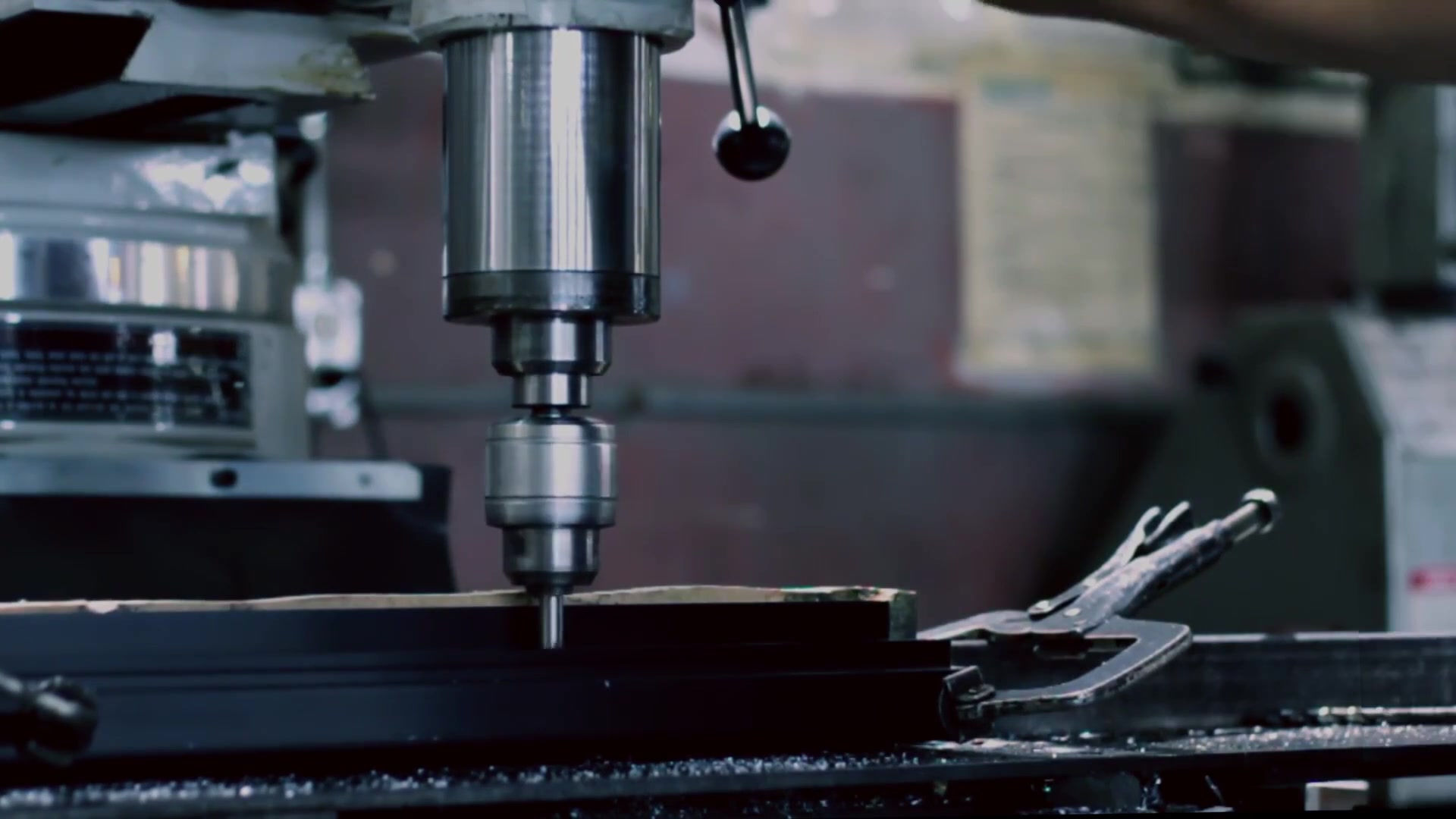
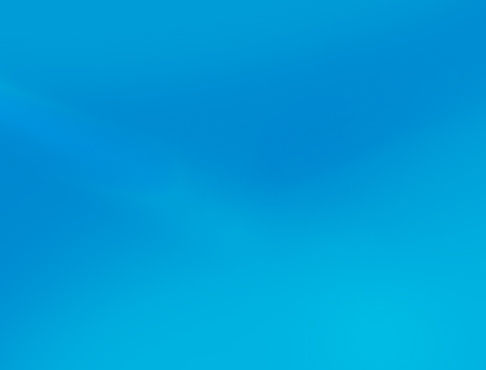
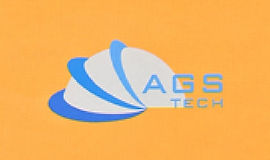
Global Custom Manufacturer, Integrator, Consolidator, Products & Services හි පුළුල් විවිධත්වයක් සඳහා බාහිරින් ලබා ගැනීමේ හවුල්කරු.
අභිරුචි නිෂ්පාදනය කරන ලද සහ රාක්කයෙන් බැහැර නිෂ්පාදන සහ සේවා නිෂ්පාදනය කිරීම, සැකසීම, ඉංජිනේරු විද්යාව, ඒකාබද්ධ කිරීම, ඒකාබද්ධ කිරීම, බාහිරින් ලබා ගැනීම සඳහා අපි ඔබේ එක-නැවතුම් මූලාශ්රය වේ.
ඔබේ භාෂාව තෝරන්න
-
අභිරුචි නිෂ්පාදනය
-
දේශීය සහ ගෝලීය ගිවිසුම් නිෂ්පාදනය
-
නිෂ්පාදන බාහිරකරණය
-
දේශීය සහ ගෝලීය ප්රසම්පාදන
-
Consolidation
-
ඉංජිනේරු අනුකලනය
-
ඉංජිනේරු සේවාවන්
අපි පිරිනමනු ලබන METAL FORGING ක්රියාවලි වර්ගය වන්නේ hot and cool die, open die and close die, impression die & flashless forgings, cogging, fullering, edging and precision forging, head-ne-shape , swaging, upset forging, metal hobbing, press & roll & radial & orbital & ring & isothermal forgings, coining, riveting, metal ball forging, metal piercing, Sizing, high energy rate forging.
අපගේ POWDER METALLURGY සහ POWDER Processing ශිල්පීය ක්රම වන්නේ කුඩු එබීම සහ සින්ටර් කිරීම, impregnation, infiltration, hot and cool isostatic pressing, metal injection molding, roll Compact, powder rolling, powder extrusion, loose sintering, spark sintering, hot pressing.
ඔබ මෙහි ක්ලික් කරන ලෙස අපි නිර්දේශ කරමු
AGS-TECH Inc. මගින් ව්යාජ ක්රියාවලි පිළිබඳ අපගේ ක්රමානුකූල නිදර්ශන බාගන්න
AGS-TECH Inc. මගින් කුඩු ලෝහ ක්රියාවලි පිළිබඳ අපගේ ක්රමානුකූල නිදර්ශන බාගන්න
ඡායාරූප සහ කටු සටහන් සහිත මෙම බාගත කළ හැකි ගොනු අප ඔබට පහතින් සපයන තොරතුරු වඩාත් හොඳින් අවබෝධ කර ගැනීමට උපකාරී වනු ඇත.
ලෝහ ව්යාජය තුළ, සම්පීඩක බලවේග යොදනු ලබන අතර ද්රව්යය විකෘති වී අපේක්ෂිත හැඩය ලබා ගනී. කර්මාන්තයේ වඩාත් සුලභ ව්යාජ ද්රව්ය වන්නේ යකඩ සහ වානේ ය, නමුත් ඇලුමිනියම්, තඹ, ටයිටේනියම්, මැග්නීසියම් වැනි තවත් බොහෝ ද්රව්ය ද ව්යාජ ලෙස සකස් කර ඇත. ව්යාජ ලෝහ කොටස් මුද්රා තැබූ ඉරිතැලීම් සහ සංවෘත හිස් අවකාශයන්ට අමතරව ධාන්ය ව්යුහයන් වැඩි දියුණු කර ඇත, එබැවින් මෙම ක්රියාවලියෙන් ලබාගත් කොටස්වල ශක්තිය වැඩි වේ. වාත්තු කිරීම හෝ යන්ත්ර කිරීම මගින් සාදන ලද කොටස් වලට වඩා ඒවායේ බර සඳහා සැලකිය යුතු ලෙස ශක්තිමත් කොටස් නිෂ්පාදනය කරයි. ලෝහය එහි අවසාන හැඩයට ගලා යාමෙන් ව්යාජ කොටස් හැඩගස්වා ඇති බැවින්, ලෝහය කොටස්වල ඉහළ ශක්තියට හේතු වන දිශානුගත ධාන්ය ව්යුහයක් ගනී. වෙනත් වචන වලින් කිවහොත්, සරල වාත්තු හෝ යන්ත්රගත කොටස් වලට සාපේක්ෂව ව්යාජ ක්රියාවලියෙන් ලබාගත් කොටස් වඩා හොඳ යාන්ත්රික ගුණාංග හෙළි කරයි. ලෝහ ව්යාජ වල බර කුඩා සැහැල්ලු කොටස් සිට රාත්තල් සිය දහස් ගණනක් දක්වා විය හැකිය. මෝටර් රථ අමතර කොටස්, ගියර්, වැඩ මෙවලම්, අත් මෙවලම්, ටර්බයින් පතුවළ, යතුරුපැදි ගියර් වැනි කොටස් මත අධික ආතතීන් යොදන යාන්ත්රිකව ඉල්ලුමක් ඇති යෙදුම් සඳහා අපි බොහෝ දුරට ව්යාජ නිෂ්පාදනය කරන්නෙමු. මෙවලම් සහ සැකසීමේ පිරිවැය සාපේක්ෂ වශයෙන් ඉහළ බැවින්, අපි මෙම නිෂ්පාදන ක්රියාවලිය නිර්දේශ කරන්නේ ඉහළ වෙළුම් නිෂ්පාදනය සඳහා සහ අඩු පරිමාවක් සඳහා පමණක් වන නමුත් අභ්යවකාශ ගොඩබෑමේ ආම්පන්න වැනි ඉහළ වටිනාකමක් ඇති තීරණාත්මක සංරචක සඳහා පමණි. මෙවලම්වල පිරිවැයට අමතරව, විශාල ප්රමාණයේ ව්යාජ කොටස් නිෂ්පාදනය කිරීමේ කාලසීමාව සමහර සරල යන්ත්රගත කොටස් හා සසඳන විට දිගු විය හැකි නමුත්, තාක්ෂණික ක්රමය ඉතා වැදගත් වන්නේ අවශ්ය කොටස් සඳහා තීරනාත්මක වේ. ගාංචු, මෝටර් රථ, ෆෝක්ලිෆ්ට්, දොඹකර කොටස්.
• HOT DIE සහ COLD DIE FORGING : Hot die forging, නමින් හැඟවෙන පරිදි, ඉහළ උෂ්ණත්වවලදී සිදු කරනු ලැබේ, එබැවින් ductility ඉහළ සහ ද්රව්යයේ ශක්තිය අඩු වේ. මෙය පහසුවෙන් විකෘති කිරීමට සහ ව්යාජ ලෙස සකස් කිරීමට පහසුකම් සපයයි. ඊට පටහැනිව, සීතල ඩයි ෆෝජිං සිදු කරනු ලබන්නේ අඩු උෂ්ණත්වවලදී වන අතර ඉහළ බලයක් අවශ්ය වන අතර එමඟින් නිෂ්පාදනය කරන ලද කොටස්වල වික්රියා දැඩි වීම, වඩා හොඳ මතුපිට නිමාව සහ නිරවද්යතාවය ඇති වේ.
• OPEN DIE සහ IMPRESSION DIE FORGING : විවෘත ඩයි ෆෝජිං වලදී, ඩයිස් සම්පීඩනය වන ද්රව්ය සීමා නොකරයි, නමුත් ප්රතිරූපයේ දී ඩයිස් තුළ ඇති කුහරයන් අපේක්ෂිත හැඩයට සාදන අතර ද්රව්ය ප්රවාහය සීමා කරයි. UPSET FORGING හෝ UPSETTING ලෙසද හැඳින්වේ, එය ඇත්ත වශයෙන්ම සමාන නොවන නමුත් ඉතා සමාන ක්රියාවලියකි, යනු විවෘත ඩයි ක්රියාවලියකි, එහිදී වැඩ කොටස පැතලි ඩයි දෙකක් අතර සැන්ඩ්විච් කර ඇති අතර සම්පීඩක බලයක් එහි උස අඩු කරයි. උස reduced වන විට, වැඩ කොටස පළල වැඩි වේ. HEADING, අවුල් සහගත ව්යාජ ක්රියාවලියකට සිලින්ඩරාකාර කොටස් ඇතුළත් වන අතර එය අවසානයේ කැළඹී ඇති අතර එහි හරස්කඩ දේශීයව වැඩි වේ. ශීර්ෂය තුළ තොගය ඩයි හරහා පෝෂණය කර, ව්යාජ ලෙස සකස් කර පසුව දිගට කපා ඇත. ක්රියාන්විතය මගින් වේගවත් ගාංචු විශාල ප්රමාණයක් නිපදවීමට හැකියාව ඇත. බොහෝ විට එය ද්රව්යය ශක්තිමත් කිරීමට අවශ්ය වන නියපොතු කෙළවර, ඉස්කුරුප්පු ඇණ, ගෙඩි සහ බෝල්ට් සෑදීමට භාවිතා කරන නිසා එය සීතල ක්රියාකාරී මෙහෙයුමකි. තවත් විවෘත ඩයි ක්රියාවලියක් වන්නේ COGGING, එහිදී වැඩ කොටස එක් එක් පියවර සමඟ පියවර මාලාවක් තුළ ව්යාජ ලෙස සකස් කර ඇති අතර එහි ප්රතිඵලයක් ලෙස ද්රව්ය සම්පීඩනය වන අතර පසුව වැඩ කොටසෙහි දිග දිගේ විවෘත ඩයි චලනය වේ. සෑම පියවරකදීම ඝනකම අඩු වන අතර දිග කුඩා ප්රමාණයකින් වැඩි වේ. මෙම ක්රියාවලිය ස්නායු ශිෂ්යයෙකු කුඩා පියවරකින් තම පැන්සල සපා කෑමට සමාන වේ. FULLERING නම් ක්රියාවලියක් යනු වෙනත් ලෝහ ව්යාජ මෙහෙයුම් සිදු වීමට පෙර වැඩ කොටසෙහි ඇති ද්රව්ය බෙදා හැරීමට පෙර පියවරක් ලෙස අප බොහෝ විට යොදවන තවත් විවෘත ඩයි ෆෝජිං ක්රමයකි. වැඩ කොටස සඳහා forging operations අවශ්ය වූ විට අපි එය භාවිතා කරමු. මෙහෙයුමේදී, උත්තල පෘෂ්ඨයන් විරූපණය වීමත් සමඟම දෙපසට ලෝහ ප්රවාහය ඇති කරයි. ෆුලර් කිරීම හා සමාන ක්රියාවලියක්, අනෙක් අතට EDGING වැඩ කොටස විකෘති කිරීම සඳහා අවතල පෘෂ්ඨ සහිත විවෘත ඩයි ඇතුළත් වේ. පසුකාලීන ව්යාජ මෙහෙයුම් සඳහා සූදානම් කිරීමේ ක්රියාවලියක් ද දාර කිරීම මගින් ද්රව්යය දෙපස සිට මධ්යයේ ප්රදේශයකට ගලා යයි. IMPRESSION DIE FORGING හෝ closed DIE FORGING ලෙසද හැඳින්වේ, එය ඩයි / අච්චුවක් භාවිතා කරන අතර එමඟින් ද්රව්යය සම්පීඩනය කර එහි ප්රවාහය එය තුළම සීමා කරයි. ඩයි එක වැසෙන අතර ද්රව්යය ඩයි/පුස් කුහරයේ හැඩය ගනී. PRECISION FORGING, විශේෂ උපකරණ සහ අච්චුව අවශ්ය වන ක්රියාවලියක්, ෆ්ලෑෂ් නොමැති හෝ ඉතා කුඩා කොටස් නිෂ්පාදනය කරයි. වෙනත් වචන වලින් කිවහොත්, කොටස්වල අවසාන මානයන් ආසන්න වනු ඇත. මෙම ක්රියාවලියේදී හොඳින් පාලනය කරන ලද ද්රව්ය ප්රමාණයක් ප්රවේශමෙන් ඇතුල් කර අච්චුව තුළ ස්ථානගත කරනු ලැබේ. අපි මෙම ක්රමය තුනී කොටස්, කුඩා ඉවසීම් සහ කෙටුම්පත් කෝණ සහිත සංකීර්ණ හැඩතල සඳහා සහ අච්චු සහ උපකරණ පිරිවැය සාධාරණීකරණය කිරීමට තරම් ප්රමාණ විශාල වන විට යොදන්නෙමු.
• FLASHLESS FORGING : ෆ්ලෑෂ් සෑදීමට කිසිදු ද්රව්ය කුහරයෙන් පිටතට ගලා යා නොහැකි ආකාරයට වැඩ කොටස ඩයි එකේ තබා ඇත. අනවශ්ය ෆ්ලෑෂ් කැපීම අවශ්ය නොවේ. එය නිරවද්ය ව්යාජ ක්රියාවලියක් වන අතර එබැවින් භාවිතා කරන ද්රව්ය ප්රමාණය සමීපව පාලනය කිරීම අවශ්ය වේ.
• මෙටල් ස්වැජිං හෝ රේඩියල් ෆෝජිං: වැඩ ෙකොටුවක් ඩයි සහ ව්යාජ ලෙස වටකුරු ලෙස ක්රියා කරයි. අභ්යන්තර වැඩ කොටස ජ්යාමිතිය ව්යාජ ලෙස සකස් කිරීම සඳහා මැන්ඩලයක් ද භාවිතා කළ හැක. චලනය කිරීමේ මෙහෙයුමේදී වැඩ කොටස සාමාන්යයෙන් තත්පරයකට පහර කිහිපයක් ලබා ගනී. swaging මගින් නිපදවන සාමාන්ය භාණ්ඩ වන්නේ උල් ටිප් මෙවලම්, ෙට්පර්ඩ් බාර්, ඉස්කුරුප්පු නියනයි.
• ලෝහ සිදුරු කිරීම: කොටස් නිෂ්පාදනයේදී අතිරේක මෙහෙයුමක් ලෙස අපි මෙම මෙහෙයුම නිතර භාවිතා කරමු. එය හරහා නොකැඩී වැඩ කොටස මතුපිට සිදුරු කිරීම සමඟ සිදුරක් හෝ කුහරයක් නිර්මාණය වේ. විදීම සිදුරකින් සිදු වන විදීමට වඩා වෙනස් බව කරුණාවෙන් සලකන්න.
• HOBBING : අපේක්ෂිත ජ්යාමිතිය සහිත පන්ච් එකක් වැඩ කොටසට තද කර අපේක්ෂිත හැඩය සහිත කුහරයක් නිර්මාණය කරයි. අපි මේ පන්ච් එකට කියන්නේ HOB කියලා. මෙහෙයුම අධි පීඩන ඇතුළත් වන අතර සීතල තුළ සිදු කරනු ලැබේ. එහි ප්රතිඵලයක් වශයෙන් ද්රව්යය සීතල ලෙස ක්රියා කර ඇති අතර දැඩි වී ඇත. එබැවින් මෙම ක්රියාවලිය අනෙකුත් නිෂ්පාදන ක්රියාවලීන් සඳහා අච්චු, ඩයි සහ කුහර නිෂ්පාදනය කිරීම සඳහා ඉතා යෝග්ය වේ. හොබ් එක නිෂ්පාදනය කළ පසු, එකින් එක යන්ත්ර කිරීමකින් තොරව එක සමාන කුහර රාශියක් පහසුවෙන් නිෂ්පාදනය කළ හැකිය.
• ROLL FORGING හෝ ROLL FORMING : ලෝහ කොටස හැඩගැන්වීම සඳහා ප්රතිවිරුද්ධ රෝල් දෙකක් භාවිතා කරයි. වැඩ ෙකොටස් ෙරෝල් බවට පෝෂණය, ෙරෝල්ස් හැරී හා පරතරය බවට වැඩ අදින්න, වැඩ පසුව රෝල් වල grooved කොටස හරහා පෝෂණය වන අතර සම්පීඩ්යතා බලවේග ද්රව්ය එහි අපේක්ෂිත හැඩය ලබා දෙයි. එය පෙරළීමේ ක්රියාවලියක් නොව ව්යාජ ක්රියාවලියකි, මන්ද එය අඛණ්ඩ ක්රියාවකට වඩා විවික්ත ක්රියාවලියකි. රෝල්ස් වතු වල ජ්යාමිතිය අවශ්ය හැඩය සහ ජ්යාමිතිය සඳහා ද්රව්ය ව්යාජ ලෙස සකස් කරයි. එය උණුසුම්ව සිදු කරනු ලැබේ. ව්යාජ ක්රියාවලියක් නිසා එය කැපී පෙනෙන යාන්ත්රික ගුණ සහිත කොටස් නිපදවන අතර එම නිසා අපි එය manufacturing මෝටර් රථ කොටස් සඳහා භාවිතා කරන අතර එය දැඩි වැඩ පරිසරයකදී අසාමාන්ය විඳදරාගැනීමක් අවශ්ය පතුවළ වැනි වේ.
• කක්ෂීය ව්යාජය: වැඩ කොටස ව්යාජ ඩයි කුහරයක දමා එය ආනත අක්ෂයක් මත භ්රමණය වන විට කක්ෂීය මාර්ගයක ගමන් කරන ඉහළ ඩයි එකක් මගින් ව්යාජ ලෙස සකස් කර ඇත. සෑම විප්ලවයකදීම, ඉහළ ඩයි සම්පූර්ණ වැඩ කොටස වෙත සම්පීඩන බලය යෙදවීම සම්පූර්ණ කරයි. මෙම විප්ලවයන් කිහිප වතාවක් පුනරාවර්තනය කිරීමෙන්, ප්රමාණවත් ව්යාජයක් සිදු කරනු ලැබේ. මෙම නිෂ්පාදන තාක්ෂණයේ වාසි වන්නේ එහි අඩු ශබ්ද ක්රියාකාරිත්වය සහ අවශ්ය අඩු බලයයි. වෙනත් වචන වලින් කිවහොත්, කුඩා බලවේග සමඟ අක්ෂයක් වටා බර ඩයි එකක් භ්රමණය කළ හැකි අතර එය ඩයි සමඟ ස්පර්ශ වන වැඩ කොටසෙහි කොටසකට විශාල පීඩනයක් යෙදිය හැකිය. මෙම ක්රියාවලිය සඳහා තැටිය හෝ කේතුකාකාර හැඩැති කොටස් සමහර විට සුදුසු වේ.
• RING FORGING : අපි නිතරම බාධාවකින් තොරව වළලු නිෂ්පාදනය කිරීමට භාවිතා කරමු. කොටස් දිගට කපා, අවුල් කර, පසුව මැද සිදුරක් නිර්මාණය කිරීම සඳහා සිදුරු කරනු ලැබේ. ඉන්පසු එය මැන්ඩලයක් මත තබා, අපේක්ෂිත මානයන් ලබා ගන්නා තෙක් මුද්ද සෙමින් කරකවන බැවින් ව්යාජ ඩයි මිටියක් එය ඉහළින් තබයි.
• රිවට් කිරීම: කොටස් සම්බන්ධ කිරීම සඳහා වන පොදු ක්රියාවලියක්, කොටස් හරහා පෙර සාදන ලද සිදුරුවලට ඇතුළු කරන ලද සෘජු ලෝහ කැබැල්ලකින් ආරම්භ වේ. ඉන්පසුව ඉහළ සහ පහළ ඩයි එකක් අතර සන්ධිය මිරිකීමෙන් ලෝහ කැබැල්ලේ කෙළවර දෙක ව්යාජ ලෙස සකසා ඇත.
• COINING : යාන්ත්රික මුද්රණ යන්ත්ර මගින් සිදු කරනු ලබන තවත් ජනප්රිය ක්රියාවලියක්, කෙටි දුරක් හරහා විශාල බලයක් යෙදවීම. “කාසිකරණය” යන නම පැමිණෙන්නේ ලෝහ කාසිවල මතුපිට ව්යාජ ලෙස සකස් කර ඇති සියුම් විස්තර මගිනි. එය බොහෝ විට නිෂ්පාදනයක් නිම කිරීමේ ක්රියාවලියක් වන අතර එහිදී මෙම තොරතුරු වැඩ කොටස වෙත මාරු කරන ඩයි මගින් යොදන විශාල බලයේ ප්රතිඵලයක් ලෙස පෘෂ්ඨයන් මත සියුම් විස්තර ලබා ගනී.
• METAL BALL FORGING : ෙබෝල ෙබයාරිං වැනි නිෂ්පාදන සඳහා උසස් තත්ත්වයෙන් නිශ්චිතව නිපදවන ලද ෙලෝහ ෙබෝල අවශ්ය ෙව්. SKEW ROLLING නමින් හැඳින්වෙන එක් තාක්ෂණයක, කොටස් අඛණ්ඩව රෝල්වලට පෝෂණය වන බැවින් අපි ප්රතිවිරුද්ධ රෝල් දෙකක් භාවිතා කරමු. රෝල් දෙකේ එක් කෙළවරක නිෂ්පාදනයක් ලෙස ලෝහ ගෝල පිට කරනු ලැබේ. ලෝහ බෝල ව්යාජ කිරීම සඳහා වන දෙවන ක්රමය වන්නේ අච්චු කුහරයේ ගෝලාකාර හැඩය ගනිමින් ඒවා අතර තබා ඇති ද්රව්ය තොගය මිරිකා දැමීමයි. බොහෝ විට නිපදවන බෝල උසස් තත්ත්වයේ නිෂ්පාදනයක් බවට පත්වීම සඳහා නිම කිරීම සහ ඔප දැමීම වැනි අමතර පියවර කිහිපයක් අවශ්ය වේ.
• ISOTHERMAL FORGING / HOT DIE FORGING : මිල අධික ක්රියාවලියක් සිදු කරනු ලබන්නේ ප්රතිලාභ / පිරිවැය වටිනාකම සාධාරණීකරණය කළ විට පමණි. ඩයි එක වැඩ කොටසට සමාන උෂ්ණත්වයකට රත් කරන උණුසුම් ක්රියාදාමයකි. ඩයි සහ වැඩ යන දෙකම එකම උෂ්ණත්වයක් ඇති බැවින්, සිසිලනය නොමැති අතර ලෝහයේ ප්රවාහ ලක්ෂණ වැඩි දියුණු වේ. මෙම මෙහෙයුම සුපිරි මිශ්ර ලෝහ සහ බාල ව්යාජ හැකියාව සහිත ද්රව්ය සඳහා හොඳින් ගැලපේ.
යාන්ත්රික ගුණ කුඩා උෂ්ණත්ව අනුක්රමික හා වෙනස්වීම් වලට ඉතා සංවේදී වේ.
• ලෝහ ප්රමාණය: එය සීතල නිම කිරීමේ ක්රියාවලියකි. බලය යොදන දිශාව හැර අනෙකුත් සියලුම දිශාවන්හි ද්රව්ය ප්රවාහය සීමා රහිත වේ. ප්රතිඵලයක් වශයෙන්, ඉතා හොඳ මතුපිට නිමාවක් සහ නිවැරදි මානයන් ලබා ගනී.
• HIGH ENERGY RTE FORGING : මෙම තාක්ෂණයට පිස්ටනයක බාහුවට සවි කර ඇති ඉහළ අච්චුවක් ඇතුළත් වන අතර එය ඉන්ධන-වායු මිශ්රණයක් ස්පාර්ක් ප්ලග් එකකින් දැල්වෙන විට වේගයෙන් තල්ලු කරනු ලැබේ. එය කාර් එන්ජිමක පිස්ටන් ක්රියාකාරිත්වයට සමානයි. අච්චුව වැඩ කොටසට ඉතා වේගයෙන් පහර දෙන අතර පසු පීඩනයට ස්තූතිවන්ත වන පරිදි ඉතා වේගයෙන් එහි මුල් ස්ථානයට පැමිණේ. වැඩේ මිලි තත්පර කිහිපයක් ඇතුළත ව්යාජ ලෙස සකස් කර ඇති අතර එම නිසා කාර්යය සිසිල් වීමට කාලයක් නොමැත. ඉතා උෂ්ණත්ව සංවේදී යාන්ත්රික ගුණ ඇති ව්යාජ කොටස් සඳහා මෙය ප්රයෝජනවත් වේ. වෙනත් වචන වලින් කියතොත්, ක්රියාවලිය කෙතරම් වේගවත්ද යත්, කොටස පුරා නියත උෂ්ණත්වය යටතේ සෑදී ඇති අතර අච්චුව/වැඩ කොටස් අතුරුමුහුණත්වල උෂ්ණත්ව අනුක්රමණයන් නොමැත.
• DIE FORGING වලදී, විශේෂ හැඩතල සහිත ගැලපෙන වානේ කුට්ටි දෙකක් අතර ලෝහ ගසනු ලැබේ, ඒවා ඩයිස් ලෙස හැඳින්වේ. ඩයිස් අතර ලෝහය මිටි කළ විට, එය ඩයි එකේ හැඩයට සමාන හැඩයක් ගනී. එය එහි අවසාන හැඩයට පැමිණි විට, එය සිසිල් කිරීමට පිටතට ගනු ලැබේ. මෙම ක්රියාවලිය නිශ්චිත හැඩයකින් යුත් ශක්තිමත් කොටස් නිෂ්පාදනය කරයි, නමුත් විශේෂිත ඩයිස් සඳහා විශාල ආයෝජනයක් අවශ්ය වේ. අප්සෙට් ෆෝජිං ලෝහ කැබැල්ලක් පැතලි කිරීමෙන් එහි විෂ්කම්භය වැඩි කරයි. එය සාමාන්යයෙන් කුඩා කොටස් සෑදීමට භාවිතා කරයි, විශේෂයෙන් බෝල්ට් සහ නිය වැනි ගාංචු මත හිස් සෑදීමට.
• POWDER METALLURGY / POWDER PROCESSING : නමට අනුව, කුඩුවලින් ඇතැම් ජ්යාමිතීන් සහ හැඩතලවල ඝන කොටස් සෑදීම සඳහා නිෂ්පාදන ක්රියාවලි ඇතුළත් වේ. මේ සඳහා ලෝහ කුඩු භාවිතා කරන්නේ නම් එය කුඩු ලෝහ කර්මාන්තයේ ක්ෂේත්රය වන අතර ලෝහ නොවන කුඩු භාවිතා කරන්නේ නම් එය කුඩු සැකසීමයි. ඝන කොටස් කුඩු වලින් නිපදවනු ලබන්නේ එබීමෙන් සහ සින්ටර් කිරීමෙනි.
POWDER Pressing මගින් කුඩු අවශ්ය හැඩයට සංයුක්ත කිරීමට භාවිතා කරයි. පළමුව, ප්රාථමික ද්රව්යය භෞතිකව කුඩු කර, එය බොහෝ කුඩා තනි අංශු වලට බෙදා ඇත. කුඩු මිශ්රණය ඩයි එකට පුරවා පන්ච් එකක් කුඩු දෙසට ගමන් කර එය අවශ්ය හැඩයට සංයුක්ත කරයි. බොහෝ දුරට කාමර උෂ්ණත්වයේ දී සිදු කරනු ලබන අතර, කුඩු එබීමෙන් ඝන කොටසක් ලබා ගන්නා අතර එය හරිත සංයුක්ත ලෙස හැඳින්වේ. සංයුක්තතාවය වැඩි දියුණු කිරීම සඳහා බයින්ඩර් සහ ලිහිසි තෙල් බහුලව භාවිතා වේ. ටොන් දහස් ගණනක ධාරිතාවයකින් යුත් හයිඩ්රොලික් මුද්රණ යන්ත්ර භාවිතයෙන් කුඩු මුද්රණ යන්ත්ර සෑදීමට අපට හැකියාව ඇත. එසේම අපට ප්රතිවිරුද්ධ ඉහළ සහ පහළ පහරවල් සහිත ද්විත්ව ක්රියා මුද්රණ මෙන්ම අතිශය සංකීර්ණ කොටස් ජ්යාමිතිය සඳහා බහු ක්රියා මුද්රණ ඇත. බොහෝ කුඩු ලෝහ / කුඩු සැකසුම් කම්හල් සඳහා වැදගත් අභියෝගයක් වන ඒකාකාරී බව AGS-TECH සඳහා විශාල ගැටළුවක් නොවේ, මන්ද වසර ගණනාවක් තිස්සේ එවැනි කොටස් අභිරුචි නිෂ්පාදනය කිරීමේ අපගේ පුළුල් අත්දැකීම් නිසාය. ඒකාකාරී බව අභියෝගයක් වන ඝන කොටස් සමඟ පවා අපි සාර්ථක වී ඇත. අපි ඔබේ ව්යාපෘතියට කැපවන්නේ නම්, අපි ඔබේ කොටස් සාදන්නෙමු. අපි කිසියම් විභව අවදානමක් දුටුවහොත්, අපි ඔබට in දන්වන්නෙමු
අත්තිකාරම්.
දෙවන පියවර වන POWDER SINTERING යනු යම් ප්රමාණයකට උෂ්ණත්වය ඉහළ නැංවීම සහ තද කළ කොටසෙහි ඇති කුඩු අංශු එකට බන්ධනය වන පරිදි යම් කාලයක් එම මට්ටමේ උෂ්ණත්වය පවත්වා ගැනීමයි. මෙය වඩාත් ශක්තිමත් බැඳීම් සහ වැඩ කොටස ශක්තිමත් කරයි. සින්ටර් කිරීම කුඩු දියවන උෂ්ණත්වයට ආසන්නව සිදු වේ. සින්ටර් කිරීමේ දී හැකිලීම සිදුවනු ඇත, ද්රව්ය ශක්තිය, ඝනත්වය, ductility, තාප සන්නායකතාවය, විද්යුත් සන්නායකතාවය වැඩි වේ. සින්ටර් කිරීම සඳහා අපට කණ්ඩායමක් සහ අඛණ්ඩ උදුනක් තිබේ. අපගේ එක් හැකියාවක් වන්නේ අප නිෂ්පාදනය කරන කොටස්වල සිදුරු මට්ටම සකස් කිරීමයි. උදාහරණයක් ලෙස කොටස් යම් ප්රමාණයකට සිදුරු සහිතව තබා ගැනීමෙන් ලෝහ පෙරහන් නිපදවීමට අපට හැකි වේ.
IMPREGNATION නම් ශිල්පීය ක්රමයක් භාවිතා කරමින්, අපි ලෝහයේ සිදුරු තෙල් වැනි තරලයකින් පුරවන්නෙමු. අපි උදාහරණයක් ලෙස ස්වයං ලිහිසි තෙල් සහිත ෙබයාරිං නිෂ්පාදනය කරන්නෙමු. INFILTRATION ක්රියාවලියේදී අපි මූලික ද්රව්යයට වඩා අඩු ද්රවාංකයක් ඇති වෙනත් ලෝහයකින් ලෝහයේ සිදුරු පුරවන්නෙමු. මෙම මිශ්රණය ලෝහ දෙකේ ද්රවාංක උෂ්ණත්වය අතර උෂ්ණත්වයකට රත් වේ. එහි ප්රතිඵලයක් වශයෙන් සමහර විශේෂ ගුණාංග ලබා ගත හැකිය. විශේෂ ලක්ෂණ හෝ ගුණාංග ලබා ගැනීමට අවශ්ය වූ විට හෝ අඩු ක්රියාවලි පියවරකින් එම කොටස නිෂ්පාදනය කළ හැකි විට අපි කුඩු නිෂ්පාදනය කරන ලද කොටස් යන්ත්ර කිරීම සහ ව්යාජ ලෙස සකස් කිරීම වැනි ද්විතියික මෙහෙයුම් ද නිතර සිදු කරන්නෙමු.
ISOSTATIC Pressing : මෙම ක්රියාවලියේදී ද්රව පීඩනය කොටස සංයුක්ත කිරීම සඳහා භාවිතා කරයි. ලෝහ කුඩු මුද්රා තැබූ නම්යශීලී කන්ටේනරයකින් සාදන ලද අච්චුවක තබා ඇත. සමස්ථිතික එබීමේදී, සාම්ප්රදායික එබීමේදී දක්නට ලැබෙන අක්ෂීය පීඩනයට පටහැනිව සෑම තැනකින්ම පීඩනය යොදනු ලැබේ. සමස්ථිතික එබීමේ වාසි වන්නේ කොටස තුළ ඒකාකාර ඝනත්වය, විශේෂයෙන් විශාල හෝ ඝන කොටස් සඳහා, උසස් ගුණාංග. එහි අවාසිය නම් දිගු චක්ර කාලය සහ සාපේක්ෂ අඩු ජ්යාමිතික නිරවද්යතාවයයි. COLD ISOSTATIC PRESSING කාමර උෂ්ණත්වයේ දී සිදු කරනු ලබන අතර නම්යශීලී අච්චුව රබර්, PVC හෝ urethane හෝ සමාන ද්රව්ය වලින් සාදා ඇත. පීඩනය හා සංයුක්ත කිරීම සඳහා භාවිතා කරන තරලය තෙල් හෝ ජලය වේ. හරිත සංයුක්තයේ සාම්ප්රදායික සින්ටර් කිරීම මෙය අනුගමනය කරයි. අනෙක් අතට උණුසුම් සමස්ථිතික එබීම ඉහළ උෂ්ණත්වවලදී සිදු කරනු ලබන අතර අච්චු ද්රව්යය උෂ්ණත්වයට ඔරොත්තු දෙන ප්රමාණවත් තරම් ඉහළ ද්රවාංකයක් සහිත තහඩු ලෝහ හෝ සෙරමික් වේ. පීඩන තරල සාමාන්යයෙන් නිෂ්ක්රිය වායුවකි. පීඩන සහ සින්ටර් කිරීමේ මෙහෙයුම් එක් පියවරකින් සිදු කෙරේ. Porosity සම්පූර්ණයෙන්ම පාහේ ඉවත් කර ඇත, uniform grain ව්යුහයක් ලබා ගනී. උණුසුම් සමස්ථිතික එබීමේ වාසිය නම් වාත්තු කිරීම සහ ව්යාජ ලෙස ඒකාබද්ධ කිරීම හා සැසඳිය හැකි කොටස් නිෂ්පාදනය කළ හැකි අතර වාත්තු කිරීම සහ ව්යාජ ලෙස සකස් කිරීම සඳහා සුදුසු නොවන ද්රව්ය භාවිතා කිරීමට හැකි වීමයි. උණුසුම් සමස්ථිතික එබීමේ අවාසිය නම් එහි ඉහළ චක්රීය කාලය වන අතර එම නිසා පිරිවැයයි. එය අඩු පරිමාවක තීරණාත්මක කොටස් සඳහා සුදුසු වේ.
ලෝහ ඉන්ජෙක්ෂන් මෝල්ඩින්: සිහින් බිත්ති සහ සවිස්තරාත්මක ජ්යාමිතිය සහිත සංකීර්ණ කොටස් නිෂ්පාදනය සඳහා ඉතා සුදුසු ක්රියාවලිය. කුඩා කොටස් සඳහා වඩාත් සුදුසුය. කුඩු සහ පොලිමර් බයින්ඩර් මිශ්ර කර, රත් කර අච්චුවකට එන්නත් කරනු ලැබේ. පොලිමර් බයින්ඩර් කුඩු අංශුවල මතුපිට ආවරණය කරයි. වාත්තු කිරීමෙන් පසු, ද්රාවකයක් භාවිතයෙන් ද්රාවණය කරන ලද අඩු උෂ්ණත්ව උණුසුමකින් බන්ධනය ඉවත් කරනු ලැබේ.
රෝල් සංයුක්ත කිරීම / කුඩු පෙරළීම : අඛණ්ඩ තීරු හෝ පත්රය නිෂ්පාදනය කිරීමට කුඩු භාවිතා වේ. කුඩු පෝෂකයකින් පෝෂණය වන අතර භ්රමණය වන රෝල් දෙකකින් පත්ර හෝ තීරු බවට සංයුක්ත වේ. මෙහෙයුම සීතල සිදු කරනු ලැබේ. පත්රය සින්ටර් උදුනකට ගෙන යනු ලැබේ. සින්ටර් කිරීමේ ක්රියාවලිය දෙවන වරටත් නැවත නැවතත් කළ හැක.
POWDER EXTRUSION : විශාල දිග සහ විෂ්කම්භය අනුපාත සහිත කොටස් තුනී තහඩු ලෝහ භාජනයක් කුඩු සමග නිස්සාරණය කිරීමෙන් නිෂ්පාදනය කෙරේ.
LOOSE SINTERING : නමට අනුව, එය පීඩන රහිත සංයුක්ත සහ සින්ටර් කිරීමේ ක්රමයකි, ලෝහ පෙරහන් වැනි ඉතා සිදුරු සහිත කොටස් නිෂ්පාදනය කිරීම සඳහා සුදුසු වේ. කුඩු සංයුක්ත කිරීමකින් තොරව පුස් කුහරයට පෝෂණය වේ.
LOOSE SINTERING : නමට අනුව, එය පීඩන රහිත සංයුක්ත සහ සින්ටර් කිරීමේ ක්රමයකි, ලෝහ පෙරහන් වැනි ඉතා සිදුරු සහිත කොටස් නිෂ්පාදනය කිරීම සඳහා සුදුසු වේ. කුඩු සංයුක්ත කිරීමකින් තොරව පුස් කුහරයට පෝෂණය වේ.
SPARK SINTERING : කුඩු ප්රතිවිරුද්ධ පන්ච් දෙකකින් අච්චුවේ සම්පීඩිත වන අතර අධි බලැති විදුලි ධාරාවක් පන්ච් වෙත යොදන අතර ඒවා අතර සැන්ඩ්විච් කර ඇති සංයුක්ත කුඩු හරහා ගමන් කරයි. අධික ධාරාව කුඩු අංශු වලින් මතුපිට පටල පුළුස්සා දමන අතර ජනනය වන තාපය සමඟ ඒවා සින්ටර් කරයි. ක්රියාවලිය වේගවත් වන්නේ තාපය පිටතින් යොදන්නේ නැති නිසා ඒ වෙනුවට එය අච්චුව තුළින් ජනනය වන බැවිනි.
HOT Pressing : අධික උෂ්ණත්වයට ඔරොත්තු දිය හැකි අච්චුවක තනි පියවරකින් කුඩු තද කර සින්ටර් කර ඇත. ඩයි එක සංයුක්ත වන විට කුඩු තාපය එයට යොදනු ලැබේ. මෙම ක්රමය මගින් අත්පත් කරගත් හොඳ නිරවද්යතාවන් සහ යාන්ත්රික ගුණාංග එය ආකර්ශනීය විකල්පයක් බවට පත් කරයි. වර්තන ලෝහ පවා මිනිරන් වැනි පුස් ද්රව්ය භාවිතයෙන් සැකසිය හැක.