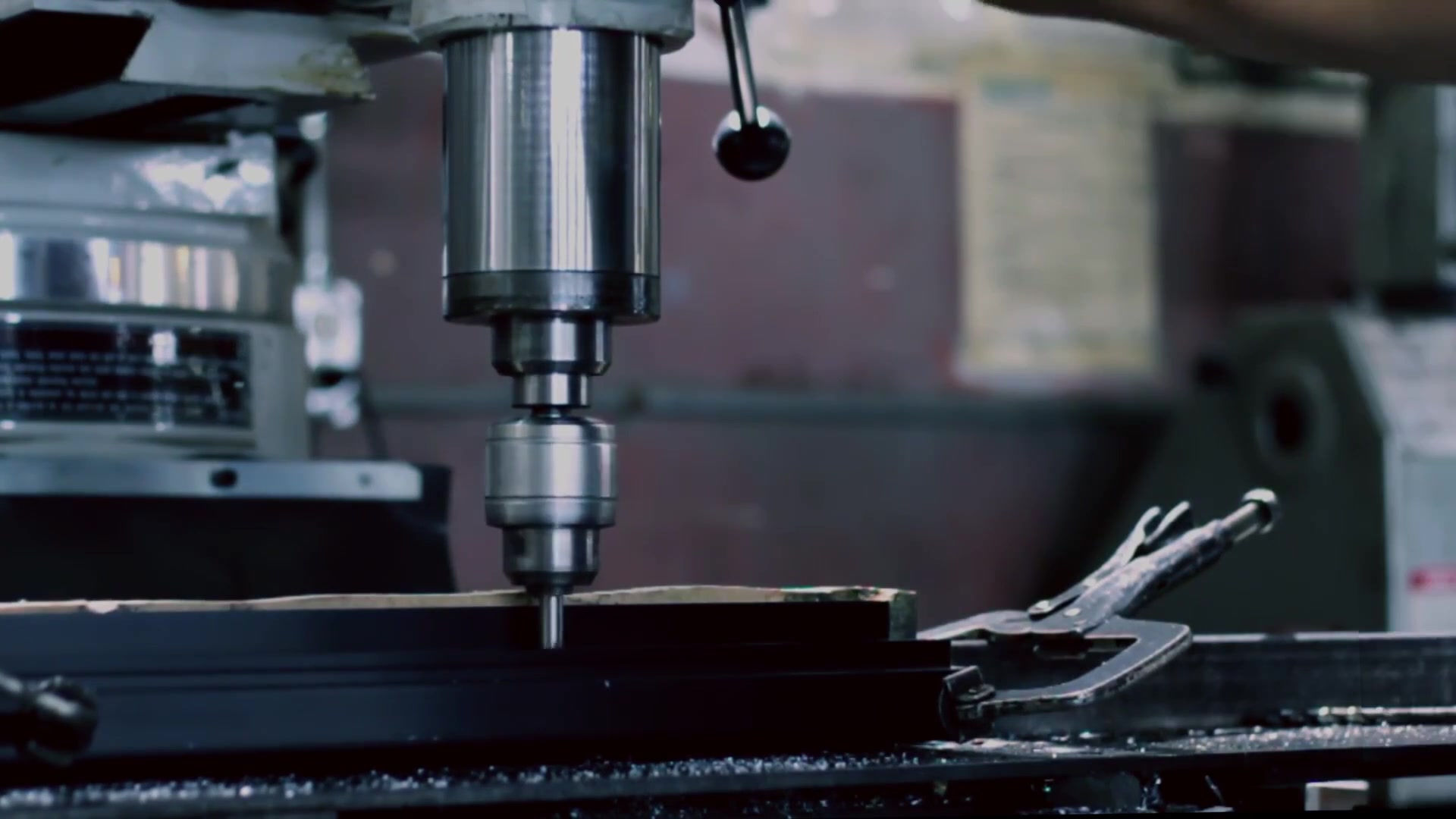
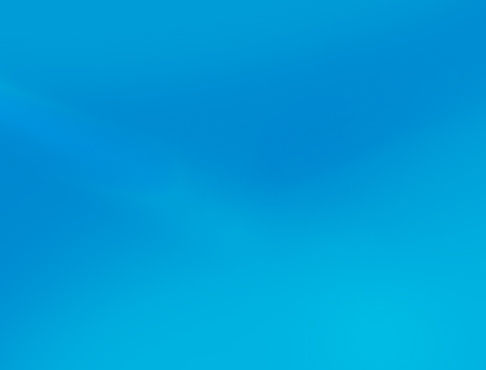
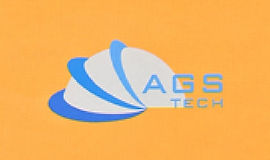
Fabricante personalizado global, integrador, consolidador, socio de subcontratación para una amplia variedad de productos y servicios.
Somos su fuente única para la fabricación, la fabricación, la ingeniería, la consolidación, la integración y la subcontratación de productos y servicios fabricados a medida y listos para usar.
Choose your Language
-
Fabricación personalizada
-
Fabricación por contrato nacional y mundial
-
Subcontratación de fabricación
-
Adquisiciones nacionales y globales
-
Consolidación
-
Integración de ingeniería
-
Servicios de Ingenieria
Unimos, ensamblamos y sujetamos sus piezas fabricadas y las convertimos en productos terminados o semielaborados mediante SOLDADURA, SOLDADURA SOLDADURA, SINTERIZACIÓN, PEGADO ADHESIVO, FIJACIÓN, PRESS FITTING. Algunos de nuestros procesos de soldadura más populares son arco, gas oxicombustible, resistencia, proyección, costura, recalcado, percusión, estado sólido, haz de electrones, láser, termita, soldadura por inducción. Nuestros procesos de soldadura fuerte populares son la soldadura fuerte con soplete, por inducción, en horno y por inmersión. Nuestros métodos de soldadura son hierro, placa caliente, horno, inducción, inmersión, ola, reflujo y soldadura ultrasónica. Para la unión adhesiva utilizamos con frecuencia termoplásticos y termoestables, resinas epoxi, fenólicos, poliuretano, aleaciones adhesivas, así como algunos otros productos químicos y cintas. Finalmente, nuestros procesos de sujeción consisten en clavar, atornillar, tuercas y pernos, remachar, remachar, fijar con alfileres, coser y grapar y ajustar a presión.
• SOLDADURA: La soldadura implica la unión de materiales fundiendo las piezas de trabajo e introduciendo materiales de aporte, que también se unen al baño de soldadura fundido. Cuando la zona se enfría, obtenemos una unión fuerte. En algunos casos se aplica presión. A diferencia de la soldadura, las operaciones de soldadura fuerte y blanda implican únicamente la fusión de un material con un punto de fusión más bajo entre las piezas de trabajo, y las piezas de trabajo no se funden. Le recomendamos que haga clic aquí paraDESCARGUE nuestras ilustraciones esquemáticas de los procesos de soldadura de AGS-TECH Inc.
Esto lo ayudará a comprender mejor la información que le brindamos a continuación.
En la SOLDADURA POR ARCO, usamos una fuente de alimentación y un electrodo para crear un arco eléctrico que funde los metales. El punto de soldadura está protegido por un gas o vapor de protección u otro material. Este proceso es popular para soldar piezas de automóviles y estructuras de acero. En la soldadura por arco metálico revestido (SMAW) o también conocida como soldadura por electrodo revestido, un electrodo revestido se acerca al material base y se genera un arco eléctrico entre ellos. La varilla del electrodo se funde y actúa como material de relleno. El electrodo también contiene fundente que actúa como una capa de escoria y emite vapores que actúan como gas de protección. Estos protegen el área de soldadura de la contaminación ambiental. No se utilizan otros rellenos. Las desventajas de este proceso son su lentitud, la necesidad de reemplazar los electrodos con frecuencia, la necesidad de eliminar la escoria residual que se origina del fundente. Una serie de metales como el hierro, el acero, el níquel, el aluminio, el cobre, etc. Se puede soldar. Sus ventajas son sus herramientas económicas y su facilidad de uso. La soldadura por arco metálico con gas (GMAW), también conocida como gas de metal inerte (MIG), tenemos alimentación continua de un relleno de alambre de electrodo consumible y un gas inerte o parcialmente inerte que fluye alrededor del alambre contra la contaminación ambiental de la región de soldadura. Se pueden soldar acero, aluminio y otros metales no ferrosos. Las ventajas de MIG son las altas velocidades de soldadura y la buena calidad. Las desventajas son su equipo complicado y los desafíos que enfrenta en ambientes exteriores ventosos porque tenemos que mantener estable el gas de protección alrededor del área de soldadura. Una variación de GMAW es la soldadura por arco con núcleo fundente (FCAW), que consiste en un tubo de metal fino lleno de materiales fundentes. A veces, el flujo dentro del tubo es suficiente para la protección contra la contaminación ambiental. La soldadura por arco sumergido (SAW, por sus siglas en inglés), un proceso ampliamente automatizado, implica la alimentación continua de alambre y un arco que se golpea bajo una capa de cubierta de fundente. Las tasas de producción y la calidad son altas, la escoria de soldadura se desprende fácilmente y tenemos un entorno de trabajo libre de humo. La desventaja es que solo se puede usar para soldar parts en ciertas posiciones. En la soldadura por arco de tungsteno con gas (GTAW) o la soldadura con gas inerte de tungsteno (TIG), utilizamos un electrodo de tungsteno junto con un relleno separado y gases inertes o casi inertes. Como sabemos, el tungsteno tiene un punto de fusión alto y es un metal muy adecuado para temperaturas muy altas. El tungsteno en TIG no se consume a diferencia de los otros métodos explicados anteriormente. Una técnica de soldadura lenta pero de alta calidad ventajosa sobre otras técnicas en la soldadura de materiales delgados. Adecuado para muchos metales. La soldadura por arco de plasma es similar pero utiliza gas de plasma para crear el arco. El arco en la soldadura por arco de plasma es relativamente más concentrado en comparación con GTAW y puede usarse para una gama más amplia de espesores de metal a velocidades mucho más altas. GTAW y la soldadura por arco de plasma se pueden aplicar a más o menos los mismos materiales.
SOLDADURA OXICOMBUSTIBLE/OXICOMBUSTIBLE también llamada soldadura oxiacetilénica, oxisoldadura, la soldadura a gas se lleva a cabo utilizando combustibles gaseosos y oxígeno para soldar. Como no se usa energía eléctrica, es portátil y se puede usar donde no hay electricidad. Usando un soplete de soldadura calentamos las piezas y el material de aporte para producir un baño de metal fundido compartido. Se pueden utilizar varios combustibles como acetileno, gasolina, hidrógeno, propano, butano…etc. En la soldadura oxicombustible utilizamos dos recipientes, uno para el combustible y otro para el oxígeno. El oxígeno oxida el combustible (lo quema).
SOLDADURA POR RESISTENCIA: Este tipo de soldadura aprovecha el calentamiento por joule y se genera calor en el lugar donde se aplica la corriente eléctrica durante un tiempo determinado. Se pasan altas corrientes a través del metal. En este lugar se forman charcos de metal fundido. Los métodos de soldadura por resistencia son populares debido a su eficiencia y poco potencial de contaminación. Sin embargo, las desventajas son que los costos del equipo son relativamente significativos y la limitación inherente a las piezas de trabajo relativamente delgadas. La SOLDADURA POR PUNTOS es uno de los principales tipos de soldadura por resistencia. Aquí unimos dos o más láminas superpuestas o piezas de trabajo usando dos electrodos de cobre para unir las láminas y pasar una corriente alta a través de ellas. El material entre los electrodos de cobre se calienta y se genera un baño de fusión en ese lugar. Luego se detiene la corriente y las puntas de los electrodos de cobre enfrían el lugar de la soldadura porque los electrodos se enfrían con agua. Aplicar la cantidad adecuada de calor al material y al grosor correctos es clave para esta técnica, porque si se aplica incorrectamente, la junta se debilitará. La soldadura por puntos tiene las ventajas de no causar una deformación significativa en las piezas de trabajo, la eficiencia energética, la facilidad de automatización y tasas de producción sobresalientes, y no requiere rellenos. La desventaja es que, dado que la soldadura se realiza en puntos en lugar de formar una costura continua, la resistencia general puede ser relativamente menor en comparación con otros métodos de soldadura. SEAM WELDING por otro lado produce soldaduras en las superficies de contacto de materiales similares. La costura puede ser a tope o solapada. La soldadura por costura comienza en un extremo y avanza progresivamente hacia el otro. Este método también usa dos electrodos de cobre para aplicar presión y corriente a la región de soldadura. Los electrodos en forma de disco giran con contacto constante a lo largo de la línea de costura y forman una soldadura continua. Aquí también, los electrodos se enfrían con agua. Las soldaduras son muy fuertes y fiables. Otros métodos son las técnicas de soldadura por proyección, flash y recalcada.
La SOLDADURA DE ESTADO SÓLIDO es un poco diferente a los métodos anteriores explicados anteriormente. La coalescencia tiene lugar a temperaturas por debajo de la temperatura de fusión de los metales unidos y sin uso de relleno metálico. La presión se puede utilizar en algunos procesos. Varios métodos son SOLDADURA DE COEXTRUSIÓN donde se extruyen metales diferentes a través del mismo troquel, SOLDADURA DE PRESIÓN EN FRÍO donde unimos aleaciones blandas por debajo de sus puntos de fusión, SOLDADURA DE DIFUSIÓN una técnica sin líneas de soldadura visibles, SOLDADURA DE EXPLOSIÓN para unir materiales diferentes, por ejemplo, aleaciones resistentes a la corrosión a estructuras aceros, SOLDADURA DE PULSO ELECTROMAGNÉTICO donde aceleramos tubos y láminas por fuerzas electromagnéticas, SOLDADURA DE FORJA que consiste en calentar los metales a altas temperaturas y martillarlos juntos, SOLDADURA DE FRICCIÓN donde con suficiente fricción se realiza la soldadura, SOLDADURA DE AGITACIÓN DE FRICCIÓN que involucra una rotación no- herramienta consumible que atraviesa la línea de unión, SOLDADURA DE PRESIÓN EN CALIENTE donde presionamos metales a temperaturas elevadas por debajo de la temperatura de fusión en vacío o gases inertes, SOLDADURA DE PRESIÓN ISOSTÁTICA EN CALIENTE un proceso en el que aplicamos presión usando gases inertes dentro de un recipiente, SOLDADURA DE RODILLO donde unimos materiales diferentes forzándolos entre dos ruedas giratorias, SOLDADURA ULTRASÓNICA donde se sueldan láminas delgadas de metal o plástico utilizando energía vibratoria de alta frecuencia.
Nuestros otros procesos de soldadura son SOLDADURA POR HAZ DE ELECTRONES con penetración profunda y procesamiento rápido, pero al ser un método costoso, lo consideramos para casos especiales, SOLDADURA CON ELECTROESCORIA, un método adecuado solo para placas gruesas y piezas de trabajo de acero, SOLDADURA POR INDUCCIÓN, donde usamos inducción electromagnética y calentar nuestras piezas de trabajo eléctricamente conductoras o ferromagnéticas, SOLDADURA POR HAZ LÁSER también con penetración profunda y procesamiento rápido pero un método costoso, SOLDADURA HÍBRIDA POR LÁSER que combina LBW con GMAW en el mismo cabezal de soldadura y capaz de salvar espacios de 2 mm entre placas, SOLDADURA POR PERCUSIÓN que consiste en una descarga eléctrica seguida de la forja de los materiales con presión aplicada, SOLDADURA TERMITA que implica una reacción exotérmica entre el aluminio y los polvos de óxido de hierro, SOLDADURA ELECTROGAS con electrodos consumibles y utilizada solo con acero en posición vertical, y finalmente SOLDADURA POR ARCO DE ESTUDIO para unir el perno a la base material con calor y presión.
Le recomendamos que haga clic aquí paraDESCARGUE nuestras ilustraciones esquemáticas de los procesos de soldadura fuerte, soldadura blanda y unión adhesiva de AGS-TECH Inc.
Esto lo ayudará a comprender mejor la información que le proporcionamos a continuación.
• SOLDADURA SOLDADURA: Unimos dos o más metales calentando los metales de aporte entre ellos por encima de sus puntos de fusión y utilizando la acción capilar para esparcirlos. El proceso es similar a la soldadura pero las temperaturas involucradas para derretir el relleno son más altas en la soldadura fuerte. Al igual que en la soldadura, el fundente protege el material de aporte de la contaminación atmosférica. Después del enfriamiento, las piezas de trabajo se unen. El proceso incluye los siguientes pasos clave: buen ajuste y espacio libre, limpieza adecuada de los materiales base, fijación adecuada, selección adecuada del fundente y la atmósfera, calentamiento del ensamblaje y, finalmente, limpieza del ensamblaje soldado. Algunos de nuestros procesos de soldadura fuerte son la soldadura fuerte con soplete, un método popular que se lleva a cabo de forma manual o automática. Es adecuado para pedidos de producción de bajo volumen y casos especializados. El calor se aplica mediante llamas de gas cerca de la junta que se está soldando. LA SOLDADURA EN HORNO requiere menos habilidad del operador y es un proceso semiautomático adecuado para la producción industrial en masa. Tanto el control de la temperatura como el control de la atmósfera en el horno son ventajas de esta técnica, ya que el primero nos permite tener ciclos de calor controlados y eliminar los calentamientos locales como ocurre en la soldadura fuerte con soplete, y el segundo protege la pieza de la oxidación. Utilizando jigging somos capaces de reducir al mínimo los costes de fabricación. Las desventajas son el alto consumo de energía, los costos del equipo y las consideraciones de diseño más desafiantes. La SOLDADURA AL VACÍO se realiza en un horno de vacío. Se mantiene la uniformidad de la temperatura y obtenemos juntas muy limpias y libres de fundente con muy pocas tensiones residuales. Los tratamientos térmicos pueden tener lugar durante la soldadura fuerte al vacío, debido a las bajas tensiones residuales presentes durante los ciclos lentos de calentamiento y enfriamiento. La principal desventaja es su alto costo porque la creación de un entorno de vacío es un proceso costoso. Otra técnica más, DIP BRAZING, une piezas fijas en las que se aplica compuesto de soldadura fuerte a las superficies de contacto. A partir de entonces, las piezas fixtured se sumergen en un baño de sal fundida como el cloruro de sodio (sal de mesa) que actúa como medio de transferencia de calor y fundente. Se excluye el aire y, por lo tanto, no se produce formación de óxido. En la SOLDADURA SOLDADURA POR INDUCCIÓN unimos materiales mediante un metal de aporte que tiene un punto de fusión más bajo que los materiales base. La corriente alterna de la bobina de inducción crea un campo electromagnético que induce el calentamiento por inducción en la mayoría de los materiales magnéticos ferrosos. El método proporciona calentamiento selectivo, buenas uniones con rellenos que fluyen solo en las áreas deseadas, poca oxidación porque no hay llamas y el enfriamiento es rápido, calentamiento rápido, consistencia e idoneidad para la fabricación de alto volumen. Para acelerar nuestros procesos y asegurar la consistencia, frecuentemente usamos preformas. Puede encontrar información sobre nuestra instalación de soldadura fuerte que produce accesorios de cerámica a metal, sellado hermético, pasamuros de vacío, vacío alto y ultraalto y componentes de control de fluidos aquí: Folleto de la fábrica de soldadura fuerte
• SOLDADURA: En la soldadura no tenemos fusión de las piezas de trabajo, sino un metal de aporte con un punto de fusión más bajo que las piezas de unión que fluye hacia la unión. El metal de aporte en la soldadura blanda se funde a una temperatura más baja que en la soldadura fuerte. Usamos aleaciones sin plomo para soldar y cumplimos con RoHS y para diferentes aplicaciones y requisitos tenemos aleaciones diferentes y adecuadas, como la aleación de plata. La soldadura nos ofrece uniones estancas a gases y líquidos. En SOLDADURA BLANDA, nuestro metal de aporte tiene un punto de fusión por debajo de los 400 Centígrados, mientras que en SOLDADURA DE PLATA y SOLDADURA BRAZADA necesitamos temperaturas más altas. La soldadura blanda utiliza temperaturas más bajas pero no da como resultado uniones fuertes para aplicaciones exigentes a temperaturas elevadas. La soldadura de plata, por otro lado, requiere altas temperaturas proporcionadas por la antorcha y nos brinda uniones fuertes adecuadas para aplicaciones de alta temperatura. La soldadura fuerte requiere las temperaturas más altas y, por lo general, se utiliza un soplete. Dado que las juntas de soldadura fuerte son muy fuertes, son buenas candidatas para reparar objetos pesados de hierro. En nuestras líneas de fabricación utilizamos tanto soldadura manual manual como líneas de soldadura automatizadas. SOLDADURA POR INDUCCIÓN utiliza corriente alterna de alta frecuencia en una bobina de cobre para facilitar el calentamiento por inducción. Se inducen corrientes en la parte soldada y, como resultado, se genera calor en la junta de alta resistencia . Este calor derrite el metal de aporte. También se utiliza fundente. La soldadura por inducción es un buen método para soldar cilindros y tuberías en un proceso continuo envolviendo las bobinas alrededor de ellos. Soldar algunos materiales como el grafito y la cerámica es más difícil porque requiere el revestimiento de las piezas de trabajo con un metal adecuado antes de soldar. Esto facilita la unión interfacial. Soldamos dichos materiales especialmente para aplicaciones de embalaje hermético. Fabricamos nuestras placas de circuito impreso (PCB) en gran volumen utilizando principalmente SOLDADURA POR ONDA. Solo para una pequeña cantidad de prototipos utilizamos soldadura manual con soldador. Utilizamos soldadura por ola tanto para ensamblajes de PCB de montaje superficial como de orificio pasante (PCBA). Un pegamento temporal mantiene los componentes unidos a la placa de circuito y el ensamblaje se coloca en un transportador y se mueve a través de un equipo que contiene soldadura fundida. Primero, la PCB recibe fundente y luego ingresa a la zona de precalentamiento. La soldadura fundida está en una bandeja y tiene un patrón de ondas estacionarias en su superficie. Cuando la PCB se mueve sobre estas ondas, estas ondas entran en contacto con la parte inferior de la PCB y se adhieren a las almohadillas de soldadura. La soldadura permanece solo en los pines y las almohadillas y no en la placa de circuito impreso. Las ondas en la soldadura fundida deben controlarse bien para que no haya salpicaduras y las puntas de las ondas no toquen ni contaminen áreas no deseadas de las placas. En la SOLDADURA POR REFLUJO, usamos una soldadura en pasta pegajosa para unir temporalmente los componentes electrónicos a las placas. Luego, las tablas se pasan por un horno de reflujo con control de temperatura. Aquí la soldadura se derrite y conecta los componentes de forma permanente. Utilizamos esta técnica tanto para componentes de montaje en superficie como para componentes de orificio pasante. El control adecuado de la temperatura y el ajuste de las temperaturas del horno son esenciales para evitar la destrucción de los componentes electrónicos de la placa al sobrecalentarlos por encima de sus límites máximos de temperatura. En el proceso de soldadura por reflujo, en realidad tenemos varias regiones o etapas, cada una con un perfil térmico distinto, como el paso de precalentamiento, el paso de remojo térmico, el reflujo y los pasos de enfriamiento. Estos diferentes pasos son esenciales para una soldadura por reflujo libre de daños de ensamblajes de placas de circuito impreso (PCBA). La SOLDADURA ULTRASÓNICA es otra técnica de uso frecuente con capacidades únicas: se puede usar para soldar vidrio, cerámica y materiales no metálicos. Por ejemplo, los paneles fotovoltaicos que no son metálicos necesitan electrodos que se puedan fijar mediante esta técnica. En la soldadura ultrasónica, desplegamos una punta de soldadura calentada que también emite vibraciones ultrasónicas. Estas vibraciones producen burbujas de cavitación en la interfaz del sustrato con el material de soldadura fundido. La energía implosiva de la cavitación modifica la superficie del óxido y elimina la suciedad y los óxidos. Durante este tiempo también se forma una capa de aleación. La soldadura en la superficie de unión incorpora oxígeno y permite la formación de un fuerte vínculo compartido entre el vidrio y la soldadura. La SOLDADURA POR INMERSIÓN se puede considerar como una versión más simple de la soldadura por ola adecuada solo para la producción a pequeña escala. Primero se aplica fundente de limpieza como en otros procesos. Los PCB con componentes montados se sumergen manualmente o de forma semiautomática en un tanque que contiene soldadura fundida. La soldadura fundida se adhiere a las áreas metálicas expuestas sin la protección de la máscara de soldadura en la placa. El equipo es simple y económico.
• UNIÓN ADHESIVA: esta es otra técnica popular que usamos con frecuencia e implica la unión de superficies con pegamentos, resinas epoxi, agentes plásticos u otros productos químicos. La unión se logra evaporando el solvente, curando con calor, curando con luz ultravioleta, curando a presión o esperando un cierto tiempo. En nuestras líneas de producción se utilizan varios pegamentos de alto rendimiento. Con procesos de aplicación y curado diseñados correctamente, la unión adhesiva puede resultar en uniones de muy baja tensión que son fuertes y confiables. Las uniones adhesivas pueden ser buenos protectores contra factores ambientales como la humedad, los contaminantes, los corrosivos, las vibraciones, etc. Las ventajas de la unión adhesiva son: se pueden aplicar a materiales que de otro modo serían difíciles de soldar, soldar o soldar. También puede ser preferible para materiales sensibles al calor que se dañarían por soldadura u otros procesos de alta temperatura. Otras ventajas de los adhesivos son que se pueden aplicar a superficies de forma irregular y aumentan el peso del ensamblaje en cantidades muy pequeñas en comparación con otros métodos. También los cambios dimensionales en las piezas son mínimos. Algunos pegamentos tienen propiedades de coincidencia de índices y se pueden usar entre componentes ópticos sin disminuir significativamente la intensidad de la señal óptica o de la luz. Las desventajas, por otro lado, son los tiempos de curado más largos que pueden ralentizar las líneas de fabricación, los requisitos de fijación, los requisitos de preparación de la superficie y la dificultad para desmontar cuando se necesita volver a trabajar. La mayoría de nuestras operaciones de unión adhesiva implican los siguientes pasos:
-Tratamiento de superficies: son comunes los procedimientos de limpieza especiales, como la limpieza con agua desionizada, la limpieza con alcohol, la limpieza con plasma o corona. Después de la limpieza podemos aplicar promotores de adherencia sobre las superficies para asegurar las mejores juntas posibles.
-Fijación de piezas: Tanto para la aplicación de adhesivos como para el curado, diseñamos y utilizamos fijaciones a medida.
-Aplicación de adhesivo: A veces usamos sistemas manuales y, según el caso, automatizados, como robótica, servomotores, actuadores lineales para entregar los adhesivos en el lugar correcto y usamos dispensadores para entregarlos en el volumen y la cantidad correctos.
-Curado: Dependiendo del adhesivo, podemos usar secado y curado simple, así como curado bajo luces UV que actúan como catalizador o curado por calor en un horno o usando elementos calefactores resistivos montados en plantillas y accesorios.
Le recomendamos que haga clic aquí paraDESCARGUE nuestras ilustraciones esquemáticas de los procesos de fijación de AGS-TECH Inc.
Esto lo ayudará a comprender mejor la información que le proporcionamos a continuación.
• PROCESOS DE FIJACIÓN: Nuestros procesos de unión mecánica se dividen en dos categorías principales: SUJETADORES y JUNTAS INTEGRALES. Ejemplos de sujetadores que utilizamos son tornillos, pasadores, tuercas, pernos, remaches. Ejemplos de juntas integrales que utilizamos son ajustes a presión y por contracción, costuras, engarces. Usando una variedad de métodos de sujeción, nos aseguramos de que nuestras uniones mecánicas sean fuertes y confiables para muchos años de uso. Los TORNILLOS y PERNOS son algunos de los sujetadores más utilizados para sujetar objetos y posicionarlos. Nuestros tornillos y pernos cumplen con los estándares ASME. Se implementan varios tipos de tornillos y pernos, incluidos tornillos de cabeza hexagonal y pernos hexagonales, tirafondos y pernos, tornillo de doble extremo, tornillo de espiga, tornillo de ojo, tornillo de espejo, tornillo de chapa, tornillo de ajuste fino, tornillos autorroscantes y autoperforantes. , tornillo de fijación, tornillos con arandelas incorporadas,… y más. Tenemos varios tipos de cabeza de tornillo, como cabeza avellanada, cúpula, redonda, con brida y varios tipos de tornillos, como ranura, phillips, cuadrado, hexágono interior. Un RIVET, por otro lado, es un sujetador mecánico permanente que consta de un eje cilíndrico liso y una cabeza por un lado. Después de la inserción, el otro extremo del remache se deforma y su diámetro se expande para que permanezca en su lugar. En otras palabras, antes de la instalación un remache tiene una cabeza y después de la instalación tiene dos. Instalamos varios tipos de remaches según la aplicación, la resistencia, la accesibilidad y el costo, como remaches de cabeza sólida/redonda, estructurales, semitubulares, ciegos, oscar, de accionamiento, al ras, de bloqueo por fricción y autoperforantes. Se puede preferir el remachado en los casos en que se deba evitar la deformación por calor y el cambio en las propiedades del material debido al calor de la soldadura. El remachado también ofrece un peso ligero y una resistencia y una resistencia especialmente buenas frente a las fuerzas de cizallamiento. Sin embargo, contra cargas de tracción, los tornillos, tuercas y pernos pueden ser más adecuados. En el proceso de CLINCHADO utilizamos punzones y matrices especiales para formar un enclavamiento mecánico entre las láminas de metal que se unen. El punzón empuja las capas de lámina de metal hacia la cavidad del troquel y da como resultado la formación de una junta permanente. No se requiere calentamiento ni enfriamiento en el clinchado y es un proceso de trabajo en frío. Es un proceso económico que puede reemplazar la soldadura por puntos en algunos casos. En PINNING utilizamos pasadores, que son elementos de máquina que se utilizan para asegurar las posiciones de las piezas de la máquina entre sí. Los tipos principales son pasadores de horquilla, pasador de chaveta, pasador de resorte, pasadores de espiga, y pasador partido. En GRAPADO utilizamos pistolas grapadoras y grapas, que son sujetadores de dos puntas que se usan para unir o unir materiales. El grapado tiene las siguientes ventajas: Económico, simple y rápido de usar, la corona de las grapas se puede usar para unir materiales unidos a tope. La corona de la grapa puede facilitar el puentear una pieza como un cable y fijarla a una superficie sin perforar o Eliminación dañina y relativamente fácil. El MONTAJE A PRESIÓN se realiza empujando las piezas juntas y la fricción entre ellas sujeta las piezas. Las piezas de ajuste a presión que consisten en un eje sobredimensionado y un orificio de tamaño insuficiente generalmente se ensamblan mediante uno de dos métodos: ya sea aplicando fuerza o aprovechando la expansión o contracción térmica de las piezas. Cuando se establece un ajuste a presión mediante la aplicación de una fuerza, usamos una prensa hidráulica o una prensa manual. Por otro lado, cuando el ajuste a presión se establece por expansión térmica, calentamos las partes envolventes y las ensamblamos en su lugar mientras están calientes. Cuando se enfrían se contraen y vuelven a sus dimensiones normales. Esto da como resultado un buen ajuste a presión. A esto lo llamamos alternativamente AJUSTE POR CONtracción. La otra forma de hacerlo es enfriando las partes envueltas antes del ensamblaje y luego deslizándolas en sus partes correspondientes. Cuando el conjunto se calienta se expanden y obtenemos un ajuste perfecto. Este último método puede ser preferible en los casos en que el calentamiento presente el riesgo de cambiar las propiedades del material. El enfriamiento es más seguro en esos casos.
Componentes y conjuntos neumáticos e hidráulicos
• Válvulas, componentes hidráulicos y neumáticos tales como O-ring, arandela, sellos, empaquetadura, anillo, cuña.
Dado que las válvulas y los componentes neumáticos vienen en una gran variedad, no podemos enumerarlos todos aquí. Dependiendo de los entornos físicos y químicos de su aplicación, tenemos productos especiales para usted. Por favor especifíquenos la aplicación, tipo de componente, especificaciones, condiciones ambientales como presión, temperatura, líquidos o gases que estarán en contacto con sus válvulas y componentes neumáticos; y elegiremos el producto más adecuado para usted o lo fabricaremos especialmente para su aplicación.