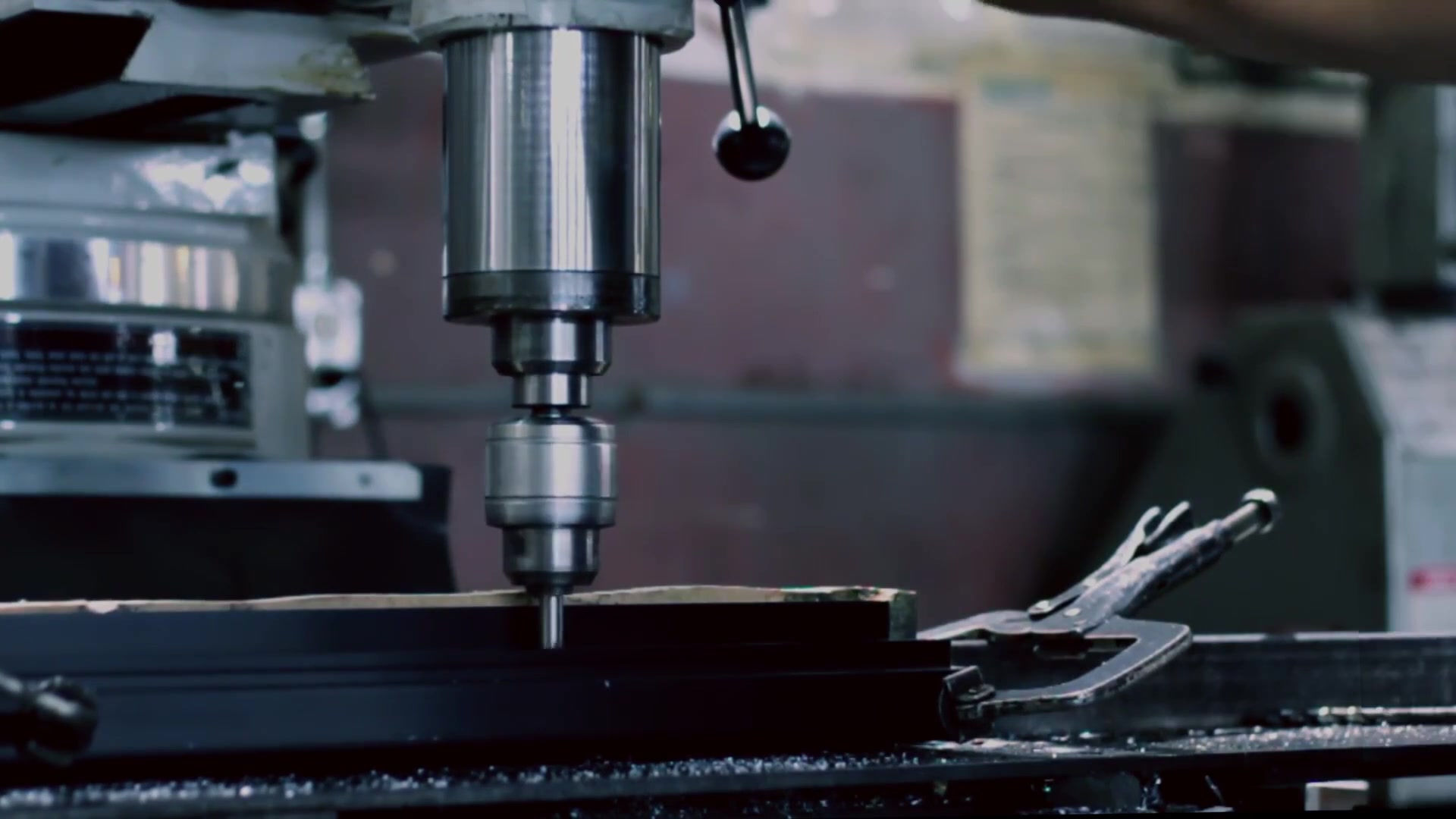
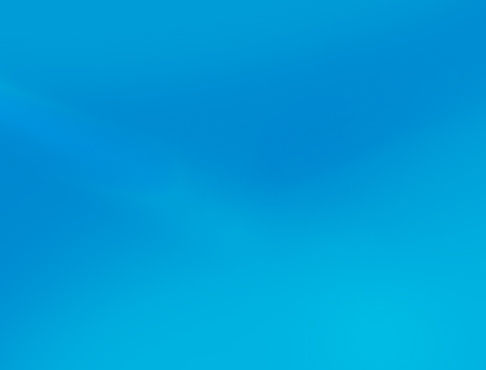
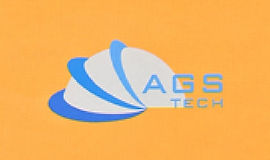
Fabricante personalizado global, integrador, consolidador, parceiro de terceirização para uma ampla variedade de produtos e serviços.
Somos sua fonte única para fabricação, fabricação, engenharia, consolidação, integração, terceirização de produtos e serviços fabricados sob encomenda e prontos para uso.
Choose your Language
-
Fabricação personalizada
-
Fabricação por contrato doméstica e global
-
Terceirização de Manufatura
-
Compras domésticas e globais
-
Consolidação
-
Integração de Engenharia
-
Serviços de engenharia
Simplificando, COMPÓSITOS ou MATERIAIS COMPOSTOS são materiais que consistem em dois ou vários materiais com diferentes propriedades físicas ou químicas, mas quando combinados tornam-se um material diferente dos materiais constituintes. Precisamos salientar que os materiais constituintes permanecem separados e distintos na estrutura. O objetivo na fabricação de um material compósito é obter um produto que seja superior aos seus constituintes e combine as características desejadas de cada constituinte. Como um exemplo; resistência, baixo peso ou preço mais baixo podem ser o motivador por trás do projeto e produção de um compósito. O tipo de compósitos que oferecemos são compósitos reforçados com partículas, compósitos reforçados com fibra, incluindo compósitos de matriz cerâmica / matriz polimérica / matriz metálica / carbono-carbono / híbridos, compósitos estruturais e laminados e estruturados em sanduíche e nanocompósitos.
As técnicas de fabricação que implantamos na fabricação de materiais compósitos são: Pultrusão, processos de produção de prepreg, colocação avançada de fibra, enrolamento de filamento, colocação de fibra sob medida, processo de laminação por spray de fibra de vidro, tufting, processo de lanxide, z-pinning.
Muitos materiais compósitos são constituídos por duas fases, a matriz, que é contínua e envolve a outra fase; e a fase dispersa que está rodeada pela matriz.
Recomendamos que você clique aqui paraBAIXE nossas Ilustrações Esquemáticas de Compósitos e Fabricação de Materiais Compósitos pela AGS-TECH Inc.
Isso ajudará você a entender melhor as informações que fornecemos abaixo.
• COMPÓSITOS REFORÇADOS COM PARTÍCULAS: Esta categoria consiste em dois tipos: compósitos de partículas grandes e compósitos reforçados por dispersão. No primeiro tipo, as interações partícula-matriz não podem ser tratadas no nível atômico ou molecular. Em vez disso, a mecânica contínua é válida. Por outro lado, em compósitos reforçados por dispersão, as partículas são geralmente muito menores na faixa de dezenas de nanômetros. Um exemplo de compósito de partículas grandes são os polímeros aos quais foram adicionados enchimentos. As cargas melhoram as propriedades do material e podem substituir parte do volume do polímero por um material mais econômico. As frações volumétricas das duas fases influenciam o comportamento do compósito. Compósitos de partículas grandes são usados com metais, polímeros e cerâmicas. Os CERMETS são exemplos de compósitos cerâmicos/metálicos. Nosso cermet mais comum é o metal duro. Consiste em cerâmica de carboneto refratário, como partículas de carboneto de tungstênio em uma matriz de um metal como cobalto ou níquel. Esses compósitos de carboneto são amplamente utilizados como ferramentas de corte para aço endurecido. As partículas de metal duro são responsáveis pela ação de corte e sua tenacidade é reforçada pela matriz metálica dúctil. Assim obtemos as vantagens de ambos os materiais em um único compósito. Outro exemplo comum de um compósito de partículas grandes que usamos são partículas de negro de fumo misturadas com borracha vulcanizada para obter um compósito com alta resistência à tração, tenacidade, rasgo e resistência à abrasão. Um exemplo de compósito reforçado por dispersão são metais e ligas metálicas reforçadas e endurecidas pela dispersão uniforme de partículas finas de um material muito duro e inerte. Quando flocos de óxido de alumínio muito pequenos são adicionados à matriz metálica de alumínio, obtemos pó de alumínio sinterizado que possui uma resistência aprimorada a altas temperaturas.
• COMPÓSITOS REFORÇADOS COM FIBRA: Esta categoria de compósitos é de fato a mais importante. O objetivo a atingir é alta resistência e rigidez por unidade de peso. A composição da fibra, comprimento, orientação e concentração nestes compósitos são críticos na determinação das propriedades e utilidade destes materiais. Existem três grupos de fibras que usamos: bigodes, fibras e fios. Os bigodes são cristais únicos muito finos e longos. Eles estão entre os materiais mais fortes. Alguns exemplos de materiais de bigode são grafite, nitreto de silício, óxido de alumínio. FIBERS por outro lado são principalmente polímeros ou cerâmicas e estão em estado policristalino ou amorfo. O terceiro grupo são os FIOS finos que possuem diâmetros relativamente grandes e consistem frequentemente em aço ou tungstênio. Um exemplo de compósito reforçado com arame são os pneus de carro que incorporam arame de aço dentro da borracha. Dependendo do material da matriz, temos os seguintes compósitos:
COMPOSTOS DE MATRIZ POLÍMERO: São compostos de resina polimérica e fibras como ingrediente de reforço. Um subgrupo desses chamados compósitos de polímero reforçado com fibra de vidro (GFRP) contém fibras de vidro contínuas ou descontínuas dentro de uma matriz polimérica. O vidro oferece alta resistência, é econômico, fácil de fabricar em fibras e é quimicamente inerte. As desvantagens são sua rigidez e rigidez limitadas, sendo as temperaturas de serviço apenas de 200 a 300 centígrados. A fibra de vidro é adequada para carrocerias automotivas e equipamentos de transporte, carrocerias de veículos marítimos, contêineres de armazenamento. Eles não são adequados para aeroespacial nem para construção de pontes devido à rigidez limitada. O outro subgrupo é chamado de Composto de Polímero Reforçado com Fibra de Carbono (CFRP). Aqui, o carbono é nosso material de fibra na matriz polimérica. O carbono é conhecido por seu alto módulo específico e resistência e sua capacidade de mantê-los em altas temperaturas. As fibras de carbono podem nos oferecer módulos de tração padrão, intermediários, altos e ultraelevados. Além disso, as fibras de carbono oferecem diversas características físicas e mecânicas e, portanto, adequadas para várias aplicações de engenharia personalizadas. Os compósitos de CFRP podem ser considerados para fabricar equipamentos esportivos e recreativos, vasos de pressão e componentes estruturais aeroespaciais. Ainda, outro subgrupo, os Compósitos Poliméricos Reforçados com Fibra de Aramida também são materiais de alta resistência e módulo. Suas relações força-peso são extraordinariamente altas. As fibras de aramida também são conhecidas pelos nomes comerciais KEVLAR e NOMEX. Sob tensão, eles têm um desempenho melhor do que outros materiais de fibra polimérica, mas são fracos em compressão. As fibras de aramida são resistentes, resistentes ao impacto, à fluência e à fadiga, estáveis em altas temperaturas, quimicamente inertes, exceto contra ácidos e bases fortes. As fibras de aramida são amplamente utilizadas em artigos esportivos, coletes à prova de balas, pneus, cordas, revestimentos de cabos de fibra óptica. Existem outros materiais de reforço de fibra, mas são usados em menor grau. Estes são boro, carboneto de silício, óxido de alumínio principalmente. O material da matriz polimérica, por outro lado, também é crítico. Ela determina a temperatura máxima de serviço do compósito porque o polímero tem geralmente uma temperatura de fusão e degradação mais baixa. Poliésteres e ésteres vinílicos são amplamente utilizados como matriz polimérica. Resinas também são utilizadas e possuem excelente resistência à umidade e propriedades mecânicas. Por exemplo, a resina de poliimida pode ser usada até cerca de 230 graus Celsius.
COMPOSTOS DE METAL-MATRIZ : Nestes materiais utilizamos uma matriz metálica dúctil e as temperaturas de serviço são geralmente superiores aos seus componentes constituintes. Quando comparados aos compósitos de matriz polimérica, estes podem ter temperaturas de operação mais altas, ser não inflamáveis e podem ter melhor resistência à degradação contra fluidos orgânicos. No entanto são mais caros. Materiais de reforço como bigodes, partículas, fibras contínuas e descontínuas; e materiais de matriz como cobre, alumínio, magnésio, titânio, superligas estão sendo comumente usados. Exemplos de aplicações são componentes do motor feitos de matriz de liga de alumínio reforçada com óxido de alumínio e fibras de carbono.
COMPOSTOS DE MATRIZ CERÂMICA: Os materiais cerâmicos são conhecidos por sua excelente confiabilidade em altas temperaturas. No entanto, são muito frágeis e apresentam baixos valores de tenacidade à fratura. Ao incorporar partículas, fibras ou whiskers de uma cerâmica na matriz de outra, podemos obter compósitos com maior tenacidade à fratura. Esses materiais embutidos basicamente inibem a propagação de trincas dentro da matriz por meio de alguns mecanismos, como desviar as pontas das trincas ou formar pontes entre as faces das trincas. Como exemplo, as aluminas que são reforçadas com whiskers de SiC são usadas como insertos de ferramentas de corte para usinagem de ligas de metal duro. Estes podem revelar melhores desempenhos em comparação com os carbonetos cimentados.
COMPOSTOS DE CARBONO-CARBONO: Tanto o reforço como a matriz são de carbono. Eles têm módulos de alta resistência à tração e resistência a altas temperaturas acima de 2000 graus centígrados, resistência à fluência, alta tenacidade à fratura, baixos coeficientes de expansão térmica, alta condutividade térmica. Essas propriedades os tornam ideais para aplicações que exigem resistência ao choque térmico. A fraqueza dos compósitos carbono-carbono é, no entanto, sua vulnerabilidade à oxidação em altas temperaturas. Exemplos típicos de uso são moldes de prensagem a quente, fabricação avançada de componentes de motores de turbina.
COMPOSTOS HÍBRIDOS: Dois ou mais tipos diferentes de fibras são misturados em uma única matriz. Assim, pode-se adaptar um novo material com uma combinação de propriedades. Um exemplo é quando ambas as fibras de carbono e de vidro são incorporadas em uma resina polimérica. As fibras de carbono fornecem rigidez e resistência de baixa densidade, mas são caras. O vidro, por outro lado, é barato, mas não tem a rigidez das fibras de carbono. O compósito híbrido vidro-carbono é mais forte e resistente e pode ser fabricado a um custo menor.
PROCESSAMENTO DE COMPÓSITOS REFORÇADOS COM FIBRA: Para plásticos reforçados com fibra contínuos com fibras uniformemente distribuídas orientadas na mesma direção, usamos as seguintes técnicas.
PULTRUSÃO: São fabricados varões, vigas e tubos de comprimentos contínuos e seções transversais constantes. As mechas contínuas de fibra são impregnadas com uma resina termofixa e são puxadas através de uma matriz de aço para preformá-las na forma desejada. Em seguida, eles passam por uma matriz de cura usinada com precisão para atingir sua forma final. Como o molde de cura é aquecido, ele cura a matriz de resina. Os extratores puxam o material através das matrizes. Utilizando núcleos ocos inseridos, conseguimos obter tubos e geometrias ocas. O método de pultrusão é automatizado e nos oferece altas taxas de produção. Qualquer comprimento de produto é possível produzir.
PROCESSO DE PRODUÇÃO PREPREG: Prepreg é um reforço de fibra contínua pré-impregnado com uma resina polimérica parcialmente curada. É amplamente utilizado para aplicações estruturais. O material vem em forma de fita e é enviado como uma fita. O fabricante o molda diretamente e o cura totalmente sem a necessidade de adicionar qualquer resina. Como os pré-impregnados sofrem reações de cura à temperatura ambiente, eles são armazenados a 0 graus centígrados ou temperaturas inferiores. Após o uso, as fitas restantes são armazenadas de volta em baixas temperaturas. Resinas termoplásticas e termofixas são usadas e fibras de reforço de carbono, aramida e vidro são comuns. Para usar prepregs, o papel de suporte do suporte é primeiro removido e, em seguida, a fabricação é realizada colocando a fita prepreg em uma superfície moldada (o processo de lay-up). Várias camadas podem ser colocadas para obter as espessuras desejadas. A prática frequente é alternar a orientação da fibra para produzir um laminado de dobra cruzada ou dobrada. Finalmente, calor e pressão são aplicados para a cura. Tanto o processamento manual quanto os processos automatizados são usados para cortar prepregs e lay-up.
ENROLAMENTO DE FILAMENTO: As fibras de reforço contínuas são posicionadas com precisão em um padrão predeterminado para seguir uma forma oca e geralmente cilíndrica. As fibras passam primeiro por um banho de resina e depois são enroladas em um mandril por um sistema automatizado. Após várias repetições de enrolamento, as espessuras desejadas são obtidas e a cura é realizada à temperatura ambiente ou dentro de um forno. Agora o mandril é removido e o produto é desmoldado. O enrolamento do filamento pode oferecer relações resistência-peso muito altas ao enrolar as fibras em padrões circunferenciais, helicoidais e polares. Tubos, tanques, invólucros são fabricados usando esta técnica.
• COMPÓSITOS ESTRUTURAIS: Geralmente são compostos por materiais homogêneos e compostos. Portanto, as propriedades destes são determinadas pelos materiais constituintes e desenho geométrico de seus elementos. Aqui estão os principais tipos:
COMPOSTOS LAMINAR: Estes materiais estruturais são feitos de chapas ou painéis bidimensionais com direções de alta resistência preferidas. As camadas são empilhadas e cimentadas juntas. Alternando as direções de alta resistência nos dois eixos perpendiculares, obtemos um compósito que possui alta resistência em ambas as direções no plano bidimensional. Ajustando os ângulos das camadas pode-se fabricar um compósito com resistência nas direções preferidas. O esqui moderno é fabricado dessa maneira.
PAINÉIS SANDWICH : Esses compósitos estruturais são leves, mas possuem alta rigidez e resistência. Os painéis sanduíche consistem em duas folhas externas feitas de um material rígido e forte, como ligas de alumínio, plásticos reforçados com fibra ou aço e um núcleo entre as folhas externas. O núcleo precisa ser leve e na maioria das vezes ter um baixo módulo de elasticidade. Os materiais de núcleo populares são espumas poliméricas rígidas, madeira e favos de mel. Os painéis sanduíche são amplamente utilizados na indústria da construção como material de cobertura, piso ou parede, e também nas indústrias aeroespaciais.
• NANOCOMPÓSITOS: Esses novos materiais consistem em partículas nanométricas embutidas em uma matriz. Usando nanocompósitos, podemos fabricar materiais de borracha que são barreiras muito boas à penetração do ar, mantendo suas propriedades de borracha inalteradas.