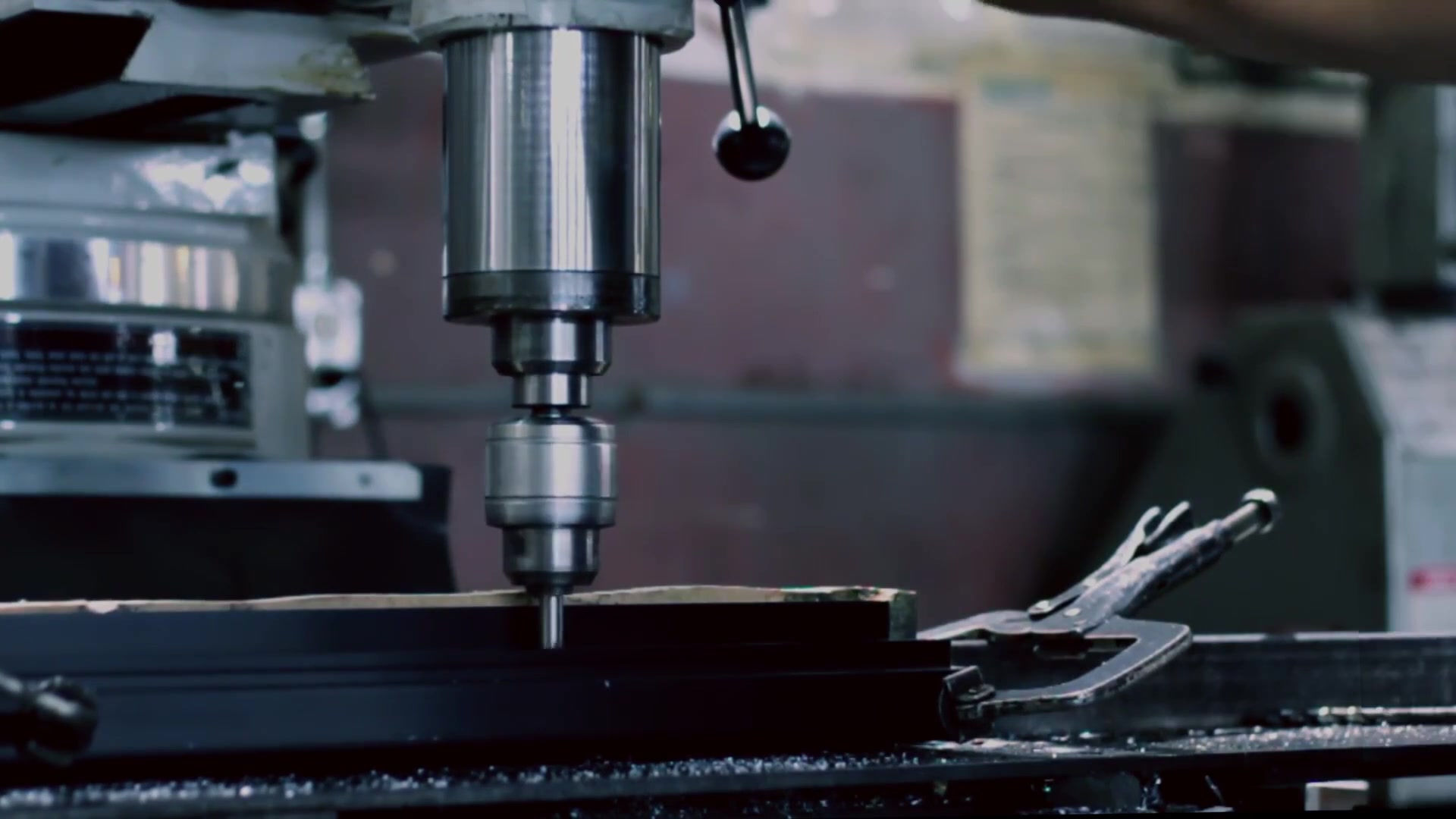
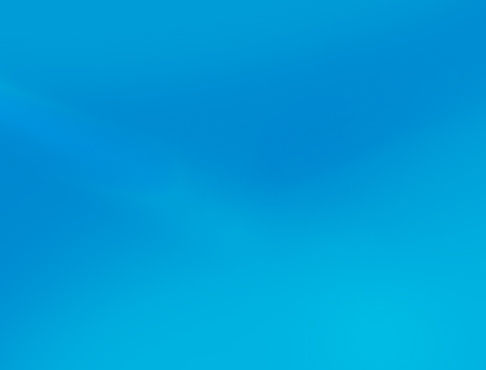
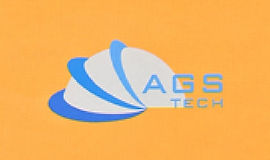
全球定制制造商、集成商、整合商、各种产品和服务的外包合作伙伴。
我们是您定制制造和现成产品和服务的制造、制造、工程、整合、集成、外包的一站式来源。
Choose your Language
-
定制制造
-
国内和全球合同制造
-
制造外包
-
国内及全球采购
-
Consolidation
-
工程集成
-
工程服务
在我们在制造中部署的众多连接技术中,特别强调焊接、钎焊、焊接、粘合剂粘合和定制机械组装,因为这些技术广泛用于密封组件制造、高科技产品制造和专业密封等应用。在这里,我们将专注于这些连接技术的更专业的方面,因为它们与先进产品和组件的制造有关。
熔焊:我们使用热量来熔化和聚结材料。热量由电力或高能光束提供。我们部署的熔焊类型是氧气燃料气体焊接、电弧焊接、高能束焊接。
固态焊接:我们在不熔化和熔合的情况下连接零件。我们的固态焊接方法有冷焊、超声波焊、电阻焊、摩擦焊、爆炸焊和扩散焊。
钎焊和焊接:它们使用填充金属,使我们能够在比焊接更低的温度下工作,从而减少对产品的结构损坏。有关我们生产陶瓷到金属配件、气密密封、真空馈入件、高真空和超高真空以及流体控制组件 的钎焊设施的信息,请参见此处:钎焊厂手册
粘合剂粘合:由于工业中使用的粘合剂的多样性以及应用的多样性,我们为此设置了专门的页面。 要访问我们关于粘合剂粘合的页面,请单击此处。
定制机械组件:我们使用各种紧固件,如螺栓、螺钉、螺母、铆钉。我们的紧固件不限于标准的现成紧固件。我们设计、开发和制造由非标准材料制成的特种紧固件,以满足特殊应用的要求。有时需要不导电或不导热,而有时需要导电。对于某些特殊应用,客户可能需要在不破坏产品的情况下无法移除的特殊紧固件。有无穷无尽的想法和应用。我们为您准备了一切,如果不是现成的,我们可以快速开发它。 要访问我们的机械装配页面,请单击此处. 让我们更详细地研究我们的各种连接技术。
OXYFUEL GAS WELDING (OFW):我们使用与氧气混合的燃料气体来产生焊接火焰。当我们使用乙炔作为燃料和氧气时,我们称之为氧乙炔气焊。富氧燃气燃烧过程中会发生两种化学反应:
C2H2 + O2 ------» 2CO + H2 + 热
2CO + H2 + 1.5 O2--------» 2 CO2 + H2O + 热量
第一个反应将乙炔分解成一氧化碳和氢气,同时产生约 33% 的总热量。上述第二个过程代表氢气和一氧化碳的进一步燃烧,同时产生约 67% 的总热量。火焰中的温度在 1533 到 3573 开尔文之间。气体混合物中的氧气百分比很重要。如果氧气含量超过一半,火焰就会变成氧化剂。这对于某些金属是不希望的,但对于其他金属是理想的。需要氧化火焰的一个例子是铜基合金,因为它在金属上形成了钝化层。另一方面,当氧含量减少时,不能充分燃烧,火焰变成还原(渗碳)火焰。还原火焰中的温度较低,因此适用于焊接和钎焊等工艺。其他气体也是潜在的燃料,但它们比乙炔有一些缺点。有时,我们以填充棒或焊丝的形式向焊接区提供填充金属。其中一些涂有助焊剂以延缓表面氧化,从而保护熔融金属。助焊剂给我们带来的另一个好处是从焊接区去除氧化物和其他物质。这导致更强的结合。氧气燃气焊接的一种变体是压力气体焊接,其中两个组件在其界面处使用氧乙炔气焊枪加热,一旦界面开始熔化,焊枪就会缩回并施加轴向力将两个部件压在一起直到界面凝固。
电弧焊接:我们使用电能在电极尖端和要焊接的零件之间产生电弧。电源可以是交流或直流,而电极是消耗性或非消耗性的。弧焊中的热传递可以用下式表示:
H / l = ex VI / v
这里 H 是热输入,l 是焊接长度,V 和 I 是施加的电压和电流,v 是焊接速度,e 是工艺效率。效率“e”越高,可用能量就越有利地用于熔化材料。热输入也可以表示为:
H = ux(音量)= ux A xl
这里 u 是熔化的比能,A 是焊缝的横截面,l 是焊缝长度。从上面的两个方程我们可以得到:
v = ex VI / u A
电弧焊的一种变体是屏蔽金属电弧焊 (SMAW),它约占所有工业和维修焊接工艺的 50%。电弧焊(棒焊)是通过将涂层电极的尖端接触工件并快速将其撤回到足以保持电弧的距离来执行的。我们称这个过程也为棒焊,因为电极是细而长的棒。在焊接过程中,电极尖端连同其涂层和电弧附近的基体金属一起熔化。基底金属、电极金属和电极涂层中的物质的混合物在焊接区域固化。电极的涂层在焊接区域脱氧并提供保护气体,从而保护它免受环境中的氧气的影响。因此,该工艺被称为保护金属电弧焊。我们使用 50 至 300 安培的电流和通常小于 10 kW 的功率水平,以实现最佳焊接性能。同样重要的是直流电流的极性(电流方向)。工件为正极而电极为负极的直极性在钣金焊接中是首选,因为它的熔深较浅,也适用于间隙非常大的接头。当我们有反极性时,即电极为正极而工件为负极,我们可以实现更深的焊接熔深。对于交流电流,由于我们有脉动电弧,我们可以使用大直径电极和最大电流焊接厚部分。 SMAW 焊接方法适用于厚度为 3 至 19 毫米甚至更厚的工件,使用多道次技术。焊缝顶部形成的熔渣需要用钢丝刷清除,以免焊缝处出现腐蚀和失效。这当然增加了保护金属电弧焊的成本。然而,SMAW 是工业和维修工作中最流行的焊接技术。
埋弧焊 (SAW):在此过程中,我们使用颗粒状焊剂材料(如石灰、二氧化硅、氟化钙、氧化锰……等)保护焊弧。粒状焊剂通过喷嘴通过重力流送入焊接区。覆盖熔融焊接区的焊剂可显着防止火花、烟雾、紫外线辐射……等,并充当热绝缘体,从而让热量深入工件。未熔合的焊剂被回收、处理和再利用。裸线圈用作电极并通过管子馈送到焊接区域。我们使用 300 到 2000 安培之间的电流。如果圆形结构(例如管道)在焊接过程中可以旋转,则埋弧焊 (SAW) 工艺仅限于水平和平面位置以及圆形焊缝。速度可以达到 5 m/min。 SAW 工艺适用于厚板,可实现高质量、坚韧、延展和均匀的焊缝。生产率,即每小时沉积的焊接材料量是 SMAW 工艺的 4 到 10 倍。
另一种电弧焊接工艺,即气体金属电弧焊接 (GMAW) 或称为金属惰性气体焊接 (MIG),是基于焊接区域受到外部气体源(如氦气、氩气、二氧化碳……等)的保护。电极金属中可能存在额外的脱氧剂。消耗性焊丝通过喷嘴送入焊接区。使用气体保护金属电弧焊 (GMAW) 进行涉及黑色金属和有色金属的制造。焊接生产率约为 SMAW 工艺的 2 倍。正在使用自动焊接设备。在此过程中,金属以三种方式之一转移:“喷涂转移”涉及每秒数百个小金属液滴从电极转移到焊接区域。另一方面,在“球状转移”中,使用富含二氧化碳的气体,并通过电弧推动熔融金属球。焊接电流高,焊接熔深更深,焊接速度大于喷射转移。因此,球状转移更适合焊接较重的部分。最后,在“短路”方法中,电极尖端接触熔融焊池,将其短路,因为金属以超过 50 滴/秒的速度以单个液滴的形式转移。低电流和电压与更细的电线一起使用。使用的功率约为 2 kW,温度相对较低,因此该方法适用于厚度小于 6 毫米的薄板。
药芯电弧焊 (FCAW) 工艺的另一个变体类似于气体保护金属电弧焊,不同之处在于电极是填充有焊剂的管。使用有芯焊剂电极的优点是它们产生更稳定的电弧,使我们有机会改善焊接金属的性能,与 SMAW 焊接相比,其焊剂的脆性和柔韧性更小,改善了焊接轮廓。自保护药芯焊条包含保护焊接区免受大气影响的材料。我们使用大约 20 kW 的功率。与 GMAW 工艺一样,FCAW 工艺也提供了实现连续焊接工艺自动化的机会,而且经济实惠。通过向焊剂芯中添加各种合金,可以开发出不同的焊接金属化学成分。
在 ELECTROGAS WELDING (EGW) 中,我们将边对边放置的零件进行焊接。有时也称为对接焊。将焊接金属放入待连接的两块之间的焊接腔中。该空间由两个水冷坝围起来,以防止熔渣倾泻而出。大坝由机械驱动向上移动。在工件可以旋转的情况下,也可以采用电气焊技术对管道进行环焊。电极通过管道馈电以保持连续电弧。电流可以约为 400 安培或 750 安培,功率水平约为 20 kW。来自药芯电极或外部源的惰性气体提供屏蔽。我们对厚度从 12 毫米到 75 毫米的钢、钛……等金属使用电气焊 (EGW)。该技术非常适合大型结构。
然而,在另一种称为电渣焊 (ESW) 的技术中,在电极和工件底部之间点燃电弧并添加助焊剂。当熔渣到达电极尖端时,电弧熄灭。能量通过熔渣的电阻连续提供。我们可以焊接厚度在 50 毫米到 900 毫米甚至更高的板材。电流约为 600 安培,而电压在 40 – 50 V 之间。焊接速度约为 12 至 36 mm/min。应用类似于电焊。
我们的非消耗性电极工艺之一,也称为钨极惰性气体焊接 (TIG) 的气体钨极电弧焊 (GTAW) 涉及通过焊丝供应填充金属。对于紧密配合的接头,有时我们不使用填充金属。在 TIG 工艺中,我们不使用助焊剂,而是使用氩气和氦气进行屏蔽。钨的熔点高,在 TIG 焊接过程中不消耗,因此可以保持恒定电流和电弧间隙。功率水平在 8 到 20 kW 之间,电流为 200 安培 (DC) 或 500 安培 (AC)。对于铝和镁,我们使用交流电来清洁氧化物。为避免钨电极受到污染,我们避免其与熔融金属接触。气体钨极电弧焊 (GTAW) 特别适用于焊接薄金属。 GTAW 焊缝质量非常好,具有良好的表面光洁度。
由于氢气成本较高,不太常用的技术是原子氢焊接 (AHW),我们在流动氢气的保护气氛中在两个钨电极之间产生电弧。 AHW 也是一种非消耗性电极焊接工艺。双原子氢气 H2 在温度超过 6273 开尔文的焊接电弧附近分解成原子形式。在击穿时,它会从电弧中吸收大量热量。当氢原子撞击相对较冷的表面焊接区时,它们重新组合成双原子形式并释放储存的热量。能量可以通过改变工件的弧距来改变。
在另一种非消耗性电极工艺中,等离子弧焊接 (PAW) 我们将集中的等离子弧引向焊接区。 PAW 中的温度达到 33,273 开尔文。几乎相等数量的电子和离子构成等离子气体。低电流引弧引发钨电极和孔之间的等离子体。工作电流一般在 100 安培左右。可以进给填充金属。在等离子弧焊中,屏蔽是通过外部屏蔽环并使用氩气和氦气等气体来完成的。在等离子弧焊中,电弧可以在电极和工件之间,也可以在电极和喷嘴之间。这种焊接技术与其他方法相比具有能量集中度更高、焊接能力更深更窄、电弧稳定性更好、焊接速度高达1米/分钟、热变形更小的优点。我们通常使用等离子弧焊来焊接厚度小于 6 毫米的铝和钛,有时甚至高达 20 毫米。
高能束焊接:另一种熔焊方法,电子束焊接 (EBW) 和激光焊接 (LBW) 作为两种变体。这些技术对我们的高科技产品制造工作具有特殊价值。在电子束焊接中,高速电子撞击工件并将其动能转化为热量。窄电子束很容易在真空室中传播。通常我们在电子束焊接中使用高真空。可焊接厚达 150 mm 的板。不需要保护气体、助焊剂或填充材料。电子束枪具有 100 kW 的容量。深而窄的焊缝具有高达 30 的高纵横比和小的热影响区是可能的。焊接速度可达12 m/min。在激光束焊接中,我们使用高功率激光作为热源。小至 10 微米的高密度激光束可深入穿透工件。激光束焊接的深宽比可能高达 10。我们同时使用脉冲和连续波激光器,前者用于薄材料,后者主要用于厚达约 25 毫米的工件。功率级别高达 100 kW。激光束焊接不太适合光学反射性很强的材料。气体也可用于焊接过程。激光束焊接方法非常适合自动化和大批量制造,可提供 2.5 m/min 至 80 m/min 的焊接速度。这种焊接技术提供的一个主要优势是可以进入其他技术无法使用的区域。激光束很容易到达如此困难的区域。不需要电子束焊接中的真空。使用激光束焊接可以获得具有良好质量和强度、低收缩、低变形、低孔隙率的焊缝。使用光纤电缆可以轻松地操纵和塑造激光束。因此,该技术非常适用于精密密封组件、电子封装等的焊接。
让我们看看我们的固态焊接技术。冷焊 (CW) 是一种使用模具或滚轮将压力而不是热量施加到配合的零件上的过程。在冷焊中,至少有一个配合部件需要具有延展性。使用两种相似的材料可获得最佳结果。如果要通过冷焊连接的两种金属不同,我们可能会得到弱而脆的接头。冷焊方法非常适用于柔软、易延展和小型工件,例如电气连接、热敏容器边缘、恒温器用双金属条等。冷焊的一种变体是滚焊(或滚焊),其中通过一对滚轮施加压力。有时我们在高温下进行滚焊以获得更好的界面强度。
我们使用的另一种固态焊接工艺是超声波焊接 (USW),其中工件受到静态法向力和振荡剪切应力。振荡剪切应力通过换能器的尖端施加。超声波焊接采用频率从 10 到 75 kHz 的振荡。在缝焊等一些应用中,我们使用旋转焊盘作为尖端。施加到工件上的剪切应力会导致小的塑性变形、分解氧化层、污染物并导致固态键合。超声波焊接所涉及的温度远低于金属的熔点温度,并且不会发生熔化。我们经常对塑料等非金属材料使用超声波焊接 (USW) 工艺。然而,在热塑性塑料中,温度确实达到了熔点。
另一种流行的技术,在摩擦焊接 (FRW) 中,热量是通过要连接的工件界面处的摩擦产生的。在摩擦焊接中,我们使一个工件保持静止,而另一个工件则固定在夹具中并以恒定速度旋转。然后工件在轴向力下接触。在某些情况下,摩擦焊接中的表面旋转速度可能达到 900m/min。在充分的界面接触后,旋转的工件突然停止,轴向力增加。焊接区通常是一个狭窄的区域。摩擦焊接技术可用于连接由多种材料制成的实心和管状零件。在 FRW 的界面上可能会产生一些飞边,但这种飞边可以通过二次加工或磨削去除。存在摩擦焊接工艺的变化。例如,“惯性摩擦焊接”涉及飞轮,其旋转动能用于焊接零件。当飞轮停止时,焊接完成。可以改变旋转质量,从而改变旋转动能。另一种变体是“线性摩擦焊接”,其中线性往复运动施加在至少一个要连接的部件上。在线性摩擦焊接中,零件不必是圆形的,它们可以是矩形、正方形或其他形状。频率可以在几十赫兹,幅度在毫米范围内,压力在几十或几百兆帕。最后,“摩擦搅拌焊接”与上面解释的其他两个有些不同。而在惯性摩擦焊接和线性摩擦焊接中,界面的加热是通过摩擦两个接触表面来实现的,而在摩擦搅拌焊接方法中,第三物体是在两个待接合的表面上摩擦。使直径为 5 至 6 mm 的旋转工具与接头接触。温度可以增加到 503 到 533 开尔文之间的值。对接头中的材料进行加热、混合和搅拌。我们在各种材料上使用搅拌摩擦焊,包括铝、塑料和复合材料。焊缝均匀,质量高,气孔最少。搅拌摩擦焊不会产生烟雾或飞溅物,并且该过程自动化程度很高。
电阻焊接 (RW):焊接所需的热量是由要连接的两个工件之间的电阻产生的。电阻焊不使用助焊剂、保护气体或自耗电极。焦耳加热发生在电阻焊中,可以表示为:
H = (平方 I) x R xtx K
H 是以焦耳(瓦特秒)为单位产生的热量,I 是以安培为单位的电流,R 是以欧姆为单位的电阻,t 是以秒为单位的电流流过的时间。因子 K 小于 1,表示未通过辐射和传导损失的能量分数。电阻焊接工艺中的电流可高达 100,000 A,但电压通常为 0.5 至 10 V。电极通常由铜合金制成。相似和不同的材料都可以通过电阻焊连接。此过程存在几种变化:“电阻点焊”涉及两个相对的圆形电极,它们接触两个片材搭接接头的表面。施加压力直到电流关闭。焊核的直径一般可达 10 毫米。电阻点焊会在焊点处留下轻微变色的压痕。点焊是我们最流行的电阻焊接技术。点焊中使用了各种电极形状,以达到难以到达的区域。我们的点焊设备是 CNC 控制的,并且有多个可以同时使用的电极。另一种变体“电阻缝焊”是使用轮式或滚轮式电极进行的,只要电流在交流电源循环中达到足够高的水平,就会产生连续的点焊。电阻缝焊产生的接头是液密和气密的。薄板的焊接速度约为 1.5 m/min 是正常的。可以施加间歇电流,以便沿焊缝以所需的间隔产生点焊。在“电阻凸焊”中,我们在要焊接的工件表面之一上压印一个或多个凸起(凹坑)。这些突起可以是圆形或椭圆形。在这些与配合部件接触的压纹点处会达到较高的局部温度。电极施加压力以压缩这些突起。电阻凸焊中的电极具有扁平尖端并且是水冷铜合金。电阻凸焊的优势在于我们能够一次完成多次焊接,从而延长电极寿命,能够焊接各种厚度的板材,能够将螺母和螺栓焊接到板材上。电阻凸焊的缺点是增加了压纹凹坑的成本。还有另一种技术,在“闪光焊接”中,当两个工件开始接触时,其末端的电弧会产生热量。该方法也可以替代地考虑电弧焊。界面温度升高,材料软化。施加轴向力并在软化区域形成焊缝。闪光焊接完成后,可以对接头进行机加工以改善外观。闪光焊获得的焊缝质量良好。功率水平为 10 至 1500 kW。闪光焊接适用于直径不超过 75 毫米的相似或异种金属和厚度在 0.2 毫米至 25 毫米之间的板材的边对边连接。 “螺柱弧焊”与闪光焊非常相似。螺栓或螺纹杆等螺柱在与板等工件接合时用作一个电极。为了集中产生的热量、防止氧化并将熔融金属保留在焊接区,在接头周围放置了一个一次性陶瓷环。最后“冲击焊接”另一种电阻焊接工艺,利用电容器提供电能。在冲击焊接中,功率会在几毫秒内迅速释放,从而在接头处产生很高的局部热量。我们在电子制造业中广泛使用冲击焊接,在这些行业中,必须避免对接头附近的敏感电子元件进行加热。
一种称为爆炸焊接的技术涉及引爆一层炸药,该炸药层放置在要连接的一个工件上。施加在工件上的非常高的压力产生湍流和波浪形界面,并发生机械联锁。爆炸焊接中的结合强度非常高。爆炸焊接是用异种金属熔覆板的好方法。在包覆之后,这些板可以被卷成更薄的部分。有时我们使用爆炸焊接来膨胀管子,这样它们就可以紧紧地密封在板上。
我们在固态连接领域的最后一种方法是扩散接合或扩散焊接 (DFW),其中主要通过界面上的原子扩散来实现良好的接合。界面处的一些塑性变形也有助于焊接。涉及的温度约为 0.5 Tm,其中 Tm 是金属的熔化温度。扩散焊接中的结合强度取决于压力、温度、接触时间和接触表面的清洁度。有时我们在界面处使用填充金属。扩散键合需要热量和压力,并由电阻或炉子和自重、压力机或其他方式提供。相似和不同的金属可以通过扩散焊接来连接。由于原子迁移需要时间,该过程相对较慢。 DFW 可以实现自动化,广泛用于制造航空航天、电子、医疗行业的复杂零件。制造的产品包括骨科植入物、传感器、航空航天结构件。扩散结合可以与超塑性成型相结合来制造复杂的钣金结构。片材上的选定位置首先进行扩散粘合,然后使用气压将未粘合区域膨胀到模具中。使用这种方法组合制造具有高刚度重量比的航空航天结构。扩散焊接/超塑性成型组合工艺通过消除对紧固件的需求减少了所需的零件数量,从而经济地生产出低应力高精度零件,并且交货时间短。
钎焊:钎焊和软钎焊技术涉及的温度低于焊接所需的温度。然而,钎焊温度高于焊接温度。在钎焊中,将填充金属放置在要连接的表面之间,并将温度升高到填充材料的熔化温度高于 723 开尔文但低于工件的熔化温度。熔融金属填充工件之间紧密配合的空间。填充金属的冷却和随后的固化导致牢固的接头。在钎焊中,填充金属沉积在接头处。与钎焊相比,钎焊中使用的填充金属要多得多。带有氧化火焰的氧乙炔焊炬用于在钎焊中沉积填充金属。由于钎焊温度较低,热影响区的问题(例如翘曲和残余应力)较少。钎焊间隙越小,接头的剪切强度越高。然而,最大抗拉强度是在最佳间隙(峰值)处实现的。低于和高于该最佳值,钎焊中的抗拉强度降低。钎焊中的典型间隙可以在 0.025 到 0.2 毫米之间。我们使用各种不同形状的钎焊材料,如预成型、粉末、环、线、条……等。并且可以专门为您的设计或产品几何形状制造这些性能。我们还会根据您的基材和应用确定钎焊材料的含量。我们经常在钎焊操作中使用助焊剂来去除不需要的氧化层并防止氧化。为了避免随后的腐蚀,焊剂通常在连接操作之后被去除。 AGS-TECH Inc. 使用各种钎焊方法,包括:
- 火炬钎焊
- 炉钎焊
- 感应钎焊
- 电阻钎焊
- 浸焊
- 红外线钎焊
- 扩散钎焊
- 高能光束
我们最常见的钎焊接头示例由具有良好强度的不同金属制成,例如硬质合金钻头、刀片、光电密封封装、密封件。
焊接:这是我们最常用的技术之一,其中焊料(填充金属)填充接头,就像在紧密配合的组件之间进行钎焊一样。我们的焊料熔点低于 723 开尔文。我们在制造操作中部署手动和自动焊接。与钎焊相比,焊接温度较低。焊接不太适合高温或高强度应用。我们使用无铅焊料以及锡铅、锡锌、铅银、镉银、锌铝合金等进行焊接。非腐蚀性树脂基以及无机酸和盐都可用作焊接中的助焊剂。我们使用特殊助焊剂来焊接可焊性低的金属。在我们必须焊接陶瓷材料、玻璃或石墨的应用中,我们首先在零件上镀上合适的金属以提高可焊性。我们流行的焊接技术是:
-回流或粘贴焊接
- 波峰焊
-炉焊
- 火炬焊接
-感应焊接
-烙铁焊接
-电阻焊接
- 浸焊
-超声波焊接
-红外线焊接
超声波焊接为我们提供了一个独特的优势,即由于超声波空化效应消除了对焊剂的需求,超声波空化效应从被连接的表面去除了氧化膜。回流焊和波峰焊是我们用于电子产品大批量制造的工业杰出技术,因此值得更详细地解释。在回流焊接中,我们使用包含焊料金属颗粒的半固态焊膏。使用筛选或模板工艺将糊剂放置在接头上。在印刷电路板 (PCB) 中,我们经常使用这种技术。当电气元件从浆料中放置到这些焊盘上时,表面张力使表面贴装封装保持对齐。放置组件后,我们在炉中加热组件,以便进行回流焊接。在这个过程中,焊膏中的溶剂蒸发,焊膏中的助焊剂被激活,元件被预热,焊料颗粒被熔化并润湿接头,最后PCB组件被缓慢冷却。我们第二种用于大批量生产 PCB 板的流行技术,即波峰焊依赖于这样一个事实,即熔融焊料润湿金属表面并仅在金属预热时形成良好的结合。熔融焊料的驻波首先由泵产生,预热和预焊的 PCB 在波上传送。焊料仅润湿暴露的金属表面,但不润湿 IC 聚合物封装和涂有聚合物的电路板。高速的热水喷射将多余的焊料从接头吹走,并防止相邻引线之间的桥接。在表面贴装封装的波峰焊中,我们首先在焊接之前将它们粘合到电路板上。再次使用筛选和模板,但这次是环氧树脂。将组件放置在正确位置后,环氧树脂固化,电路板倒置并进行波峰焊。