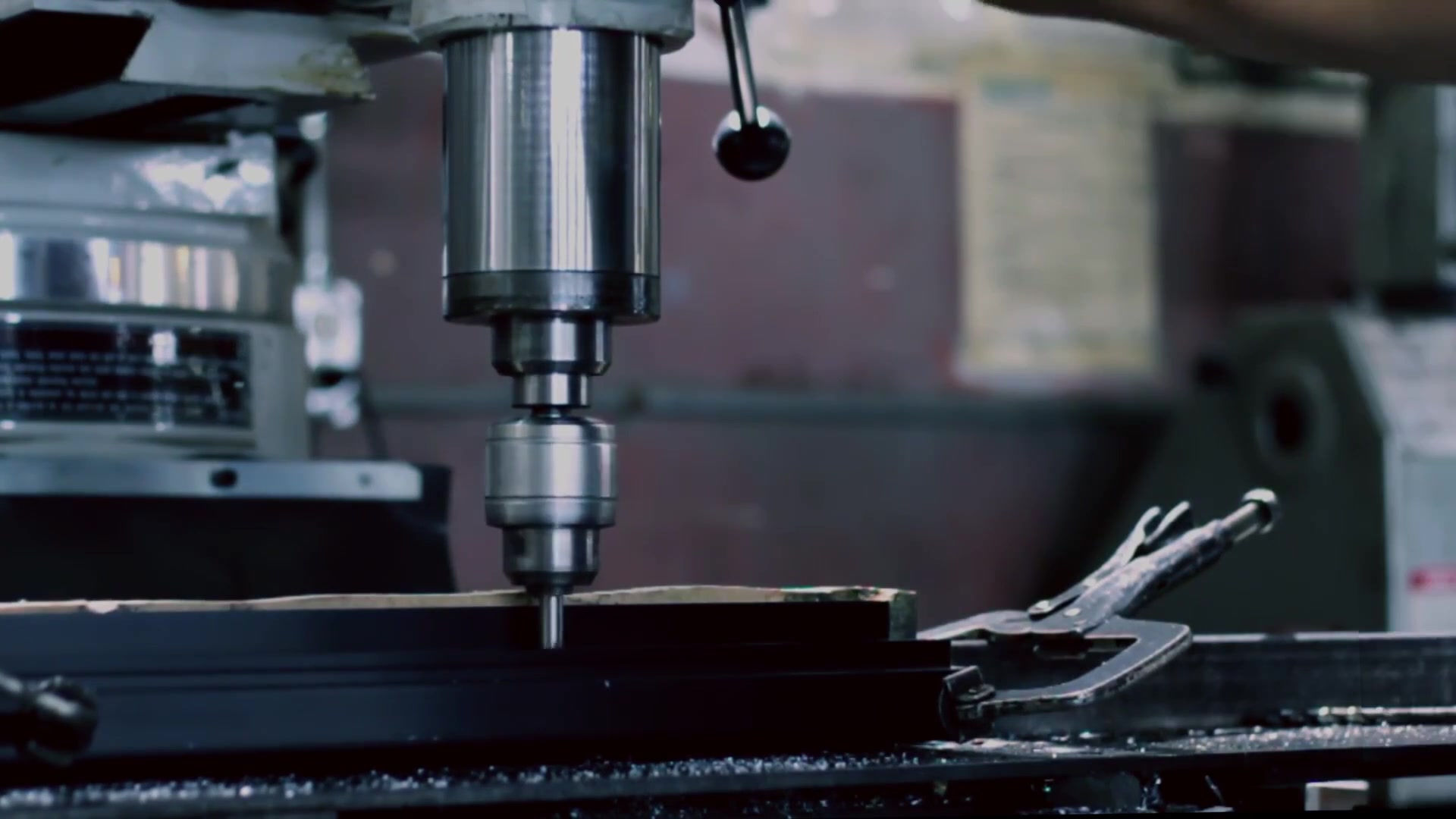
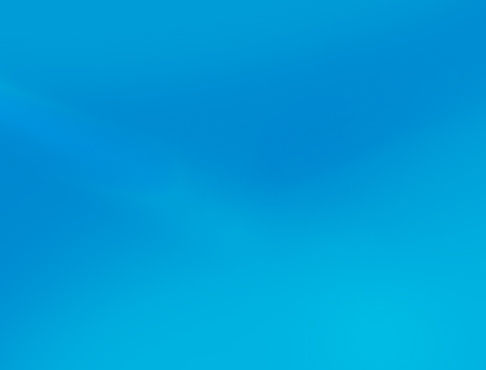
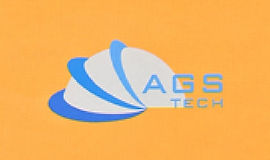
గ్లోబల్ కస్టమ్ మ్యానుఫ్యాక్చరర్, ఇంటిగ్రేటర్, కన్సాలిడేటర్, అనేక రకాల ఉత్పత్తులు & సేవల కోసం అవుట్సోర్సింగ్ భాగస్వామి.
కస్టమ్ తయారీ మరియు ఆఫ్-షెల్ఫ్ ఉత్పత్తులు & సేవల తయారీ, కల్పన, ఇంజనీరింగ్, కన్సాలిడేషన్, ఇంటిగ్రేషన్, అవుట్సోర్సింగ్ కోసం మేము మీ వన్-స్టాప్ మూలం.
మీ భాషను ఎంచుకోండి
-
కస్టమ్ తయారీ
-
దేశీయ & గ్లోబల్ కాంట్రాక్ట్ తయారీ
-
తయారీ అవుట్సోర్సింగ్
-
దేశీయ & ప్రపంచ సేకరణ
-
కన్సాలిడేషన్
-
ఇంజనీరింగ్ ఇంటిగ్రేషన్
-
ఇంజనీరింగ్ సేవలు
మేము తయారీలో ఉపయోగించే అనేక జాయినింగ్ టెక్నిక్లలో, వెల్డింగ్, బ్రేజింగ్, సోల్డరింగ్, అడెసివ్ బాండింగ్ మరియు కస్టమ్ మెకానికల్ అసెంబ్లీకి ప్రత్యేక ప్రాధాన్యత ఇవ్వబడింది, ఎందుకంటే ఈ సాంకేతికతలు హెర్మెటిక్ సీలింగ్ ఉత్పత్తుల తయారీ మరియు ప్రత్యేక మాన్యుఫ్యాక్ట్-అసెంబ్లీ వంటి అప్లికేషన్లలో విస్తృతంగా ఉపయోగించబడుతున్నాయి. అధునాతన ఉత్పత్తులు మరియు అసెంబ్లీల తయారీకి సంబంధించినవి కాబట్టి ఈ చేరిక సాంకేతికతలకు సంబంధించిన మరింత ప్రత్యేకమైన అంశాలపై మేము ఇక్కడ దృష్టి పెడతాము.
ఫ్యూజన్ వెల్డింగ్: మేము పదార్థాలను కరిగించడానికి మరియు కలపడానికి వేడిని ఉపయోగిస్తాము. విద్యుత్ లేదా అధిక శక్తి కిరణాల ద్వారా వేడి సరఫరా చేయబడుతుంది. మేము అమలు చేసే ఫ్యూజన్ వెల్డింగ్ రకాలు ఆక్సిఫ్యూయల్ గ్యాస్ వెల్డింగ్, ఆర్క్ వెల్డింగ్, హై-ఎనర్జీ-బీమ్ వెల్డింగ్.
సాలిడ్-స్టేట్ వెల్డింగ్: మేము ద్రవీభవన మరియు కలయిక లేకుండా భాగాలను కలుపుతాము. మా ఘన-స్థితి వెల్డింగ్ పద్ధతులు కోల్డ్, అల్ట్రాసోనిక్, రెసిస్టెన్స్, ఫ్రిక్షన్, ఎక్స్ప్లోషన్ వెల్డింగ్ మరియు డిఫ్యూజన్ బాండింగ్.
బ్రేజింగ్ & సోల్డరింగ్: అవి పూరక లోహాలను ఉపయోగిస్తాయి మరియు వెల్డింగ్ కంటే తక్కువ ఉష్ణోగ్రతల వద్ద పని చేసే ప్రయోజనాన్ని అందిస్తాయి, తద్వారా ఉత్పత్తులకు తక్కువ నిర్మాణ నష్టం జరుగుతుంది. సిరామిక్ నుండి మెటల్ ఫిట్టింగ్లు, హెర్మెటిక్ సీలింగ్, వాక్యూమ్ ఫీడ్త్రూలు, హై మరియు అల్ట్రాహై వాక్యూమ్ మరియు ఫ్లూయిడ్ కంట్రోల్ కాంపోనెంట్స్ వరకు ఉత్పత్తి చేసే మా బ్రేజింగ్ సౌకర్యం గురించి సమాచారాన్ని ఇక్కడ చూడవచ్చు:బ్రేజింగ్ ఫ్యాక్టరీ బ్రోచర్
అంటుకునే బంధం: పరిశ్రమలో ఉపయోగించే అడ్హెసివ్ల వైవిధ్యం మరియు అప్లికేషన్ల వైవిధ్యం కారణంగా, మేము దీని కోసం ప్రత్యేక పేజీని కలిగి ఉన్నాము. అంటుకునే బంధం గురించి మా పేజీకి వెళ్లడానికి, దయచేసి ఇక్కడ క్లిక్ చేయండి.
కస్టమ్ మెకానికల్ అసెంబ్లీ: మేము బోల్ట్లు, స్క్రూలు, నట్స్, రివెట్స్ వంటి అనేక రకాల ఫాస్టెనర్లను ఉపయోగిస్తాము. మా ఫాస్టెనర్లు ప్రామాణిక ఆఫ్-షెల్ఫ్ ఫాస్టెనర్లకు మాత్రమే పరిమితం కాలేదు. మేము ప్రామాణికం కాని మెటీరియల్ల నుండి తయారు చేయబడిన స్పెషాలిటీ ఫాస్టెనర్లను డిజైన్ చేస్తాము, అభివృద్ధి చేస్తాము మరియు తయారు చేస్తాము, తద్వారా అవి ప్రత్యేక అప్లికేషన్ల అవసరాలను తీర్చగలవు. కొన్నిసార్లు విద్యుత్ లేదా ఉష్ణ వాహకత అవసరం అయితే కొన్నిసార్లు వాహకత అవసరం. కొన్ని ప్రత్యేక అప్లికేషన్ల కోసం, ఉత్పత్తిని నాశనం చేయకుండా తొలగించలేని ప్రత్యేక ఫాస్టెనర్లను కస్టమర్ కోరుకోవచ్చు. అంతులేని ఆలోచనలు మరియు అప్లికేషన్లు ఉన్నాయి. మేము మీ కోసం అన్నీ కలిగి ఉన్నాము, ఆఫ్-షెల్ఫ్ కాకపోతే మేము దానిని త్వరగా అభివృద్ధి చేయవచ్చు. మెకానికల్ అసెంబ్లీలో మా పేజీకి వెళ్లడానికి, దయచేసి ఇక్కడ క్లిక్ చేయండి. మరిన్ని వివరాలలో మా వివిధ చేరిక పద్ధతులను పరిశీలిద్దాం.
ఆక్సిఫ్యూయల్ గ్యాస్ వెల్డింగ్ (OFW): మేము వెల్డింగ్ మంటను ఉత్పత్తి చేయడానికి ఆక్సిజన్తో కలిపిన ఇంధన వాయువును ఉపయోగిస్తాము. మేము ఎసిటిలీన్ను ఇంధనంగా మరియు ఆక్సిజన్గా ఉపయోగించినప్పుడు, మేము దానిని ఆక్సియాసిటిలీన్ గ్యాస్ వెల్డింగ్ అని పిలుస్తాము. ఆక్సిఫ్యూయల్ గ్యాస్ దహన ప్రక్రియలో రెండు రసాయన ప్రతిచర్యలు జరుగుతాయి:
C2H2 + O2 ------» 2CO + H2 + వేడి
2CO + H2 + 1.5 O2---------» 2 CO2 + H2O + హీట్
మొదటి ప్రతిచర్య ఎసిటిలీన్ను కార్బన్ మోనాక్సైడ్ మరియు హైడ్రోజన్గా విడదీస్తుంది, అయితే మొత్తం వేడిలో 33% ఉత్పత్తి చేస్తుంది. పైన ఉన్న రెండవ ప్రక్రియ హైడ్రోజన్ మరియు కార్బన్ మోనాక్సైడ్ యొక్క మరింత దహనాన్ని సూచిస్తుంది, అయితే మొత్తం వేడిలో 67% ఉత్పత్తి చేస్తుంది. మంటలో ఉష్ణోగ్రతలు 1533 నుండి 3573 కెల్విన్ మధ్య ఉంటాయి. గ్యాస్ మిశ్రమంలో ఆక్సిజన్ శాతం ముఖ్యం. ఆక్సిజన్ కంటెంట్ సగానికి పైగా ఉంటే, మంట ఆక్సిడైజింగ్ ఏజెంట్ అవుతుంది. ఇది కొన్ని లోహాలకు అవాంఛనీయమైనది అయితే మరికొన్నింటికి కావాల్సినది. ఆక్సీకరణ జ్వాల కావాల్సినప్పుడు ఒక ఉదాహరణ రాగి-ఆధారిత మిశ్రమాలు ఎందుకంటే ఇది లోహంపై నిష్క్రియ పొరను ఏర్పరుస్తుంది. మరోవైపు, ఆక్సిజన్ కంటెంట్ తగ్గినప్పుడు, పూర్తి దహన సాధ్యం కాదు మరియు మంట తగ్గించే (కార్బరైజింగ్) మంటగా మారుతుంది. తగ్గించే మంటలో ఉష్ణోగ్రతలు తక్కువగా ఉంటాయి కాబట్టి ఇది టంకం మరియు బ్రేజింగ్ వంటి ప్రక్రియలకు అనుకూలంగా ఉంటుంది. ఇతర వాయువులు కూడా సంభావ్య ఇంధనాలు, కానీ అవి ఎసిటిలీన్ కంటే కొన్ని ప్రతికూలతలు కలిగి ఉంటాయి. అప్పుడప్పుడు మేము పూరక రాడ్లు లేదా వైర్ రూపంలో వెల్డ్ జోన్కు పూరక లోహాలను సరఫరా చేస్తాము. వాటిలో కొన్ని ఉపరితలాల ఆక్సీకరణను నిరోధించడానికి ఫ్లక్స్తో పూత పూయబడి తద్వారా కరిగిన లోహాన్ని రక్షిస్తాయి. ఫ్లక్స్ మాకు ఇచ్చే అదనపు ప్రయోజనం వెల్డ్ జోన్ నుండి ఆక్సైడ్లు మరియు ఇతర పదార్ధాల తొలగింపు. ఇది బలమైన బంధానికి దారితీస్తుంది. ఆక్సిఫ్యూయల్ గ్యాస్ వెల్డింగ్ యొక్క వైవిధ్యం ప్రెజర్ గ్యాస్ వెల్డింగ్, ఇక్కడ రెండు భాగాలు ఆక్సియాసిటిలీన్ గ్యాస్ టార్చ్ని ఉపయోగించి వాటి ఇంటర్ఫేస్ వద్ద వేడి చేయబడతాయి మరియు ఇంటర్ఫేస్ కరగడం ప్రారంభించిన తర్వాత, టార్చ్ ఉపసంహరించబడుతుంది మరియు రెండు భాగాలను కలిపి నొక్కడానికి అక్షసంబంధ శక్తి వర్తించబడుతుంది. ఇంటర్ఫేస్ పటిష్టం అయ్యే వరకు.
ARC వెల్డింగ్: ఎలక్ట్రోడ్ చిట్కా మరియు వెల్డింగ్ చేయవలసిన భాగాల మధ్య ఆర్క్ను ఉత్పత్తి చేయడానికి మేము విద్యుత్ శక్తిని ఉపయోగిస్తాము. విద్యుత్ సరఫరా AC లేదా DC కావచ్చు, అయితే ఎలక్ట్రోడ్లు వినియోగించదగినవి లేదా వినియోగించలేనివి. ఆర్క్ వెల్డింగ్లో ఉష్ణ బదిలీ క్రింది సమీకరణం ద్వారా వ్యక్తీకరించబడుతుంది:
H / l = ex VI / v
ఇక్కడ H అనేది హీట్ ఇన్పుట్, l అనేది వెల్డ్ పొడవు, V మరియు I అనేది వోల్టేజ్ మరియు కరెంట్ వర్తించబడుతుంది, v అనేది వెల్డింగ్ వేగం మరియు e అనేది ప్రక్రియ సామర్థ్యం. అధిక సామర్థ్యం "e" మరింత ప్రయోజనకరంగా అందుబాటులో ఉన్న శక్తిని పదార్థాన్ని కరిగించడానికి ఉపయోగించబడుతుంది. హీట్ ఇన్పుట్ కూడా ఇలా వ్యక్తీకరించవచ్చు:
H = ux (వాల్యూమ్) = ux A xl
ఇక్కడ u అనేది కరిగే నిర్దిష్ట శక్తి, A అనేది వెల్డ్ యొక్క క్రాస్ సెక్షన్ మరియు l వెల్డ్ పొడవు. పై రెండు సమీకరణాల నుండి మనం పొందవచ్చు:
v = మాజీ VI / u A
ఆర్క్ వెల్డింగ్ యొక్క వైవిధ్యం షీల్డ్ మెటల్ ఆర్క్ వెల్డింగ్ (SMAW) ఇది అన్ని పారిశ్రామిక మరియు నిర్వహణ వెల్డింగ్ ప్రక్రియలలో 50% ఉంటుంది. ఎలక్ట్రిక్ ఆర్క్ వెల్డింగ్ (స్టిక్ వెల్డింగ్) అనేది పూతతో కూడిన ఎలక్ట్రోడ్ యొక్క కొనను వర్క్పీస్కు తాకడం ద్వారా మరియు ఆర్క్ను నిర్వహించడానికి తగినంత దూరానికి త్వరగా ఉపసంహరించుకోవడం ద్వారా నిర్వహించబడుతుంది. ఎలక్ట్రోడ్లు సన్నగా మరియు పొడవాటి కర్రలుగా ఉన్నందున మేము ఈ ప్రక్రియను స్టిక్-వెల్డింగ్ అని కూడా పిలుస్తాము. వెల్డింగ్ ప్రక్రియలో, ఎలక్ట్రోడ్ యొక్క కొన దాని పూత మరియు ఆర్క్ సమీపంలోని బేస్ మెటల్తో పాటు కరుగుతుంది. ఎలక్ట్రోడ్ పూత నుండి మూల లోహం, ఎలక్ట్రోడ్ మెటల్ మరియు పదార్ధాల మిశ్రమం వెల్డ్ ప్రాంతంలో ఘనీభవిస్తుంది. ఎలక్ట్రోడ్ యొక్క పూత డీఆక్సిడైజ్ చేస్తుంది మరియు వెల్డ్ ప్రాంతంలో ఒక రక్షిత వాయువును అందిస్తుంది, తద్వారా పర్యావరణంలోని ఆక్సిజన్ నుండి రక్షించబడుతుంది. అందువల్ల ఈ ప్రక్రియను షీల్డ్ మెటల్ ఆర్క్ వెల్డింగ్ అంటారు. మేము వాంఛనీయ వెల్డ్ పనితీరు కోసం 50 మరియు 300 ఆంపియర్ల మధ్య కరెంట్లను ఉపయోగిస్తాము మరియు పవర్ లెవెల్స్ సాధారణంగా 10 kW కంటే తక్కువ. DC కరెంట్ (కరెంట్ ప్రవాహం యొక్క దిశ) యొక్క ధ్రువణత కూడా ముఖ్యమైనది. వర్క్పీస్ సానుకూలంగా మరియు ఎలక్ట్రోడ్ ప్రతికూలంగా ఉన్న స్ట్రెయిట్ ధ్రువణత షీట్ మెటల్ల వెల్డింగ్లో దాని నిస్సార వ్యాప్తి కారణంగా మరియు చాలా విస్తృత ఖాళీలు ఉన్న కీళ్లకు ప్రాధాన్యత ఇవ్వబడుతుంది. మనకు రివర్స్ పోలారిటీ ఉన్నప్పుడు, అంటే ఎలక్ట్రోడ్ సానుకూలంగా మరియు వర్క్పీస్ ప్రతికూలంగా ఉన్నప్పుడు మనం లోతైన వెల్డ్ చొచ్చుకుపోవడాన్ని సాధించగలము. AC కరెంట్తో, మేము పల్సేటింగ్ ఆర్క్లను కలిగి ఉన్నందున, మేము పెద్ద వ్యాసం కలిగిన ఎలక్ట్రోడ్లు మరియు గరిష్ట ప్రవాహాలను ఉపయోగించి మందపాటి విభాగాలను వెల్డ్ చేయవచ్చు. SMAW వెల్డింగ్ పద్ధతి 3 నుండి 19 మిమీ వరకు ఉండే వర్క్పీస్ మందం మరియు మల్టిపుల్-పాస్ టెక్నిక్లను ఉపయోగించడం కోసం అనుకూలంగా ఉంటుంది. వెల్డ్ పైన ఏర్పడిన స్లాగ్ ఒక వైర్ బ్రష్ను ఉపయోగించి తొలగించాల్సిన అవసరం ఉంది, తద్వారా వెల్డ్ ప్రదేశంలో తుప్పు మరియు వైఫల్యం ఉండదు. ఇది షీల్డ్ మెటల్ ఆర్క్ వెల్డింగ్ ఖర్చును పెంచుతుంది. ఏది ఏమైనప్పటికీ SMAW అనేది పరిశ్రమ మరియు మరమ్మత్తు పనిలో అత్యంత ప్రజాదరణ పొందిన వెల్డింగ్ టెక్నిక్.
సబ్మెర్జ్డ్ ఆర్క్ వెల్డింగ్ (SAW): ఈ ప్రక్రియలో మేము లైమ్, సిలికా, కాల్షియం ఫ్లోరైడ్, మాంగనీస్ ఆక్సైడ్ వంటి గ్రాన్యులర్ ఫ్లక్స్ మెటీరియల్లను ఉపయోగించి వెల్డ్ ఆర్క్ను షీల్డ్ చేస్తాము. గ్రాన్యులర్ ఫ్లక్స్ ఒక ముక్కు ద్వారా గురుత్వాకర్షణ ప్రవాహం ద్వారా వెల్డ్ జోన్లోకి మృదువుగా ఉంటుంది. కరిగిన వెల్డ్ జోన్ను కప్పి ఉంచే ఫ్లక్స్ స్పార్క్స్, పొగలు, UV రేడియేషన్ మొదలైన వాటి నుండి గణనీయంగా రక్షిస్తుంది మరియు థర్మల్ ఇన్సులేటర్గా పనిచేస్తుంది, తద్వారా వేడిని వర్క్పీస్లోకి లోతుగా చొచ్చుకుపోయేలా చేస్తుంది. ఫ్యూజ్ చేయని ఫ్లక్స్ పునరుద్ధరించబడుతుంది, చికిత్స చేయబడుతుంది మరియు తిరిగి ఉపయోగించబడుతుంది. బేర్ కాయిల్ ఎలక్ట్రోడ్గా ఉపయోగించబడుతుంది మరియు వెల్డ్ ప్రాంతానికి ట్యూబ్ ద్వారా అందించబడుతుంది. మేము 300 మరియు 2000 ఆంపియర్ల మధ్య ప్రవాహాలను ఉపయోగిస్తాము. వెల్డింగ్ సమయంలో వృత్తాకార నిర్మాణం (పైపులు వంటివి) యొక్క భ్రమణ సాధ్యమైతే సబ్మెర్జ్డ్ ఆర్క్ వెల్డింగ్ (SAW) ప్రక్రియ సమాంతర మరియు ఫ్లాట్ స్థానాలు మరియు వృత్తాకార వెల్డ్స్కు పరిమితం చేయబడింది. వేగం 5 మీ/నిమిషానికి చేరుకోవచ్చు. SAW ప్రక్రియ మందపాటి ప్లేట్లకు అనుకూలంగా ఉంటుంది మరియు అధిక-నాణ్యత, కఠినమైన, సాగే మరియు ఏకరీతి వెల్డ్స్లో ఫలితాలను అందిస్తుంది. ఉత్పాదకత, అంటే SMAW ప్రక్రియతో పోలిస్తే గంటకు జమ చేయబడిన వెల్డ్ మెటీరియల్ మొత్తం 4 నుండి 10 రెట్లు ఎక్కువ.
మరొక ఆర్క్ వెల్డింగ్ ప్రక్రియ, అవి GAS METAL ARC వెల్డింగ్ (GMAW) లేదా ప్రత్యామ్నాయంగా మెటల్ ఇన్నర్ట్ గ్యాస్ వెల్డింగ్ (MIG)గా సూచించబడుతుంది, ఇది హీలియం, ఆర్గాన్, కార్బన్ డయాక్సైడ్ వంటి బాహ్య వాయువుల ద్వారా రక్షించబడే వెల్డ్ ప్రాంతంపై ఆధారపడి ఉంటుంది. ఎలక్ట్రోడ్ మెటల్లో అదనపు డియోక్సిడైజర్లు ఉండవచ్చు. వినియోగించదగిన వైర్ వెల్డ్ జోన్లోకి నాజిల్ ద్వారా మృదువుగా ఉంటుంది. బాట్ ఫెర్రస్ మరియు నాన్ ఫెర్రస్ లోహాలతో కూడిన ఫాబ్రికేషన్ గ్యాస్ మెటల్ ఆర్క్ వెల్డింగ్ (GMAW) ఉపయోగించి నిర్వహించబడుతుంది. వెల్డింగ్ ఉత్పాదకత SMAW ప్రక్రియ కంటే 2 రెట్లు ఎక్కువ. ఆటోమేటెడ్ వెల్డింగ్ పరికరాలు ఉపయోగించబడుతున్నాయి. ఈ ప్రక్రియలో మెటల్ మూడు మార్గాలలో ఒకదానిలో బదిలీ చేయబడుతుంది: "స్ప్రే ట్రాన్స్ఫర్" అనేది ఎలక్ట్రోడ్ నుండి వెల్డ్ ప్రాంతానికి సెకనుకు అనేక వందల చిన్న మెటల్ బిందువుల బదిలీని కలిగి ఉంటుంది. మరోవైపు "గ్లోబులర్ ట్రాన్స్ఫర్"లో, కార్బన్ డయాక్సైడ్ అధికంగా ఉండే వాయువులు ఉపయోగించబడతాయి మరియు కరిగిన లోహం యొక్క గ్లోబుల్స్ ఎలక్ట్రిక్ ఆర్క్ ద్వారా ముందుకు సాగుతాయి. వెల్డింగ్ ప్రవాహాలు ఎక్కువగా ఉంటాయి మరియు స్ప్రే బదిలీ కంటే ఎక్కువ వెల్డింగ్ వేగం, లోతుగా వ్యాప్తి చెందుతాయి. అందువలన గ్లోబులర్ బదిలీ భారీ విభాగాలను వెల్డింగ్ చేయడానికి ఉత్తమం. చివరగా, "షార్ట్ సర్క్యూటింగ్" పద్ధతిలో, ఎలక్ట్రోడ్ చిట్కా కరిగిన వెల్డ్ పూల్ను తాకుతుంది, 50 చుక్కలు/సెకను కంటే ఎక్కువ రేటుతో మెటల్గా షార్ట్ సర్క్యూట్ చేయడం వ్యక్తిగత బిందువులలో బదిలీ చేయబడుతుంది. సన్నని తీగతో పాటు తక్కువ ప్రవాహాలు మరియు వోల్టేజీలు ఉపయోగించబడతాయి. ఉపయోగించిన శక్తులు సుమారు 2 kW మరియు ఉష్ణోగ్రతలు సాపేక్షంగా తక్కువగా ఉంటాయి, ఈ పద్ధతి 6mm మందం కంటే తక్కువ సన్నని షీట్లకు అనుకూలంగా ఉంటుంది.
మరొక వైవిధ్యం FLUX-CORED ARC వెల్డింగ్ (FCAW) ప్రక్రియ గ్యాస్ మెటల్ ఆర్క్ వెల్డింగ్ వలె ఉంటుంది, ఎలక్ట్రోడ్ అనేది ఫ్లక్స్తో నిండిన ట్యూబ్. కోర్డ్-ఫ్లక్స్ ఎలక్ట్రోడ్లను ఉపయోగించడం వల్ల కలిగే ప్రయోజనాలు ఏమిటంటే అవి మరింత స్థిరమైన ఆర్క్లను ఉత్పత్తి చేస్తాయి, SMAW వెల్డింగ్, మెరుగైన వెల్డింగ్ ఆకృతులతో పోలిస్తే వెల్డ్ లోహాల లక్షణాలను మెరుగుపరచడం, తక్కువ పెళుసుగా మరియు సౌకర్యవంతమైన స్వభావాన్ని దాని ఫ్లక్స్ను మెరుగుపరిచే అవకాశాన్ని ఇస్తాయి. సెల్ఫ్-షీల్డ్ కోర్డ్ ఎలక్ట్రోడ్లు వాతావరణానికి వ్యతిరేకంగా వెల్డ్ జోన్ను రక్షించే పదార్థాలను కలిగి ఉంటాయి. మేము దాదాపు 20 kW శక్తిని ఉపయోగిస్తాము. GMAW ప్రక్రియ వలె, FCAW ప్రక్రియ కూడా నిరంతర వెల్డింగ్ కోసం ప్రక్రియలను ఆటోమేట్ చేయడానికి అవకాశాన్ని అందిస్తుంది మరియు ఇది ఆర్థికంగా ఉంటుంది. ఫ్లక్స్ కోర్కు వివిధ మిశ్రమాలను జోడించడం ద్వారా వివిధ వెల్డ్ మెటల్ కెమిస్ట్రీలను అభివృద్ధి చేయవచ్చు.
ఎలెక్ట్రోగ్యాస్ వెల్డింగ్ (EGW) లో మేము అంచు నుండి అంచు వరకు ఉంచిన ముక్కలను వెల్డ్ చేస్తాము. దీనిని కొన్నిసార్లు బట్ వెల్డింగ్ అని కూడా పిలుస్తారు. వెల్డ్ మెటల్ చేరడానికి రెండు ముక్కల మధ్య వెల్డ్ కుహరంలో ఉంచబడుతుంది. కరిగిన స్లాగ్ బయటకు పోకుండా ఉండటానికి స్థలం రెండు నీటి-చల్లని ఆనకట్టలచే చుట్టబడి ఉంటుంది. మెకానికల్ డ్రైవ్ల ద్వారా ఆనకట్టలు పైకి తరలించబడతాయి. వర్క్పీస్ని తిప్పగలిగినప్పుడు, పైపుల చుట్టుకొలత వెల్డింగ్ కోసం ఎలక్ట్రోగాస్ వెల్డింగ్ టెక్నిక్ని కూడా ఉపయోగించవచ్చు. ఎలక్ట్రోడ్లు ఒక నిరంతర ఆర్క్ ఉంచడానికి ఒక కండ్యూట్ ద్వారా మృదువుగా ఉంటాయి. కరెంట్లు దాదాపు 400 ఆంపియర్లు లేదా 750 ఆంపియర్లు మరియు పవర్ లెవల్స్ 20 kW చుట్టూ ఉండవచ్చు. ఫ్లక్స్-కోర్డ్ ఎలక్ట్రోడ్ లేదా బాహ్య మూలం నుండి ఉద్భవించే జడ వాయువులు రక్షణను అందిస్తాయి. మేము 12mm నుండి 75mm వరకు మందంతో స్టీల్స్, టైటానియం....మొదలైన లోహాల కోసం ఎలక్ట్రోగాస్ వెల్డింగ్ (EGW)ని ఉపయోగిస్తాము. సాంకేతికత పెద్ద నిర్మాణాలకు బాగా సరిపోతుంది.
అయినప్పటికీ, ELECTROSLAG WELDING (ESW) అని పిలువబడే మరొక సాంకేతికతలో ఆర్క్ ఎలక్ట్రోడ్ మరియు వర్క్పీస్ యొక్క దిగువ మధ్య మండించబడుతుంది మరియు ఫ్లక్స్ జోడించబడుతుంది. కరిగిన స్లాగ్ ఎలక్ట్రోడ్ చిట్కాకు చేరుకున్నప్పుడు, ఆర్క్ ఆరిపోతుంది. కరిగిన స్లాగ్ యొక్క విద్యుత్ నిరోధకత ద్వారా శక్తి నిరంతరం సరఫరా చేయబడుతుంది. మేము 50 mm మరియు 900 mm మరియు అంతకంటే ఎక్కువ మందంతో ప్లేట్లను వెల్డ్ చేయవచ్చు. కరెంట్లు దాదాపు 600 ఆంపియర్లు అయితే వోల్టేజీలు 40 – 50 V మధ్య ఉంటాయి. వెల్డింగ్ వేగం 12 నుండి 36 mm/min వరకు ఉంటుంది. అప్లికేషన్లు ఎలక్ట్రోగాస్ వెల్డింగ్ మాదిరిగానే ఉంటాయి.
మా వినియోగించలేని ఎలక్ట్రోడ్ ప్రక్రియలలో ఒకటి, TUNGSTEN ఇన్నర్ట్ గ్యాస్ వెల్డింగ్ (TIG) అని కూడా పిలువబడే GAS TUNGSTEN ARC వెల్డింగ్ (GTAW) అనేది వైర్ ద్వారా పూరక లోహాన్ని సరఫరా చేస్తుంది. దగ్గరగా సరిపోయే కీళ్ల కోసం కొన్నిసార్లు మేము పూరక లోహాన్ని ఉపయోగించము. TIG ప్రక్రియలో మేము ఫ్లక్స్ను ఉపయోగించము, కానీ షీల్డింగ్ కోసం ఆర్గాన్ మరియు హీలియంను ఉపయోగిస్తాము. టంగ్స్టన్ అధిక ద్రవీభవన స్థానం కలిగి ఉంది మరియు TIG వెల్డింగ్ ప్రక్రియలో వినియోగించబడదు, కాబట్టి స్థిరమైన కరెంట్ అలాగే ఆర్క్ గ్యాప్లను నిర్వహించవచ్చు. శక్తి స్థాయిలు 8 నుండి 20 kW మధ్య ఉంటాయి మరియు 200 ఆంపియర్ (DC) లేదా 500 Ampere (AC) వద్ద కరెంట్లు ఉంటాయి. అల్యూమినియం మరియు మెగ్నీషియం కోసం మేము దాని ఆక్సైడ్ క్లీనింగ్ ఫంక్షన్ కోసం AC కరెంట్ని ఉపయోగిస్తాము. టంగ్స్టన్ ఎలక్ట్రోడ్ యొక్క కాలుష్యాన్ని నివారించడానికి, మేము కరిగిన లోహాలతో దాని సంబంధాన్ని నివారిస్తాము. గ్యాస్ టంగ్స్టన్ ఆర్క్ వెల్డింగ్ (GTAW) సన్నని లోహాలను వెల్డింగ్ చేయడానికి ప్రత్యేకంగా ఉపయోగపడుతుంది. GTAW వెల్డ్స్ మంచి ఉపరితల ముగింపుతో చాలా అధిక నాణ్యతతో ఉంటాయి.
హైడ్రోజన్ వాయువు యొక్క అధిక ధర కారణంగా, తక్కువ తరచుగా ఉపయోగించే సాంకేతికత అటామిక్ హైడ్రోజన్ వెల్డింగ్ (AHW), ఇక్కడ మేము ప్రవహించే హైడ్రోజన్ వాయువు యొక్క రక్షిత వాతావరణంలో రెండు టంగ్స్టన్ ఎలక్ట్రోడ్ల మధ్య ఆర్క్ను ఉత్పత్తి చేస్తాము. AHW అనేది వినియోగించలేని ఎలక్ట్రోడ్ వెల్డింగ్ ప్రక్రియ కూడా. డయాటోమిక్ హైడ్రోజన్ వాయువు H2 ఉష్ణోగ్రతలు 6273 కెల్విన్ కంటే ఎక్కువగా ఉన్న వెల్డింగ్ ఆర్క్ దగ్గర దాని పరమాణు రూపంలోకి విచ్ఛిన్నమవుతుంది. విచ్ఛిన్నం చేస్తున్నప్పుడు, ఇది ఆర్క్ నుండి పెద్ద మొత్తంలో వేడిని గ్రహిస్తుంది. హైడ్రోజన్ పరమాణువులు సాపేక్షంగా చల్లటి ఉపరితలంగా ఉండే వెల్డ్ జోన్ను తాకినప్పుడు, అవి డయాటోమిక్ రూపంలోకి తిరిగి కలిసిపోయి నిల్వ చేయబడిన వేడిని విడుదల చేస్తాయి. వర్క్పీస్ను ఆర్క్ దూరానికి మార్చడం ద్వారా శక్తి మారవచ్చు.
మరొక వినియోగించలేని ఎలక్ట్రోడ్ ప్రక్రియలో, ప్లాస్మా ARC వెల్డింగ్ (PAW) మేము వెల్డ్ జోన్ వైపు మళ్లించబడిన సాంద్రీకృత ప్లాస్మా ఆర్క్ని కలిగి ఉన్నాము. PAWలో ఉష్ణోగ్రతలు 33,273 కెల్విన్లకు చేరుకుంటాయి. దాదాపు సమాన సంఖ్యలో ఎలక్ట్రాన్లు మరియు అయాన్లు ప్లాస్మా వాయువును తయారు చేస్తాయి. తక్కువ-కరెంట్ పైలట్ ఆర్క్ టంగ్స్టన్ ఎలక్ట్రోడ్ మరియు ఆరిఫైస్ మధ్య ఉన్న ప్లాస్మాను ప్రారంభిస్తుంది. ఆపరేటింగ్ కరెంట్లు సాధారణంగా 100 ఆంపియర్లు ఉంటాయి. ఒక పూరక మెటల్ ఫీడ్ కావచ్చు. ప్లాస్మా ఆర్క్ వెల్డింగ్లో, షీల్డింగ్ అనేది బయటి షీల్డింగ్ రింగ్ ద్వారా మరియు ఆర్గాన్ మరియు హీలియం వంటి వాయువులను ఉపయోగించడం ద్వారా సాధించబడుతుంది. ప్లాస్మా ఆర్క్ వెల్డింగ్లో, ఆర్క్ ఎలక్ట్రోడ్ మరియు వర్క్పీస్ మధ్య లేదా ఎలక్ట్రోడ్ మరియు నాజిల్ మధ్య ఉండవచ్చు. ఈ వెల్డింగ్ సాంకేతికత అధిక శక్తి ఏకాగ్రత, లోతైన మరియు ఇరుకైన వెల్డింగ్ సామర్ధ్యం, మెరుగైన ఆర్క్ స్థిరత్వం, 1 మీటర్/నిమిషానికి అధిక వెల్డింగ్ వేగం, తక్కువ ఉష్ణ వక్రీకరణ వంటి ఇతర పద్ధతుల కంటే ప్రయోజనాలను కలిగి ఉంది. మేము సాధారణంగా ప్లాస్మా ఆర్క్ వెల్డింగ్ను 6 మిమీ కంటే తక్కువ మందం మరియు కొన్నిసార్లు అల్యూమినియం మరియు టైటానియం కోసం 20 మిమీ వరకు ఉపయోగిస్తాము.
హై-ఎనర్జీ-బీమ్ వెల్డింగ్: ఎలక్ట్రాన్-బీమ్ వెల్డింగ్ (EBW) మరియు లేజర్ వెల్డింగ్ (LBW)తో రెండు రకాలైన ఫ్యూజన్ వెల్డింగ్ పద్ధతి. మా హైటెక్ ఉత్పత్తుల తయారీ పని కోసం ఈ పద్ధతులు ప్రత్యేక విలువను కలిగి ఉంటాయి. ఎలక్ట్రాన్-బీమ్ వెల్డింగ్లో, హై స్పీడ్ ఎలక్ట్రాన్లు వర్క్పీస్ను తాకాయి మరియు వాటి గతి శక్తి వేడిగా మార్చబడుతుంది. ఎలక్ట్రాన్ల యొక్క ఇరుకైన పుంజం వాక్యూమ్ చాంబర్లో సులభంగా ప్రయాణిస్తుంది. సాధారణంగా మనం ఈ-బీమ్ వెల్డింగ్లో అధిక వాక్యూమ్ని ఉపయోగిస్తాము. 150 mm మందపాటి ప్లేట్లు వెల్డింగ్ చేయబడతాయి. రక్షిత వాయువులు, ఫ్లక్స్ లేదా పూరక పదార్థం అవసరం లేదు. ఎలెక్రాన్ బీమ్ గన్లు 100 kW సామర్థ్యాలను కలిగి ఉంటాయి. 30 వరకు అధిక కారక నిష్పత్తులతో లోతైన మరియు ఇరుకైన వెల్డ్స్ మరియు చిన్న వేడి-ప్రభావిత మండలాలు సాధ్యమే. వెల్డింగ్ వేగం 12 m / min చేరవచ్చు. లేజర్-బీమ్ వెల్డింగ్లో మేము అధిక-శక్తి లేజర్లను వేడికి మూలంగా ఉపయోగిస్తాము. అధిక సాంద్రత కలిగిన 10 మైక్రాన్ల చిన్న లేజర్ కిరణాలు వర్క్పీస్లోకి లోతుగా చొచ్చుకుపోయేలా చేస్తాయి. లేజర్-బీమ్ వెల్డింగ్తో 10 వరకు లోతు నుండి వెడల్పు నిష్పత్తులు సాధ్యమవుతాయి. మేము పల్సెడ్ మరియు నిరంతర వేవ్ లేజర్లు రెండింటినీ ఉపయోగిస్తాము, మునుపటిది సన్నని పదార్థాల కోసం అప్లికేషన్లలో మరియు రెండోది ఎక్కువగా 25 మిమీ వరకు మందపాటి వర్క్పీస్ల కోసం. శక్తి స్థాయిలు 100 kW వరకు ఉంటాయి. లేజర్ పుంజం వెల్డింగ్ అనేది ఆప్టికల్గా చాలా ప్రతిబింబించే పదార్థాలకు సరిగ్గా సరిపోదు. వెల్డింగ్ ప్రక్రియలో వాయువులను కూడా ఉపయోగించవచ్చు. లేజర్ బీమ్ వెల్డింగ్ పద్ధతి ఆటోమేషన్ & అధిక వాల్యూమ్ తయారీకి బాగా సరిపోతుంది మరియు 2.5 m/min మరియు 80 m/min మధ్య వెల్డింగ్ వేగాన్ని అందించగలదు. ఈ వెల్డింగ్ టెక్నిక్ అందించే ఒక ప్రధాన ప్రయోజనం ఇతర సాంకేతికతలను ఉపయోగించలేని ప్రాంతాలకు యాక్సెస్. అలాంటి కష్టతరమైన ప్రాంతాలకు లేజర్ కిరణాలు సులభంగా ప్రయాణించగలవు. ఎలక్ట్రాన్-బీమ్ వెల్డింగ్లో వలె వాక్యూమ్ అవసరం లేదు. లేజర్ బీమ్ వెల్డింగ్తో మంచి నాణ్యత & బలం, తక్కువ సంకోచం, తక్కువ వక్రీకరణ, తక్కువ సచ్ఛిద్రత కలిగిన వెల్డ్స్ను పొందవచ్చు. ఫైబర్ ఆప్టిక్ కేబుల్స్ ఉపయోగించి లేజర్ కిరణాలను సులభంగా మార్చవచ్చు మరియు ఆకృతి చేయవచ్చు. ఖచ్చితత్వంతో కూడిన హెర్మెటిక్ అసెంబ్లీలు, ఎలక్ట్రానిక్ ప్యాకేజీలు... మొదలైన వాటి వెల్డింగ్ కోసం సాంకేతికత బాగా సరిపోతుంది.
మన SOLID STATE వెల్డింగ్ పద్ధతులను చూద్దాం. కోల్డ్ వెల్డింగ్ (CW) అనేది ఒక ప్రక్రియ, ఇక్కడ వేడికి బదులుగా పీడనం లేదా రోల్స్ ఉపయోగించి జత చేయబడిన భాగాలకు వర్తించబడుతుంది. కోల్డ్ వెల్డింగ్లో, సంభోగం చేసే భాగాలలో కనీసం ఒకటి సాగేదిగా ఉండాలి. రెండు సారూప్య పదార్థాలతో ఉత్తమ ఫలితాలు పొందవచ్చు. కోల్డ్ వెల్డింగ్తో జత చేయాల్సిన రెండు లోహాలు అసమానంగా ఉంటే, మనం బలహీనమైన మరియు పెళుసుగా ఉండే కీళ్లను పొందవచ్చు. ఎలక్ట్రికల్ కనెక్షన్లు, హీట్ సెన్సిటివ్ కంటైనర్ అంచులు, థర్మోస్టాట్ల కోసం బైమెటాలిక్ స్ట్రిప్స్ వంటి మృదువైన, సాగే మరియు చిన్న వర్క్పీస్లకు కోల్డ్ వెల్డింగ్ పద్ధతి బాగా సరిపోతుంది. కోల్డ్ వెల్డింగ్ యొక్క ఒక వైవిధ్యం రోల్ బాండింగ్ (లేదా రోల్ వెల్డింగ్), ఇక్కడ ఒత్తిడి ఒక జత రోల్స్ ద్వారా వర్తించబడుతుంది. కొన్నిసార్లు మేము మెరుగైన ఇంటర్ఫేషియల్ బలం కోసం ఎత్తైన ఉష్ణోగ్రతల వద్ద రోల్ వెల్డింగ్ చేస్తాము.
మేము ఉపయోగించే మరొక ఘన స్థితి వెల్డింగ్ ప్రక్రియ అల్ట్రాసోనిక్ వెల్డింగ్ (USW), ఇక్కడ వర్క్పీస్లు స్థిరమైన సాధారణ శక్తికి మరియు డోలనం చేసే షీరింగ్ ఒత్తిళ్లకు లోబడి ఉంటాయి. ఓసిలేటింగ్ షిరింగ్ ఒత్తిళ్లు ట్రాన్స్డ్యూసర్ యొక్క కొన ద్వారా వర్తించబడతాయి. అల్ట్రాసోనిక్ వెల్డింగ్ 10 నుండి 75 kHz వరకు ఫ్రీక్వెన్సీలతో డోలనాలను అమలు చేస్తుంది. సీమ్ వెల్డింగ్ వంటి కొన్ని అనువర్తనాల్లో, మేము తిరిగే వెల్డింగ్ డిస్క్ను చిట్కాగా ఉపయోగిస్తాము. వర్క్పీస్లకు వర్తించే షీరింగ్ ఒత్తిళ్లు చిన్న ప్లాస్టిక్ వైకల్యాలకు కారణమవుతాయి, ఆక్సైడ్ పొరలు, కలుషితాలను విచ్ఛిన్నం చేస్తాయి మరియు ఘన స్థితి బంధానికి దారితీస్తాయి. అల్ట్రాసోనిక్ వెల్డింగ్లో ఉండే ఉష్ణోగ్రతలు లోహాల ద్రవీభవన స్థానం ఉష్ణోగ్రతల కంటే తక్కువగా ఉంటాయి మరియు కలయిక జరగదు. ప్లాస్టిక్ల వంటి నాన్మెటాలిక్ పదార్థాల కోసం మేము తరచుగా అల్ట్రాసోనిక్ వెల్డింగ్ (USW) ప్రక్రియను ఉపయోగిస్తాము. థర్మోప్లాస్టిక్స్లో, ఉష్ణోగ్రతలు ద్రవీభవన స్థానాలకు చేరుకుంటాయి.
మరొక ప్రసిద్ధ సాంకేతికత, FRICTION వెల్డింగ్ (FRW)లో చేరాల్సిన వర్క్పీస్ల ఇంటర్ఫేస్లో ఘర్షణ ద్వారా వేడి ఉత్పత్తి అవుతుంది. ఘర్షణ వెల్డింగ్లో మేము వర్క్పీస్లలో ఒకదాన్ని స్థిరంగా ఉంచుతాము, మరొక వర్క్పీస్ ఫిక్చర్లో ఉంచబడుతుంది మరియు స్థిరమైన వేగంతో తిప్పబడుతుంది. అప్పుడు వర్క్పీస్లు అక్షసంబంధ శక్తి క్రిందకి తీసుకురాబడతాయి. రాపిడి వెల్డింగ్లో భ్రమణ ఉపరితల వేగం కొన్ని సందర్భాల్లో 900మీ/నిమిషానికి చేరుకోవచ్చు. తగినంత ఇంటర్ఫేషియల్ పరిచయం తర్వాత, తిరిగే వర్క్పీస్ అకస్మాత్తుగా ఆపివేయబడుతుంది మరియు అక్షసంబంధ శక్తి పెరుగుతుంది. వెల్డ్ జోన్ సాధారణంగా ఇరుకైన ప్రాంతం. వివిధ రకాల పదార్థాలతో తయారు చేయబడిన ఘన మరియు గొట్టపు భాగాలను చేరడానికి ఘర్షణ వెల్డింగ్ సాంకేతికతను ఉపయోగించవచ్చు. FRWలోని ఇంటర్ఫేస్లో కొంత ఫ్లాష్ అభివృద్ధి చెందుతుంది, అయితే ఈ ఫ్లాష్ను సెకండరీ మ్యాచింగ్ లేదా గ్రైండింగ్ ద్వారా తొలగించవచ్చు. ఘర్షణ వెల్డింగ్ ప్రక్రియ యొక్క వైవిధ్యాలు ఉన్నాయి. ఉదాహరణకు "జడత్వం రాపిడి వెల్డింగ్" అనేది ఒక ఫ్లైవీల్ను కలిగి ఉంటుంది, దీని భ్రమణ గతి శక్తి భాగాలను వెల్డింగ్ చేయడానికి ఉపయోగించబడుతుంది. ఫ్లైవీల్ ఆగినప్పుడు వెల్డ్ పూర్తవుతుంది. భ్రమణ ద్రవ్యరాశి వైవిధ్యంగా ఉంటుంది మరియు తద్వారా భ్రమణ గతి శక్తి. మరొక వైవిధ్యం "లీనియర్ ఫ్రిక్షన్ వెల్డింగ్", ఇక్కడ లీనియర్ రెసిప్రొకేటింగ్ మోషన్ చేరాల్సిన భాగాలలో కనీసం ఒకదానిపై విధించబడుతుంది. లీనియర్ రాపిడిలో వెల్డింగ్ భాగాలు వృత్తాకారంగా ఉండవలసిన అవసరం లేదు, అవి దీర్ఘచతురస్రాకారంగా, చతురస్రాకారంగా లేదా ఇతర ఆకారాన్ని కలిగి ఉంటాయి. పౌనఃపున్యాలు పదుల Hzలలో ఉండవచ్చు, మిల్లీమీటర్ల పరిధిలో వ్యాప్తి మరియు ఒత్తిడి పదుల లేదా వందల MPaలో ఉండవచ్చు. చివరగా "ఘర్షణ కదిలించు వెల్డింగ్" పైన వివరించిన ఇతర రెండింటి కంటే కొంత భిన్నంగా ఉంటుంది. జడత్వ రాపిడి వెల్డింగ్ మరియు లీనియర్ ఫ్రిక్షన్ వెల్డింగ్లో ఇంటర్ఫేస్ల తాపన రెండు సంపర్క ఉపరితలాలను రుద్దడం ద్వారా రాపిడి ద్వారా సాధించబడుతుంది, రాపిడి స్టిర్ వెల్డింగ్ పద్ధతిలో చేరాల్సిన రెండు ఉపరితలాలకు వ్యతిరేకంగా మూడవ శరీరాన్ని రుద్దుతారు. 5 నుండి 6 మిమీ వ్యాసం కలిగిన తిరిగే సాధనం ఉమ్మడితో సంబంధంలోకి తీసుకురాబడుతుంది. ఉష్ణోగ్రతలు 503 నుండి 533 కెల్విన్ మధ్య విలువలకు పెరుగుతాయి. ఉమ్మడిలో పదార్థం యొక్క తాపన, మిక్సింగ్ మరియు గందరగోళాన్ని జరుగుతుంది. మేము అల్యూమినియం, ప్లాస్టిక్లు మరియు మిశ్రమాలతో సహా పలు రకాల పదార్థాలపై ఘర్షణ స్టిర్ వెల్డింగ్ని ఉపయోగిస్తాము. వెల్డ్స్ ఏకరీతిగా ఉంటాయి మరియు కనీస రంధ్రాలతో నాణ్యత ఎక్కువగా ఉంటుంది. ఘర్షణ స్టైర్ వెల్డింగ్లో పొగలు లేదా చిందులు ఉత్పత్తి చేయబడవు మరియు ప్రక్రియ బాగా ఆటోమేటెడ్ అవుతుంది.
రెసిస్టెన్స్ వెల్డింగ్ (RW): వెల్డింగ్కు అవసరమైన వేడిని చేరాల్సిన రెండు వర్క్పీస్ల మధ్య విద్యుత్ నిరోధకత ద్వారా ఉత్పత్తి చేయబడుతుంది. రెసిస్టెన్స్ వెల్డింగ్లో ఫ్లక్స్, షీల్డింగ్ వాయువులు లేదా వినియోగించదగిన ఎలక్ట్రోడ్లు ఉపయోగించబడవు. జూల్ హీటింగ్ రెసిస్టెన్స్ వెల్డింగ్లో జరుగుతుంది మరియు ఇలా వ్యక్తీకరించవచ్చు:
H = (స్క్వేర్ I) x R xtx K
H అనేది జూల్స్లో ఉత్పత్తి చేయబడిన వేడి (వాట్-సెకన్లు), ఆంపియర్లలో I కరెంట్, ఓమ్స్లో R రెసిస్టెన్స్, t అనేది కరెంట్ ప్రవహించే సెకన్లలో సమయం. కారకం K 1 కంటే తక్కువ మరియు రేడియేషన్ మరియు ప్రసరణ ద్వారా కోల్పోని శక్తి యొక్క భిన్నాన్ని సూచిస్తుంది. రెసిస్టెన్స్ వెల్డింగ్ ప్రక్రియలలోని కరెంట్లు 100,000 A స్థాయికి చేరుకోగలవు, అయితే వోల్టేజీలు సాధారణంగా 0.5 నుండి 10 వోల్ట్లు ఉంటాయి. ఎలక్ట్రోడ్లు సాధారణంగా రాగి మిశ్రమాలతో తయారు చేయబడతాయి. రెసిస్టెన్స్ వెల్డింగ్ ద్వారా సారూప్య మరియు అసమాన పదార్థాలు రెండూ చేరవచ్చు. ఈ ప్రక్రియ కోసం అనేక వైవిధ్యాలు ఉన్నాయి: "రెసిస్టెన్స్ స్పాట్ వెల్డింగ్" అనేది రెండు షీట్ల ల్యాప్ జాయింట్ యొక్క ఉపరితలాలను సంప్రదించే రెండు వ్యతిరేక రౌండ్ ఎలక్ట్రోడ్లను కలిగి ఉంటుంది. కరెంట్ ఆపివేయబడే వరకు ఒత్తిడి వర్తించబడుతుంది. వెల్డ్ నగెట్ సాధారణంగా 10 మిమీ వరకు వ్యాసం కలిగి ఉంటుంది. రెసిస్టెన్స్ స్పాట్ వెల్డింగ్ వెల్డ్ స్పాట్స్ వద్ద కొద్దిగా రంగు మారిన ఇండెంటేషన్ మార్కులను వదిలివేస్తుంది. స్పాట్ వెల్డింగ్ అనేది మా అత్యంత ప్రజాదరణ పొందిన రెసిస్టెన్స్ వెల్డింగ్ టెక్నిక్. కష్టతరమైన ప్రాంతాలను చేరుకోవడానికి స్పాట్ వెల్డింగ్లో వివిధ ఎలక్ట్రోడ్ ఆకారాలు ఉపయోగించబడతాయి. మా స్పాట్ వెల్డింగ్ పరికరాలు CNC నియంత్రించబడతాయి మరియు ఏకకాలంలో ఉపయోగించగల బహుళ ఎలక్ట్రోడ్లను కలిగి ఉంటాయి. మరొక వైవిధ్యం "రెసిస్టెన్స్ సీమ్ వెల్డింగ్" అనేది వీల్ లేదా రోలర్ ఎలక్ట్రోడ్లతో నిర్వహించబడుతుంది, ఇది AC పవర్ సైకిల్లో కరెంట్ తగినంత అధిక స్థాయికి చేరుకున్నప్పుడు నిరంతర స్పాట్ వెల్డ్స్ను ఉత్పత్తి చేస్తుంది. రెసిస్టెన్స్ సీమ్ వెల్డింగ్ ద్వారా ఉత్పత్తి చేయబడిన కీళ్ళు ద్రవ మరియు వాయువు గట్టిగా ఉంటాయి. సన్నని షీట్లకు 1.5 m/min వెల్డింగ్ వేగం సాధారణం. ఒకరు అడపాదడపా ప్రవాహాలను వర్తింపజేయవచ్చు, తద్వారా స్పాట్ వెల్డ్స్ సీమ్ వెంట కావలసిన వ్యవధిలో ఉత్పత్తి చేయబడతాయి. "రెసిస్టెన్స్ ప్రొజెక్షన్ వెల్డింగ్"లో మేము వెల్డింగ్ చేయవలసిన వర్క్పీస్ ఉపరితలాలలో ఒకదానిపై ఒకటి లేదా అంతకంటే ఎక్కువ ప్రొజెక్షన్లను (డింపుల్స్) ఎంబోస్ చేస్తాము. ఈ అంచనాలు గుండ్రంగా లేదా ఓవల్గా ఉండవచ్చు. సంభోగం భాగంతో సంబంధంలోకి వచ్చే ఈ ఎంబోస్డ్ మచ్చల వద్ద అధిక స్థానికీకరించిన ఉష్ణోగ్రతలు చేరుకుంటాయి. ఈ అంచనాలను కుదించడానికి ఎలక్ట్రోడ్లు ఒత్తిడిని కలిగిస్తాయి. రెసిస్టెన్స్ ప్రొజెక్షన్ వెల్డింగ్లోని ఎలక్ట్రోడ్లు ఫ్లాట్ టిప్స్ను కలిగి ఉంటాయి మరియు నీరు చల్లబడిన రాగి మిశ్రమాలు. రెసిస్టెన్స్ ప్రొజెక్షన్ వెల్డింగ్ యొక్క ప్రయోజనం ఏమిటంటే, ఒక స్ట్రోక్లో అనేక వెల్డ్స్కు మన సామర్థ్యం, తద్వారా పొడిగించిన ఎలక్ట్రోడ్ జీవితం, వివిధ మందం కలిగిన షీట్లను వెల్డ్ చేసే సామర్థ్యం, షీట్లకు గింజలు మరియు బోల్ట్లను వెల్డ్ చేసే సామర్థ్యం. రెసిస్టెన్స్ ప్రొజెక్షన్ వెల్డింగ్ యొక్క ప్రతికూలత పల్లాలను ఎంబాసింగ్ చేయడానికి అదనపు ఖర్చు. ఇంకొక సాంకేతికత, "ఫ్లాష్ వెల్డింగ్"లో రెండు వర్క్పీస్ల చివర్లలోని ఆర్క్ నుండి అవి సంపర్కం చేయడం ప్రారంభించినప్పుడు వేడి ఉత్పత్తి అవుతుంది. ఈ పద్ధతి ప్రత్యామ్నాయంగా ఆర్క్ వెల్డింగ్గా కూడా పరిగణించబడుతుంది. ఇంటర్ఫేస్ వద్ద ఉష్ణోగ్రత పెరుగుతుంది మరియు పదార్థం మృదువుగా ఉంటుంది. ఒక అక్షసంబంధ శక్తి వర్తించబడుతుంది మరియు మెత్తబడిన ప్రాంతం వద్ద ఒక వెల్డ్ ఏర్పడుతుంది. ఫ్లాష్ వెల్డింగ్ పూర్తయిన తర్వాత, ఉమ్మడి మెరుగైన ప్రదర్శన కోసం యంత్రం చేయవచ్చు. ఫ్లాష్ వెల్డింగ్ ద్వారా పొందిన వెల్డ్ నాణ్యత మంచిది. శక్తి స్థాయిలు 10 నుండి 1500 kW వరకు ఉంటాయి. 75 మిమీ వ్యాసం వరకు సారూప్య లేదా అసమాన లోహాలు మరియు 0.2 మిమీ నుండి 25 మిమీ మందం మధ్య ఉన్న షీట్లను అంచు నుండి అంచు వరకు కలపడానికి ఫ్లాష్ వెల్డింగ్ అనుకూలంగా ఉంటుంది. "స్టడ్ ఆర్క్ వెల్డింగ్" అనేది ఫ్లాష్ వెల్డింగ్కు చాలా పోలి ఉంటుంది. బోల్ట్ లేదా థ్రెడ్ రాడ్ వంటి స్టడ్ ఒక ప్లేట్ వంటి వర్క్పీస్కి చేరినప్పుడు ఒక ఎలక్ట్రోడ్గా పనిచేస్తుంది. ఉత్పత్తి చేయబడిన వేడిని కేంద్రీకరించడానికి, ఆక్సీకరణను నిరోధించడానికి మరియు కరిగిన లోహాన్ని వెల్డ్ జోన్లో ఉంచడానికి, ఉమ్మడి చుట్టూ పునర్వినియోగపరచలేని సిరామిక్ రింగ్ ఉంచబడుతుంది. చివరగా "పెర్కషన్ వెల్డింగ్" మరొక రెసిస్టెన్స్ వెల్డింగ్ ప్రక్రియ, విద్యుత్ శక్తిని సరఫరా చేయడానికి కెపాసిటర్ను ఉపయోగిస్తుంది. పెర్కషన్ వెల్డింగ్లో శక్తి మిల్లీసెకన్ల వ్యవధిలో విడుదల చేయబడుతుంది, ఇది ఉమ్మడి వద్ద అధిక స్థానికీకరించిన వేడిని అభివృద్ధి చేస్తుంది. మేము ఎలక్ట్రానిక్స్ తయారీ పరిశ్రమలో పెర్కషన్ వెల్డింగ్ను విస్తృతంగా ఉపయోగిస్తాము, ఇక్కడ ఉమ్మడి సమీపంలోని సున్నితమైన ఎలక్ట్రానిక్ భాగాలను వేడి చేయడం నివారించాలి.
ఎక్స్ప్లోషన్ వెల్డింగ్ అని పిలువబడే ఒక సాంకేతికతలో పేలుడు పదార్ధం యొక్క పొరను పేల్చడం ఉంటుంది, అది చేరాల్సిన పని భాగాలలో ఒకదానిపై ఉంచబడుతుంది. వర్క్పీస్పై ఉన్న అధిక పీడనం అల్లకల్లోలమైన మరియు ఉంగరాల ఇంటర్ఫేస్ను ఉత్పత్తి చేస్తుంది మరియు మెకానికల్ ఇంటర్లాకింగ్ జరుగుతుంది. పేలుడు వెల్డింగ్లో బాండ్ బలాలు చాలా ఎక్కువగా ఉంటాయి. పేలుడు వెల్డింగ్ అనేది అసమాన లోహాలతో ప్లేట్ల క్లాడింగ్ కోసం మంచి పద్ధతి. క్లాడింగ్ తర్వాత, ప్లేట్లను సన్నగా విభజించవచ్చు. కొన్నిసార్లు మేము ట్యూబ్లను విస్తరించడానికి పేలుడు వెల్డింగ్ను ఉపయోగిస్తాము, తద్వారా అవి ప్లేట్కు వ్యతిరేకంగా గట్టిగా మూసివేయబడతాయి.
ఘన స్థితి చేరే డొమైన్లో మా చివరి పద్ధతి డిఫ్యూజన్ బాండింగ్ లేదా డిఫ్యూజన్ వెల్డింగ్ (DFW), దీనిలో ప్రధానంగా ఇంటర్ఫేస్ అంతటా అణువుల వ్యాప్తి ద్వారా మంచి ఉమ్మడి సాధించబడుతుంది. ఇంటర్ఫేస్ వద్ద కొన్ని ప్లాస్టిక్ వైకల్యం కూడా వెల్డింగ్కు దోహదం చేస్తుంది. ఉష్ణోగ్రతలు సుమారు 0.5 Tm ఉంటుంది, ఇక్కడ Tm లోహం యొక్క కరిగే ఉష్ణోగ్రత ఉంటుంది. డిఫ్యూజన్ వెల్డింగ్లో బాండ్ బలం ఒత్తిడి, ఉష్ణోగ్రత, సంప్రదింపు సమయం మరియు సంప్రదింపు ఉపరితలాల శుభ్రతపై ఆధారపడి ఉంటుంది. కొన్నిసార్లు మేము ఇంటర్ఫేస్లో పూరక లోహాలను ఉపయోగిస్తాము. వ్యాప్తి బంధంలో వేడి మరియు పీడనం అవసరం మరియు విద్యుత్ నిరోధకత లేదా ఫర్నేస్ మరియు చనిపోయిన బరువులు, ప్రెస్ లేదా ఇతర వాటి ద్వారా సరఫరా చేయబడతాయి. సారూప్య మరియు అసమాన లోహాలు వ్యాప్తి వెల్డింగ్తో చేరవచ్చు. పరమాణువులు మారడానికి పట్టే సమయం కారణంగా ప్రక్రియ చాలా నెమ్మదిగా ఉంటుంది. DFW స్వయంచాలకంగా ఉంటుంది మరియు ఏరోస్పేస్, ఎలక్ట్రానిక్స్, వైద్య పరిశ్రమల కోసం సంక్లిష్ట భాగాల తయారీలో విస్తృతంగా ఉపయోగించబడుతుంది. తయారు చేయబడిన ఉత్పత్తులలో ఆర్థోపెడిక్ ఇంప్లాంట్లు, సెన్సార్లు, ఏరోస్పేస్ స్ట్రక్చరల్ సభ్యులు ఉన్నాయి. సంక్లిష్ట షీట్ మెటల్ నిర్మాణాలను రూపొందించడానికి డిఫ్యూజన్ బాండింగ్ను సూపర్ప్లాస్టిక్ ఫార్మింగ్తో కలపవచ్చు. షీట్లపై ఎంచుకున్న స్థానాలు మొదట వ్యాప్తి బంధంతో ఉంటాయి, ఆపై అన్బాండెడ్ ప్రాంతాలు వాయు పీడనాన్ని ఉపయోగించి అచ్చుగా విస్తరించబడతాయి. అధిక దృఢత్వం నుండి బరువు నిష్పత్తులతో ఏరోస్పేస్ నిర్మాణాలు ఈ పద్ధతుల కలయికను ఉపయోగించి తయారు చేయబడతాయి. డిఫ్యూజన్ వెల్డింగ్ / సూపర్ప్లాస్టిక్ ఫార్మింగ్ కంబైన్డ్ ప్రాసెస్ ఫాస్టెనర్ల అవసరాన్ని తొలగించడం ద్వారా అవసరమైన భాగాల సంఖ్యను తగ్గిస్తుంది, ఫలితంగా తక్కువ-ఒత్తిడి అత్యంత ఖచ్చితమైన భాగాలు ఆర్థికంగా మరియు తక్కువ లీడ్ టైమ్లతో ఉంటాయి.
బ్రేజింగ్: బ్రేజింగ్ మరియు టంకం సాంకేతికతలు వెల్డింగ్ కోసం అవసరమైన వాటి కంటే తక్కువ ఉష్ణోగ్రతలను కలిగి ఉంటాయి. బ్రేజింగ్ ఉష్ణోగ్రతలు టంకం ఉష్ణోగ్రతల కంటే ఎక్కువగా ఉంటాయి. బ్రేజింగ్లో చేరాల్సిన ఉపరితలాల మధ్య పూరక లోహం ఉంచబడుతుంది మరియు ఉష్ణోగ్రతలు పూరక పదార్థం యొక్క ద్రవీభవన ఉష్ణోగ్రతకు 723 కెల్విన్ కంటే ఎక్కువగా ఉంటాయి కానీ వర్క్పీస్ల ద్రవీభవన ఉష్ణోగ్రతల కంటే తక్కువగా ఉంటాయి. కరిగిన లోహం వర్క్పీస్ల మధ్య దగ్గరగా ఉండే స్థలాన్ని నింపుతుంది. ఫైలర్ మెటల్ యొక్క శీతలీకరణ మరియు తదుపరి పటిష్టత వలన బలమైన కీళ్ళు ఏర్పడతాయి. బ్రేజ్ వెల్డింగ్లో పూరక లోహం జాయింట్లో జమ చేయబడుతుంది. బ్రేజింగ్తో పోలిస్తే బ్రేజ్ వెల్డింగ్లో చాలా ఎక్కువ ఫిల్లర్ మెటల్ ఉపయోగించబడుతుంది. ఆక్సిడైజింగ్ ఫ్లేమ్తో కూడిన ఆక్సియాసిటిలిన్ టార్చ్ బ్రేజ్ వెల్డింగ్లో ఫిల్లర్ మెటల్ను డిపాజిట్ చేయడానికి ఉపయోగించబడుతుంది. బ్రేజింగ్లో తక్కువ ఉష్ణోగ్రతల కారణంగా, వార్పింగ్ మరియు అవశేష ఒత్తిళ్లు వంటి వేడి ప్రభావిత ప్రాంతాలలో సమస్యలు తక్కువగా ఉంటాయి. బ్రేజింగ్లో చిన్న క్లియరెన్స్ గ్యాప్ ఉమ్మడి యొక్క కోత బలం ఎక్కువగా ఉంటుంది. అయితే గరిష్ట తన్యత బలం ఒక వాంఛనీయ గ్యాప్ (ఒక గరిష్ట విలువ) వద్ద సాధించబడుతుంది. ఈ వాంఛనీయ విలువ క్రింద మరియు పైన, బ్రేజింగ్లో తన్యత బలం తగ్గుతుంది. బ్రేజింగ్లో సాధారణ క్లియరెన్స్లు 0.025 మరియు 0.2 మిమీ మధ్య ఉండవచ్చు. మేము పెర్ఫార్మ్లు, పౌడర్, రింగ్లు, వైర్, స్ట్రిప్....మొదలైన విభిన్న ఆకృతులతో విభిన్నమైన బ్రేజింగ్ మెటీరియల్లను ఉపయోగిస్తాము. మరియు వీటిని మీ డిజైన్ లేదా ఉత్పత్తి జ్యామితి కోసం ప్రత్యేకంగా తయారు చేయవచ్చు. మేము మీ బేస్ మెటీరియల్స్ మరియు అప్లికేషన్ ప్రకారం బ్రేజింగ్ మెటీరియల్ల కంటెంట్ను కూడా నిర్ణయిస్తాము. అవాంఛిత ఆక్సైడ్ పొరలను తొలగించడానికి మరియు ఆక్సీకరణను నిరోధించడానికి బ్రేజింగ్ ఆపరేషన్లలో మేము తరచుగా ఫ్లక్స్లను ఉపయోగిస్తాము. తదుపరి తుప్పును నివారించడానికి, చేరిన ఆపరేషన్ తర్వాత ఫ్లక్స్ సాధారణంగా తొలగించబడతాయి. AGS-TECH Inc. వివిధ బ్రేజింగ్ పద్ధతులను ఉపయోగిస్తుంది, వీటిలో:
- టార్చ్ బ్రేజింగ్
- ఫర్నేస్ బ్రేజింగ్
- ఇండక్షన్ బ్రేజింగ్
- రెసిస్టెన్స్ బ్రేజింగ్
- డిప్ బ్రేజింగ్
- ఇన్ఫ్రారెడ్ బ్రేజింగ్
- డిఫ్యూజన్ బ్రేజింగ్
- అధిక శక్తి పుంజం
కార్బైడ్ డ్రిల్ బిట్స్, ఇన్సర్ట్లు, ఆప్టోఎలక్ట్రానిక్ హెర్మెటిక్ ప్యాకేజీలు, సీల్స్ వంటి మంచి బలంతో అసమానమైన లోహాలతో తయారు చేయబడిన బ్రేజ్డ్ జాయింట్ల యొక్క మా అత్యంత సాధారణ ఉదాహరణలు.
టంకం: ఇది చాలా తరచుగా ఉపయోగించే పద్ధతుల్లో ఒకటి, ఇక్కడ టంకము (ఫిల్లర్ మెటల్) దగ్గరగా ఉండే భాగాల మధ్య బ్రేజింగ్లో జాయింట్ను నింపుతుంది. మా సోల్డర్లు 723 కెల్విన్ కంటే తక్కువ మెల్టింగ్ పాయింట్లను కలిగి ఉన్నాయి. మేము తయారీ కార్యకలాపాలలో మాన్యువల్ మరియు ఆటోమేటెడ్ టంకం రెండింటినీ అమలు చేస్తాము. బ్రేజింగ్తో పోలిస్తే, టంకం ఉష్ణోగ్రతలు తక్కువగా ఉంటాయి. అధిక-ఉష్ణోగ్రత లేదా అధిక-శక్తి అనువర్తనాలకు టంకం చాలా సరిఅయినది కాదు. మేము సీసం-రహిత టంకములతో పాటు టిన్-లీడ్, టిన్-జింక్, లెడ్-సిల్వర్, కాడ్మియం-సిల్వర్, జింక్-అల్యూమినియం మిశ్రమాలను టంకం కోసం ఉపయోగిస్తాము. నాన్కార్రోసివ్ రెసిన్-ఆధారిత అలాగే అకర్బన ఆమ్లాలు మరియు లవణాలు రెండూ టంకంలో ఫ్లక్స్గా ఉపయోగించబడతాయి. మేము తక్కువ టంకముతో లోహాలను టంకము చేయడానికి ప్రత్యేక ఫ్లక్స్లను ఉపయోగిస్తాము. సిరామిక్ మెటీరియల్స్, గ్లాస్ లేదా గ్రాఫైట్ టంకము చేయాల్సిన అప్లికేషన్లలో, ముందుగా టంకం పెరగడానికి తగిన లోహంతో భాగాలను ప్లేట్ చేస్తాము. మా ప్రసిద్ధ టంకం పద్ధతులు:
-రిఫ్లో లేదా అతికించండి టంకం
-వేవ్ టంకం
-ఫర్నేస్ టంకం
- టార్చ్ టంకం
-ఇండక్షన్ టంకం
-ఐరన్ టంకం
-రెసిస్టెన్స్ టంకం
-డిప్ టంకం
-అల్ట్రాసోనిక్ టంకం
-ఇన్ఫ్రారెడ్ టంకం
అల్ట్రాసోనిక్ టంకం మాకు ఒక ప్రత్యేక ప్రయోజనాన్ని అందిస్తుంది, దీని ద్వారా అల్ట్రాసోనిక్ పుచ్చు ప్రభావం కారణంగా ఫ్లక్స్ల అవసరం తొలగించబడుతుంది, ఇది చేరిన ఉపరితలాల నుండి ఆక్సైడ్ ఫిల్మ్లను తొలగిస్తుంది. రిఫ్లో మరియు వేవ్ టంకం అనేది ఎలక్ట్రానిక్స్లో అధిక వాల్యూమ్ తయారీకి మా పారిశ్రామికంగా అత్యుత్తమ సాంకేతికతలు మరియు అందువల్ల మరింత వివరంగా వివరించడం విలువ. రిఫ్లో టంకంలో, మేము టంకము-లోహ కణాలను కలిగి ఉన్న సెమిసోలిడ్ పేస్ట్లను ఉపయోగిస్తాము. స్క్రీనింగ్ లేదా స్టెన్సిలింగ్ ప్రక్రియను ఉపయోగించి పేస్ట్ జాయింట్పై ఉంచబడుతుంది. ప్రింటెడ్ సర్క్యూట్ బోర్డ్లలో (PCB) మేము ఈ పద్ధతిని తరచుగా ఉపయోగిస్తాము. పేస్ట్ నుండి ఈ ప్యాడ్లపై ఎలక్ట్రికల్ భాగాలను ఉంచినప్పుడు, ఉపరితల ఉద్రిక్తత ఉపరితల-మౌంట్ ప్యాకేజీలను సమలేఖనం చేస్తుంది. భాగాలను ఉంచిన తర్వాత, మేము అసెంబ్లీని కొలిమిలో వేడి చేస్తాము, తద్వారా రిఫ్లో టంకం జరుగుతుంది. ఈ ప్రక్రియలో, పేస్ట్లోని ద్రావకాలు ఆవిరైపోతాయి, పేస్ట్లోని ఫ్లక్స్ సక్రియం చేయబడుతుంది, భాగాలు ముందుగా వేడి చేయబడతాయి, టంకము కణాలు కరిగించి జాయింట్ను తడి చేస్తాయి మరియు చివరకు PCB అసెంబ్లీ నెమ్మదిగా చల్లబడుతుంది. PCB బోర్డ్ల యొక్క అధిక వాల్యూమ్ ఉత్పత్తికి మా రెండవ ప్రసిద్ధ సాంకేతికత, అంటే వేవ్ టంకం అనేది కరిగిన టంకములను తడి మెటల్ ఉపరితలాలను మరియు మెటల్ను వేడిచేసినప్పుడు మాత్రమే మంచి బంధాలను ఏర్పరుస్తుంది. కరిగిన టంకము యొక్క స్టాండింగ్ లామినార్ వేవ్ మొదట పంపు ద్వారా ఉత్పత్తి చేయబడుతుంది మరియు ముందుగా వేడిచేసిన మరియు ప్రీఫ్లక్స్ చేయబడిన PCBలు తరంగంపైకి పంపబడతాయి. టంకము బహిర్గతమైన మెటల్ ఉపరితలాలను మాత్రమే తడి చేస్తుంది కానీ IC పాలిమర్ ప్యాకేజీలను లేదా పాలిమర్-కోటెడ్ సర్క్యూట్ బోర్డ్లను తడి చేయదు. వేడి నీటి జెట్ యొక్క అధిక-వేగం జాయింట్ నుండి అదనపు టంకమును దెబ్బతీస్తుంది మరియు ప్రక్కనే ఉన్న లీడ్స్ మధ్య వంతెనను నిరోధిస్తుంది. ఉపరితల-మౌంట్ ప్యాకేజీల వేవ్ టంకంలో మేము మొదట వాటిని టంకం చేయడానికి ముందు సర్క్యూట్ బోర్డ్కు అంటుకునేలా చేస్తాము. మళ్లీ స్క్రీనింగ్ మరియు స్టెన్సిలింగ్ ఉపయోగించబడుతుంది కానీ ఈసారి ఎపోక్సీ కోసం. భాగాలు వాటి సరైన స్థానాల్లో ఉంచబడిన తర్వాత, ఎపోక్సీ నయమవుతుంది, బోర్డులు విలోమం చేయబడతాయి మరియు వేవ్ టంకం జరుగుతుంది.