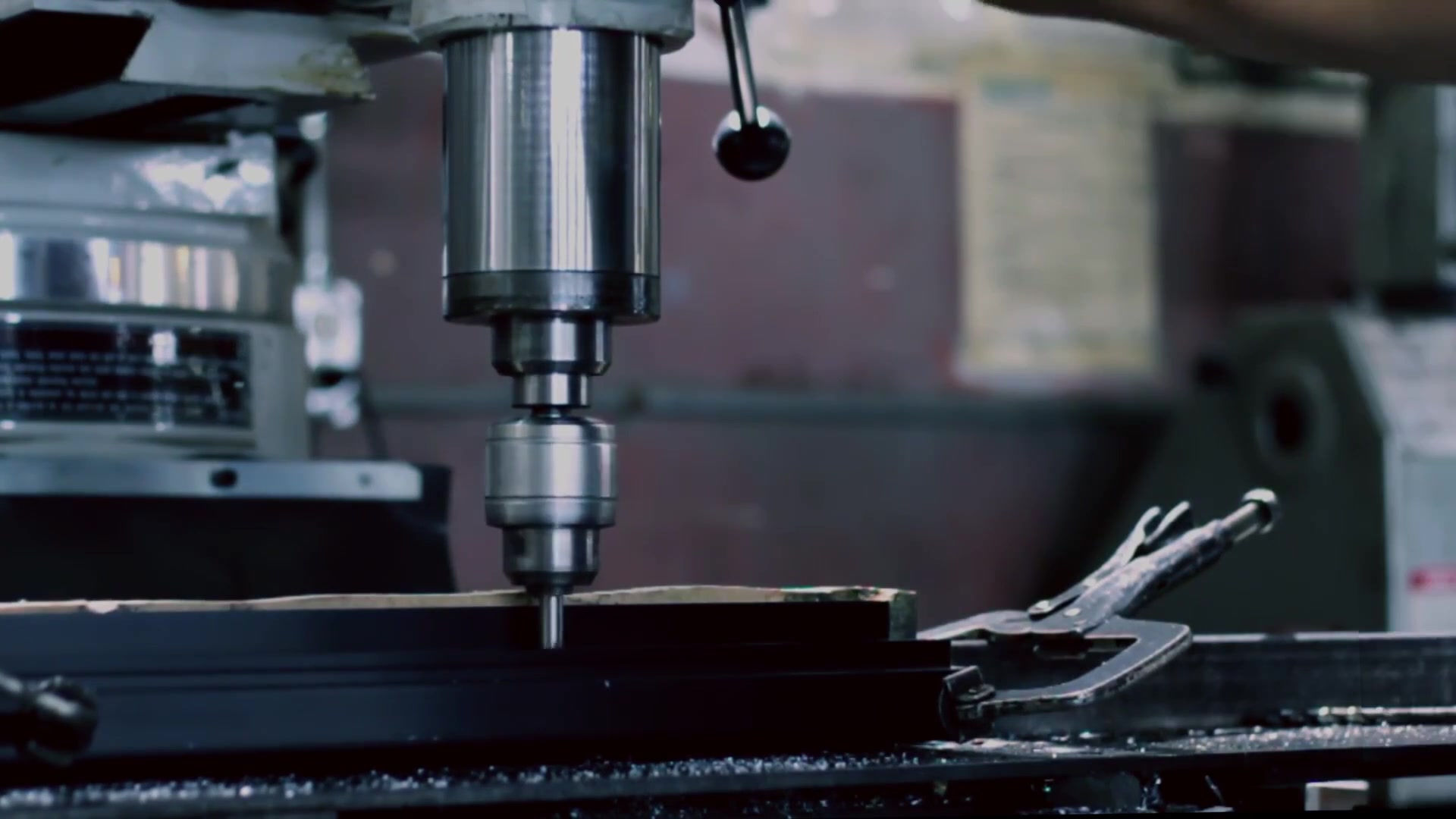
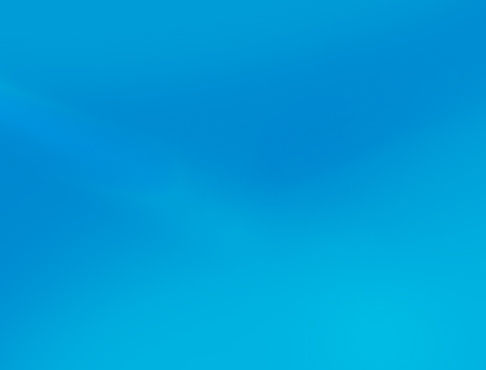
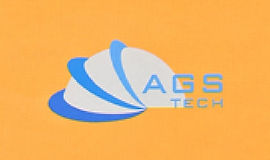
全球定制制造商、集成商、整合商、各种产品和服务的外包合作伙伴。
我们是您定制制造和现成产品和服务的制造、制造、工程、整合、集成、外包的一站式来源。
Choose your Language
-
定制制造
-
国内和全球合同制造
-
制造外包
-
国内及全球采购
-
Consolidation
-
工程集成
-
工程服务
我们提供的金属锻造工艺类型包括冷热模、开模和闭模、印模和无飞边锻件、 cogging、富勒、磨边和精密锻造、近净形、镦锻, 型锻, 镦粗锻造, 金属滚齿, 压力 & 轧制 & 径向 & 轨道 & 环 & 等温锻造, 压印, 铆接, 金属球锻造, 金属穿孔, 定径, 高能量锻造。
我们的粉末冶金和粉末加工技术是粉末压制和烧结、浸渍、渗透、冷热等静压、金属注射成型、辊压、粉末轧制、粉末挤压、松散烧结、火花烧结、热压。
我们建议您点击这里
这些带有照片和草图的可下载文件将帮助您更好地理解我们在下面为您提供的信息。
在金属锻造中,施加压缩力并使材料变形并获得所需的形状。工业中最常见的锻造材料是铁和钢,但铝、铜、钛、镁等许多其他材料也被广泛锻造。锻造金属零件除了密封裂纹和封闭空隙外,还具有改善的晶粒结构,因此通过该工艺获得的零件强度更高。锻造生产的零件的重量比铸造或机加工的零件强得多。由于锻造零件是通过使金属流动成最终形状来成型的,因此金属呈现出定向晶粒结构,从而使零件具有出色的强度。换句话说,与简单的铸造或机加工零件相比,通过锻造工艺获得的零件具有更好的机械性能。金属锻件的重量可以从小型轻质零件到数十万磅。我们主要为机械要求高的应用制造锻件,这些应用对汽车零件、齿轮、作业工具、手动工具、涡轮轴、摩托车齿轮等部件施加高应力。由于工具和设置成本相对较高,我们建议仅将这种制造工艺用于大批量生产和小批量但高价值的关键部件,例如航空起落架。除了模具成本外,与一些简单的机加工零件相比,大批量锻造零件的制造周期可能更长,但该技术对于 需要非凡强度的零件至关重要,例如螺栓、螺母、特殊应用紧固件,汽车,叉车,起重机零件。
• 热模锻和冷模锻:热模锻,顾名思义是在高温下进行的,因此延展性高,材料强度低。这有利于容易变形和锻造。相反,冷模锻是在较低温度下进行的,需要更高的力,这会导致应变硬化、更好的表面光洁度和制造零件的精度。
• 开放式模锻和压模锻造:在开放式模锻中,模具不限制被压缩的材料,而在压模锻造中,模具内的型腔在将材料锻造成所需形状时限制材料流动。镦粗锻造或也称为镦粗,实际上并不相同,而是一个非常相似的过程, 是一种开模工艺,工件夹在两个平模之间,压缩力降低了它的高度。随着高度为 reduced,工件宽度增加。 HEADING,镦粗锻造过程涉及在其端部镦粗并且其横截面局部增加的圆柱形坯料。在打头时,原料通过模具进料,锻造,然后切割成一定长度。该操作能够快速生产大量紧固件。大多数情况下,它是一种冷加工操作,因为它用于制造需要加强材料的钉子端、螺钉端、螺母和螺栓。另一种开模工艺是COGGING,其中工件在一系列步骤中进行锻造,每一步都会导致材料压缩以及开模沿工件长度的后续运动。在每一步,厚度都会减少,长度会增加少量。这个过程就像一个紧张的学生一直在小步咬着他的铅笔。称为 FULLERING 的工艺是另一种开放式模锻方法,我们经常将其部署为在进行其他金属锻造操作之前将材料分布在工件中的较早步骤。我们在工件需要多次 forging operations 时使用它。在操作中,凸面模具变形,导致金属向两侧流出。另一方面,与充分加工类似的过程,EDGING 涉及带有凹面的开放式模具以使工件变形。磨边也是后续锻造操作的准备过程,使材料从两侧流入中心区域。印象模锻或封闭模锻也称为使用模具/模具压缩材料并限制其在自身内部的流动。模具关闭,材料形成模具/模具型腔的形状。精密锻造是一种需要特殊设备和模具的工艺,可以生产没有飞边或飞边很少的零件。换句话说,零件将具有接近最终尺寸。在这个过程中,精心控制数量的材料被小心地插入并定位在模具内。我们将这种方法用于具有薄截面、小公差和拔模斜度的复杂形状,并且当数量大到足以证明模具和设备成本合理时。
• 无飞边锻造:工件放置在模具中的方式是没有材料流出型腔形成飞边。因此不需要不希望的闪光修整。这是一种精密锻造工艺,因此需要严格控制使用的材料量。
• 金属锻造或径向锻造:工件由模具沿圆周作用并锻造。心轴也可用于锻造内部工件几何形状。在型锻操作中,工件通常每秒接受几次冲程。通过型锻生产的典型物品是尖头工具、锥形棒、螺丝刀。
• 金属穿孔:我们经常将此操作用作零件制造中的附加操作。通过在工件表面上穿孔而不穿透它来创建孔或腔。请注意,穿孔不同于钻孔,钻孔会形成通孔。
• 滚齿:将具有所需几何形状的冲头压入工件并形成所需形状的型腔。我们称这种冲床为滚刀。该操作涉及高压并在低温下进行。因此,材料经过冷加工和应变硬化。因此,该工艺非常适合为其他制造工艺制造模具、冲模和型腔。一旦制造出滚刀,就可以轻松制造许多相同的腔体,而无需一个一个地加工它们。
• 滚锻或滚压成型:两个相对的滚轮用于成型金属零件。工件被送入轧辊,轧辊转动并将工件拉入间隙,然后将工件送入轧辊的凹槽部分,压缩力使材料具有所需的形状。它不是轧制过程,而是锻造过程,因为它是离散的而不是连续的操作。轧辊上的几何形状将材料锻造成所需的形状和几何形状。它是热执行的。由于是一种锻造工艺,它生产的零件具有出色的机械性能,因此我们将其用于 制造汽车零件,例如需要在恶劣的工作环境中具有非凡耐久性的轴。
• 轨道锻造:工件放入锻模腔中,由上模锻造,上模在倾斜轴上旋转时沿轨道运行。每转一圈,上模完成对整个工件施加压力。通过多次重复这些旋转,进行了充分的锻造。这种制造技术的优点是它的低噪音操作和所需的力量较小。换句话说,可以用很小的力使重型模具绕轴旋转,从而对与模具接触的工件部分施加较大的压力。圆盘或锥形零件有时非常适合此过程。
• 环锻:我们经常用于制造无缝环。毛坯被切割成一定长度,镦粗,然后一直穿过以形成一个中心孔。然后将其放在心轴上,锻模从上方对其进行锤击,同时环慢慢旋转,直到获得所需的尺寸。
• 铆接:连接零件的常见过程,首先将直金属件插入穿过零件的预制孔中。然后通过挤压上下模之间的接头锻造金属件的两端。
• 压印:另一种由机械压力机进行的流行工艺,在短距离内施加较大的力。 “铸币”这个名字来源于金属硬币表面锻造的精细细节。它主要是一种产品的精加工工艺,由于模具施加的巨大力将这些细节转移到工件上,从而在表面上获得了精细的细节。
• 金属球锻造:球轴承等产品需要高质量精密制造的金属球。在一种称为倾斜轧制的技术中,我们使用两个相对的轧辊,当原料不断地送入轧辊时,它们会不断旋转。在两个辊的一端,金属球作为产品被弹出。金属球锻造的第二种方法是使用模具挤压放置在它们之间的材料,使模具腔体呈球形。通常,生产的球需要一些额外的步骤,例如精加工和抛光,才能成为高质量的产品。
• 等温锻造/热模锻:仅在收益/成本价值合理时才执行的昂贵过程。一种热加工工艺,其中模具被加热到与工件大致相同的温度。由于模具和工件的温度大致相同,因此无需冷却,金属的流动特性得到改善。该操作非常适合锻造性较差的超级合金和材料及其材料
机械性能对小的温度梯度和变化非常敏感。
• 金属施胶:这是一种冷加工工艺。除了施加力的方向外,所有方向的材料流动都不受限制。结果,获得了非常好的表面光洁度和精确的尺寸。
• 高能率锻造:该技术涉及连接在活塞臂上的上模,当燃料-空气混合物被火花塞点燃时,该上模被迅速推动。它类似于汽车发动机中活塞的操作。由于背压,模具非常快速地撞击工件,然后非常快速地返回到其原始位置。作品在几毫秒内完成锻造,因此没有时间让作品冷却。这对于具有对温度非常敏感的机械性能的难以锻造的零件很有用。换句话说,该过程是如此之快,以至于零件始终在恒温下形成,并且在模具/工件界面处不会有温度梯度。
• 在模锻中,金属在两个匹配的具有特殊形状的钢块之间被敲打,称为模具。当金属在模具之间被锤击时,它的形状与模具中的形状相同。 当它达到最终形状时,取出冷却。该工艺生产出形状精确的坚固零件,但需要对专用模具进行更大的投资。镦粗锻造通过压平金属件来增加其直径。它通常用于制作小零件,特别是在螺栓和钉子等紧固件上形成头部。
• 粉末冶金/粉末加工:顾名思义,它涉及用粉末制造某些几何形状和形状的固体部件的制造工艺。如果为此目的使用金属粉末,则属于粉末冶金领域,如果使用非金属粉末,则属于粉末加工。固体零件由粉末通过压制和烧结制成。
POWDER PRESSING 用于将粉末压实成所需的形状。首先,主要材料是物理粉化的,将其分成许多小的单个颗粒。将粉末混合物填充到模具中,然后冲头向粉末移动并将其压实成所需的形状。大多在室温下进行,用粉末压制得到固体部分,称为生坯。粘合剂和润滑剂通常用于增强压实性。我们有能力使用数千吨容量的液压机进行粉末压制成型。此外,我们还提供带有相对顶部和底部冲头的双动压力机以及用于高度复杂零件几何形状的多动压力机。对于许多粉末冶金/粉末加工厂来说,均匀性是一个重要挑战,但对于 AGS-TECH 来说并不是什么大问题,因为我们在定制制造此类零件方面拥有多年的丰富经验。即使对于均匀性构成挑战的较厚部分,我们也取得了成功。如果我们致力于您的项目,我们将制造您的零件。如果我们发现任何潜在风险,我们会通知您 in
Advance.
粉末烧结是第二步,涉及将温度升高到一定程度并在该温度下保持一定时间,以便压制部件中的粉末颗粒可以结合在一起。这导致更牢固的结合和工件的加强。烧结发生在接近粉末的熔化温度。在烧结过程中会发生收缩,使材料强度、密度、延展性、导热性、导电性增加。我们确实有用于烧结的间歇式和连续式炉。我们的一项能力是调整我们生产的零件的孔隙率水平。例如,我们可以通过在一定程度上保持零件的多孔性来生产金属过滤器。
使用一种称为浸渍的技术,我们用油等流体填充金属的孔隙。例如,我们确实生产自润滑的油浸轴承。在渗透过程中,我们用另一种熔点低于基材的金属填充金属的孔隙。将混合物加热到两种金属的熔化温度之间的温度。结果,可以获得一些特殊的性质。当需要获得特殊特征或性能或可以用更少的工艺步骤制造零件时,我们还经常对粉末制造的零件进行加工和锻造等二次加工。
等静压:在这个过程中,流体压力被用来压紧零件。将金属粉末放入由密封的柔性容器制成的模具中。在等静压中,压力是从四面八方施加的,这与传统压制中看到的轴向压力相反。等静压的优点是零件内的密度均匀,特别是对于较大或较厚的零件,具有优越的性能。它的缺点是循环时间长和几何精度相对较低。冷等静压在室温下进行,柔性模具由橡胶、PVC或聚氨酯或类似材料制成。用于加压和压实的流体是油或水。生坯的常规烧结遵循这一点。另一方面,热等静压是在高温下进行的,模具材料是金属板或陶瓷,具有足够高的熔点以抵抗温度。加压流体通常是惰性气体。压制和烧结操作在一个步骤中进行。孔隙率几乎完全消除,得到了 uniform grain 结构。热等静压的优点是可以生产出与铸锻相结合的零件,同时使不适合铸锻的材料可以使用。热等静压的缺点是循环时间长,因此成本高。适用于小体积的关键部位。
金属注射成型:非常适合生产具有薄壁和详细几何形状的复杂零件的工艺。最适合较小的零件。将粉末和聚合物粘合剂混合、加热并注入模具中。聚合物粘合剂覆盖粉末颗粒的表面。成型后,通过低温加热或使用溶剂溶解去除粘合剂。
ROLL COMPACTION / POWDER ROLLING : 粉末用于生产连续的带材或片材。粉末从进料器进料并通过两个旋转辊压实成片材或条材。操作在冷态下进行。板材被送入烧结炉。可以第二次重复烧结过程。
粉末挤出:长径比大的零件是通过用粉末挤出薄金属板容器制造的。
松散烧结:顾名思义,它是一种无压压实和烧结方法,适用于生产非常多孔的零件,例如金属过滤器。粉末在没有压实的情况下被送入模腔。
松散烧结:顾名思义,它是一种无压压实和烧结方法,适用于生产非常多孔的零件,例如金属过滤器。粉末在没有压实的情况下被送入模腔。
火花烧结:粉末在模具中被两个相对的冲头压缩,大功率电流被施加到冲头上,并通过夹在它们之间的压实粉末。高电流烧掉粉末颗粒的表面薄膜,并用产生的热量将它们烧结。这个过程很快,因为热量不是从外部施加的,而是从模具内部产生的。
热压:粉末在可承受高温的模具中一步压制和烧结。当模具压实时,粉末热量被施加到它上面。通过这种方法获得的良好精度和机械性能使其成为一种有吸引力的选择。甚至难熔金属也可以使用石墨等模具材料进行加工。