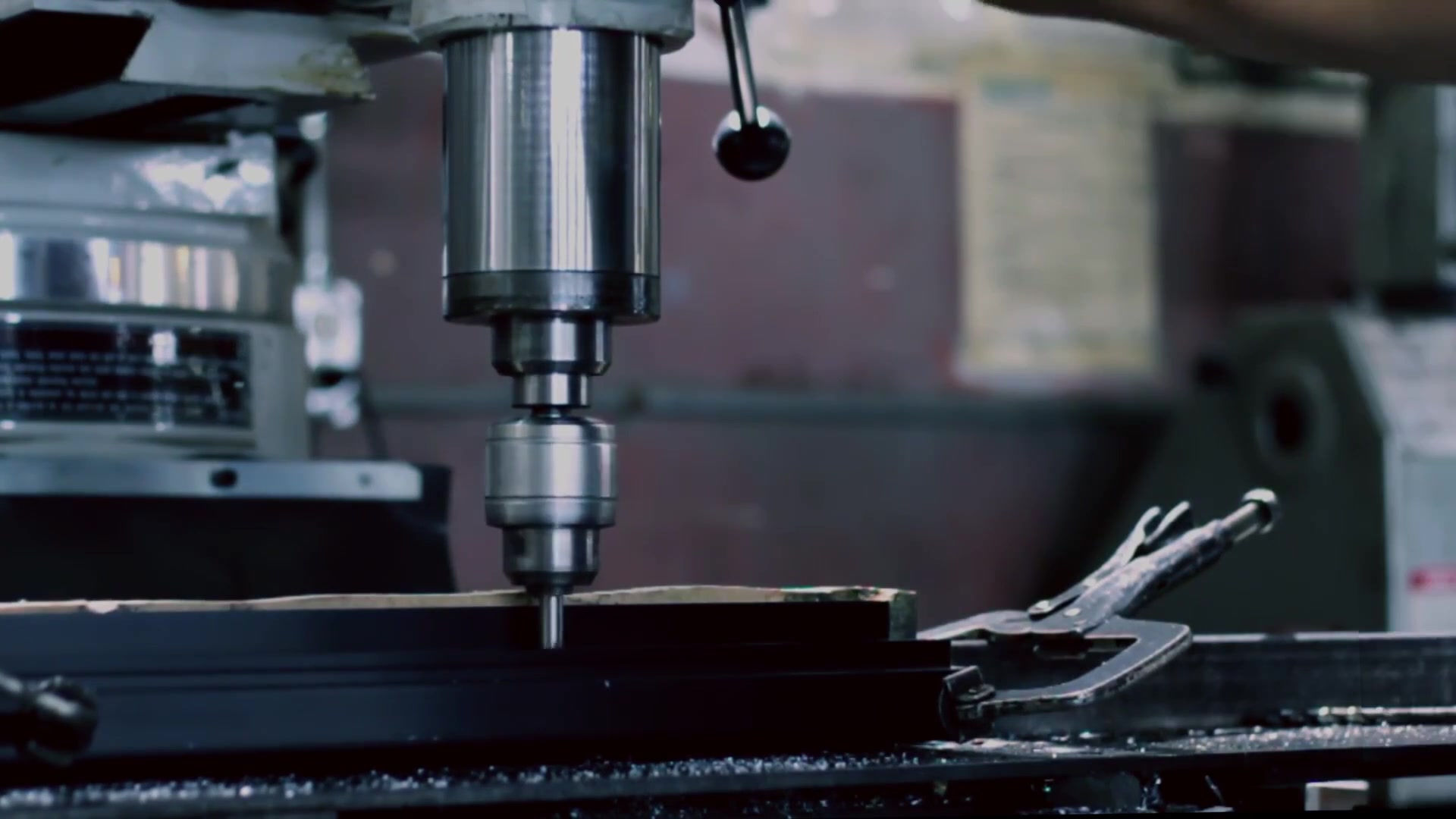
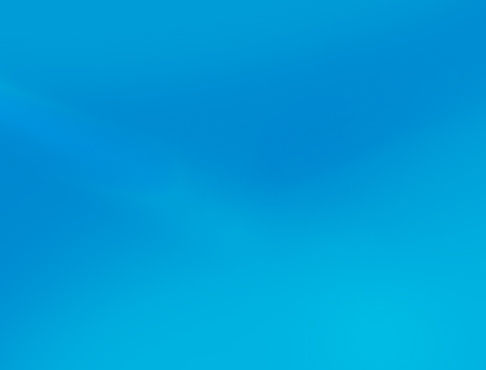
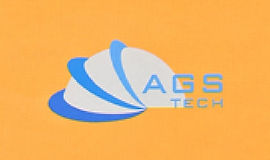
Fabricante personalizado global, integrador, consolidador, socio de subcontratación para una amplia variedad de productos y servicios.
Somos su fuente única para la fabricación, la fabricación, la ingeniería, la consolidación, la integración y la subcontratación de productos y servicios fabricados a medida y listos para usar.
Choose your Language
-
Fabricación personalizada
-
Fabricación por contrato nacional y mundial
-
Subcontratación de fabricación
-
Adquisiciones nacionales y globales
-
Consolidación
-
Integración de ingeniería
-
Servicios de Ingenieria
Fabricación y fabricación de microelectrónica y semiconductores
Muchas de nuestras técnicas y procesos de nanofabricación, microfabricación y mesomafabricación que se explican en los otros menús se pueden utilizar para MICROELECTRONICS MANUFACTURING too. Sin embargo, debido a la importancia de la microelectrónica en nuestros productos, aquí nos concentraremos en el tema de las aplicaciones específicas de estos procesos. Los procesos relacionados con la microelectrónica también se conocen ampliamente como SEMICONDUCTOR FABRICATION processes. Nuestros servicios de diseño y fabricación de ingeniería de semiconductores incluyen:
- Diseño, desarrollo y programación de placas FPGA
- Servicios de fundición de microelectrónica: diseño, creación de prototipos y fabricación, servicios de terceros
- Preparación de obleas de semiconductores: troceado, rectificado, adelgazamiento, colocación de retículas, clasificación de troqueles, selección y colocación, inspección
- Diseño y fabricación de paquetes microelectrónicos: diseño y fabricación estándar y personalizados
- Ensamblaje y empaquetado y prueba de circuitos integrados de semiconductores: Unión de troqueles, cables y chips, encapsulación, ensamblaje, marcado y marca
- Estructuras de plomo para dispositivos semiconductores: diseño y fabricación estándar y personalizados
- Diseño y fabricación de disipadores de calor para microelectrónica: diseño y fabricación estándar y personalizados
- Diseño y fabricación de sensores y actuadores: diseño y fabricación estándar y personalizados
- Diseño y fabricación de circuitos optoelectrónicos y fotónicos
Examinemos las tecnologías de prueba y fabricación de microelectrónica y semiconductores con más detalle para que pueda comprender mejor los servicios y productos que ofrecemos.
Diseño, desarrollo y programación de placas FPGA: las matrices de puertas programables en campo (FPGA) son chips de silicio reprogramables. A diferencia de los procesadores que se encuentran en las computadoras personales, la programación de un FPGA vuelve a cablear el chip para implementar la funcionalidad del usuario en lugar de ejecutar una aplicación de software. Usando bloques lógicos preconstruidos y recursos de enrutamiento programables, los chips FPGA se pueden configurar para implementar una funcionalidad de hardware personalizada sin usar una placa de pruebas ni un soldador. Las tareas de computación digital se llevan a cabo en software y se compilan en un archivo de configuración o flujo de bits que contiene información sobre cómo se deben conectar los componentes entre sí. Los FPGA se pueden usar para implementar cualquier función lógica que un ASIC podría realizar y son completamente reconfigurables y se les puede dar una "personalidad" completamente diferente al volver a compilar una configuración de circuito diferente. Los FPGA combinan las mejores partes de los circuitos integrados específicos de la aplicación (ASIC) y los sistemas basados en procesadores. Estos beneficios incluyen lo siguiente:
• Tiempos de respuesta de E/S más rápidos y funcionalidad especializada
• Superar la potencia informática de los procesadores de señales digitales (DSP)
• Creación rápida de prototipos y verificación sin el proceso de fabricación de ASIC personalizado
• Implementación de funcionalidad personalizada con la confiabilidad de hardware determinista dedicado
• Actualizable en campo, lo que elimina el gasto de rediseño y mantenimiento de ASIC personalizado
Los FPGA brindan velocidad y confiabilidad, sin requerir grandes volúmenes para justificar el gran gasto inicial del diseño ASIC personalizado. El silicio reprogramable también tiene la misma flexibilidad de software que se ejecuta en sistemas basados en procesadores y no está limitado por la cantidad de núcleos de procesamiento disponibles. A diferencia de los procesadores, los FPGA son verdaderamente de naturaleza paralela, por lo que las diferentes operaciones de procesamiento no tienen que competir por los mismos recursos. Cada tarea de procesamiento independiente se asigna a una sección dedicada del chip y puede funcionar de forma autónoma sin ninguna influencia de otros bloques lógicos. Como resultado, el rendimiento de una parte de la aplicación no se ve afectado cuando se agrega más procesamiento. Algunos FPGA tienen características analógicas además de funciones digitales. Algunas características analógicas comunes son la velocidad de giro programable y la fuerza de accionamiento en cada pin de salida, lo que permite al ingeniero establecer tasas lentas en pines con poca carga que, de lo contrario, sonarían o se acoplarían de manera inaceptable, y establecer tasas más fuertes y rápidas en pines con mucha carga en alta velocidad. canales que, de otro modo, correrían demasiado lento. Otra característica analógica relativamente común son los comparadores diferenciales en los pines de entrada diseñados para conectarse a canales de señalización diferencial. Algunos FPGA de señal mixta tienen convertidores periféricos de analógico a digital (ADC) y convertidores de digital a analógico (DAC) integrados con bloques de acondicionamiento de señales analógicas que les permiten operar como un sistema en un chip.
Brevemente, los 5 principales beneficios de los chips FPGA son:
1. Buen rendimiento
2. Corto tiempo de comercialización
3. Bajo costo
4. Alta confiabilidad
5. Capacidad de mantenimiento a largo plazo
Buen rendimiento: con su capacidad de acomodar el procesamiento paralelo, los FPGA tienen una mejor potencia informática que los procesadores de señales digitales (DSP) y no requieren una ejecución secuencial como los DSP y pueden lograr más por ciclos de reloj. El control de entradas y salidas (E/S) a nivel de hardware proporciona tiempos de respuesta más rápidos y una funcionalidad especializada para adaptarse a los requisitos de la aplicación.
Tiempo de comercialización corto: los FPGA ofrecen flexibilidad y capacidades de creación rápida de prototipos y, por lo tanto, un tiempo de comercialización más corto. Nuestros clientes pueden probar una idea o concepto y verificarlo en hardware sin pasar por el largo y costoso proceso de fabricación del diseño ASIC personalizado. Podemos implementar cambios incrementales e iterar en un diseño de FPGA en cuestión de horas en lugar de semanas. El hardware estándar comercial también está disponible con diferentes tipos de E/S ya conectados a un chip FPGA programable por el usuario. La creciente disponibilidad de herramientas de software de alto nivel ofrece valiosos núcleos de IP (funciones preconstruidas) para control avanzado y procesamiento de señales.
Bajo costo: los gastos de ingeniería no recurrentes (NRE) de los diseños ASIC personalizados superan los de las soluciones de hardware basadas en FPGA. La gran inversión inicial en ASIC puede justificarse para los OEM que producen muchos chips al año; sin embargo, muchos usuarios finales necesitan una funcionalidad de hardware personalizada para los muchos sistemas en desarrollo. Nuestro FPGA de silicio programable le ofrece algo sin costos de fabricación ni largos plazos de entrega para el ensamblaje. Los requisitos del sistema cambian con frecuencia con el tiempo, y el costo de realizar cambios incrementales en los diseños de FPGA es insignificante en comparación con el gran gasto de volver a girar un ASIC.
Alta confiabilidad: las herramientas de software proporcionan el entorno de programación y los circuitos FPGA son una verdadera implementación de la ejecución del programa. Los sistemas basados en procesadores generalmente involucran múltiples capas de abstracción para ayudar a programar tareas y compartir recursos entre múltiples procesos. La capa del controlador controla los recursos de hardware y el sistema operativo administra la memoria y el ancho de banda del procesador. Para cualquier núcleo de procesador dado, solo se puede ejecutar una instrucción a la vez, y los sistemas basados en procesadores corren el riesgo continuo de que las tareas de tiempo crítico se anticipen entre sí. Los FPGA, que no utilizan sistemas operativos, plantean preocupaciones mínimas de confiabilidad con su verdadera ejecución en paralelo y hardware determinista dedicado a cada tarea.
Capacidad de mantenimiento a largo plazo: los chips FPGA se pueden actualizar en el campo y no requieren el tiempo y el costo que implica el rediseño de ASIC. Los protocolos de comunicación digital, por ejemplo, tienen especificaciones que pueden cambiar con el tiempo, y las interfaces basadas en ASIC pueden causar problemas de mantenimiento y compatibilidad futura. Por el contrario, los chips FPGA reconfigurables pueden mantenerse al día con las modificaciones futuras potencialmente necesarias. A medida que los productos y sistemas maduran, nuestros clientes pueden realizar mejoras funcionales sin perder tiempo rediseñando el hardware y modificando los diseños de las placas.
Servicios de fundición de microelectrónica: Nuestros servicios de fundición de microelectrónica incluyen diseño, creación de prototipos y fabricación, servicios de terceros. Brindamos asistencia a nuestros clientes durante todo el ciclo de desarrollo del producto, desde el soporte de diseño hasta la creación de prototipos y el soporte de fabricación de chips semiconductores. Nuestro objetivo en los servicios de soporte de diseño es permitir un enfoque correcto desde la primera vez para diseños digitales, analógicos y de señal mixta de dispositivos semiconductores. Por ejemplo, están disponibles herramientas de simulación específicas de MEMS. Fabs que pueden manejar obleas de 6 y 8 pulgadas para CMOS y MEMS integrados están a su servicio. Ofrecemos a nuestros clientes soporte de diseño para todas las principales plataformas de automatización de diseño electrónico (EDA), proporcionando modelos correctos, kits de diseño de procesos (PDK), bibliotecas analógicas y digitales, y soporte de diseño para fabricación (DFM). Ofrecemos dos opciones de creación de prototipos para todas las tecnologías: el servicio Multi Product Wafer (MPW), donde varios dispositivos se procesan en paralelo en una oblea, y el servicio Multi Level Mask (MLM) con cuatro niveles de máscara dibujados en la misma retícula. Estos son más económicos que el conjunto completo de máscaras. El servicio MLM es muy flexible en comparación con las fechas fijas del servicio MPW. Las empresas pueden preferir subcontratar productos de semiconductores a una fundición de microelectrónica por una serie de razones, incluida la necesidad de una segunda fuente, el uso de recursos internos para otros productos y servicios, la voluntad de no tener fábrica y disminuir el riesgo y la carga de operar una fábrica de semiconductores, etc. AGS-TECH ofrece procesos de fabricación de microelectrónica de plataforma abierta que se pueden reducir para tiradas pequeñas de obleas, así como para la fabricación en masa. En determinadas circunstancias, sus herramientas de fabricación de microelectrónica o MEMS existentes o conjuntos completos de herramientas pueden transferirse como herramientas consignadas o herramientas vendidas desde su fábrica a nuestro sitio de fabricación, o sus productos de microelectrónica y MEMS existentes pueden rediseñarse utilizando tecnologías de proceso de plataforma abierta y trasladarse a un proceso disponible en nuestra fábrica. Esto es más rápido y económico que una transferencia de tecnología personalizada. Sin embargo, si se desea, se pueden transferir los procesos de fabricación de microelectrónica/MEMS existentes del cliente.
Preparación de obleas de semiconductores: Si lo desean los clientes después de microfabricar las obleas, llevamos a cabo operaciones de corte en cubitos, rectificado, adelgazamiento, colocación de retículas, clasificación de troqueles, selección y colocación e inspección en obleas de semiconductores. El procesamiento de obleas de semiconductores implica metrología entre los diversos pasos de procesamiento. Por ejemplo, los métodos de prueba de película delgada basados en elipsometría o reflectometría se utilizan para controlar estrictamente el espesor del óxido de la puerta, así como el espesor, el índice de refracción y el coeficiente de extinción de la fotorresistencia y otros recubrimientos. Utilizamos equipos de prueba de obleas de semiconductores para verificar que las obleas no hayan sido dañadas por pasos de procesamiento anteriores hasta la prueba. Una vez que se han completado los procesos iniciales, los dispositivos microelectrónicos semiconductores se someten a una variedad de pruebas eléctricas para determinar si funcionan correctamente. Nos referimos a la proporción de dispositivos microelectrónicos en la oblea que se encontró que funcionan correctamente como el "rendimiento". Las pruebas de chips microelectrónicos en la oblea se llevan a cabo con un probador electrónico que presiona pequeñas sondas contra el chip semiconductor. La máquina automatizada marca cada chip microelectrónico defectuoso con una gota de tinte. Los datos de prueba de obleas se registran en una base de datos de computadora central y los chips de semiconductores se clasifican en contenedores virtuales de acuerdo con límites de prueba predeterminados. Los datos de clasificación resultantes se pueden graficar o registrar en un mapa de obleas para rastrear defectos de fabricación y marcar chips defectuosos. Este mapa también se puede utilizar durante el montaje y el envasado de obleas. En la prueba final, los chips microelectrónicos se prueban nuevamente después del empaque, ya que es posible que falten cables de conexión o que el paquete altere el rendimiento analógico. Después de que se prueba una oblea de semiconductores, normalmente se reduce su espesor antes de que la oblea se marque y luego se rompa en troqueles individuales. Este proceso se denomina troceado de obleas de semiconductores. Utilizamos máquinas automáticas de recoger y colocar fabricadas especialmente para la industria de la microelectrónica para clasificar las matrices de semiconductores buenas y malas. Solo se empaquetan los chips semiconductores buenos y sin marcar. A continuación, en el proceso de empaquetado de microelectrónica de plástico o cerámica, montamos la matriz del semiconductor, conectamos las almohadillas de la matriz a las clavijas del paquete y sellamos la matriz. Se utilizan pequeños cables de oro para conectar las almohadillas a los pines mediante máquinas automáticas. El paquete a escala de chip (CSP) es otra tecnología de empaquetado de microelectrónica. Un paquete dual en línea (DIP) de plástico, como la mayoría de los paquetes, es varias veces más grande que el chip semiconductor real colocado en el interior, mientras que los chips CSP son casi del tamaño del chip microelectrónico; y se puede construir un CSP para cada troquel antes de cortar en dados la oblea de semiconductor. Los chips microelectrónicos empacados se vuelven a probar para asegurarse de que no se dañen durante el empaque y que el proceso de interconexión de matriz a clavija se haya completado correctamente. Usando láseres, grabamos los nombres y números de los chips en el paquete.
Diseño y fabricación de paquetes microelectrónicos: ofrecemos diseño y fabricación de paquetes microelectrónicos tanto listos para usar como personalizados. Como parte de este servicio también se realiza el modelado y simulación de paquetes microelectrónicos. El modelado y la simulación garantizan el diseño virtual de experimentos (DoE) para lograr la solución óptima, en lugar de probar paquetes en el campo. Esto reduce el costo y el tiempo de producción, especialmente para el desarrollo de nuevos productos en microelectrónica. Este trabajo también nos brinda la oportunidad de explicar a nuestros clientes cómo el ensamblaje, la confiabilidad y las pruebas afectarán sus productos microelectrónicos. El objetivo principal del empaque microelectrónico es diseñar un sistema electrónico que satisfaga los requisitos para una aplicación particular a un costo razonable. Debido a las muchas opciones disponibles para interconectar y albergar un sistema microelectrónico, la elección de una tecnología de empaquetado para una aplicación determinada requiere una evaluación experta. Los criterios de selección para paquetes de microelectrónica pueden incluir algunos de los siguientes impulsores tecnológicos:
-Cableabilidad
-Rendir
-Costo
-Propiedades de disipación de calor
-Rendimiento de blindaje electromagnético
-Resistencia mecánica
-Fiabilidad
Estas consideraciones de diseño para paquetes de microelectrónica afectan la velocidad, la funcionalidad, las temperaturas de unión, el volumen, el peso y más. El objetivo principal es seleccionar la tecnología de interconexión más rentable y confiable. Utilizamos software y métodos de análisis sofisticados para diseñar paquetes de microelectrónica. El empaquetado de microelectrónica se ocupa del diseño de métodos para la fabricación de sistemas electrónicos en miniatura interconectados y la confiabilidad de esos sistemas. Específicamente, el empaquetado de microelectrónica implica el enrutamiento de señales mientras se mantiene la integridad de la señal, la distribución de tierra y energía a los circuitos integrados de semiconductores, la dispersión del calor disipado mientras se mantiene la integridad estructural y del material, y la protección del circuito de los peligros ambientales. En general, los métodos para empaquetar circuitos integrados microelectrónicos implican el uso de un PWB con conectores que proporcionan las E/S del mundo real a un circuito electrónico. Los enfoques tradicionales de empaquetado de microelectrónica implican el uso de paquetes únicos. La principal ventaja de un paquete de un solo chip es la capacidad de probar completamente el IC microelectrónico antes de interconectarlo al sustrato subyacente. Dichos dispositivos semiconductores empaquetados se montan en un orificio pasante o se montan en la superficie del PWB. Los paquetes de microelectrónica montados en superficie no requieren orificios pasantes para atravesar toda la placa. En cambio, los componentes microelectrónicos montados en la superficie se pueden soldar a ambos lados del PWB, lo que permite una mayor densidad de circuitos. Este enfoque se denomina tecnología de montaje superficial (SMT). La adición de paquetes de estilo de matriz de área, como matrices de rejilla esférica (BGA) y paquetes de escala de chip (CSP), hace que SMT sea competitiva con las tecnologías de empaque de microelectrónica de semiconductores de mayor densidad. Una tecnología de empaque más nueva implica la conexión de más de un dispositivo semiconductor en un sustrato de interconexión de alta densidad, que luego se monta en un paquete grande, proporcionando pines de E/S y protección ambiental. Esta tecnología de módulo multichip (MCM) se caracteriza además por las tecnologías de sustrato utilizadas para interconectar los circuitos integrados adjuntos. MCM-D representa capas delgadas de metal y dieléctricas depositadas. Los sustratos MCM-D tienen las densidades de cableado más altas de todas las tecnologías MCM gracias a las sofisticadas tecnologías de procesamiento de semiconductores. MCM-C se refiere a sustratos “cerámicos” multicapa, cocidos a partir de capas alternas apiladas de tintas metálicas tamizadas y láminas cerámicas sin cocer. Usando MCM-C obtenemos una capacidad de cableado moderadamente densa. MCM-L se refiere a sustratos multicapa hechos de "laminados" de PWB metalizados apilados, que se modelan individualmente y luego se laminan. Solía ser una tecnología de interconexión de baja densidad, sin embargo, ahora MCM-L se está acercando rápidamente a la densidad de las tecnologías de empaquetado de microelectrónica MCM-C y MCM-D. La tecnología de empaquetado de microelectrónica de conexión directa de chip (DCA) o chip-on-board (COB) implica montar los circuitos integrados de microelectrónica directamente en el PWB. Un encapsulante de plástico, que se "aglomera" sobre el circuito integrado desnudo y luego se cura, brinda protección ambiental. Los circuitos integrados de microelectrónica se pueden interconectar al sustrato utilizando métodos de unión por cable o flip-chip. La tecnología DCA es particularmente económica para los sistemas que están limitados a 10 o menos circuitos integrados de semiconductores, ya que una mayor cantidad de chips puede afectar el rendimiento del sistema y los ensamblajes DCA pueden ser difíciles de volver a trabajar. Una ventaja común a las opciones de paquete DCA y MCM es la eliminación del nivel de interconexión del paquete IC de semiconductores, lo que permite una mayor proximidad (retardos de transmisión de señal más cortos) y una inductancia de cable reducida. La principal desventaja de ambos métodos es la dificultad de comprar circuitos integrados microelectrónicos completamente probados. Otras desventajas de las tecnologías DCA y MCM-L incluyen una gestión térmica deficiente gracias a la baja conductividad térmica de los laminados PWB y un coeficiente de expansión térmica deficiente entre la matriz del semiconductor y el sustrato. Resolver el problema del desajuste de la expansión térmica requiere un sustrato intercalador como el molibdeno para el troquel unido por alambre y un epoxi de relleno inferior para el troquel flip-chip. El módulo portador multichip (MCCM) combina todos los aspectos positivos de DCA con la tecnología MCM. El MCCM es simplemente un MCM pequeño en un soporte de metal delgado que se puede unir o unir mecánicamente a un PWB. El fondo de metal actúa como disipador de calor y como mediador de tensión para el sustrato de MCM. El MCCM tiene cables periféricos para unión de cables, soldadura o unión de lengüetas a un PWB. Los circuitos integrados de semiconductores desnudos están protegidos con un material glob-top. Cuando se comunique con nosotros, analizaremos su aplicación y los requisitos para elegir la mejor opción de empaque de microelectrónica para usted.
Ensamblaje, empaque y prueba de circuitos integrados de semiconductores: Como parte de nuestros servicios de fabricación de microelectrónica, ofrecemos unión de troqueles, cables y chips, encapsulación, ensamblaje, marcado y marcado, pruebas. Para que funcione un chip semiconductor o un circuito microelectrónico integrado, debe estar conectado al sistema que controlará o al que proporcionará instrucciones. El conjunto de circuitos integrados de microelectrónica proporciona las conexiones para la transferencia de energía e información entre el chip y el sistema. Esto se logra conectando el chip microelectrónico a un paquete o conectándolo directamente a la PCB para estas funciones. Las conexiones entre el chip y el paquete o la placa de circuito impreso (PCB) se realizan mediante unión de cables, orificio pasante o ensamblaje de chip invertido. Somos un líder de la industria en la búsqueda de soluciones de empaquetado de circuitos integrados de microelectrónica para cumplir con los complejos requisitos de los mercados inalámbricos y de Internet. Ofrecemos miles de formatos y tamaños de paquetes diferentes, que van desde paquetes de circuitos integrados de microelectrónica de estructura de plomo tradicionales para montaje en superficie y orificio pasante, hasta las últimas soluciones de escala de chip (CSP) y matriz de rejilla de bolas (BGA) requeridas en aplicaciones de alta densidad y gran cantidad de pines. . Una amplia variedad de paquetes están disponibles en stock, incluidos CABGA (Chip Array BGA), CQFP, CTBGA (Chip Array Thin Core BGA), CVBGA (Very Thin Chip Array BGA), Flip Chip, LCC, LGA, MQFP, PBGA, PDIP, PLCC, PoP - Paquete sobre paquete, PoP TMV - A través del molde, SOIC / SOJ, SSOP, TQFP, TSOP, WLP (Paquete de nivel de oblea)…..etc. La unión de cables con cobre, plata u oro se encuentran entre los populares en microelectrónica. El alambre de cobre (Cu) ha sido un método para conectar troqueles de semiconductores de silicio a los terminales del paquete de microelectrónica. Con el reciente aumento en el costo del cable de oro (Au), el cable de cobre (Cu) es una forma atractiva de administrar el costo total del paquete en microelectrónica. También se parece al alambre de oro (Au) debido a sus propiedades eléctricas similares. La autoinductancia y la autocapacitancia son casi las mismas para el alambre de oro (Au) y cobre (Cu), mientras que el alambre de cobre (Cu) tiene una resistividad más baja. En aplicaciones de microelectrónica donde la resistencia debida al cable de enlace puede afectar negativamente el rendimiento del circuito, el uso de cable de cobre (Cu) puede ofrecer una mejora. Los alambres de aleación de cobre, cobre revestido de paladio (PCC) y plata (Ag) han surgido como alternativas a los alambres con aglomerante de oro debido al costo. Los cables a base de cobre son económicos y tienen baja resistividad eléctrica. Sin embargo, la dureza del cobre dificulta su uso en muchas aplicaciones, como aquellas con estructuras de almohadillas de unión frágiles. Para estas aplicaciones, Ag-Alloy ofrece propiedades similares a las del oro, mientras que su costo es similar al de PCC. El alambre Ag-Alloy es más suave que el PCC, lo que da como resultado una menor salpicadura de Al y un menor riesgo de daños en la almohadilla de unión. El alambre Ag-Alloy es el mejor reemplazo de bajo costo para aplicaciones que necesitan unión de matriz a matriz, unión en cascada, paso de almohadilla de unión ultrafino y aberturas de almohadilla de unión pequeñas, altura de bucle ultra baja. Brindamos una gama completa de servicios de prueba de semiconductores que incluyen pruebas de obleas, varios tipos de pruebas finales, pruebas a nivel de sistema, pruebas de tiras y servicios completos de fin de línea. Probamos una variedad de tipos de dispositivos semiconductores en todas nuestras familias de paquetes, que incluyen radiofrecuencia, señal analógica y mixta, digital, administración de energía, memoria y varias combinaciones, como ASIC, módulos de múltiples chips, System-in-Package (SiP) y empaques 3D apilados, sensores y dispositivos MEMS como acelerómetros y sensores de presión. Nuestro hardware de prueba y equipo de contacto son adecuados para tamaño de paquete personalizado SiP, soluciones de contacto de dos lados para paquete sobre paquete (PoP), TMV PoP, enchufes FusionQuad, MicroLeadFrame de múltiples filas, pilar de cobre de paso fino. El equipo de prueba y los pisos de prueba están integrados con herramientas CIM / CAM, análisis de rendimiento y monitoreo de rendimiento para brindar un rendimiento de muy alta eficiencia la primera vez. Ofrecemos numerosos procesos de prueba de microelectrónica adaptativa para nuestros clientes y ofrecemos flujos de prueba distribuidos para SiP y otros flujos de ensamblaje complejos. AGS-TECH ofrece una gama completa de servicios de consultoría, desarrollo e ingeniería de pruebas en todo el ciclo de vida de sus productos de microelectrónica y semiconductores. Entendemos los mercados únicos y los requisitos de prueba para SiP, automotriz, redes, juegos, gráficos, computación, RF/inalámbrico. Los procesos de fabricación de semiconductores requieren soluciones de marcado rápidas y controladas con precisión. Las velocidades de marcado de más de 1000 caracteres/segundo y las profundidades de penetración de material de menos de 25 micrones son comunes en la industria de microelectrónica de semiconductores que utilizan láseres avanzados. Somos capaces de marcar compuestos de moldes, obleas, cerámicas y más con una entrada de calor mínima y una repetibilidad perfecta. Utilizamos láseres de alta precisión para marcar incluso las piezas más pequeñas sin dañarlas.
Marcos de plomo para dispositivos semiconductores: tanto el diseño y la fabricación estándar como personalizados son posibles. Los marcos de plomo se utilizan en los procesos de ensamblaje de dispositivos semiconductores y son esencialmente capas delgadas de metal que conectan el cableado desde los terminales eléctricos diminutos en la superficie microelectrónica del semiconductor hasta los circuitos a gran escala en los dispositivos eléctricos y PCB. Los marcos de plomo se utilizan en casi todos los paquetes de microelectrónica de semiconductores. La mayoría de los paquetes de circuitos integrados de microelectrónica se fabrican colocando el chip de silicio semiconductor en un marco de plomo, luego conectando el chip a los cables metálicos de ese marco de plomo y, posteriormente, cubriendo el chip de microelectrónica con una cubierta de plástico. Este empaque microelectrónico simple y de costo relativamente bajo sigue siendo la mejor solución para muchas aplicaciones. Los marcos de plomo se producen en tiras largas, lo que permite que se procesen rápidamente en máquinas de ensamblaje automatizadas y, por lo general, se utilizan dos procesos de fabricación: algún tipo de fotograbado y estampado. En microelectrónica, el diseño de marcos de conductores a menudo demanda especificaciones y características personalizadas, diseños que mejoran las propiedades eléctricas y térmicas y requisitos de tiempo de ciclo específicos. Tenemos una amplia experiencia en la fabricación de marcos de plomo microelectrónicos para una variedad de diferentes clientes que utilizan grabado y estampado fotográfico asistidos por láser.
Diseño y fabricación de disipadores de calor para microelectrónica: diseño y fabricación estándar y personalizados. Con el aumento de la disipación de calor de los dispositivos microelectrónicos y la reducción de los factores de forma generales, la gestión térmica se convierte en un elemento más importante del diseño de productos electrónicos. La consistencia en el rendimiento y la esperanza de vida de los equipos electrónicos están inversamente relacionados con la temperatura de los componentes del equipo. La relación entre la fiabilidad y la temperatura de funcionamiento de un dispositivo semiconductor de silicio típico muestra que una reducción de la temperatura corresponde a un aumento exponencial de la fiabilidad y la esperanza de vida del dispositivo. Por lo tanto, se puede lograr una vida útil prolongada y un rendimiento confiable de un componente microelectrónico semiconductor controlando efectivamente la temperatura de funcionamiento del dispositivo dentro de los límites establecidos por los diseñadores. Los disipadores de calor son dispositivos que mejoran la disipación de calor de una superficie caliente, generalmente la carcasa exterior de un componente generador de calor, a un ambiente más frío, como el aire. Para las siguientes discusiones, se supone que el aire es el fluido refrigerante. En la mayoría de las situaciones, la transferencia de calor a través de la interfaz entre la superficie sólida y el aire refrigerante es la menos eficiente dentro del sistema, y la interfaz sólido-aire representa la mayor barrera para la disipación de calor. Un disipador de calor reduce esta barrera principalmente al aumentar el área de superficie que está en contacto directo con el refrigerante. Esto permite disipar más calor y/o reduce la temperatura de funcionamiento del dispositivo semiconductor. El objetivo principal de un disipador de calor es mantener la temperatura del dispositivo microelectrónico por debajo de la temperatura máxima permitida especificada por el fabricante del dispositivo semiconductor.
Podemos clasificar los disipadores de calor en términos de métodos de fabricación y sus formas. Los tipos más comunes de disipadores de calor enfriados por aire incluyen:
- Estampados: las láminas de cobre o aluminio se estampan en las formas deseadas. se utilizan en la refrigeración por aire tradicional de componentes electrónicos y ofrecen una solución económica a los problemas térmicos de baja densidad. Son adecuados para la producción de alto volumen.
- Extrusión: Estos disipadores de calor permiten la formación de elaboradas formas bidimensionales capaces de disipar grandes cargas de calor. Se pueden cortar, maquinar y agregar opciones. Un corte transversal producirá disipadores de calor omnidireccionales con aletas rectangulares, y la incorporación de aletas dentadas mejora el rendimiento aproximadamente entre un 10 y un 20 %, pero con una tasa de extrusión más lenta. Los límites de extrusión, como la altura de la aleta y el grosor de la aleta, generalmente dictan la flexibilidad en las opciones de diseño. La típica relación de aspecto entre la altura de la aleta y la separación de hasta 6 y un grosor mínimo de la aleta de 1,3 mm se pueden lograr con técnicas de extrusión estándar. Se puede obtener una relación de aspecto de 10 a 1 y un grosor de aleta de 0,8″ con características especiales de diseño de matriz. Sin embargo, a medida que aumenta la relación de aspecto, se compromete la tolerancia de extrusión.
- Aletas unidas/fabricadas: la mayoría de los disipadores de calor enfriados por aire tienen convección limitada, y el rendimiento térmico general de un disipador de calor enfriado por aire a menudo se puede mejorar significativamente si se puede exponer más área de superficie a la corriente de aire. Estos disipadores de calor de alto rendimiento utilizan epoxi relleno de aluminio termoconductor para unir aletas planas en una placa base de extrusión ranurada. Este proceso permite una relación de aspecto de altura de aleta a espacio mucho mayor de 20 a 40, lo que aumenta significativamente la capacidad de enfriamiento sin aumentar la necesidad de volumen.
- Fundición: Los procesos de fundición en arena, a la cera perdida y en matriz para aluminio o cobre/bronce están disponibles con o sin asistencia de vacío. Usamos esta tecnología para la fabricación de disipadores de calor de aletas de pin de alta densidad que brindan el máximo rendimiento cuando se usa enfriamiento por impacto.
- Aletas plegadas: La chapa ondulada de aluminio o cobre aumenta la superficie y el rendimiento volumétrico. Luego, el disipador de calor se une a una placa base o directamente a la superficie de calentamiento mediante epoxi o soldadura fuerte. No es adecuado para disipadores de calor de alto perfil debido a la disponibilidad y la eficiencia de las aletas. Por lo tanto, permite fabricar disipadores de calor de alto rendimiento.
Al seleccionar un disipador de calor apropiado que cumpla con los criterios térmicos requeridos para sus aplicaciones de microelectrónica, debemos examinar varios parámetros que afectan no solo el rendimiento del disipador de calor en sí, sino también el rendimiento general del sistema. La elección de un tipo particular de disipador de calor en microelectrónica depende en gran medida del presupuesto térmico permitido para el disipador de calor y las condiciones externas que lo rodean. Nunca hay un valor único de resistencia térmica asignado a un disipador de calor dado, ya que la resistencia térmica varía con las condiciones de enfriamiento externas.
Diseño y fabricación de sensores y actuadores: Están disponibles tanto el diseño y la fabricación estándar como personalizados. Ofrecemos soluciones con procesos listos para usar para sensores inerciales, sensores de presión y presión relativa y dispositivos sensores de temperatura IR. Al usar nuestros bloques de IP para acelerómetros, IR y sensores de presión o al aplicar su diseño de acuerdo con las especificaciones disponibles y las reglas de diseño, podemos entregarle dispositivos de sensores basados en MEMS en cuestión de semanas. Además de MEMS, se pueden fabricar otros tipos de estructuras de sensores y actuadores.
Diseño y fabricación de circuitos optoelectrónicos y fotónicos: Un circuito integrado fotónico u óptico (PIC) es un dispositivo que integra múltiples funciones fotónicas. Puede parecerse a los circuitos integrados electrónicos en microelectrónica. La principal diferencia entre los dos es que un circuito integrado fotónico proporciona funcionalidad para señales de información impuestas en longitudes de onda ópticas en el espectro visible o infrarrojo cercano de 850 nm a 1650 nm. Las técnicas de fabricación son similares a las que se utilizan en los circuitos integrados de microelectrónica en los que se utiliza la fotolitografía para modelar las obleas para el grabado y la deposición de material. A diferencia de la microelectrónica de semiconductores, donde el dispositivo principal es el transistor, no existe un único dispositivo dominante en la optoelectrónica. Los chips fotónicos incluyen guías de ondas de interconexión de baja pérdida, divisores de potencia, amplificadores ópticos, moduladores ópticos, filtros, láseres y detectores. Estos dispositivos requieren una variedad de diferentes materiales y técnicas de fabricación y, por lo tanto, es difícil realizarlos todos en un solo chip. Nuestras aplicaciones de circuitos integrados fotónicos se encuentran principalmente en las áreas de comunicación por fibra óptica, computación biomédica y fotónica. Algunos ejemplos de productos optoelectrónicos que podemos diseñar y fabricar para usted son LED (diodos emisores de luz), láseres de diodo, receptores optoelectrónicos, fotodiodos, módulos de distancia láser, módulos láser personalizados y más.