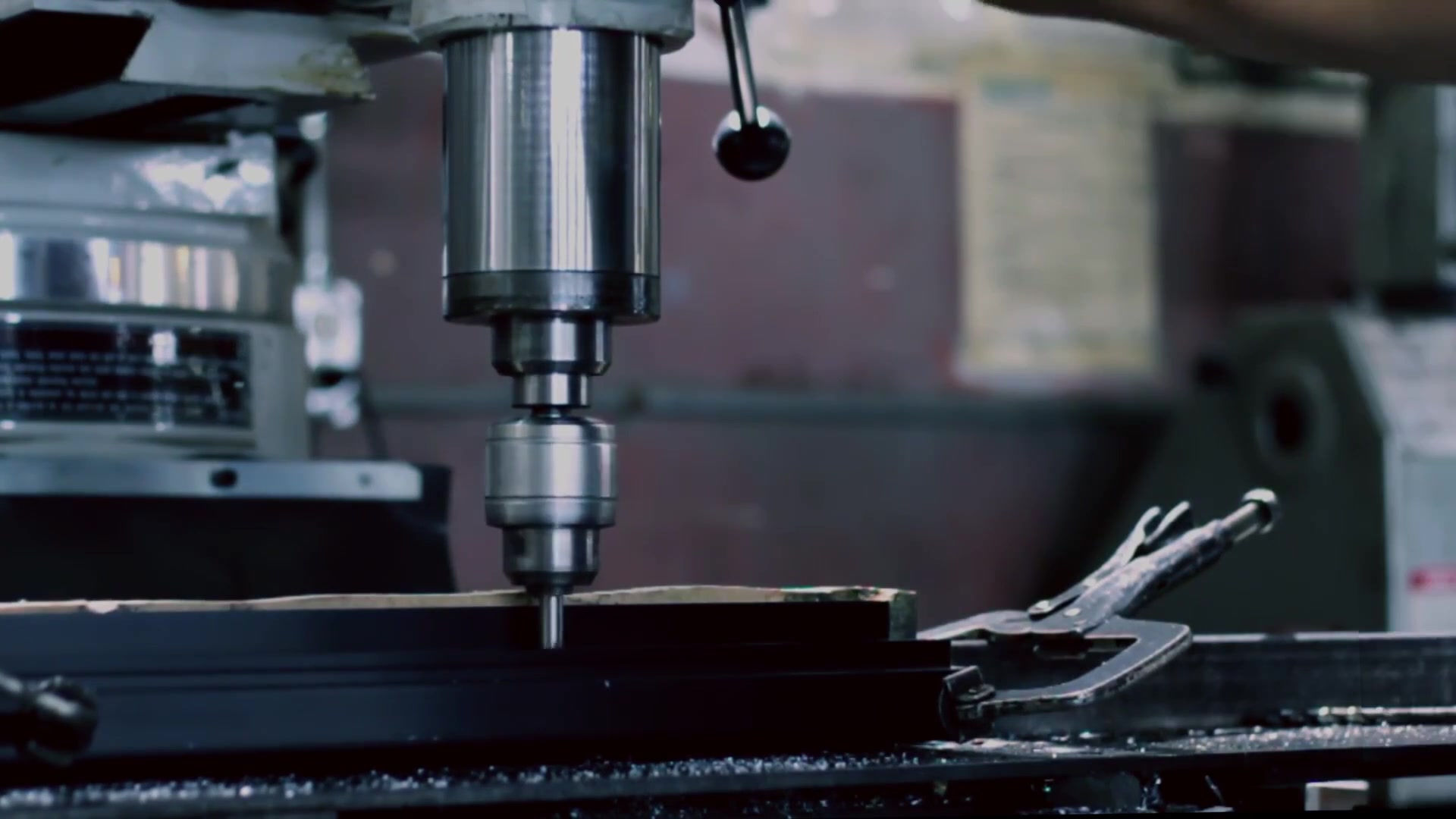
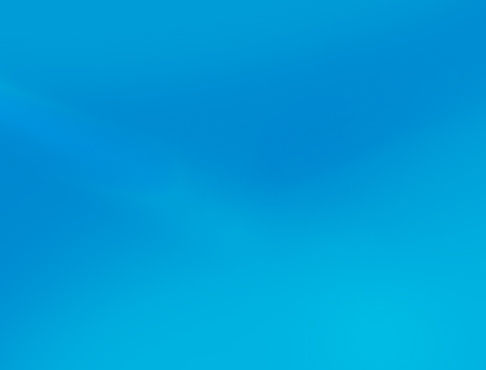
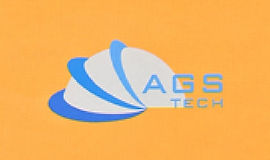
عالمی کسٹم مینوفیکچرر، انٹیگریٹر، کنسولیڈیٹر، مصنوعات اور خدمات کی وسیع اقسام کے لیے آؤٹ سورسنگ پارٹنر۔
ہم مینوفیکچرنگ، فیبریکیشن، انجینئرنگ، کنسولیڈیشن، انٹیگریشن، اپنی مرضی کے مطابق تیار کردہ اور آف شیلف پروڈکٹس اور خدمات کی آؤٹ سورسنگ کے لیے آپ کا واحد ذریعہ ہیں۔
Choose your Language
-
اپنی مرضی کے مطابق مینوفیکچرنگ
-
گھریلو اور عالمی کنٹریکٹ مینوفیکچرنگ
-
مینوفیکچرنگ آؤٹ سورسنگ
-
گھریلو اور عالمی خریداری
-
Consolidation
-
انجینئرنگ انٹیگریشن
-
انجینئرنگ سروسز
ہم جس قسم کے شیشے کی تیاری کی پیشکش کرتے ہیں وہ ہیں کنٹینر گلاس، گلاس اڑانے، گلاس فائبر اور نلیاں اور راڈ، گھریلو اور صنعتی شیشے کا سامان، لیمپ اور بلب، عین مطابق گلاس مولڈنگ، آپٹیکل پرزے اور اسمبلیاں، فلیٹ اور شیٹ اور فلوٹ گلاس۔ ہم ہاتھ بنانے کے ساتھ ساتھ مشین کی تشکیل بھی کرتے ہیں۔
ہمارے مشہور تکنیکی سیرامک مینوفیکچرنگ کے عمل میں ڈائی پریسنگ، آئسوسٹیٹک پریسنگ، ہاٹ آئسوسٹیٹک پریسنگ، ہاٹ پریسنگ، سلپ کاسٹنگ، ٹیپ کاسٹنگ، اخراج، انجکشن مولڈنگ، گرین مشیننگ، سنٹرنگ یا فائرنگ، ڈائمنڈ گرائنڈنگ، ہرمیٹک اسمبلیاں ہیں۔
ہمارا مشورہ ہے کہ آپ یہاں کلک کریں۔
AGS-TECH Inc کی طرف سے شیشے کی تشکیل اور تشکیل کے عمل کی ہماری اسکیمیٹک عکاسی ڈاؤن لوڈ کریں۔
AGS-TECH Inc کے ذریعے تکنیکی سیرامک مینوفیکچرنگ کے عمل کی ہماری اسکیمیٹک عکاسی ڈاؤن لوڈ کریں۔
تصاویر اور خاکوں کے ساتھ ڈاؤن لوڈ کے قابل یہ فائلیں آپ کو ان معلومات کو بہتر طور پر سمجھنے میں مدد کریں گی جو ہم آپ کو ذیل میں فراہم کر رہے ہیں۔
کنٹینر گلاس مینوفیکچر: ہم نے مینوفیکچرنگ کے لیے پریس اور بلو کے ساتھ ساتھ بلو اور بلو لائنز کو خودکار بنایا ہے۔ بلو اور بلو کے عمل میں ہم ایک گوب کو خالی سانچے میں ڈالتے ہیں اور اوپر سے کمپریسڈ ہوا کا ایک جھونکا لگا کر گردن بناتے ہیں۔ اس کے فوراً بعد، کمپریسڈ ہوا دوسری بار دوسری سمت سے کنٹینر کی گردن کے ذریعے اڑائی جاتی ہے تاکہ بوتل کی پری شکل بن سکے۔ اس پری فارم کو پھر اصل مولڈ میں منتقل کیا جاتا ہے، اسے نرم کرنے کے لیے دوبارہ گرم کیا جاتا ہے اور پری فارم کو اس کے آخری کنٹینر کی شکل دینے کے لیے کمپریسڈ ہوا لگائی جاتی ہے۔ مزید واضح طور پر، اس پر دباؤ ڈالا جاتا ہے اور اسے بلو مولڈ گہا کی دیواروں کے خلاف دھکیل دیا جاتا ہے تاکہ اس کی مطلوبہ شکل اختیار کی جا سکے۔ آخر میں، تیار کردہ شیشے کے کنٹینر کو بعد میں دوبارہ گرم کرنے اور مولڈنگ کے دوران پیدا ہونے والے دباؤ کو دور کرنے کے لیے اینیلنگ اوون میں منتقل کیا جاتا ہے اور اسے کنٹرول شدہ انداز میں ٹھنڈا کیا جاتا ہے۔ پریس اور بلو کے طریقہ کار میں، پگھلے ہوئے گوبس کو پیریسن مولڈ (خالی مولڈ) میں ڈالا جاتا ہے اور پیریسن شکل (خالی شکل) میں دبایا جاتا ہے۔ اس کے بعد خالی جگہوں کو بلو مولڈ میں منتقل کیا جاتا ہے اور "بلو اینڈ بلو پروسیس" کے تحت اوپر بیان کردہ عمل کی طرح اڑا دیا جاتا ہے۔ اینیلنگ اور تناؤ سے نجات جیسے بعد کے اقدامات ایک جیسے یا ایک جیسے ہیں۔
• گلاس اڑانا: ہم روایتی ہینڈ اڑانے کے ساتھ ساتھ خودکار آلات کے ساتھ کمپریسڈ ہوا کا استعمال کرتے ہوئے شیشے کی مصنوعات تیار کر رہے ہیں۔ کچھ آرڈرز کے لیے روایتی اڑانا ضروری ہوتا ہے، جیسے پراجیکٹس جن میں شیشے کا آرٹ ورک شامل ہوتا ہے، یا ایسے پروجیکٹس جن میں ڈھیلے برداشت والے حصوں کی ایک چھوٹی تعداد کی ضرورت ہوتی ہے، پروٹوٹائپنگ/ڈیمو پروجیکٹس.... وغیرہ۔ روایتی شیشے کو اڑانے میں کھوکھلی دھات کے پائپ کو پگھلے ہوئے شیشے کے برتن میں ڈبونا اور شیشے کے مواد کی کچھ مقدار جمع کرنے کے لیے پائپ کو گھمانا شامل ہے۔ پائپ کی نوک پر جمع ہونے والے شیشے کو فلیٹ لوہے پر لپیٹ دیا جاتا ہے، جس کی شکل مطلوبہ، لمبا، دوبارہ گرم اور ہوا سے اڑا دیا جاتا ہے۔ تیار ہونے پر اسے ایک سانچے میں ڈالا جاتا ہے اور ہوا اڑا دی جاتی ہے۔ دھات کے ساتھ شیشے کے رابطے سے بچنے کے لیے سڑنا گہا گیلا ہے۔ پانی کی فلم ان کے درمیان ایک کشن کی طرح کام کرتی ہے۔ دستی اڑانا ایک محنتی سست عمل ہے اور صرف پروٹو ٹائپنگ یا زیادہ قیمت والی اشیاء کے لیے موزوں ہے، سستے فی ٹکڑا ہائی والیوم آرڈرز کے لیے موزوں نہیں ہے۔
گھریلو اور صنعتی شیشے کے سامان کی مینوفیکچرنگ: مختلف قسم کے شیشے کے مواد کا استعمال کرتے ہوئے شیشے کے سامان کی ایک بڑی قسم تیار کی جا رہی ہے۔ کچھ شیشے گرمی سے بچنے والے اور لیبارٹری کے شیشے کے سامان کے لیے موزوں ہوتے ہیں جبکہ کچھ کئی بار ڈش واشرز کو برداشت کرنے کے لیے کافی اچھے ہوتے ہیں اور گھریلو مصنوعات بنانے کے لیے موزوں ہوتے ہیں۔ ویسٹ لیک مشینوں کے استعمال سے روزانہ پینے کے شیشے کے دسیوں ہزار ٹکڑے تیار کیے جا رہے ہیں۔ آسان بنانے کے لیے، پگھلے ہوئے شیشے کو ویکیوم کے ذریعے اکٹھا کیا جاتا ہے اور اسے پہلے کی شکلیں بنانے کے لیے سانچوں میں ڈالا جاتا ہے۔ پھر ہوا کو سانچوں میں اڑا دیا جاتا ہے، یہ دوسرے سانچے میں منتقل ہو جاتے ہیں اور ہوا دوبارہ اڑا دی جاتی ہے اور شیشہ اپنی آخری شکل اختیار کر لیتا ہے۔ ہاتھ سے اڑانے کی طرح، یہ سانچوں کو پانی سے گیلا رکھا جاتا ہے۔ مزید اسٹریچنگ فنشنگ آپریشن کا حصہ ہے جہاں گردن بن رہی ہے۔ اضافی شیشہ جل گیا ہے۔ اس کے بعد اوپر بیان کردہ کنٹرول شدہ ری ہیٹنگ اور کولنگ کا عمل مندرجہ ذیل ہے۔
شیشے کی ٹیوب اور چھڑی کی تشکیل: شیشے کی ٹیوبوں کی تیاری کے لیے جو اہم عمل ہم استعمال کرتے ہیں وہ ہیں DANNER اور VELLO کے عمل۔ ڈینر کے عمل میں، بھٹی سے شیشہ بہتا ہے اور ریفریکٹری مواد سے بنی مائل آستین پر گرتا ہے۔ آستین کو گھومنے والی کھوکھلی شافٹ یا بلو پائپ پر لے جایا جاتا ہے۔ اس کے بعد شیشے کو آستین کے گرد لپیٹ دیا جاتا ہے اور آستین کے نیچے اور شافٹ کی نوک پر بہتی ہوئی ایک ہموار تہہ بن جاتی ہے۔ ٹیوب بننے کی صورت میں، ہوا کو کھوکھلی نوک کے ساتھ بلو پائپ کے ذریعے اڑایا جاتا ہے، اور چھڑی بننے کی صورت میں ہم شافٹ پر ٹھوس ٹپس استعمال کرتے ہیں۔ اس کے بعد نلیاں یا سلاخیں لے جانے والے رولرس کے اوپر کھینچی جاتی ہیں۔ شیشے کی ٹیوبوں کی دیوار کی موٹائی اور قطر جیسے طول و عرض کو آستین کے قطر کو ترتیب دے کر اور ہوا کے دباؤ کو مطلوبہ قدر پر اڑا کر، درجہ حرارت، شیشے کے بہاؤ کی شرح اور ڈرائنگ کی رفتار کو ایڈجسٹ کر کے مطلوبہ اقدار کے مطابق کیا جاتا ہے۔ دوسری طرف ویلو گلاس ٹیوب مینوفیکچرنگ کے عمل میں شیشہ شامل ہوتا ہے جو بھٹی سے باہر اور کھوکھلی مینڈریل یا گھنٹی کے ساتھ پیالے میں جاتا ہے۔ شیشہ پھر مینڈریل اور پیالے کے درمیان ہوا کی جگہ سے گزرتا ہے اور ایک ٹیوب کی شکل اختیار کر لیتا ہے۔ اس کے بعد یہ رولرس کے اوپر سے ایک ڈرائنگ مشین تک جاتا ہے اور اسے ٹھنڈا کیا جاتا ہے۔ کولنگ لائن کے اختتام پر کٹنگ اور فائنل پروسیسنگ ہوتی ہے۔ ٹیوب کے طول و عرض کو ڈینر کے عمل کی طرح ایڈجسٹ کیا جاسکتا ہے۔ ڈینر کا ویلو پروسیس سے موازنہ کرتے وقت، ہم کہہ سکتے ہیں کہ ویلو پروسیس بڑی مقدار میں پیداوار کے لیے ایک بہتر فٹ ہے جب کہ ڈینر کا عمل درست چھوٹے والیوم ٹیوب آرڈرز کے لیے بہتر فٹ ہو سکتا ہے۔
• شیٹ اور فلیٹ اور فلوٹ شیشے کی پروسیسنگ: ہمارے پاس سب ملی میٹر موٹائی سے لے کر کئی سینٹی میٹر تک موٹائی میں فلیٹ شیشے کی بڑی مقدار ہے۔ ہمارے فلیٹ شیشے تقریبا آپٹیکل کمال کے ہیں۔ ہم خصوصی کوٹنگز کے ساتھ گلاس پیش کرتے ہیں جیسے آپٹیکل کوٹنگز، جہاں کیمیائی بخارات جمع کرنے کی تکنیک کا استعمال کوٹنگز جیسے اینٹی ریفلیکشن یا آئینے کی کوٹنگ کے لیے کیا جاتا ہے۔ اس کے علاوہ شفاف conductive ملعمع کاری عام ہیں. شیشے پر ہائیڈرو فوبک یا ہائیڈرو فیلک کوٹنگز بھی دستیاب ہیں، اور کوٹنگ جو شیشے کو خود سے صاف کرتی ہے۔ ٹیمپرڈ، بلٹ پروف اور پرتدار شیشے ابھی تک دیگر مقبول اشیاء ہیں۔ ہم نے شیشے کو مطلوبہ رواداری کے ساتھ مطلوبہ شکل میں کاٹ دیا۔ دیگر ثانوی آپریشنز جیسے مڑے ہوئے یا موڑنے والے فلیٹ گلاس دستیاب ہیں۔
• PRECISION GLASS MOLDING: ہم اس تکنیک کو زیادہ تر درست نظری اجزاء کی تیاری کے لیے استعمال کرتے ہیں بغیر زیادہ مہنگی اور وقت لینے والی تکنیک جیسے پیسنے، لیپنگ اور پالش کرنے کی ضرورت کے۔ یہ تکنیک ہمیشہ بہترین آپٹکس کو بہترین بنانے کے لیے کافی نہیں ہوتی، لیکن کچھ معاملات جیسے صارفین کی مصنوعات، ڈیجیٹل کیمرے، میڈیکل آپٹکس میں یہ اعلی حجم کی تیاری کے لیے ایک کم مہنگا اچھا اختیار ہو سکتا ہے۔ اس کے علاوہ اس کا شیشہ بنانے کی دوسری تکنیکوں پر ایک فائدہ ہے جہاں پیچیدہ جیومیٹریوں کی ضرورت ہوتی ہے، جیسے اسفیئرز کے معاملے میں۔ بنیادی عمل میں شیشے کے خالی حصے کے ساتھ ہمارے مولڈ کے نچلے حصے کو لوڈ کرنا، آکسیجن کو ہٹانے کے لیے پراسیس چیمبر کا انخلا، مولڈ کو بند کرنے کے قریب، ڈائی اور شیشے کو اورکت روشنی کے ساتھ تیز اور آئسو تھرمل گرم کرنا، مولڈ کے حصوں کو مزید بند کرنا شامل ہے۔ نرم شیشے کو آہستہ آہستہ کنٹرول انداز میں مطلوبہ موٹائی تک دبانے کے لیے، اور آخر میں شیشے کو ٹھنڈا کرنا اور چیمبر کو نائٹروجن سے بھرنا اور مصنوعات کو ہٹانا۔ درست درجہ حرارت کنٹرول، مولڈ بند کرنے کا فاصلہ، سڑنا بند کرنے کی قوت، مولڈ اور شیشے کے مواد کی توسیع کے گتانک کا ملاپ اس عمل میں کلیدی حیثیت رکھتا ہے۔
• شیشے کے آپٹیکل اجزاء اور اسمبلیوں کی تیاری: عین مطابق شیشے کی مولڈنگ کے علاوہ، بہت سے قیمتی عمل ہیں جو ہم اعلیٰ معیار کے آپٹیکل پرزہ جات بنانے کے لیے استعمال کرتے ہیں اور ایپلی کیشنز کی مانگ کے لیے اسمبلیاں بناتے ہیں۔ آپٹیکل گریڈ کے شیشوں کو باریک خاص کھرچنے والی سلریوں میں پیسنا، لیپ کرنا اور پالش کرنا آپٹیکل لینز، پرزم، فلیٹ وغیرہ بنانے کے لیے ایک فن اور سائنس ہے۔ سطح کی ہمواری، لہرائی، ہمواری اور خرابی سے پاک آپٹیکل سطحوں کو اس طرح کے عمل کے ساتھ بہت زیادہ تجربے کی ضرورت ہوتی ہے۔ ماحول میں چھوٹی تبدیلیوں کا نتیجہ تصریح کی مصنوعات سے باہر ہو سکتا ہے اور مینوفیکچرنگ لائن کو روک سکتا ہے۔ ایسے معاملات ہیں جہاں صاف کپڑے سے آپٹیکل سطح پر ایک ہی وائپ کسی پروڈکٹ کو تصریحات پر پورا اتر سکتا ہے یا ٹیسٹ میں ناکام ہو سکتا ہے۔ استعمال ہونے والے کچھ مشہور شیشے کے مواد میں فیوزڈ سلکا، کوارٹج، BK7 ہیں۔ نیز اس طرح کے اجزاء کی اسمبلی کے لیے مخصوص تجربہ کی ضرورت ہوتی ہے۔ بعض اوقات خصوصی گلوز کا استعمال کیا جاتا ہے۔ تاہم، بعض اوقات آپٹیکل کانٹیکٹنگ نامی تکنیک بہترین انتخاب ہوتی ہے اور اس میں منسلک آپٹیکل شیشوں کے درمیان کوئی مواد شامل نہیں ہوتا ہے۔ یہ بغیر کسی گلو کے ایک دوسرے سے منسلک ہونے کے لیے فلیٹ سطحوں سے جسمانی طور پر رابطہ کرنے پر مشتمل ہوتا ہے۔ بعض صورتوں میں مکینیکل اسپیسرز، عین مطابق شیشے کی سلاخیں یا گیندیں، کلیمپ یا مشینی دھاتی اجزاء آپٹیکل اجزاء کو مخصوص فاصلوں پر اور ایک دوسرے سے مخصوص جیومیٹرک واقفیت کے ساتھ جمع کرنے کے لیے استعمال کیے جا رہے ہیں۔ آئیے ہم ہائی اینڈ آپٹکس بنانے کے لیے اپنی کچھ مشہور تکنیکوں کا جائزہ لیتے ہیں۔
پیسنا اور لیپ کرنا اور پالش کرنا: آپٹیکل جزو کی کھردری شکل شیشے کو خالی پیسنے سے حاصل کی جاتی ہے۔ اس کے بعد آپٹیکل اجزاء کی کھردری سطحوں کو مطلوبہ سطح کی شکلوں والے ٹولز کے خلاف گھما کر اور رگڑ کر لیپنگ اور پالش کی جاتی ہے۔ آپٹکس اور شکل دینے والے ٹولز کے درمیان چھوٹے کھرچنے والے ذرات اور سیال کے ساتھ گارا ڈالا جا رہا ہے۔ اس طرح کے گارے میں کھرچنے والے ذرات کے سائز کو مطلوبہ ہمواری کی ڈگری کے مطابق منتخب کیا جا سکتا ہے۔ مطلوبہ شکلوں سے اہم آپٹیکل سطحوں کے انحراف کو استعمال ہونے والی روشنی کی طول موج کے لحاظ سے ظاہر کیا جاتا ہے۔ ہمارے اعلی درستگی والے آپٹکس میں طول موج کا دسواں حصہ (طول موج/10) رواداری ہے یا اس سے بھی زیادہ سخت ممکن ہے۔ سطحی پروفائل کے علاوہ، اہم سطحوں کو اسکین کیا جاتا ہے اور سطح کی دیگر خصوصیات اور نقائص جیسے کہ طول و عرض، خروںچ، چپس، گڑھے، دھبے وغیرہ کا جائزہ لیا جاتا ہے۔ آپٹیکل مینوفیکچرنگ فلور میں ماحولیاتی حالات پر سخت کنٹرول اور جدید ترین آلات کے ساتھ وسیع میٹرولوجی اور جانچ کی ضروریات اسے صنعت کی ایک چیلنجنگ شاخ بناتی ہیں۔
• گلاس مینوفیکچرنگ میں ثانوی عمل: ایک بار پھر، جب شیشے کے ثانوی اور تکمیلی عمل کی بات آتی ہے تو ہم صرف آپ کی تخیل تک محدود ہیں۔ یہاں ہم ان میں سے کچھ کی فہرست دیتے ہیں:
شیشے پر کوٹنگز (آپٹیکل، الیکٹریکل، ٹرائبلوجیکل، تھرمل، فنکشنل، مکینیکل...) مثال کے طور پر ہم شیشے کی سطح کی خصوصیات کو تبدیل کر سکتے ہیں جس سے یہ مثال کے طور پر گرمی کی عکاسی کرتا ہے تاکہ یہ عمارت کے اندرونی حصوں کو ٹھنڈا رکھے، یا نینو ٹیکنالوجی کا استعمال کرتے ہوئے ایک طرف اورکت کو جذب کر سکے۔ اس سے عمارتوں کے اندرونی حصے کو گرم رکھنے میں مدد ملتی ہے کیونکہ شیشے کی سب سے باہری سطح عمارت کے اندر انفراریڈ شعاعوں کو جذب کر کے اسے واپس اندر تک پھیر دے گی۔
-ایچنگ on گلاس
- اپلائیڈ سیرامک لیبلنگ (ACL)
- کندہ کاری
- شعلہ پالش کرنا
-کیمیکل پالش
- داغ لگانا
تکنیکی سیرامکس کی مینوفیکچرنگ
• ڈائی پریسنگ: ڈائی میں بند دانے دار پاؤڈر کے غیر محوری کمپیکشن پر مشتمل ہوتا ہے
• ہاٹ پریسنگ: ڈائی پریسنگ کی طرح لیکن کثافت کو بڑھانے کے لیے درجہ حرارت کے اضافے کے ساتھ۔ پاؤڈر یا کمپیکٹڈ پرفارم کو گریفائٹ ڈائی میں رکھا جاتا ہے اور غیر محوری دباؤ لگایا جاتا ہے جب کہ ڈائی کو اعلی درجہ حرارت جیسے 2000 C پر رکھا جاتا ہے۔ سیرامک پاؤڈر کی پروسیسنگ کی قسم کے لحاظ سے درجہ حرارت مختلف ہو سکتا ہے۔ پیچیدہ شکلوں اور جیومیٹریوں کے لیے بعد میں دیگر پروسیسنگ جیسے ہیرے کی پیسنے کی ضرورت ہو سکتی ہے۔
• آئی ایس او سٹیٹک پریسنگ: دانے دار پاؤڈر یا ڈائی پریسڈ کمپیکٹ کو ایئر ٹائٹ کنٹینرز میں اور پھر ایک بند پریشر برتن میں رکھا جاتا ہے جس کے اندر مائع ہوتا ہے۔ اس کے بعد وہ دباؤ والے برتن کے دباؤ کو بڑھا کر کمپیکٹ کیے جاتے ہیں۔ برتن کے اندر مائع دباؤ والی قوتوں کو یکساں طور پر ایئر ٹائٹ کنٹینر کے پورے سطحی علاقے پر منتقل کرتا ہے۔ اس طرح مواد کو یکساں طور پر کمپیکٹ کیا جاتا ہے اور اس کے لچکدار کنٹینر اور اس کے اندرونی پروفائل اور خصوصیات کی شکل اختیار کر لیتا ہے۔
• ہاٹ آئیسوسٹیٹک پریسنگ: آئسوسٹیٹک پریسنگ کی طرح، لیکن دباؤ والے گیس کے ماحول کے علاوہ، ہم اعلی درجہ حرارت پر کمپیکٹ کو سنٹر کرتے ہیں۔ گرم آئسوسٹیٹک دبانے کے نتیجے میں اضافی کثافت اور طاقت میں اضافہ ہوتا ہے۔
• سلپ کاسٹنگ / ڈرین کاسٹنگ : ہم مولڈ کو مائیکرو میٹر سائز کے سیرامک پارٹیکلز اور کیریئر مائع کے سسپنشن سے بھرتے ہیں۔ اس مرکب کو "پرچی" کہا جاتا ہے۔ سڑنا میں سوراخ ہوتے ہیں اور اس وجہ سے مرکب میں موجود مائع کو مولڈ میں فلٹر کیا جاتا ہے۔ نتیجے کے طور پر، سڑنا کی اندرونی سطحوں پر ایک کاسٹ بنتا ہے۔ sintering کے بعد، حصوں کو سڑنا سے باہر لے جایا جا سکتا ہے.
• ٹیپ کاسٹنگ: ہم فلیٹ حرکت پذیر کیریئر کی سطحوں پر سیرامک سلریز کاسٹ کر کے سیرامک ٹیپ تیار کرتے ہیں۔ سلریوں میں سیرامک پاؤڈر ہوتے ہیں جو بائنڈنگ اور لے جانے کے مقاصد کے لیے دوسرے کیمیکلز کے ساتھ ملتے ہیں۔ جب سالوینٹس بخارات بنتے ہیں تو سیرامک کی گھنی اور لچکدار چادریں پیچھے رہ جاتی ہیں جنہیں حسب منشا کاٹا یا رول کیا جا سکتا ہے۔
• اخراج کی تشکیل: دوسرے اخراج کے عمل کی طرح، بائنڈر اور دیگر کیمیکلز کے ساتھ سیرامک پاؤڈر کا ایک نرم مرکب ڈائی سے گزر کر اس کی کراس سیکشنل شکل حاصل کرتا ہے اور پھر اسے مطلوبہ لمبائی میں کاٹا جاتا ہے۔ یہ عمل سرد یا گرم سرامک مرکب کے ساتھ کیا جاتا ہے۔
• لو پریشر انجیکشن مولڈنگ: ہم بائنڈر اور سالوینٹس کے ساتھ سیرامک پاؤڈر کا مرکب تیار کرتے ہیں اور اسے ایسے درجہ حرارت پر گرم کرتے ہیں جہاں اسے آسانی سے دبایا جا سکتا ہے اور ٹول کیویٹی میں زبردستی لایا جا سکتا ہے۔ مولڈنگ سائیکل مکمل ہونے کے بعد، حصہ نکال دیا جاتا ہے اور بائنڈنگ کیمیکل کو جلا دیا جاتا ہے۔ انجکشن مولڈنگ کا استعمال کرتے ہوئے، ہم اقتصادی طور پر اعلی حجم میں پیچیدہ حصوں کو حاصل کر سکتے ہیں. سوراخ جو کہ 10 ملی میٹر موٹی دیوار پر ایک ملی میٹر کا ایک چھوٹا سا حصہ ہے ممکن ہے، دھاگے بغیر مشینی کے ممکن ہیں، جتنی سخت برداشت +/- 0.5% ممکن ہو اور مشین کے پرزے بھی کم ہوں ، دیوار کی موٹائی 0.5 ملی میٹر سے 12.5 ملی میٹر کی لمبائی کے ساتھ ساتھ 6.5 ملی میٹر سے 150 ملی میٹر کی لمبائی تک دیوار کی موٹائی ممکن ہے۔
• گرین مشیننگ: اسی دھاتی مشینی ٹولز کا استعمال کرتے ہوئے، ہم دبائے ہوئے سیرامک مواد کو مشین بنا سکتے ہیں جب وہ چاک کی طرح نرم ہوں۔ +/- 1٪ کی رواداری ممکن ہے۔ بہتر رواداری کے لیے ہم ڈائمنڈ پیسنے کا استعمال کرتے ہیں۔
• SINTERING یا FIRING : sintering مکمل کثافت کو ممکن بناتا ہے۔ گرین کمپیکٹ حصوں پر نمایاں سکڑاؤ ہوتا ہے، لیکن یہ کوئی بڑا مسئلہ نہیں ہے کیونکہ جب ہم حصے اور ٹولنگ کو ڈیزائن کرتے ہیں تو ہم ان جہتی تبدیلیوں کو مدنظر رکھتے ہیں۔ پاؤڈر کے ذرات آپس میں بندھے ہوئے ہیں اور کمپیکشن کے عمل سے پیدا ہونے والی پورسٹی کو کافی حد تک ہٹا دیا جاتا ہے۔
• ڈائمنڈ پیسنا: دنیا کا سب سے مشکل مواد "ہیرا" سیرامکس جیسے سخت مواد کو پیسنے کے لیے استعمال کیا جا رہا ہے اور درست حصے حاصل کیے جاتے ہیں۔ مائیکرو میٹر رینج میں رواداری اور بہت ہموار سطحیں حاصل کی جا رہی ہیں۔ اس کے اخراجات کی وجہ سے، ہم صرف اس تکنیک پر غور کرتے ہیں جب ہمیں واقعی اس کی ضرورت ہوتی ہے۔
ہرمیٹک اسمبلیاں وہ ہیں جو عملی طور پر بات کرتے ہوئے انٹرفیس کے درمیان مادے، ٹھوس، مائعات یا گیسوں کے تبادلے کی اجازت نہیں دیتی ہیں۔ ہرمیٹک سگ ماہی ہوا بند ہے۔ مثال کے طور پر ہرمیٹک الیکٹرانک انکلوژرز وہ ہوتے ہیں جو پیکڈ ڈیوائس کے حساس اندرونی مواد کو نمی، آلودگی یا گیسوں سے نقصان نہ پہنچاتے ہیں۔ کوئی بھی چیز 100% ہرمیٹک نہیں ہے، لیکن جب ہم ہرمیٹی کی بات کرتے ہیں تو عملی طور پر ہمارا مطلب یہ ہے کہ اس حد تک ہرمیٹیسیٹی ہے کہ رساو کی شرح اتنی کم ہے کہ آلات عام ماحولیاتی حالات میں بہت لمبے عرصے تک محفوظ رہتے ہیں۔ ہماری ہرمیٹک اسمبلیاں دھات، شیشے اور سیرامک اجزاء، دھاتی سیرامک، سیرامک دھاتی سیرامک، دھاتی سیرامک دھات، دھات سے دھات، دھاتی گلاس، دھاتی گلاس، دھاتی شیشے، دھاتی شیشے، شیشے کے شیشے پر مشتمل ہوتی ہیں۔ دھات اور شیشے سے شیشے اور دھاتی گلاس سیرامک بانڈنگ کے دیگر تمام امتزاج۔ ہم مثال کے طور پر سیرامک کے اجزاء کو دھاتی کوٹ کر سکتے ہیں تاکہ وہ اسمبلی میں موجود دیگر اجزاء کے ساتھ مضبوطی سے منسلک ہو سکیں اور ان میں سگ ماہی کی بہترین صلاحیت ہو۔ ہمارے پاس آپٹیکل ریشوں یا فیڈ تھرو کو دھات کے ساتھ کوٹنگ کرنے اور ان کو انکلوژرز میں سولڈرنگ یا بریز کرنے کا طریقہ معلوم ہے، اس لیے کوئی گیس ان انکلوژرز میں نہیں گزرتی اور نہ ہی لیک ہوتی ہے۔ اس لیے ان کا استعمال الیکٹرانک انکلوژرز تیار کرنے کے لیے کیا جاتا ہے تاکہ حساس آلات کو گھیر لیا جا سکے اور انہیں بیرونی ماحول سے محفوظ رکھا جا سکے۔ ان کی بہترین سگ ماہی خصوصیات کے علاوہ، دیگر خصوصیات جیسے تھرمل ایکسپینشن گتانک، اخترتی مزاحمت، نان آؤٹ گیسنگ فطرت، بہت طویل زندگی، غیر موصل نوعیت، تھرمل موصلیت کی خصوصیات، اینٹی سٹیٹک نوعیت... وغیرہ۔ شیشے اور سیرامک مواد کو مخصوص ایپلی کیشنز کے لیے انتخاب بنائیں۔ سیرامک سے دھاتی فٹنگز، ہرمیٹک سیلنگ، ویکیوم فیڈ تھرو، ہائی اور انتہائی ہائی ویکیوم اور فلوئڈ کنٹرول اجزاء کی تیاری کی ہماری سہولت کے بارے میں معلومات یہاں مل سکتی ہیں:ہرمیٹک اجزاء فیکٹری بروشر