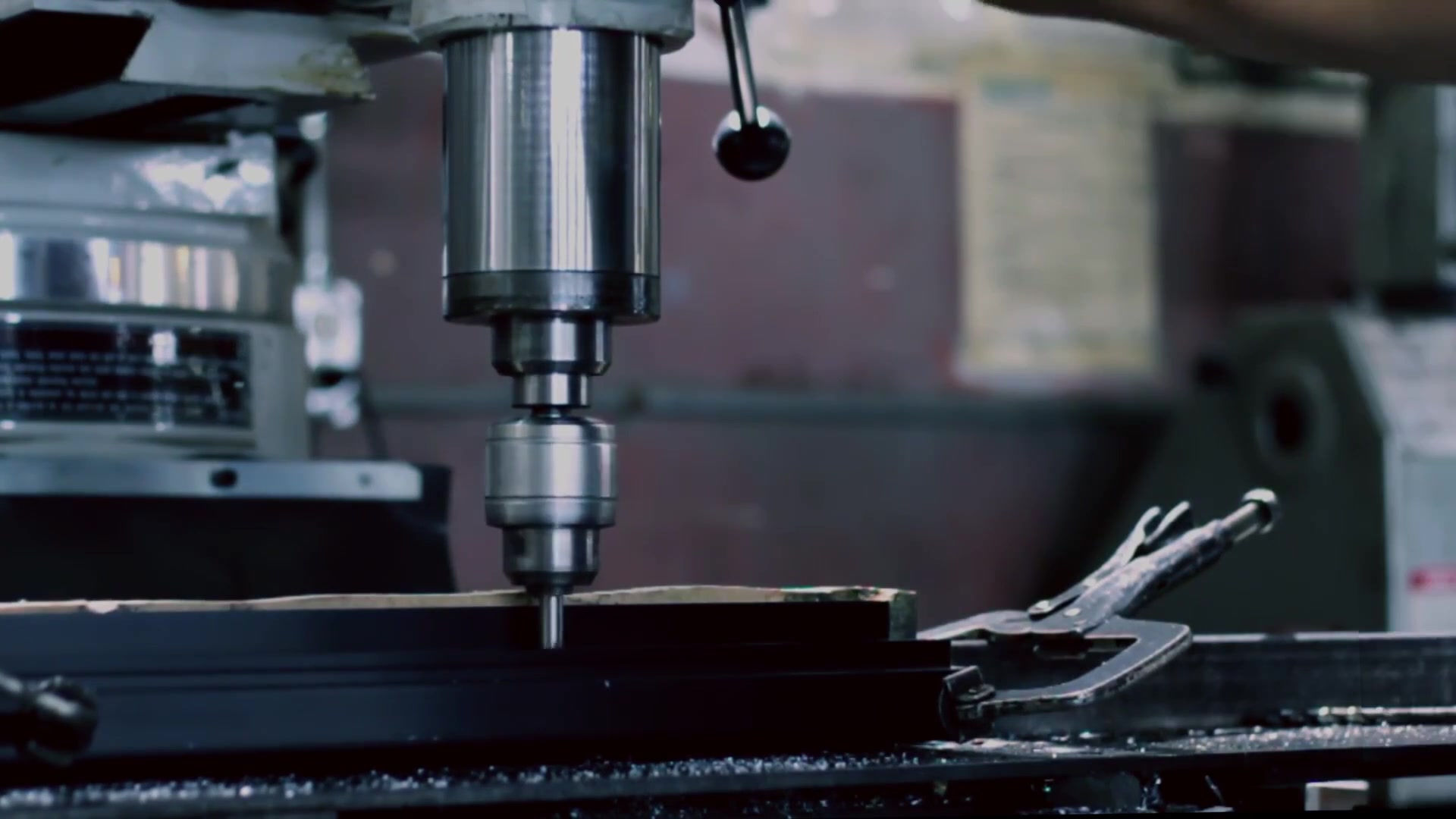
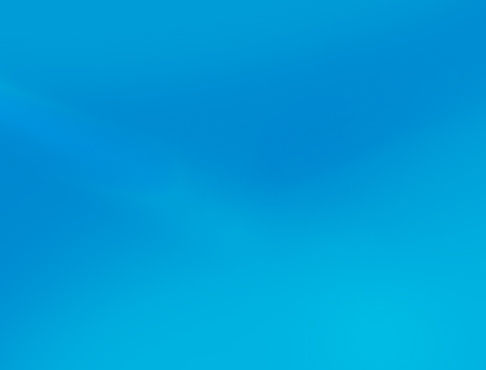
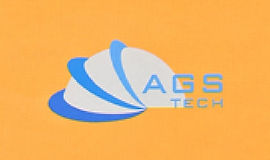
Globális egyedi gyártó, integrátor, konszolidátor, kiszervezési partner a termékek és szolgáltatások széles skálájához.
Mi vagyunk az Ön egyablakos forrása a gyártás, gyártás, tervezés, konszolidáció, integráció, egyedi gyártású és késztermékek és szolgáltatások kiszervezése terén.
Choose your Language
-
Egyedi gyártás
-
Belföldi és globális szerződéses gyártás
-
Gyártási outsourcing
-
Belföldi és globális beszerzés
-
Consolidation
-
Mérnöki integráció
-
Mérnöki szolgáltatások
Az általunk a gyártásban alkalmazott számos ÖSSZEFOGLALÁSI technika közül kiemelt hangsúlyt kap a HEGESZTÉS, FORRSZÍTÁS, RAGASZTÁS és EGYEDI MECHANIKAI ÖSSZESZERELÉS, mert ezeket a technikákat széles körben alkalmazzák olyan alkalmazásokban, mint a hermetikus szerelvények gyártása, a high-tech termékgyártás és a speciális tömítés. Itt ezeknek az illesztési technikáknak a speciálisabb aspektusaira koncentrálunk, mivel ezek a fejlett termékek és szerelvények gyártásához kapcsolódnak.
FÚZIÓS HEGESZTÉS: Hőt használunk az anyagok olvasztására és egyesítésére. A hőt elektromos árammal vagy nagyenergiájú gerendákkal biztosítják. Az általunk alkalmazott fúziós hegesztés típusok: OXYFUEL GÁZHEGESZTÉS, ÍVHEGESZTÉS, NAGYENERGIÁJÚ HEGESZTÉS.
SZILÁRDHEZETŐ HEGESZTÉS: Az alkatrészeket olvasztás és ömlesztés nélkül egyesítjük. Szilárdtest-hegesztési módszereink a HIDEG, ULTRAHANGOS, ELLENÁLLÁS, SÚRLÁS, ROBBANÁS HEGESZTÉS és DIFFÚZIÓS RAGASZTÁS.
FORRASZTÁS ÉS FORRASZTÁS: Töltőfémeket használnak, és azt az előnyt biztosítják, hogy alacsonyabb hőmérsékleten dolgozunk, mint a hegesztésnél, így kevesebb szerkezeti sérülés keletkezik a termékeken. A kerámia-fém idomokat, hermetikus tömítést, vákuumátvezetéseket, magas és ultramagas vákuum- és folyadékszabályozási alkatrészeket gyártó keményforrasztóüzemünkkel kapcsolatos információkat itt találja:Forrasztógyári prospektus
RAGASZTÁS: Az iparban használt ragasztók és az alkalmazások sokfélesége miatt külön oldalunk van erre. A ragasztással foglalkozó oldalunk megtekintéséhez kattintson ide.
EGYEDI MECHANIKAI ÖSSZESZERELÉS: Különféle rögzítőelemeket használunk, például csavarokat, csavarokat, anyákat, szegecseket. Rögzítőink nem korlátozódnak a szokásos, polcról kapható kötőelemekre. Speciális kötőelemeket tervezünk, fejlesztünk és gyártunk, amelyek nem szabványos anyagokból készülnek, hogy megfeleljenek a speciális alkalmazások követelményeinek. Néha elektromos vagy hő nem vezetőképesség kívánatos, míg néha vezetőképesség. Egyes speciális alkalmazásokhoz az ügyfélnek olyan speciális rögzítőelemekre van szüksége, amelyeket nem lehet eltávolítani a termék tönkretétele nélkül. Végtelen sok ötlet és alkalmazás létezik. Nálunk mindent megtalálsz, ha nem készen, gyorsan kifejlesztjük. A mechanikus összeszereléssel foglalkozó oldalunk megtekintéséhez kattintson ide. Nézzük meg részletesebben a különféle illesztési technikáinkat.
OXYFUEL GAS HEGESZTÉS (OFW): A hegesztési láng előállításához oxigénnel kevert fűtőgázt használunk. Ha acetilént használunk tüzelőanyagként és oxigénként, azt oxiacetilén gázhegesztésnek nevezzük. Az oxigéngáz égési folyamatában két kémiai reakció megy végbe:
C2H2 + O2 ------» 2CO + H2 + Hő
2CO + H2 + 1,5 O2--------» 2 CO2 + H2O + Hő
Az első reakció során az acetilént szén-monoxidra és hidrogénre disszociálják, miközben a teljes hőtermelés mintegy 33%-át állítják elő. A fenti második eljárás a hidrogén és a szén-monoxid további elégetését jelenti, miközben a teljes hő mintegy 67%-át állítják elő. A láng hőmérséklete 1533 és 3573 Kelvin között van. A gázkeverék oxigénszázaléka fontos. Ha az oxigéntartalom több mint a fele, akkor a láng oxidálószerré válik. Ez egyes fémeknél nemkívánatos, mások számára viszont kívánatos. Egy példa arra, amikor az oxidáló láng kívánatos, a rézalapú ötvözetek, mivel passziváló réteget képeznek a fémen. Másrészt, ha az oxigéntartalom csökken, a teljes égés nem lehetséges, és a láng redukáló (karburáló) lánggá válik. A redukáló láng hőmérséklete alacsonyabb, ezért alkalmas olyan eljárásokra, mint a forrasztás és keményforrasztás. Más gázok is potenciális tüzelőanyagok, de van néhány hátrányuk az acetilénhez képest. Alkalmanként töltőrudak vagy huzalok formájában töltőfémeket szállítunk a hegesztési zónába. Némelyikük folyasztószerrel van bevonva, hogy késleltesse a felületek oxidációját, és így védje az olvadt fémet. A fluxus további előnye az oxidok és egyéb anyagok eltávolítása a hegesztési zónából. Ez erősebb kötődéshez vezet. Az oxigéngázos hegesztés egy változata a NYOMÁSOS GÁZHEGESZTÉS, ahol a két komponenst a határfelületükön hevítik fel oxiacetilén gázpisztoly segítségével, és amint a határfelület elkezd olvadni, a pisztolyt kihúzzák, és axiális erőt alkalmaznak a két rész összenyomására. amíg a felület megszilárdul.
ÍVHEGESZTÉS: Az elektromos energiát használva ívet hozunk létre az elektróda csúcsa és a hegesztendő részek között. A tápegység lehet AC vagy DC, míg az elektródák fogyaszthatók vagy nem fogyaszthatók. Az ívhegesztés hőátadása a következő egyenlettel fejezhető ki:
H / l = ex VI / v
Itt H a hőbevitel, l a hegesztési varrat hossza, V és I az alkalmazott feszültség és áram, v a hegesztési sebesség és e a folyamat hatékonysága. Minél nagyobb az „e” hatásfok, annál előnyösebben hasznosul a rendelkezésre álló energia az anyag olvasztására. A hőbevitel a következőképpen is kifejezhető:
H = ux (térfogat) = ux A xl
Itt u az olvadás fajlagos energiája, A a varrat keresztmetszete és l a varrat hossza. A fenti két egyenletből a következőket kaphatjuk:
v = ex VI / u A
Az ívhegesztés egy változata a SHIELDED METAL ARC WELDING (SMAW), amely az összes ipari és karbantartási hegesztési folyamat mintegy 50%-át teszi ki. AZ ELEKTROMOS ÍVHEGESZTÉS (STAC HEGESZTÉS) úgy történik, hogy a bevonatos elektróda hegyét hozzáérinti a munkadarabhoz, és gyorsan visszahúzza az ív fenntartásához elegendő távolságra. Ezt az eljárást pálcás hegesztésnek is nevezzük, mivel az elektródák vékony és hosszú pálcikák. A hegesztési folyamat során az elektróda hegye a bevonattal és az ív közelében lévő nem nemesfémmel együtt megolvad. Az alapfém, az elektródfém és az elektródabevonatból származó anyagok keveréke megszilárdul a hegesztési területen. Az elektróda bevonata dezoxidálódik és védőgázt képez a hegesztési tartományban, így megvédi a környezet oxigénjétől. Ezért az eljárást árnyékolt fém ívhegesztésnek nevezik. Az optimális hegesztési teljesítmény érdekében 50 és 300 amper közötti áramerősséget és általában 10 kW-nál kisebb teljesítményszintet használunk. Szintén fontos az egyenáram polaritása (az áram áramlási iránya). Az egyenes polaritás, ahol a munkadarab pozitív, az elektróda pedig negatív, előnyös a fémlemezek hegesztésénél a sekély behatolása miatt, valamint a nagyon széles hézagokkal rendelkező kötéseknél is. Fordított polaritás esetén, azaz az elektróda pozitív és a munkadarab negatív, akkor mélyebb hegesztési behatolást érhetünk el. Váltakozó árammal, mivel pulzáló íveink vannak, vastag szakaszokat tudunk hegeszteni nagy átmérőjű elektródákkal és maximális áramerősségekkel. Az SMAW hegesztési módszer 3-19 mm-es és még ennél is nagyobb vastagságú munkadarabokhoz alkalmas többszörös menetes technikával. A hegesztési varrat tetején keletkezett salakot drótkefével kell eltávolítani, hogy ne legyen korrózió és tönkremenetel a hegesztési helyen. Ez természetesen növeli az árnyékolt fém ívhegesztés költségeit. Ennek ellenére az SMAW a legnépszerűbb hegesztési technika az iparban és a javítási munkákban.
MERÜLT ÍVHEGESZTÉS (FŰRÉSZ): Ebben a folyamatban a hegesztési ívet szemcsés folyasztószerekkel árnyékoljuk, mint például mész, szilícium-dioxid, kalcium-fluorid, mangán-oxid stb. A szemcsés folyasztószert egy fúvókán keresztül gravitációs áramlással táplálják a hegesztési zónába. Az olvadt hegesztési zónát lefedő fluxus jelentősen véd a szikrától, füsttől, UV sugárzástól stb., és hőszigetelőként működik, így a hő mélyen behatol a munkadarabba. A meg nem ömlesztett fluxust visszanyerjük, kezeljük és újra felhasználjuk. Egy csupasz tekercset használnak elektródaként, és egy csövön keresztül a hegesztési területre vezetik. 300 és 2000 amper közötti áramot használunk. A merülőíves hegesztési (SAW) eljárás vízszintes és lapos helyzetekre és körhegesztésekre korlátozódik, ha a hegesztés során a kör alakú szerkezet (például csövek) elfordulása lehetséges. A sebesség elérheti az 5 m/perc-et. A SAW eljárás vastag lemezekhez alkalmas, és kiváló minőségű, szívós, képlékeny és egyenletes hegesztést eredményez. A termelékenység, vagyis az óránként felvitt hegesztési anyag mennyisége 4-10-szerese az SMAW eljáráshoz képest.
Egy másik ívhegesztési eljárás, nevezetesen a GAS METAL ARC WELDING (GMAW) vagy más néven METAL INERT GAS WELDING (MIG) azon alapul, hogy a hegesztési területet külső gázforrások, például hélium, argon, szén-dioxid stb. védik. Az elektródfémben további deoxidálószerek is lehetnek. A fogyóhuzalt egy fúvókán keresztül vezetik be a hegesztési zónába. A vas- és színesfémeket egyaránt tartalmazó gyártás gázíves fémívhegesztéssel (GMAW) történik. A hegesztési termelékenység körülbelül kétszerese az SMAW-eljárásénak. Automatizált hegesztőberendezéseket használnak. A fémet ebben a folyamatban háromféleképpen továbbítják: „Spray Transfer”: másodpercenként több száz kis fémcsepp átvitele az elektródáról a hegesztési területre. A „globuláris átvitelben” viszont szén-dioxidban gazdag gázokat használnak, és az olvadt fémgömböket az elektromos ív hajtja. A hegesztőáramok nagyok, a hegesztési varrat mélyebb behatolása, a hegesztési sebesség nagyobb, mint a permetezésnél. Így a gömb alakú átvitel jobb a nehezebb szakaszok hegesztéséhez. Végül a „rövidzárlatos” módszernél az elektróda csúcsa hozzáér az olvadt hegesztési medencéhez, rövidre zárva azt, miközben a fém 50 csepp/másodperc feletti sebességgel kerül át az egyes cseppekben. Alacsony áramot és feszültséget vékonyabb vezetékkel együtt használnak. A felhasznált teljesítmény körülbelül 2 kW és a hőmérséklet viszonylag alacsony, így ez a módszer alkalmas 6 mm-nél kisebb vékony lemezekhez.
A FLUX-CORED ARC WELDING (FCAW) eljárás egy másik változata hasonló a gázos fémívhegesztéshez, azzal a különbséggel, hogy az elektróda egy folyasztószerrel töltött cső. A mag-folyasztószeres elektródák használatának előnye, hogy stabilabb íveket hoznak létre, lehetőséget adnak a hegesztett fémek tulajdonságainak javítására, az SMAW-hegesztéshez képest kevésbé rideg és rugalmas folyasztószer, jobb hegesztési kontúrok. Az önárnyékolt magelektródák olyan anyagokat tartalmaznak, amelyek védik a hegesztési zónát a légkörtől. Kb. 20 kW teljesítményt használunk. A GMAW eljáráshoz hasonlóan az FCAW eljárás is lehetőséget kínál a folyamatos hegesztési folyamatok automatizálására, és gazdaságos. Különböző hegesztési fémek kémiája fejleszthető ki különböző ötvözetek hozzáadásával a folyasztószermaghoz.
Az ELECTROGAS WELDING (EGW) során az egymás mellett elhelyezett darabokat hegesztjük. Néha TOMPHEGESZTÉSnek is nevezik. A hegesztett fémet egy hegesztési üregbe helyezik két összekapcsolandó darab közé. A teret két vízhűtéses gát veszi körül, hogy az olvadt salak ne ömljön ki. A gátak mozgatása mechanikus hajtásokkal történik. Ha a munkadarab forgatható, akkor az elektrogázos hegesztési technikát csövek kerületi hegesztésére is használhatjuk. Az elektródákat egy vezetéken keresztül vezetik be a folyamatos ív fenntartása érdekében. Az áramerősség körülbelül 400 Amper vagy 750 Amper, a teljesítményszint pedig körülbelül 20 kW. A fluxusmagos elektródából vagy külső forrásból származó inert gázok árnyékolást biztosítanak. Az elektrogázos hegesztést (EGW) használjuk fémekhez, például acélokhoz, titánhoz stb. 12-75 mm vastagságban. A technika jól illeszkedik nagyméretű szerkezetekhez.
Mégis, egy másik technikában, az ELECTROSLAG WELDING (ESW) néven, az ívet meggyújtják az elektróda és a munkadarab alja között, és hozzáadják a fluxust. Amikor az olvadt salak eléri az elektróda csúcsát, az ív kialszik. Az energiaellátás az olvadt salak elektromos ellenállásán keresztül folyamatosan történik. 50 mm és 900 mm közötti vastagságú lemezeket is tudunk hegeszteni. Az áramerősség körülbelül 600 Amper, míg a feszültség 40-50 V között van. A hegesztési sebesség 12-36 mm/perc. Az alkalmazások hasonlóak az elektrogázhegesztéshez.
Egyik nem fogyó elektródával kapcsolatos eljárásunk, a GAS TUNGSTEN ARC WELDING (GTAW), más néven TUNGSTEN INERT GAS WELDING (TIG), magában foglalja a töltőfém huzalon történő ellátását. A szorosan illeszkedő hézagokhoz néha nem használunk töltőfémet. A TIG folyamatban nem folyasztószert használunk, hanem argont és héliumot használunk az árnyékoláshoz. A volfrám magas olvadáspontú, és a TIG hegesztési folyamat során nem fogyasztják, így az állandó áram és az ívhézag is fenntartható. A teljesítményszint 8 és 20 kW között van, az áramerősség pedig 200 Amper (DC) vagy 500 Amper (AC). Alumínium és magnézium esetében AC áramot használunk az oxidtisztító funkcióhoz. A volfrámelektróda szennyeződésének elkerülése érdekében kerüljük az olvadt fémekkel való érintkezést. A Gas Tungsten Arc Welding (GTAW) különösen vékony fémek hegesztésére alkalmas. A GTAW varratok nagyon jó minőségűek, jó felületi minőséggel.
A hidrogéngáz magasabb költsége miatt ritkábban alkalmazott technika az ATOMIC HYDROGEN WELDING (AHW), ahol áramló hidrogéngáz árnyékoló atmoszférájában ívet hozunk létre két volfrámelektróda között. Az AHW egy nem fogyó elektródahegesztési eljárás is. A H2 kétatomos hidrogéngáz atomformájára bomlik a hegesztési ív közelében, ahol a hőmérséklet meghaladja a 6273 Kelvint. Lebomlása során nagy mennyiségű hőt vesz fel az ívből. Amikor a hidrogénatomok nekiütköznek a hegesztési zónának, amely egy viszonylag hideg felület, akkor újra kétatomos formává egyesülnek, és felszabadítják a tárolt hőt. Az energia változtatható a munkadarab ívtávolságra való változtatásával.
Egy másik nem fogyó elektróda eljárásban, a PLASMA ARC WELDING (PAW) során koncentrált plazmaívet irányítunk a hegesztési zóna felé. A hőmérséklet PAW-ban eléri a 33 273 Kelvint. Közel azonos számú elektron és ion alkotja a plazmagázt. Egy kisáramú pilotív indítja el a plazmát, amely a volfrámelektróda és a nyílás között van. Az üzemi áramok általában 100 amper körül mozognak. Töltőfém adagolható. A plazmaíves hegesztésnél az árnyékolást egy külső árnyékoló gyűrű és gázok, például argon és hélium felhasználásával valósítják meg. A plazmaívhegesztésnél az ív lehet az elektróda és a munkadarab, vagy az elektróda és a fúvóka között. Ennek a hegesztési technikának az előnyei a többi módszerhez képest nagyobb energiakoncentráció, mélyebb és keskenyebb hegesztési képesség, jobb ívstabilitás, nagyobb hegesztési sebesség akár 1 méter/percig, kisebb hőtorzulás. Általában plazmaívhegesztést alkalmazunk 6 mm-nél kisebb vastagságoknál, esetenként pedig 20 mm-es vastagságnál alumínium és titán esetében.
NAGYENERGIÁJÚ HEGESZTÉS: Egy másik típusú fúziós hegesztési módszer, két változatként elektronsugaras hegesztéssel (EBW) és lézerhegesztéssel (LBW). Ezek a technikák különösen értékesek csúcstechnológiás termékeink gyártása során. Az elektronsugaras hegesztés során nagy sebességű elektronok ütköznek a munkadarabba, és mozgási energiájuk hővé alakul. A keskeny elektronnyaláb könnyen halad a vákuumkamrában. Az e-sugaras hegesztésnél általában nagyvákuumot használunk. 150 mm vastag lemezek hegeszthetők. Nincs szükség védőgázra, folyasztószerre vagy töltőanyagra. Az elektronsugaras fegyverek 100 kW teljesítményűek. Mély és keskeny hegesztések lehetségesek akár 30-ig terjedő nagy oldalaránnyal és kis hőhatású zónákkal. A hegesztési sebesség elérheti a 12 m/perc értéket. A lézersugaras hegesztésnél nagy teljesítményű lézereket használunk hőforrásként. A 10 mikronos nagy sűrűségű lézersugarak mélyen behatolnak a munkadarabba. A lézersugaras hegesztéssel akár 10-es mélység-szélesség arány is elérhető. Mind pulzáló, mind folyamatos hullámú lézereket használunk, az előbbit vékony anyagokhoz, az utóbbit pedig leginkább 25 mm-es vastagságú munkadarabokhoz. A teljesítményszint 100 kW-ig terjed. A lézersugaras hegesztés nem alkalmas optikailag nagyon visszaverő anyagokhoz. A hegesztési folyamat során gázok is használhatók. A lézersugaras hegesztési módszer jól illeszkedik az automatizáláshoz és a nagy volumenű gyártáshoz, és 2,5 m/perc és 80 m/perc közötti hegesztési sebességet kínál. Ennek a hegesztési technikának az egyik fő előnye, hogy olyan területekhez is hozzáférhet, ahol más technikák nem használhatók. A lézersugarak könnyen eljuthatnak ilyen nehéz területekre. Nincs szükség vákuumra, mint az elektronsugaras hegesztésnél. A lézersugaras hegesztéssel jó minőségű és szilárdságú, alacsony zsugorodású, alacsony torzítású, alacsony porozitású hegesztések érhetők el. A lézersugarak könnyen kezelhetők és formázhatók száloptikai kábelekkel. A technika tehát kiválóan alkalmas precíziós hermetikus szerelvények, elektronikai csomagok stb. hegesztésére.
Nézzük meg a SZILÁRDÁLLÁSÚ HEGESZTÉSI technikáinkat. A HIDEGHEGESZTÉS (CW) egy olyan folyamat, ahol hő helyett nyomást alkalmaznak szerszámok vagy hengerek segítségével a párosított részekre. Hideghegesztésnél legalább az egyik illeszkedő alkatrésznek képlékenynek kell lennie. A legjobb eredményt két hasonló anyaggal lehet elérni. Ha a hideghegesztéssel összekötendő két fém különbözik, akkor gyenge és törékeny kötéseket kaphatunk. A hideghegesztési módszer jól alkalmazható puha, képlékeny és kisméretű munkadarabokhoz, például elektromos csatlakozásokhoz, hőérzékeny tartályélekhez, bimetál szalagokhoz termosztátokhoz stb. A hideghegesztés egyik változata a tekercskötés (vagy tekercshegesztés), ahol a nyomást egy hengerpáron keresztül fejtik ki. Néha a hengeres hegesztést magasabb hőmérsékleten végezzük a jobb felületi szilárdság érdekében.
Egy másik általunk használt szilárdtest-hegesztési eljárás az ULTRAHANGOS HEGESZTÉS (USW), ahol a munkadarabokat statikus normálerő és oszcilláló nyírófeszültségek érik. Az oszcilláló nyírófeszültségeket egy átalakító hegyén keresztül fejtik ki. Az ultrahangos hegesztés 10-75 kHz frekvenciájú rezgéseket alkalmaz. Egyes alkalmazásokban, például varrathegesztésnél, forgó hegesztőtárcsát használunk hegyként. A munkadarabokra ható nyírófeszültségek kis képlékeny alakváltozásokat okoznak, felbontják az oxidrétegeket, szennyeződéseket és szilárdtest-kötéshez vezetnek. Az ultrahangos hegesztésnél alkalmazott hőmérséklet jóval a fémek olvadáspontja alatt van, és nem történik fúzió. Gyakran használjuk az ultrahangos hegesztési (USW) eljárást nemfémes anyagokhoz, például műanyagokhoz. A hőre lágyuló műanyagokban azonban a hőmérséklet eléri az olvadáspontot.
Egy másik népszerű technika, a DRICTION WELDING (FRW) során a hő súrlódás révén keletkezik az összekapcsolandó munkadarabok határfelületén. A dörzshegesztésnél az egyik munkadarabot álló helyzetben tartjuk, míg a másik munkadarabot egy rögzítőben tartjuk és állandó sebességgel forgatjuk. Ezután a munkadarabokat axiális erő hatására érintkezésbe hozzuk. A felületi forgási sebesség dörzshegesztésnél egyes esetekben elérheti a 900 m/perc értéket. Elegendő határfelületi érintkezés után a forgó munkadarab hirtelen leáll, és az axiális erő megnő. A hegesztési zóna általában egy szűk terület. A súrlódó hegesztési technika különféle anyagokból készült tömör és cső alakú alkatrészek összekapcsolására használható. Az FRW-ben előfordulhat némi vaku az interfészen, de ez a vaku eltávolítható másodlagos megmunkálással vagy köszörüléssel. A súrlódó hegesztési eljárásnak vannak változatai. Például a „tehetetlenségi súrlódásos hegesztés” egy lendkereket foglal magában, amelynek forgási kinetikus energiáját használják fel az alkatrészek hegesztésére. A hegesztés akkor fejeződik be, amikor a lendkerék megáll. A forgó tömeg és így a forgási mozgási energia változtatható. Egy másik változat a „lineáris súrlódásos hegesztés”, ahol lineáris oda-vissza mozgást gyakorolnak legalább az egyik összeillesztendő alkatrészre. A lineáris dörzshegesztésnél az alkatrészeknek nem kell kör alakúaknak lenniük, lehetnek téglalap alakúak, négyzet alakúak vagy más alakúak. A frekvenciák tíz Hz-ben, az amplitúdók milliméteres tartományban, a nyomások pedig tíz- vagy száz MPa-ban lehetnek. Végül a „súrlódó keverős hegesztés” némileg eltér a fentebb ismertetett másik kettőtől. Míg a tehetetlenségi súrlódásos hegesztésnél és a lineáris súrlódásos hegesztésnél a határfelületek felmelegítése súrlódás révén valósul meg két érintkező felület dörzsölésével, addig a súrlódó keverős hegesztésnél egy harmadik testet dörzsölnek a két összekapcsolandó felülethez. Egy 5-6 mm átmérőjű forgó szerszám érintkezik a kötéssel. A hőmérséklet 503 és 533 Kelvin közötti értékekre emelkedhet. A hézagban az anyag melegítése, keverése és keverése történik. A súrlódó keverős hegesztést különféle anyagokon alkalmazzuk, beleértve az alumíniumot, a műanyagokat és a kompozitokat. A hegesztési varratok egységesek, minősége kiváló, minimális pórusokkal. A súrlódó keverőhegesztés során nem keletkeznek gőzök vagy fröccsenések, és a folyamat jól automatizált.
ELLENÁLLÁS HEGESZTÉS (RW): A hegesztéshez szükséges hőt a két összeillesztendő munkadarab közötti elektromos ellenállás termeli. Az ellenálláshegesztés során nem használnak folyasztószert, védőgázt vagy fogyó elektródákat. A Joule-melegítés ellenálláshegesztésben történik, és a következőképpen fejezhető ki:
H = (I. négyzet) x R xtx K
H a keletkező hő joule-ban (watt-másodpercben), I áram Amperben, R ellenállás ohmban, t az áram átfolyási ideje másodpercben. A K tényező kisebb, mint 1, és az energia azon hányadát jelenti, amely nem vész el a sugárzás és a vezetés során. Az ellenállás-hegesztési folyamatokban az áramok elérhetik a 100 000 A-t is, de a feszültségek általában 0,5-10 Volt. Az elektródák jellemzően rézötvözetből készülnek. Ellenálláshegesztéssel hasonló és eltérő anyagok is összekapcsolhatók. Ennek az eljárásnak számos változata létezik: Az „ellenállási ponthegesztés” két egymással szemben lévő kerek elektródát foglal magában, amelyek érintkeznek a két lap átlapolt csatlakozásának felületeivel. A nyomást addig alkalmazzák, amíg az áramot le nem kapcsolják. A hegesztési rög általában legfeljebb 10 mm átmérőjű. Az ellenállási ponthegesztés enyhén elszíneződött bemélyedésnyomokat hagy a hegesztési pontokon. A ponthegesztés a legnépszerűbb ellenállás-hegesztési technikánk. A ponthegesztésben különféle elektródaformákat használnak a nehéz területek elérése érdekében. Ponthegesztő berendezésünk CNC vezérlésű, és több elektródával rendelkezik, amelyek egyidejűleg használhatók. Az „ellenállási varrathegesztés” egy másik változata kerék- vagy görgős elektródákkal történik, amelyek folyamatos ponthegesztést hoznak létre, amikor az áram eléri a kellően magas szintet a váltakozó áramú tápciklusban. Az ellenállási hegesztéssel előállított kötések folyadék- és gáztömörek. A körülbelül 1,5 m/perc hegesztési sebesség normális vékony lemezeknél. Alkalmazhatunk szakaszos áramokat, így a ponthegesztések a varrat mentén kívánt időközönként jönnek létre. Az „ellenállási vetületi hegesztésnél” egy vagy több kiemelkedést (gödröcskét) domborítunk a hegesztendő munkadarab egyik felületére. Ezek a kiemelkedések lehetnek kerekek vagy oválisak. Ezeken a dombornyomott helyeken, amelyek érintkezésbe kerülnek az illeszkedő résszel, magas helyi hőmérséklet érhető el. Az elektródák nyomást fejtenek ki, hogy összenyomják ezeket a kiemelkedéseket. Az ellenállás-kivetítő hegesztésben használt elektródák lapos hegyűek, és vízhűtéses rézötvözetekből állnak. Az ellenállás-kivetítő hegesztés előnye, hogy egy lökettel több hegesztést tudunk elvégezni, ezáltal meghosszabbodik az elektródák élettartama, különböző vastagságú lemezek hegeszthetősége, valamint anyák és csavarok lemezre hegeszthetősége. Az ellenállás-kivetítő hegesztés hátránya a mélyedések domborításának többletköltsége. Egy másik technika, a „villanóhegesztés” során a két munkadarab végén lévő ívből hő keletkezik, amikor azok érintkezni kezdenek. Ez a módszer alternatív megoldásként ívhegesztésnek is tekinthető. A határfelület hőmérséklete emelkedik, és az anyag meglágyul. Axiális erőt fejtenek ki, és hegesztési varrat keletkezik a lágyított tartományban. A villanóhegesztés befejezése után a kötés megmunkálható a jobb megjelenés érdekében. A villanóhegesztéssel kapott hegesztési minőség jó. A teljesítményszint 10-1500 kW. A villanóhegesztés alkalmas hasonló vagy eltérő fémek 75 mm átmérőig és 0,2 mm és 25 mm közötti vastagságú lemezek élek közötti összekötésére. A „csapos ívhegesztés” nagyon hasonlít a villanóhegesztéshez. A csap, például egy csavar vagy menetes rúd egy elektródaként szolgál, miközben egy munkadarabhoz, például egy lemezhez csatlakozik. A keletkező hő koncentrálása, az oxidáció megelőzése és az olvadt fém hegesztési zónában való megtartása érdekében eldobható kerámiagyűrűt helyeznek a kötés köré. Végül az „ütőhegesztés” egy másik ellenálláshegesztési eljárás, amely kondenzátort használ az elektromos energia ellátására. Ütőhegesztésnél a teljesítmény ezredmásodperceken belül lemerül, nagyon gyorsan nagy helyi hőt fejlesztve a csatlakozásnál. Az ütős hegesztést széles körben alkalmazzuk az elektronikai gyártóiparban, ahol kerülni kell az érzékeny elektronikai alkatrészek felmelegedését a csatlakozás közelében.
A ROBBANÁSI HEGESZTÉSnek nevezett technika magában foglalja egy robbanóanyag-réteg felrobbantását, amelyet az összeillesztendő munkadarabok egyikére helyeznek. A munkadarabra kifejtett nagyon nagy nyomás turbulens és hullámos felületet hoz létre, és mechanikus reteszelés történik. A robbanásveszélyes hegesztésnél a kötési szilárdság nagyon magas. A robbantásos hegesztés jó módszer a lemezek különböző fémekkel történő burkolására. A burkolat után a lemezeket vékonyabb részekre lehet hengerelni. Néha robbantásos hegesztést alkalmazunk a csövek kiterjesztésére, hogy azok szorosan a lemezhez tapadjanak.
Utolsó módszerünk a szilárdtest-illesztés tartományán belül a DIFFÚZIÓS KÖTÖTÉS vagy DIFFÚZIÓS HEGESZTÉS (DFW), amelyben a jó kötést főként az atomok határfelületi diffúziójával érjük el. A felületen előforduló képlékeny alakváltozás is hozzájárul a hegesztéshez. Az érintett hőmérséklet körülbelül 0,5 Tm, ahol Tm a fém olvadáspontja. A diffúziós hegesztés kötési szilárdsága a nyomástól, a hőmérséklettől, az érintkezési időtől és az érintkező felületek tisztaságától függ. Néha töltőfémeket használunk a határfelületen. Hőre és nyomásra van szükség a diffúziós kötésnél, és elektromos ellenállással vagy kemencével és önsúlyokkal, préssel vagy mással biztosítják. Hasonló és eltérő fémek diffúziós hegesztéssel is összekapcsolhatók. A folyamat viszonylag lassú az atomok migrációjához szükséges idő miatt. A DFW automatizálható, és széles körben használják összetett alkatrészek gyártásában a repülőgépiparban, az elektronikában és az orvosi iparban. A gyártott termékek között ortopédiai implantátumok, érzékelők, repülőgép-szerkezeti elemek találhatók. A diffúziós kötés kombinálható a SZUPERPLASTIC FORMING-mal összetett fémlemez szerkezetek készítéséhez. A lapok kiválasztott helyeit először diffúziós ragasztással kötik össze, majd a nem ragasztott részeket légnyomással formába expandálják. A módszerek ezen kombinációjával nagy merevség/tömeg arányú repülőgép- és űrszerkezeteket gyártanak. A diffúziós hegesztés / szuperplasztikus alakítás kombinált eljárása csökkenti a szükséges alkatrészek számát azáltal, hogy nincs szükség kötőelemekre, alacsony feszültségű, rendkívül pontos alkatrészeket eredményez gazdaságosan és rövid átfutási idővel.
FORRÁS: A keményforrasztási technikák alacsonyabb hőmérsékletet igényelnek, mint a hegesztéshez szükséges. A keményforrasztási hőmérséklet azonban magasabb, mint a forrasztási hőmérséklet. A keményforrasztás során az összeillesztendő felületek közé töltőanyagot helyeznek, és a hőmérsékletet a töltőanyag olvadási hőmérsékletére 723 Kelvin fölé, de a munkadarabok olvadási hőmérséklete alá emelik. Az olvadt fém kitölti a munkadarabok közötti szorosan illeszkedő teret. A reszelőfém lehűtése és ezt követő megszilárdulása erős kötéseket eredményez. A keményforrasztó hegesztésnél a töltőanyag a csatlakozásnál lerakódik. A keményforrasztásnál lényegesen több töltőfémet használnak fel, mint a keményforrasztásnál. Az oxidáló lánggal rendelkező oxi-acetilén pisztolyt keményforrasztó hegesztésnél a töltőfém leválasztására használják. A keményforrasztásnál alacsonyabb hőmérsékletnek köszönhetően kisebbek a problémák a hő által érintett zónákban, mint például a vetemedés és a maradék feszültség. Minél kisebb a hézag a keményforrasztásnál, annál nagyobb a kötés nyírószilárdsága. A maximális szakítószilárdság azonban optimális résnél (csúcsérték) érhető el. Ezen optimális érték alatt és felett a keményforrasztás szakítószilárdsága csökken. A tipikus hézagok keményforrasztásnál 0,025 és 0,2 mm között lehetnek. Különféle formájú keményforrasztási anyagokat használunk, mint például forrasztó, por, gyűrűk, huzal, szalag stb. és ezeket kifejezetten az Ön tervezési vagy termékgeometriájának megfelelően tudja legyártani. Meghatározzuk a keményforrasztó anyagok tartalmát is az Ön alapanyagának és felhasználásának megfelelően. A keményforrasztási műveleteknél gyakran használunk folyasztószereket a nem kívánt oxidrétegek eltávolítására és az oxidáció megelőzésére. A későbbi korrózió elkerülése érdekében a folyasztószereket általában az illesztési művelet után eltávolítják. Az AGS-TECH Inc. különféle keményforrasztási módszereket alkalmaz, többek között:
- Fáklyaforrasztás
- Kemencés keményforrasztás
- Indukciós keményforrasztás
- Ellenállási keményforrasztás
- Merítési keményforrasztás
- Infravörös keményforrasztás
- Diffúziós keményforrasztás
- High Energy Beam
A leggyakrabban használt keményforrasztott kötéseink jó szilárdságú, eltérő fémekből készülnek, mint például keményfém fúrószárak, betétek, optoelektronikus hermetikus tokok, tömítések.
FORRASZTÁS: Ez az egyik leggyakrabban használt technikánk, ahol a forrasztóanyag (töltőfém) kitölti a hézagot, mint a szorosan illeszkedő alkatrészek közötti keményforrasztáskor. Forraszanyagaink olvadáspontja 723 Kelvin alatt van. A gyártási műveletekben kézi és automatizált forrasztást egyaránt alkalmazunk. A keményforrasztáshoz képest a forrasztási hőmérséklet alacsonyabb. A forrasztás nem nagyon alkalmas magas hőmérsékletű vagy nagy szilárdságú alkalmazásokhoz. Forrasztáshoz ólommentes forrasztóanyagokat, valamint ón-ólom, ón-cink, ólom-ezüst, kadmium-ezüst, cink-alumínium ötvözeteket használunk. Mind a nem korrozív gyantaalapú, mind a szervetlen savakat és sókat folyasztószerként használják a forrasztáshoz. Speciális folyasztószereket használunk alacsony forraszthatóságú fémek forrasztásához. Azokban az alkalmazásokban, ahol kerámia anyagokat, üveget vagy grafitot kell forrasztanunk, először az alkatrészeket megfelelő fémmel bevonjuk a jobb forraszthatóság érdekében. Népszerű forrasztási technikáink a következők:
- Reflow vagy Paste forrasztás
- Hullámforrasztás
-Kemence forrasztás
- Fáklya forrasztás
- Indukciós forrasztás
- Vasforrasztás
- Ellenállásos forrasztás
- Merítési forrasztás
- Ultrahangos forrasztás
- Infravörös forrasztás
Az ultrahangos forrasztás egyedülálló előnyt kínál számunkra, mivel az ultrahangos kavitációs hatásnak köszönhetően nincs szükség folyasztószerre, amely eltávolítja az oxidfilmeket az összekapcsolandó felületekről. A Reflow és Wave forrasztás iparilag kiemelkedő technikáink az elektronikai nagy volumenű gyártáshoz, ezért érdemes részletesebben elmagyarázni. Az újrafolyós forrasztásnál félszilárd pasztákat használunk, amelyek forrasztófém részecskéket tartalmaznak. A pasztát szita- vagy sablonozási eljárással helyezik az illesztésre. A nyomtatott áramköri lapoknál (PCB) gyakran alkalmazzuk ezt a technikát. Amikor elektromos alkatrészeket helyeznek ezekre a pasztából készült párnákra, a felületi feszültség egy vonalban tartja a felületre szerelhető csomagokat. Az alkatrészek elhelyezése után a szerelvényt kemencében felmelegítjük, így megtörténik a visszafolyó forrasztás. A folyamat során a pasztában lévő oldószerek elpárolognak, a pasztában lévő fluxus aktiválódik, az alkatrészek előmelegednek, a forrasztási részecskék megolvasztják és nedvesítik a kötést, végül a PCB-szerelvény lassan lehűl. Második népszerű technikánk a nyomtatott áramköri lapok nagy volumenű gyártására, nevezetesen a hullámforrasztás azon a tényen alapul, hogy az olvadt forrasztóanyagok nedvesítik a fémfelületeket, és csak akkor hoznak létre jó kötést, ha a fémet előmelegítik. Az olvadt forrasztóanyag álló lamináris hullámát először egy szivattyú generálja, és az előmelegített és előmelegített PCB-ket a hullámon továbbítják. A forrasztás csak a szabaddá vált fémfelületeket nedvesíti, de nem nedvesíti az IC polimer csomagokat, sem a polimer bevonatú áramköri lapokat. A nagy sebességű forró vízsugár kifújja a felesleges forrasztást a csatlakozásból, és megakadályozza a szomszédos vezetékek közötti áthidalást. A felületre szerelhető csomagok hullámforrasztásánál először ragasztjuk őket az áramköri lapra a forrasztás előtt. Ismét szűrést és stencilezést alkalmaznak, de ezúttal epoxira. Miután az alkatrészeket a megfelelő helyükre helyezték, az epoxi megkeményedik, a táblákat felfordítják, és megtörténik a hullámforrasztás.