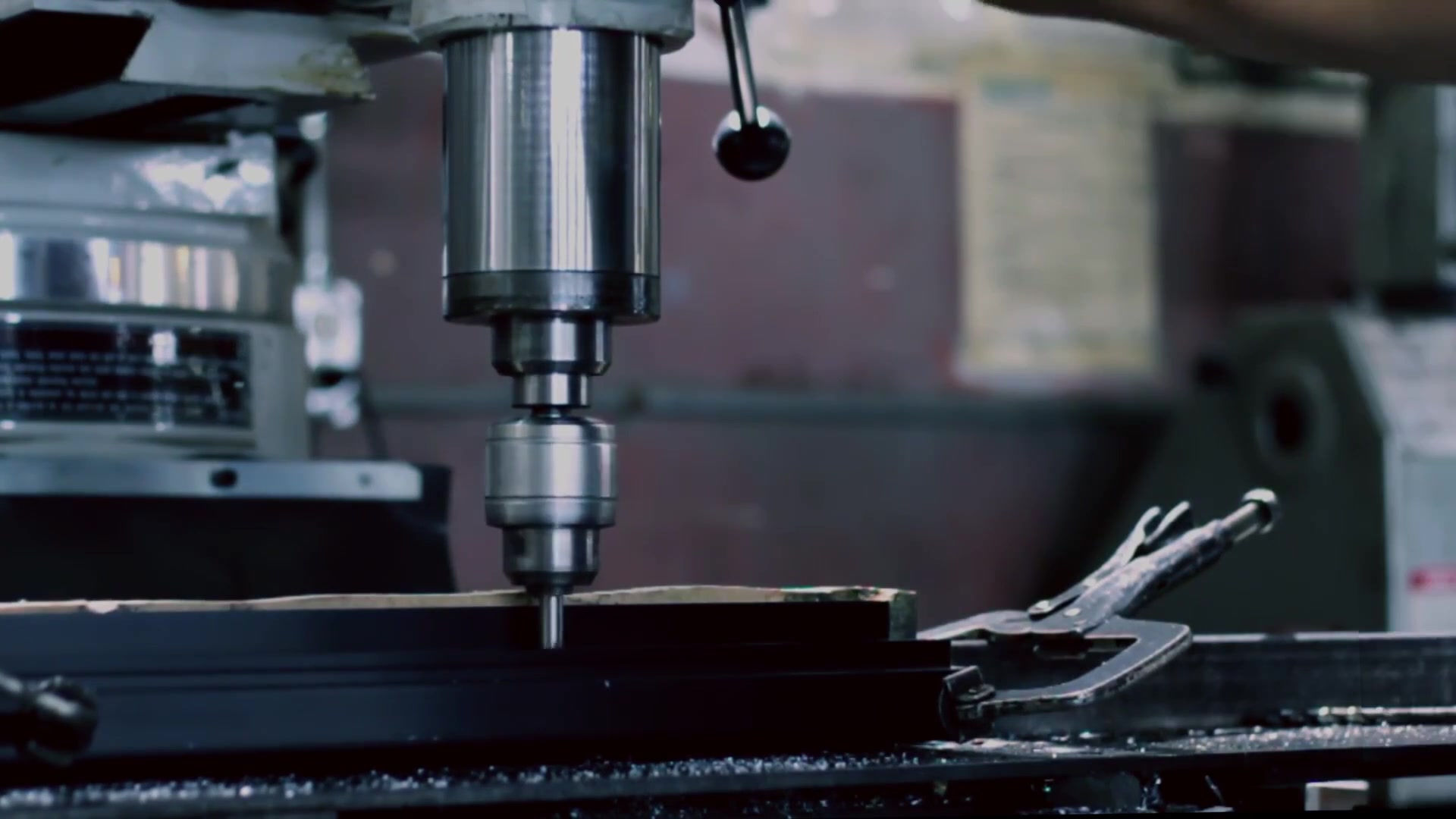
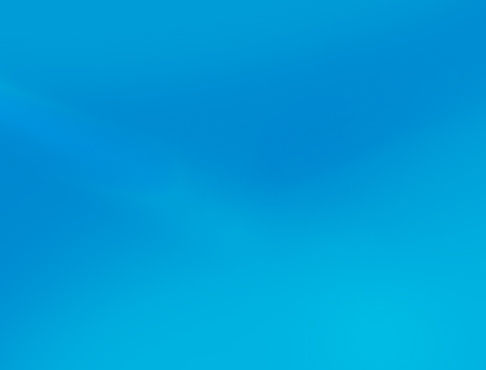
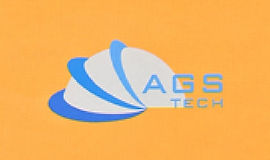
Fabricante personalizado global, integrador, consolidador, parceiro de terceirização para uma ampla variedade de produtos e serviços.
Somos sua fonte única para fabricação, fabricação, engenharia, consolidação, integração, terceirização de produtos e serviços fabricados sob encomenda e prontos para uso.
Choose your Language
-
Fabricação personalizada
-
Fabricação por contrato doméstica e global
-
Terceirização de Manufatura
-
Compras domésticas e globais
-
Consolidação
-
Integração de Engenharia
-
Serviços de engenharia
Unimos, montamos e fixamos suas peças fabricadas e as transformamos em produtos acabados ou semi-acabados por meio de SOLDAGEM, BRASILAGEM, SOLDAGEM, SINTERNIZAÇÃO, COLAGEM ADESIVA, FIXAÇÃO, PRESS FITTING. Alguns de nossos processos de soldagem mais populares são arco, gás oxicorte, resistência, projeção, costura, rebordo, percussão, estado sólido, feixe de elétrons, laser, termita, soldagem por indução. Nossos processos de brasagem populares são tocha, indução, forno e brasagem por imersão. Nossos métodos de solda são ferro, placa quente, forno, indução, mergulho, onda, refluxo e solda ultra-sônica. Para a colagem adesiva, usamos frequentemente termoplásticos e termofixos, epóxis, fenólicos, poliuretano, ligas adesivas, bem como alguns outros produtos químicos e fitas. Finalmente, nossos processos de fixação consistem em pregar, aparafusar, porcas e parafusos, rebitar, rebitar, fixar, costurar e grampear e encaixar.
• SOLDAGEM: A soldagem envolve a união de materiais através da fusão das peças de trabalho e introdução de materiais de enchimento, que também une a poça de fusão fundida. Quando a área esfria, obtemos uma junta forte. A pressão é aplicada em alguns casos. Ao contrário da soldagem, as operações de brasagem e soldagem envolvem apenas a fusão de um material com menor ponto de fusão entre as peças, e as peças não derretem. Recomendamos que você clique aqui paraBAIXE nossas Ilustrações Esquemáticas de Processos de Soldagem da AGS-TECH Inc.
Isso ajudará você a entender melhor as informações que fornecemos abaixo.
Em ARC WELDING, usamos uma fonte de alimentação e um eletrodo para criar um arco elétrico que derrete os metais. O ponto de soldagem é protegido por um gás ou vapor de proteção ou outro material. Este processo é popular para soldagem de peças automotivas e estruturas de aço. Na soldagem a arco de metal blindado (SMAW) ou também conhecida como soldagem por bastão, um bastão de eletrodo é aproximado do material base e um arco elétrico é gerado entre eles. A haste do eletrodo derrete e atua como material de enchimento. O eletrodo também contém fluxo que atua como uma camada de escória e libera vapores que atuam como gás de proteção. Estes protegem a área de solda da contaminação ambiental. Nenhum outro enchimento está sendo usado. As desvantagens deste processo são a sua lentidão, necessidade de substituição frequente dos eletrodos, necessidade de cavar a escória residual proveniente do fluxo. Uma série de metais como ferro, aço, níquel, alumínio, cobre...etc. Pode ser soldado. Suas vantagens são suas ferramentas baratas e facilidade de uso. Soldagem a arco de metal a gás (GMAW) também conhecida como gás metal-inerte (MIG), temos alimentação contínua de um eletrodo consumível de enchimento de arame e um gás inerte ou parcialmente inerte que flui ao redor do arame contra a contaminação ambiental da região de solda. Aço, alumínio e outros metais não ferrosos podem ser soldados. As vantagens do MIG são altas velocidades de soldagem e boa qualidade. As desvantagens são seus equipamentos complicados e desafios enfrentados em ambientes externos ventosos porque temos que manter o gás de proteção ao redor da área de soldagem estável. Uma variação do GMAW é a soldagem a arco com núcleo de fluxo (FCAW), que consiste em um tubo de metal fino preenchido com materiais de fluxo. Às vezes, o fluxo dentro do tubo é suficiente para proteção contra contaminação ambiental. A soldagem por arco submerso (SAW) amplamente um processo automatizado, envolve alimentação contínua de arame e arco que é atingido sob uma camada de cobertura de fluxo. As taxas de produção e qualidade são altas, a escória de soldagem sai facilmente e temos um ambiente de trabalho livre de fumaça. A desvantagem é que ele só pode ser usado para soldar parts em determinadas posições. Na soldagem a arco de tungstênio a gás (GTAW) ou soldagem a gás inerte de tungstênio (TIG), usamos um eletrodo de tungstênio junto com um enchimento separado e gases inertes ou quase inertes. Como sabemos, o tungstênio tem um alto ponto de fusão e é um metal muito adequado para temperaturas muito altas. O Tungstênio em TIG não é consumido ao contrário dos outros métodos explicados acima. Uma técnica de soldagem lenta, mas de alta qualidade, vantajosa sobre outras técnicas de soldagem de materiais finos. Adequado para muitos metais. A soldagem a arco de plasma é semelhante, mas usa gás de plasma para criar o arco. O arco na soldagem a arco plasma é relativamente mais concentrado em comparação ao GTAW e pode ser usado para uma ampla faixa de espessuras de metal em velocidades muito mais altas. A soldagem GTAW e a arco plasma podem ser aplicadas a mais ou menos os mesmos materiais.
OXY-FUEL / OXYFUEL WELDING também chamada de soldagem oxiacetileno, soldagem oxi, soldagem a gás é realizada usando combustíveis gasosos e oxigênio para soldagem. Como não há energia elétrica, é portátil e pode ser usado onde não há eletricidade. Usando uma tocha de solda, aquecemos as peças e o material de enchimento para produzir uma piscina de metal fundido compartilhada. Vários combustíveis podem ser usados, como acetileno, gasolina, hidrogênio, propano, butano, etc. Na soldagem oxi-combustível usamos dois recipientes, um para o combustível e outro para o oxigênio. O oxigênio oxida o combustível (queima).
SOLDAGEM POR RESISTÊNCIA: Este tipo de soldagem aproveita o aquecimento joule e o calor é gerado no local onde a corrente elétrica é aplicada por um determinado tempo. Altas correntes são passadas através do metal. Poças de metal fundido são formadas neste local. Os métodos de soldagem por resistência são populares devido à sua eficiência, pouco potencial de poluição. No entanto, as desvantagens são os custos do equipamento serem relativamente significativos e a limitação inerente a peças de trabalho relativamente finas. A SOLDAGEM POR PONTO é um tipo importante de soldagem por resistência. Aqui nós juntamos duas ou mais folhas sobrepostas ou peças de trabalho usando dois eletrodos de cobre para prender as folhas e passar uma alta corrente através delas. O material entre os eletrodos de cobre aquece e uma poça de fusão é gerada nesse local. A corrente é então interrompida e as pontas dos eletrodos de cobre resfriam o local da solda porque os eletrodos são resfriados a água. Aplicar a quantidade certa de calor ao material e espessura corretos é fundamental para esta técnica, porque se aplicado incorretamente a junta ficará fraca. A soldagem a ponto tem as vantagens de não causar deformações significativas nas peças de trabalho, eficiência energética, facilidade de automação e excelentes taxas de produção, além de não exigir enchimentos. A desvantagem é que, como a soldagem ocorre em pontos em vez de formar uma costura contínua, a resistência geral pode ser relativamente menor em comparação com outros métodos de soldagem. SEAM WELDING, por outro lado, produz soldas nas superfícies de contato de materiais semelhantes. A costura pode ser de topo ou de sobreposição. A soldagem da costura começa em uma extremidade e se move progressivamente para a outra. Este método também utiliza dois eletrodos de cobre para aplicar pressão e corrente na região da solda. Os eletrodos em forma de disco giram com contato constante ao longo da linha de costura e fazem uma solda contínua. Aqui também, os eletrodos são resfriados por água. As soldas são muito fortes e confiáveis. Outros métodos são as técnicas de soldagem por projeção, flash e rebordo.
A SOLDAGEM EM ESTADO SÓLIDO é um pouco diferente dos métodos anteriores explicados acima. A coalescência ocorre em temperaturas abaixo da temperatura de fusão dos metais unidos e sem uso de carga metálica. A pressão pode ser usada em alguns processos. Vários métodos são SOLDAGEM POR COEXTRUSÃO onde metais diferentes são extrudados através da mesma matriz, SOLDAGEM POR PRESSÃO A FRIO onde unimos ligas macias abaixo de seus pontos de fusão, SOLDAGEM POR DIFUSÃO uma técnica sem linhas de solda visíveis, SOLDAGEM POR EXPLOSÃO para unir materiais diferentes, por exemplo, ligas resistentes à corrosão a estruturas aços, SOLDAGEM POR PULSO ELETROMAGNÉTICO onde aceleramos tubos e chapas por forças eletromagnéticas, SOLDAGEM DE FORJA que consiste em aquecer os metais a altas temperaturas e martelá-los juntos, SOLDAGEM POR FRICÇÃO onde se realiza com suficiente soldagem por fricção, SOLDAGEM POR FRICTION STIR que envolve um processo rotativo não ferramenta consumível que atravessa a linha de junção, HOT PRESSURE WELDING onde pressionamos metais juntos em temperaturas elevadas abaixo da temperatura de fusão em vácuo ou gases inertes, HOT ISOSTATIC PRESSURE WELDING um processo onde aplicamos pressão usando gases inertes dentro de um recipiente, ROLL WELDING onde unimos materiais diferentes, forçando-os entre duas rodas giratórias, SOLDAGEM ULTRA-SÔNICA onde são soldadas chapas finas de metal ou plástico usando energia vibracional de alta frequência.
Nossos outros processos de soldagem são ELECTRON BEAM WELDING com penetração profunda e processamento rápido, mas sendo um método caro, o consideramos para casos especiais, ELECTROSLAG WELDING um método adequado apenas para chapas grossas pesadas e peças de aço, SOLDAGEM POR INDUÇÃO onde usamos indução eletromagnética e aquecer nossas peças eletricamente condutoras ou ferromagnéticas, LASER BEAM WELDING também com penetração profunda e processamento rápido, mas um método caro, LASER HYBRID WELDING que combina LBW com GMAW no mesmo cabeçote de soldagem e capaz de preencher folgas de 2 mm entre placas, PERCUSSION WELDING que envolve uma descarga elétrica seguida de forjamento dos materiais com pressão aplicada, THERMIT WELDING envolvendo reação exotérmica entre pós de alumínio e óxido de ferro., ELECTROGAS WELDING com eletrodos consumíveis e usado apenas com aço na posição vertical, e finalmente STUD ARC WELDING para unir pino à base material com calor e pressão.
Recomendamos que você clique aqui paraBAIXE nossas ilustrações esquemáticas de processos de brasagem, soldagem e colagem adesiva pela AGS-TECH Inc
Isso ajudará você a entender melhor as informações que fornecemos abaixo.
• BRASAGEM : Nós unimos dois ou mais metais aquecendo metais de adição entre eles acima de seus pontos de fusão e usando ação capilar para espalhar. O processo é semelhante à soldagem, mas as temperaturas envolvidas para derreter o enchimento são mais altas na brasagem. Como na soldagem, o fluxo protege o material de enchimento da contaminação atmosférica. Após o resfriamento, as peças de trabalho são unidas. O processo envolve as seguintes etapas principais: Bom ajuste e folga, limpeza adequada dos materiais de base, fixação adequada, seleção adequada de fluxo e atmosfera, aquecimento do conjunto e, finalmente, limpeza do conjunto brasado. Alguns de nossos processos de brasagem são TORCH BRAZING, um método popular realizado manualmente ou de forma automatizada. É adequado para pedidos de produção de baixo volume e casos especializados. O calor é aplicado usando chamas de gás perto da junta que está sendo brasada. A BRAÇADURA DE FORNO requer menos habilidade do operador e é um processo semiautomático adequado para produção industrial em massa. Tanto o controle da temperatura quanto o controle da atmosfera no forno são vantagens desta técnica, pois o primeiro permite ter ciclos de calor controlados e eliminar o aquecimento local como é o caso da brasagem com maçarico, e o segundo protege a peça da oxidação. Usando jigging, somos capazes de reduzir ao mínimo os custos de fabricação. As desvantagens são o alto consumo de energia, custos de equipamentos e considerações de projeto mais desafiadoras. A BRASAGEM A VÁCUO ocorre em um forno de vácuo. A uniformidade da temperatura é mantida e obtemos juntas sem fluxo, muito limpas e com muito poucas tensões residuais. Os tratamentos térmicos podem ocorrer durante a brasagem a vácuo, devido às baixas tensões residuais presentes durante os ciclos lentos de aquecimento e resfriamento. A principal desvantagem é seu alto custo, pois a criação de ambiente de vácuo é um processo caro. Ainda outra técnica DIP BRAZING une peças fixas onde o composto de brasagem é aplicado em superfícies de contato. Em seguida, as peças fixtured são mergulhadas em um banho de um sal fundido, como cloreto de sódio (sal de mesa), que atua como um meio de transferência de calor e fluxo. O ar é excluído e, portanto, não ocorre a formação de óxido. Na BRAÇADURA POR INDUÇÃO unimos materiais por um metal de adição que tem um ponto de fusão mais baixo do que os materiais de base. A corrente alternada da bobina de indução cria um campo eletromagnético que induz o aquecimento por indução em materiais magnéticos principalmente ferrosos. O método fornece aquecimento seletivo, boas juntas com enchimentos fluindo apenas nas áreas desejadas, pouca oxidação porque não há chamas e o resfriamento é rápido, aquecimento rápido, consistência e adequação para fabricação de alto volume. Para agilizar nossos processos e garantir a consistência, usamos frequentemente pré-formas. Informações sobre nossas instalações de brasagem que produzem conexões de cerâmica para metal, vedação hermética, passagens a vácuo, componentes de controle de fluido e alto e ultra-alto vácuo podem ser encontradas aqui: Brochura da Fábrica de Brasagem
• SOLDA: Na solda não temos a fusão das peças de trabalho, mas sim um metal de adição com ponto de fusão mais baixo do que as peças de união que desembocam na junta. O metal de adição na solda derrete a uma temperatura mais baixa do que na brasagem. Usamos ligas isentas de chumbo para soldagem e temos conformidade com RoHS e para diferentes aplicações e requisitos temos ligas diferentes e adequadas, como liga de prata. A soldagem nos oferece juntas que são estanques a gases e líquidos. Em SOFT SOLDERING, nosso metal de adição tem um ponto de fusão abaixo de 400 Centígrados, enquanto em SILVER SOLDERING e BRAZING precisamos de temperaturas mais altas. A soldagem suave usa temperaturas mais baixas, mas não resulta em juntas fortes para aplicações exigentes em temperaturas elevadas. A soldagem de prata, por outro lado, requer altas temperaturas fornecidas pela tocha e nos dá juntas fortes adequadas para aplicações de alta temperatura. A brasagem requer as temperaturas mais altas e geralmente uma tocha está sendo usada. Como as juntas de brasagem são muito fortes, elas são boas candidatas para reparar objetos pesados de ferro. Em nossas linhas de fabricação, usamos tanto a solda manual manual quanto as linhas de solda automatizadas. INDUCTION SOLDERING usa corrente CA de alta frequência em uma bobina de cobre para facilitar o aquecimento por indução. As correntes são induzidas na parte soldada e, como resultado, o calor é gerado na alta resistência joint. Este calor derrete o metal de adição. O fluxo também é usado. A soldagem por indução é um bom método para soldar cilindros e tubos em um processo contínuo envolvendo as bobinas em torno deles. A soldagem de alguns materiais como grafite e cerâmica é mais difícil, pois requer o chapeamento das peças com um metal adequado antes da soldagem. Isso facilita a ligação interfacial. Soldamos esses materiais especialmente para aplicações de embalagens herméticas. Fabricamos nossas placas de circuito impresso (PCB) em alto volume principalmente usando SOLDA ONDA. Apenas para pequenas quantidades de prototipagem, usamos solda manual usando ferro de solda. Usamos solda por onda para montagens de PCB de passagem e montagem em superfície (PCBA). Uma cola temporária mantém os componentes presos à placa de circuito e o conjunto é colocado em uma esteira e se desloca por um equipamento que contém solda derretida. Primeiro o PCB é fluxado e então entra na zona de pré-aquecimento. A solda derretida está em uma panela e tem um padrão de ondas estacionárias em sua superfície. Quando o PCB se move sobre essas ondas, essas ondas entram em contato com a parte inferior do PCB e grudam nas almofadas de solda. A solda fica apenas nos pinos e pads e não na própria PCB. As ondas na solda derretida devem ser bem controladas para que não haja respingos e os topos das ondas não toquem e contaminem áreas indesejadas das placas. Em REFLOW SOLDERING, utilizamos uma pasta de solda adesiva para fixar temporariamente os componentes eletrônicos nas placas. Em seguida, as placas são colocadas em um forno de refluxo com controle de temperatura. Aqui a solda derrete e conecta os componentes permanentemente. Usamos essa técnica tanto para componentes de montagem em superfície quanto para componentes de furos passantes. O controle adequado da temperatura e o ajuste das temperaturas do forno são essenciais para evitar a destruição dos componentes eletrônicos da placa por superaquecimento dos mesmos acima de seus limites máximos de temperatura. No processo de soldagem por refluxo, na verdade, temos várias regiões ou estágios, cada um com um perfil térmico distinto, como etapa de pré-aquecimento, etapa de imersão térmica, etapas de refluxo e resfriamento. Essas diferentes etapas são essenciais para uma soldagem por refluxo sem danos de conjuntos de placas de circuito impresso (PCBA). ULTRASONIC SOLDERING é outra técnica frequentemente usada com capacidades únicas - pode ser usada para soldar vidro, cerâmica e materiais não metálicos. Por exemplo, painéis fotovoltaicos que não são metálicos precisam de eletrodos que podem ser fixados usando esta técnica. Na soldagem ultrassônica, implantamos uma ponta de solda aquecida que também emite vibrações ultrassônicas. Essas vibrações produzem bolhas de cavitação na interface do substrato com o material de solda fundido. A energia implosiva da cavitação modifica a superfície do óxido e remove a sujeira e os óxidos. Durante este tempo, uma camada de liga também é formada. A solda na superfície de ligação incorpora oxigênio e permite a formação de uma forte ligação compartilhada entre o vidro e a solda. A SOLDA DIP pode ser considerada como uma versão mais simples da solda por onda adequada apenas para produção em pequena escala. O primeiro fluxo de limpeza é aplicado como em outros processos. PCBs com componentes montados são mergulhados manualmente ou de forma semi-automática em um tanque contendo solda derretida. A solda derretida adere às áreas metálicas expostas desprotegidas pela máscara de solda na placa. O equipamento é simples e barato.
• COLAGEM ADESIVA : Esta é outra técnica popular que usamos com frequência e envolve a colagem de superfícies usando colas, epóxis, agentes plásticos ou outros produtos químicos. A ligação é realizada por evaporação do solvente, por cura por calor, por cura por luz UV, por cura por pressão ou esperando um certo tempo. Várias colas de alto desempenho são usadas em nossas linhas de produção. Com processos de aplicação e cura projetados adequadamente, a colagem adesiva pode resultar em ligações de tensão muito baixas que são fortes e confiáveis. As ligações adesivas podem ser bons protetores contra fatores ambientais como umidade, contaminantes, corrosivos, vibração...etc. As vantagens da colagem adesiva são: elas podem ser aplicadas a materiais que de outra forma seriam difíceis de soldar, soldar ou brasar. Também pode ser preferível para materiais sensíveis ao calor que seriam danificados por soldagem ou outros processos de alta temperatura. Outras vantagens dos adesivos são que eles podem ser aplicados em superfícies de formato irregular e aumentar o peso da montagem em quantidades muito pequenas quando comparado a outros métodos. Também as mudanças dimensionais nas peças são muito mínimas. Algumas colas têm propriedades de correspondência de índice e podem ser usadas entre componentes ópticos sem diminuir significativamente a intensidade da luz ou do sinal óptico. As desvantagens, por outro lado, são os tempos de cura mais longos que podem retardar as linhas de fabricação, requisitos de fixação, requisitos de preparação de superfície e dificuldade de desmontagem quando o retrabalho é necessário. A maioria de nossas operações de colagem adesiva envolve as seguintes etapas:
-Tratamento de superfície: Procedimentos especiais de limpeza, como limpeza com água deionizada, limpeza com álcool, limpeza com plasma ou corona, são comuns. Após a limpeza, podemos aplicar promotores de adesão nas superfícies para garantir as melhores juntas possíveis.
- Fixação de peças: Tanto para aplicação de adesivos quanto para cura, projetamos e usamos fixações personalizadas.
-Aplicação de adesivos: Às vezes usamos sistemas manuais e, às vezes, dependendo do caso, sistemas automatizados, como robótica, servomotores, atuadores lineares para entregar os adesivos no local certo e usamos dispensadores para entregá-los no volume e quantidade certos.
-Cura: Dependendo do adesivo, podemos usar secagem e cura simples, bem como cura sob luz UV que atua como catalisador ou cura térmica em um forno ou usando elementos de aquecimento resistivos montados em gabaritos e acessórios.
Recomendamos que você clique aqui paraBAIXE nossas ilustrações esquemáticas de processos de fixação da AGS-TECH Inc.
Isso ajudará você a entender melhor as informações que fornecemos abaixo.
• PROCESSOS DE FIXAÇÃO: Nossos processos de união mecânica se dividem em duas categorias: FIXADORES e JUNTAS INTEGRAL. Exemplos de fixadores que usamos são parafusos, pinos, porcas, parafusos, rebites. Exemplos de juntas integrais que usamos são encaixes de pressão e contração, costuras, crimpagens. Usando uma variedade de métodos de fixação, garantimos que nossas juntas mecânicas sejam fortes e confiáveis por muitos anos de uso. PARAFUSOS e PARAFUSOS são alguns dos fixadores mais comumente usados para manter objetos juntos e posicionamento. Nossos parafusos e cavilhas atendem aos padrões ASME. Vários tipos de parafusos e cavilhas são implantados, incluindo parafusos sextavados e parafusos sextavados, parafusos e parafusos de retenção, parafuso de extremidade dupla, parafuso de bucha, parafuso de olhal, parafuso de espelho, parafuso de chapa metálica, parafuso de ajuste fino, parafusos autoperfurantes e auto-roscantes , parafuso de fixação, parafusos com arruelas embutidas... e muito mais. Temos vários tipos de cabeça de parafuso, como cabeça escareada, cúpula, redonda, flangeada e vários tipos de acionamento de parafuso, como slot, phillips, quadrado, soquete hexagonal. Um RIVET por outro lado é um fixador mecânico permanente que consiste em um eixo cilíndrico liso e uma cabeça por um lado. Após a inserção, a outra extremidade do rebite é deformada e seu diâmetro é ampliado para que permaneça no lugar. Em outras palavras, antes da instalação um rebite tem uma cabeça e após a instalação tem duas. Instalamos vários tipos de rebites dependendo da aplicação, resistência, acessibilidade e custo, como rebites de cabeça sólida/redonda, rebites estruturais, semi-tubulares, cegos, oscar, drive, flush, friction-lock, rebites autoperfurantes. A rebitagem pode ser preferida nos casos em que a deformação térmica e a mudança nas propriedades do material devido ao calor da soldagem precisam ser evitadas. A rebitagem também oferece peso leve e especialmente boa resistência e resistência contra forças de cisalhamento. Contra cargas de tração, no entanto, parafusos, porcas e parafusos podem ser mais adequados. No processo de CLINCHING utilizamos punções e matrizes especiais para formar um intertravamento mecânico entre as chapas metálicas que estão sendo unidas. O punção empurra as camadas de chapa metálica para dentro da cavidade da matriz e resulta na formação de uma junta permanente. Nenhum aquecimento e nenhum resfriamento é necessário no clinching e é um processo de trabalho a frio. É um processo econômico que pode substituir a soldagem a ponto em alguns casos. No PINNING usamos pinos que são elementos de máquina usados para fixar posições de peças de máquinas em relação umas às outras. Os principais tipos são pinos de forquilha, contrapino, pino de mola, pinos de cavilha, and split pin. No STAPLING usamos pistolas e grampos de grampeamento que são fixadores de duas pontas usados para unir ou encadernar materiais. O grampeamento tem as seguintes vantagens: Econômico, simples e rápido de usar, a coroa dos grampos pode ser usada para unir materiais unidos, A coroa do grampo pode facilitar a ligação de uma peça como um cabo e a fixação em uma superfície sem perfurar ou remoção prejudicial e relativamente fácil. O PRESS FITTING é realizado empurrando as peças juntas e o atrito entre elas prende as peças. As peças de encaixe por pressão que consistem em um eixo superdimensionado e um furo subdimensionado geralmente são montadas por um dos dois métodos: aplicando força ou aproveitando a expansão ou contração térmica das peças. Quando um encaixe de pressão é estabelecido pela aplicação de uma força, usamos uma prensa hidráulica ou uma prensa manual. Por outro lado, quando o encaixe de pressão é estabelecido por expansão térmica, aquecemos as partes envolventes e as montamos em seus lugares enquanto quentes. Quando esfriam, eles se contraem e voltam às suas dimensões normais. Isso resulta em um bom ajuste de pressão. Chamamos isso alternativamente de SHRINK-FITTING. A outra maneira de fazer isso é resfriando as peças envelopadas antes da montagem e, em seguida, deslizando-as em suas peças correspondentes. Quando o conjunto aquece, eles se expandem e obtemos um ajuste apertado. Este último método pode ser preferível nos casos em que o aquecimento apresenta o risco de alterar as propriedades do material. O resfriamento é mais seguro nesses casos.
Componentes e conjuntos pneumáticos e hidráulicos
• Válvulas, componentes hidráulicos e pneumáticos como O-ring, arruela, vedações, gaxeta, anel, calço.
Como as válvulas e os componentes pneumáticos vêm em uma grande variedade, não podemos listar tudo aqui. Dependendo dos ambientes físicos e químicos de sua aplicação, temos produtos especiais para você. Por favor, especifique-nos a aplicação, tipo de componente, especificações, condições ambientais como pressão, temperatura, líquidos ou gases que estarão em contato com suas válvulas e componentes pneumáticos; e nós escolheremos o produto mais adequado para você ou fabricaremos especialmente para sua aplicação.