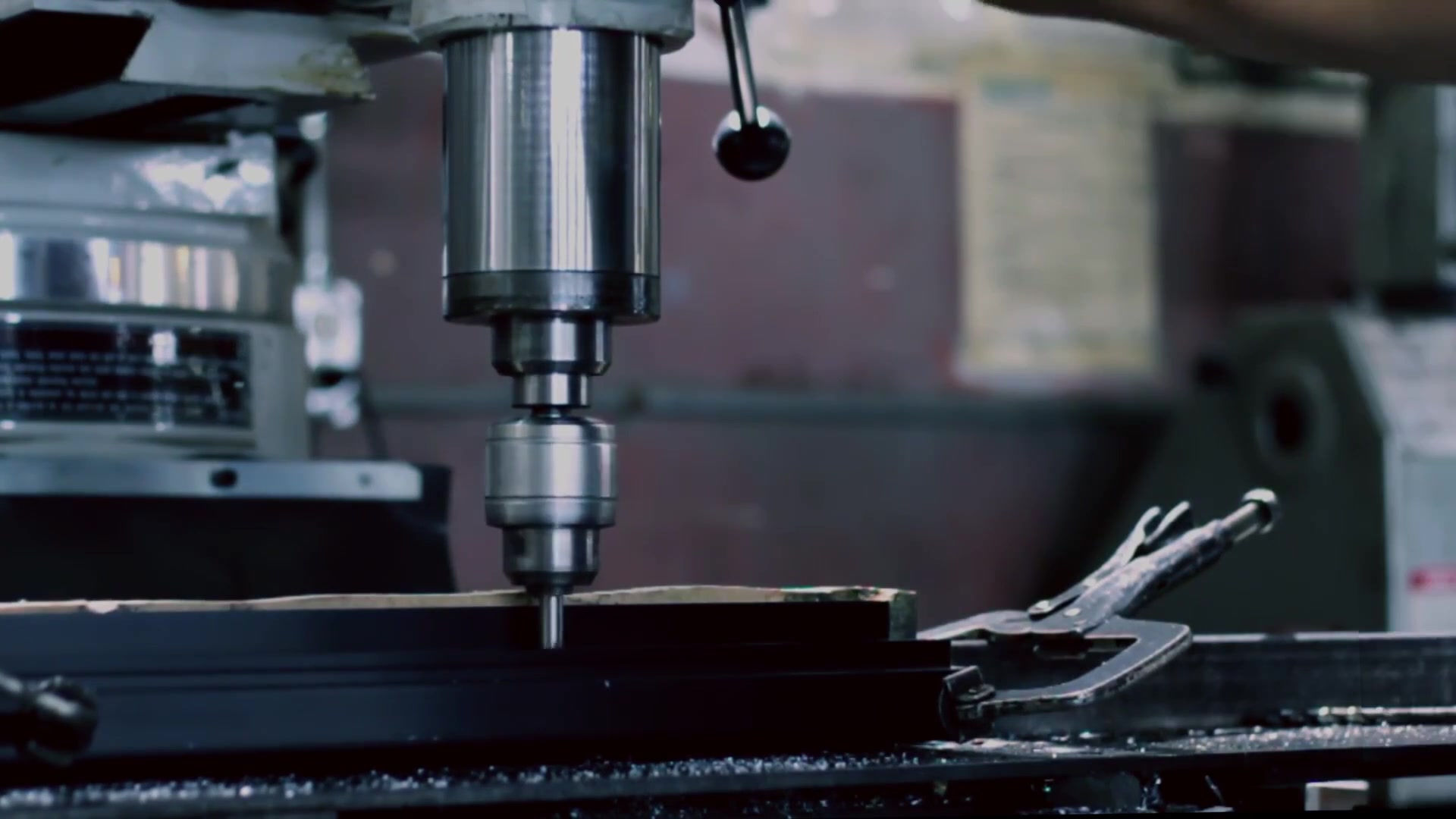
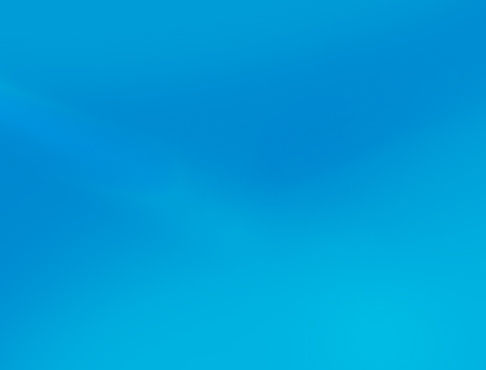
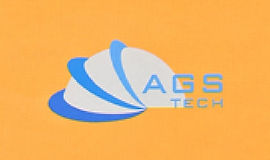
Çok Çeşitli Ürün ve Hizmetler için Küresel Özel Fason Üretici, Entegratör, Montaj Tedarikçisi, Global Imalat Ortağı.
Özel imal edilmiş ve kullanıma hazır fason ürün imalatı ve hizmetlerin tedariği, mühendisliği, konsolidasyonu, entegrasyonu, küresel fason üretim için tek durak kaynağınız biziz.
Choose your Language
-
Özel İmalatlar
-
Yerli & Global Fason Üretim
-
İmalat Dış Kaynak Kullanımı
-
Yurtiçi ve Küresel Tedarik
-
Konsolidasyon
-
Mühendislik Entegrasyonu
-
Mühendislik Hizmetleri
Son yıllarda HIZLI İMALAT veya HIZLI PROTOTİPLEME için talepte artış gördük. Bu süreç aynı zamanda MASAÜSTÜ ÜRETİM veya SERBEST FORM İMALAT olarak da adlandırılabilir. Temel olarak, bir parçanın katı bir fiziksel modeli, doğrudan üç boyutlu bir CAD çiziminden yapılır. Parçaları katmanlar halinde oluşturduğumuz bu çeşitli teknikler için KATKILI İMALAT terimini kullanıyoruz. Entegre bilgisayar destekli donanım ve yazılım kullanarak eklemeli üretim gerçekleştiriyoruz. Hızlı prototipleme ve üretim tekniklerimiz STEROLİTOGRAFİ, POLİJET, KAYNAKLI-DEPOZİSYON MODELLEME, SEÇİCİ LAZER SİNTERLEME, ELEKTRON IŞINI ERİTME, ÜÇ BOYUTLU BASKI, DOĞRUDAN ÜRETİM, HIZLI TAKIMLARDIR. için buraya tıklamanızı öneririz.AGS-TECH Inc. Katmanlı İmalat ve Hızlı İmalat Proseslerinin Şematik Gösterimlerimizi İNDİRİN
Bu, aşağıda size sağladığımız bilgileri daha iyi anlamanıza yardımcı olacaktır.
Hızlı prototipleme bize şunları sağlar: 1.) Konsept ürün tasarımı, bir 3D / CAD sistemi kullanılarak bir monitörde farklı açılardan görüntülenir. 2.) Metalik olmayan ve metalik olmayan malzemelerden prototipler üretilir ve fonksiyonel, teknik ve estetik açıdan incelenir. 3.) Çok kısa sürede düşük maliyetli prototipleme gerçekleştirilir. Eklemeli imalat, tek tek dilimlerin üst üste istiflenmesi ve yapıştırılmasıyla bir somun ekmek yapımına benzetilebilir. Yani ürün dilim dilim veya katman katman birbiri üzerine bırakılarak üretilir. Çoğu parça saatler içinde üretilebilir. Parçalara çok hızlı ihtiyaç duyuluyorsa veya ihtiyaç duyulan miktarlar düşükse ve kalıp ve alet yapımı çok pahalı ve zaman alıyorsa teknik iyidir. Ancak pahalı hammaddeler nedeniyle bir parçanın maliyeti pahalıdır.
• STEREOLİTOGRAFİ : STL olarak da kısaltılan bu teknik, bir sıvı fotopolimerin üzerine bir lazer ışını odaklanarak sertleştirilmesi ve belirli bir şekle getirilmesine dayanır. Lazer fotopolimeri polimerize eder ve sertleştirir. UV lazer ışını fotopolimer karışımının yüzeyi boyunca programlanmış şekle göre taranarak parça, aşağıdan yukarıya, birbiri üzerine kademeli olarak ayrı ayrı dilimler halinde üretilir. Sistemde programlanan geometrileri elde etmek için lazer noktasının taranması birçok kez tekrarlanır. Parça tamamen imal edildikten sonra platformdan çıkarılır, lekelenir ve ultrasonik ve alkol banyosu ile temizlenir. Ardından, polimerin tamamen kürlendiğinden ve sertleştiğinden emin olmak için birkaç saat UV ışınlarına maruz bırakılır. İşlemi özetlemek gerekirse, fotopolimer karışımına daldırılan bir platform ve bir UV lazer ışını kontrol edilerek istenilen parçanın şekline göre servo kontrol sistemi ile hareket ettirilir ve polimer tabakası katman katman fotokürlenerek parça elde edilir. Elbette üretilen parçanın maksimum boyutları stereolitografi ekipmanı tarafından belirlenir.
• POLYJET : Mürekkep püskürtmeli baskıya benzer şekilde, polijette, yapı tepsisine fotopolimer bırakan sekiz baskı kafamız var. Jetlerin yanına yerleştirilen ultraviyole ışık, her katmanı anında sertleştirir ve sertleştirir. Polijette iki malzeme kullanılmaktadır. İlk malzeme, gerçek modeli üretmek içindir. İkinci malzeme, destek için jel benzeri bir reçine kullanılır. Bu malzemelerin her ikisi de katman katman biriktirilir ve aynı anda kürlenir. Modelin tamamlanmasından sonra destek malzemesi sulu bir çözelti ile çıkarılır. Kullanılan reçineler stereolitografiye (STL) benzer. Polyjet, stereolitografiye göre aşağıdaki avantajlara sahiptir: 1.) Parçaların temizlenmesine gerek yoktur. 2.) İşlem sonrası kürlemeye gerek yok 3.) Daha küçük katman kalınlıkları mümkündür ve böylece daha iyi çözünürlük elde ederiz ve daha ince parçalar üretebiliriz.
• FUSED DEPOSITION MODELING : FDM olarak da kısaltılır, bu yöntemde robot kontrollü bir ekstrüder kafası bir masa üzerinde iki ana yönde hareket eder. Kablo gerektiği gibi indirilir ve yükseltilir. Başlıktaki ısıtılmış bir kalıbın ağzından, termoplastik bir filament ekstrüde edilir ve bir köpük temel üzerine bir başlangıç tabakası biriktirilir. Bu, önceden belirlenmiş bir yolu izleyen ekstrüder kafası tarafından gerçekleştirilir. İlk katmandan sonra tabla indirilir ve sonraki katmanlar üst üste bırakılır. Bazen karmaşık bir parça üretirken, biriktirmenin belirli yönlerde devam edebilmesi için destek yapılarına ihtiyaç duyulur. Bu durumlarda, bir destek malzemesi, model malzemeden daha zayıf olacak şekilde bir katman üzerinde daha az yoğun bir filaman aralığı ile ekstrüde edilir. Bu destek yapıları daha sonra parçanın tamamlanmasından sonra çözülebilir veya kırılabilir. Ekstrüder kalıbı boyutları, ekstrüde edilmiş katmanların kalınlığını belirler. FDM işlemi, eğik dış düzlemlerde kademeli yüzeylere sahip parçalar üretir. Bu pürüzlülük kabul edilemez ise, bunları düzeltmek için kimyasal buharlı polisaj veya ısıtılmış bir alet kullanılabilir. Bu adımları ortadan kaldırmak ve makul geometrik toleransları elde etmek için bir kaplama malzemesi olarak bir cila mumu bile mevcuttur.
• SEÇİCİ LAZER SİNTERLEME : SLS olarak da adlandırılan işlem, polimer, seramik veya metalik tozların seçici olarak bir nesneye sinterlenmesine dayanır. İşleme odasının alt kısmında iki silindir bulunur: Kısmi yapılı bir silindir ve bir toz besleme silindiri. İlki, sinterlenmiş parçanın oluşturulduğu yere aşamalı olarak indirilir ve ikincisi, bir silindir mekanizması aracılığıyla parça yapılı silindire toz tedarik etmek için aşamalı olarak yükseltilir. Önce parça yapılı silindirde ince bir toz tabakası biriktirilir, ardından bir lazer ışını bu tabakaya odaklanır, belirli bir enine kesiti izler ve eritir/sinterler ve ardından bir katı halinde yeniden katılaşır. Toz, lazer ışını tarafından vurulmayan alanlar gevşek kalır ancak yine de katı kısmı destekler. Daha sonra başka bir toz tabakası biriktirilir ve parçayı elde etmek için işlem birçok kez tekrarlanır. Sonunda, gevşek toz parçacıkları çalkalanır. Tüm bunlar, üretilen parçanın 3D CAD programı tarafından oluşturulan talimatlar kullanılarak bir süreç kontrol bilgisayarı tarafından gerçekleştirilir. Uygun polimer bağlayıcılarla polimerler (ABS, PVC, polyester gibi), mum, metaller ve seramikler gibi çeşitli malzemeler biriktirilebilir.
• ELECTRON-BEAM MELTING : Seçici lazer sinterlemeye benzer, ancak vakumda prototip yapmak için titanyum veya kobalt krom tozlarını eritmek için elektron ışını kullanılır. Paslanmaz çelikler, alüminyum ve bakır alaşımları üzerinde bu işlemi gerçekleştirmek için bazı geliştirmeler yapılmıştır. Üretilen parçaların yorulma dayanımının arttırılması gerekiyorsa, ikincil işlem olarak parça imalatının ardından sıcak izostatik pres kullanıyoruz.
• ÜÇ BOYUTLU BASKI : Yine 3DP ile gösterilir, bu teknikte bir yazıcı kafası, metalik olmayan veya metalik bir toz tabakası üzerine inorganik bir bağlayıcı bırakır. Toz yatağını taşıyan bir piston kademeli olarak alçaltılır ve her adımda bağlayıcı katman katman biriktirilir ve bağlayıcı tarafından kaynaştırılır. Kullanılan toz malzemeler polimer karışımları ve lifleri, döküm kumu, metallerdir. Farklı bağlayıcı kafaları ve farklı renk bağlayıcıları aynı anda kullanarak çeşitli renkler elde edebiliriz. İşlem mürekkep püskürtmeli baskıya benzer, ancak renkli bir tabaka elde etmek yerine renkli üç boyutlu bir nesne elde ederiz. Üretilen parçalar gözenekli olabilir ve bu nedenle yoğunluğunu ve mukavemetini arttırmak için sinterleme ve metal infiltrasyonu gerektirebilir. Sinterleme bağlayıcıyı yakacak ve metal tozlarını birbirine kaynatacaktır. Parçaları yapmak için paslanmaz çelik, alüminyum, titanyum gibi metaller kullanılabilir ve sızma malzemeleri olarak yaygın olarak bakır ve bronz kullanırız. Bu tekniğin güzelliği, karmaşık ve hareketli montajların bile çok hızlı bir şekilde üretilebilmesidir. Örneğin bir dişli takımı, bir alet olarak bir anahtar yapılabilir ve kullanıma hazır hareketli ve döner parçalara sahip olacaktır. Montajın farklı bileşenleri farklı renklerde ve hepsi bir arada üretilebilir. Broşürümüzü indirin:Metal 3D Baskı Temelleri
• DOĞRUDAN ÜRETİM ve HIZLI TAKIM: Tasarım değerlendirmesi, sorun gidermenin yanı sıra, ürünlerin doğrudan üretimi veya ürünlere doğrudan uygulanması için hızlı prototipleme kullanıyoruz. Başka bir deyişle, hızlı prototipleme, onları daha iyi ve daha rekabetçi hale getirmek için geleneksel süreçlere dahil edilebilir. Örneğin, hızlı prototipleme, desenler ve kalıplar üretebilir. Hızlı prototipleme operasyonları ile oluşturulan bir eriyen ve yanan polimerin kalıpları, hassas döküm için birleştirilebilir ve yatırım yapılabilir. Bahsedilecek başka bir örnek, seramik döküm kabuk üretmek için 3DP kullanmak ve bunu kabuk döküm işlemleri için kullanmaktır. Enjeksiyon kalıpları ve kalıp ekleri bile hızlı prototipleme ile üretilebilir ve kalıp yapım süresinden haftalar veya aylarca tasarruf edilebilir. Sadece istenilen parçanın CAD dosyasını analiz ederek, yazılım kullanarak takım geometrisini üretebiliriz. İşte popüler hızlı takımlama yöntemlerimizden bazıları:
RTV (Oda Sıcaklığında Vulkanizasyon) KALIPLAMA / ÜRETAN DÖKÜM : İstenilen parçanın kalıbını yapmak için hızlı prototipleme kullanılarak kullanılabilir. Daha sonra bu kalıp bir ayırma maddesi ile kaplanır ve kalıp yarımlarını oluşturmak için kalıbın üzerine sıvı RTV kauçuğu dökülür. Daha sonra, bu kalıp yarımları sıvı üretanların enjeksiyon kalıbı için kullanılır. Kalıp ömrü kısadır, yalnızca 0 veya 30 döngü gibi ancak küçük parti üretimi için yeterlidir.
ACES (Acetal Clear Epoxy Solid) ENJEKSİYON KALIPLAMA : Stereolitografi gibi hızlı prototipleme tekniklerini kullanarak enjeksiyon kalıpları üretmekteyiz. Bu kalıplar, epoksi, alüminyum dolgulu epoksi veya metaller gibi malzemelerle doldurmaya izin veren açık uçlu kabuklardır. Yine kalıp ömrü onlarca veya maksimum yüzlerce parça ile sınırlıdır.
PÜSKÜRTME METAL TAKIM PROSESİ : Hızlı prototipleme yaparak kalıp yapıyoruz. Desen yüzeyine çinko-alüminyum alaşımı püskürtüp kaplıyoruz. Metal kaplamalı desen daha sonra bir şişenin içine yerleştirilir ve bir epoksi veya alüminyum dolgulu epoksi ile kaplanır. Son olarak, çıkarılır ve bu tür iki yarım kalıp üreterek enjeksiyon kalıplama için eksiksiz bir kalıp elde ederiz. Bu kalıplar daha uzun ömürlüdür, bazı durumlarda malzeme ve sıcaklıklara bağlı olarak binlerce parça üretebilirler.
KEELTOOL PROSESİ : Bu teknikle 100.000 ila 10 Milyon çevrim ömrüne sahip kalıplar üretilebilir. Hızlı prototipleme kullanarak bir RTV kalıbı üretiyoruz. Kalıp daha sonra A6 takım çeliği tozu, tungsten karbür, polimer bağlayıcıdan oluşan bir karışımla doldurulur ve kürlenmeye bırakılır. Bu kalıp daha sonra polimerin yanması ve metal tozlarının kaynaşması için ısıtılır. Bir sonraki adım, son kalıbı üretmek için bakır sızmasıdır. Gerekirse daha iyi boyutsal doğruluklar için kalıp üzerinde talaşlı imalat ve polisaj gibi ikincil işlemler yapılabilir.