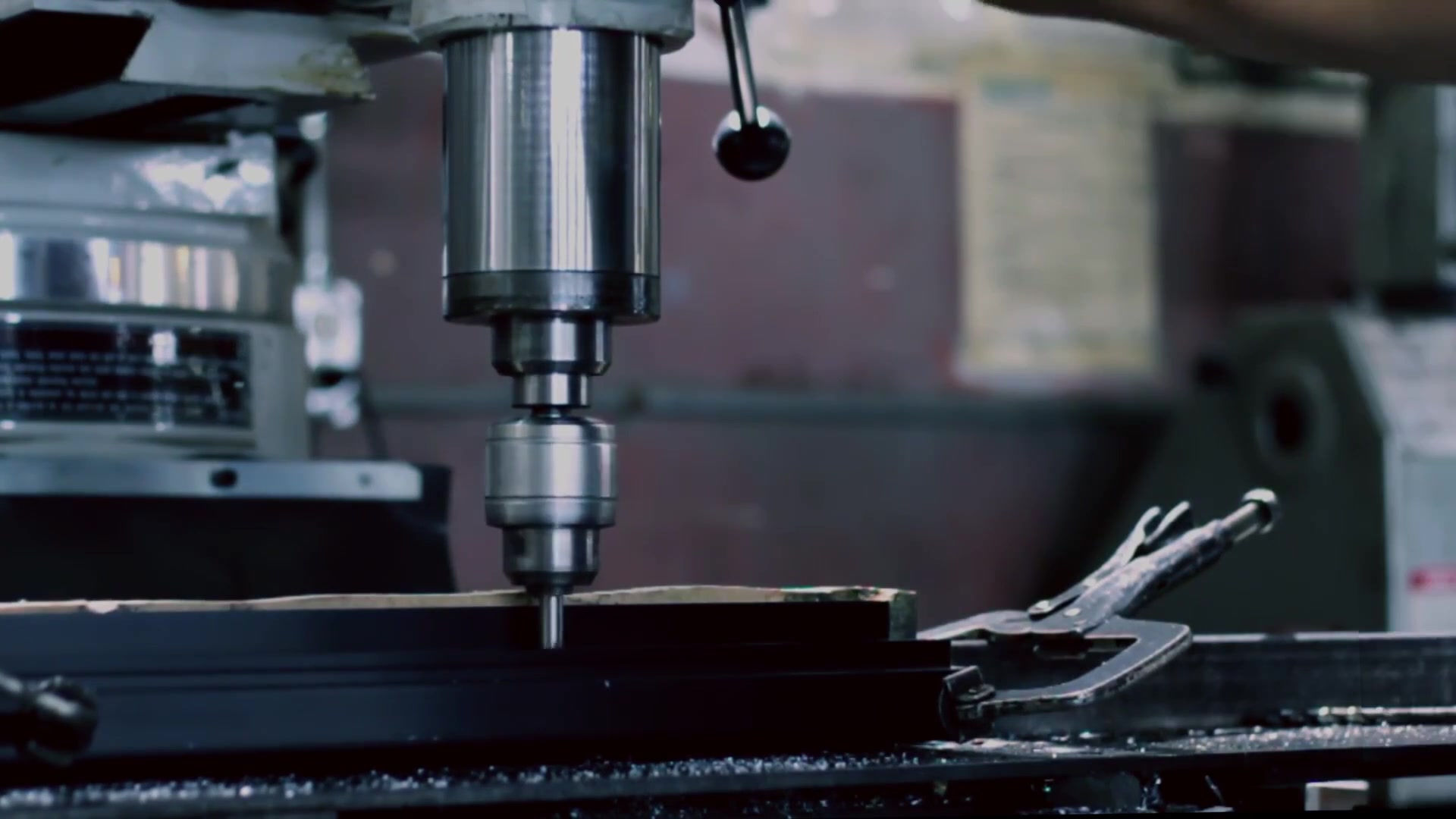
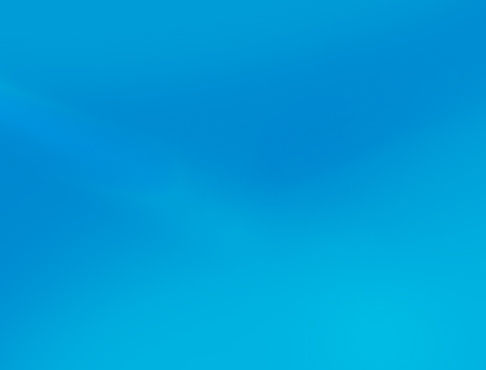
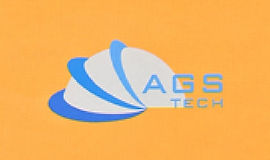
Fabricant mondial sur mesure, intégrateur, consolidateur, partenaire d'externalisation pour une grande variété de produits et services.
Nous sommes votre source unique pour la fabrication, la fabrication, l'ingénierie, la consolidation, l'intégration, l'externalisation de produits et services fabriqués sur mesure et prêts à l'emploi.
Choisissez votre langue
-
Fabrication sur mesure
-
Fabrication sous contrat nationale et mondiale
-
Sous-traitance de fabrication
-
Approvisionnement national et mondial
-
Consolidation
-
Intégration d'ingénierie
-
Services d'ingénierie
Les types de fabrication de verre que nous proposons sont le verre de récipient, le soufflage de verre, la fibre de verre, les tubes et les tiges, la verrerie domestique et industrielle, les lampes et les ampoules, le moulage de précision du verre, les composants et assemblages optiques, le verre plat, le verre plat et le verre flotté. Nous effectuons à la fois le formage à la main et le formage à la machine.
Nos procédés de fabrication de céramiques techniques populaires sont le pressage, le pressage isostatique, le pressage isostatique à chaud, le pressage à chaud, le coulage en barbotine, le coulage en bande, l'extrusion, le moulage par injection, l'usinage vert, le frittage ou la cuisson, le meulage au diamant, les assemblages hermétiques.
Nous vous recommandons de cliquer ici pour
TÉLÉCHARGEZ nos illustrations schématiques des processus de formage et de façonnage du verre par AGS-TECH Inc.
Ces fichiers téléchargeables avec photos et croquis vous aideront à mieux comprendre les informations que nous vous fournissons ci-dessous.
• FABRICATION DE VERRE D'EMBALLAGE : Nous disposons de lignes automatisées PRESS AND BLOW ainsi que BLOW AND BLOW pour la fabrication. Dans le processus de soufflage et de soufflage, nous déposons une paraison dans un moule vierge et formons le col en appliquant un coup d'air comprimé par le haut. Immédiatement après cela, de l'air comprimé est soufflé une seconde fois depuis l'autre direction à travers le goulot du récipient pour former la préforme de la bouteille. Cette préforme est ensuite transférée dans le moule réel, réchauffée pour ramollir et de l'air comprimé est appliqué pour donner à la préforme sa forme finale de récipient. Plus explicitement, il est pressurisé et poussé contre les parois de la cavité du moule de soufflage pour prendre sa forme souhaitée. Enfin, le récipient en verre fabriqué est transféré dans un four de recuit pour un réchauffage ultérieur et l'élimination des contraintes produites lors du moulage et est refroidi de manière contrôlée. Dans la méthode de pressage et de soufflage, les paraisons fondues sont placées dans un moule à paraison (moule vierge) et pressées en forme de paraison (forme vierge). Les ébauches sont ensuite transférées dans des moules de soufflage et soufflées de la même manière que le processus décrit ci-dessus sous «Processus de soufflage et de soufflage». Les étapes suivantes comme le recuit et le soulagement des contraintes sont similaires ou identiques.
• SOUFFLAGE DU VERRE : Nous fabriquons des produits en verre en utilisant le soufflage à la main conventionnel ainsi qu'en utilisant de l'air comprimé avec des équipements automatisés. Pour certaines commandes, un soufflage conventionnel est nécessaire, comme les projets impliquant des œuvres d'art en verre, ou des projets qui nécessitent un plus petit nombre de pièces avec des tolérances lâches, des projets de prototypage / démo… etc. Le soufflage de verre conventionnel implique le trempage d'un tuyau métallique creux dans un pot de verre fondu et la rotation du tuyau pour recueillir une certaine quantité de matériau de verre. Le verre recueilli sur le bout de la pipe est roulé sur du fer plat, façonné à volonté, allongé, réchauffé et soufflé à l'air. Lorsqu'il est prêt, il est inséré dans un moule et de l'air est soufflé. La cavité du moule est humide pour éviter le contact du verre avec le métal. Le film d'eau agit comme un coussin entre eux. Le soufflage manuel est un processus lent à forte intensité de main-d'œuvre et ne convient qu'au prototypage ou aux articles de grande valeur, ne convient pas aux commandes bon marché à volume élevé par pièce.
• FABRICATION DE VERRERIE DOMESTIQUE ET INDUSTRIELLE : En utilisant différents types de matériaux en verre, une grande variété de verrerie est produite. Certains verres sont résistants à la chaleur et conviennent à la verrerie de laboratoire, tandis que d'autres sont suffisamment bons pour résister plusieurs fois au lave-vaisselle et conviennent à la fabrication de produits domestiques. À l'aide des machines Westlake, des dizaines de milliers de verres à boire sont produits chaque jour. Pour simplifier, le verre en fusion est collecté sous vide et inséré dans des moules pour fabriquer les préformes. Ensuite, de l'air est insufflé dans les moules, ceux-ci sont transférés dans un autre moule et de l'air est soufflé à nouveau et le verre prend sa forme définitive. Comme pour le soufflage à la main, ces moules sont maintenus humides avec de l'eau. Un étirement supplémentaire fait partie de l'opération de finition où le col est formé. L'excédent de verre est brûlé. Ensuite, le processus de réchauffage et de refroidissement contrôlés décrit ci-dessus suit.
• FORMAGE DE TUBE & BARRE DE VERRE : Les principaux procédés que nous utilisons pour la fabrication des tubes de verre sont les procédés DANNER et VELLO. Dans le procédé Danner, le verre d'un four s'écoule et tombe sur un manchon incliné en matériaux réfractaires. Le manchon est porté sur un arbre creux rotatif ou chalumeau. Le verre est ensuite enroulé autour du manchon et forme une couche lisse coulant le long du manchon et sur la pointe de la tige. Dans le cas de la formation de tubes, l'air est soufflé à travers un chalumeau à pointe creuse, et dans le cas de la formation de tiges, nous utilisons des pointes pleines sur l'arbre. Les tubes ou tiges sont ensuite tirés sur des rouleaux porteurs. Les dimensions telles que l'épaisseur de paroi et le diamètre des tubes de verre sont ajustées aux valeurs souhaitées en réglant le diamètre du manchon et en soufflant la pression d'air à une valeur souhaitée, en ajustant la température, le débit de verre et la vitesse d'étirage. Le processus de fabrication du tube de verre Vello, quant à lui, implique du verre qui sort d'un four et dans un bol avec un mandrin creux ou une cloche. Le verre traverse alors l'espace d'air entre le mandrin et le bol et prend la forme d'un tube. Ensuite, il se déplace sur des rouleaux jusqu'à une machine d'étirage et est refroidi. À la fin de la ligne de refroidissement, la coupe et le traitement final ont lieu. Les dimensions du tube peuvent être ajustées comme dans le procédé Danner. En comparant le processus Danner à Vello, nous pouvons dire que le processus Vello convient mieux à la production en grande quantité, tandis que le processus Danner peut être mieux adapté aux commandes précises de tubes de plus petit volume.
• TRAITEMENT DES FEUILLES & VERRE PLAT & FLOAT : Nous disposons de grandes quantités de verre plat dans des épaisseurs allant du submillimétrique à plusieurs centimètres. Nos verres plats sont d'une perfection presque optique. Nous proposons du verre avec des revêtements spéciaux tels que les revêtements optiques, où la technique de dépôt chimique en phase vapeur est utilisée pour mettre des revêtements tels que l'antireflet ou le revêtement miroir. Les revêtements conducteurs transparents sont également courants. Sont également disponibles des revêtements hydrophobes ou hydrophiles sur le verre et des revêtements qui rendent le verre autonettoyant. Les verres trempés, pare-balles et feuilletés sont d'autres articles populaires. Nous coupons le verre dans la forme souhaitée avec les tolérances souhaitées. D'autres opérations secondaires comme le cintrage ou le cintrage du verre plat sont possibles.
• MOULAGE DE PRÉCISION DU VERRE : Nous utilisons cette technique principalement pour fabriquer des composants optiques de précision sans avoir besoin de techniques plus coûteuses et chronophages comme le meulage, le rodage et le polissage. Cette technique n'est pas toujours suffisante pour tirer le meilleur parti des meilleures optiques, mais dans certains cas, comme les produits de consommation, les appareils photo numériques, l'optique médicale, elle peut être une bonne option moins coûteuse pour la fabrication à grand volume. Il présente également un avantage par rapport aux autres techniques de formage du verre où des géométries complexes sont requises, comme dans le cas des asphères. Le processus de base implique le chargement de la face inférieure de notre moule avec l'ébauche de verre, l'évacuation de la chambre de traitement pour l'élimination de l'oxygène, la fermeture proche du moule, le chauffage rapide et isotherme de la matrice et du verre avec une lumière infrarouge, une fermeture supplémentaire des moitiés de moule presser le verre ramolli lentement de façon contrôlée jusqu'à l'épaisseur désirée, et enfin refroidissement du verre et remplissage de la chambre avec de l'azote et élimination du produit. Le contrôle précis de la température, la distance de fermeture du moule, la force de fermeture du moule, l'adaptation des coefficients de dilatation du moule et du verre sont essentiels dans ce processus.
• FABRICATION DE COMPOSANTS ET D'ASSEMBLAGES OPTIQUES EN VERRE : outre le moulage de précision du verre, nous utilisons un certain nombre de procédés précieux pour fabriquer des composants et des assemblages optiques de haute qualité pour des applications exigeantes. Le meulage, le rodage et le polissage de verres de qualité optique dans de fines suspensions abrasives spéciales sont un art et une science pour la fabrication de lentilles optiques, de prismes, de plats et plus encore. La planéité de surface, l'ondulation, le lissé et les surfaces optiques sans défaut nécessitent une grande expérience de ces processus. De petits changements dans l'environnement peuvent entraîner des produits hors spécifications et entraîner l'arrêt de la chaîne de fabrication. Il existe des cas où un simple essuyage sur la surface optique avec un chiffon propre peut rendre un produit conforme aux spécifications ou échouer au test. Certains matériaux de verre populaires utilisés sont la silice fondue, le quartz, le BK7. De plus, l'assemblage de tels composants nécessite une expérience de niche spécialisée. Parfois, des colles spéciales sont utilisées. Cependant, une technique appelée mise en contact optique est parfois le meilleur choix et n'implique aucun matériau entre les verres optiques attachés. Il consiste à mettre physiquement en contact des surfaces planes pour les attacher les unes aux autres sans colle. Dans certains cas, des entretoises mécaniques, des tiges ou billes de verre de précision, des pinces ou des composants métalliques usinés sont utilisés pour assembler les composants optiques à certaines distances et avec certaines orientations géométriques les uns par rapport aux autres. Examinons certaines de nos techniques populaires de fabrication d'optiques haut de gamme.
MEULAGE & RODAGE & POLISSAGE : La forme brute du composant optique est obtenue par meulage d'une ébauche de verre. Ensuite, le rodage et le polissage sont effectués en faisant tourner et en frottant les surfaces rugueuses des composants optiques contre des outils avec des formes de surface souhaitées. Des boues contenant de minuscules particules abrasives et du liquide sont versées entre l'optique et les outils de mise en forme. Les tailles de particules abrasives dans de telles suspensions peuvent être choisies en fonction du degré de planéité souhaité. Les écarts des surfaces optiques critiques par rapport aux formes souhaitées sont exprimés en termes de longueurs d'onde de la lumière utilisée. Nos optiques de haute précision ont des tolérances d'un dixième de longueur d'onde (longueur d'onde/10) ou même plus sont possibles. Outre le profil de surface, les surfaces critiques sont numérisées et évaluées pour d'autres caractéristiques et défauts de surface tels que les dimensions, les rayures, les éclats, les piqûres, les taches, etc. Le contrôle strict des conditions environnementales dans l'atelier de fabrication optique et les exigences de métrologie et de test étendues avec des équipements de pointe en font une branche de l'industrie difficile.
• PROCESSUS SECONDAIRES DANS LA FABRICATION DU VERRE : Encore une fois, nous ne sommes limités que par votre imagination lorsqu'il s'agit de processus secondaires et de finition du verre. Nous en énumérons ici quelques-uns :
-Revêtements sur verre (optique, électrique, tribologique, thermique, fonctionnel, mécanique...). Par exemple, nous pouvons modifier les propriétés de surface du verre en le faisant par exemple réfléchir la chaleur afin qu'il garde les intérieurs des bâtiments frais, ou faire en sorte qu'un côté absorbe l'infrarouge à l'aide de la nanotechnologie. Cela permet de garder l'intérieur des bâtiments au chaud, car la couche de verre la plus externe absorbe le rayonnement infrarouge à l'intérieur du bâtiment et le renvoie vers l'intérieur.
-Gravure sur verre
-Étiquetage céramique appliqué (ACL)
-Gravure
-Polissage à la flamme
-Polissage chimique
-La coloration
FABRICATION DE CÉRAMIQUES TECHNIQUES
• DIE PRESSING : Consiste en un compactage uniaxial de poudres granulaires confinées dans une filière
• PRESSAGE A CHAUD : Semblable au pressage à chaud mais avec l'ajout de température pour améliorer la densification. La poudre ou la préforme compactée est placée dans une matrice en graphite et une pression uniaxiale est appliquée tandis que la matrice est maintenue à des températures élevées telles que 2000 C. Les températures peuvent être différentes selon le type de poudre céramique en cours de traitement. Pour les formes et géométries compliquées, d'autres traitements ultérieurs tels que le meulage au diamant peuvent être nécessaires.
• PRESSAGE ISOSTATIQUE : La poudre granulaire ou les compacts pressés sont placés dans des conteneurs hermétiques puis dans un récipient sous pression fermé avec du liquide à l'intérieur. Ensuite, ils sont compactés en augmentant la pression du récipient sous pression. Le liquide à l'intérieur du récipient transmet les forces de pression uniformément sur toute la surface du récipient hermétique. Le matériau est ainsi compacté uniformément et prend la forme de son contenant souple et de son profil et de ses caractéristiques internes.
• PRESSAGE ISOSTATIQUE A CHAUD : Similaire au pressage isostatique, mais en plus de l'atmosphère gazeuse sous pression, nous frittons le compact à haute température. Le pressage isostatique à chaud entraîne une densification supplémentaire et une résistance accrue.
• SLIP CASTING / DRAIN CASTING : Nous remplissons le moule avec une suspension de particules céramiques de taille micrométrique et de liquide porteur. Ce mélange est appelé « barbotine ». Le moule a des pores et donc le liquide du mélange est filtré dans le moule. En conséquence, un moulage est formé sur les surfaces intérieures du moule. Après frittage, les pièces peuvent être sorties du moule.
• MOULAGE DE RUBAN : Nous fabriquons des rubans céramiques en coulant des boues céramiques sur des surfaces planes porteuses en mouvement. Les bouillies contiennent des poudres céramiques mélangées à d'autres produits chimiques à des fins de liaison et de transport. Au fur et à mesure que les solvants s'évaporent, il reste des feuilles de céramique denses et flexibles qui peuvent être coupées ou roulées à volonté.
• FORMAGE PAR EXTRUSION : Comme dans d'autres processus d'extrusion, un mélange mou de poudre céramique avec des liants et d'autres produits chimiques est passé à travers une filière pour acquérir sa forme en coupe transversale et est ensuite coupé aux longueurs désirées. Le processus est effectué avec des mélanges céramiques froids ou chauffés.
• MOULAGE PAR INJECTION BASSE PRESSION : Nous préparons un mélange de poudre céramique avec des liants et des solvants et le chauffons à une température où il peut être facilement pressé et forcé dans la cavité de l'outil. Une fois le cycle de moulage terminé, la pièce est éjectée et le liant chimique est brûlé. En utilisant le moulage par injection, nous pouvons obtenir des pièces complexes à des volumes élevés de manière économique. Des trous qui sont une infime fraction de millimètre sur une paroi de 10 mm d'épaisseur sont possibles, des filetages sont possibles sans autre usinage, des tolérances aussi serrées que +/- 0,5% sont possibles et même inférieures lorsque les pièces sont usinées , des épaisseurs de paroi de l'ordre de 0,5 mm à une longueur de 12,5 mm sont possibles ainsi que des épaisseurs de paroi de 6,5 mm à une longueur de 150 mm.
• USINAGE VERT : Avec les mêmes outils d'usinage des métaux, nous pouvons usiner les céramiques pressées alors qu'elles sont encore tendres comme de la craie. Des tolérances de +/- 1% sont possibles. Pour de meilleures tolérances, nous utilisons une rectification au diamant.
• FRITTAGE ou CUISSON : Le frittage permet une densification complète. Un retrait important se produit sur les pièces compactes vertes, mais ce n'est pas un gros problème puisque nous prenons en compte ces changements dimensionnels lorsque nous concevons la pièce et l'outillage. Les particules de poudre sont liées ensemble et la porosité induite par le processus de compactage est supprimée dans une large mesure.
• BROYAGE AU DIAMANT : Le matériau le plus dur au monde, le « diamant », est utilisé pour broyer des matériaux durs comme la céramique et des pièces de précision sont obtenues. Des tolérances de l'ordre du micromètre et des surfaces très lisses sont atteintes. En raison de son coût, nous n'envisageons cette technique que lorsque nous en avons vraiment besoin.
• LES ENSEMBLES HERMÉTIQUES sont ceux qui ne permettent pratiquement aucun échange de matière, solide, liquide ou gazeux entre les interfaces. Le scellement hermétique est étanche à l'air. Par exemple, les boîtiers électroniques hermétiques sont ceux qui maintiennent le contenu intérieur sensible d'un appareil emballé à l'abri de l'humidité, des contaminants ou des gaz. Rien n'est hermétique à 100%, mais quand on parle d'herméticité on veut dire qu'en termes pratiques, il y a herméticité dans la mesure où le taux de fuite est si faible que les appareils sont sûrs dans des conditions environnementales normales pendant de très longues durées. Nos assemblages hermétiques sont constitués de composants métal, verre et céramique, métal-céramique, céramique-métal-céramique, métal-céramique-métal, métal sur métal, métal-verre, métal-verre-métal, verre-métal-verre, verre- métal et verre sur verre et toutes les autres combinaisons de collage métal-verre-céramique. Nous pouvons par exemple revêtir de métal les composants en céramique afin qu'ils puissent être fortement liés aux autres composants de l'assemblage et avoir une excellente capacité d'étanchéité. Nous avons le savoir-faire pour revêtir les fibres optiques ou les traversées de métal et les souder ou les braser aux boîtiers, afin qu'aucun gaz ne passe ou ne fuie dans les boîtiers. Ils sont donc utilisés pour fabriquer des boîtiers électroniques pour encapsuler des appareils sensibles et les protéger de l'atmosphère extérieure. Outre leurs excellentes caractéristiques d'étanchéité, d'autres propriétés telles que le coefficient de dilatation thermique, la résistance à la déformation, la nature non dégazante, la très longue durée de vie, la nature non conductrice, les propriétés d'isolation thermique, la nature antistatique... etc. faire du verre et des matériaux céramiques le choix pour certaines applications. Des informations sur notre usine de production de raccords céramique-métal, d'étanchéité hermétique, de traversées de vide, de composants de contrôle des fluides et des vides poussés et ultra-poussés peuvent être trouvées ici :Brochure de l'usine de composants hermétiques