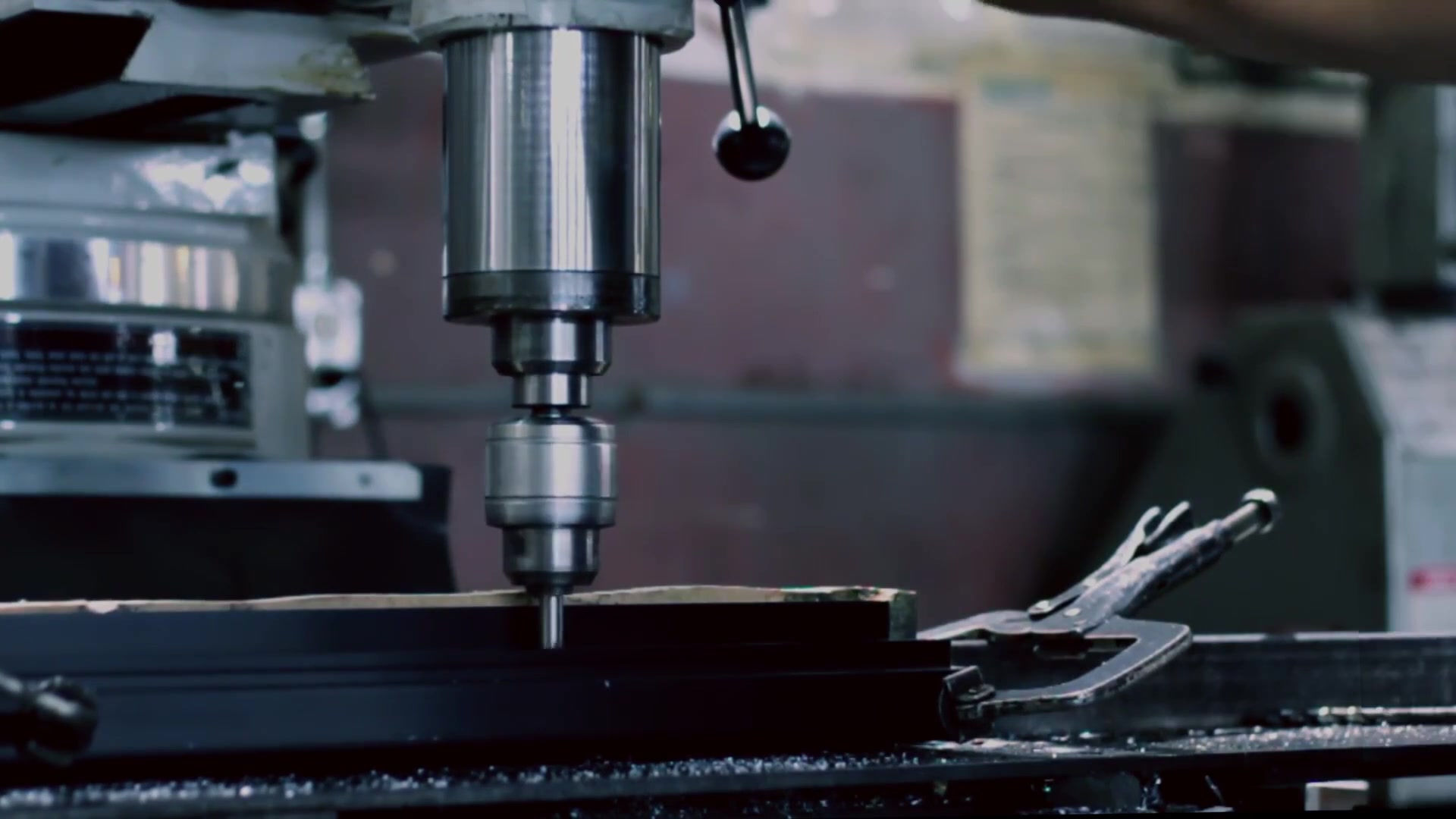
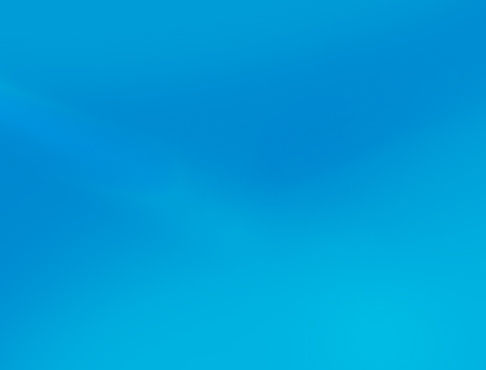
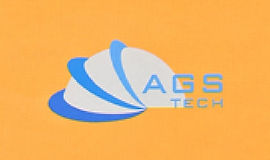
उत्पादों और सेवाओं की एक विस्तृत विविधता के लिए वैश्विक कस्टम निर्माता, इंटीग्रेटर, कंसोलिडेटर, आउटसोर्सिंग पार्टनर।
हम विनिर्माण, निर्माण, इंजीनियरिंग, समेकन, एकीकरण, कस्टम निर्मित और ऑफ-शेल्फ उत्पादों और सेवाओं की आउटसोर्सिंग के लिए आपके वन-स्टॉप स्रोत हैं।
Choose your Language
-
कस्टम विनिर्माण
-
घरेलू और वैश्विक अनुबंध निर्माण
-
विनिर्माण आउटसोर्सिंग
-
घरेलू और वैश्विक खरीद
-
समेकन
-
इंजीनियरिंग एकीकरण
-
अभियांत्रिकी सेवा
हम जिस प्रकार की धातु फोर्जिंग प्रक्रियाओं की पेशकश करते हैं, वे हैं हॉट एंड कोल्ड डाई, ओपन डाई और क्लोज्ड डाई, इंप्रेशन डाई और फ्लैशलेस फोर्जिंग, cogging, फुलरिंग, एजिंग और सटीक फोर्जिंग, नियर-नेट-शेप, हेडिंग , स्विंगिंग, अपसेट फोर्जिंग, मेटल हॉबिंग, प्रेस एंड रोल एंड रेडियल एंड ऑर्बिटल एंड रिंग एंड इज़ोटेर्मल फोर्जिंग, कॉइनिंग, रिवेटिंग, मेटल बॉल फोर्जिंग, मेटल पियर्सिंग, साइज़िंग, हाई एनर्जी रेट फोर्जिंग।
हमारे पाउडर धातुकर्म और पाउडर प्रसंस्करण तकनीक पाउडर दबाने और सिंटरिंग, संसेचन, घुसपैठ, गर्म और ठंडे आइसोस्टैटिक दबाने, धातु इंजेक्शन मोल्डिंग, रोल संघनन, पाउडर रोलिंग, पाउडर एक्सट्रूज़न, लूज सिंटरिंग, स्पार्क सिंटरिंग, हॉट प्रेसिंग हैं।
हम अनुशंसा करते हैं कि आप यहां क्लिक करें
AGS-TECH Inc. द्वारा फोर्जिंग प्रक्रियाओं के हमारे योजनाबद्ध चित्र डाउनलोड करें
AGS-TECH Inc. द्वारा पाउडर धातुकर्म प्रक्रियाओं के हमारे योजनाबद्ध चित्र डाउनलोड करें
फ़ोटो और स्केच के साथ डाउनलोड करने योग्य ये फ़ाइलें आपको नीचे दी गई जानकारी को बेहतर ढंग से समझने में मदद करेंगी।
धातु फोर्जिंग में, संपीड़ित बल लागू होते हैं और सामग्री विकृत हो जाती है और वांछित आकार प्राप्त होता है। उद्योग में सबसे आम जाली सामग्री लोहा और इस्पात हैं, लेकिन कई अन्य जैसे एल्यूमीनियम, तांबा, टाइटेनियम, मैग्नीशियम भी व्यापक रूप से जाली हैं। जाली धातु के हिस्सों ने सीलबंद दरारों और बंद खाली जगहों के अलावा अनाज संरचनाओं में सुधार किया है, इस प्रकार इस प्रक्रिया से प्राप्त भागों की ताकत अधिक है। फोर्जिंग से ऐसे पुर्जे बनते हैं जो कास्टिंग या मशीनिंग द्वारा बनाए गए पुर्जों की तुलना में अपने वजन के हिसाब से काफी मजबूत होते हैं। चूंकि जाली भागों को धातु के प्रवाह को उसके अंतिम आकार में बनाकर आकार दिया जाता है, धातु एक दिशात्मक अनाज संरचना लेती है जो भागों की बेहतर ताकत के लिए जिम्मेदार होती है। दूसरे शब्दों में, फोर्जिंग प्रक्रिया द्वारा प्राप्त भाग साधारण कास्ट या मशीनीकृत भागों की तुलना में बेहतर यांत्रिक गुणों को प्रकट करते हैं। धातु फोर्जिंग का वजन छोटे हल्के भागों से लेकर सैकड़ों हजारों पाउंड तक हो सकता है। हम ज्यादातर यांत्रिक रूप से मांग वाले अनुप्रयोगों के लिए फोर्जिंग का निर्माण करते हैं जहां ऑटोमोटिव पार्ट्स, गियर, वर्क टूल्स, हैंड टूल्स, टर्बाइन शाफ्ट, मोटरसाइकिल गियर जैसे हिस्सों पर उच्च तनाव लागू होते हैं। चूंकि टूलींग और सेट-अप लागत अपेक्षाकृत अधिक है, इसलिए हम इस निर्माण प्रक्रिया को केवल उच्च मात्रा में उत्पादन और कम मात्रा के लिए लेकिन उच्च मूल्य वाले महत्वपूर्ण घटकों जैसे एयरोस्पेस लैंडिंग गियर के लिए अनुशंसा करते हैं। टूलींग की लागत के अलावा, बड़ी मात्रा में जाली भागों के लिए निर्माण का समय कुछ साधारण मशीनी भागों की तुलना में लंबा हो सकता है, लेकिन तकनीक उन भागों के लिए महत्वपूर्ण है जो बोल्ट, नट, विशेष अनुप्रयोग जैसे असाधारण ताकत की आवश्यकता होती है। फास्टनरों, मोटर वाहन, फोर्कलिफ्ट, क्रेन भागों।
• हॉट डाई और कोल्ड डाई फोर्जिंग: हॉट डाई फोर्जिंग, जैसा कि नाम से पता चलता है, उच्च तापमान पर किया जाता है, इसलिए लचीलापन अधिक होता है और सामग्री की ताकत कम होती है। यह आसान विरूपण और फोर्जिंग की सुविधा प्रदान करता है। इसके विपरीत, कोल्ड डाई फोर्जिंग को कम तापमान पर किया जाता है और इसके लिए उच्च बलों की आवश्यकता होती है जिसके परिणामस्वरूप निर्मित भागों की तनाव सख्त, बेहतर सतह खत्म और सटीकता होती है।
• ओपन डाई और इंप्रेशन डाई फोर्जिंग: ओपन डाई फोर्जिंग में, डाईज सामग्री को संकुचित होने से नहीं रोकता है, जबकि इंप्रेशन डाई फोर्जिंग में डाई के भीतर कैविटी सामग्री प्रवाह को प्रतिबंधित करती है जबकि यह वांछित आकार में जाली होती है। UPSET FORGING या UPSETTING भी कहा जाता है, जो वास्तव में वही नहीं बल्कि एक बहुत ही समान प्रक्रिया है, एक खुली मरने की प्रक्रिया है जहां काम का टुकड़ा दो फ्लैट मरने के बीच सैंडविच होता है और एक संपीड़न बल इसकी ऊंचाई कम कर देता है। जैसे-जैसे ऊंचाई होती है reduced, वर्कपीस की चौड़ाई बढ़ती जाती है। हेडिंग, एक परेशान फोर्जिंग प्रक्रिया में बेलनाकार स्टॉक शामिल होता है जो इसके अंत में परेशान होता है और इसके क्रॉस सेक्शन को स्थानीय रूप से बढ़ाया जाता है। शीर्ष में स्टॉक को डाई, जाली के माध्यम से खिलाया जाता है और फिर लंबाई में काटा जाता है। ऑपरेशन तेजी से बड़ी मात्रा में फास्टनरों का उत्पादन करने में सक्षम है। अधिकतर यह एक कोल्ड वर्किंग ऑपरेशन है क्योंकि इसका उपयोग नेल एंड्स, स्क्रू एंड्स, नट और बोल्ट बनाने के लिए किया जाता है जहां सामग्री को मजबूत करने की आवश्यकता होती है। एक अन्य ओपन डाई प्रक्रिया COGGING है, जहां वर्क पीस को प्रत्येक चरण के साथ चरणों की एक श्रृंखला में जाली बनाया जाता है जिसके परिणामस्वरूप सामग्री का संपीड़न होता है और वर्कपीस की लंबाई के साथ ओपन डाई की बाद की गति होती है। प्रत्येक चरण में, मोटाई कम हो जाती है और लंबाई थोड़ी मात्रा में बढ़ जाती है। यह प्रक्रिया एक घबराए हुए छात्र की तरह है जो अपनी पेंसिल को छोटे-छोटे चरणों में काटता है। फुलरिंग नामक एक प्रक्रिया एक और खुली डाई फोर्जिंग विधि है जिसे हम अक्सर अन्य धातु फोर्जिंग संचालन होने से पहले वर्कपीस में सामग्री को वितरित करने के लिए पहले चरण के रूप में तैनात करते हैं। हम इसका उपयोग तब करते हैं जब वर्कपीस को कई फोर्जिंग_सीसी781905-5cde-3194-bb3b-136bad5cf58d_operations की आवश्यकता होती है। ऑपरेशन में, उत्तल सतहों के साथ मर जाते हैं और दोनों तरफ धातु के प्रवाह का कारण बनते हैं। फुलरिंग के लिए एक समान प्रक्रिया, दूसरी ओर EDGING में काम के टुकड़े को ख़राब करने के लिए अवतल सतहों के साथ ओपन डाई शामिल है। बाद के फोर्जिंग संचालन के लिए एक प्रारंभिक प्रक्रिया को भी किनारा करना दोनों पक्षों से केंद्र में एक क्षेत्र में सामग्री प्रवाह बनाता है। इम्प्रेशन डाई फोर्जिंग या क्लोज्ड डाई फोर्जिंग जैसा कि इसे डाई / मोल्ड का उपयोग भी कहा जाता है जो सामग्री को संपीड़ित करता है और इसके प्रवाह को अपने भीतर प्रतिबंधित करता है। डाई बंद हो जाती है और सामग्री डाई / मोल्ड कैविटी का आकार ले लेती है। सटीक फोर्जिंग, विशेष उपकरण और मोल्ड की आवश्यकता वाली एक प्रक्रिया, बिना या बहुत कम फ्लैश वाले भागों का उत्पादन करती है। दूसरे शब्दों में, भागों के पास अंतिम आयाम होंगे। इस प्रक्रिया में सामग्री की एक अच्छी तरह से नियंत्रित मात्रा को सावधानी से डाला जाता है और मोल्ड के अंदर रखा जाता है। हम इस विधि को जटिल आकार के लिए पतले वर्गों, छोटे सहनशीलता और ड्राफ्ट कोणों के साथ तैनात करते हैं और जब मात्रा मोल्ड और उपकरण लागत को उचित ठहराने के लिए पर्याप्त होती है।
• फ्लैशलेस फोर्जिंग: वर्कपीस को डाई में इस तरह रखा जाता है कि कोई भी सामग्री कैविटी से बाहर नहीं निकल सके और फ्लैश बन सके। इस प्रकार किसी अवांछित फ्लैश ट्रिमिंग की आवश्यकता नहीं है। यह एक सटीक फोर्जिंग प्रक्रिया है और इस प्रकार उपयोग की जाने वाली सामग्री की मात्रा के निकट नियंत्रण की आवश्यकता होती है।
• धातु की अदला-बदली या रेडियल फोर्जिंग: एक काम के टुकड़े पर परिधिगत रूप से डाई और जाली द्वारा कार्य किया जाता है। इंटीरियर वर्क पीस ज्योमेट्री बनाने के लिए एक खराद का धुरा भी इस्तेमाल किया जा सकता है। स्वेजिंग ऑपरेशन में वर्कपीस आमतौर पर प्रति सेकंड कई स्ट्रोक प्राप्त करता है। स्वैगिंग द्वारा उत्पादित विशिष्ट वस्तुएं नुकीले सिरे वाले उपकरण, टेपर्ड बार, स्क्रूड्राइवर हैं।
• धातु भेदी: हम इस ऑपरेशन को अक्सर भागों के निर्माण में एक अतिरिक्त ऑपरेशन के रूप में उपयोग करते हैं। वर्कपीस की सतह पर छेद किए बिना छेद करके एक छेद या गुहा बनाया जाता है। कृपया ध्यान दें कि पियर्सिंग ड्रिलिंग से अलग है जिसके परिणामस्वरूप छेद होता है।
• हॉबिंग: वांछित ज्यामिति के साथ एक पंच को वर्कपीस में दबाया जाता है और वांछित आकार के साथ एक गुहा बनाता है। हम इस पंच को HOB कहते हैं। ऑपरेशन में उच्च दबाव शामिल है और ठंड में किया जाता है। एक परिणाम के रूप में सामग्री ठंडा काम किया है और कठोर तनाव है। इसलिए यह प्रक्रिया अन्य निर्माण प्रक्रियाओं के लिए मोल्ड, डाई और कैविटी के निर्माण के लिए बहुत उपयुक्त है। एक बार हॉब निर्मित हो जाने के बाद, कोई भी व्यक्ति एक-एक करके मशीन की आवश्यकता के बिना कई समान गुहाओं का निर्माण आसानी से कर सकता है।
• रोल फोर्जिंग या रोल बनाने: धातु के हिस्से को आकार देने के लिए दो विरोधी रोल का उपयोग किया जाता है। वर्क पीस को रोल्स में फीड किया जाता है, रोल्स मुड़ते हैं और काम को गैप में खींचते हैं, फिर वर्क को रोल्स के ग्रोव्ड हिस्से के माध्यम से फीड किया जाता है और कंप्रेसिव फोर्स सामग्री को उसका वांछित आकार देते हैं। यह एक रोलिंग प्रक्रिया नहीं बल्कि एक फोर्जिंग प्रक्रिया है, क्योंकि यह एक सतत संचालन के बजाय एक असतत है। रोल ग्रोव्स पर ज्यामिति सामग्री को आवश्यक आकार और ज्यामिति के लिए बनाती है। इसे गर्म किया जाता है। फोर्जिंग प्रक्रिया होने के कारण यह उत्कृष्ट यांत्रिक गुणों वाले भागों का उत्पादन करती है और इसलिए हम इसका उपयोग शाफ्ट जैसे ऑटोमोटिव भागों के निर्माण के लिए करते हैं जिन्हें कठिन कार्य वातावरण में असाधारण सहनशक्ति की आवश्यकता होती है।
• कक्षीय फोर्जिंग: वर्कपीस को फोर्जिंग डाई कैविटी में रखा जाता है और एक ऊपरी डाई द्वारा जाली बनाई जाती है जो एक झुकाव वाले अक्ष पर घूमते हुए एक कक्षीय पथ में यात्रा करती है। प्रत्येक क्रांति में, ऊपरी पासा पूरे काम के टुकड़े पर संपीडित बल लगाता है। इन क्रांतियों को कई बार दोहराने से पर्याप्त फोर्जिंग की जाती है। इस निर्माण तकनीक के फायदे इसके कम शोर संचालन और कम बलों की जरूरत है। दूसरे शब्दों में, छोटे बलों के साथ कोई भी काम के टुकड़े के एक हिस्से पर बड़े दबाव को लागू करने के लिए एक अक्ष के चारों ओर एक भारी पासे को घुमा सकता है जो कि डाई के संपर्क में है। कभी-कभी डिस्क या शंक्वाकार भाग इस प्रक्रिया के लिए उपयुक्त होते हैं।
• रिंग फोर्जिंग: हम अक्सर सीमलेस रिंग बनाने के लिए उपयोग करते हैं। स्टॉक को लंबाई में काटा जाता है, परेशान किया जाता है और फिर एक केंद्रीय छेद बनाने के लिए सभी तरह से छेद किया जाता है। फिर इसे एक खराद का धुरा पर रखा जाता है और एक फोर्जिंग डाई इसे ऊपर से हथौड़े से मारती है क्योंकि रिंग को धीरे-धीरे घुमाया जाता है जब तक कि वांछित आयाम प्राप्त नहीं हो जाते।
• रिवेटिंग : पुर्जों को जोड़ने की एक सामान्य प्रक्रिया, पुर्जों के माध्यम से पहले से बने छिद्रों में सीधे धातु के टुकड़े डालने से शुरू होती है। इसके बाद धातु के टुकड़े के दोनों सिरों को ऊपरी और निचले डाई के बीच के जोड़ को निचोड़कर जाली बनाया जाता है।
• सिक्का बनाना : यांत्रिक प्रेस द्वारा की जाने वाली एक और लोकप्रिय प्रक्रिया, जिसमें कम दूरी पर बड़ी ताकतें लगाई जाती हैं। "सिक्का" नाम धातु के सिक्कों की सतहों पर जालीदार बारीक विवरणों से आता है। यह ज्यादातर एक उत्पाद के लिए एक परिष्करण प्रक्रिया है जहां इन विवरणों को काम के टुकड़े में स्थानांतरित करने वाले डाई द्वारा लागू बड़े बल के परिणामस्वरूप सतहों पर बारीक विवरण प्राप्त किया जाता है।
• धातु बॉल फोर्जिंग: बॉल बेयरिंग जैसे उत्पादों के लिए उच्च गुणवत्ता वाली सटीक रूप से निर्मित धातु की गेंदों की आवश्यकता होती है। SKEW रॉलिंग नामक एक तकनीक में, हम दो विरोधी रोल का उपयोग करते हैं जो लगातार घूमते रहते हैं क्योंकि स्टॉक को लगातार रोल में फीड किया जा रहा है। दो रोलों के एक छोर पर धातु के गोले उत्पाद के रूप में निकाले जाते हैं। धातु की गेंद फोर्जिंग के लिए एक दूसरी विधि डाई का उपयोग कर रही है जो मोल्ड गुहा के गोलाकार आकार लेते हुए उनके बीच रखे सामग्री स्टॉक को निचोड़ती है। अक्सर उत्पादित गेंदों को उच्च गुणवत्ता वाला उत्पाद बनने के लिए कुछ अतिरिक्त चरणों जैसे परिष्करण और पॉलिशिंग की आवश्यकता होती है।
• इज़ोटेर्मल फोर्जिंग / हॉट डाई फोर्जिंग: एक महंगी प्रक्रिया केवल तभी की जाती है जब लाभ / लागत मूल्य उचित हो। एक गर्म काम करने की प्रक्रिया जहां डाई को वर्कपीस के समान तापमान पर गर्म किया जाता है। चूंकि दोनों मर जाते हैं और काम एक ही तापमान के बारे में होते हैं, इसलिए कोई शीतलन नहीं होता है और धातु की प्रवाह विशेषताओं में सुधार होता है। ऑपरेशन सुपर मिश्र धातुओं और घटिया फोर्जेबिलिटी और सामग्री के साथ एक अच्छा फिट है जिसका
यांत्रिक गुण छोटे तापमान प्रवणता और परिवर्तनों के प्रति बहुत संवेदनशील होते हैं।
• मेटल साइजिंग: यह कोल्ड फिनिशिंग प्रक्रिया है। जिस दिशा में बल लगाया जाता है, उसे छोड़कर सभी दिशाओं में सामग्री प्रवाह अप्रतिबंधित है। नतीजतन, बहुत अच्छी सतह खत्म और सटीक आयाम प्राप्त होते हैं।
• उच्च ऊर्जा दर फोर्जिंग: इस तकनीक में पिस्टन की बांह से जुड़ा एक ऊपरी साँचा शामिल होता है जिसे तेजी से धकेला जाता है क्योंकि ईंधन-वायु मिश्रण एक स्पार्क प्लग द्वारा प्रज्वलित होता है। यह कार के इंजन में पिस्टन के संचालन जैसा दिखता है। मोल्ड काम के टुकड़े को बहुत तेजी से हिट करता है और फिर बैकप्रेशर की बदौलत बहुत तेजी से अपनी मूल स्थिति में लौट आता है। काम कुछ मिलीसेकंड के भीतर जाली हो जाता है और इसलिए काम के ठंडा होने का समय नहीं होता है। यह उन भागों को बनाने के लिए उपयोगी है जिनमें बहुत तापमान संवेदनशील यांत्रिक गुण होते हैं। दूसरे शब्दों में प्रक्रिया इतनी तेज है कि पूरे हिस्से में निरंतर तापमान के तहत हिस्सा बनता है और मोल्ड/वर्क पीस इंटरफेस पर तापमान प्रवणता नहीं होगी।
• डाई फोर्जिंग में, धातु को दो मेल खाने वाले स्टील ब्लॉकों के बीच विशेष आकार के साथ पीटा जाता है, जिसे डाई कहा जाता है। जब धातु को पासे के बीच अंकित किया जाता है, तो यह उसी आकार का हो जाता है जैसा कि पासे में होता है। जब यह अपने अंतिम आकार में पहुंच जाता है, तो इसे ठंडा होने के लिए निकाल लिया जाता है। यह प्रक्रिया मजबूत भागों का निर्माण करती है जो एक सटीक आकार के होते हैं, लेकिन विशेष मरने के लिए बड़े निवेश की आवश्यकता होती है। अपसेट फोर्जिंग धातु के टुकड़े को चपटा करके उसका व्यास बढ़ा देता है। यह आमतौर पर छोटे भागों को बनाने के लिए उपयोग किया जाता है, विशेष रूप से बोल्ट और नाखून जैसे फास्टनरों पर सिर बनाने के लिए।
• पाउडर धातुकर्म/पाउडर प्रसंस्करण: जैसा कि नाम से ही स्पष्ट है, इसमें पाउडर से कुछ ज्यामिति और आकृतियों के ठोस हिस्से बनाने के लिए निर्माण प्रक्रियाएं शामिल हैं। यदि इस उद्देश्य के लिए धातु पाउडर का उपयोग किया जाता है तो यह पाउडर धातु विज्ञान का क्षेत्र है और यदि गैर-धातु पाउडर का उपयोग किया जाता है तो यह पाउडर प्रसंस्करण होता है। पाउडर को दबाने और सिंटरिंग द्वारा ठोस भागों का उत्पादन किया जाता है।
पाउडर प्रेसिंग का उपयोग पाउडर को वांछित आकार में कॉम्पैक्ट करने के लिए किया जाता है। सबसे पहले, प्राथमिक सामग्री को भौतिक रूप से पाउडर किया जाता है, इसे कई छोटे व्यक्तिगत कणों में विभाजित किया जाता है। पाउडर मिश्रण को डाई में भर दिया जाता है और एक पंच पाउडर की ओर बढ़ता है और इसे वांछित आकार में जमा देता है। ज्यादातर कमरे के तापमान पर किया जाता है, पाउडर को दबाकर एक ठोस भाग प्राप्त किया जाता है और इसे ग्रीन कॉम्पैक्ट कहा जाता है। बाइंडर्स और लुब्रिकेंट्स का इस्तेमाल आमतौर पर कॉम्पेक्टेबिलिटी बढ़ाने के लिए किया जाता है। हम कई हजार टन क्षमता वाले हाइड्रोलिक प्रेस का उपयोग करके पाउडर प्रेस बनाने में सक्षम हैं। इसके अलावा हमारे पास डबल एक्शन प्रेस हैं जिनमें शीर्ष और नीचे के घूंसे के साथ-साथ अत्यधिक जटिल भाग ज्यामिति के लिए कई एक्शन प्रेस हैं। एकरूपता जो कई पाउडर धातु विज्ञान / पाउडर प्रसंस्करण संयंत्रों के लिए एक महत्वपूर्ण चुनौती है, एजीएस-टेक के लिए कोई बड़ी समस्या नहीं है क्योंकि कई वर्षों से ऐसे भागों के कस्टम निर्माण में हमारे व्यापक अनुभव के कारण। मोटे हिस्सों के साथ भी जहां एकरूपता एक चुनौती है, हम सफल हुए हैं। अगर हम आपकी परियोजना के लिए प्रतिबद्ध हैं, तो हम आपके हिस्से बनाएंगे। यदि हमें कोई संभावित जोखिम दिखाई देता है, तो हम आपको in में सूचित करेंगे।
अग्रिम.
पाउडर सिंटरिंग, जो दूसरा चरण है, में तापमान को एक निश्चित डिग्री तक बढ़ाना और उस स्तर पर तापमान को एक निश्चित समय तक बनाए रखना शामिल है ताकि दबाए गए हिस्से में पाउडर कण एक साथ बंध सकें। यह बहुत मजबूत बंधन और वर्कपीस को मजबूत करता है। पाउडर के पिघलने के तापमान के करीब सिंटरिंग होता है। सिंटरिंग के दौरान संकोचन होगा, भौतिक शक्ति, घनत्व, लचीलापन, तापीय चालकता, विद्युत चालकता बढ़ जाती है। हमारे पास सिंटरिंग के लिए बैच और निरंतर भट्टियां हैं। हमारी क्षमताओं में से एक हमारे द्वारा उत्पादित भागों के सरंध्रता के स्तर को समायोजित करना है। उदाहरण के लिए हम भागों को कुछ हद तक छिद्रपूर्ण रखकर धातु फिल्टर का उत्पादन करने में सक्षम हैं।
इम्प्रेग्नेशन नामक तकनीक का उपयोग करते हुए, हम धातु के छिद्रों को तेल जैसे तरल पदार्थ से भरते हैं। हम उदाहरण के लिए तेल संसेचित बियरिंग्स का उत्पादन करते हैं जो स्वयं-चिकनाई कर रहे हैं। इन्फिल्ट्रेशन प्रक्रिया में हम धातु के छिद्रों को आधार सामग्री की तुलना में कम गलनांक वाली दूसरी धातु से भरते हैं। मिश्रण को दो धातुओं के पिघलने वाले तापमान के बीच के तापमान पर गर्म किया जाता है। इसके फलस्वरूप कुछ विशेष गुण प्राप्त हो सकते हैं। जब विशेष सुविधाओं या गुणों को प्राप्त करने की आवश्यकता होती है या जब कम प्रक्रिया चरणों के साथ भाग का निर्माण किया जा सकता है, तो हम पाउडर निर्मित भागों पर मशीनिंग और फोर्जिंग जैसे माध्यमिक संचालन भी करते हैं।
आइसोस्टैटिक प्रेसिंग: इस प्रक्रिया में भाग को संकुचित करने के लिए द्रव दबाव का उपयोग किया जा रहा है। धातु के पाउडर को एक सीलबंद लचीले कंटेनर से बने सांचे में रखा जाता है। आइसोस्टैटिक प्रेसिंग में, पारंपरिक दबाव में देखे जाने वाले अक्षीय दबाव के विपरीत, चारों ओर से दबाव डाला जाता है। आइसोस्टैटिक प्रेसिंग के फायदे भाग के भीतर एक समान घनत्व हैं, विशेष रूप से बड़े या मोटे भागों के लिए, बेहतर गुण। इसका नुकसान लंबे चक्र समय और अपेक्षाकृत कम ज्यामितीय सटीकता है। कोल्ड आइसोस्टैटिक प्रेसिंग कमरे के तापमान पर की जाती है और लचीला मोल्ड रबर, पीवीसी या यूरेथेन या इसी तरह की सामग्री से बना होता है। दबाव बनाने और संघनन के लिए इस्तेमाल किया जाने वाला द्रव तेल या पानी है। हरे रंग की कॉम्पैक्ट की पारंपरिक सिंटरिंग इस प्रकार है। दूसरी ओर हॉट आइसोस्टैटिक प्रेसिंग उच्च तापमान पर की जाती है और मोल्ड सामग्री शीट मेटल या सिरेमिक होती है जिसमें उच्च पर्याप्त गलनांक होता है जो तापमान का प्रतिरोध करता है। दबाव डालने वाला द्रव आमतौर पर एक अक्रिय गैस होता है। प्रेसिंग और सिंटरिंग ऑपरेशन एक चरण में किए जाते हैं। सरंध्रता लगभग पूरी तरह से समाप्त हो गई है, एक समान ग्रेन संरचना प्राप्त की जाती है। गर्म आइसोस्टैटिक दबाने का लाभ यह है कि यह कास्टिंग और फोर्जिंग के लिए तुलनीय भागों का उत्पादन कर सकता है, जबकि सामग्री बनाने के लिए जो कि कास्टिंग और फोर्जिंग के लिए उपयुक्त नहीं हैं, का उपयोग किया जा सकता है। गर्म आइसोस्टैटिक प्रेसिंग का नुकसान इसका उच्च चक्र समय है और इसलिए लागत है। यह कम मात्रा के महत्वपूर्ण भागों के लिए उपयुक्त है।
धातु इंजेक्शन मोल्डिंग: पतली दीवारों और विस्तृत ज्यामिति के साथ जटिल भागों के उत्पादन के लिए बहुत उपयुक्त प्रक्रिया। छोटे भागों के लिए सबसे उपयुक्त। पाउडर और पॉलीमर बाइंडर को मिलाया जाता है, गर्म किया जाता है और एक सांचे में डाला जाता है। पॉलिमर बाइंडर पाउडर कणों की सतहों को कोट करता है। मोल्डिंग के बाद, एक विलायक का उपयोग करके भंग के कम तापमान हीटिंग द्वारा बाइंडर को हटा दिया जाता है।
रोल संघनन/पाउडर रोलिंग: पाउडर का उपयोग निरंतर स्ट्रिप्स या शीट बनाने के लिए किया जाता है। पाउडर को एक फीडर से खिलाया जाता है और दो घूर्णन रोल द्वारा शीट या स्ट्रिप्स में संकुचित किया जाता है। ऑपरेशन ठंडा किया जाता है। शीट को सिंटरिंग भट्टी में ले जाया जाता है। सिंटरिंग प्रक्रिया को दूसरी बार दोहराया जा सकता है।
पाउडर एक्सट्रूज़न: बड़ी लंबाई से व्यास अनुपात वाले भागों का निर्माण पाउडर के साथ एक पतली शीट धातु के कंटेनर को बाहर निकालकर किया जाता है।
लूज सिंटरिंग: जैसा कि नाम से ही स्पष्ट है, यह एक दबाव रहित संघनन और सिंटरिंग विधि है, जो धातु फिल्टर जैसे बहुत छिद्रपूर्ण भागों के उत्पादन के लिए उपयुक्त है। पाउडर को बिना संघनन के मोल्ड गुहा में डाला जाता है।
लूज सिंटरिंग: जैसा कि नाम से ही स्पष्ट है, यह एक दबाव रहित संघनन और सिंटरिंग विधि है, जो धातु फिल्टर जैसे बहुत छिद्रपूर्ण भागों के उत्पादन के लिए उपयुक्त है। पाउडर को बिना संघनन के मोल्ड गुहा में डाला जाता है।
स्पार्क सिंटरिंग: पाउडर को दो विरोधी पंचों द्वारा मोल्ड में संपीड़ित किया जाता है और एक उच्च शक्ति विद्युत प्रवाह को पंच पर लगाया जाता है और उनके बीच सैंडविच किए गए कॉम्पैक्ट पाउडर से होकर गुजरता है। उच्च धारा पाउडर कणों से सतह की फिल्मों को जला देती है और उत्पन्न गर्मी के साथ उन्हें सिंटर कर देती है। प्रक्रिया तेज है क्योंकि गर्मी बाहर से नहीं बल्कि मोल्ड के भीतर से उत्पन्न होती है।
गर्म दबाव: पाउडर को एक ही चरण में दबाया जाता है और एक मोल्ड में पाप किया जाता है जो उच्च तापमान का सामना कर सकता है। जैसे ही डाई संकुचित होती है, उस पर पाउडर हीट लगाई जाती है। इस विधि द्वारा प्राप्त अच्छी सटीकता और यांत्रिक गुण इसे एक आकर्षक विकल्प बनाते हैं। यहां तक कि अपवर्तक धातुओं को ग्रेफाइट जैसे मोल्ड सामग्री का उपयोग करके संसाधित किया जा सकता है।