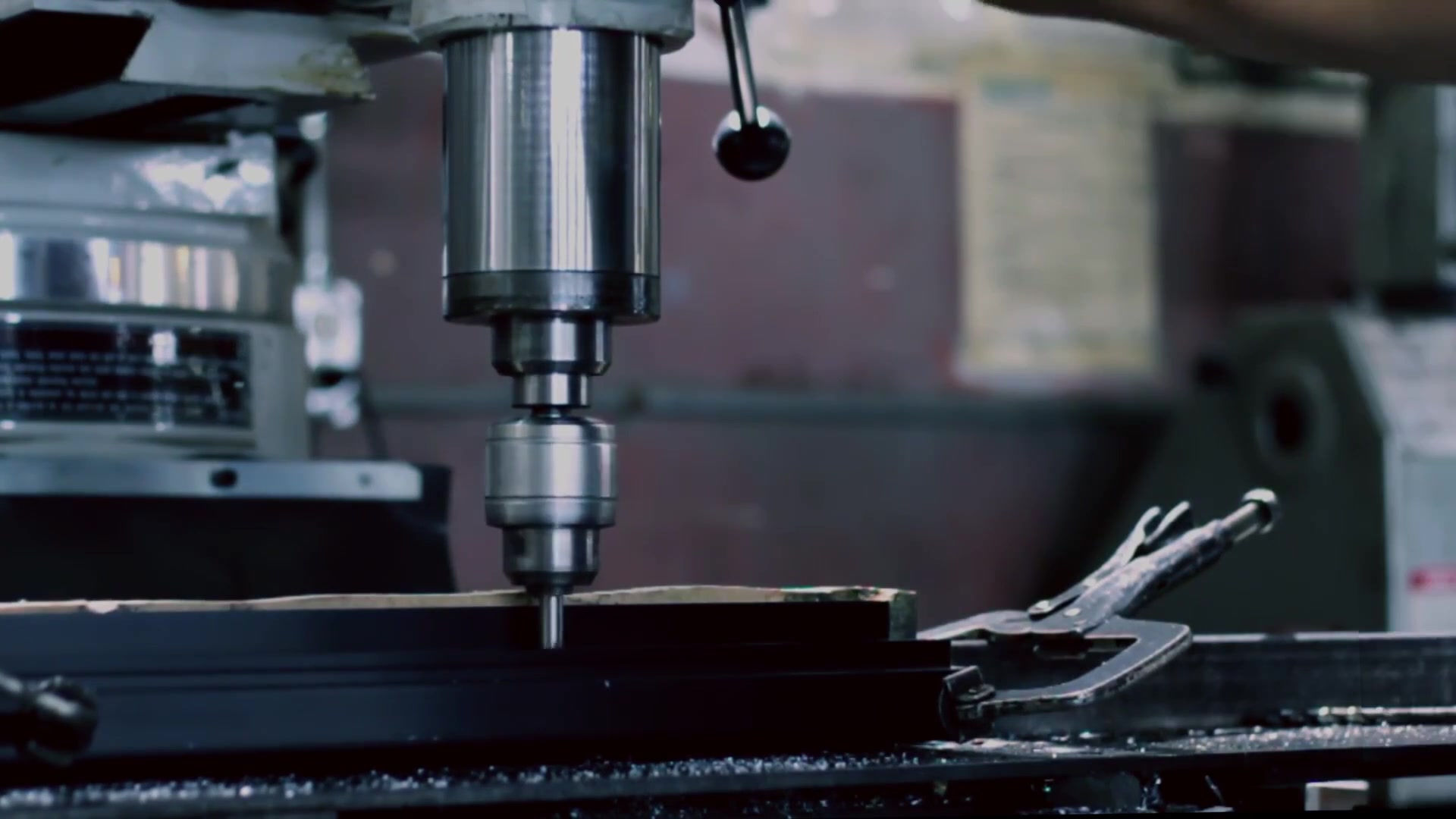
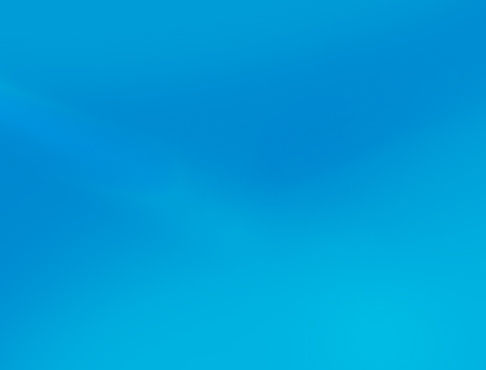
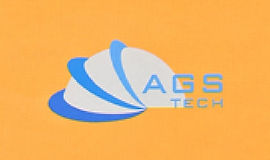
تولید کننده سفارشی جهانی، یکپارچه ساز، تثبیت کننده، شریک برون سپاری برای طیف گسترده ای از محصولات و خدمات.
ما منبع اصلی شما برای تولید، ساخت، مهندسی، ادغام، ادغام، برون سپاری محصولات و خدمات تولید شده سفارشی و خارج از قفسه هستیم.
زبان خود را انتخاب کنید
-
ساخت سفارشی
-
ساخت قرارداد داخلی و جهانی
-
برون سپاری تولید
-
تدارکات داخلی و جهانی
-
Consolidation
-
ادغام مهندسی
-
خدمات مهندسی
نوع تولید شیشه ای که ما ارائه می دهیم عبارتند از: شیشه کانتینری، دمیدن شیشه، الیاف و لوله و میله شیشه، ظروف شیشه ای خانگی و صنعتی، لامپ و لامپ، قالب گیری شیشه ای دقیق، قطعات و مجموعه های نوری، شیشه های تخت و ورق و فلوت. ما هم فرمینگ با دست و هم فرمینگ ماشین را انجام می دهیم.
فرآیندهای محبوب فنی تولید سرامیک ما عبارتند از پرس قالب، پرس ایزواستاتیک، پرس گرم ایزواستاتیک، پرس گرم، ریختهگری لغزشی، ریختهگری نوار، اکستروژن، قالبگیری تزریقی، ماشینکاری سبز، تف جوشی یا پخت، سنگزنی الماس، مجموعههای هرمتیک.
توصیه می کنیم اینجا را کلیک کنید
دانلود تصاویر شماتیک فرآیندهای شکل دهی و شکل دهی شیشه توسط AGS-TECH Inc.
دانلود تصاویر شماتیک ما از فرآیندهای فنی تولید سرامیک توسط AGS-TECH Inc.
این فایلهای دانلودی به همراه عکسها و طرحها به شما در درک بهتر اطلاعاتی که در زیر در اختیار شما قرار میدهیم کمک میکنند.
• تولید شیشه ظروف: ما خطوط پرس و دمش خودکار و همچنین خطوط دمنده و دمنده را برای تولید داریم. در فرآیند دمیدن و دمیدن، یک گوب را در قالب خالی می اندازیم و با ضربه ای از هوای فشرده از بالا، گردن را تشکیل می دهیم. بلافاصله پس از این، هوای فشرده برای بار دوم از جهت دیگر از طریق گردن ظرف دمیده می شود تا پیش فرم بطری را تشکیل دهد. سپس این پیشفرم به قالب واقعی منتقل میشود، مجدداً گرم میشود تا نرم شود و هوای فشرده اعمال میشود تا شکل ظرف نهایی به پیشفرم بدهد. به طور واضح تر، تحت فشار قرار می گیرد و به دیواره های حفره قالب دمنده فشار داده می شود تا شکل دلخواه خود را بگیرد. در نهایت، ظرف شیشهای تولید شده برای گرم کردن مجدد و حذف تنشهای حاصل از قالبگیری به یک کوره بازپخت منتقل میشود و به صورت کنترلشده سرد میشود. در روش پرس و دم، گودهای مذاب را در قالب پاریسون (قالب خالی) قرار داده و به شکل پاریسون (شکل خالی) فشار می دهند. سپس مواد خالی به قالبهای دمنده منتقل میشوند و مانند فرآیندی که در بالا در قسمت «فرآیند دمیدن و دمیدن» توضیح داده شد، دمیده میشوند. مراحل بعدی مانند بازپخت و کاهش استرس مشابه یا مشابه هستند.
• دمیدن شیشه: ما محصولات شیشه ای را با استفاده از دمیدن دستی معمولی و همچنین با استفاده از هوای فشرده با تجهیزات خودکار تولید کرده ایم. برای برخی از سفارشات، دمیدن معمولی ضروری است، مانند پروژههایی که شامل کارهای هنری شیشهای هستند، یا پروژههایی که به تعداد قطعات کمتری با تلورانسهای ضعیف نیاز دارند، پروژههای نمونهسازی/دمو... و غیره. دمیدن شیشه معمولی شامل فرو بردن یک لوله فلزی توخالی در یک گلدان شیشه مذاب و چرخاندن لوله برای جمع آوری مقداری از مواد شیشه است. شیشه جمعآوریشده در نوک لوله بر روی آهن مسطح، به شکل دلخواه، کشیده، دوباره گرم شده و هوا دمیده میشود. پس از آماده شدن، داخل قالب گذاشته و هوا دمیده می شود. حفره قالب مرطوب است تا از تماس شیشه با فلز جلوگیری شود. فیلم آب مانند یک بالشتک بین آنها عمل می کند. دمیدن دستی یک فرآیند آهسته کار فشرده است و فقط برای نمونه سازی یا اقلام با ارزش بالا مناسب است و برای سفارشات ارزان قیمت در هر قطعه مناسب نیست.
• ساخت ظروف شیشه ای خانگی و صنعتی: با استفاده از انواع مواد شیشه ای انواع زیادی ظروف شیشه ای تولید می شود. برخی از لیوان ها مقاوم در برابر حرارت هستند و برای ظروف آزمایشگاهی مناسب هستند، در حالی که برخی از آنها به اندازه کافی برای مقاومت در برابر ماشین های ظرفشویی برای چندین بار خوب هستند و برای ساخت محصولات داخلی مناسب هستند. با استفاده از دستگاه های Westlake روزانه ده ها هزار قطعه لیوان نوشیدنی تولید می شود. برای سادهتر شدن، شیشه مذاب با خلاء جمعآوری میشود و برای ساختن پیشفرمها در قالب قرار میگیرد. سپس هوا به داخل قالب ها دمیده می شود، این ها به قالب دیگری منتقل می شوند و دوباره هوا دمیده می شود و شیشه شکل نهایی خود را به خود می گیرد. مانند دمیدن دستی، این قالب ها با آب مرطوب نگه داشته می شوند. کشش بیشتر بخشی از عملیات تکمیلی است که در آن گردن در حال شکل گیری است. شیشه اضافی سوخته است. پس از آن فرآیند گرمایش و سرمایش مجدد کنترل شده که در بالا توضیح داده شد به شرح زیر است.
• شکل دهی لوله و میله شیشه ای: فرآیندهای اصلی که ما برای ساخت لوله های شیشه ای استفاده می کنیم، فرآیندهای DANNER و VELLO هستند. در فرآیند دانر، شیشه از یک کوره جریان می یابد و روی یک آستین شیبدار ساخته شده از مواد نسوز می افتد. آستین بر روی یک محور توخالی چرخان یا لوله دمنده حمل می شود. سپس شیشه به دور آستین پیچیده می شود و یک لایه صاف تشکیل می دهد که به سمت پایین آستین و روی نوک میل جریان می یابد. در حالت تیوبفرمینگ، هوا از طریق لوله دمنده با نوک توخالی دمیده میشود و در شکلگیری میلهای از نوکهای جامد روی شفت استفاده میکنیم. سپس لوله ها یا میله ها روی غلتک های حامل کشیده می شوند. ابعادی مانند ضخامت دیواره و قطر لوله های شیشه ای با تنظیم قطر آستین و دمیدن فشار هوا به مقدار دلخواه، تنظیم دما، سرعت جریان شیشه و سرعت کشیدن به مقادیر دلخواه تنظیم می شود. از طرف دیگر، فرآیند تولید لوله شیشهای Vello شامل شیشهای است که از کوره بیرون میرود و به کاسهای با سنبه یا زنگ توخالی وارد میشود. سپس شیشه از فضای هوایی بین سنبه و کاسه عبور می کند و شکل لوله ای به خود می گیرد. سپس از روی غلتک ها به ماشین کشش می رود و خنک می شود. در انتهای خط خنک کننده برش و پردازش نهایی انجام می شود. ابعاد لوله را می توان درست مانند فرآیند Danner تنظیم کرد. هنگام مقایسه فرآیند Danner با Vello، میتوان گفت که فرآیند Vello برای تولید مقادیر زیاد مناسبتر است، در حالی که فرآیند Danner ممکن است برای سفارشات لولههای با حجم کوچکتر مناسبتر باشد.
فرآوری شیشههای شیت و تخت و فلوت: ما مقادیر زیادی شیشههای مسطح در ضخامتهای متفاوت از ضخامتهای زیر میلیمتری تا چندین سانتیمتر داریم. عینک های تخت ما تقریباً از نظر نوری کامل هستند. ما شیشه ای را با پوشش های خاص مانند پوشش های نوری ارائه می دهیم که در آن از روش رسوب بخار شیمیایی برای قرار دادن پوشش هایی مانند پوشش ضد انعکاس یا آینه استفاده می شود. همچنین پوشش های رسانای شفاف رایج هستند. همچنین پوششهای آبگریز یا آبدوست روی شیشه و پوششی که شیشه را خود تمیز میکند نیز موجود است. عینک های سکوریت، ضد گلوله و لمینت از دیگر اقلام محبوب هستند. شیشه را با تلورانس های دلخواه به شکل دلخواه برش می دهیم. سایر عملیات ثانویه مانند خم کردن یا خم کردن شیشه تخت در دسترس هستند.
قالب گیری شیشه ای دقیق: ما از این تکنیک بیشتر برای ساخت قطعات نوری دقیق بدون نیاز به تکنیک های گران تر و زمان برتر مانند سنگ زنی، لایه برداری و پرداخت استفاده می کنیم. این تکنیک همیشه برای ساخت بهترین اپتیک کافی نیست، اما در برخی موارد مانند محصولات مصرفی، دوربینهای دیجیتال، اپتیکهای پزشکی میتواند گزینه ارزانتری برای تولید با حجم بالا باشد. همچنین نسبت به دیگر تکنیک های شکل دهی شیشه که در آن هندسه های پیچیده مورد نیاز است، مانند در مورد قیر، مزیت دارد. فرآیند اصلی شامل بارگذاری قسمت پایینی قالب با شیشه خالی، تخلیه محفظه فرآیند برای حذف اکسیژن، نزدیک شدن به بسته شدن قالب، گرم کردن سریع و همدما قالب و شیشه با نور مادون قرمز، بسته شدن بیشتر نیمه های قالب است. شیشه نرم شده را به آرامی و به صورت کنترل شده به ضخامت مورد نظر فشار دهید و در نهایت شیشه خنک شود و محفظه با نیتروژن پر شود و محصول خارج شود. کنترل دقیق دما، فاصله بسته شدن قالب، نیروی بسته شدن قالب، تطبیق ضرایب انبساط قالب و مواد شیشه ای در این فرآیند کلیدی هستند.
• ساخت قطعات و مجموعه های نوری شیشه ای: علاوه بر قالب گیری شیشه ای دقیق، تعدادی از فرآیندهای ارزشمندی وجود دارد که ما برای ساخت قطعات و مجموعه های نوری با کیفیت بالا برای کاربردهای سخت استفاده می کنیم. سنگ زنی، روکش و صیقل دادن شیشه های درجه نوری در دوغاب های ساینده خاص، یک هنر و علم برای ساخت لنزهای نوری، منشور، تخت و غیره است. صافی سطح، موج دار بودن، صافی و سطوح نوری بدون نقص نیاز به تجربه زیادی با چنین فرآیندهایی دارد. تغییرات کوچک در محیط می تواند منجر به خارج شدن محصولات با مشخصات فنی شود و خط تولید را متوقف کند. مواردی وجود دارد که تنها یک پاک کردن روی سطح نوری با یک پارچه تمیز می تواند باعث شود که یک محصول با مشخصات مطابقت داشته باشد یا در تست شکست بخورد. برخی از مواد محبوب شیشه ای مورد استفاده عبارتند از: سیلیس ذوب شده، کوارتز، BK7. همچنین مونتاژ چنین قطعاتی نیاز به تجربه تخصصی در طاقچه دارد. گاهی اوقات از چسب های مخصوص استفاده می شود. با این حال، گاهی اوقات تکنیکی به نام تماس نوری بهترین انتخاب است و شامل هیچ ماده ای در بین شیشه های نوری متصل نیست. این شامل تماس فیزیکی با سطوح صاف برای اتصال بدون چسب به یکدیگر است. در برخی موارد از اسپیسرهای مکانیکی، میلهها یا گلولههای شیشهای دقیق، گیرهها یا اجزای فلزی ماشینکاری شده برای مونتاژ اجزای نوری در فواصل معین و با جهتگیریهای هندسی خاص به یکدیگر استفاده میشود. اجازه دهید برخی از تکنیک های محبوب خود را برای ساخت اپتیک های پیشرفته بررسی کنیم.
سنگ زنی و لپینگ و صیقل دادن: شکل خشن قطعه نوری با آسیاب کردن یک شیشه خالی به دست می آید. سپس با چرخاندن و مالش سطوح ناصاف اجزای نوری بر روی ابزارهایی با شکل های سطحی دلخواه، لایه برداری و پرداخت انجام می شود. دوغاب هایی با ذرات ساینده ریز و سیال در بین اپتیک و ابزارهای شکل دهنده ریخته می شوند. اندازه ذرات ساینده در این گونه دوغاب ها را می توان با توجه به درجه صافی مورد نظر انتخاب کرد. انحراف سطوح نوری بحرانی از اشکال مورد نظر بر حسب طول موج نور مورد استفاده بیان می شود. اپتیک با دقت بالا ما دارای یک دهم طول موج (Wavelength/10) تلورانس یا حتی بیشتر از آن ممکن است. علاوه بر پروفیل سطح، سطوح بحرانی اسکن می شوند و از نظر سایر ویژگی ها و عیوب سطح مانند ابعاد، خراش ها، براده ها، حفره ها، لکه ها و غیره ارزیابی می شوند. کنترل شدید شرایط محیطی در کف تولید نوری و الزامات اندازه گیری و آزمایش گسترده با تجهیزات پیشرفته این صنعت را به یک شاخه چالش برانگیز از صنعت تبدیل کرده است.
• فرآیندهای ثانویه در تولید شیشه: باز هم، ما فقط در مورد فرآیندهای ثانویه و تکمیلی شیشه به تخیل شما محدود می شویم. در اینجا تعدادی از آنها را فهرست می کنیم:
-پوشش روی شیشه (نوری، الکتریکی، تریبولوژیکی، حرارتی، عملکردی، مکانیکی...). به عنوان مثال میتوانیم ویژگیهای سطحی شیشه را تغییر دهیم و بهعنوان مثال، گرما را منعکس کنیم تا فضای داخلی ساختمان خنک بماند، یا با استفاده از فناوری نانو، یک طرف مادون قرمز را جذب کند. این به گرم نگه داشتن داخل ساختمان ها کمک می کند زیرا بیرونی ترین لایه سطحی شیشه اشعه مادون قرمز را در داخل ساختمان جذب می کند و آن را به داخل بازتاب می دهد.
-اچینگ روی شیشه
-برچسب سرامیکی کاربردی (ACL)
-حکاکی
- پرداخت شعله ای
- پولیش شیمیایی
-رنگآمیزی
ساخت سرامیک های فنی
• پرس دای: شامل فشرده سازی تک محوری پودرهای دانه ای محصور در قالب است.
• پرس گرم: شبیه پرس قالب است اما با افزودن دما برای افزایش تراکم. پودر یا پریفرم فشرده در قالب گرافیتی قرار می گیرد و فشار تک محوری اعمال می شود در حالی که قالب در دماهای بالا مانند 2000 درجه سانتیگراد نگهداری می شود. دماها بسته به نوع پودر سرامیکی در حال پردازش می تواند متفاوت باشد. برای شکلها و هندسههای پیچیده، ممکن است به پردازشهای بعدی دیگر مانند آسیاب الماس نیاز باشد.
• پرس ایزواستاتیک: پودرهای گرانول یا مواد فشرده قالبی در ظروف دربسته قرار می گیرند و سپس در یک ظرف تحت فشار بسته با مایع داخل آن قرار می گیرند. سپس با افزایش فشار مخزن تحت فشار فشرده می شوند. مایع داخل ظرف، نیروهای فشار را به طور یکنواخت در کل سطح ظرف محفوظ منتقل می کند. بنابراین مواد به طور یکنواخت فشرده می شوند و شکل ظرف انعطاف پذیر و مشخصات داخلی و ویژگی های آن را به خود می گیرند.
• پرس ایزواستاتیک گرم: مشابه پرس ایزواستاتیک است، اما علاوه بر اتمسفر گاز تحت فشار، ما فشرده را در دمای بالا تف جوشی می کنیم. پرس ایزواستاتیک داغ منجر به تراکم بیشتر و افزایش استحکام می شود.
• ریخته گری لغزنده / ریخته گری تخلیه: قالب را با سوسپانسیونی از ذرات سرامیکی به اندازه میکرومتر و مایع حامل پر می کنیم. این مخلوط "لغزش" نامیده می شود. قالب دارای منافذ است و بنابراین مایع موجود در مخلوط به داخل قالب فیلتر می شود. در نتیجه روی سطوح داخلی قالب قالبی تشکیل می شود. پس از پخت می توان قطعات را از قالب خارج کرد.
• ریخته گری نواری: ما نوارهای سرامیکی را با ریخته گری دوغاب های سرامیکی بر روی سطوح حامل متحرک مسطح تولید می کنیم. دوغاب ها حاوی پودرهای سرامیکی مخلوط با سایر مواد شیمیایی برای مقاصد اتصال و حمل هستند. همانطور که حلال ها تبخیر می شوند ورقه های متراکم و انعطاف پذیر سرامیکی باقی می مانند که می توانند به دلخواه بریده یا نورد شوند.
• شکل دهی اکستروژن: مانند سایر فرآیندهای اکستروژن، مخلوط نرم پودر سرامیک با بایندرها و سایر مواد شیمیایی از داخل قالب عبور داده می شود تا شکل مقطع خود را به دست آورد و سپس در طول های دلخواه برش داده می شود. این فرآیند با مخلوط های سرامیکی سرد یا گرم شده انجام می شود.
قالب گیری تزریقی با فشار کم: مخلوطی از پودر سرامیک را با چسب ها و حلال ها تهیه می کنیم و آن را تا دمایی گرم می کنیم که بتوان آن را به راحتی فشار داد و به داخل حفره ابزار وارد کرد. هنگامی که چرخه قالب گیری کامل شد، قطعه خارج می شود و ماده شیمیایی اتصال سوزانده می شود. با استفاده از قالبگیری تزریقی، میتوانیم قطعات پیچیده را در حجمهای بالا از نظر اقتصادی بدست آوریم. سوراخها که کسری کوچک از میلیمتر بر روی دیواری با ضخامت 10 میلیمتر هستند، امکانپذیر است، رزوهها بدون ماشینکاری دیگر امکانپذیر است، تلرانسهایی تا حد سختی تا 0.5% +/- ممکن است زمانی که قطعات ماشین کاری شوند، حتی کمتر ضخامت دیوار از 0.5 میلی متر تا طول 12.5 میلی متر و همچنین ضخامت دیوار 6.5 میلی متر تا طول 150 میلی متر امکان پذیر است.
• ماشینکاری سبز: با استفاده از همان ابزارهای ماشینکاری فلزی، می توانیم مواد سرامیکی فشرده را در حالی که هنوز مانند گچ نرم هستند، ماشین کنیم. تحمل +/- 1٪ امکان پذیر است. برای تحمل بهتر از آسیاب الماس استفاده می کنیم.
زینترینگ یا پخت: زینترینگ، متراکم شدن کامل را ممکن می سازد. انقباض قابل توجهی در قسمت های فشرده سبز رخ می دهد، اما این مشکل بزرگی نیست زیرا ما این تغییرات ابعادی را هنگام طراحی قطعه و ابزار در نظر می گیریم. ذرات پودر به یکدیگر متصل می شوند و تخلخل ناشی از فرآیند تراکم تا حد زیادی از بین می رود.
• سنگ زنی الماس: سخت ترین ماده جهان "الماس" برای آسیاب کردن مواد سخت مانند سرامیک و قطعات دقیق به دست می آید. تلورانس ها در محدوده میکرومتر و سطوح بسیار صاف به دست می آیند. با توجه به هزینه ای که دارد، ما این تکنیک را تنها زمانی در نظر می گیریم که واقعاً به آن نیاز داشته باشیم.
• مجموعه های HERMETIC آنهایی هستند که عملاً اجازه تبادل ماده، جامد، مایع یا گاز را بین سطوح مشترک نمی دهند. آب بندی هرمتیک هوادار است. به عنوان مثال محفظه های الکترونیکی هرمتیک آنهایی هستند که محتویات داخلی حساس یک دستگاه بسته بندی شده را از رطوبت، آلاینده ها یا گازها در امان نگه می دارند. هیچ چیز 100% هرمتیک نیست، اما وقتی از هرمسیتی صحبت می کنیم، منظورمان این است که از نظر عملی، هرمتیکی وجود دارد تا جایی که میزان نشتی آنقدر کم است که دستگاه ها در شرایط محیطی عادی برای مدت زمان طولانی ایمن هستند. مجموعه های هرمتیک ما شامل اجزای فلزی، شیشه ای و سرامیکی، فلز-سرامیک، سرامیک-فلز-سرامیک، فلز-سرامیک-فلز، فلز به فلز، فلز-شیشه، فلز-شیشه-فلز، شیشه-فلز-شیشه، شیشه- فلز و شیشه به شیشه و سایر ترکیبات اتصال فلز-شیشه-سرامیک. به عنوان مثال، میتوانیم اجزای سرامیکی را پوشش فلزی بپوشانیم تا بتوانند به شدت به اجزای دیگر در مجموعه متصل شوند و قابلیت آببندی عالی داشته باشند. ما دانش پوشش دادن فیبرهای نوری یا ورودی ها را با فلز و لحیم کاری یا لحیم کاری آنها به محفظه ها داریم، بنابراین هیچ گازی به داخل محفظه ها عبور نمی کند یا نشت نمی کند. بنابراین از آنها برای ساخت محفظه های الکترونیکی برای محصور کردن دستگاه های حساس و محافظت از آنها در برابر جو بیرونی استفاده می شود. علاوه بر ویژگیهای آببندی عالی، ویژگیهای دیگری مانند ضریب انبساط حرارتی، مقاومت در برابر تغییر شکل، ماهیت عدم خروج گاز، طول عمر بسیار طولانی، ماهیت نارسانا، خواص عایق حرارتی، طبیعت ضد الکتریسیته ساکن... مواد شیشه ای و سرامیکی را برای کاربردهای خاص انتخاب کنید. اطلاعات مربوط به تاسیسات ما برای تولید اتصالات سرامیکی به فلز، آب بندی هرمتیک، ورودی خلاء، اجزای کنترل خلاء و سیال بالا و فوق العاده بالا را می توانید در اینجا بیابید:بروشور Hermetic Components Factory