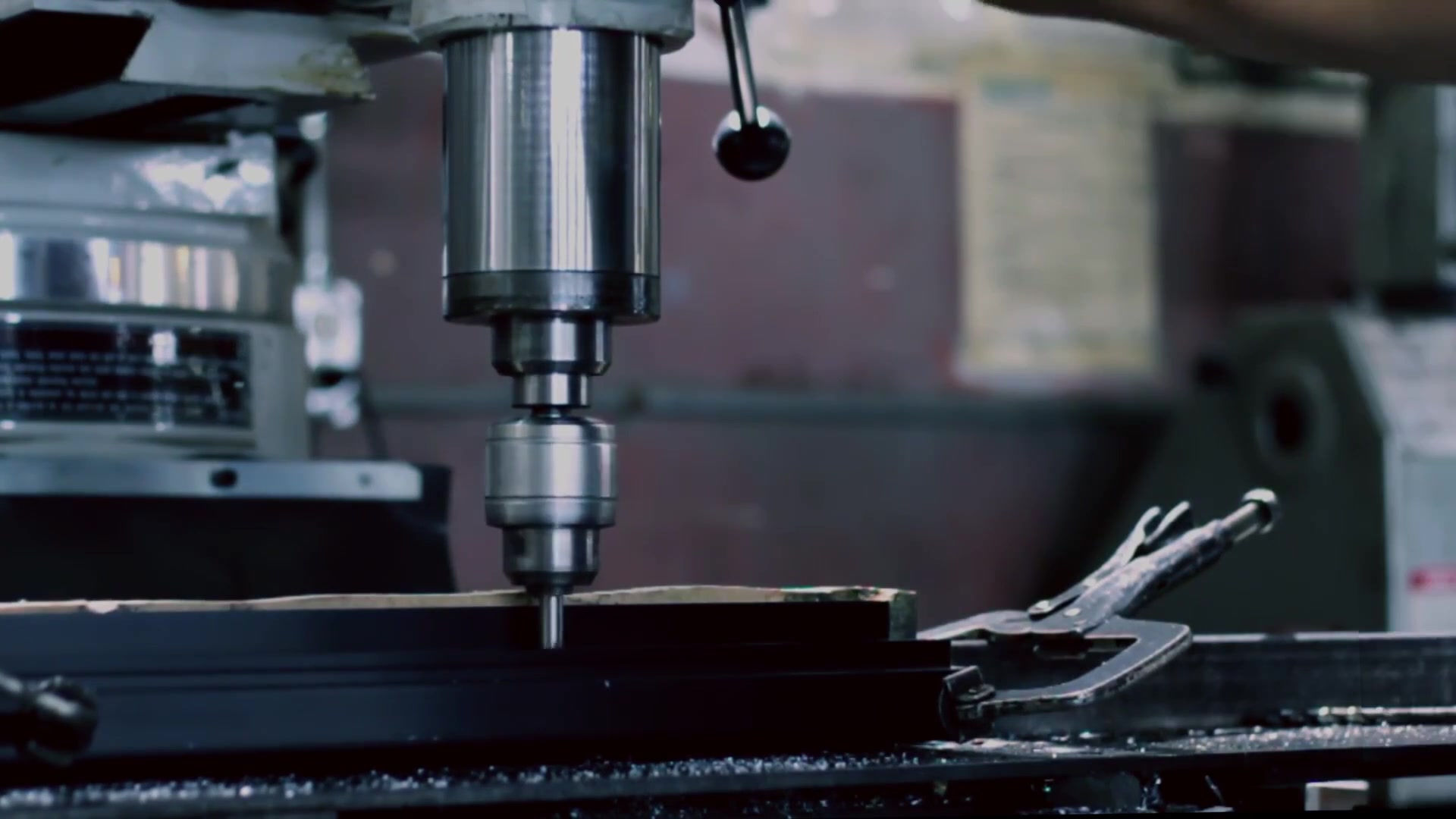
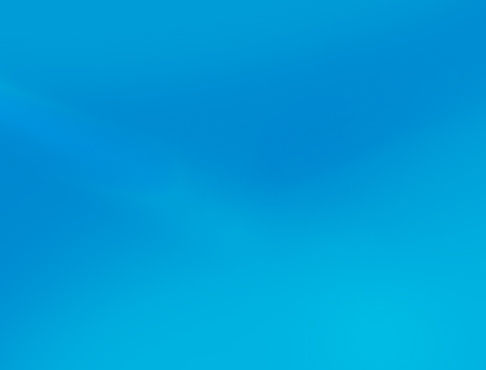
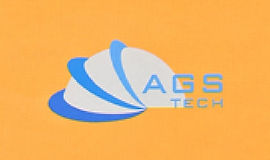
Fabricante personalizado global, integrador, consolidador, socio de subcontratación para una amplia variedad de productos y servicios.
Somos su fuente única para la fabricación, la fabricación, la ingeniería, la consolidación, la integración y la subcontratación de productos y servicios fabricados a medida y listos para usar.
Choose your Language
-
Fabricación personalizada
-
Fabricación por contrato nacional y mundial
-
Subcontratación de fabricación
-
Adquisiciones nacionales y globales
-
Consolidación
-
Integración de ingeniería
-
Servicios de Ingenieria
El tipo de fabricación de vidrio que ofrecemos es vidrio para envases, vidrio soplado, fibra de vidrio, tubos y varillas, cristalería doméstica e industrial, lámparas y bombillas, moldeado de vidrio de precisión, componentes y ensamblajes ópticos, vidrio plano, plano y flotado. Realizamos tanto el formado a mano como el formado a máquina.
Nuestros populares procesos de fabricación de cerámica técnica son el prensado en matriz, el prensado isostático, el prensado isostático en caliente, el prensado en caliente, la fundición deslizante, la fundición en cinta, la extrusión, el moldeo por inyección, el mecanizado en verde, la sinterización o la cocción, el pulido con diamante y los conjuntos herméticos.
Le recomendamos que haga clic aquí para
DESCARGUE nuestras ilustraciones esquemáticas de los procesos de formación y modelado de vidrio de AGS-TECH Inc.
Estos archivos descargables con fotos y bocetos te ayudarán a comprender mejor la información que te proporcionamos a continuación.
• FABRICACIÓN DE ENVASES DE VIDRIO: Disponemos de líneas automatizadas de PRENSADO Y SOPLADO así como de SOPLADO Y SOPLADO para su fabricación. En el proceso de soplado y soplado, dejamos caer una gota en un molde en blanco y formamos el cuello aplicando un golpe de aire comprimido desde la parte superior. Inmediatamente después de esto, se sopla aire comprimido por segunda vez desde la otra dirección a través del cuello del recipiente para formar la preforma de la botella. Luego, esta preforma se transfiere al molde real, se vuelve a calentar para que se ablande y se aplica aire comprimido para darle a la preforma su forma de recipiente final. Más explícitamente, se presuriza y empuja contra las paredes de la cavidad del molde de soplado para que adopte la forma deseada. Finalmente, el envase de vidrio fabricado se traslada a un horno de recocido para su posterior recalentamiento y eliminación de tensiones producidas durante el moldeo y se enfría de forma controlada. En el método de prensado y soplado, las gotas fundidas se colocan en un molde de parisón (molde en blanco) y se prensan en forma de parisón (forma en blanco). Luego, los espacios en blanco se transfieren a moldes de soplado y se soplan de manera similar al proceso descrito anteriormente en "Proceso de soplado y soplado". Los pasos posteriores, como el recocido y el alivio de tensión, son similares o iguales.
• SOPLADO DE VIDRIO: Venimos fabricando productos de vidrio usando soplado manual convencional así como también usando aire comprimido con equipos automatizados. Para algunos pedidos es necesario el soplado convencional, como proyectos que involucran obras de arte en vidrio, o proyectos que requieren un número menor de piezas con tolerancias sueltas, proyectos de prototipos/demostraciones, etc. El soplado de vidrio convencional implica la inmersión de un tubo de metal hueco en una olla de vidrio fundido y la rotación del tubo para recoger una cierta cantidad de material de vidrio. El vidrio recogido en la punta de la tubería se enrolla sobre hierro plano, se le da la forma deseada, se alarga, se recalienta y se sopla con aire. Cuando está listo, se inserta en un molde y se sopla aire. La cavidad del molde está húmeda para evitar el contacto del vidrio con el metal. La película de agua actúa como un colchón entre ellos. El soplado manual es un proceso lento que requiere mucha mano de obra y solo es adecuado para la creación de prototipos o artículos de alto valor, no es adecuado para pedidos económicos de gran volumen por pieza.
• FABRICACIÓN DE CRISTALES DOMÉSTICOS E INDUSTRIALES: Utilizando varios tipos de materiales de vidrio se produce una gran variedad de artículos de vidrio. Algunos vasos son resistentes al calor y adecuados para la cristalería de laboratorio, mientras que otros son lo suficientemente buenos para soportar los lavavajillas durante muchas veces y son aptos para la fabricación de productos domésticos. Con las máquinas Westlake se producen decenas de miles de vasos para beber al día. Para simplificar, el vidrio fundido se recolecta al vacío y se inserta en moldes para hacer las preformas. Luego se sopla aire en los moldes, estos se trasladan a otro molde y se vuelve a soplar aire y el vidrio toma su forma final. Como en el soplado manual, estos moldes se mantienen húmedos con agua. El estiramiento adicional es parte de la operación de acabado donde se forma el cuello. El exceso de vidrio se quema. A continuación sigue el proceso de recalentamiento y enfriamiento controlado descrito anteriormente.
• FORMACIÓN DE TUBOS Y VARILLAS DE VIDRIO: Los principales procesos que utilizamos para la fabricación de tubos de vidrio son los procesos DANNER y VELLO. En el Proceso Danner, el vidrio de un horno fluye y cae sobre un manguito inclinado hecho de materiales refractarios. El manguito se transporta sobre un eje hueco giratorio o soplete. Luego, el vidrio se envuelve alrededor del manguito y forma una capa suave que fluye hacia abajo del manguito y sobre la punta del eje. En el caso de la formación de tubos, se sopla aire a través de un soplete con punta hueca, y en el caso de la formación de varillas, usamos puntas sólidas en el eje. A continuación, los tubos o varillas se arrastran sobre rodillos portadores. Las dimensiones como el grosor de la pared y el diámetro de los tubos de vidrio se ajustan a los valores deseados ajustando el diámetro del manguito y soplando la presión del aire a un valor deseado, ajustando la temperatura, la tasa de flujo del vidrio y la velocidad de estirado. El proceso de fabricación de tubos de vidrio Vello, por otro lado, involucra vidrio que sale de un horno y entra en un recipiente con un mandril o campana hueca. Luego, el vidrio atraviesa el espacio de aire entre el mandril y el recipiente y toma la forma de un tubo. A continuación, viaja sobre rodillos hasta una máquina de estirado y se enfría. Al final de la línea de enfriamiento tiene lugar el corte y el procesamiento final. Las dimensiones del tubo se pueden ajustar como en el proceso Danner. Al comparar el proceso Danner con Vello, podemos decir que el proceso Vello se adapta mejor a la producción de grandes cantidades, mientras que el proceso Danner puede ser más adecuado para pedidos precisos de tubos de menor volumen.
• PROCESAMIENTO DE VIDRIO LÁMINA, PLANO Y FLOTADOR: Disponemos de grandes cantidades de vidrio plano en espesores que van desde espesores submilimétricos hasta varios centímetros. Nuestros vasos planos son de una perfección casi óptica. Ofrecemos vidrios con recubrimientos especiales como recubrimientos ópticos, donde se utiliza la técnica de deposición química de vapor para colocar recubrimientos como antireflejos o espejo. También son comunes los revestimientos conductores transparentes. También están disponibles revestimientos hidrofóbicos o hidrofílicos sobre vidrio y revestimientos que hacen que el vidrio sea autolimpiante. Los vidrios templados, a prueba de balas y laminados son otros artículos populares. Cortamos el vidrio en la forma deseada con las tolerancias deseadas. Están disponibles otras operaciones secundarias como curvar o doblar vidrio plano.
• MOLDEADO DE VIDRIO DE PRECISIÓN: Utilizamos esta técnica principalmente para fabricar componentes ópticos de precisión sin necesidad de técnicas más costosas y lentas como esmerilado, lapeado y pulido. Esta técnica no siempre es suficiente para hacer lo mejor de la mejor óptica, pero en algunos casos, como productos de consumo, cámaras digitales, óptica médica, puede ser una buena opción menos costosa para la fabricación de alto volumen. También tiene una ventaja sobre las otras técnicas de formación de vidrio donde se requieren geometrías complejas, como en el caso de las esferas. El proceso básico incluye la carga del lado inferior de nuestro molde con la pieza de vidrio, la evacuación de la cámara de proceso para la eliminación de oxígeno, el cierre cercano del molde, el calentamiento rápido e isotérmico de la matriz y el vidrio con luz infrarroja, y el cierre adicional de las mitades del molde. prensar el vidrio reblandecido lentamente de forma controlada hasta el espesor deseado, y finalmente enfriar el vidrio y llenar la cámara con nitrógeno y retirar el producto. El control preciso de la temperatura, la distancia de cierre del molde, la fuerza de cierre del molde, la coincidencia de los coeficientes de expansión del molde y el material de vidrio son clave en este proceso.
• FABRICACIÓN DE ENSAMBLAJES Y COMPONENTES ÓPTICOS DE VIDRIO: además del moldeo de vidrio de precisión, utilizamos varios procesos valiosos para fabricar ensamblajes y componentes ópticos de alta calidad para aplicaciones exigentes. Esmerilar, lapear y pulir vidrios de grado óptico en lechadas finas de abrasivo especial es un arte y una ciencia para fabricar lentes ópticos, prismas, planos y más. La planitud de la superficie, la ondulación, la suavidad y las superficies ópticas libres de defectos requieren mucha experiencia con tales procesos. Pequeños cambios en el entorno pueden dar como resultado productos fuera de las especificaciones y detener la línea de fabricación. Hay casos en los que una sola limpieza de la superficie óptica con un paño limpio puede hacer que un producto cumpla con las especificaciones o falle la prueba. Algunos materiales de vidrio populares utilizados son sílice fundida, cuarzo, BK7. Además, el ensamblaje de dichos componentes requiere experiencia en un nicho especializado. A veces se utilizan colas especiales. Sin embargo, a veces una técnica llamada contacto óptico es la mejor opción y no involucra ningún material entre los vidrios ópticos adjuntos. Consiste en contactar físicamente superficies planas para unirlas entre sí sin necesidad de pegamento. En algunos casos, se utilizan espaciadores mecánicos, varillas o bolas de vidrio de precisión, abrazaderas o componentes de metal mecanizado para ensamblar los componentes ópticos a ciertas distancias y con ciertas orientaciones geométricas entre sí. Examinemos algunas de nuestras técnicas populares para la fabricación de ópticas de gama alta.
RECTIFICADO Y LAPIDO Y PULIDO: La forma rugosa del componente óptico se obtiene rectificando una pieza de vidrio. A continuación, el lapeado y el pulido se llevan a cabo girando y frotando las superficies rugosas de los componentes ópticos contra herramientas con las formas superficiales deseadas. Se vierten lodos con diminutas partículas abrasivas y líquido entre la óptica y las herramientas de modelado. Los tamaños de las partículas abrasivas en dichas suspensiones se pueden elegir de acuerdo con el grado de planeidad deseado. Las desviaciones de las superficies ópticas críticas de las formas deseadas se expresan en términos de longitudes de onda de la luz que se utiliza. Nuestra óptica de alta precisión tiene tolerancias de décimas de longitud de onda (longitud de onda/10) o incluso es posible que sean más estrictas. Además del perfil de la superficie, las superficies críticas se escanean y evalúan en busca de otras características y defectos de la superficie, como dimensiones, rayones, astillas, hoyos, motas, etc. El estricto control de las condiciones ambientales en la planta de fabricación óptica y los extensos requisitos de prueba y metrología con equipos de última generación hacen de esta una rama industrial desafiante.
• PROCESOS SECUNDARIOS EN LA FABRICACIÓN DE VIDRIO: Una vez más, solo estamos limitados por su imaginación cuando se trata de procesos secundarios y de acabado del vidrio. Aquí enumeramos algunos de ellos:
-Recubrimientos sobre vidrio (ópticos, eléctricos, tribológicos, térmicos, funcionales, mecánicos...). Como ejemplo, podemos alterar las propiedades de la superficie del vidrio, por ejemplo, haciendo que refleje el calor para que mantenga frescos los interiores de los edificios, o hacer que un lado absorba el infrarrojo usando nanotecnología. Esto ayuda a mantener caliente el interior de los edificios porque la capa de vidrio de la superficie exterior absorberá la radiación infrarroja dentro del edificio y la irradiará de regreso al interior.
-Grabado sobre vidrio
-Etiquetado cerámico aplicado (ACL)
-Grabado
-pulido a la llama
-Pulido químico
-Tinte
FABRICACIÓN DE CERÁMICA TÉCNICA
• PRENSADO EN MATRIZ: Consiste en la compactación uniaxial de polvos granulares confinados en una matriz
• PRENSADO EN CALIENTE: Similar al prensado en matriz pero con la adición de temperatura para mejorar la densificación. El polvo o la preforma compactada se colocan en una matriz de grafito y se aplica presión uniaxial mientras la matriz se mantiene a altas temperaturas, como 2000 C. Las temperaturas pueden ser diferentes según el tipo de polvo cerámico que se procese. Para formas y geometrías complicadas, puede ser necesario otro procesamiento posterior, como el pulido con diamante.
• PRENSADO ISOSTÁTICO: El polvo granular o los compactos prensados en matriz se colocan en recipientes herméticos y luego en un recipiente a presión cerrado con líquido en su interior. Posteriormente, se compactan aumentando la presión del recipiente a presión. El líquido dentro del recipiente transfiere las fuerzas de presión de manera uniforme sobre toda la superficie del recipiente hermético. El material se compacta así uniformemente y toma la forma de su contenedor flexible y su perfil y características internas.
• PRENSADO ISOSTÁTICO EN CALIENTE: Similar al prensado isostático, pero además de atmósfera de gas presurizado, sinterizamos el compacto a alta temperatura. El prensado isostático en caliente da como resultado una densificación adicional y una mayor resistencia.
• SLIP CASTING / DREN CASTING: Llenamos el molde con una suspensión de partículas cerámicas de tamaño micrométrico y líquido portador. Esta mezcla se llama “deslizamiento”. El molde tiene poros y por lo tanto el líquido de la mezcla se filtra en el molde. Como resultado, se forma un molde en las superficies internas del molde. Después de la sinterización, las piezas se pueden sacar del molde.
• FUNDICIÓN DE CINTA: fabricamos cintas cerámicas mediante la fundición de lodos cerámicos sobre superficies móviles planas de soporte. Las lechadas contienen polvos cerámicos mezclados con otros productos químicos con fines de unión y transporte. A medida que los solventes se evaporan, quedan láminas de cerámica densas y flexibles que se pueden cortar o enrollar según se desee.
• FORMACIÓN POR EXTRUSIÓN: Al igual que en otros procesos de extrusión, una mezcla suave de polvo cerámico con aglutinantes y otros productos químicos se pasa a través de un troquel para adquirir su forma de sección transversal y luego se corta en las longitudes deseadas. El proceso se realiza con mezclas cerámicas en frío o en caliente.
• MOLDEO POR INYECCIÓN A BAJA PRESIÓN: Preparamos una mezcla de polvo cerámico con aglutinantes y solventes y la calentamos a una temperatura en la que se pueda presionar y forzar fácilmente en la cavidad de la herramienta. Una vez que se completa el ciclo de moldeo, la pieza se expulsa y el químico aglutinante se quema. Mediante el moldeo por inyección, podemos obtener piezas complejas en grandes volúmenes de forma económica. Son posibles agujeros que son una pequeña fracción de milímetro en una pared de 10 mm de espesor, son posibles roscas sin necesidad de mecanizar más, son posibles tolerancias tan estrechas como +/- 0,5 % e incluso menores cuando las piezas están mecanizadas , son posibles espesores de pared del orden de 0,5 mm hasta una longitud de 12,5 mm, así como espesores de pared de 6,5 mm hasta una longitud de 150 mm.
• MECANIZADO ECOLÓGICO: Utilizando las mismas herramientas de mecanizado de metal, podemos mecanizar materiales cerámicos prensados cuando todavía están blandos como la tiza. Son posibles tolerancias de +/- 1%. Para mejores tolerancias utilizamos rectificado de diamante.
• SINTERIZACIÓN o COCCIÓN: La sinterización permite una densificación total. Se produce una contracción significativa en las piezas compactas verdes, pero esto no es un gran problema ya que tenemos en cuenta estos cambios dimensionales cuando diseñamos la pieza y las herramientas. Las partículas de polvo se unen y la porosidad inducida por el proceso de compactación se elimina en gran medida.
• RECTIFICADO DE DIAMANTE: El material más duro del mundo, el “diamante”, se utiliza para rectificar materiales duros como la cerámica y se obtienen piezas de precisión. Se están logrando tolerancias en el rango de micrómetros y superficies muy lisas. Debido a su costo, solo consideramos esta técnica cuando realmente la necesitamos.
• MONTAJES HERMÉTICOS son aquellos que prácticamente no permiten ningún intercambio de materia, sólidos, líquidos o gases entre interfaces. El sellado hermético es hermético. Por ejemplo, los recintos electrónicos herméticos son aquellos que mantienen el contenido interior sensible de un dispositivo empaquetado sin daños por la humedad, los contaminantes o los gases. Nada es 100% hermético, pero cuando hablamos de hermeticidad nos referimos a que, en términos prácticos, hay hermeticidad en la medida en que la tasa de fuga es tan baja que los dispositivos son seguros en condiciones ambientales normales durante tiempos muy prolongados. Nuestros conjuntos herméticos consisten en componentes de metal, vidrio y cerámica, metal-cerámica, cerámica-metal-cerámica, metal-cerámica-metal, metal con metal, metal-vidrio, metal-vidrio-metal, vidrio-metal-vidrio, vidrio- metal y vidrio a vidrio y todas las demás combinaciones de unión metal-vidrio-cerámica. Por ejemplo, podemos recubrir con metal los componentes cerámicos para que puedan unirse fuertemente a otros componentes en el ensamblaje y tener una excelente capacidad de sellado. Tenemos el conocimiento de recubrir fibras ópticas o pasamuros con metal y soldarlos a las cajas, de modo que no pasen gases ni se filtren en las cajas. Por lo tanto, se utilizan para fabricar cajas electrónicas para encapsular dispositivos sensibles y protegerlos de la atmósfera exterior. Además de sus excelentes características de sellado, otras propiedades como el coeficiente de expansión térmica, resistencia a la deformación, naturaleza no desgasificadora, vida útil muy larga, naturaleza no conductora, propiedades de aislamiento térmico, naturaleza antiestática, etc. hacen que los materiales de vidrio y cerámica sean la elección para ciertas aplicaciones. Puede encontrar información sobre nuestras instalaciones que producen accesorios de cerámica a metal, sellado hermético, pasamuros de vacío, alto y ultraalto vacío y componentes de control de fluidos aquí:Folleto de la fábrica de componentes herméticos