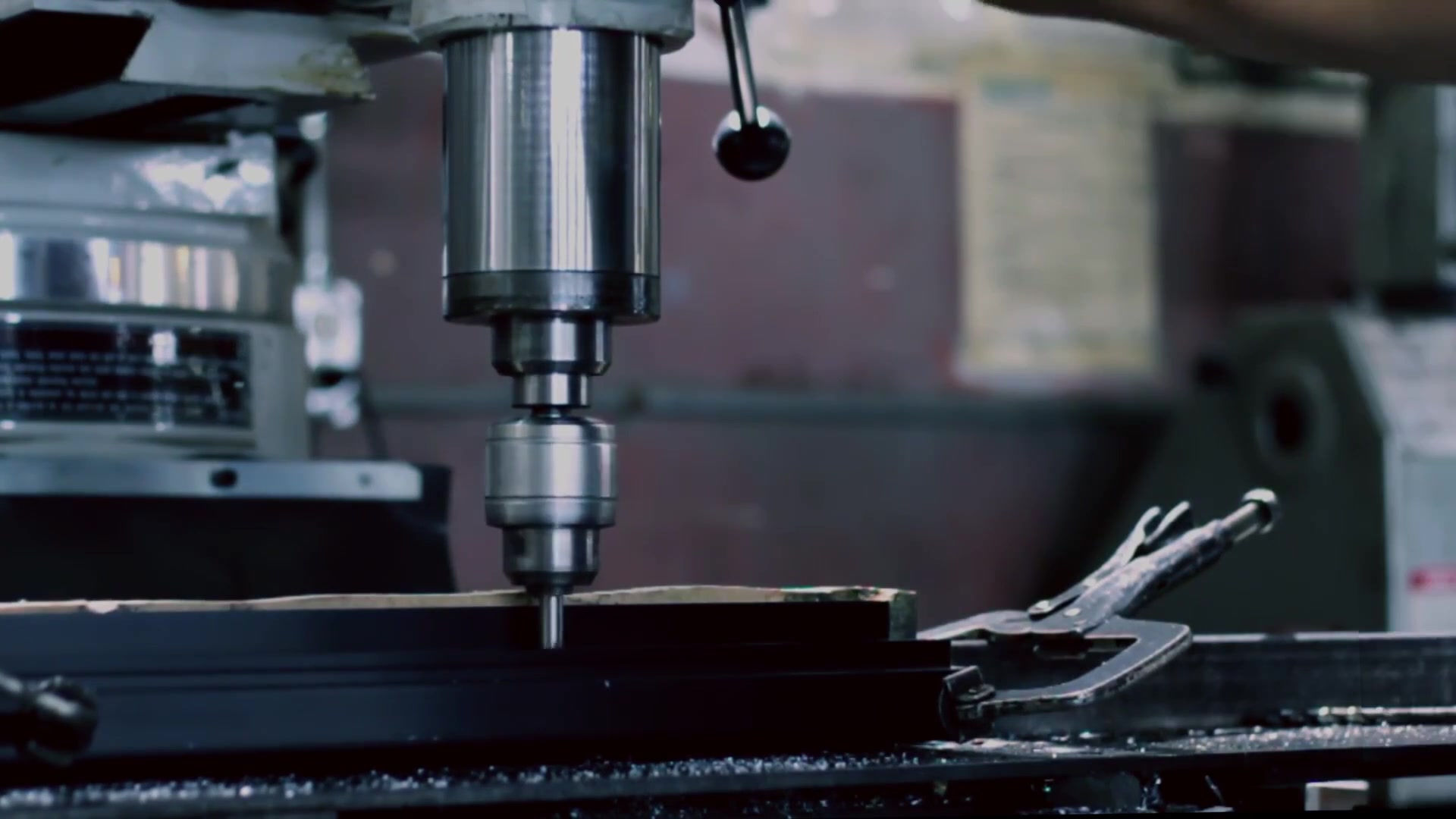
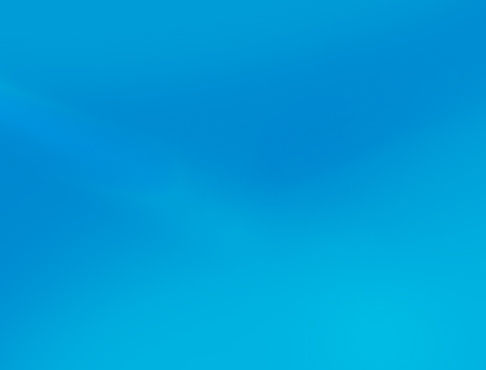
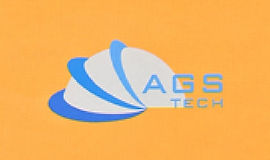
Global Custom Manufacturer, Integrator, Consolidator, Outsourcing Partner for et bredt utvalg av produkter og tjenester.
Vi er din one-stop-kilde for produksjon, fabrikasjon, engineering, konsolidering, integrasjon, outsourcing av spesialproduserte og hylleprodukter og tjenester.
Choose your Language
-
Tilpasset produksjon
-
Innenlandsk og global kontraktsproduksjon
-
Outsourcing av produksjon
-
Innenlandske og globale innkjøp
-
Consolidation
-
Engineering Integration
-
Ingeniørtjenester
Blant de mange SAMLING-teknikkene vi bruker i produksjon, legges det spesiell vekt på SVEISING, LØDNING, LØDNING, LISTEBINDING og TILPASSET MEKANISK MONTERING fordi disse teknikkene er mye brukt i applikasjoner som produksjon av hermetiske sammenstillinger, høyteknologisk produktproduksjon og spesialforsegling. Her vil vi konsentrere oss om de mer spesialiserte aspektene ved disse sammenføyningsteknikkene da de er relatert til produksjon av avanserte produkter og sammenstillinger.
FUSJONSVEISING: Vi bruker varme til å smelte og smelte sammen materialer. Varme tilføres av elektrisitet eller høyenergibjelker. Typene fusjonssveising vi implementerer er OXYFUEL GASSVEISING, BUESVEISING, HØYENERGISVEISING.
SVEISING I SOLIDSTATE: Vi skjøter sammen deler uten smelting og sammensmelting. Våre solid-state sveisemetoder er KALDE, ULTRALYD, MOTSTAND, FRIKKSJON, EKSPLOSJONSSVEISING og DIFFUSJONSBINDING.
LODING OG LØDING: De bruker fyllmetaller og gir oss fordelen av å jobbe ved lavere temperaturer enn ved sveising, og dermed mindre strukturelle skader på produktene. Informasjon om vårt loddeanlegg som produserer keramiske til metallfittings, hermetisk forsegling, vakuumgjennomføringer, høy- og ultrahøyvakuum og væskekontrollkomponenter finner du her:Loddefabrikkbrosjyre
LISTERBINDING: På grunn av mangfoldet av lim som brukes i industrien og også mangfoldet av bruksområder, har vi en dedikert side for dette. For å gå til siden vår om liming, klikk her.
TILPASSET MEKANISK MONTERING: Vi bruker en rekke festemidler som bolter, skruer, muttere, nagler. Våre festemidler er ikke begrenset til standard hyllefester. Vi designer, utvikler og produserer spesialfester som er laget av ikke-standard materialer, slik at de kan møte kravene til spesielle bruksområder. Noen ganger er elektrisk eller varme ikke-konduktivitet ønsket mens noen ganger konduktivitet. For noen spesielle bruksområder kan en kunde ønske spesielle festemidler som ikke kan fjernes uten å ødelegge produktet. Det er uendelige ideer og bruksområder. Vi har alt for deg, hvis ikke hyllevare kan vi raskt utvikle det. For å gå til vår side om mekanisk montering, vennligst klikk her. La oss undersøke våre ulike sammenføyningsteknikker i flere detaljer.
OXYFUEL GASS WELDING (OFW): Vi bruker en brenngass blandet med oksygen for å produsere sveiseflammen. Når vi bruker acetylen som drivstoff og oksygen, kaller vi det oksyacetylengassveising. To kjemiske reaksjoner forekommer i oksyfuelgassforbrenningsprosessen:
C2H2 + O2 ------» 2CO + H2 + Varme
2CO + H2 + 1,5 O2--------» 2 CO2 + H2O + Varme
Den første reaksjonen dissosierer acetylen til karbonmonoksid og hydrogen mens den produserer omtrent 33 % av den totale varmen som genereres. Den andre prosessen ovenfor representerer ytterligere forbrenning av hydrogenet og karbonmonoksidet mens den produserer omtrent 67 % av den totale varmen. Temperaturene i flammen er mellom 1533 og 3573 Kelvin. Oksygenprosenten i gassblandingen er viktig. Hvis oksygeninnholdet er mer enn halvparten, blir flammen et oksidasjonsmiddel. Dette er uønsket for noen metaller, men ønskelig for andre. Et eksempel når oksiderende flamme er ønskelig er kobberbaserte legeringer fordi det danner et passiveringslag over metallet. På den annen side, når oksygeninnholdet reduseres, er full forbrenning ikke mulig og flammen blir en reduserende (karboniserende) flamme. Temperaturene i en reduserende flamme er lavere og er derfor egnet for prosesser som lodding og lodding. Andre gasser er også potensielle drivstoff, men de har noen ulemper i forhold til acetylen. Av og til leverer vi tilsatsmetaller til sveisesonen i form av fyllstaver eller tråd. Noen av dem er belagt med flussmiddel for å forsinke oksidasjon av overflater og dermed beskytte det smeltede metallet. En ekstra fordel fluksen gir oss er fjerning av oksider og andre stoffer fra sveisesonen. Dette fører til sterkere binding. En variant av oxyfuel-gassveisingen er TRYKKGASSVEISING, hvor de to komponentene varmes opp ved grensesnittet ved hjelp av oksyacetylengassbrenner og når grensesnittet begynner å smelte, trekkes brenneren tilbake og en aksial kraft påføres for å presse de to delene sammen til grensesnittet er størknet.
BUESVEISING: Vi bruker elektrisk energi til å produsere en lysbue mellom elektrodespissen og deler som skal sveises. Strømforsyningen kan være AC eller DC mens elektrodene enten er forbrukbare eller ikke-forbrukbare. Varmeoverføring ved buesveising kan uttrykkes ved følgende ligning:
H/l = ex VI/v
Her er H varmetilførselen, l er sveiselengden, V og I er spenningen og strømmen som påføres, v er sveisehastigheten og e er prosesseffektiviteten. Jo høyere effektivitet "e" jo mer fordelaktig brukes den tilgjengelige energien til å smelte materialet. Varmetilførselen kan også uttrykkes som:
H = ux (Volum) = ux A xl
Her er u den spesifikke energien for smelting, A tverrsnittet av sveisen og l sveiselengden. Fra de to ligningene ovenfor kan vi få:
v = ex VI / u A
En variant av buesveising er SHIELDED METAL ARRC WELDING (SMAW) som utgjør omtrent 50 % av alle industri- og vedlikeholdssveiseprosesser. ELEKTRISK BUESVEISING (STIKKSVEISING) utføres ved å berøre tuppen av en belagt elektrode til arbeidsstykket og raskt trekke det tilbake til en avstand som er tilstrekkelig til å opprettholde lysbuen. Vi kaller denne prosessen også stavsveising fordi elektrodene er tynne og lange pinner. Under sveiseprosessen smelter tuppen av elektroden sammen med belegget og basismetallet i nærheten av lysbuen. En blanding av basismetallet, elektrodemetallet og stoffer fra elektrodebelegget størkner i sveiseområdet. Belegget på elektroden deoksiderer og gir en beskyttelsesgass i sveiseområdet, og beskytter den mot oksygenet i miljøet. Derfor blir prosessen referert til som skjermet metallbuesveising. Vi bruker strømmer mellom 50 og 300 Ampere og effektnivåer generelt mindre enn 10 kW for optimal sveiseytelse. Også av betydning er polariteten til DC-strømmen (strømretningen). Rett polaritet hvor arbeidsstykket er positivt og elektroden er negativ foretrekkes ved sveising av metallplater på grunn av dens grunne penetrering og også for skjøter med meget store mellomrom. Når vi har omvendt polaritet, dvs. at elektroden er positiv og arbeidsstykke negativ kan vi oppnå dypere sveisegjennomtrengninger. Med vekselstrøm, siden vi har pulserende lysbuer, kan vi sveise tykke seksjoner ved hjelp av elektroder med stor diameter og maksimale strømmer. SMAW-sveisemetoden er egnet for arbeidsstykketykkelser på 3 til 19 mm og enda mer ved bruk av flergangsteknikker. Slaggen som dannes på toppen av sveisen må fjernes med en stålbørste, slik at det ikke oppstår korrosjon og svikt i sveiseområdet. Dette øker selvfølgelig kostnadene for skjermet metallbuesveising. Likevel er SMAW den mest populære sveiseteknikken innen industri og reparasjonsarbeid.
NEKKET BUESVEISING (SAG): I denne prosessen skjermer vi sveisebuen ved å bruke granulære flussmaterialer som kalk, silika, kalsiumflorid, manganoksid...osv. Det granulære flussmiddelet mates inn i sveisesonen ved tyngdekraftstrøm gjennom en dyse. Flussmiddelet som dekker den smeltede sveisesonen beskytter betydelig mot gnister, røyk, UV-stråling osv. og fungerer som en termisk isolator, og lar dermed varmen trenge dypt inn i arbeidsstykket. Den usmeltede fluksen gjenvinnes, behandles og gjenbrukes. En spole av bare brukes som elektrode og mates gjennom et rør til sveiseområdet. Vi bruker strømmer mellom 300 og 2000 Ampere. Den neddykkede buesveisingsprosessen (SAW) er begrenset til horisontale og flate posisjoner og sirkulære sveiser hvis rotasjon av den sirkulære strukturen (som rør) er mulig under sveising. Hastighetene kan nå 5 m/min. SAW-prosessen er egnet for tykke plater og resulterer i høykvalitets, seige, duktile og jevne sveiser. Produktiviteten, det vil si mengden sveisemateriale som avsettes per time, er 4 til 10 ganger mengden sammenlignet med SMAW-prosessen.
En annen buesveiseprosess, nemlig GAS METAL ARRC WELDING (GMAW) eller alternativt referert til som METAL INERT GAS WELDING (MIG) er basert på at sveiseområdet er skjermet av eksterne gasskilder som helium, argon, karbondioksid...osv. Det kan være ytterligere deoksideringsmidler tilstede i elektrodemetallet. Forbrukstråd føres gjennom en dyse inn i sveisesonen. Fremstilling som involverer både jernholdige og ikke-jernholdige metaller utføres ved bruk av gassmetallbuesveising (GMAW). Sveiseproduktiviteten er omtrent 2 ganger høyere enn SMAW-prosessen. Automatisert sveiseutstyr brukes. Metall overføres på en av tre måter i denne prosessen: "Spray Transfer" innebærer overføring av flere hundre små metalldråper per sekund fra elektrode til sveiseområdet. I "Globular Transfer" på den annen side brukes karbondioksidrike gasser og kuler av smeltet metall drives frem av den elektriske lysbuen. Sveisestrømmene er høye og sveiseinntrengningen dypere, sveisehastigheten høyere enn ved sprayoverføring. Dermed er kuleoverføringen bedre for sveising av tyngre seksjoner. Til slutt, i "Short Circuiting"-metoden, berører elektrodespissen det smeltede sveisebassenget, og kortslutter det som metall med hastigheter over 50 dråper/sekund overføres i individuelle dråper. Lave strømmer og spenninger brukes sammen med tynnere ledning. Effektene som brukes er ca. 2 kW og temperaturene relativt lave, noe som gjør denne metoden egnet for tynne plater med en tykkelse på mindre enn 6 mm.
En annen variant av FLUX-CORED ARC WELDING (FCAW)-prosessen ligner gassmetallbuesveising, bortsett fra at elektroden er et rør fylt med flussmiddel. Fordelene med å bruke elektroder med kjerneflux er at de produserer mer stabile lysbuer, gir oss muligheten til å forbedre egenskapene til sveisemetaller, mindre sprø og fleksible natur av fluksen sammenlignet med SMAW-sveising, forbedrede sveisekonturer. Selvskjermede kjerneelektroder inneholder materialer som skjermer sveisesonen mot atmosfæren. Vi bruker ca 20 kW effekt. I likhet med GMAW-prosessen gir FCAW-prosessen også muligheten til å automatisere prosesser for kontinuerlig sveising, og det er økonomisk. Ulike sveisemetallkjemier kan utvikles ved å tilsette forskjellige legeringer til flukskjernen.
I ELECTROGAS WELDING (EGW) sveiser vi de plasserte delene kant i kant. Det kalles noen ganger også STUMSSVEISING. Sveisemetall legges inn i et sveisehulrom mellom to stykker som skal skjøtes. Rommet er omsluttet av to vannkjølte demninger for å hindre at smeltet slagget renner ut. Demningene flyttes opp av mekaniske drivverk. Når arbeidsstykket kan roteres, kan vi også bruke elektrogassveisingsteknikken til omkretsveising av rør. Elektroder mates gjennom en kanal for å holde en kontinuerlig lysbue. Strømmene kan være rundt 400 Ampere eller 750 Ampere og effektnivåer rundt 20 kW. Inerte gasser som stammer fra enten en flukskjernet elektrode eller ekstern kilde gir skjerming. Vi bruker elektrogassveising (EGW) for metaller som stål, titan osv. med tykkelser fra 12 mm til 75 mm. Teknikken passer godt for store konstruksjoner.
Likevel, i en annen teknikk kalt ELECTROSLAG WELDING (ESW) blir lysbuen antent mellom elektroden og bunnen av arbeidsstykket og fluss tilsettes. Når smeltet slagg når elektrodespissen, slukkes lysbuen. Energi tilføres kontinuerlig gjennom den elektriske motstanden til det smeltede slagget. Vi kan sveise plater med tykkelser mellom 50 mm og 900 mm og enda høyere. Strømmen er rundt 600 Ampere mens spenningene er mellom 40 – 50 V. Sveisehastighetene er rundt 12 til 36 mm/min. Bruksområder ligner på elektrogassveising.
En av våre ikke-forbrukbare elektrodeprosesser, GAS TUNGSTEN ARC WELDING (GTAW), også kjent som TUNGSTEN INERT GAS WELDING (TIG), involverer tilførsel av et tilsatsmetall med en ledning. For tettsittende skjøter bruker vi noen ganger ikke tilsatsmetallet. I TIG-prosessen bruker vi ikke fluks, men bruker argon og helium til skjerming. Wolfram har et høyt smeltepunkt og forbrukes ikke i TIG-sveiseprosessen, derfor kan konstant strøm samt lysbuespalter opprettholdes. Effektnivåer er mellom 8 og 20 kW og strømmer på enten 200 Ampere (DC) eller 500 Ampere (AC). For aluminium og magnesium bruker vi vekselstrøm for oksidrensefunksjonen. For å unngå forurensning av wolframelektroden unngår vi kontakten med smeltede metaller. Gass Tungsten Arc Welding (GTAW) er spesielt nyttig for sveising av tynne metaller. GTAW sveiser er av meget høy kvalitet med god overflatefinish.
På grunn av de høyere kostnadene for hydrogengass, er en mindre hyppig brukt teknikk ATOMIC HYDROGEN WELDING (AHW), hvor vi genererer en bue mellom to wolframelektroder i en skjermende atmosfære av flytende hydrogengass. AHW er også en ikke-forbrukbar elektrodesveiseprosess. Den diatomiske hydrogengassen H2 brytes ned til sin atomære form nær sveisebuen der temperaturen er over 6273 Kelvin. Mens den brytes ned, absorberer den store mengder varme fra lysbuen. Når hydrogenatomene treffer sveisesonen som er en relativt kald overflate, rekombinerer de til diatomisk form og frigjør den lagrede varmen. Energi kan varieres ved å endre arbeidsstykket til bueavstand.
I en annen ikke-forbrukbar elektrodeprosess, PLASMA ARC WELDING (PAW), har vi en konsentrert plasmabue rettet mot sveisesonen. Temperaturene når 33.273 Kelvin i PAW. Et nesten like stort antall elektroner og ioner utgjør plasmagassen. En lavstrøms pilotbue initierer plasmaet som er mellom wolframelektroden og åpningen. Driftsstrømmene er vanligvis rundt 100 ampere. Et fyllmetall kan tilføres. Ved plasmabuesveising oppnås skjerming av en ytre skjermring og ved bruk av gasser som argon og helium. Ved plasmabuesveising kan lysbuen være mellom elektroden og arbeidsstykket eller mellom elektroden og dysen. Denne sveiseteknikken har fordelene fremfor andre metoder med høyere energikonsentrasjon, dypere og smalere sveiseevne, bedre buestabilitet, høyere sveisehastigheter opp til 1 meter/min, mindre termisk forvrengning. Vi bruker vanligvis plasmabuesveising for tykkelser mindre enn 6 mm og noen ganger opptil 20 mm for aluminium og titan.
HØYENERGISVEISING: En annen type fusjonssveisemetode med elektronstrålesveising (EBW) og lasersveising (LBW) som to varianter. Disse teknikkene er av spesiell verdi for vårt høyteknologiske produktproduksjonsarbeid. Ved elektronstrålesveising treffer høyhastighetselektroner arbeidsstykket og deres kinetiske energi omdannes til varme. Den smale elektronstrålen beveger seg lett i vakuumkammeret. Generelt bruker vi høyvakuum i e-beam sveising. Plater så tykke som 150 mm kan sveises. Ingen beskyttelsesgasser, flussmiddel eller fyllmateriale er nødvendig. Elektronstrålepistoler har en kapasitet på 100 kW. Dype og smale sveiser med høye sideforhold opp til 30 og små varmepåvirkede soner er mulig. Sveisehastigheter kan nå 12 m/min. Ved laserstrålesveising bruker vi høyeffektlasere som varmekilde. Laserstråler så små som 10 mikron med høy tetthet muliggjør dyp penetrasjon i arbeidsstykket. Dybde-til-bredde-forhold så mye som 10 er mulig med laserstrålesveising. Vi bruker både pulserende og kontinuerlige lasere, med førstnevnte i applikasjoner for tynne materialer og sistnevnte mest for tykke arbeidsstykker opp til ca. 25 mm. Effektnivåer er opptil 100 kW. Laserstrålesveisingen er ikke godt egnet for optisk svært reflekterende materialer. Gasser kan også brukes i sveiseprosessen. Laserstrålesveisemetoden egner seg godt for automatisering og høyvolumproduksjon og kan tilby sveisehastigheter mellom 2,5 m/min og 80 m/min. En stor fordel med denne sveiseteknikken er tilgang til områder hvor andre teknikker ikke kan brukes. Laserstråler kan lett reise til slike vanskelige områder. Ingen vakuum som ved elektronstrålesveising er nødvendig. Sveiser med god kvalitet og styrke, lav krymping, lav forvrengning, lav porøsitet kan oppnås med laserstrålesveising. Laserstråler kan enkelt manipuleres og formes ved hjelp av fiberoptiske kabler. Teknikken er derfor godt egnet for sveising av presisjonshermetiske sammenstillinger, elektroniske pakker...osv.
La oss se på våre SOLID STATE SVEISEteknikker. KALDSVEISING (CW) er en prosess hvor trykk i stedet for varme påføres ved hjelp av dyser eller ruller til delene som er parret. Ved kaldsveising må minst en av de sammenkoblede delene være duktil. Best resultat oppnås med to lignende materialer. Hvis de to metallene som skal sammenføyes med kaldsveising er forskjellige, kan vi få svake og sprø skjøter. Kaldsveisemetoden er godt egnet for myke, duktile og små arbeidsstykker som elektriske koblinger, varmefølsomme beholderkanter, bimetalllister for termostater...osv. En variant av kaldsveising er rullbinding (eller rullsveising), hvor trykket påføres gjennom et par ruller. Noen ganger utfører vi rullesveising ved høye temperaturer for bedre grenseflatestyrke.
En annen solid state sveiseprosess vi bruker er ULTRASONIC WELDING (USW), hvor arbeidsstykkene utsettes for en statisk normalkraft og oscillerende skjærspenninger. De oscillerende skjærspenningene påføres gjennom spissen av en transduser. Ultralydsveising distribuerer oscillasjoner med frekvenser fra 10 til 75 kHz. I noen applikasjoner som sømsveising bruker vi en roterende sveiseskive som spiss. Skjærspenninger påført arbeidsstykkene forårsaker små plastiske deformasjoner, bryter opp oksidlag, forurensninger og fører til faststoffbinding. Temperaturer involvert i ultralydsveising er langt under smeltepunkttemperaturer for metaller og ingen fusjon finner sted. Vi bruker ofte ultralydsveiseprosessen (USW) for ikke-metalliske materialer som plast. I termoplast når temperaturen imidlertid smeltepunkter.
En annen populær teknikk, i FRICTION WELDING (FRW) genereres varmen gjennom friksjon ved grensesnittet mellom arbeidsstykkene som skal sammenføyes. Ved friksjonssveising holder vi ett av arbeidsstykkene stasjonært mens det andre arbeidsstykket holdes i en fikstur og roteres med konstant hastighet. Arbeidsstykkene bringes deretter i kontakt under en aksial kraft. Rotasjonshastigheten på overflaten ved friksjonssveising kan i noen tilfeller nå 900 m/min. Etter tilstrekkelig grenseflatekontakt bringes det roterende arbeidsstykket til bråstopp og aksialkraften økes. Sveisesonen er generelt et smalt område. Friksjonssveiseteknikken kan brukes til å sammenføye solide og rørformede deler laget av en rekke materialer. Noe blits kan utvikles ved grensesnittet i FRW, men denne blitsen kan fjernes ved sekundær maskinering eller sliping. Variasjoner av friksjonssveiseprosessen finnes. For eksempel involverer "treghetsfriksjonssveising" et svinghjul hvis rotasjonskinetiske energi brukes til å sveise delene. Sveisingen er fullført når svinghjulet stopper. Den roterende massen kan varieres og dermed den roterende kinetiske energien. En annen variant er "lineær friksjonssveising", der lineær frem- og tilbakegående bevegelse pålegges minst en av komponentene som skal skjøtes. Ved lineær friksjon trenger sveising ikke å være sirkulære, de kan være rektangulære, kvadratiske eller av annen form. Frekvenser kan være i titalls Hz, amplituder i millimeterområdet og trykk i titalls eller hundrevis av MPa. Til slutt er "friction stir welding" noe annerledes enn de to andre forklart ovenfor. Mens ved treghetsfriksjonssveising og lineær friksjonssveising oppnås oppvarming av grensesnitt gjennom friksjon ved å gni to kontaktflater, i friksjonsomrøringssveisingsmetoden gnis et tredje legeme mot de to overflatene som skal sammenføyes. Et roterende verktøy med en diameter på 5 til 6 mm bringes i kontakt med skjøten. Temperaturene kan øke til verdier mellom 503 til 533 Kelvin. Oppvarming, blanding og omrøring av materialet i fugen foregår. Vi bruker friksjonsrørsveising på en rekke materialer, inkludert aluminium, plast og kompositter. Sveisene er jevne og kvaliteten er høy med minimum porer. Ingen røyk eller sprut produseres ved friksjonsrørsveising, og prosessen er godt automatisert.
MOTSTANDSVEISING (RW): Varmen som kreves for sveising produseres av den elektriske motstanden mellom de to arbeidsstykkene som skal sammenføyes. Ingen flussmiddel, beskyttelsesgasser eller forbrukselektroder brukes i motstandssveising. Joule-oppvarming skjer ved motstandssveising og kan uttrykkes som:
H = (kvadrat I) x R xtx K
H er varme generert i joule (watt-sekunder), I strøm i ampere, R motstand i ohm, t er tiden i sekunder strømmen flyter gjennom. Faktoren K er mindre enn 1 og representerer brøkdelen av energi som ikke går tapt gjennom stråling og ledning. Strømmer i motstandssveiseprosesser kan nå nivåer så høye som 100 000 A, men spenningene er typisk 0,5 til 10 volt. Elektroder er vanligvis laget av kobberlegeringer. Både lignende og forskjellige materialer kan sammenføyes ved motstandssveising. Det finnes flere variasjoner for denne prosessen: "Motstandspunktsveising" involverer to motsatte runde elektroder som kommer i kontakt med overflatene til overlappingsskjøten til de to arkene. Trykk påføres til strømmen slås av. Sveiseklumpen er vanligvis opptil 10 mm i diameter. Motstandspunktsveising etterlater litt misfargede fordypningsmerker ved sveisepunkter. Punktsveising er vår mest populære motstandssveiseteknikk. Ulike elektrodeformer brukes i punktsveising for å nå vanskelige områder. Vårt punktsveiseutstyr er CNC-styrt og har flere elektroder som kan brukes samtidig. En annen variant av "motstandssømsveising" utføres med hjul- eller rulleelektroder som produserer kontinuerlige punktsveisinger når strømmen når et tilstrekkelig høyt nivå i vekselstrømsyklusen. Skjøter produsert ved motstandssømsveising er væske- og gasstette. Sveisehastigheter på ca. 1,5 m/min er normalt for tynne plater. Man kan påføre intermitterende strømmer slik at det produseres punktsveis med ønskede intervaller langs sømmen. Ved "motstandsprojeksjonssveising" preger vi en eller flere fremspring (groper) på en av arbeidsstykkets overflater som skal sveises. Disse fremspringene kan være runde eller ovale. Høye lokaliserte temperaturer oppnås ved disse pregede flekkene som kommer i kontakt med parringsdelen. Elektroder utøver trykk for å komprimere disse fremspringene. Elektroder i motstandsprojeksjonssveising har flate spisser og er vannkjølte kobberlegeringer. Fordelen med motstandsprojeksjonssveising er vår evne til å utføre flere sveiser i ett slag, og dermed den utvidede elektrodelevetiden, evnen til å sveise plater av forskjellige tykkelser, evnen til å sveise muttere og bolter til plater. Ulempen med motstandsprojeksjonssveising er den ekstra kostnaden ved å prege fordypningene. Enda en teknikk, ved "flash-sveising" genereres varme fra lysbuen ved endene av de to arbeidsstykkene når de begynner å komme i kontakt. Denne metoden kan også alternativt betraktes som buesveising. Temperaturen ved grensesnittet stiger, og materialet mykner. En aksial kraft påføres og en sveis dannes ved det mykede området. Etter at hurtigsveisingen er fullført, kan skjøten maskineres for forbedret utseende. Sveisekvaliteten oppnådd ved hurtigsveising er god. Effektnivåer er 10 til 1500 kW. Hurtigsveising er egnet for kant-til-kant-sammenføyning av lignende eller ulikt metall opp til 75 mm diameter og plater mellom 0,2 mm til 25 mm tykkelse. "Stud arc welding" ligner veldig på flash-sveising. Tappen som en bolt eller gjenget stang tjener som én elektrode mens den er sammenføyd med et arbeidsstykke som en plate. For å konsentrere den genererte varmen, forhindre oksidasjon og beholde det smeltede metallet i sveisesonen, plasseres en keramisk engangsring rundt skjøten. Til slutt "slagsveising" en annen motstandssveiseprosess, bruker en kondensator for å levere den elektriske energien. Ved perkusjonssveising utlades kraften i løpet av millisekunder veldig raskt og utvikler høy lokalisert varme ved skjøten. Vi bruker slagsveising mye i elektronikkindustrien hvor oppvarming av sensitive elektroniske komponenter i nærheten av skjøten må unngås.
En teknikk kalt EKSPLOSJONSSVEISING innebærer detonering av et lag med sprengstoff som legges over et av arbeidsstykkene som skal sammenføyes. Det svært høye trykket som utøves på arbeidsstykket gir et turbulent og bølget grensesnitt og mekanisk sammenlåsing finner sted. Bindingsstyrkene ved eksplosiv sveising er svært høye. Eksplosjonssveising er en god metode for kledning av plater med forskjellige metaller. Etter kledning kan platene rulles til tynnere seksjoner. Noen ganger bruker vi eksplosjonssveising for å ekspandere rør slik at de blir tett tett mot platen.
Vår siste metode innenfor domenet solid state-sammenføyning er DIFFUSION BONDING eller DIFFUSION WELDING (DFW) der en god skjøt oppnås hovedsakelig ved diffusjon av atomer over grensesnittet. Noe plastisk deformasjon ved grensesnittet bidrar også til sveisingen. Temperaturer involvert er rundt 0,5 Tm der Tm er smeltetemperaturen til metallet. Bindestyrken ved diffusjonssveising avhenger av trykk, temperatur, kontakttid og renslighet av kontaktflater. Noen ganger bruker vi fyllmetaller i grensesnittet. Varme og trykk kreves i diffusjonsbinding og leveres av elektrisk motstand eller ovn og dødvekter, presse eller annet. Lignende og forskjellige metaller kan sammenføyes med diffusjonssveising. Prosessen er relativt langsom på grunn av tiden det tar for atomer å migrere. DFW kan automatiseres og er mye brukt i produksjon av komplekse deler for romfart, elektronikk, medisinsk industri. Produktene som produseres inkluderer ortopediske implantater, sensorer, strukturelle elementer i luftfarten. Diffusjonsbinding kan kombineres med SUPERPLASTISK FORMING for å fremstille komplekse platemetallstrukturer. Utvalgte steder på arkene blir først diffusjonsbundet, og deretter utvides de ubundne områdene til en form ved hjelp av lufttrykk. Luftfartskonstruksjoner med høye stivhet-til-vekt-forhold er produsert ved å bruke denne kombinasjonen av metoder. Den kombinerte prosessen for diffusjonssveising/superplastforming reduserer antallet deler som kreves ved å eliminere behovet for festemidler, noe som resulterer i lavstressende svært nøyaktige deler økonomisk og med korte ledetider.
LODDING: Lodde- og loddeteknikkene innebærer lavere temperaturer enn de som kreves for sveising. Loddetemperaturer er imidlertid høyere enn loddetemperaturer. Ved lodding plasseres et fyllmetall mellom overflatene som skal sammenføyes og temperaturene heves til smeltetemperaturen til fyllmaterialet over 723 Kelvin, men under smeltetemperaturene til arbeidsstykkene. Det smeltede metallet fyller det tettsittende rommet mellom arbeidsstykkene. Avkjøling og etterfølgende størkning av filtermetallet resulterer i sterke skjøter. Ved loddesveising avsettes tilsatsmetallet ved skjøten. Det brukes betydelig mer tilsatsmetall i loddesveising sammenlignet med lodding. Oksyacetylenbrenner med oksiderende flamme brukes til å avsette fyllmetallet ved loddesveising. På grunn av lavere temperaturer i lodding, er problemer i varmepåvirkede soner som vridning og restspenninger mindre. Jo mindre klaringsgap ved lodding, desto høyere er skjærstyrken til skjøten. Maksimal strekkfasthet oppnås imidlertid ved et optimalt gap (en toppverdi). Under og over denne optimale verdien avtar strekkfastheten ved lodding. Typiske klaringer ved lodding kan være mellom 0,025 og 0,2 mm. Vi bruker en rekke loddematerialer med forskjellige former som performs, pulver, ringer, wire, strips...osv. og kan produsere disse utfører spesielt for ditt design eller produktgeometri. Vi bestemmer også innholdet av loddematerialene i henhold til dine basismaterialer og bruksområder. Vi bruker ofte flussmidler i loddingsoperasjoner for å fjerne uønskede oksidlag og forhindre oksidasjon. For å unngå påfølgende korrosjon, fjernes flussmidler vanligvis etter sammenføyningsoperasjonen. AGS-TECH Inc. bruker ulike loddemetoder, inkludert:
- Lodding av fakkel
- Ovnslodding
- Induksjonslodding
- Motstandslodding
- Dypplodding
- Infrarød lodding
- Diffusjonslodding
- Høyenergistråle
Våre vanligste eksempler på loddede skjøter er laget av forskjellige metaller med god styrke som hardmetallbor, innsatser, optoelektroniske hermetiske pakker, tetninger.
LODNING : Dette er en av våre mest brukte teknikker der loddetinn (fyllmetallet) fyller skjøten som ved lodding mellom tettsittende komponenter. Loddemetallene våre har smeltepunkter under 723 Kelvin. Vi bruker både manuell og automatisert lodding i produksjonsoperasjoner. Sammenlignet med lodding er loddetemperaturene lavere. Lodding er lite egnet for bruk med høy temperatur eller høy styrke. Vi bruker blyfrie loddemetaller samt tinn-bly, tinn-sink, bly-sølv, kadmium-sølv, sink-aluminium legeringer i tillegg til andre for lodding. Både ikke-korrosive harpiksbaserte så vel som uorganiske syrer og salter brukes som flussmiddel ved lodding. Vi bruker spesielle flussmidler for å lodde metaller med lav loddeevne. I applikasjoner hvor vi skal lodde keramiske materialer, glass eller grafitt, belegger vi først delene med et passende metall for økt loddeevne. Våre populære loddeteknikker er:
-Reflow eller Paste Lodding
- Bølgelodding
-Ovnslodding
- Lodding av fakkel
-Induksjonslodding
-Iron Lodding
- Motstandslodding
-Dip lodding
- Ultralyd lodding
-Infrarød lodding
Ultrasonisk lodding gir oss en unik fordel der behovet for flussmidler elimineres på grunn av ultrasonisk kavitasjonseffekt som fjerner oksidfilmer fra overflatene som skal sammenføyes. Reflow og Wave lodding er våre industrielt fremragende teknikker for høyvolumproduksjon innen elektronikk og derfor verdt å forklare nærmere. Ved reflow-lodding bruker vi halvfaste pastaer som inkluderer loddemetallpartikler. Pastaen plasseres på skjøten ved hjelp av en screening- eller stensileringsprosess. I kretskort (PCB) bruker vi ofte denne teknikken. Når elektriske komponenter plasseres på disse putene fra pasta, holder overflatespenningen de overflatemonterte pakkene på linje. Etter å ha plassert komponentene, varmer vi sammenstillingen i en ovn slik at reflow-loddingen finner sted. Under denne prosessen fordamper løsningsmidlene i pastaen, fluksen i pastaen aktiveres, komponentene forvarmes, loddepartiklene smeltes og fukter skjøten, og til slutt avkjøles PCB-enheten sakte. Vår andre populære teknikk for høyvolumproduksjon av PCB-plater, nemlig bølgelodding er avhengig av at smeltet loddemateriale fukter metalloverflater og danner gode bindinger kun når metallet er forvarmet. En stående laminær bølge av smeltet loddemetall genereres først av en pumpe, og de forvarmede og preflukserte PCB-ene føres over bølgen. Loddemetallet fukter bare utsatte metalloverflater, men fukter ikke IC-polymerpakkene eller de polymerbelagte kretskortene. En høyhastighets varmtvannsstråle blåser overflødig loddemetall fra skjøten og forhindrer brodannelse mellom tilstøtende ledninger. Ved bølgelodding av overflatemonterte pakker limer vi dem først til kretskortet før lodding. Igjen brukes skjerming og stensilering, men denne gangen for epoksy. Etter at komponentene er plassert på riktig plassering, er epoksyen herdet, platene snus og bølgelodding finner sted.