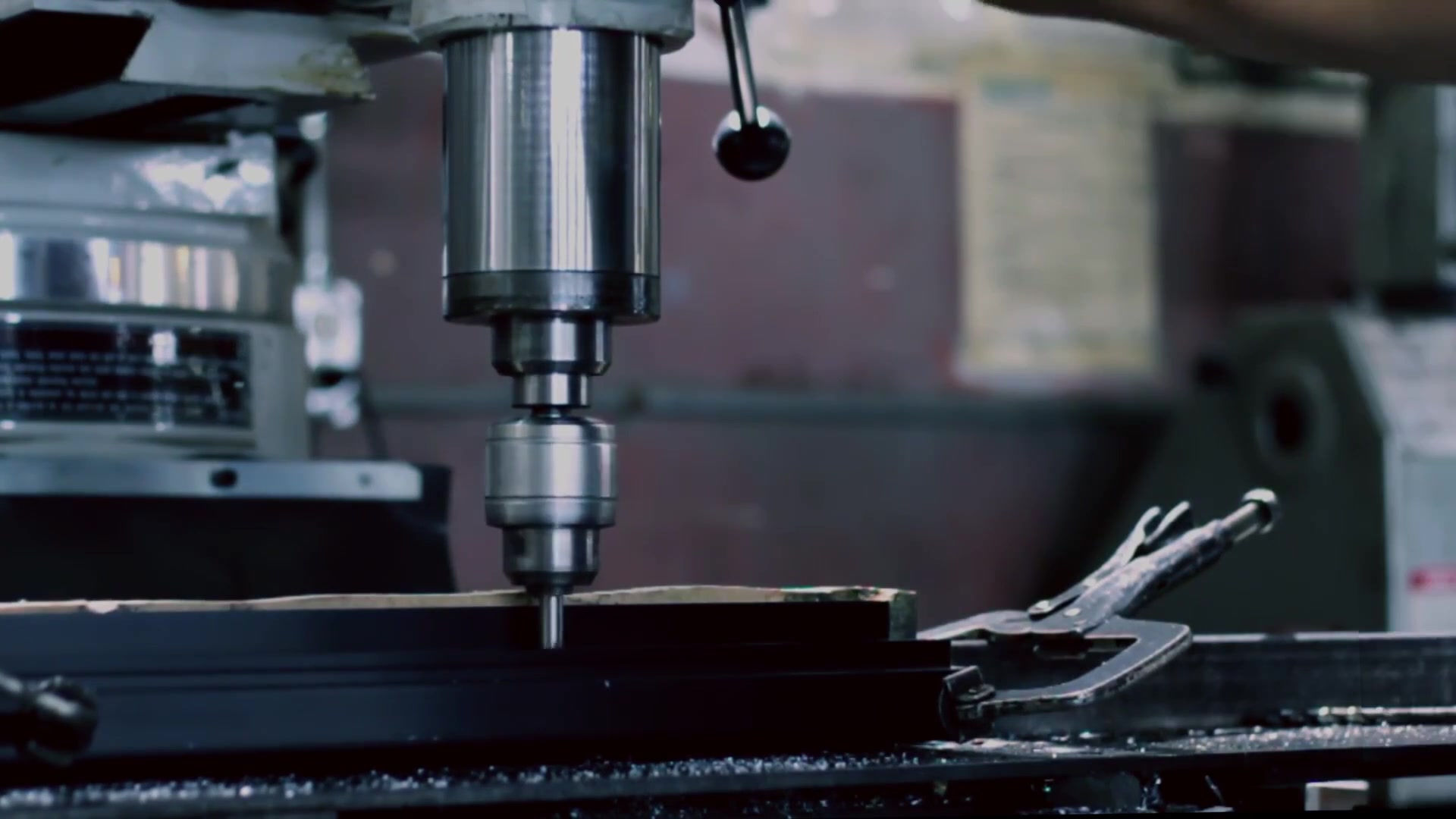
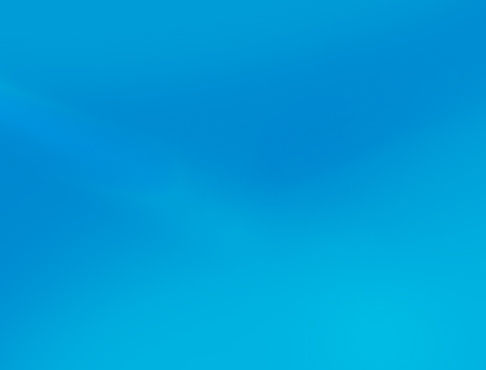
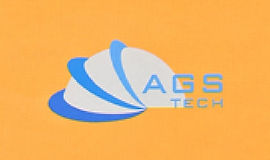
గ్లోబల్ కస్టమ్ మ్యానుఫ్యాక్చరర్, ఇంటిగ్రేటర్, కన్సాలిడేటర్, అనేక రకాల ఉత్పత్తులు & సేవల కోసం అవుట్సోర్సింగ్ భాగస్వామి.
కస్టమ్ తయారీ మరియు ఆఫ్-షెల్ఫ్ ఉత్పత్తులు & సేవల తయారీ, కల్పన, ఇంజనీరింగ్, కన్సాలిడేషన్, ఇంటిగ్రేషన్, అవుట్సోర్సింగ్ కోసం మేము మీ వన్-స్టాప్ మూలం.
మీ భాషను ఎంచుకోండి
-
కస్టమ్ తయారీ
-
దేశీయ & గ్లోబల్ కాంట్రాక్ట్ తయారీ
-
తయారీ అవుట్సోర్సింగ్
-
దేశీయ & ప్రపంచ సేకరణ
-
కన్సాలిడేషన్
-
ఇంజనీరింగ్ ఇంటిగ్రేషన్
-
ఇంజనీరింగ్ సేవలు
మేము అందించే మెటల్ ఫోర్జింగ్ ప్రక్రియల రకాలు హాట్ అండ్ కోల్డ్ డై, ఓపెన్ డై మరియు క్లోజ్డ్ డై, ఇంప్రెషన్ డై & ఫ్లాష్లెస్ ఫోర్జింగ్లు, cogging, ఫుల్లరింగ్, ఎడ్జింగ్ మరియు ప్రెసిషన్ ఫోర్జింగ్, హెడ్-నియర్-షేప్ , స్వేజింగ్, అప్సెట్ ఫోర్జింగ్, మెటల్ హాబింగ్, ప్రెస్ & రోల్ & రేడియల్ & ఆర్బిటల్ & రింగ్ & ఐసోథర్మల్ ఫోర్జింగ్లు, కాయినింగ్, రివెటింగ్, మెటల్ బాల్ ఫోర్జింగ్, మెటల్ పియర్సింగ్, సైజింగ్, హై ఎనర్జీ రేట్ ఫోర్జింగ్.
మా పౌడర్ మెటలర్జీ మరియు పౌడర్ ప్రాసెసింగ్ టెక్నిక్లు పౌడర్ ప్రెస్సింగ్ మరియు సింటరింగ్, ఇంప్రెగ్నేషన్, ఇన్ఫిల్ట్రేషన్, హాట్ అండ్ కోల్డ్ ఐసోస్టాటిక్ ప్రెస్సింగ్, మెటల్ ఇంజెక్షన్ మోల్డింగ్, రోల్ కాంపాక్షన్, పౌడర్ రోలింగ్, పౌడర్ ఎక్స్ట్రాషన్, లూస్ సింటరింగ్, స్పార్క్ సింటరింగ్, హాట్ ప్రెస్సింగ్.
మీరు ఇక్కడ క్లిక్ చేయాలని మేము సిఫార్సు చేస్తున్నాము
AGS-TECH Inc. ద్వారా ఫోర్జింగ్ ప్రక్రియల మా స్కీమాటిక్ ఇలస్ట్రేషన్లను డౌన్లోడ్ చేయండి
AGS-TECH Inc. ద్వారా పౌడర్ మెటలర్జీ ప్రక్రియల మా స్కీమాటిక్ ఇలస్ట్రేషన్లను డౌన్లోడ్ చేయండి
ఫోటోలు మరియు స్కెచ్లతో కూడిన ఈ డౌన్లోడ్ చేయదగిన ఫైల్లు మేము దిగువ మీకు అందిస్తున్న సమాచారాన్ని బాగా అర్థం చేసుకోవడంలో మీకు సహాయపడతాయి.
మెటల్ ఫోర్జింగ్లో, సంపీడన శక్తులు వర్తించబడతాయి మరియు పదార్థం వైకల్యంతో మరియు కావలసిన ఆకృతిని పొందుతుంది. పరిశ్రమలో అత్యంత సాధారణ నకిలీ పదార్థాలు ఇనుము మరియు ఉక్కు, అయితే అల్యూమినియం, రాగి, టైటానియం, మెగ్నీషియం వంటి అనేక ఇతర పదార్థాలు కూడా విస్తృతంగా నకిలీ చేయబడ్డాయి. నకిలీ మెటల్ భాగాలు మూసివున్న పగుళ్లు మరియు మూసివేసిన ఖాళీ స్థలాలకు అదనంగా ధాన్యం నిర్మాణాలను మెరుగుపరిచాయి, అందువలన ఈ ప్రక్రియ ద్వారా పొందిన భాగాల బలం ఎక్కువగా ఉంటుంది. ఫోర్జింగ్ అనేది కాస్టింగ్ లేదా మ్యాచింగ్ ద్వారా తయారు చేయబడిన భాగాల కంటే వాటి బరువు కోసం గణనీయంగా బలమైన భాగాలను ఉత్పత్తి చేస్తుంది. లోహాన్ని దాని తుది ఆకృతిలోకి ప్రవహించేలా చేయడం ద్వారా నకిలీ భాగాలు ఆకృతి చేయబడినందున, లోహం ఒక దిశాత్మక ధాన్యం నిర్మాణాన్ని తీసుకుంటుంది, ఇది భాగాల యొక్క ఉన్నతమైన బలానికి కారణమవుతుంది. మరో మాటలో చెప్పాలంటే, సాధారణ తారాగణం లేదా యంత్ర భాగాలతో పోలిస్తే ఫోర్జింగ్ ప్రక్రియ ద్వారా పొందిన భాగాలు మెరుగైన యాంత్రిక లక్షణాలను వెల్లడిస్తాయి. మెటల్ ఫోర్జింగ్ల బరువు చిన్న తేలికపాటి భాగాల నుండి వందల వేల పౌండ్ల వరకు ఉంటుంది. ఆటోమోటివ్ పార్ట్స్, గేర్లు, వర్క్ టూల్స్, హ్యాండ్ టూల్స్, టర్బైన్ షాఫ్ట్లు, మోటార్సైకిల్ గేర్ వంటి భాగాలపై అధిక ఒత్తిళ్లు వర్తించే యాంత్రికంగా డిమాండ్ ఉన్న అప్లికేషన్ల కోసం మేము ఎక్కువగా ఫోర్జింగ్లను తయారు చేస్తాము. టూలింగ్ మరియు సెటప్ ఖర్చులు సాపేక్షంగా ఎక్కువగా ఉన్నందున, మేము ఈ తయారీ ప్రక్రియను అధిక వాల్యూమ్ ఉత్పత్తికి మరియు తక్కువ వాల్యూమ్ కోసం మాత్రమే సిఫార్సు చేస్తున్నాము, అయితే ఏరోస్పేస్ ల్యాండింగ్ గేర్ వంటి అధిక విలువ కలిగిన కీలకమైన భాగాలు. టూలింగ్ ఖర్చుతో పాటు, కొన్ని సాధారణ యంత్ర భాగాలతో పోల్చితే పెద్ద పరిమాణంలో నకిలీ భాగాల తయారీ లీడ్ టైమ్లు ఎక్కువగా ఉంటాయి, అయితే టెక్నిక్ అనేది పార్ట్లకు చాలా కీలకం, ఇది అద్వితీయమైన బలం, ప్రత్యేకత, అప్లికేషన్లు, అప్లికేషన్లు ఫాస్టెనర్లు, ఆటోమోటివ్, ఫోర్క్లిఫ్ట్, క్రేన్ భాగాలు.
• హాట్ డై మరియు కోల్డ్ డై ఫోర్జింగ్ : హాట్ డై ఫోర్జింగ్, పేరు సూచించినట్లుగా, అధిక ఉష్ణోగ్రతల వద్ద నిర్వహించబడుతుంది, డక్టిలిటీ ఎక్కువగా ఉంటుంది మరియు పదార్థం యొక్క బలం తక్కువగా ఉంటుంది. ఇది సులభంగా వైకల్యం మరియు ఫోర్జింగ్ను సులభతరం చేస్తుంది. దీనికి విరుద్ధంగా, కోల్డ్ డై ఫోర్జింగ్ తక్కువ ఉష్ణోగ్రతల వద్ద నిర్వహించబడుతుంది మరియు అధిక బలాలు అవసరమవుతాయి, దీని ఫలితంగా స్ట్రెయిన్ గట్టిపడటం, మెరుగైన ఉపరితల ముగింపు మరియు తయారు చేయబడిన భాగాల యొక్క ఖచ్చితత్వం.
• ఓపెన్ డై మరియు ఇంప్రెషన్ డై ఫోర్జింగ్ : ఓపెన్ డై ఫోర్జింగ్లో, డైస్ కంప్రెస్ చేయబడిన మెటీరియల్ను నిరోధించదు, అయితే ఇంప్రెషన్లో డైస్లోని కావిటీస్ను ఫోర్జింగ్ చేయడం వల్ల అది కావలసిన ఆకృతిలో నకిలీ చేయబడినప్పుడు మెటీరియల్ ప్రవాహాన్ని నిరోధిస్తుంది. అప్సెట్ ఫోర్జింగ్ లేదా అప్సెట్టింగ్ అని కూడా పిలుస్తారు, ఇది వాస్తవానికి అదే కాదు కానీ చాలా సారూప్య ప్రక్రియ, అనేది ఓపెన్ డై ప్రక్రియ, ఇక్కడ వర్క్ పీస్ రెండు ఫ్లాట్ డైల మధ్య శాండ్విచ్ చేయబడుతుంది మరియు సంపీడన శక్తి దాని ఎత్తును తగ్గిస్తుంది. ఎత్తు reduced అయినందున, పని ముక్క వెడల్పు పెరుగుతుంది. హెడ్డింగ్, అప్సెట్ ఫోర్జింగ్ ప్రాసెస్లో స్థూపాకార స్టాక్ ఉంటుంది, అది దాని చివరలో కలత చెందుతుంది మరియు దాని క్రాస్ సెక్షన్ స్థానికంగా పెరుగుతుంది. హెడ్డింగ్లో స్టాక్ డై ద్వారా ఫీడ్ చేయబడి, నకిలీ చేసి, ఆపై పొడవుకు కత్తిరించబడుతుంది. ఆపరేషన్ అధిక మొత్తంలో ఫాస్టెనర్లను వేగంగా ఉత్పత్తి చేయగలదు. ఎక్కువగా ఇది ఒక చల్లని పని ఆపరేషన్, ఎందుకంటే ఇది గోరు చివరలను, స్క్రూ చివరలను, గింజలు మరియు బోల్ట్లను తయారు చేయడానికి ఉపయోగిస్తారు, ఇక్కడ పదార్థాన్ని బలోపేతం చేయాలి. మరొక ఓపెన్ డై ప్రక్రియ COGGING, ఇక్కడ వర్క్ పీస్ ప్రతి దశతో వరుస దశల్లో నకిలీ చేయబడుతుంది, దీని ఫలితంగా పదార్థం యొక్క కుదింపు మరియు వర్క్ పీస్ పొడవునా ఓపెన్ డై యొక్క తదుపరి కదలిక ఏర్పడుతుంది. ప్రతి దశలో, మందం తగ్గుతుంది మరియు పొడవు కొద్దిగా పెరుగుతుంది. ఈ ప్రక్రియ ఒక నాడీ విద్యార్థి తన పెన్సిల్ను చిన్న చిన్న దశల్లో కొరికినట్లుగా ఉంటుంది. FULLERING అని పిలవబడే ప్రక్రియ మరొక ఓపెన్ డై ఫోర్జింగ్ పద్ధతి, ఇతర మెటల్ ఫోర్జింగ్ కార్యకలాపాలు జరగడానికి ముందు వర్క్పీస్లోని మెటీరియల్ని పంపిణీ చేయడానికి మేము తరచుగా ప్రారంభ దశగా ఉపయోగిస్తాము. వర్క్ పీస్కి అనేక forging operations అవసరమైనప్పుడు మేము దానిని ఉపయోగిస్తాము. ఆపరేషన్లో, కుంభాకార ఉపరితలాలు వైకల్యంతో మరణిస్తాయి మరియు రెండు వైపులా లోహ ప్రవాహాన్ని కలిగిస్తాయి. ఫుల్లరింగ్కు సమానమైన ప్రక్రియ, మరోవైపు EDGING అనేది వర్క్పీస్ను వికృతీకరించడానికి పుటాకార ఉపరితలాలతో ఓపెన్ డైని కలిగి ఉంటుంది. అంచులు వేయడం అనేది తదుపరి ఫోర్జింగ్ ఆపరేషన్ల కోసం ఒక సన్నాహక ప్రక్రియ, పదార్థం రెండు వైపుల నుండి మధ్యలో ఉన్న ప్రాంతంలోకి ప్రవహిస్తుంది. ఇంప్రెషన్ డై ఫోర్జింగ్ లేదా క్లోజ్డ్ డై ఫోర్జింగ్ అని కూడా పిలుస్తారు, ఇది డై / అచ్చును ఉపయోగిస్తుంది, అది మెటీరియల్ను కుదిస్తుంది మరియు దాని ప్రవాహాన్ని దానిలోనే పరిమితం చేస్తుంది. డై మూసివేయబడుతుంది మరియు పదార్థం డై / అచ్చు కుహరం ఆకారాన్ని తీసుకుంటుంది. PRECISION FORGING, ప్రత్యేక పరికరాలు మరియు అచ్చు అవసరమయ్యే ప్రక్రియ, ఫ్లాష్ లేని లేదా చాలా తక్కువ భాగాలను ఉత్పత్తి చేస్తుంది. మరో మాటలో చెప్పాలంటే, భాగాలు చివరి కొలతలు కలిగి ఉంటాయి. ఈ ప్రక్రియలో బాగా నియంత్రిత మొత్తం పదార్థం జాగ్రత్తగా చొప్పించబడుతుంది మరియు అచ్చు లోపల ఉంచబడుతుంది. మేము ఈ పద్ధతిని సన్నని విభాగాలు, చిన్న టాలరెన్స్లు మరియు డ్రాఫ్ట్ యాంగిల్స్తో సంక్లిష్ట ఆకృతుల కోసం మరియు అచ్చు మరియు పరికరాల ఖర్చులను సమర్థించేంత పెద్ద పరిమాణంలో ఉన్నప్పుడు అమలు చేస్తాము.
• ఫ్లాష్లెస్ ఫోర్జింగ్: వర్క్పీస్ డైలో ఉంచబడుతుంది, తద్వారా కుహరం నుండి ఫ్లాష్ని ఏర్పరచడానికి ఏ పదార్థం బయటకు ప్రవహించదు. కాబట్టి అవాంఛనీయ ఫ్లాష్ ట్రిమ్మింగ్ అవసరం లేదు. ఇది ఖచ్చితత్వంతో కూడిన నకిలీ ప్రక్రియ మరియు అందుచేత ఉపయోగించిన మెటీరియల్ మొత్తంపై నిశిత నియంత్రణ అవసరం.
• మెటల్ స్వేజింగ్ లేదా రేడియల్ ఫోర్జింగ్ : ఒక వర్క్ పీస్ చుట్టుకొలతతో డై మరియు ఫోర్జ్ చేయడం ద్వారా పని చేస్తుంది. ఇంటీరియర్ వర్క్ పీస్ జ్యామితిని నకిలీ చేయడానికి మాండ్రెల్ కూడా ఉపయోగించవచ్చు. స్వేజింగ్ ఆపరేషన్లో పని భాగం సాధారణంగా సెకనుకు అనేక స్ట్రోక్లను అందుకుంటుంది. స్వేజింగ్ ద్వారా ఉత్పత్తి చేయబడిన సాధారణ వస్తువులు పాయింటెడ్ టిప్ టూల్స్, టేపర్డ్ బార్లు, స్క్రూడ్రైవర్లు.
• మెటల్ పియర్సింగ్: మేము ఈ ఆపరేషన్ను విడిభాగాల తయారీలో అదనపు ఆపరేషన్గా తరచుగా ఉపయోగిస్తాము. ఒక రంధ్రం లేదా కుహరం ద్వారా బద్దలు లేకుండా పని ముక్క ఉపరితలంపై కుట్లు సృష్టించబడుతుంది. రంధ్రం ద్వారా రంధ్రం చేసే డ్రిల్లింగ్ కంటే పియర్సింగ్ భిన్నంగా ఉంటుందని దయచేసి గమనించండి.
• హాబింగ్ : కావలసిన జ్యామితితో ఒక పంచ్ వర్క్ పీస్లో నొక్కబడుతుంది మరియు కావలసిన ఆకారంతో ఒక కుహరాన్ని సృష్టిస్తుంది. మేము ఈ పంచ్ను HOB అని పిలుస్తాము. ఆపరేషన్ అధిక ఒత్తిళ్లను కలిగి ఉంటుంది మరియు చల్లని వద్ద నిర్వహించబడుతుంది. ఫలితంగా, పదార్థం చల్లగా పని చేస్తుంది మరియు గట్టిపడుతుంది. అందువల్ల ఈ ప్రక్రియ ఇతర తయారీ ప్రక్రియలకు అచ్చులు, డై మరియు కావిటీస్ తయారీకి చాలా అనుకూలంగా ఉంటుంది. హాబ్ను తయారు చేసిన తర్వాత, వాటిని ఒక్కొక్కటిగా మెషిన్ చేయాల్సిన అవసరం లేకుండానే అనేక సారూప్య కావిటీలను సులభంగా తయారు చేయవచ్చు.
• రోల్ ఫోర్జింగ్ లేదా రోల్ ఫార్మింగ్ : మెటల్ భాగాన్ని ఆకృతి చేయడానికి రెండు వ్యతిరేక రోల్స్ ఉపయోగించబడతాయి. వర్క్ పీస్ రోల్స్లోకి మృదువుగా ఉంటుంది, రోల్స్ మలుపు తిరుగుతాయి మరియు పనిని గ్యాప్లోకి లాగుతాయి, ఆ పనిని రోల్స్ యొక్క గాడి భాగం ద్వారా అందించబడుతుంది మరియు సంపీడన శక్తులు పదార్థానికి కావలసిన ఆకారాన్ని ఇస్తాయి. ఇది రోలింగ్ ప్రక్రియ కాదు, నకిలీ ప్రక్రియ, ఎందుకంటే ఇది నిరంతర ఆపరేషన్ కంటే వివిక్తమైనది. రోల్స్ గ్రోవ్స్లోని జ్యామితి అవసరమైన ఆకారం మరియు జ్యామితికి పదార్థాన్ని నకిలీ చేస్తుంది. ఇది వేడిగా నిర్వహించబడుతుంది. నకిలీ ప్రక్రియ అయినందున ఇది అత్యుత్తమ యాంత్రిక లక్షణాలతో భాగాలను ఉత్పత్తి చేస్తుంది మరియు అందువల్ల మేము దీనిని manufacturing ఆటోమోటివ్ భాగాలైన షాఫ్ట్ల వంటి కఠినమైన పని వాతావరణంలో అసాధారణమైన ఓర్పును కలిగి ఉండటానికి ఉపయోగిస్తాము.
• ఆర్బిటల్ ఫోర్జింగ్: వర్క్ పీస్ ఒక ఫోర్జింగ్ డై కేవిటీలో ఉంచబడుతుంది మరియు ఒక వంపుతిరిగిన అక్షం మీద తిరుగుతున్నప్పుడు కక్ష్య మార్గంలో ప్రయాణించే ఎగువ డై ద్వారా నకిలీ చేయబడుతుంది. ప్రతి విప్లవం వద్ద, ఎగువ డై మొత్తం వర్క్ పీస్కు సంపీడన శక్తులను ప్రయోగించడం పూర్తి చేస్తుంది. ఈ విప్లవాలను అనేక సార్లు పునరావృతం చేయడం ద్వారా, తగినంత ఫోర్జింగ్ జరుగుతుంది. ఈ తయారీ సాంకేతికత యొక్క ప్రయోజనాలు దాని తక్కువ శబ్దం ఆపరేషన్ మరియు తక్కువ బలాలు అవసరం. మరో మాటలో చెప్పాలంటే, చిన్న శక్తులతో ఒక అక్షం చుట్టూ భారీ డైని తిప్పవచ్చు, ఇది డైతో సంబంధంలో ఉన్న వర్క్ పీస్లోని ఒక విభాగంపై పెద్ద ఒత్తిడిని వర్తింపజేయవచ్చు. డిస్క్ లేదా శంఖు ఆకారపు భాగాలు కొన్నిసార్లు ఈ ప్రక్రియకు బాగా సరిపోతాయి.
• రింగ్ ఫోర్జింగ్: మేము తరచుగా అతుకులు లేని రింగులను తయారు చేయడానికి ఉపయోగిస్తాము. స్టాక్ పొడవుగా కత్తిరించబడుతుంది, కలత చెందుతుంది మరియు కేంద్ర రంధ్రం సృష్టించడానికి అన్ని మార్గం గుండా కుట్టబడుతుంది. అప్పుడు అది ఒక మాండ్రెల్పై ఉంచబడుతుంది మరియు కావలసిన కొలతలు పొందే వరకు రింగ్ నెమ్మదిగా తిప్పబడినందున దానిని పైనుండి ఫోర్జింగ్ డై సుత్తితో కొడుతుంది.
• రివెటింగ్: భాగాలను కలపడం కోసం ఒక సాధారణ ప్రక్రియ, భాగాల ద్వారా ముందుగా తయారు చేయబడిన రంధ్రాలలో చొప్పించిన నేరుగా మెటల్ ముక్కతో ప్రారంభమవుతుంది. ఆ తర్వాత లోహపు ముక్క యొక్క రెండు చివరలు ఎగువ మరియు దిగువ డై మధ్య జాయింట్ను పిండడం ద్వారా నకిలీ చేయబడతాయి.
• కాయినింగ్ : మెకానికల్ ప్రెస్ ద్వారా నిర్వహించబడే మరొక ప్రసిద్ధ ప్రక్రియ, తక్కువ దూరం వరకు పెద్ద బలగాలను ప్రయోగించడం. లోహపు నాణేల ఉపరితలాలపై నకిలీ చేయబడిన చక్కటి వివరాల నుండి "కాయినింగ్" అనే పేరు వచ్చింది. ఇది చాలావరకు ఒక ఉత్పత్తికి పూర్తి చేసే ప్రక్రియ, ఈ వివరాలను వర్క్ పీస్కి బదిలీ చేసే డై ద్వారా వర్తించే పెద్ద శక్తి ఫలితంగా ఉపరితలాలపై చక్కటి వివరాలు పొందబడతాయి.
• మెటల్ బాల్ ఫోర్జింగ్ : బాల్ బేరింగ్ల వంటి ఉత్పత్తులకు అధిక నాణ్యతతో ఖచ్చితంగా తయారు చేయబడిన మెటల్ బాల్స్ అవసరం. SKEW ROLLING అని పిలువబడే ఒక టెక్నిక్లో, స్టాక్ను రోల్స్లోకి నిరంతరంగా అందించడం వలన మేము నిరంతరం తిరిగే రెండు వ్యతిరేక రోల్లను ఉపయోగిస్తాము. రెండు రోల్స్ యొక్క ఒక చివర లోహ గోళాలు ఉత్పత్తిగా బయటకు వస్తాయి. మెటల్ బాల్ ఫోర్జింగ్ కోసం రెండవ పద్ధతి అచ్చు కుహరం యొక్క గోళాకార ఆకారాన్ని తీసుకొని వాటి మధ్య ఉంచిన మెటీరియల్ స్టాక్ను పిండి వేయడాన్ని ఉపయోగించడం. తరచుగా ఉత్పత్తి చేయబడిన బంతులు అధిక నాణ్యత గల ఉత్పత్తిగా మారడానికి ఫినిషింగ్ మరియు పాలిషింగ్ వంటి కొన్ని అదనపు దశలు అవసరమవుతాయి.
• ఐసోథర్మల్ ఫోర్జింగ్ / హాట్ డై ఫోర్జింగ్ : ప్రయోజనం / ఖర్చు విలువ సమర్థించబడినప్పుడు మాత్రమే ఖరీదైన ప్రక్రియ నిర్వహించబడుతుంది. వర్క్ పీస్ మాదిరిగానే డైని దాదాపు అదే ఉష్ణోగ్రతకు వేడి చేసే హాట్ వర్కింగ్ ప్రాసెస్. డై మరియు పని రెండూ ఒకే ఉష్ణోగ్రతలో ఉండటం వలన, శీతలీకరణ ఉండదు మరియు మెటల్ యొక్క ప్రవాహ లక్షణాలు మెరుగుపడతాయి. నాసిరకం ఫోర్జిబిలిటీ మరియు మెటీరియల్స్ ఉన్న సూపర్ అల్లాయ్లు మరియు మెటీరియల్లకు ఈ ఆపరేషన్ బాగా సరిపోతుంది.
యాంత్రిక లక్షణాలు చిన్న ఉష్ణోగ్రత ప్రవణతలు మరియు మార్పులకు చాలా సున్నితంగా ఉంటాయి.
• మెటల్ సైజింగ్ : ఇది కోల్డ్ ఫినిషింగ్ ప్రక్రియ. శక్తి వర్తించే దిశను మినహాయించి అన్ని దిశలలో మెటీరియల్ ప్రవాహం అనియంత్రితమైనది. ఫలితంగా, చాలా మంచి ఉపరితల ముగింపు మరియు ఖచ్చితమైన కొలతలు పొందబడతాయి.
• HIGH ఎనర్జీ రేట్ ఫోర్జింగ్: టెక్నిక్లో పిస్టన్ చేతికి జోడించబడిన పై అచ్చు ఉంటుంది, ఇది ఒక స్పార్క్ ప్లగ్ ద్వారా మండించబడిన ఇంధన-గాలి మిశ్రమం వేగంగా నెట్టబడుతుంది. ఇది కారు ఇంజిన్లోని పిస్టన్ల ఆపరేషన్ను పోలి ఉంటుంది. అచ్చు వర్క్ పీస్ను చాలా వేగంగా తాకుతుంది మరియు బ్యాక్ప్రెజర్ కారణంగా చాలా వేగంగా దాని అసలు స్థానానికి తిరిగి వస్తుంది. పని కొన్ని మిల్లీసెకన్లలో నకిలీ చేయబడుతుంది మరియు అందువల్ల పనిని చల్లబరచడానికి సమయం లేదు. ఇది చాలా ఉష్ణోగ్రత సెన్సిటివ్ మెకానికల్ లక్షణాలను కలిగి ఉండే హార్డ్ టు ఫోర్జ్ భాగాలకు ఉపయోగపడుతుంది. మరో మాటలో చెప్పాలంటే, ప్రక్రియ చాలా వేగంగా ఉంటుంది, భాగం అంతటా స్థిరమైన ఉష్ణోగ్రతలో ఏర్పడుతుంది మరియు అచ్చు/వర్క్ పీస్ ఇంటర్ఫేస్ల వద్ద ఉష్ణోగ్రత ప్రవణతలు ఉండవు.
• DIE FORGINGలో, డైస్ అని పిలువబడే ప్రత్యేక ఆకారాలతో సరిపోలే రెండు ఉక్కు దిమ్మెల మధ్య మెటల్ కొట్టబడుతుంది. డైస్ల మధ్య లోహాన్ని కొట్టినప్పుడు, అది డైలోని ఆకారాల మాదిరిగానే ఉంటుంది. ఇది దాని తుది ఆకృతికి చేరుకున్నప్పుడు, అది చల్లబరచడానికి బయటకు తీయబడుతుంది. ఈ ప్రక్రియ ఖచ్చితమైన ఆకారంలో ఉండే బలమైన భాగాలను ఉత్పత్తి చేస్తుంది, అయితే ప్రత్యేకమైన డైస్ల కోసం పెద్ద పెట్టుబడి అవసరం. అప్సెట్ ఫోర్జింగ్ ఒక మెటల్ ముక్కను చదును చేయడం ద్వారా దాని వ్యాసాన్ని పెంచుతుంది. ఇది సాధారణంగా చిన్న భాగాలను తయారు చేయడానికి, ముఖ్యంగా బోల్ట్లు మరియు నెయిల్స్ వంటి ఫాస్టెనర్లపై హెడ్లను రూపొందించడానికి ఉపయోగిస్తారు.
• పౌడర్ మెటలర్జీ / పౌడర్ ప్రాసెసింగ్: పేరు సూచించినట్లుగా, ఇది నిర్దిష్ట జ్యామితి మరియు ఆకారాల యొక్క ఘన భాగాలను పౌడర్ల నుండి తయారు చేయడానికి తయారీ ప్రక్రియలను కలిగి ఉంటుంది. ఈ ప్రయోజనం కోసం మెటల్ పౌడర్లను ఉపయోగిస్తే అది పౌడర్ మెటలర్జీ రాజ్యం మరియు నాన్-మెటల్ పౌడర్లను ఉపయోగిస్తే అది పౌడర్ ప్రాసెసింగ్. నొక్కడం మరియు సింటరింగ్ చేయడం ద్వారా పౌడర్ల నుండి ఘన భాగాలు ఉత్పత్తి చేయబడతాయి.
POWDER PRESSING అనేది పౌడర్లను కావలసిన ఆకారాలలో కుదించడానికి ఉపయోగించబడుతుంది. మొదట, ప్రాథమిక పదార్థం భౌతికంగా పొడిగా ఉంటుంది, దానిని అనేక చిన్న వ్యక్తిగత కణాలుగా విభజిస్తుంది. పౌడర్ మిశ్రమం డైలో నింపబడుతుంది మరియు ఒక పంచ్ పౌడర్ వైపు కదులుతుంది మరియు దానిని కావలసిన ఆకారంలో కుదించబడుతుంది. ఎక్కువగా గది ఉష్ణోగ్రత వద్ద నిర్వహిస్తారు, పొడిని నొక్కడం ద్వారా ఒక ఘన భాగం లభిస్తుంది మరియు దానిని గ్రీన్ కాంపాక్ట్ అంటారు. బైండర్లు మరియు కందెనలు సాధారణంగా కాంపాక్టబిలిటీని పెంచడానికి ఉపయోగిస్తారు. మేము అనేక వేల టన్నుల సామర్థ్యంతో హైడ్రాలిక్ ప్రెస్లను ఉపయోగించి పౌడర్ ప్రెస్ను రూపొందించగల సామర్థ్యం కలిగి ఉన్నాము. అలాగే అత్యంత సంక్లిష్టమైన పార్ట్ జ్యామితి కోసం మేము వ్యతిరేక టాప్ & బాటమ్ పంచ్లతో డబుల్ యాక్షన్ ప్రెస్లను అలాగే బహుళ యాక్షన్ ప్రెస్లను కలిగి ఉన్నాము. అనేక పౌడర్ మెటలర్జీ / పౌడర్ ప్రాసెసింగ్ ప్లాంట్లకు ఒక ముఖ్యమైన సవాలుగా ఉన్న ఏకరూపత AGS-TECHకి పెద్ద సమస్య కాదు ఎందుకంటే చాలా సంవత్సరాలుగా ఇటువంటి భాగాలను కస్టమ్ తయారీలో మా విస్తృతమైన అనుభవం ఉంది. ఏకరూపత సవాలుగా ఉన్న మందమైన భాగాలతో కూడా మేము విజయం సాధించాము. మేము మీ ప్రాజెక్ట్కు కట్టుబడి ఉంటే, మేము మీ భాగాలను తయారు చేస్తాము. మేము ఏవైనా సంభావ్య ప్రమాదాలను చూసినట్లయితే, మేము మీకు in తెలియజేస్తాము
అడ్వాన్స్.
రెండవ దశ అయిన POWDER SINTERING, ఉష్ణోగ్రతను ఒక నిర్దిష్ట స్థాయికి పెంచడం మరియు ఆ స్థాయిలో ఉష్ణోగ్రతను నిర్దిష్ట సమయం వరకు నిర్వహించడం, తద్వారా నొక్కిన భాగంలోని పొడి కణాలు ఒకదానితో ఒకటి బంధించబడతాయి. ఇది చాలా బలమైన బంధాలకు దారితీస్తుంది మరియు పని భాగాన్ని బలోపేతం చేస్తుంది. సింటరింగ్ పొడి యొక్క ద్రవీభవన ఉష్ణోగ్రతకు దగ్గరగా జరుగుతుంది. సింటరింగ్ సమయంలో సంకోచం సంభవిస్తుంది, పదార్థ బలం, సాంద్రత, డక్టిలిటీ, ఉష్ణ వాహకత, విద్యుత్ వాహకత పెరుగుతుంది. మేము సింటరింగ్ కోసం బ్యాచ్ మరియు నిరంతర ఫర్నేస్లను కలిగి ఉన్నాము. మేము ఉత్పత్తి చేసే భాగాల సచ్ఛిద్రత స్థాయిని సర్దుబాటు చేయడం మా సామర్థ్యాలలో ఒకటి. ఉదాహరణకు, మేము భాగాలను కొంత వరకు పోరస్గా ఉంచడం ద్వారా మెటల్ ఫిల్టర్లను ఉత్పత్తి చేయగలము.
IMPREGNATION అనే టెక్నిక్ని ఉపయోగించి, మనం లోహంలోని రంధ్రాలను నూనె వంటి ద్రవంతో నింపుతాము. మేము ఉదాహరణకు స్వీయ కందెన చమురు కలిపిన బేరింగ్లు ఉత్పత్తి చేస్తాము. ఇన్ఫిల్ట్రేషన్ ప్రక్రియలో మనం ఒక లోహపు రంధ్రాలను ఆధార పదార్థం కంటే తక్కువ ద్రవీభవన స్థానం ఉన్న మరొక లోహంతో నింపుతాము. మిశ్రమం రెండు లోహాల ద్రవీభవన ఉష్ణోగ్రతల మధ్య ఉష్ణోగ్రతకు వేడి చేయబడుతుంది. ఫలితంగా కొన్ని ప్రత్యేక లక్షణాలను పొందవచ్చు. ప్రత్యేక లక్షణాలు లేదా లక్షణాలను పొందవలసి వచ్చినప్పుడు లేదా తక్కువ ప్రాసెస్ దశలతో భాగాన్ని తయారు చేయగలిగినప్పుడు మేము పౌడర్ తయారు చేసిన భాగాలపై మ్యాచింగ్ మరియు ఫోర్జింగ్ వంటి ద్వితీయ కార్యకలాపాలను కూడా తరచుగా చేస్తాము.
ఐసోస్టాటిక్ ప్రెస్సింగ్: ఈ ప్రక్రియలో భాగాన్ని కుదించడానికి ద్రవ పీడనం ఉపయోగించబడుతుంది. మెటల్ పౌడర్లను మూసివున్న సౌకర్యవంతమైన కంటైనర్తో తయారు చేసిన అచ్చులో ఉంచుతారు. ఐసోస్టాటిక్ నొక్కడంలో, సాంప్రదాయిక నొక్కడంలో కనిపించే అక్షసంబంధ పీడనానికి విరుద్ధంగా, చుట్టుపక్కల నుండి ఒత్తిడి వర్తించబడుతుంది. ఐసోస్టాటిక్ నొక్కడం యొక్క ప్రయోజనాలు భాగం లోపల ఏకరీతి సాంద్రత, ప్రత్యేకించి పెద్ద లేదా మందమైన భాగాలకు, ఉన్నతమైన లక్షణాలు. దీని ప్రతికూలత దీర్ఘ చక్రాల సమయాలు మరియు సాపేక్షంగా తక్కువ రేఖాగణిత ఖచ్చితత్వం. కోల్డ్ ఐసోస్టాటిక్ ప్రెస్సింగ్ గది ఉష్ణోగ్రత వద్ద నిర్వహించబడుతుంది మరియు సౌకర్యవంతమైన అచ్చు రబ్బరు, PVC లేదా యురేథేన్ లేదా సారూప్య పదార్థాలతో తయారు చేయబడుతుంది. ఒత్తిడి మరియు కుదించడానికి ఉపయోగించే ద్రవం నూనె లేదా నీరు. ఆకుపచ్చ కాంపాక్ట్ యొక్క సాంప్రదాయిక సింటరింగ్ దీనిని అనుసరిస్తుంది. మరోవైపు హాట్ ఐసోస్టాటిక్ నొక్కడం అధిక ఉష్ణోగ్రతల వద్ద నిర్వహించబడుతుంది మరియు అచ్చు పదార్థం ఉష్ణోగ్రతలను నిరోధించే తగినంత అధిక ద్రవీభవన స్థానం కలిగిన షీట్ మెటల్ లేదా సిరామిక్. ఒత్తిడి కలిగించే ద్రవం సాధారణంగా జడ వాయువు. నొక్కడం మరియు సింటరింగ్ కార్యకలాపాలు ఒక దశలో నిర్వహించబడతాయి. సచ్ఛిద్రత దాదాపు పూర్తిగా తొలగించబడింది, ఏకరీతి grain నిర్మాణం పొందబడింది. హాట్ ఐసోస్టాటిక్ నొక్కడం యొక్క ప్రయోజనం ఏమిటంటే, ఇది కాస్టింగ్ మరియు ఫోర్జింగ్తో పోల్చదగిన భాగాలను ఉత్పత్తి చేయగలదు, అయితే కాస్టింగ్ మరియు ఫోర్జింగ్కు అనుకూలం కాని పదార్థాలను ఉపయోగించడం సాధ్యమవుతుంది. హాట్ ఐసోస్టాటిక్ నొక్కడం యొక్క ప్రతికూలత దాని అధిక చక్ర సమయం మరియు అందువలన ఖర్చు. ఇది తక్కువ వాల్యూమ్ యొక్క క్లిష్టమైన భాగాలకు అనుకూలంగా ఉంటుంది.
మెటల్ ఇంజెక్షన్ మోల్డింగ్: సన్నని గోడలు మరియు వివరణాత్మక జ్యామితితో సంక్లిష్ట భాగాలను ఉత్పత్తి చేయడానికి చాలా సరిఅయిన ప్రక్రియ. చిన్న భాగాలకు అత్యంత అనుకూలమైనది. పొడులు మరియు పాలీమర్ బైండర్లను కలిపి, వేడి చేసి, అచ్చులోకి ఇంజెక్ట్ చేస్తారు. పాలిమర్ బైండర్ పొడి కణాల ఉపరితలాలను పూస్తుంది. మౌల్డింగ్ తర్వాత, బైండర్ ఒక ద్రావకం ఉపయోగించి కరిగిన తక్కువ ఉష్ణోగ్రత తాపన ద్వారా తొలగించబడుతుంది.
రోల్ కంపాక్షన్ / పౌడర్ రోలింగ్: పొడులు నిరంతర స్ట్రిప్స్ లేదా షీట్ను ఉత్పత్తి చేయడానికి ఉపయోగిస్తారు. పౌడర్ ఫీడర్ నుండి ఫీడ్ చేయబడుతుంది మరియు షీట్ లేదా స్ట్రిప్స్లో రెండు తిరిగే రోల్స్ ద్వారా కుదించబడుతుంది. ఆపరేషన్ చల్లగా జరుగుతుంది. షీట్ సింటరింగ్ ఫర్నేస్లోకి తీసుకువెళతారు. సింటరింగ్ ప్రక్రియ రెండవసారి పునరావృతం కావచ్చు.
పౌడర్ ఎక్స్ట్రూషన్: పెద్ద పొడవు మరియు వ్యాసం నిష్పత్తులు కలిగిన భాగాలు ఒక సన్నని షీట్ మెటల్ కంటైనర్ను పొడితో వెలికితీయడం ద్వారా తయారు చేయబడతాయి.
లూస్ సింటరింగ్ : పేరు సూచించినట్లుగా, ఇది ఒత్తిడి లేని కుదింపు మరియు సింటరింగ్ పద్ధతి, మెటల్ ఫిల్టర్ల వంటి చాలా పోరస్ భాగాలను ఉత్పత్తి చేయడానికి అనుకూలంగా ఉంటుంది. పౌడర్ కుదించబడకుండా అచ్చు కుహరంలోకి అందించబడుతుంది.
లూస్ సింటరింగ్ : పేరు సూచించినట్లుగా, ఇది ఒత్తిడి లేని కుదింపు మరియు సింటరింగ్ పద్ధతి, మెటల్ ఫిల్టర్ల వంటి చాలా పోరస్ భాగాలను ఉత్పత్తి చేయడానికి అనుకూలంగా ఉంటుంది. పౌడర్ కుదించబడకుండా అచ్చు కుహరంలోకి అందించబడుతుంది.
SPARK SINTERING : పౌడర్ రెండు వ్యతిరేక పంచ్ల ద్వారా అచ్చులో కుదించబడుతుంది మరియు పంచ్కు అధిక శక్తి విద్యుత్ ప్రవాహాన్ని వర్తించబడుతుంది మరియు వాటి మధ్య శాండ్విచ్ చేయబడిన కాంపాక్ట్ పౌడర్ గుండా వెళుతుంది. అధిక విద్యుత్తు పొడి కణాల నుండి ఉపరితల పొరలను కాల్చివేస్తుంది మరియు ఉత్పన్నమైన వేడితో వాటిని సింటర్స్ చేస్తుంది. ప్రక్రియ వేగంగా ఉంటుంది ఎందుకంటే వేడిని బయటి నుండి వర్తించదు, బదులుగా అది అచ్చు లోపల నుండి ఉత్పత్తి చేయబడుతుంది.
వేడి నొక్కడం: అధిక ఉష్ణోగ్రతలను తట్టుకోగల అచ్చులో పౌడర్లను ఒకే దశలో ఒత్తడం మరియు సిన్టర్ చేయడం జరుగుతుంది. డై కాంపాక్ట్ అయినప్పుడు పొడి వేడి దానికి వర్తించబడుతుంది. ఈ పద్ధతి ద్వారా సాధించిన మంచి ఖచ్చితత్వాలు మరియు యాంత్రిక లక్షణాలు ఆకర్షణీయమైన ఎంపికగా చేస్తాయి. గ్రాఫైట్ వంటి అచ్చు పదార్థాలను ఉపయోగించడం ద్వారా వక్రీభవన లోహాలను కూడా ప్రాసెస్ చేయవచ్చు.