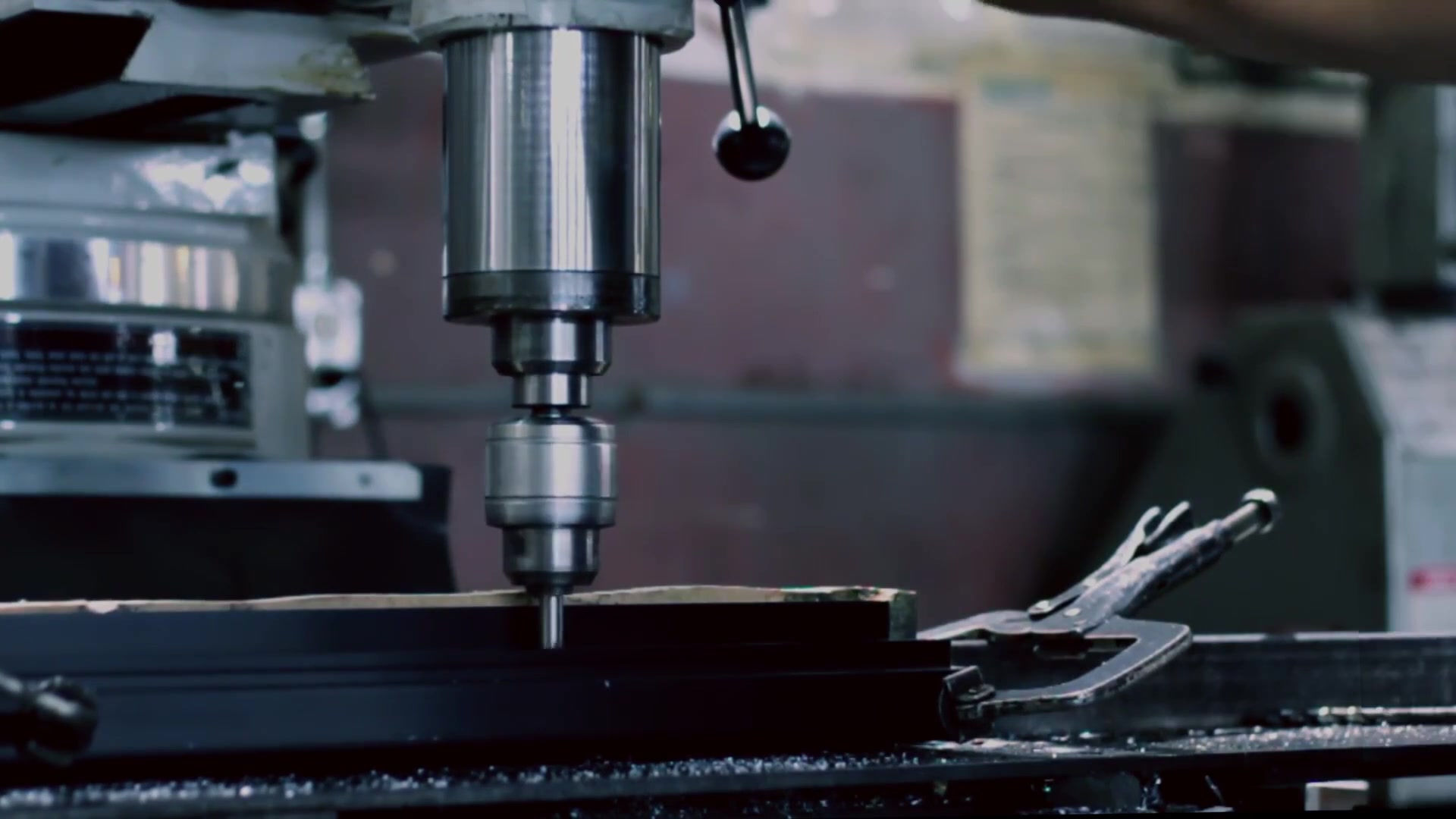
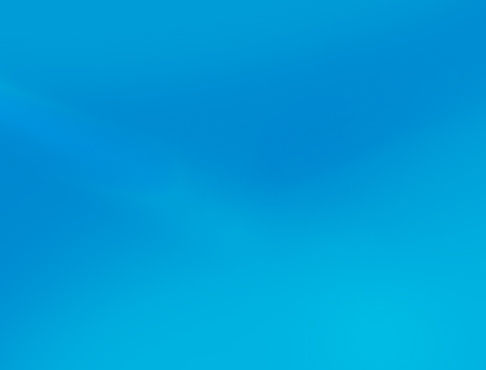
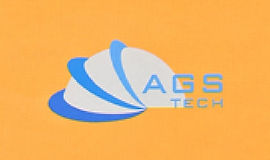
Globale pasgemaakte vervaardiger, integreerder, konsolideerder, uitkontrakteringsvennoot vir 'n wye verskeidenheid produkte en dienste.
Ons is jou eenstopbron vir vervaardiging, vervaardiging, ingenieurswese, konsolidasie, integrasie, uitkontraktering van pasgemaakte en van die rak produkte en dienste af.
Kies jou taal
-
Pasgemaakte vervaardiging
-
Binnelandse en globale kontrakvervaardiging
-
Vervaardiging Uitkontraktering
-
Binnelandse en globale verkryging
-
Consolidation
-
Ingenieursintegrasie
-
Ingenieursdienste
Die tipe glasvervaardiging wat ons aanbied, is houerglas, glasblaas, glasvesel & buise & staaf, huishoudelike en industriële glasware, lamp en gloeilamp, presisie glasgietwerk, optiese komponente en samestellings, plat & plaat & floatglas. Ons voer beide handvorming sowel as masjienvorming uit.
Ons gewilde tegniese keramiekvervaardigingsprosesse is matryspers, isostatiese pers, warm isostatiese pers, warm pers, glipgiet, bandgiet, ekstrusie, spuitgiet, groen bewerking, sinter of brand, diamantslyp, hermetiese samestellings.
Ons beveel aan dat jy hier klik om
Laai ons skematiese illustrasies van glasvorming en -vormingsprosesse af deur AGS-TECH Inc.
Laai ons skematiese illustrasies af van tegniese keramiekvervaardigingsprosesse deur AGS-TECH Inc.
Hierdie aflaaibare lêers met foto's en sketse sal jou help om die inligting wat ons hieronder verskaf beter te verstaan.
• HOUERGLAS VERVAARDIGING: Ons het geoutomatiseerde DRUK EN BLAAS sowel as BLAAS EN BLAAS lyne vir vervaardiging. In die blaas-en-blaas-proses laat ons 'n gob in leë vorm val en vorm die nek deur 'n blaas saamgeperste lug van bo af toe te dien. Onmiddellik hierna word saamgeperste lug 'n tweede keer van die ander rigting deur die houernek geblaas om die voorvorm van die bottel te vorm. Hierdie voorvorm word dan na die werklike vorm oorgedra, herverhit om sag te word en saamgeperste lug word toegedien om die voorvorm sy finale houervorm te gee. Meer eksplisiet word dit onder druk geplaas en teen die mure van die blaasvormholte gedruk om die gewenste vorm aan te neem. Laastens word die vervaardigde glashouer in 'n uitgloeioond oorgeplaas vir daaropvolgende herverhitting en verwydering van spanning wat tydens die gietvorm ontstaan en word op 'n beheerde wyse afgekoel. In die pers-en-blaas-metode word gesmelte gobs in 'n parison-vorm (blanko vorm) geplaas en in die parison-vorm (leë vorm) gedruk. Die spasies word dan na blaasvorms oorgeplaas en geblaas soortgelyk aan die proses wat hierbo beskryf is onder "Blas en Blaas Proses". Daaropvolgende stappe soos uitgloeiing en spanningsverligting is soortgelyk of dieselfde.
• GLASBLAAIS: Ons vervaardig glasprodukte deur gebruik te maak van konvensionele handblaas sowel as die gebruik van saamgeperste lug met outomatiese toerusting. Vir sommige bestellings is konvensionele blaas nodig, soos projekte wat glaskunswerk behels, of projekte wat 'n kleiner aantal onderdele met los toleransies benodig, prototipering/demo-projekte ….ens. Konvensionele glasblaas behels die doop van 'n hol metaalpyp in 'n pot gesmelte glas en draai die pyp om 'n mate van die glasmateriaal te versamel. Die glas wat op die punt van die pyp versamel word, word op plat yster gerol, gevorm soos verlang, verleng, herverhit en lug geblaas. Wanneer dit gereed is, word dit in 'n vorm geplaas en lug word geblaas. Die vormholte is nat om kontak van die glas met metaal te vermy. Die waterfilm dien soos 'n kussing tussen hulle. Handblaas is 'n arbeidsintensiewe stadige proses en slegs geskik vir prototipering of items van hoë waarde, nie geskik vir goedkoop per stuk hoë volume bestellings nie.
• VERVAARDIGING VAN HUISLIKE EN INDUSTRIËLE GLASWERK: Deur verskeie tipes glasmateriaal te gebruik, word 'n groot verskeidenheid glasware vervaardig. Sommige glase is hittebestand en geskik vir laboratoriumglasware, terwyl sommige goed genoeg is om skottelgoedwassers baie keer te weerstaan en geskik is om huishoudelike produkte te maak. Met behulp van Westlake-masjiene word tienduisende stukke drinkglase per dag vervaardig. Om dit te vereenvoudig, word gesmelte glas deur vakuum versamel en in vorms geplaas om die voorvorms te maak. Dan word lug in die vorms geblaas, dit word na 'n ander vorm oorgeplaas en lug word weer geblaas en die glas neem sy finale vorm aan. Soos in die handblaas, word hierdie vorms nat gehou met water. Verdere strek is deel van die afrondingsoperasie waar die nek gevorm word. Oortollige glas word afgebrand. Daarna volg die beheerde herverhitting en verkoelingsproses hierbo beskryf.
• GLASBUIS EN -STAAFVORMING: Die hoofprosesse wat ons gebruik vir die vervaardiging van glasbuise is die DANNER- en VELLO-prosesse. In die Danner-proses vloei glas uit 'n oond en val dit op 'n skuins huls wat van vuurvaste materiale gemaak is. Die huls word op 'n roterende hol as of blaaspyp gedra. Die glas word dan om die mou gedraai en vorm 'n gladde laag wat langs die mou af en oor die punt van die skag vloei. In die geval van buisvorming word lug deur 'n blaaspyp met hol punt geblaas, en in die geval van staafvorming gebruik ons soliede punte op die as. Die buise of stawe word dan oor drarolle getrek. Die afmetings soos wanddikte en deursnee van die glasbuise word na verlangde waardes aangepas deur die deursnee van die huls te stel en lugdruk op 'n gewenste waarde te blaas, die temperatuur, tempo van vloei van glas en spoed van trek aan te pas. Die Vello-glasbuisvervaardigingsproses behels aan die ander kant glas wat uit 'n oond beweeg en in 'n bak met 'n hol deurn of klok. Die glas gaan dan deur die lugruimte tussen die deur en die bak en neem die vorm van 'n buis aan. Daarna beweeg dit oor rollers na 'n tekenmasjien en word afgekoel. Aan die einde van die koellyn vind sny en finale verwerking plaas. Die buisafmetings kan net soos in die Danner-proses aangepas word. Wanneer ons die Danner- met Vello-proses vergelyk, kan ons sê dat die Vello-proses beter geskik is vir groot hoeveelhede produksie, terwyl die Danner-proses beter geskik is vir presiese kleiner volume buisbestellings.
• VERWERKING VAN PLAAT- & PLAT- & FLATGLAS: Ons het groot hoeveelhede plat glas in diktes wat wissel van submilimeterdiktes tot etlike sentimeters. Ons plat glase is van byna optiese perfeksie. Ons bied glas met spesiale bedekkings soos optiese bedekkings, waar chemiese dampneerslagtegniek gebruik word om bedekkings soos antirefleksie of spieëlbedekking te plaas. Ook deursigtige geleidende bedekkings is algemeen. Ook beskikbaar is hidrofobiese of hidrofiele bedekkings op glas, en bedekking wat glas selfreinigend maak. Geharde, koeëlvaste en gelamineerde glase is nog ander gewilde items. Ons sny glas in gewenste vorm met verlangde toleransies. Ander sekondêre bewerkings soos buiging of buiging van plat glas is beskikbaar.
• PRESISIE GLAS VOER: Ons gebruik hierdie tegniek meestal vir die vervaardiging van presisie optiese komponente sonder die behoefte aan duurder en tydrowende tegnieke soos slyp, lap en poleer. Hierdie tegniek is nie altyd voldoende om die beste van die beste optika te maak nie, maar in sommige gevalle, soos verbruikersprodukte, digitale kameras, mediese optika, kan dit 'n goedkoper goeie opsie wees vir hoëvolume-vervaardiging. Dit het ook 'n voordeel bo die ander glasvormingstegnieke waar komplekse geometrieë vereis word, soos in die geval van asfere. Die basiese proses behels die laai van die onderkant van ons vorm met die glas leeg, ontruiming van die proseskamer vir suurstofverwydering, naby sluiting van die vorm, vinnige en isotermiese verhitting van die matrys en glas met infrarooi lig, verdere sluiting van die vormhelftes om die versagte glas stadig op 'n beheerde wyse tot die verlangde dikte te druk, en uiteindelik die glas af te koel en die kamer met stikstof te vul en die produk te verwyder. Presiese temperatuurbeheer, vorm sluiting afstand, vorm sluiting krag, wat ooreenstem met die koëffisiënte van uitsetting van die vorm en glas materiaal is die sleutel in hierdie proses.
• VERVAARDIGING VAN OPTIESE KOMPONENTE EN SAMESTELLINGS VAN GLAS: Benewens presisie glasgietwerk, is daar 'n aantal waardevolle prosesse wat ons gebruik om optiese komponente en samestellings van hoë gehalte vir veeleisende toepassings te maak. Slyp, lap en poleer van optiese graad glase in fyn spesiale skuur slurries is 'n kuns en wetenskap vir die maak van optiese lense, prismas, flats en meer. Oppervlakvlakheid, golwendheid, gladheid en defekvrye optiese oppervlaktes vereis baie ondervinding met sulke prosesse. Klein veranderinge in omgewing kan lei tot produkte wat nie meer spesifikasies is nie en die vervaardigingslyn tot stilstand bring. Daar is gevalle waar 'n enkele vee op die optiese oppervlak met 'n skoon lap 'n produk aan die spesifikasies kan laat voldoen of die toets kan druip. Sommige gewilde glasmateriaal wat gebruik word, is saamgesmelte silika, kwarts, BK7. Ook die samestelling van sulke komponente vereis gespesialiseerde nis-ervaring. Soms word spesiale gom gebruik. Soms is 'n tegniek genaamd optiese kontak egter die beste keuse en behels geen materiaal tussen aangehegte optiese bril nie. Dit bestaan uit fisiese kontak met plat oppervlaktes om sonder gom aan mekaar te heg. In sommige gevalle word meganiese spasieerders, presisieglasstawe of -balle, klampe of bewerkte metaalkomponente gebruik om die optiese komponente op sekere afstande en met sekere geometriese oriëntasies na mekaar te monteer. Kom ons ondersoek sommige van ons gewilde tegnieke vir die vervaardiging van hoë-end optika.
SLYP & LAPPING & POLIERING: Die growwe vorm van die optiese komponent word verkry deur 'n glasblanko te maal. Daarna word lap en polering uitgevoer deur die ruwe oppervlaktes van die optiese komponente te draai en te vryf teen gereedskap met gewenste oppervlakvorms. Slakke met klein skuurdeeltjies en vloeistof word tussen die optika en die vormgereedskap ingegooi. Die skuurdeeltjiegroottes in sulke slurries kan gekies word volgens die verlangde mate van platheid. Die afwykings van kritieke optiese oppervlaktes van gewenste vorms word uitgedruk in terme van golflengtes van die lig wat gebruik word. Ons hoë-presisie-optika het tiende van 'n golflengte (golflengte/10) toleransies of selfs strenger is moontlik. Behalwe oppervlakprofiel, word die kritieke oppervlaktes geskandeer en geëvalueer vir ander oppervlakkenmerke en defekte soos afmetings, skrape, skyfies, putte, spikkels ... ens. Die streng beheer van omgewingstoestande in die optiese vervaardigingsvloer en uitgebreide metrologie- en toetsvereistes met die nuutste toerusting maak dit 'n uitdagende tak van die industrie.
• SEKONDÊRE PROSESSE IN GLASVERVAARDIGING: Weereens, ons is net beperk met jou verbeelding wanneer dit kom by sekondêre en afwerkingsprosesse van glas. Hier lys ons 'n paar van hulle:
-Bedekkings op glas (opties, elektries, tribologies, termies, funksioneel, meganies...). As 'n voorbeeld kan ons oppervlak-eienskappe van glas verander sodat dit byvoorbeeld hitte weerkaats sodat dit die gebou se binnekant koel hou, of eenkant infrarooi absorberend maak deur nanotegnologie te gebruik. Dit help om die binnekant van geboue warm te hou omdat die buitenste oppervlaklaag glas die infrarooi straling binne die gebou sal absorbeer en dit na binne sal terugstraal.
-Ets op glas
- Toegepaste keramieketikettering (ACL)
- Gravure
-Vlam poleer
- Chemiese polering
- Verkleuring
VERVAARDIGING VAN TEGNIESE KERAMIEK
• STERFPERSING: Bestaan uit eenassige verdigting van korrelpoeiers wat in 'n matrys opgesluit is
• WARMPERSING: Soortgelyk aan die pers maar met die byvoeging van temperatuur om verdigting te verbeter. Poeier of gekompakteerde voorvorm word in grafietmatrys geplaas en eenassige druk word toegepas terwyl die matrys by hoë temperature soos 2000 C gehou word. Temperature kan verskil afhangende van die tipe keramiekpoeier wat verwerk word. Vir ingewikkelde vorms en geometrieë kan ander daaropvolgende verwerking soos diamantslyp nodig wees.
• ISOSTATIESE PERSING : Korrelpoeier of stanspers word in lugdigte houers geplaas en dan in 'n geslote drukhouer met vloeistof binne. Daarna word hulle gekompakteer deur die drukhouer se druk te verhoog. Die vloeistof binne die houer dra die drukkragte eenvormig oor die hele oppervlak van die lugdigte houer oor. Die materiaal word dus eenvormig gekompakteer en neem die vorm aan van sy buigsame houer en sy interne profiel en kenmerke.
• WARM ISOSTATIESE PERSING : Soortgelyk aan isostatiese persing, maar benewens drukgas-atmosfeer, sinter ons die kompak by hoë temperatuur. Warm isostatiese pers lei tot bykomende verdigting en verhoogde sterkte.
• SLIPGIETEN / DREINEERGIETEN: Ons vul die vorm met 'n suspensie van mikrometergrootte keramiekdeeltjies en draervloeistof. Hierdie mengsel word "glip" genoem. Die vorm het porieë en daarom word die vloeistof in die mengsel in die vorm gefiltreer. As gevolg hiervan word 'n gietvorm op die binne-oppervlaktes van die vorm gevorm. Na sintering kan die dele uit die vorm gehaal word.
• BANDGOOI: Ons vervaardig keramiekbande deur keramiekflotte op plat bewegende draeroppervlaktes te giet. Die flodders bevat keramiekpoeiers gemeng met ander chemikalieë vir bind- en dradoeleindes. Soos die oplosmiddels verdamp, word digte en buigsame velle keramiek agtergelaat wat na wense gesny of gerol kan word.
• EKSTRUSIEVORMING: Soos in ander ekstrusieprosesse, word 'n sagte mengsel van keramiekpoeier met bindmiddels en ander chemikalieë deur 'n matrys gevoer om sy deursneevorm te verkry en dan op verlangde lengtes gesny. Die proses word uitgevoer met koue of verhitte keramiekmengsels.
• LAEDRUK INSPUITVORMING: Ons berei 'n mengsel van keramiekpoeier met bindmiddels en oplosmiddels voor en verhit dit tot 'n temperatuur waar dit maklik in die gereedskapholte gedruk en ingedruk kan word. Sodra die gietsiklus voltooi is, word die deel uitgewerp en die bindmiddel word afgebrand. Deur spuitgietwerk te gebruik, kan ons ingewikkelde onderdele teen hoë volumes ekonomies verkry. Gate wat 'n klein fraksie van 'n millimeter op 'n 10mm dik muur is, is moontlik, skroefdraad is moontlik sonder verdere bewerking, toleransies so nou as +/- 0.5% is moontlik en selfs laer wanneer onderdele gemasjineer word , wanddiktes in die orde van 0,5 mm tot 'n lengte van 12,5 mm is moontlik asook wanddiktes van 6,5 mm tot 'n lengte van 150 mm.
• GROEN MAJERING: Deur dieselfde metaalbewerkingsgereedskap te gebruik, kan ons geperste keramiekmateriaal masjineer terwyl dit nog sag soos kryt is. Toleransies van +/- 1% is moontlik. Vir beter toleransies gebruik ons diamantslyp.
• SINTERING of BRAND: Sintering maak volle verdigting moontlik. Beduidende krimping vind plaas op die groen kompakte dele, maar dit is nie 'n groot probleem nie aangesien ons hierdie dimensionele veranderinge in ag neem wanneer ons die onderdeel en gereedskap ontwerp. Poeierdeeltjies word aan mekaar gebind en porositeit wat deur die verdigtingsproses geïnduseer word, word in groot mate verwyder.
• DIAMANTSLYP: Die wêreld se hardste materiaal "diamant" word gebruik om harde materiale soos keramiek te slyp en presisieonderdele word verkry. Toleransies in die mikrometerreeks en baie gladde oppervlaktes word bereik. As gevolg van die koste daarvan, oorweeg ons hierdie tegniek slegs wanneer ons dit regtig nodig het.
• HERMETIESE SAMESTELLINGS is dié wat prakties gesproke geen uitruiling van materie, vaste stowwe, vloeistowwe of gasse tussen raakvlakke toelaat nie. Hermetiese verseëling is lugdig. Hermetiese elektroniese omhulsels is byvoorbeeld dié wat die sensitiewe binne-inhoud van 'n verpakte toestel ongedeerd hou deur vog, kontaminante of gasse. Niks is 100% hermeties nie, maar as ons van hermetisiteit praat, bedoel ons dit in praktiese terme, dat daar hermetisiteit is in die mate dat die lektempo so laag is dat die toestelle vir baie lang tye veilig is onder normale omgewingstoestande. Ons hermetiese samestellings bestaan uit metaal-, glas- en keramiekkomponente, metaal-keramiek, keramiek-metaal-keramiek, metaal-keramiek-metaal, metaal tot metaal, metaal-glas, metaal-glas-metaal, glas-metaal-glas, glas- metaal en glas tot glas en alle ander kombinasies van metaal-glas-keramiekbinding. Ons kan byvoorbeeld die keramiekkomponente met metaal bedek sodat hulle sterk aan ander komponente in die samestelling gebind kan word en uitstekende seëlvermoë het. Ons het die kundigheid om optiese vesels of deurvoere met metaal te bedek en dit aan die omhulsels te soldeer of te soldeer, so geen gasse gaan of lek in die omhulsels nie. Daarom word hulle gebruik vir die vervaardiging van elektroniese omhulsels om sensitiewe toestelle in te kap en hulle teen die buitenste atmosfeer te beskerm. Benewens hul uitstekende seëleienskappe, ander eienskappe soos die termiese uitsettingskoëffisiënt, vervormingsweerstand, nie-uitgassing aard, baie lang leeftyd, niegeleidende aard, termiese isolasie eienskappe, antistatiese aard ... ens. maak glas en keramiek materiaal die keuse vir sekere toepassings. Inligting oor ons fasiliteit wat keramiek-tot-metaal-toebehore vervaardig, hermetiese verseëling, vakuumdeurvoere, hoë en ultrahoë vakuum en vloeistofbeheerkomponente kan hier gevind word:Hermetiese komponente fabrieksbrosjure