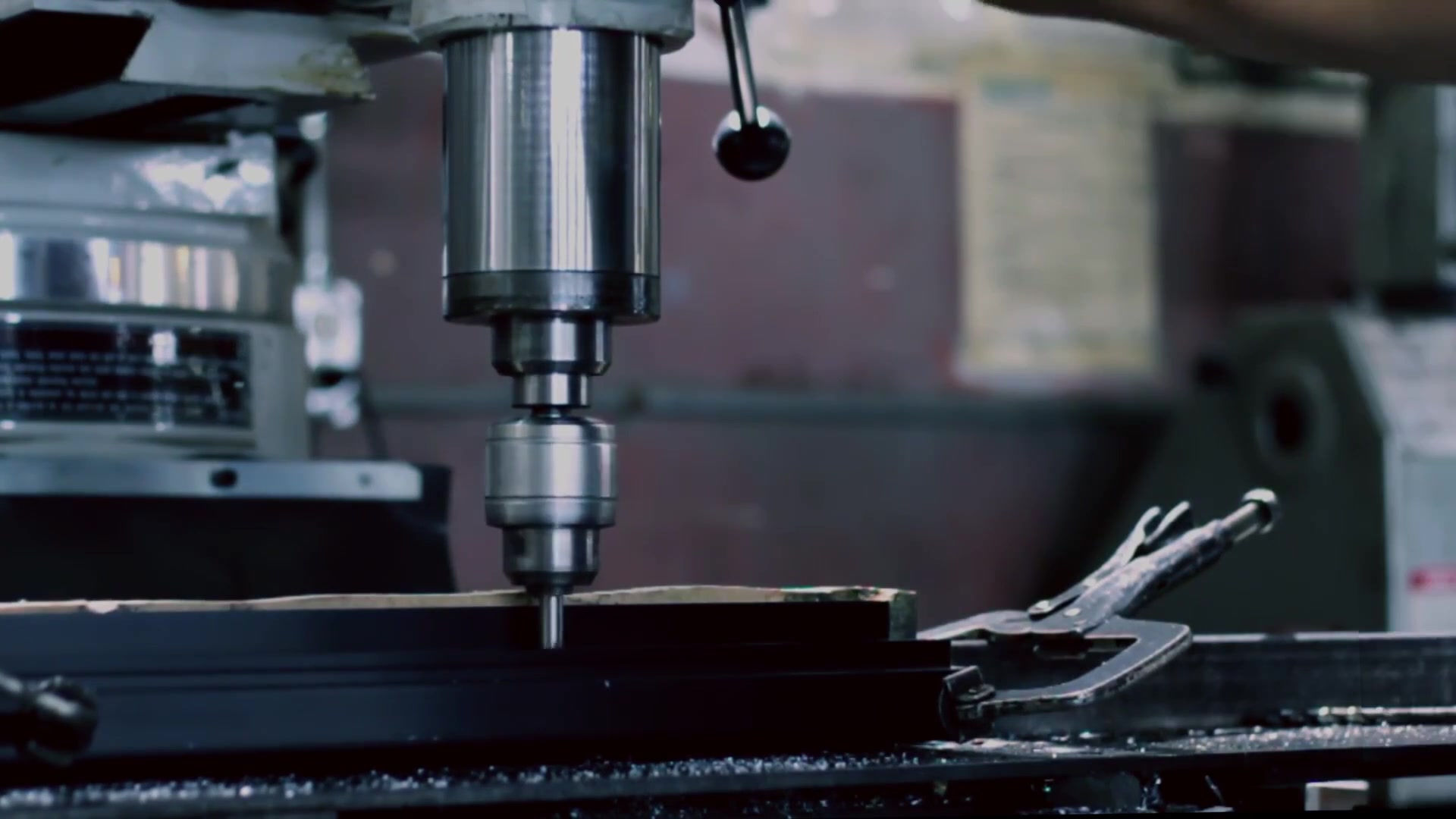
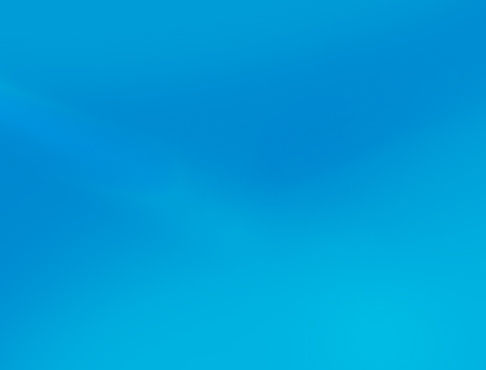
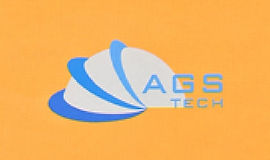
تولید کننده سفارشی جهانی، یکپارچه ساز، تثبیت کننده، شریک برون سپاری برای طیف گسترده ای از محصولات و خدمات.
ما منبع اصلی شما برای تولید، ساخت، مهندسی، ادغام، ادغام، برون سپاری محصولات و خدمات تولید شده سفارشی و خارج از قفسه هستیم.
زبان خود را انتخاب کنید
-
ساخت سفارشی
-
ساخت قرارداد داخلی و جهانی
-
برون سپاری تولید
-
تدارکات داخلی و جهانی
-
Consolidation
-
ادغام مهندسی
-
خدمات مهندسی
We use the PLASMA CUTTING and PLASMA MACHINING processes to cut and machine steel, aluminum, metals and other materials of ضخامت های مختلف با استفاده از مشعل پلاسما. در برش پلاسما (که گاهی اوقات PLASMA-ARC CUTTING نیز نامیده می شود)، یک گاز بی اثر یا هوای فشرده با سرعت زیاد از یک نازل خارج می شود و به طور همزمان یک قوس الکتریکی از نازل به آن گاز تشکیل می شود. سطح در حال برش، تبدیل بخشی از آن گاز به پلاسما. برای ساده تر، پلاسما را می توان به عنوان حالت چهارم ماده توصیف کرد. سه حالت ماده جامد، مایع و گاز است. برای مثال معمول آب، این سه حالت یخ، آب و بخار هستند. تفاوت بین این حالت ها به سطح انرژی آنها مربوط می شود. وقتی انرژی را به صورت گرما به یخ اضافه می کنیم، ذوب می شود و آب تشکیل می شود. وقتی انرژی بیشتری اضافه می کنیم، آب به شکل بخار تبخیر می شود. با افزودن انرژی بیشتر به بخار، این گازها یونیزه می شوند. این فرآیند یونیزاسیون باعث می شود که گاز رسانای الکتریکی شود. ما این گاز یونیزه و رسانای الکتریکی را "پلاسما" می نامیم. پلاسما بسیار داغ است و فلز در حال برش را ذوب می کند و در عین حال فلز مذاب را از برش دور می کند. ما از پلاسما برای برش مواد نازک و ضخیم، آهنی و غیر آهنی به طور یکسان استفاده می کنیم. مشعل های دستی ما معمولاً می توانند صفحه فولادی با ضخامت 2 اینچ را برش دهند و مشعل های قوی تر با کنترل رایانه ما می توانند فولاد تا ضخامت 6 اینچ را برش دهند. برش های پلاسما یک مخروط بسیار داغ و موضعی برای برش ایجاد می کنند و بنابراین برای برش ورق های فلزی در اشکال منحنی و زاویه دار بسیار مناسب هستند. دمای تولید شده در برش قوس پلاسما بسیار بالا و در حدود 9673 کلوین در مشعل پلاسمای اکسیژن است. این یک فرآیند سریع، عرض کوچک و پرداخت سطح خوب را به ما ارائه می دهد. در سیستم های ما که از الکترودهای تنگستن استفاده می کنند، پلاسما خنثی است و با استفاده از گازهای آرگون، آرگون-H2 یا نیتروژن تشکیل می شود. با این حال، گاهی اوقات از گازهای اکسید کننده مانند هوا یا اکسیژن نیز استفاده می کنیم و در آن سیستم ها الکترود مس با هافنیوم است. مزیت مشعل پلاسمای هوا این است که از هوا به جای گازهای گران قیمت استفاده می کند، بنابراین به طور بالقوه هزینه کلی ماشینکاری را کاهش می دهد.
Our HF-TYPE PLASMA CUTTING machines از هد با فرکانس بالا و ولتاژ بالا برای تابش ولتاژ هوا استفاده می کنند. برشهای پلاسما HF ما نیازی به تماس مشعل با مواد قطعه کار در ابتدا ندارند و برای کاربردهایی که شامل COMPUTER NUMERICAL CONTROL (CNC)_cc781905-31905-381905-2000 میشوند، مناسب هستند. تولیدکنندگان دیگر از ماشینهای اولیه استفاده میکنند که برای شروع به تماس نوک با فلز اصلی نیاز دارند و سپس جداسازی شکاف رخ میدهد. این برشهای پلاسما ابتداییتر در هنگام راهاندازی بیشتر در معرض آسیب نوک و سپر تماسی هستند.
Our PILOT-ARC TYPE PLASMA machines از یک فرآیند دو مرحله ای برای تولید پلاسما بدون نیاز به تماس اولیه استفاده می کنند. در مرحله اول، یک مدار ولتاژ بالا و جریان کم برای راه اندازی یک جرقه بسیار کوچک با شدت بالا در بدنه مشعل استفاده می شود و یک جیب کوچک از گاز پلاسما تولید می کند. به این قوس خلبان می گویند. قوس خلبان دارای یک مسیر الکتریکی برگشتی است که در سر مشعل تعبیه شده است. قوس پایلوت تا زمانی که به قطعه کار نزدیک شود حفظ و نگهداری می شود. در آنجا قوس پیلوت قوس اصلی برش پلاسما را مشتعل می کند. قوس های پلاسما بسیار داغ هستند و در محدوده 25000 درجه سانتیگراد = 45000 درجه فارنهایت قرار دارند.
روش سنتیتری که ما نیز به کار میبریم این است OXYFUEL-GAS CUTTING (OFC) که در آن از awel استفاده میکنیم. این عملیات در برش فولاد، چدن و فولاد چدنی استفاده می شود. اصل برش در برش اکسی سوخت گاز بر اکسیداسیون، سوزاندن و ذوب فولاد است. عرض کرف در برش اکسی سوخت گاز در همسایگی 1.5 تا 10 میلی متر است. فرآیند قوس پلاسما به عنوان جایگزینی برای فرآیند اکسی سوخت دیده شده است. فرآیند قوس پلاسما با فرآیند سوخت اکسی تفاوت دارد زیرا با استفاده از قوس برای ذوب فلز عمل می کند در حالی که در فرآیند اکسی سوخت، اکسیژن فلز را اکسید می کند و گرمای حاصل از واکنش گرمازا فلز را ذوب می کند. بنابراین، برخلاف فرآیند اکسی سوخت، فرآیند پلاسما را می توان برای برش فلزاتی که اکسیدهای نسوز مانند فولاد ضد زنگ، آلومینیوم و آلیاژهای غیر آهنی تشکیل می دهند، به کار برد.
PLASMA GOUGING یک فرآیند مشابه با برش پلاسما، معمولاً با تجهیزات مشابه برش پلاسما انجام می شود. به جای برش مواد، پلاسما گوگ از پیکربندی مشعل متفاوتی استفاده می کند. نازل مشعل و پخش کننده گاز معمولاً متفاوت است و فاصله مشعل تا قطعه کار برای دمیدن فلز بیشتر است. پلاسما گوگ را می توان در کاربردهای مختلف از جمله برداشتن جوش برای کار مجدد استفاده کرد.
برخی از برش های پلاسما ما روی میز CNC تعبیه شده اند. میزهای CNC دارای یک کامپیوتر برای کنترل سر مشعل برای ایجاد برش های تیز تمیز هستند. تجهیزات پلاسما CNC مدرن ما قادر به برش چند محوری مواد ضخیم هستند و فرصت هایی را برای درزهای جوشکاری پیچیده که در غیر این صورت امکان پذیر نیست، فراهم می کند. برشهای قوس پلاسما ما با استفاده از کنترلهای قابل برنامهریزی بسیار خودکار هستند. برای مواد نازک تر، ما برش لیزر را به برش پلاسما ترجیح می دهیم، بیشتر به دلیل توانایی برتر برش سوراخ برش لیزری ما. ما همچنین ماشینهای برش پلاسما CNC عمودی را به کار میگیریم که ردپایی کوچکتر، انعطافپذیری بیشتر، ایمنی بهتر و عملکرد سریعتر را به ما ارائه میدهد. کیفیت لبه برش پلاسما مشابه آن چیزی است که با فرآیندهای برش اکسی سوخت به دست می آید. با این حال، از آنجایی که فرآیند پلاسما با ذوب شدن قطع میشود، یکی از ویژگیهای بارز درجه ذوب بیشتر به سمت بالای فلز است که منجر به گرد شدن لبه بالایی، مربعی ضعیف لبه یا یک اریب در لبه برش میشود. ما از مدلهای جدید مشعلهای پلاسما با نازل کوچکتر و قوس پلاسمایی نازکتر برای بهبود انقباض قوس استفاده میکنیم تا گرمایش یکنواختتری در بالا و پایین برش ایجاد کنیم. این به ما امکان می دهد تا دقت لیزری را روی لبه های برش پلاسما و ماشین کاری شده به دست آوریم. Our برش قوس پلاسما با تحمل بالا (HTPAC) سیستمهایی که دارای مخاطرات پلاسمایی بالا هستند. تمرکز پلاسما با وادار کردن پلاسمای تولید شده اکسیژن به چرخش به هنگام ورود به دهانه پلاسما و تزریق جریان ثانویه گاز در پایین دست نازل پلاسما حاصل می شود. ما یک میدان مغناطیسی مجزا در اطراف قوس داریم. این امر با حفظ چرخش ناشی از گاز چرخان، جت پلاسما را تثبیت می کند. با ترکیب کنترل دقیق CNC با این مشعلهای کوچکتر و نازکتر، میتوانیم قطعاتی را تولید کنیم که نیاز به پرداخت کم یا بدون پرداخت دارند. نرخ حذف مواد در ماشینکاری پلاسما بسیار بالاتر از فرآیندهای ماشینکاری تخلیه الکتریکی (EDM) و ماشینکاری پرتو لیزری (LBM) است و قطعات را می توان با قابلیت تکرارپذیری خوب ماشینکاری کرد.
جوشکاری قوس پلاسما (PAW) فرآیندی شبیه به جوشکاری قوسی تنگستن گازی (GTAW) است. قوس الکتریکی بین یک الکترود به طور کلی از تنگستن متخلخل و قطعه کار تشکیل می شود. تفاوت اصلی با GTAW این است که در PAW، با قرار دادن الکترود در داخل بدنه مشعل، قوس پلاسما را می توان از پوشش گاز محافظ جدا کرد. پلاسما سپس از طریق یک نازل مسی ریز سوراخ می شود که قوس و پلاسمای خروجی از روزنه را در سرعت های بالا و دمای نزدیک به 20000 درجه سانتی گراد منقبض می کند. جوشکاری قوس پلاسما پیشرفتی نسبت به فرآیند GTAW است. فرآیند جوشکاری PAW از یک الکترود تنگستن غیر مصرفی و یک قوس منقبض شده از طریق یک نازل مسی با سوراخ ریز استفاده می کند. PAW را می توان برای اتصال تمام فلزات و آلیاژهایی که با GTAW قابل جوش هستند استفاده کرد. چندین تغییر اساسی فرآیند PAW با تغییر جریان، سرعت جریان گاز پلاسما و قطر روزنه ممکن است، از جمله:
میکرو پلاسما (< 15 آمپر)
حالت ذوب (15-400 آمپر)
حالت سوراخ کلید (بیش از 100 آمپر)
در جوشکاری قوس پلاسما (PAW) غلظت انرژی بیشتری نسبت به GTAW بدست می آوریم. نفوذ عمیق و باریک با حداکثر عمق 12 تا 18 میلی متر (0.47 تا 0.71 اینچ) بسته به ماده قابل دستیابی است. پایداری بیشتر قوس طول قوس بسیار طولانیتری (استانداخت) و تحمل بسیار بیشتر در برابر تغییرات طول قوس را ممکن میسازد.
به عنوان یک نقطه ضعف، PAW در مقایسه با GTAW به تجهیزات نسبتاً گران و پیچیده ای نیاز دارد. همچنین تعمیر و نگهداری مشعل بسیار مهم و چالش برانگیزتر است. سایر معایب PAW عبارتند از: روشهای جوشکاری پیچیدهتر هستند و نسبت به تغییرات در تناسب و غیره تحمل کمتری دارند. مهارت اپراتور کمی بیشتر از GTAW است. تعویض روزنه ضروری است.