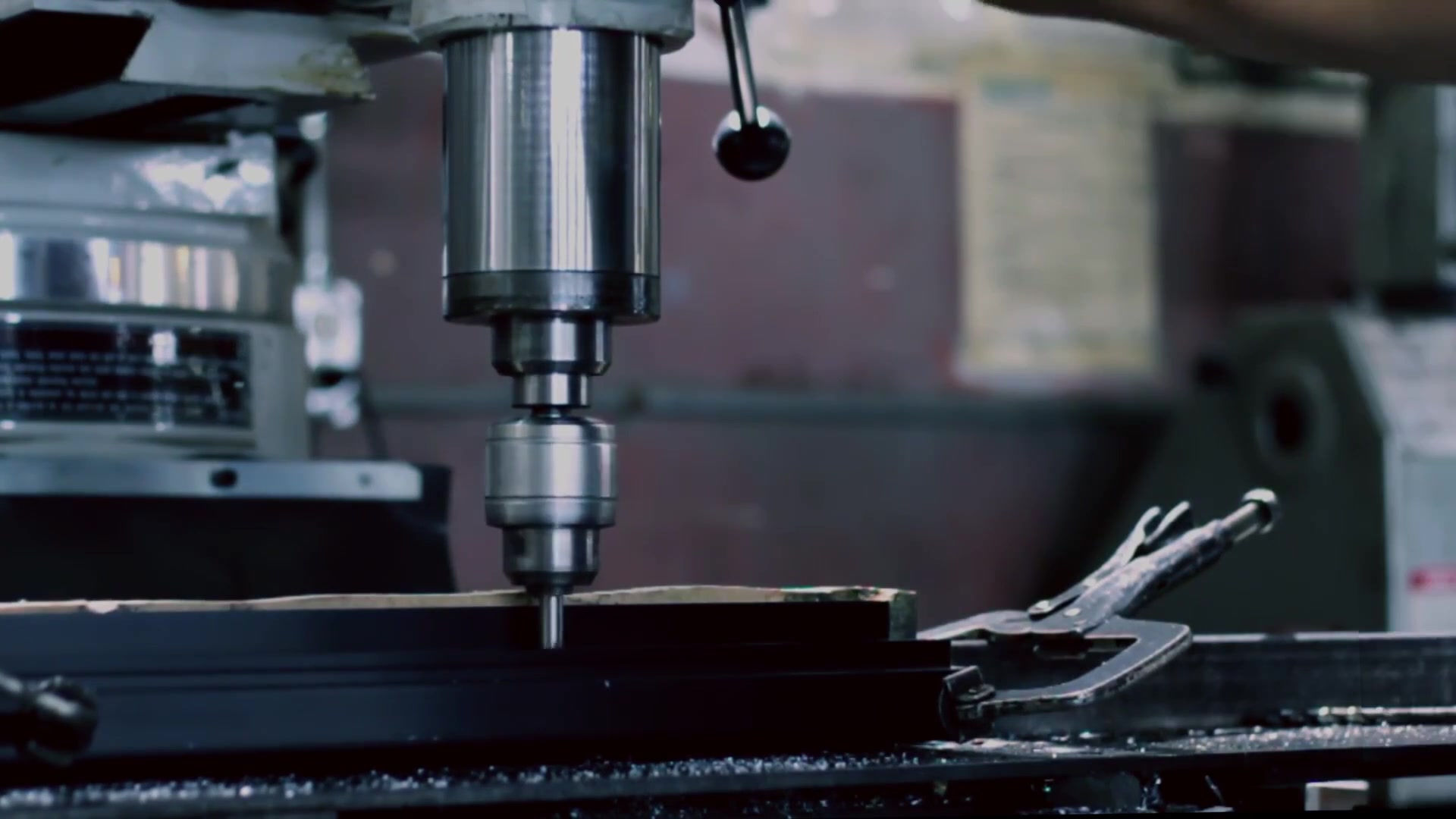
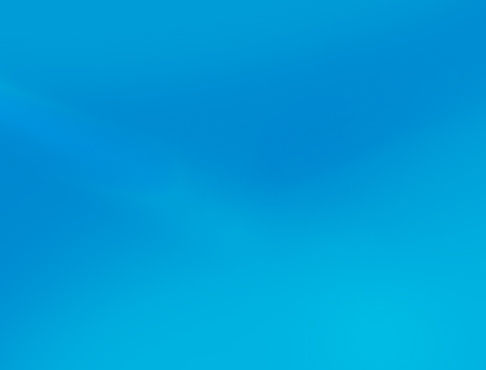
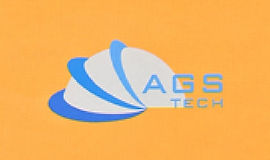
全球定制制造商、集成商、整合商、各种产品和服务的外包合作伙伴。
我们是您定制制造和现成产品和服务的制造、制造、工程、整合、集成、外包的一站式来源。
Choose your Language
-
定制制造
-
国内和全球合同制造
-
制造外包
-
国内及全球采购
-
Consolidation
-
工程集成
-
工程服务
Another popular NON-CONVENTIONAL MACHINING technique we frequently use is ULTRASONIC MACHINING (UM), also widely known as ULTRASONIC冲击磨削,其中材料通过微碎屑和磨粒侵蚀从工件表面去除,使用以超声波频率振荡的振动工具,借助在工件和工具之间自由流动的磨料浆。它与大多数其他传统加工操作不同,因为它产生的热量非常少。超声波加工工具的尖端称为“超声焊极”,其振动幅度为 0.05 至 0.125 mm,频率约为 20 kHz。尖端的振动将高速传递到工具和工件表面之间的细磨粒。该工具从不接触工件,因此磨削压力很少超过 2 磅。这种工作原理使这种操作非常适合加工极硬和易碎的材料,例如玻璃、蓝宝石、红宝石、钻石和陶瓷。磨粒位于浓度为 20 至 60%(体积)的水浆中。浆料还充当远离切割/加工区域的碎屑的载体。我们主要使用碳化硼、氧化铝和碳化硅作为磨粒,粒度从粗加工的 100 到精加工的 1000 不等。超声波加工 (UM) 技术最适用于硬脆材料,如陶瓷和玻璃、碳化物、宝石、硬化钢。超声波加工的表面光洁度取决于工件/工具的硬度和所用磨粒的平均直径。刀尖通常是低碳钢、镍和软钢,通过刀架连接到换能器上。超声波加工过程利用金属的塑性变形作为工具和工件的脆性。工具振动并向下推动含有颗粒的磨料浆,直到颗粒撞击脆性工件。在此操作过程中,工件被分解,同时工具非常轻微弯曲。使用精细磨料,我们可以实现 0.0125 毫米的尺寸公差,使用超声波加工 (UM) 甚至可以达到更好的效果。加工时间取决于工具的振动频率、晶粒尺寸和硬度以及浆液的粘度。浆液的粘度越低,它带走用过的磨料的速度就越快。晶粒尺寸必须等于或大于工件的硬度。例如,我们可以通过超声波加工在 1.2 毫米宽的玻璃条上加工多个直径为 0.4 毫米的对齐孔。
让我们稍微了解一下超声波加工过程的物理特性。由于颗粒撞击固体表面产生的高应力,超声波加工中的微碎屑成为可能。颗粒和表面之间的接触时间非常短,大约为 10 到 100 微秒。接触时间可以表示为:
to = 5r/Co x (Co/v) exp 1/5
这里 r 是球形粒子的半径,Co 是工件中的弹性波速度 (Co = sqroot E/d),v 是粒子撞击表面的速度。
粒子施加在表面上的力由动量变化率获得:
F = d(mv)/dt
这里 m 是颗粒质量。颗粒(颗粒)从表面撞击和反弹的平均力为:
Favg = 2mv / to
这里是联系时间。当将数字插入该表达式时,我们看到即使零件非常小,由于接触面积也非常小,因此施加的力和应力非常高,从而导致微碎裂和腐蚀。
旋转超声波加工 (RUM):这种方法是超声波加工的一种变体,我们用一种工具替换磨料浆,该工具具有金属结合的金刚石磨料,这些磨料在工具表面浸渍或电镀。该工具被旋转和超声波振动。我们以恒定的压力将工件压在旋转和振动的工具上。旋转超声波加工工艺使我们能够以高材料去除率在硬质材料上加工深孔。
由于我们部署了许多传统和非常规制造技术,因此每当您对特定产品以及最快、最经济的制造和制造方式有任何疑问时,我们都可以为您提供帮助。