 또는 특정 시간 대기에 의해 수행됩니다. 당사의 생산 라인에는 다양한 고성능 접착제가 사용됩니다. 적절하게 설계된 적용 및 경화 공정을 통해 접착 결합은 강력하고 신뢰할 수 있는 매우 낮은 응력 결합을 생성할 수 있습니다. 접착제는 습기, 오염 물질, 부식성, 진동 등의 환경 요인에 대한 좋은 보호 장치가 될 수 있습니다. 접착 결합의 장점은 다음과 같습니다. 그렇지 않으면 납땜, 용접 또는 납땜하기 어려운 재료에 적용할 수 있습니다. 또한 용접 또는 기타 고온 공정에 의해 손상되는 열에 민감한 재료에 적합할 수 있습니다. 접착제의 다른 장점은 불규칙한 모양의 표면에 적용할 수 있고 다른 방법과 비교할 때 매우 적은 양으로 조립 중량을 증가시킬 수 있다는 것입니다. 또한 부품의 치수 변화가 매우 적습니다. 일부 접착제는 굴절률 일치 특성을 가지며 빛 또는 광학 신호 강도를 크게 감소시키지 않으면서 광학 부품 사이에 사용할 수 있습니다. 반면에 단점은 경화 시간이 길어 제조 라인, 고정 장치 요구 사항, 표면 준비 요구 사항 및 재작업이 필요할 때 분해하기 어려운 속도를 늦출 수 있습니다. 대부분의 접착 접합 작업에는 다음 단계가 포함됩니다.
-표면 처리: 탈이온수 세척, 알코올 세척, 플라즈마 또는 코로나 세척과 같은 특수 세척 절차가 일반적입니다. 청소 후 가능한 한 최상의 접합을 보장하기 위해 표면에 접착 촉진제를 적용할 수 있습니다.
-부품 고정: 접착제 도포와 경화 모두를 위해 맞춤형 고정 장치를 설계하고 사용합니다.
-접착제 적용: 우리는 때로는 수동을 사용하고 때로는 로봇 공학, 서보 모터, 선형 액추에이터와 같은 자동화 시스템을 사용하여 접착제를 올바른 위치에 전달하고 디스펜서를 사용하여 적절한 양과 양으로 전달합니다.
-경화: 접착제에 따라 단순 건조 및 경화, 촉매 역할을 하는 UV 광선 하에서의 경화 또는 오븐에서 열경화 또는 지그 및 고정구에 장착된 저항 발열체를 사용하는 경화를 사용할 수 있습니다.
여기를 클릭하는 것이 좋습니다.AGS-TECH Inc.의 고정 프로세스 개략도를 다운로드하십시오.
이렇게 하면 아래에서 제공하는 정보를 더 잘 이해하는 데 도움이 됩니다.
• FASTENING PROCESSES: 당사의 기계적 결합 프로세스는 FASTENERS 및 INTEGRAL JOINTS의 두 가지 브래드 범주로 나뉩니다. 우리가 사용하는 패스너의 예로는 나사, 핀, 너트, 볼트, 리벳이 있습니다. 우리가 사용하는 일체형 조인트의 예로는 스냅 및 열박음, 솔기, 크림프가 있습니다. 다양한 고정 방법을 사용하여 기계식 조인트가 수년 동안 견고하고 신뢰할 수 있는지 확인합니다. 나사와 볼트는 물체를 함께 고정하고 위치를 지정하는 데 가장 일반적으로 사용되는 패스너입니다. 당사의 나사와 볼트는 ASME 표준을 충족합니다. 육각 캡 나사 및 육각 볼트, 래그 나사 및 볼트, 양단 나사, 맞춤 나사, 아이 나사, 미러 나사, 판금 나사, 미세 조정 나사, 셀프 드릴링 및 셀프 태핑 나사 등 다양한 유형의 나사 및 볼트가 배치됩니다. , 고정 나사, 내장 와셔가 있는 나사 등… 접시머리, 돔, 원형, 플랜지 머리와 같은 다양한 나사 머리 유형과 슬롯, 필립스, 사각형, 육각 소켓과 같은 다양한 나사 드라이브 유형이 있습니다. 다른 한편으로 A RIVET은 한편으로는 매끄러운 원통형 샤프트와 헤드로 구성된 영구 기계식 패스너입니다. 삽입 후 리벳의 다른 쪽 끝이 변형되고 직경이 확장되어 제자리에 유지됩니다. 즉, 리벳을 설치하기 전에는 헤드가 하나이고 설치 후에는 헤드가 두 개입니다. 솔리드/라운드 헤드 리벳, 구조용, 반관형, 블라인드, 오스카, 드라이브, 플러시, 마찰 잠금, 셀프 피어싱 리벳 등 용도, 강도, 접근성 및 비용에 따라 다양한 유형의 리벳을 설치합니다. 용접 열로 인한 열 변형 및 재료 특성의 변화를 피해야 하는 경우 리벳팅이 선호될 수 있습니다. 리벳팅은 또한 경량이며 특히 전단력에 대한 우수한 강도와 내구성을 제공합니다. 그러나 인장 하중에 대해서는 나사, 너트 및 볼트가 더 적합할 수 있습니다. CLINCHING 공정에서 우리는 접합되는 판금 사이에 기계적 인터록을 형성하기 위해 특수 펀치와 다이를 사용합니다. 펀치는 판금 층을 다이 캐비티로 밀어넣고 영구 조인트를 형성합니다. 클린칭 시 가열 및 냉각이 필요하지 않으며 냉간 가공 공정입니다. 경우에 따라 스폿 용접을 대체할 수 있는 경제적인 공정입니다. PINNING에서 우리는 기계 부품의 상대적인 위치를 고정하는 데 사용되는 기계 요소인 핀을 사용합니다. 주요 유형은 클레비스 핀, 분할 핀, 스프링 핀, 맞춤 핀, 및 분할 핀입니다. 스테이플링에서는 재료를 결합하거나 묶는 데 사용되는 두 갈래 패스너인 스테이플링 건과 스테이플을 사용합니다. 스테이플링에는 다음과 같은 장점이 있습니다. 경제적이고 간단하며 사용이 빠릅니다. 스테이플의 크라운을 사용하여 서로 맞댐된 재료를 연결할 수 있습니다. 스테이플의 크라운을 사용하면 케이블과 같은 조각을 쉽게 연결하여 구멍을 뚫거나 표면에 고정할 수 있습니다. 손상, 비교적 쉬운 제거. PRESS FITTING은 부품을 서로 밀어서 수행하며 부품 간의 마찰로 부품이 고정됩니다. 오버사이즈 샤프트와 언더사이즈 구멍으로 구성된 압입 부품은 일반적으로 힘을 가하거나 부품의 열팽창 또는 수축을 이용하는 두 가지 방법 중 하나로 조립됩니다. 힘을 가해 압입을 할 때 유압프레스나 수동프레스를 사용합니다. 반면에 열팽창에 의해 압입이 이루어지면 우리는 둘러싸는 부품을 가열하고 뜨거울 때 제자리에 조립합니다. 냉각되면 수축하고 원래 크기로 돌아갑니다. 그 결과 압입이 잘 됩니다. 우리는 이것을 SHRINK-FITTING이라고 부릅니다. 이 작업을 수행하는 다른 방법은 조립 전에 엔벨로프 부품을 냉각한 다음 짝을 이루는 부품으로 밀어 넣는 것입니다. 조립품이 예열되면 팽창하여 꽉 끼게 됩니다. 이 후자의 방법은 가열이 재료 특성을 변경할 위험이 있는 경우에 선호될 수 있습니다. 이러한 경우 냉각이 더 안전합니다.
공압 및 유압 부품 및 어셈블리
• 밸브, O-링, 와셔, 씰, 개스킷, 링, 심과 같은 유압 및 공압 부품.
밸브와 공압 부품은 매우 다양하기 때문에 여기에 모든 것을 나열할 수는 없습니다. 응용 프로그램의 물리적 및 화학적 환경에 따라 특수 제품이 있습니다. 밸브 및 공압 부품과 접촉하게 될 압력, 온도, 액체 또는 가스와 같은 애플리케이션, 구성 요소 유형, 사양, 환경 조건을 지정하십시오. 그리고 우리는 귀하에게 가장 적합한 제품을 선택하거나 귀하의 응용 분야에 맞게 특별히 제조할 것입니다.