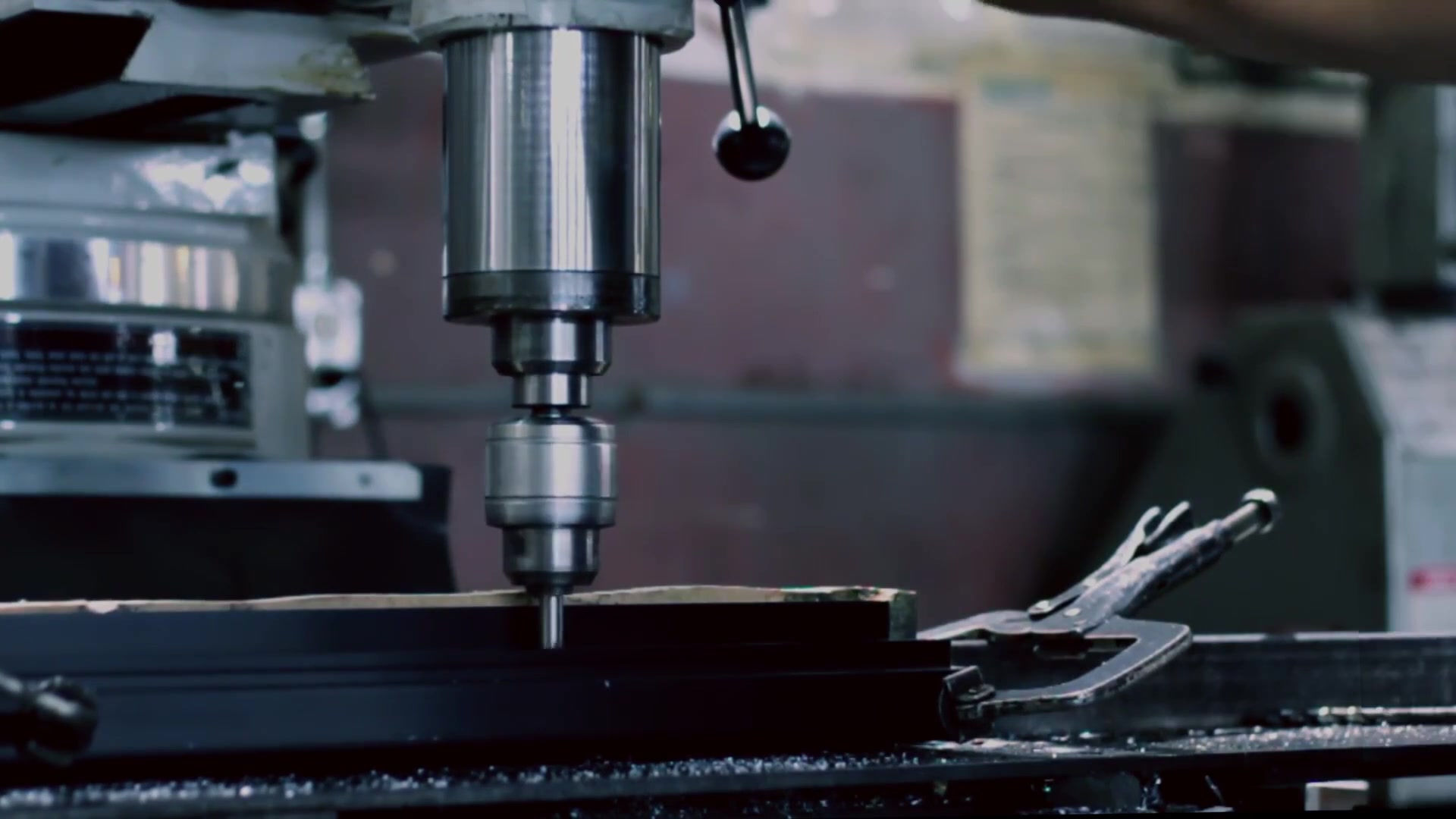
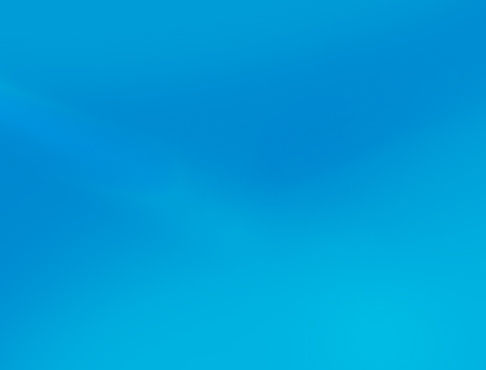
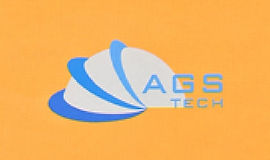
Pandaigdigang Custom na Manufacturer, Integrator, Consolidator, Outsourcing Partner para sa Maraming Iba't Ibang Produkto at Serbisyo.
Kami ang iyong one-stop source para sa pagmamanupaktura, fabrication, engineering, consolidation, integration, outsourcing ng custom na manufactured at off-shelf na mga produkto at serbisyo.
Piliin ang iyong Wika
-
Custom na Paggawa
-
Domestic at Global Contract Manufacturing
-
Paggawa ng Outsourcing
-
Domestic at Global Procurement
-
Consolidation
-
Pagsasama-sama ng Engineering
-
Serbisyong inhinyero
Kabilang sa maraming diskarte sa PAGSASAMA na ipinapatupad namin sa pagmamanupaktura, binibigyan ng espesyal na diin ang WELDING, BRAZING, SOLDERING, ADHESIVE BONDING at CUSTOM MECHANICAL ASSEMBLY dahil malawakang ginagamit ang mga diskarteng ito sa mga aplikasyon tulad ng pagmamanupaktura ng hermetic assemblies, high-tech na paggawa ng produkto at espesyal na sealing. Dito tayo magtutuon ng pansin sa mga mas espesyal na aspeto ng mga diskarte sa pagsali na ito dahil nauugnay ang mga ito sa paggawa ng mga advanced na produkto at assemblies.
FUSION WELDING: Gumagamit kami ng init upang matunaw at magsama-sama ang mga materyales. Ang init ay ibinibigay ng kuryente o mga high-energy beam. Ang mga uri ng fusion welding na aming idine-deploy ay OXYFUEL GAS WELDING, ARC WELDING, HIGH-ENERGY-BEAM WELDING.
SOLID-STATE WELDING: Pinagsasama namin ang mga bahagi nang hindi natutunaw at nagsasama. Ang aming solid-state na paraan ng welding ay COLD, ULTRASONIC, RESISTANCE, FRICTION, EXPLOSION WELDING at DIFFUSION BONDING.
BRAZING & SOLDERING: Gumagamit sila ng mga filler metal at nagbibigay sa amin ng kalamangan sa pagtatrabaho sa mas mababang temperatura kaysa sa welding, kaya mas kaunting pinsala sa istruktura sa mga produkto. Ang impormasyon sa aming brazing facility na gumagawa ng ceramic to metal fittings, hermetic sealing, vacuum feedthroughs, high at ultrahigh vacuum at fluid control components ay matatagpuan dito:Brochure ng Brazing Factory
ADHESIVE BONDING: Dahil sa pagkakaiba-iba ng adhesives na ginagamit sa industriya at sa pagkakaiba-iba din ng mga application, mayroon kaming nakalaang pahina para dito. Upang pumunta sa aming pahina tungkol sa adhesive bonding, mangyaring mag-click dito.
CUSTOM MECHANICAL ASSEMBLY: Gumagamit kami ng iba't ibang mga fastener tulad ng bolts, screws, nuts, rivets. Ang aming mga fastener ay hindi limitado sa karaniwang off-shelf fasteners. Kami ay nagdidisenyo, gumagawa at gumagawa ng mga espesyal na fastener na ginawa mula sa hindi karaniwang mga materyales upang matugunan nila ang mga kinakailangan para sa mga espesyal na aplikasyon. Minsan ang electrical o heat non-conductivity ay ninanais samantalang kung minsan ay conductivity. Para sa ilang espesyal na application, maaaring gusto ng isang customer ang mga espesyal na fastener na hindi matatanggal nang hindi sinisira ang produkto. Mayroong walang katapusang mga ideya at aplikasyon. Mayroon kaming lahat para sa iyo, kung hindi sa labas, maaari naming mabilis na mabuo ito. Upang pumunta sa aming pahina sa mekanikal na pagpupulong, mangyaring mag-click dito. Suriin natin ang iba't ibang diskarte sa pagsali sa higit pang mga detalye.
OXYFUEL GAS WELDING (OFW): Gumagamit kami ng fuel gas na hinaluan ng oxygen upang makagawa ng welding flame. Kapag ginamit natin ang acetylene bilang panggatong at oxygen, tinatawag natin itong oxyacetylene gas welding. Dalawang reaksiyong kemikal ang nangyayari sa proseso ng pagkasunog ng oxyfuel gas:
C2H2 + O2 ------» 2CO + H2 + Heat
2CO + H2 + 1.5 O2--------» 2 CO2 + H2O + Heat
Ang unang reaksyon ay naghihiwalay sa acetylene sa carbon monoxide at hydrogen habang gumagawa ng humigit-kumulang 33% ng kabuuang init na nabuo. Ang pangalawang proseso sa itaas ay kumakatawan sa karagdagang pagkasunog ng hydrogen at carbon monoxide habang gumagawa ng humigit-kumulang 67% ng kabuuang init. Ang mga temperatura sa apoy ay nasa pagitan ng 1533 hanggang 3573 Kelvin. Ang porsyento ng oxygen sa pinaghalong gas ay mahalaga. Kung ang nilalaman ng oxygen ay higit sa kalahati, ang apoy ay nagiging isang oxidizing agent. Ito ay hindi kanais-nais para sa ilang mga metal ngunit kanais-nais para sa iba. Isang halimbawa kapag ang oxidizing flame ay kanais-nais ay tanso-based na mga haluang metal dahil ito ay bumubuo ng isang passivation layer sa ibabaw ng metal. Sa kabilang banda, kapag ang nilalaman ng oxygen ay nabawasan, ang buong pagkasunog ay hindi posible at ang apoy ay nagiging isang pagbabawas (carburizing) na apoy. Ang mga temperatura sa isang pagbabawas ng apoy ay mas mababa at samakatuwid ito ay angkop para sa mga proseso tulad ng paghihinang at pagpapatigas. Ang iba pang mga gas ay mga potensyal na panggatong din, ngunit mayroon silang ilang mga disadvantages kaysa sa acetylene. Paminsan-minsan ay nagbibigay kami ng mga filler metal sa weld zone sa anyo ng mga filler rod o wire. Ang ilan sa mga ito ay pinahiran ng flux upang pigilan ang oksihenasyon ng mga ibabaw at sa gayon ay pinoprotektahan ang tinunaw na metal. Ang karagdagang benepisyo na ibinibigay sa atin ng flux ay ang pag-alis ng mga oxide at iba pang substance mula sa weld zone. Ito ay humahantong sa mas malakas na pagbubuklod. Ang isang pagkakaiba-iba ng welding ng oxyfuel gas ay ang PRESSURE GAS WELDING, kung saan ang dalawang bahagi ay pinainit sa kanilang interface gamit ang oxyacetylene gas torch at sa sandaling ang interface ay nagsimulang matunaw, ang tanglaw ay aalisin at isang axial force ay inilapat upang pindutin ang dalawang bahagi nang magkasama hanggang sa maging solid ang interface.
ARC WELDING: Gumagamit kami ng de-koryenteng enerhiya upang makagawa ng arko sa pagitan ng dulo ng elektrod at mga bahaging hinangin. Ang power supply ay maaaring AC o DC habang ang mga electrodes ay consumable o nonconsumable. Ang paglipat ng init sa arc welding ay maaaring ipahayag sa pamamagitan ng sumusunod na equation:
H / l = ex VI / v
Narito ang H ang input ng init, l ang haba ng weld, V at I ang boltahe at kasalukuyang inilapat, v ang bilis ng hinang at e ang kahusayan ng proseso. Kung mas mataas ang kahusayan "e" mas kapaki-pakinabang ang magagamit na enerhiya na ginagamit upang matunaw ang materyal. Ang input ng init ay maaari ding ipahayag bilang:
H = ux (Volume) = ux A xl
Narito u ang tiyak na enerhiya para sa pagtunaw, A ang cross section ng weld at l ang haba ng weld. Mula sa dalawang equation sa itaas maaari nating makuha ang:
v = ex VI / u A
Ang pagkakaiba-iba ng arc welding ay ang SHIELDED METAL ARC WELDING (SMAW) na bumubuo ng halos 50% ng lahat ng proseso ng pang-industriya at pagpapanatili ng welding. Ang ELECTRIC ARC WELDING (STICK WELDING) ay ginagawa sa pamamagitan ng pagpindot sa dulo ng isang coated electrode sa workpiece at mabilis na i-withdraw ito sa isang distansya na sapat upang mapanatili ang arc. Ang prosesong ito ay tinatawag din naming stick-welding dahil ang mga electrodes ay manipis at mahabang stick. Sa panahon ng proseso ng hinang, ang dulo ng elektrod ay natutunaw kasama ang patong nito at ang base metal sa paligid ng arko. Ang pinaghalong base metal, electrode metal at mga substance mula sa electrode coating ay nagpapatigas sa weld area. Ang patong ng elektrod ay nagde-deoxidize at nagbibigay ng shielding gas sa weld region, kaya pinoprotektahan ito mula sa oxygen sa kapaligiran. Samakatuwid ang proseso ay tinutukoy bilang shielded metal arc welding. Gumagamit kami ng mga agos sa pagitan ng 50 at 300 Amperes at mga antas ng kuryente sa pangkalahatan ay mas mababa sa 10 kW para sa pinakamabuting pagganap ng weld. Gayundin ng kahalagahan ay ang polarity ng DC kasalukuyang (direksyon ng kasalukuyang daloy). Ang tuwid na polarity kung saan ang workpiece ay positibo at ang elektrod ay negatibo ay ginustong sa hinang ng mga sheet metal dahil sa mababaw na pagtagos nito at gayundin para sa mga joints na may napakalawak na puwang. Kapag tayo ay may reverse polarity, ibig sabihin, ang elektrod ay positibo at ang workpiece ay negatibo, makakamit natin ang mas malalim na pagpasok ng weld. Sa kasalukuyang AC, dahil mayroon kaming mga pulsating arc, maaari kaming magwelding ng makapal na mga seksyon gamit ang mga electrodes na may malalaking diameter at pinakamataas na alon. Ang pamamaraan ng welding ng SMAW ay angkop para sa mga kapal ng workpiece na 3 hanggang 19 mm at higit pa gamit ang mga diskarteng multiple-pass. Ang slag na nabuo sa tuktok ng weld ay kailangang alisin gamit ang isang wire brush, upang walang kaagnasan at pagkabigo sa lugar ng hinang. Ito siyempre ay nagdaragdag sa halaga ng shielded metal arc welding. Gayunpaman ang SMAW ay ang pinakasikat na welding technique sa industriya at pagkukumpuni.
SUBMERGED ARC WELDING (SAW): Sa prosesong ito, pinoprotektahan namin ang weld arc gamit ang granular flux na materyales tulad ng lime, silica, calcium floride, manganese oxide....atbp. Ang butil-butil na pagkilos ng bagay ay pinapakain sa weld zone sa pamamagitan ng gravity flow sa pamamagitan ng isang nozzle. Ang flux na sumasaklaw sa molten weld zone ay makabuluhang pinoprotektahan mula sa sparks, fumes, UV radiation...atbp at nagsisilbing thermal insulator, kaya hinahayaan ang init na tumagos nang malalim sa workpiece. Ang unfused flux ay nakuhang muli, ginagamot at muling ginagamit. Ang isang coil ng hubad ay ginagamit bilang elektrod at pinapakain sa pamamagitan ng isang tubo sa lugar ng hinang. Gumagamit kami ng mga agos sa pagitan ng 300 at 2000 Amperes. Ang proseso ng submerged arc welding (SAW) ay limitado sa pahalang at patag na mga posisyon at pabilog na welds kung posible ang pag-ikot ng pabilog na istraktura (tulad ng mga tubo) sa panahon ng hinang. Ang mga bilis ay maaaring umabot sa 5 m/min. Ang proseso ng SAW ay angkop para sa makapal na mga plato at nagreresulta sa mataas na kalidad, matigas, ductile at pare-parehong welds. Ang pagiging produktibo, iyon ay ang halaga ng weld material na idineposito kada oras ay 4 hanggang 10 beses ang halaga kumpara sa proseso ng SMAW.
Ang isa pang proseso ng arc welding, katulad ng GAS METAL ARC WELDING (GMAW) o alternatibong tinutukoy bilang METAL INERT GAS WELDING (MIG) ay batay sa lugar ng hinang na pinangangalagaan ng mga panlabas na pinagmumulan ng mga gas tulad ng helium, argon, carbon dioxide....atbp. Maaaring may mga karagdagang deoxidizer na naroroon sa electrode metal. Ang consumable wire ay pinapakain sa pamamagitan ng nozzle papunta sa weld zone. Ang paggawa na kinasasangkutan ng bot ferrous gayundin ang mga nonferrous na metal ay isinasagawa gamit ang gas metal arc welding (GMAW). Ang pagiging produktibo ng welding ay halos 2 beses kaysa sa proseso ng SMAW. Ginagamit ang mga automated welding equipment. Ang metal ay inililipat sa isa sa tatlong paraan sa prosesong ito: Ang "Spray Transfer" ay nagsasangkot ng paglipat ng ilang daang maliliit na patak ng metal bawat segundo mula sa elektrod patungo sa lugar ng hinang. Sa "Globular Transfer" sa kabilang banda, ang mga gas na mayaman sa carbon dioxide ay ginagamit at ang mga globule ng tinunaw na metal ay itinutulak ng electric arc. Mataas ang welding currents at mas malalim ang weld penetration, mas mabilis ang welding kaysa sa spray transfer. Kaya ang globular transfer ay mas mahusay para sa hinang mas mabibigat na seksyon. Sa wakas, sa pamamaraang "Short Circuiting", ang dulo ng electrode ay dumadampi sa molten weld pool, ang short circuiting nito bilang metal sa bilis na higit sa 50 droplets/segundo ay inililipat sa mga indibidwal na droplet. Ang mga mababang alon at boltahe ay ginagamit kasama ng mas manipis na kawad. Ang mga kapangyarihang ginamit ay humigit-kumulang 2 kW at medyo mababa ang temperatura, na ginagawang angkop ang pamamaraang ito para sa manipis na mga sheet na mas mababa sa 6mm ang kapal.
Ang isa pang pagkakaiba-iba ng proseso ng FLUX-CORED ARC WELDING (FCAW) ay katulad ng gas metal arc welding, maliban na ang elektrod ay isang tubo na puno ng flux. Ang mga bentahe ng paggamit ng mga cored-flux electrodes ay ang paggawa ng mga ito ng mas matatag na mga arko, nagbibigay sa amin ng pagkakataon na mapabuti ang mga katangian ng mga weld metal, hindi gaanong malutong at nababaluktot na katangian ng pagkilos ng bagay nito kumpara sa SMAW welding, pinahusay na mga contour ng welding. Ang self-shielded cored electrodes ay naglalaman ng mga materyales na sumasangga sa weld zone laban sa atmospera. Gumagamit kami ng halos 20 kW na kapangyarihan. Tulad ng proseso ng GMAW, nag-aalok din ang proseso ng FCAW ng pagkakataon na i-automate ang mga proseso para sa tuluy-tuloy na hinang, at ito ay matipid. Ang iba't ibang weld metal chemistries ay maaaring mabuo sa pamamagitan ng pagdaragdag ng iba't ibang mga haluang metal sa flux core.
Sa ELECTROGAS WELDING (EGW) hinangin namin ang mga piraso na nakalagay sa gilid sa gilid. Minsan tinatawag din itong BUTT WELDING. Ang weld metal ay inilalagay sa isang weld cavity sa pagitan ng dalawang piraso na pagsasamahin. Ang espasyo ay napapalibutan ng dalawang water-cooled na dam upang hindi bumuhos ang nilusaw na slag. Ang mga dam ay inilipat sa pamamagitan ng mga mekanikal na drive. Kapag maaaring paikutin ang workpiece, maaari din nating gamitin ang electrogas welding technique para sa circumferential welding ng mga tubo. Ang mga electrodes ay pinapakain sa pamamagitan ng isang conduit upang mapanatili ang isang tuluy-tuloy na arko. Ang mga agos ay maaaring nasa paligid ng 400Amperes o 750 Amperes at mga antas ng kapangyarihan sa paligid ng 20 kW. Ang mga inert gas na nagmumula sa alinman sa flux-cored electrode o external source ay nagbibigay ng shielding. Ginagamit namin ang electrogas welding (EGW) para sa mga metal tulad ng steels, titanium….etc na may kapal mula 12mm hanggang 75mm. Ang pamamaraan ay angkop para sa malalaking istruktura.
Gayunpaman, sa isa pang pamamaraan na tinatawag na ELECTROSLAG WELDING (ESW) ang arko ay nag-aapoy sa pagitan ng elektrod at sa ilalim ng workpiece at idinagdag ang flux. Kapag ang molten slag ay umabot sa dulo ng elektrod, ang arko ay pinapatay. Ang enerhiya ay patuloy na ibinibigay sa pamamagitan ng electrical resistance ng molten slag. Maaari tayong magwelding ng mga plate na may kapal sa pagitan ng 50 mm at 900 mm at mas mataas pa. Ang mga agos ay nasa 600 Ampere habang ang mga boltahe ay nasa pagitan ng 40 – 50 V. Ang mga bilis ng hinang ay nasa paligid ng 12 hanggang 36 mm/min. Ang mga aplikasyon ay katulad ng electrogas welding.
Isa sa aming mga hindi natutunaw na proseso ng electrode, ang GAS TUNGSTEN ARC WELDING (GTAW) na kilala rin bilang TUNGSTEN INERT GAS WELDING (TIG) ay kinabibilangan ng supply ng isang filler metal sa pamamagitan ng wire. Para sa malapit na magkasya sa mga joints kung minsan ay hindi namin ginagamit ang filler metal. Sa proseso ng TIG hindi kami gumagamit ng flux, ngunit gumagamit ng argon at helium para sa shielding. Ang Tungsten ay may mataas na punto ng pagkatunaw at hindi natutunaw sa proseso ng TIG welding, samakatuwid ang pare-pareho ang kasalukuyang pati na rin ang arc gaps ay maaaring mapanatili. Ang mga antas ng kuryente ay nasa pagitan ng 8 hanggang 20 kW at ang mga agos sa alinman sa 200 Ampere (DC) o 500 Ampere (AC). Para sa aluminyo at magnesiyo ginagamit namin ang AC current para sa oxide cleaning function nito. Upang maiwasan ang kontaminasyon ng tungsten electrode, iniiwasan namin ang pakikipag-ugnay nito sa mga tinunaw na metal. Ang Gas Tungsten Arc Welding (GTAW) ay lalong kapaki-pakinabang para sa pagwelding ng mga manipis na metal. Ang GTAW welds ay may napakataas na kalidad na may magandang surface finish.
Dahil sa mas mataas na halaga ng hydrogen gas, ang isang hindi gaanong madalas na ginagamit na pamamaraan ay ang ATOMIC HYDROGEN WELDING (AHW), kung saan kami ay bumubuo ng isang arko sa pagitan ng dalawang tungsten electrodes sa isang shielding atmosphere ng dumadaloy na hydrogen gas. Ang AHW ay isa ring nonconsumable electrode welding process. Ang diatomic hydrogen gas H2 ay bumagsak sa atomic form nito malapit sa welding arc kung saan ang temperatura ay higit sa 6273 Kelvin. Habang nasira, sumisipsip ito ng malaking halaga ng init mula sa arko. Kapag ang mga hydrogen atoms ay tumama sa weld zone na medyo malamig na ibabaw, sila ay muling pinagsama sa diatomic na anyo at pinakawalan ang nakaimbak na init. Maaaring iba-iba ang enerhiya sa pamamagitan ng pagpapalit ng workpiece sa arc distance.
Sa isa pang nonconsumable na proseso ng electrode, ang PLASMA ARC WELDING (PAW) ay mayroon tayong concentrated plasma arc na nakadirekta patungo sa weld zone. Ang temperatura ay umabot sa 33,273 Kelvin sa PAW. Ang halos pantay na bilang ng mga electron at ion ay bumubuo sa plasma gas. Ang isang mababang-kasalukuyang pilot arc ay nagpapasimula ng plasma na nasa pagitan ng tungsten electrode at orifice. Ang mga operating currents ay karaniwang nasa 100 Amperes. Maaaring pakainin ang isang filler metal. Sa plasma arc welding, ang shielding ay ginagawa sa pamamagitan ng panlabas na shielding ring at paggamit ng mga gas tulad ng argon at helium. Sa plasma arc welding, ang arc ay maaaring nasa pagitan ng electrode at workpiece o sa pagitan ng electrode at nozzle. Ang welding technique na ito ay may mga pakinabang sa iba pang mga paraan ng mas mataas na konsentrasyon ng enerhiya, mas malalim at mas makitid na kakayahan sa welding, mas mahusay na arc stability, mas mataas na bilis ng welding hanggang 1 metro/min, mas mababa ang thermal distortion. Karaniwang ginagamit namin ang plasma arc welding para sa mga kapal na mas mababa sa 6 mm at minsan hanggang 20 mm para sa aluminyo at titanium.
HIGH-ENERGY-BEAM WELDING: Isa pang uri ng fusion welding method na may electron-beam welding (EBW) at laser welding (LBW) bilang dalawang variant. Ang mga diskarteng ito ay may partikular na halaga para sa aming paggawa ng mga high-tech na produkto. Sa electron-beam welding, ang mga high speed na electron ay tumama sa workpiece at ang kanilang kinetic energy ay na-convert sa init. Ang makitid na sinag ng mga electron ay madaling maglakbay sa silid ng vacuum. Sa pangkalahatan ay gumagamit kami ng mataas na vacuum sa e-beam welding. Ang mga plato na kasing kapal ng 150 mm ay maaaring welded. Walang shielding gas, flux o filler material ang kailangan. Ang mga electron beam gun ay may 100 kW na kapasidad. Malalim at makitid na welds na may mataas na aspect ratio hanggang 30 at maliit na heat-affected zone ay posible. Ang bilis ng hinang ay maaaring umabot sa 12 m/min. Sa laser-beam welding ginagamit namin ang mga high-power na laser bilang pinagmumulan ng init. Ang mga laser beam na kasing liit ng 10 microns na may mataas na density ay nagbibigay-daan sa malalim na pagtagos sa workpiece. Depth-to-width ratios hangga't 10 ay posible sa laser-beam welding. Ginagamit namin ang parehong pulsed pati na rin ang tuloy-tuloy na wave laser, na ang una ay ginagamit para sa mga manipis na materyales at ang huli ay kadalasang para sa makapal na workpieces hanggang sa humigit-kumulang 25 mm. Ang mga antas ng kapangyarihan ay hanggang sa 100 kW. Ang laser beam welding ay hindi angkop para sa optically very reflective na materyales. Ang mga gas ay maaari ding gamitin sa proseso ng hinang. Ang pamamaraan ng laser beam welding ay angkop para sa automation at high volume manufacturing at maaaring mag-alok ng mga bilis ng welding sa pagitan ng 2.5 m/min at 80 m/min. Ang isang pangunahing bentahe na inaalok ng welding technique na ito ay ang access sa mga lugar kung saan hindi magagamit ang ibang mga technique. Ang mga laser beam ay madaling maglakbay sa mga mahihirap na rehiyon. Walang vacuum tulad ng sa electron-beam welding ay kailangan. Ang mga welds na may magandang kalidad at lakas, mababang pag-urong, mababang pagbaluktot, mababang porosity ay maaaring makuha sa laser beam welding. Ang mga laser beam ay madaling manipulahin at hugis gamit ang fiber optic cables. Ang pamamaraan ay kaya angkop para sa welding ng precision hermetic assemblies, electronic packages...atbp.
Tingnan natin ang aming mga diskarte sa SOLID STATE WELDING. Ang COLD WELDING (CW) ay isang proseso kung saan ang pressure sa halip na init ay inilapat gamit ang mga dies o roll sa mga bahaging pinag-isa. Sa malamig na hinang, hindi bababa sa isa sa mga bahagi ng isinangkot ay kailangang maging ductile. Ang pinakamahusay na mga resulta ay nakuha sa dalawang magkatulad na materyales. Kung ang dalawang metal na pagdurugtong sa malamig na hinang ay hindi magkatulad, maaari tayong makakuha ng mahina at malutong na mga kasukasuan. Ang paraan ng malamig na welding ay angkop para sa malambot, ductile at maliliit na workpiece tulad ng mga de-koryenteng koneksyon, mga gilid ng lalagyan na sensitibo sa init, mga bimetallic strip para sa mga thermostat...atbp. Ang isang pagkakaiba-iba ng malamig na hinang ay roll bonding (o roll welding), kung saan ang presyon ay inilalapat sa pamamagitan ng isang pares ng mga rolyo. Minsan nagsasagawa kami ng roll welding sa mataas na temperatura para sa mas mahusay na lakas ng interface.
Ang isa pang solid state na proseso ng welding na ginagamit namin ay ang ULTRASONIC WELDING (USW), kung saan ang mga workpiece ay sumasailalim sa isang static na normal na puwersa at oscillating shearing stresses. Ang oscillating shearing stresses ay inilalapat sa dulo ng isang transducer. Ang ultrasonic welding ay naglalagay ng mga oscillations na may mga frequency mula 10 hanggang 75 kHz. Sa ilang mga aplikasyon tulad ng seam welding, gumagamit kami ng umiikot na welding disk bilang tip. Ang mga shearing stresses na inilapat sa mga workpiece ay nagdudulot ng maliliit na plastic deformation, nasira ang mga layer ng oxide, mga contaminant at humantong sa solid state bonding. Ang mga temperaturang kasangkot sa ultrasonic welding ay mas mababa sa temperatura ng melting point para sa mga metal at walang pagsasanib na nagaganap. Madalas naming ginagamit ang proseso ng ultrasonic welding (USW) para sa mga nonmetallic na materyales tulad ng mga plastik. Sa thermoplastics, ang mga temperatura ay umabot sa mga punto ng pagkatunaw gayunpaman.
Isa pang tanyag na pamamaraan, sa FRICTION WELDING (FRW) ang init ay nabubuo sa pamamagitan ng friction sa interface ng mga workpiece na pagsasamahin. Sa friction welding pinapanatili namin ang isa sa mga workpiece na nakatigil habang ang isa pang workpiece ay hawak sa isang kabit at pinaikot sa isang pare-pareho ang bilis. Ang mga workpiece ay dinadala sa contact sa ilalim ng isang axial force. Ang bilis ng ibabaw ng pag-ikot sa friction welding ay maaaring umabot sa 900m/min sa ilang mga kaso. Pagkatapos ng sapat na interfacial contact, ang umiikot na workpiece ay dinadala sa biglaang paghinto at ang axial force ay tumaas. Ang weld zone ay karaniwang isang makitid na rehiyon. Ang friction welding technique ay maaaring gamitin upang pagdugtungan ang mga solid at tubular na bahagi na gawa sa iba't ibang materyales. Ang ilang flash ay maaaring bumuo sa interface sa FRW, ngunit ang flash na ito ay maaaring alisin sa pamamagitan ng pangalawang machining o paggiling. Ang mga pagkakaiba-iba ng proseso ng friction welding ay umiiral. Halimbawa, ang "inertia friction welding" ay nagsasangkot ng isang flywheel na ang rotational kinetic energy ay ginagamit upang hinangin ang mga bahagi. Kumpleto ang weld kapag huminto ang flywheel. Ang umiikot na masa ay maaaring iba-iba at sa gayon ay ang rotational kinetic energy. Ang isa pang pagkakaiba-iba ay ang "linear friction welding", kung saan ang linear reciprocating motion ay ipinapataw sa kahit isa sa mga bahaging pagsasamahin. Sa linear friction welding parts ay hindi kailangang maging pabilog, maaari silang maging hugis-parihaba, parisukat o ng iba pang hugis. Ang mga frequency ay maaaring nasa sampu-sampung Hz, mga amplitude sa hanay ng millimeters at mga presyon sa sampu o daan-daang MPa. Sa wakas, ang "friction stir welding" ay medyo naiiba kaysa sa iba pang dalawang ipinaliwanag sa itaas. Samantalang sa inertia friction welding at linear friction welding heating ng mga interface ay nakakamit sa pamamagitan ng friction sa pamamagitan ng pagkuskos ng dalawang contacting surface, sa friction stir welding na paraan ng pangatlong katawan ay kuskusin laban sa dalawang ibabaw na pagsasamahin. Ang isang umiikot na tool na 5 hanggang 6 mm diameter ay dinadala sa contact sa joint. Ang mga temperatura ay maaaring tumaas sa mga halaga sa pagitan ng 503 hanggang 533 Kelvin. Nagaganap ang pag-init, paghahalo at pagpapakilos ng materyal sa joint. Ginagamit namin ang friction stir welding sa iba't ibang materyales kabilang ang aluminum, plastic at composites. Ang mga welds ay pare-pareho at mataas ang kalidad na may pinakamababang pores. Walang fumes o spatter ang nagagawa sa friction stir welding at ang proseso ay maayos na awtomatiko.
RESISTANCE WELDING (RW): Ang init na kinakailangan para sa welding ay ginawa ng electrical resistance sa pagitan ng dalawang workpiece na pagsasamahin. Walang flux, shielding gas o consumable electrodes ang ginagamit sa resistance welding. Ang pag-init ng joule ay nagaganap sa welding ng paglaban at maaaring ipahayag bilang:
H = (Square I) x R xtx K
Ang H ay init na nabuo sa joules (watt-segundo), I kasalukuyang sa Amperes, R resistance sa Ohms, t ay ang oras sa mga segundo na dumadaloy ang kasalukuyang. Ang factor K ay mas mababa sa 1 at kumakatawan sa fraction ng enerhiya na hindi nawawala sa pamamagitan ng radiation at conduction. Ang mga alon sa mga proseso ng welding ng paglaban ay maaaring umabot sa mga antas na kasing taas ng 100,000 A ngunit ang mga boltahe ay karaniwang 0.5 hanggang 10 Volts. Ang mga electrodes ay karaniwang gawa sa mga haluang tanso. Ang parehong magkatulad at hindi magkatulad na mga materyales ay maaaring pagsamahin sa pamamagitan ng welding ng paglaban. Mayroong ilang mga pagkakaiba-iba para sa prosesong ito: Ang "Resistance spot welding" ay nagsasangkot ng dalawang magkasalungat na round electrodes na nakikipag-ugnay sa mga ibabaw ng lap joint ng dalawang sheet. Inilapat ang presyon hanggang sa patayin ang kasalukuyang. Ang weld nugget ay karaniwang hanggang 10 mm ang lapad. Ang resistance spot welding ay nag-iiwan ng bahagyang kupas na mga marka ng indentation sa mga weld spot. Ang spot welding ay ang aming pinakasikat na resistance welding technique. Ang iba't ibang mga hugis ng elektrod ay ginagamit sa spot welding upang maabot ang mahihirap na lugar. Ang aming kagamitan sa spot welding ay kontrolado ng CNC at mayroong maraming electrodes na maaaring gamitin nang sabay-sabay. Ang isa pang pagkakaiba-iba ng "resistance seam welding" ay isinasagawa gamit ang mga electrodes ng gulong o roller na gumagawa ng tuluy-tuloy na spot welds sa tuwing ang kasalukuyang ay umabot sa isang sapat na mataas na antas sa AC power cycle. Ang mga joints na ginawa ng resistance seam welding ay likido at gas tight. Ang bilis ng welding na humigit-kumulang 1.5 m/min ay normal para sa manipis na mga sheet. Ang isa ay maaaring maglapat ng mga pasulput-sulpot na alon upang ang mga spot welds ay ginawa sa nais na mga pagitan sa kahabaan ng tahi. Sa "resistance projection welding" nag-emboss kami ng isa o higit pang mga projection (dimples) sa isa sa mga ibabaw ng workpiece na hinangin. Ang mga projection na ito ay maaaring bilog o hugis-itlog. Naaabot ang matataas na naka-localize na temperatura sa mga embossed spot na ito na nakikipag-ugnayan sa bahagi ng isinangkot. Ang mga electrodes ay nagbibigay ng presyon upang i-compress ang mga projection na ito. Ang mga electrodes sa resistance projection welding ay may mga flat na tip at mga water cooled na tansong haluang metal. Ang bentahe ng resistance projection welding ay ang ating kakayahan sa isang bilang ng mga welds sa isang stroke, kaya ang pinahabang buhay ng elektrod, kakayahang magwelding ng mga sheet ng iba't ibang kapal, kakayahang magwelding ng mga nuts at bolts sa mga sheet. Ang kawalan ng resistance projection welding ay ang idinagdag na halaga ng embossing ng mga dimples. Ang isa pang pamamaraan, sa "flash welding" na init ay nabuo mula sa arko sa mga dulo ng dalawang workpiece habang nagsisimula silang makipag-ugnayan. Ang pamamaraang ito ay maaari ding isaalang-alang ang arc welding. Ang temperatura sa interface ay tumataas, at ang materyal ay lumalambot. Ang isang axial force ay inilapat at isang weld ay nabuo sa pinalambot na rehiyon. Matapos makumpleto ang flash welding, ang joint ay maaaring makina para sa pinabuting hitsura. Ang kalidad ng weld na nakuha sa pamamagitan ng flash welding ay mabuti. Ang mga antas ng kapangyarihan ay 10 hanggang 1500 kW. Ang flash welding ay angkop para sa gilid-sa-gilid na pagdugtong ng magkatulad o hindi magkatulad na mga metal hanggang sa 75 mm diameter at mga sheet sa pagitan ng 0.2 mm hanggang 25 mm ang kapal. Ang "stud arc welding" ay halos kapareho sa flash welding. Ang stud tulad ng isang bolt o sinulid na baras ay nagsisilbing isang elektrod habang pinagsama sa isang workpiece tulad ng isang plato. Upang pag-concentrate ang nabuong init, maiwasan ang oksihenasyon at panatilihin ang tinunaw na metal sa weld zone, isang disposable ceramic ring ang inilalagay sa paligid ng joint. Sa wakas, ang "percussion welding" ay isa pang proseso ng resistance welding, na gumagamit ng capacitor upang matustusan ang elektrikal na enerhiya. Sa percussion welding ang kapangyarihan ay nadidischarge sa loob ng millisecond ng oras nang napakabilis na nagkakaroon ng mataas na localized na init sa joint. Malawakang ginagamit namin ang percussion welding sa industriya ng pagmamanupaktura ng electronics kung saan kailangang iwasan ang pag-init ng mga sensitibong bahagi ng electronic sa paligid ng joint.
Ang isang pamamaraan na tinatawag na EXPLOSION WELDING ay nagsasangkot ng pagpapasabog ng isang layer ng paputok na ilalagay sa ibabaw ng isa sa mga workpiece na pagsasamahin. Ang napakataas na presyon na ibinibigay sa workpiece ay gumagawa ng isang magulong at kulot na interface at nagaganap ang mekanikal na interlocking. Ang mga lakas ng bono sa explosive welding ay napakataas. Ang welding ng pagsabog ay isang mahusay na paraan para sa pag-cladding ng mga plato na may magkakaibang mga metal. Pagkatapos ng cladding, ang mga plato ay maaaring igulong sa mas manipis na mga seksyon. Minsan gumagamit kami ng explosion welding para sa pagpapalawak ng mga tubo upang mai-sealed ang mga ito nang mahigpit sa plato.
Ang aming huling paraan sa loob ng domain ng solid state joining ay ang DIFFUSION BONDING o DIFFUSION WELDING (DFW) kung saan ang isang magandang joint ay nakakamit pangunahin sa pamamagitan ng diffusion ng mga atom sa interface. Ang ilang mga plastic deformation sa interface ay nag-aambag din sa hinang. Ang mga kasangkot na temperatura ay nasa paligid ng 0.5 Tm kung saan ang Tm ay temperatura ng pagkatunaw ng metal. Ang lakas ng bono sa diffusion welding ay nakasalalay sa presyon, temperatura, oras ng pakikipag-ugnay at kalinisan ng mga ibabaw na nakikipag-ugnayan. Minsan gumagamit kami ng mga filler metal sa interface. Ang init at presyon ay kinakailangan sa diffusion bonding at ibinibigay ng electrical resistance o furnace at dead weights, press or else. Ang magkatulad at hindi magkatulad na mga metal ay maaaring pagsamahin sa diffusion welding. Ang proseso ay medyo mabagal dahil sa oras na kinakailangan para sa mga atom na lumipat. Maaaring awtomatiko ang DFW at malawakang ginagamit sa paggawa ng mga kumplikadong bahagi para sa aerospace, electronics, medikal na industriya. Kasama sa mga produktong ginawa ang orthopedic implants, sensor, aerospace structural member. Ang diffusion bonding ay maaaring isama sa SUPERPLASTIC FORMING upang makagawa ng mga kumplikadong istruktura ng sheet metal. Ang mga napiling lokasyon sa mga sheet ay unang diffusion bonded at pagkatapos ay ang mga unbonded na rehiyon ay pinalawak sa isang molde gamit ang air pressure. Ang mga istruktura ng aerospace na may mataas na stiffness-to-weight ratios ay ginawa gamit ang kumbinasyong ito ng mga pamamaraan. Ang diffusion welding / superplastic forming pinagsamang proseso ay binabawasan ang bilang ng mga bahagi na kinakailangan sa pamamagitan ng pag-aalis ng pangangailangan para sa mga fastener, na nagreresulta sa mababang-stress na lubos na tumpak na mga bahagi sa matipid at may maikling oras ng lead.
BRAZING: Ang brazing at soldering techniques ay may kasamang mas mababang temperatura kaysa sa mga kinakailangan para sa welding. Gayunpaman, ang mga temperatura ng pagpapatigas ay mas mataas kaysa sa mga temperatura ng paghihinang. Sa pagpapatigas ng isang filler metal ay inilalagay sa pagitan ng mga ibabaw na pagsasamahin at ang mga temperatura ay itataas sa temperatura ng pagkatunaw ng materyal na tagapuno sa itaas ng 723 Kelvin ngunit mas mababa sa temperatura ng pagkatunaw ng mga workpiece. Pinupuno ng tinunaw na metal ang malapit na angkop na espasyo sa pagitan ng mga workpiece. Ang paglamig at kasunod na solidification ng filer metal ay nagreresulta sa malalakas na joints. Sa braze welding ang filler metal ay idineposito sa joint. Mas maraming filler metal ang ginagamit sa braze welding kumpara sa brazing. Ang oxyacetylene torch na may oxidizing flame ay ginagamit para ideposito ang filler metal sa braze welding. Dahil sa mas mababang temperatura sa brazing, mas mababa ang mga problema sa mga apektadong lugar ng init gaya ng warping at mga natitirang stress. Kung mas maliit ang clearance gap sa brazing, mas mataas ang shear strength ng joint. Ang pinakamataas na lakas ng tensile gayunpaman ay nakakamit sa pinakamainam na puwang (isang pinakamataas na halaga). Sa ibaba at sa itaas ng pinakamabuting halaga na ito, ang lakas ng makunat sa pagpapatigas ay bumababa. Ang mga karaniwang clearance sa brazing ay maaaring nasa pagitan ng 0.025 at 0.2 mm. Gumagamit kami ng iba't ibang mga brazing na materyales na may iba't ibang hugis tulad ng performs, powder, rings, wire, strip…..etc. at maaaring gumawa ng mga gumaganap na ito para sa iyong disenyo o geometry ng produkto. Tinutukoy din namin ang nilalaman ng mga materyales sa pagpapatigas ayon sa iyong mga batayang materyales at aplikasyon. Madalas kaming gumagamit ng mga flux sa mga pagpapatakbo ng brazing upang alisin ang mga hindi gustong mga layer ng oxide at maiwasan ang oksihenasyon. Upang maiwasan ang kasunod na kaagnasan, ang mga flux ay karaniwang inaalis pagkatapos ng operasyon ng pagsali. Gumagamit ang AGS-TECH Inc. ng iba't ibang paraan ng pagpapatigas, kabilang ang:
- Torch Brazing
- Pagpapatigas ng Pugon
- Induction Brazing
- Pagpapatigas ng Paglaban
- Isawsaw ang Brazing
- Infrared Brazing
- Diffusion Brazing
- High Energy Beam
Ang aming pinakakaraniwang mga halimbawa ng brazed joints ay gawa sa magkakaibang mga metal na may mahusay na lakas tulad ng carbide drill bits, inserts, optoelectronic hermetic packages, seal.
PAGSOLDER : Ito ang isa sa aming pinakamadalas na ginagamit na mga diskarte kung saan pinupuno ng solder (filler metal) ang joint gaya ng pagpapatigas sa pagitan ng mga bahaging malapit na magkasya. Ang aming mga solder ay may mga melting point na mas mababa sa 723 Kelvin. Nag-deploy kami ng manu-mano at awtomatikong paghihinang sa mga operasyon ng pagmamanupaktura. Kung ikukumpara sa pagpapatigas, ang mga temperatura ng paghihinang ay mas mababa. Ang paghihinang ay hindi masyadong angkop para sa mataas na temperatura o mataas na lakas na mga aplikasyon. Gumagamit kami ng mga lead-free na panghinang pati na rin ang tin-lead, tin-zinc, lead-silver, cadmium-silver, zinc-aluminum alloys bukod sa iba pa para sa paghihinang. Parehong noncorrosive resin-based pati na rin ang mga inorganic acid at salts ay ginagamit bilang flux sa paghihinang. Gumagamit kami ng mga espesyal na flux para sa paghihinang ng mga metal na may mababang solderability. Sa mga application kung saan kailangan nating maghinang ng mga ceramic na materyales, salamin o grapayt, pinahiran muna natin ang mga bahagi na may angkop na metal para sa mas mataas na solderability. Ang aming mga sikat na pamamaraan ng paghihinang ay:
-Reflow o I-paste ang Paghihinang
-Wave Soldering
-Paghihinang ng Pugon
-Sulo Paghihinang
-Induction Soldering
-Iron Paghihinang
-Resistance Soldering
-Isawsaw ang paghihinang
-Ultrasonic Soldering
-Infrared na Paghihinang
Ang ultrasonic na paghihinang ay nag-aalok sa amin ng isang natatanging kalamangan kung saan ang pangangailangan para sa mga flux ay inalis dahil sa ultrasonic cavitation effect na nag-aalis ng mga oxide film mula sa mga ibabaw na pinagsanib. Ang Reflow at Wave soldering ay ang aming namumukod-tanging mga diskarte sa industriya para sa mataas na volume na pagmamanupaktura sa electronics at samakatuwid ay sulit na ipaliwanag nang mas detalyado. Sa reflow soldering, gumagamit kami ng mga semisolid paste na may kasamang solder-metal particle. Ang paste ay inilalagay sa joint gamit ang screening o stenciling process. Sa mga naka-print na circuit board (PCB) madalas naming ginagamit ang pamamaraang ito. Kapag ang mga de-koryenteng sangkap ay inilagay sa mga pad na ito mula sa paste, pinapanatili ng pag-igting sa ibabaw na nakahanay ang mga pakete sa ibabaw-mount. Pagkatapos ilagay ang mga bahagi, pinainit namin ang pagpupulong sa isang pugon upang maganap ang reflow soldering. Sa panahon ng prosesong ito, ang mga solvent sa paste ay sumingaw, ang flux sa paste ay isinaaktibo, ang mga bahagi ay pinainit, ang mga particle ng panghinang ay natutunaw at binabasa ang joint, at sa wakas ang PCB assembly ay pinalamig nang dahan-dahan. Ang aming pangalawang tanyag na pamamaraan para sa mataas na dami ng produksyon ng mga PCB board, lalo na ang wave soldering ay umaasa sa katotohanan na ang mga tinunaw na solder ay basa sa mga ibabaw ng metal at bumubuo lamang ng magagandang bono kapag ang metal ay pinainit. Ang isang nakatayong laminar wave ng molten solder ay unang nabuo sa pamamagitan ng isang pump at ang preheated at prefluxed na mga PCB ay dinadala sa ibabaw ng wave. Binabasa lamang ng solder ang mga nakalantad na ibabaw ng metal ngunit hindi binabasa ang mga pakete ng IC polymer o ang mga circuit board na pinahiran ng polymer. Ang isang mataas na bilis ng hot water jet ay humihip ng labis na solder mula sa joint at pinipigilan ang pag-bridging sa pagitan ng mga katabing lead. Sa wave soldering ng surface-mount packages, idinidikit muna namin ang mga ito sa circuit board bago maghinang. Muli screening at stenciling ay ginagamit ngunit oras na ito para sa epoxy. Matapos mailagay ang mga sangkap sa kanilang mga tamang lokasyon, ang epoxy ay gumaling, ang mga board ay baligtad at ang wave soldering ay nagaganap.