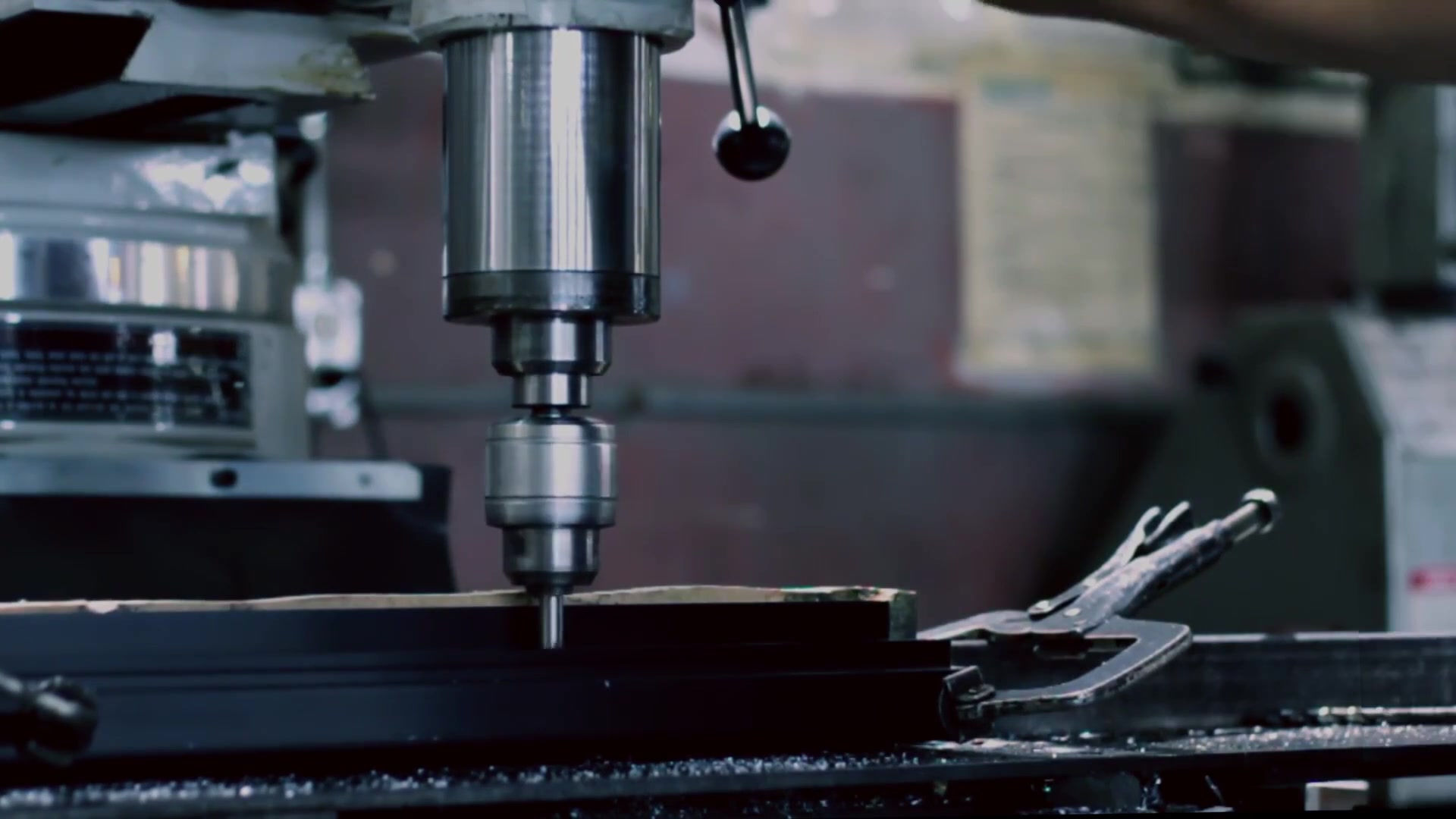
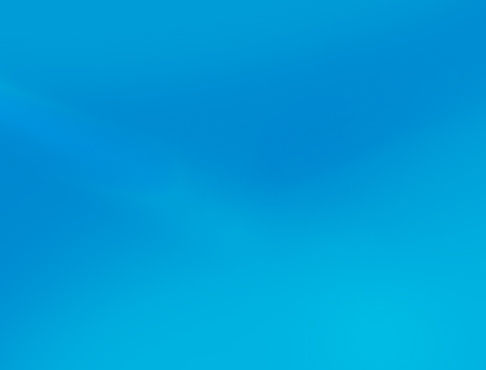
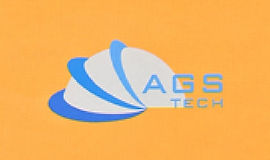
Fabricant mondial sur mesure, intégrateur, consolidateur, partenaire d'externalisation pour une grande variété de produits et services.
Nous sommes votre source unique pour la fabrication, la fabrication, l'ingénierie, la consolidation, l'intégration, l'externalisation de produits et services fabriqués sur mesure et prêts à l'emploi.
Choisissez votre langue
-
Fabrication sur mesure
-
Fabrication sous contrat nationale et mondiale
-
Sous-traitance de fabrication
-
Approvisionnement national et mondial
-
Consolidation
-
Intégration d'ingénierie
-
Services d'ingénierie
Parmi les nombreuses techniques d'ASSEMBLAGE que nous déployons dans la fabrication, un accent particulier est mis sur le SOUDAGE, le BRASAGE, le SOUDAGE, le COLLAGE et l'ASSEMBLAGE MÉCANIQUE SUR MESURE car ces techniques sont largement utilisées dans des applications telles que la fabrication d'assemblages hermétiques, la fabrication de produits de haute technologie et l'étanchéité spécialisée. Ici, nous nous concentrerons sur les aspects plus spécialisés de ces techniques d'assemblage car ils sont liés à la fabrication de produits et d'assemblages avancés.
SOUDAGE PAR FUSION : Nous utilisons la chaleur pour faire fondre et coalescer les matériaux. La chaleur est fournie par l'électricité ou des poutres à haute énergie. Les types de soudage par fusion que nous déployons sont le SOUDAGE AU GAZ OXYFUEL, LE SOUDAGE À L'ARC, LE SOUDAGE PAR FAISCEAU À HAUTE ÉNERGIE.
SOUDAGE À L'ÉTAT SOLIDE : Nous assemblons des pièces sans fusion ni fusion. Nos méthodes de soudage à l'état solide sont le soudage à froid, par ultrasons, par résistance, par friction, par explosion et par diffusion.
BRASAGE & SOUDURE : Ils utilisent des métaux d'apport et nous donnent l'avantage de travailler à des températures plus basses qu'en soudage, donc moins de dommages structurels aux produits. Des informations sur notre installation de brasage produisant des raccords céramique-métal, des joints hermétiques, des traversées de vide, des composants de contrôle des fluides et des vides poussés et ultra-poussés peuvent être trouvées ici :Brochure de l'usine de brasage
COLLAGE ADHÉSIF : En raison de la diversité des adhésifs utilisés dans l'industrie et aussi de la diversité des applications, nous avons une page dédiée à cela. Pour accéder à notre page sur le collage, veuillez cliquer ici.
ASSEMBLAGE MÉCANIQUE SUR MESURE : Nous utilisons une variété de fixations telles que des boulons, des vis, des écrous, des rivets. Nos fixations ne se limitent pas aux fixations standard du commerce. Nous concevons, développons et fabriquons des fixations spécialisées fabriquées à partir de matériaux non standard afin qu'elles puissent répondre aux exigences d'applications spéciales. Parfois, la non-conductivité électrique ou thermique est souhaitée, tandis que parfois la conductivité. Pour certaines applications spéciales, un client peut vouloir des attaches spéciales qui ne peuvent pas être retirées sans détruire le produit. Il existe une infinité d'idées et d'applications. Nous avons tout pour vous, sinon nous pouvons le développer rapidement. Pour accéder à notre page sur l'assemblage mécanique, veuillez cliquer ici. Examinons plus en détail nos différentes techniques d'assemblage.
SOUDAGE AU GAZ OXYFUEL (OFW): Nous utilisons un gaz combustible mélangé à de l'oxygène pour produire la flamme de soudage. Lorsque nous utilisons de l'acétylène comme combustible et de l'oxygène, nous appelons cela le soudage au gaz oxyacétylène. Deux réactions chimiques se produisent dans le processus de combustion des gaz oxycombustibles :
C2H2 + O2 ------» 2CO + H2 + Chaleur
2CO + H2 + 1,5 O2--------» 2 CO2 + H2O + Chaleur
La première réaction dissocie l'acétylène en monoxyde de carbone et en hydrogène tout en produisant environ 33 % de la chaleur totale générée. Le deuxième processus ci-dessus représente une combustion supplémentaire de l'hydrogène et du monoxyde de carbone tout en produisant environ 67 % de la chaleur totale. Les températures dans la flamme sont comprises entre 1533 et 3573 Kelvin. Le pourcentage d'oxygène dans le mélange gazeux est important. Si la teneur en oxygène est supérieure à la moitié, la flamme devient un agent oxydant. Ceci est indésirable pour certains métaux mais souhaitable pour d'autres. Un exemple où la flamme oxydante est souhaitable est les alliages à base de cuivre car elle forme une couche de passivation sur le métal. D'autre part, lorsque la teneur en oxygène est réduite, la combustion complète n'est pas possible et la flamme devient une flamme réductrice (carburation). Les températures dans une flamme réductrice sont plus basses et conviennent donc à des processus tels que le brasage et le brasage. D'autres gaz sont également des carburants potentiels, mais ils présentent certains inconvénients par rapport à l'acétylène. Occasionnellement, nous fournissons des métaux d'apport à la zone de soudure sous forme de baguettes ou de fils d'apport. Certains d'entre eux sont recouverts d'un flux pour retarder l'oxydation des surfaces et protéger ainsi le métal en fusion. Un avantage supplémentaire que le flux nous donne est l'élimination des oxydes et autres substances de la zone de soudure. Cela conduit à une liaison plus forte. Une variante du soudage au gaz oxygaz est le SOUDAGE AU GAZ SOUS PRESSION, où les deux composants sont chauffés à leur interface à l'aide d'une torche à gaz oxyacétylène et une fois que l'interface commence à fondre, la torche est retirée et une force axiale est appliquée pour presser les deux pièces ensemble. jusqu'à ce que l'interface soit solidifiée.
SOUDAGE À L'ARC : Nous utilisons l'énergie électrique pour produire un arc entre la pointe de l'électrode et les pièces à souder. L'alimentation peut être CA ou CC tandis que les électrodes sont consommables ou non consommables. Le transfert de chaleur dans le soudage à l'arc peut être exprimé par l'équation suivante :
H / l = ex VI / v
Ici, H est l'apport de chaleur, l est la longueur de soudure, V et I sont la tension et le courant appliqués, v est la vitesse de soudage et e est l'efficacité du processus. Plus le rendement "e" est élevé, plus l'énergie disponible est utilisée de manière bénéfique pour faire fondre le matériau. L'apport de chaleur peut également être exprimé par :
H = ux (Volume) = ux A xl
Ici u est l'énergie spécifique de fusion, A la section de la soudure et l la longueur de la soudure. A partir des deux équations ci-dessus, nous pouvons obtenir :
v = ex VI / u A
Une variante du soudage à l'arc est le SHIELDED METAL ARC WELDING (SMAW) qui constitue environ 50% de tous les procédés de soudage industriels et de maintenance. LE SOUDAGE À L'ARC ÉLECTRIQUE (SOUDAGE À LA BAGUETTE) est effectué en touchant la pointe d'une électrode enrobée sur la pièce à usiner et en la retirant rapidement à une distance suffisante pour maintenir l'arc. Nous appelons également ce processus le soudage à la baguette car les électrodes sont des baguettes fines et longues. Pendant le processus de soudage, la pointe de l'électrode fond avec son revêtement et le métal de base à proximité de l'arc. Un mélange de métal de base, de métal d'électrode et de substances provenant du revêtement d'électrode se solidifie dans la zone de soudure. Le revêtement de l'électrode se désoxyde et fournit un gaz de protection dans la zone de soudure, la protégeant ainsi de l'oxygène de l'environnement. Par conséquent, le processus est appelé soudage à l'arc sous protection. Nous utilisons des courants entre 50 et 300 ampères et des niveaux de puissance généralement inférieurs à 10 kW pour des performances de soudage optimales. La polarité du courant continu (sens de circulation du courant) est également importante. La polarité droite où la pièce est positive et l'électrode est négative est préférée dans le soudage des tôles en raison de sa pénétration peu profonde et également pour les joints avec des espaces très larges. Lorsque nous avons une polarité inversée, c'est-à-dire que l'électrode est positive et la pièce négative, nous pouvons obtenir des pénétrations de soudure plus profondes. Avec le courant alternatif, puisque nous avons des arcs pulsés, nous pouvons souder des sections épaisses en utilisant des électrodes de grand diamètre et des courants maximum. Le procédé de soudage SMAW est adapté pour des épaisseurs de pièces de 3 à 19 mm et même plus en utilisant des techniques multipasses. Le laitier formé sur le dessus de la soudure doit être enlevé à l'aide d'une brosse métallique, de sorte qu'il n'y ait pas de corrosion et de défaillance au niveau de la soudure. Cela augmente bien sûr le coût du soudage à l'arc sous protection. Néanmoins, le SMAW est la technique de soudage la plus populaire dans l'industrie et les travaux de réparation.
SOUDAGE À L'ARC SUBMERGÉ (SAW): Dans ce processus, nous protégeons l'arc de soudage en utilisant des matériaux de flux granulaires comme la chaux, la silice, le fluorure de calcium, l'oxyde de manganèse… etc. Le flux granulaire est introduit dans la zone de soudure par écoulement gravitaire à travers une buse. Le flux recouvrant la zone de soudure fondue protège de manière significative des étincelles, des fumées, des rayons UV… etc. et agit comme un isolant thermique, laissant ainsi la chaleur pénétrer profondément dans la pièce. Le flux non fondu est récupéré, traité et réutilisé. Une bobine de nu est utilisée comme électrode et alimentée à travers un tube jusqu'à la zone de soudure. Nous utilisons des courants entre 300 et 2000 Ampères. Le processus de soudage à l'arc submergé (SAW) est limité aux positions horizontales et plates et aux soudures circulaires si la rotation de la structure circulaire (telle que les tuyaux) est possible pendant le soudage. Les vitesses peuvent atteindre 5 m/min. Le procédé SAW convient aux tôles épaisses et permet d'obtenir des soudures de haute qualité, résistantes, ductiles et uniformes. La productivité, c'est-à-dire la quantité de matériau de soudure déposée par heure, est de 4 à 10 fois supérieure à celle du procédé SMAW.
Un autre procédé de soudage à l'arc, à savoir le GAS METAL ARC WELDING (GMAW) ou alternativement appelé METAL INERT GAS WELDING (MIG) est basé sur le fait que la zone de soudure est protégée par des sources externes de gaz comme l'hélium, l'argon, le dioxyde de carbone… .etc. Il peut y avoir des désoxydants supplémentaires présents dans le métal d'électrode. Le fil consommable est introduit à travers une buse dans la zone de soudure. La fabrication impliquant des métaux aussi bien ferreux que non ferreux est réalisée par soudage à l'arc sous gaz et métal (GMAW). La productivité du soudage est environ 2 fois supérieure à celle du procédé SMAW. Un équipement de soudage automatisé est utilisé. Le métal est transféré de l'une des trois manières suivantes dans ce processus : Le « transfert par pulvérisation » implique le transfert de plusieurs centaines de petites gouttelettes de métal par seconde de l'électrode à la zone de soudure. Dans le « transfert globulaire », en revanche, des gaz riches en dioxyde de carbone sont utilisés et des globules de métal en fusion sont propulsés par l'arc électrique. Les courants de soudage sont élevés et la pénétration de la soudure plus profonde, la vitesse de soudage est supérieure à celle du transfert par pulvérisation. Ainsi le transfert globulaire est meilleur pour souder des sections plus lourdes. Enfin, dans la méthode de "court-circuit", la pointe de l'électrode touche le bain de soudure fondu, le court-circuitant lorsque le métal à des taux supérieurs à 50 gouttelettes/seconde est transféré en gouttelettes individuelles. Des courants et des tensions faibles sont utilisés avec des fils plus fins. Les puissances utilisées sont de l'ordre de 2 kW et les températures relativement basses, ce qui rend cette méthode adaptée aux tôles minces de moins de 6 mm d'épaisseur.
Une autre variante du procédé de SOUDAGE À L'ARC À FLUX FOURRÉ (FCAW) est similaire au soudage à l'arc sous gaz, sauf que l'électrode est un tube rempli de flux. Les avantages de l'utilisation d'électrodes à flux fourré sont qu'elles produisent des arcs plus stables, nous donnent la possibilité d'améliorer les propriétés des métaux soudés, la nature moins fragile et flexible de son flux par rapport au soudage SMAW, des contours de soudage améliorés. Les électrodes fourrées auto-protégées contiennent des matériaux qui protègent la zone de soudure contre l'atmosphère. Nous utilisons environ 20 kW de puissance. Comme le procédé GMAW, le procédé FCAW offre également la possibilité d'automatiser les procédés de soudage en continu, et il est économique. Différentes chimies de métal fondu peuvent être développées en ajoutant divers alliages au noyau de flux.
En SOUDAGE ELECTROGAZ (EGW), nous soudons les pièces placées bord à bord. Il est parfois aussi appelé SOUDAGE BOUT À BOUT. Le métal fondu est placé dans une cavité de soudure entre deux pièces à assembler. L'espace est entouré de deux barrages refroidis à l'eau pour empêcher le laitier fondu de se déverser. Les barrages sont déplacés par des entraînements mécaniques. Lorsque la pièce peut être tournée, nous pouvons également utiliser la technique de soudage électrogaz pour le soudage circonférentiel des tuyaux. Les électrodes sont alimentées à travers un conduit pour maintenir un arc continu. Les courants peuvent être d'environ 400 ampères ou 750 ampères et les niveaux de puissance d'environ 20 kW. Les gaz inertes provenant d'une électrode à noyau de flux ou d'une source externe fournissent un blindage. Nous utilisons le soudage électrogaz (EGW) pour les métaux tels que les aciers, le titane….etc avec des épaisseurs de 12mm à 75mm. La technique est adaptée aux grandes structures.
Pourtant, dans une autre technique appelée ELECTROSLAG WELDING (ESW), l'arc est allumé entre l'électrode et le fond de la pièce et le flux est ajouté. Lorsque le laitier fondu atteint la pointe de l'électrode, l'arc s'éteint. L'énergie est fournie en continu par la résistance électrique du laitier en fusion. Nous pouvons souder des plaques d'épaisseurs comprises entre 50 mm et 900 mm et même plus. Les courants sont d'environ 600 ampères tandis que les tensions sont comprises entre 40 et 50 V. Les vitesses de soudage sont d'environ 12 à 36 mm/min. Les applications sont similaires au soudage électrogaz.
L'un de nos procédés d'électrodes non consommables, le GAS TUNGSTEN ARC WELDING (GTAW) également connu sous le nom de TUNGSTEN INERT GAS WELDING (TIG) implique l'apport d'un métal d'apport par un fil. Pour les joints bien ajustés, nous n'utilisons parfois pas le métal d'apport. Dans le procédé TIG, nous n'utilisons pas de flux, mais utilisons de l'argon et de l'hélium pour le blindage. Le tungstène a un point de fusion élevé et n'est pas consommé dans le processus de soudage TIG, donc un courant constant ainsi que des écarts d'arc peuvent être maintenus. Les niveaux de puissance sont compris entre 8 et 20 kW et les courants à 200 ampères (DC) ou 500 ampères (AC). Pour l'aluminium et le magnésium, nous utilisons le courant alternatif pour sa fonction de nettoyage des oxydes. Pour éviter la contamination de l'électrode de tungstène, nous évitons son contact avec des métaux en fusion. Le soudage à l'arc au gaz tungstène (GTAW) est particulièrement utile pour le soudage de métaux minces. Les soudures GTAW sont de très haute qualité avec un bon état de surface.
En raison du coût plus élevé de l'hydrogène gazeux, une technique moins fréquemment utilisée est le SOUDAGE À L'HYDROGÈNE ATOMIQUE (AHW), où nous générons un arc entre deux électrodes de tungstène dans une atmosphère de protection d'hydrogène gazeux en circulation. L'AHW est également un procédé de soudage à électrode non consommable. L'hydrogène gazeux diatomique H2 se décompose en sa forme atomique près de l'arc de soudage où les températures sont supérieures à 6273 Kelvin. En se décomposant, il absorbe une grande quantité de chaleur de l'arc. Lorsque les atomes d'hydrogène frappent la zone de soudure qui est une surface relativement froide, ils se recombinent sous forme diatomique et libèrent la chaleur emmagasinée. L'énergie peut être modifiée en changeant la distance de la pièce à l'arc.
Dans un autre processus d'électrode non consommable, PLASMA ARC WELDING (PAW), nous avons un arc plasma concentré dirigé vers la zone de soudure. Les températures atteignent 33 273 Kelvin en PAW. Un nombre presque égal d'électrons et d'ions composent le gaz plasmagène. Un arc pilote à faible courant initie le plasma qui se trouve entre l'électrode de tungstène et l'orifice. Les courants de fonctionnement sont généralement autour de 100 Ampères. Un métal d'apport peut être amené. Dans le soudage à l'arc plasma, le blindage est réalisé par un anneau de blindage extérieur et en utilisant des gaz tels que l'argon et l'hélium. Dans le soudage à l'arc plasma, l'arc peut se situer entre l'électrode et la pièce ou entre l'électrode et la buse. Cette technique de soudage présente les avantages par rapport aux autres méthodes d'une concentration d'énergie plus élevée, d'une capacité de soudage plus profonde et plus étroite, d'une meilleure stabilité de l'arc, de vitesses de soudage plus élevées jusqu'à 1 mètre/min, d'une moindre distorsion thermique. On utilise généralement le soudage à l'arc plasma pour des épaisseurs inférieures à 6 mm et parfois jusqu'à 20 mm pour l'aluminium et le titane.
SOUDAGE PAR FAISCEAU À HAUTE ÉNERGIE : Un autre type de procédé de soudage par fusion avec le soudage par faisceau d'électrons (EBW) et le soudage au laser (LBW) en deux variantes. Ces techniques sont particulièrement précieuses pour nos travaux de fabrication de produits de haute technologie. Dans le soudage par faisceau d'électrons, des électrons à grande vitesse frappent la pièce et leur énergie cinétique est convertie en chaleur. Le faisceau étroit d'électrons se déplace facilement dans la chambre à vide. Généralement, nous utilisons un vide poussé dans le soudage par faisceau d'électrons. Des tôles aussi épaisses que 150 mm peuvent être soudées. Aucun gaz de protection, flux ou matériau de remplissage n'est nécessaire. Les canons à faisceau d'électrons ont des capacités de 100 kW. Des soudures profondes et étroites avec des rapports d'aspect élevés jusqu'à 30 et de petites zones affectées par la chaleur sont possibles. Les vitesses de soudage peuvent atteindre 12 m/min. Dans le soudage par faisceau laser, nous utilisons des lasers à haute puissance comme source de chaleur. Des faisceaux laser aussi petits que 10 microns à haute densité permettent une pénétration profonde dans la pièce. Des rapports profondeur/largeur jusqu'à 10 sont possibles avec le soudage par faisceau laser. Nous utilisons à la fois des lasers à impulsions et à ondes continues, les premiers dans les applications pour les matériaux minces et les seconds principalement pour les pièces épaisses jusqu'à environ 25 mm. Les niveaux de puissance vont jusqu'à 100 kW. Le soudage par faisceau laser n'est pas bien adapté aux matériaux optiquement très réfléchissants. Des gaz peuvent également être utilisés dans le processus de soudage. La méthode de soudage par faisceau laser est bien adaptée à l'automatisation et à la fabrication à grand volume et peut offrir des vitesses de soudage comprises entre 2,5 m/min et 80 m/min. L'un des principaux avantages de cette technique de soudage est l'accès à des zones où d'autres techniques ne peuvent pas être utilisées. Les faisceaux laser peuvent facilement se déplacer vers ces régions difficiles. Aucun vide comme dans le soudage par faisceau d'électrons n'est nécessaire. Des soudures de bonne qualité et résistance, un faible retrait, une faible distorsion et une faible porosité peuvent être obtenues avec le soudage par faisceau laser. Les faisceaux laser peuvent être facilement manipulés et façonnés à l'aide de câbles à fibres optiques. La technique est donc bien adaptée au soudage d'assemblages hermétiques de précision, de boîtiers électroniques…etc.
Examinons nos techniques de SOUDAGE À L'ÉTAT SOLIDE. Le SOUDAGE À FROID (CW) est un processus où la pression au lieu de la chaleur est appliquée à l'aide de matrices ou de rouleaux sur les pièces qui sont accouplées. En soudage à froid, au moins une des pièces d'accouplement doit être ductile. Les meilleurs résultats sont obtenus avec deux matériaux similaires. Si les deux métaux à assembler par soudage à froid sont différents, nous pouvons obtenir des joints faibles et cassants. La méthode de soudage à froid est bien adaptée aux pièces souples, ductiles et petites telles que les connexions électriques, les bords de conteneurs sensibles à la chaleur, les bilames pour thermostats… etc. Une variante du soudage à froid est le soudage au rouleau (ou soudage au rouleau), où la pression est appliquée à travers une paire de rouleaux. Parfois, nous effectuons le soudage au rouleau à des températures élevées pour une meilleure résistance interfaciale.
Un autre procédé de soudage à l'état solide que nous utilisons est le SOUDAGE ULTRASONIQUE (USW), où les pièces sont soumises à une force normale statique et à des contraintes de cisaillement oscillantes. Les contraintes de cisaillement oscillantes sont appliquées à travers la pointe d'un transducteur. Le soudage par ultrasons déploie des oscillations avec des fréquences de 10 à 75 kHz. Dans certaines applications telles que le soudage à la molette, nous utilisons un disque de soudage rotatif comme pointe. Les contraintes de cisaillement appliquées aux pièces provoquent de petites déformations plastiques, cassent les couches d'oxyde, les contaminants et conduisent à une liaison à l'état solide. Les températures impliquées dans le soudage par ultrasons sont bien inférieures aux températures de point de fusion des métaux et aucune fusion n'a lieu. Nous utilisons fréquemment le procédé de soudage par ultrasons (USW) pour les matériaux non métalliques comme les plastiques. Dans les thermoplastiques, les températures atteignent cependant des points de fusion.
Autre technique populaire, dans le SOUDAGE PAR FRICTION (FRW), la chaleur est générée par frottement à l'interface des pièces à assembler. Dans le soudage par friction, nous maintenons l'une des pièces à l'arrêt tandis que l'autre pièce est maintenue dans un montage et tourne à une vitesse constante. Les pièces sont alors mises en contact sous une force axiale. La vitesse de rotation de surface en soudage par friction peut atteindre 900 m/min dans certains cas. Après un contact interfacial suffisant, la pièce en rotation est arrêtée brusquement et la force axiale est augmentée. La zone de soudure est généralement une région étroite. La technique de soudage par friction peut être utilisée pour assembler des pièces solides et tubulaires constituées de divers matériaux. Un peu de bavure peut se développer à l'interface dans FRW, mais cette bavure peut être éliminée par un usinage secondaire ou un meulage. Des variantes du procédé de soudage par friction existent. Par exemple, le "soudage par friction à inertie" implique un volant d'inertie dont l'énergie cinétique de rotation est utilisée pour souder les pièces. La soudure est terminée lorsque le volant s'arrête. La masse en rotation peut être variée et donc l'énergie cinétique de rotation. Une autre variante est le "soudage par friction linéaire", où un mouvement alternatif linéaire est imposé à au moins un des composants à assembler. Dans le soudage par friction linéaire, les pièces ne doivent pas nécessairement être circulaires, elles peuvent être rectangulaires, carrées ou d'une autre forme. Les fréquences peuvent être de l'ordre de dizaines de Hz, les amplitudes de l'ordre du millimètre et les pressions de l'ordre de dizaines ou de centaines de MPa. Enfin, le "soudage par friction-malaxage" est quelque peu différent des deux autres expliqués ci-dessus. Alors que dans le soudage par friction à inertie et le soudage par friction linéaire, le chauffage des interfaces est obtenu par frottement en frottant deux surfaces en contact, dans le procédé de soudage par friction-malaxage, un troisième corps est frotté contre les deux surfaces à assembler. Un outil rotatif de 5 à 6 mm de diamètre est mis en contact avec le joint. Les températures peuvent atteindre des valeurs comprises entre 503 et 533 Kelvin. Le chauffage, le mélange et l'agitation du matériau dans le joint ont lieu. Nous utilisons le soudage par friction-malaxage sur une variété de matériaux, y compris l'aluminium, les plastiques et les composites. Les soudures sont uniformes et la qualité est élevée avec un minimum de pores. Aucune fumée ou éclaboussure n'est produite lors du soudage par friction-malaxage et le processus est bien automatisé.
SOUDAGE PAR RESISTANCE (RW) : La chaleur nécessaire au soudage est produite par la résistance électrique entre les deux pièces à assembler. Aucun flux, gaz de protection ou électrode consommable n'est utilisé dans le soudage par résistance. L'échauffement Joule a lieu dans le soudage par résistance et peut être exprimé comme suit :
H = (Carré I) x R xtx K
H est la chaleur générée en joules (watt-secondes), I courant en ampères, R résistance en ohms, t est le temps en secondes que le courant traverse. Le facteur K est inférieur à 1 et représente la fraction d'énergie qui n'est pas perdue par rayonnement et conduction. Les courants dans les procédés de soudage par résistance peuvent atteindre des niveaux aussi élevés que 100 000 A, mais les tensions sont généralement de 0,5 à 10 volts. Les électrodes sont généralement constituées d'alliages de cuivre. Des matériaux similaires et différents peuvent être assemblés par soudage par résistance. Plusieurs variantes existent pour ce procédé : Le « soudage par points par résistance » implique deux électrodes rondes opposées en contact avec les surfaces du joint à recouvrement des deux tôles. La pression est appliquée jusqu'à ce que le courant soit coupé. Le noyau de soudure mesure généralement jusqu'à 10 mm de diamètre. Le soudage par points par résistance laisse des marques d'indentation légèrement décolorées aux points de soudure. Le soudage par points est notre technique de soudage par résistance la plus populaire. Diverses formes d'électrodes sont utilisées dans le soudage par points afin d'atteindre les zones difficiles. Notre équipement de soudage par points est contrôlé par CNC et possède plusieurs électrodes pouvant être utilisées simultanément. Une autre variante, le "soudage à la molette par résistance", est réalisée avec des électrodes à roue ou à rouleau qui produisent des points de soudure continus chaque fois que le courant atteint un niveau suffisamment élevé dans le cycle de courant alternatif. Les joints produits par soudage à la molette par résistance sont étanches aux liquides et aux gaz. Des vitesses de soudage d'environ 1,5 m/min sont normales pour les tôles minces. On peut appliquer des courants intermittents de sorte que des soudures par points soient produites à des intervalles souhaités le long du joint. Dans le «soudage par projection par résistance», nous estampons une ou plusieurs saillies (empreintes) sur l'une des surfaces de la pièce à souder. Ces saillies peuvent être rondes ou ovales. Des températures localisées élevées sont atteintes au niveau de ces points en relief qui entrent en contact avec la pièce d'accouplement. Des électrodes exercent une pression pour comprimer ces saillies. Les électrodes de soudage par projection par résistance ont des pointes plates et sont des alliages de cuivre refroidis à l'eau. L'avantage du soudage par projection par résistance est notre capacité à effectuer un certain nombre de soudures en un seul coup, d'où la durée de vie prolongée de l'électrode, la capacité de souder des tôles de différentes épaisseurs, la capacité de souder des écrous et des boulons sur des tôles. L'inconvénient du soudage par projection par résistance est le coût supplémentaire du gaufrage des alvéoles. Encore une autre technique, dans le "soudage par étincelage", la chaleur est générée à partir de l'arc aux extrémités des deux pièces lorsqu'elles commencent à entrer en contact. Cette méthode peut également être considérée comme un soudage à l'arc. La température à l'interface augmente et le matériau se ramollit. Une force axiale est appliquée et une soudure est formée au niveau de la région ramollie. Une fois le soudage par étincelage terminé, le joint peut être usiné pour améliorer son apparence. La qualité de la soudure obtenue par étincelage est bonne. Les niveaux de puissance sont de 10 à 1500 kW. Le soudage par étincelage convient à l'assemblage bord à bord de métaux similaires ou différents jusqu'à 75 mm de diamètre et de tôles d'une épaisseur comprise entre 0,2 mm et 25 mm. Le "soudage à l'arc des goujons" est très similaire au soudage par étincelage. Le goujon tel qu'un boulon ou une tige filetée sert d'électrode lorsqu'il est joint à une pièce telle qu'une plaque. Pour concentrer la chaleur générée, empêcher l'oxydation et retenir le métal en fusion dans la zone de soudure, un anneau en céramique jetable est placé autour du joint. Enfin, le "soudage par percussion", un autre procédé de soudage par résistance, utilise un condensateur pour fournir l'énergie électrique. Dans le soudage par percussion, la puissance est déchargée en quelques millisecondes, développant très rapidement une chaleur localisée élevée au niveau du joint. Nous utilisons largement le soudage par percussion dans l'industrie de la fabrication électronique où le chauffage des composants électroniques sensibles à proximité du joint doit être évité.
Une technique appelée SOUDAGE PAR EXPLOSION implique la détonation d'une couche d'explosif qui est placée sur l'une des pièces à assembler. La pression très élevée exercée sur la pièce produit une interface turbulente et ondulée et un emboîtement mécanique se produit. Les forces de liaison en soudage explosif sont très élevées. Le soudage par explosion est une bonne méthode pour le revêtement de plaques avec des métaux différents. Après placage, les plaques peuvent être laminées en sections plus minces. Parfois, nous utilisons le soudage par explosion pour dilater les tubes afin qu'ils soient bien scellés contre la plaque.
Notre dernière méthode dans le domaine de l'assemblage à l'état solide est le DIFFUSION BONDING ou DIFFUSION WELDING (DFW) dans lequel un bon joint est obtenu principalement par diffusion d'atomes à travers l'interface. Certaines déformations plastiques à l'interface contribuent également au soudage. Les températures mises en jeu sont de l'ordre de 0,5 Tm où Tm est la température de fusion du métal. La force de liaison dans le soudage par diffusion dépend de la pression, de la température, du temps de contact et de la propreté des surfaces de contact. Parfois, nous utilisons des métaux d'apport à l'interface. La chaleur et la pression sont nécessaires dans le collage par diffusion et sont fournies par une résistance électrique ou un four et des poids morts, une presse ou autre. Des métaux similaires et différents peuvent être assemblés par soudage par diffusion. Le processus est relativement lent en raison du temps nécessaire aux atomes pour migrer. DFW peut être automatisé et est largement utilisé dans la fabrication de pièces complexes pour les industries aérospatiale, électronique et médicale. Les produits fabriqués comprennent des implants orthopédiques, des capteurs, des éléments structurels aérospatiaux. Le collage par diffusion peut être combiné avec SUPERPLASTIC FORMING pour fabriquer des structures complexes en tôle. Des emplacements sélectionnés sur les feuilles sont d'abord liés par diffusion, puis les régions non liées sont expansées dans un moule à l'aide d'une pression d'air. Les structures aérospatiales avec des rapports rigidité/poids élevés sont fabriquées en utilisant cette combinaison de méthodes. Le processus combiné de soudage par diffusion / formage superplastique réduit le nombre de pièces nécessaires en éliminant le besoin de fixations, se traduit par des pièces à faible contrainte très précises de manière économique et avec des délais de livraison courts.
BRASAGE : Les techniques de brasage et de brasage impliquent des températures plus basses que celles requises pour le soudage. Cependant, les températures de brasage sont plus élevées que les températures de brasage. Lors du brasage, un métal d'apport est placé entre les surfaces à assembler et les températures sont portées à la température de fusion du matériau d'apport au-dessus de 723 Kelvin mais en dessous des températures de fusion des pièces. Le métal en fusion remplit l'espace étroitement ajusté entre les pièces. Le refroidissement et la solidification subséquente du métal d'apport donnent des joints solides. Dans le brasage, le métal d'apport est déposé au niveau du joint. Beaucoup plus de métal d'apport est utilisé dans le soudo-brasage que dans le brasage. La torche oxyacétylénique à flamme oxydante est utilisée pour déposer le métal d'apport en brasage. En raison des températures plus basses lors du brasage, les problèmes au niveau des zones affectées par la chaleur, tels que le gauchissement et les contraintes résiduelles, sont moindres. Plus l'écart de dégagement dans le brasage est petit, plus la résistance au cisaillement du joint est élevée. La résistance à la traction maximale est cependant atteinte à un écart optimal (une valeur maximale). Au-dessous et au-dessus de cette valeur optimale, la résistance à la traction dans le brasage diminue. Les jeux typiques de brasage peuvent être compris entre 0,025 et 0,2 mm. Nous utilisons une variété de matériaux de brasage avec différentes formes telles que des préformes, de la poudre, des anneaux, du fil, des bandes…..etc. et peut fabriquer ces préformes spécialement pour votre conception ou la géométrie de votre produit. Nous déterminons également le contenu des matériaux de brasage en fonction de vos matériaux de base et de votre application. Nous utilisons fréquemment des flux dans les opérations de brasage pour éliminer les couches d'oxyde indésirables et empêcher l'oxydation. Pour éviter une corrosion ultérieure, les flux sont généralement éliminés après l'opération d'assemblage. AGS-TECH Inc. utilise diverses méthodes de brasage, notamment :
- Brasage au chalumeau
- Brasage au four
- Brasage par induction
- Brasage par résistance
- Brasage par trempage
- Brasage infrarouge
- Brasage par diffusion
- Faisceau à haute énergie
Nos exemples les plus courants de joints brasés sont constitués de métaux dissemblables ayant une bonne résistance, tels que des forets en carbure, des inserts, des boîtiers hermétiques optoélectroniques, des joints.
SOUDURE : C'est l'une de nos techniques les plus fréquemment utilisées où la soudure (métal d'apport) remplit le joint comme dans le brasage entre des composants étroitement ajustés. Nos soudures ont des points de fusion inférieurs à 723 Kelvin. Nous déployons à la fois le soudage manuel et automatisé dans les opérations de fabrication. Par rapport au brasage, les températures de brasage sont plus basses. La soudure n'est pas très adaptée aux applications à haute température ou à haute résistance. Nous utilisons des soudures sans plomb ainsi que des alliages étain-plomb, étain-zinc, plomb-argent, cadmium-argent, zinc-aluminium et autres pour le brasage. Les acides et sels non corrosifs à base de résine ainsi que les acides et sels inorganiques sont utilisés comme fondant dans le brasage. Nous utilisons des flux spéciaux pour souder les métaux à faible soudabilité. Dans les applications où nous devons souder des matériaux céramiques, du verre ou du graphite, nous plaquons d'abord les pièces avec un métal approprié pour une meilleure soudabilité. Nos techniques de soudure populaires sont :
-Refusion ou pâte à souder
-Soudure à la vague
-Four à souder
-Soudage au chalumeau
-Soudage par induction
- Fer à souder
-Soudage par résistance
-Soudage au trempé
-Soudage par ultrasons
-Soudage infrarouge
Le soudage par ultrasons nous offre un avantage unique en ce sens que le besoin de flux est éliminé en raison de l'effet de cavitation ultrasonique qui élimine les films d'oxyde des surfaces à assembler. La soudure par refusion et à la vague sont nos techniques exceptionnelles sur le plan industriel pour la fabrication de gros volumes dans l'électronique et méritent donc d'être expliquées plus en détail. Dans le brasage par refusion, nous utilisons des pâtes semi-solides contenant des particules de métal de soudure. La pâte est placée sur le joint à l'aide d'un processus de criblage ou de pochoir. Dans les cartes de circuits imprimés (PCB), nous utilisons fréquemment cette technique. Lorsque des composants électriques sont placés sur ces pastilles à partir de pâte, la tension superficielle maintient les boîtiers de montage en surface alignés. Après avoir placé les composants, nous chauffons l'ensemble dans un four afin que la soudure par refusion ait lieu. Au cours de ce processus, les solvants de la pâte s'évaporent, le flux dans la pâte est activé, les composants sont préchauffés, les particules de soudure sont fondues et mouillent le joint, et enfin l'assemblage PCB est refroidi lentement. Notre deuxième technique populaire pour la production à grand volume de cartes de circuits imprimés, à savoir le soudage à la vague, repose sur le fait que les soudures fondues mouillent les surfaces métalliques et forment de bonnes liaisons uniquement lorsque le métal est préchauffé. Une onde laminaire stationnaire de soudure fondue est d'abord générée par une pompe et les PCB préchauffés et préfluxés sont transportés sur l'onde. La soudure ne mouille que les surfaces métalliques exposées mais ne mouille pas les boîtiers polymères IC ni les cartes de circuits revêtues de polymère. Un jet d'eau chaude à grande vitesse souffle l'excès de soudure du joint et empêche le pontage entre les fils adjacents. Lors du soudage à la vague de boîtiers à montage en surface, nous les collons d'abord de manière adhésive à la carte de circuit imprimé avant de les souder. Encore une fois, le criblage et le pochoir sont utilisés, mais cette fois pour l'époxy. Une fois les composants placés à leur emplacement correct, l'époxy est durci, les cartes sont inversées et le soudage à la vague a lieu.