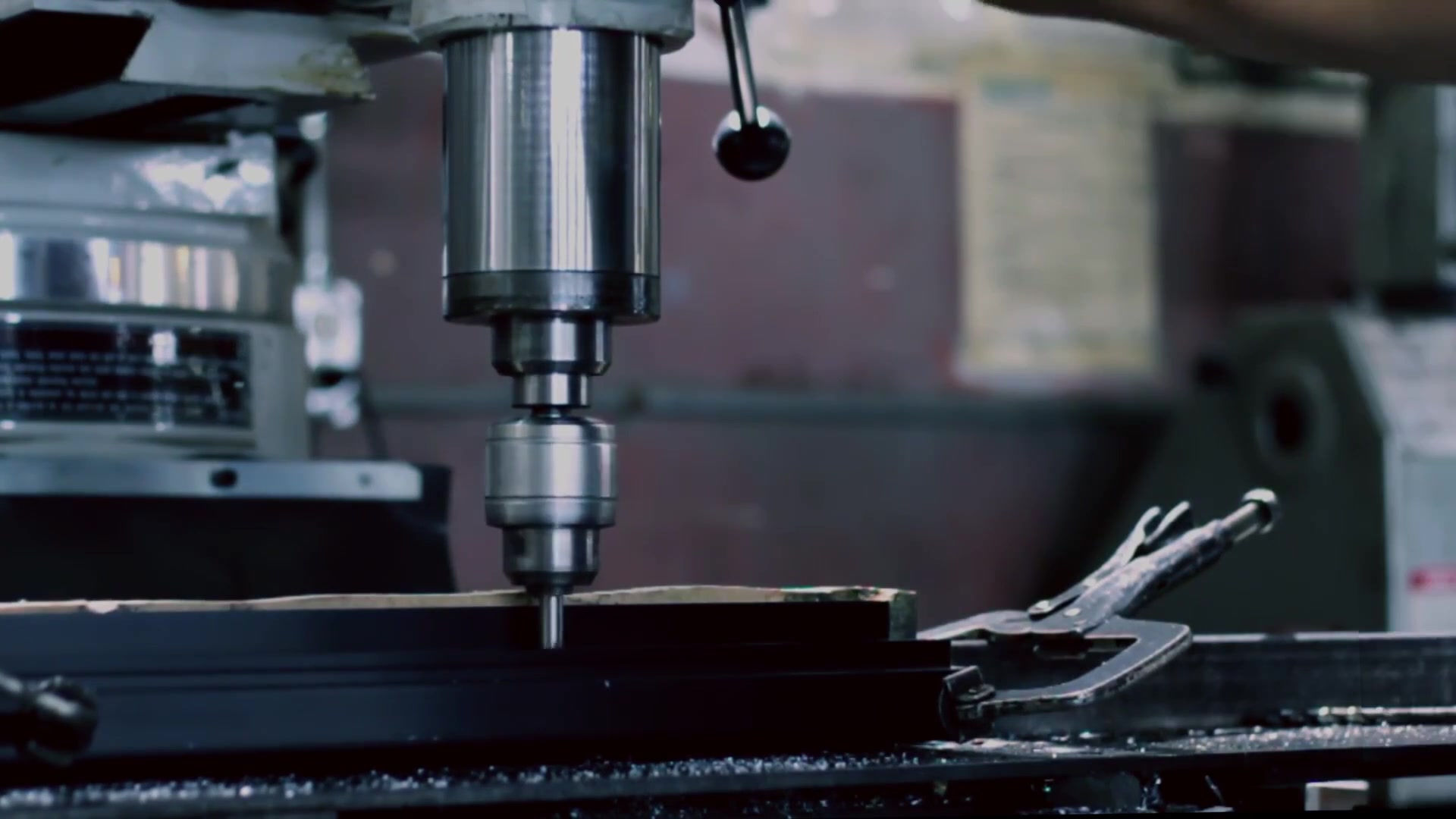
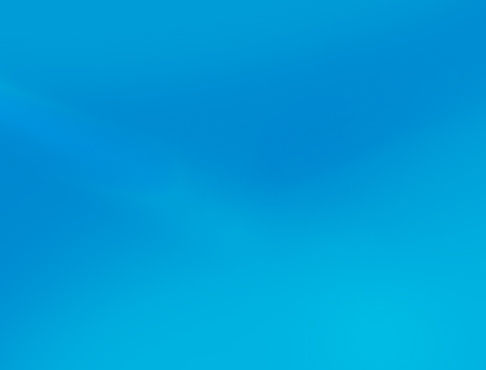
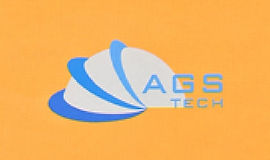
Fabricante personalizado global, integrador, consolidador, socio de subcontratación para una amplia variedad de productos y servicios.
Somos su fuente única para la fabricación, la fabricación, la ingeniería, la consolidación, la integración y la subcontratación de productos y servicios fabricados a medida y listos para usar.
Choose your Language
-
Fabricación personalizada
-
Fabricación por contrato nacional y mundial
-
Subcontratación de fabricación
-
Adquisiciones nacionales y globales
-
Consolidación
-
Integración de ingeniería
-
Servicios de Ingenieria
El tipo de procesos de FORJADO DE METALES que ofrecemos son matriz en frío y en caliente, matriz abierta y matriz cerrada, matriz de impresión y forjado sin rebabas, cogging, fullering, ribeteado y forjado de precisión, forma casi neta, encabezado , estampado, forjado recalcado, tallado de metal, prensado y laminado, forjado radial, orbital, de anillo e isotérmico, acuñado, remachado, forjado de bolas de metal, perforado de metal, dimensionado, forjado de alta tasa de energía.
Nuestras técnicas de METALURGIA DE POLVO y PROCESAMIENTO DE POLVO son prensado y sinterizado de polvo, impregnación, infiltración, prensado isostático en frío y en caliente, moldeo por inyección de metal, compactación con rodillos, laminado de polvo, extrusión de polvo, sinterizado suelto, sinterizado por chispa, prensado en caliente.
Le recomendamos que haga clic aquí para
DESCARGUE nuestras ilustraciones esquemáticas de los procesos de forja de AGS-TECH Inc.
DESCARGUE nuestras ilustraciones esquemáticas de los procesos de pulvimetalurgia de AGS-TECH Inc.
Estos archivos descargables con fotos y bocetos te ayudarán a comprender mejor la información que te proporcionamos a continuación.
En la forja de metales, se aplican fuerzas de compresión y se deforma el material y se obtiene la forma deseada. Los materiales forjados más comunes en la industria son el hierro y el acero, pero muchos otros, como el aluminio, el cobre, el titanio y el magnesio, también se forjan ampliamente. Las piezas de metal forjado tienen estructuras de grano mejoradas además de grietas selladas y espacios vacíos cerrados, por lo que la resistencia de las piezas obtenidas por este proceso es mayor. La forja produce piezas que son significativamente más resistentes por su peso que las piezas fabricadas por fundición o mecanizado. Dado que las piezas forjadas se moldean haciendo que el metal fluya hasta su forma final, el metal adquiere una estructura de grano direccional que explica la resistencia superior de las piezas. En otras palabras, las piezas obtenidas por el proceso de forja presentan mejores propiedades mecánicas en comparación con las piezas de fundición simple o mecanizadas. El peso de las piezas forjadas de metal puede variar desde piezas pequeñas y livianas hasta cientos de miles de libras. Fabricamos piezas forjadas principalmente para aplicaciones mecánicamente exigentes en las que se aplican grandes tensiones en piezas como piezas de automóviles, engranajes, herramientas de trabajo, herramientas manuales, ejes de turbinas, engranajes de motocicletas. Debido a que los costos de configuración y herramientas son relativamente altos, recomendamos este proceso de fabricación solo para la producción de alto volumen y para componentes críticos de bajo volumen pero de alto valor, como el tren de aterrizaje aeroespacial. Además del costo de las herramientas, los plazos de entrega de fabricación para grandes cantidades de piezas forjadas pueden ser más largos en comparación con algunas piezas mecanizadas simples, pero la técnica es crucial para las piezas que requieren una resistencia extraordinaria, como pernos, tuercas, aplicaciones especiales tornillería, automotriz, montacargas, repuestos para grúas.
• FORJA EN CALIENTE Y EN FRÍO: La forja en caliente, como su nombre lo indica, se realiza a altas temperaturas, por lo que la ductilidad es alta y la resistencia del material baja. Esto facilita la fácil deformación y forja. Por el contrario, la forja en frío se lleva a cabo a temperaturas más bajas y requiere fuerzas más altas, lo que da como resultado un endurecimiento por deformación, un mejor acabado superficial y precisión de las piezas fabricadas.
• FORJA DE MATRIZ ABIERTA e IMPRESIÓN: En la forja de matriz abierta, las matrices no restringen el material que se comprime, mientras que en la forja de matriz de impresión, las cavidades dentro de las matrices restringen el flujo de material mientras se forja en la forma deseada. FORJADO ALTERADO o también llamado ALTERADO, que en realidad no es lo mismo pero es un proceso muy similar, es un proceso de troquel abierto en el que la pieza de trabajo se intercala entre dos troqueles planos y una fuerza de compresión reduce su altura. A medida que la altura is reduced, el ancho de la pieza de trabajo aumenta. HEADING, un proceso de forja recalcada involucra un material cilíndrico que está recalcado en su extremo y su sección transversal aumenta localmente. En el encabezado, el material se alimenta a través del troquel, se forja y luego se corta a la medida. La operación es capaz de producir grandes cantidades de sujetadores rápidamente. En su mayoría, es una operación de trabajo en frío porque se usa para hacer extremos de clavos, extremos de tornillos, tuercas y pernos donde el material necesita ser reforzado. Otro proceso de troquel abierto es COGGING, donde la pieza de trabajo se forja en una serie de pasos y cada paso da como resultado la compresión del material y el movimiento subsiguiente del troquel abierto a lo largo de la pieza de trabajo. En cada paso, el grosor se reduce y la longitud aumenta en una pequeña cantidad. El proceso se asemeja a un estudiante nervioso que muerde su lápiz todo el tiempo en pequeños pasos. Un proceso llamado FULLERING es otro método de forjado con troquel abierto que a menudo implementamos como un paso anterior para distribuir el material en la pieza de trabajo antes de que se lleven a cabo otras operaciones de forjado de metal. Lo usamos cuando la pieza de trabajo requiere varias forging operations. En la operación, el troquel con superficies convexas se deforma y hace que el metal fluya hacia ambos lados. Un proceso similar al batanado, el BORDEADO, por otro lado, implica un troquel abierto con superficies cóncavas para deformar la pieza de trabajo. El canteado, también un proceso preparatorio para las operaciones de forjado posteriores, hace que el material fluya desde ambos lados hacia un área en el centro. La FORJA EN MATRIZ DE IMPRESIÓN o FORJA EN MATRIZ CERRADA, como también se le llama, utiliza una matriz/molde que comprime el material y restringe su flujo dentro de sí mismo. El troquel se cierra y el material toma la forma de la cavidad del troquel/molde. LA FORJA DE PRECISIÓN, un proceso que requiere equipos y moldes especiales, produce piezas sin rebaba o con muy poca rebaba. En otras palabras, las piezas tendrán dimensiones casi finales. En este proceso, una cantidad bien controlada de material se inserta y coloca cuidadosamente dentro del molde. Implementamos este método para formas complejas con secciones delgadas, pequeñas tolerancias y ángulos de desmoldeo y cuando las cantidades son lo suficientemente grandes como para justificar los costos del molde y el equipo.
• FORJA SIN FLASH: La pieza de trabajo se coloca en la matriz de tal manera que ningún material pueda fluir fuera de la cavidad para formar flash. Por lo tanto, no se necesita un recorte de flash no deseado. Es un proceso de forjado de precisión y, por lo tanto, requiere un control estricto de la cantidad de material utilizado.
• ESTAMPACIÓN DE METALES o FORJA RADIAL: Una pieza de trabajo se actúa circunferencialmente sobre una matriz y se forja. También se puede usar un mandril para forjar la geometría interior de la pieza de trabajo. En la operación de estampado, la pieza de trabajo recibe típicamente varios golpes por segundo. Los artículos típicos producidos por estampado son herramientas de punta puntiaguda, barras cónicas, destornilladores.
• PERFORACIÓN DE METALES: Utilizamos esta operación frecuentemente como una operación adicional en la fabricación de piezas. Se crea un agujero o cavidad con perforación en la superficie de la pieza de trabajo sin romperla. Tenga en cuenta que la perforación es diferente a la perforación que da como resultado un orificio pasante.
• TALADRO : Se presiona un punzón con la geometría deseada en la pieza de trabajo y crea una cavidad con la forma deseada. A este golpe lo llamamos HOB. La operación implica altas presiones y se realiza en frío. Como resultado, el material se trabaja en frío y se endurece por deformación. Por tanto este proceso es muy adecuado para la fabricación de moldes, matrices y cavidades para otros procesos de fabricación. Una vez fabricada la placa, se pueden fabricar fácilmente muchas cavidades idénticas sin necesidad de mecanizarlas una a una.
• ROLL FORGING o ROLL FORMING: Se utilizan dos rodillos opuestos para dar forma a la pieza metálica. La pieza de trabajo se introduce en los rodillos, los rodillos giran y empujan el trabajo hacia el espacio, luego el trabajo se alimenta a través de la parte ranurada de los rodillos y las fuerzas de compresión le dan al material la forma deseada. No es un proceso de laminación sino un proceso de forja, porque es una operación discreta en lugar de continua. La geometría en los surcos de los rodillos forja el material a la forma y geometría requeridas. Se realiza en caliente. Debido a que es un proceso de forja, produce piezas con excelentes propiedades mecánicas y, por lo tanto, lo usamos para fabricación de piezas de automóviles, como ejes, que deben tener una resistencia extraordinaria en entornos de trabajo difíciles.
• FORJA ORBITAL: la pieza de trabajo se coloca en una cavidad de matriz de forja y se forja mediante una matriz superior que se desplaza en una trayectoria orbital mientras gira sobre un eje inclinado. En cada revolución, el troquel superior termina de ejercer fuerzas de compresión en toda la pieza de trabajo. Repitiendo estas revoluciones varias veces, se realiza una forja suficiente. Las ventajas de esta técnica de fabricación son su bajo nivel de ruido y la necesidad de menos fuerzas. En otras palabras, con pequeñas fuerzas se puede girar un troquel pesado alrededor de un eje para aplicar grandes presiones sobre una sección de la pieza de trabajo que está en contacto con el troquel. Las piezas con forma de disco o cónicas a veces son una buena opción para este proceso.
• FORJA DE ANILLOS: Utilizamos frecuentemente para fabricar anillos sin costura. El material se corta a la medida, se revuelve y luego se perfora completamente para crear un orificio central. Luego se coloca en un mandril y un troquel de forja lo martilla desde arriba mientras el anillo gira lentamente hasta obtener las dimensiones deseadas.
• REMACHADO: Un proceso común para unir partes, comienza con una pieza de metal recta insertada en agujeros prefabricados a través de las partes. A partir de entonces, los dos extremos de la pieza de metal se forjan apretando la unión entre un troquel superior e inferior.
• CINADO : Otro proceso popular realizado por prensa mecánica, ejerciendo grandes fuerzas en una corta distancia. El nombre "acuñación" proviene de los finos detalles que se forjan en las superficies de las monedas de metal. Es principalmente un proceso de acabado de un producto donde se obtienen detalles finos en las superficies como resultado de la gran fuerza aplicada por el troquel que transfiere estos detalles a la pieza de trabajo.
• FORJA DE BOLAS METÁLICAS: productos como los rodamientos de bolas requieren bolas metálicas de alta calidad fabricadas con precisión. En una técnica llamada SKEW ROLLING, usamos dos rodillos opuestos que giran continuamente a medida que el material se alimenta continuamente a los rodillos. En un extremo de los dos rodillos se expulsan esferas de metal como producto. Un segundo método para la forja de bolas de metal es usar un troquel que aprieta el stock de material colocado entre ellos tomando la forma esférica de la cavidad del molde. A menudo, los balones producidos requieren algunos pasos adicionales, como el acabado y el pulido, para convertirse en un producto de alta calidad.
• FORJA ISOTÉRMICA / FORJA EN CALIENTE: Un proceso costoso que se realiza solo cuando el valor beneficio/costo está justificado. Un proceso de trabajo en caliente en el que el troquel se calienta a aproximadamente la misma temperatura que la pieza de trabajo. Dado que tanto la matriz como el trabajo tienen aproximadamente la misma temperatura, no hay enfriamiento y se mejoran las características de flujo del metal. La operación es adecuada para superaleaciones y materiales con forjabilidad inferior y materiales cuyos
las propiedades mecánicas son muy sensibles a pequeños gradientes y cambios de temperatura.
• CALIBRADO DE METALES: Es un proceso de acabado en frío. El flujo de material no está restringido en todas las direcciones con la excepción de la dirección en la que se aplica la fuerza. Como resultado, se obtienen muy buenos acabados superficiales y dimensiones precisas.
• FORJA DE ALTO RENDIMIENTO DE ENERGÍA: La técnica consiste en un molde superior unido al brazo de un pistón que se empuja rápidamente cuando una bujía enciende una mezcla de combustible y aire. Se asemeja al funcionamiento de los pistones en el motor de un automóvil. El molde golpea la pieza de trabajo muy rápido y luego vuelve a su posición original muy rápido gracias a la contrapresión. El trabajo se fragua en unos pocos milisegundos y, por lo tanto, no hay tiempo para que el trabajo se enfríe. Esto es útil para piezas difíciles de forjar que tienen propiedades mecánicas muy sensibles a la temperatura. En otras palabras, el proceso es tan rápido que la pieza se forma bajo una temperatura constante y no habrá gradientes de temperatura en las interfaces del molde/pieza de trabajo.
• En la FORJA EN MATRICES, el metal se golpea entre dos bloques de acero iguales con formas especiales, llamados matrices. Cuando el metal se martilla entre los troqueles, asume la misma forma que las formas en el troquel. Cuando alcanza su forma definitiva se saca a enfriar. Este proceso produce piezas fuertes que tienen una forma precisa, pero requiere una mayor inversión para los troqueles especializados. La forja alterada aumenta el diámetro de una pieza de metal al aplanarla. Generalmente se usa para hacer piezas pequeñas, especialmente para formar cabezas en sujetadores como pernos y clavos.
• POLVOMETALURGIA / PROCESAMIENTO DE POLVO: Como su nombre lo indica, involucra procesos de manufactura para hacer partes sólidas de ciertas geometrías y formas a partir de polvos. Si se utilizan polvos metálicos para este propósito, es el ámbito de la pulvimetalurgia y si se utilizan polvos no metálicos, es el procesamiento de polvos. Las piezas sólidas se producen a partir de polvos mediante prensado y sinterización.
El PRENSADO DE POLVO se usa para compactar polvos en las formas deseadas. Primero, el material primario se pulveriza físicamente, dividiéndolo en muchas pequeñas partículas individuales. La mezcla de polvo se llena en la matriz y un punzón se mueve hacia el polvo y lo compacta en la forma deseada. Realizado mayoritariamente a temperatura ambiente, con el prensado de polvo se obtiene una parte sólida y se denomina compacto verde. Los aglutinantes y lubricantes se utilizan comúnmente para mejorar la compactabilidad. Somos capaces de formar prensas de polvo usando prensas hidráulicas con varios miles de toneladas de capacidad. También tenemos prensas de doble acción con punzones superiores e inferiores opuestos, así como prensas de acción múltiple para geometrías de piezas altamente complejas. La uniformidad, que es un desafío importante para muchas plantas de procesamiento de pulvimetalurgia/polvo, no es un gran problema para AGS-TECH debido a nuestra amplia experiencia en la fabricación personalizada de este tipo de piezas durante muchos años. Incluso con piezas más gruesas donde la uniformidad representa un desafío, hemos tenido éxito. Si nos comprometemos con tu proyecto, fabricaremos tus piezas. Si vemos algún riesgo potencial, le informaremos en
avance.
LA SINTERIZACIÓN DE POLVO, que es el segundo paso, implica el aumento de la temperatura hasta cierto grado y el mantenimiento de la temperatura a ese nivel durante un cierto tiempo para que las partículas de polvo en la parte prensada puedan unirse entre sí. Esto da como resultado uniones mucho más fuertes y un fortalecimiento de la pieza de trabajo. La sinterización tiene lugar cerca de la temperatura de fusión del polvo. Durante la sinterización se producirá una contracción, la resistencia del material, la densidad, la ductilidad, la conductividad térmica y la conductividad eléctrica aumentarán. Disponemos de hornos discontinuos y continuos para la sinterización. Una de nuestras capacidades es ajustar el nivel de porosidad de las piezas que producimos. Por ejemplo, podemos producir filtros de metal manteniendo las partes porosas hasta cierto punto.
Mediante una técnica denominada IMPREGNACIÓN, rellenamos los poros del metal con un fluido como el aceite. Producimos, por ejemplo, rodamientos impregnados de aceite que son autolubricantes. En el proceso de INFILTRACIÓN llenamos los poros de un metal con otro metal de menor punto de fusión que el material base. La mezcla se calienta a una temperatura intermedia entre las temperaturas de fusión de los dos metales. Como resultado, se pueden obtener algunas propiedades especiales. También realizamos con frecuencia operaciones secundarias, como mecanizado y forjado en piezas fabricadas con polvo, cuando es necesario obtener características o propiedades especiales o cuando la pieza se puede fabricar con menos pasos de proceso.
PRENSADO ISOSTÁTICO: En este proceso se utiliza la presión de un fluido para compactar la pieza. Los polvos metálicos se colocan en un molde hecho de un recipiente flexible sellado. En el prensado isostático, la presión se aplica desde todos los lados, a diferencia de la presión axial que se observa en el prensado convencional. Las ventajas del prensado isostático son la densidad uniforme dentro de la pieza, especialmente para piezas más grandes o más gruesas, propiedades superiores. Su desventaja son los largos tiempos de ciclo y las precisiones geométricas relativamente bajas. El PRENSADO ISOSTÁTICO EN FRÍO se realiza a temperatura ambiente y el molde flexible es de caucho, PVC o uretano o materiales similares. El fluido utilizado para presurizar y compactar es aceite o agua. A esto sigue la sinterización convencional del compacto verde. EL PRENSADO ISOSTÁTICO EN CALIENTE, por el contrario, se realiza a altas temperaturas y el material del molde es chapa o cerámica con un punto de fusión suficientemente alto para resistir las temperaturas. El fluido de presurización suele ser un gas inerte. Las operaciones de prensado y sinterizado se realizan en un solo paso. La porosidad se elimina casi por completo, se obtiene una estructura uniform grain. La ventaja del prensado isostático en caliente es que puede producir piezas comparables a la fundición y la forja combinadas, al tiempo que permite utilizar materiales que no son adecuados para la fundición y la forja. La desventaja del prensado isostático en caliente es su tiempo de ciclo alto y, por lo tanto, su costo. Es adecuado para piezas críticas de bajo volumen.
MOLDEO POR INYECCIÓN DE METALES: Proceso muy adecuado para producir piezas complejas con paredes delgadas y geometrías detalladas. Más adecuado para piezas más pequeñas. Los polvos y el aglutinante polimérico se mezclan, calientan e inyectan en un molde. El aglutinante polimérico recubre las superficies de las partículas de polvo. Después del moldeo, el aglutinante se elimina mediante calentamiento a baja temperatura o disuelto usando un solvente.
COMPACTACIÓN DE ROLLOS / LAMINACIÓN DE POLVO: Los polvos se utilizan para producir tiras o láminas continuas. El polvo se alimenta desde un alimentador y se compacta mediante dos rodillos giratorios en láminas o tiras. La operación se realiza en frío. La hoja se lleva a un horno de sinterización. El proceso de sinterización puede repetirse una segunda vez.
EXTRUSIÓN DE POLVO: Las piezas con una gran relación longitud/diámetro se fabrican mediante la extrusión de un recipiente de chapa fina con polvo.
SINTERIZACIÓN SUELTA: Como su nombre lo indica, es un método de compactación y sinterización sin presión, adecuado para producir piezas muy porosas como filtros metálicos. El polvo se introduce en la cavidad del molde sin compactarse.
SINTERIZACIÓN SUELTA: Como su nombre lo indica, es un método de compactación y sinterización sin presión, adecuado para producir piezas muy porosas como filtros metálicos. El polvo se introduce en la cavidad del molde sin compactarse.
SINTERIZACIÓN POR CHISPA: El polvo se comprime en el molde mediante dos punzones opuestos y se aplica una corriente eléctrica de alta potencia al punzón y pasa a través del polvo compactado intercalado entre ellos. La alta corriente quema las películas superficiales de las partículas de polvo y las sinteriza con el calor generado. El proceso es rápido porque no se aplica calor desde el exterior sino que se genera desde el interior del molde.
PRENSADO EN CALIENTE: Los polvos se prensan y sinterizan en un solo paso en un molde que puede soportar las altas temperaturas. A medida que la matriz se compacta, se le aplica el calor del polvo. Las buenas precisiones y propiedades mecánicas logradas con este método lo convierten en una opción atractiva. Incluso los metales refractarios se pueden procesar utilizando materiales de molde como el grafito.