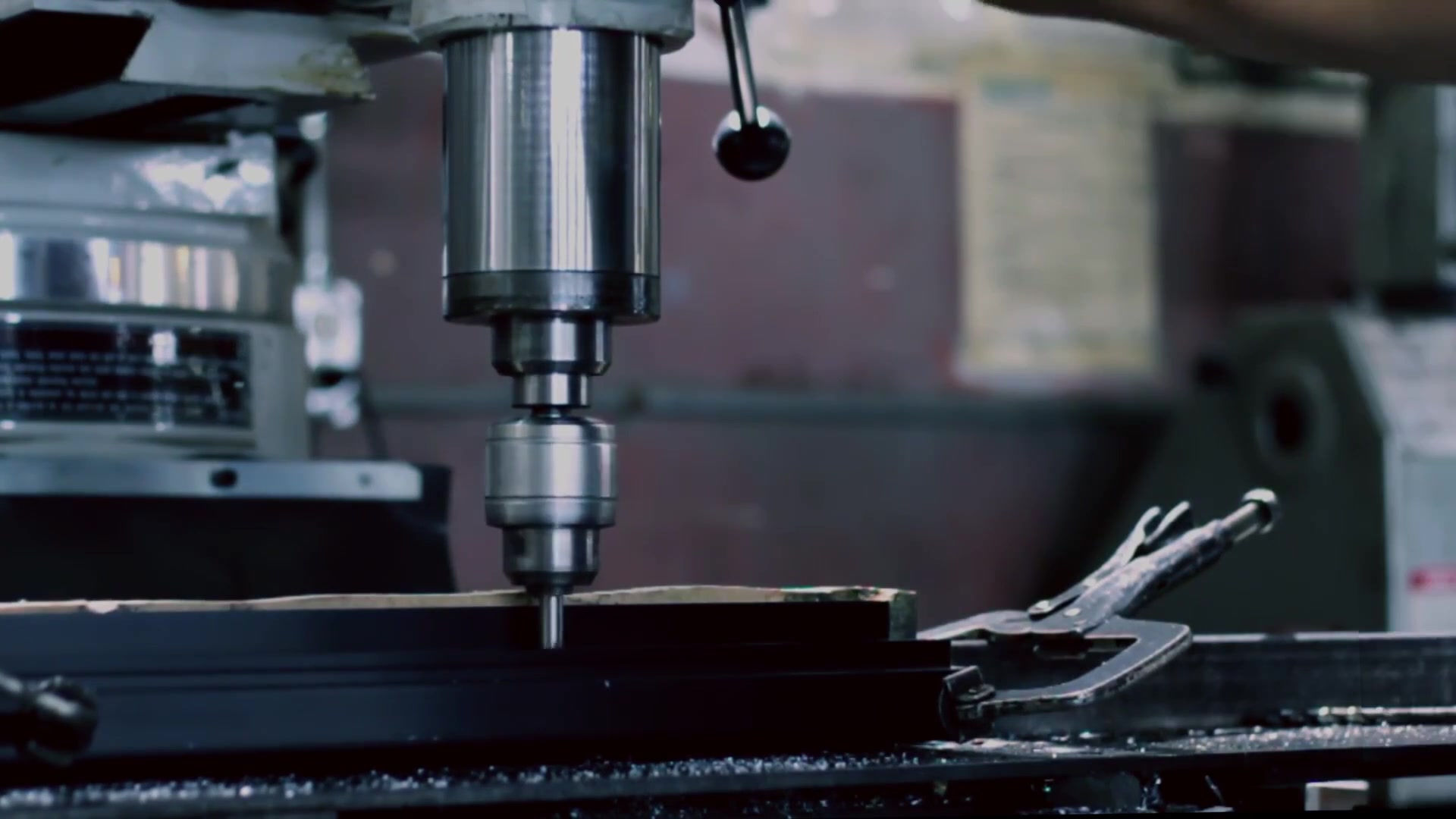
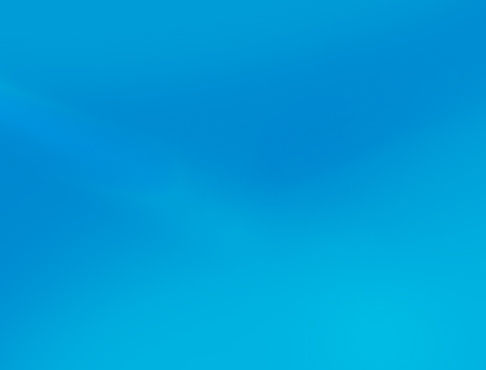
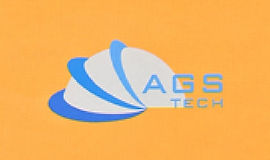
Global Custom Manufacturer, Integrator, Consolidator, Outsourcing Partner for et bredt utvalg av produkter og tjenester.
Vi er din one-stop-kilde for produksjon, fabrikasjon, engineering, konsolidering, integrasjon, outsourcing av spesialproduserte og hylleprodukter og tjenester.
Choose your Language
-
Tilpasset produksjon
-
Innenlandsk og global kontraktsproduksjon
-
Outsourcing av produksjon
-
Innenlandske og globale innkjøp
-
Consolidation
-
Engineering Integration
-
Ingeniørtjenester
Våre tilpassede støpe- og maskineringsteknikker er forbrukbare og ikke-forbrukbare støpegods, jernholdig og ikke-jernholdig støping, sand, dyse, sentrifugal, kontinuerlig, keramisk form, investering, tapt skum, nesten nett-form, permanent form (gravitasjonsstøping), gips støpeform (gipsstøping) og skallavstøpninger, maskinerte deler produsert ved fresing og dreiing ved bruk av konvensjonelt så vel som CNC-utstyr, maskinering av sveitsisk type for høykapasitets rimelige små presisjonsdeler, skruebearbeiding for festemidler, ikke-konvensjonell maskinering. Vær oppmerksom på at i tillegg til metaller og metallegeringer, bearbeider vi keramiske, glass- og plastkomponenter også i noen tilfeller når produksjon av en form ikke er tiltalende eller ikke er alternativet. Maskinering av polymermaterialer krever den spesialiserte erfaringen vi har på grunn av utfordringen plast og gummi gir på grunn av deres mykhet, ikke-stivhet...osv. For maskinering av keramikk og glass, se vår side om ikke-konvensjonell fabrikasjon. AGS-TECH Inc. produserer og leverer både lette og tunge støpegods. Vi har levert metallstøpegods og maskinerte deler til kjeler, varmevekslere, biler, mikromotorer, vindturbiner, matemballasjeutstyr og mer. Vi anbefaler at du klikker her for å LAST NED våre skjematiske illustrasjoner av maskinerings- og støpeprosesser av AGS-TECH Inc.
Dette vil hjelpe deg å bedre forstå informasjonen vi gir deg nedenfor. La oss se på noen av de ulike teknikkene vi tilbyr i detalj:
• FORBRUGSTØPNING: Denne brede kategorien refererer til metoder som involverer midlertidige og ikke-gjenbrukbare former. Eksempler er sand, gips, skall, investering (også kalt tapt-voks) og gipsstøping.
• SANDSTØPING: En prosess der sand brukes som formmateriale. En veldig gammel metode og fortsatt veldig populær i den grad at flertallet av metallstøpegods er laget med denne teknikken. Lave kostnader selv ved lav mengde produksjon. Egnet for produksjon av små og store deler. Teknikken kan brukes til å produsere deler i løpet av dager eller uker med svært liten investering. Den fuktige sanden bindes sammen med leire, bindemidler eller spesialoljer. Sand er vanligvis inneholdt i formbokser og hulrom og portsystem lages ved å komprimere sanden rundt modeller. Prosessene er:
1.) Plassering av modellen i sand for å lage formen
2.) Innbygging av modell og sand i et portsystem
3.) Fjerning av modell
4.) Fylling av formhulrom med smeltet metall
5.) Avkjøling av metallet
6.) Knusing av sandformen og fjerning av støpegodset
• GIPSSTØPING: I likhet med sandstøping, og i stedet for sand, brukes gips som støpemateriale. Kort produksjonstid som sandstøping og rimelig. Gode dimensjonstoleranser og overflatefinish. Den største ulempen er at den bare kan brukes med metaller med lavt smeltepunkt som aluminium og sink.
• SKALLSTØPNING: Ligner også på sandstøping. Mugghulrom oppnådd ved herdet skall av sand og termoherdende harpiksbindemiddel i stedet for en kolbe fylt med sand som i sandstøpeprosessen. Nesten ethvert metall som er egnet til å støpes med sand, kan støpes ved skallstøping. Prosessen kan oppsummeres som:
1.) Produksjon av skallformen. Sand som brukes har en mye mindre kornstørrelse sammenlignet med sand som brukes i sandstøping. Den fine sanden er blandet med herdeplast. Metallmønsteret er belagt med et skillemiddel for å gjøre fjerning av skallet lettere. Deretter varmes metallmønsteret opp og sandblandingen poreres eller blåses inn i det varme støpemønsteret. Et tynt skall dannes på overflaten av mønsteret. Tykkelsen på dette skallet kan justeres ved å variere hvor lenge sandharpiksblandingen er i kontakt med metallmønsteret. Den løse sanden fjernes deretter med det skalldekkede mønsteret igjen.
2.) Deretter varmes skallet og mønsteret i en ovn slik at skallet stivner. Etter at herdingen er fullført, kastes skallet ut av mønsteret ved hjelp av pinner innebygd i mønsteret.
3.) To slike skjell settes sammen ved å lime eller klemme og utgjøre hele formen. Nå settes skallformen inn i en beholder der den støttes av sand eller metallhagl under støpeprosessen.
4.) Nå kan det varme metallet helles i skallformen.
Fordeler med skallstøping er produkter med meget god overflatefinish, mulighet for å produsere komplekse deler med høy dimensjonsnøyaktighet, prosess lett å automatisere, økonomisk for store volumproduksjoner.
Ulempene er at formene krever god ventilasjon på grunn av gasser som dannes når smeltet metall kommer i kontakt med bindemiddelkjemikaliet, de herdeplastiske harpiksene og metallmønstrene er dyre. På grunn av kostnadene ved metallmønstre, kan det hende at teknikken ikke egner seg godt for små produksjonskjøringer.
• INVESTERINGSTØPING (også kjent som LOST-WAX CASTING): Også en svært gammel teknikk og egnet for produksjon av kvalitetsdeler med høy nøyaktighet, repeterbarhet, allsidighet og integritet fra mange metaller, ildfaste materialer og spesielle høyytelseslegeringer. Små så vel som store deler kan produseres. En kostbar prosess sammenlignet med noen av de andre metodene, men en stor fordel er muligheten til å produsere deler med nesten netto form, intrikate konturer og detaljer. Så kostnadene er noe oppveid av eliminering av omarbeid og maskinering i noen tilfeller. Selv om det kan være variasjoner, er her et sammendrag av den generelle investeringsavstøpningsprosessen:
1.) Oppretting av originalt mastermønster fra voks eller plast. Hver avstøpning trenger ett mønster da disse blir ødelagt i prosessen. Det er også nødvendig med støpeform som mønstre produseres fra, og det meste av tiden er støpeformen eller maskinert. Fordi formen ikke trenger å åpnes, kan komplekse støpinger oppnås, mange voksmønstre kan kobles sammen som grenene på et tre og helles sammen, og dermed muliggjøre produksjon av flere deler fra en enkelt støping av metallet eller metallegeringen.
2.) Deretter dyppes eller helles mønsteret over med en ildfast oppslemming som består av veldig finkornet silika, vann, bindemidler. Dette resulterer i et keramisk lag over overflaten av mønsteret. Det ildfaste strøket på mønster får tørke og stivne. Dette trinnet er der navnet investeringsstøping kommer fra: Ildfast slurry legges over voksmønsteret.
3.) På dette trinnet snus den herdede keramiske formen opp ned og varmes opp slik at voksen smelter og renner ut av formen. Et hulrom er igjen for metallstøpingen.
4.) Etter at voksen er ute, varmes den keramiske formen opp til enda høyere temperatur som resulterer i forsterkning av formen.
5.) Metallstøping helles i den varme formen som fyller alle intrikate seksjoner.
6.) Støping får stivne
7.) Til slutt brytes den keramiske formen og produserte deler kuttes fra treet.
Her er en lenke til Brosjyre for Investment Casting Plant
• STØPING AV EVAPORATIV MØNSTER: Prosessen bruker et mønster laget av et materiale som polystyrenskum som vil fordampe når varmt smeltet metall helles i formen. Det er to typer av denne prosessen: LOST FOAM CASTING som bruker ubundet sand og FULL MOLD CASTING som bruker limt sand. Her er de generelle prosesstrinnene:
1.) Lag mønsteret av et materiale som polystyren. Når store mengder skal produseres, støpes mønsteret. Hvis en del har en kompleks form, kan det hende at flere seksjoner av slikt skummateriale må limes sammen for å danne mønsteret. Vi belegger ofte mønsteret med en ildfast blanding for å skape en god overflatefinish på støpen.
2.) Mønsteret legges deretter i formsand.
3.) Det smeltede metallet helles i formen, og fordamper skummønsteret, dvs. polystyren i de fleste tilfeller når det strømmer gjennom formhulen.
4.) Det smeltede metallet blir liggende i sandformen for å herde.
5.) Etter at den er herdet, fjerner vi støpen.
I noen tilfeller krever produktet vi produserer en kjerne i mønsteret. Ved evaporativ støping er det ikke nødvendig å plassere og sikre en kjerne i formhulen. Teknikken egner seg for fremstilling av svært komplekse geometrier, den kan enkelt automatiseres for høyvolumproduksjon, og det er ingen skillelinjer i den støpte delen. Den grunnleggende prosessen er enkel og økonomisk å implementere. For store volumproduksjoner, siden en dyse eller form er nødvendig for å produsere mønstrene fra polystyren, kan dette være noe kostbart.
• IKKE-EKSPANDERBAR STØPING: Denne brede kategorien refererer til metoder der formen ikke trenger å reformeres etter hver produksjonssyklus. Eksempler er permanent, dyse, kontinuerlig og sentrifugalstøping. Repeterbarhet oppnås og deler kan karakteriseres som NÆR NETTOFORM.
• PERMANENT STØPING: Gjenbrukbare former laget av metall brukes til flere støpinger. En permanent form kan vanligvis brukes i titusenvis av ganger før den slites ut. Tyngdekraft, gasstrykk eller vakuum brukes vanligvis til å fylle formen. Former (også kalt form) er vanligvis laget av jern, stål, keramikk eller andre metaller. Den generelle prosessen er:
1.) Maskin og lag formen. Det er vanlig å maskinere formen av to metallblokker som passer sammen og kan åpnes og lukkes. Både delfunksjonene så vel som portsystemet er vanligvis maskinert inn i støpeformen.
2.) De indre formoverflatene er belagt med en slurry som inneholder ildfaste materialer. Dette bidrar til å kontrollere varmestrømmen og fungerer som et smøremiddel for enkel fjerning av den støpte delen.
3.) Deretter lukkes de permanente formhalvdelene og formen varmes opp.
4.) Smeltet metall helles i form og la stille for størkning.
5.) Før mye avkjøling skjer, fjerner vi delen fra permanent form ved hjelp av ejektorer når formhalvdelene åpnes.
Vi bruker ofte permanent formstøping for metaller med lavt smeltepunkt som sink og aluminium. For stålstøpegods bruker vi grafitt som formmateriale. Noen ganger oppnår vi komplekse geometrier ved å bruke kjerner i permanente former. Fordeler med denne teknikken er støpegods med gode mekaniske egenskaper oppnådd ved rask avkjøling, ensartethet i egenskaper, god nøyaktighet og overflatefinish, lave avslagsrater, mulighet for å automatisere prosessen og produsere høye volumer økonomisk. Ulemper er høye initiale installasjonskostnader som gjør den uegnet for operasjoner med lavt volum, og begrensninger på størrelsen på delene som produseres.
• DISTØPING: En dyse maskineres og smeltet metall skyves under høyt trykk inn i formhulrom. Både ikke-jernholdige så vel som jernholdige metaller er mulige. Prosessen er egnet for store produksjonsserier av små til mellomstore deler med detaljer, ekstremt tynne vegger, dimensjonskonsistens og god overflatefinish. AGS-TECH Inc. er i stand til å produsere veggtykkelser så små som 0,5 mm ved hjelp av denne teknikken. Som ved permanent formstøping, må formen bestå av to halvdeler som kan åpnes og lukkes for fjerning av produsert del. En støpeform kan ha flere hulrom for å muliggjøre produksjon av flere støpegods med hver syklus. Pressstøpeformer er veldig tunge og mye større enn delene de produserer, derfor også dyre. Vi reparerer og erstatter utslitte dyser gratis for våre kunder så lenge de bestiller deler hos oss. Dysene våre har lang levetid i flere hundre tusen sykluser.
Her er de grunnleggende forenklede prosesstrinnene:
1.) Produksjon av formen generelt fra stål
2.) Form installert på støpemaskin
3.) Stempelet tvinger smeltet metall til å strømme inn i formhulene og fyller ut de intrikate funksjonene og tynne veggene
4.) Etter å ha fylt formen med det smeltede metallet, lar støpingen herde under trykk
5.) Form åpnes og støping fjernes ved hjelp av utkasterstifter.
6.) Nå smøres den tomme dysen igjen og klemmes fast for neste syklus.
Ved trykkstøping bruker vi ofte innleggsstøping hvor vi inkorporerer en ekstra del i formen og støper metallet rundt den. Etter størkning blir disse delene en del av det støpte produktet. Fordeler med støping er gode mekaniske egenskaper til delene, mulighet for intrikate egenskaper, fine detaljer og god overflatefinish, høy produksjonshastighet, enkel automatisering. Ulemper er: Ikke særlig egnet for lavt volum på grunn av høye dyse- og utstyrskostnader, begrensninger i former som kan støpes, små runde merker på støpte deler som følge av kontakt med ejektorstifter, tynn metallglimt presset ut ved skillelinjen, behov for ventiler langs skillelinjen mellom dysen, nødvendigheten av å holde formtemperaturen lav ved bruk av vannsirkulasjon.
• SENTRIFUGAL STØPING: Smeltet metall helles inn i midten av den roterende formen ved rotasjonsaksen. Sentrifugalkrefter kaster metallet mot periferien og lar det stivne mens formen fortsetter å rotere. Både horisontale og vertikale akserotasjoner kan brukes. Deler med runde innerflater samt andre ikke-runde former kan støpes. Prosessen kan oppsummeres som:
1.) Smeltet metall helles i sentrifugalform. Metallet blir deretter tvunget til ytterveggene på grunn av spinning av formen.
2.) Når formen roterer, stivner metallstøpen
Sentrifugalstøping er en egnet teknikk for produksjon av hule sylindiriske deler som rør, ikke behov for innløp, stigerør og portelementer, god overflatefinish og detaljerte egenskaper, ingen krympeproblemer, mulighet for å produsere lange rør med svært store diametre, høyhastighets produksjonsevne .
• KONTINUERLIG STØPING ( STRANDSTØPING ): Brukes til å støpe en kontinuerlig lengde av metall. I utgangspunktet er det smeltede metallet støpt inn i todimensjonal profil av formen, men lengden er ubestemt. Nytt smeltet metall mates konstant inn i formen når støpegodset beveger seg nedover med lengden økende med tiden. Metaller som kobber, stål, aluminium støpes til lange tråder ved hjelp av kontinuerlig støpeprosess. Prosessen kan ha forskjellige konfigurasjoner, men den vanlige kan forenkles som:
1.) Smeltet metall helles i en beholder plassert høyt over formen med godt beregnede mengder og strømningshastigheter og strømmer gjennom den vannkjølte formen. Metallstøpingen som helles i formen størkner til en startstang plassert i bunnen av formen. Denne startstangen gir rullene noe å ta tak i til å begynne med.
2.) Den lange metallstrengen bæres av ruller med konstant hastighet. Rullene endrer også retningen på strømmen av metalltråd fra vertikal til horisontal.
3.) Etter at den kontinuerlige støpingen har tilbakelagt en viss horisontal avstand, skjærer en brenner eller sag som beveger seg med støpen raskt den til ønskede lengder.
Kontinuerlig støpeprosess kan integreres med RULLING PROCESS, hvor det kontinuerlig støpte metallet kan mates direkte inn i et valseverk for å produsere I-Beams, T-Beams….osv. Kontinuerlig støping gir ensartede egenskaper gjennom hele produktet, den har høy størkningshastighet, reduserer kostnadene på grunn av svært lavt materialetap, tilbyr en prosess hvor lasting av metall, støping, størkning, skjæring og støpefjerning alt skjer i en kontinuerlig operasjon og resulterer dermed i høy produktivitet og høy kvalitet. En viktig faktor er imidlertid den høye initialinvesteringen, oppsettskostnadene og plassbehovet.
• MASKINERINGSTJENESTER: Vi tilbyr tre-, fire- og femakset maskinering. Typen maskineringsprosesser vi bruker er DREIING, FRESING, BORING, BORING, BROASJING, HØVLING, SAGING, SLIPPING, LAPPING, POLERING og IKKE-TRADISJONELL MASKINERING som er videreutviklet under en annen meny på nettsiden vår. For det meste av vår produksjon bruker vi CNC-maskiner. Men for noen operasjoner passer konvensjonelle teknikker bedre, og derfor stoler vi på dem også. Våre maskineringsevner når det høyest mulige nivået, og noen mest krevende deler er produsert på et AS9100-sertifisert anlegg. Jetmotorblader krever høyspesialisert produksjonserfaring og riktig utstyr. Luftfartsindustrien har svært strenge standarder. Noen komponenter med komplekse geometriske strukturer produseres lettest ved femakset maskinering, som bare finnes i noen maskineringsanlegg inkludert vårt. Vårt luftfartssertifiserte anlegg har den nødvendige erfaringen i samsvar med omfattende dokumentasjonskrav fra luftfartsindustrien.
Ved DREI-operasjoner roteres et arbeidsstykke og flyttes mot et skjæreverktøy. For denne prosessen brukes en maskin kalt dreiebenk.
I FRESING har en maskin kalt fresemaskin et roterende verktøy for å bringe skjærekanter til å ligge mot et arbeidsstykke.
BORING involverer en roterende kutter med skjærekanter som produserer hull ved kontakt med arbeidsstykket. Borepresser, dreiebenker eller freser brukes vanligvis.
I BORING-operasjoner flyttes et verktøy med en enkelt bøyd spiss inn i et grovt hull i et spinnende arbeidsstykke for å forstørre hullet litt og forbedre nøyaktigheten. Den brukes til fine etterbehandlingsformål.
BRASJING involverer et tannverktøy for å fjerne materiale fra et arbeidsstykke i én omgang av brosjen (tannet verktøy). Ved lineær broasing løper brosjen lineært mot en overflate av arbeidsstykket for å utføre kuttet, mens ved roterende broaching roteres brosjen og presses inn i arbeidsstykket for å kutte en aksesymmetrisk form.
SWISS TYPE MACHINING er en av våre verdifulle teknikker vi bruker for høyvolumsproduksjon av små høypresisjonsdeler. Ved å bruke dreiebenk av sveitsisk type dreier vi små, komplekse, presisjonsdeler billig. I motsetning til konvensjonelle dreiebenker der arbeidsstykket holdes stasjonært og verktøyet beveger seg, i dreiesentre av sveitsisk type, tillates arbeidsstykket å bevege seg i Z-aksen og verktøyet er stasjonært. Ved bearbeiding av sveitsisk type holdes stangen i maskinen og føres frem gjennom en styrebøssing i z-aksen, og blottlegger bare delen som skal bearbeides. På denne måten sikres et stramt grep og nøyaktigheten er meget høy. Tilgjengeligheten av strømførende verktøy gir mulighet til å frese og bore etter hvert som materialet går videre fra føringsbøssingen. Y-aksen til utstyret av sveitsisk type gir fulle fresemuligheter og sparer mye tid i produksjonen. Videre har våre maskiner bor og boreverktøy som opererer på delen når den holdes i underspindelen. Vår sveitsiske maskineringsevne gir oss en helautomatisert komplett maskineringsmulighet i en enkelt operasjon.
Maskinering er et av de største segmentene i AGS-TECH Inc.-virksomheten. Vi bruker den enten som en primær operasjon eller en sekundær operasjon etter støping eller ekstrudering av en del slik at alle tegningsspesifikasjoner oppfylles.
• OVERFLATEBEHANDLING: Vi tilbyr et stort utvalg av overflatebehandlinger og overflatebehandling, for eksempel overflatebehandling for å forbedre vedheft, avsetning av tynt oksidlag for å forbedre vedheft av belegg, sandblåsing, kjemisk film, anodisering, nitrering, pulverlakkering, spraybelegg , ulike avanserte metalliserings- og belegningsteknikker inkludert sputtering, elektronstråle, fordampning, plettering, harde belegg som diamantlignende karbon (DLC) eller titanbelegg for bore- og skjæreverktøy.
• PRODUKTMERKING OG ETIKETTER: Mange av våre kunder krever merking og merking, lasermerking, gravering på metalldeler. Hvis du har et slikt behov, la oss diskutere hvilket alternativ som passer best for deg.
Her er noen av de mest brukte metallstøpte produktene. Siden disse er hyllevare, kan du spare på muggkostnader i tilfelle noen av disse passer dine behov:
KLIKK HER FOR Å LASTE NED våre 11-serie pressstøpte aluminiumsbokser fra AGS-Electronics