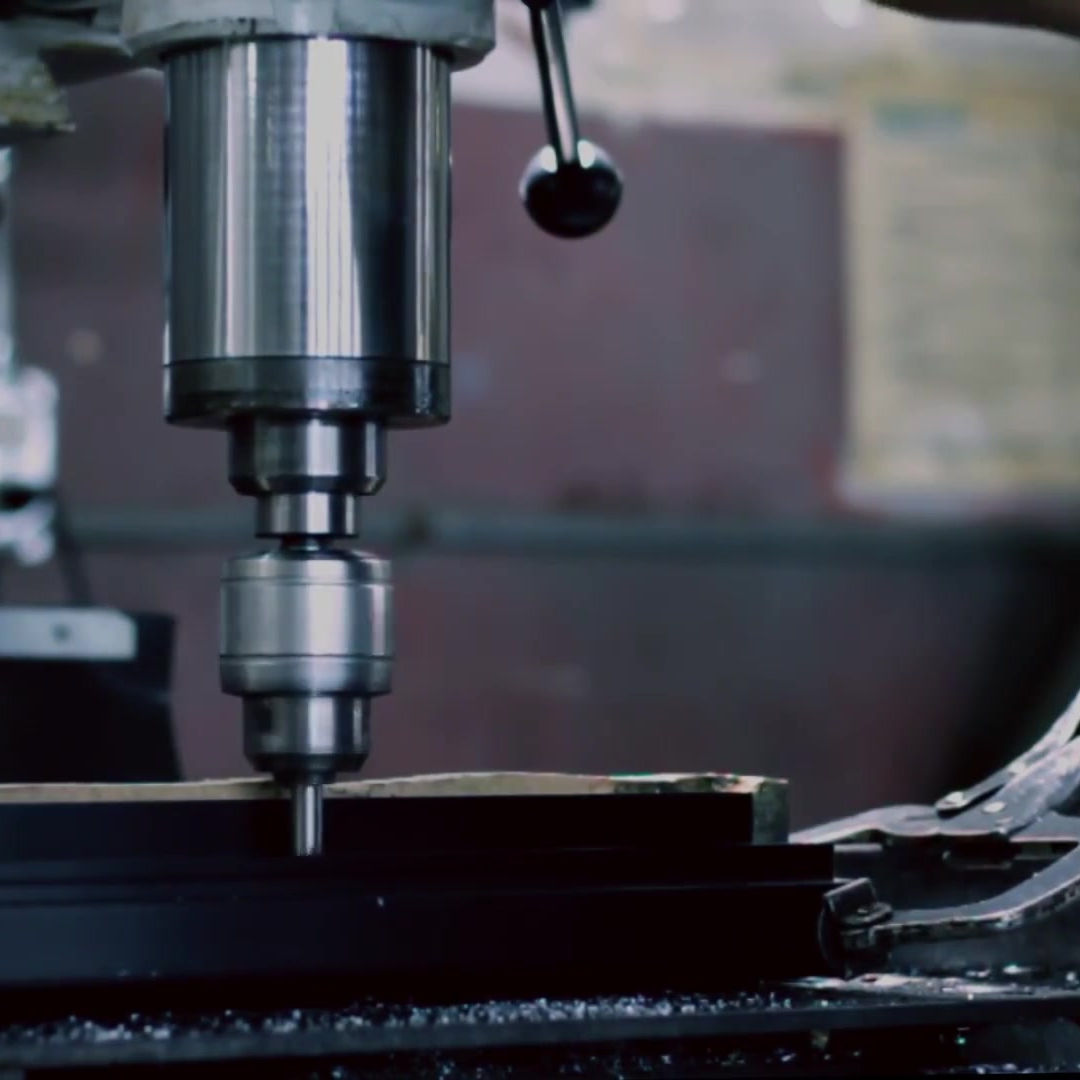
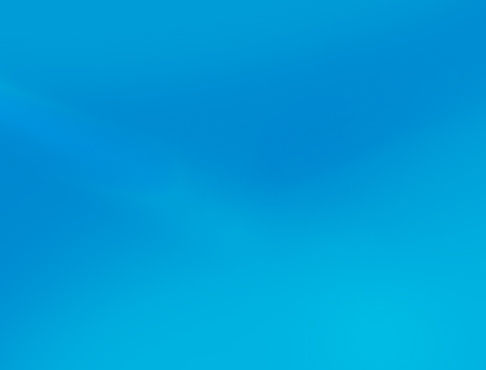
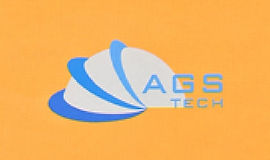
다양한 제품 및 서비스를 위한 글로벌 맞춤형 제조업체, 통합업체, 통합업체, 아웃소싱 파트너.
우리는 맞춤형 제조 및 기성 제품 및 서비스의 제조, 제조, 엔지니어링, 통합, 통합, 아웃소싱을 위한 원스톱 소스입니다.
Choose your Language
-
맞춤형 제조
-
국내 및 글로벌 계약 제조
-
제조 아웃소싱
-
국내 및 글로벌 조달
-
통합
-
엔지니어링 통합
-
엔지니어링 서비스
Search Results
공란으로 164개 검색됨
- Global Product Finder Locator for Off Shelf Products
Global Product Finder Locator for Off Shelf Products AGS-TECH, Inc. 는 귀하의 글로벌 맞춤형 제조업체, 통합업체, 통합업체, 아웃소싱 파트너. 우리는 제조, 제조, 엔지니어링, 통합, 아웃소싱을 위한 원스톱 소스입니다. If you exactly know the product you are searching, please fill out the table below If filling out the form below is not possible or too difficult, we do accept your request by email also. Simply write us at sales@agstech.net Get a Price Quote on a known brand, model, part number....etc. First name Last name Email Phone Product Name Product Make or Brand Please Enter Manufacturer Part Number if Known Please Enter SKU Code if You Know: Your Application for the Product Quantity Needed Do You have a price target ? If so, please let us know: Give us more details if you want: Condition of Product Needed New Used Does Not Matter If you have any, upload product relevant files by clicking at the below link. Don't worry, the link below will pop up a new window for downloading your files. You will not navigate away from this current window. After uploading your files, close ONLY the Dropbox Window, but not this page. Make sure to fill out all spaces and click the submit button below. CLICK HERE TO UPLOAD FILES Request a Quote Thanks! We’ll send you a price quote shortly. PREVIOUS PAGE 우리는 AGS-TECH Inc., 제조 및 제조 및 엔지니어링 및 아웃소싱 및 통합을 위한 원스톱 소스입니다. 우리는 맞춤형 제조, 부분조립, 제품 조립 및 엔지니어링 서비스를 제공하는 세계에서 가장 다양한 엔지니어링 통합업체입니다.
- Custom Made Products Data Entry
Custom Made Products Data Entry, Custom Manufactured Parts, Assemblies, Plastic Molds, Casting, CNC Machining, Extrusion, Metal Forging, Spring Manufacturing, Products Assembly, PCBA, PCB AGS-TECH, Inc. 는 귀하의 글로벌 맞춤형 제조업체, 통합업체, 통합업체, 아웃소싱 파트너. 우리는 제조, 제조, 엔지니어링, 통합, 아웃소싱을 위한 원스톱 소스입니다. Fill In your info if you you need custom design & development & prototyping & mass production: If filling out the form below is not possible or too difficult, we do accept your request by email also. Simply write us at sales@agstech.net Get a Price Quote on a custom designed, developed, prototyped or manufactured product. First name Last name Email Phone Product Name Your Application for the Product Quantity Needed Do you have a price target ? If you do have, please let us know your expected price: Give us more details if you want: Do you accept offshore manufacturing ? YES NO If you have any, upload product relevant files by clicking at the below link. Don't worry, the link below will pop up a new window for downloading your files. You will not navigate away from this current window. After uploading your files, close ONLY the Dropbox Window, but not this page. Make sure to fill out all spaces and click the submit button below. Files that will help us quote your specially tailored product are technical drawings, bill of materials, photos, sketches....etc. You can download more than one file. CLICK HERE TO UPLOAD FILES Request a Quote Thanks! We’ll send you a price quote shortly. PREVIOUS PAGE 우리는 AGS-TECH Inc., 제조 및 제조 및 엔지니어링 및 아웃소싱 및 통합을 위한 원스톱 소스입니다. 우리는 맞춤형 제조, 부분조립, 제품 조립 및 엔지니어링 서비스를 제공하는 세계에서 가장 다양한 엔지니어링 통합업체입니다.
- Coating Thickness Gauge, Surface Roughness Tester, Nondestructive Test
Coating Thickness Gauge - Surface Roughness Tester - Nondestructive Testing - SADT - Mitech - AGS-TECH Inc. - NM - USA 코팅 표면 테스트 기기 코팅 및 표면 평가를 위한 테스트 장비는 다음과 같습니다. 우리의 주요 초점은 on NON-DESTRUCTIVE TEST METHODS입니다. 우리는 SADTand MITECH와 같은 고품질 브랜드를 취급합니다. 우리 주변의 모든 표면의 상당 부분이 코팅되어 있습니다. 코팅은 우수한 외관, 보호 및 제품에 발수성, 향상된 마찰력, 마모 및 내마모성과 같은 원하는 특정 기능을 부여하는 등 다양한 목적을 제공합니다. 따라서 코팅 및 제품 표면의 특성과 품질을 측정, 테스트 및 평가할 수 있는 능력이 매우 중요합니다. 두께를 고려하면 코팅은 크게 두 가지 주요 그룹으로 분류할 수 있습니다. SADT 브랜드 계측 및 테스트 장비 카탈로그를 다운로드하려면 여기를 클릭하십시오. 이 카탈로그에서 표면 및 코팅 평가를 위한 이러한 도구 중 일부를 찾을 수 있습니다. 코팅 두께 측정기 Mitech Model MCT200에 대한 브로셔를 다운로드하려면 여기를 클릭하십시오. 이러한 목적으로 사용되는 도구 및 기술 중 일부는 다음과 같습니다. 코팅 두께 측정기 : 코팅 유형에 따라 다른 유형의 코팅 테스터가 필요합니다. 따라서 다양한 기술에 대한 기본적인 이해는 사용자가 올바른 장비를 선택하는 데 필수적입니다. The Magnetic Induction Method of coating thickness 측정 we 측정 철 기판 위의 비자성 코팅 및 비자성 기판 위의 자기 코팅 프로브를 샘플 위에 놓고 표면과 접촉하는 프로브 팁과 베이스 기판 사이의 선형 거리를 측정합니다. 측정 프로브 내부에는 변화하는 자기장을 생성하는 코일이 있습니다. 프로브가 샘플에 배치되면 이 필드의 자속 밀도는 자성 코팅의 두께 또는 자성 기판의 존재에 의해 변경됩니다. 자기 인덕턴스의 변화는 프로브의 2차 코일에 의해 측정됩니다. 2차 코일의 출력은 마이크로프로세서로 전송되어 디지털 디스플레이에 코팅 두께 측정값으로 표시됩니다. 이 빠른 테스트는 액체 또는 분말 코팅, 강철 또는 철 기판 위의 크롬, 아연, 카드뮴 또는 인산염과 같은 도금에 적합합니다. 0.1mm보다 두꺼운 페인트 또는 분말과 같은 코팅이 이 방법에 적합합니다. 자기 유도 방법은 니켈의 부분 자기 특성으로 인해 강철 코팅 위에 니켈이 적합하지 않습니다. 위상 감지 와전류 방법은 이러한 코팅에 더 적합합니다. 자기 유도 방법이 실패하기 쉬운 또 다른 유형의 코팅은 아연 도금 강판입니다. 프로브는 전체 두께와 동일한 두께를 읽습니다. 최신 모델 기기는 코팅을 통해 기질 물질을 감지하여 자체 교정이 가능합니다. 이것은 물론 베어 기판을 사용할 수 없거나 기판 재료를 알 수 없는 경우에 매우 유용합니다. 그러나 더 저렴한 장비 버전은 코팅되지 않은 노출된 기판에서 기기를 교정해야 합니다. The Eddy Current Methods of coating thickness 측정 measures nonconductive coatings on nonferrous 도전성 기판, 일부 비철금속 전도성 코팅 비철 전도성 기판의 비전도성 코팅 및 비전도성 금속 코팅 코일 및 유사한 프로브를 포함하는 이전에 언급한 자기 유도 방식과 유사합니다. 와전류 방식의 코일은 여자와 측정의 이중 기능을 가지고 있습니다. 이 프로브 코일은 고주파 발진기에 의해 구동되어 교류 고주파 필드를 생성합니다. 금속 도체 근처에 배치하면 도체에 와전류가 생성됩니다. 프로브 코일에서 임피던스 변경이 발생합니다. 프로브 코일과 전도성 기판 재료 사이의 거리는 임피던스 변화의 양을 결정하며, 이는 측정될 수 있고 코팅 두께와 상관관계가 있으며 디지털 판독값의 형태로 표시됩니다. 적용 분야에는 알루미늄 및 비자성 스테인리스강의 액체 또는 분말 코팅과 알루미늄의 양극 산화 처리가 포함됩니다. 이 방법의 신뢰성은 부품의 형상과 코팅의 두께에 따라 달라집니다. 판독을 수행하기 전에 기질을 알아야 합니다. 와전류 프로브는 알루미늄 기판 위의 강철 및 니켈과 같은 자성 기판 위의 비자성 코팅을 측정하는 데 사용해서는 안 됩니다. 사용자가 자성 또는 비철 전도성 기판 위의 코팅을 측정해야 하는 경우 기판을 자동으로 인식하는 이중 자기 유도/와전류 게이지를 사용하는 것이 가장 좋습니다. 세 번째 방법인 the Coulometric 코팅 두께 측정 방법은 많은 중요한 기능을 가진 파괴 테스트 방법입니다. 자동차 산업에서 이중 니켈 코팅을 측정하는 것은 주요 응용 분야 중 하나입니다. 전기량 측정법에서 금속 코팅의 알려진 크기 영역의 무게는 코팅의 국부적 양극 스트리핑을 통해 결정됩니다. 그런 다음 코팅 두께의 단위 면적당 질량이 계산됩니다. 코팅에 대한 이러한 측정은 특정 코팅을 벗겨내기 위해 특별히 선택된 전해질로 채워진 전기분해 전지를 사용하여 이루어집니다. 테스트 셀에는 일정한 전류가 흐르고 코팅 물질이 양극 역할을 하기 때문에 도금이 벗겨집니다. 전류 밀도와 표면적은 일정하므로 코팅 두께는 코팅을 벗겨내는 데 걸리는 시간에 비례합니다. 이 방법은 전도성 기판의 전기 전도성 코팅을 측정하는 데 매우 유용합니다. Coulometric 방법은 샘플에서 여러 층의 코팅 두께를 결정하는 데 사용할 수도 있습니다. 예를 들어, 니켈과 구리의 두께는 강철 기판에 니켈의 상부 코팅과 중간 구리 코팅이 있는 부품에서 측정할 수 있습니다. 다층 코팅의 또 다른 예는 플라스틱 기판 위의 구리 위의 니켈 위의 크롬입니다. 전기량 테스트 방법은 무작위 샘플 수가 적은 전기도금 설비에서 널리 사용됩니다. 그러나 네 번째 방법은 코팅 두께를 측정하기 위한 the Beta 후방 산란 방법입니다. 베타 방출 동위 원소는 베타 입자로 테스트 샘플을 조사합니다. 베타 입자 빔은 구멍을 통해 코팅된 구성 요소로 향하고 이러한 입자의 일부는 예상대로 코팅에서 구멍을 통해 후방 산란되어 가이거 뮬러 튜브의 얇은 창을 관통합니다. 가이거 뮬러 관의 가스가 이온화되어 관 전극에 순간적인 방전을 일으킵니다. 펄스 형태의 방전이 계산되고 코팅 두께로 변환됩니다. 원자 번호가 높은 물질은 베타 입자를 더 많이 후방 산란시킵니다. 구리를 기질로 하고 40 마이크론 두께의 금 코팅을 한 샘플의 경우 베타 입자는 기질과 코팅 물질 모두에 의해 산란됩니다. 금 코팅 두께가 증가하면 후방 산란율도 증가합니다. 따라서 산란된 입자 비율의 변화는 코팅 두께의 척도입니다. 베타 후방 산란 방법에 적합한 응용 프로그램은 코팅과 기판의 원자 번호가 20% 차이가 나는 응용 프로그램입니다. 여기에는 전자 부품의 금, 은 또는 주석, 공작 기계의 코팅, 배관 설비의 장식 도금, 전자 부품, 세라믹 및 유리의 증착 코팅, 금속 위에 오일 또는 윤활유와 같은 유기 코팅이 포함됩니다. 베타 후방 산란 방법은 더 두꺼운 코팅 및 자기 유도 또는 와전류 방법이 작동하지 않는 기판 및 코팅 조합에 유용합니다. 합금의 변화는 베타 후방 산란 방법에 영향을 미치며 보상을 위해 다양한 동위원소와 다중 보정이 필요할 수 있습니다. 예를 들어 구리 위의 주석/납 또는 인쇄 회로 기판 및 접촉 핀에 잘 알려진 인/청동 위의 주석이 있으며 이러한 경우 합금의 변화는 더 비싼 X선 형광 방법으로 더 잘 측정될 것입니다. X선 형광 코팅 두께 측정법 비접촉 방식으로 매우 얇은 다층 합금 부품 측정 가능 부품이 X선에 노출됩니다. 콜리메이터는 X선을 시험 표본의 정확히 정의된 영역에 초점을 맞춥니다. 이 X-방사선은 시험 표본의 코팅과 기질 재료 모두에서 특징적인 X-선 방출(즉, 형광)을 유발합니다. 이 특징적인 X선 방출은 에너지 분산 검출기로 감지됩니다. 적절한 전자 장치를 사용하여 코팅 재료 또는 기판에서 방출되는 X선만 등록할 수 있습니다. 중간층이 존재할 때 특정 코팅을 선택적으로 감지하는 것도 가능합니다. 이 기술은 인쇄 회로 기판, 보석 및 광학 부품에 널리 사용됩니다. X선 형광은 유기 코팅에 적합하지 않습니다. 측정된 코팅의 두께는 0.5-0.8mils를 초과해서는 안 됩니다. 그러나 베타 후방 산란 방법과 달리 X선 형광은 유사한 원자 번호를 가진 코팅을 측정할 수 있습니다(예: 구리보다 니켈). 이전에 언급했듯이 다양한 합금은 기기의 교정에 영향을 미칩니다. 모재와 코팅의 두께를 분석하는 것은 정밀한 판독을 보장하는 데 중요합니다. 오늘날의 시스템과 소프트웨어 프로그램은 품질을 희생하지 않으면서 여러 번 교정해야 할 필요성을 줄여줍니다. 마지막으로 위에서 언급한 여러 모드에서 작동할 수 있는 게이지가 있다는 점을 언급할 가치가 있습니다. 일부는 사용의 유연성을 위해 분리 가능한 프로브가 있습니다. 이러한 최신 기기의 대부분은 다른 모양의 표면이나 다른 재료에 사용되더라도 공정 제어 및 최소한의 교정 요구 사항을 위한 통계 분석 기능을 제공합니다. SURFACE ROUGHNESS TESTERS : 표면 거칠기는 이상적인 형태에서 표면의 법선 벡터 방향의 편차로 정량화됩니다. 이러한 편차가 크면 표면이 거친 것으로 간주됩니다. 작으면 표면이 매끄러운 것으로 간주됩니다. 표면 거칠기를 측정하고 기록하는 데 SURFACE PROFILOMETERS 라는 상용 기기가 사용됩니다. 일반적으로 사용되는 도구 중 하나는 표면 위의 직선을 따라 이동하는 다이아몬드 스타일러스를 특징으로 합니다. 기록 장비는 표면의 굴곡을 보정하고 거칠기만 표시할 수 있습니다. 표면 거칠기는 a.) 간섭계 및 b.) 광학 현미경, 주사 전자 현미경, 레이저 또는 원자간력 현미경(AFM)을 통해 관찰할 수 있습니다. 현미경 기술은 덜 민감한 기기로 특징을 포착할 수 없는 매우 매끄러운 표면을 이미징하는 데 특히 유용합니다. 입체 사진은 표면의 3D 보기에 유용하며 표면 거칠기를 측정하는 데 사용할 수 있습니다. 3D 표면 측정은 세 가지 방법으로 수행할 수 있습니다. an optical-interference microscope shines는 반사 표면에 대해 빛을 비추고 간섭 무늬 90을 기록합니다. 5cde-3194-bb3b-136bad5cf58d_는 간섭계 기술을 통해 표면을 측정하거나 표면에서 일정한 초점 거리를 유지하기 위해 대물 렌즈를 이동하여 표면을 측정하는 데 사용됩니다. 그러면 렌즈의 움직임이 표면의 척도가 됩니다. 마지막으로 세 번째 방법인 the atomic-force microscope는 원자 규모에서 매우 매끄러운 표면을 측정하는 데 사용됩니다. 즉, 이 장비를 사용하면 표면에 있는 원자도 구별할 수 있습니다. 이 정교하고 비교적 고가의 장비는 시편 표면의 100미크론 제곱 미만의 영역을 스캔합니다. GLOSS METERS, COLOR READERS, COLOR DIFFERENCE METER : A GLOSSMETER 표면의 광택. 광택의 척도는 고정된 강도와 각도의 광선을 표면에 투사하고 동일하지만 반대 각도에서 반사량을 측정하여 얻습니다. 광택계는 페인트, 도자기, 종이, 금속 및 플라스틱 제품 표면과 같은 다양한 재료에 사용됩니다. 광택 측정은 제품의 품질을 보장하는 데 도움이 될 수 있습니다. 우수한 제조 관행은 공정의 일관성을 요구하며 여기에는 일관된 표면 마감 및 외관이 포함됩니다. 광택 측정은 다양한 형상에서 수행됩니다. 이것은 표면 재료에 따라 다릅니다. 예를 들어 금속은 반사 수준이 높기 때문에 확산 산란 및 흡수로 인해 각도 의존성이 더 높은 코팅 및 플라스틱과 같은 비금속에 비해 각도 의존성이 낮습니다. 광원 및 관찰 수신 각도 구성으로 전체 반사 각도의 작은 범위에서 측정할 수 있습니다. 광택계의 측정 결과는 정의된 굴절률을 가진 검정색 유리 표준에서 반사된 빛의 양과 관련이 있습니다. 광택 표준에 대한 비율과 비교하여 시편에 대한 입사광에 대한 반사광의 비율은 광택 단위(GU)로 기록됩니다. 측정 각도는 입사광과 반사광 사이의 각도를 나타냅니다. 대부분의 산업용 코팅에는 세 가지 측정 각도(20°, 60° 및 85°)가 사용됩니다. 각도는 예상 광택 범위를 기반으로 선택되며 측정에 따라 다음 조치가 취해집니다. 광택 범위...........60° 값...........동작 고광택 ............>70 GU........... 측정이 70 GU를 초과하는 경우 측정 정확도를 최적화하기 위해 테스트 설정을 20°로 변경합니다. 중간 광택...........10 - 70 GU 저광택..............<10 GU........... 측정이 10 GU 미만인 경우 측정 정확도를 최적화하기 위해 테스트 설정을 85°로 변경합니다. 60° 단일 각도 기기, 20°와 60°를 결합한 이중 각도 유형 및 20°, 60° 및 85°를 결합한 삼중 각도 유형의 세 가지 유형의 기기가 상업적으로 이용 가능합니다. 다른 재료에는 두 개의 추가 각도가 사용되며, 45° 각도는 세라믹, 필름, 직물 및 양극 산화 알루미늄 측정에 지정되고 측정 각도 75°는 종이 및 인쇄물에 지정됩니다. A COLOR READER or also referred to as COLORIMETER is a device that measures the absorbance of particular wavelengths of light by 특정 솔루션. 색도계는 용질의 농도가 흡광도에 비례한다는 Beer-Lambert 법칙을 적용하여 주어진 용액에서 알려진 용질의 농도를 결정하는 데 가장 일반적으로 사용됩니다. 당사의 휴대용 컬러 리더기는 플라스틱, 페인팅, 도금, 직물, 인쇄, 염색, 버터, 감자튀김, 커피, 구운 제품 및 토마토와 같은 식품에도 사용할 수 있습니다. 색상에 대한 전문 지식이 없는 아마추어도 사용할 수 있습니다. 컬러 리더기의 종류가 많기 때문에 응용 프로그램은 무궁무진합니다. 품질 관리에서 주로 샘플이 사용자가 설정한 색상 허용 범위 내에 있도록 하는 데 사용됩니다. 예를 들어, USDA 승인 지수를 사용하여 가공 토마토 제품의 색상을 측정하고 등급을 매기는 휴대용 토마토 비색계가 있습니다. 또 다른 예로는 산업 표준 측정을 사용하여 전체 생두, 볶은 콩 및 볶은 커피의 색상을 측정하도록 특별히 설계된 휴대용 커피 색도계가 있습니다. Our COLOR DIFFERENCE METERS display 직접 색상 차이 E*ab, L*a*b, CIE_IEh. 표준 편차는 E*ab0.2 이내입니다. 모든 색상에서 작동하며 테스트에 몇 초밖에 걸리지 않습니다. METALLURGICAL MICROSCOPES and INVERTED METALLOGRAPHIC MICROSCOPE : Metallurgical microscope is usually an optical microscope, but differs from others in the method of the specimen illumination. 금속은 불투명한 물질이므로 전면 조명으로 조명해야 합니다. 따라서 광원은 현미경 튜브 내에 있습니다. 튜브에는 일반 유리 반사경이 설치되어 있습니다. 금속 현미경의 일반적인 배율은 x50 – x1000 범위입니다. 명시야 조명은 밝은 배경과 기공, 가장자리 및 에칭된 입자 경계와 같은 어두운 비평면 구조 특징을 가진 이미지를 생성하는 데 사용됩니다. 암시야 조명은 어두운 배경과 기공, 가장자리 및 에칭된 입자 경계와 같은 밝고 평평하지 않은 구조 특징이 있는 이미지를 생성하는 데 사용됩니다. 편광은 교차편광에 반응하여 마그네슘, 알파-티타늄, 아연과 같은 비입방 결정 구조의 금속을 관찰하는 데 사용됩니다. 편광된 빛은 조명기와 분석기 앞에 위치하고 접안 렌즈 앞에 놓인 편광판에 의해 생성됩니다. 및 상단 Nomarsky 프리즘은 명시야에서 볼 수 없는 특징을 관찰할 수 있게 하는 차동 간섭 대비 시스템에 사용됩니다. , 무대 위는 아래를 가리키고 목표와 포탑은 무대 아래를 가리키고 있습니다. 도립 현미경은 기존 현미경의 경우와 같이 유리 슬라이드보다 더 자연스러운 조건에서 큰 용기 바닥의 특징을 관찰하는 데 유용합니다. 도립현미경은 연마된 샘플을 스테이지 상단에 놓고 반사 대물렌즈를 사용하여 아래에서 볼 수 있는 야금 응용 분야와 조작 장치 및 장치가 보유하는 미세 도구를 위해 시편 위의 공간이 필요한 미세 조작 응용 분야에 사용됩니다. 다음은 표면 및 코팅 평가를 위한 일부 테스트 장비에 대한 간략한 요약입니다. 위에 제공된 제품 카탈로그 링크에서 이에 대한 세부 정보를 다운로드할 수 있습니다. 표면 거칠기 시험기 SADT RoughScan : 이것은 디지털 판독값에 표시된 측정값으로 표면 거칠기를 확인하기 위한 휴대용 배터리 전원식 기기입니다. 이 기기는 사용하기 쉽고 실험실, 제조 환경, 상점 및 표면 거칠기 테스트가 필요한 모든 곳에서 사용할 수 있습니다. SADT GT 시리즈 광택계 : GT 시리즈 광택계는 국제 표준 ISO2813, ASTMD523 및 DIN67530에 따라 설계 및 제조되었습니다. 기술적인 매개변수는 JJG696-2002를 따릅니다. GT45 광택계는 플라스틱 필름 및 세라믹, 작은 면적 및 곡면 측정을 위해 특별히 설계되었습니다. SADT GMS/GM60 시리즈 광택계 : 이 광택계는 국제 표준 ISO2813, ISO7668, ASTM D523, ASTM D2457에 따라 설계 및 제조되었습니다. 기술적인 매개변수는 또한 JJG696-2002를 따릅니다. 당사의 GM 시리즈 광택계는 페인팅, 코팅, 플라스틱, 세라믹, 가죽 제품, 종이, 인쇄물, 바닥재 등을 측정하는 데 적합합니다. 매력적이고 사용자 친화적인 디자인, 3각 광택 데이터가 동시에 표시됨, 측정 데이터를 위한 대용량 메모리, 데이터를 편리하게 전송하기 위한 최신 블루투스 기능 및 착탈식 메모리 카드, 데이터 출력을 분석하기 위한 특수 광택 소프트웨어, 배터리 부족 및 메모리 가득 참 지시자. 내부 블루투스 모듈과 USB 인터페이스를 통해 GM 광택계는 데이터를 PC로 전송하거나 인쇄 인터페이스를 통해 프린터로 내보낼 수 있습니다. 옵션인 SD 카드를 사용하여 메모리를 필요한 만큼 확장할 수 있습니다. 정확한 색상 판독기 SADT SC 80 : 이 색상 판독기는 주로 플라스틱, 그림, 도금, 섬유 및 의상, 인쇄물 및 염료 제조 산업에 사용됩니다. 색상 분석을 수행할 수 있습니다. 2.4인치 컬러 스크린과 휴대형 디자인으로 편안한 사용이 가능합니다. 사용자 선택을 위한 3가지 종류의 광원, SCI 및 SCE 모드 전환 및 메타메리즘 분석은 다양한 작업 조건에서 테스트 요구 사항을 충족합니다. 허용오차 설정, 색차값 자동판정, 색편차 기능으로 색에 대한 전문지식이 없어도 쉽게 색을 판단할 수 있습니다. 전문 색상 분석 소프트웨어를 사용하여 색상 데이터 분석을 수행하고 출력 다이어그램에서 색상 차이를 관찰할 수 있습니다. 옵션인 미니 프린터를 사용하면 현장에서 컬러 데이터를 인쇄할 수 있습니다. 휴대용 색차 측정기 SADT SC 20 : 이 휴대용 색차 측정기는 플라스틱 및 인쇄 제품의 품질 관리에 널리 사용됩니다. 색상을 효율적이고 정확하게 캡처하는 데 사용됩니다. 작동하기 쉽고 E*ab, L*a*b, CIE_L*a*b, CIE_L*c*h., E*ab0.2 내의 표준 편차로 색상 차이를 표시하며 USB 확장을 통해 컴퓨터에 연결할 수 있습니다. 소프트웨어에 의한 검사를 위한 인터페이스. Metallurgical Microscope SADT SM500 : 실험실이나 현장에서 금속의 야금학적 평가에 이상적으로 적합한 독립형 휴대용 야금 현미경입니다. 휴대용 디자인과 독특한 마그네틱 스탠드를 갖춘 SM500은 비파괴 검사를 위해 모든 각도, 평면도, 곡률 및 표면 복잡성에서 철 금속 표면에 직접 부착할 수 있습니다. SADT SM500은 또한 디지털 카메라 또는 CCD 이미지 처리 시스템과 함께 사용하여 데이터 전송, 분석, 저장 및 인쇄를 위해 야금 이미지를 PC로 다운로드할 수 있습니다. 기본적으로 현장 샘플 준비, 현미경, 카메라가 있으며 현장에서 AC 전원 공급 장치가 필요하지 않은 휴대용 야금 실험실입니다. LED 조명을 흐리게 하여 빛의 변화가 필요 없는 자연스러운 색상으로 언제 보아도 최상의 영상을 제공합니다. 이 기기에는 작은 샘플용 추가 스탠드, 접안렌즈가 있는 디지털 카메라 어댑터, 인터페이스가 있는 CCD, 접안렌즈 5x/10x/15x/16x, 대물렌즈 4x/5x/20x/25x/40x/100x, 미니 그라인더, 전해 연마기, 휠 헤드 세트, 연마 천 휠, 복제 필름, 필터(녹색, 파란색, 노란색), 전구. 휴대용 야금 현미경 SADT 모델 SM-3 : 이 기기는 특수 자성 베이스를 제공하여 공작물에 단단히 고정되며 대규모 롤 테스트 및 직접 관찰에 적합하며 절단 및 샘플링 필요, LED 조명, 균일한 색온도, 가열 없음, 전후좌우 이동 메커니즘, 검사 포인트 조정에 편리, 디지털 카메라 연결 및 PC에서 직접 녹화 관찰용 어댑터. 옵션 액세서리는 SADT SM500 모델과 유사합니다. 자세한 내용은 위의 링크에서 제품 카탈로그를 다운로드하십시오. 금속 현미경 SADT 모델 XJP-6A : 이 금속 현미경은 모든 종류의 금속 및 합금의 미세 구조를 식별하고 분석하기 위해 공장, 학교, 과학 연구 기관에서 쉽게 사용할 수 있습니다. 금속 재료 테스트, 주물의 품질 검증 및 금속화된 재료의 금속 조직 분석에 이상적인 도구입니다. 도립 금속 현미경 SADT 모델 SM400 : 설계를 통해 금속 샘플의 입자를 검사할 수 있습니다. 생산 라인에 설치가 쉽고 휴대가 간편합니다. SM400은 대학 및 공장에 적합합니다. 디지털 카메라를 삼안 튜브에 부착하기 위한 어댑터도 제공됩니다. 이 모드는 고정 크기의 금속 이미지 인쇄의 MI가 필요합니다. 표준 배율과 60% 이상의 관찰 보기로 컴퓨터 인쇄용 CCD 어댑터를 선택했습니다. 도립 금속 현미경 SADT 모델 SD300M : 무한 초점 광학 장치는 고해상도 이미지를 제공합니다. 장거리 관찰 대물렌즈, 20mm 폭의 시야, 거의 모든 샘플 크기, 무거운 하중을 수용하는 3판 기계식 스테이지로 대형 부품의 비파괴 현미경 검사가 가능합니다. 3판 구조로 현미경의 안정성과 내구성을 제공합니다. 광학 장치는 높은 NA와 긴 시야 거리를 제공하여 밝은 고해상도 이미지를 제공합니다. SD300M의 새로운 광학 코팅은 방진 및 방습 기능을 제공합니다. 자세한 내용 및 기타 유사한 장비는 장비 웹사이트를 방문하십시오. http://www.sourceindustrialsupply.com CLICK Product Finder-Locator Service 이전 페이지
- Chemical Physical Environmental Analyzers, NDT, Nondestructive Testing
Chemical Physical Environmental Analyzers, NDT, Nondestructive Testing, Analytical Balance, Chromatograph, Mass Spectrometer, Gas Analyzer, Moisture Analyzer 화학, 물리, 환경 분석기 The industrial CHEMICAL ANALYZERS we provide are: CHROMATOGRAPHS, MASS SPECTROMETERS, RESIDUAL GAS ANALYZERS, GAS DETECTORS, MOISTURE ANALYZER, DIGITAL GRAIN AND WOOD MOISTURE 미터, 분석 저울 The industrial PYHSICAL ANALYSIS INSTRUMENTS we offer are: SPECTROPHOTOMETERS, POLARIMETER, REFRACTOMETER, LUX METER, 광택계, 색상 판독기, 색차계 , 디지털 레이저 거리 측정기, 레이저 거리 측정기, 초음파 케이블 높이 측정기, 사운드 레벨 측정기, 초음파 거리 측정기, 디지털 초음파 결함 검출기 , 경도시험기 , 야금현미경 , 표면 거칠기 시험기 , 초음파 두께 게이지 , 진동계, 타코미터 . 강조 표시된 제품의 경우 해당 컬러 text above를 클릭하여 관련 페이지를 방문하십시오. CERS ENVIRONMENTAL ANALYZERS we가 제공하는 HRONMENTAL ANALYZERS cc781905-5cde-319 SADT 브랜드 계측 및 테스트 장비 카탈로그를 다운로드하려면 여기를 클릭하십시오. . 여기에서 위에 나열된 장비의 일부 모델을 찾을 수 있습니다. CHROMATOGRAPHY 는 구성 요소를 두 단계 사이에 분리하도록 분배하는 물리적 분리 방법입니다. 하나는 고정상(정지상)이고 다른 하나(이동상)는 정해진 방향으로 이동합니다. 즉, 혼합물의 분리를 위한 실험실 기술을 말합니다. 혼합물은 이동상이라고 하는 유체에 용해되어 고정상이라고 하는 다른 물질을 포함하는 구조를 통해 이동합니다. 혼합물의 다양한 구성 요소는 서로 다른 속도로 이동하여 분리됩니다. 분리는 이동상과 고정상 간의 차등 분할을 기반으로 합니다. 화합물의 분배 계수의 작은 차이는 고정상에 차등 체류를 초래하여 분리를 변화시킵니다. 크로마토그래피는 정제와 같은 고급 용도를 위해 혼합물의 성분을 분리하거나 혼합물에서 분석물(크로마토그래피 중에 분리되는 물질)의 상대적 비율을 측정하는 데 사용할 수 있습니다. 종이 크로마토그래피, 가스 크로마토그래피 및 고성능 액체 크로마토그래피와 같은 여러 크로마토그래피 방법이 있습니다. ANALYTICAL CHROMATOGRAPHY_cc781905-5cde-3194-bb3b-136bad_is5cf58d의 농도를 결정하는 데 사용됩니다. 샘플. 크로마토그램에서 다른 피크 또는 패턴은 분리된 혼합물의 다른 성분에 해당합니다. 최적의 시스템에서 각 신호는 분리된 해당 분석물의 농도에 비례합니다. CHROMATOGRAPH 라는 장비는 정교한 분리를 가능하게 합니다. 다음과 같은 이동상의 물리적 상태에 따라 특수화된 유형이 있습니다. 기체-액체 크로마토그래피(GLC)라고도 하는 기체 크로마토그래피(GC)는 이동상이 기체인 분리 기술입니다. 가스 크로마토그래프에 사용되는 고온은 열에 의해 변성되기 때문에 생화학에서 접하는 고분자량 바이오폴리머 또는 단백질에 적합하지 않습니다. 그러나 이 기술은 석유화학, 환경 모니터링, 화학 연구 및 산업 화학 분야에서 사용하기에 적합합니다. 반면에, 액체 크로마토그래피(LC)는 이동상이 액체인 분리 기술입니다. a MASS SPECTROMETER 는 개별 분자의 특성을 측정하기 위해 이온을 이온으로 변환하여 외부 자기장에 의해 가속 이동합니다. 질량 분석기는 위에서 설명한 크로마토그래프와 다른 분석 기기에 사용됩니다. 일반적인 질량 분석기의 관련 구성 요소는 다음과 같습니다. 이온 소스: 작은 샘플은 일반적으로 전자 손실에 의해 양이온으로 이온화됩니다. 질량 분석기: 이온은 질량과 전하에 따라 분류 및 분리됩니다. 검출기: 분리된 이온을 측정하고 결과를 차트에 표시합니다. 이온은 반응성이 높고 수명이 짧기 때문에 이온의 형성 및 조작은 진공에서 수행되어야 합니다. 이온이 취급될 수 있는 압력은 대략 10-5 내지 10-8 torr이다. 위에 나열된 세 가지 작업은 다른 방식으로 수행할 수 있습니다. 하나의 일반적인 절차에서 이온화는 고에너지 전자 빔에 의해 영향을 받고 이온 분리는 빔의 이온을 가속하고 집중시킨 다음 외부 자기장에 의해 구부러짐으로써 달성됩니다. 그런 다음 이온은 전자적으로 감지되고 결과 정보는 컴퓨터에 저장 및 분석됩니다. 분광계의 핵심은 이온 소스입니다. 여기에서 샘플의 분자는 가열된 필라멘트에서 방출되는 전자에 의해 충격을 받습니다. 이것을 전자원이라고 합니다. 가스 및 휘발성 액체 샘플은 저장소에서 이온 소스로 누출될 수 있으며 비휘발성 고체 및 액체는 직접 도입될 수 있습니다. 전자 충격에 의해 형성된 양이온은 대전된 반발판에 의해 밀려나고(음이온은 그것에 끌림), 이온이 빔으로 통과하는 슬릿이 있는 다른 전극으로 가속됩니다. 이러한 이온 중 일부는 더 작은 양이온과 중성 조각으로 파편화됩니다. 수직 자기장은 반경이 각 이온의 질량에 반비례하는 아크에서 이온 빔을 편향시킵니다. 가벼운 이온은 무거운 이온보다 더 많이 편향됩니다. 자기장의 강도를 변화시킴으로써 다른 질량의 이온이 고진공에서 곡선 튜브의 끝에 고정된 검출기에 점진적으로 집중될 수 있습니다. 질량 스펙트럼은 수직 막대 그래프로 표시되며, 각 막대는 특정 질량 대 전하 비율(m/z)을 갖는 이온을 나타내고 막대의 길이는 이온의 상대적 존재비를 나타냅니다. 가장 강한 이온은 존재비 100으로 지정되며 이를 베이스 피크라고 합니다. 질량 분석기에서 형성되는 대부분의 이온은 단일 전하를 가지므로 m/z 값은 질량 자체와 동일합니다. 최신 질량 분석기는 매우 높은 분해능을 가지며 단일 원자 질량 단위(amu)로 다른 이온을 쉽게 구별할 수 있습니다. A RESIDUAL GAS ANALYZER(RGA) 는 작고 견고한 질량 분석기입니다. 위에서 질량 분석기에 대해 설명했습니다. RGA는 연구실, 표면 과학 설정, 가속기, 주사 현미경과 같은 진공 시스템의 공정 제어 및 오염 모니터링을 위해 설계되었습니다. 사중극자 기술을 활용하는 두 가지 구현이 있습니다. 개방형 이온 소스(OIS) 또는 폐쇄 이온 소스(CIS)를 사용하는 것입니다. RGA는 대부분의 경우 진공의 품질을 모니터링하고 배경 간섭이 없는 상태에서 ppm 미만의 검출 가능성을 갖는 미세한 불순물을 쉽게 검출하는 데 사용됩니다. 이러한 불순물은 (10)Exp -14 Torr 수준까지 측정할 수 있으며, 잔류 가스 분석기는 민감한 현장 헬륨 누출 감지기로도 사용됩니다. 진공 시스템은 공정을 시작하기 전에 낮은 수준의 공기 누출 및 오염 물질에 대한 진공 씰의 무결성과 진공 품질을 확인해야 합니다. 최신 잔류 가스 분석기는 사중극자 프로브, 전자 제어 장치, 데이터 수집 및 분석, 프로브 제어에 사용되는 실시간 Windows 소프트웨어 패키지와 함께 제공됩니다. 일부 소프트웨어는 둘 이상의 RGA가 필요할 때 다중 헤드 작동을 지원합니다. 적은 수의 부품으로 단순한 설계로 가스 방출을 최소화하고 진공 시스템에 불순물이 유입될 가능성을 줄입니다. 자동 정렬 부품을 사용하는 프로브 디자인은 청소 후 쉽게 재조립됩니다. 최신 장치의 LED 표시기는 전자 증배관, 필라멘트, 전자 시스템 및 프로브의 상태에 대한 즉각적인 피드백을 제공합니다. 수명이 길고 쉽게 교체 가능한 필라멘트는 전자 방출에 사용됩니다. 향상된 감도와 더 빠른 스캔 속도를 위해 5 × (10)Exp -14 Torr까지의 부분 압력을 감지하는 전자 증배기가 옵션으로 제공되기도 합니다. 잔류 가스 분석기의 또 다른 매력적인 기능은 내장된 탈기 기능입니다. 전자 충격 탈착을 사용하여 이온 소스를 철저히 세척하여 배경 소음에 대한 이온화 장치의 기여를 크게 줄입니다. 넓은 다이내믹 레인지로 사용자는 크고 작은 가스 농도를 동시에 측정할 수 있습니다. A MOISTURE ANALYZER 건조 공정 후 남은 건조 질량을 미리 칭량한 원물의 적외선 에너지로 결정 습도는 습윤 물질의 무게와 관련하여 계산됩니다. 건조 과정에서 재료의 수분 감소가 디스플레이에 표시됩니다. 수분 분석기는 수분과 건조 질량의 양뿐만 아니라 휘발성 및 고정 물질의 일관성을 높은 정확도로 측정합니다. 수분 분석기의 계량 시스템은 현대 저울의 모든 특성을 가지고 있습니다. 이러한 계측 도구는 페이스트, 목재, 접착 재료, 먼지 등을 분석하기 위해 산업 부문에서 사용됩니다. 제조 및 공정 품질 보증을 위해 미량 수분 측정이 필요한 많은 응용 분야가 있습니다. 플라스틱, 의약품 및 열처리 공정에서 고체의 미량 수분을 제어해야 합니다. 가스 및 액체의 미량 수분도 측정 및 제어해야 합니다. 예로는 건조한 공기, 탄화수소 처리, 순수 반도체 가스, 벌크 순수 가스, 파이프라인의 천연 가스 등이 있습니다. 건조 손실 유형 분석기는 시료 트레이 및 주변 가열 요소가 있는 전자 저울을 통합합니다. 고체의 휘발성 함량이 주로 물인 경우 LOD 기술을 사용하면 수분 함량을 잘 측정할 수 있습니다. 물의 양을 결정하는 정확한 방법은 독일 화학자가 개발한 Karl Fischer 적정입니다. 이 방법은 휘발성 물질을 감지하는 건조 손실과 달리 물만 감지합니다. 그러나 천연 가스의 경우 수분 측정을 위한 특수 방법이 있습니다. 천연 가스는 매우 높은 수준의 고체 및 액체 오염 물질과 다양한 농도의 부식제를 포함하는 독특한 상황을 야기하기 때문입니다. MOISTURE METERS are는 물질 또는 물질의 수분 비율을 측정하기 위한 테스트 장비입니다. 이 정보를 사용하여 다양한 산업 분야의 작업자는 재료가 사용할 준비가 되었는지, 너무 젖었는지 또는 너무 건조한지 판단합니다. 예를 들어, 목재 및 종이 제품은 수분 함량에 매우 민감합니다. 치수 및 무게를 포함한 물리적 특성은 수분 함량의 영향을 많이 받습니다. 중량으로 대량의 목재를 구입하는 경우, 수분 함량을 측정하여 가격을 인상하기 위해 의도적으로 물을 주지 않았는지 확인하는 것이 현명할 것입니다. 일반적으로 두 가지 기본 유형의 수분 측정기를 사용할 수 있습니다. 한 가지 유형은 재료의 수분 함량이 증가함에 따라 점점 더 낮아지는 재료의 전기 저항을 측정합니다. 전기 저항 유형의 수분 측정기를 사용하면 두 개의 전극이 재료에 삽입되고 전기 저항은 장치의 전자 출력에서 수분 함량으로 변환됩니다. 두 번째 유형의 수분 측정기는 재료의 유전 특성에 의존하며 표면 접촉만 필요합니다. The ANALYTICAL BALANCE 는 샘플 및 침전물의 정확한 칭량에 사용되는 정량 분석의 기본 도구입니다. 일반적인 저울은 0.1밀리그램의 질량 차이를 결정할 수 있어야 합니다. 미시 분석에서 저울은 약 1,000배 더 민감해야 합니다. 특수 작업의 경우 더 높은 감도의 저울을 사용할 수 있습니다. 분석 저울의 측정 팬은 문이 있는 투명한 인클로저 내부에 있어 먼지가 쌓이지 않고 실내의 기류가 저울 작동에 영향을 미치지 않습니다. 제품의 변동이나 손실 없이 균형 변동과 1마이크로그램까지의 질량 측정을 방지하는 부드러운 난기류 없는 기류 및 환기가 있습니다. 유용한 용량 전반에 걸쳐 일관된 응답을 유지하려면 샘플이 추가되는 빔의 동일한 면에서 질량을 빼서 균형 빔, 즉 받침점에 일정한 하중을 유지함으로써 달성됩니다. 전자 분석 저울은 실제 질량을 사용하는 대신 측정되는 질량에 대응하는 데 필요한 힘을 측정합니다. 따라서 중력 차이를 보상하기 위해 보정 조정이 이루어져야 합니다. 분석 저울은 전자석을 사용하여 측정 중인 샘플에 대항하는 힘을 생성하고 저울을 달성하는 데 필요한 힘을 측정하여 결과를 출력합니다. SPECTROPHOTOMETRY 는 파장의 함수로서 재료의 반사 또는 투과 특성을 정량적으로 측정한 장비입니다. 목적. 스펙트럼 대역폭(테스트 샘플을 통해 전송할 수 있는 색상 범위), 샘플 투과율, 샘플 흡수의 대수 범위 및 반사율 측정 비율은 분광 광도계에 중요합니다. 이 테스트 장비는 광학 필터, 빔 스플리터, 반사경, 거울 등의 성능을 평가해야 하는 광학 부품 테스트에 널리 사용됩니다. 제약 및 의료 솔루션, 화학 물질, 염료, 색상 등의 투과 및 반사 특성 측정을 포함하여 분광 광도계의 다른 많은 응용 프로그램이 있습니다. 이러한 테스트는 생산의 배치 간 일관성을 보장합니다. 분광 광도계는 제어 또는 보정에 따라 관찰된 파장을 사용한 계산을 통해 대상에 존재하는 물질과 그 양을 결정할 수 있습니다. 다루는 파장 범위는 일반적으로 다양한 제어 및 보정을 사용하여 200nm - 2500nm 사이입니다. 이러한 빛 범위 내에서 관심 파장에 대한 특정 표준을 사용하여 기계에서 보정이 필요합니다. 분광 광도계에는 단일 빔과 이중 빔의 두 가지 주요 유형이 있습니다. 이중 빔 분광 광도계는 기준 샘플을 포함하는 경로와 테스트 샘플을 포함하는 다른 경로의 두 광 경로 사이의 광도를 비교합니다. 반면에 단일 빔 분광 광도계는 테스트 샘플을 삽입하기 전후에 빔의 상대 광도를 측정합니다. 이중 빔 장비의 측정을 비교하는 것이 더 쉽고 안정적이지만 단일 빔 장비는 더 큰 동적 범위를 가질 수 있고 광학적으로 더 간단하고 더 작습니다. 분광 광도계는 사용자가 생산 중 현장 측정을 수행하는 데 도움이 될 수 있는 다른 기기 및 시스템에도 설치할 수 있습니다. 최신 분광 광도계의 일반적인 이벤트 순서는 다음과 같이 요약할 수 있습니다. 먼저 광원이 샘플에 이미징되고 빛의 일부가 샘플에서 투과되거나 반사됩니다. 그런 다음 샘플에서 나온 빛은 빛의 파장을 분리하고 순차적으로 광검출기에 초점을 맞추는 모노크로메이터의 입구 슬릿에 이미징됩니다. 가장 일반적인 분광 광도계는 UV 및 VISIBLE SPECTROPHOTOMETERS 이며 자외선 및 040 nm 범위에서 작동합니다. 그들 중 일부는 근적외선 영역도 포함합니다. 한편, IR SPECTROPHOTOMETERS 는 적외선 영역에서 측정의 기술적 요구 사항으로 인해 더 복잡하고 비용이 많이 듭니다. 적외선 광센서는 더 가치가 있으며 적외선 측정은 또한 거의 모든 것이 특히 약 5m를 초과하는 파장에서 열복사로 IR 광선을 방출하기 때문에 어렵습니다. 유리 및 플라스틱과 같은 다른 유형의 분광 광도계에 사용되는 많은 재료는 적외선을 흡수하여 광학 매체로 적합하지 않습니다. 이상적인 광학 재료는 강하게 흡수하지 않는 브롬화칼륨과 같은 염입니다. A POLARIMETER 광활성 물질을 통해 편광된 빛을 통과시켜 발생하는 회전 각도를 측정합니다. 일부 화학 물질은 광학적으로 활성이며 편광(단방향) 빛은 통과할 때 왼쪽(시계 반대 방향) 또는 오른쪽(시계 방향)으로 회전합니다. 빛이 회전하는 정도를 회전각이라고 합니다. 식품, 음료 및 제약 산업에서 제품 또는 성분 품질을 결정하기 위해 널리 사용되는 응용 분야 중 하나인 농도 및 순도 측정이 이루어집니다. 편광계로 순도를 계산할 수 있는 특정 회전을 표시하는 일부 샘플에는 스테로이드, 항생제, 마약, 비타민, 아미노산, 폴리머, 전분, 설탕이 포함됩니다. 많은 화학 물질은 구별하는 데 사용할 수 있는 고유한 특정 회전을 나타냅니다. Polarimeter는 농도 및 샘플 셀의 길이와 같은 다른 변수가 제어되거나 최소한 알려진 경우 이를 기반으로 미지의 표본을 식별할 수 있습니다. 반면에 샘플의 특정 회전이 이미 알려진 경우 샘플을 포함하는 용액의 농도 및/또는 순도를 계산할 수 있습니다. 자동 편광계는 사용자가 변수에 대한 일부 입력을 입력하면 이를 계산합니다. A REFRACTOMETER 는 굴절률 측정용 광학 테스트 장비입니다. 이 기기는 빛이 구부러지는 정도, 즉 빛이 공기에서 샘플로 이동할 때 굴절되는 정도를 측정하며 일반적으로 샘플의 굴절률을 결정하는 데 사용됩니다. 굴절계에는 다섯 가지 유형이 있습니다. 기존 휴대용 굴절계, 디지털 휴대용 굴절계, 실험실 또는 Abbe 굴절계, 인라인 공정 굴절계, 마지막으로 가스의 굴절률을 측정하기 위한 Rayleigh 굴절계입니다. 굴절계는 광물학, 의학, 수의학, 자동차 산업 등 다양한 분야에서 보석, 혈액 샘플, 자동차 냉각수, 산업용 오일과 같은 다양한 제품을 검사하는 데 널리 사용됩니다. 굴절률은 액체 샘플을 분석하기 위한 광학 매개변수입니다. 굴절률을 알려진 값과 비교하여 시료의 정체를 확인하거나 확인하는 역할을 하고 굴절률을 순수한 물질의 값과 비교하여 시료의 순도를 평가하는 데 도움이 되며 용액에서 용질의 농도를 결정하는 데 도움이 됩니다. 용액의 굴절률을 표준 곡선과 비교함으로써. 굴절계의 유형에 대해 간략히 살펴보겠습니다. TRADITIONAL REFRACTOMETERS 유리 임계각에 의해 투영되는 작은 그림자 선과 굴절 원리의 이점 시편을 작은 덮개판과 측정 프리즘 사이에 놓습니다. 그림자 선이 눈금과 교차하는 지점이 판독값을 나타냅니다. 굴절률이 온도에 따라 달라지기 때문에 자동 온도 보상이 있습니다. DIGITAL HANDHELD REFRACTOMETERS 경량 내수성 테스트 장치 측정 시간은 매우 짧고 2~3초의 범위에 불과합니다. LABORATORY REFRACTOMETERS 는 여러 매개변수를 측정하려는 사용자에게 이상적입니다. 인쇄물을 가져 가라. 실험실 굴절계는 휴대용 굴절계보다 더 넓은 범위와 더 높은 정확도를 제공합니다. 컴퓨터에 연결하여 외부에서 제어할 수 있습니다. INLINE 프로세스 굴절계 원격에서 특정 통계를 원격으로 수집하도록 구성할 수 있습니다. 마이크로프로세서 제어는 이러한 장치를 매우 다재다능하고 시간을 절약하며 경제적으로 만드는 컴퓨터 성능을 제공합니다. 마지막으로, the RAYLEIGH REFRACTOMETER 는 가스의 굴절률을 측정하는 데 사용됩니다. 빛의 품질은 작업장, 공장, 병원, 진료소, 학교, 공공 건물 및 기타 여러 장소에서 매우 중요합니다. 명도). 특수 광학 필터는 사람 눈의 분광 감도와 일치합니다. 광도는 발-촛불 또는 럭스(lx)로 측정되고 보고됩니다. 1럭스는 제곱미터당 1루멘과 같고 1피트 촛불은 제곱피트당 1루멘과 같습니다. 최신 조도계에는 측정값을 기록하기 위한 내부 메모리 또는 데이터 로거, 입사광 각도의 코사인 보정 및 판독값 분석을 위한 소프트웨어가 장착되어 있습니다. UVA 방사선을 측정하기 위한 럭스 미터가 있습니다. 고급 버전 럭스 미터는 CIE를 충족하는 클래스 A 상태, 그래픽 디스플레이, 통계 분석 기능, 최대 300klx의 넓은 측정 범위, 수동 또는 자동 범위 선택, USB 및 기타 출력을 제공합니다. A LASER RANGEFINDER 는 레이저 빔을 사용하여 물체까지의 거리를 측정하는 테스트 장비입니다. 대부분의 레이저 거리 측정기 작동은 비행 시간 원리를 기반으로 합니다. 레이저 펄스가 대상을 향해 좁은 빔으로 전송되고 펄스가 대상에서 반사되어 발신자에게 반환되는 데 걸리는 시간이 측정됩니다. 그러나 이 장비는 고정밀 서브밀리미터 측정에는 적합하지 않습니다. 일부 레이저 거리 측정기는 도플러 효과 기술을 사용하여 물체가 물체의 속도뿐만 아니라 거리계를 향해 또는 멀어지는지 여부를 결정합니다. 레이저 거리 측정기의 정밀도는 레이저 펄스의 상승 또는 하강 시간과 수신기의 속도에 의해 결정됩니다. 매우 날카로운 레이저 펄스와 매우 빠른 감지기를 사용하는 거리 측정기는 몇 밀리미터 내에서 물체까지의 거리를 측정할 수 있습니다. 레이저 빔은 레이저 빔의 발산으로 인해 결국 장거리로 퍼집니다. 또한 공기 중의 기포로 인한 왜곡으로 인해 탁 트인 지형에서 1km 이상의 장거리 및 습하고 안개가 많은 장소에서는 더 짧은 거리에서 물체의 거리를 정확하게 판독하기 어렵습니다. 고급 군용 거리 측정기는 최대 25km의 범위에서 작동하며 쌍안경 또는 단안경과 결합되어 컴퓨터에 무선으로 연결할 수 있습니다. 레이저 거리 측정기는 3D 물체 인식 및 모델링, 그리고 고정밀 스캐닝 기능을 제공하는 ToF 3D 스캐너와 같은 다양한 컴퓨터 비전 관련 분야에 사용됩니다. 단일 개체의 여러 각도에서 검색된 범위 데이터를 사용하여 가능한 한 적은 오류로 완전한 3D 모델을 생성할 수 있습니다. 컴퓨터 비전 애플리케이션에 사용되는 레이저 거리 측정기는 10분의 1밀리미터 이하의 깊이 분해능을 제공합니다. 스포츠, 건설, 산업, 창고 관리와 같은 레이저 거리 측정기의 다른 많은 응용 분야가 있습니다. 최신 레이저 측정 도구에는 방의 면적 및 부피와 같은 간단한 계산을 수행하고 영국식 단위와 미터법 단위를 전환하는 기능과 같은 기능이 포함되어 있습니다. An ULTRASONIC DISTANCE METER 는 레이저 거리 측정기와 유사한 원리로 작동하지만, 사람의 귀에 들리기에는 너무 높은 음높이 대신 소리를 사용합니다. 음속은 초당 약 1/3km에 불과하므로 시간 측정이 더 쉽습니다. 초음파는 레이저 거리 측정기와 동일한 많은 장점, 즉 한 사람과 한 손으로 조작할 수 있는 장점이 있습니다. 대상에 개인적으로 액세스할 필요가 없습니다. 그러나 초음파 거리 측정기는 본질적으로 덜 정확합니다. 왜냐하면 소리는 레이저 빛보다 초점을 맞추기가 훨씬 더 어렵기 때문입니다. 정확도는 일반적으로 몇 센티미터 또는 그보다 더 나쁜 반면 레이저 거리 측정기의 경우 몇 밀리미터입니다. 초음파는 대상으로 크고 부드럽고 평평한 표면이 필요합니다. 이것은 심각한 제한 사항입니다. 좁은 파이프나 이와 유사한 작은 대상은 측정할 수 없습니다. 초음파 신호는 미터에서 원뿔 모양으로 퍼지며 방해가 되는 물체는 측정을 방해할 수 있습니다. 레이저 조준을 사용하더라도 소리 반사가 감지되는 표면이 레이저 점이 보이는 표면과 동일한지 확신할 수 없습니다. 이로 인해 오류가 발생할 수 있습니다. 범위는 수십 미터로 제한되지만 레이저 거리 측정기는 수백 미터를 측정할 수 있습니다. 이러한 모든 제한 사항에도 불구하고 초음파 거리 측정기는 훨씬 저렴합니다. Handheld ULTRASONIC CABLE HEIGHT METER is는 케이블 처짐, 케이블 높이 및 지상까지의 오버헤드 간극을 측정하기 위한 테스트 장비입니다. 그것은 케이블 접촉과 무거운 유리 섬유 기둥의 사용을 제거하기 때문에 케이블 높이 측정에 가장 안전한 방법입니다. 케이블 높이 측정기는 다른 초음파 거리 측정기와 마찬가지로 대상에 초음파를 보내고 반향 시간을 측정하고 음속을 기준으로 거리를 계산하고 기온에 따라 자체적으로 조정하는 1인 간단한 조작 장치입니다. A SOUND LEVEL METER 는 음압 레벨을 측정하는 시험기입니다. 소음 측정기는 다양한 종류의 소음을 정량화하기 위한 소음 공해 연구에 유용합니다. 소음 공해 측정은 건설, 항공 우주 및 기타 여러 산업에서 중요합니다. ANSI(American National Standards Institute)는 소음계를 0, 1 및 2의 세 가지 유형으로 지정합니다. 관련 ANSI 표준은 세 가지 정밀도 수준에 따라 성능 및 정확도 허용 오차를 설정합니다. 유형 0은 실험실에서 사용하고 유형 1은 현장의 정밀 측정에 사용되며 Type 2는 범용 측정에 사용됩니다. 규정 준수를 위해 ANSI 유형 2 소음계 및 선량계를 사용한 판독값은 정확도가 ±2dBA인 반면 유형 1 기기는 정확도가 ±1dBA인 것으로 간주됩니다. 유형 2 미터는 소음 측정을 위한 OSHA의 최소 요구 사항이며 일반적으로 범용 소음 조사에 충분합니다. 보다 정확한 유형 1 미터는 비용 효율적인 소음 제어 설계를 위한 것입니다. 주파수 가중치, 최대 음압 레벨...등과 관련된 국제 산업 표준은 관련된 세부 사항으로 인해 여기에서 범위를 벗어납니다. 특정 소음계를 구매하기 전에 작업장에서 요구하는 표준 준수 사항을 확인하고 특정 모델의 테스트 장비를 구매할 때 올바른 결정을 내리는 것이 좋습니다. ENVIRONMENTAL ANALYZERS like TEMPERATURE & HUMIDITY CYCLING CHAMBERS, ENVIRONMENTAL TESTING CHAMBERS come in a variety of sizes, configurations and functions depending on the area of application, 특정 산업 표준 준수가 필요하고 최종 사용자가 필요로 합니다. 사용자 정의 요구 사항에 따라 구성 및 제조할 수 있습니다. MIL-STD, SAE, ASTM과 같은 광범위한 테스트 사양이 있어 제품에 가장 적합한 온도 습도 프로파일을 결정하는 데 도움이 됩니다. 온도/습도 테스트는 일반적으로 다음을 위해 수행됩니다. 가속 노화: 정상적인 사용 상태에서 실제 수명을 알 수 없는 경우 제품의 수명을 추정합니다. 가속화된 노화는 제품의 예상 수명보다 상대적으로 짧은 시간 내에 높은 수준의 제어된 온도, 습도 및 압력에 제품을 노출시킵니다. 제품 수명을 확인하기 위해 오랜 시간과 몇 년을 기다리는 대신 이러한 챔버를 사용하여 훨씬 더 짧고 합리적인 시간 내에 이러한 테스트를 사용하여 수명을 결정할 수 있습니다. Accelerated Weathering: 습기, 이슬, 열, UV 등의 노출을 시뮬레이션합니다. 풍화 및 UV 노출은 코팅, 플라스틱, 잉크, 유기 재료, 장치 등을 손상시킵니다. 장기간 UV 노출 시 퇴색, 황변, 균열, 박리, 취성, 인장 강도 손실 및 박리가 발생합니다. 가속 내후성 테스트는 제품이 시간의 테스트를 견딜 수 있는지 여부를 결정하기 위해 설계되었습니다. 열 흡수/노출 열 충격: 급격한 온도 변화를 견딜 수 있는 재료, 부품 및 구성 요소의 능력을 결정하기 위한 것입니다. 열 충격 챔버는 고온 및 저온 영역 사이에서 제품을 빠르게 순환하여 여러 계절 및 수년 동안 자연 또는 산업 환경의 경우와 같이 다중 열 팽창 및 수축의 효과를 확인합니다. 사전 및 사후 컨디셔닝: 재료, 용기, 패키지, 장치 등의 컨디셔닝용 자세한 내용 및 기타 유사한 장비는 장비 웹사이트를 방문하십시오. http://www.sourceindustrialsupply.com CLICK Product Finder-Locator Service 이전 페이지
- Micro Assembly & Packaging - Micromechanical Fasteners - Self Assembly
Micro Assembly & Packaging - Micromechanical Fasteners - Self Assembly - Adhesive Micromechanical Fastening - AGS-TECH Inc. - New Mexico - USA 마이크로 어셈블리 및 패키징 우리는 이미 our MICRO ASSEMBLY 및 PACKAGING 136bad5cf58d_136bad5cf58d_dedccf-microelectronics와 관련된 제품 및 제품을 특별히 요약했습니다.마이크로일렉트로닉스 제조/반도체 제조. 여기서 우리는 기계, 광학, 마이크로 전자, 광전자 및 이들의 조합으로 구성된 하이브리드 시스템을 포함한 모든 종류의 제품에 사용하는 보다 일반적이고 보편적인 마이크로 어셈블리 및 패키징 기술에 집중할 것입니다. 여기에서 논의하는 기술은 더 다재다능하며 더 비정상적이고 비표준적인 응용 프로그램에서 사용되는 것으로 간주될 수 있습니다. 다시 말해서 여기에서 논의된 마이크로 어셈블리 및 패키징 기술은 우리가 "기본적으로" 생각하는 데 도움이 되는 도구입니다. 다음은 당사의 특별한 마이크로 조립 및 포장 방법 중 일부입니다. - 수동 마이크로 조립 및 포장 - 자동화된 마이크로 어셈블리 및 패키징 - 유체 자가조립 등 자가조립 방식 - 진동, 중력 또는 정전기력 등을 이용한 확률론적 마이크로 어셈블리. - 미세 기계식 패스너 사용 - 접착식 미세 기계식 고정 다재다능한 마이크로 어셈블리 및 패키징 기술 중 일부를 더 자세히 살펴보겠습니다. 수동 마이크로 조립 및 포장: 수동 작업은 비용이 많이 들 수 있으며 현미경으로 이러한 소형 부품을 조립하는 것과 관련된 눈의 피로와 손재주 제한으로 인해 작업자에게 비실용적일 수 있는 정밀도 수준이 필요할 수 있습니다. 그러나 소량의 특수 애플리케이션의 경우 수동 마이크로 어셈블리가 가장 좋은 옵션일 수 있습니다. 자동화된 마이크로 어셈블리 시스템의 설계 및 구성이 반드시 필요한 것은 아니기 때문입니다. 자동화된 마이크로 어셈블리 및 포장: 당사의 마이크로 어셈블리 시스템은 어셈블리를 보다 쉽고 비용 효율적으로 만들도록 설계되어 마이크로 머신 기술을 위한 새로운 애플리케이션을 개발할 수 있습니다. 로봇 시스템을 사용하여 마이크론 수준의 장치와 구성 요소를 미세 조립할 수 있습니다. 다음은 자동화된 마이크로 어셈블리 및 패키징 장비 및 기능 중 일부입니다. • 나노미터 위치 분해능을 갖춘 로봇 작업 셀을 포함한 최고 수준의 모션 제어 장비 • 마이크로 어셈블리를 위한 완전 자동화된 CAD 기반 작업 셀 • 다양한 배율 및 피사계 심도(DOF)에서 이미지 처리 루틴을 테스트하기 위해 CAD 도면에서 합성 현미경 이미지를 생성하는 푸리에 광학 방법 • 정밀 마이크로 조립 및 패키징을 위한 마이크로 핀셋, 매니퓰레이터 및 액추에이터의 맞춤형 설계 및 생산 기능 • 레이저 간섭계 • 힘 피드백을 위한 스트레인 게이지 • 서브미크론 허용오차를 가진 부품의 미세 정렬 및 미세 조립을 위한 서보 메커니즘 및 모터를 제어하는 실시간 컴퓨터 비전 • 주사전자현미경(SEM) 및 투과전자현미경(TEM) • 12자유도 나노 매니퓰레이터 당사의 자동화된 마이크로 어셈블리 프로세스는 단일 단계로 여러 포스트 또는 위치에 여러 기어 또는 기타 구성요소를 배치할 수 있습니다. 우리의 미세 조작 능력은 엄청납니다. 우리는 표준이 아닌 특별한 아이디어로 당신을 돕기 위해 여기 있습니다. 마이크로 및 나노 자가 조립 방법: 자가 조립 프로세스에서 기존 구성 요소의 무질서한 시스템은 외부 방향 없이 구성 요소 간의 특정 국부적 상호 작용의 결과로 조직화된 구조 또는 패턴을 형성합니다. 자체 조립 구성 요소는 로컬 상호 작용만 경험하고 일반적으로 결합 방법을 제어하는 간단한 규칙 집합을 따릅니다. 이 현상은 규모와 무관하고 거의 모든 규모의 자체 구성 및 제조 시스템에 사용할 수 있지만 우리는 마이크로 자체 조립 및 나노 자체 조립에 중점을 둡니다. 미세한 장치를 만드는 데 있어 가장 유망한 아이디어 중 하나는 자가 조립 과정을 이용하는 것입니다. 복잡한 구조는 자연 환경에서 빌딩 블록을 결합하여 만들 수 있습니다. 예를 들어, 단일 기판에 여러 배치의 마이크로 구성요소를 마이크로 어셈블리하는 방법이 설정되었습니다. 기질은 소수성 코팅된 금 결합 부위로 준비됩니다. 마이크로 어셈블리를 수행하기 위해 탄화수소 오일이 기판에 도포되고 물에서 소수성 결합 부위만 적십니다. 그런 다음 마이크로 구성 요소를 물에 추가하고 기름에 젖은 결합 부위에 조립합니다. 더욱이, 전기화학적 방법을 사용하여 특정 기질 결합 부위를 비활성화함으로써 원하는 결합 부위에서 미세 조립이 일어나도록 제어할 수 있습니다. 이 기술을 반복적으로 적용하면 서로 다른 배치의 마이크로 부품을 단일 기판에 순차적으로 조립할 수 있습니다. 미세 조립 절차 후 전기 도금을 수행하여 미세 조립 구성 요소의 전기 연결을 설정합니다. 확률적 마이크로 어셈블리: 부품이 동시에 조립되는 병렬 마이크로 어셈블리에는 결정론적 마이크로 어셈블리와 확률론적 마이크로 어셈블리가 있습니다. 결정론적 마이크로 어셈블리에서 부품과 기판의 대상 간의 관계는 미리 알려져 있습니다. 반면에 확률적 마이크로 어셈블리에서 이 관계는 알 수 없거나 무작위입니다. 부품은 일부 원동력에 의해 구동되는 확률적 프로세스에서 자가 조립됩니다. 마이크로 자가 조립이 일어나기 위해서는 결합력이 있어야 하고, 결합이 선택적으로 일어나야 하고, 마이크로 조립 부품이 함께 움직일 수 있어야 합니다. 확률적 마이크로 어셈블리에는 구성 요소에 작용하는 진동, 정전기, 미세 유체 또는 기타 힘이 여러 번 동반됩니다. 확률적 마이크로 어셈블리는 개별 구성 요소의 처리가 더 어려워지기 때문에 빌딩 블록이 더 작을 때 특히 유용합니다. 확률적 자기조립은 자연에서도 관찰될 수 있다. 마이크로 기계식 패스너: 마이크로 스케일에서 나사 및 경첩과 같은 기존 유형의 패스너는 현재의 제조 제약과 큰 마찰력으로 인해 쉽게 작동하지 않습니다. 반면에 마이크로 스냅 패스너는 마이크로 어셈블리 애플리케이션에서 더 쉽게 작동합니다. 마이크로 스냅 패스너는 마이크로 조립 중에 함께 스냅되는 한 쌍의 결합 표면으로 구성된 변형 가능한 장치입니다. 단순하고 선형적인 조립 동작으로 인해 스냅 패스너는 다중 또는 계층 구성 요소가 있는 장치 또는 마이크로 광기계 플러그, 메모리가 있는 센서와 같은 마이크로 조립 작업에서 광범위한 응용 분야를 가지고 있습니다. 다른 마이크로 어셈블리 패스너는 "키 잠금" 조인트와 "인터록" 조인트입니다. 키 잠금 조인트는 한 마이크로 부품의 "키"를 다른 마이크로 부품의 결합 슬롯에 삽입하는 것으로 구성됩니다. 제 위치에 고정은 첫 번째 마이크로 부품을 다른 마이크로 부품으로 변환하여 달성됩니다. 인터록 조인트는 슬릿이 있는 한 마이크로 부품을 슬릿이 있는 다른 마이크로 부품에 수직으로 삽입하여 생성됩니다. 슬릿은 억지 끼워맞춤을 생성하고 일단 미세 부품이 결합되면 영구적입니다. ADHESIVE MICROMECHANICAL FASTENING: 접착식 기계적 고정은 3D 마이크로 장치를 구성하는 데 사용됩니다. 고정 프로세스에는 자체 정렬 메커니즘과 접착 결합이 포함됩니다. 자체 정렬 메커니즘은 접착성 마이크로 어셈블리에 배치되어 위치 정확도를 높입니다. 로봇 마이크로 매니퓰레이터에 결합된 마이크로 프로브가 접착제를 픽업하여 대상 위치에 정확하게 부착합니다. 빛을 경화시키면 접착제가 경화됩니다. 경화된 접착제는 미세 조립 부품을 제자리에 유지하고 강력한 기계적 접합을 제공합니다. 전도성 접착제를 사용하여 안정적인 전기 연결을 얻을 수 있습니다. 접착식 기계적 고정은 간단한 작업만 필요로 하며 자동 미세 조립에서 중요한 안정적인 연결과 높은 위치 정확도를 얻을 수 있습니다. 이 방법의 실현 가능성을 입증하기 위해 3D 회전 광 스위치를 포함하여 많은 3차원 MEMS 장치가 미세 조립되었습니다. CLICK Product Finder-Locator Service 이전 페이지
- Mesomanufacturing,Mesoscale Manufacturing,Miniature Device Fabrication
Mesomanufacturing - Mesoscale Manufacturing - Miniature Device Fabrication - Tiny Motors - AGS-TECH Inc. - New Mexico Mesoscale 제조 / Mesomanufacturing 기존의 생산 기술을 사용하여 우리는 육안으로 볼 수 있는 비교적 크고 "거시적" 구조를 생산합니다. With MESOMANUFACTURING 하지만 우리는 소형 장치용 부품을 생산합니다. 메소제조는 MESOSCALE MANUFACTURING or_cc781905라고도 합니다. 메소제조는 매크로 제조와 마이크로 제조 모두를 겹칩니다. 메조제작의 예로는 보청기, 스텐트, 초소형 모터가 있습니다. 중간 제조의 첫 번째 접근 방식은 거대 제조 프로세스를 축소하는 것입니다. 예를 들어 치수가 수십 밀리미터이고 무게가 1.5W인 모터가 100그램인 작은 선반은 축소가 발생한 중간 제조의 좋은 예입니다. 두 번째 접근 방식은 미세 제조 프로세스를 확장하는 것입니다. 예를 들어 LIGA 프로세스는 확장되어 메소제조의 영역에 들어갈 수 있습니다. 당사의 중간 제조 공정은 실리콘 기반 MEMS 공정과 기존의 소형 기계 가공 사이의 격차를 해소하고 있습니다. Mesoscale 공정은 스테인리스 스틸, 세라믹 및 유리와 같은 기존 재료에서 미크론 크기 기능을 갖는 2차원 및 3차원 부품을 제작할 수 있습니다. 현재 우리가 사용할 수 있는 메소제조 공정에는 집속 이온 빔(FIB) 스퍼터링, 마이크로 밀링, 마이크로 터닝, 엑시머 레이저 절제, 펨토초 레이저 절제 및 마이크로 전자 방전(EDM) 가공이 포함됩니다. 이러한 중간 규모 공정은 절삭 가공 기술(즉, 재료 제거)을 사용하는 반면, LIGA 공정은 적층 중간 규모 공정입니다. 중간 제조 공정은 기능과 성능 사양이 다릅니다. 관심 있는 가공 성능 사양에는 최소 형상 크기, 형상 공차, 형상 위치 정확도, 표면 마감 및 재료 제거율(MRR)이 포함됩니다. 우리는 중간 규모 부품이 필요한 전기 기계 부품을 중간 제조할 수 있는 능력을 보유하고 있습니다. Subtractive mesomanufacturing 공정으로 제작된 mesoscale 부품은 다양한 mesomanufacturing 공정에서 생성되는 다양한 재료와 표면 조건으로 인해 고유한 마찰 특성을 갖습니다. 이러한 빼기 메조스케일 가공 기술은 청결, 조립 및 마찰과 관련된 문제를 야기합니다. 메조 가공 공정 중에 생성되는 메조 스케일 먼지 및 파편 입자 크기가 메조 스케일 기능과 비슷할 수 있기 때문에 청결은 메조 제조에서 매우 중요합니다. 중간 규모 밀링 및 터닝은 구멍을 막을 수 있는 칩과 버를 생성할 수 있습니다. 메조제작 방식에 따라 표면 형태와 표면 마감 조건이 크게 달라집니다. 중규모 부품은 다루기 어렵고 정렬하기가 어렵기 때문에 대부분의 경쟁업체가 극복할 수 없는 조립을 어렵게 만듭니다. 메소제조의 수율은 경쟁사보다 훨씬 높기 때문에 더 나은 가격을 제공할 수 있다는 이점이 있습니다. MESOSCALE 가공 공정: 당사의 주요 메조 제조 기술은 집속 이온 빔(FIB), 마이크로 밀링 및 마이크로 터닝, 레이저 메조 가공, 마이크로 EDM(전기 방전 가공)입니다. FIB(집속 이온 빔), 마이크로 밀링 및 마이크로 터닝을 사용한 메조 제조: FIB는 갈륨 이온 빔 충격에 의해 공작물에서 재료를 스퍼터링합니다. 공작물은 정밀 스테이지 세트에 장착되고 갈륨 소스 아래의 진공 챔버에 배치됩니다. 진공 챔버의 변환 및 회전 단계는 FIB 메소제조를 위해 갈륨 이온 빔에 사용할 수 있는 공작물의 다양한 위치를 만듭니다. 조정 가능한 전기장은 미리 정의된 투영 영역을 덮기 위해 빔을 스캔합니다. 고전압 전위로 인해 갈륨 이온 소스가 가속되어 공작물과 충돌합니다. 충돌은 공작물에서 원자를 제거합니다. FIB 메조 머시닝 프로세스의 결과는 거의 수직면을 생성할 수 있습니다. 우리가 사용할 수 있는 일부 FIB는 5나노미터만큼 작은 빔 직경을 가지므로 FIB를 중간 규모 및 심지어 마이크로 규모의 기계로 만들 수 있습니다. 우리는 고정밀 밀링 머신에 마이크로 밀링 도구를 장착하여 알루미늄 채널을 가공합니다. FIB를 사용하여 우리는 미세 선삭 로드를 제작하기 위해 선반에서 사용할 수 있는 마이크로 터닝 도구를 제작할 수 있습니다. 즉, FIB는 최종 공작물에 직접 메조 머시닝 기능 외에 하드 툴링을 기계가공하는 데 사용할 수 있습니다. 재료 제거 속도가 느리기 때문에 FIB는 큰 형상을 직접 가공하는 데 비실용적입니다. 그러나 경공구는 재료를 인상적인 속도로 제거할 수 있으며 몇 시간의 가공 시간 동안 충분히 내구성이 있습니다. 그럼에도 불구하고 FIB는 실질적인 재료 제거율이 필요하지 않은 복잡한 3차원 형상을 직접 메조 가공하는 데 실용적입니다. 노출 길이와 입사각은 직접 가공된 형상의 형상에 큰 영향을 줄 수 있습니다. 레이저 메조 제조: 엑시머 레이저는 메조 제조에 사용됩니다. 엑시머 레이저는 나노초 펄스의 자외선 펄스로 재료를 가공합니다. 공작물은 정밀 병진 단계에 장착됩니다. 컨트롤러는 고정된 UV 레이저 빔에 대한 작업 조각의 움직임을 조정하고 펄스의 발사를 조정합니다. 마스크 투영 기술을 사용하여 메조 가공 형상을 정의할 수 있습니다. 마스크는 레이저 플루언스가 너무 낮아 마스크를 제거할 수 없는 빔의 확장된 부분에 삽입됩니다. 마스크 형상은 렌즈를 통해 축소되고 작업물에 투영됩니다. 이 접근 방식은 여러 구멍(어레이)을 동시에 가공하는 데 사용할 수 있습니다. 당사의 엑시머 및 YAG 레이저는 12미크론만큼 작은 피처 크기를 갖는 폴리머, 세라믹, 유리 및 금속을 가공하는 데 사용할 수 있습니다. UV 파장(248nm)과 레이저 메조가공/메조 머시닝에서 공작물 사이의 우수한 결합은 수직 채널 벽을 생성합니다. 보다 깨끗한 레이저 메조 가공 방식은 Ti-sapphire 펨토초 레이저를 사용하는 것입니다. 이러한 중간 제조 공정에서 검출 가능한 파편은 나노 크기의 입자입니다. 펨토초 레이저를 사용하여 깊은 1미크론 크기의 피처를 미세 가공할 수 있습니다. 펨토초 레이저 절제 공정은 열적 절제 재료 대신 원자 결합을 끊는다는 점에서 독특합니다. 펨토초 레이저 메조 머시닝/마이크로 머시닝 공정은 더 깨끗하고 미크론이 가능하며 재료에 따라 달라지지 않기 때문에 메조 제조에서 특별한 위치를 차지합니다. Micro-EDM을 이용한 메조제작(Electro-Discharge Machining): 방전가공은 스파크 침식 공정을 통해 재료를 제거합니다. 당사의 마이크로 EDM 기계는 25미크론의 작은 형상을 생산할 수 있습니다. 싱커 및 와이어 마이크로 EDM 기계의 경우 피쳐 크기를 결정하기 위한 두 가지 주요 고려 사항은 전극 크기와 오버범 갭입니다. 직경이 10미크론을 조금 넘고 수 미크론 정도의 오버범(over-bum)이 사용되는 전극이 사용됩니다. 싱커 방전가공기를 위한 복잡한 형상의 전극을 생성하려면 노하우가 필요합니다. 흑연과 구리는 모두 전극 재료로 널리 사용됩니다. 중간 규모 부품에 대한 복잡한 싱커 EDM 전극을 제조하는 한 가지 접근 방식은 LIGA 공정을 사용하는 것입니다. 전극 재료인 구리는 LIGA 몰드에 도금될 수 있습니다. 그런 다음 구리 LIGA 전극을 싱커 EDM 기계에 장착하여 스테인리스 스틸 또는 코바르와 같은 다른 재료로 부품을 메조 제조할 수 있습니다. 모든 작업에 하나의 메조 제조 프로세스가 충분하지 않습니다. 일부 중간 규모 프로세스는 다른 프로세스보다 더 광범위하지만 각 프로세스에는 틈새 시장이 있습니다. 대부분의 경우 기계 구성 요소의 성능을 최적화하기 위해 다양한 재료가 필요하며 스테인리스 스틸과 같은 기존 재료는 오랜 역사를 가지고 있고 수년 동안 매우 잘 특성화되어 왔기 때문에 편안합니다. 메조제작 공정을 통해 우리는 전통적인 재료를 사용할 수 있습니다. 빼기 중간 규모 가공 기술은 재료 기반을 확장합니다. 골링은 메소제조의 일부 재료 조합에서 문제가 될 수 있습니다. 각각의 특정 중간 규모 가공 공정은 표면 거칠기와 형태에 고유한 영향을 미칩니다. 마이크로 밀링 및 마이크로 터닝은 기계적 문제를 일으킬 수 있는 버와 입자를 생성할 수 있습니다. Micro-EDM은 특정 마모 및 마찰 특성을 가질 수 있는 재주조 층을 남길 수 있습니다. 중간 규모 부품 간의 마찰 효과는 제한된 접촉 지점을 가질 수 있으며 표면 접촉 모델에 의해 정확하게 모델링되지 않습니다. 마이크로 EDM과 같은 일부 중간 규모 가공 기술은 여전히 추가 개발이 필요한 펨토초 레이저 메조 가공과 같은 다른 기술과 달리 상당히 성숙했습니다. CLICK Product Finder-Locator Service 이전 페이지
- Camera Systems & Components, Optic Scanner, Optical Readers, CCD
Camera Systems - Components - Optic Scanner - Optical Readers - Imaging System - CCD - Optomechanical Systems - IR Cameras 맞춤형 카메라 시스템 제조 및 조립 AGS-TECH는 다음을 제공합니다. • 카메라 시스템, 카메라 구성 요소 및 맞춤형 카메라 어셈블리 • 맞춤 설계 및 제조된 광학 스캐너, 판독기, 광학 보안 제품 어셈블리. • 이미징 및 비이미징 광학, LED 조명, 광섬유 및 CCD 카메라를 통합하는 정밀 광학, 광기계 및 전기 광학 어셈블리 • 당사의 광학 엔지니어가 개발한 제품은 다음과 같습니다. - 감시 및 보안 애플리케이션을 위한 전방위 잠망경 및 카메라. 360 x 60º 시야각 고해상도 이미지, 스티칭이 필요하지 않습니다. - 내부 공동 광각 비디오 카메라 - 초슬림 직경 0.6mm의 유연한 비디오 내시경. 모든 의료용 비디오 커플러는 표준 내시경 접안렌즈에 적합하며 완전히 밀봉되어 흠뻑 젖을 수 있습니다. 의료용 내시경 및 카메라 시스템을 보려면 다음을 방문하십시오. http://www.agsmedical.com - 반강성 내시경용 비디오 카메라 및 커플러 - Eye-Q 비디오 프로브. 3차원 측정기용 비접촉 줌 비디오 프로브. - ODIN 위성용 광학 분광기 및 IR 이미징 시스템(OSIRIS). 우리 엔지니어들은 비행 장치 조립, 정렬, 통합 및 테스트 작업을 수행했습니다. - NASA 상부대기연구위성(UARS)용 바람영상간섭계(WINDII). 우리 엔지니어들은 조립, 통합 및 테스트에 대한 컨설팅을 진행했습니다. WINDII 성능 및 작동 수명은 설계 목표 및 요구 사항을 훨씬 초과했습니다. 응용 프로그램에 따라 카메라 응용 프로그램에 필요한 치수, 픽셀 수, 해상도, 파장 감도를 결정합니다. 적외선, 가시광선 및 기타 파장에 적합한 시스템을 구축할 수 있습니다. 자세히 알아보려면 지금 문의하십시오. 브로셔 다운로드 디자인 파트너십 프로그램 또한 여기를 클릭하여 기성품에 대한 포괄적인 전기 및 전자 부품 카탈로그를 다운로드하십시오. CLICK Product Finder-Locator Service 이전 페이지
- Electronic Testers, Electrical Properties Testing, Oscilloscope, Pulse
Electronic Testers - Electrical Test Equipment - Electrical Properties Testing - Oscilloscope - Signal Generator - Function Generator - Pulse Generator - Frequency Synthesizer - Multimeter 전자 테스터 전자 테스터라는 용어는 주로 전기 및 전자 부품 및 시스템의 테스트, 검사 및 분석에 사용되는 테스트 장비를 말합니다. 업계에서 가장 인기 있는 제품을 제공합니다. 전원 공급 장치 및 신호 발생 장치: 전원 공급 장치, 신호 발생기, 주파수 합성기, 함수 발생기, 디지털 패턴 발생기, 펄스 발생기, 신호 주입기 미터: 디지털 멀티미터, LCR 미터, EMF 미터, 커패시턴스 미터, 브리지 계측기, 클램프 미터, 가우스미터/테슬라미터/자력계, 접지 저항 미터 분석기: 오실로스코프, 논리 분석기, 스펙트럼 분석기, 프로토콜 분석기, 벡터 신호 분석기, 시간 영역 반사계, 반도체 곡선 추적기, 네트워크 분석기, 위상 역 회전 테스터 자세한 내용 및 기타 유사한 장비는 장비 웹사이트를 방문하십시오. http://www.sourceindustrialsupply.com 업계 전반에 걸쳐 일상적으로 사용되는 이러한 장비에 대해 간략히 살펴보겠습니다. 계측 목적으로 공급하는 전원 공급 장치는 개별, 벤치탑 및 독립형 장치입니다. 조정 가능한 조정 전기 전원 공급 장치는 입력 전압 또는 부하 전류가 변하더라도 출력 값을 조정할 수 있고 출력 전압 또는 전류가 일정하게 유지되기 때문에 가장 널리 사용되는 전원 공급 장치입니다. 절연 전원 공급 장치에는 전원 입력과 전기적으로 독립적인 전원 출력이 있습니다. 전력 변환 방식에 따라 LINEAR 및 SWITCHING POWER SUPPLIES가 있습니다. 선형 전원 공급 장치는 선형 영역에서 작동하는 모든 유효 전력 변환 구성 요소를 사용하여 입력 전원을 직접 처리하는 반면, 스위칭 전원 공급 장치에는 주로 비선형 모드(예: 트랜지스터)에서 작동하는 구성 요소가 있으며 이전에 전력을 AC 또는 DC 펄스로 변환합니다. 처리. 스위칭 전원 공급 장치는 구성 요소가 선형 작동 영역에서 보내는 시간이 더 짧기 때문에 전력 손실이 적기 때문에 일반적으로 선형 공급 장치보다 더 효율적입니다. 애플리케이션에 따라 DC 또는 AC 전원이 사용됩니다. 다른 인기 있는 장치는 전압, 전류 또는 주파수가 RS232 또는 GPIB와 같은 디지털 인터페이스 또는 아날로그 입력을 통해 원격으로 제어될 수 있는 프로그래밍 가능한 전원 공급 장치입니다. 그들 중 다수는 작업을 모니터링하고 제어하기 위한 통합 마이크로컴퓨터를 가지고 있습니다. 이러한 기기는 자동화된 테스트 목적에 필수적입니다. 일부 전자 전원 공급 장치는 과부하 시 전원을 차단하는 대신 전류 제한을 사용합니다. 전자 제한은 일반적으로 실험실 벤치 유형 기기에 사용됩니다. 신호 발생기는 반복 또는 비반복 아날로그 또는 디지털 신호를 생성하는 실험실 및 산업 분야에서 널리 사용되는 또 다른 장비입니다. 또는 FUNCTION GENERATORS, DIGITAL PATTERN GENERATORS 또는 FREQUENCY GENERATORS라고도 합니다. 함수 발생기는 사인파, 스텝 펄스, 사각 및 삼각 파형, 임의 파형과 같은 단순 반복 파형을 생성합니다. 임의 파형 생성기를 사용하여 사용자는 주파수 범위, 정확도 및 출력 레벨의 게시된 제한 내에서 임의 파형을 생성할 수 있습니다. 단순한 파형 세트로 제한되는 함수 발생기와 달리 임의 파형 발생기는 사용자가 다양한 방법으로 소스 파형을 지정할 수 있도록 합니다. RF 및 마이크로파 신호 발생기는 셀룰러 통신, WiFi, GPS, 방송, 위성 통신 및 레이더와 같은 애플리케이션에서 구성 요소, 수신기 및 시스템을 테스트하는 데 사용됩니다. RF 신호 발생기는 일반적으로 몇 kHz에서 6GHz 사이에서 작동하는 반면 마이크로파 신호 발생기는 특수 하드웨어를 사용하여 1MHz 미만에서 최소 20GHz, 심지어 수백 GHz 범위까지 훨씬 더 넓은 주파수 범위 내에서 작동합니다. RF 및 마이크로파 신호 발생기는 아날로그 또는 벡터 신호 발생기로 더 분류할 수 있습니다. AUDIO-FREQUENCY SIGNAL GENERATORS는 오디오 주파수 범위 이상에서 신호를 생성합니다. 오디오 장비의 주파수 응답을 확인하는 전자 연구실 응용 프로그램이 있습니다. 벡터 신호 발생기(디지털 신호 발생기라고도 함)는 디지털 변조 무선 신호를 생성할 수 있습니다. 벡터 신호 생성기는 GSM, W-CDMA(UMTS) 및 Wi-Fi(IEEE 802.11)와 같은 산업 표준을 기반으로 신호를 생성할 수 있습니다. 논리 신호 발생기는 디지털 패턴 발생기라고도 합니다. 이러한 발생기는 논리 유형의 신호, 즉 기존 전압 레벨의 형태로 논리 1 및 0을 생성합니다. 논리 신호 발생기는 디지털 집적 회로 및 임베디드 시스템의 기능 검증 및 테스트를 위한 자극 소스로 사용됩니다. 위에 언급된 장치는 범용입니다. 그러나 사용자 지정 특정 응용 프로그램을 위해 설계된 다른 많은 신호 발생기가 있습니다. 신호 주입기는 회로에서 신호 추적을 위한 매우 유용하고 빠른 문제 해결 도구입니다. 기술자는 라디오 수신기와 같은 장치의 결함 단계를 매우 빠르게 결정할 수 있습니다. 신호 인젝터는 스피커 출력에 적용될 수 있으며 신호가 들리면 회로의 이전 단계로 이동할 수 있습니다. 이 경우 오디오 증폭기이고 주입된 신호가 다시 들리면 신호가 더 이상 들리지 않을 때까지 회로의 단계 위로 신호 주입을 이동할 수 있습니다. 이렇게 하면 문제의 위치를 찾는 데 도움이 됩니다. MULTIMETER는 여러 측정 기능을 하나의 장치에 결합한 전자 측정기입니다. 일반적으로 멀티미터는 전압, 전류 및 저항을 측정합니다. 디지털 및 아날로그 버전 모두 사용할 수 있습니다. 당사는 휴대용 휴대용 멀티미터 장치와 인증된 교정이 포함된 실험실 등급 모델을 제공합니다. 최신 멀티미터는 전압(AC/DC 모두), 볼트, 전류(AC/DC 모두), 암페어, 저항(옴)과 같은 많은 매개변수를 측정할 수 있습니다. 또한 일부 멀티미터는 온도 테스트 프로브를 사용하여 캐패시턴스(패럿), 컨덕턴스(지멘스), 데시벨, 듀티 사이클(퍼센트), 주파수(헤르츠), 인덕턴스(헨리), 온도(섭씨 또는 화씨)를 측정합니다. 일부 멀티미터에는 다음도 포함됩니다. 회로 도통 시 소리, 다이오드(다이오드 접합의 순방향 강하 측정), 트랜지스터(전류 게인 및 기타 매개변수 측정), 배터리 확인 기능, 조도 측정 기능, 산도 및 알칼리도(pH) 측정 기능 및 상대 습도 측정 기능. 최신 멀티미터는 종종 디지털입니다. 최신 디지털 멀티미터에는 종종 계측 및 테스트에서 매우 강력한 도구로 사용할 수 있는 임베디드 컴퓨터가 있습니다. 다음과 같은 기능이 포함됩니다. • 자동 범위 지정, 가장 중요한 숫자가 표시되도록 테스트 중인 수량에 대한 올바른 범위를 선택합니다. •직류 판독의 자동 극성은 적용된 전압이 양수인지 음수인지 보여줍니다. •샘플링 및 홀드, 테스트 중인 회로에서 계측기를 제거한 후 검사를 위해 가장 최근 판독값을 래치합니다. •반도체 접합부의 전압 강하에 대한 전류 제한 테스트. 트랜지스터 테스터를 대체하지는 않지만 디지털 멀티미터의 이 기능은 다이오드 및 트랜지스터 테스트를 용이하게 합니다. • 측정값의 빠른 변화를 더 잘 시각화하기 위해 테스트 중인 수량의 막대 그래프 표현. •저대역폭 오실로스코프. • 자동차 타이밍 및 드웰 신호에 대한 테스트가 포함된 자동차 회로 테스터. • 데이터 수집 기능은 주어진 기간 동안 최대 및 최소 판독값을 기록하고 고정된 간격으로 많은 샘플을 채취합니다. •결합된 LCR 미터. 일부 멀티미터는 컴퓨터와 인터페이스할 수 있지만 일부는 측정값을 저장하고 컴퓨터에 업로드할 수 있습니다. 또 다른 매우 유용한 도구인 LCR METER는 구성 요소의 인덕턴스(L), 커패시턴스(C) 및 저항(R)을 측정하기 위한 계측 기기입니다. 임피던스는 내부적으로 측정되고 디스플레이를 위해 해당 커패시턴스 또는 인덕턴스 값으로 변환됩니다. 테스트 중인 커패시터 또는 인덕터에 임피던스의 상당한 저항성 성분이 없는 경우 판독값은 합리적으로 정확합니다. 고급 LCR 미터는 실제 인덕턴스와 커패시턴스를 측정하고 커패시터의 등가 직렬 저항과 유도성 부품의 Q 계수도 측정합니다. 테스트 중인 장치는 AC 전압 소스에 영향을 받고 미터는 테스트된 장치를 통과하는 전압과 전류를 측정합니다. 전압 대 전류의 비율에서 미터는 임피던스를 결정할 수 있습니다. 전압과 전류 사이의 위상각도 일부 기기에서 측정됩니다. 임피던스와 결합하여 테스트된 장치의 등가 커패시턴스 또는 인덕턴스 및 저항을 계산하고 표시할 수 있습니다. LCR 미터에는 100Hz, 120Hz, 1kHz, 10kHz 및 100kHz의 선택 가능한 테스트 주파수가 있습니다. Benchtop LCR 미터는 일반적으로 100kHz 이상의 선택 가능한 테스트 주파수를 가지고 있습니다. 여기에는 종종 AC 측정 신호에 DC 전압 또는 전류를 중첩할 수 있는 가능성이 포함됩니다. 일부 미터는 이러한 DC 전압 또는 전류를 외부에서 공급할 수 있는 가능성을 제공하지만 다른 장치는 내부적으로 공급합니다. EMF METER는 전자기장(EMF)을 측정하기 위한 테스트 및 계측 기기입니다. 대부분은 전자기 복사 플럭스 밀도(DC 필드) 또는 시간 경과에 따른 전자기장의 변화(AC 필드)를 측정합니다. 1축 및 3축 기기 버전이 있습니다. 단일 축 미터는 3축 미터보다 비용이 적게 들지만 미터가 필드의 한 차원만 측정하기 때문에 테스트를 완료하는 데 더 오래 걸립니다. 측정을 완료하려면 단일 축 EMF 미터를 기울이고 세 축 모두를 켜야 합니다. 반면에 3축 미터는 3개의 축을 모두 동시에 측정하지만 더 비쌉니다. EMF 미터는 전기 배선과 같은 소스에서 발생하는 AC 전자기장을 측정할 수 있는 반면 GAUSSMETERS/TESLAMETERS 또는 MAGNETOMETERS는 직류가 존재하는 소스에서 방출되는 DC 필드를 측정합니다. 대부분의 EMF 미터는 미국 및 유럽 주전원의 주파수에 해당하는 50 및 60Hz 교류 필드를 측정하도록 보정됩니다. 20Hz만큼 낮은 교대 필드를 측정할 수 있는 다른 미터가 있습니다. EMF 측정은 광범위한 주파수에서 광대역으로 수행하거나 관심 주파수 범위만 주파수 선택적으로 모니터링할 수 있습니다. CAPACITANCE METER는 대부분 이산 캐패시터의 캐패시턴스를 측정하는데 사용되는 테스트 장비입니다. 일부 미터는 커패시턴스만 표시하는 반면 다른 미터는 누설, 등가 직렬 저항 및 인덕턴스를 표시합니다. 고급 테스트 장비는 테스트 중인 커패시터를 브리지 회로에 삽입하는 것과 같은 기술을 사용합니다. 브리지의 균형을 맞추기 위해 브리지에 있는 다른 다리의 값을 변경하여 알 수 없는 커패시터의 값을 결정합니다. 이 방법은 더 높은 정밀도를 보장합니다. 브리지는 직렬 저항과 인덕턴스를 측정할 수도 있습니다. 피코패럿에서 패럿까지의 커패시터를 측정할 수 있습니다. 브리지 회로는 누설 전류를 측정하지 않지만 DC 바이어스 전압을 인가하여 누설을 직접 측정할 수 있습니다. 많은 BRIDGE INSTRUMENTS를 컴퓨터에 연결할 수 있으며 데이터 교환을 통해 판독값을 다운로드하거나 브리지를 외부에서 제어할 수 있습니다. 이러한 브리지 장비는 빠르게 진행되는 생산 및 품질 관리 환경에서 테스트 자동화를 위한 go/no go 테스트를 제공합니다. 그러나 또 다른 시험기인 CLAMP METER는 전압계와 클램프형 전류계를 결합한 전기 시험기이다. 클램프 미터의 대부분의 최신 버전은 디지털입니다. 최신 클램프 미터는 디지털 멀티미터의 대부분의 기본 기능을 가지고 있지만 제품에 내장된 변류기 기능이 추가되었습니다. 큰 AC 전류를 전달하는 도체 주위에 계측기의 "턱"을 고정하면 해당 전류는 전력 변압기의 철심과 유사한 턱을 통해 결합되어 미터 입력의 션트를 가로질러 연결된 2차 권선으로 연결됩니다. , 작동 원리는 변압기와 매우 유사합니다. 코어를 감싼 1차 권선 수에 대한 2차 권선 수의 비율로 인해 훨씬 더 적은 전류가 미터 입력에 전달됩니다. 기본은 조가 고정되는 하나의 도체로 표시됩니다. 2차측에 1000개의 권선이 있는 경우 2차측 전류는 1차측에서 흐르는 전류의 1/1000이며, 이 경우 측정되는 도체입니다. 따라서 측정 중인 도체의 1A 전류는 미터 입력에서 0.001A의 전류를 생성합니다. 클램프 미터를 사용하면 2차 권선의 회전 수를 늘려 훨씬 더 큰 전류를 쉽게 측정할 수 있습니다. 대부분의 테스트 장비와 마찬가지로 고급 클램프 미터는 로깅 기능을 제공합니다. 접지 저항 테스터는 접지 전극과 토양 저항을 테스트하는 데 사용됩니다. 장비 요구 사항은 적용 범위에 따라 다릅니다. 최신 클램프 온 접지 테스트 장비는 접지 루프 테스트를 단순화하고 비침습 누설 전류 측정을 가능하게 합니다. 우리가 판매하는 분석기 중에는 의심할 여지 없이 가장 널리 사용되는 장비 중 하나인 오실로스코프가 있습니다. OSCILLOGRAPH라고도 하는 오실로스코프는 일정하게 변화하는 신호 전압을 시간의 함수로 하나 이상의 신호에 대한 2차원 플롯으로 관찰할 수 있는 일종의 전자 테스트 장비입니다. 소리 및 진동과 같은 비전기적 신호도 전압으로 변환되어 오실로스코프에 표시될 수 있습니다. 오실로스코프는 시간에 따른 전기 신호의 변화를 관찰하는 데 사용되며, 전압과 시간은 보정된 눈금에 대해 연속적으로 그래프로 표시되는 모양을 나타냅니다. 파형의 관찰 및 분석은 진폭, 주파수, 시간 간격, 상승 시간 및 왜곡과 같은 속성을 보여줍니다. 오실로스코프는 반복적인 신호가 화면에서 연속적인 형태로 관찰될 수 있도록 조정할 수 있습니다. 많은 오실로스코프에는 단일 이벤트를 계측기에서 캡처하여 비교적 오랜 시간 동안 표시할 수 있는 저장 기능이 있습니다. 이것은 우리가 직접 지각할 수 없는 사건을 너무 빨리 관찰할 수 있게 합니다. 최신 오실로스코프는 가볍고 컴팩트한 휴대용 기기입니다. 현장 서비스 애플리케이션을 위한 소형 배터리 구동 기기도 있습니다. 실험실 등급 오실로스코프는 일반적으로 벤치탑 장치입니다. 오실로스코프와 함께 사용할 수 있는 다양한 프로브와 입력 케이블이 있습니다. 귀하의 응용 프로그램에 사용할 조언이 필요한 경우 당사에 문의하십시오. 두 개의 수직 입력이 있는 오실로스코프를 이중 추적 오실로스코프라고 합니다. 단일 빔 CRT를 사용하여 입력을 다중화하며 일반적으로 한 번에 두 개의 트레이스를 표시할 수 있을 만큼 충분히 빠르게 입력을 전환합니다. 더 많은 트레이스가 있는 오실로스코프도 있습니다. 4개의 입력이 이들 사이에서 공통입니다. 일부 멀티 트레이스 오실로스코프는 외부 트리거 입력을 선택적인 수직 입력으로 사용하고 일부는 최소한의 제어만 가능한 세 번째 및 네 번째 채널을 가지고 있습니다. 최신 오실로스코프에는 전압에 대한 여러 입력이 있으므로 하나의 가변 전압을 다른 전압과 비교하는 데 사용할 수 있습니다. 이것은 예를 들어 다이오드와 같은 구성 요소에 대한 IV 곡선(전류 대 전압 특성)을 그래프로 표시하는 데 사용됩니다. 높은 주파수와 빠른 디지털 신호의 경우 수직 증폭기의 대역폭과 샘플링 속도는 충분히 높아야 합니다. 일반적인 용도의 경우 일반적으로 최소 100MHz의 대역폭이면 충분합니다. 훨씬 낮은 대역폭은 오디오 주파수 애플리케이션에만 충분합니다. 스위핑의 유용한 범위는 적절한 트리거링 및 스위프 지연과 함께 1초에서 100나노초입니다. 안정적인 디스플레이를 위해서는 잘 설계된 안정적인 트리거 회로가 필요합니다. 트리거 회로의 품질은 우수한 오실로스코프의 핵심입니다. 또 다른 주요 선택 기준은 샘플 메모리 깊이와 샘플 속도입니다. 기본 수준의 최신 DSO에는 이제 채널당 1MB 이상의 샘플 메모리가 있습니다. 종종 이 샘플 메모리는 채널 간에 공유되며 때로는 더 낮은 샘플 속도에서만 완전히 사용할 수 있습니다. 가장 높은 샘플 속도에서 메모리는 수십 KB로 제한될 수 있습니다. 최신 '실시간'' 샘플링 속도 DSO는 일반적으로 샘플 속도에서 입력 대역폭의 5-10배를 갖습니다. 따라서 100MHz 대역폭 DSO의 샘플 속도는 500Ms/s - 1Gs/s입니다. 샘플링 속도가 크게 증가하여 1세대 디지털 스코프에 가끔 존재했던 잘못된 신호 표시가 크게 제거되었습니다. 대부분의 최신 오실로스코프는 GPIB, 이더넷, 직렬 포트 및 USB와 같은 하나 이상의 외부 인터페이스 또는 버스를 제공하여 외부 소프트웨어에 의한 원격 기기 제어를 허용합니다. 다음은 다양한 오실로스코프 유형 목록입니다. 음극선 오실로스코프 듀얼 빔 오실로스코프 아날로그 스토리지 오실로스코프 디지털 오실로스코프 혼합 신호 오실로스코프 휴대용 오실로스코프 PC 기반 오실로스코프 논리 분석기는 디지털 시스템 또는 디지털 회로에서 여러 신호를 캡처하고 표시하는 장비입니다. 로직 분석기는 캡처된 데이터를 타이밍 다이어그램, 프로토콜 디코딩, 상태 머신 트레이스, 어셈블리 언어로 변환할 수 있습니다. 로직 분석기는 고급 트리거링 기능을 가지고 있으며 사용자가 디지털 시스템에서 많은 신호 간의 타이밍 관계를 확인해야 할 때 유용합니다. 모듈식 로직 분석기는 섀시 또는 메인프레임과 로직 분석기 모듈로 구성됩니다. 섀시 또는 메인프레임에는 디스플레이, 컨트롤, 제어 컴퓨터 및 데이터 캡처 하드웨어가 설치된 여러 슬롯이 포함됩니다. 각 모듈에는 특정 수의 채널이 있으며 여러 모듈을 결합하여 매우 높은 채널 수를 얻을 수 있습니다. 다수의 모듈을 결합하여 높은 채널 수와 일반적으로 모듈식 로직 분석기의 더 높은 성능을 얻을 수 있는 기능은 모듈식 로직 분석기를 더 비싸게 만듭니다. 최고급 모듈형 로직 분석기의 경우 사용자는 자신의 호스트 PC를 제공하거나 시스템과 호환되는 임베디드 컨트롤러를 구입해야 할 수 있습니다. 휴대용 논리 분석기는 공장에서 설치된 옵션과 함께 모든 것을 단일 패키지로 통합합니다. 일반적으로 모듈식보다 성능이 낮지만 범용 디버깅을 위한 경제적인 계측 도구입니다. PC 기반 논리 분석기에서 하드웨어는 USB 또는 이더넷 연결을 통해 컴퓨터에 연결되고 캡처된 신호를 컴퓨터의 소프트웨어에 전달합니다. 이러한 장치는 개인용 컴퓨터의 기존 키보드, 디스플레이 및 CPU를 사용하기 때문에 일반적으로 훨씬 작고 저렴합니다. 로직 분석기는 디지털 이벤트의 복잡한 시퀀스에서 트리거된 다음 테스트 중인 시스템에서 많은 양의 디지털 데이터를 캡처할 수 있습니다. 오늘날 특수 커넥터가 사용됩니다. 로직 분석기 프로브의 발전으로 여러 공급업체가 지원하는 공통 공간이 생겨 최종 사용자에게 추가 자유를 제공합니다. 소프트 터치; D-Max를 사용 중입니다. 이 프로브는 프로브와 회로 기판 사이에 내구성 있고 안정적인 기계적 및 전기적 연결을 제공합니다. 스펙트럼 분석기는 장비의 전체 주파수 범위 내에서 입력 신호의 크기 대 주파수를 측정합니다. 주요 용도는 신호 스펙트럼의 전력을 측정하는 것입니다. 광학 및 음향 스펙트럼 분석기도 있지만 여기서는 전기 입력 신호를 측정하고 분석하는 전자 분석기에 대해서만 설명합니다. 전기 신호에서 얻은 스펙트럼은 주파수, 전력, 고조파, 대역폭 등에 대한 정보를 제공합니다. 주파수는 수평축에 표시되고 신호 진폭은 수직축에 표시됩니다. 스펙트럼 분석기는 무선 주파수, RF 및 오디오 신호의 주파수 스펙트럼 분석을 위해 전자 산업에서 널리 사용됩니다. 신호의 스펙트럼을 보면 신호의 요소와 이를 생성하는 회로의 성능을 밝힐 수 있습니다. 스펙트럼 분석기는 매우 다양한 측정을 수행할 수 있습니다. 신호의 스펙트럼을 얻는 데 사용되는 방법을 살펴보면 스펙트럼 분석기 유형을 분류할 수 있습니다. - SWEPT-TUNED SPECTRUM ANALYZER는 수퍼헤테로다인 수신기를 사용하여 입력 신호 스펙트럼의 일부(전압 제어 발진기 및 믹서 사용)를 대역 통과 필터의 중심 주파수로 하향 변환합니다. 수퍼헤테로다인 아키텍처에서 전압 제어 발진기는 기기의 전체 주파수 범위를 활용하여 다양한 주파수 범위에서 스위프됩니다. 스위프 튜닝된 스펙트럼 분석기는 라디오 수신기의 후손입니다. 따라서 스위프 튜닝 분석기는 튜닝 필터 분석기(TRF 라디오와 유사) 또는 슈퍼헤테로다인 분석기입니다. 사실, 가장 단순한 형태로 스위프 튜닝 스펙트럼 분석기는 자동으로 튜닝(스윕)되는 주파수 범위를 가진 주파수 선택 전압계로 생각할 수 있습니다. 본질적으로 사인파의 rms 값을 표시하도록 보정된 주파수 선택형 피크 응답 전압계입니다. 스펙트럼 분석기는 복잡한 신호를 구성하는 개별 주파수 성분을 표시할 수 있습니다. 그러나 위상 정보는 제공하지 않고 크기 정보만 제공합니다. 최신 스윕 튜닝 분석기(특히 슈퍼헤테로다인 분석기)는 다양한 측정을 수행할 수 있는 정밀 장치입니다. 그러나 주어진 범위의 모든 주파수를 동시에 평가할 수 없기 때문에 주로 정상 상태 또는 반복적인 신호를 측정하는 데 사용됩니다. 모든 주파수를 동시에 평가하는 기능은 실시간 분석기에서만 가능합니다. - 실시간 스펙트럼 분석기: FFT 스펙트럼 분석기는 파형을 입력 신호의 주파수 스펙트럼 구성 요소로 변환하는 수학적 프로세스인 이산 푸리에 변환(DFT)을 계산합니다. 푸리에 또는 FFT 스펙트럼 분석기는 또 다른 실시간 스펙트럼 분석기 구현입니다. 푸리에 분석기는 디지털 신호 처리를 사용하여 입력 신호를 샘플링하고 주파수 영역으로 변환합니다. 이 변환은 FFT(고속 푸리에 변환)를 사용하여 수행됩니다. FFT는 데이터를 시간 영역에서 주파수 영역으로 변환하는 데 사용되는 수학 알고리즘인 이산 푸리에 변환을 구현한 것입니다. 다른 유형의 실시간 스펙트럼 분석기, 즉 병렬 필터 분석기는 각각 다른 대역 통과 주파수를 갖는 여러 대역 통과 필터를 결합합니다. 각 필터는 항상 입력에 연결된 상태를 유지합니다. 초기 안정화 시간 후 병렬 필터 분석기는 분석기의 측정 범위 내의 모든 신호를 즉시 감지하고 표시할 수 있습니다. 따라서 병렬 필터 분석기는 실시간 신호 분석을 제공합니다. 병렬 필터 분석기는 빠르며 과도 신호 및 시변 신호를 측정합니다. 그러나 병렬 필터 분석기의 주파수 분해능은 대역통과 필터의 폭에 따라 분해능이 결정되기 때문에 대부분의 스위프 튜닝된 분석기보다 훨씬 낮습니다. 넓은 주파수 범위에서 정밀한 분해능을 얻으려면 많은 개별 필터가 필요하므로 비용이 많이 들고 복잡합니다. 이것이 시장에서 가장 단순한 것을 제외하고 대부분의 병렬 필터 분석기가 비싼 이유입니다. - 벡터 신호 분석(VSA): 과거에는 스위프 튜닝 및 슈퍼헤테로다인 스펙트럼 분석기가 오디오에서 마이크로파를 통해 밀리미터 주파수에 이르기까지 광범위한 주파수 범위를 다루었습니다. 또한 DSP(디지털 신호 처리) 집약적 FFT(고속 푸리에 변환) 분석기는 고해상도 스펙트럼 및 네트워크 분석을 제공했지만 아날로그-디지털 변환 및 신호 처리 기술의 한계로 인해 저주파에 제한되었습니다. 오늘날의 광대역, 벡터 변조, 시변 신호는 FFT 분석 및 기타 DSP 기술의 기능을 크게 활용합니다. 벡터 신호 분석기는 슈퍼헤테로다인 기술과 고속 ADC 및 기타 DSP 기술을 결합하여 빠른 고해상도 스펙트럼 측정, 복조 및 고급 시간 영역 분석을 제공합니다. VSA는 통신, 비디오, 방송, 수중 음파 탐지기 및 초음파 이미징 애플리케이션에 사용되는 버스트, 과도 또는 변조 신호와 같은 복잡한 신호를 특성화하는 데 특히 유용합니다. 폼 팩터에 따라 스펙트럼 분석기는 벤치탑, 휴대용, 핸드헬드 및 네트워크로 분류됩니다. 벤치탑 모델은 실험실 환경이나 제조 영역과 같이 스펙트럼 분석기를 AC 전원에 연결할 수 있는 애플리케이션에 유용합니다. 벤치 탑 스펙트럼 분석기는 일반적으로 휴대용 또는 휴대용 버전보다 더 나은 성능과 사양을 제공합니다. 그러나 일반적으로 더 무겁고 냉각용 팬이 여러 개 있습니다. 일부 벤치탑 스펙트럼 분석기는 전원 콘센트에서 멀리 떨어진 곳에서도 사용할 수 있도록 배터리 팩을 옵션으로 제공합니다. 그것들을 휴대용 스펙트럼 분석기라고 합니다. 휴대용 모델은 스펙트럼 분석기를 측정하기 위해 외부로 가져가거나 사용 중에 휴대해야 하는 애플리케이션에 유용합니다. 우수한 휴대용 스펙트럼 분석기는 사용자가 전원 콘센트가 없는 장소에서 작업할 수 있도록 하는 선택적 배터리 전원 작동, 밝은 햇빛, 어둠 또는 먼지가 많은 조건, 가벼운 무게에서도 화면을 읽을 수 있도록 명확하게 볼 수 있는 디스플레이를 제공할 것으로 예상됩니다. 휴대용 스펙트럼 분석기는 스펙트럼 분석기가 매우 가볍고 작아야 하는 응용 분야에 유용합니다. 휴대용 분석기는 더 큰 시스템에 비해 제한된 기능을 제공합니다. 그러나 휴대용 스펙트럼 분석기의 장점은 매우 낮은 전력 소비, 사용자가 야외에서 자유롭게 이동할 수 있는 배터리 전원 작동, 매우 작은 크기 및 가벼운 무게입니다. 마지막으로 NETWORKED SPECTRUM ANALYZERS에는 디스플레이가 포함되어 있지 않으며 지리적으로 분산된 새로운 차원의 스펙트럼 모니터링 및 분석 애플리케이션을 가능하게 하도록 설계되었습니다. 주요 속성은 분석기를 네트워크에 연결하고 네트워크를 통해 이러한 장치를 모니터링하는 기능입니다. 많은 스펙트럼 분석기에 제어용 이더넷 포트가 있지만 일반적으로 효율적인 데이터 전송 메커니즘이 부족하고 분산 방식으로 배포하기에는 너무 부피가 크거나 비용이 많이 듭니다. 이러한 장치의 분산 특성으로 인해 송신기의 지리적 위치, 동적 스펙트럼 액세스를 위한 스펙트럼 모니터링 및 기타 여러 애플리케이션이 가능합니다. 이러한 장치는 분석기 네트워크 전체에서 데이터 캡처를 동기화하고 저렴한 비용으로 네트워크 효율적인 데이터 전송을 가능하게 합니다. 프로토콜 분석기는 통신 채널을 통해 신호 및 데이터 트래픽을 캡처하고 분석하는 데 사용되는 하드웨어 및/또는 소프트웨어를 통합한 도구입니다. 프로토콜 분석기는 주로 성능 측정 및 문제 해결에 사용됩니다. 네트워크에 연결하여 핵심 성과 지표를 계산하여 네트워크를 모니터링하고 문제 해결 활동을 가속화합니다. NETWORK PROTOCOL ANALYZER는 네트워크 관리자 툴킷의 중요한 부분입니다. 네트워크 프로토콜 분석은 네트워크 통신의 상태를 모니터링하는 데 사용됩니다. 네트워크 장치가 특정 방식으로 작동하는 이유를 알아내기 위해 관리자는 프로토콜 분석기를 사용하여 트래픽을 스니핑하고 유선을 통해 전달되는 데이터와 프로토콜을 노출합니다. 네트워크 프로토콜 분석기는 다음을 수행하는 데 사용됩니다. - 해결하기 어려운 문제 해결 - 악성 소프트웨어/맬웨어를 탐지하고 식별합니다. 침입 탐지 시스템 또는 허니팟으로 작업하십시오. - 기준 트래픽 패턴 및 네트워크 활용 메트릭과 같은 정보 수집 - 네트워크에서 제거할 수 있도록 사용하지 않는 프로토콜 식별 - 침투 테스트를 위한 트래픽 생성 - 트래픽 도청(예: 승인되지 않은 인스턴트 메시징 트래픽 또는 무선 액세스 포인트 찾기) 시간 영역 반사계(TDR)는 시간 영역 반사 측정을 사용하여 연선 및 동축 케이블, 커넥터, 인쇄 회로 기판 등과 같은 금속 케이블의 결함을 특성화하고 찾는 장비입니다. 시간 영역 반사계는 도체를 따라 반사를 측정합니다. 이를 측정하기 위해 TDR은 입사 신호를 도체에 전송하고 반사를 확인합니다. 도체의 임피던스가 균일하고 적절하게 종단되면 반사가 없고 나머지 입사 신호는 종단에 의해 맨 끝에서 흡수됩니다. 그러나 어딘가에 임피던스 변화가 있으면 입사 신호의 일부가 소스로 다시 반사됩니다. 반사는 입사 신호와 같은 모양을 갖지만 부호와 크기는 임피던스 레벨의 변화에 따라 달라집니다. 임피던스가 단계적으로 증가하면 반사는 입사 신호와 동일한 부호를 가지며 임피던스가 단계적으로 감소하면 반사는 반대 부호를 갖습니다. 반사는 시간 영역 반사계의 출력/입력에서 측정되고 시간의 함수로 표시됩니다. 또는 신호 전파 속도가 주어진 전송 매체에 대해 거의 일정하기 때문에 디스플레이는 케이블 길이의 함수로 전송 및 반사를 표시할 수 있습니다. TDR은 케이블 임피던스와 길이, 커넥터 및 스플라이스 손실 및 위치를 분석하는 데 사용할 수 있습니다. TDR 임피던스 측정은 설계자가 시스템 상호 연결의 신호 무결성 분석을 수행하고 디지털 시스템 성능을 정확하게 예측할 수 있는 기회를 제공합니다. TDR 측정은 기판 특성화 작업에 널리 사용됩니다. 회로 기판 설계자는 기판 트레이스의 특성 임피던스를 결정하고 기판 구성 요소에 대한 정확한 모델을 계산하며 기판 성능을 보다 정확하게 예측할 수 있습니다. 시간 영역 반사계의 다른 많은 응용 분야가 있습니다. SEMICONDUCTOR CURVE TRACER는 다이오드, 트랜지스터, 사이리스터와 같은 이산 반도체 소자의 특성을 분석하는 테스트 장비입니다. 이 계측기는 오실로스코프를 기반으로 하지만 테스트 중인 장치를 자극하는 데 사용할 수 있는 전압 및 전류 소스도 포함합니다. 테스트 중인 장치의 두 단자에 스위프 전압을 적용하고 각 전압에서 장치가 흐르도록 허용하는 전류의 양을 측정합니다. VI(전압 대 전류)라는 그래프가 오실로스코프 화면에 표시됩니다. 구성에는 인가된 최대 전압, 인가된 전압의 극성(양극과 음극 모두의 자동 인가 포함), 장치와 직렬로 삽입된 저항이 포함됩니다. 다이오드와 같은 2개의 터미널 장치의 경우 장치를 완전히 특성화하는 데 충분합니다. 곡선 추적기는 다이오드의 순방향 전압, 역방향 누설 전류, 역방향 항복 전압 등과 같은 모든 흥미로운 매개변수를 표시할 수 있습니다. 트랜지스터 및 FET와 같은 3단자 장치도 베이스 또는 게이트 단자와 같이 테스트 중인 장치의 제어 단자에 대한 연결을 사용합니다. 트랜지스터 및 기타 전류 기반 장치의 경우 베이스 또는 기타 제어 단자 전류가 단계적입니다. 전계 효과 트랜지스터(FET)의 경우 계단식 전류 대신 계단식 전압이 사용됩니다. 구성된 메인 단자 전압 범위를 통해 전압을 스위핑함으로써 제어 신호의 각 전압 단계에 대해 VI 곡선 그룹이 자동으로 생성됩니다. 이 곡선 그룹을 사용하면 트랜지스터의 이득 또는 사이리스터 또는 TRIAC의 트리거 전압을 매우 쉽게 결정할 수 있습니다. 최신 반도체 곡선 추적기는 직관적인 Windows 기반 사용자 인터페이스, IV, CV 및 펄스 생성, 펄스 IV, 모든 기술에 포함된 응용 프로그램 라이브러리 등과 같은 많은 매력적인 기능을 제공합니다. 위상 회전 테스터/표시기: 이들은 3상 시스템 및 개방/비통전 위상에서 위상 시퀀스를 식별하기 위한 작고 견고한 테스트 장비입니다. 회전 기계, 모터를 설치하고 발전기 출력을 확인하는 데 이상적입니다. 애플리케이션 중에는 적절한 위상 시퀀스 식별, 누락된 와이어 위상 감지, 회전 기계에 대한 적절한 연결 결정, 활성 회로 감지 등이 있습니다. FREQUENCY COUNTER는 주파수를 측정하는 데 사용되는 테스트 장비입니다. 주파수 카운터는 일반적으로 특정 기간 내에 발생하는 이벤트 수를 누적하는 카운터를 사용합니다. 계산할 이벤트가 전자 형식인 경우 계측기에 대한 간단한 인터페이스만 있으면 됩니다. 더 복잡한 신호는 계산에 적합하도록 약간의 조절이 필요할 수 있습니다. 대부분의 주파수 카운터에는 입력에 일종의 증폭기, 필터링 및 성형 회로가 있습니다. 디지털 신호 처리, 감도 제어 및 히스테리시스는 성능을 향상시키는 다른 기술입니다. 본질적으로 전자적이지 않은 다른 유형의 주기적 이벤트는 변환기를 사용하여 변환해야 합니다. RF 주파수 카운터는 저주파 카운터와 동일한 원리로 작동합니다. 오버플로 전에 더 많은 범위가 있습니다. 매우 높은 마이크로파 주파수의 경우 많은 설계에서 고속 프리스케일러를 사용하여 신호 주파수를 일반 디지털 회로가 작동할 수 있는 지점으로 낮춥니다. 마이크로파 주파수 카운터는 최대 거의 100GHz의 주파수를 측정할 수 있습니다. 이러한 고주파수 이상에서 측정할 신호는 믹서에서 국부 발진기의 신호와 결합되어 직접 측정을 위해 충분히 낮은 차이 주파수에서 신호를 생성합니다. 주파수 카운터의 인기 있는 인터페이스는 다른 최신 기기와 유사한 RS232, USB, GPIB 및 이더넷입니다. 측정 결과를 보내는 것 외에도 카운터는 사용자가 정의한 측정 한계를 초과할 때 사용자에게 알릴 수 있습니다. 자세한 내용 및 기타 유사한 장비는 장비 웹사이트를 방문하십시오. http://www.sourceindustrialsupply.com CLICK Product Finder-Locator Service 이전 페이지
- Brazing, Soldering, Welding, Joining Processes, Assembly Services
Brazing - Soldering - Welding - Joining Processes - Assembly Services - Subassemblies - Assemblies - Custom Manufacturing - AGS-TECH Inc. - NM - USA 브레이징 및 납땜 및 용접 우리가 제조에 사용하는 많은 결합 기술 중에서 용접, 브레이징, 납땜, 접착 본딩 및 맞춤형 기계 조립에 특히 중점을 둡니다. 이러한 기술은 밀폐형 조립품의 제조, 첨단 제품 제조 및 특수 밀봉과 같은 응용 분야에서 널리 사용되기 때문입니다. 여기에서는 고급 제품 및 어셈블리의 제조와 관련된 이러한 접합 기술의 보다 전문화된 측면에 집중할 것입니다. 융합 용접: 우리는 열을 사용하여 재료를 녹이고 합칩니다. 열은 전기 또는 고에너지 빔으로 공급됩니다. 우리가 배포하는 융합 용접의 유형은 산소 연료 가스 용접, 아크 용접, 고에너지 빔 용접입니다. SOLID-STATE WELDING: 용융 및 융합 없이 부품을 접합합니다. 우리의 고체 용접 방법은 냉간, 초음파, 저항, 마찰, 폭발 용접 및 확산 접합입니다. BRAZING & SOLDERING: 그들은 용가재를 사용하고 용접보다 낮은 온도에서 작업할 수 있는 이점을 제공하므로 제품의 구조적 손상이 적습니다. 세라믹-금속 피팅, 밀폐 밀봉, 진공 피드스루, 고진공 및 초고진공 및 유체 제어 부품을 생산하는 당사의 브레이징 시설에 대한 정보는 여기에서 확인할 수 있습니다.브레이징 공장 브로셔 ADHESIVE BONDING: 업계에서 사용되는 접착제의 다양성과 응용 분야의 다양성 때문에 이에 대한 전용 페이지가 있습니다. 접착제 본딩에 대한 페이지로 이동하려면 여기를 클릭하십시오. 맞춤형 기계 조립: 우리는 볼트, 나사, 너트, 리벳과 같은 다양한 패스너를 사용합니다. 당사의 패스너는 표준 기성품 패스너에 국한되지 않습니다. 우리는 비표준 재료로 만든 특수 패스너를 설계, 개발 및 제조하므로 특수 응용 분야의 요구 사항을 충족할 수 있습니다. 때로는 전기 또는 열 비전도성이 필요한 반면 때로는 전도성이 필요합니다. 일부 특수 용도의 경우 고객은 제품을 파괴하지 않고는 제거할 수 없는 특수 패스너를 원할 수 있습니다. 끝없는 아이디어와 응용 프로그램이 있습니다. 기성품이 아니라면 신속하게 개발할 수 있습니다. 기계 조립에 대한 페이지로 이동하려면 여기를 클릭하십시오. . 다양한 결합 기술을 더 자세히 살펴보겠습니다. OXYFUEL GAS WELDING(OFW): 우리는 용접 불꽃을 생성하기 위해 산소와 혼합된 연료 가스를 사용합니다. 우리가 아세틸렌을 연료와 산소로 사용할 때 우리는 그것을 옥시아세틸렌 가스 용접이라고 부릅니다. 순산소 가스 연소 과정에서 두 가지 화학 반응이 발생합니다. C2H2 + O2 ------» 2CO + H2 + 열 2CO + H2 + 1.5 O2--------» 2 CO2 + H2O + 열 첫 번째 반응은 생성된 총 열의 약 33%를 생성하면서 아세틸렌을 일산화탄소와 수소로 분해합니다. 위의 두 번째 공정은 전체 열의 약 67%를 생성하면서 수소와 일산화탄소의 추가 연소를 나타냅니다. 화염의 온도는 1533~3573Kelvin입니다. 가스 혼합물의 산소 비율이 중요합니다. 산소 함량이 절반 이상이면 화염이 산화제가됩니다. 이것은 일부 금속에는 바람직하지 않지만 다른 금속에는 바람직합니다. 산화 화염이 바람직한 경우의 예는 구리 기반 합금이 금속 위에 보호층을 형성하기 때문입니다. 한편, 산소 함량이 감소하면 완전 연소가 불가능하여 화염이 환원(침탄) 화염이 된다. 환원 화염의 온도는 더 낮기 때문에 납땜 및 납땜과 같은 공정에 적합합니다. 다른 가스도 잠재적인 연료이지만 아세틸렌에 비해 몇 가지 단점이 있습니다. 때때로 우리는 용가재를 용가재 또는 와이어 형태로 용접부에 공급합니다. 그들 중 일부는 표면의 산화를 지연시켜 용탕을 보호하기 위해 플럭스로 코팅되어 있습니다. 플럭스가 우리에게 제공하는 추가적인 이점은 용접 영역에서 산화물 및 기타 물질을 제거하는 것입니다. 이것은 더 강한 결합으로 이어집니다. 산소 연료 가스 용접의 변형은 PRESSURE GAS WELDING으로, 두 구성 요소가 oxyacetylene 가스 토치를 사용하여 경계면에서 가열되고 경계면이 녹기 시작하면 토치가 물러나고 축 방향 힘이 두 부품을 함께 누르기 위해 적용됩니다. 인터페이스가 굳을 때까지. 아크 용접: 전기 에너지를 사용하여 전극 팁과 용접할 부품 사이에 아크를 생성합니다. 전원 공급 장치는 AC 또는 DC일 수 있으며 전극은 소모성 또는 비소모성입니다. 아크 용접의 열 전달은 다음 방정식으로 표현할 수 있습니다. H / l = 전 VI / v 여기서 H는 입력 열, l은 용접 길이, V와 I는 인가된 전압 및 전류, v는 용접 속도, e는 공정 효율입니다. 효율 "e"가 높을수록 재료를 녹이는 데 사용 가능한 에너지가 더 유리하게 사용됩니다. 열 입력은 다음과 같이 표현할 수도 있습니다. H = ux(볼륨) = ux A xl 여기서 u는 용융에 대한 비에너지, A는 용접부의 단면적, l은 용접 길이입니다. 위의 두 방정식에서 다음을 얻을 수 있습니다. v = 전 VI / 유 A 아크 용접의 변형은 SHIELDED METAL ARC WELDING(SMAW)으로 모든 산업 및 유지보수 용접 공정의 약 50%를 구성합니다. ELECTRIC ARC WELDING(STICK WELDING)은 코팅된 전극의 끝부분을 공작물에 대고 아크를 유지하기에 충분한 거리로 빠르게 빼내는 방식으로 수행됩니다. 전극이 얇고 긴 막대기 때문에 이 과정을 막대기 용접이라고도 합니다. 용접 과정에서 전극의 끝은 아크 주변의 코팅과 모재와 함께 녹습니다. 모재, 전극 금속 및 전극 코팅 물질의 혼합물이 용접 영역에서 응고됩니다. 전극의 코팅은 탈산되고 용접 영역에 차폐 가스를 제공하여 환경의 산소로부터 보호합니다. 따라서 이 공정을 차폐 금속 아크 용접이라고 합니다. 최적의 용접 성능을 위해 50에서 300A 사이의 전류와 일반적으로 10kW 미만의 전력 수준을 사용합니다. 또한 DC 전류의 극성(전류 흐름 방향)도 중요합니다. 공작물이 양극이고 전극이 음극인 직선 극성은 관통이 얕고 간격이 매우 넓은 접합부 때문에 판금 용접에 선호됩니다. 극성이 반대인 경우, 즉 전극이 양극이고 공작물이 음극이면 더 깊은 용접 침투를 얻을 수 있습니다. AC 전류를 사용하면 맥동하는 아크가 있기 때문에 큰 직경의 전극과 최대 전류를 사용하여 두꺼운 부분을 용접할 수 있습니다. SMAW 용접 방법은 3~19mm 두께의 공작물에 적합하며, 다중 패스 기술을 사용하면 그 이상도 가능합니다. 용접부 상부에 형성된 슬래그는 와이어 브러시를 사용하여 제거해야 용접부 부식 및 파손이 발생하지 않습니다. 이것은 물론 차폐 금속 아크 용접 비용을 추가합니다. 그럼에도 불구하고 SMAW는 산업 및 수리 작업에서 가장 널리 사용되는 용접 기술입니다. SUBMERGED ARC WELDING(SAW): 이 공정에서 우리는 석회, 실리카, 칼슘 플로라이드, 망간 산화물… 입상 플럭스는 노즐을 통한 중력 흐름에 의해 용접 영역으로 공급됩니다. 용융된 용접 영역을 덮고 있는 플럭스는 스파크, 흄, 자외선 등으로부터 크게 보호하고 단열재 역할을 하여 열이 공작물 깊숙이 침투하도록 합니다. 융합되지 않은 플럭스는 회수, 처리 및 재사용됩니다. 노출된 코일은 전극으로 사용되며 튜브를 통해 용접 영역으로 공급됩니다. 우리는 300에서 2000A 사이의 전류를 사용합니다. 서브머지드 아크 용접(SAW) 공정은 용접 중 원형 구조물(파이프 등)의 회전이 가능한 경우 수평 및 평면 위치 및 원형 용접으로 제한됩니다. 속도는 5m/min에 도달할 수 있습니다. SAW 공정은 두꺼운 판재에 적합하며 고품질, 강인성, 연성 및 균일한 용접 결과를 제공합니다. 시간당 용착되는 용접재료의 양인 생산성은 SMAW 공정에 비해 4~10배 정도이다. GAS METAL ARC WELDING(GMAW) 또는 METAL INERT GAS WELDING(MIG)이라고도 하는 또 다른 아크 용접 공정은 헬륨, 아르곤, 이산화탄소 등의 외부 가스 공급원에 의해 보호되는 용접 영역을 기반으로 합니다. 전극 금속에 추가적인 탈산제가 존재할 수 있습니다. 소모성 와이어는 노즐을 통해 용접 영역으로 공급됩니다. 봇 철 및 비철 금속을 포함하는 제작은 가스 금속 아크 용접(GMAW)을 사용하여 수행됩니다. 용접 생산성은 SMAW 공정의 약 2배입니다. 자동화 용접 장비를 사용하고 있습니다. 금속은 이 프로세스에서 세 가지 방법 중 하나로 전달됩니다. "분무 전달"에는 전극에서 용접 영역으로 초당 수백 개의 작은 금속 방울이 전달됩니다. 반면에 "Globular Transfer"에서는 이산화탄소가 풍부한 가스가 사용되며 용융 금속의 구체가 전기 아크에 의해 추진됩니다. 용접 전류가 높고 용접 침투가 더 깊으며 용접 속도는 스프레이 전송보다 빠릅니다. 따라서 구형 전송은 더 무거운 섹션을 용접하는 데 더 좋습니다. 마지막으로 "단락" 방법에서는 전극 팁이 용융된 용접 풀에 닿아 50방울/초 이상의 속도로 금속을 단락시켜 개별 방울로 전달됩니다. 더 얇은 와이어와 함께 낮은 전류 및 전압이 사용됩니다. 사용되는 전력은 약 2kW이고 온도가 상대적으로 낮기 때문에 이 방법은 두께가 6mm 미만인 얇은 시트에 적합합니다. FCAW(FLUX-CORED ARC WELDING) 공정의 또 다른 변형은 전극이 플럭스로 채워진 튜브라는 점을 제외하면 가스 금속 아크 용접과 유사합니다. 코어 플럭스 전극을 사용하는 장점은 더 안정적인 아크를 생성하고, 용접 금속의 특성을 개선할 수 있는 기회를 제공하며, SMAW 용접에 비해 플럭스의 덜 부서지고 유연한 특성, 개선된 용접 윤곽을 제공한다는 것입니다. 자체 차폐 코어형 전극에는 대기로부터 용접 영역을 차폐하는 재료가 포함되어 있습니다. 우리는 약 20kW의 전력을 사용합니다. GMAW 공정과 마찬가지로 FCAW 공정도 연속 용접 공정을 자동화할 수 있는 기회를 제공하며 경제적입니다. 다양한 합금을 플럭스 코어에 추가하여 다양한 용접 금속 화학을 개발할 수 있습니다. ELECTROGAS WELDING(EGW)에서는 배치된 조각을 가장자리에서 가장자리로 용접합니다. 때때로 BUTT WELDING이라고도 합니다. 용접 금속은 접합할 두 조각 사이의 용접 캐비티에 넣습니다. 이 공간은 용융 슬래그가 쏟아지는 것을 방지하기 위해 두 개의 수냉식 댐으로 둘러싸여 있습니다. 댐은 기계식 드라이브에 의해 위로 이동됩니다. 공작물이 회전할 수 있는 경우 파이프의 원주 용접에도 전기 가스 용접 기술을 사용할 수 있습니다. 전극은 연속적인 아크를 유지하기 위해 도관을 통해 공급됩니다. 전류는 약 400A 또는 750A이고 전력 수준은 약 20kW입니다. 플럭스 코어 전극 또는 외부 소스에서 발생하는 불활성 가스가 차폐를 제공합니다. 우리는 12mm ~ 75mm 두께의 강철, 티타늄 등의 금속에 전기 가스 용접(EGW)을 사용합니다. 이 기술은 대형 구조물에 적합합니다. 그러나 ESW(ELECTROSLAG WELDING)라고 하는 또 다른 기술에서는 전극과 공작물의 바닥 사이에 아크가 점화되고 플럭스가 추가됩니다. 용융 슬래그가 전극 팁에 도달하면 아크가 소멸됩니다. 용융 슬래그의 전기 저항을 통해 에너지가 지속적으로 공급됩니다. 우리는 두께가 50mm에서 900mm 사이 또는 그 이상인 판을 용접할 수 있습니다. 전류는 약 600A이고 전압은 40~50V입니다. 용접 속도는 약 12~36mm/min입니다. 응용 분야는 전기 가스 용접과 유사합니다. 당사의 비소모성 전극 공정 중 하나인 TIG(텅스텐 불활성 가스 용접)라고도 하는 GTAW(가스 텅스텐 아크 용접)는 와이어를 통한 용가재 공급을 포함합니다. 밀착 조인트의 경우 때때로 용가재를 사용하지 않습니다. TIG 공정에서 우리는 플럭스를 사용하지 않고 차폐를 위해 아르곤과 헬륨을 사용합니다. 텅스텐은 녹는점이 높아 TIG 용접 공정에서 소모되지 않아 아크 갭은 물론 일정한 전류를 유지할 수 있다. 전력 수준은 8 ~ 20kW이고 전류는 200A(DC) 또는 500A(AC)입니다. 알루미늄 및 마그네슘의 경우 산화물 세척 기능을 위해 AC 전류를 사용합니다. 텅스텐 전극의 오염을 피하기 위해 용융 금속과의 접촉을 피합니다. 가스 텅스텐 아크 용접(GTAW)은 얇은 금속을 용접하는 데 특히 유용합니다. GTAW 용접은 우수한 표면 조도와 함께 매우 고품질입니다. 수소 가스의 더 높은 비용으로 인해 덜 자주 사용되는 기술은 원자 수소 용접(AHW)입니다. 여기서 우리는 흐르는 수소 가스의 차폐 분위기에서 두 개의 텅스텐 전극 사이에 아크를 생성합니다. AHW는 또한 비소모성 전극 용접 공정입니다. 이원자 수소 가스 H2는 온도가 6273Kelvin 이상인 용접 아크 근처에서 원자 형태로 분해됩니다. 분해하면서 아크에서 많은 양의 열을 흡수합니다. 수소 원자는 상대적으로 차가운 표면인 용접 영역에 부딪히면 이원자 형태로 재결합하여 저장된 열을 방출합니다. 워크피스를 아크 거리로 변경하여 에너지를 변경할 수 있습니다. 또 다른 비소모성 전극 공정인 PLASMA ARC WELDING(PAW)에서는 용접 영역을 향해 집중된 플라즈마 아크가 있습니다. 온도는 PAW에서 33,273Kelvin에 이릅니다. 거의 같은 수의 전자와 이온이 플라즈마 가스를 구성합니다. 저전류 파일럿 아크는 텅스텐 전극과 오리피스 사이에 있는 플라즈마를 시작합니다. 작동 전류는 일반적으로 약 100A입니다. 용가재가 공급될 수 있다. 플라즈마 아크 용접에서 차폐는 외부 차폐 링과 아르곤 및 헬륨과 같은 가스를 사용하여 수행됩니다. 플라즈마 아크 용접에서 아크는 전극과 공작물 사이 또는 전극과 노즐 사이에 있을 수 있습니다. 이 용접 기술은 더 높은 에너지 집중, 더 깊고 더 좁은 용접 능력, 더 나은 아크 안정성, 최대 1미터/분의 더 빠른 용접 속도, 더 적은 열 변형 등의 다른 방법에 비해 장점이 있습니다. 우리는 일반적으로 두께가 6mm 미만인 경우 플라즈마 아크 용접을 사용하고 알루미늄 및 티타늄의 경우 최대 20mm까지 사용합니다. 고 에너지 빔 용접: 전자 빔 용접(EBW)과 레이저 용접(LBW)을 두 가지 변형으로 사용하는 또 다른 유형의 융합 용접 방법입니다. 이러한 기술은 당사의 하이테크 제품 제조 작업에 특히 가치가 있습니다. 전자빔 용접에서 고속 전자가 공작물에 충돌하고 운동 에너지가 열로 변환됩니다. 좁은 전자빔은 진공 챔버에서 쉽게 이동합니다. 일반적으로 우리는 전자빔 용접에서 고진공을 사용합니다. 두께가 150mm인 판도 용접할 수 있습니다. 차폐 가스, 플럭스 또는 충전재가 필요하지 않습니다. 전자 빔 건의 용량은 100kW입니다. 최대 30의 높은 종횡비와 작은 열 영향 영역을 가진 깊고 좁은 용접이 가능합니다. 용접 속도는 12m/min에 달할 수 있습니다. 레이저 빔 용접에서는 고출력 레이저를 열원으로 사용합니다. 고밀도의 10미크론 정도의 작은 레이저 빔은 공작물에 깊숙이 침투할 수 있습니다. 레이저 빔 용접으로 깊이 대 너비 비율이 10까지 가능합니다. 우리는 펄스 레이저와 연속파 레이저를 모두 사용합니다. 전자는 얇은 재료에 적용하고 후자는 최대 약 25mm의 두꺼운 공작물에 주로 사용합니다. 전력 수준은 최대 100kW입니다. 레이저 빔 용접은 광학적으로 매우 반사적인 재료에는 적합하지 않습니다. 가스는 또한 용접 과정에서 사용될 수 있습니다. 레이저 빔 용접 방법은 자동화 및 대량 생산에 적합하며 2.5m/min ~ 80m/min의 용접 속도를 제공할 수 있습니다. 이 용접 기술이 제공하는 한 가지 주요 이점은 다른 기술을 사용할 수 없는 영역에 접근할 수 있다는 것입니다. 레이저 빔은 이러한 어려운 영역으로 쉽게 이동할 수 있습니다. 전자빔 용접과 같은 진공이 필요하지 않습니다. 레이저 빔 용접으로 우수한 품질 및 강도, 낮은 수축률, 낮은 왜곡, 낮은 다공성의 용접을 얻을 수 있습니다. 레이저 빔은 광섬유 케이블을 사용하여 쉽게 조작하고 모양을 만들 수 있습니다. 따라서 이 기술은 정밀 밀폐 어셈블리, 전자 패키지 등의 용접에 적합합니다. 솔리드 스테이트 용접 기술을 살펴보겠습니다. 냉간 용접(CW)은 접합되는 부품에 다이 또는 롤을 사용하여 열 대신 압력을 가하는 공정입니다. 냉간 용접에서 결합 부품 중 적어도 하나는 연성이 있어야 합니다. 두 개의 유사한 재료로 최상의 결과를 얻을 수 있습니다. 냉간 용접으로 접합할 두 금속이 서로 다른 경우 접합부가 약하고 부서지기 쉽습니다. 냉간 용접 방법은 전기 연결부, 열에 민감한 용기 가장자리, 온도 조절기용 바이메탈 스트립 등과 같은 부드럽고 연성이 있으며 작은 공작물에 매우 적합합니다. 냉간 용접의 한 변형은 한 쌍의 롤을 통해 압력이 가해지는 롤 본딩(또는 롤 용접)입니다. 때때로 우리는 더 나은 계면 강도를 위해 고온에서 롤 용접을 수행합니다. 우리가 사용하는 또 다른 고체 상태 용접 공정은 초음파 용접(USW)으로, 여기서 공작물은 정적 수직력과 진동 전단 응력을 받습니다. 진동 전단 응력은 변환기의 끝 부분을 통해 적용됩니다. 초음파 용접은 10 ~ 75kHz 주파수의 진동을 전개합니다. 심 용접과 같은 일부 응용 분야에서는 회전 용접 디스크를 팁으로 사용합니다. 공작물에 가해지는 전단 응력은 작은 소성 변형을 일으키고 산화물 층, 오염 물질을 분해하고 고체 상태의 결합을 유도합니다. 초음파 용접과 관련된 온도는 금속의 융점 온도보다 훨씬 낮고 융합이 일어나지 않습니다. 우리는 플라스틱과 같은 비금속 재료에 초음파 용접(USW) 공정을 자주 사용합니다. 그러나 열가소성 수지의 경우 온도가 융점에 도달합니다. 또 다른 인기 있는 기술인 FRICTION WELDING(FRW)에서는 접합할 공작물의 계면에서 마찰을 통해 열이 생성됩니다. 마찰 용접에서 우리는 공작물 중 하나를 고정 상태로 유지하고 다른 공작물은 고정 장치에 고정하고 일정한 속도로 회전합니다. 그런 다음 공작물은 축 방향의 힘을 받아 접촉하게 됩니다. 마찰 용접의 표면 회전 속도는 경우에 따라 900m/min에 도달할 수 있습니다. 충분한 계면 접촉 후 회전하는 공작물이 갑자기 멈추고 축 방향 힘이 증가합니다. 용접 영역은 일반적으로 좁은 영역입니다. 마찰 용접 기술은 다양한 재료로 만들어진 고체 및 관형 부품을 결합하는 데 사용할 수 있습니다. FRW의 인터페이스에서 일부 플래시가 발생할 수 있지만 이 플래시는 2차 가공 또는 연삭으로 제거할 수 있습니다. 마찰 용접 공정의 변형이 존재합니다. 예를 들어 "관성 마찰 용접"에는 부품을 용접하는 데 회전 운동 에너지가 사용되는 플라이휠이 포함됩니다. 플라이휠이 멈추면 용접이 완료된 것입니다. 회전 질량은 변할 수 있고 따라서 회전 운동 에너지는 변할 수 있습니다. 또 다른 변형은 선형 왕복 운동이 결합할 구성 요소 중 하나 이상에 부과되는 "선형 마찰 용접"입니다. 선형 마찰 용접 부품은 원형일 필요가 없으며 직사각형, 정사각형 또는 기타 모양이 될 수 있습니다. 주파수는 수십 Hz, 진폭은 밀리미터 범위, 압력은 수십 또는 수백 MPa일 수 있습니다. 마지막으로 "마찰 교반 용접"은 위에서 설명한 다른 두 가지와 다소 다릅니다. 관성 마찰 용접 및 선형 마찰 용접에서 계면의 가열은 두 개의 접촉 표면을 문지름으로써 마찰을 통해 달성되는 반면, 마찰 교반 용접 방법에서는 결합할 두 표면에 대해 세 번째 본체를 문지릅니다. 직경 5~6mm의 회전 도구를 조인트에 접촉시킵니다. 온도는 503에서 533Kelvin 사이의 값으로 증가할 수 있습니다. 접합부에서 재료의 가열, 혼합 및 교반이 발생합니다. 우리는 알루미늄, 플라스틱 및 복합 재료를 포함한 다양한 재료에 마찰 교반 용접을 사용합니다. 용접은 균일하고 최소한의 기공으로 품질이 높습니다. 마찰교반용접에서 흄이나 스패터가 발생하지 않으며 공정이 잘 자동화되어 있습니다. 저항 용접(RW): 용접에 필요한 열은 접합할 두 공작물 사이의 전기 저항에 의해 생성됩니다. 저항 용접에는 플럭스, 차폐 가스 또는 소모성 전극을 사용하지 않습니다. 줄 가열은 저항 용접에서 발생하며 다음과 같이 표현할 수 있습니다. H = (제곱 I) x R xtx K H는 줄(와트-초)로 생성된 열, I 전류(암페어), R 저항(옴), t는 전류가 흐르는 시간(초)입니다. 계수 K는 1보다 작으며 복사와 전도를 통해 손실되지 않는 에너지의 비율을 나타냅니다. 저항 용접 공정의 전류는 100,000A까지 올라갈 수 있지만 전압은 일반적으로 0.5~10볼트입니다. 전극은 일반적으로 구리 합금으로 만들어집니다. 유사 재료와 이종 재료 모두 저항 용접으로 접합할 수 있습니다. 이 프로세스에는 몇 가지 변형이 있습니다. "저항 스폿 용접"은 두 시트의 랩 조인트 표면에 접촉하는 두 개의 대향 원형 전극을 포함합니다. 전류가 꺼질 때까지 압력이 가해집니다. 용접 너깃은 일반적으로 직경이 최대 10mm입니다. 저항 스폿 용접은 용접 지점에 약간 변색된 자국을 남깁니다. 스폿 용접은 우리가 가장 많이 사용하는 저항 용접 기술입니다. 어려운 영역에 도달하기 위해 다양한 전극 모양이 스폿 용접에 사용됩니다. 우리의 스폿 용접 장비는 CNC로 제어되며 동시에 사용할 수 있는 여러 전극이 있습니다. 또 다른 변형 "저항 솔기 용접"은 AC 전원 사이클에서 전류가 충분히 높은 수준에 도달할 때마다 연속 스폿 용접을 생성하는 휠 또는 롤러 전극으로 수행됩니다. 저항 솔기 용접으로 생성된 조인트는 액체 및 기체 기밀입니다. 얇은 시트의 경우 약 1.5m/min의 용접 속도가 정상입니다. 이음매를 따라 원하는 간격으로 스폿 용접이 생성되도록 간헐적 전류를 적용할 수 있습니다. "저항 돌출 용접"에서는 용접할 공작물 표면 중 하나에 하나 이상의 돌출부(딤플)를 엠보싱합니다. 이러한 돌출부는 원형 또는 타원형일 수 있습니다. 결합 부품과 접촉하는 이러한 엠보싱 지점에서 국부적으로 높은 온도에 도달합니다. 전극은 이러한 돌출부를 압축하기 위해 압력을 가합니다. 저항 투영 용접의 전극은 팁이 평평하고 수냉식 구리 합금입니다. 저항 투영 용접의 장점은 한 번에 여러 번 용접할 수 있어 전극 수명이 연장되고 다양한 두께의 시트를 용접할 수 있으며 너트와 볼트를 시트에 용접할 수 있다는 것입니다. 저항 투영 용접의 단점은 딤플을 엠보싱하는 추가 비용입니다. 또 다른 기술인 "플래시 용접"에서는 두 공작물이 접촉하기 시작할 때 두 공작물의 끝 부분에 있는 아크에서 열이 생성됩니다. 이 방법은 대안적으로 아크 용접을 고려할 수도 있습니다. 계면의 온도가 상승하고 재료가 부드러워집니다. 축방향 힘이 가해지고 연화된 영역에 용접이 형성됩니다. 플래시 용접이 완료된 후 접합부를 가공하여 외관을 개선할 수 있습니다. 플래시 용접으로 얻은 용접 품질이 좋습니다. 전력 수준은 10 ~ 1500kW입니다. 플래시 용접은 최대 직경 75mm의 유사 또는 이종 금속과 0.2mm ~ 25mm 두께의 시트를 가장자리에서 가장자리로 접합하는 데 적합합니다. "스터드 아크 용접"은 플래시 용접과 매우 유사합니다. 볼트 또는 나사 막대와 같은 스터드는 플레이트와 같은 공작물에 결합되는 동안 하나의 전극 역할을 합니다. 발생된 열을 집중시키고 산화를 방지하며 용융 금속을 용접 영역에 유지하기 위해 일회용 세라믹 링이 접합부 주위에 배치됩니다. 마지막으로 "타악기 용접"은 또 다른 저항 용접 공정으로 커패시터를 사용하여 전기 에너지를 공급합니다. 타악기 용접에서 전력은 매우 빠르게 조인트에서 국부적으로 높은 열을 발생시키는 밀리초 내에 방전됩니다. 우리는 조인트 부근에서 민감한 전자 부품의 가열을 피해야 하는 전자 제조 산업에서 충격 용접을 널리 사용합니다. EXPLOSION WELDING이라고 하는 기술은 결합할 공작물 중 하나 위에 놓는 폭발물 층의 폭발을 포함합니다. 공작물에 가해지는 매우 높은 압력은 난류와 물결 모양의 계면을 생성하고 기계적 연동이 발생합니다. 폭발 용접의 결합 강도는 매우 높습니다. 폭발 용접은 이종 금속으로 판을 피복하는 좋은 방법입니다. 클래딩 후 플레이트는 더 얇은 섹션으로 말릴 수 있습니다. 때로는 튜브를 확장하기 위해 폭발 용접을 사용하여 플레이트에 단단히 밀봉됩니다. 고체 상태 접합 영역 내에서 우리의 마지막 방법은 좋은 접합이 주로 계면을 가로질러 원자의 확산에 의해 달성되는 확산 접합 또는 확산 용접(DFW)입니다. 계면에서의 약간의 소성 변형도 용접에 기여합니다. 관련된 온도는 Tm이 금속의 용융 온도인 약 0.5 Tm입니다. 확산 용접의 접착 강도는 압력, 온도, 접촉 시간 및 접촉 표면의 청결도에 따라 달라집니다. 때때로 우리는 인터페이스에서 용가재를 사용합니다. 열과 압력은 확산 접합에 필요하며 전기 저항 또는 로 및 자중, 프레스 또는 기타에 의해 공급됩니다. 유사 금속 및 이종 금속을 확산 용접으로 접합할 수 있습니다. 원자가 이동하는 데 걸리는 시간으로 인해 프로세스가 상대적으로 느립니다. DFW는 자동화할 수 있으며 항공 우주, 전자, 의료 산업의 복잡한 부품 제조에 널리 사용됩니다. 제조된 제품에는 정형외과용 임플란트, 센서, 항공우주 구조 부재가 포함됩니다. 확산 결합은 SUPERPLASTIC FORMING과 결합하여 복잡한 판금 구조를 제작할 수 있습니다. 시트의 선택된 위치는 먼저 확산 결합된 다음 결합되지 않은 영역이 공기 압력을 사용하여 금형으로 확장됩니다. 높은 강성 대 중량 비율을 갖는 항공우주 구조물은 이러한 방법의 조합을 사용하여 제조됩니다. 확산 용접/초소성 성형 결합 공정은 패스너의 필요성을 제거하여 필요한 부품 수를 줄이며 결과적으로 경제적이고 짧은 리드 타임으로 저응력 고정밀 부품을 생성합니다. 브레이징: 브레이징 및 납땜 기술은 용접에 필요한 것보다 낮은 온도를 포함합니다. 그러나 납땜 온도는 납땜 온도보다 높습니다. 브레이징에서는 접합할 표면 사이에 용가재를 놓고 온도를 723Kelvin보다 높지만 공작물의 용융 온도보다 낮은 용가재의 용융 온도까지 올립니다. 용융 금속은 공작물 사이의 밀착 공간을 채웁니다. 필러 금속의 냉각 및 후속 응고로 인해 접합부가 강해집니다. 납땜 용접에서 용가재는 접합부에 증착됩니다. 브레이징에 비해 브레이즈 용접에 훨씬 더 많은 용가재가 사용됩니다. 산화 화염이 있는 옥시아세틸렌 토치는 납땜 용접에서 용가재를 증착하는 데 사용됩니다. 브레이징의 낮은 온도로 인해 뒤틀림 및 잔류 응력과 같은 열 영향 영역에서의 문제가 적습니다. 브레이징의 클리어런스 갭이 작을수록 조인트의 전단 강도가 높아집니다. 그러나 최대 인장 강도는 최적의 간격(피크 값)에서 달성됩니다. 이 최적값 이하 및 이상에서는 브레이징의 인장 강도가 감소합니다. 브레이징의 일반적인 간극은 0.025~0.2mm입니다. 우리는 수행, 분말, 링, 와이어, 스트립 등 다양한 모양의 다양한 브레이징 재료를 사용합니다. 설계 또는 제품 형상을 위해 특별히 이러한 성능을 제조할 수 있습니다. 우리는 또한 귀하의 기본 재료 및 응용 분야에 따라 납땜 재료의 함량을 결정합니다. 우리는 원치 않는 산화물 층을 제거하고 산화를 방지하기 위해 납땜 작업에서 플럭스를 자주 사용합니다. 후속 부식을 방지하기 위해 일반적으로 접합 작업 후에 플럭스를 제거합니다. AGS-TECH Inc.는 다음을 포함한 다양한 브레이징 방법을 사용합니다. - 토치 브레이징 - 퍼니스 브레이징 - 인덕션 브레이징 - 저항 브레이징 - 딥 브레이징 - 적외선 브레이징 - 확산 브레이징 - 고에너지 빔 브레이징 조인트의 가장 일반적인 예는 카바이드 드릴 비트, 인서트, 광전자 밀폐 패키지, 씰과 같이 강도가 우수한 이종 금속으로 만들어집니다. 솔더링 : 이것은 밀접하게 맞는 부품 사이의 브레이징에서처럼 솔더(필러 금속)가 조인트를 채우는 가장 자주 사용되는 기술 중 하나입니다. 당사 솔더의 융점은 723Kelvin 미만입니다. 우리는 제조 작업에서 수동 및 자동 납땜을 모두 사용합니다. 브레이징에 비해 납땜 온도가 낮습니다. 납땜은 고온 또는 고강도 응용 분야에 적합하지 않습니다. 우리는 납땜을 위해 다른 것 외에 주석-납, 주석-아연, 납-은, 카드뮴-은, 아연-알루미늄 합금뿐만 아니라 무연 땜납을 사용합니다. 비부식성 수지 기반 및 무기산 및 염 모두 납땜에서 플럭스로 사용됩니다. 우리는 납땜성이 낮은 금속을 납땜하기 위해 특수 플럭스를 사용합니다. 세라믹 재료, 유리 또는 흑연을 납땜해야 하는 응용 분야에서는 먼저 납땜 가능성을 높이기 위해 적절한 금속으로 부품을 도금합니다. 당사의 인기 있는 납땜 기술은 다음과 같습니다. - 리플 로우 또는 페이스트 솔더링 - 웨이브 솔더링 -로 납땜 - 토치 납땜 - 유도 납땜 -철 납땜 - 저항 납땜 - 딥 솔더링 - 초음파 납땜 -적외선 납땜 초음파 납땜은 결합되는 표면에서 산화막을 제거하는 초음파 캐비테이션 효과로 인해 플럭스가 필요하지 않은 독특한 이점을 제공합니다. 리플로우 및 웨이브 솔더링은 전자 제품의 대량 생산을 위한 산업적으로 뛰어난 기술이므로 더 자세히 설명할 가치가 있습니다. 리플 로우 솔더링에서 우리는 솔더 금속 입자를 포함하는 반고체 페이스트를 사용합니다. 페이스트는 스크리닝 또는 스텐실링 공정을 사용하여 접합부에 배치됩니다. 인쇄 회로 기판(PCB)에서 우리는 이 기술을 자주 사용합니다. 전기 부품을 페이스트로 이러한 패드에 배치하면 표면 장력이 표면 실장 패키지를 정렬된 상태로 유지합니다. 부품을 배치한 후 리플로우 솔더링이 발생하도록 로에서 어셈블리를 가열합니다. 이 과정에서 페이스트의 용매가 증발하고 페이스트의 플럭스가 활성화되고 구성 요소가 예열되고 솔더 입자가 녹아 조인트가 젖고 마지막으로 PCB 어셈블리가 천천히 냉각됩니다. PCB 보드의 대량 생산을 위한 두 번째 인기 있는 기술인 웨이브 솔더링은 용융 솔더가 금속 표면을 적시고 금속이 예열된 경우에만 좋은 결합을 형성한다는 사실에 의존합니다. 용융 솔더의 정상 층류는 먼저 펌프에 의해 생성되고 예열되고 사전 플럭스된 PCB는 웨이브를 통해 전달됩니다. 솔더는 노출된 금속 표면만 적시지만 IC 폴리머 패키지나 폴리머 코팅 회로 기판은 적시지 않습니다. 고속의 뜨거운 물 분사는 접합부에서 과도한 땜납을 불어내고 인접한 리드 사이의 브리징을 방지합니다. 표면 실장 패키지의 웨이브 솔더링에서 우리는 먼저 솔더링하기 전에 회로 기판에 접착식으로 접합합니다. 다시 스크리닝 및 스텐실링이 사용되지만 이번에는 에폭시에 사용됩니다. 구성 요소가 올바른 위치에 배치된 후 에폭시가 경화되고 기판이 뒤집어지고 웨이브 솔더링이 수행됩니다. CLICK Product Finder-Locator Service 이전 페이지
- Waterjet Machining, WJ Cutting, Abrasive Water Jet, WJM, AWJM, AJM
Waterjet Machining - WJ Cutting - Abrasive Water Jet - Hydrodynamic Machining - WJM - AWJM - AJM - AGS-TECH Inc. - USA 워터젯 가공 및 연마재 워터젯 및 연마재-젯 가공 및 절단 The principle of operation of WATER-JET, ABRASIVE WATER-JET and ABRASIVE-JET MACHINING & CUTTING is based 공작물을 때리는 빠르게 흐르는 흐름의 운동량 변화에. 이 운동량 변화 동안 강한 힘이 작용하여 공작물을 절단합니다. This WATERJET CUTTING & MACHINING (WJM) techniques는 3배의 정밀하고 정밀한 사운드를 기반으로 하며 매우 정밀하고 정밀한 연마 속도를 기반으로 합니다. 거의 모든 재료. 가죽, 플라스틱 등 일부 소재의 경우 연마제를 생략할 수 있으며, 절단은 물로만 가능합니다. 워터젯 가공은 석재, 유리 및 금속의 복잡하고 매우 얇은 세부 사항을 절단하는 것부터 다른 기술로는 할 수 없는 일을 할 수 있습니다. 티타늄의 신속한 홀 드릴링. 당사의 워터젯 절단기는 재료 유형에 제한 없이 다양한 치수의 대형 평면 스톡 재료를 처리할 수 있습니다. 자르고 부품을 제조하기 위해 파일에서 컴퓨터로 이미지를 스캔하거나 엔지니어가 프로젝트의 CAD(Computer Aided Drawing)를 준비할 수 있습니다. 절단할 재료의 유형, 두께 및 원하는 절단 품질을 결정해야 합니다. 노즐이 단순히 렌더링된 이미지 패턴을 따르기 때문에 복잡한 디자인은 문제가 되지 않습니다. 디자인은 당신의 상상력에 의해서만 제한됩니다. 귀하의 프로젝트에 대해 오늘 저희에게 연락하여 제안 및 견적을 제공하도록 하십시오. 이 세 가지 유형의 프로세스를 자세히 살펴보겠습니다. WATER-JET MACHINING(WJM): 프로세스는 동등하게 HYDRODYNAMIC MACHINING이라고 부를 수 있습니다. 워터젯에서 발생하는 고도로 국부적인 힘은 절단 및 디버링 작업에 사용됩니다. 간단히 말해서, 워터 제트는 재료의 좁고 매끄러운 홈을 자르는 톱과 같은 역할을 합니다. 워터젯 가공의 압력 수준은 약 400MPa로 효율적인 작업에 충분합니다. 필요한 경우 이 값의 몇 배에 해당하는 압력을 생성할 수 있습니다. 제트 노즐의 직경은 0.05~1mm 정도입니다. 직물, 플라스틱, 고무, 가죽, 단열재, 종이, 복합재료 등 다양한 비금속 재료를 워터젯 커터로 절단합니다. 비닐과 폼으로 만든 자동차 대시보드 덮개와 같은 복잡한 모양도 다축 CNC 제어 워터젯 가공 장비를 사용하여 절단할 수 있습니다. 워터젯 가공은 다른 절단 공정과 비교할 때 효율적이고 깨끗한 공정입니다. 이 기술의 주요 이점 중 일부는 다음과 같습니다. - 구멍을 미리 뚫을 필요 없이 작업물의 어느 위치에서나 절단을 시작할 수 있습니다. - 상당한 열이 발생하지 않음 - 워터젯 가공 및 절단 공정은 공작물의 처짐 및 굽힘이 발생하지 않기 때문에 유연한 재료에 매우 적합합니다. - 생성되는 버가 최소화됩니다. - 워터젯 절단 및 가공은 물을 사용하는 친환경적이고 안전한 공정입니다. ABRASIVE WATER-JET MACHINING(AWJM): 이 공정에서 탄화규소 또는 산화알루미늄과 같은 연마 입자가 워터젯에 포함됩니다. 이는 순수 워터젯 가공보다 재료 제거율을 높입니다. 금속, 비금속, 복합 재료 및 기타 재료는 AWJM을 사용하여 절단할 수 있습니다. 이 기술은 열을 생성하는 다른 기술을 사용하여 절단할 수 없는 열에 민감한 재료를 절단하는 데 특히 유용합니다. 우리는 3mm 크기의 최소 구멍과 약 25mm의 최대 깊이를 생산할 수 있습니다. 절단 속도는 가공되는 재료에 따라 분당 수 미터에 이를 수 있습니다. 금속의 경우 AWJM의 절단 속도는 플라스틱에 비해 낮습니다. 다축 로봇 제어 기계를 사용하여 복잡한 3차원 부품을 가공하여 두 번째 공정 없이 치수를 완성할 수 있습니다. 노즐 치수와 직경을 일정하게 유지하기 위해 절단 작업의 정확성과 반복성을 유지하는 데 중요한 사파이어 노즐을 사용합니다. ABRASIVE-JET MACHINING (AJM) : 이 공정에서 건조 공기, 질소 또는 연마 입자를 포함하는 이산화탄소의 고속 제트가 제어된 조건에서 공작물을 때리고 절단합니다. Abrasive-Jet Machining은 매우 단단하고 부서지기 쉬운 금속 및 비금속 재료의 작은 구멍, 슬롯 및 복잡한 패턴을 절단하고, 디버링 및 부품의 플래시 제거, 트리밍 및 베벨링, 산화물과 같은 표면 필름 제거, 표면이 불규칙한 부품 세척에 사용됩니다. 가스 압력은 약 850kPa이고 연마제 분사 속도는 약 300m/s입니다. 연마 입자의 직경은 약 10~50미크론입니다. 고속 연마 입자는 날카로운 모서리를 둥글게 만들고 구멍이 좁아지는 경향이 있습니다. 따라서 연마제에 의해 가공될 부품의 설계자는 이러한 점을 고려하고 생산된 부품에 이러한 날카로운 모서리와 구멍이 필요하지 않은지 확인해야 합니다. 워터젯, 연마제 워터젯 및 연마제-젯 가공 공정은 절단 및 디버링 작업에 효과적으로 사용할 수 있습니다. 이러한 기술은 하드 툴링을 사용하지 않기 때문에 고유한 유연성을 가지고 있습니다. CLICK Product Finder-Locator Service 이전 페이지
- Computer Networking Equipment, Intermediate Systems, InterWorking Unit
Computer Networking Equipment - Intermediate Systems - InterWorking Unit - IWU - IS - Router - Bridge - Switch - Hub available from AGS-TECH Inc. 네트워킹 장비, 네트워크 장치, 중간 시스템, 연동 유닛 컴퓨터 네트워킹 장치는 컴퓨터 네트워크에서 데이터를 중재하는 장비입니다. 컴퓨터 네트워킹 장치는 NETWORK EQUIPMENT, INTERMEDIATE SYSTEMS(IS) 또는 INTERWORKING UNIT(IWU)라고도 합니다. 마지막 수신기이거나 데이터를 생성하는 장치를 HOST 또는 DATA TERMINAL EQUIPMENT라고 합니다. 우리가 제공하는 고품질 브랜드 중에는 ATOP TECHNOLOGIES, JANZ TEC, ICP DAS 및 KORENIX가 있습니다. TOP TECHNOLOGIES 다운로드 compact 제품 브로셔 (ATOP Technologies 제품 다운로드 List 2021) JANZ TEC 브랜드 컴팩트 제품 브로셔 다운로드 코레닉스 브랜드 컴팩트 제품 브로셔 다운로드 ICP DAS 브랜드 산업용 통신 및 네트워킹 제품 브로셔 다운로드 열악한 환경을 위한 ICP DAS 브랜드 산업용 이더넷 스위치 다운로드 ICP DAS 브랜드 PAC 임베디드 컨트롤러 및 DAQ 브로셔 다운로드 ICP DAS 브랜드 산업용 터치 패드 브로셔 다운로드 ICP DAS 브랜드 원격 IO 모듈 및 IO 확장 장치 브로셔 다운로드 ICP DAS 브랜드 PCI 보드 및 IO 카드 다운로드 프로젝트에 적합한 산업용 등급 네트워킹 장치를 선택하려면 여기를 클릭하여 산업용 컴퓨터 매장으로 이동하십시오. 브로셔 다운로드 디자인 파트너십 프로그램 다음은 유용할 수 있는 네트워킹 장치에 대한 몇 가지 기본 정보입니다. 컴퓨터 네트워킹 장치 목록 / 일반적인 기본 네트워킹 장치: ROUTER: 이것은 데이터 패킷을 패킷의 목적지로 전달할 수 있는 다음 네트워크 지점을 결정하는 특수 네트워크 장치입니다. 게이트웨이와 달리 다른 프로토콜과 인터페이스할 수 없습니다. OSI 레이어 3에서 작동합니다. BRIDGE: 데이터 링크 계층을 따라 여러 네트워크 세그먼트를 연결하는 장치입니다. OSI 레이어 2에서 작동합니다. SWITCH: 하나의 네트워크 세그먼트에서 다른 네트워크 세그먼트로 세그먼트를 연결하는 특정 라인(의도한 대상)에 트래픽을 할당하는 장치입니다. 따라서 허브와 달리 스위치는 네트워크 트래픽을 분할하여 네트워크의 모든 시스템이 아닌 다른 대상으로 보냅니다. OSI 레이어 2에서 작동합니다. 허브: 여러 이더넷 세그먼트를 함께 연결하고 단일 세그먼트로 작동합니다. 즉, 허브는 모든 개체 간에 공유되는 대역폭을 제공합니다. 허브는 네트워크에서 두 개 이상의 이더넷 터미널을 연결하는 가장 기본적인 하드웨어 장치 중 하나입니다. 따라서 개별 노드 간에 전용 연결을 제공하는 스위치와 달리 허브에 연결된 컴퓨터는 한 번에 한 대의 컴퓨터만 전송할 수 있습니다. OSI 레이어 1에서 작동합니다. REPEATER: 네트워크의 한 부분에서 다른 부분으로 보내는 동안 수신된 디지털 신호를 증폭 및/또는 재생성하는 장치입니다. OSI 레이어 1에서 작동합니다. 당사의 일부 HYBRID NETWORK 장치: MULTILAYER SWITCH: OSI 레이어 2를 켜는 것 외에도 상위 프로토콜 레이어에서 기능을 제공하는 스위치입니다. 프로토콜 변환기: 이것은 비동기 및 동기 전송과 같은 두 가지 다른 유형의 전송 사이를 변환하는 하드웨어 장치입니다. BRIDGE ROUTER(B ROUTER): 이 장비는 라우터와 브리지 기능을 결합하므로 OSI 레이어 2 및 3에서 작동합니다. 다음은 서로 다른 네트워크의 연결 지점(예: 내부 및 외부 네트워크 사이)에 가장 자주 배치되는 하드웨어 및 소프트웨어 구성 요소 중 일부입니다. 프록시: 클라이언트가 다른 네트워크 서비스에 간접적으로 네트워크를 연결할 수 있도록 하는 컴퓨터 네트워크 서비스입니다. 방화벽: 네트워크 정책에 의해 금지된 통신 유형을 방지하기 위해 네트워크에 배치된 하드웨어 및/또는 소프트웨어입니다. NETWORK ADDRESS TRANSLATOR: 내부 네트워크 주소를 외부 네트워크 주소로 또는 그 반대로 변환하는 하드웨어 및/또는 소프트웨어로 제공되는 네트워크 서비스. 네트워크 또는 전화 접속 연결을 설정하기 위한 기타 널리 사용되는 하드웨어: 멀티플렉서: 이 장치는 여러 전기 신호를 단일 신호로 결합합니다. NETWORK INTERFACE CONTROLLER: 연결된 컴퓨터가 네트워크를 통해 통신할 수 있도록 하는 컴퓨터 하드웨어. WIRELESS NETWORK INTERFACE CONTROLLER: 연결된 컴퓨터가 WLAN으로 통신할 수 있도록 하는 컴퓨터 하드웨어. 모뎀: 이것은 아날로그 '캐리어' 신호(예: 사운드)를 변조하여 디지털 정보를 인코딩하고 전송된 정보를 디코딩하기 위해 이러한 캐리어 신호를 복조하는 장치입니다. 전화망. ISDN TERMINAL ADAPTER(TA): ISDN(통합 서비스 디지털 네트워크)을 위한 특수 게이트웨이입니다. LINE DRIVER: 신호를 증폭하여 전송거리를 증가시키는 장치입니다. 베이스밴드 네트워크 전용. CLICK Product Finder-Locator Service 이전 페이지
- Test Equipment for Testing Paper & Packaging Products
Test Equipment for Testing Paper & Packaging Products, Adhesive Tape Peel Test Machine, Carton Compressive Tester, Foam Compression Hardness Tester, Zero Drop Test Machine, Package Incline Impact Tester 전자 테스터 전자 테스터라는 용어는 주로 전기 및 전자 부품 및 시스템의 테스트, 검사 및 분석에 사용되는 테스트 장비를 말합니다. 업계에서 가장 인기 있는 제품을 제공합니다. 전원 공급 장치 및 신호 발생 장치: 전원 공급 장치, 신호 발생기, 주파수 합성기, 함수 발생기, 디지털 패턴 발생기, 펄스 발생기, 신호 주입기 미터: 디지털 멀티미터, LCR 미터, EMF 미터, 커패시턴스 미터, 브리지 계측기, 클램프 미터, 가우스미터/테슬라미터/자력계, 접지 저항 미터 분석기: 오실로스코프, 논리 분석기, 스펙트럼 분석기, 프로토콜 분석기, 벡터 신호 분석기, 시간 영역 반사계, 반도체 곡선 추적기, 네트워크 분석기, 위상 역 회전 테스터 자세한 내용 및 기타 유사한 장비는 장비 웹사이트를 방문하십시오. http://www.sourceindustrialsupply.com 업계 전반에 걸쳐 일상적으로 사용되는 이러한 장비에 대해 간략히 살펴보겠습니다. 계측 목적으로 공급하는 전원 공급 장치는 개별, 벤치탑 및 독립형 장치입니다. 조정 가능한 조정 전기 전원 공급 장치는 입력 전압 또는 부하 전류가 변하더라도 출력 값을 조정할 수 있고 출력 전압 또는 전류가 일정하게 유지되기 때문에 가장 널리 사용되는 전원 공급 장치입니다. 절연 전원 공급 장치에는 전원 입력과 전기적으로 독립적인 전원 출력이 있습니다. 전력 변환 방식에 따라 LINEAR 및 SWITCHING POWER SUPPLIES가 있습니다. 선형 전원 공급 장치는 선형 영역에서 작동하는 모든 유효 전력 변환 구성 요소를 사용하여 입력 전원을 직접 처리하는 반면, 스위칭 전원 공급 장치에는 주로 비선형 모드(예: 트랜지스터)에서 작동하는 구성 요소가 있으며 이전에 전력을 AC 또는 DC 펄스로 변환합니다. 처리. 스위칭 전원 공급 장치는 구성 요소가 선형 작동 영역에서 보내는 시간이 더 짧기 때문에 전력 손실이 적기 때문에 일반적으로 선형 공급 장치보다 더 효율적입니다. 애플리케이션에 따라 DC 또는 AC 전원이 사용됩니다. 다른 인기 있는 장치는 전압, 전류 또는 주파수가 RS232 또는 GPIB와 같은 디지털 인터페이스 또는 아날로그 입력을 통해 원격으로 제어될 수 있는 프로그래밍 가능한 전원 공급 장치입니다. 그들 중 다수는 작업을 모니터링하고 제어하기 위한 통합 마이크로컴퓨터를 가지고 있습니다. 이러한 기기는 자동화된 테스트 목적에 필수적입니다. 일부 전자 전원 공급 장치는 과부하 시 전원을 차단하는 대신 전류 제한을 사용합니다. 전자 제한은 일반적으로 실험실 벤치 유형 기기에 사용됩니다. 신호 발생기는 반복 또는 비반복 아날로그 또는 디지털 신호를 생성하는 실험실 및 산업 분야에서 널리 사용되는 또 다른 장비입니다. 또는 FUNCTION GENERATORS, DIGITAL PATTERN GENERATORS 또는 FREQUENCY GENERATORS라고도 합니다. 함수 발생기는 사인파, 스텝 펄스, 사각 및 삼각 파형, 임의 파형과 같은 단순 반복 파형을 생성합니다. 임의 파형 생성기를 사용하여 사용자는 주파수 범위, 정확도 및 출력 레벨의 게시된 제한 내에서 임의 파형을 생성할 수 있습니다. 단순한 파형 세트로 제한되는 함수 발생기와 달리 임의 파형 발생기는 사용자가 다양한 방법으로 소스 파형을 지정할 수 있도록 합니다. RF 및 마이크로파 신호 발생기는 셀룰러 통신, WiFi, GPS, 방송, 위성 통신 및 레이더와 같은 애플리케이션에서 구성 요소, 수신기 및 시스템을 테스트하는 데 사용됩니다. RF 신호 발생기는 일반적으로 몇 kHz에서 6GHz 사이에서 작동하는 반면 마이크로파 신호 발생기는 특수 하드웨어를 사용하여 1MHz 미만에서 최소 20GHz, 심지어 수백 GHz 범위까지 훨씬 더 넓은 주파수 범위 내에서 작동합니다. RF 및 마이크로파 신호 발생기는 아날로그 또는 벡터 신호 발생기로 더 분류할 수 있습니다. AUDIO-FREQUENCY SIGNAL GENERATORS는 오디오 주파수 범위 이상에서 신호를 생성합니다. 오디오 장비의 주파수 응답을 확인하는 전자 연구실 응용 프로그램이 있습니다. 벡터 신호 발생기(디지털 신호 발생기라고도 함)는 디지털 변조 무선 신호를 생성할 수 있습니다. 벡터 신호 생성기는 GSM, W-CDMA(UMTS) 및 Wi-Fi(IEEE 802.11)와 같은 산업 표준을 기반으로 신호를 생성할 수 있습니다. 논리 신호 발생기는 디지털 패턴 발생기라고도 합니다. 이러한 발생기는 논리 유형의 신호, 즉 기존 전압 레벨의 형태로 논리 1 및 0을 생성합니다. 논리 신호 발생기는 디지털 집적 회로 및 임베디드 시스템의 기능 검증 및 테스트를 위한 자극 소스로 사용됩니다. 위에 언급된 장치는 범용입니다. 그러나 사용자 지정 특정 응용 프로그램을 위해 설계된 다른 많은 신호 발생기가 있습니다. 신호 주입기는 회로에서 신호 추적을 위한 매우 유용하고 빠른 문제 해결 도구입니다. 기술자는 라디오 수신기와 같은 장치의 결함 단계를 매우 빠르게 결정할 수 있습니다. 신호 인젝터는 스피커 출력에 적용될 수 있으며 신호가 들리면 회로의 이전 단계로 이동할 수 있습니다. 이 경우 오디오 증폭기이고 주입된 신호가 다시 들리면 신호가 더 이상 들리지 않을 때까지 회로의 단계 위로 신호 주입을 이동할 수 있습니다. 이렇게 하면 문제의 위치를 찾는 데 도움이 됩니다. MULTIMETER는 여러 측정 기능을 하나의 장치에 결합한 전자 측정기입니다. 일반적으로 멀티미터는 전압, 전류 및 저항을 측정합니다. 디지털 및 아날로그 버전 모두 사용할 수 있습니다. 당사는 휴대용 휴대용 멀티미터 장치와 인증된 교정이 포함된 실험실 등급 모델을 제공합니다. 최신 멀티미터는 전압(AC/DC 모두), 볼트, 전류(AC/DC 모두), 암페어, 저항(옴)과 같은 많은 매개변수를 측정할 수 있습니다. 또한 일부 멀티미터는 온도 테스트 프로브를 사용하여 캐패시턴스(패럿), 컨덕턴스(지멘스), 데시벨, 듀티 사이클(퍼센트), 주파수(헤르츠), 인덕턴스(헨리), 온도(섭씨 또는 화씨)를 측정합니다. 일부 멀티미터에는 다음도 포함됩니다. 회로 도통 시 소리, 다이오드(다이오드 접합의 순방향 강하 측정), 트랜지스터(전류 게인 및 기타 매개변수 측정), 배터리 확인 기능, 조도 측정 기능, 산도 및 알칼리도(pH) 측정 기능 및 상대 습도 측정 기능. 최신 멀티미터는 종종 디지털입니다. 최신 디지털 멀티미터에는 종종 계측 및 테스트에서 매우 강력한 도구로 사용할 수 있는 임베디드 컴퓨터가 있습니다. 다음과 같은 기능이 포함됩니다. • 자동 범위 지정, 가장 중요한 숫자가 표시되도록 테스트 중인 수량에 대한 올바른 범위를 선택합니다. •직류 판독의 자동 극성은 적용된 전압이 양수인지 음수인지 보여줍니다. •샘플링 및 홀드, 테스트 중인 회로에서 계측기를 제거한 후 검사를 위해 가장 최근 판독값을 래치합니다. •반도체 접합부의 전압 강하에 대한 전류 제한 테스트. 트랜지스터 테스터를 대체하지는 않지만 디지털 멀티미터의 이 기능은 다이오드 및 트랜지스터 테스트를 용이하게 합니다. • 측정값의 빠른 변화를 더 잘 시각화하기 위해 테스트 중인 수량의 막대 그래프 표현. •저대역폭 오실로스코프. • 자동차 타이밍 및 드웰 신호에 대한 테스트가 포함된 자동차 회로 테스터. • 데이터 수집 기능은 주어진 기간 동안 최대 및 최소 판독값을 기록하고 고정된 간격으로 많은 샘플을 채취합니다. •결합된 LCR 미터. 일부 멀티미터는 컴퓨터와 인터페이스할 수 있지만 일부는 측정값을 저장하고 컴퓨터에 업로드할 수 있습니다. 또 다른 매우 유용한 도구인 LCR METER는 구성 요소의 인덕턴스(L), 커패시턴스(C) 및 저항(R)을 측정하기 위한 계측 기기입니다. 임피던스는 내부적으로 측정되고 디스플레이를 위해 해당 커패시턴스 또는 인덕턴스 값으로 변환됩니다. 테스트 중인 커패시터 또는 인덕터에 임피던스의 상당한 저항성 성분이 없는 경우 판독값은 합리적으로 정확합니다. 고급 LCR 미터는 실제 인덕턴스와 커패시턴스를 측정하고 커패시터의 등가 직렬 저항과 유도성 부품의 Q 계수도 측정합니다. 테스트 중인 장치는 AC 전압 소스에 영향을 받고 미터는 테스트된 장치를 통과하는 전압과 전류를 측정합니다. 전압 대 전류의 비율에서 미터는 임피던스를 결정할 수 있습니다. 전압과 전류 사이의 위상각도 일부 기기에서 측정됩니다. 임피던스와 결합하여 테스트된 장치의 등가 커패시턴스 또는 인덕턴스 및 저항을 계산하고 표시할 수 있습니다. LCR 미터에는 100Hz, 120Hz, 1kHz, 10kHz 및 100kHz의 선택 가능한 테스트 주파수가 있습니다. Benchtop LCR 미터는 일반적으로 100kHz 이상의 선택 가능한 테스트 주파수를 가지고 있습니다. 여기에는 종종 AC 측정 신호에 DC 전압 또는 전류를 중첩할 수 있는 가능성이 포함됩니다. 일부 미터는 이러한 DC 전압 또는 전류를 외부에서 공급할 수 있는 가능성을 제공하지만 다른 장치는 내부적으로 공급합니다. EMF METER는 전자기장(EMF)을 측정하기 위한 테스트 및 계측 기기입니다. 대부분은 전자기 복사 플럭스 밀도(DC 필드) 또는 시간 경과에 따른 전자기장의 변화(AC 필드)를 측정합니다. 1축 및 3축 기기 버전이 있습니다. 단일 축 미터는 3축 미터보다 비용이 적게 들지만 미터가 필드의 한 차원만 측정하기 때문에 테스트를 완료하는 데 더 오래 걸립니다. 측정을 완료하려면 단일 축 EMF 미터를 기울이고 세 축 모두를 켜야 합니다. 반면에 3축 미터는 3개의 축을 모두 동시에 측정하지만 더 비쌉니다. EMF 미터는 전기 배선과 같은 소스에서 발생하는 AC 전자기장을 측정할 수 있는 반면 GAUSSMETERS/TESLAMETERS 또는 MAGNETOMETERS는 직류가 존재하는 소스에서 방출되는 DC 필드를 측정합니다. 대부분의 EMF 미터는 미국 및 유럽 주전원의 주파수에 해당하는 50 및 60Hz 교류 필드를 측정하도록 보정됩니다. 20Hz만큼 낮은 교대 필드를 측정할 수 있는 다른 미터가 있습니다. EMF 측정은 광범위한 주파수에서 광대역으로 수행하거나 관심 주파수 범위만 주파수 선택적으로 모니터링할 수 있습니다. CAPACITANCE METER는 대부분 이산 캐패시터의 캐패시턴스를 측정하는데 사용되는 테스트 장비입니다. 일부 미터는 커패시턴스만 표시하는 반면 다른 미터는 누설, 등가 직렬 저항 및 인덕턴스를 표시합니다. 고급 테스트 장비는 테스트 중인 커패시터를 브리지 회로에 삽입하는 것과 같은 기술을 사용합니다. 브리지의 균형을 맞추기 위해 브리지에 있는 다른 다리의 값을 변경하여 알 수 없는 커패시터의 값을 결정합니다. 이 방법은 더 높은 정밀도를 보장합니다. 브리지는 직렬 저항과 인덕턴스를 측정할 수도 있습니다. 피코패럿에서 패럿까지의 커패시터를 측정할 수 있습니다. 브리지 회로는 누설 전류를 측정하지 않지만 DC 바이어스 전압을 인가하여 누설을 직접 측정할 수 있습니다. 많은 BRIDGE INSTRUMENTS를 컴퓨터에 연결할 수 있으며 데이터 교환을 통해 판독값을 다운로드하거나 브리지를 외부에서 제어할 수 있습니다. 이러한 브리지 장비는 빠르게 진행되는 생산 및 품질 관리 환경에서 테스트 자동화를 위한 go/no go 테스트를 제공합니다. 그러나 또 다른 시험기인 CLAMP METER는 전압계와 클램프형 전류계를 결합한 전기 시험기이다. 클램프 미터의 대부분의 최신 버전은 디지털입니다. 최신 클램프 미터는 디지털 멀티미터의 대부분의 기본 기능을 가지고 있지만 제품에 내장된 변류기 기능이 추가되었습니다. 큰 AC 전류를 전달하는 도체 주위에 계측기의 "턱"을 고정하면 해당 전류는 전력 변압기의 철심과 유사한 턱을 통해 결합되어 미터 입력의 션트를 가로질러 연결된 2차 권선으로 연결됩니다. , 작동 원리는 변압기와 매우 유사합니다. 코어를 감싼 1차 권선 수에 대한 2차 권선 수의 비율로 인해 훨씬 더 적은 전류가 미터 입력에 전달됩니다. 기본은 조가 고정되는 하나의 도체로 표시됩니다. 2차측에 1000개의 권선이 있는 경우 2차측 전류는 1차측에서 흐르는 전류의 1/1000이며, 이 경우 측정되는 도체입니다. 따라서 측정 중인 도체의 1A 전류는 미터 입력에서 0.001A의 전류를 생성합니다. 클램프 미터를 사용하면 2차 권선의 회전 수를 늘려 훨씬 더 큰 전류를 쉽게 측정할 수 있습니다. 대부분의 테스트 장비와 마찬가지로 고급 클램프 미터는 로깅 기능을 제공합니다. 접지 저항 테스터는 접지 전극과 토양 저항을 테스트하는 데 사용됩니다. 장비 요구 사항은 적용 범위에 따라 다릅니다. 최신 클램프 온 접지 테스트 장비는 접지 루프 테스트를 단순화하고 비침습 누설 전류 측정을 가능하게 합니다. 우리가 판매하는 분석기 중에는 의심할 여지 없이 가장 널리 사용되는 장비 중 하나인 오실로스코프가 있습니다. OSCILLOGRAPH라고도 하는 오실로스코프는 일정하게 변화하는 신호 전압을 시간의 함수로 하나 이상의 신호에 대한 2차원 플롯으로 관찰할 수 있는 일종의 전자 테스트 장비입니다. 소리 및 진동과 같은 비전기적 신호도 전압으로 변환되어 오실로스코프에 표시될 수 있습니다. 오실로스코프는 시간에 따른 전기 신호의 변화를 관찰하는 데 사용되며, 전압과 시간은 보정된 눈금에 대해 연속적으로 그래프로 표시되는 모양을 나타냅니다. 파형의 관찰 및 분석은 진폭, 주파수, 시간 간격, 상승 시간 및 왜곡과 같은 속성을 보여줍니다. 오실로스코프는 반복적인 신호가 화면에서 연속적인 형태로 관찰될 수 있도록 조정할 수 있습니다. 많은 오실로스코프에는 단일 이벤트를 계측기에서 캡처하여 비교적 오랜 시간 동안 표시할 수 있는 저장 기능이 있습니다. 이것은 우리가 직접 지각할 수 없는 사건을 너무 빨리 관찰할 수 있게 합니다. 최신 오실로스코프는 가볍고 컴팩트한 휴대용 기기입니다. 현장 서비스 애플리케이션을 위한 소형 배터리 구동 기기도 있습니다. 실험실 등급 오실로스코프는 일반적으로 벤치탑 장치입니다. 오실로스코프와 함께 사용할 수 있는 다양한 프로브와 입력 케이블이 있습니다. 귀하의 응용 프로그램에 사용할 조언이 필요한 경우 당사에 문의하십시오. 두 개의 수직 입력이 있는 오실로스코프를 이중 추적 오실로스코프라고 합니다. 단일 빔 CRT를 사용하여 입력을 다중화하며 일반적으로 한 번에 두 개의 트레이스를 표시할 수 있을 만큼 충분히 빠르게 입력을 전환합니다. 더 많은 트레이스가 있는 오실로스코프도 있습니다. 4개의 입력이 이들 사이에서 공통입니다. 일부 멀티 트레이스 오실로스코프는 외부 트리거 입력을 선택적인 수직 입력으로 사용하고 일부는 최소한의 제어만 가능한 세 번째 및 네 번째 채널을 가지고 있습니다. 최신 오실로스코프에는 전압에 대한 여러 입력이 있으므로 하나의 가변 전압을 다른 전압과 비교하는 데 사용할 수 있습니다. 이것은 예를 들어 다이오드와 같은 구성 요소에 대한 IV 곡선(전류 대 전압 특성)을 그래프로 표시하는 데 사용됩니다. 높은 주파수와 빠른 디지털 신호의 경우 수직 증폭기의 대역폭과 샘플링 속도는 충분히 높아야 합니다. 일반적인 용도의 경우 일반적으로 최소 100MHz의 대역폭이면 충분합니다. 훨씬 낮은 대역폭은 오디오 주파수 애플리케이션에만 충분합니다. 스위핑의 유용한 범위는 적절한 트리거링 및 스위프 지연과 함께 1초에서 100나노초입니다. 안정적인 디스플레이를 위해서는 잘 설계된 안정적인 트리거 회로가 필요합니다. 트리거 회로의 품질은 우수한 오실로스코프의 핵심입니다. 또 다른 주요 선택 기준은 샘플 메모리 깊이와 샘플 속도입니다. 기본 수준의 최신 DSO에는 이제 채널당 1MB 이상의 샘플 메모리가 있습니다. 종종 이 샘플 메모리는 채널 간에 공유되며 때로는 더 낮은 샘플 속도에서만 완전히 사용할 수 있습니다. 가장 높은 샘플 속도에서 메모리는 수십 KB로 제한될 수 있습니다. 최신 '실시간'' 샘플링 속도 DSO는 일반적으로 샘플 속도에서 입력 대역폭의 5-10배를 갖습니다. 따라서 100MHz 대역폭 DSO의 샘플 속도는 500Ms/s - 1Gs/s입니다. 샘플링 속도가 크게 증가하여 1세대 디지털 스코프에 가끔 존재했던 잘못된 신호 표시가 크게 제거되었습니다. 대부분의 최신 오실로스코프는 GPIB, 이더넷, 직렬 포트 및 USB와 같은 하나 이상의 외부 인터페이스 또는 버스를 제공하여 외부 소프트웨어에 의한 원격 기기 제어를 허용합니다. 다음은 다양한 오실로스코프 유형 목록입니다. 음극선 오실로스코프 듀얼 빔 오실로스코프 아날로그 스토리지 오실로스코프 디지털 오실로스코프 혼합 신호 오실로스코프 휴대용 오실로스코프 PC 기반 오실로스코프 논리 분석기는 디지털 시스템 또는 디지털 회로에서 여러 신호를 캡처하고 표시하는 장비입니다. 로직 분석기는 캡처된 데이터를 타이밍 다이어그램, 프로토콜 디코딩, 상태 머신 트레이스, 어셈블리 언어로 변환할 수 있습니다. 로직 분석기는 고급 트리거링 기능을 가지고 있으며 사용자가 디지털 시스템에서 많은 신호 간의 타이밍 관계를 확인해야 할 때 유용합니다. 모듈식 로직 분석기는 섀시 또는 메인프레임과 로직 분석기 모듈로 구성됩니다. 섀시 또는 메인프레임에는 디스플레이, 컨트롤, 제어 컴퓨터 및 데이터 캡처 하드웨어가 설치된 여러 슬롯이 포함됩니다. 각 모듈에는 특정 수의 채널이 있으며 여러 모듈을 결합하여 매우 높은 채널 수를 얻을 수 있습니다. 다수의 모듈을 결합하여 높은 채널 수와 일반적으로 모듈식 로직 분석기의 더 높은 성능을 얻을 수 있는 기능은 모듈식 로직 분석기를 더 비싸게 만듭니다. 최고급 모듈형 로직 분석기의 경우 사용자는 자신의 호스트 PC를 제공하거나 시스템과 호환되는 임베디드 컨트롤러를 구입해야 할 수 있습니다. 휴대용 논리 분석기는 공장에서 설치된 옵션과 함께 모든 것을 단일 패키지로 통합합니다. 일반적으로 모듈식보다 성능이 낮지만 범용 디버깅을 위한 경제적인 계측 도구입니다. PC 기반 논리 분석기에서 하드웨어는 USB 또는 이더넷 연결을 통해 컴퓨터에 연결되고 캡처된 신호를 컴퓨터의 소프트웨어에 전달합니다. 이러한 장치는 개인용 컴퓨터의 기존 키보드, 디스플레이 및 CPU를 사용하기 때문에 일반적으로 훨씬 작고 저렴합니다. 로직 분석기는 디지털 이벤트의 복잡한 시퀀스에서 트리거된 다음 테스트 중인 시스템에서 많은 양의 디지털 데이터를 캡처할 수 있습니다. 오늘날 특수 커넥터가 사용됩니다. 로직 분석기 프로브의 발전으로 여러 공급업체가 지원하는 공통 공간이 생겨 최종 사용자에게 추가 자유를 제공합니다. 소프트 터치; D-Max를 사용 중입니다. 이 프로브는 프로브와 회로 기판 사이에 내구성 있고 안정적인 기계적 및 전기적 연결을 제공합니다. 스펙트럼 분석기는 장비의 전체 주파수 범위 내에서 입력 신호의 크기 대 주파수를 측정합니다. 주요 용도는 신호 스펙트럼의 전력을 측정하는 것입니다. 광학 및 음향 스펙트럼 분석기도 있지만 여기서는 전기 입력 신호를 측정하고 분석하는 전자 분석기에 대해서만 설명합니다. 전기 신호에서 얻은 스펙트럼은 주파수, 전력, 고조파, 대역폭 등에 대한 정보를 제공합니다. 주파수는 수평축에 표시되고 신호 진폭은 수직축에 표시됩니다. 스펙트럼 분석기는 무선 주파수, RF 및 오디오 신호의 주파수 스펙트럼 분석을 위해 전자 산업에서 널리 사용됩니다. 신호의 스펙트럼을 보면 신호의 요소와 이를 생성하는 회로의 성능을 밝힐 수 있습니다. 스펙트럼 분석기는 매우 다양한 측정을 수행할 수 있습니다. 신호의 스펙트럼을 얻는 데 사용되는 방법을 살펴보면 스펙트럼 분석기 유형을 분류할 수 있습니다. - SWEPT-TUNED SPECTRUM ANALYZER는 수퍼헤테로다인 수신기를 사용하여 입력 신호 스펙트럼의 일부(전압 제어 발진기 및 믹서 사용)를 대역 통과 필터의 중심 주파수로 하향 변환합니다. 수퍼헤테로다인 아키텍처에서 전압 제어 발진기는 기기의 전체 주파수 범위를 활용하여 다양한 주파수 범위에서 스위프됩니다. 스위프 튜닝된 스펙트럼 분석기는 라디오 수신기의 후손입니다. 따라서 스위프 튜닝 분석기는 튜닝 필터 분석기(TRF 라디오와 유사) 또는 슈퍼헤테로다인 분석기입니다. 사실, 가장 단순한 형태로 스위프 튜닝 스펙트럼 분석기는 자동으로 튜닝(스윕)되는 주파수 범위를 가진 주파수 선택 전압계로 생각할 수 있습니다. 본질적으로 사인파의 rms 값을 표시하도록 보정된 주파수 선택형 피크 응답 전압계입니다. 스펙트럼 분석기는 복잡한 신호를 구성하는 개별 주파수 성분을 표시할 수 있습니다. 그러나 위상 정보는 제공하지 않고 크기 정보만 제공합니다. 최신 스윕 튜닝 분석기(특히 슈퍼헤테로다인 분석기)는 다양한 측정을 수행할 수 있는 정밀 장치입니다. 그러나 주어진 범위의 모든 주파수를 동시에 평가할 수 없기 때문에 주로 정상 상태 또는 반복적인 신호를 측정하는 데 사용됩니다. 모든 주파수를 동시에 평가하는 기능은 실시간 분석기에서만 가능합니다. - 실시간 스펙트럼 분석기: FFT 스펙트럼 분석기는 파형을 입력 신호의 주파수 스펙트럼 구성 요소로 변환하는 수학적 프로세스인 이산 푸리에 변환(DFT)을 계산합니다. 푸리에 또는 FFT 스펙트럼 분석기는 또 다른 실시간 스펙트럼 분석기 구현입니다. 푸리에 분석기는 디지털 신호 처리를 사용하여 입력 신호를 샘플링하고 주파수 영역으로 변환합니다. 이 변환은 FFT(고속 푸리에 변환)를 사용하여 수행됩니다. FFT는 데이터를 시간 영역에서 주파수 영역으로 변환하는 데 사용되는 수학 알고리즘인 이산 푸리에 변환을 구현한 것입니다. 다른 유형의 실시간 스펙트럼 분석기, 즉 병렬 필터 분석기는 각각 다른 대역 통과 주파수를 갖는 여러 대역 통과 필터를 결합합니다. 각 필터는 항상 입력에 연결된 상태를 유지합니다. 초기 안정화 시간 후 병렬 필터 분석기는 분석기의 측정 범위 내의 모든 신호를 즉시 감지하고 표시할 수 있습니다. 따라서 병렬 필터 분석기는 실시간 신호 분석을 제공합니다. 병렬 필터 분석기는 빠르며 과도 신호 및 시변 신호를 측정합니다. 그러나 병렬 필터 분석기의 주파수 분해능은 대역통과 필터의 폭에 따라 분해능이 결정되기 때문에 대부분의 스위프 튜닝된 분석기보다 훨씬 낮습니다. 넓은 주파수 범위에서 정밀한 분해능을 얻으려면 많은 개별 필터가 필요하므로 비용이 많이 들고 복잡합니다. 이것이 시장에서 가장 단순한 것을 제외하고 대부분의 병렬 필터 분석기가 비싼 이유입니다. - 벡터 신호 분석(VSA): 과거에는 스위프 튜닝 및 슈퍼헤테로다인 스펙트럼 분석기가 오디오에서 마이크로파를 통해 밀리미터 주파수에 이르기까지 광범위한 주파수 범위를 다루었습니다. 또한 DSP(디지털 신호 처리) 집약적 FFT(고속 푸리에 변환) 분석기는 고해상도 스펙트럼 및 네트워크 분석을 제공했지만 아날로그-디지털 변환 및 신호 처리 기술의 한계로 인해 저주파에 제한되었습니다. 오늘날의 광대역, 벡터 변조, 시변 신호는 FFT 분석 및 기타 DSP 기술의 기능을 크게 활용합니다. 벡터 신호 분석기는 슈퍼헤테로다인 기술과 고속 ADC 및 기타 DSP 기술을 결합하여 빠른 고해상도 스펙트럼 측정, 복조 및 고급 시간 영역 분석을 제공합니다. VSA는 통신, 비디오, 방송, 수중 음파 탐지기 및 초음파 이미징 애플리케이션에 사용되는 버스트, 과도 또는 변조 신호와 같은 복잡한 신호를 특성화하는 데 특히 유용합니다. 폼 팩터에 따라 스펙트럼 분석기는 벤치탑, 휴대용, 핸드헬드 및 네트워크로 분류됩니다. 벤치탑 모델은 실험실 환경이나 제조 영역과 같이 스펙트럼 분석기를 AC 전원에 연결할 수 있는 애플리케이션에 유용합니다. 벤치 탑 스펙트럼 분석기는 일반적으로 휴대용 또는 휴대용 버전보다 더 나은 성능과 사양을 제공합니다. 그러나 일반적으로 더 무겁고 냉각용 팬이 여러 개 있습니다. 일부 벤치탑 스펙트럼 분석기는 전원 콘센트에서 멀리 떨어진 곳에서도 사용할 수 있도록 배터리 팩을 옵션으로 제공합니다. 그것들을 휴대용 스펙트럼 분석기라고 합니다. 휴대용 모델은 스펙트럼 분석기를 측정하기 위해 외부로 가져가거나 사용 중에 휴대해야 하는 애플리케이션에 유용합니다. 우수한 휴대용 스펙트럼 분석기는 사용자가 전원 콘센트가 없는 장소에서 작업할 수 있도록 하는 선택적 배터리 전원 작동, 밝은 햇빛, 어둠 또는 먼지가 많은 조건, 가벼운 무게에서도 화면을 읽을 수 있도록 명확하게 볼 수 있는 디스플레이를 제공할 것으로 예상됩니다. 휴대용 스펙트럼 분석기는 스펙트럼 분석기가 매우 가볍고 작아야 하는 응용 분야에 유용합니다. 휴대용 분석기는 더 큰 시스템에 비해 제한된 기능을 제공합니다. 그러나 휴대용 스펙트럼 분석기의 장점은 매우 낮은 전력 소비, 사용자가 야외에서 자유롭게 이동할 수 있는 배터리 전원 작동, 매우 작은 크기 및 가벼운 무게입니다. 마지막으로 NETWORKED SPECTRUM ANALYZERS에는 디스플레이가 포함되어 있지 않으며 지리적으로 분산된 새로운 차원의 스펙트럼 모니터링 및 분석 애플리케이션을 가능하게 하도록 설계되었습니다. 주요 속성은 분석기를 네트워크에 연결하고 네트워크를 통해 이러한 장치를 모니터링하는 기능입니다. 많은 스펙트럼 분석기에 제어용 이더넷 포트가 있지만 일반적으로 효율적인 데이터 전송 메커니즘이 부족하고 분산 방식으로 배포하기에는 너무 부피가 크거나 비용이 많이 듭니다. 이러한 장치의 분산 특성으로 인해 송신기의 지리적 위치, 동적 스펙트럼 액세스를 위한 스펙트럼 모니터링 및 기타 여러 애플리케이션이 가능합니다. 이러한 장치는 분석기 네트워크 전체에서 데이터 캡처를 동기화하고 저렴한 비용으로 네트워크 효율적인 데이터 전송을 가능하게 합니다. 프로토콜 분석기는 통신 채널을 통해 신호 및 데이터 트래픽을 캡처하고 분석하는 데 사용되는 하드웨어 및/또는 소프트웨어를 통합한 도구입니다. 프로토콜 분석기는 주로 성능 측정 및 문제 해결에 사용됩니다. 네트워크에 연결하여 핵심 성과 지표를 계산하여 네트워크를 모니터링하고 문제 해결 활동을 가속화합니다. NETWORK PROTOCOL ANALYZER는 네트워크 관리자 툴킷의 중요한 부분입니다. 네트워크 프로토콜 분석은 네트워크 통신의 상태를 모니터링하는 데 사용됩니다. 네트워크 장치가 특정 방식으로 작동하는 이유를 알아내기 위해 관리자는 프로토콜 분석기를 사용하여 트래픽을 스니핑하고 유선을 통해 전달되는 데이터와 프로토콜을 노출합니다. 네트워크 프로토콜 분석기는 다음을 수행하는 데 사용됩니다. - 해결하기 어려운 문제 해결 - 악성 소프트웨어/맬웨어를 탐지하고 식별합니다. 침입 탐지 시스템 또는 허니팟으로 작업하십시오. - 기준 트래픽 패턴 및 네트워크 활용 메트릭과 같은 정보 수집 - 네트워크에서 제거할 수 있도록 사용하지 않는 프로토콜 식별 - 침투 테스트를 위한 트래픽 생성 - 트래픽 도청(예: 승인되지 않은 인스턴트 메시징 트래픽 또는 무선 액세스 포인트 찾기) 시간 영역 반사계(TDR)는 시간 영역 반사 측정을 사용하여 연선 및 동축 케이블, 커넥터, 인쇄 회로 기판 등과 같은 금속 케이블의 결함을 특성화하고 찾는 장비입니다. 시간 영역 반사계는 도체를 따라 반사를 측정합니다. 이를 측정하기 위해 TDR은 입사 신호를 도체에 전송하고 반사를 확인합니다. 도체의 임피던스가 균일하고 적절하게 종단되면 반사가 없고 나머지 입사 신호는 종단에 의해 맨 끝에서 흡수됩니다. 그러나 어딘가에 임피던스 변화가 있으면 입사 신호의 일부가 소스로 다시 반사됩니다. 반사는 입사 신호와 같은 모양을 갖지만 부호와 크기는 임피던스 레벨의 변화에 따라 달라집니다. 임피던스가 단계적으로 증가하면 반사는 입사 신호와 동일한 부호를 가지며 임피던스가 단계적으로 감소하면 반사는 반대 부호를 갖습니다. 반사는 시간 영역 반사계의 출력/입력에서 측정되고 시간의 함수로 표시됩니다. 또는 신호 전파 속도가 주어진 전송 매체에 대해 거의 일정하기 때문에 디스플레이는 케이블 길이의 함수로 전송 및 반사를 표시할 수 있습니다. TDR은 케이블 임피던스와 길이, 커넥터 및 스플라이스 손실 및 위치를 분석하는 데 사용할 수 있습니다. TDR 임피던스 측정은 설계자가 시스템 상호 연결의 신호 무결성 분석을 수행하고 디지털 시스템 성능을 정확하게 예측할 수 있는 기회를 제공합니다. TDR 측정은 기판 특성화 작업에 널리 사용됩니다. 회로 기판 설계자는 기판 트레이스의 특성 임피던스를 결정하고 기판 구성 요소에 대한 정확한 모델을 계산하며 기판 성능을 보다 정확하게 예측할 수 있습니다. 시간 영역 반사계의 다른 많은 응용 분야가 있습니다. SEMICONDUCTOR CURVE TRACER는 다이오드, 트랜지스터, 사이리스터와 같은 이산 반도체 소자의 특성을 분석하는 테스트 장비입니다. 이 계측기는 오실로스코프를 기반으로 하지만 테스트 중인 장치를 자극하는 데 사용할 수 있는 전압 및 전류 소스도 포함합니다. 테스트 중인 장치의 두 단자에 스위프 전압을 적용하고 각 전압에서 장치가 흐르도록 허용하는 전류의 양을 측정합니다. VI(전압 대 전류)라는 그래프가 오실로스코프 화면에 표시됩니다. 구성에는 인가된 최대 전압, 인가된 전압의 극성(양극과 음극 모두의 자동 인가 포함), 장치와 직렬로 삽입된 저항이 포함됩니다. 다이오드와 같은 2개의 터미널 장치의 경우 장치를 완전히 특성화하는 데 충분합니다. 곡선 추적기는 다이오드의 순방향 전압, 역방향 누설 전류, 역방향 항복 전압 등과 같은 모든 흥미로운 매개변수를 표시할 수 있습니다. 트랜지스터 및 FET와 같은 3단자 장치도 베이스 또는 게이트 단자와 같이 테스트 중인 장치의 제어 단자에 대한 연결을 사용합니다. 트랜지스터 및 기타 전류 기반 장치의 경우 베이스 또는 기타 제어 단자 전류가 단계적입니다. 전계 효과 트랜지스터(FET)의 경우 계단식 전류 대신 계단식 전압이 사용됩니다. 구성된 메인 단자 전압 범위를 통해 전압을 스위핑함으로써 제어 신호의 각 전압 단계에 대해 VI 곡선 그룹이 자동으로 생성됩니다. 이 곡선 그룹을 사용하면 트랜지스터의 이득 또는 사이리스터 또는 TRIAC의 트리거 전압을 매우 쉽게 결정할 수 있습니다. 최신 반도체 곡선 추적기는 직관적인 Windows 기반 사용자 인터페이스, IV, CV 및 펄스 생성, 펄스 IV, 모든 기술에 포함된 응용 프로그램 라이브러리 등과 같은 많은 매력적인 기능을 제공합니다. 위상 회전 테스터/표시기: 이들은 3상 시스템 및 개방/비통전 위상에서 위상 시퀀스를 식별하기 위한 작고 견고한 테스트 장비입니다. 회전 기계, 모터를 설치하고 발전기 출력을 확인하는 데 이상적입니다. 애플리케이션 중에는 적절한 위상 시퀀스 식별, 누락된 와이어 위상 감지, 회전 기계에 대한 적절한 연결 결정, 활성 회로 감지 등이 있습니다. FREQUENCY COUNTER는 주파수를 측정하는 데 사용되는 테스트 장비입니다. 주파수 카운터는 일반적으로 특정 기간 내에 발생하는 이벤트 수를 누적하는 카운터를 사용합니다. 계산할 이벤트가 전자 형식인 경우 계측기에 대한 간단한 인터페이스만 있으면 됩니다. 더 복잡한 신호는 계산에 적합하도록 약간의 조절이 필요할 수 있습니다. 대부분의 주파수 카운터에는 입력에 일종의 증폭기, 필터링 및 성형 회로가 있습니다. 디지털 신호 처리, 감도 제어 및 히스테리시스는 성능을 향상시키는 다른 기술입니다. 본질적으로 전자적이지 않은 다른 유형의 주기적 이벤트는 변환기를 사용하여 변환해야 합니다. RF 주파수 카운터는 저주파 카운터와 동일한 원리로 작동합니다. 오버플로 전에 더 많은 범위가 있습니다. 매우 높은 마이크로파 주파수의 경우 많은 설계에서 고속 프리스케일러를 사용하여 신호 주파수를 일반 디지털 회로가 작동할 수 있는 지점으로 낮춥니다. 마이크로파 주파수 카운터는 최대 거의 100GHz의 주파수를 측정할 수 있습니다. 이러한 고주파수 이상에서 측정할 신호는 믹서에서 국부 발진기의 신호와 결합되어 직접 측정을 위해 충분히 낮은 차이 주파수에서 신호를 생성합니다. 주파수 카운터의 인기 있는 인터페이스는 다른 최신 기기와 유사한 RS232, USB, GPIB 및 이더넷입니다. 측정 결과를 보내는 것 외에도 카운터는 사용자가 정의한 측정 한계를 초과할 때 사용자에게 알릴 수 있습니다. 자세한 내용 및 기타 유사한 장비는 장비 웹사이트를 방문하십시오. http://www.sourceindustrialsupply.com For other similar equipment, please visit our equipment website: http://www.sourceindustrialsupply.com CLICK Product Finder-Locator Service 이전 페이지