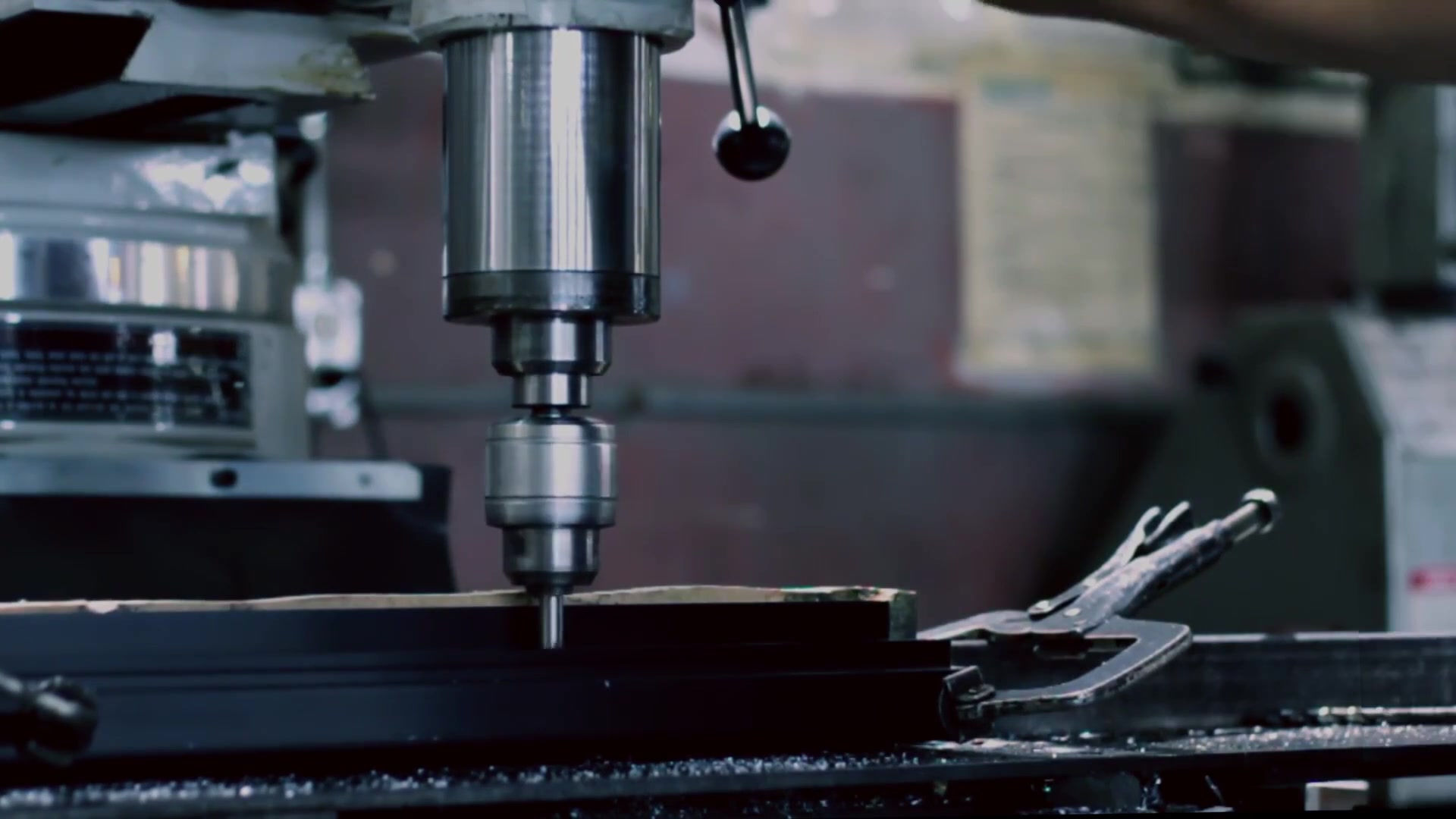
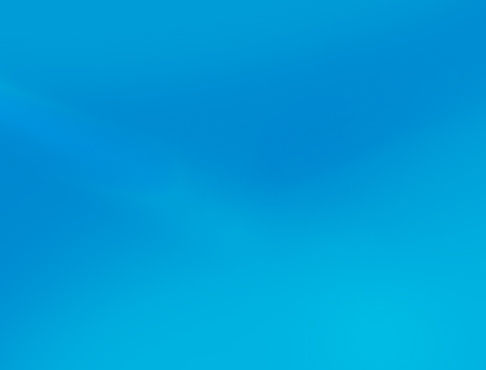
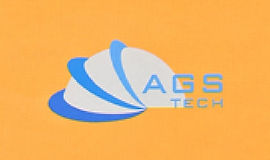
Çok Çeşitli Ürün ve Hizmetler için Küresel Özel Fason Üretici, Entegratör, Montaj Tedarikçisi, Global Imalat Ortağı.
Özel imal edilmiş ve kullanıma hazır fason ürün imalatı ve hizmetlerin tedariği, mühendisliği, konsolidasyonu, entegrasyonu, küresel fason üretim için tek durak kaynağınız biziz.
Choose your Language
-
Özel İmalatlar
-
Yerli & Global Fason Üretim
-
İmalat Dış Kaynak Kullanımı
-
Yurtiçi ve Küresel Tedarik
-
Konsolidasyon
-
Mühendislik Entegrasyonu
-
Mühendislik Hizmetleri
İmalatta kullandığımız birçok BİRLEŞTİRME tekniği arasında KAYNAKLAMA, LEHİM, LEHİM, YAPIŞTIRICI BAĞLAMA ve ÖZEL MEKANİK MONTAJ konularına özel önem verilmektedir, çünkü bu teknikler hermetik tertibatların imalatı, yüksek teknoloji ürünü üretim ve özel sızdırmazlık gibi uygulamalarda yaygın olarak kullanılmaktadır. Burada, bu birleştirme tekniklerinin gelişmiş ürün ve montajların imalatıyla ilgili olduğu için daha özel yönlerine odaklanacağız.
FÜZYON KAYNAK: Malzemeleri eritmek ve birleştirmek için ısı kullanıyoruz. Isı, elektrik veya yüksek enerjili ışınlarla sağlanır. Kullandığımız ergitme kaynağı türleri OKSİYAKIT GAZ KAYNAĞI, ARK KAYNAĞI, YÜKSEK ENERJİLİ KİRİŞ KAYNAĞIDIR.
KATI HAL KAYNAK: Parçaları eritmeden ve ergitmeden birleştiriyoruz. Katı hal kaynak yöntemlerimiz SOĞUK, ULTRASONİK, DİRENÇ, SÜRTÜNME, PATLAMALI KAYNAK ve DİFÜZYON BAĞLAMASI'dır.
LEHİM VE LEHİM: Dolgu metalleri kullanırlar ve bize kaynaktan daha düşük sıcaklıklarda çalışma avantajı sağlarlar, böylece ürünlere daha az yapısal hasar verirler. Seramikten metale bağlantı parçaları, hermetik sızdırmazlık, vakumlu geçişler, yüksek ve ultra yüksek vakum ve sıvı kontrol bileşenleri üreten lehimleme tesisimiz hakkında bilgiler burada bulunabilir:Lehimleme Fabrikası Broşürü
YAPIŞTIRICI YAPIŞTIRMA: Endüstride kullanılan yapıştırıcıların çeşitliliği ve uygulama çeşitliliği nedeniyle bunun için ayrılmış bir sayfamız var. Yapıştırıcı yapıştırma ile ilgili sayfamıza gitmek için lütfen tıklayınız.
ÖZEL MEKANİK MONTAJ: Cıvata, vida, somun, perçin gibi çeşitli bağlantı elemanları kullanıyoruz. Bağlantı elemanlarımız standart raf bağlantı elemanları ile sınırlı değildir. Özel uygulamalar için gereksinimleri karşılayabilmeleri için standart olmayan malzemelerden yapılmış özel bağlantı elemanları tasarlıyor, geliştiriyor ve üretiyoruz. Bazen elektriksel veya ısı iletkenliği olmaması istenirken bazen de iletkenlik istenmektedir. Bazı özel uygulamalar için müşteri, ürüne zarar vermeden çıkarılamayan özel bağlantı elemanları isteyebilir. Sonsuz fikir ve uygulamalar var. Sizin için her şeye sahibiz, kullanıma hazır değilse de hızla geliştirebiliriz. Mekanik montaj sayfamıza gitmek için lütfen tıklayınız.. Çeşitli birleştirme tekniklerimizi daha detaylı inceleyelim.
OKSİYAKIT GAZ KAYNAĞI (OFW): Kaynak alevini üretmek için oksijenle karıştırılmış bir yakıt gazı kullanıyoruz. Yakıt ve oksijen olarak asetilen kullandığımızda buna oksiasetilen gaz kaynağı diyoruz. Oksiyakıt gaz yakma işleminde iki kimyasal reaksiyon meydana gelir:
C2H2 + O2 ------» 2CO + H2 + Isı
2CO + H2 + 1.5 O2 --------» 2 CO2 + H2O + Isı
İlk reaksiyon, üretilen toplam ısının yaklaşık %33'ünü üretirken asetileni karbon monoksit ve hidrojene ayrıştırır. Yukarıdaki ikinci işlem, toplam ısının yaklaşık %67'sini üretirken hidrojen ve karbon monoksitin daha fazla yanmasını temsil eder. Alevdeki sıcaklıklar 1533 ila 3573 Kelvin arasındadır. Gaz karışımındaki oksijen yüzdesi önemlidir. Oksijen içeriği yarıdan fazlaysa, alev oksitleyici bir madde haline gelir. Bu, bazı metaller için istenmeyen bir durumdur, ancak diğerleri için arzu edilir. Oksitleyici alev istendiğinde bir örnek, metal üzerinde bir pasivasyon tabakası oluşturduğu için bakır bazlı alaşımlardır. Öte yandan, oksijen içeriği azaldığında tam yanma mümkün değildir ve alev, indirgeyici (karbürleyici) bir alev haline gelir. Bir indirgeyici alevdeki sıcaklıklar daha düşüktür ve bu nedenle lehimleme ve sert lehimleme gibi işlemler için uygundur. Diğer gazlar da potansiyel yakıtlardır, ancak asetilene göre bazı dezavantajları vardır. Bazen kaynak bölgesine dolgu çubukları veya tel şeklinde dolgu metalleri tedarik ediyoruz. Bazıları yüzeylerin oksidasyonunu geciktirmek ve böylece erimiş metali korumak için akı ile kaplanmıştır. Akının bize sağladığı ek bir fayda, kaynak bölgesinden oksitlerin ve diğer maddelerin uzaklaştırılmasıdır. Bu daha güçlü bağlanmaya yol açar. Oksiyakıt gaz kaynağının bir varyasyonu, iki bileşenin ara yüzeylerinde oksiasetilen gazlı torç kullanılarak ısıtıldığı ve arayüz erimeye başladığında torç geri çekildiği ve iki parçayı birbirine bastırmak için eksenel bir kuvvet uygulandığı BASINÇ GAZ KAYNAĞIDIR. Arayüz katılaşana kadar.
ARK KAYNAĞI: Elektrot ucu ile kaynak yapılacak parçalar arasında bir ark oluşturmak için elektrik enerjisi kullanıyoruz. Elektrotlar tüketilebilir veya tüketilemezken güç kaynağı AC veya DC olabilir. Ark kaynağında ısı transferi aşağıdaki denklem ile ifade edilebilir:
H / l = eski VI / v
Burada H ısı girdisi, l kaynak uzunluğu, V ve I uygulanan voltaj ve akım, v kaynak hızı ve e proses verimliliğidir. Verimlilik “e” ne kadar yüksek olursa, malzemeyi eritmek için mevcut enerji o kadar faydalı olur. Isı girdisi şu şekilde de ifade edilebilir:
H = ux (Hacim) = ux A xl
Burada u, erime için özgül enerji, A kaynağın kesiti ve l kaynak uzunluğudur. Yukarıdaki iki denklemden şunu elde edebiliriz:
v = eski VI / u A
Ark kaynağının bir varyasyonu, tüm endüstriyel ve bakım kaynak işlemlerinin yaklaşık %50'sini oluşturan KORUMALI METAL ARK KAYNAĞI (SMAW)'dır. ELEKTRİK ARKI KAYNAĞI (STICK KAYNAK), kaplanmış bir elektrotun ucunu iş parçasına değdirerek ve arkı korumak için yeterli bir mesafeye hızla geri çekerek gerçekleştirilir. Elektrotlar ince ve uzun çubuklar olduğu için bu işleme stik kaynak da diyoruz. Kaynak işlemi sırasında, elektrotun ucu, kaplaması ve ark çevresindeki ana metal ile birlikte erir. Ana metal, elektrot metali ve elektrot kaplamasındaki maddelerin bir karışımı kaynak bölgesinde katılaşır. Elektrodun kaplaması oksijeni giderir ve kaynak bölgesinde koruyucu bir gaz sağlar, böylece onu ortamdaki oksijenden korur. Bu nedenle proses korumalı metal ark kaynağı olarak adlandırılır. Optimum kaynak performansı için 50 ila 300 Amper arasında akımlar ve genellikle 10 kW'dan düşük güç seviyeleri kullanıyoruz. Ayrıca DC akımının polaritesi de önemlidir (akımın akış yönü). İş parçasının pozitif ve elektrotun negatif olduğu düz polarite, sığ penetrasyonundan dolayı sacların kaynağında ve ayrıca çok geniş boşluklu birleşimlerde tercih edilir. Ters polariteye sahip olduğumuzda, yani elektrot pozitif ve iş parçası negatif olduğunda daha derin kaynak penetrasyonları elde edebiliriz. AC akımı ile, titreşimli arklara sahip olduğumuz için, büyük çaplı elektrotlar ve maksimum akımlar kullanarak kalın bölümleri kaynaklayabiliriz. SMAW kaynak yöntemi, çoklu geçiş teknikleri kullanılarak 3 ila 19 mm ve daha fazla iş parçası kalınlıkları için uygundur. Kaynak bölgesinde korozyon ve bozulma olmaması için kaynağın üst kısmında oluşan cürufun tel fırça ile temizlenmesi gerekir. Bu elbette korumalı metal ark kaynağının maliyetine katkıda bulunur. Yine de SMAW, endüstride ve onarım işlerinde en popüler kaynak tekniğidir.
DALDIRILMIŞ ARK KAYNAĞI (TESTERE): Bu işlemde kaynak arkını kireç, silika, kalsiyum florür, manganez oksit….vb. Granül akı, bir memeden yerçekimi akışıyla kaynak bölgesine beslenir. Erimiş kaynak bölgesini kaplayan akı, kıvılcımlardan, dumanlardan, UV radyasyonundan vb. önemli ölçüde korur ve bir termal yalıtkan görevi görür, böylece ısının iş parçasının derinliklerine nüfuz etmesine izin verir. Kaynaştırılmamış akı geri kazanılır, işlenir ve yeniden kullanılır. Elektrot olarak çıplak bir bobin kullanılır ve bir borudan kaynak alanına beslenir. 300 ile 2000 Amper arasında akımlar kullanıyoruz. Tozaltı ark kaynağı (SAW) işlemi, kaynak sırasında dairesel yapının (boru gibi) dönüşü mümkünse, yatay ve düz konumlar ve dairesel kaynaklarla sınırlıdır. Hızlar 5 m/dk'ya ulaşabilir. SAW işlemi kalın levhalar için uygundur ve yüksek kaliteli, sağlam, sünek ve tek tip kaynaklarla sonuçlanır. Verimlilik, yani saatte biriken kaynak malzemesi miktarı, SMAW işlemine kıyasla miktarın 4 ila 10 katıdır.
GAZ METAL ARK KAYNAĞI (GMAW) veya alternatif olarak METAL ATIL GAZ KAYNAĞI (MIG) olarak adlandırılan diğer bir ark kaynağı işlemi, helyum, argon, karbon dioksit vb. gibi harici gaz kaynakları tarafından korunan kaynak alanına dayanır. Elektrot metalinde ek oksijen giderici maddeler bulunabilir. Sarf malzemesi teli, bir memeden kaynak bölgesine beslenir. Bot demirli ve demir dışı metalleri içeren imalat, gaz metal ark kaynağı (GMAW) kullanılarak gerçekleştirilir. Kaynak verimliliği, SMAW işleminin yaklaşık 2 katıdır. Otomatik kaynak ekipmanı kullanılmaktadır. Metal bu süreçte üç yoldan biriyle aktarılır: “Sprey Transferi” elektrottan kaynak alanına saniyede birkaç yüz küçük metal damlacığının transferini içerir. “Globüler Transfer”de ise karbondioksitçe zengin gazlar kullanılır ve ergimiş metal kürecikleri elektrik arkıyla itilir. Kaynak akımları yüksektir ve kaynak penetrasyonu daha derindir, kaynak hızı sprey transferinden daha yüksektir. Bu nedenle, daha ağır bölümlerin kaynağı için küresel transfer daha iyidir. Son olarak, “Kısa Devre” yönteminde, elektrot ucu erimiş kaynak havuzuna dokunur, metal olarak kısa devre yaparak 50 damla/saniyenin üzerindeki hızlarda ayrı damlacıklar halinde aktarılır. Daha ince tel ile birlikte düşük akım ve gerilimler kullanılır. Kullanılan güçler yaklaşık 2 kW ve sıcaklıklar nispeten düşüktür, bu da bu yöntemi 6 mm'den daha ince levhalar için uygun hale getirir.
KAYNAKLI ARK KAYNAĞI (FCAW) işleminin bir başka varyasyonu, elektrotun akı ile doldurulmuş bir tüp olması dışında gaz metal ark kaynağına benzer. Özlü akı elektrotları kullanmanın avantajları, daha kararlı arklar üretmeleri, bize kaynak metallerinin özelliklerini iyileştirme fırsatı vermeleri, SMAW kaynağına kıyasla akısının daha az kırılgan ve esnek doğası, iyileştirilmiş kaynak konturları. Kendinden korumalı özlü elektrotlar, kaynak bölgesini atmosfere karşı koruyan malzemeler içerir. Yaklaşık 20 kW güç kullanıyoruz. GMAW süreci gibi, FCAW süreci de sürekli kaynak için süreçleri otomatikleştirme fırsatı sunar ve ekonomiktir. Akı çekirdeğine çeşitli alaşımlar eklenerek farklı kaynak metali kimyaları geliştirilebilir.
ELEKTROGAZ KAYNAĞI'nda (EGW) kenar uca yerleştirilmiş parçaları kaynatıyoruz. Bazen ALIN KAYNAĞI olarak da adlandırılır. Kaynak metali, birleştirilecek iki parça arasındaki bir kaynak boşluğuna konur. Alan, erimiş cürufun dışarı dökülmesini önlemek için su soğutmalı iki barajla çevrilidir. Barajlar mekanik tahriklerle yukarı doğru hareket ettirilir. İş parçası döndürülebildiğinde, boruların çevresel kaynağı için de elektrogaz kaynak tekniğini kullanabiliriz. Elektrotlar, sürekli bir ark tutmak için bir kanaldan beslenir. Akımlar 400 Amper veya 750 Amper civarında ve güç seviyeleri 20 kW civarında olabilir. Akı çekirdekli elektrottan veya harici kaynaktan kaynaklanan soy gazlar, koruma sağlar. 12 mm'den 75 mm'ye kadar kalınlıktaki çelikler, titanyum vb. metaller için elektrogaz kaynağı (EGW) kullanıyoruz. Teknik, büyük yapılar için iyi bir seçimdir.
Yine ELEKTROSLAG KAYNAĞI (ESW) adı verilen başka bir teknikte, elektrot ile iş parçasının altı arasında ark ateşlenir ve akı eklenir. Erimiş cüruf elektrot ucuna ulaştığında ark söner. Enerji, erimiş cürufun elektrik direnci yoluyla sürekli olarak sağlanır. Kalınlıkları 50 mm ile 900 mm arasında ve hatta daha yüksek olan plakaları kaynaklayabiliriz. Akımlar 600 Amper civarında, gerilimler ise 40 – 50 V arasındadır. Kaynak hızları 12 ila 36 mm/dk civarındadır. Uygulamalar elektrogaz kaynağına benzer.
Sarf malzemesi olmayan elektrot proseslerimizden biri olan, TUNGSTEN INERT GAZ KAYNAĞI (TIG) olarak da bilinen GAZ TUNGSTEN ARK KAYNAĞI (GTAW), bir tel ile bir dolgu metali beslemesini içerir. Sıkı geçmeli bağlantılar için bazen dolgu metali kullanmayız. TIG işleminde akı kullanmıyoruz, ekranlama için argon ve helyum kullanıyoruz. Tungsten yüksek bir erime noktasına sahiptir ve TIG kaynak işleminde tüketilmez, bu nedenle sabit akım ve ark boşlukları korunabilir. Güç seviyeleri 8 ila 20 kW arasındadır ve akımlar 200 Amper (DC) veya 500 Amper (AC) değerindedir. Alüminyum ve magnezyum için oksit temizleme işlevi için AC akımı kullanıyoruz. Tungsten elektrotun kirlenmesini önlemek için erimiş metallerle temasından kaçınıyoruz. Gaz Tungsten Ark Kaynağı (GTAW), özellikle ince metallerin kaynağı için kullanışlıdır. GTAW kaynakları, iyi yüzey kalitesi ile çok yüksek kalitededir.
Hidrojen gazının daha yüksek maliyeti nedeniyle, daha az kullanılan bir teknik, akan hidrojen gazının koruyucu bir atmosferinde iki tungsten elektrot arasında bir ark oluşturduğumuz ATOMİK HİDROJEN KAYNAĞIDIR (AHW). AHW aynı zamanda tüketilmeyen bir elektrot kaynak işlemidir. İki atomlu hidrojen gazı H2, sıcaklıkların 6273 Kelvin'in üzerinde olduğu kaynak arkının yakınında atomik biçimine ayrılır. Parçalanırken arktan büyük miktarda ısı emer. Hidrojen atomları, nispeten soğuk bir yüzey olan kaynak bölgesine çarptığında, iki atomlu formda yeniden birleşir ve depolanan ısıyı serbest bırakır. Enerji, iş parçasının ark mesafesine değiştirilmesiyle değiştirilebilir.
Başka bir sarf malzemesi olmayan elektrot işleminde, PLAZMA ARK KAYNAĞI (PAW), kaynak bölgesine doğru yönlendirilmiş konsantre bir plazma arkımız vardır. Sıcaklıklar PAW'da 33.273 Kelvin'e ulaşıyor. Neredeyse eşit sayıda elektron ve iyon plazma gazını oluşturur. Düşük akımlı bir pilot ark, tungsten elektrot ile delik arasındaki plazmayı başlatır. Çalışma akımları genellikle 100 Amper civarındadır. Bir dolgu metali beslenebilir. Plazma ark kaynağında, koruma, bir dış koruma halkası ve argon ve helyum gibi gazlar kullanılarak gerçekleştirilir. Plazma ark kaynağında ark elektrot ile iş parçası arasında veya elektrot ile meme arasında olabilir. Bu kaynak tekniği, daha yüksek enerji konsantrasyonu, daha derin ve daha dar kaynak kabiliyeti, daha iyi ark kararlılığı, 1 metre/dk'ya kadar daha yüksek kaynak hızları, daha az termal bozulma gibi diğer yöntemlere göre avantajlara sahiptir. Genellikle 6 mm'den az ve bazen alüminyum ve titanyum için 20 mm'ye kadar olan kalınlıklar için plazma ark kaynağı kullanıyoruz.
YÜKSEK ENERJİLİ KİRİŞ KAYNAĞI: Elektron ışını kaynağı (EBW) ve lazer kaynağı (LBW) olmak üzere iki farklı füzyon kaynağı yöntemidir. Bu teknikler, yüksek teknoloji ürünü üretim çalışmalarımız için özellikle değerlidir. Elektron ışını kaynağında, yüksek hızlı elektronlar iş parçasına çarpar ve kinetik enerjileri ısıya dönüştürülür. Dar elektron demeti vakum odasında kolayca hareket eder. Genellikle e-kiriş kaynağında yüksek vakum kullanırız. 150 mm kalınlığa kadar olan levhalar kaynak yapılabilir. Koruyucu gaz, akı veya dolgu malzemesi gerekmez. Elektron ışın tabancaları 100 kW kapasiteye sahiptir. 30'a kadar yüksek en-boy oranlarına ve ısıdan etkilenen küçük bölgelere sahip derin ve dar kaynaklar mümkündür. Kaynak hızları 12 m/dk'ya ulaşabilir. Lazer ışını kaynağında ısı kaynağı olarak yüksek güçlü lazerler kullanıyoruz. Yüksek yoğunluklu 10 mikron kadar küçük lazer ışınları, iş parçasına derinlemesine nüfuz etmeyi sağlar. Lazer ışını kaynağı ile 10'a kadar derinlik-genişlik oranları mümkündür. Hem darbeli hem de sürekli dalga lazerleri kullanıyoruz, birincisi ince malzemeler için uygulamalarda ve ikincisi çoğunlukla yaklaşık 25 mm'ye kadar kalın iş parçaları için. Güç seviyeleri 100 kW'a kadardır. Lazer ışını kaynağı, optik olarak çok yansıtıcı malzemeler için pek uygun değildir. Kaynak işleminde gazlar da kullanılabilir. Lazer ışını kaynağı yöntemi, otomasyon ve yüksek hacimli üretim için çok uygundur ve 2,5 m/dak ile 80 m/dak arasında kaynak hızları sunabilir. Bu kaynak tekniğinin sunduğu önemli bir avantaj, diğer tekniklerin kullanılamadığı alanlara erişimdir. Lazer ışınları bu kadar zor bölgelere kolaylıkla seyahat edebilir. Elektron ışını kaynağında olduğu gibi vakum gerekmez. Lazer ışını kaynağı ile kaliteli ve mukavemetli, düşük büzülme, düşük distorsiyon, düşük poroziteye sahip kaynaklar elde edilebilir. Lazer ışınları, fiber optik kablolar kullanılarak kolayca manipüle edilebilir ve şekillendirilebilir. Bu nedenle teknik, hassas hermetik tertibatların, elektronik paketlerin vb. kaynaklanması için çok uygundur.
KATI HAL KAYNAK tekniklerimize bakalım. SOĞUK KAYNAK (CW), çiftleştirilen parçalara kalıp veya rulolar kullanılarak ısı yerine basıncın uygulandığı bir işlemdir. Soğuk kaynakta, eşleşen parçalardan en az birinin sünek olması gerekir. En iyi sonuçlar iki benzer malzeme ile elde edilir. Soğuk kaynakla birleştirilecek iki metal farklı ise, zayıf ve kırılgan bağlantılar elde edebiliriz. Soğuk kaynak yöntemi, elektrik bağlantıları, ısıya duyarlı kap kenarları, termostatlar için bimetal şeritler vb. gibi yumuşak, sünek ve küçük iş parçaları için çok uygundur. Soğuk kaynağın bir varyasyonu, basıncın bir çift rulo aracılığıyla uygulandığı rulo bağlamadır (veya rulo kaynağı). Bazen daha iyi arayüz mukavemeti için yüksek sıcaklıklarda rulo kaynağı yapıyoruz.
Kullandığımız diğer bir katı hal kaynak işlemi, iş parçalarının statik normal kuvvete ve salınımlı kesme gerilmelerine maruz kaldığı ULTRASONİK KAYNAK (USW) yöntemidir. Salınımlı kesme gerilmeleri, bir dönüştürücünün ucu aracılığıyla uygulanır. Ultrasonik kaynak, 10 ila 75 kHz frekanslı salınımları dağıtır. Dikiş kaynağı gibi bazı uygulamalarda uç olarak dönen bir kaynak diski kullanıyoruz. İş parçalarına uygulanan kesme gerilmeleri, küçük plastik deformasyonlara, oksit tabakalarının, kirleticilerin kırılmasına ve katı hal yapışmasına neden olur. Ultrasonik kaynakla ilgili sıcaklıklar, metaller için erime noktası sıcaklıklarının çok altındadır ve füzyon gerçekleşmez. Plastik gibi metalik olmayan malzemeler için sıklıkla ultrasonik kaynak (USW) işlemini kullanırız. Ancak termoplastiklerde sıcaklıklar erime noktalarına ulaşır.
Bir başka popüler teknik olan SÜRTÜNME KAYNAĞI'nda (FRW) ısı, birleştirilecek iş parçalarının arayüzünde sürtünme yoluyla üretilir. Sürtünme kaynağında iş parçalarından birini sabit tutarken, diğer iş parçası bir fikstürde tutulur ve sabit bir hızda döndürülür. İş parçaları daha sonra eksenel bir kuvvet altında temas ettirilir. Sürtünme kaynağında yüzey dönüş hızı bazı durumlarda 900m/dk'ya ulaşabilir. Yeterli arayüz temasından sonra dönen iş parçası ani bir duruşa getirilir ve eksenel kuvvet arttırılır. Kaynak bölgesi genellikle dar bir bölgedir. Sürtünme kaynağı tekniği, çeşitli malzemelerden yapılmış katı ve boru şeklindeki parçaları birleştirmek için kullanılabilir. FRW'de arayüzde bir miktar flaş oluşabilir, ancak bu flaş ikincil işleme veya taşlama ile kaldırılabilir. Sürtünme kaynağı işleminin varyasyonları mevcuttur. Örneğin, "atalet sürtünme kaynağı", parçaları kaynaklamak için dönme kinetik enerjisi kullanılan bir volanı içerir. Volan durduğunda kaynak tamamlanır. Dönen kütle ve dolayısıyla dönme kinetik enerjisi değiştirilebilir. Diğer bir varyasyon, birleştirilecek bileşenlerden en az birine doğrusal ileri geri hareketin uygulandığı “doğrusal sürtünme kaynağı”dır. Lineer sürtünme kaynağında parçaların dairesel olması gerekmez, dikdörtgen, kare veya başka şekillerde olabilirler. Frekanslar onlarca Hz, genlikler milimetre aralığında ve basınçlar onlarca veya yüzlerce MPa aralığında olabilir. Son olarak, "sürtünme karıştırma kaynağı" yukarıda açıklanan diğer ikisinden biraz farklıdır. Atalet sürtünme kaynağı ve lineer sürtünme kaynağında arayüzlerin ısıtılması, temas eden iki yüzeyin sürtünmesi ile sürtünme yoluyla sağlanırken, sürtünme karıştırma kaynağı yönteminde birleştirilecek iki yüzeye üçüncü bir gövde sürülür. 5 ila 6 mm çapında dönen bir alet mafsal ile temas ettirilir. Sıcaklıklar 503 ila 533 Kelvin arasındaki değerlere yükselebilir. Derzdeki malzemenin ısıtılması, karıştırılması ve karıştırılması gerçekleşir. Alüminyum, plastik ve kompozitler dahil olmak üzere çeşitli malzemeler üzerinde sürtünme karıştırma kaynağı kullanıyoruz. Kaynaklar üniform ve minimum gözenekli kalite yüksektir. Sürtünmeli karıştırma kaynağında duman veya sıçrama oluşmaz ve süreç iyi bir şekilde otomatikleştirilmiştir.
DİRENÇ KAYNAĞI (RW): Kaynak için gerekli ısı, birleştirilecek iki iş parçası arasındaki elektrik direnci ile üretilir. Direnç kaynağında akı, koruyucu gazlar veya sarf elektrotları kullanılmaz. Joule ısıtması direnç kaynağında gerçekleşir ve şu şekilde ifade edilebilir:
H = (I Kare) x R xtx K
H, joule (watt-saniye) cinsinden üretilen ısıdır, Amper cinsinden I akımı, Ohm cinsinden R direnci, t, akımın aktığı saniye cinsinden zamandır. K faktörü 1'den küçüktür ve radyasyon ve iletim yoluyla kaybolmayan enerji fraksiyonunu temsil eder. Direnç kaynağı işlemlerindeki akımlar 100.000 A'ya kadar çıkabilir, ancak voltajlar tipik olarak 0,5 ila 10 Volt'tur. Elektrotlar tipik olarak bakır alaşımlarından yapılır. Hem benzer hem de farklı malzemeler direnç kaynağı ile birleştirilebilir. Bu işlem için çeşitli varyasyonlar mevcuttur: "Direnç nokta kaynağı", iki levhanın bindirme bağlantısının yüzeyleriyle temas eden karşılıklı iki yuvarlak elektrot içerir. Akım kesilene kadar basınç uygulanır. Kaynak külçesinin çapı genellikle 10 mm'ye kadardır. Direnç nokta kaynağı, kaynak noktalarında hafif renksiz girinti izleri bırakır. Punta kaynağı, en popüler direnç kaynağı tekniğimizdir. Punta kaynağında zor bölgelere ulaşmak için çeşitli elektrot şekilleri kullanılmaktadır. Punta kaynak ekipmanımız CNC kontrollü olup, aynı anda kullanılabilen birden fazla elektrota sahiptir. Diğer bir varyasyon "direnç dikiş kaynağı", AC güç çevriminde akım yeterince yüksek bir seviyeye ulaştığında sürekli nokta kaynakları üreten tekerlek veya silindir elektrotlarla gerçekleştirilir. Direnç dikiş kaynağı ile üretilen bağlantılar sıvı ve gaz sızdırmazdır. İnce saclar için yaklaşık 1,5 m/dk'lık kaynak hızları normaldir. Aralıklı akımlar uygulanabilir, böylece dikiş boyunca istenen aralıklarla nokta kaynakları üretilebilir. “Direnç projeksiyon kaynağında”, kaynak yapılacak iş parçası yüzeylerinden birinde bir veya daha fazla çıkıntı (çukur) kabartıyoruz. Bu çıkıntılar yuvarlak veya oval olabilir. Eşleşen parça ile temas eden bu kabartmalı noktalarda yüksek yerel sıcaklıklara ulaşılır. Elektrotlar bu çıkıntıları sıkıştırmak için basınç uygular. Direnç projeksiyon kaynağındaki elektrotlar düz uçlara sahiptir ve su soğutmalı bakır alaşımlarıdır. Direnç projeksiyon kaynağının avantajı, tek strokta çok sayıda kaynak yapabilmemiz, dolayısıyla daha uzun elektrot ömrü, çeşitli kalınlıklarda sac kaynak yapabilme, somun ve cıvataları saclara kaynak yapabilme yeteneğimizdir. Direnç projeksiyon kaynağının dezavantajı, çukurları kabartmanın ek maliyetidir. Yine bir başka teknik, "flaş kaynak"ta, iki iş parçasının temas etmeye başlamasıyla uçlarındaki arktan ısı üretilir. Bu yöntem alternatif olarak ark kaynağı olarak da düşünülebilir. Ara yüzeydeki sıcaklık yükselir ve malzeme yumuşar. Eksenel bir kuvvet uygulanır ve yumuşatılmış bölgede bir kaynak oluşur. Flaş kaynak tamamlandıktan sonra, daha iyi görünüm için bağlantı işlenebilir. Flaş kaynak ile elde edilen kaynak kalitesi iyidir. Güç seviyeleri 10 ila 1500 kW arasındadır. Flaş kaynak, 75 mm çapa kadar benzer veya farklı metallerin ve 0,2 mm ila 25 mm kalınlıktaki sacların uçtan uca birleştirilmesi için uygundur. “Saplama ark kaynağı”, flaş kaynağına çok benzer. Cıvata veya dişli çubuk gibi saplama, plaka gibi bir iş parçasına birleştirilirken bir elektrot görevi görür. Üretilen ısıyı yoğunlaştırmak, oksidasyonu önlemek ve erimiş metali kaynak bölgesinde tutmak için bağlantının etrafına tek kullanımlık bir seramik halka yerleştirilir. Son olarak, başka bir direnç kaynağı işlemi olan “darbeli kaynak”, elektrik enerjisini sağlamak için bir kapasitör kullanır. Darbeli kaynakta, güç milisaniyeler içinde çok hızlı bir şekilde boşaltılır ve eklemde yüksek lokalize ısı oluşur. Vurmalı kaynak, bağlantı çevresindeki hassas elektronik bileşenlerin ısıtılmasından kaçınılması gereken elektronik imalat endüstrisinde yaygın olarak kullanıyoruz.
PATLAMA KAYNAĞI adı verilen bir teknik, birleştirilecek iş parçalarından birinin üzerine konan bir patlayıcı tabakasının patlatılmasını içerir. İş parçasına uygulanan çok yüksek basınç, türbülanslı ve dalgalı bir arayüz oluşturur ve mekanik kilitleme gerçekleşir. Patlayıcı kaynakta bağ kuvvetleri çok yüksektir. Patlama kaynağı, farklı metallerle plakaların kaplanması için iyi bir yöntemdir. Kaplamadan sonra, plakalar daha ince bölümler halinde yuvarlanabilir. Bazen boruları genişletmek için patlama kaynağı kullanırız, böylece levhaya sıkıca yalıtılırlar.
Katı hal birleştirme alanındaki son yöntemimiz DİFÜZYON BAĞLAMASI veya DİFÜZYON KAYNAĞI (DFW) olup, burada esas olarak atomların arayüz boyunca difüzyonu ile iyi bir bağlantı sağlanır. Arayüzdeki bazı plastik deformasyonlar da kaynağa katkıda bulunur. İlgili sıcaklıklar, Tm'nin metalin erime sıcaklığı olduğu yerde 0,5 Tm civarındadır. Difüzyon kaynağındaki bağ gücü, basınç, sıcaklık, temas süresi ve temas eden yüzeylerin temizliğine bağlıdır. Bazen arayüzde dolgu metalleri kullanırız. Difüzyon bağlamada ısı ve basınç gereklidir ve elektrik direnci veya fırın ve ölü ağırlıklar, pres veya başka bir şey tarafından sağlanır. Difüzyon kaynağı ile benzer ve farklı metaller birleştirilebilir. Atomların göç etmesi için geçen süre nedeniyle süreç nispeten yavaştır. DFW otomatikleştirilebilir ve havacılık, elektronik, tıp endüstrileri için karmaşık parçaların imalatında yaygın olarak kullanılır. Üretilen ürünler arasında ortopedik implantlar, sensörler, havacılık yapısal elemanları bulunur. Difüzyon yapıştırma, karmaşık sac metal yapılar üretmek için SÜPERPLASTİK ŞEKİLLENDİRME ile birleştirilebilir. Levhalar üzerinde seçilen yerler önce difüzyonla birleştirilir ve daha sonra bağlanmamış bölgeler hava basıncı kullanılarak bir kalıba genişletilir. Yüksek sertlik-ağırlık oranlarına sahip havacılık yapıları, bu yöntemlerin kombinasyonu kullanılarak üretilir. Difüzyon kaynağı / süper plastik şekillendirme kombine işlemi, bağlantı elemanlarına olan ihtiyacı ortadan kaldırarak gerekli parça sayısını azaltır, ekonomik olarak ve kısa teslim süreleri ile düşük gerilimli, son derece hassas parçalar sağlar.
LEHİMLEME: Lehimleme ve lehimleme teknikleri, kaynak için gerekli olandan daha düşük sıcaklıklar içerir. Bununla birlikte, lehimleme sıcaklıkları lehimleme sıcaklıklarından daha yüksektir. Sert lehimlemede, birleştirilecek yüzeyler arasına bir dolgu metali yerleştirilir ve sıcaklıklar, dolgu malzemesinin erime sıcaklığına 723 Kelvin'in üzerine, ancak iş parçalarının erime sıcaklıklarının altına yükseltilir. Erimiş metal, iş parçaları arasındaki sıkı oturan boşluğu doldurur. Dolgu metalinin soğutulması ve ardından katılaşması, güçlü bağlantılara neden olur. Sert lehim kaynağında dolgu metali bağlantı noktasında biriktirilir. Sert lehim kaynağında, sert lehimlemeye kıyasla önemli ölçüde daha fazla dolgu metali kullanılır. Sert lehim kaynağında dolgu metalini biriktirmek için oksitleyici alevli oksiasetilen torcu kullanılır. Lehimlemede daha düşük sıcaklıklar nedeniyle, ısıdan etkilenen bölgelerde eğilme ve artık gerilmeler gibi sorunlar daha azdır. Lehimlemede boşluk ne kadar küçük olursa, bağlantının kesme mukavemeti o kadar yüksek olur. Ancak maksimum çekme mukavemeti, optimum bir boşlukta (bir tepe değeri) elde edilir. Bu optimum değerin altında ve üstünde, sert lehimlemede çekme mukavemeti azalır. Lehimlemede tipik boşluklar 0,025 ile 0,2 mm arasında olabilir. Performans, toz, halka, tel, şerit…..vs gibi farklı şekillerde çeşitli lehim malzemeleri kullanıyoruz. ve bu performansları tasarımınız veya ürün geometriniz için özel olarak üretebilir. Ayrıca lehim malzemelerinin içeriğini de temel malzemelerinize ve uygulamanıza göre belirliyoruz. İstenmeyen oksit katmanlarını gidermek ve oksidasyonu önlemek için lehimleme işlemlerinde sıklıkla eritkenler kullanırız. Müteakip korozyonu önlemek için, birleştirme işleminden sonra akılar genellikle uzaklaştırılır. AGS-TECH Inc., aşağıdakiler de dahil olmak üzere çeşitli lehimleme yöntemleri kullanır:
- Torç Lehimleme
- Fırın Lehimleme
- İndüksiyonlu Lehimleme
- Direnç Lehimleme
- Daldırma Lehimleme
- Kızılötesi Lehimleme
- Difüzyon Lehimleme
- Yüksek Enerji Işını
Lehimli bağlantıların en yaygın örnekleri, karbür matkap uçları, uçlar, optoelektronik hermetik paketler, contalar gibi iyi mukavemete sahip farklı metallerden yapılır.
LEHİM : En sık kullanılan tekniklerimizden biri olan lehimin (dolgu metali) birbirine sıkı oturan bileşenler arasında lehimlemede olduğu gibi eklemi doldurduğu tekniklerden biridir. Lehimlerimiz 723 Kelvin'in altında erime noktalarına sahiptir. İmalat operasyonlarında hem manuel hem de otomatik lehimleme kullanıyoruz. Lehimleme ile karşılaştırıldığında, lehimleme sıcaklıkları daha düşüktür. Lehimleme, yüksek sıcaklık veya yüksek mukavemetli uygulamalar için çok uygun değildir. Lehimleme için kurşunsuz lehimler ile kalay-kurşun, kalay-çinko, kurşun-gümüş, kadmiyum-gümüş, çinko-alüminyum alaşımlarının yanı sıra diğer lehimler de kullanıyoruz. Lehimlemede eritici olarak hem aşındırıcı olmayan reçine bazlı hem de inorganik asitler ve tuzlar kullanılır. Düşük lehimlenebilirliğe sahip metalleri lehimlemek için özel eriticiler kullanıyoruz. Seramik malzemeleri, cam veya grafiti lehimlememiz gereken uygulamalarda, lehimlenebilirliği artırmak için önce parçaları uygun bir metalle kaplıyoruz. Popüler lehimleme tekniklerimiz şunlardır:
-Yeniden Akıtma veya Yapıştır Lehimleme
-Dalga Lehimleme
-Fırın Lehimleme
-Meşale Lehimleme
-İndüksiyon Lehimleme
-Demir Lehimleme
-Direnç Lehimleme
-Dip lehimleme
-Ultrasonik Lehimleme
-Kızılötesi Lehimleme
Ultrasonik lehimleme, birleştirilmekte olan yüzeylerden oksit filmlerini kaldıran ultrasonik kavitasyon etkisi sayesinde flux ihtiyacını ortadan kaldıran benzersiz bir avantaj sunar. Yeniden akış ve Dalga lehimleme, elektronikte yüksek hacimli üretim için endüstriyel olarak öne çıkan tekniklerimizdir ve bu nedenle daha ayrıntılı olarak açıklamaya değer. Yeniden akışlı lehimlemede, lehim metal parçacıkları içeren yarı katı macunlar kullanıyoruz. Macun, bir eleme veya şablonlama işlemi kullanılarak derz üzerine yerleştirilir. Baskılı devre kartlarında (PCB) bu tekniği sıklıkla kullanırız. Elektrikli bileşenler macundan bu pedlerin üzerine yerleştirildiğinde, yüzey gerilimi yüzeye monte paketleri hizalı tutar. Bileşenleri yerleştirdikten sonra, yeniden akış lehimlemenin gerçekleşmesi için montajı bir fırında ısıtıyoruz. Bu işlem sırasında pastadaki solventler buharlaşır, pastadaki flux aktive edilir, bileşenler önceden ısıtılır, lehim parçacıkları eritilir ve eklemi ıslatır ve son olarak PCB takımı yavaşça soğutulur. PCB panolarının yüksek hacimli üretimi için ikinci popüler tekniğimiz, yani dalga lehimleme, erimiş lehimlerin metal yüzeyleri ıslatmasına ve yalnızca metal önceden ısıtıldığında iyi bağlar oluşturmasına dayanır. Erimiş lehimin duran laminer dalgası önce bir pompa tarafından üretilir ve önceden ısıtılmış ve önceden akıtılmış PCB'ler dalga üzerinde taşınır. Lehim yalnızca açıkta kalan metal yüzeyleri ıslatır, ancak IC polimer paketlerini veya polimer kaplı devre kartlarını ıslatmaz. Yüksek hızlı bir sıcak su jeti, bağlantıdaki fazla lehimi üfler ve bitişik kablolar arasında köprü oluşmasını önler. Yüzeye monte paketlerin dalga lehimlemesinde, lehimlemeden önce bunları devre kartına yapıştırarak yapıştırıyoruz. Yine eleme ve şablonlama kullanılmış ancak bu sefer epoksi için. Bileşenler doğru yerlerine yerleştirildikten sonra epoksi kürlenir, levhalar ters çevrilir ve dalga lehimleme gerçekleşir.