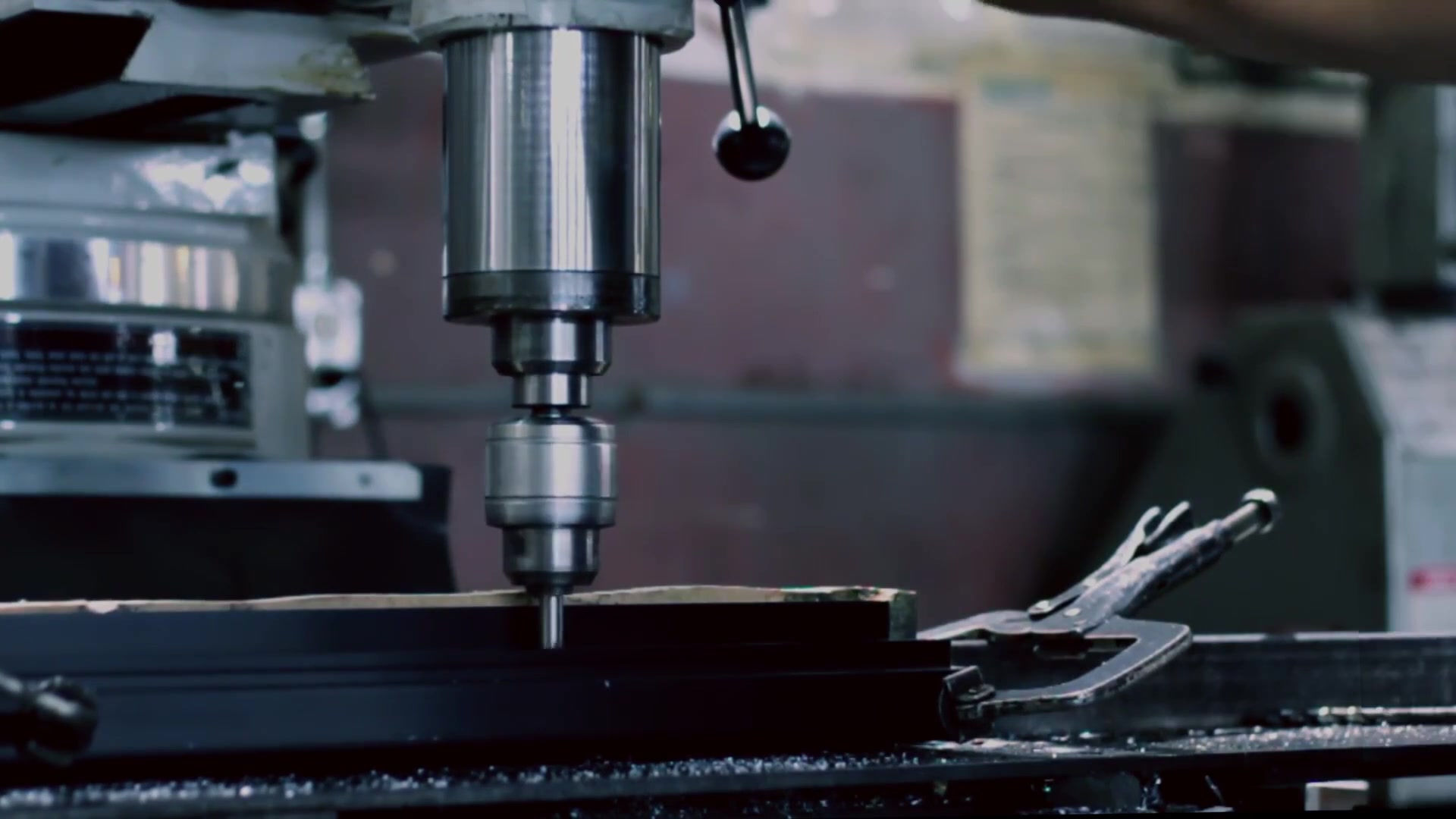
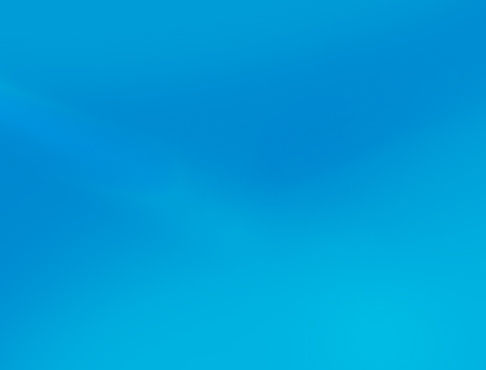
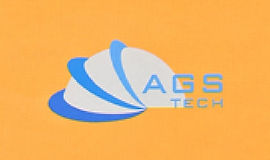
全球定制制造商、集成商、整合商、各种产品和服务的外包合作伙伴。
我们是您定制制造和现成产品和服务的制造、制造、工程、整合、集成、外包的一站式来源。
Choose your Language
-
定制制造
-
国内和全球合同制造
-
制造外包
-
国内及全球采购
-
Consolidation
-
工程集成
-
工程服务
微电子和半导体制造与制造
我们在其他菜单下解释的许多纳米制造、微制造和细观制造技术和工艺可用于 MICROELECTRONICS MANUFACTURING too。然而,由于微电子在我们产品中的重要性,我们将在这里集中讨论这些工艺的主题特定应用。微电子相关工艺也被广泛称为 SEMICONDUCTOR FABRICATION processes。我们的半导体工程设计和制造服务包括:
- FPGA板卡设计开发编程
- 微电子代工服务:设计、原型制作和制造、第三方服务
- 半导体晶圆制备:切割、背磨、减薄、光罩放置、芯片分类、取放、检查
- 微电子封装设计和制造:现货和定制设计和制造
- Semiconductor IC组装&封装&测试:Die、Wire and Chip Bonding、Encapsulation、Assembly、Marking and Branding
- 半导体器件的引线框架:现货和定制设计和制造
- 微电子散热器的设计和制造:现货和定制设计和制造
- 传感器和执行器设计与制造:现货和定制设计与制造
- 光电和光子电路设计与制造
让我们更详细地研究微电子和半导体制造和测试技术,以便您更好地了解我们提供的服务和产品。
FPGA 板设计与开发和编程:现场可编程门阵列 (FPGA) 是可重新编程的硅芯片。与您在个人计算机中找到的处理器相反,对 FPGA 进行编程会重新连接芯片本身以实现用户的功能,而不是运行软件应用程序。使用预构建的逻辑块和可编程路由资源,FPGA 芯片可以配置为实现自定义硬件功能,而无需使用面包板和烙铁。数字计算任务在软件中执行并编译成配置文件或比特流,其中包含有关组件应如何连接在一起的信息。 FPGA 可用于实现 ASIC 可以执行的任何逻辑功能,并且可以完全重新配置,并且可以通过重新编译不同的电路配置来赋予完全不同的“个性”。 FPGA 结合了专用集成电路 (ASIC) 和基于处理器的系统的最佳部分。这些好处包括:
• 更快的 I/O 响应时间和专用功能
• 超过数字信号处理器 (DSP) 的计算能力
• 快速原型设计和验证,无需定制 ASIC 的制造过程
• 使用专用确定性硬件的可靠性实现自定义功能
• 可现场升级,无需定制 ASIC 重新设计和维护费用
FPGA 提供速度和可靠性,不需要大量的量来证明定制 ASIC 设计的大量前期费用是合理的。可重编程芯片还具有与基于处理器的系统上运行的软件相同的灵活性,并且不受可用处理内核数量的限制。与处理器不同,FPGA 本质上是真正的并行,因此不同的处理操作不必竞争相同的资源。每个独立的处理任务都分配给芯片的一个专用部分,并且可以自主运行而不受其他逻辑块的任何影响。因此,当添加更多处理时,应用程序的一部分的性能不会受到影响。除了数字功能外,一些 FPGA 还具有模拟功能。一些常见的模拟功能是每个输出引脚上的可编程压摆率和驱动强度,允许工程师在轻负载引脚上设置慢速,否则会振铃或耦合不可接受,并在高速重载引脚上设置更强、更快的速率否则会运行太慢的频道。另一个相对常见的模拟功能是设计用于连接到差分信号通道的输入引脚上的差分比较器。一些混合信号 FPGA 集成了外围模数转换器 (ADC) 和数模转换器 (DAC) 以及模拟信号调理模块,允许它们作为片上系统运行。
简而言之,FPGA 芯片的 5 大优势是:
1. 性能好
2. 上市时间短
3. 低成本
4. 高可靠性
5、长期维护能力
良好的性能——凭借其适应并行处理的能力,FPGA 比数字信号处理器 (DSP) 具有更好的计算能力,并且不需要像 DSP 那样的顺序执行,并且每个时钟周期可以完成更多任务。在硬件级别控制输入和输出 (I/O) 可提供更快的响应时间和专门的功能,以紧密匹配应用程序要求。
上市时间短——FPGA 提供了灵活性和快速原型设计能力,从而缩短了上市时间。我们的客户可以测试一个想法或概念并在硬件中验证它,而无需经历漫长而昂贵的定制 ASIC 设计制造过程。我们可以在数小时而不是数周内实现增量更改和迭代 FPGA 设计。商业现成的硬件也可用于已连接到用户可编程 FPGA 芯片的不同类型的 I/O。高级软件工具的日益普及为高级控制和信号处理提供了宝贵的 IP 内核(预建功能)。
低成本——定制 ASIC 设计的非经常性工程 (NRE) 费用超过了基于 FPGA 的硬件解决方案。对于每年生产许多芯片的原始设备制造商来说,对 ASIC 的大量初始投资是合理的,但是许多最终用户需要为正在开发的许多系统定制硬件功能。我们的可编程硅 FPGA 为您提供无需制造成本或较长的组装交货时间的产品。系统要求经常随着时间而变化,与重新设计 ASIC 的巨额费用相比,对 FPGA 设计进行增量更改的成本可以忽略不计。
高可靠性——软件工具提供编程环境,FPGA电路是程序执行的真正实现。基于处理器的系统通常涉及多个抽象层,以帮助任务调度和在多个进程之间共享资源。驱动层控制硬件资源,操作系统管理内存和处理器带宽。对于任何给定的处理器内核,一次只能执行一条指令,并且基于处理器的系统不断面临时间关键任务相互抢占的风险。 FPGA 不使用操作系统,其真正的并行执行和专用于每项任务的确定性硬件对可靠性的担忧最小化。
长期维护能力——FPGA 芯片可现场升级,不需要重新设计 ASIC 所涉及的时间和成本。例如,数字通信协议的规范会随着时间而改变,而基于 ASIC 的接口可能会导致维护和前向兼容性挑战。相反,可重新配置的 FPGA 芯片可以跟上未来可能需要的修改。随着产品和系统的成熟,我们的客户可以在不花时间重新设计硬件和修改电路板布局的情况下进行功能增强。
微电子代工服务:我们的微电子代工服务包括设计、原型制作和制造、第三方服务。我们在整个产品开发周期内为客户提供帮助——从半导体芯片的设计支持到原型制作和制造支持。我们在设计支持服务方面的目标是为半导体器件的数字、模拟和混合信号设计提供一次正确的方法。例如,可以使用 MEMS 特定的仿真工具。可以处理用于集成 CMOS 和 MEMS 的 6 英寸和 8 英寸晶圆的晶圆厂随时为您服务。我们为客户提供所有主要电子设计自动化 (EDA) 平台的设计支持,提供正确的模型、流程设计套件 (PDK)、模拟和数字库以及制造设计 (DFM) 支持。我们为所有技术提供两种原型设计选项:多产品晶圆 (MPW) 服务,其中多个设备在一个晶圆上并行处理,以及多级掩模 (MLM) 服务,在同一个掩模版上绘制四个掩模级别。这些比全套面罩更经济。与 MPW 服务的固定日期相比,传销服务非常灵活。出于多种原因,公司可能更愿意将半导体产品外包给微电子代工厂,包括需要第二个来源、将内部资源用于其他产品和服务、愿意无晶圆厂并降低运营半导体工厂的风险和负担……等等。 AGS-TECH 提供开放平台的微电子制造工艺,可以按比例缩小以用于小晶圆运行以及大规模制造。在某些情况下,您现有的微电子或 MEMS 制造工具或完整的工具集可以作为委托工具或出售工具从您的工厂转移到我们的工厂,或者您现有的微电子和 MEMS 产品可以使用开放平台工艺技术重新设计并移植到我们工厂提供的工艺。这比定制技术转让更快、更经济。但是,如果需要,可以转移客户现有的微电子/MEMS 制造工艺。
半导体晶圆制备: 晶圆微加工后,如果客户需要,我们对半导体晶圆进行切割、背磨、减薄、光罩放置、芯片分类、拾取和放置、检查操作。半导体晶圆加工涉及各种加工步骤之间的计量。例如,基于椭偏仪或反射仪的薄膜测试方法,用于严格控制栅氧化层的厚度,以及光刻胶和其他涂层的厚度、折射率和消光系数。我们使用半导体晶圆测试设备来验证晶圆在测试之前没有被之前的处理步骤损坏。一旦前端工艺完成,半导体微电子器件将接受各种电气测试,以确定它们是否正常工作。我们将晶圆上发现性能正常的微电子器件的比例称为“良率”。晶圆上的微电子芯片的测试是使用电子测试仪进行的,该电子测试仪将微小的探针压在半导体芯片上。自动化机器用一滴染料标记每个坏的微电子芯片。晶圆测试数据被记录到中央计算机数据库中,并且半导体芯片根据预定的测试限制被分类到虚拟箱中。生成的分箱数据可以在晶圆图上绘制或记录,以追踪制造缺陷并标记不良芯片。该图也可以在晶圆组装和封装过程中使用。在最终测试中,微电子芯片在封装后再次测试,因为可能缺少键合线,或者封装可能会改变模拟性能。在测试半导体晶圆后,通常会在晶圆被刻痕然后将其分解成单个管芯之前将其厚度减小。这个过程称为半导体晶片切割。我们使用专为微电子行业制造的自动贴片机来分拣半导体芯片的好坏。只封装好的、未标记的半导体芯片。接下来,在微电子塑料或陶瓷封装过程中,我们安装半导体管芯,将管芯焊盘连接到封装上的引脚,然后密封管芯。微小的金线用于使用自动化机器将焊盘连接到引脚。芯片级封装(CSP)是另一种微电子封装技术。与大多数封装一样,塑料双列直插式封装 (DIP) 比放置在内部的实际半导体管芯大几倍,而 CSP 芯片几乎与微电子管芯一样大;并且可以在半导体晶圆切割之前为每个裸片构建一个CSP。对封装后的微电子芯片进行重新测试,以确保它们在封装过程中没有损坏,并且芯片到引脚的互连过程正确完成。然后,我们使用激光蚀刻封装上的芯片名称和编号。
微电子封装设计和制造:我们提供微电子封装的现成和定制设计和制造。作为该服务的一部分,还进行了微电子封装的建模和仿真。建模和仿真确保了虚拟实验设计 (DoE) 以实现最佳解决方案,而不是在现场测试包。这降低了成本和生产时间,特别是对于微电子领域的新产品开发。这项工作还使我们有机会向我们的客户解释组装、可靠性和测试将如何影响他们的微电子产品。微电子封装的主要目标是设计一个电子系统,以合理的成本满足特定应用的要求。由于可用于互连和容纳微电子系统的选项有很多,因此为给定应用选择封装技术需要专家评估。微电子封装的选择标准可能包括以下一些技术驱动因素:
-可接线性
-屈服
-成本
-散热性能
-电磁屏蔽性能
-机械韧性
-可靠性
微电子封装的这些设计考虑因素会影响速度、功能、结温、体积、重量等。主要目标是选择最具成本效益但最可靠的互连技术。我们使用复杂的分析方法和软件来设计微电子封装。微电子封装涉及互连微型电子系统的制造方法的设计以及这些系统的可靠性。具体来说,微电子封装涉及在保持信号完整性的同时路由信号、为半导体集成电路分配接地和电源、在保持结构和材料完整性的同时分散散热,以及保护电路免受环境危害。通常,封装微电子 IC 的方法涉及使用带有连接器的 PWB,这些连接器为电子电路提供真实世界的 I/O。传统的微电子封装方法涉及使用单个封装。单芯片封装的主要优点是能够在将微电子 IC 互连到底层基板之前对其进行全面测试。这种封装的半导体器件要么通孔安装,要么表面安装到PWB。表面贴装微电子封装不需要通孔穿过整个电路板。相反,表面安装的微电子元件可以焊接到 PWB 的两侧,从而实现更高的电路密度。这种方法称为表面贴装技术 (SMT)。球栅阵列 (BGA) 和芯片级封装 (CSP) 等面阵列式封装的增加使 SMT 与最高密度的半导体微电子封装技术具有竞争力。一种较新的封装技术涉及将多个半导体器件连接到高密度互连基板上,然后将其安装在一个大封装中,提供 I/O 引脚和环境保护。这种多芯片模块 (MCM) 技术的进一步特点是用于互连连接的 IC 的基板技术。 MCM-D 代表沉积的薄膜金属和电介质多层。由于先进的半导体加工技术,MCM-D 基板在所有 MCM 技术中具有最高的布线密度。 MCM-C 是指多层“陶瓷”基材,由经过筛选的金属油墨和未烧制的陶瓷片堆叠交替层烧制而成。使用 MCM-C,我们获得了中等密集的布线容量。 MCM-L 是指由堆叠的金属化 PWB“层压板”制成的多层基板,这些基板经过单独图案化然后层压。它曾经是一种低密度互连技术,但现在 MCM-L 正在迅速接近 MCM-C 和 MCM-D 微电子封装技术的密度。直接芯片连接 (DCA) 或板上芯片 (COB) 微电子封装技术涉及将微电子 IC 直接安装到 PWB。一种塑料封装剂,它被“覆盖”在裸露的 IC 上,然后固化,提供了环境保护。微电子 IC 可以使用倒装芯片或引线键合方法与基板互连。 DCA 技术对于限制在 10 个或更少半导体 IC 的系统特别经济,因为大量芯片会影响系统良率并且 DCA 组件可能难以返工。 DCA 和 MCM 封装选项的一个共同优势是消除了半导体 IC 封装互连级别,这允许更接近(更短的信号传输延迟)并减少引线电感。这两种方法的主要缺点是难以购买经过全面测试的微电子 IC。 DCA 和 MCM-L 技术的其他缺点包括由于 PWB 层压板的低热导率以及半导体芯片和基板之间的热膨胀系数匹配差而导致的热管理不良。解决热膨胀失配问题需要一个中介基板,例如用于引线键合芯片的钼和用于倒装芯片芯片的底部填充环氧树脂。多芯片载体模块 (MCCM) 将 DCA 的所有积极方面与 MCM 技术相结合。 MCCM 只是一个薄金属载体上的小型 MCM,可以粘合或机械连接到 PWB。金属底部作为 MCM 基板的散热器和应力中介层。 MCCM 具有用于引线键合、焊接或接线片键合到 PWB 的外围引线。裸露的半导体 IC 使用球形顶部材料进行保护。当您联系我们时,我们将讨论您的应用和要求,为您选择最佳的微电子封装选项。
半导体 IC 组装与封装与测试:作为我们微电子制造服务的一部分,我们提供芯片、引线和芯片键合、封装、组装、标记和品牌推广、测试。为了使半导体芯片或集成微电子电路发挥作用,它需要连接到它将控制或提供指令的系统。微电子集成电路组件确实为芯片和系统之间的电源和信息传输提供了连接。这是通过将微电子芯片连接到封装或将其直接连接到 PCB 来实现这些功能的。芯片与封装或印刷电路板 (PCB) 之间的连接是通过引线键合、通孔或倒装芯片组装实现的。我们是寻找微电子 IC 封装解决方案以满足无线和互联网市场复杂要求的行业领导者。我们提供数千种不同的封装格式和尺寸,从用于通孔和表面贴装的传统引线框架微电子 IC 封装,到高引脚数和高密度应用所需的最新芯片级 (CSP) 和球栅阵列 (BGA) 解决方案.有多种封装可供现货供应,包括 CABGA(芯片阵列 BGA)、CQFP、CTBGA(芯片阵列薄核 BGA)、CVBGA(超薄芯片阵列 BGA)、倒装芯片、LCC、LGA、MQFP、PBGA、PDIP、 PLCC、PoP - Package on Package、PoP TMV - Through Mold Via、SOIC / SOJ、SSOP、TQFP、TSOP、WLP(晶圆级封装)……等。使用铜、银或金的引线键合在微电子领域很流行。铜 (Cu) 线是一种将硅半导体管芯连接到微电子封装端子的方法。随着最近金 (Au) 线成本的增加,铜 (Cu) 线是管理微电子整体封装成本的一种有吸引力的方式。由于其相似的电气特性,它也类似于金 (Au) 线。金 (Au) 和铜 (Cu) 线的自感和自电容几乎相同,而铜 (Cu) 线的电阻率较低。在微电子应用中,由于键合线的电阻会对电路性能产生负面影响,使用铜 (Cu) 线可以提供改进。由于成本原因,铜、镀钯铜 (PCC) 和银 (Ag) 合金线已成为金键合线的替代品。铜基线价格低廉,电阻率低。然而,铜的硬度使其难以在许多应用中使用,例如那些具有易碎焊盘结构的应用。对于这些应用,Ag-Alloy 提供与金相似的特性,而其成本与 PCC 相似。 Ag-Alloy 线比 PCC 更柔软,从而降低 Al-Splash 和降低焊盘损坏的风险。银合金线是需要芯片对芯片键合、瀑布键合、超细键合焊盘间距和小键合焊盘开口、超低环路高度的应用的最佳低成本替代品。我们提供全方位的半导体测试服务,包括晶圆测试、各种类型的最终测试、系统级测试、条带测试和完整的生产线终端服务。我们在所有封装系列中测试各种半导体器件类型,包括射频、模拟和混合信号、数字、电源管理、内存和各种组合,例如 ASIC、多芯片模块、系统级封装 (SiP) 和堆叠式 3D 封装、传感器和 MEMS 设备,例如加速度计和压力传感器。我们的测试硬件和接触设备适用于定制封装尺寸 SiP、封装上封装 (PoP) 的双面接触解决方案、TMV PoP、FusionQuad 插座、多排 MicroLeadFrame、细间距铜柱。测试设备和测试台与 CIM / CAM 工具、良率分析和性能监控集成在一起,可在第一时间提供非常高的良率。我们为客户提供众多自适应微电子测试流程,并为 SiP 和其他复杂装配流程提供分布式测试流程。 AGS-TECH 为您的整个半导体和微电子产品生命周期提供全方位的测试咨询、开发和工程服务。我们了解 SiP、汽车、网络、游戏、图形、计算、RF/无线的独特市场和测试要求。半导体制造过程需要快速且精确控制的标记解决方案。超过 1000 个字符/秒的打标速度和小于 25 微米的材料穿透深度在使用先进激光器的半导体微电子行业中很常见。我们能够以最少的热输入和完美的可重复性标记模具化合物、晶片、陶瓷等。我们使用高精度激光打标,即使是最小的零件也不会损坏。
半导体设备的引线框架:现成的和定制的设计和制造都是可能的。引线框架用于半导体器件组装过程,本质上是薄金属层,将半导体微电子表面上的微小电气端子的布线连接到电气器件和 PCB 上的大规模电路。几乎所有的半导体微电子封装都使用引线框架。大多数微电子集成电路封装是通过将半导体硅芯片放置在引线框架上,然后将芯片引线键合到该引线框架的金属引线上,然后用塑料盖覆盖微电子芯片。这种简单且成本相对较低的微电子封装仍然是许多应用的最佳解决方案。引线框架以长条形式生产,这使得它们可以在自动化装配机上快速加工,通常使用两种制造工艺:某种光刻和冲压。在微电子引线框架设计中,通常需要定制规格和功能、增强电气和热性能的设计以及特定的周期时间要求。我们在使用激光辅助光刻和冲压为一系列不同客户制造微电子引线框架方面拥有丰富的经验。
微电子散热器的设计和制造:现成的和定制的设计和制造。随着微电子器件散热的增加和整体外形尺寸的减小,热管理成为电子产品设计中更加重要的元素。电子设备性能和寿命的一致性与设备的元件温度成反比。典型硅半导体器件的可靠性和工作温度之间的关系表明,温度的降低对应于器件可靠性和预期寿命的指数增长。因此,通过将器件工作温度有效控制在设计人员设定的范围内,可以实现半导体微电子元件的长寿命和可靠性能。散热器是增强从热表面(通常是发热组件的外壳)到较冷环境(例如空气)的散热的装置。对于以下讨论,假设空气是冷却流体。在大多数情况下,固体表面和冷却空气之间的界面上的热传递在系统内效率最低,而固体-空气界面代表了最大的散热障碍。散热器主要通过增加与冷却剂直接接触的表面积来降低此障碍。这允许散发更多热量和/或降低半导体器件的工作温度。散热器的主要目的是将微电子器件的温度保持在半导体器件制造商规定的最大允许温度以下。
我们可以根据制造方法及其形状对散热器进行分类。最常见的风冷散热器类型包括:
- 冲压件:将铜或铝金属片冲压成所需的形状。它们用于电子元件的传统空气冷却,并为低密度热问题提供经济的解决方案。它们适用于大批量生产。
- 挤压:这些散热器可以形成精细的二维形状,能够消散大量的热负荷。它们可以被切割、加工和添加选项。横切将生产全方位的矩形针翅式散热器,并结合锯齿状翅片将性能提高约 10% 至 20%,但挤出速度较慢。挤压限制,例如翅片高度到间隙翅片厚度,通常决定了设计选项的灵活性。使用标准挤压技术可实现高达 6 的典型翅片高度与间隙纵横比和 1.3 毫米的最小翅片厚度。通过特殊的模具设计特征可以获得 10 比 1 的纵横比和 0.8 英寸的翅片厚度。然而,随着纵横比的增加,挤压公差会受到影响。
- 粘合/装配式翅片:大多数风冷散热器都受到对流限制,如果更多的表面积可以暴露在气流中,风冷散热器的整体热性能通常可以显着提高。这些高性能散热器利用导热铝填充环氧树脂将平面翅片粘合到带槽的挤压基板上。这个过程允许更大的翅片高度与间隙的纵横比为 20 到 40,显着提高冷却能力而不增加体积需求。
- 铸件:铝或铜/青铜的砂、失蜡和压铸工艺可使用或不使用真空辅助。我们使用这项技术制造高密度针翅式散热器,在使用冲击冷却时提供最佳性能。
- 折叠翅片:由铝或铜制成的波纹金属板增加了表面积和体积性能。然后将散热器连接到基板或通过环氧树脂或钎焊直接连接到加热表面。考虑到可用性和翅片效率,它不适用于高配置散热器。因此,它允许制造高性能散热器。
在为您的微电子应用选择满足所需热标准的合适散热器时,我们需要检查各种参数,这些参数不仅会影响散热器本身的性能,还会影响系统的整体性能。微电子中特定类型的散热器的选择很大程度上取决于散热器允许的热预算和散热器周围的外部条件。从来没有为给定的散热器分配一个单一的热阻值,因为热阻随外部冷却条件而变化。
传感器和执行器设计与制造:可提供现成和定制设计与制造。我们为惯性传感器、压力和相对压力传感器以及红外温度传感器设备提供具有即用型工艺的解决方案。通过将我们的 IP 模块用于加速度计、IR 和压力传感器,或者根据可用的规范和设计规则应用您的设计,我们可以在几周内将基于 MEMS 的传感器设备交付给您。除了 MEMS,还可以制造其他类型的传感器和致动器结构。
光电和光子电路设计和制造:光子或光学集成电路 (PIC) 是一种集成多种光子功能的器件。它可以类似于微电子学中的电子集成电路。两者的主要区别在于光子集成电路为施加在可见光谱或近红外 850 nm-1650 nm 的光波长上的信息信号提供功能。制造技术与微电子集成电路中使用的技术相似,在微电子集成电路中,使用光刻技术对晶圆进行图案化以进行蚀刻和材料沉积。与主要器件是晶体管的半导体微电子学不同,光电子学中没有单一的主导器件。光子芯片包括低损耗互连波导、功率分配器、光放大器、光调制器、滤波器、激光器和检测器。这些设备需要各种不同的材料和制造技术,因此很难在单个芯片上实现所有这些。我们光子集成电路的应用主要在光纤通信、生物医学和光子计算领域。我们可以为您设计和制造的一些示例光电产品包括 LED(发光二极管)、二极管激光器、光电接收器、光电二极管、激光测距模块、定制激光模块等。