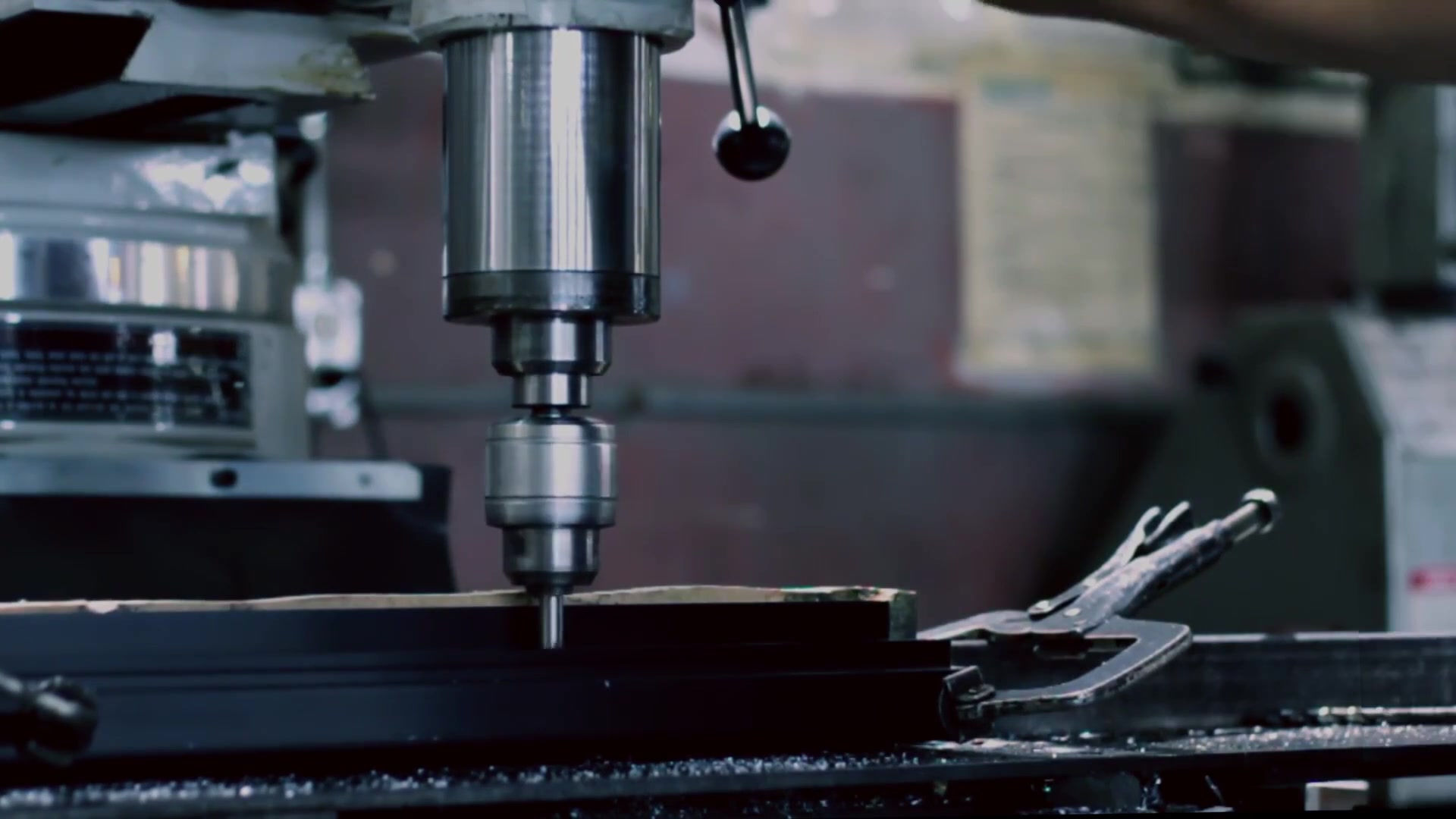
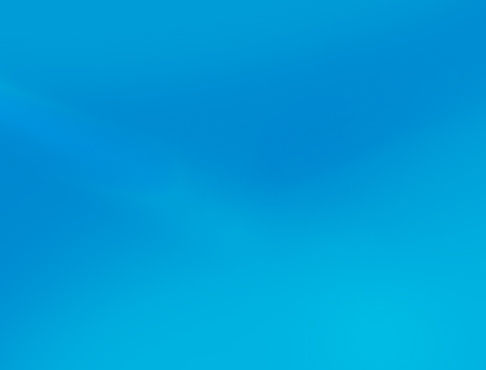
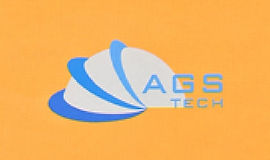
Глобални произвођач по мери, интегратор, консолидатор, спољни партнер за широку палету производа и услуга.
_д04а07д8-9цд1-3239-9149-20813д6ц673б_
Ми смо ваш извор на једном месту за производњу, фабриковање, инжењеринг, консолидацију, интеграцију, екстернализацију производа и услуга произведених по наруџби и готових производа.
Изаберите свој језик
-
Цустом Мануфацтуринг
-
Домаћа и глобална производња по уговору
-
Оутсоурцинг производње
-
Домаће и глобалне набавке
-
Цонсолидатион_д04а07д8-9цд1-3239-9149-20813д6ц673б_
-
Енгинееринг Интегратион_д04а07д8-9цд1-3239-9149-20813д6ц673б_
-
Инжењерске услуге
Последњих година, приметили смо пораст потражње за БРЗОМ ПРОИЗВОДњом или БРЗОМ ИЗРАДОМ ПРОТОТИПА. Овај процес се такође може назвати ПРОИЗВОДЊА СТОЛА или ИЗРАДА СЛОБОДНЕ ФОРМЕ. У основи, чврст физички модел дела се прави директно из тродимензионалног ЦАД цртежа. Користимо термин АДИТИВНА ПРОИЗВОДЊА за ове различите технике где градимо делове у слојевима. Користећи интегрисани компјутерски вођен хардвер и софтвер вршимо адитивну производњу. Наше брзе технике израде прототипа и производње су СТЕРЕОЛИТОГРАФИЈА, ПОЛИЈЕТ, МОДЕЛИРАЊЕ ФУСЕД-ДЕПОСИТИОН, СЕЛЕКТИВНО ЛАСЕРСКО СИНТЕРИНГ, ТОПЉЕЊЕ ЕЛЕКТРОНСКИМ СНОМ, ТРОДИМЕНЗИОНАЛНА ШТАМПА, ДИРЕКТНА ПРОИЗВОДЊА, БРЗИ АЛАТИ. Препоручујемо вам да кликнете овде да бистеПРЕУЗМИТЕ наше шематске илустрације адитивне производње и брзих производних процеса од стране АГС-ТЕЦХ Инц._цц781905-5цде-3194-бб3б-136бад5цф58д_
Ово ће вам помоћи да боље разумете информације које вам пружамо у наставку._цц781905-5цде-3194-бб3б-136бад5цф58д_
_цц781905-5цде-3194-бб3б-136бад5цф58д_
Брза израда прототипа нам омогућава: 1.) Концептуални дизајн производа се посматра из различитих углова на монитору користећи 3Д/ЦАД систем. 2.) Прототипови од неметалних и металних материјала се производе и проучавају са функционалног, техничког и естетског аспекта. 3.) Израда прототипа по ниској цени у врло кратком времену је постигнута. Адитивна производња може да личи на израду векне хлеба слагањем и лепљењем појединачних кришки једна на другу. Другим речима, производ се производи парче по кришку, или слој по слој наносе један на други. Већина делова се може произвести у року од неколико сати. Техника је добра ако су делови потребни веома брзо или ако су потребне количине мале, а прављење калупа и алата је прескупо и одузима време. Међутим, цена дела је скупа због скупих сировина._цц781905-5цде-3194-бб3б-136бад5цф58д_
_цц781905-5цде-3194-бб3б-136бад5цф58д_
• СТЕРЕОЛИТОГРАФИЈА: Ова техника такође скраћено СТЛ, заснована је на очвршћавању и очвршћавању течног фотополимера у одређени облик фокусирањем ласерског зрака на њега. Ласер полимеризује фотополимер и лечи га. Скенирањем УВ ласерског зрака према програмираном облику дуж површине фотополимерне мешавине, део се производи одоздо према горе у појединачним кришкама распоређеним једна на другу. Скенирање ласерске тачке се понавља много пута да би се постигле геометрије програмиране у систему. Након што је део потпуно произведен, скида се са платформе, упија и чисти ултразвучно и алкохолном купком. Затим се излаже УВ зрачењу неколико сати како би се уверио да је полимер потпуно очврснуо и очврснуо. Да сумирамо процес, платформа која је уроњена у мешавину фотополимера и УВ ласерски сноп се контролишу и померају кроз серво-контролни систем према облику жељеног дела и део се добија фотоочвршћавањем полимера слој по слој. Наравно, максималне димензије произведеног дела су одређене стереолитографском опремом._цц781905-5цде-3194-бб3б-136бад5цф58д_
_цц781905-5цде-3194-бб3б-136бад5цф58д_
• ПОЛИЈЕТ : Слично инкјет штампи, у полијет штампачу имамо осам глава за штампање које наносе фотополимер на лежиште. Ултраљубичасто светло постављено поред млазница одмах очвршћава и очвршћава сваки слој. У полијет-у се користе два материјала. Први материјал је за производњу стварног модела. Други материјал, смола слична гелу, користи се за подршку. Оба ова материјала се наносе слој по слој и истовремено очвршћавају. _цц781905-5цде-3194-бб3б-136бад5цф58д_Након завршетка модела, потпорни материјал се уклања воденим раствором. Смоле које се користе су сличне стереолитографији (СТЛ). Полијет има следеће предности у односу на стереолитографију: 1.) Нема потребе за чишћењем делова. 2.) Нема потребе за постпроцесним очвршћавањем 3.) Мање дебљине слојева су могуће и на тај начин добијамо бољу резолуцију и можемо произвести финије делове.
_цц781905-5цде-3194-бб3б-136бад5цф58д_
• МОДЕЛИРАЊЕ ФУСЕД ДЕПОСИТИОН МОДЕЛИНГ : Такође скраћено као ФДМ, у овој методи глава екструдера контролисана роботом креће се у два основна правца преко стола. Кабл се спушта и подиже по потреби. Из отвора загрејане матрице на глави, екструдира се термопластични филамент и почетни слој се наноси на темељ од пене. Ово се постиже помоћу главе екструдера која прати унапред одређену путању. Након почетног слоја, сто се спушта и наредни слојеви се наносе један на други. Понекад су приликом производње компликованог дела потребне потпорне структуре како би се таложење могло наставити у одређеним правцима. У овим случајевима, потпорни материјал се екструдира са мање густим размаком филамента на слоју тако да је слабији од материјала модела. Ове потпорне структуре се касније могу растворити или одломити након завршетка дела. Димензије матрице за екструдер одређују дебљину екструдираних слојева. ФДМ процес производи делове са степенастим површинама на косим спољашњим равнима. Ако је ова храпавост неприхватљива, може се користити полирање хемијском паром или загрејани алат за њихово изглађивање. Чак је и восак за полирање доступан као материјал за премазивање да би се елиминисали ови кораци и постигле разумне геометријске толеранције. _цц781905-5цде-3194-бб3б-136бад5цф58д_ _цц781905-5цде-3194-бб3б-136бад5цф58д_
_цц781905-5цде-3194-бб3б-136бад5цф58д_
• СЕЛЕКТИВНО ЛАСЕРСКО СИНТЕРИНГ: Такође означен као СЛС, процес се заснива на синтеровању полимера, керамичких или металних прахова селективно у објекат. Дно коморе за обраду има два цилиндра: цилиндар делимично грађени и цилиндар за довод праха. Први се постепено спушта до места где се формира синтеровани део, а други се постепено подиже да би довео прах у цилиндар за израду делова кроз механизам са ваљцима. Прво се танак слој праха нанесе у цилиндар са делимично грађеним, а затим се ласерски зрак фокусира на тај слој, пратећи и топи/синтерујући одређени попречни пресек, који се затим поново учвршћује у чврсту материју. Пудер је подручја која нису погођена ласерским зраком остају лабави, али и даље подржавају чврсти део. Затим се наноси још један слој праха и процес се понавља много пута да би се добио део. На крају се растресите честице праха. Све ово изводи компјутер за контролу процеса користећи упутства генерисана 3Д ЦАД програмом дела који се производи. Могу се депоновати различити материјали као што су полимери (као што су АБС, ПВЦ, полиестер), восак, метали и керамика са одговарајућим полимерним везивом.
_цц781905-5цде-3194-бб3б-136бад5цф58д_
• ЕЛЕКТРОНСКИ ЗРАК _цц781905-5цде-3194-бб3б-136бад5цф58д_ТОЉЕЊЕ: Слично селективном ласерском синтеровању, али коришћењем електронског зрака за топљење праха титанијума или кобалт хрома за прављење прототипова у вакууму. Неки развоји су направљени за извођење овог процеса на нерђајућим челицима, алуминијуму и легурама бакра. Ако је потребно повећати отпорност на замор произведених делова, користимо топло изостатичко пресовање након производње делова као секундарни процес. _цц781905-5цде-3194-бб3б-136бад5цф58д__цц781905-5цде-3194-бб3б-136бад5цф58д_
_цц781905-5цде-3194-бб3б-136бад5цф58д_
• ТРОДИМЕНЗИОНАЛНО ШТАМПАЊЕ: Такође означено са 3ДП, у овој техници глава штампача наноси неорганско везиво на слој неметалног или металног праха. Клип који носи слој праха се постепено спушта и на сваком кораку везиво се наноси _цц781905-5цде-3194-бб3б-136бад5цф58д_слој по слој и спаја везиво. Прашкасти материјали који се користе су мешавине полимера и влакана, ливнички песак, метали. Коришћењем различитих глава везива истовремено и везива различитих боја можемо добити различите боје. Процес је сличан инкјет штампи, али уместо добијања обојеног листа добијамо обојени тродимензионални објекат. Произведени делови могу бити порозни и стога могу захтевати синтеровање и инфилтрацију метала да би се повећала његова густина и чврстоћа. Синтеровањем ће сагорети везиво и спојити метални прах заједно. Метали као што су нерђајући челик, алуминијум, титанијум се могу користити за израду делова, а као материјал за инфилтрацију обично користимо бакар и бронзу. Лепота ове технике је у томе што се чак и компликовани и покретни склопови могу произвести веома брзо. На пример, склоп зупчаника, кључ као алат може се направити и имаће покретне и окретне делове спремне за употребу. Различите компоненте склопа могу се произвести у различитим бојама и све у једном тренутку._цц781905-5цде-3194-бб3б-136бад5цф58д_ Преузмите нашу брошуру на:Основе металног 3Д штампања
_цц781905-5цде-3194-бб3б-136бад5цф58д_
• ДИРЕКТНА ПРОИЗВОДЊА и БРЗИ АЛАТИ: Поред процене дизајна, решавања проблема користимо брзу израду прототипа за директну производњу производа или директну примену у производе. Другим речима, брза израда прототипа се може уградити у конвенционалне процесе како би били бољи и конкурентнији. На пример, брза израда прототипа може да произведе обрасце и калупе. Обрасци топљења и сагоревања полимера који се стварају брзим операцијама израде прототипа могу се саставити за ливење и уложити. Други пример који треба поменути је коришћење 3ДП-а за производњу љуске за ливење керамике и коришћење за операције ливења љуске. Чак се и калупи за бризгање и уметци калупа могу произвести брзим прототипом и може се уштедети много недеља или месеци времена израде калупа. Само анализом ЦАД датотеке жељеног дела, можемо произвести геометрију алата помоћу софтвера. Ево неких од наших популарних брзих метода алата:
РТВ (Вулканизација на собној температури) МОЛДИНГ / УРЕТАНО ЛИВАЊЕ : Коришћење брзог прототипа може се користити за прављење шаблона жељеног дела. Затим се овај узорак премазује средством за раздвајање и течна РТВ гума се сипа преко шаре да би се добиле половине калупа. Затим, ове половине калупа се користе за бризгање течних уретана. Век трајања калупа је кратак, само 0 или 30 циклуса, али довољно за производњу малих серија._цц781905-5цде-3194-бб3б-136бад5цф58д_
АЦЕС (Ацетал Цлеар Епоки Солид) ИЊЕКТИРАЊЕ: Користећи технике брзе израде прототипа као што је стереолитографија, производимо калупе за ињектирање. Ови калупи су шкољке са отвореним крајем како би се омогућило пуњење материјалима као што су епоксид, епоксид пуњен алуминијумом или метали. Опет је век трајања калупа ограничен на десетине или највише стотине делова._цц781905-5цде-3194-бб3б-136бад5цф58д_
ПРОЦЕС ПРСКАЊЕГ МЕТАЛНИХ АЛАТА: Користимо брзу израду прототипа и правимо шаблон. Попрскамо легуру цинк-алуминијум на површину узорка и премажемо је. Узорак са металним премазом се затим ставља у боцу и прелива са епоксидом или алуминијумом пуњеним епоксидом. На крају се уклања и израдом две такве половине калупа добијамо комплетан калуп за бризгање. Ови калупи имају дужи животни век, у неким случајевима у зависности од материјала и температуре могу произвести делове у хиљадама._цц781905-5цде-3194-бб3б-136бад5цф58д_
КЕЕЛТООЛ ПРОЦЕС: Ова техника може произвести калупе са животним циклусом од 100.000 до 10 милиона. Користећи брзу израду прототипа производимо РТВ калуп. Калуп се затим напуни мешавином која се састоји од праха алатног челика А6, волфрамовог карбида, полимерног везива и остави да се очврсне. Овај калуп се затим загрева да би се полимер сагорео и метални прах спојио. _цц781905-5цде-3194-бб3б-136бад5цф58д_Следећи корак је инфилтрација бакра за производњу коначног калупа. Ако је потребно, секундарне операције као што су обрада и полирање могу се извршити на калупу за бољу тачност димензија. _цц781905-5цде-3194-бб3б-136бад5цф58д_ _цц781905-5цде-3194-бб3б-136бад5цф58д__цц781905-5цде-3194-бб3б-1356бад_