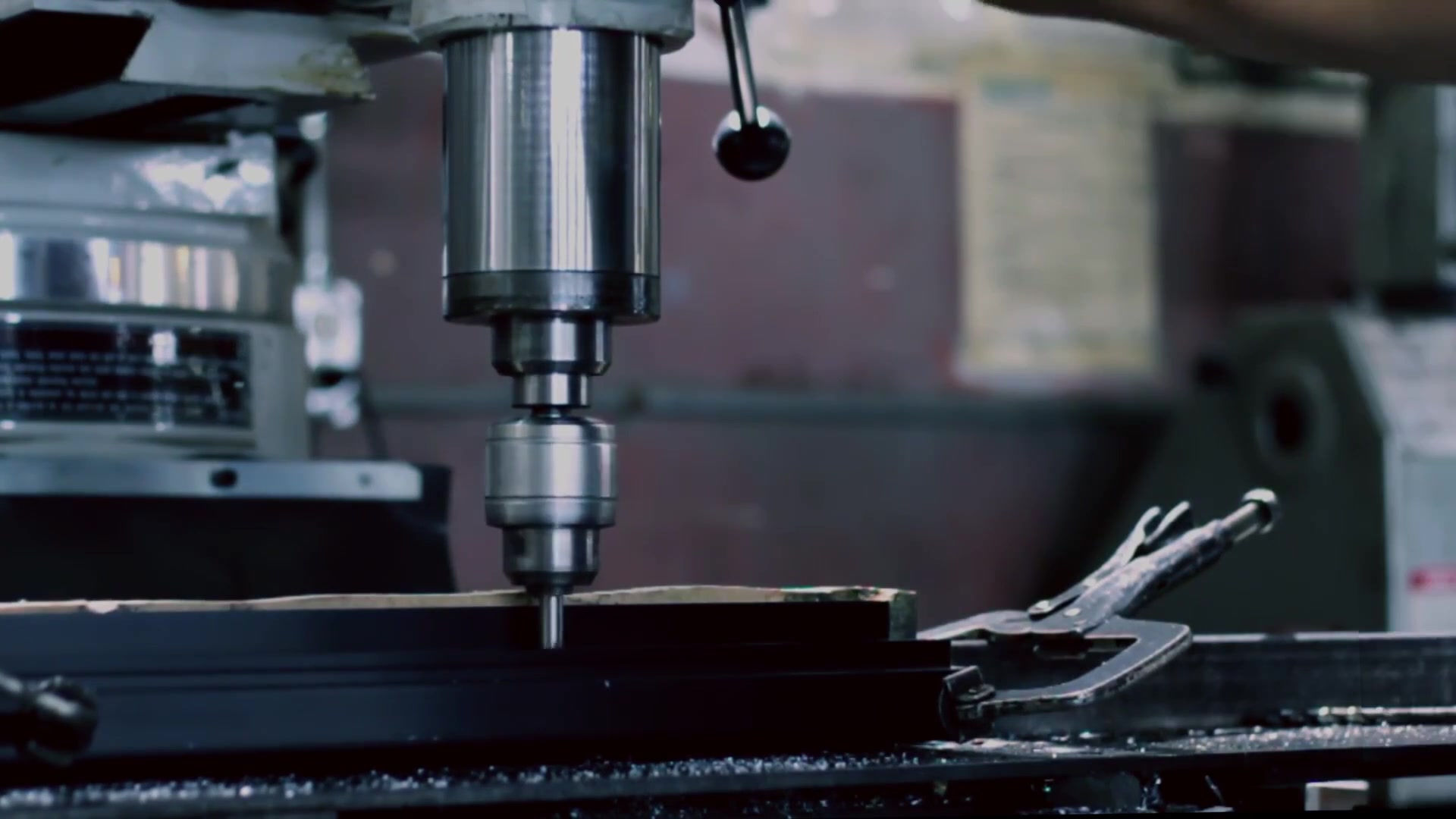
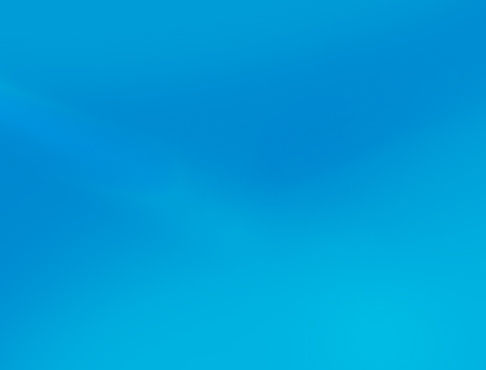
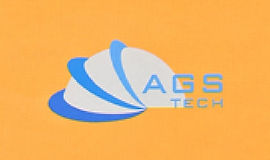
Глабальны індывідуальны вытворца, інтэгратар, кансалідатар, партнёр па аўтсорсінгу шырокага спектру прадуктаў і паслуг.
Мы ваша адзіная крыніца для вытворчасці, вырабу, праектавання, кансалідацыі, інтэграцыі, аўтсорсінгу вырабленых на заказ і гатовых прадуктаў і паслуг.
Выберыце мову
-
Вытворчасць на заказ
-
Унутраная і глабальная кантрактная вытворчасць
-
Аўтсорсінг вытворчасці
-
Унутраныя і сусветныя закупкі
-
Кансалідацыя
-
Інжынерная інтэграцыя
-
Інжынерныя паслугі
Тып вытворчасці шкла, які мы прапануем, - гэта тарнае шкло, выдзіманне шкла, шкловалакно, трубкі і стрыжні, бытавы і прамысловы шкляны посуд, лямпы і колбы, дакладнае ліццё шкла, аптычныя кампаненты і агрэгаты, плоскае і ліставае і флоат-шкло. Мы выконваем як ручную, так і машынную фармоўку.
Нашымі папулярнымі працэсамі вытворчасці тэхнічнай керамікі з'яўляюцца штампы, ізастатычнае прэсаванне, гарачае ізастатычнае прэсаванне, гарачае прэсаванне, шлікернае ліццё, стужкавае ліццё, экструзія, ліццё пад ціскам, апрацоўка без апрацоўкі, спяканне або абпал, алмазнае шліфаванне, герметычныя вузлы.
Мы рэкамендуем вам націснуць тут, каб
СПАМПУЙЦЕ нашы схематычныя ілюстрацыі працэсаў фармоўкі і фарміравання шкла ад AGS-TECH Inc.
СПАМПУЙЦЕ нашы схематычныя ілюстрацыі працэсаў вытворчасці тэхнічнай керамікі ад AGS-TECH Inc.
Гэтыя запампаваныя файлы з фотаздымкамі і эскізамі дапамогуць вам лепш зразумець інфармацыю, якую мы даем вам ніжэй.
• ВЫТВОРЧАСЦЬ ТАРЫ ШКЛА: у нас ёсць аўтаматызаваныя лініі Прэс і выдзімання, а таксама лініі выдзімання і выдзімання для вытворчасці. У працэсе выдзімання і выдзімання мы апускаем кавалачак у пустую форму і фарміруем гарлавіну, наносячы ўдар сціснутага паветра зверху. Адразу пасля гэтага сціснутае паветра другі раз прадзьмухваецца з іншага боку праз гарлавіну кантэйнера для фарміравання папярэдняй формы бутэлькі. Затым гэтая папярэдняя форма пераносіцца ў сапраўдную форму, зноў награваецца для змякчэння і падаецца сціснутае паветра, каб надаць папярэдняй форме канчатковую форму ёмістасці. Дакладней кажучы, ён знаходзіцца пад ціскам і прыціскаецца да сценак паражніны выдувной формы, каб прыняць патрэбную форму. Нарэшце, выраблены шкляны кантэйнер перамяшчаецца ў печ для абпалу для наступнага разагрэву і зняцця напружанняў, якія ўзнікаюць падчас фармавання, і кантралявана астуджаецца. Пры метадзе прэсавання і выдзімання расплаўленыя кавалачкі кладуцца ў форму для запарвання (пустая форма) і прэсуюцца ў форму для загатоўкі (форма для загатоўкі). Затым нарыхтоўкі пераносяцца ў формы для выдзімання і выдзімаюцца аналагічна працэсу, апісанаму вышэй у раздзеле «Працэс выдзімання і выдзімання». Наступныя этапы, такія як адпал і зняцце напружання, падобныя або аднолькавыя.
• ВЫДВУМ ШКЛА: мы вырабляем шкляныя вырабы з выкарыстаннем звычайнага ручнога выдзімання, а таксама з выкарыстаннем сціснутага паветра з аўтаматызаваным абсталяваннем. Для некаторых заказаў патрабуецца звычайнае выдзіманне, напрыклад, праекты, звязаныя са шклом, або праекты, якія патрабуюць меншай колькасці дэталяў са свабоднымі допускамі, стварэнне прататыпаў / дэманстрацыйныя праекты... і г.д. Звычайнае выдзіманне шкла прадугледжвае апусканне полай металічнай трубы ў ёмістасць з расплаўленым шклом і кручэнне трубы для збору некаторай колькасці шклянога матэрыялу. Шкло, сабранае на кончыку трубы, пракатваюць на плоскім прасе, яму надаюць жаданую форму, падаўжаюць, зноў награваюць і абдзімаюць. Пасля гатоўнасці яго ўстаўляюць у форму і нагнятаюць паветра. Паражніну формы змочваюць, каб пазбегнуць кантакту шкла з металам. Вадзяная плёнка дзейнічае як падушка паміж імі. Ручное выдзіманне - гэта працаёмкі павольны працэс, які падыходзіць толькі для стварэння прататыпаў або прадметаў высокай каштоўнасці, не падыходзіць для недарагіх заказаў на вялікую колькасць штук.
• ВЫТВОРЧАСЦЬ БЫТАВОГА І ПРАМЫСЛОВАГА ШКЛА: з выкарыстаннем розных відаў шкла вырабляецца вялікая разнастайнасць шкляных вырабаў. Некаторыя шклянкі з'яўляюцца тэрмаўстойлівымі і падыходзяць для лабараторнага посуду, у той час як некаторыя дастаткова добрыя для таго, каб вытрымліваць шматразовае мыццё ў посудамыйных машынах і падыходзяць для вырабу хатніх вырабаў. З дапамогай машын Westlake штодня вырабляюцца дзясяткі тысяч шклянак. Каб спрасціць, расплаўленае шкло збіраецца з дапамогай вакууму і ўстаўляецца ў формы для вырабу папярэдніх формаў. Затым у формы ўдзімаецца паветра, яны пераносяцца ў іншую форму, і зноў удзімаецца паветра, і шкло прымае канчатковую форму. Як і пры ручным выдзіманні, гэтыя формы змочваюць вадой. Далейшае расцягванне з'яўляецца часткай аздаблення, дзе фарміруецца гарлавіна. Лішняе шкло выпальваецца. Пасля гэтага адбываецца працэс кантраляванага паўторнага нагрэву і астуджэння, апісаны вышэй.
• ФАРМАВАННЕ ШКЛЯНЫХ ТРУБ І ПРЫЖНЯЎ: Асноўнымі працэсамі, якія мы выкарыстоўваем для вытворчасці шкляных трубак, з'яўляюцца працэсы DANNER і VELLO. У працэсе Даннера шкло з печы цячэ і падае на нахільную гільзу з вогнетрывалых матэрыялаў. Гільза ажыццяўляецца на які верціцца полым вале або духаўной трубе. Затым шкло абгортваецца вакол гільзы і ўтварае гладкі пласт, які цячэ па гільзе і на кончыку стрыжня. У выпадку фармавання труб паветра прадзімаецца праз паветранадзімалку з полым наканечнікам, а ў выпадку фармавання стрыжня мы выкарыстоўваем суцэльныя наканечнікі на вале. Затым трубы або стрыжні нацягваюцца на нясучыя ролікі. Такія памеры, як таўшчыня сценкі і дыяметр шкляных трубак, рэгулююцца да жаданых значэнняў шляхам усталявання дыяметра гільзы і патрэбнага ціску паветра, рэгулюючы тэмпературу, хуткасць патоку шкла і хуткасць выцягвання. З іншага боку, працэс вырабу шкляной трубкі Vello ўключае шкло, якое выцясняе з печы ў чашу з полай апраўкай або раструбам. Затым шкло праходзіць праз паветраную прастору паміж апраўкай і чашай і прымае форму трубкі. Пасля гэтага ён перамяшчаецца па роліках у машыну для выцяжкі і астуджаецца. У канцы лініі астуджэння адбываецца рэзка і канчатковая апрацоўка. Памеры труб можна рэгуляваць, як і ў працэсе Даннера. Калі параўноўваць працэс Danner з Vello, мы можам сказаць, што працэс Vello лепш падыходзіць для вытворчасці вялікіх аб'ёмаў, тады як працэс Danner можа лепш падыходзіць для дакладных заказаў труб меншага аб'ёму.
• АПРАЦОЎКА ЛІСТАВАГА, ПЛОСКАГА І ФЛОАТ-ШКЛА: у нас ёсць вялікая колькасць ліставога шкла таўшчынёй ад субміліметраў да некалькіх сантыметраў. Нашы плоскія акуляры амаль аптычна дасканалыя. Мы прапануем шкло са спецыяльнымі пакрыццямі, такімі як аптычныя пакрыцця, дзе для нанясення пакрыццяў, такіх як антыблікавае або люстраное пакрыццё, выкарыстоўваецца метад хімічнага асаджэння з паравай фазы. Таксама распаўсюджаны празрыстыя токаправодныя пакрыцця. Таксама даступныя гідрафобныя або гідрафільныя пакрыцця на шкле, а таксама пакрыццё, якое робіць шкло самаачышчальным. Загартаванае, куленепрабівальнае і ламінаванае шкло - гэта і іншыя папулярныя рэчы. Мы наразаем шкло патрэбнай формы з патрэбнымі допускамі. Даступныя і іншыя дадатковыя аперацыі, такія як выгіб або выгіб плоскага шкла.
• ПРЕЦИЗИОННОЕ ЛІТВАННЕ ШКЛА: мы выкарыстоўваем гэтую тэхніку ў асноўным для вытворчасці дакладных аптычных кампанентаў без патрэбы ў больш дарагіх і працаёмкіх метадах, такіх як шліфоўка, прыцірка і паліроўка. Гэтай тэхнікі не заўсёды дастаткова для вырабу найлепшай оптыкі, але ў некаторых выпадках, такіх як спажывецкія тавары, лічбавыя камеры, медыцынская оптыка, яна можа быць менш дарагім добрым варыянтам для вытворчасці вялікіх аб'ёмаў. Акрамя таго, ён мае перавагу перад іншымі метадамі фармавання шкла, дзе патрабуецца складаная геаметрыя, напрыклад, у выпадку з асферамі. Асноўны працэс уключае загрузку ніжняга боку нашай формы шкляной нарыхтоўкай, ачыстку тэхналагічнай камеры для выдалення кіслароду, блізкае закрыццё формы, хуткі і ізатэрмічны нагрэў формы і шкла інфрачырвоным святлом, далейшае закрыццё палов формы. павольнае прэсаванне размякчанага шкла ў кантраляваным рэжыме да патрэбнай таўшчыні, і, нарэшце, астуджэнне шкла і запаўненне камеры азотам і выдаленне прадукту. Дакладны кантроль тэмпературы, адлегласць закрыцця формы, сіла закрыцця формы, адпаведнасць каэфіцыентаў пашырэння формы і шкла з'яўляюцца ключавымі ў гэтым працэсе.
• ВЫТВОРЧАСЦЬ ШКЛЯНЫХ АПТЫЧНЫХ КАМПАНЕНТАЎ І ЗБОРАЎ: Акрамя дакладнага фармавання шкла, існуе шэраг каштоўных працэсаў, якія мы выкарыстоўваем для вырабу высакаякасных аптычных кампанентаў і зборак для патрабавальных прыкладанняў. Шліфаванне, прыцірка і паліроўка шкла аптычнага класа ў тонкай спецыяльнай абразіўнай суспензіі - гэта мастацтва і навука для вырабу аптычных лінзаў, прызмаў, плоскіх лінзаў і іншага. Плоскасць паверхні, хвалістасць, гладкасць і аптычныя паверхні без дэфектаў патрабуюць вялікага вопыту ў такіх працэсах. Невялікія змены ў навакольным асяроддзі могуць прывесці да выхаду прадукцыі з тэхнічных характарыстык і прыпынку вытворчай лініі. Бываюць выпадкі, калі адно праціранне аптычнай паверхні чыстай тканінай можа прывесці да таго, што прадукт адпавядае спецыфікацыям або не пройдзе тэст. Некаторыя папулярныя шкляныя матэрыялы, якія выкарыстоўваюцца, - гэта плаўлены кремнезем, кварц, BK7. Таксама зборка такіх кампанентаў патрабуе спецыялізаванага нішавага вопыту. Часам выкарыстоўваюцца спецыяльныя клеі. Аднак часам метад, які называецца аптычным кантактам, з'яўляецца лепшым выбарам і не прадугледжвае выкарыстання матэрыялу паміж прымацаванымі аптычнымі шкламі. Ён складаецца з фізічнага кантакту плоскіх паверхняў для злучэння адна з адной без клею. У некаторых выпадках для зборкі аптычных кампанентаў на пэўных адлегласцях і з пэўнай геаметрычнай арыентацыяй адзін да аднаго выкарыстоўваюцца механічныя пракладкі, дакладныя шкляныя стрыжні або шарыкі, заціскі або апрацаваныя металічныя кампаненты. Давайце разгледзім некаторыя з нашых папулярных метадаў вырабу высокакласнай оптыкі.
ШЛІФОЎКА І ПРЫТЫРКА І ПАЛІРАВАННЕ: Грубая форма аптычнага кампанента атрымліваецца пры шліфоўцы шкляной нарыхтоўкі. Пасля гэтага прыцірка і паліроўка выконваюцца шляхам кручэння і трэння шурпатых паверхняў аптычных кампанентаў аб інструменты з патрэбнай формай паверхні. Суспензіі з драбнюткімі абразіўнымі часціцамі і вадкасць заліваюцца паміж оптыкай і інструментамі для фармавання. Памер абразіўных часціц у такіх суспензіях можна выбіраць у залежнасці ад жаданай ступені роўнасці. Адхіленні крытычных аптычных паверхняў ад патрэбнай формы выражаюцца праз даўжыні хваль выкарыстоўванага святла. Наша высокадакладная оптыка мае допускі на дзесятую частку даўжыні хвалі (Даўжыня хвалі/10), а магчыма нават больш жорсткія. Акрамя профілю паверхні, крытычныя паверхні скануюцца і ацэньваюцца на іншыя асаблівасці паверхні і дэфекты, такія як памеры, драпіны, сколы, ямкі, плямы ... і г.д. Жорсткі кантроль умоў навакольнага асяроддзя на цэху па вытворчасці аптычных вырабаў і шырокія патрабаванні да метралогіі і выпрабаванняў з самым сучасным абсталяваннем робяць гэтую галіну прамысловасці складанай.
• ДАПАМОЖНЫЯ ПРАЦЭСЫ Ў ВЫТВОРЧАСЦІ ШКЛА: Зноў жа, мы абмежаваныя толькі вашым уяўленнем, калі справа даходзіць да другасных і аздабленчых працэсаў шкла. Вось некаторыя з іх:
-Пакрыцці на шкле (аптычныя, электрычныя, трыбалагічныя, тэрмічныя, функцыянальныя, механічныя...). У якасці прыкладу мы можам змяніць уласцівасці паверхні шкла, у выніку чаго яно, напрыклад, адлюстроўвае цяпло, падтрымліваючы прахалоду ў інтэр'еры будынка, або зрабіць адзін бок інфрачырвонага паглынання з дапамогай нанатэхналогій. Гэта дапамагае захоўваць цяпло ўнутры будынкаў, таму што крайні паверхневы пласт шкла будзе паглынаць інфрачырвонае выпраменьванне ўнутры будынка і выпраменьваць яго назад унутр.
- Гравіраванне на шкле
-Прыкладная керамічная маркіроўка (ACL)
-Гравюра
- Полымя паліроўка
-Хімічная паліроўка
-Афарбоўка
ВЫТВОРЧАСЦЬ ТЭХНІЧНАЙ КЕРАМІКІ
• ПРАСАВАННЕ ПРАШКІ: Складаецца з аднавосевага ўшчыльнення грануляваных парашкоў, змешчаных у форму.
• ГАРАЧАЕ ПРАСАВАННЕ: падобна на прэсаванне, але з даданнем тэмпературы для ўзмацнення ўшчыльнення. Парашок або ўшчыльненую нарыхтоўку змяшчаюць у графітавы штамп і прыкладваюць аднавосевы ціск, у той час як штамп вытрымліваюць пры высокіх тэмпературах, такіх як 2000 C. Тэмпературы могуць адрознівацца ў залежнасці ад тыпу керамічнага парашка, які апрацоўваецца. Для складаных формаў і геаметрыі можа спатрэбіцца іншая наступная апрацоўка, напрыклад алмазная шліфоўка.
• ІЗАСТАТЫЧНАЕ Прэсаванне: грануляваны парашок або прэсаваныя прэсы змяшчаюць у герметычныя кантэйнеры, а затым у закрытую ёмістасць пад ціскам з вадкасцю ўнутры. Пасля гэтага яны ўшчыльняюцца шляхам павышэння ціску ў ёмістасці высокага ціску. Вадкасць унутры ёмістасці раўнамерна перадае сілы ціску па ўсёй паверхні герметычнага кантэйнера. Такім чынам, матэрыял раўнамерна ўшчыльняецца і прымае форму свайго гнуткага кантэйнера і яго ўнутраны профіль і характарыстыкі.
• ГАРЯЧЫ ІЗАСТАТЫЧНЫ Прэс: Падобна ізастатычнаму прэсаванню, але ў дадатак да атмасферы газу пад ціскам мы спекаем кампакт пры высокай тэмпературы. Гарачае изостатическое прэсаванне прыводзіць да дадатковага ўшчыльнення і павышэнню трываласці.
• Шлікернае ліццё / Дрэнажнае ліццё: мы запаўняем форму суспензіяй керамічных часціц мікраметровага памеру і вадкасці-носьбіта. Гэтая сумесь называецца «сліп». Форма мае пары, і таму вадкасць у сумесі фільтруецца ў форму. У выніку на ўнутраных паверхнях формы ўтворыцца злепак. Пасля спякання дэталі можна вымаць з формы.
• ЛІЦЦЁ СТУЖК: Мы вырабляем керамічныя стужкі шляхам адлівання керамічных суспензій на плоскія рухомыя паверхні носьбітаў. Завісі ўтрымліваюць керамічныя парашкі, змешаныя з іншымі хімічнымі рэчывамі для звязвання і пераноскі. Па меры выпарэння растваральнікаў застаюцца шчыльныя і гнуткія лісты керамікі, якія можна рэзаць або скручваць па жаданні.
• ЭКСТРАЗІЙНЫ ФАРМАВАННЕ: Як і ў іншых працэсах экструзіі, мяккая сумесь керамічнага парашка са звязальнымі рэчывамі і іншымі хімічнымі рэчывамі прапускаецца праз штамп для набыцця формы папярочнага сячэння, а затым разразаецца на патрэбную даўжыню. Працэс выконваецца з халоднымі або нагрэтымі керамічнымі сумесямі.
• ЛІЦЦЕ ПАД НІЗКІМ ЦІСКАМ: мы рыхтуем сумесь керамічнага парашка са звязальнымі рэчывамі і растваральнікамі і награваем яе да тэмпературы, пры якой яе можна лёгка націснуць і ўціснуць у паражніну інструмента. Пасля завяршэння цыкла фармавання дэталь выкідваецца, а злучнае хімічнае рэчыва спальваецца. Выкарыстоўваючы ліццё пад ціскам, мы можам эканамічна атрымліваць складаныя дэталі ў вялікіх аб'ёмах. Магчымы адтуліны , якія складаюць малюсенькія долі міліметра на сцяне таўшчынёй 10 мм, магчымыя разьбы без дадатковай механічнай апрацоўкі, магчымыя допускі +/- 0,5% і нават ніжэй, калі дэталі апрацоўваюцца на машыне. , магчымыя таўшчыні сценак ад 0,5 мм да даўжыні 12,5 мм, а таксама таўшчыні сценак ад 6,5 мм да даўжыні 150 мм.
• ЗЯЛЁНАЯ АБРАБОТКА: выкарыстоўваючы тыя ж інструменты для апрацоўкі металу, мы можам апрацоўваць прэсаваныя керамічныя матэрыялы, пакуль яны яшчэ мяккія, як мел. Дапушчальныя адхіленні +/- 1%. Для лепшых допускаў мы выкарыстоўваем алмазнае шліфаванне.
• Спяканне або абпал: спяканне робіць магчымым поўнае ўшчыльненне. На зялёных кампактных дэталях адбываецца значная ўсаджванне, але гэта не вялікая праблема, паколькі мы ўлічваем гэтыя змены памераў пры распрацоўцы дэталяў і інструментаў. Часціцы парашка злучаюцца разам, і сітаватасць, выкліканая працэсам ушчыльнення, у значнай ступені выдаляецца.
• АЛМАЗНАЯ ШЛІФКА: самы цвёрды ў свеце матэрыял «алмаз» выкарыстоўваецца для шліфоўкі цвёрдых матэрыялаў, такіх як кераміка, і атрымліваюцца дакладныя дэталі. Дасягаюцца допускі ў мікраметровым дыяпазоне і вельмі гладкія паверхні. З-за яго кошту мы разглядаем гэты метад толькі тады, калі ён нам сапраўды патрэбны.
• ГЕРМЕТЫЧНЫЯ ЗБОРЫ - гэта тыя, якія практычна не дазваляюць абменьвацца рэчывамі, цвёрдымі рэчывамі, вадкасцямі або газамі паміж інтэрфейсамі. Герметызацыя герметычная. Напрыклад, герметычныя электронныя карпусы - гэта тыя, у якіх адчувальнае ўнутранае змесціва ўпакаванай прылады не пашкоджана вільгаццю, забруджваннямі або газамі. Нішто не з'яўляецца 100% герметычным, але калі мы гаворым пра герметычнасць, мы маем на ўвазе, што ў практычным плане герметычнасць існуе ў такой ступені, што ўзровень уцечкі настолькі нізкі, што прылады бяспечныя ў нармальных умовах навакольнага асяроддзя на працягу вельмі доўгага часу. Нашы герметычныя вузлы складаюцца з металічных, шкляных і керамічных кампанентаў, метала-керамікі, керамікі-метал-керамікі, метал-керамікі-метал, метал-метал, метал-шкло, метал-шкло-метал, шкло-метал-шкло, шкло- метал і шкло са шклом і ўсе іншыя камбінацыі злучэння метал-шклокераміка. Напрыклад, мы можам пакрыць керамічныя кампаненты металічным пакрыццём, каб яны маглі быць трывала злучаны з іншымі кампанентамі ў зборцы і мець выдатную герметычнасць. У нас ёсць ноу-хау пакрыцця аптычных валокнаў або праходных каналаў металам і прыпайвання іх да карпусоў, каб газы не праходзілі і не прасочваліся ў карпусы. Таму яны выкарыстоўваюцца для вытворчасці электронных карпусоў для інкапсуляцыі адчувальных прылад і абароны іх ад знешняй атмасферы. Акрамя выдатных характарыстык ушчыльнення, іншыя ўласцівасці, такія як каэфіцыент цеплавога пашырэння, устойлівасць да дэфармацыі, невылучэнне газаў, вельмі доўгі тэрмін службы, неправоднасць, цеплаізаляцыйныя ўласцівасці, антыстатычнасць і г.д. зрабіць шкляныя і керамічныя матэрыялы выбарам для пэўных прыкладанняў. Інфармацыю аб нашым прадпрыемстве па вытворчасці фітынгаў з керамікі да металу, герметычнай герметызацыі, вакуумных каналаў, высокага і звышвысокага вакууму і кампанентаў кантролю вадкасці можна знайсці тут:Брашура завода герметычных кампанентаў