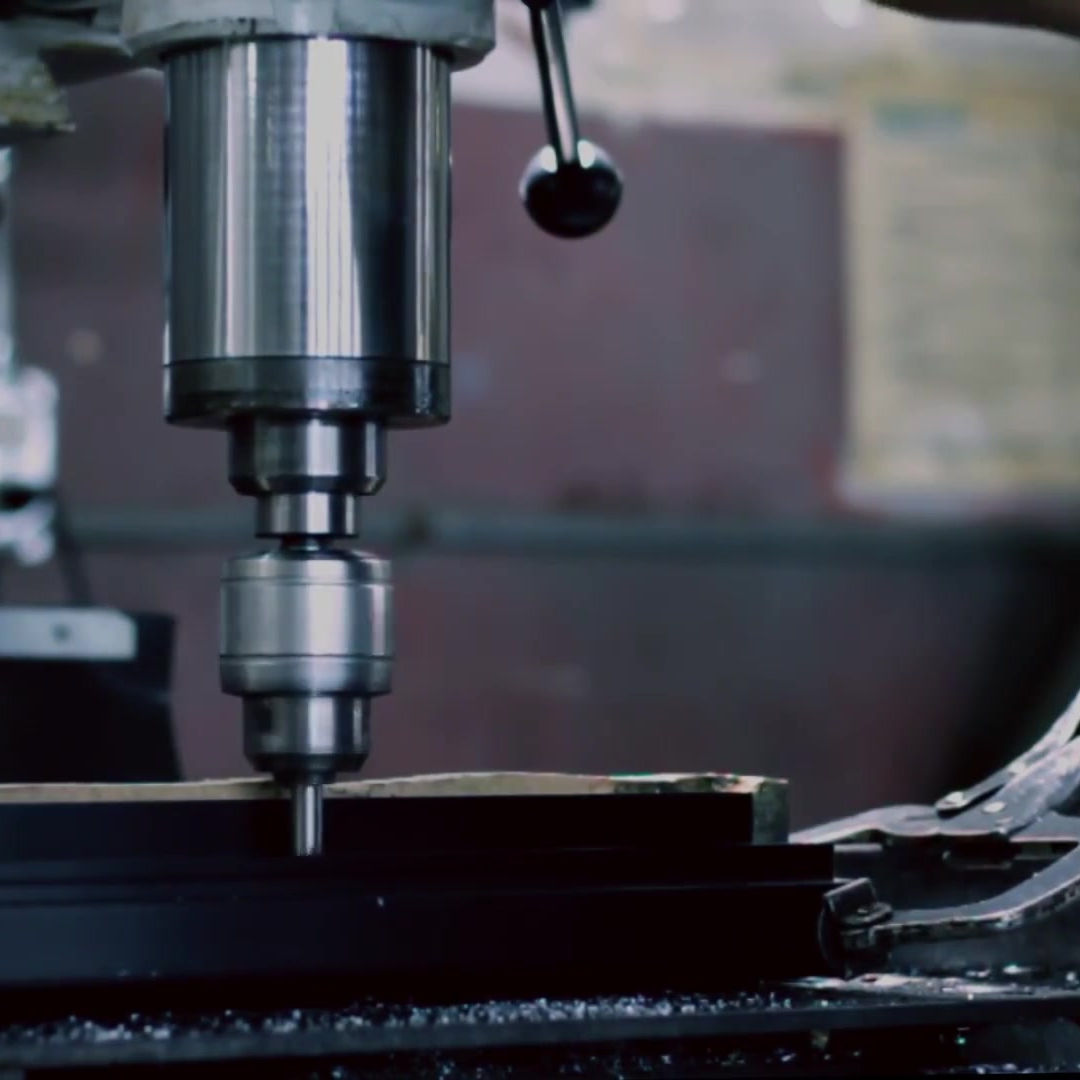
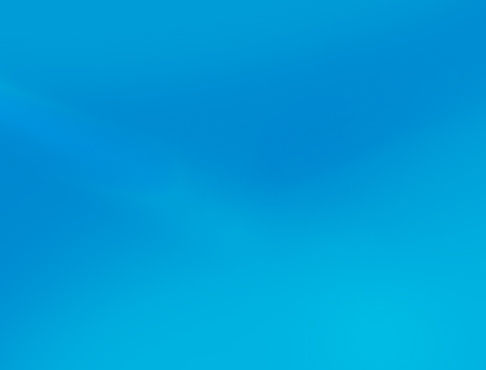
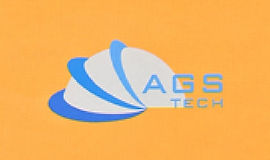
다양한 제품 및 서비스를 위한 글로벌 맞춤형 제조업체, 통합업체, 통합업체, 아웃소싱 파트너.
우리는 맞춤형 제조 및 기성 제품 및 서비스의 제조, 제조, 엔지니어링, 통합, 통합, 아웃소싱을 위한 원스톱 소스입니다.
Choose your Language
-
맞춤형 제조
-
국내 및 글로벌 계약 제조
-
제조 아웃소싱
-
국내 및 글로벌 조달
-
통합
-
엔지니어링 통합
-
엔지니어링 서비스
Search Results
공란으로 164개 검색됨
- Test Equipment for Furniture Testing
Test Equipment for Furniture Testing, Sofa Durability Tester, Chair Base Static Tester, Chair Drop Impact Tester, Mattress Firmness Tester 전자 테스터 전자 테스터라는 용어는 주로 전기 및 전자 부품 및 시스템의 테스트, 검사 및 분석에 사용되는 테스트 장비를 말합니다. 업계에서 가장 인기 있는 제품을 제공합니다. 전원 공급 장치 및 신호 발생 장치: 전원 공급 장치, 신호 발생기, 주파수 합성기, 함수 발생기, 디지털 패턴 발생기, 펄스 발생기, 신호 주입기 미터: 디지털 멀티미터, LCR 미터, EMF 미터, 커패시턴스 미터, 브리지 계측기, 클램프 미터, 가우스미터/테슬라미터/자력계, 접지 저항 미터 분석기: 오실로스코프, 논리 분석기, 스펙트럼 분석기, 프로토콜 분석기, 벡터 신호 분석기, 시간 영역 반사계, 반도체 곡선 추적기, 네트워크 분석기, 위상 역 회전 테스터 자세한 내용 및 기타 유사한 장비는 장비 웹사이트를 방문하십시오. http://www.sourceindustrialsupply.com 업계 전반에 걸쳐 일상적으로 사용되는 이러한 장비에 대해 간략히 살펴보겠습니다. 계측 목적으로 공급하는 전원 공급 장치는 개별, 벤치탑 및 독립형 장치입니다. 조정 가능한 조정 전기 전원 공급 장치는 입력 전압 또는 부하 전류가 변하더라도 출력 값을 조정할 수 있고 출력 전압 또는 전류가 일정하게 유지되기 때문에 가장 널리 사용되는 전원 공급 장치입니다. 절연 전원 공급 장치에는 전원 입력과 전기적으로 독립적인 전원 출력이 있습니다. 전력 변환 방식에 따라 LINEAR 및 SWITCHING POWER SUPPLIES가 있습니다. 선형 전원 공급 장치는 선형 영역에서 작동하는 모든 유효 전력 변환 구성 요소를 사용하여 입력 전원을 직접 처리하는 반면, 스위칭 전원 공급 장치에는 주로 비선형 모드(예: 트랜지스터)에서 작동하는 구성 요소가 있으며 이전에 전력을 AC 또는 DC 펄스로 변환합니다. 처리. 스위칭 전원 공급 장치는 구성 요소가 선형 작동 영역에서 보내는 시간이 더 짧기 때문에 전력 손실이 적기 때문에 일반적으로 선형 공급 장치보다 더 효율적입니다. 애플리케이션에 따라 DC 또는 AC 전원이 사용됩니다. 다른 인기 있는 장치는 전압, 전류 또는 주파수가 RS232 또는 GPIB와 같은 디지털 인터페이스 또는 아날로그 입력을 통해 원격으로 제어될 수 있는 프로그래밍 가능한 전원 공급 장치입니다. 그들 중 다수는 작업을 모니터링하고 제어하기 위한 통합 마이크로컴퓨터를 가지고 있습니다. 이러한 기기는 자동화된 테스트 목적에 필수적입니다. 일부 전자 전원 공급 장치는 과부하 시 전원을 차단하는 대신 전류 제한을 사용합니다. 전자 제한은 일반적으로 실험실 벤치 유형 기기에 사용됩니다. 신호 발생기는 반복 또는 비반복 아날로그 또는 디지털 신호를 생성하는 실험실 및 산업 분야에서 널리 사용되는 또 다른 장비입니다. 또는 FUNCTION GENERATORS, DIGITAL PATTERN GENERATORS 또는 FREQUENCY GENERATORS라고도 합니다. 함수 발생기는 사인파, 스텝 펄스, 사각 및 삼각 파형, 임의 파형과 같은 단순 반복 파형을 생성합니다. 임의 파형 생성기를 사용하여 사용자는 주파수 범위, 정확도 및 출력 레벨의 게시된 제한 내에서 임의 파형을 생성할 수 있습니다. 단순한 파형 세트로 제한되는 함수 발생기와 달리 임의 파형 발생기는 사용자가 다양한 방법으로 소스 파형을 지정할 수 있도록 합니다. RF 및 마이크로파 신호 발생기는 셀룰러 통신, WiFi, GPS, 방송, 위성 통신 및 레이더와 같은 애플리케이션에서 구성 요소, 수신기 및 시스템을 테스트하는 데 사용됩니다. RF 신호 발생기는 일반적으로 몇 kHz에서 6GHz 사이에서 작동하는 반면 마이크로파 신호 발생기는 특수 하드웨어를 사용하여 1MHz 미만에서 최소 20GHz, 심지어 수백 GHz 범위까지 훨씬 더 넓은 주파수 범위 내에서 작동합니다. RF 및 마이크로파 신호 발생기는 아날로그 또는 벡터 신호 발생기로 더 분류할 수 있습니다. AUDIO-FREQUENCY SIGNAL GENERATORS는 오디오 주파수 범위 이상에서 신호를 생성합니다. 오디오 장비의 주파수 응답을 확인하는 전자 연구실 응용 프로그램이 있습니다. 벡터 신호 발생기(디지털 신호 발생기라고도 함)는 디지털 변조 무선 신호를 생성할 수 있습니다. 벡터 신호 생성기는 GSM, W-CDMA(UMTS) 및 Wi-Fi(IEEE 802.11)와 같은 산업 표준을 기반으로 신호를 생성할 수 있습니다. 논리 신호 발생기는 디지털 패턴 발생기라고도 합니다. 이러한 발생기는 논리 유형의 신호, 즉 기존 전압 레벨의 형태로 논리 1 및 0을 생성합니다. 논리 신호 발생기는 디지털 집적 회로 및 임베디드 시스템의 기능 검증 및 테스트를 위한 자극 소스로 사용됩니다. 위에 언급된 장치는 범용입니다. 그러나 사용자 지정 특정 응용 프로그램을 위해 설계된 다른 많은 신호 발생기가 있습니다. 신호 주입기는 회로에서 신호 추적을 위한 매우 유용하고 빠른 문제 해결 도구입니다. 기술자는 라디오 수신기와 같은 장치의 결함 단계를 매우 빠르게 결정할 수 있습니다. 신호 인젝터는 스피커 출력에 적용될 수 있으며 신호가 들리면 회로의 이전 단계로 이동할 수 있습니다. 이 경우 오디오 증폭기이고 주입된 신호가 다시 들리면 신호가 더 이상 들리지 않을 때까지 회로의 단계 위로 신호 주입을 이동할 수 있습니다. 이렇게 하면 문제의 위치를 찾는 데 도움이 됩니다. MULTIMETER는 여러 측정 기능을 하나의 장치에 결합한 전자 측정기입니다. 일반적으로 멀티미터는 전압, 전류 및 저항을 측정합니다. 디지털 및 아날로그 버전 모두 사용할 수 있습니다. 당사는 휴대용 휴대용 멀티미터 장치와 인증된 교정이 포함된 실험실 등급 모델을 제공합니다. 최신 멀티미터는 전압(AC/DC 모두), 볼트, 전류(AC/DC 모두), 암페어, 저항(옴)과 같은 많은 매개변수를 측정할 수 있습니다. 또한 일부 멀티미터는 온도 테스트 프로브를 사용하여 캐패시턴스(패럿), 컨덕턴스(지멘스), 데시벨, 듀티 사이클(퍼센트), 주파수(헤르츠), 인덕턴스(헨리), 온도(섭씨 또는 화씨)를 측정합니다. 일부 멀티미터에는 다음도 포함됩니다. 회로 도통 시 소리, 다이오드(다이오드 접합의 순방향 강하 측정), 트랜지스터(전류 게인 및 기타 매개변수 측정), 배터리 확인 기능, 조도 측정 기능, 산도 및 알칼리도(pH) 측정 기능 및 상대 습도 측정 기능. 최신 멀티미터는 종종 디지털입니다. 최신 디지털 멀티미터에는 종종 계측 및 테스트에서 매우 강력한 도구로 사용할 수 있는 임베디드 컴퓨터가 있습니다. 다음과 같은 기능이 포함됩니다. • 자동 범위 지정, 가장 중요한 숫자가 표시되도록 테스트 중인 수량에 대한 올바른 범위를 선택합니다. •직류 판독의 자동 극성은 적용된 전압이 양수인지 음수인지 보여줍니다. •샘플링 및 홀드, 테스트 중인 회로에서 계측기를 제거한 후 검사를 위해 가장 최근 판독값을 래치합니다. •반도체 접합부의 전압 강하에 대한 전류 제한 테스트. 트랜지스터 테스터를 대체하지는 않지만 디지털 멀티미터의 이 기능은 다이오드 및 트랜지스터 테스트를 용이하게 합니다. • 측정값의 빠른 변화를 더 잘 시각화하기 위해 테스트 중인 수량의 막대 그래프 표현. •저대역폭 오실로스코프. • 자동차 타이밍 및 드웰 신호에 대한 테스트가 포함된 자동차 회로 테스터. • 데이터 수집 기능은 주어진 기간 동안 최대 및 최소 판독값을 기록하고 고정된 간격으로 많은 샘플을 채취합니다. •결합된 LCR 미터. 일부 멀티미터는 컴퓨터와 인터페이스할 수 있지만 일부는 측정값을 저장하고 컴퓨터에 업로드할 수 있습니다. 또 다른 매우 유용한 도구인 LCR METER는 구성 요소의 인덕턴스(L), 커패시턴스(C) 및 저항(R)을 측정하기 위한 계측 기기입니다. 임피던스는 내부적으로 측정되고 디스플레이를 위해 해당 커패시턴스 또는 인덕턴스 값으로 변환됩니다. 테스트 중인 커패시터 또는 인덕터에 임피던스의 상당한 저항성 성분이 없는 경우 판독값은 합리적으로 정확합니다. 고급 LCR 미터는 실제 인덕턴스와 커패시턴스를 측정하고 커패시터의 등가 직렬 저항과 유도성 부품의 Q 계수도 측정합니다. 테스트 중인 장치는 AC 전압 소스에 영향을 받고 미터는 테스트된 장치를 통과하는 전압과 전류를 측정합니다. 전압 대 전류의 비율에서 미터는 임피던스를 결정할 수 있습니다. 전압과 전류 사이의 위상각도 일부 기기에서 측정됩니다. 임피던스와 결합하여 테스트된 장치의 등가 커패시턴스 또는 인덕턴스 및 저항을 계산하고 표시할 수 있습니다. LCR 미터에는 100Hz, 120Hz, 1kHz, 10kHz 및 100kHz의 선택 가능한 테스트 주파수가 있습니다. Benchtop LCR 미터는 일반적으로 100kHz 이상의 선택 가능한 테스트 주파수를 가지고 있습니다. 여기에는 종종 AC 측정 신호에 DC 전압 또는 전류를 중첩할 수 있는 가능성이 포함됩니다. 일부 미터는 이러한 DC 전압 또는 전류를 외부에서 공급할 수 있는 가능성을 제공하지만 다른 장치는 내부적으로 공급합니다. EMF METER는 전자기장(EMF)을 측정하기 위한 테스트 및 계측 기기입니다. 대부분은 전자기 복사 플럭스 밀도(DC 필드) 또는 시간 경과에 따른 전자기장의 변화(AC 필드)를 측정합니다. 1축 및 3축 기기 버전이 있습니다. 단일 축 미터는 3축 미터보다 비용이 적게 들지만 미터가 필드의 한 차원만 측정하기 때문에 테스트를 완료하는 데 더 오래 걸립니다. 측정을 완료하려면 단일 축 EMF 미터를 기울이고 세 축 모두를 켜야 합니다. 반면에 3축 미터는 3개의 축을 모두 동시에 측정하지만 더 비쌉니다. EMF 미터는 전기 배선과 같은 소스에서 발생하는 AC 전자기장을 측정할 수 있는 반면 GAUSSMETERS/TESLAMETERS 또는 MAGNETOMETERS는 직류가 존재하는 소스에서 방출되는 DC 필드를 측정합니다. 대부분의 EMF 미터는 미국 및 유럽 주전원의 주파수에 해당하는 50 및 60Hz 교류 필드를 측정하도록 보정됩니다. 20Hz만큼 낮은 교대 필드를 측정할 수 있는 다른 미터가 있습니다. EMF 측정은 광범위한 주파수에서 광대역으로 수행하거나 관심 주파수 범위만 주파수 선택적으로 모니터링할 수 있습니다. CAPACITANCE METER는 대부분 이산 캐패시터의 캐패시턴스를 측정하는데 사용되는 테스트 장비입니다. 일부 미터는 커패시턴스만 표시하는 반면 다른 미터는 누설, 등가 직렬 저항 및 인덕턴스를 표시합니다. 고급 테스트 장비는 테스트 중인 커패시터를 브리지 회로에 삽입하는 것과 같은 기술을 사용합니다. 브리지의 균형을 맞추기 위해 브리지에 있는 다른 다리의 값을 변경하여 알 수 없는 커패시터의 값을 결정합니다. 이 방법은 더 높은 정밀도를 보장합니다. 브리지는 직렬 저항과 인덕턴스를 측정할 수도 있습니다. 피코패럿에서 패럿까지의 커패시터를 측정할 수 있습니다. 브리지 회로는 누설 전류를 측정하지 않지만 DC 바이어스 전압을 인가하여 누설을 직접 측정할 수 있습니다. 많은 BRIDGE INSTRUMENTS를 컴퓨터에 연결할 수 있으며 데이터 교환을 통해 판독값을 다운로드하거나 브리지를 외부에서 제어할 수 있습니다. 이러한 브리지 장비는 빠르게 진행되는 생산 및 품질 관리 환경에서 테스트 자동화를 위한 go/no go 테스트를 제공합니다. 그러나 또 다른 시험기인 CLAMP METER는 전압계와 클램프형 전류계를 결합한 전기 시험기이다. 클램프 미터의 대부분의 최신 버전은 디지털입니다. 최신 클램프 미터는 디지털 멀티미터의 대부분의 기본 기능을 가지고 있지만 제품에 내장된 변류기 기능이 추가되었습니다. 큰 AC 전류를 전달하는 도체 주위에 계측기의 "턱"을 고정하면 해당 전류는 전력 변압기의 철심과 유사한 턱을 통해 결합되어 미터 입력의 션트를 가로질러 연결된 2차 권선으로 연결됩니다. , 작동 원리는 변압기와 매우 유사합니다. 코어를 감싼 1차 권선 수에 대한 2차 권선 수의 비율로 인해 훨씬 더 적은 전류가 미터 입력에 전달됩니다. 기본은 조가 고정되는 하나의 도체로 표시됩니다. 2차측에 1000개의 권선이 있는 경우 2차측 전류는 1차측에서 흐르는 전류의 1/1000이며, 이 경우 측정되는 도체입니다. 따라서 측정 중인 도체의 1A 전류는 미터 입력에서 0.001A의 전류를 생성합니다. 클램프 미터를 사용하면 2차 권선의 회전 수를 늘려 훨씬 더 큰 전류를 쉽게 측정할 수 있습니다. 대부분의 테스트 장비와 마찬가지로 고급 클램프 미터는 로깅 기능을 제공합니다. 접지 저항 테스터는 접지 전극과 토양 저항을 테스트하는 데 사용됩니다. 장비 요구 사항은 적용 범위에 따라 다릅니다. 최신 클램프 온 접지 테스트 장비는 접지 루프 테스트를 단순화하고 비침습 누설 전류 측정을 가능하게 합니다. 우리가 판매하는 분석기 중에는 의심할 여지 없이 가장 널리 사용되는 장비 중 하나인 오실로스코프가 있습니다. OSCILLOGRAPH라고도 하는 오실로스코프는 일정하게 변화하는 신호 전압을 시간의 함수로 하나 이상의 신호에 대한 2차원 플롯으로 관찰할 수 있는 일종의 전자 테스트 장비입니다. 소리 및 진동과 같은 비전기적 신호도 전압으로 변환되어 오실로스코프에 표시될 수 있습니다. 오실로스코프는 시간에 따른 전기 신호의 변화를 관찰하는 데 사용되며, 전압과 시간은 보정된 눈금에 대해 연속적으로 그래프로 표시되는 모양을 나타냅니다. 파형의 관찰 및 분석은 진폭, 주파수, 시간 간격, 상승 시간 및 왜곡과 같은 속성을 보여줍니다. 오실로스코프는 반복적인 신호가 화면에서 연속적인 형태로 관찰될 수 있도록 조정할 수 있습니다. 많은 오실로스코프에는 단일 이벤트를 계측기에서 캡처하여 비교적 오랜 시간 동안 표시할 수 있는 저장 기능이 있습니다. 이것은 우리가 직접 지각할 수 없는 사건을 너무 빨리 관찰할 수 있게 합니다. 최신 오실로스코프는 가볍고 컴팩트한 휴대용 기기입니다. 현장 서비스 애플리케이션을 위한 소형 배터리 구동 기기도 있습니다. 실험실 등급 오실로스코프는 일반적으로 벤치탑 장치입니다. 오실로스코프와 함께 사용할 수 있는 다양한 프로브와 입력 케이블이 있습니다. 귀하의 응용 프로그램에 사용할 조언이 필요한 경우 당사에 문의하십시오. 두 개의 수직 입력이 있는 오실로스코프를 이중 추적 오실로스코프라고 합니다. 단일 빔 CRT를 사용하여 입력을 다중화하며 일반적으로 한 번에 두 개의 트레이스를 표시할 수 있을 만큼 충분히 빠르게 입력을 전환합니다. 더 많은 트레이스가 있는 오실로스코프도 있습니다. 4개의 입력이 이들 사이에서 공통입니다. 일부 멀티 트레이스 오실로스코프는 외부 트리거 입력을 선택적인 수직 입력으로 사용하고 일부는 최소한의 제어만 가능한 세 번째 및 네 번째 채널을 가지고 있습니다. 최신 오실로스코프에는 전압에 대한 여러 입력이 있으므로 하나의 가변 전압을 다른 전압과 비교하는 데 사용할 수 있습니다. 이것은 예를 들어 다이오드와 같은 구성 요소에 대한 IV 곡선(전류 대 전압 특성)을 그래프로 표시하는 데 사용됩니다. 높은 주파수와 빠른 디지털 신호의 경우 수직 증폭기의 대역폭과 샘플링 속도는 충분히 높아야 합니다. 일반적인 용도의 경우 일반적으로 최소 100MHz의 대역폭이면 충분합니다. 훨씬 낮은 대역폭은 오디오 주파수 애플리케이션에만 충분합니다. 스위핑의 유용한 범위는 적절한 트리거링 및 스위프 지연과 함께 1초에서 100나노초입니다. 안정적인 디스플레이를 위해서는 잘 설계된 안정적인 트리거 회로가 필요합니다. 트리거 회로의 품질은 우수한 오실로스코프의 핵심입니다. 또 다른 주요 선택 기준은 샘플 메모리 깊이와 샘플 속도입니다. 기본 수준의 최신 DSO에는 이제 채널당 1MB 이상의 샘플 메모리가 있습니다. 종종 이 샘플 메모리는 채널 간에 공유되며 때로는 더 낮은 샘플 속도에서만 완전히 사용할 수 있습니다. 가장 높은 샘플 속도에서 메모리는 수십 KB로 제한될 수 있습니다. 최신 '실시간'' 샘플링 속도 DSO는 일반적으로 샘플 속도에서 입력 대역폭의 5-10배를 갖습니다. 따라서 100MHz 대역폭 DSO의 샘플 속도는 500Ms/s - 1Gs/s입니다. 샘플링 속도가 크게 증가하여 1세대 디지털 스코프에 가끔 존재했던 잘못된 신호 표시가 크게 제거되었습니다. 대부분의 최신 오실로스코프는 GPIB, 이더넷, 직렬 포트 및 USB와 같은 하나 이상의 외부 인터페이스 또는 버스를 제공하여 외부 소프트웨어에 의한 원격 기기 제어를 허용합니다. 다음은 다양한 오실로스코프 유형 목록입니다. 음극선 오실로스코프 듀얼 빔 오실로스코프 아날로그 스토리지 오실로스코프 디지털 오실로스코프 혼합 신호 오실로스코프 휴대용 오실로스코프 PC 기반 오실로스코프 논리 분석기는 디지털 시스템 또는 디지털 회로에서 여러 신호를 캡처하고 표시하는 장비입니다. 로직 분석기는 캡처된 데이터를 타이밍 다이어그램, 프로토콜 디코딩, 상태 머신 트레이스, 어셈블리 언어로 변환할 수 있습니다. 로직 분석기는 고급 트리거링 기능을 가지고 있으며 사용자가 디지털 시스템에서 많은 신호 간의 타이밍 관계를 확인해야 할 때 유용합니다. 모듈식 로직 분석기는 섀시 또는 메인프레임과 로직 분석기 모듈로 구성됩니다. 섀시 또는 메인프레임에는 디스플레이, 컨트롤, 제어 컴퓨터 및 데이터 캡처 하드웨어가 설치된 여러 슬롯이 포함됩니다. 각 모듈에는 특정 수의 채널이 있으며 여러 모듈을 결합하여 매우 높은 채널 수를 얻을 수 있습니다. 다수의 모듈을 결합하여 높은 채널 수와 일반적으로 모듈식 로직 분석기의 더 높은 성능을 얻을 수 있는 기능은 모듈식 로직 분석기를 더 비싸게 만듭니다. 최고급 모듈형 로직 분석기의 경우 사용자는 자신의 호스트 PC를 제공하거나 시스템과 호환되는 임베디드 컨트롤러를 구입해야 할 수 있습니다. 휴대용 논리 분석기는 공장에서 설치된 옵션과 함께 모든 것을 단일 패키지로 통합합니다. 일반적으로 모듈식보다 성능이 낮지만 범용 디버깅을 위한 경제적인 계측 도구입니다. PC 기반 논리 분석기에서 하드웨어는 USB 또는 이더넷 연결을 통해 컴퓨터에 연결되고 캡처된 신호를 컴퓨터의 소프트웨어에 전달합니다. 이러한 장치는 개인용 컴퓨터의 기존 키보드, 디스플레이 및 CPU를 사용하기 때문에 일반적으로 훨씬 작고 저렴합니다. 로직 분석기는 디지털 이벤트의 복잡한 시퀀스에서 트리거된 다음 테스트 중인 시스템에서 많은 양의 디지털 데이터를 캡처할 수 있습니다. 오늘날 특수 커넥터가 사용됩니다. 로직 분석기 프로브의 발전으로 여러 공급업체가 지원하는 공통 공간이 생겨 최종 사용자에게 추가 자유를 제공합니다. 소프트 터치; D-Max를 사용 중입니다. 이 프로브는 프로브와 회로 기판 사이에 내구성 있고 안정적인 기계적 및 전기적 연결을 제공합니다. 스펙트럼 분석기는 장비의 전체 주파수 범위 내에서 입력 신호의 크기 대 주파수를 측정합니다. 주요 용도는 신호 스펙트럼의 전력을 측정하는 것입니다. 광학 및 음향 스펙트럼 분석기도 있지만 여기서는 전기 입력 신호를 측정하고 분석하는 전자 분석기에 대해서만 설명합니다. 전기 신호에서 얻은 스펙트럼은 주파수, 전력, 고조파, 대역폭 등에 대한 정보를 제공합니다. 주파수는 수평축에 표시되고 신호 진폭은 수직축에 표시됩니다. 스펙트럼 분석기는 무선 주파수, RF 및 오디오 신호의 주파수 스펙트럼 분석을 위해 전자 산업에서 널리 사용됩니다. 신호의 스펙트럼을 보면 신호의 요소와 이를 생성하는 회로의 성능을 밝힐 수 있습니다. 스펙트럼 분석기는 매우 다양한 측정을 수행할 수 있습니다. 신호의 스펙트럼을 얻는 데 사용되는 방법을 살펴보면 스펙트럼 분석기 유형을 분류할 수 있습니다. - SWEPT-TUNED SPECTRUM ANALYZER는 수퍼헤테로다인 수신기를 사용하여 입력 신호 스펙트럼의 일부(전압 제어 발진기 및 믹서 사용)를 대역 통과 필터의 중심 주파수로 하향 변환합니다. 수퍼헤테로다인 아키텍처에서 전압 제어 발진기는 기기의 전체 주파수 범위를 활용하여 다양한 주파수 범위에서 스위프됩니다. 스위프 튜닝된 스펙트럼 분석기는 라디오 수신기의 후손입니다. 따라서 스위프 튜닝 분석기는 튜닝 필터 분석기(TRF 라디오와 유사) 또는 슈퍼헤테로다인 분석기입니다. 사실, 가장 단순한 형태로 스위프 튜닝 스펙트럼 분석기는 자동으로 튜닝(스윕)되는 주파수 범위를 가진 주파수 선택 전압계로 생각할 수 있습니다. 본질적으로 사인파의 rms 값을 표시하도록 보정된 주파수 선택형 피크 응답 전압계입니다. 스펙트럼 분석기는 복잡한 신호를 구성하는 개별 주파수 성분을 표시할 수 있습니다. 그러나 위상 정보는 제공하지 않고 크기 정보만 제공합니다. 최신 스윕 튜닝 분석기(특히 슈퍼헤테로다인 분석기)는 다양한 측정을 수행할 수 있는 정밀 장치입니다. 그러나 주어진 범위의 모든 주파수를 동시에 평가할 수 없기 때문에 주로 정상 상태 또는 반복적인 신호를 측정하는 데 사용됩니다. 모든 주파수를 동시에 평가하는 기능은 실시간 분석기에서만 가능합니다. - 실시간 스펙트럼 분석기: FFT 스펙트럼 분석기는 파형을 입력 신호의 주파수 스펙트럼 구성 요소로 변환하는 수학적 프로세스인 이산 푸리에 변환(DFT)을 계산합니다. 푸리에 또는 FFT 스펙트럼 분석기는 또 다른 실시간 스펙트럼 분석기 구현입니다. 푸리에 분석기는 디지털 신호 처리를 사용하여 입력 신호를 샘플링하고 주파수 영역으로 변환합니다. 이 변환은 FFT(고속 푸리에 변환)를 사용하여 수행됩니다. FFT는 데이터를 시간 영역에서 주파수 영역으로 변환하는 데 사용되는 수학 알고리즘인 이산 푸리에 변환을 구현한 것입니다. 다른 유형의 실시간 스펙트럼 분석기, 즉 병렬 필터 분석기는 각각 다른 대역 통과 주파수를 갖는 여러 대역 통과 필터를 결합합니다. 각 필터는 항상 입력에 연결된 상태를 유지합니다. 초기 안정화 시간 후 병렬 필터 분석기는 분석기의 측정 범위 내의 모든 신호를 즉시 감지하고 표시할 수 있습니다. 따라서 병렬 필터 분석기는 실시간 신호 분석을 제공합니다. 병렬 필터 분석기는 빠르며 과도 신호 및 시변 신호를 측정합니다. 그러나 병렬 필터 분석기의 주파수 분해능은 대역통과 필터의 폭에 따라 분해능이 결정되기 때문에 대부분의 스위프 튜닝된 분석기보다 훨씬 낮습니다. 넓은 주파수 범위에서 정밀한 분해능을 얻으려면 많은 개별 필터가 필요하므로 비용이 많이 들고 복잡합니다. 이것이 시장에서 가장 단순한 것을 제외하고 대부분의 병렬 필터 분석기가 비싼 이유입니다. - 벡터 신호 분석(VSA): 과거에는 스위프 튜닝 및 슈퍼헤테로다인 스펙트럼 분석기가 오디오에서 마이크로파를 통해 밀리미터 주파수에 이르기까지 광범위한 주파수 범위를 다루었습니다. 또한 DSP(디지털 신호 처리) 집약적 FFT(고속 푸리에 변환) 분석기는 고해상도 스펙트럼 및 네트워크 분석을 제공했지만 아날로그-디지털 변환 및 신호 처리 기술의 한계로 인해 저주파에 제한되었습니다. 오늘날의 광대역, 벡터 변조, 시변 신호는 FFT 분석 및 기타 DSP 기술의 기능을 크게 활용합니다. 벡터 신호 분석기는 슈퍼헤테로다인 기술과 고속 ADC 및 기타 DSP 기술을 결합하여 빠른 고해상도 스펙트럼 측정, 복조 및 고급 시간 영역 분석을 제공합니다. VSA는 통신, 비디오, 방송, 수중 음파 탐지기 및 초음파 이미징 애플리케이션에 사용되는 버스트, 과도 또는 변조 신호와 같은 복잡한 신호를 특성화하는 데 특히 유용합니다. 폼 팩터에 따라 스펙트럼 분석기는 벤치탑, 휴대용, 핸드헬드 및 네트워크로 분류됩니다. 벤치탑 모델은 실험실 환경이나 제조 영역과 같이 스펙트럼 분석기를 AC 전원에 연결할 수 있는 애플리케이션에 유용합니다. 벤치 탑 스펙트럼 분석기는 일반적으로 휴대용 또는 휴대용 버전보다 더 나은 성능과 사양을 제공합니다. 그러나 일반적으로 더 무겁고 냉각용 팬이 여러 개 있습니다. 일부 벤치탑 스펙트럼 분석기는 전원 콘센트에서 멀리 떨어진 곳에서도 사용할 수 있도록 배터리 팩을 옵션으로 제공합니다. 그것들을 휴대용 스펙트럼 분석기라고 합니다. 휴대용 모델은 스펙트럼 분석기를 측정하기 위해 외부로 가져가거나 사용 중에 휴대해야 하는 애플리케이션에 유용합니다. 우수한 휴대용 스펙트럼 분석기는 사용자가 전원 콘센트가 없는 장소에서 작업할 수 있도록 하는 선택적 배터리 전원 작동, 밝은 햇빛, 어둠 또는 먼지가 많은 조건, 가벼운 무게에서도 화면을 읽을 수 있도록 명확하게 볼 수 있는 디스플레이를 제공할 것으로 예상됩니다. 휴대용 스펙트럼 분석기는 스펙트럼 분석기가 매우 가볍고 작아야 하는 응용 분야에 유용합니다. 휴대용 분석기는 더 큰 시스템에 비해 제한된 기능을 제공합니다. 그러나 휴대용 스펙트럼 분석기의 장점은 매우 낮은 전력 소비, 사용자가 야외에서 자유롭게 이동할 수 있는 배터리 전원 작동, 매우 작은 크기 및 가벼운 무게입니다. 마지막으로 NETWORKED SPECTRUM ANALYZERS에는 디스플레이가 포함되어 있지 않으며 지리적으로 분산된 새로운 차원의 스펙트럼 모니터링 및 분석 애플리케이션을 가능하게 하도록 설계되었습니다. 주요 속성은 분석기를 네트워크에 연결하고 네트워크를 통해 이러한 장치를 모니터링하는 기능입니다. 많은 스펙트럼 분석기에 제어용 이더넷 포트가 있지만 일반적으로 효율적인 데이터 전송 메커니즘이 부족하고 분산 방식으로 배포하기에는 너무 부피가 크거나 비용이 많이 듭니다. 이러한 장치의 분산 특성으로 인해 송신기의 지리적 위치, 동적 스펙트럼 액세스를 위한 스펙트럼 모니터링 및 기타 여러 애플리케이션이 가능합니다. 이러한 장치는 분석기 네트워크 전체에서 데이터 캡처를 동기화하고 저렴한 비용으로 네트워크 효율적인 데이터 전송을 가능하게 합니다. 프로토콜 분석기는 통신 채널을 통해 신호 및 데이터 트래픽을 캡처하고 분석하는 데 사용되는 하드웨어 및/또는 소프트웨어를 통합한 도구입니다. 프로토콜 분석기는 주로 성능 측정 및 문제 해결에 사용됩니다. 네트워크에 연결하여 핵심 성과 지표를 계산하여 네트워크를 모니터링하고 문제 해결 활동을 가속화합니다. NETWORK PROTOCOL ANALYZER는 네트워크 관리자 툴킷의 중요한 부분입니다. 네트워크 프로토콜 분석은 네트워크 통신의 상태를 모니터링하는 데 사용됩니다. 네트워크 장치가 특정 방식으로 작동하는 이유를 알아내기 위해 관리자는 프로토콜 분석기를 사용하여 트래픽을 스니핑하고 유선을 통해 전달되는 데이터와 프로토콜을 노출합니다. 네트워크 프로토콜 분석기는 다음을 수행하는 데 사용됩니다. - 해결하기 어려운 문제 해결 - 악성 소프트웨어/맬웨어를 탐지하고 식별합니다. 침입 탐지 시스템 또는 허니팟으로 작업하십시오. - 기준 트래픽 패턴 및 네트워크 활용 메트릭과 같은 정보 수집 - 네트워크에서 제거할 수 있도록 사용하지 않는 프로토콜 식별 - 침투 테스트를 위한 트래픽 생성 - 트래픽 도청(예: 승인되지 않은 인스턴트 메시징 트래픽 또는 무선 액세스 포인트 찾기) 시간 영역 반사계(TDR)는 시간 영역 반사 측정을 사용하여 연선 및 동축 케이블, 커넥터, 인쇄 회로 기판 등과 같은 금속 케이블의 결함을 특성화하고 찾는 장비입니다. 시간 영역 반사계는 도체를 따라 반사를 측정합니다. 이를 측정하기 위해 TDR은 입사 신호를 도체에 전송하고 반사를 확인합니다. 도체의 임피던스가 균일하고 적절하게 종단되면 반사가 없고 나머지 입사 신호는 종단에 의해 맨 끝에서 흡수됩니다. 그러나 어딘가에 임피던스 변화가 있으면 입사 신호의 일부가 소스로 다시 반사됩니다. 반사는 입사 신호와 같은 모양을 갖지만 부호와 크기는 임피던스 레벨의 변화에 따라 달라집니다. 임피던스가 단계적으로 증가하면 반사는 입사 신호와 동일한 부호를 가지며 임피던스가 단계적으로 감소하면 반사는 반대 부호를 갖습니다. 반사는 시간 영역 반사계의 출력/입력에서 측정되고 시간의 함수로 표시됩니다. 또는 신호 전파 속도가 주어진 전송 매체에 대해 거의 일정하기 때문에 디스플레이는 케이블 길이의 함수로 전송 및 반사를 표시할 수 있습니다. TDR은 케이블 임피던스와 길이, 커넥터 및 스플라이스 손실 및 위치를 분석하는 데 사용할 수 있습니다. TDR 임피던스 측정은 설계자가 시스템 상호 연결의 신호 무결성 분석을 수행하고 디지털 시스템 성능을 정확하게 예측할 수 있는 기회를 제공합니다. TDR 측정은 기판 특성화 작업에 널리 사용됩니다. 회로 기판 설계자는 기판 트레이스의 특성 임피던스를 결정하고 기판 구성 요소에 대한 정확한 모델을 계산하며 기판 성능을 보다 정확하게 예측할 수 있습니다. 시간 영역 반사계의 다른 많은 응용 분야가 있습니다. SEMICONDUCTOR CURVE TRACER는 다이오드, 트랜지스터, 사이리스터와 같은 이산 반도체 소자의 특성을 분석하는 테스트 장비입니다. 이 계측기는 오실로스코프를 기반으로 하지만 테스트 중인 장치를 자극하는 데 사용할 수 있는 전압 및 전류 소스도 포함합니다. 테스트 중인 장치의 두 단자에 스위프 전압을 적용하고 각 전압에서 장치가 흐르도록 허용하는 전류의 양을 측정합니다. VI(전압 대 전류)라는 그래프가 오실로스코프 화면에 표시됩니다. 구성에는 인가된 최대 전압, 인가된 전압의 극성(양극과 음극 모두의 자동 인가 포함), 장치와 직렬로 삽입된 저항이 포함됩니다. 다이오드와 같은 2개의 터미널 장치의 경우 장치를 완전히 특성화하는 데 충분합니다. 곡선 추적기는 다이오드의 순방향 전압, 역방향 누설 전류, 역방향 항복 전압 등과 같은 모든 흥미로운 매개변수를 표시할 수 있습니다. 트랜지스터 및 FET와 같은 3단자 장치도 베이스 또는 게이트 단자와 같이 테스트 중인 장치의 제어 단자에 대한 연결을 사용합니다. 트랜지스터 및 기타 전류 기반 장치의 경우 베이스 또는 기타 제어 단자 전류가 단계적입니다. 전계 효과 트랜지스터(FET)의 경우 계단식 전류 대신 계단식 전압이 사용됩니다. 구성된 메인 단자 전압 범위를 통해 전압을 스위핑함으로써 제어 신호의 각 전압 단계에 대해 VI 곡선 그룹이 자동으로 생성됩니다. 이 곡선 그룹을 사용하면 트랜지스터의 이득 또는 사이리스터 또는 TRIAC의 트리거 전압을 매우 쉽게 결정할 수 있습니다. 최신 반도체 곡선 추적기는 직관적인 Windows 기반 사용자 인터페이스, IV, CV 및 펄스 생성, 펄스 IV, 모든 기술에 포함된 응용 프로그램 라이브러리 등과 같은 많은 매력적인 기능을 제공합니다. 위상 회전 테스터/표시기: 이들은 3상 시스템 및 개방/비통전 위상에서 위상 시퀀스를 식별하기 위한 작고 견고한 테스트 장비입니다. 회전 기계, 모터를 설치하고 발전기 출력을 확인하는 데 이상적입니다. 애플리케이션 중에는 적절한 위상 시퀀스 식별, 누락된 와이어 위상 감지, 회전 기계에 대한 적절한 연결 결정, 활성 회로 감지 등이 있습니다. FREQUENCY COUNTER는 주파수를 측정하는 데 사용되는 테스트 장비입니다. 주파수 카운터는 일반적으로 특정 기간 내에 발생하는 이벤트 수를 누적하는 카운터를 사용합니다. 계산할 이벤트가 전자 형식인 경우 계측기에 대한 간단한 인터페이스만 있으면 됩니다. 더 복잡한 신호는 계산에 적합하도록 약간의 조절이 필요할 수 있습니다. 대부분의 주파수 카운터에는 입력에 일종의 증폭기, 필터링 및 성형 회로가 있습니다. 디지털 신호 처리, 감도 제어 및 히스테리시스는 성능을 향상시키는 다른 기술입니다. 본질적으로 전자적이지 않은 다른 유형의 주기적 이벤트는 변환기를 사용하여 변환해야 합니다. RF 주파수 카운터는 저주파 카운터와 동일한 원리로 작동합니다. 오버플로 전에 더 많은 범위가 있습니다. 매우 높은 마이크로파 주파수의 경우 많은 설계에서 고속 프리스케일러를 사용하여 신호 주파수를 일반 디지털 회로가 작동할 수 있는 지점으로 낮춥니다. 마이크로파 주파수 카운터는 최대 거의 100GHz의 주파수를 측정할 수 있습니다. 이러한 고주파수 이상에서 측정할 신호는 믹서에서 국부 발진기의 신호와 결합되어 직접 측정을 위해 충분히 낮은 차이 주파수에서 신호를 생성합니다. 주파수 카운터의 인기 있는 인터페이스는 다른 최신 기기와 유사한 RS232, USB, GPIB 및 이더넷입니다. 측정 결과를 보내는 것 외에도 카운터는 사용자가 정의한 측정 한계를 초과할 때 사용자에게 알릴 수 있습니다. 자세한 내용 및 기타 유사한 장비는 장비 웹사이트를 방문하십시오. http://www.sourceindustrialsupply.com For other similar equipment, please visit our equipment website: http://www.sourceindustrialsupply.com CLICK Product Finder-Locator Service 이전 페이지
- Ultrasonic Machining, Ultrasonic Impact Grinding, Custom Manufacturing
Ultrasonic Machining, Ultrasonic Impact Grinding, Rotary Ultrasonic Machining, Non-Conventional Machining, Custom Manufacturing - AGS-TECH Inc. New Mexico, USA 초음파 가공 및 회전식 초음파 가공 및 초음파 충격 연삭 Another popular NON-CONVENTIONAL MACHINING technique we frequently use is ULTRASONIC MACHINING (UM), also widely known as ULTRASONIC 충격 연삭(IMPACT GRINDING)은 공작물과 도구 사이를 자유롭게 흐르는 연마 슬러리의 도움을 받아 초음파 주파수에서 진동하는 진동 도구를 사용하여 연마 입자로 미세 칩화 및 침식에 의해 공작물 표면에서 재료가 제거됩니다. 열이 거의 발생하지 않기 때문에 대부분의 다른 기존 가공 작업과 다릅니다. 초음파 가공 도구의 끝 부분은 0.05~0.125mm의 진폭과 20kHz 부근의 주파수에서 진동하는 "소노트로드"라고 합니다. 팁의 진동은 공구와 공작물의 표면 사이의 미세한 연마 입자에 고속을 전달합니다. 공구는 공작물과 접촉하지 않으므로 연삭 압력은 거의 2파운드를 넘지 않습니다. 이 작동 원리로 인해 이 작업은 유리, 사파이어, 루비, 다이아몬드 및 세라믹과 같은 매우 단단하고 부서지기 쉬운 재료를 가공하는 데 적합합니다. 연마 입자는 20~60부피% 농도의 물 슬러리 내에 있습니다. 슬러리는 또한 절단/가공 영역에서 떨어진 파편의 운반체 역할을 합니다. 우리는 연마 입자로 주로 탄화붕소, 산화알루미늄 및 탄화규소를 사용하며, 입자 크기는 황삭 공정의 경우 100에서 마감 공정의 경우 1000입니다. 초음파 가공(UM) 기술은 세라믹 및 유리, 탄화물, 보석, 경화강과 같이 단단하고 부서지기 쉬운 재료에 가장 적합합니다. 초음파 가공의 표면 조도는 공작물/공구의 경도와 사용된 연마 입자의 평균 직경에 따라 달라집니다. 툴팁은 일반적으로 툴홀더를 통해 변환기에 부착된 저탄소강, 니켈 및 연강입니다. 초음파 가공 공정은 공구에 금속의 소성 변형과 공작물의 취성을 활용합니다. 공구는 입자가 부서지기 쉬운 공작물에 영향을 미칠 때까지 입자를 포함하는 연마 슬러리를 진동시키고 아래로 누릅니다. 이 작업 중에 공구가 매우 약간 구부러지는 동안 공작물이 파손됩니다. 미세한 연마재를 사용하여 0.0125mm의 치수 공차를 달성할 수 있으며 초음파 가공(UM)을 사용하면 더 좋습니다. 가공 시간은 공구가 진동하는 빈도, 입자 크기 및 경도, 슬러리 유체의 점도에 따라 다릅니다. 슬러리 유체의 점성이 낮을수록 사용한 연마제를 더 빨리 제거할 수 있습니다. 입자 크기는 공작물의 경도보다 크거나 같아야 합니다. 예를 들어 초음파 가공으로 1.2mm 너비의 유리 스트립에 직경 0.4mm의 여러 정렬 구멍을 가공할 수 있습니다. 초음파 가공 공정의 물리학에 대해 조금 알아보겠습니다. 고체 표면을 때리는 입자에 의해 생성되는 높은 응력 덕분에 초음파 가공에서 마이크로칩이 가능합니다. 입자와 표면 사이의 접촉 시간은 10~100마이크로초 정도로 매우 짧습니다. 접촉 시간은 다음과 같이 표현할 수 있습니다. ~ = 5r/Co x (Co/v) exp 1/5 여기서 r은 구형 입자의 반경, Co는 공작물의 탄성파 속도(Co = sqroot E/d), v는 입자가 표면에 부딪히는 속도입니다. 입자가 표면에 가하는 힘은 운동량 변화율에서 구합니다. F = d(mv)/dt 여기서 m은 입자 질량입니다. 표면에서 부딪치고 반발하는 입자(입자)의 평균 힘은 다음과 같습니다. 즐겨찾기 = 2mv / to 여기까지가 연락 시간입니다. 이 식에 숫자를 대입하면 부품이 매우 작더라도 접촉 면적도 매우 작기 때문에 가해지는 힘과 응력이 상당히 높아서 마이크로칩과 침식이 발생함을 알 수 있습니다. ROTARY ULTRASONIC MACHINING(RUM): 이 방법은 연마 슬러리를 도구 표면에 함침되거나 전기도금된 금속 결합 다이아몬드 연마재가 있는 도구로 교체하는 초음파 기계 가공의 변형입니다. 공구가 회전하고 초음파로 진동합니다. 회전 및 진동 도구에 대해 일정한 압력으로 공작물을 누릅니다. 회전식 초음파 가공 공정은 높은 재료 제거율로 단단한 재료에 깊은 구멍을 생성하는 것과 같은 기능을 제공합니다. 우리는 다수의 기존 및 비전통적인 제조 기술을 사용하기 때문에 특정 제품과 가장 빠르고 경제적인 제조 및 제조 방법에 대해 질문이 있을 때마다 도움을 드릴 수 있습니다. CLICK Product Finder-Locator Service 이전 페이지
- Functional Decorative Coatings - Thin Film - Thick Films - AR Coating
Functional & Decorative Coatings, Thin Film, Thick Films, Antireflective and Reflective Mirror Coating - AGS-TECH Inc. 기능성 도료 / 장식 도료 / 박막 / 후막 A COATING 는 물체의 표면에 바르는 덮개입니다. Coatings can be in the form of THIN FILM (less than 1 micron thick) or THICK FILM ( 1 마이크론 이상의 두께). 코팅을 적용하는 목적에 따라 제공할 수 있습니다 DECORATIVE COATINGS_cc781905-5cde-3194-bb3b3b-136bad5cf58d_and/or_cc781905 때로는 접착성, 습윤성, 내식성 또는 내마모성과 같은 기질의 표면 특성을 변경하기 위해 기능성 코팅을 적용합니다. 반도체 장치 제조와 같은 일부 다른 경우에는 완제품의 필수 부분이 되는 자화 또는 전기 전도성과 같은 완전히 새로운 특성을 추가하기 위해 기능성 코팅을 적용합니다. 가장 인기 있는 FUNCTIONAL COATINGS are: 접착 코팅: 예는 접착 테이프, 다림질 직물입니다. 접착 특성을 변경하기 위해 다른 기능적 접착 코팅이 적용됩니다. 예를 들어, 접착력이 없는 PTFE 코팅 조리 팬, 후속 코팅이 잘 접착되도록 하는 프라이머가 있습니다. 마찰 코팅: 이 기능성 코팅은 마찰, 윤활 및 마모의 원리와 관련이 있습니다. 한 재료가 다른 재료 위에 미끄러지거나 문지르는 모든 제품은 복잡한 마찰 상호 작용의 영향을 받습니다. 고관절 임플란트 및 기타 인공 보철물과 같은 제품은 특정 방식으로 윤활되는 반면 다른 제품은 기존 윤활제를 사용할 수 없는 고온 슬라이딩 부품과 같이 윤활되지 않습니다. 압축된 산화물 층의 형성은 이러한 슬라이딩 기계 부품의 마모를 방지하는 것으로 입증되었습니다. 마찰 기능 코팅은 기계 요소의 마모를 최소화하고, 금형 및 금형과 같은 제조 도구의 마모 및 공차 편차를 최소화하고, 전력 요구 사항을 최소화하고, 기계 및 장비를 보다 에너지 효율적으로 만드는 등 산업계에서 큰 이점을 제공합니다. 광학 코팅: 예로는 반사 방지(AR) 코팅, 거울용 반사 코팅, 눈을 보호하거나 기판의 수명을 연장하기 위한 UV 흡수 코팅, 일부 유색 조명에 사용되는 착색, 착색 유리 및 선글라스가 있습니다. 촉매 코팅 self-cleaning 유리에 적용된 것과 같은. 감광 코팅 사진 필름과 같은 제품을 만드는 데 사용 보호 코팅: 페인트는 의도적으로 장식적인 것 외에도 제품을 보호하는 것으로 간주될 수 있습니다. 플라스틱 및 기타 재료의 경질 긁힘 방지 코팅은 긁힘 감소, 내마모성 향상 등을 위해 가장 널리 사용되는 기능성 코팅 중 하나입니다. 도금과 같은 부식 방지 코팅도 매우 인기가 있습니다. 다른 보호 기능 코팅은 방수 직물과 종이에, 항균 표면 코팅은 수술 도구 및 임플란트에 적용됩니다. 친수성/소수성 코팅: 습윤(친수성) 및 비습윤(소수성) 기능의 얇고 두꺼운 필름은 수분 흡수가 바람직하거나 바람직하지 않은 응용 분야에서 중요합니다. 고급 기술을 사용하여 제품 표면을 쉽게 젖거나 젖지 않도록 변경할 수 있습니다. 일반적인 응용 분야는 직물, 드레싱, 가죽 부츠, 제약 또는 수술 제품입니다. 친수성이란 수소결합을 통해 물(H2O)과 일시적으로 결합할 수 있는 분자의 물리적 성질을 말한다. 이것은 열역학적으로 유리하며 이러한 분자를 물뿐만 아니라 다른 극성 용매에도 용해시킵니다. 친수성 분자와 소수성 분자는 각각 극성 분자와 비극성 분자로도 알려져 있습니다. 자기 코팅: 이 기능적 코팅은 자기 플로피 디스크, 카세트, 자기 줄무늬, 자기 광학 저장 장치, 유도 기록 매체, 자기 저항 센서 및 제품의 박막 헤드와 같은 자기 특성을 추가합니다. 자성 박막은 전자 산업에서 주로 사용되는 수 마이크로미터 이하의 두께를 갖는 자성 재료의 시트입니다. 자성 박막은 원자 배열에서 단결정, 다결정, 비정질 또는 다층 기능 코팅일 수 있습니다. 강자성 필름과 페리자성 필름이 모두 사용됩니다. 강자성 기능 코팅은 일반적으로 전이 금속 기반 합금입니다. 예를 들어 퍼멀로이는 니켈-철 합금입니다. 가닛 또는 비정질 필름과 같은 페리자성 기능 코팅은 철 또는 코발트 및 희토류와 같은 전이 금속을 포함하며 페리자성 특성은 퀴리 온도의 큰 변화 없이 낮은 전체 자기 모멘트를 달성할 수 있는 자기 광학 응용 분야에서 유리합니다. . 일부 센서 요소는 자기장과 함께 전기 저항과 같은 전기적 특성이 변화하는 원리에 따라 작동합니다. 반도체 기술에서 디스크 저장 기술에 사용되는 자기 저항 헤드는 이러한 원리로 작동합니다. 매우 큰 자기 저항 신호(거대 자기 저항)는 자성 및 비자성 재료를 포함하는 자기 다층 및 복합 재료에서 관찰됩니다. 전기 또는 전자 코팅: 이러한 기능 코팅은 저항과 같은 제품을 제조하기 위한 전도성, 변압기에 사용되는 자석 와이어 코팅의 경우와 같은 절연 특성과 같은 전기 또는 전자 특성을 추가합니다. 장식용 코팅: 장식용 코팅에 대해 이야기할 때 옵션은 상상에 의해서만 제한됩니다. 후막 및 박막 유형 코팅 모두 성공적으로 설계되어 과거에 고객 제품에 적용되었습니다. 기판의 기하학적 모양과 재료 및 적용 조건의 어려움에 관계없이 원하는 장식 코팅에 대한 정확한 Pantone 코드 및 적용 방법과 같은 화학적, 물리적 측면을 항상 공식화할 수 있습니다. 모양이나 색상이 다른 복잡한 패턴도 가능합니다. 플라스틱 폴리머 부품을 금속처럼 보이게 할 수 있습니다. 우리는 다양한 패턴으로 압출물에 색상을 지정할 수 있으며 양극 처리된 것처럼 보이지도 않습니다. 이상한 모양의 부분을 미러 코팅할 수 있습니다. 또한, 동시에 기능성 코팅으로도 작용하는 장식용 코팅제를 제조할 수 있습니다. 기능성 코팅에 사용되는 아래 언급된 박막 및 후막 증착 기술은 장식 코팅에 사용할 수 있습니다. 다음은 인기 있는 장식용 코팅제입니다. - PVD 박막 장식 코팅 - 전기도금 장식 코팅 - CVD 및 PECVD 박막 장식 코팅 - 열 증발 장식 코팅 - 롤투롤 장식 코팅 - 전자빔 산화물 간섭 장식 코팅 - 이온 도금 - 장식 코팅을 위한 음극 아크 증발 - PVD + 포토리소그래피, PVD에 중금도금 - 유리 착색용 에어로졸 코팅 - 변색 방지 코팅 - 장식용 구리-니켈-크롬 시스템 - 장식용 분체도장 - 장식용 페인팅, 안료, 충전제, 콜로이드 실리카 분산제 등을 사용한 맞춤형 페인트 제형 장식용 코팅에 대한 요구 사항이 있는 경우 당사에 연락하여 전문적인 의견을 제공할 수 있습니다. 색상 판독기, 색상 비교기 등의 고급 도구가 있습니다. 코팅의 일관된 품질을 보장합니다. 얇고 두꺼운 필름 코팅 공정: 여기에 가장 널리 사용되는 기술이 있습니다. 전기도금 / 화학도금 (경질크롬, 화학니켈) 전기 도금은 장식 목적, 금속의 부식 방지 또는 기타 목적을 위해 가수분해에 의해 한 금속을 다른 금속에 도금하는 과정입니다. 전기도금을 통해 제품의 대부분에 강철, 아연 또는 플라스틱과 같은 저렴한 금속을 사용한 다음 더 나은 외관, 보호 및 제품에 필요한 기타 특성을 위해 외부에 다른 금속을 필름 형태로 적용할 수 있습니다. 화학 도금으로도 알려진 무전해 도금은 외부 전력을 사용하지 않고 발생하는 수용액에서 여러 동시 반응을 포함하는 비 갈바니 도금 방법입니다. 반응은 수소가 환원제에 의해 방출되고 산화되어 부품 표면에 음전하를 생성할 때 수행됩니다. 이 얇고 두꺼운 필름의 장점은 우수한 내식성, 낮은 처리 온도, 보어 홀, 슬롯 등에 침착 가능성입니다. 단점은 제한된 코팅 재료 선택, 코팅의 상대적으로 부드러운 특성, 환경 오염 처리 수조가 필요하다는 것입니다. 시안화물, 중금속, 불화물, 오일과 같은 화학 물질을 포함하여 표면 복제의 정확도가 제한됩니다. 확산 공정 (질화, 연질화, 붕소화, 인산염 처리 등) 열처리로에서 확산된 요소는 일반적으로 고온에서 금속 표면과 반응하는 가스에서 발생합니다. 이것은 가스의 열 해리의 결과로 순수한 열 및 화학 반응일 수 있습니다. 어떤 경우에는 확산 요소가 솔리드에서 시작됩니다. 이러한 열화학 코팅 공정의 장점은 우수한 내식성, 우수한 재현성입니다. 이들의 단점은 상대적으로 부드러운 코팅, 제한된 기본 재료 선택(질화에 적합해야 함), 긴 처리 시간, 관련된 환경 및 건강 위험, 후처리 요구 사항입니다. CVD(화학 기상 증착) CVD는 고품질, 고성능, 고체 코팅을 생산하는 데 사용되는 화학 공정입니다. 이 과정에서 박막도 생성됩니다. 전형적인 CVD에서, 기판은 원하는 박막을 생성하기 위해 기판 표면 상에서 반응 및/또는 분해되는 하나 이상의 휘발성 전구체에 노출된다. 이러한 박막 및 후막 필름의 장점은 높은 내마모성, 경제적으로 더 두꺼운 코팅을 생성할 수 있는 가능성, 보어 홀, 슬롯 등에 대한 적합성입니다. CVD 공정의 단점은 높은 처리 온도, 여러 금속(예: TiAlN)으로 코팅하는 것이 어렵거나 불가능하고, 모서리가 둥글고, 환경에 유해한 화학 물질을 사용한다는 것입니다. PACVD / PECVD(플라즈마 보조 화학 기상 증착) PACVD는 Plasma Enhanced CVD를 나타내는 PECVD라고도 합니다. PVD 코팅 공정에서는 박막 및 후막 재료가 고체 형태에서 증발되는 반면, PECVD에서는 코팅이 기체 상태에서 발생합니다. 전구체 가스는 코팅에 사용할 수 있도록 플라즈마에서 분해됩니다. 이 박막 및 후막 증착 기술의 장점은 CVD에 비해 상당히 낮은 공정 온도가 가능하고 정밀한 코팅이 증착된다는 것입니다. PACVD의 단점은 보어 홀, 슬롯 등에 대한 적합성이 제한적이라는 것입니다. PVD(물리적 증착) PVD 공정은 원하는 필름 재료의 기화된 형태를 공작물 표면에 응축시켜 박막을 증착하는 데 사용되는 다양한 순수 물리적 진공 증착 방법입니다. 스퍼터링 및 증발 코팅은 PVD의 예입니다. 장점은 환경에 해로운 물질과 배출물이 생성되지 않고 다양한 코팅이 생성될 수 있으며 코팅 온도가 대부분의 강철의 최종 열처리 온도보다 낮고 정밀하게 재현 가능한 얇은 코팅, 높은 내마모성, 낮은 마찰 계수입니다. 단점은 구멍, 슬롯 등입니다. 개구부의 직경 또는 너비와 동일한 깊이까지만 코팅할 수 있으며 특정 조건에서만 내식성이 있으며 균일한 필름 두께를 얻기 위해서는 증착 중에 부품을 회전시켜야 합니다. 기능 및 장식 코팅의 접착력은 기질에 따라 다릅니다. 또한, 박막 및 후막 코팅의 수명은 습도, 온도... 등과 같은 환경 매개변수에 따라 달라집니다. 따라서 기능적 또는 장식적 코팅을 고려하기 전에 당사에 문의하여 의견을 구하십시오. 고객의 기판과 용도에 가장 적합한 코팅 재료와 코팅 기술을 선택하여 가장 엄격한 품질 기준에 따라 증착할 수 있습니다. 박막 및 후막 증착 기능에 대한 자세한 내용은 AGS-TECH Inc.에 문의하십시오. 디자인 지원이 필요하십니까? 프로토타입이 필요하십니까? 대량 생산이 필요하십니까? 우리는 당신을 돕기 위해 여기 있습니다. CLICK Product Finder-Locator Service 이전 페이지
- Lighting, Illumination, LED Assembly, Fixture, Marine Lighting, Lights
Lighting, Illumination, LED Assembly, Lighting Fixture, Marine Lighting, Warning Lights, Panel Light, Indicator Lamps, Fiber Optic Illumination, AGS-TECH Inc. 조명 및 조명 시스템 제조 및 조립 엔지니어링 통합업체로서 AGS-TECH는 맞춤형 설계 및 제조 LIGHTING & ILLUMINATION SYSTEMS를 제공할 수 있습니다. 광학 설계, 최적화 및 시뮬레이션을 위한 ZEMAX 및 CODE V와 같은 소프트웨어 도구와 조명 및 조명 시스템의 조명, 광도, 밀도, 색도 출력 등을 테스트하는 펌웨어가 있습니다. 보다 구체적으로 다음을 제공합니다. • 조명 및 조명 기구, 어셈블리, 시스템, 저전력 에너지 절약형 LED 또는 형광등 기반 조명 어셈블리를 광학 사양, 요구 사항 및 요구 사항에 따라 제공합니다. • 선박, 보트, 화학 공장, 잠수함 등 가혹한 환경을 위한 특수 응용 조명 및 조명 시스템. 황동 및 청동과 같은 내염성 재료로 만들어진 인클로저 및 특수 커넥터 포함. • 광섬유, 광섬유 다발 또는 도파관 장치를 기반으로 하는 조명 및 조명 시스템. • 가시광선 및 UV 또는 IR과 같은 기타 스펙트럼 영역에서 작동하는 조명 및 조명 시스템. 조명 및 조명 시스템과 관련된 일부 브로셔는 아래 링크에서 다운로드할 수 있습니다. LED 다이 및 칩 카탈로그 다운로드 LED 조명 카탈로그 다운로드 Relight 모델 LED 조명 브로셔 표시등 및 경고등 카탈로그 다운로드 UL 및 CE 및 IP65 인증 ND16100111-1150582가 포함된 추가 표시등 브로셔 다운로드 LED 디스플레이 패널용 브로셔 다운로드 브로셔 다운로드 디자인 파트너십 프로그램 조명 및 조명 시스템을 포함한 광학 시스템 설계를 위해 ZEMAX 및 CODE V와 같은 소프트웨어 프로그램을 사용합니다. 우리는 일련의 계단식 광학 구성 요소와 그 결과 조명 분포, 빔 각도 등을 시뮬레이션할 수 있는 전문 지식을 보유하고 있습니다. 귀하의 애플리케이션이 자동차 조명 또는 건물 조명과 같은 자유 공간 광학인지 여부; 또는 도파관, 광섬유 ....등과 같은 유도 광학 장치, 우리는 조명 밀도 분포를 최적화하고 에너지를 절약하고 원하는 스펙트럼 출력, 확산 조명 특성 등을 얻기 위한 광학 설계 전문 지식을 보유하고 있습니다. 우리는 오토바이 헤드램프, 미등, 가시 파장 프리즘 및 액체 레벨 센서용 렌즈 어셈블리와 같은 제품을 설계 및 제조했습니다....등. 고객의 필요와 예산에 따라 기성 부품으로 조명 및 조명 시스템을 설계 및 조립할 수 있을 뿐만 아니라 맞춤 설계 및 제조할 수 있습니다. 에너지 위기가 심화됨에 따라 가정과 기업은 일상 생활에서 에너지 절약 전략과 제품을 구현하기 시작했습니다. 조명은 에너지 소비를 획기적으로 줄일 수 있는 주요 분야 중 하나입니다. 우리가 알고 있듯이, 전통적인 필라멘트 기반 전구는 많은 에너지를 소비합니다. 형광등은 훨씬 적은 양의 조명을 소비하고 LED(Light Emitting Diodes)는 훨씬 적은 양의 조명을 소비하여 동일한 양의 조명을 제공하기 위해 소비하는 에너지를 기존 전구의 약 15%에 불과합니다. 이것은 LED가 일부만 소비한다는 것을 의미합니다! SMD 유형의 LED는 또한 매우 경제적이고 안정적이며 개선된 현대적인 외관으로 조립될 수 있습니다. 특수 디자인 조명 및 조명 시스템에 원하는 수량의 LED 칩을 부착할 수 있으며 유리 하우징, 패널 및 기타 구성 요소를 맞춤 제작할 수 있습니다. 에너지 절약 외에도 조명 시스템의 미학이 중요한 역할을 할 수 있습니다. 일부 응용 분야에서는 장비를 부식시키고 시간이 지남에 따라 오작동 또는 미적 외관을 초래할 수 있는 염분 물방울에 의해 부정적인 영향을 받는 보트 및 선박의 경우와 같이 조명 시스템의 부식 및 손상을 최소화하거나 방지하기 위해 특수 재료가 필요합니다. 따라서 스포트라이트 시스템, 비상 조명 시스템, 자동차 조명 시스템, 장식용 또는 건축용 조명 시스템, 생물 연구소용 조명 및 조명 기기를 개발 중이든 상관없이 당사에 연락하여 의견을 구하십시오. 우리는 귀하의 프로젝트를 향상시키고 기능, 미학, 신뢰성을 추가하고 비용을 절감할 수 있는 것을 제공할 수 있습니다. 엔지니어링 및 연구 개발 기능에 대한 자세한 내용은 엔지니어링 사이트 에서 확인할 수 있습니다.http://www.ags-engineering.com CLICK Product Finder-Locator Service 이전 페이지
- Adhesive Bonding - Adhesives - Sealing - Fastening - Joining
Adhesive Bonding - Adhesives - Sealing - Fastening - Joining Nonmetallic Materials - Optical Contacting - UV Bonding - Specialty Glue - Epoxy - Custom Assembly 접착제 본딩 및 씰링 및 맞춤형 기계적 고정 및 조립 당사의 다른 가장 가치 있는 결합 기술 중에는 접착 결합, 기계적 고정 및 조립, 비금속 재료 결합이 있습니다. 우리는 제조 작업에서의 중요성과 이와 관련된 광범위한 내용 때문에 이러한 결합 및 조립 기술에 대해 이 섹션을 할애합니다. ADHESIVE BONDING: 거의 밀폐 수준의 밀봉에 사용할 수 있는 특수 에폭시가 있다는 것을 알고 계셨습니까? 필요한 밀봉 수준에 따라 밀봉 제를 선택하거나 공식화합니다. 또한 일부 실런트는 열 경화가 가능한 반면 다른 실런트는 UV 광선만 경화하면 된다는 사실을 알고 계십니까? 귀하의 응용 분야를 설명하면 귀하에게 적합한 에폭시를 공식화할 수 있습니다. 기포가 없거나 짝을 이루는 부품의 열팽창 계수와 일치하는 것이 필요할 수 있습니다. 우리는 모든 것을 가지고 있습니다! 저희에게 연락하여 귀하의 응용 프로그램을 설명하십시오. 그런 다음 귀하에게 가장 적합한 재료를 선택하거나 귀하의 과제에 대한 솔루션을 맞춤형으로 공식화할 것입니다. 당사의 재료는 검사 보고서, 재료 데이터 시트 및 인증과 함께 제공됩니다. 우리는 매우 경제적으로 구성 요소를 조립하고 완성된 품질 검사 제품을 배송할 수 있습니다. 접착제는 액체, 용액, 페이스트, 유제, 분말, 테이프 및 필름과 같은 다양한 형태로 제공됩니다. 당사는 접합 공정에 세 가지 기본 유형의 접착제를 사용합니다. -천연 접착제 -무기 접착제 -합성유기접착제 제조 및 제조의 하중 지지 응용을 위해 우리는 높은 응집력을 가진 접착제를 사용하며 대부분 합성 유기 접착제이며 열가소성 또는 열경화성 폴리머일 수 있습니다. 합성 유기 접착제는 가장 중요한 범주이며 다음과 같이 분류할 수 있습니다. 화학적 반응성 접착제: 인기 있는 예로는 실리콘, 폴리우레탄, 에폭시, 페놀, 폴리이미드, 록타이트와 같은 혐기성 물질이 있습니다. 감압 접착제: 일반적인 예로는 천연 고무, 니트릴 고무, 폴리아크릴레이트, 부틸 고무가 있습니다. 핫멜트 접착제: 예로는 에틸렌-비닐-아세테이트 공중합체, 폴리아미드, 폴리에스테르, 폴리올레핀과 같은 열가소성 수지가 있습니다. 반응성 핫멜트 접착제: 우레탄 화학을 기반으로 하는 열경화성 부분이 있습니다. 증발/확산 접착제: 인기 있는 것은 비닐, 아크릴, 페놀, 폴리우레탄, 합성 및 천연 고무입니다. 필름 및 테이프 유형 접착제: 나일론 에폭시, 엘라스토머 에폭시, 니트릴 페놀, 폴리이미드가 그 예입니다. 지연 점착제: 여기에는 폴리비닐 아세테이트, 폴리스티렌, 폴리아미드가 포함됩니다. 전기 및 열 전도성 접착제: 인기 있는 예로는 에폭시, 폴리우레탄, 실리콘, 폴리이미드가 있습니다. 화학 물질에 따라 우리가 제조에 사용하는 접착제는 다음과 같이 분류할 수 있습니다. - Epoxy 기반 접착 시스템: 고강도 및 473Kelvin의 고온 내구성이 특징입니다. 샌드 몰드 주조의 접합제가 이 유형입니다. - 아크릴: 오염된 더러운 표면과 관련된 응용 분야에 적합합니다. - 혐기성 접착제 시스템: 산소 결핍에 의한 경화. 단단하고 부서지기 쉬운 결합. - 시아노아크릴레이트: 경화 시간이 1분 미만인 얇은 본드 라인. - 우레탄 : 인성과 유연성이 우수한 실런트로 널리 사용됩니다. - 실리콘: 습기 및 용제에 대한 내성, 높은 충격 및 박리 강도로 잘 알려져 있습니다. 최대 며칠의 비교적 긴 경화 시간. 접착제 결합의 특성을 최적화하기 위해 여러 접착제를 결합할 수 있습니다. 예는 에폭시-실리콘, 니트릴-페놀 결합 접착제 시스템입니다. 폴리이미드 및 폴리벤즈이미다졸은 고온 응용 분야에 사용됩니다. 접착 조인트는 전단력, 압축력 및 인장력을 잘 견디지만 박리력이 가해지면 쉽게 파손될 수 있습니다. 따라서 접착 접합에서는 응용 분야를 고려하고 그에 따라 접합부를 설계해야 합니다. 표면 준비는 또한 접착 결합에서 매우 중요합니다. 우리는 접착 결합에서 계면의 강도와 신뢰성을 높이기 위해 표면을 청소, 처리 및 수정합니다. 특수 프라이머를 사용하는 플라즈마 세척과 같은 습식 및 건식 에칭 기술이 당사의 일반적인 방법 중 하나입니다. 얇은 산화물과 같은 접착 촉진층은 일부 응용 분야에서 접착력을 향상시킬 수 있습니다. 표면 거칠기를 증가시키는 것도 접착 결합 전에 유리할 수 있지만 과도한 거칠기는 공기를 가두어 접착 결합 계면이 더 약해질 수 있기 때문에 잘 제어되고 과장되지 않아야 합니다. 우리는 접착 결합 작업 후 제품의 품질과 강도를 테스트하기 위해 비파괴적인 방법을 사용합니다. 우리의 기술에는 음향 충격, IR 감지, 초음파 테스트와 같은 방법이 포함됩니다. 접착 결합의 장점은 다음과 같습니다. - 접착 본딩은 구조적 강도, 밀봉 및 절연 기능, 진동 및 소음 억제를 제공할 수 있습니다. -접착 접합은 패스너 또는 용접을 사용한 접합의 필요성을 제거하여 계면에서 국부적인 응력을 제거할 수 있습니다. - 일반적으로 접착제 접착을 위한 구멍이 필요하지 않으므로 부품의 외관에 영향을 미치지 않습니다. - 얇고 깨지기 쉬운 부품을 손상 없이 접착할 수 있으며 무게를 크게 증가시키지 않습니다. -접착 접합은 크기가 상당히 다른 매우 다른 재료로 만들어진 부품을 접합하는 데 사용할 수 있습니다. - 열에 민감한 부품은 낮은 온도로 안전하게 접착이 가능합니다. 그러나 접착 결합에는 몇 가지 단점이 있으므로 고객은 조인트 설계를 마무리하기 전에 다음을 고려해야 합니다. -접착식 조인트 구성 요소의 서비스 온도는 상대적으로 낮습니다. -접착 접합은 접합 및 경화 시간이 오래 걸릴 수 있습니다. -접착접착시 표면처리가 필요합니다. - 특히 대형 구조물의 경우 접착식으로 접합된 조인트를 비파괴적으로 테스트하는 것이 어려울 수 있습니다. - 접착 본딩은 열화, 응력 부식, 용해 등으로 인해 장기적으로 신뢰성 문제를 제기할 수 있습니다. 당사의 뛰어난 제품 중 하나는 납 기반 솔더를 대체할 수 있는 전기 전도성 접착제입니다. 은, 알루미늄, 구리, 금과 같은 충전제는 이러한 페이스트를 전도성으로 만듭니다. 충전제는 은 또는 금의 박막으로 코팅된 플레이크, 입자 또는 중합체 입자의 형태일 수 있습니다. 충전제는 전기 외에도 열전도율을 향상시킬 수 있습니다. 제품 제조에 사용되는 다른 접합 프로세스를 계속 진행하겠습니다. 기계적 고정 및 조립: 기계적 고정은 제조 용이성, 조립 및 분해 용이성, 운송 용이성, 부품 교체, 유지 보수 및 수리 용이성, 이동 및 조정 가능한 제품의 설계 용이성, 저렴한 비용을 제공합니다. 고정을 위해 다음을 사용합니다. 나사식 패스너: 볼트, 나사 및 너트가 그 예입니다. 응용 분야에 따라 진동을 완화하기 위해 특별히 설계된 너트와 잠금 와셔를 제공할 수 있습니다. 리벳팅: 리벳은 영구적인 기계적 결합 및 조립 공정의 가장 일반적인 방법 중 하나입니다. 리벳이 구멍에 삽입되고 그 끝이 업셋에 의해 변형됩니다. 상온은 물론 고온에서도 리벳팅으로 조립을 합니다. 스티칭/스테이플링/클린칭: 이러한 조립 작업은 제조에 널리 사용되며 기본적으로 종이 및 판지에 사용되는 것과 동일합니다. 금속 및 비금속 재료 모두 구멍을 미리 뚫을 필요 없이 신속하게 결합 및 조립할 수 있습니다. 시밍(Seaming): 용기 및 금속 캔 제조에 널리 사용되는 저렴하고 빠른 접합 기술입니다. 두 개의 얇은 재료를 함께 접는 것을 기반으로 합니다. 특히 밀봉재 및 접착제를 사용하여 접합을 수행하는 경우 기밀 및 수밀 접합이 가능합니다. 압착: 압착은 패스너를 사용하지 않는 접합 방법입니다. 전기 또는 광섬유 커넥터는 때때로 크림핑을 사용하여 설치됩니다. 대량 생산에서 크림핑은 평면 및 관형 구성 요소를 빠르게 결합하고 조립하는 데 없어서는 안될 기술입니다. 스냅인 패스너: 스냅 핏은 조립 및 제조 시 경제적인 결합 기술이기도 합니다. 구성 요소를 빠르게 조립 및 분해할 수 있으며 가정용품, 장난감, 가구 등에 적합합니다. 수축 및 압입: 또 다른 기계적 조립 기술, 즉 수축 연결은 두 구성요소의 차등 열 팽창 및 수축 원리를 기반으로 하는 반면 압입에서는 한 구성요소가 다른 구성요소 위로 힘을 가하여 접합 강도가 우수합니다. 우리는 케이블 하네스의 조립 및 제조, 샤프트에 기어 및 캠 장착에 열박음 장치를 널리 사용합니다. 비금속 재료 결합: 열가소성 플라스틱은 접합할 계면에서 가열 및 용융될 수 있으며 압력 접착제를 적용하여 융합을 통해 접합할 수 있습니다. 대안적으로, 동일한 유형의 열가소성 충전제가 접합 공정에 사용될 수 있다. 폴리에틸렌과 같은 일부 폴리머의 접합은 산화로 인해 어려울 수 있습니다. 이러한 경우 산화에 대해 질소와 같은 불활성 차폐 가스를 사용할 수 있습니다. 외부 열원과 내부 열원 모두 폴리머의 접착 접합에 사용할 수 있습니다. 열가소성 수지의 접착 접합에 일반적으로 사용하는 외부 소스의 예로는 뜨거운 공기 또는 가스, IR 복사, 가열 도구, 레이저, 저항성 전기 가열 요소가 있습니다. 내부 열원 중 일부는 초음파 용접 및 마찰 용접입니다. 일부 조립 및 제조 응용 분야에서는 폴리머를 접착하기 위해 접착제를 사용합니다. PTFE(테프론) 또는 PE(폴리에틸렌)와 같은 일부 폴리머는 표면 에너지가 낮기 때문에 적절한 접착제로 접착 접합 공정을 완료하기 전에 프라이머를 먼저 도포합니다. 접합에서 또 다른 인기 있는 기술은 토너가 폴리머 계면에 먼저 적용되는 "Clearweld Process"입니다. 그런 다음 레이저가 계면을 향하지만 폴리머를 가열하지 않고 토너를 가열합니다. 이를 통해 잘 정의된 인터페이스만 가열하여 국부적인 용접을 수행할 수 있습니다. 열가소성 수지 조립의 다른 대체 접합 기술은 패스너, 셀프 태핑 나사, 통합 스냅 패스너를 사용하는 것입니다. 제조 및 조립 작업의 이국적인 기술은 폴리머에 작은 마이크론 크기의 입자를 삽입하고 고주파 전자기장을 사용하여 접합할 계면에서 유도 가열 및 용융시키는 것입니다. 반면 열경화성 물질은 온도가 올라가도 부드러워지거나 녹지 않습니다. 따라서 열경화성 플라스틱의 접착 접합은 일반적으로 나사산 또는 기타 성형 인서트, 기계적 패스너 및 용제 접합을 사용하여 수행됩니다. 당사 제조 공장의 유리 및 세라믹과 관련된 결합 및 조립 작업과 관련하여 다음과 같은 몇 가지 일반적인 관찰 사항이 있습니다. 세라믹 또는 유리를 접착하기 어려운 재료와 결합해야 하는 경우 세라믹 또는 유리 재료는 종종 자기 자신을 쉽게 접착시킨 다음 접착하기 어려운 물질에 결합하는 금속입니다. 세라믹이나 유리에 얇은 금속 코팅이 있으면 금속에 더 쉽게 납땜될 수 있습니다. 도자기는 때때로 뜨겁고 부드럽고 끈적 거리면서 성형 과정에서 함께 결합되고 조립됩니다. 탄화물은 코발트 또는 니켈-몰리브덴 합금과 같은 금속 바인더를 매트릭스 재료로 사용하는 경우 금속에 더 쉽게 납땜될 수 있습니다. 우리는 초경 절삭 공구를 강철 공구 홀더에 납땜합니다. 안경은 뜨겁고 부드러울 때 서로와 금속에 잘 접착됩니다. 세라믹-금속 피팅, 밀폐 밀봉, 진공 피드스루, 고진공 및 초고진공 및 유체 제어 구성 요소를 생산하는 당사 시설에 대한 정보는 여기에서 확인할 수 있습니다.브레이징 공장 브로셔 CLICK Product Finder-Locator Service 이전 페이지
- Clutch, Brake, Friction Clutches, Belt Clutch, Dog & Hydraulic Clutch
Clutch, Brake, Friction Clutches, Belt Clutch, Dog Clutch, Hydraulic Clutch, Electromagnetic Clutch, Overruning Clutch, Wrap Spring Clutch, Frictional Brake 클러치 및 브레이크 어셈블리 CLUTCHES are 샤프트를 원하는 대로 연결하거나 분리할 수 있는 커플 링 유형입니다. A CLUTCH 는 동력과 운동을 한 구성 요소(구동 부재)에서 다른 구성 요소(구동 부재)로 전달하는 기계 장치입니다. 클러치는 동력 또는 모션의 전달을 양적으로 또는 시간이 지남에 따라 제어해야 할 때마다 사용됩니다(예: 전기 드라이버는 클러치를 사용하여 전달되는 토크의 양을 제한하고 자동차 클러치는 바퀴에 전달되는 엔진 동력을 제어합니다). 가장 단순한 응용 분야에서 클러치는 두 개의 회전 샤프트(구동 샤프트 또는 라인 샤프트)가 있는 장치에 사용됩니다. 이러한 장치에서 하나의 샤프트는 일반적으로 모터 또는 다른 유형의 동력 장치(구동 부재)에 부착되고 다른 샤프트(구동 부재)는 수행할 작업에 대한 출력을 제공합니다. 예를 들어, 토크 제어 드릴에서 하나의 샤프트는 모터로 구동되고 다른 샤프트는 드릴 척을 구동합니다. 클러치는 두 샤프트를 연결하여 함께 잠기고 같은 속도로 회전(결합), 함께 잠겨 있지만 다른 속도로 회전(미끄럼) 또는 잠금 해제되어 다른 속도로 회전(해제)될 수 있습니다. 다음 유형의 클러치를 제공합니다. 마찰 클러치: - 다중 플레이트 클러치 - 습식 및 건식 - 원심 - 콘 클러치 - 토크 리미터 벨트 클러치 도그 클러치 유압 클러치 전자기 클러치 오버런닝 클러치(프리휠) 랩 스프링 클러치 오토바이, 자동차, 트럭, 트레일러, 잔디 깎기, 산업 기계 등의 제조 라인에서 사용할 클러치 어셈블리에 대해서는 당사에 문의하십시오. 브레이크: A BRAKE 는 움직임을 억제하는 기계 장치입니다. 가장 일반적으로 브레이크는 마찰을 사용하여 운동 에너지를 열로 변환하지만 다른 에너지 변환 방법도 사용할 수 있습니다. 회생 제동은 많은 에너지를 전기 에너지로 변환하고 나중에 사용하기 위해 배터리에 저장할 수 있습니다. 와전류 브레이크는 자기장을 사용하여 브레이크 디스크, 핀 또는 레일의 운동 에너지를 전류로 변환한 후 열로 변환합니다. 브레이크 시스템의 다른 방법은 압축 공기 또는 압축 오일과 같은 저장된 형태로 운동 에너지를 위치 에너지로 변환합니다. 회전하는 플라이휠에 에너지를 전달하는 것과 같이 운동 에너지를 다양한 형태로 변환하는 제동 방법이 있습니다. 당사가 제공하는 일반 유형의 브레이크는 다음과 같습니다. 마찰 브레이크 펌핑 브레이크 전자기 브레이크 당사는 귀하의 애플리케이션에 맞는 맞춤형 클러치 및 브레이크 시스템을 설계하고 제작할 수 있는 능력을 보유하고 있습니다. - 여기를 클릭하여 파우더 클러치 및 브레이크 및 장력 제어 시스템에 대한 카탈로그를 다운로드하십시오. - 여기를 클릭하여 Non-Excited Brake 카탈로그를 다운로드하십시오. 카탈로그를 다운로드하려면 아래 링크를 클릭하십시오. - 에어 디스크 및 에어 샤프트 브레이크 및 클러치 및 안전 디스크 스프링 브레이크 - 1~35페이지 - 에어 디스크 및 에어 샤프트 브레이크 및 클러치 및 안전 디스크 스프링 브레이크 - 36~71페이지 - 에어 디스크 및 에어 샤프트 브레이크 및 클러치 및 안전 디스크 스프링 브레이크 - 72~86페이지 - 전자기 클러치 및 브레이크 CLICK Product Finder-Locator Service 이전 페이지
- PCB, PCBA, Printed Circuit Board Assembly, Surface Mount Assembly, SMA
PCB - PCBA - Printed Circuit Board Assembly - Rigid Flexible Multilayer - Surface Mount Assembly - SMA - AGS-TECH Inc. PCB 및 PCBA 제조 및 조립 우리는 제공한다: PCB: 인쇄 회로 기판 PCBA: 인쇄 회로 기판 어셈블리 • 모든 유형의 인쇄 회로 기판 어셈블리(PCB, 경질, 연성 및 다층) • 필요에 따라 기판 또는 전체 PCBA 어셈블리. • 스루홀 및 표면 실장 어셈블리(SMA) Gerber 파일, BOM, 구성 요소 사양을 보내주십시오. 지정된 정확한 구성 요소를 사용하여 PCB 및 PCBA를 조립하거나 일치하는 대안을 제공할 수 있습니다. 우리는 PCB 및 PCBA를 배송한 경험이 있으며 정전기 손상을 방지하기 위해 정전기 방지 백에 포장해야 합니다. 극한 환경을 위한 PCB에는 종종 부품이 납땜된 후 침지 또는 스프레이로 적용되는 등각 코팅이 있습니다. 코팅은 부식 및 누설 전류 또는 결로로 인한 단락을 방지합니다. 당사의 등각 코팅은 일반적으로 실리콘 고무, 폴리우레탄, 아크릴 또는 에폭시의 희석 용액에 담근 것입니다. 일부는 진공 챔버에서 PCB에 스퍼터링된 엔지니어링 플라스틱입니다. 안전 표준 UL 796은 장치 또는 기기의 구성 요소로 사용하기 위한 인쇄 배선판에 대한 구성 요소 안전 요구 사항을 다룹니다. 당사의 테스트는 가연성, 최대 작동 온도, 전기 추적, 열 변형 및 전기가 흐르는 전기 부품의 직접 지원과 같은 특성을 분석합니다. PCB 보드는 단층 또는 다층, 강성 또는 유연한 형태의 유기 또는 무기 기본 재료를 사용할 수 있습니다. 회로 구성에는 에칭, 다이 스탬핑, 프리컷, 플러시 프레스, 첨가제 및 도금 도체 기술이 포함될 수 있습니다. 인쇄된 부품을 사용할 수 있습니다. 패턴 매개변수의 적합성, 온도 및 최대 솔더 한계는 적용 가능한 최종 제품 구성 및 요구 사항에 따라 결정되어야 합니다. 기다리지 말고 자세한 정보, 설계 지원, 프로토타입 및 대량 생산에 대해 문의하십시오. 필요한 경우 라벨링, 포장, 배송, 수입 및 통관, 보관 및 배송을 모두 처리해 드립니다. 아래에서 PCB 및 PCBA 어셈블리에 대한 관련 브로셔 및 카탈로그를 다운로드할 수 있습니다. 경질 PCB 제조를 위한 일반 공정 기능 및 허용 오차 알루미늄 PCB 제조를 위한 일반 공정 기능 및 허용 오차 Flexible 및 Rigid-Flexible PCB 제조를 위한 일반 프로세스 기능 및 허용오차 일반 PCB 제조 공정 인쇄 회로 기판 어셈블리 PCBA 제조의 일반 공정 요약 인쇄 회로 기판 제조 공장 개요 PCB 및 PCBA 조립 프로젝트에서 사용할 수 있는 당사 제품에 대한 추가 브로셔: 퀵 핏 단자, USB 플러그 및 소켓, 마이크로 핀 및 잭 등과 같은 기성 상호 연결 구성 요소 및 하드웨어에 대한 카탈로그를 다운로드하려면 여기를 클릭하십시오. 단자대 및 커넥터 터미널 블록 일반 카탈로그 표준 방열판 압출 방열판 Easy Click 방열판은 PCB 어셈블리를 위한 완벽한 제품입니다. 중간 - 고전력 전자 시스템용 슈퍼 파워 방열판 슈퍼 핀이 있는 방열판 LCD 모듈 리셉터클-전원 엔트리-커넥터 카탈로그 브로셔 다운로드 디자인 파트너십 프로그램 제조 작업 및 기능 대신 당사의 엔지니어링 및 연구 및 개발 기능에 관심이 있으시면 엔지니어링 사이트 를 방문하시기 바랍니다.http://www.ags-engineering.com CLICK Product Finder-Locator Service 이전 페이지
- Fiber Optic Components, Splicing Enclosures, FTTH Node, CATV Products
Fiber Optic Components - Splicing Enclosures - FTTH Node - Fiber Distribution Box - Optical Platform - CATV Products - Telecommunication Optics - AGS-TECH Inc. 광섬유 제품 우리는 다음을 제공합니다: • 광섬유 커넥터, 어댑터, 터미네이터, 피그테일, 패치코드, 커넥터 전면판, 선반, 통신 랙, 광섬유 분배 상자, 접합 인클로저, FTTH 노드, 광 플랫폼, 광섬유 탭, 스플리터-결합기, 고정 및 가변 광 감쇠기, 광 스위치 , DWDM, MUX/DEMUX, EDFA, 라만 증폭기 및 기타 증폭기, 절연체, 순환기, 이득 평탄화기, 통신 시스템용 맞춤형 광섬유 어셈블리, 광 도파관 장치, CATV 제품 • 레이저 및 광검출기, PSD(Position Sensitive Detectors), 쿼드셀 • 산업 적용을 위한 광섬유 어셈블리(파이프 내부, 틈새, 공동, 본체 내부의 조명, 광 전달 또는 검사....). • 의료용 광섬유 어셈블리(site 참조)http://www.agsmedical.com 의료용 내시경 및 커플러용). 당사 엔지니어들이 개발한 제품 중에는 직경 0.6mm의 초슬림형 플렉시블 비디오 내시경과 광섬유 종단 검사 간섭계가 있습니다. 간섭계는 광섬유 커넥터 제조의 공정 및 최종 검사를 위해 엔지니어가 개발했습니다. 우리는 견고하고 신뢰할 수 있으며 수명이 긴 조립품을 위해 특수 접합 및 부착 기술과 재료를 사용합니다. 고온/저온과 같은 광범위한 환경 사이클에서도; 높은 습도/낮은 습도 우리의 어셈블리는 손상되지 않고 계속 작동합니다. 수동 광섬유 구성 요소에 대한 카탈로그 다운로드 활성 광섬유 제품에 대한 카탈로그 다운로드 여유 공간 광학 부품 및 어셈블리에 대한 카탈로그 다운로드 CLICK Product Finder-Locator Service 이전 페이지
- Tanks and Containers, USA, AGS-TECH Inc.
AGS-TECH offers off-shelf and custom manufactured tanks and containers of various sizes. We supply wire mesh cage containers, stainless, aluminum and metal tanks and containers, IBC tanks, plastic and polymer containers, fiberglass tanks, collapsible tanks. 탱크 및 컨테이너 우리는 불활성 폴리머, 스테인리스 스틸 등으로 만든 화학 물질, 분말, 액체 및 가스 저장 용기와 탱크를 공급합니다. 우리는 접을 수 있는 롤링 컨테이너, 쌓을 수 있는 컨테이너, 접을 수 있는 컨테이너, 건설, 식품, 제약, 화학, 석유화학 등과 같은 많은 산업 분야에서 응용 프로그램을 찾는 기타 유용한 기능을 가진 컨테이너를 보유하고 있습니다. 응용 프로그램에 대해 알려주십시오. 가장 적합한 용기를 추천해 드리겠습니다. 대용량 스테인리스 스틸 또는 기타 재료 용기는 주문 및 귀하의 사양에 따라 맞춤 제작됩니다. 더 작은 용기는 일반적으로 기성품으로 제공되며 수량에 합당한 경우 맞춤 제작할 수도 있습니다. 양이 많은 경우 귀하의 사양에 따라 플라스틱 용기 및 탱크를 불거나 회전시킬 수 있습니다. 탱크 및 컨테이너의 주요 유형은 다음과 같습니다. 와이어 메쉬 케이지 컨테이너 우리는 다양한 와이어 메쉬 케이지 컨테이너를 재고로 보유하고 있으며 귀하의 사양과 요구 사항에 따라 맞춤 제작할 수도 있습니다. 당사의 와이어 메쉬 케이지 컨테이너에는 다음과 같은 제품이 포함됩니다. 쌓을 수 있는 케이지 팔레트 접이식 철망 롤 컨테이너 접이식 철망 용기 우리의 모든 철망 케이지 컨테이너는 최고 품질의 스테인리스 또는 연강 재료로 만들어지며 비스테인리스 버전 일반적으로 _cc781905-5cde-3194-bb3b-136bad5cf58d를 사용하여 부식 및 부식 방지 코팅되어 있습니다. 3194-bb3b-136bad5cf58d_hot dip or powder 코팅. 마감 색상은 일반적으로 zinc: 흰색 또는 노란색입니다. 또는 귀하의 요청에 따라 분말 코팅. 우리의 철망 케이지 컨테이너 는 엄격한 품질 관리 절차에 따라 조립되고 기계적 충격, 중량 운반 능력, 내구성, 강도 및 장기 신뢰성에 대해 테스트되었습니다. 우리의 철망 케이지 컨테이너는 국제 품질 표준은 물론 미국 및 국제 운송 산업 표준을 준수합니다. 철망 케이지 컨테이너는 일반적으로 보관 상자 및 쓰레기통, 보관 카트, 운송 카트 등으로 사용됩니다. 철망 케이지 컨테이너를 선택할 때 적재 용량, 컨테이너 자체의 무게, 그리드의 치수, 외부 및 내부 치수, 공간 절약형 운송 및 보관을 위해 평평하게 접히는 컨테이너가 필요한지 여부와 같은 중요한 매개변수를 고려하십시오. 20피트 또는 40피트 선적 컨테이너에 몇 개의 특정 컨테이너를 실을 수 있는지도 고려하십시오. 결론은 와이어 메쉬 케이지 컨테이너가 일회용 포장에 대한 오래 지속되고 경제적이며 환경 친화적인 대안이라는 것입니다. 아래는 와이어 메쉬 컨테이너 제품의 다운로드 가능한 브로셔입니다. - Wire Mesh Container Quote Design Form (다운로드하려면 클릭하여 작성하고 이메일을 보내주십시오) 스테인리스 및 금속 탱크 및 용기 당사의 스테인리스 및 기타 금속 탱크 및 용기는 크림과 액체를 저장하는 데 이상적입니다. 그들은 cosmetics, 제약 및 식품 및 음료 산업 및 기타 산업에 이상적입니다. 그들은 유럽, 미국 및 국제 지침을 준수합니다. 우리의 스테인리스 및 금속 탱크는 easy_cc781905-5cde-3194-bb3b-5cd15cde-3194-bb3b-5ccd156bad5cf58d_to_cc781905-5cde 136bad5cf58d_이 컨테이너는 안정적인 기반을 가지고 있으며 보관 영역 없이 살균할 수 있습니다 . 스테인리스 및 금속 탱크 및 용기 와 같은 모든 유형의 액세서리(예: 세척 헤드 통합 integration)를 장착할 수 있습니다. 우리의 용기는 압력을 가할 수 있습니다. 공장과 작업장에 쉽게 적용할 수 있습니다. 컨테이너의 작동 압력은 다양하므로 요구 사항과 사양을 비교하십시오. 당사의 알루미늄 용기와 탱크도 업계에서 매우 인기가 있습니다. 일부 모델은 바퀴가 달린 이동식이고 다른 모델은 쌓을 수 있습니다. 우리는 위험 제품 운송에 대해 승인된 분말, 과립 및 알약 저장 탱크가 있습니다. UN 및 사양. 스테인레스 및 금속 탱크 및 용기의 내부 및 외부 치수, 벽 두께는 귀하의 요구 사항에 따라 달라질 수 있습니다. 스테인리스 및 알루미늄 탱크 및 컨테이너 쌓을 수 있는 탱크 및 컨테이너 바퀴 달린 탱크 및 컨테이너 IBC & GRV 탱크 분말, 과립 및 펠렛 저장 탱크 맞춤형 설계 및 제작 탱크 및 컨테이너 아래 링크를 클릭하여 Stainless 및 금속 탱크 및 컨테이너에 대한 브로셔를 다운로드하십시오. IBC 탱크 및 컨테이너 플라스틱 및 폴리머 탱크 및 컨테이너 AGS-TECH는 다양한 플라스틱 및 폴리머 소재의 탱크 및 컨테이너를 공급합니다. 귀하의 요청과 함께 당사에 연락하고 가장 적절한 제품을 인용할 수 있도록 다음을 지정하는 것이 좋습니다. - 신청 - 재료 등급 - 치수 - 마치다 - 포장 요구 사항 - 수량 예를 들어 FDA 승인 식품 등급 플라스틱 재료는 음료, 곡물, 과일 주스 등을 보관하는 일부 용기에 중요합니다. 반면에 화학 물질이나 의약품을 저장하기 위해 플라스틱 및 폴리머 탱크 및 용기가 필요한 경우 내용물에 대한 플라스틱 재료의 불활성이 가장 중요합니다. 재료에 대한 의견은 당사에 문의하십시오. 또한 브로셔 below에서 기성품 플라스틱 및 폴리머 탱크 및 용기를 주문할 수 있습니다. 플라스틱 및 폴리머 탱크 및 컨테이너에 대한 브로셔를 다운로드하려면 아래 링크를 클릭하십시오. IBC 탱크 및 컨테이너 유리 섬유 탱크 및 컨테이너 우리는 유리 섬유 materials로 만든 탱크 및 용기를 제공합니다. 우리의 탱크 유리 섬유 탱크 및 컨테이너 meet US 및 국제적 저장 기준_cc781905-5cde-3194-bb 유리 섬유 탱크 및 용기 ASTM 4097을 준수하는 접촉 성형 라미네이트 및 ASTM 3299를 준수하는 필라멘트 기반 권선 라미네이트로 제작됩니다. 저장되는 제품의 농도, 온도 및 부식 거동에 관한 것입니다. FDA 승인 및 난연성 수지를 특수 용도로 사용할 수 있습니다. 가장 적합한 유리 섬유 탱크 및 용기를 인용할 수 있도록 귀하의 요청과 함께 당사에 연락하고 다음을 지정하는 것이 좋습니다. - 신청 - 재료 기대치 및 사양 - 치수 - 마치다 - 포장 요구 사항 - 수량 필요 우리는 기꺼이 당신에게 우리의 의견을 줄 것입니다. 또한 당사 브로셔 below에서 기성품 유리 섬유 tanks 및 용기를 주문할 수 있습니다. 당사의 기성품 포트폴리오에 있는 유리 섬유 탱크 및 용기 중 어느 것도 만족하지 못하는 경우 저희에게 알려주십시오. 그러면 귀하의 필요에 따라 맞춤형 제조를 고려할 수 있습니다. 접을 수 있는 탱크 및 컨테이너 접을 수 있는 물 탱크 및 컨테이너는 당신의 최선의 선택은 플라스틱 배럴 및 기타 컨테이너가 너무 작거나 비실용적입니다. 또한 콘크리트 또는 금속 탱크를 구축하지 않고 신속하게 많은 양의 물 또는 액체가 필요할 때 당사의 접이식 탱크 및 컨테이너가 이상적입니다. 이름에서 알 수 있듯이 접을 수 있는 탱크 및 컨테이너는 접을 수 있습니다. 즉, 사용 후 축소하고 롤링할 수 있으며 매우 컴팩트하고 부피가 작아서 비었을 때 보관 및 운송이 용이합니다. 재사용이 가능합니다. 우리는 귀하의 사양에 따라 모든 크기와 모델을 제공할 수 있습니다. 접을 수 있는 탱크 및 컨테이너의 일반적인 기능: - 색상: 블루, 오렌지, 그레이, 짙은 녹색, 블랙, ..... 등. - 재질: PVC - 용량 : 일반적으로 200~30000리터 사이 - 가벼운 무게, 쉬운 조작. - 최소 포장 크기로 운송 및 보관이 용이합니다. - 오염 없음 water - 코팅된 직물의 고강도, 접착력 최대 60lb/in. - 이음매의 높은 강도는 고주파 용융 및 탱크 본체와 동일한 폴리우레탄으로 밀봉되어 있으므로 탱크는 우수한 성능을 가집니다. 물에 안전합니다. 접을 수 있는 탱크 및 컨테이너의 응용 분야: · 임시 보관 · 빗물 수집 · 주거 및 공공 물 저장 · 방위 물 저장 응용 프로그램 · 물 처리 · 비상 보관 및 구호 · 관개 · 건설 회사는 교량 최대 하중을 테스트하기 위해 PVC 물 탱크를 선택합니다 · 소방 우리는 또한 OEM 주문을 받아들입니다. 맞춤형 라벨링, 포장 및 로고 인쇄가 가능합니다. 이전 페이지
- Computer Chassis, Racks, Shelves, 19 inch Rack, 23 inch Rack, Case
Computer Chassis - Racks - Shelves - 19 inch Rack - 23 inch Rack - Computer and Instrument Case Manufacturing - AGS-TECH Inc. - New Mexico - USA 섀시, 랙, 산업용 컴퓨터용 마운트 We offer you the most durable and reliable INDUSTRIAL COMPUTER CHASSIS, RACKS, MOUNTS, RACK MOUNT INSTRUMENTS and RACK MOUNTED SYSTEMS, SUBRACK, SHELF, 19 INCH & 23 INCH RACKS, FULL SİZE and HALF RACKS, OPEN and CLOSED RACK, MOUNTING HARDWARE, STRUCTURAL AND SUPPORT COMPONENTS, RAILS and SLIDES, TWO andFOUR POST RACKS that meet international and industry standards. 기성품 외에도 특별히 맞춤화된 섀시, 랙 및 마운트를 제작할 수 있습니다. 재고가 있는 브랜드 이름 중 일부는 BELKIN, HEWLETT PACKARD, KENDALL HOWARD, GREAT LAKES, APC, RITTAL, LIEBERT, RALOY, SHARK RACKIES, UPSITE TECH입니다. DFI-ITOX 브랜드 산업용 섀시를 다운로드하려면 여기를 클릭하십시오. AGS-Electronics에서 06 시리즈 플러그인 섀시를 다운로드하려면 여기를 클릭하십시오. AGS-Electronics에서 01 시리즈 계기 케이스 System-I를 다운로드하려면 여기를 클릭하십시오. AGS-Electronics에서 05 시리즈 계기 케이스 System-V를 다운로드하려면 여기를 클릭하십시오. 적합한 산업용 등급 섀시, 랙 또는 마운트를 선택하려면 여기를 클릭하여 산업용 컴퓨터 매장으로 이동하십시오. 브로셔 다운로드 디자인 파트너십 프로그램 다음은 참조용으로 유용한 몇 가지 주요 용어입니다. A RACK UNIT or U(덜 일반적으로 RU라고 함)는 a_3b099 장착용 장비 높이를 설명하는 데 사용되는 측정 단위입니다. -136bad5cf58d_19인치 rack or a 23인치 rack_cc58190의 치수를 참조하십시오. 랙의 장착 프레임, 즉 랙 내부에 장착할 수 있는 장비의 너비). 하나의 랙 장치는 높이가 1.75인치(44.45mm)입니다. 랙 장착형 장비의 크기는 흔히 'U'로 표시됩니다. 예를 들어, 하나의 랙 장치는 종종 ''1U'', 2개의 랙 장치는 ''2U'' 등으로 지칭됩니다. 일반 전체 크기 랙 is 44U, 즉 6피트가 조금 넘는 장비를 수용합니다. 그러나 컴퓨팅 및 정보 기술에서 half-rack 는 일반적으로 높이가 1U이고 스위치 랙 깊이가 절반인 스위치 랙(예: 4 , 라우터, KVM 스위치 또는 서버), 두 개의 장치를 1U의 공간에 장착할 수 있습니다(랙 전면에 하나, 후면에 하나). 랙 엔클로저 자체를 설명하는 데 사용할 때 하프 랙이라는 용어는 일반적으로 높이가 24U인 랙 엔클로저를 의미합니다. 랙의 전면 패널 또는 필러 패널은 1.75인치(44.45mm)의 정확한 배수가 아닙니다. 인접한 랙 장착 구성 요소 사이에 공간을 허용하기 위해 패널의 높이는 전체 랙 장치 수보다 1/32인치(0.031인치 또는 0.79mm) 낮습니다. 따라서 1U 전면 패널의 높이는 1.719인치(43.66mm)입니다. 19인치 랙은 여러 장비 모듈을 장착하기 위한 표준화된 프레임 또는 인클로저입니다. 각 모듈에는 19인치(482.6mm) 너비의 전면 패널이 있으며, 여기에는 나사로 모듈을 랙 프레임에 고정할 수 있도록 양쪽에 돌출된 가장자리 또는 귀가 포함됩니다. 랙에 배치하도록 설계된 장비는 일반적으로 rack-mount, 랙 장착 기기, 랙 장착 시스템, 랙 장착 섀시, 서브랙, 랙 장착 가능 또는 때로는 단순히 선반으로 설명됩니다. 23인치 랙은 19인치 랙보다 덜 일반적이지만 전화(주로), 컴퓨터, 오디오 및 기타 장비를 수용하는 데 사용됩니다. 크기는 설치된 장비의 전면판 너비를 나타냅니다. 랙 장치는 수직 간격의 척도이며 19인치 및 23인치(580mm) 랙 모두에 공통입니다. 구멍 간격은 1인치(25mm) 센터(Western Electric 표준)에 있거나 19인치(480mm) 랙(0.625인치/15.9mm 간격)과 동일합니다. CLICK Product Finder-Locator Service 이전 페이지
- Mesh & Wire, USA, AGS-TECH Inc.
We supply wire and wire mesh, galvanized wires, metal wire, black annealed wire, wire mesh filters, wire cloth, perforated metal mesh, wire mesh fence and panels, conveyor belt mesh, wire mesh containers and customized wire mesh products to your specifications. 메쉬 및 와이어 우리는 아연 도금 철선, PVC 코팅 철 바인딩 와이어, 철망, 철망, fencing 전선, 컨베이어 벨트 메쉬, 천공 금속 메쉬를 포함한 철망 제품을 공급합니다. 기성품 와이어 메쉬 제품 외에도 귀하의 사양 및 요구 사항에 따라 메쉬 및 metal 와이어 제품을 맞춤 제작합니다. 우리는 고객 요구 사항에 따라 원하는 크기, 라벨 및 패키지로 자릅니다. 특정 와이어 및 메쉬 제품에 대한 자세한 내용을 보려면 아래 하위 메뉴를 클릭하십시오. 아연 도금 전선 및 금속 전선 이 전선은 산업 전반에 걸쳐 수많은 응용 분야에서 사용됩니다. 예를 들어 아연 도금 철선은 상당한 인장 강도의 로프와 같이 바인딩 및 부착 목적으로 자주 사용됩니다. 이 금속 와이어는 용융 아연 도금 처리되어 금속 외관을 갖거나 PVC 코팅 및 착색 될 수 있습니다. 가시철사에는 다양한 면도날 유형이 있으며 침입자를 제한 구역 외부로 유지하는 데 사용됩니다. 다양한 와이어 게이지를 재고에서 구할 수 있습니다. 긴 전선 코일로 들어옵니다. 수량에 여유가 있을 경우 원하는 길이와 코일 치수로 제작할 수 있습니다. Galvanized Wires, Metal Wires, Barbed Wire의 맞춤형 라벨링 및 포장이 가능합니다. 브로셔 다운로드: - 금속 와이어 - 아연 도금 - 흑색 소둔 와이어 메쉬 필터 이들은 대부분 얇은 스테인레스 스틸 와이어 메쉬로 만들어지며 액체, 먼지, 분말 등을 필터링하기 위한 필터로 산업계에서 널리 사용됩니다. 철망 필터는 몇 밀리미터 범위의 두께를 가지고 있습니다. AGS-TECH는 군용 해군 조명 시스템의 전자파 차폐를 위해 1mm 미만의 와이어 직경의 와이어 메쉬 제조를 달성했습니다. 고객 사양에 따라 치수의 와이어 메쉬 필터를 제조합니다. 정사각형, 원형 및 타원형이 일반적으로 사용되는 형상입니다. 우리 필터의 와이어 직경과 메쉬 수는 귀하가 선택할 수 있습니다. 필터 메쉬가 왜곡되거나 손상되지 않도록 크기에 맞게 자르고 가장자리를 프레임합니다. 우리의 와이어 메쉬 필터는 높은 변형률, 긴 수명, 강력하고 안정적인 모서리를 가지고 있습니다. 와이어 메쉬 필터의 일부 사용 영역은 화학 산업, 제약 산업, 양조장, 음료, 전자파 차폐, 자동차 산업, 기계 응용 분야 등입니다. - 철망 및 천 브로셔 (와이어 메쉬 필터 포함) 천공된 금속 메쉬 우리의 천공 금속 메쉬 시트는 아연 도금 강판, 저탄소 강, 스테인리스 강, 동판, 니켈 판 또는 고객의 요청에 따라 생산됩니다. 다양한 hole 모양과 패턴은 원하는대로 스탬프 할 수 있습니다. 당사의 천공된 금속 메쉬는 부드러움, 완벽한 표면 평탄도, 강도 및 내구성을 제공하며 많은 응용 분야에 적합합니다. 천공된 금속 메쉬를 공급함으로써 우리는 실내 방음, 소음기 제조, 광업, 의약, 식품 가공, 환기, 농업 저장, 기계적 보호 등을 포함한 많은 산업 및 응용 분야의 요구를 충족했습니다. 지금 전화하세요. 귀하의 사양과 요구 사항에 따라 천공 된 금속 메쉬를 행복하게 자르고, 스탬프하고, 구부리고, 제작할 것입니다. - 철망 및 천 브로셔 (천공된 금속 메쉬 포함) 철망 울타리 및 패널 및 보강재 철망은 건설, 조경, 주택 개량, 원예, 도로 건설 등에 널리 사용됩니다. with 건설 중 울타리 및 보강 패널로 철망을 널리 사용합니다._cc781905-5cde-3194- bb3b-136bad5cf58d_아래에서 다운로드 가능한 브로셔를 참조하여 원하는 메쉬 오프닝, 와이어 게이지, 색상 및 마감 모델을 선택하십시오. 우리의 모든 철망 울타리 및 패널 및 보강 제품은 국제 산업 표준을 준수합니다. 다양한 철망 울타리 구조를 재고에서 사용할 수 있습니다. - 철망 및 천 브로셔 (펜스 및 패널 및 보강재에 대한 정보 포함) 컨베이어 벨트 메쉬 우리의 컨베이어 벨트 메쉬는 일반적으로 강화 메쉬 스테인레스 스틸 와이어, 스테인레스 철 와이어, 니크롬 와이어, 총알 와이어로 만들어집니다. 석유, 야금, 식품 산업, 제약, 유리 산업, 부품 납품 공장 또는 시설 내... 등 대부분의 컨베이어 벨트 메쉬의 Weave Style은 스프링으로 사전 굽힘 후 와이어 삽입입니다. 와이어 직경은 일반적으로 0.8-2.5mm입니다. 와이어 두께는 일반적으로 5-13.2mm입니다. 일반적인 색상은 일반적으로 Silver입니다. 일반적으로 너비는 0.4m~3m, 길이는 0.5~100m입니다. 컨베이어 벨트 메쉬는 내열성이 있습니다. 체인 유형, 컨베이어 벨트 메쉬의 너비 및 길이는 사용자 정의 가능한 매개변수 중 하나입니다. - 철망 및 천 브로셔 (당사의 능력에 대한 일반 정보 포함) 맞춤형 철망 제품(예: 케이블 트레이, 등자....등) 철망 및 천공 금속 메쉬에서 케이블 트레이, 교반기, 패러데이 케이지 및 EM 차폐 구조, 와이어 바구니 및 트레이, 건축 개체, 예술품, 육류 산업에서 사용되는 강철 와이어 메쉬 장갑과 같은 다양한 맞춤형 제품을 제조할 수 있습니다. 부상 방지 등... 맞춤형 철망, 천공 금속 및 확장 금속은 원하는 응용 분야에 맞게 크기로 절단하고 평평하게 할 수 있습니다. 평평한 철망은 일반적으로 기계 가드, 환기 스크린, 버너 스크린, 보안 스크린, 액체 배수 스크린, 천장 패널 및 기타 여러 응용 분야로 사용됩니다. 우리는 귀하의 프로젝트 및 제품 요구 사항을 충족시키기 위해 구멍 모양과 크기를 가진 맞춤형 천공 금속을 만들 수 있습니다. 천공된 금속은 용도가 다양합니다. 우리는 또한 코팅된 철망을 제공할 수 있습니다. 코팅은 맞춤형 철망 제품의 내구성을 향상시키고 녹 방지 장벽을 제공할 수 있습니다. 사용 가능한 맞춤형 와이어 메쉬 코팅에는 분말 코팅, 전기 연마, 용융 아연 도금, 나일론, 페인팅, 알루미늄 도금, 전기 아연 도금, PVC, 케블라 등이 포함됩니다. 맞춤형 철망으로 와이어로 직조하거나 천공 시트로 판금에서 스탬핑 및 펀칭 및 편평화 여부에 관계없이 맞춤형 제품 요구 사항에 대해 AGS-TECH 에 문의하십시오. - 철망 및 천 브로셔 (맞춤형 와이어 메쉬 생산 기능에 대한 많은 정보 포함) - 와이어 메쉬 케이블 트레이 및 바구니 브로셔 (이 브로셔의 제품 외에도 사양에 따라 맞춤형 케이블 트레이를 얻을 수 있습니다.) - 와이어 메쉬 컨테이너 견적 디자인 양식 (다운로드를 클릭하여 작성하고 이메일을 보내주세요) 이전 페이지
- Electric Discharge Machining, EDM, Spark Machining, Die Sinking
Electric Discharge Machining - EDM - Spark Machining - Die Sinking - Wire Erosion - Custom Manufacturing - AGS-TECH Inc. EDM 가공, 방전 밀링 및 그라인딩 ELECTRICAL DISCHARGE MACHINING (EDM), also referred to as SPARK-EROSION or ELECTRODISCHARGE MACHINING, SPARK ERODING, DIE SINKING_cc781905-5cde-3194-bb3b -136bad5cf58d_or WIRE EROSION, is a NON-CONVENTIONAL MANUFACTURING process where erosion of metals takes place and desired shape is obtained using electrical discharges in the form 스파크. 우리는 또한 몇 가지 종류의 EDM, 즉 NO-WEAR EDM, WIRE EDM(WEDM), EDM GRINDING(EDG), DIE-SINKING EDM, ELECTRICAL-DISCHARGE MILLING,7ccm-E900 -5cde-3194-bb3b-136bad5cf58d_and ELECTROCHEMICAL-DISCHARGE 연마(ECDG). 당사의 EDM 시스템은 형상 도구/전극 및 DC 전원 공급 장치에 연결되고 전기적으로 비전도성 유전체 유체에 삽입된 공작물로 구성됩니다. 1940년 이후 방전 가공은 제조 산업에서 가장 중요하고 인기 있는 생산 기술 중 하나가 되었습니다. 두 전극 사이의 거리가 줄어들면 전극 사이의 체적에 있는 전기장의 세기가 일부 지점에서 유전체의 세기보다 커지며, 이것이 끊어지고 결국 두 전극 사이에 전류가 흐르는 다리가 형성됩니다. 강한 전기 아크가 생성되어 상당한 가열로 공작물의 일부와 일부 공구 재료가 녹습니다. 결과적으로 두 전극에서 재료가 제거됩니다. 동시에 유전체 유체가 빠르게 가열되어 아크 갭에서 유체가 증발합니다. 전류 흐름이 중지되거나 중지되면 주변 유전체 유체에 의해 가스 거품에서 열이 제거되고 거품이 공동화(붕괴)합니다. 기포의 붕괴와 유전체 유체의 흐름에 의해 생성된 충격파는 공작물 표면에서 파편을 씻어내고 용융된 공작물 재료를 유전체 유체로 동반합니다. 이러한 방전의 반복률은 50~500kHz, 전압은 50~380V, 전류는 0.1~500A입니다. 광유, 등유 또는 증류수 및 탈이온수와 같은 새로운 액체 유전체는 일반적으로 고체 입자(잔해 형태)를 운반하는 전극 간 부피로 전달되고 유전체의 절연 특성이 복원됩니다. 전류가 흐르면 두 전극 사이의 전위차가 파괴되기 전의 상태로 복원되어 새로운 액체 절연 파괴가 발생할 수 있습니다. 당사의 최신 방전 기계(EDM)는 수치 제어된 움직임을 제공하며 유전성 유체용 펌프 및 여과 시스템이 장착되어 있습니다. 방전 가공(EDM)은 주로 경금속 또는 기존 기술로 가공하기 매우 어려운 금속에 사용되는 가공 방법입니다. EDM으로 절연 세라믹을 가공하는 방법도 제안되었지만 EDM은 일반적으로 전기 전도체인 모든 재료와 함께 작동합니다. 용융점과 용융 잠열은 방전당 제거되는 금속의 부피를 결정하는 특성입니다. 이 값이 높을수록 재료 제거 속도가 느려집니다. 방전 가공 공정에는 기계적 에너지가 필요하지 않기 때문에 가공물의 경도, 강도 및 인성은 제거율에 영향을 미치지 않습니다. 방전 주파수 또는 방전당 에너지, 전압 및 전류는 재료 제거율을 제어하기 위해 변경됩니다. 재료 제거율과 표면 거칠기는 전류 밀도가 증가하고 스파크 주파수가 감소함에 따라 증가합니다. EDM을 사용하여 사전 경화된 강철의 복잡한 윤곽이나 공동을 연화하고 다시 경화시키기 위한 열처리 없이 절단할 수 있습니다. 티타늄, 하스텔로이, 코바르 및 인코넬과 같은 금속 또는 금속 합금에 이 방법을 사용할 수 있습니다. EDM 공정의 적용에는 다결정 다이아몬드 공구의 성형이 포함됩니다. EDM은 전기화학가공(ECM), 워터젯 절단(WJ, AWJ), 레이저 절단과 같은 공정과 함께 비전통적 또는 비전통적 가공 방법으로 간주됩니다. 다른 한편으로, 기존의 기계가공 방법은 선삭, 밀링, 연삭, 드릴링 및 재료 제거 메커니즘이 본질적으로 기계적 힘에 기초하는 기타 공정을 포함합니다. 방전 가공(EDM)용 전극은 흑연, 황동, 구리 및 구리-텅스텐 합금으로 만들어집니다. 전극 직경은 0.1mm까지 가능합니다. 공구 마모는 EDM의 치수 정확도에 부정적인 영향을 미치는 바람직하지 않은 현상이므로 극성을 반대로 하고 구리 공구를 사용하여 공구 마모를 최소화함으로써 NO-WEAR EDM이라는 프로세스를 활용합니다. 이상적으로 말하면 방전 가공(EDM)은 전극 사이의 유전체 액체의 일련의 고장 및 복원으로 간주될 수 있습니다. 그러나 실제로 전극간 영역에서 파편을 제거하는 것은 거의 항상 부분적입니다. 이로 인해 전극 간 영역의 유전체의 전기적 특성이 공칭 값과 다르고 시간에 따라 변합니다. 전극 간 거리(스파크 갭)는 사용된 특정 기계의 제어 알고리즘에 의해 조정됩니다. EDM의 스파크 갭은 불행하게도 때때로 파편에 의해 단락될 수 있습니다. 전극의 제어 시스템은 두 전극(공구 및 공작물)이 단락되는 것을 방지할 만큼 충분히 빠르게 반응하지 않을 수 있습니다. 이 원치 않는 단락은 이상적인 경우와 다르게 재료 제거에 기여합니다. 항상 전극간 영역에 전류가 흐르도록 유전체의 절연성을 회복시켜 공구-전극의 원치 않는 형태 변화(손상) 가능성을 최소화하기 위해 플러싱 작용을 가장 중요하게 생각합니다. 및 공작물. 특정 형상을 얻기 위해 EDM 도구는 공작물에 닿지 않고 공작물에 매우 가까운 원하는 경로를 따라 안내되며 사용 중인 모션 제어 성능에 최대한 주의를 기울입니다. 이러한 방식으로 많은 전류 방전/스파크가 발생하고 각각은 작은 크레이터가 형성되는 공구와 공작물 모두에서 재료를 제거하는 데 기여합니다. 크레이터의 크기는 당면한 특정 작업에 대해 설정된 기술 매개변수의 함수이며 크기는 나노스케일(예: 마이크로 EDM 작업의 경우)에서 황삭 조건에서 수백 마이크로미터까지 다양합니다. 공구의 이러한 작은 크레이터는 "공구 마모"라고 하는 전극의 점진적인 침식을 유발합니다. 공작물의 형상에 대한 마모의 해로운 영향을 상쇄하기 위해 가공 작업 중에 공구 전극을 지속적으로 교체합니다. 때때로 우리는 지속적으로 교체된 와이어를 전극으로 사용하여 이를 달성합니다(이 EDM 프로세스는 WIRE EDM 라고도 함). 때때로 우리는 공구 전극의 일부만 실제로 가공 공정에 참여하고 이 부분이 정기적으로 변경되는 방식으로 도구 전극을 사용합니다. 예를 들어 회전 디스크를 도구 전극으로 사용하는 경우입니다. 이 프로세스를 EDM 연삭이라고 합니다. 우리가 배포하는 또 다른 기술은 마모를 보상하기 위해 동일한 EDM 작업 중에 크기와 모양이 다른 전극 세트를 사용하는 것입니다. 우리는 이것을 다중 전극 기술이라고 부르며, 도구 전극이 원하는 모양의 음으로 복제되고 단일 방향, 일반적으로 수직 방향(즉, z축)을 따라 블랭크 쪽으로 전진할 때 가장 일반적으로 사용됩니다. 이것은 공작물이 잠긴 유전체 액체로의 도구 싱크와 유사하므로 다음과 같이 표시됩니다. 3194-bb3b-136bad5cf58d_CONVENTIONAL EDM or RAM EDM 이 작업을 위한 기계는 SINKER EDM이라고 합니다. 이러한 유형의 EDM용 전극은 복잡한 형태를 가지고 있습니다. 여러 방향을 따라 이동하는 일반적으로 단순한 모양의 전극을 사용하여 최종 형상을 얻었고 회전도 적용되는 경우 이를 EDM 밀링이라고 합니다. 마모 정도는 작동에 사용된 기술 매개변수(극성, 최대 전류, 개방 회로 전압)에 따라 엄격하게 달라집니다. 예를 들어, in micro-EDM( m-EDM이라고도 함)에서 이러한 매개변수는 일반적으로 심각한 마모를 생성하는 값으로 설정됩니다. 따라서 마모는 축적된 노하우를 사용하여 최소화하는 부분에서 큰 문제입니다. 예를 들어 흑연 전극의 마모를 최소화하기 위해 밀리초 이내에 제어할 수 있는 디지털 발전기는 전기 침식이 일어날 때 극성을 반전시킵니다. 이는 전극에 침식된 흑연을 계속해서 침착시키는 전기도금과 유사한 효과를 가져온다. 또 다른 방법으로 소위 ''제로 마모'' 회로는 방전이 시작되고 중지되는 빈도를 최소화하여 가능한 한 오랫동안 방전을 유지합니다. 방전 가공에서 재료 제거율은 다음과 같이 추정할 수 있습니다. MRR = 4 x 10 exp(4) x I x Tw exp(-1.23) 여기서 MRR은 mm3/min, I는 전류(암페어), Tw는 공작물 융점(K-273.15K)입니다. exp는 지수를 의미합니다. 한편, 전극의 마모율 W는 다음과 같이 구할 수 있습니다. 중량 = ( 1.1 x 10exp(11) ) x I x Ttexp(-2.38) 여기서 Wt는 mm3/min 단위이고 Tt는 K-273.15K 단위의 전극 재료의 융점입니다. 마지막으로 전극 R에 대한 공작물의 마모 비율은 다음과 같이 얻을 수 있습니다. R = 2.25 x Trex(-2.38) 여기서 Tr은 전극에 대한 공작물의 융점 비율입니다. 싱커 EDM : 싱커 EDM, 라고도 CAVITY TYPE EDM or_cc781905-5cde-5로 구성되어 있습니다. 전극과 공작물은 전원 공급 장치에 연결됩니다. 전원 공급 장치는 둘 사이에 전위를 생성합니다. 전극이 공작물에 접근함에 따라 유체에서 절연 파괴가 발생하여 플라즈마 채널을 형성하고 작은 스파크 점프가 발생합니다. 스파크는 일반적으로 한 번에 하나씩 발생합니다. 그 이유는 전극간 공간의 다른 위치가 동일한 모든 위치에서 동시에 스파크를 발생시킬 수 있는 동일한 국부적 전기적 특성을 가질 가능성이 거의 없기 때문입니다. 초당 수십만 개의 스파크가 전극과 공작물 사이의 임의의 지점에서 발생합니다. 모재가 침식되고 스파크 갭이 연속적으로 증가함에 따라 전극은 CNC 기계에 의해 자동으로 낮아져 프로세스가 중단 없이 계속될 수 있습니다. 당사 장비에는 ''시간' 및 '오프 시간''으로 알려진 제어 주기가 있습니다. 켜짐 시간 설정은 스파크의 길이 또는 지속 시간을 결정합니다. 시간이 길수록 해당 스파크와 해당 사이클에 대한 모든 후속 스파크에 대해 더 깊은 캐비티가 생성되어 공작물에 거친 마무리가 생성되고 그 반대의 경우도 마찬가지입니다. 오프 시간은 하나의 스파크가 다른 스파크로 교체되는 시간입니다. 더 긴 오프 시간은 유전체 유체가 노즐을 통해 흘러내리도록 하여 침식된 파편을 청소하여 단락을 방지합니다. 이러한 설정은 마이크로 초 단위로 조정됩니다. 와이어 EDM : In WIRE ELECTRICAL DISCHARGE MACHINING (WEDM), also called WIRE-CUT EDM or WIRE CUTTING, we feed a 유전체 유체 탱크에 잠긴 공작물을 통해 황동의 얇은 단일 가닥 금속 와이어. 와이어 EDM은 EDM의 중요한 변형입니다. 우리는 때때로 와이어 컷 EDM을 사용하여 300mm 두께의 판을 절단하고 다른 제조 방법으로 기계로 가공하기 어려운 경금속으로 펀치, 도구 및 다이를 만듭니다. 띠톱으로 윤곽을 절단하는 것과 유사한 이 과정에서 스풀에서 지속적으로 공급되는 와이어가 상부 및 하부 다이아몬드 가이드 사이에 고정됩니다. CNC 제어 가이드는 x-y 평면에서 이동하고 상단 가이드는 z-u-v 축에서 독립적으로 이동할 수 있어 테이퍼 및 전환 모양(예: 바닥의 원 및 상단). 상부 가이드는 x–y–u–v–i–j–k–l–의 축 이동을 제어할 수 있습니다. 이를 통해 WEDM은 매우 복잡하고 섬세한 모양을 절단할 수 있습니다. 최고의 경제적 비용과 가공 시간을 달성하는 장비의 평균 절단 커프는 Ø 0.25 황동, 구리 또는 텅스텐 와이어를 사용하여 0.335mm입니다. 그러나 당사 CNC 장비의 상부 및 하부 다이아몬드 가이드는 약 0.004mm까지 정확하며 Ø 0.02mm 와이어를 사용하여 0.021mm만큼 작은 절단 경로 또는 커프를 가질 수 있습니다. 따라서 정말 좁은 절단이 가능합니다. 와이어의 측면에서 가공물까지 스파크가 발생하여 침식의 원인이 되기 때문에 절단 폭이 와이어의 폭보다 큽니다. 이 '오버컷'은 많은 응용 분야에서 필요하며 예측 가능하므로 보상할 수 있습니다(마이크로 EDM에서는 자주 발생하지 않음). 와이어 스풀은 깁니다. 0.25mm 와이어의 8kg 스풀은 길이가 19km가 조금 넘습니다. 와이어 직경은 20마이크로미터만큼 작을 수 있으며 기하학적 정밀도는 +/- 1마이크로미터에 가깝습니다. 우리는 일반적으로 와이어를 한 번만 사용하고 상대적으로 저렴하기 때문에 재활용합니다. 0.15~9m/min의 일정한 속도로 이동하며 절단 중에 일정한 절단(슬롯)이 유지됩니다. 와이어 컷 EDM 공정에서 우리는 물을 유전체 유체로 사용하여 필터와 탈이온화 장치로 물의 저항과 기타 전기적 특성을 제어합니다. 물은 절단 영역에서 절단 파편을 씻어냅니다. 플러싱은 주어진 재료 두께에 대한 최대 이송 속도를 결정하는 중요한 요소이므로 이를 일관되게 유지합니다. 와이어 EDM의 절단 속도는 50mm 두께의 D2 공구강의 경우 18,000mm2/hr과 같이 단위 시간당 절단된 단면적으로 표시됩니다. 이 경우 선형 절단 속도는 18,000/50 = 360mm/hr입니다. 와이어 EDM의 재료 제거율은 다음과 같습니다. MRR = Vf xhxb 여기서 MRR은 mm3/min, Vf는 공작물로 들어가는 와이어의 이송 속도(mm/min), h는 두께 또는 높이(mm), b는 커프(kerf)입니다. b = dw + 2s 여기서 dw는 와이어 직경이고 s는 와이어와 공작물 사이의 간격(mm)입니다. 더 엄격한 공차와 함께 현대적인 다축 EDM 와이어 절단 머시닝 센터에는 두 부품을 동시에 절단하기 위한 멀티 헤드, 와이어 파손 방지 제어, 와이어 파손 시 자동 셀프 스레딩 기능 및 프로그래밍된 기능과 같은 기능이 추가되었습니다. 작업, 직선 및 각진 절단 기능을 최적화하기 위한 가공 전략. Wire-EDM은 재료 제거에 높은 절삭 부하가 필요하지 않기 때문에 낮은 잔류 응력을 제공합니다. 펄스당 에너지/전력이 상대적으로 낮으면(마무리 작업에서와 같이) 낮은 잔류 응력으로 인해 재료의 기계적 특성에 거의 변화가 없을 것으로 예상됩니다. 전기 방전 연삭(EDG) : 연삭 휠에는 연마제가 포함되어 있지 않으며 흑연 또는 황동으로 만들어집니다. 회전하는 휠과 공작물 사이의 반복적인 스파크는 공작물 표면에서 재료를 제거합니다. 재료 제거율은 다음과 같습니다. MRR = K x I 여기에서 MRR은 mm3/min 단위, I는 전류 단위 암페어, K는 mm3/A-min 단위의 공작물 재료 계수입니다. 부품의 좁은 슬릿을 보기 위해 방전 연삭을 자주 사용합니다. 우리는 때때로 EDG(Electrical-Discharge Grinding) 공정과 화학 작용에 의해 물질이 제거되는 ECG(Electrochemical Grinding) 공정을 결합합니다. 프로세스는 ELECTROCHEMICAL-DISCHARGE GRINDING(ECDG)이라고 합니다. ECDG 프로세스는 상대적으로 더 많은 전력을 소비하지만 EDG보다 빠른 프로세스입니다. 우리는 주로 이 기술을 사용하여 초경 공구를 연삭합니다. 방전 가공의 응용: 시제품 생산: 우리는 특히 생산량이 상대적으로 적은 항공우주, 자동차 및 전자 산업을 위해 금형 제작, 도구 및 다이 제조는 물론 프로토타입 및 생산 부품을 만드는 데 EDM 공정을 사용합니다. Sinker EDM에서 흑연, 구리 텅스텐 또는 순수 구리 전극은 원하는(음의) 모양으로 가공되어 수직 램의 끝에서 공작물로 공급됩니다. 주화 다이 만들기: 주화(스탬핑) 공정으로 보석과 배지를 생산하기 위한 다이를 만드는 경우, 포지티브 마스터는 순은으로 만들 수 있습니다. 왜냐하면 (적절한 기계 설정으로) 마스터가 크게 침식되어 한 번만 사용되기 때문입니다. 그 결과 생성된 네거티브 다이는 경화되고 드롭 해머로 사용되어 청동, 은 또는 낮은 증거 금 합금의 컷아웃 시트 블랭크에서 스탬핑된 플랫을 생성합니다. 배지의 경우 이러한 플랫은 다른 다이에 의해 곡면으로 더 성형될 수 있습니다. 이러한 유형의 EDM은 일반적으로 유성 유전체에 잠겨 수행됩니다. 완성된 물체는 경질(유리) 또는 연질(페인트) 에나멜 및/또는 순금 또는 니켈로 전기도금하여 더욱 정제할 수 있습니다. 은과 같은 더 부드러운 재료는 정교하게 손으로 조각할 수 있습니다. 작은 구멍 드릴링: 와이어 절단 EDM 기계에서 우리는 작은 구멍 드릴링 EDM을 사용하여 와이어 절단 EDM 작업을 위해 와이어를 끼울 공작물에 관통 구멍을 만듭니다. 특별히 작은 구멍 드릴링을 위한 별도의 EDM 헤드가 와이어 컷 기계에 장착되어 있어 사전 드릴링 없이 필요에 따라 큰 경화 플레이트에서 완성 부품이 부식되도록 합니다. 우리는 또한 작은 구멍 EDM을 사용하여 제트 엔진에 사용되는 터빈 블레이드의 가장자리에 구멍을 뚫습니다. 이 작은 구멍을 통한 가스 흐름은 엔진이 가능한 것보다 더 높은 온도를 사용할 수 있도록 합니다. 이 블레이드는 고온의 매우 단단한 단결정 합금으로 만들어지기 때문에 종횡비가 높은 이러한 구멍의 기존 기계가공이 매우 어렵고 심지어 불가능합니다. 작은 구멍 EDM의 다른 응용 분야는 연료 시스템 구성 요소를 위한 미세한 구멍을 만드는 것입니다. 통합 EDM 헤드 외에도 블라인드 또는 관통 홀을 가공하기 위해 x–y 축이 있는 독립형 소형 홀 드릴링 EDM 장비를 배포합니다. EDM은 플러싱 에이전트 및 유전체로 전극을 통해 흐르는 일정한 증류수 또는 탈이온수 흐름과 함께 척에서 회전하는 긴 황동 또는 구리 튜브 전극으로 구멍을 뚫습니다. 일부 작은 구멍 드릴링 EDM은 10초 이내에 연강 또는 경화강의 100mm를 드릴링할 수 있습니다. 이 드릴링 작업에서 0.3mm와 6.1mm 사이의 구멍을 얻을 수 있습니다. 금속 분해 가공: 우리는 또한 공작물에서 부러진 도구(드릴 비트 또는 탭)를 제거하기 위한 특정 목적을 위한 특수 EDM 기계를 보유하고 있습니다. 이 공정을 '금속 분해 가공''이라고 합니다. 장점 및 단점 방전 가공: EDM의 장점은 다음과 같은 가공을 포함합니다. - 기존의 절삭 공구로 생산하기 어려운 복잡한 형상 - 공차에 매우 가까운 매우 단단한 재료 - 기존의 절삭 공구가 과도한 절삭 공구 압력으로 부품을 손상시킬 수 있는 매우 작은 공작물. - 공구와 공작물이 직접 접촉하지 않습니다. 따라서 섬세한 단면과 약한 재료를 왜곡 없이 가공할 수 있습니다. - 우수한 표면조도를 얻을 수 있다. - 아주 미세한 구멍을 쉽게 뚫을 수 있습니다. EDM의 단점은 다음과 같습니다. - 재료 제거 속도가 느림. - ram/sinker EDM용 전극을 만드는 데 사용되는 추가 시간과 비용. - 전극 마모로 인해 공작물의 날카로운 모서리 재현이 어렵습니다. - 소비전력이 높다. - '오버컷'이 형성됩니다. - 가공 중 과도한 공구 마모가 발생합니다. - 전기적으로 비전도성인 재료는 특정 프로세스 설정으로만 가공할 수 있습니다. CLICK Product Finder-Locator Service 이전 페이지