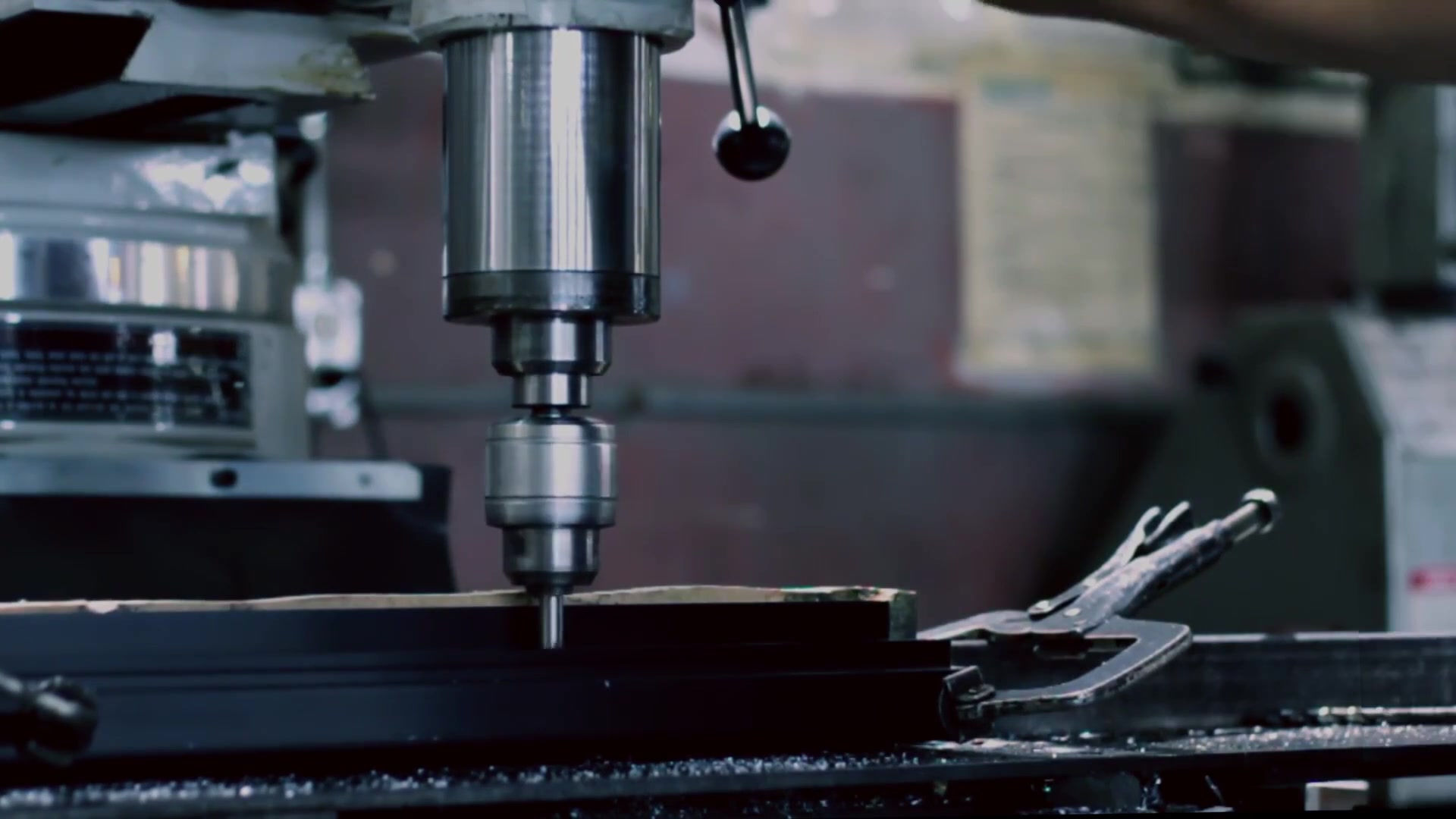
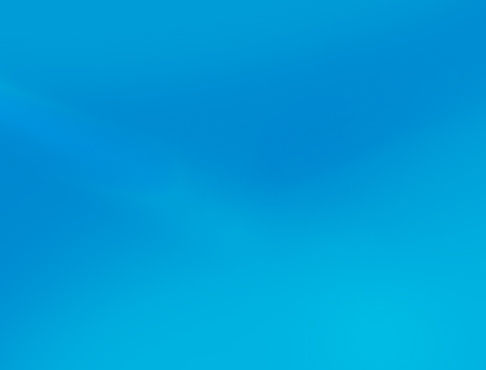
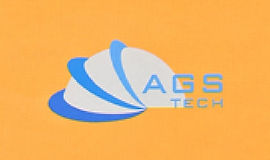
గ్లోబల్ కస్టమ్ మ్యానుఫ్యాక్చరర్, ఇంటిగ్రేటర్, కన్సాలిడేటర్, అనేక రకాల ఉత్పత్తులు & సేవల కోసం అవుట్సోర్సింగ్ భాగస్వామి.
కస్టమ్ తయారీ మరియు ఆఫ్-షెల్ఫ్ ఉత్పత్తులు & సేవల తయారీ, కల్పన, ఇంజనీరింగ్, కన్సాలిడేషన్, ఇంటిగ్రేషన్, అవుట్సోర్సింగ్ కోసం మేము మీ వన్-స్టాప్ మూలం.
మీ భాషను ఎంచుకోండి
-
కస్టమ్ తయారీ
-
దేశీయ & గ్లోబల్ కాంట్రాక్ట్ తయారీ
-
తయారీ అవుట్సోర్సింగ్
-
దేశీయ & ప్రపంచ సేకరణ
-
కన్సాలిడేషన్
-
ఇంజనీరింగ్ ఇంటిగ్రేషన్
-
ఇంజనీరింగ్ సేవలు
ఇటీవలి సంవత్సరాలలో, ర్యాపిడ్ మాన్యుఫాక్చరింగ్ లేదా ర్యాపిడ్ ప్రోటోటైపింగ్ కోసం డిమాండ్ పెరగడాన్ని మేము చూశాము. ఈ ప్రక్రియను డెస్క్టాప్ తయారీ లేదా ఉచిత-ఫారమ్ ఫాబ్రికేషన్ అని కూడా పిలుస్తారు. ప్రాథమికంగా ఒక భాగం యొక్క ఘన భౌతిక నమూనా నేరుగా త్రిమితీయ CAD డ్రాయింగ్ నుండి తయారు చేయబడింది. మేము పొరలలో భాగాలను నిర్మించే ఈ వివిధ సాంకేతికతలకు సంకలిత తయారీ అనే పదాన్ని ఉపయోగిస్తాము. ఇంటిగ్రేటెడ్ కంప్యూటర్ ఆధారిత హార్డ్వేర్ మరియు సాఫ్ట్వేర్ ఉపయోగించి మేము సంకలిత తయారీని చేస్తాము. మా వేగవంతమైన ప్రోటోటైపింగ్ మరియు తయారీ పద్ధతులు స్టీరియోలిథోగ్రఫీ, పాలిజెట్, ఫ్యూజ్డ్-డిపోజిషన్ మోడలింగ్, సెలెక్టివ్ లేజర్ సింటరింగ్, ఎలక్ట్రాన్ బీమ్ మెల్టింగ్, త్రీ డైమెన్షనల్ ప్రింటింగ్, డైరెక్ట్ మ్యానుఫ్యాక్టరింగ్. మీరు ఇక్కడ క్లిక్ చేయాలని మేము సిఫార్సు చేస్తున్నాముAGS-TECH Inc. ద్వారా సంకలిత తయారీ మరియు వేగవంతమైన తయారీ ప్రక్రియల యొక్క మా స్కీమాటిక్ ఇలస్ట్రేషన్లను డౌన్లోడ్ చేయండి
మేము మీకు దిగువ అందిస్తున్న సమాచారాన్ని బాగా అర్థం చేసుకోవడంలో ఇది మీకు సహాయం చేస్తుంది.
రాపిడ్ ప్రోటోటైపింగ్ మాకు అందిస్తుంది: 1.) 3D / CAD సిస్టమ్ని ఉపయోగించి మానిటర్లో సంభావిత ఉత్పత్తి రూపకల్పన వివిధ కోణాల నుండి వీక్షించబడుతుంది. 2.) నాన్మెటాలిక్ మరియు మెటాలిక్ మెటీరియల్స్ నుండి ప్రోటోటైప్లు క్రియాత్మక, సాంకేతిక మరియు సౌందర్య అంశాల నుండి తయారు చేయబడతాయి మరియు అధ్యయనం చేయబడతాయి. 3.) చాలా తక్కువ సమయంలో తక్కువ ఖర్చుతో కూడిన ప్రోటోటైపింగ్ సాధించబడుతుంది. సంకలిత తయారీని ఒకదానిపై ఒకటి పేర్చడం మరియు బంధించడం ద్వారా బ్రెడ్ రొట్టె నిర్మాణాన్ని పోలి ఉంటుంది. మరో మాటలో చెప్పాలంటే, ఉత్పత్తిని స్లైస్ ద్వారా తయారు చేస్తారు, లేదా పొరల వారీగా ఒకదానికొకటి జమ చేస్తారు. చాలా భాగాలను గంటల వ్యవధిలో ఉత్పత్తి చేయవచ్చు. భాగాలు చాలా త్వరగా అవసరమైతే లేదా అవసరమైన పరిమాణం తక్కువగా ఉంటే మరియు అచ్చు మరియు సాధనాన్ని తయారు చేయడం చాలా ఖరీదైనది మరియు సమయం తీసుకుంటే సాంకేతికత మంచిది. అయితే ఖరీదైన ముడి పదార్థాల కారణంగా ఒక భాగం యొక్క ధర ఖరీదైనది.
• స్టీరియోలిథోగ్రఫీ: ఈ టెక్నిక్ STL అని కూడా సంక్షిప్తీకరించబడింది, లిక్విడ్ ఫోటోపాలిమర్పై లేజర్ కిరణాన్ని కేంద్రీకరించడం ద్వారా ఒక నిర్దిష్ట ఆకృతిలోకి క్యూరింగ్ మరియు గట్టిపడటంపై ఆధారపడి ఉంటుంది. లేజర్ ఫోటోపాలిమర్ను పాలిమరైజ్ చేస్తుంది మరియు దానిని నయం చేస్తుంది. ఫోటోపాలిమర్ మిశ్రమం యొక్క ఉపరితలంతో పాటు ప్రోగ్రామ్ చేయబడిన ఆకృతి ప్రకారం UV లేజర్ పుంజం స్కాన్ చేయడం ద్వారా భాగం ఒకదానికొకటి క్యాస్కేడ్ చేయబడిన వ్యక్తిగత ముక్కలలో దిగువ నుండి పైకి ఉత్పత్తి చేయబడుతుంది. సిస్టమ్లోకి ప్రోగ్రామ్ చేయబడిన జ్యామితిని సాధించడానికి లేజర్ స్పాట్ యొక్క స్కానింగ్ చాలాసార్లు పునరావృతమవుతుంది. భాగం పూర్తిగా తయారు చేయబడిన తర్వాత, అది ప్లాట్ఫారమ్ నుండి తీసివేయబడుతుంది, బ్లాట్ చేయబడింది మరియు అల్ట్రాసోనిక్గా మరియు ఆల్కహాల్ బాత్తో శుభ్రం చేయబడుతుంది. తర్వాత, పాలిమర్ పూర్తిగా నయమైందని మరియు గట్టిపడిందని నిర్ధారించుకోవడానికి ఇది కొన్ని గంటలపాటు UV వికిరణానికి గురవుతుంది. ప్రక్రియను సంగ్రహంగా చెప్పాలంటే, ఫోటోపాలిమర్ మిశ్రమంలో ముంచిన ప్లాట్ఫారమ్ మరియు UV లేజర్ పుంజం నియంత్రించబడతాయి మరియు కావలసిన భాగం యొక్క ఆకృతిని బట్టి సర్వో-నియంత్రణ వ్యవస్థ ద్వారా తరలించబడతాయి మరియు పొర ద్వారా పాలిమర్ పొరను ఫోటోక్యూరింగ్ చేయడం ద్వారా భాగం పొందబడుతుంది. ఉత్పత్తి భాగం యొక్క గరిష్ట కొలతలు స్టీరియోలిథోగ్రఫీ పరికరాల ద్వారా నిర్ణయించబడతాయి.
• POLYJET : ఇంక్జెట్ ప్రింటింగ్ లాగానే, పాలీజెట్లో మనకు ఎనిమిది ప్రింట్ హెడ్లు ఉన్నాయి, ఇవి బిల్డ్ ట్రేలో ఫోటోపాలిమర్ను డిపాజిట్ చేస్తాయి. జెట్ల పక్కన ఉంచిన అతినీలలోహిత కాంతి వెంటనే ప్రతి పొరను నయం చేస్తుంది మరియు గట్టిపరుస్తుంది. పాలీజెట్లో రెండు పదార్థాలు ఉపయోగించబడతాయి. మొదటి పదార్థం అసలు మోడల్ను తయారు చేయడం. రెండవ పదార్థం, జెల్ లాంటి రెసిన్ మద్దతు కోసం ఉపయోగించబడుతుంది. ఈ రెండు పదార్థాలు పొరల వారీగా జమ చేయబడతాయి మరియు ఏకకాలంలో నయం చేయబడతాయి. మోడల్ పూర్తయిన తర్వాత, సజల ద్రావణంతో సపోర్ట్ మెటీరియల్ తీసివేయబడుతుంది. ఉపయోగించిన రెసిన్లు స్టీరియోలిథోగ్రఫీ (STL) మాదిరిగానే ఉంటాయి. స్టీరియోలిథోగ్రఫీ కంటే పాలీజెట్ క్రింది ప్రయోజనాలను కలిగి ఉంది: 1.) భాగాలను శుభ్రపరచడం అవసరం లేదు. 2.) పోస్ట్ప్రాసెస్ క్యూరింగ్ అవసరం లేదు 3.) చిన్న పొర మందం సాధ్యమవుతుంది మరియు తద్వారా మనం మంచి రిజల్యూషన్ను పొందుతాము మరియు చక్కటి భాగాలను తయారు చేయగలము.
• ఫ్యూజ్డ్ డిపోజిషన్ మోడలింగ్: FDM అని కూడా సంక్షిప్తీకరించబడింది, ఈ పద్ధతిలో రోబోట్-నియంత్రిత ఎక్స్ట్రూడర్ హెడ్ టేబుల్పై రెండు సూత్రాల దిశల్లో కదులుతుంది. అవసరమైన విధంగా కేబుల్ తగ్గించబడుతుంది మరియు పెంచబడుతుంది. తలపై వేడిచేసిన డై యొక్క రంధ్రం నుండి, ఒక థర్మోప్లాస్టిక్ ఫిలమెంట్ వెలికితీయబడుతుంది మరియు ప్రారంభ పొర నురుగు పునాదిపై జమ చేయబడుతుంది. ముందుగా నిర్ణయించిన మార్గాన్ని అనుసరించే ఎక్స్ట్రూడర్ హెడ్ ద్వారా ఇది సాధించబడుతుంది. ప్రారంభ పొర తర్వాత, పట్టిక తగ్గించబడుతుంది మరియు తదుపరి పొరలు ఒకదానిపై ఒకటి జమ చేయబడతాయి. కొన్నిసార్లు సంక్లిష్టమైన భాగాన్ని తయారు చేస్తున్నప్పుడు, నిర్దిష్ట దిశలలో నిక్షేపణ కొనసాగేలా సహాయక నిర్మాణాలు అవసరమవుతాయి. ఈ సందర్భాలలో, ఒక సపోర్టింగ్ మెటీరియల్ పొరపై తక్కువ దట్టమైన ఫిలమెంట్ అంతరాన్ని కలిగి ఉంటుంది, తద్వారా ఇది మోడల్ మెటీరియల్ కంటే బలహీనంగా ఉంటుంది. ఈ సపోర్టు స్ట్రక్చర్లను ఆ భాగం పూర్తయిన తర్వాత కరిగించవచ్చు లేదా విచ్ఛిన్నం చేయవచ్చు. ఎక్స్ట్రూడర్ డై కొలతలు వెలికితీసిన పొరల మందాన్ని నిర్ణయిస్తాయి. FDM ప్రక్రియ వాలుగా ఉన్న బాహ్య విమానాలపై స్టెప్డ్ ఉపరితలాలతో భాగాలను ఉత్పత్తి చేస్తుంది. ఈ కరుకుదనం ఆమోదయోగ్యం కానట్లయితే, వీటిని సున్నితంగా చేయడానికి రసాయన ఆవిరి పాలిషింగ్ లేదా వేడిచేసిన సాధనాన్ని ఉపయోగించవచ్చు. పాలిషింగ్ మైనపు కూడా ఈ దశలను తొలగించడానికి మరియు సహేతుకమైన రేఖాగణిత సహనాన్ని సాధించడానికి పూత పదార్థంగా అందుబాటులో ఉంది.
• సెలెక్టివ్ లేజర్ సింటరింగ్ : SLSగా కూడా సూచించబడుతుంది, ఈ ప్రక్రియ పాలిమర్, సిరామిక్ లేదా మెటాలిక్ పౌడర్లను ఎంపిక చేసి ఒక వస్తువులోకి సింటరింగ్ చేయడంపై ఆధారపడి ఉంటుంది. ప్రాసెసింగ్ చాంబర్ దిగువన రెండు సిలిండర్లు ఉన్నాయి: పార్ట్-బిల్డ్ సిలిండర్ మరియు పౌడర్-ఫీడ్ సిలిండర్. మునుపటిది సిన్టర్డ్ భాగం ఏర్పడే చోటికి క్రమంగా తగ్గించబడుతుంది మరియు రెండోది రోలర్ మెకానిజం ద్వారా పార్ట్-బిల్డ్ సిలిండర్కు పౌడర్ను సరఫరా చేయడానికి క్రమంగా పెంచబడుతుంది. ముందుగా పౌడర్ యొక్క పలుచని పొర పార్ట్-బిల్డ్ సిలిండర్లో నిక్షిప్తం చేయబడుతుంది, తర్వాత లేజర్ పుంజం ఆ పొరపై కేంద్రీకరించబడుతుంది, ఒక నిర్దిష్ట క్రాస్ సెక్షన్ను గుర్తించడం మరియు కరిగించడం/సింటరింగ్ చేయడం, అది ఘన రూపంలోకి మారుతుంది. పౌడర్ అంటే లేజర్ పుంజం దెబ్బతినని ప్రాంతాలు వదులుగా ఉంటాయి కానీ ఇప్పటికీ ఘన భాగానికి మద్దతు ఇస్తాయి. అప్పుడు పొడి యొక్క మరొక పొర జమ చేయబడుతుంది మరియు భాగాన్ని పొందేందుకు ప్రక్రియ చాలాసార్లు పునరావృతమవుతుంది. చివర్లో, వదులుగా ఉన్న పొడి కణాలు కదిలించబడతాయి. తయారు చేయబడుతున్న భాగం యొక్క 3D CAD ప్రోగ్రామ్ ద్వారా రూపొందించబడిన సూచనలను ఉపయోగించి ఇవన్నీ ప్రాసెస్-కంట్రోల్ కంప్యూటర్ ద్వారా నిర్వహించబడతాయి. పాలిమర్లు (ABS, PVC, పాలిస్టర్ వంటివి), మైనపు, లోహాలు మరియు తగిన పాలిమర్ బైండర్లతో కూడిన సిరామిక్లు వంటి వివిధ పదార్థాలను డిపాజిట్ చేయవచ్చు.
• ELECTRON-BEAM MELTING : సెలెక్టివ్ లేజర్ సింటరింగ్ లాగానే ఉంటుంది, అయితే వాక్యూమ్లో ప్రోటోటైప్లను తయారు చేయడానికి టైటానియం లేదా కోబాల్ట్ క్రోమ్ పౌడర్లను కరిగించడానికి ఎలక్ట్రాన్ బీమ్ని ఉపయోగించడం. స్టెయిన్లెస్ స్టీల్స్, అల్యూమినియం మరియు రాగి మిశ్రమాలపై ఈ ప్రక్రియను నిర్వహించడానికి కొన్ని అభివృద్ధి చేయబడింది. ఉత్పత్తి చేయబడిన భాగాల యొక్క అలసట బలాన్ని పెంచాల్సిన అవసరం ఉన్నట్లయితే, మేము ద్వితీయ ప్రక్రియగా పార్ట్ తయారీ తర్వాత హాట్ ఐసోస్టాటిక్ నొక్కడం ఉపయోగిస్తాము.
• త్రీ-డైమెన్షనల్ ప్రింటింగ్ : 3DPతో కూడా సూచించబడుతుంది, ఈ టెక్నిక్లో ప్రింట్ హెడ్ ఒక అకర్బన బైండర్ను నాన్మెటాలిక్ లేదా మెటాలిక్ పౌడర్ పొరపై జమ చేస్తుంది. పౌడర్ బెడ్ను మోసే పిస్టన్ క్రమంగా తగ్గించబడుతుంది మరియు ప్రతి దశలోనూ బైండర్ layer ద్వారా పొరల వారీగా జమ చేయబడుతుంది మరియు బైండర్ ద్వారా ఫ్యూజ్ చేయబడుతుంది. ఉపయోగించిన పౌడర్ పదార్థాలు పాలిమర్ల మిశ్రమాలు మరియు ఫైబర్స్, ఫౌండరీ ఇసుక, లోహాలు. వేర్వేరు బైండర్ హెడ్లను ఏకకాలంలో మరియు విభిన్న రంగు బైండర్లను ఉపయోగించి మనం వివిధ రంగులను పొందవచ్చు. ఈ ప్రక్రియ ఇంక్జెట్ ప్రింటింగ్ను పోలి ఉంటుంది కానీ రంగు షీట్ను పొందే బదులు మనం రంగు త్రిమితీయ వస్తువును పొందుతాము. ఉత్పత్తి చేయబడిన భాగాలు పోరస్ కావచ్చు మరియు దాని సాంద్రత మరియు బలాన్ని పెంచడానికి సింటరింగ్ మరియు మెటల్ ఇన్ఫిల్ట్రేషన్ అవసరం కావచ్చు. సింటరింగ్ బైండర్ను కాల్చివేస్తుంది మరియు మెటల్ పౌడర్లను ఫ్యూజ్ చేస్తుంది. స్టెయిన్లెస్ స్టీల్, అల్యూమినియం, టైటానియం వంటి లోహాలు భాగాలను తయారు చేయడానికి ఉపయోగించవచ్చు మరియు చొరబాటు పదార్థాలుగా మనం సాధారణంగా రాగి మరియు కాంస్యాన్ని ఉపయోగిస్తాము. ఈ సాంకేతికత యొక్క అందం ఏమిటంటే సంక్లిష్టమైన మరియు కదిలే సమావేశాలు కూడా చాలా త్వరగా తయారు చేయబడతాయి. ఉదాహరణకు ఒక గేర్ అసెంబ్లీ, ఒక సాధనంగా ఒక రెంచ్ తయారు చేయవచ్చు మరియు కదిలే మరియు టర్నింగ్ భాగాలను ఉపయోగించడానికి సిద్ధంగా ఉంటుంది. అసెంబ్లీలోని వివిధ భాగాలను వేర్వేరు రంగులతో తయారు చేయవచ్చు మరియు అన్నింటినీ ఒకే షాట్లో తయారు చేయవచ్చు. మా బ్రోచర్ను ఇందులో డౌన్లోడ్ చేసుకోండి:మెటల్ 3D ప్రింటింగ్ బేసిక్స్
• ప్రత్యక్ష తయారీ మరియు రాపిడ్ టూలింగ్: డిజైన్ మూల్యాంకనం, ట్రబుల్షూటింగ్తో పాటు ఉత్పత్తుల యొక్క ప్రత్యక్ష తయారీకి లేదా ఉత్పత్తుల్లోకి నేరుగా దరఖాస్తు చేయడానికి మేము వేగవంతమైన నమూనాను ఉపయోగిస్తాము. మరో మాటలో చెప్పాలంటే, వేగవంతమైన ప్రోటోటైపింగ్ వాటిని మెరుగైన మరియు మరింత పోటీగా చేయడానికి సాంప్రదాయ ప్రక్రియలలో చేర్చబడుతుంది. ఉదాహరణకు, వేగవంతమైన ప్రోటోటైపింగ్ నమూనాలు మరియు అచ్చులను ఉత్పత్తి చేస్తుంది. వేగవంతమైన ప్రోటోటైపింగ్ కార్యకలాపాల ద్వారా సృష్టించబడిన ద్రవీభవన మరియు మండే పాలిమర్ యొక్క నమూనాలను పెట్టుబడి కాస్టింగ్ కోసం సమీకరించవచ్చు మరియు పెట్టుబడి పెట్టవచ్చు. ప్రస్తావించడానికి మరొక ఉదాహరణ సిరామిక్ కాస్టింగ్ షెల్ను ఉత్పత్తి చేయడానికి 3DPని ఉపయోగించడం మరియు షెల్ కాస్టింగ్ కార్యకలాపాలకు ఉపయోగించడం. ఇంజెక్షన్ అచ్చులు మరియు అచ్చు ఇన్సర్ట్లు కూడా వేగవంతమైన నమూనా ద్వారా ఉత్పత్తి చేయబడతాయి మరియు అనేక వారాలు లేదా నెలల అచ్చు తయారీకి ప్రధాన సమయాన్ని ఆదా చేయవచ్చు. కావలసిన భాగం యొక్క CAD ఫైల్ను మాత్రమే విశ్లేషించడం ద్వారా, మేము సాఫ్ట్వేర్ని ఉపయోగించి సాధనం జ్యామితిని ఉత్పత్తి చేయవచ్చు. ఇక్కడ మా ప్రసిద్ధ శీఘ్ర సాధన పద్ధతులు కొన్ని:
RTV (గది-ఉష్ణోగ్రత వల్కనైజింగ్) మోల్డింగ్ / యూరేథేన్ కాస్టింగ్: త్వరిత నమూనాను ఉపయోగించి కావలసిన భాగం యొక్క నమూనాను తయారు చేయడానికి ఉపయోగించవచ్చు. అప్పుడు ఈ నమూనాను విడిపోయే ఏజెంట్తో పూత పూయాలి మరియు అచ్చు భాగాలను ఉత్పత్తి చేయడానికి ద్రవ RTV రబ్బరు నమూనాపై పోస్తారు. తరువాత, ఈ అచ్చు భాగాలు అచ్చు ద్రవ యురేథేన్లను ఇంజెక్షన్ చేయడానికి ఉపయోగిస్తారు. అచ్చు జీవితం చిన్నది, కేవలం 0 లేదా 30 సైకిల్స్ లాగా ఉంటుంది కానీ చిన్న బ్యాచ్ ఉత్పత్తికి సరిపోతుంది.
ACES (ఎసిటల్ క్లియర్ ఎపోక్సీ సాలిడ్) ఇంజెక్షన్ మౌల్డింగ్: స్టీరియోలిథోగ్రఫీ వంటి వేగవంతమైన ప్రోటోటైపింగ్ పద్ధతులను ఉపయోగించి, మేము ఇంజెక్షన్ అచ్చులను ఉత్పత్తి చేస్తాము. ఈ అచ్చులు ఎపాక్సి, అల్యూమినియం-నిండిన ఎపాక్సి లేదా లోహాలు వంటి పదార్థాలతో నింపడానికి అనుమతించడానికి ఓపెన్ ఎండ్తో షెల్లు. మళ్లీ అచ్చు జీవితం పదుల లేదా గరిష్టంగా వందల భాగాలకు పరిమితం చేయబడింది.
స్ప్రేడ్ మెటల్ టూలింగ్ ప్రాసెస్: మేము వేగవంతమైన నమూనాను ఉపయోగిస్తాము మరియు నమూనాను తయారు చేస్తాము. మేము నమూనా ఉపరితలంపై జింక్-అల్యూమినియం మిశ్రమాన్ని స్ప్రే చేస్తాము మరియు దానిని కోట్ చేస్తాము. లోహపు పూతతో ఉన్న నమూనా ఒక ఫ్లాస్క్ లోపల ఉంచబడుతుంది మరియు ఒక ఎపోక్సీ లేదా అల్యూమినియంతో నిండిన ఎపాక్సీతో కుండలో ఉంచబడుతుంది. చివరగా, అది తీసివేయబడుతుంది మరియు అలాంటి రెండు అచ్చు భాగాలను ఉత్పత్తి చేయడం ద్వారా మేము ఇంజెక్షన్ మోల్డింగ్ కోసం పూర్తి అచ్చును పొందుతాము. ఈ అచ్చులు ఎక్కువ కాలం జీవిస్తాయి, కొన్ని సందర్భాల్లో పదార్థం మరియు ఉష్ణోగ్రతల ఆధారంగా అవి వేలల్లో భాగాలను ఉత్పత్తి చేయగలవు.
కీల్టూల్ ప్రక్రియ: ఈ సాంకేతికత 100,000 నుండి 10 మిలియన్ సైకిల్ జీవితాలతో అచ్చులను ఉత్పత్తి చేయగలదు. వేగవంతమైన నమూనాను ఉపయోగించి మేము RTV అచ్చును ఉత్పత్తి చేస్తాము. అచ్చు తదుపరి A6 టూల్ స్టీల్ పౌడర్, టంగ్స్టన్ కార్బైడ్, పాలిమర్ బైండర్తో కూడిన మిశ్రమంతో నింపబడి, నయం చేయడానికి వీలు కల్పిస్తుంది. ఈ అచ్చు పాలిమర్ను కాల్చివేయడానికి మరియు మెటల్ పౌడర్లను ఫ్యూజ్ చేయడానికి వేడి చేయబడుతుంది. తదుపరి దశ తుది అచ్చును ఉత్పత్తి చేయడానికి రాగి చొరబాటు. అవసరమైతే, మెరుగైన డైమెన్షనల్ ఖచ్చితత్వాల కోసం అచ్చుపై మ్యాచింగ్ మరియు పాలిషింగ్ వంటి ద్వితీయ కార్యకలాపాలను నిర్వహించవచ్చు. _cc781905-5cde-3194-bb3b-1358bad_5