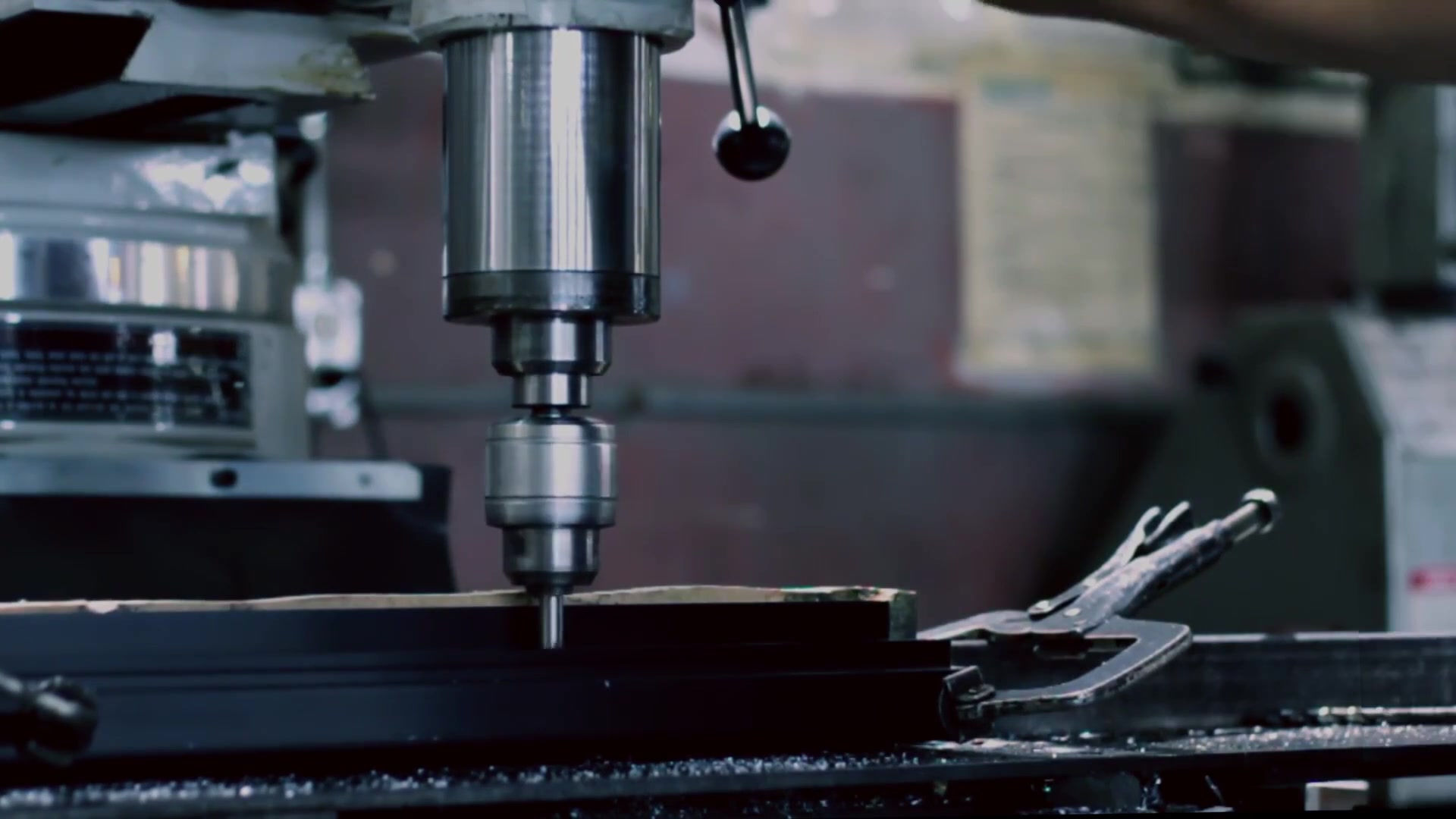
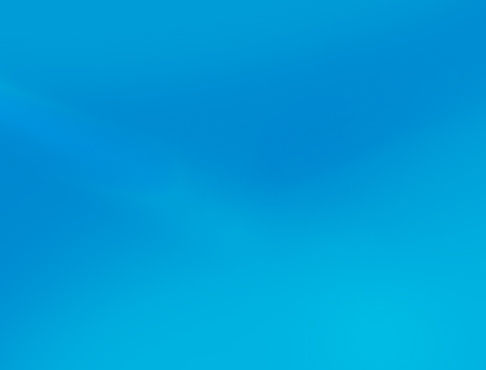
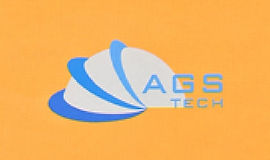
ผู้ผลิตที่กำหนดเองระดับโลก ผู้รวบรวม ผู้รวบรวม พันธมิตรเอาท์ซอร์สสำหรับผลิตภัณฑ์และบริการที่หลากหลาย
เราเป็นแหล่งข้อมูลครบวงจรสำหรับการผลิต การแปรรูป วิศวกรรม การรวมบัญชี การบูรณาการ การเอาท์ซอร์สผลิตภัณฑ์และบริการที่ผลิตขึ้นเองและนอกชั้นวาง
เลือกภาษาของคุณ
-
การผลิตแบบกำหนดเอง
-
การผลิตตามสัญญาในประเทศและทั่วโลก
-
การผลิตเอาท์ซอร์ส
-
การจัดซื้อจัดจ้างในประเทศและทั่วโลก
-
การรวมบัญชี
-
การรวมทางวิศวกรรม
-
บริการด้านวิศวกรรม
ในบรรดาเทคนิค JOINING ต่างๆ ที่เราปรับใช้ในการผลิต เราให้ความสำคัญเป็นพิเศษกับ WELDING, BRAZING, SOLDERING, ADHESIVE BONDING และ CUSTOM MECHANICAL ASSEMBLY เนื่องจากเทคนิคเหล่านี้ใช้กันอย่างแพร่หลายในการใช้งาน เช่น การผลิตชุดประกอบสุญญากาศ การผลิตผลิตภัณฑ์ไฮเทค และการปิดผนึกเฉพาะทาง ในที่นี้เราจะเน้นเฉพาะด้านที่เชี่ยวชาญมากขึ้นของเทคนิคการต่อเชื่อมเหล่านี้ เนื่องจากเกี่ยวข้องกับการผลิตผลิตภัณฑ์และส่วนประกอบขั้นสูง
การเชื่อมแบบฟิวชั่น: เราใช้ความร้อนในการหลอมและรวมวัสดุเข้าด้วยกัน ความร้อนมาจากไฟฟ้าหรือคานพลังงานสูง ประเภทของการเชื่อมแบบฟิวชันที่เราปรับใช้ ได้แก่ การเชื่อมด้วยแก๊สออกซิเจน, การเชื่อมอาร์ค, การเชื่อมด้วยลำแสงพลังงานสูง
การเชื่อมแบบ SOLID-STATE: เราเชื่อมชิ้นส่วนโดยไม่หลอมละลายและหลอมละลาย วิธีการเชื่อมแบบโซลิดสเตตของเรามีทั้งแบบเย็น แบบอัลตราโซนิก ความต้านทาน แรงเสียดทาน การเชื่อมแบบระเบิด และการเชื่อมแบบกระจาย
การประสานและการบัดกรี: พวกเขาใช้โลหะฟิลเลอร์และทำให้เราได้เปรียบในการทำงานที่อุณหภูมิต่ำกว่าในการเชื่อม ซึ่งทำให้ผลิตภัณฑ์เสียหายทางโครงสร้างน้อยลง ข้อมูลเกี่ยวกับโรงงานประสานของเราที่ผลิตอุปกรณ์เซรามิกกับโลหะ การซีลสุญญากาศ การป้อนผ่านสุญญากาศ ส่วนประกอบควบคุมสุญญากาศและของเหลวสูงและสูงพิเศษ สามารถพบได้ที่นี่:โบรชัวร์โรงงานประสาน
การยึดติดด้วยกาว: เนื่องจากความหลากหลายของกาวที่ใช้ในอุตสาหกรรมและการใช้งานที่หลากหลาย เราจึงมีหน้าเฉพาะสำหรับสิ่งนี้ หากต้องการไปยังหน้าเกี่ยวกับการติดกาว โปรดคลิกที่นี่
การประกอบกลไกแบบกำหนดเอง: เราใช้รัดต่างๆ เช่น สลักเกลียว สกรู น็อต หมุดย้ำ ตัวยึดของเราไม่ได้จำกัดอยู่แค่ตัวยึดแบบมาตรฐานนอกชั้นวาง เราออกแบบ พัฒนา และผลิตตัวยึดแบบพิเศษที่ทำจากวัสดุที่ไม่ได้มาตรฐานเพื่อให้ตรงตามข้อกำหนดสำหรับการใช้งานพิเศษ บางครั้งต้องการการนำไฟฟ้าหรือความร้อนที่ไม่เป็นสื่อกระแสไฟฟ้าในขณะที่บางครั้งก็ต้องการการนำไฟฟ้า สำหรับการใช้งานพิเศษบางอย่าง ลูกค้าอาจต้องการรัดพิเศษที่ไม่สามารถถอดออกได้โดยไม่ทำลายผลิตภัณฑ์ มีแนวคิดและการใช้งานที่ไม่สิ้นสุด เรามีทุกอย่างให้คุณ หากไม่ขายหน้าร้าน เราก็สามารถพัฒนาได้อย่างรวดเร็ว ไปที่หน้าของเราเกี่ยวกับการประกอบเครื่องจักร โปรดคลิกที่นี่. ให้เราตรวจสอบเทคนิคการเข้าร่วมแบบต่างๆ ในรายละเอียดเพิ่มเติม
OXYFUEL GAS WELDING (OFW): เราใช้ก๊าซเชื้อเพลิงผสมกับออกซิเจนเพื่อผลิตเปลวไฟเชื่อม เมื่อเราใช้อะเซทิลีนเป็นเชื้อเพลิงและออกซิเจน เราเรียกว่าการเชื่อมด้วยแก๊สออกซีอะเซทิลีน ปฏิกิริยาเคมีสองอย่างเกิดขึ้นในกระบวนการเผาไหม้ก๊าซออกซีฟูเอล:
C2H2 + O2 ------» 2CO + H2 + ความร้อน
2CO + H2 + 1.5 O2---------» 2 CO2 + H2O + ความร้อน
ปฏิกิริยาแรกแยกอะเซทิลีนออกเป็นคาร์บอนมอนอกไซด์และไฮโดรเจนในขณะที่สร้างความร้อนขึ้นประมาณ 33% กระบวนการที่สองข้างต้นแสดงถึงการเผาไหม้เพิ่มเติมของไฮโดรเจนและคาร์บอนมอนอกไซด์ในขณะที่ผลิตความร้อนประมาณ 67% ของความร้อนทั้งหมด อุณหภูมิในเปลวไฟอยู่ระหว่าง 1533 ถึง 3573 เคลวิน เปอร์เซ็นต์ออกซิเจนในส่วนผสมของแก๊สมีความสำคัญ หากปริมาณออกซิเจนมากกว่าครึ่งหนึ่ง เปลวไฟจะกลายเป็นตัวออกซิไดซ์ สิ่งนี้ไม่พึงปรารถนาสำหรับโลหะบางชนิด แต่เป็นที่ต้องการสำหรับโลหะอื่นๆ ตัวอย่างเมื่อต้องการออกซิไดซ์เปลวไฟคือโลหะผสมที่มีทองแดงเป็นส่วนประกอบเนื่องจากจะสร้างชั้นฟิล์มบนโลหะ ในทางกลับกัน เมื่อปริมาณออกซิเจนลดลง การเผาไหม้ทั้งหมดจะไม่สามารถทำได้และเปลวไฟจะกลายเป็นเปลวไฟรีดิวซ์ (คาร์บูไรซิ่ง) อุณหภูมิในเปลวไฟรีดิวซ์จะต่ำกว่า ดังนั้นจึงเหมาะสำหรับกระบวนการต่างๆ เช่น การบัดกรีและการประสาน ก๊าซอื่นๆ ก็เป็นเชื้อเพลิงที่มีศักยภาพเช่นกัน แต่ก็มีข้อเสียอยู่บ้างเมื่อเทียบกับอะเซทิลีน ในบางครั้ง เราจัดหาโลหะเติมให้กับบริเวณรอยเชื่อมในรูปแบบของแท่งหรือลวดเติม บางส่วนถูกเคลือบด้วยฟลักซ์เพื่อชะลอการเกิดออกซิเดชันของพื้นผิว และด้วยเหตุนี้จึงปกป้องโลหะหลอมเหลว ประโยชน์เพิ่มเติมที่ฟลักซ์มอบให้คือการกำจัดออกไซด์และสารอื่นๆ ออกจากบริเวณรอยเชื่อม สิ่งนี้นำไปสู่การยึดติดที่แน่นแฟ้นยิ่งขึ้น รูปแบบของการเชื่อมด้วยแก๊สออกซีเชื้อเพลิงคือ PRESSURE GAS WELDING ซึ่งส่วนประกอบทั้งสองจะถูกทำให้ร้อนที่ส่วนต่อประสานโดยใช้หัวเชื่อมก๊าซออกซีอะเซทิลีน และเมื่อส่วนต่อประสานเริ่มละลาย คบเพลิงจะถูกถอนออกและใช้แรงตามแนวแกนเพื่อกดทั้งสองส่วนเข้าด้วยกัน จนกว่าอินเทอร์เฟซจะแข็งตัว
การเชื่อมอาร์ค: เราใช้พลังงานไฟฟ้าเพื่อสร้างส่วนโค้งระหว่างปลายอิเล็กโทรดกับชิ้นส่วนที่จะเชื่อม แหล่งจ่ายไฟสามารถเป็น AC หรือ DC ในขณะที่อิเล็กโทรดเป็นวัสดุสิ้นเปลืองหรือไม่สิ้นเปลือง การถ่ายเทความร้อนในการเชื่อมอาร์คสามารถแสดงได้โดยสมการต่อไปนี้:
H / l = อดีต VI / v
H คืออินพุตความร้อน l คือความยาวเชื่อม V และ I คือแรงดันและกระแสที่ใช้ v คือความเร็วในการเชื่อม และ e คือประสิทธิภาพของกระบวนการ ยิ่งประสิทธิภาพ “e” สูงขึ้นเท่าใด พลังงานที่มีอยู่ก็จะถูกนำมาใช้ในการหลอมวัสดุให้เกิดประโยชน์มากขึ้นเท่านั้น อินพุตความร้อนยังสามารถแสดงเป็น:
H = ux (ระดับเสียง) = ux A xl
นี่คือพลังงานจำเพาะสำหรับการหลอม A คือหน้าตัดของรอยเชื่อมและ l ความยาวเชื่อม จากสมการทั้งสองข้างต้น เราจะได้:
v = อดีต VI / u A
รูปแบบหนึ่งของการเชื่อมอาร์กคือ SHIELDED METAL ARC WELDING (SMAW) ซึ่งคิดเป็นประมาณ 50% ของกระบวนการเชื่อมอุตสาหกรรมและการบำรุงรักษาทั้งหมด การเชื่อมอาร์คด้วยไฟฟ้า (STICK WELDING) ทำได้โดยการสัมผัสส่วนปลายของอิเล็กโทรดที่เคลือบเข้ากับชิ้นงาน และดึงออกอย่างรวดเร็วจนถึงระยะที่เพียงพอต่อการคงส่วนโค้งไว้ เราเรียกกระบวนการนี้ว่าการเชื่อมแบบติดเพราะอิเล็กโทรดเป็นแท่งที่บางและยาว ในระหว่างกระบวนการเชื่อม ปลายของอิเล็กโทรดจะละลายพร้อมกับการเคลือบและโลหะฐานในบริเวณใกล้เคียงกับส่วนโค้ง ส่วนผสมของโลหะฐาน โลหะอิเล็กโทรด และสารจากการเคลือบอิเล็กโทรดจะแข็งตัวในบริเวณรอยเชื่อม การเคลือบอิเล็กโทรดจะขจัดออกซิไดซ์และให้ก๊าซป้องกันในบริเวณรอยเชื่อม ดังนั้นจึงป้องกันจากออกซิเจนในสิ่งแวดล้อม ดังนั้นกระบวนการนี้จึงเรียกว่าการเชื่อมอาร์กโลหะแบบหุ้มฉนวน เราใช้กระแสระหว่าง 50 ถึง 300 แอมแปร์และระดับพลังงานโดยทั่วไปน้อยกว่า 10 กิโลวัตต์เพื่อประสิทธิภาพการเชื่อมที่เหมาะสมที่สุด สิ่งที่สำคัญก็คือขั้วของกระแสไฟตรง (ทิศทางการไหลของกระแส) ควรใช้ขั้วตรงที่ชิ้นงานเป็นบวกและขั้วไฟฟ้าเป็นลบในการเชื่อมโลหะแผ่นเนื่องจากมีการแทรกซึมที่ตื้นและสำหรับข้อต่อที่มีช่องว่างกว้างมาก เมื่อเรามีขั้วย้อนกลับ กล่าวคือ อิเล็กโทรดเป็นบวกและลบของชิ้นงาน เราสามารถเจาะรอยเชื่อมได้ลึกขึ้น ด้วยกระแสไฟ AC เนื่องจากเรามีส่วนโค้งเป็นจังหวะ เราจึงสามารถเชื่อมส่วนที่หนาได้โดยใช้อิเล็กโทรดขนาดเส้นผ่านศูนย์กลางขนาดใหญ่และกระแสสูงสุด วิธีการเชื่อม SMAW เหมาะสำหรับชิ้นงานที่มีความหนาตั้งแต่ 3 ถึง 19 มม. และมากยิ่งขึ้นโดยใช้เทคนิคหลายรอบ ตะกรันที่เกิดขึ้นที่ด้านบนของรอยเชื่อมจะต้องถูกลบออกโดยใช้แปรงลวด เพื่อไม่ให้เกิดการกัดกร่อนและความล้มเหลวที่บริเวณรอยเชื่อม แน่นอนว่าสิ่งนี้จะเพิ่มค่าใช้จ่ายในการเชื่อมอาร์คโลหะที่มีฉนวนหุ้ม อย่างไรก็ตาม SMAW เป็นเทคนิคการเชื่อมที่ได้รับความนิยมมากที่สุดในอุตสาหกรรมและงานซ่อมแซม
การเชื่อมอาร์คใต้น้ำ (SAW): ในขั้นตอนนี้ เราป้องกันส่วนโค้งของรอยเชื่อมโดยใช้วัสดุฟลักซ์ที่เป็นเม็ด เช่น มะนาว ซิลิกา แคลเซียมฟลอไรด์ แมงกานีสออกไซด์….เป็นต้น ฟลักซ์แบบแกรนูลจะถูกป้อนเข้าสู่บริเวณรอยเชื่อมโดยแรงโน้มถ่วงที่ไหลผ่านหัวฉีด ฟลักซ์ที่ปกคลุมบริเวณรอยเชื่อมหลอมเหลวช่วยปกป้องจากประกายไฟ ควัน รังสียูวี….ฯลฯ และทำหน้าที่เป็นฉนวนความร้อน จึงปล่อยให้ความร้อนแทรกซึมลึกเข้าไปในชิ้นงาน ฟลักซ์ที่ยังไม่ได้หลอมจะถูกกู้คืน บำบัด และนำกลับมาใช้ใหม่ ขดลวดเปลือยใช้เป็นอิเล็กโทรดและป้อนผ่านท่อไปยังพื้นที่เชื่อม เราใช้กระแสระหว่าง 300 ถึง 2000 แอมแปร์ กระบวนการเชื่อมอาร์กใต้น้ำ (SAW) ถูกจำกัดให้อยู่ในตำแหน่งแนวนอนและแนวราบ และการเชื่อมแบบวงกลม หากการหมุนของโครงสร้างวงกลม (เช่น ท่อ) เป็นไปได้ในระหว่างการเชื่อม ความเร็วสามารถเข้าถึง 5 เมตร/นาที กระบวนการ SAW เหมาะสำหรับแผ่นหนาและให้รอยเชื่อมคุณภาพสูง เหนียว เหนียว และสม่ำเสมอ ความสามารถในการผลิต นั่นคือปริมาณของวัสดุเชื่อมที่ฝากต่อชั่วโมงคือ 4 ถึง 10 เท่าของปริมาณเมื่อเทียบกับกระบวนการ SMAW
กระบวนการเชื่อมอาร์กอีกรูปแบบหนึ่งคือ GAS METAL ARC WELDING (GMAW) หรือเรียกอีกอย่างว่า METAL INERT GAS WELDING (MIG) ขึ้นอยู่กับพื้นที่เชื่อมที่มีการป้องกันจากแหล่งก๊าซภายนอก เช่น ฮีเลียม อาร์กอน คาร์บอนไดออกไซด์….เป็นต้น อาจมีสารขจัดออกซิไดซ์เพิ่มเติมอยู่ในโลหะอิเล็กโทรด ลวดสิ้นเปลืองจะถูกป้อนผ่านหัวฉีดเข้าไปในบริเวณรอยเชื่อม การผลิตที่เกี่ยวข้องกับบอทเหล็กและโลหะนอกกลุ่มเหล็กจะดำเนินการโดยใช้การเชื่อมอาร์กโลหะด้วยแก๊ส (GMAW) ความสามารถในการเชื่อมประมาณ 2 เท่าของกระบวนการ SMAW กำลังใช้อุปกรณ์เชื่อมอัตโนมัติ โลหะถูกถ่ายโอนด้วยวิธีใดวิธีหนึ่งจากสามวิธีในกระบวนการนี้: “การถ่ายเทด้วยสเปรย์” เกี่ยวข้องกับการถ่ายโอนหยดโลหะขนาดเล็กหลายร้อยเม็ดต่อวินาทีจากอิเล็กโทรดไปยังบริเวณรอยเชื่อม ในอีกทางหนึ่ง "Globular Transfer" ใช้ก๊าซที่อุดมด้วยคาร์บอนไดออกไซด์และโลหะหลอมเหลวที่หลอมละลายถูกขับเคลื่อนด้วยอาร์คไฟฟ้า กระแสเชื่อมสูงและเชื่อมเจาะลึก ความเร็วในการเชื่อมมากกว่าในการถ่ายโอนสเปรย์ ดังนั้นการถ่ายโอนแบบทรงกลมจะดีกว่าสำหรับการเชื่อมส่วนที่หนักกว่า สุดท้าย ในวิธี "การลัดวงจรไฟฟ้า" ปลายอิเล็กโทรดจะสัมผัสกับบ่อเชื่อมที่หลอมละลาย ทำให้เกิดไฟฟ้าลัดวงจรในขณะที่โลหะในอัตรามากกว่า 50 หยด/วินาที จะถูกถ่ายโอนในแต่ละหยด ใช้กระแสและแรงดันไฟต่ำร่วมกับลวดทินเนอร์ กำลังไฟฟ้าที่ใช้ประมาณ 2 กิโลวัตต์และอุณหภูมิค่อนข้างต่ำ ทำให้วิธีนี้เหมาะสำหรับแผ่นบางที่มีความหนาน้อยกว่า 6 มม.
อีกรูปแบบหนึ่งของกระบวนการ FLUX-CORED ARC WELDING (FCAW) คล้ายกับการเชื่อมอาร์กโลหะด้วยแก๊ส ยกเว้นว่าอิเล็กโทรดจะเป็นหลอดที่เต็มไปด้วยฟลักซ์ ข้อดีของการใช้อิเล็กโทรด cored-flux คือทำให้เกิดอาร์คที่มีเสถียรภาพมากขึ้น ทำให้เรามีโอกาสปรับปรุงคุณสมบัติของโลหะเชื่อม มีความเปราะและยืดหยุ่นน้อยกว่าของฟลักซ์เมื่อเปรียบเทียบกับการเชื่อม SMAW รูปทรงการเชื่อมที่ดีขึ้น อิเล็กโทรดคอร์ที่มีฉนวนป้องกันตัวเองประกอบด้วยวัสดุที่ป้องกันบริเวณรอยเชื่อมจากชั้นบรรยากาศ เราใช้พลังงานประมาณ 20 กิโลวัตต์ เช่นเดียวกับกระบวนการ GMAW กระบวนการ FCAW ยังเปิดโอกาสให้กระบวนการอัตโนมัติสำหรับการเชื่อมอย่างต่อเนื่อง และประหยัด เคมีของโลหะเชื่อมที่แตกต่างกันสามารถพัฒนาได้โดยการเพิ่มโลหะผสมต่างๆ ลงในแกนฟลักซ์
ในการเชื่อมด้วยไฟฟ้า (EGW) เราเชื่อมชิ้นงานจากขอบหนึ่งไปอีกขอบหนึ่ง บางครั้งเรียกว่า BUTT WELDING เชื่อมโลหะเข้าไปในช่องเชื่อมระหว่างสองชิ้นที่จะเข้าร่วม พื้นที่ล้อมรอบด้วยเขื่อนระบายความร้อนด้วยน้ำสองแห่งเพื่อป้องกันไม่ให้ตะกรันที่หลอมละลายไหลออกมา เขื่อนถูกเคลื่อนขึ้นโดยใช้กลไกขับเคลื่อน เมื่อชิ้นงานสามารถหมุนได้ เราก็สามารถใช้เทคนิคการเชื่อมด้วยไฟฟ้าแก๊สสำหรับการเชื่อมตามเส้นรอบวงของท่อได้เช่นกัน อิเล็กโทรดถูกป้อนผ่านท่อเพื่อให้ส่วนโค้งต่อเนื่อง กระแสไฟฟ้าสามารถอยู่ที่ประมาณ 400 แอมแปร์หรือ 750 แอมแปร์ และระดับพลังงานประมาณ 20 กิโลวัตต์ ก๊าซเฉื่อยที่เกิดจากอิเล็กโทรดที่มีแกนฟลักซ์หรือแหล่งภายนอกให้การป้องกัน เราใช้การเชื่อมด้วยไฟฟ้า (EGW) สำหรับโลหะ เช่น เหล็ก ไททาเนียม….ฯลฯ ที่มีความหนาตั้งแต่ 12 มม. ถึง 75 มม. เทคนิคนี้เหมาะสำหรับโครงสร้างขนาดใหญ่
ทว่าในเทคนิคอื่นที่เรียกว่า ELECTROSLAG WELDING (ESW) อาร์กจะจุดประกายระหว่างอิเล็กโทรดกับด้านล่างของชิ้นงานและเพิ่มฟลักซ์ เมื่อตะกรันหลอมเหลวไปถึงปลายอิเล็กโทรด ส่วนโค้งก็จะดับลง พลังงานถูกจ่ายอย่างต่อเนื่องผ่านความต้านทานไฟฟ้าของตะกรันหลอมเหลว เราสามารถเชื่อมเพลตที่มีความหนาตั้งแต่ 50 มม. ถึง 900 มม. และสูงกว่านั้นอีก กระแสไฟอยู่ที่ประมาณ 600 แอมแปร์ ในขณะที่แรงดันไฟฟ้าอยู่ระหว่าง 40 – 50 โวลต์ ความเร็วในการเชื่อมอยู่ที่ประมาณ 12 ถึง 36 มม./นาที การใช้งานคล้ายกับการเชื่อมด้วยไฟฟ้า
หนึ่งในกระบวนการอิเล็กโทรดที่ไม่สิ้นเปลืองของเรา GAS TUNGSTEN ARC WELDING (GTAW) หรือที่รู้จักในชื่อ TUNGSTEN INERT GAS WELDING (TIG) เกี่ยวข้องกับการจัดหาโลหะเติมด้วยลวด สำหรับข้อต่อที่กระชับพอดี บางครั้งเราไม่ใช้โลหะเสริม ในกระบวนการ TIG เราไม่ใช้ฟลักซ์ แต่ใช้อาร์กอนและฮีเลียมเพื่อป้องกัน ทังสเตนมีจุดหลอมเหลวสูงและไม่ได้ใช้ในกระบวนการเชื่อม TIG ดังนั้นจึงสามารถรักษากระแสคงที่และช่องว่างอาร์คได้ ระดับพลังงานอยู่ระหว่าง 8 ถึง 20 กิโลวัตต์ และกระแสไฟที่ 200 แอมแปร์ (DC) หรือ 500 แอมแปร์ (AC) สำหรับอะลูมิเนียมและแมกนีเซียม เราใช้กระแสไฟ AC สำหรับฟังก์ชันทำความสะอาดออกไซด์ เพื่อหลีกเลี่ยงการปนเปื้อนของอิเล็กโทรดทังสเตน เราหลีกเลี่ยงการสัมผัสกับโลหะหลอมเหลว การเชื่อมอาร์กทังสเตนแก๊ส (GTAW) มีประโยชน์อย่างยิ่งสำหรับการเชื่อมโลหะบาง รอยเชื่อม GTAW มีคุณภาพสูงและมีผิวสำเร็จที่ดี
เนื่องจากก๊าซไฮโดรเจนมีต้นทุนสูงขึ้น เทคนิคที่ใช้น้อยกว่าคือ ATOMIC HYDROGEN WELDING (AHW) ซึ่งเราสร้างส่วนโค้งระหว่างอิเล็กโทรดทังสเตนสองขั้วในบรรยากาศป้องกันของก๊าซไฮโดรเจนที่ไหลอยู่ AHW ยังเป็นกระบวนการเชื่อมอิเล็กโทรดที่ไม่สิ้นเปลืองอีกด้วย ก๊าซไฮโดรเจนไดอะตอมมิก H2 แตกตัวเป็นรูปอะตอมใกล้กับส่วนโค้งของการเชื่อมซึ่งมีอุณหภูมิสูงกว่า 6273 เคลวิน ในขณะที่พังทลายจะดูดซับความร้อนจำนวนมากจากส่วนโค้ง เมื่ออะตอมไฮโดรเจนกระทบบริเวณรอยเชื่อมซึ่งเป็นพื้นผิวที่ค่อนข้างเย็น พวกมันจะรวมตัวกันใหม่ในรูปแบบไดอะตอมมิกและปล่อยความร้อนที่เก็บไว้ พลังงานสามารถเปลี่ยนแปลงได้โดยการเปลี่ยนชิ้นงานเป็นระยะทางอาร์ค
ในกระบวนการอิเล็กโทรดอื่นที่ไม่สิ้นเปลือง PLASMA ARC WELDING (PAW) เรามีพลาสมาอาร์คเข้มข้นพุ่งตรงไปยังบริเวณรอยเชื่อม อุณหภูมิถึง 33,273 เคลวินใน PAW อิเล็กตรอนและไอออนจำนวนเกือบเท่ากันประกอบเป็นแก๊สพลาสมา ส่วนโค้งนำร่องกระแสไฟต่ำเริ่มต้นพลาสม่าซึ่งอยู่ระหว่างอิเล็กโทรดทังสเตนและปาก กระแสไฟที่ใช้งานโดยทั่วไปจะอยู่ที่ประมาณ 100 แอมแปร์ อาจมีการป้อนโลหะเติม ในการเชื่อมอาร์กพลาสม่า การป้องกันทำได้โดยวงแหวนป้องกันด้านนอกและใช้ก๊าซ เช่น อาร์กอนและฮีเลียม ในการเชื่อมอาร์กพลาสม่า อาร์คอาจอยู่ระหว่างอิเล็กโทรดกับชิ้นงาน หรือระหว่างอิเล็กโทรดกับหัวฉีด เทคนิคการเชื่อมนี้มีข้อได้เปรียบเหนือวิธีการอื่นๆ ที่มีความเข้มข้นของพลังงานสูง ความสามารถในการเชื่อมที่ลึกและแคบกว่า ความเสถียรของส่วนโค้งที่ดีขึ้น ความเร็วในการเชื่อมที่สูงขึ้นถึง 1 เมตร/นาที ความผิดเพี้ยนจากความร้อนน้อยลง โดยทั่วไปเราใช้การเชื่อมแบบพลาสม่าอาร์คสำหรับความหนาน้อยกว่า 6 มม. และบางครั้งอาจสูงถึง 20 มม. สำหรับอะลูมิเนียมและไททาเนียม
HIGH-ENERGY-BEAM WELDING: วิธีการเชื่อมแบบฟิวชันอีกรูปแบบหนึ่งที่มีการเชื่อมด้วยลำแสงอิเล็กตรอน (EBW) และการเชื่อมด้วยเลเซอร์ (LBW) เป็นสองรูปแบบ เทคนิคเหล่านี้มีค่าเป็นพิเศษสำหรับงานการผลิตผลิตภัณฑ์ไฮเทคของเรา ในการเชื่อมด้วยลำแสงอิเล็กตรอน อิเล็กตรอนความเร็วสูงจะชนชิ้นงานและพลังงานจลน์ของพวกมันจะถูกแปลงเป็นความร้อน ลำอิเล็กตรอนแคบเดินทางได้ง่ายในห้องสุญญากาศ โดยทั่วไปเราใช้สุญญากาศสูงในการเชื่อมด้วยลำแสงอิเล็กทรอนิกส์ แผ่นหนาถึง 150 มม. เชื่อมได้ ไม่จำเป็นต้องใช้ก๊าซ ฟลักซ์ หรือวัสดุตัวเติม ปืนบีมอีเลครอนมีความจุ 100 กิโลวัตต์ เชื่อมลึกและแคบที่มีอัตราส่วนกว้างยาวสูงถึง 30 และโซนที่ได้รับผลกระทบจากความร้อนขนาดเล็กได้ ความเร็วในการเชื่อมสามารถเข้าถึง 12 ม./นาที ในการเชื่อมด้วยลำแสงเลเซอร์ เราใช้เลเซอร์กำลังสูงเป็นแหล่งความร้อน ลำแสงเลเซอร์ขนาดเล็กถึง 10 ไมครอนที่มีความหนาแน่นสูงช่วยให้เจาะเข้าไปในชิ้นงานได้ลึก อัตราส่วนความลึกต่อความกว้างได้มากถึง 10 ด้วยการเชื่อมด้วยลำแสงเลเซอร์ เราใช้ทั้งเลเซอร์แบบพัลซิ่งและแบบคลื่นต่อเนื่อง โดยเลเซอร์แบบแรกใช้กับวัสดุบางและแบบหลังส่วนใหญ่สำหรับชิ้นงานที่มีความหนาไม่เกิน 25 มม. ระดับพลังงานสูงถึง 100 กิโลวัตต์ การเชื่อมด้วยลำแสงเลเซอร์ไม่เหมาะกับวัสดุที่สะท้อนแสงมาก อาจใช้แก๊สในกระบวนการเชื่อม วิธีการเชื่อมด้วยลำแสงเลเซอร์เหมาะอย่างยิ่งสำหรับระบบอัตโนมัติและการผลิตที่มีปริมาณมาก และสามารถให้ความเร็วในการเชื่อมระหว่าง 2.5 ม./นาที ถึง 80 ม./นาที ข้อได้เปรียบที่สำคัญอย่างหนึ่งของเทคนิคการเชื่อมนี้คือการเข้าถึงพื้นที่ที่ไม่สามารถใช้เทคนิคอื่นได้ ลำแสงเลเซอร์สามารถเดินทางไปยังบริเวณที่ยากลำบากได้อย่างง่ายดาย ไม่ต้องใช้สุญญากาศเหมือนในการเชื่อมด้วยลำแสงอิเล็กตรอน การเชื่อมที่มีคุณภาพและความแข็งแรง การหดตัวต่ำ การบิดเบือนต่ำ ความพรุนต่ำ สามารถรับได้ด้วยการเชื่อมด้วยลำแสงเลเซอร์ ลำแสงเลเซอร์สามารถจัดการและจัดรูปแบบได้ง่ายโดยใช้สายไฟเบอร์ออปติก เทคนิคนี้จึงเหมาะอย่างยิ่งสำหรับการเชื่อมชุดประกอบสุญญากาศที่มีความแม่นยำ แพ็คเกจอิเล็กทรอนิกส์… ฯลฯ
ให้เราดูเทคนิคการเชื่อมแบบโซลิดสเตตของเรา COLD WELDING (CW) เป็นกระบวนการที่ใช้แรงดันแทนความร้อนโดยใช้แม่พิมพ์หรือม้วนกับชิ้นส่วนที่ผสมพันธุ์ ในการเชื่อมแบบเย็น ชิ้นส่วนที่ผสมพันธุ์อย่างน้อยหนึ่งชิ้นจะต้องมีความเหนียว ได้ผลลัพธ์ที่ดีที่สุดด้วยวัสดุสองชนิดที่คล้ายคลึงกัน หากโลหะสองชนิดที่จะเชื่อมด้วยการเชื่อมเย็นไม่เหมือนกัน เราอาจได้รับข้อต่อที่เปราะบางและเปราะ วิธีการเชื่อมแบบเย็นนี้เหมาะอย่างยิ่งสำหรับชิ้นงานที่อ่อนนุ่ม เหนียว และขนาดเล็ก เช่น การเชื่อมต่อทางไฟฟ้า ขอบภาชนะที่ไวต่อความร้อน แถบ bimetallic สำหรับเทอร์โมสตัท...เป็นต้น รูปแบบหนึ่งของการเชื่อมแบบเย็นคือการเชื่อมแบบม้วน (หรือการเชื่อมแบบม้วน) ซึ่งใช้แรงดันผ่านม้วนคู่ บางครั้งเราทำการเชื่อมแบบม้วนที่อุณหภูมิสูงเพื่อความแข็งแรงของพื้นผิวที่ดีขึ้น
กระบวนการเชื่อมแบบโซลิดสเตตอีกรูปแบบหนึ่งที่เราใช้คือ ULTRASONIC WELDING (USW) ซึ่งชิ้นงานต้องอยู่ภายใต้แรงสถิตปกติและความเค้นเฉือนแบบสั่น แรงเฉือนแบบสั่นถูกนำไปใช้กับส่วนปลายของทรานสดิวเซอร์ การเชื่อมด้วยอัลตราโซนิกปรับใช้การสั่นด้วยความถี่ตั้งแต่ 10 ถึง 75 kHz ในการใช้งานบางอย่าง เช่น การเชื่อมตะเข็บ เราใช้จานเชื่อมแบบหมุนเป็นปลาย แรงเฉือนที่ใช้กับชิ้นงานทำให้เกิดการเสียรูปของพลาสติกขนาดเล็ก ชั้นออกไซด์แตกตัว สารปนเปื้อน และนำไปสู่การยึดติดของโซลิดสเตต อุณหภูมิที่เกี่ยวข้องกับการเชื่อมด้วยอัลตราโซนิกนั้นต่ำกว่าอุณหภูมิจุดหลอมเหลวของโลหะและไม่มีการหลอมรวมเกิดขึ้น เราใช้กระบวนการเชื่อมด้วยคลื่นเสียงความถี่สูง (USW) บ่อยครั้งสำหรับวัสดุที่ไม่ใช่โลหะ เช่น พลาสติก ในเทอร์โมพลาสติก อุณหภูมิจะถึงจุดหลอมเหลวอย่างไรก็ตาม
อีกเทคนิคหนึ่งที่ได้รับความนิยม ใน FRICTION WELDING (FRW) ความร้อนจะเกิดขึ้นจากการเสียดสีที่ส่วนต่อประสานของชิ้นงานที่จะเชื่อมต่อ ในการเชื่อมแบบเสียดทาน เราเก็บชิ้นงานชิ้นหนึ่งไว้กับที่ ในขณะที่อีกชิ้นถูกยึดไว้ในฟิกซ์เจอร์และหมุนด้วยความเร็วคงที่ จากนั้นชิ้นงานจะถูกสัมผัสภายใต้แรงในแนวแกน ความเร็วพื้นผิวของการหมุนในการเชื่อมแบบเสียดทานอาจสูงถึง 900m/min ในบางกรณี หลังจากสัมผัสประสานกันอย่างเพียงพอ ชิ้นงานที่หมุนได้จะหยุดกะทันหันและแรงในแนวแกนจะเพิ่มขึ้น บริเวณรอยเชื่อมโดยทั่วไปจะเป็นบริเวณแคบ เทคนิคการเชื่อมแบบเสียดทานสามารถใช้เชื่อมชิ้นส่วนที่เป็นของแข็งและท่อที่ทำจากวัสดุต่างๆ ได้ แฟลชบางตัวอาจพัฒนาที่ส่วนต่อประสานใน FRW แต่แฟลชนี้สามารถลบออกได้ด้วยการตัดเฉือนหรือการเจียรรอง รูปแบบของกระบวนการเชื่อมแบบเสียดทานมีอยู่ ตัวอย่างเช่น “การเชื่อมเสียดทานความเฉื่อย” เกี่ยวข้องกับมู่เล่ที่ใช้พลังงานจลน์ในการหมุนเพื่อเชื่อมชิ้นส่วน การเชื่อมจะเสร็จสมบูรณ์เมื่อมู่เล่หยุด มวลหมุนสามารถเปลี่ยนแปลงได้และด้วยเหตุนี้พลังงานจลน์ในการหมุน อีกรูปแบบหนึ่งคือ “การเชื่อมเสียดทานเชิงเส้น” ซึ่งการเคลื่อนที่แบบลูกสูบเชิงเส้นถูกกำหนดบนส่วนประกอบอย่างน้อยหนึ่งชิ้นที่จะเชื่อมต่อ ชิ้นส่วนเชื่อมแบบเสียดทานเชิงเส้นไม่จำเป็นต้องมีลักษณะเป็นวงกลม อาจเป็นสี่เหลี่ยม สี่เหลี่ยมจัตุรัส หรือรูปทรงอื่นๆ ความถี่สามารถอยู่ในหน่วย Hz, แอมพลิจูดในช่วงมิลลิเมตร และความดันในหน่วย MPa หลักสิบหรือหลายร้อย ในที่สุด “การเชื่อมด้วยแรงเสียดทานกวน” ค่อนข้างแตกต่างจากอีกสองข้อที่อธิบายข้างต้น ในขณะที่การเชื่อมด้วยแรงเสียดทานความเฉื่อยและการให้ความร้อนในการเชื่อมด้วยแรงเสียดทานเชิงเส้นของส่วนต่อประสานนั้นเกิดขึ้นได้จากการเสียดสีโดยการถูพื้นผิวสัมผัสสองอัน ในวิธีการเชื่อมแบบกวนด้วยแรงเสียดทาน วัตถุที่สามจะถูกถูกับพื้นผิวทั้งสองที่จะเชื่อมเข้าด้วยกัน เครื่องมือหมุนที่มีเส้นผ่านศูนย์กลาง 5 ถึง 6 มม. ถูกนำไปสัมผัสกับข้อต่อ อุณหภูมิสามารถเพิ่มเป็นค่าระหว่าง 503 ถึง 533 เคลวิน ให้ความร้อน ผสม และกวนวัสดุในข้อต่อ เราใช้การเชื่อมแบบกวนด้วยแรงเสียดทานกับวัสดุหลายประเภท เช่น อะลูมิเนียม พลาสติก และคอมโพสิต รอยเชื่อมมีความสม่ำเสมอและมีคุณภาพสูงโดยมีรูพรุนน้อยที่สุด ไม่มีควันหรือโปรยลงมาในการเชื่อมแบบกวนด้วยแรงเสียดทาน และกระบวนการนี้เป็นไปโดยอัตโนมัติอย่างดี
RESISTANCE WELDING (RW): ความร้อนที่จำเป็นสำหรับการเชื่อมเกิดจากความต้านทานไฟฟ้าระหว่างชิ้นงานทั้งสองที่จะเชื่อมเข้าด้วยกัน ไม่มีการใช้ฟลักซ์ ก๊าซป้องกัน หรืออิเล็กโทรดสิ้นเปลืองในการเชื่อมความต้านทาน การให้ความร้อนแบบจูลเกิดขึ้นในการเชื่อมแบบต้านทานและสามารถแสดงได้ดังนี้
H = (สี่เหลี่ยม I) x R xtx K
H คือความร้อนที่สร้างขึ้นในหน่วยจูล (วัตต์-วินาที) ฉันปัจจุบันเป็นแอมแปร์ ความต้านทาน R เป็นโอห์ม t คือเวลาเป็นวินาทีที่กระแสไหลผ่าน ปัจจัย K น้อยกว่า 1 และแสดงถึงเศษส่วนของพลังงานที่ไม่สูญเสียผ่านการแผ่รังสีและการนำ กระแสในกระบวนการเชื่อมความต้านทานสามารถเข้าถึงระดับสูงถึง 100,000 A แต่โดยทั่วไปแล้วแรงดันไฟฟ้าจะอยู่ที่ 0.5 ถึง 10 โวลต์ อิเล็กโทรดมักจะทำจากโลหะผสมทองแดง ทั้งวัสดุที่คล้ายคลึงกันและไม่เหมือนกันสามารถเชื่อมเข้าด้วยกันได้โดยการเชื่อมความต้านทาน มีหลายรูปแบบสำหรับกระบวนการนี้: “การเชื่อมแบบจุดต้านทาน” เกี่ยวข้องกับอิเล็กโทรดทรงกลมที่ตรงข้ามกันสองตัวที่สัมผัสกับพื้นผิวของรอยต่อหน้าตักของทั้งสองแผ่น แรงดันถูกนำไปใช้จนกระแสไฟดับ ตัวเชื่อมโดยทั่วไปจะมีเส้นผ่านศูนย์กลางไม่เกิน 10 มม. การเชื่อมแบบจุดต้านทานจะทำให้รอยเยื้องเปลี่ยนสีเล็กน้อยที่จุดเชื่อม การเชื่อมแบบจุดเป็นเทคนิคการเชื่อมแบบต้านทานที่ได้รับความนิยมมากที่สุดของเรา รูปทรงอิเล็กโทรดต่างๆ ถูกนำมาใช้ในการเชื่อมแบบจุดเพื่อเข้าถึงพื้นที่ที่ยากลำบาก อุปกรณ์เชื่อมแบบจุดของเราควบคุมด้วย CNC และมีอิเล็กโทรดหลายตัวที่สามารถใช้พร้อมกันได้ อีกรูปแบบหนึ่งคือ "การเชื่อมตะเข็บต้านทาน" โดยใช้อิเล็กโทรดล้อหรือลูกกลิ้งที่ผลิตรอยเชื่อมแบบจุดต่อเนื่องเมื่อใดก็ตามที่กระแสถึงระดับสูงเพียงพอในวงจรไฟฟ้ากระแสสลับ ข้อต่อที่เกิดจากการเชื่อมตะเข็บแบบต้านทานจะเป็นของเหลวและแก๊สแน่น ความเร็วในการเชื่อมประมาณ 1.5 ม./นาที เป็นเรื่องปกติสำหรับแผ่นบาง หนึ่งอาจใช้กระแสเป็นระยะเพื่อให้เกิดรอยเชื่อมในช่วงเวลาที่ต้องการตามตะเข็บ ใน “การเชื่อมการฉายภาพแนวต้าน” เราทำการฉายภาพ (ลักยิ้ม) หนึ่งส่วนขึ้นไปบนพื้นผิวชิ้นงานที่จะเชื่อม ประมาณการเหล่านี้อาจเป็นทรงกลมหรือวงรี อุณหภูมิที่มีการแปลสูงจะอยู่ที่จุดนูนเหล่านี้ซึ่งสัมผัสกับส่วนการผสมพันธุ์ อิเล็กโทรดออกแรงกดเพื่อบีบอัดการคาดการณ์เหล่านี้ อิเล็กโทรดในการเชื่อมแบบฉายภาพต้านทานมีปลายแบนและเป็นโลหะผสมทองแดงที่ระบายความร้อนด้วยน้ำ ข้อดีของการเชื่อมแบบโปรเจกชันความต้านทานคือความสามารถของเราในการเชื่อมจำนวนมากในจังหวะเดียว ดังนั้นอายุการใช้งานของอิเล็กโทรดที่ยืดเยื้อ ความสามารถในการเชื่อมแผ่นที่มีความหนาต่างๆ ความสามารถในการเชื่อมน็อตและสลักเกลียวเข้ากับแผ่น ข้อเสียของการเชื่อมแบบโปรเจกชันความต้านทานคือต้นทุนเพิ่มของการนูนรอยบุ๋ม อีกเทคนิคหนึ่งคือ ความร้อนที่เกิดจาก "การเชื่อมด้วยแฟลช" จะถูกสร้างขึ้นจากส่วนโค้งที่ปลายชิ้นงานทั้งสองเมื่อเริ่มสัมผัสกัน วิธีนี้อาจพิจารณาอีกวิธีหนึ่งคือการเชื่อมอาร์ก อุณหภูมิที่ส่วนต่อประสานเพิ่มขึ้นและวัสดุนิ่มลง ใช้แรงตามแนวแกนและเกิดรอยเชื่อมที่บริเวณที่อ่อนตัว หลังจากการเชื่อมด้วยแฟลชเสร็จสิ้นแล้ว สามารถกลึงข้อต่อเพื่อให้มีลักษณะที่ดีขึ้นได้ คุณภาพการเชื่อมที่ได้จากการเชื่อมด้วยแฟลชนั้นดี ระดับพลังงานคือ 10 ถึง 1500 กิโลวัตต์ การเชื่อมแบบแฟลชเหมาะสำหรับการเชื่อมแบบขอบจรดขอบของโลหะที่คล้ายคลึงกันหรือไม่เหมือนกันซึ่งมีเส้นผ่านศูนย์กลางสูงสุด 75 มม. และแผ่นที่มีความหนาระหว่าง 0.2 มม. ถึง 25 มม. “การเชื่อมอาร์กสตั๊ด” คล้ายกับการเชื่อมแบบแฟลชมาก สตั๊ดเช่นโบลต์หรือแกนเกลียวทำหน้าที่เป็นอิเล็กโทรดเดียวในขณะที่เชื่อมต่อกับชิ้นงานเช่นเพลท เพื่อให้ความร้อนที่เกิดขึ้นเข้มข้นขึ้น ป้องกันการเกิดออกซิเดชันและเก็บโลหะหลอมเหลวไว้ในบริเวณรอยเชื่อม จึงมีการวางวงแหวนเซรามิกแบบใช้แล้วทิ้งไว้รอบรอยต่อ ในที่สุด "การเชื่อมแบบกระทบ" อีกกระบวนการเชื่อมความต้านทาน ใช้ตัวเก็บประจุเพื่อจ่ายพลังงานไฟฟ้า ในการเชื่อมแบบเพอร์คัชชัน พลังงานจะคายประจุออกมาภายในเสี้ยววินาทีของเวลาอย่างรวดเร็ว ทำให้เกิดความร้อนเฉพาะจุดสูงที่ข้อต่อ เราใช้การเชื่อมแบบกระทบกระแทกอย่างกว้างขวางในอุตสาหกรรมการผลิตอุปกรณ์อิเล็กทรอนิกส์ ซึ่งต้องหลีกเลี่ยงการให้ความร้อนกับชิ้นส่วนอิเล็กทรอนิกส์ที่มีความละเอียดอ่อนในบริเวณใกล้เคียงกับข้อต่อ
เทคนิคที่เรียกว่า EXPLOSION WELDING เกี่ยวข้องกับการระเบิดของชั้นของวัตถุระเบิดที่วางทับชิ้นงานชิ้นใดชิ้นหนึ่งที่จะเชื่อมเข้าด้วยกัน แรงดันที่สูงมากที่กระทำต่อชิ้นงานทำให้เกิดส่วนต่อประสานที่ปั่นป่วนและเป็นคลื่น และเกิดการประสานกันทางกล แรงยึดเหนี่ยวในการเชื่อมที่ระเบิดได้สูงมาก การเชื่อมด้วยการระเบิดเป็นวิธีที่ดีในการหุ้มแผ่นโลหะที่ไม่เหมือนกัน หลังจากการหุ้มแล้ว แผ่นอาจรีดเป็นส่วนที่บางลง บางครั้งเราใช้การเชื่อมแบบระเบิดเพื่อขยายท่อเพื่อให้ปิดสนิทกับเพลต
วิธีสุดท้ายของเราภายในโดเมนของการเชื่อมแบบโซลิดสเตตคือ DIFFUSION BONDING หรือ DIFFUSION WELDING (DFW) ซึ่งข้อต่อที่ดีจะเกิดขึ้นได้จากการแพร่ของอะตอมผ่านอินเทอร์เฟซเป็นหลัก การเสียรูปพลาสติกบางส่วนที่ส่วนต่อประสานนั้นมีส่วนช่วยในการเชื่อม อุณหภูมิที่เกี่ยวข้องอยู่ที่ประมาณ 0.5 Tm โดยที่ Tm คืออุณหภูมิหลอมเหลวของโลหะ แรงยึดเหนี่ยวในการเชื่อมแบบกระจายขึ้นอยู่กับแรงดัน อุณหภูมิ เวลาสัมผัส และความสะอาดของพื้นผิวสัมผัส บางครั้งเราใช้โลหะเติมที่ส่วนต่อประสาน ต้องใช้ความร้อนและแรงดันในการยึดติดแบบแพร่ และจัดหาโดยความต้านทานไฟฟ้าหรือเตาหลอมและตุ้มน้ำหนักตาย แรงกด หรืออย่างอื่น สามารถเชื่อมโลหะที่เหมือนกันและไม่เหมือนกันด้วยการเชื่อมแบบกระจาย กระบวนการนี้ค่อนข้างช้าเนื่องจากใช้เวลาในการย้ายอะตอม DFW เป็นระบบอัตโนมัติและมีการใช้กันอย่างแพร่หลายในการผลิตชิ้นส่วนที่ซับซ้อนสำหรับอุตสาหกรรมการบินและอวกาศ อิเล็กทรอนิกส์ การแพทย์ ผลิตภัณฑ์ที่ผลิต ได้แก่ รากฟันเทียมออร์โธปิดิกส์ เซ็นเซอร์ ส่วนประกอบโครงสร้างการบินและอวกาศ การยึดติดแบบแพร่สามารถใช้ร่วมกับ SUPERPLASTIC FORMING เพื่อสร้างโครงสร้างโลหะแผ่นที่ซับซ้อนได้ ตำแหน่งที่เลือกบนแผ่นงานจะถูกเชื่อมประสานก่อน จากนั้นบริเวณที่ไม่ผูกมัดจะขยายเป็นแม่พิมพ์โดยใช้แรงดันอากาศ โครงสร้างการบินและอวกาศที่มีอัตราส่วนความแข็งต่อน้ำหนักสูงผลิตขึ้นโดยใช้วิธีการนี้ร่วมกัน กระบวนการรวมการเชื่อมแบบกระจาย / การขึ้นรูปซุปเปอร์พลาสติกช่วยลดจำนวนชิ้นส่วนที่ต้องการโดยไม่จำเป็นต้องใช้ตัวยึด ส่งผลให้ชิ้นส่วนที่มีความเค้นต่ำมีความแม่นยำสูงในราคาประหยัดและใช้เวลานำสั้น
การประสาน: เทคนิคการประสานและการบัดกรีเกี่ยวข้องกับอุณหภูมิที่ต่ำกว่าที่จำเป็นสำหรับการเชื่อม อุณหภูมิในการประสานจะสูงกว่าอุณหภูมิในการบัดกรีอย่างไรก็ตาม ในการประสานโลหะฟิลเลอร์จะถูกวางระหว่างพื้นผิวที่จะเชื่อมและอุณหภูมิจะเพิ่มขึ้นจนถึงอุณหภูมิหลอมเหลวของวัสดุตัวเติมที่สูงกว่า 723 เคลวิน แต่ต่ำกว่าอุณหภูมิหลอมเหลวของชิ้นงาน โลหะหลอมเหลวจะเติมช่องว่างที่พอดีระหว่างชิ้นงาน การหล่อเย็นและการแข็งตัวในภายหลังของโลหะ filer ส่งผลให้เกิดข้อต่อที่แข็งแรง ในการเชื่อมประสานโลหะฟิลเลอร์จะสะสมอยู่ที่ข้อต่อ มีการใช้โลหะเติมในการเชื่อมประสานมากกว่ามากเมื่อเทียบกับการประสาน ไฟฉาย Oxyacetylene ที่มีเปลวไฟออกซิไดซ์ใช้เพื่อสะสมโลหะฟิลเลอร์ในการเชื่อมด้วยทองเหลือง เนื่องจากอุณหภูมิในการประสานที่ต่ำกว่า ปัญหาที่บริเวณที่ได้รับผลกระทบจากความร้อน เช่น การบิดเบี้ยวและความเค้นตกค้างจะน้อยลง ยิ่งช่องว่างระหว่างช่องว่างในการประสานยิ่งน้อย ค่าแรงเฉือนของข้อต่อยิ่งสูง ค่าความต้านทานแรงดึงสูงสุดทำได้ที่ช่องว่างที่เหมาะสม (ค่าสูงสุด) ด้านล่างและเหนือค่าที่เหมาะสมนี้ ความต้านทานแรงดึงในการประสานจะลดลง ช่องว่างทั่วไปในการประสานสามารถอยู่ระหว่าง 0.025 ถึง 0.2 มม. เราใช้วัสดุประสานที่หลากหลายที่มีรูปร่างแตกต่างกัน เช่น การทำงาน ผง แหวน ลวด แถบ…..ฯลฯ และสามารถผลิตสิ่งเหล่านี้ได้โดยเฉพาะสำหรับการออกแบบหรือรูปทรงผลิตภัณฑ์ของคุณ นอกจากนี้เรายังกำหนดเนื้อหาของวัสดุประสานตามวัสดุพื้นฐานและการใช้งานของคุณ เราใช้ฟลักซ์ในการประสานเพื่อขจัดชั้นออกไซด์ที่ไม่ต้องการและป้องกันการเกิดออกซิเดชัน เพื่อหลีกเลี่ยงการกัดกร่อนที่ตามมา โดยทั่วไปฟลักซ์จะถูกลบออกหลังจากการดำเนินการเชื่อม AGS-TECH Inc. ใช้วิธีการประสานที่หลากหลาย รวมถึง:
- การประสานคบเพลิง
- ประสานเตา
- ประสานการเหนี่ยวนำ
- ต้านทานประสาน
- จุ่มประสาน
- ประสานอินฟราเรด
- การประสานแบบกระจาย
- ลำแสงพลังงานสูง
ตัวอย่างที่พบบ่อยที่สุดของข้อต่อเชื่อมประสานของเราทำจากโลหะที่แตกต่างกันซึ่งมีความแข็งแรงดี เช่น ดอกสว่านคาร์ไบด์ เม็ดมีด แพ็คเกจออปโตอิเล็กทรอนิกส์แบบสุญญากาศ ซีล
การบัดกรี : นี่เป็นเทคนิคที่ใช้บ่อยที่สุดวิธีหนึ่งของเราในการประสาน (โลหะเติม) เติมรอยต่อเช่นเดียวกับการประสานระหว่างส่วนประกอบที่ยึดแน่น หัวแร้งของเรามีจุดหลอมเหลวต่ำกว่า 723 เคลวิน เราปรับใช้การบัดกรีแบบแมนนวลและแบบอัตโนมัติในการปฏิบัติงานด้านการผลิต เมื่อเทียบกับการบัดกรีแข็ง อุณหภูมิในการบัดกรีจะต่ำกว่า การบัดกรีไม่เหมาะสำหรับการใช้งานที่มีอุณหภูมิสูงหรือมีความแข็งแรงสูง เราใช้โลหะบัดกรีไร้สารตะกั่วเช่นเดียวกับดีบุก-ตะกั่ว ดีบุก-สังกะสี ตะกั่ว-เงิน แคดเมียม-เงิน โลหะผสมสังกะสี-อลูมิเนียม นอกเหนือจากชนิดอื่นๆ สำหรับการบัดกรี ทั้งกรดและเกลืออนินทรีย์ที่ไม่กัดกร่อนเป็นส่วนประกอบหลัก ถูกใช้เป็นฟลักซ์ในการบัดกรี เราใช้ฟลักซ์พิเศษในการบัดกรีโลหะที่มีความสามารถในการบัดกรีต่ำ ในการใช้งานที่เราต้องบัดกรีวัสดุเซรามิก แก้ว หรือกราไฟต์ ก่อนอื่นเราจะชุบชิ้นส่วนด้วยโลหะที่เหมาะสมเพื่อเพิ่มความสามารถในการบัดกรี เทคนิคการบัดกรีที่เป็นที่นิยมของเราคือ:
-Reflow หรือ Paste การประสาน
-คลื่นบัดกรี
-เตาบัดกรี
-ไฟฉายบัดกรี
- การบัดกรีแบบเหนี่ยวนำ
-หัวแร้ง
-ความต้านทานการบัดกรี
- การบัดกรีแบบจุ่ม
-อัลตราโซนิกบัดกรี
-อินฟราเรดบัดกรี
การบัดกรีด้วยอัลตราโซนิกทำให้เราได้เปรียบที่ไม่เหมือนใครโดยไม่จำเป็นต้องใช้ฟลักซ์เนื่องจากเอฟเฟกต์คาวิเทชั่นอัลตราโซนิกซึ่งเอาฟิล์มออกไซด์ออกจากพื้นผิวที่เชื่อมต่อ การบัดกรีแบบรีโฟลว์และแบบเวฟเป็นเทคนิคที่โดดเด่นทางอุตสาหกรรมของเราสำหรับการผลิตอุปกรณ์อิเล็กทรอนิกส์ในปริมาณมาก ดังนั้นจึงควรค่าแก่การอธิบายในรายละเอียดที่มากขึ้น ในการบัดกรีแบบรีโฟลว์ เราใช้แป้งกึ่งแข็งที่มีอนุภาคโลหะบัดกรี วางแปะลงบนข้อต่อโดยใช้กระบวนการคัดกรองหรือลายฉลุ ในแผงวงจรพิมพ์ (PCB) เรามักใช้เทคนิคนี้ เมื่อวางส่วนประกอบทางไฟฟ้าลงบนแผ่นอิเล็กโทรดเหล่านี้จากการวาง แรงตึงผิวจะทำให้แพ็คเกจยึดพื้นผิวอยู่ในแนวเดียวกัน หลังจากวางส่วนประกอบแล้ว เราให้ความร้อนแก่ส่วนประกอบในเตาหลอมเพื่อให้เกิดการบัดกรีแบบรีโฟลว์ ในระหว่างกระบวนการนี้ ตัวทำละลายในแป้งจะระเหย ฟลักซ์ในแป้งจะถูกกระตุ้น ส่วนประกอบจะถูกอุ่นก่อน อนุภาคบัดกรีจะละลายและทำให้ข้อต่อเปียก และในที่สุด การประกอบ PCB จะถูกทำให้เย็นลงอย่างช้าๆ เทคนิคที่ได้รับความนิยมอันดับสองของเราสำหรับการผลิตแผ่น PCB ในปริมาณมาก กล่าวคือ การบัดกรีด้วยคลื่นขึ้นอยู่กับข้อเท็จจริงที่ว่าการบัดกรีที่หลอมละลายทำให้พื้นผิวโลหะเปียกและเกิดพันธะที่ดีเฉพาะเมื่อโลหะถูกทำให้ร้อนเท่านั้น คลื่นลามินาร์แบบยืนของตัวประสานที่หลอมละลายถูกสร้างขึ้นครั้งแรกโดยปั๊ม และ PCB ที่อุ่นและพรีฟลักซ์จะถูกลำเลียงผ่านคลื่น บัดกรีเปียกเฉพาะพื้นผิวโลหะที่สัมผัส แต่ไม่เปียกแพ็คเกจโพลิเมอร์ IC หรือแผงวงจรเคลือบโพลีเมอร์ การฉีดน้ำร้อนด้วยความเร็วสูงจะเป่าบัดกรีส่วนเกินออกจากข้อต่อและป้องกันการเชื่อมระหว่างตะกั่วที่อยู่ติดกัน ในการบัดกรีด้วยคลื่นของแพ็คเกจยึดพื้นผิว ก่อนอื่นเราจะทำการบัดกรีพวกมันกับแผงวงจรก่อนทำการบัดกรี ใช้การคัดกรองและการฉลุอีกครั้ง แต่คราวนี้สำหรับอีพ็อกซี่ หลังจากวางส่วนประกอบในตำแหน่งที่ถูกต้องแล้ว อีพ็อกซี่จะหายขาด แผงจะถูกกลับหัวและทำการบัดกรีด้วยคลื่น