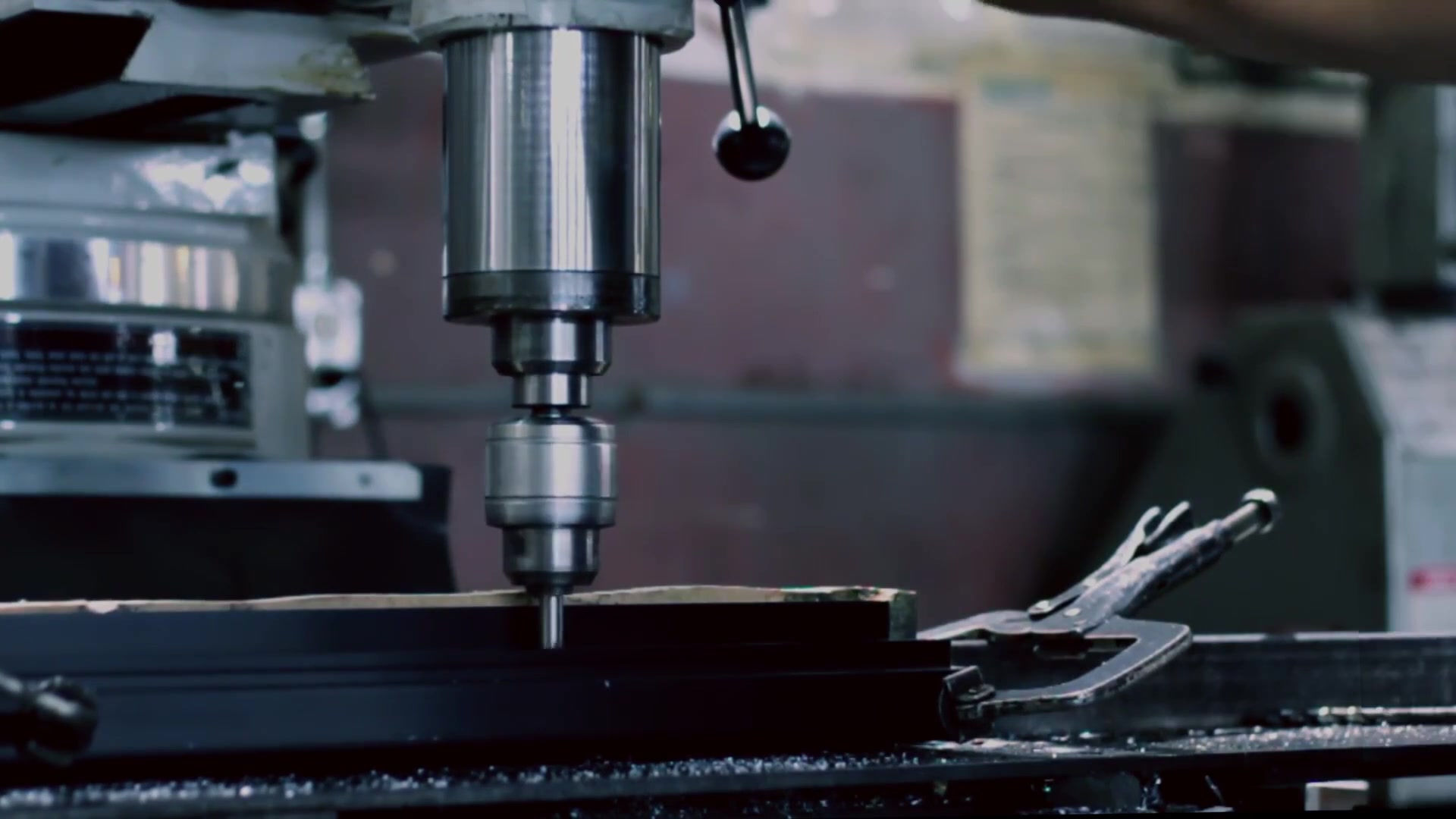
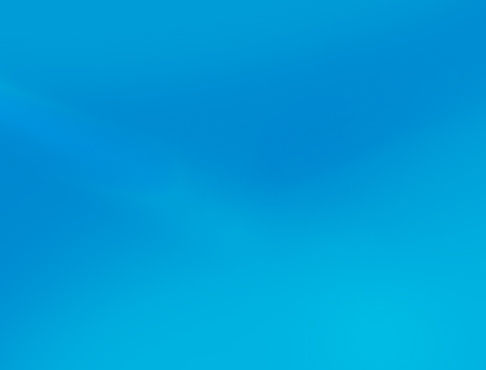
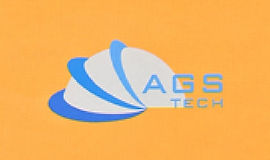
تولید کننده سفارشی جهانی، یکپارچه ساز، تثبیت کننده، شریک برون سپاری برای طیف گسترده ای از محصولات و خدمات.
ما منبع اصلی شما برای تولید، ساخت، مهندسی، ادغام، ادغام، برون سپاری محصولات و خدمات تولید شده سفارشی و خارج از قفسه هستیم.
زبان خود را انتخاب کنید
-
ساخت سفارشی
-
ساخت قرارداد داخلی و جهانی
-
برون سپاری تولید
-
تدارکات داخلی و جهانی
-
Consolidation
-
ادغام مهندسی
-
خدمات مهندسی
نوع فرآیندهای آهنگری فلزی که ما ارائه می دهیم عبارتند از قالب سرد و گرم، قالب باز و قالب بسته، قالب قالب گیری و آهنگری بدون فلاش، cogging، فولرینگ، لبه گذاری و آهنگری دقیق، شکل دهی نزدیک به شبکه. ، تاب دادن، آهنگری ناراحت کننده، سوراخکاری فلزی، پرس و رول و آهنگری شعاعی و مداری و حلقه ای و همدما، سکه زنی، پرچ کردن، آهنگری گلوله ای فلزی، سوراخ کردن فلز، اندازه، آهنگری با نرخ انرژی بالا.
متالورژی پودر و تکنیک های پردازش پودر ما عبارتند از پرس و تف جوشی پودر، اشباع، نفوذ، پرس ایزواستاتیک گرم و سرد، قالب گیری تزریق فلز، فشرده سازی رول، نورد پودر، اکستروژن پودر، تف جوشی شل، تف جوشی جرقه ای، پرس گرم.
توصیه می کنیم اینجا را کلیک کنید
دانلود تصاویر شماتیک ما از فرآیندهای آهنگری توسط AGS-TECH Inc.
دانلود تصاویر شماتیک ما از فرآیندهای متالورژی پودر توسط AGS-TECH Inc.
این فایلهای دانلودی به همراه عکسها و طرحها به شما در درک بهتر اطلاعاتی که در زیر در اختیار شما قرار میدهیم کمک میکنند.
در آهنگری فلزات نیروهای فشاری وارد می شود و ماده تغییر شکل داده و شکل مورد نظر به دست می آید. متداول ترین مواد آهنگری در صنعت آهن و فولاد هستند، اما بسیاری از مواد دیگر مانند آلومینیوم، مس، تیتانیوم، منیزیم نیز به طور گسترده آهنگری می شوند. قطعات فلزی آهنگری علاوه بر ترک های مهر و موم شده و فضاهای خالی بسته، ساختار دانه را بهبود بخشیده اند، بنابراین استحکام قطعات به دست آمده از این فرآیند بیشتر است. آهنگری قطعاتی را تولید میکند که بهطور قابلتوجهی نسبت به قطعاتی که با ریختهگری یا ماشینکاری ساخته میشوند، قویتر هستند. از آنجایی که قطعات آهنگری با ایجاد جریان فلز به شکل نهایی خود شکل میگیرند، فلز ساختار دانهای جهتدار به خود میگیرد که استحکام برتر قطعات را به خود اختصاص میدهد. به عبارت دیگر، قطعات بهدستآمده از فرآیند آهنگری، خواص مکانیکی بهتری را در مقایسه با قطعات ساده ریختهگری یا ماشینکاری شده نشان میدهند. وزن آهنگرهای فلزی می تواند از قطعات سبک وزن کوچک تا صدها هزار پوند متغیر باشد. ما آهنگرها را بیشتر برای کاربردهای مکانیکی میسازیم که در آن تنشهای زیاد بر روی قطعاتی مانند قطعات خودرو، چرخ دندهها، ابزار کار، ابزار دستی، شفت توربین، چرخ دنده موتور سیکلت اعمال میشود. از آنجایی که هزینههای ابزارآلات و راهاندازی نسبتاً زیاد است، ما این فرآیند تولید را فقط برای تولید با حجم بالا و برای قطعات مهم با حجم کم اما با ارزش بالا مانند ارابه فرود هوافضا توصیه میکنیم. علاوه بر هزینه ابزار، زمان تولید قطعات آهنگری با مقادیر زیاد می تواند در مقایسه با برخی از قطعات ماشینکاری ساده طولانی تر باشد، اما این تکنیک برای قطعاتی که نیازمند استحکام فوق العاده ای مانند پیچ و مهره، مهره، کاربرد ویژه بسیار مهم است. بست، خودرو، لیفتراک، قطعات جرثقیل.
• قالب داغ و قالب سرد: آهنگری قالب داغ، همانطور که از نامش پیداست در دماهای بالا انجام می شود، بنابراین شکل پذیری بالا و استحکام مواد کم است. این تغییر شکل و آهنگری آسان را تسهیل می کند. برعکس، فورج قالب سرد در دماهای پایینتر انجام میشود و به نیروهای بیشتری نیاز دارد که منجر به سخت شدن کرنش، سطح بهتر و دقت قطعات تولید شده میشود.
قالب باز و قالب گیری قالب: در آهنگری قالب باز، قالب ها مواد فشرده شده را محدود نمی کنند، در حالی که در قالب قالب گیری، حفره های درون قالب ها جریان مواد را در حالی که به شکل دلخواه آهنگری می کنند، محدود می کنند. UPSET FORGING یا UPSETTING نیز نامیده می شود، که در واقع یکسان نیست اما یک فرآیند بسیار مشابه است، یک فرآیند قالب باز است که در آن قطعه کار بین دو قالب تخت قرار می گیرد و نیروی فشاری ارتفاع آن را کاهش می دهد. با کاهش ارتفاع، عرض قطعه کار افزایش می یابد. HEADING، یک فرآیند آهنگری آشفته شامل استوانهای است که در انتهای خود به هم ریخته و سطح مقطع آن به صورت موضعی افزایش مییابد. در هد، استوک از طریق قالب تغذیه می شود، آهنگری می شود و سپس به طول بریده می شود. این عملیات قادر است مقادیر بالایی از اتصال دهنده ها را به سرعت تولید کند. عمدتاً یک عملیات سرد کار است زیرا برای ساخت انتهای میخ، انتهای پیچ، مهره و پیچ و مهره در جایی که مواد نیاز به تقویت دارند استفاده می شود. یکی دیگر از فرآیندهای قالب باز COGGING است که در آن قطعه کار در یک سری مراحل آهنگری می شود که در هر مرحله منجر به فشرده سازی مواد و حرکت بعدی قالب باز در طول قطعه کار می شود. در هر مرحله ضخامت کاهش می یابد و طول به مقدار کمی افزایش می یابد. این فرآیند شبیه یک دانش آموز عصبی است که مداد خود را در تمام مراحل کوچک گاز می گیرد. فرآیندی به نام FULLERING یکی دیگر از روش های آهنگری قالب باز است که ما اغلب به عنوان مرحله اولیه برای توزیع مواد در قطعه کار قبل از انجام سایر عملیات آهنگری فلز به کار می بریم. زمانی از آن استفاده می کنیم که قطعه کار نیاز به چندین عملیات فورج داشته باشد. در این عملیات، قالب با سطوح محدب تغییر شکل داده و باعث جریان فلز به دو طرف می شود. از طرف دیگر، EDGING فرآیندی مشابه با پر کردن، شامل قالب باز با سطوح مقعر برای تغییر شکل قطعه کار است. لبهبندی همچنین یک فرآیند آمادهسازی برای عملیات آهنگری بعدی است که باعث میشود مواد از هر دو طرف به یک ناحیه در مرکز جریان یابد. IMPRESSION DIE FORGING یا CLOSED DIE FORGING همانطور که به آن نیز گفته می شود از قالب / قالبی استفاده می کند که مواد را فشرده می کند و جریان آن را در داخل خود محدود می کند. قالب بسته می شود و مواد به شکل حفره قالب / قالب می گیرند. آهنگری دقیق، فرآیندی که به تجهیزات و قالب خاصی نیاز دارد، قطعاتی را بدون فلاش یا بسیار کم تولید می کند. به عبارت دیگر قطعات تقریباً ابعاد نهایی خواهند داشت. در این فرآیند مقداری از مواد به خوبی کنترل شده با دقت وارد شده و در داخل قالب قرار می گیرد. ما این روش را برای اشکال پیچیده با مقاطع نازک، تلورانس های کوچک و زوایای کشش و زمانی که مقادیر به اندازه کافی بزرگ هستند تا هزینه های قالب و تجهیزات را توجیه کنند، به کار می بریم.
• آهنگری بدون فلاش: قطعه کار به گونه ای در قالب قرار می گیرد که هیچ ماده ای نتواند از حفره خارج شود و فلاش را تشکیل دهد. بنابراین نیازی به برش ناخواسته فلاش نیست. این یک فرآیند آهنگری دقیق است و بنابراین نیاز به کنترل دقیق مقدار مواد مورد استفاده دارد.
• آهنگری فلزی یا آهنگری شعاعی: یک قطعه کار به صورت محیطی توسط قالب و آهنگری بر روی آن اثر می گذارد. همچنین می توان از سنبه برای جعل هندسه قطعه کار داخلی استفاده کرد. در عملیات swaging قطعه کار معمولاً چندین ضربه در ثانیه دریافت می کند. اقلام معمولی که توسط چرخاندن تولید می شوند عبارتند از ابزارهای نوک تیز، میله های مخروطی، پیچ گوشتی ها.
• سوراخ کردن فلز: ما اغلب از این عملیات به عنوان یک عملیات اضافی در ساخت قطعات استفاده می کنیم. یک سوراخ یا حفره با سوراخ کردن روی سطح قطعه کار بدون شکستن آن ایجاد می شود. لطفاً توجه داشته باشید که سوراخ کردن با سوراخ کردن متفاوت است که منجر به ایجاد سوراخ می شود.
• HOBBING : پانچ با هندسه دلخواه در قطعه کار فشرده شده و حفره ای به شکل دلخواه ایجاد می کند. ما به این پانچ HOB می گوییم. این عملیات شامل فشارهای بالا است و در سرما انجام می شود. در نتیجه مواد سرد کار شده و با کرنش سخت می شوند. بنابراین این فرآیند برای ساخت قالب، قالب و حفره برای سایر فرآیندهای تولید بسیار مناسب است. هنگامی که اجاق گاز ساخته شد، می توان به راحتی بسیاری از حفره های یکسان را بدون نیاز به ماشینکاری تک تک آنها ساخت.
• ROLL FORGING یا ROLL FORMING : دو رول متضاد برای شکل دادن به قسمت فلزی استفاده می شود. قطعه کار وارد رول ها می شود، رول ها می چرخند و کار را به داخل شکاف می کشند، سپس کار از طریق قسمت شیاردار رول ها وارد می شود و نیروهای فشاری شکل دلخواه را به مواد می دهند. این یک فرآیند نورد نیست، بلکه یک فرآیند آهنگری است، زیرا یک عملیات گسسته و نه پیوسته است. هندسه روی نخلستان های رول، مواد را به شکل و هندسه مورد نیاز جعل می کند. گرم اجرا می شود. به دلیل اینکه یک فرآیند آهنگری است، قطعاتی با خواص مکانیکی برجسته تولید می کند و بنابراین از آن برای ساخت قطعات خودرو مانند شفت هایی که نیاز به استقامت فوق العاده در محیط های کاری سخت دارند استفاده می کنیم.
• آهنگری مداری: قطعه کار در یک حفره قالب آهنگری قرار داده می شود و توسط قالب بالایی که در یک مسیر مداری حرکت می کند و در یک محور شیبدار می چرخد، آهنگری می شود. در هر چرخش، قالب بالایی اعمال نیروهای فشاری را به کل قطعه کار تکمیل می کند. با تکرار چند بار این چرخش ها آهنگری کافی انجام می شود. از مزایای این روش ساخت می توان به عملکرد کم صدا و نیروهای کمتر مورد نیاز آن اشاره کرد. به عبارت دیگر با نیروهای کم می توان یک قالب سنگین را حول یک محور چرخاند تا فشارهای زیادی بر روی قسمتی از قطعه کار که در تماس با قالب است اعمال شود. قطعات دیسکی یا مخروطی شکل گاهی اوقات برای این فرآیند مناسب هستند.
• آهنگری حلقه: ما اغلب برای تولید حلقه های بدون درز استفاده می کنیم. استوک به طول بریده می شود، ناراحت می شود و سپس تا انتها سوراخ می شود تا یک سوراخ مرکزی ایجاد شود. سپس روی سنبه قرار میگیرد و قالب آهنگری آن را از بالا میکوبد و حلقه به آرامی میچرخد تا ابعاد دلخواه به دست آید.
پرچ کردن: یک فرآیند معمول برای اتصال قطعات، با یک قطعه فلزی مستقیم که در سوراخ های از پیش ساخته شده از طریق قطعات وارد می شود، شروع می شود. سپس دو سر قطعه فلزی با فشردن محل اتصال بین قالب بالایی و پایینی آهنگری می شود.
• سکه گذاری: یکی دیگر از فرآیندهای رایج که توسط پرس مکانیکی انجام می شود و نیروهای زیادی را در فاصله کوتاهی اعمال می کند. نام سکهسازی از جزئیات ظریفی که بر روی سطوح سکههای فلزی جعل میشود، گرفته میشود. این عمدتاً یک فرآیند تکمیلی برای محصولی است که در آن جزئیات ظریف بر روی سطوح در نتیجه نیروی زیاد اعمال شده توسط قالب که این جزئیات را به قطعه کار منتقل می کند، به دست می آید.
• آهنگری گلوله ای فلزی: محصولاتی مانند بلبرینگ ها به توپ های فلزی با کیفیت بالا نیاز دارند. در یک تکنیک به نام SKEW ROLLING، از دو رول متضاد استفاده میکنیم که بهطور پیوسته در حال چرخش استوک به طور مداوم به رولها میچرخند. در یک انتهای دو رول، کره های فلزی به عنوان محصول خارج می شوند. روش دوم برای آهنگری گلوله ای فلزی استفاده از قالبی است که مواد موجود در بین آنها را فشرده می کند و شکل کروی حفره قالب را می گیرد. اغلب اوقات توپ های تولید شده برای تبدیل شدن به یک محصول با کیفیت به مراحل اضافی مانند تکمیل و پرداخت نیاز دارند.
• آهنگری ایزوترمال / آهنگری قالب داغ: یک فرآیند گران قیمت که تنها زمانی انجام می شود که سود / ارزش هزینه توجیه شده باشد. یک فرآیند کار داغ که در آن قالب تا دمایی برابر با قطعه کار گرم می شود. از آنجایی که دمای قالب و کار تقریباً یکسان است، خنک کننده وجود ندارد و ویژگی های جریان فلز بهبود می یابد. این عملیات برای سوپر آلیاژها و مواد با قابلیت جعل پذیری پایین و موادی که مناسب است
خواص مکانیکی به شیب و تغییرات دما بسیار حساس است.
• اندازه فلز: این یک فرآیند تکمیل سرد است. جریان مواد در تمام جهات به استثنای جهتی که نیرو در آن اعمال می شود، نامحدود است. در نتیجه سطح بسیار خوب و ابعاد دقیق به دست می آید.
• آهنگری با نرخ انرژی بالا: این تکنیک شامل قالب بالایی متصل به بازوی پیستون است که با مشتعل شدن مخلوط سوخت و هوا توسط یک شمع به سرعت هل داده می شود. این شبیه عملکرد پیستون در موتور ماشین است. قالب خیلی سریع به قطعه کار برخورد می کند و سپس به لطف فشار برگشتی خیلی سریع به موقعیت اولیه خود باز می گردد. کار در عرض چند میلی ثانیه فورج می شود و بنابراین زمانی برای خنک شدن کار وجود ندارد. این برای قطعات سخت آهنگری که دارای خواص مکانیکی بسیار حساس به دما هستند مفید است. به عبارت دیگر فرآیند آنقدر سریع است که قطعه تحت دمای ثابت در سرتاسر شکل میگیرد و شیب دما در رابطهای قالب/قطعه کار وجود نخواهد داشت.
• در DIE FORGING، فلز بین دو بلوک فولادی منطبق با اشکال خاص در آنها که قالب نامیده می شود، کوبیده می شود. هنگامی که فلز بین قالب ها کوبیده می شود، شکلی مشابه شکل های موجود در قالب به خود می گیرد. وقتی به شکل نهایی رسید بیرون می آورند تا خنک شود. این فرآیند قطعات محکمی را تولید می کند که شکل دقیقی دارند، اما نیاز به سرمایه گذاری بیشتر برای قالب های تخصصی دارد. آهنگری ناراحت کننده قطر یک قطعه فلز را با صاف کردن آن افزایش می دهد. به طور کلی برای ساخت قطعات کوچک، به ویژه برای ایجاد سر بر روی اتصال دهنده ها مانند پیچ و مهره استفاده می شود.
• متالورژی پودر / پردازش پودر: همانطور که از نام آن پیداست، شامل فرآیندهای ساخت برای ساخت قطعات جامد هندسه ها و اشکال خاص از پودر است. اگر از پودرهای فلزی برای این منظور استفاده شود، حوزه متالورژی پودر و اگر از پودرهای غیر فلزی استفاده شود، فرآوری پودر است. قطعات جامد از پودرها با پرس و تف جوشی تولید می شوند.
پودر پرس برای فشرده سازی پودرها به شکل دلخواه استفاده می شود. ابتدا، ماده اولیه به صورت فیزیکی پودر می شود و آن را به بسیاری از ذرات کوچک جداگانه تقسیم می کند. مخلوط پودر داخل قالب پر می شود و پانچ به سمت پودر حرکت می کند و آن را به شکل دلخواه فشرده می کند. بیشتر در دمای اتاق انجام می شود که با پرس پودر یک قسمت جامد به دست می آید و به آن فشرده سبز می گویند. چسب ها و روان کننده ها معمولا برای افزایش تراکم پذیری استفاده می شوند. ما قادر به شکل دهی پرس پودری با استفاده از پرس های هیدرولیک با ظرفیت چند هزار تن هستیم. همچنین ما پرس های دوتایی با پانچ های بالا و پایین مخالف و همچنین پرس های چندگانه برای هندسه های بسیار پیچیده قطعات داریم. یکنواختی که یک چالش مهم برای بسیاری از کارخانه های متالورژی پودر / فرآوری پودر است، مشکل بزرگی برای AGS-TECH به دلیل تجربه گسترده ما در تولید سفارشی چنین قطعاتی برای سال ها نیست. حتی با قطعات ضخیم تر که یکنواختی یک چالش است، ما موفق شده ایم. اگر ما به پروژه شما متعهد باشیم، قطعات شما را خواهیم ساخت. در صورت مشاهده هرگونه خطر احتمالی، به شما اطلاع خواهیم داد in
advance.
زینترینگ پودری که مرحله دوم است، شامل افزایش دما تا حد معینی و حفظ دما در آن سطح برای مدت معینی است تا ذرات پودر در قسمت فشرده شده بتوانند به یکدیگر بچسبند. این منجر به پیوندهای بسیار قوی تر و استحکام قطعه کار می شود. تف جوشی نزدیک به دمای ذوب پودر انجام می شود. در طول پخت، انقباض رخ می دهد، استحکام مواد، چگالی، شکل پذیری، هدایت حرارتی، هدایت الکتریکی افزایش می یابد. ما کوره های دسته ای و پیوسته برای پخت داریم. یکی از قابلیت های ما تنظیم سطح تخلخل قطعاتی است که تولید می کنیم. به عنوان مثال، ما قادر به تولید فیلترهای فلزی با متخلخل نگه داشتن قطعات تا حدی هستیم.
با استفاده از تکنیکی به نام IMPREGNATION، منافذ فلز را با مایعی مانند روغن پر می کنیم. ما به عنوان مثال یاتاقان های آغشته به روغن تولید می کنیم که خود روان کننده هستند. در فرآیند INFILTRATION، منافذ یک فلز را با فلز دیگری با نقطه ذوب پایینتر از ماده پایه پر میکنیم. مخلوط تا دمای بین دمای ذوب دو فلز گرم می شود. در نتیجه می توان برخی از خواص ویژه را به دست آورد. ما همچنین اغلب عملیات ثانویه مانند ماشینکاری و آهنگری را بر روی قطعات تولید شده پودر انجام می دهیم، زمانی که باید ویژگی ها یا ویژگی های خاصی را به دست آورد یا زمانی که قطعه را می توان با مراحل فرآیند کمتری تولید کرد.
پرس ایزواستاتیک: در این فرآیند از فشار سیال برای فشرده سازی قطعه استفاده می شود. پودرهای فلزی در یک قالب ساخته شده از یک ظرف انعطاف پذیر در بسته قرار می گیرند. در پرس ایزواستاتیک، بر خلاف فشار محوری که در پرس معمولی دیده می شود، فشار از اطراف اعمال می شود. از مزایای پرس ایزواستاتیک، چگالی یکنواخت درون قطعه، به ویژه برای قطعات بزرگتر یا ضخیم تر، خواص برتر است. نقطه ضعف آن زمان چرخه طولانی و دقت هندسی نسبتا کم است. پرس ایزواستاتیک سرد در دمای اتاق انجام می شود و قالب انعطاف پذیر از لاستیک، PVC یا یورتان یا مواد مشابه ساخته شده است. سیال مورد استفاده برای فشار دادن و فشرده سازی روغن یا آب است. تف جوشی معمولی فشرده سبز به دنبال این است. از طرف دیگر فشار ایزواستاتیک گرم در دماهای بالا انجام می شود و مواد قالب از ورق فلز یا سرامیک با نقطه ذوب به اندازه کافی بالا است که در برابر دما مقاومت می کند. سیال تحت فشار معمولاً یک گاز بی اثر است. عملیات پرس و تف جوشی در یک مرحله انجام می شود. تخلخل تقریباً به طور کامل حذف شده است، یک ساختار uniform grain به دست می آید. مزیت پرس ایزواستاتیک گرم این است که می تواند قطعاتی قابل مقایسه با ترکیب ریخته گری و آهنگری تولید کند و در عین حال موادی را که برای ریخته گری و آهنگری مناسب نیستند قابل استفاده باشد. نقطه ضعف پرس ایزواستاتیک گرم زمان چرخه بالا و در نتیجه هزینه آن است. برای قسمت های بحرانی با حجم کم مناسب است.
قالبگیری تزریقی فلز: فرآیندی بسیار مناسب برای تولید قطعات پیچیده با دیوارههای نازک و هندسههای دقیق. مناسب ترین برای قطعات کوچکتر. پودرها و بایندر پلیمری مخلوط، حرارت داده شده و به قالب تزریق می شوند. بایندر پلیمری سطوح ذرات پودر را می پوشاند. پس از قالب گیری، بایندر با حرارت دادن در دمای پایین محلول با استفاده از یک حلال حذف می شود.
فشرده سازی رول / نورد پودری: از پودرها برای تولید نوارها یا ورق های پیوسته استفاده می شود. پودر از یک فیدر تغذیه می شود و توسط دو رول چرخان به صورت ورق یا نوار فشرده می شود. عملیات به صورت سرد انجام می شود. ورق به داخل کوره تف جوشی حمل می شود. فرآیند پخت ممکن است برای بار دوم تکرار شود.
اکستروژن پودری: قطعات با نسبت طول به قطر زیاد با اکسترود کردن یک ظرف ورق فلزی نازک با پودر ساخته می شوند.
تف جوشی شل: همانطور که از نام آن پیداست، روشی بدون فشار و بدون فشار است که برای تولید قطعات بسیار متخلخل مانند فیلترهای فلزی مناسب است. پودر بدون فشرده شدن به داخل حفره قالب وارد می شود.
تف جوشی شل: همانطور که از نام آن پیداست، روشی بدون فشار و بدون فشار است که برای تولید قطعات بسیار متخلخل مانند فیلترهای فلزی مناسب است. پودر بدون فشرده شدن به داخل حفره قالب وارد می شود.
SPARK SINTERING : پودر توسط دو پانچ مخالف در قالب فشرده می شود و جریان الکتریکی با قدرت بالا به پانچ وارد می شود و از پودر فشرده که در بین آنها قرار گرفته است عبور می کند. جریان بالا، لایههای سطحی را از ذرات پودر میسوزاند و آنها را با گرمای تولید شده متخلخل میکند. این فرآیند سریع است زیرا گرما از خارج اعمال نمی شود بلکه از داخل قالب تولید می شود.
پرس گرم: پودرها در یک مرحله در قالبی که می تواند در برابر درجه حرارت بالا مقاومت کند، فشرده و پخته می شوند. همانطور که قالب فشرده می شود، گرمای پودر به آن اعمال می شود. دقت و خواص مکانیکی خوب به دست آمده توسط این روش، آن را به گزینه ای جذاب تبدیل می کند. حتی فلزات نسوز را می توان با استفاده از مواد قالب مانند گرافیت پردازش کرد.