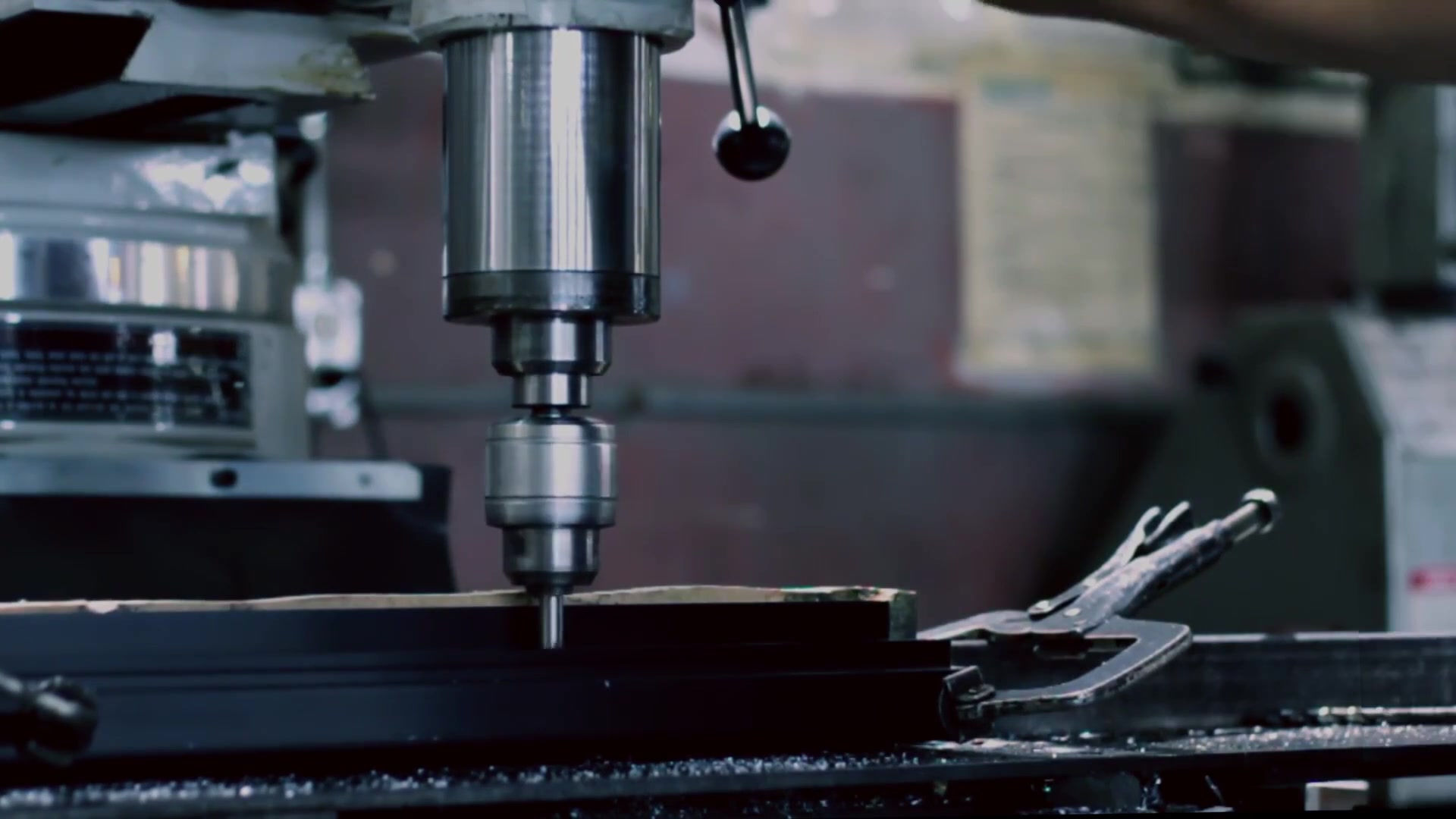
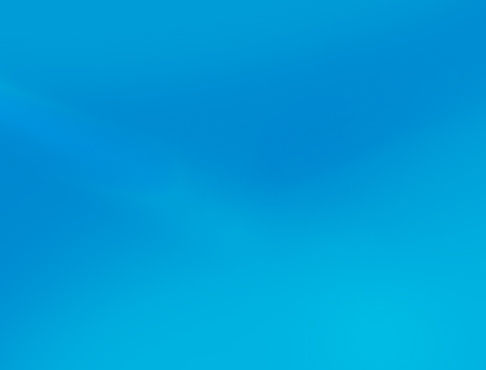
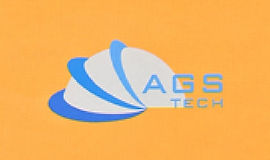
さまざまな製品とサービスのグローバル カスタム メーカー、インテグレーター、コンソリデーター、アウトソーシング パートナー。
私たちは、製造、製造、エンジニアリング、統合、統合、カスタム製造および既製の製品とサービスのアウトソーシングのワンストップ ソースです。
Choose your Language
-
カスタム製造
-
国内およびグローバルな受託製造
-
製造アウトソーシング
-
国内およびグローバル調達
-
連結
-
エンジニアリング統合
-
エンジニアリングサービス
当社が提供するガラス製造の種類は、コンテナ ガラス、ガラス吹き、ガラス繊維 & チューブ & ロッド、家庭用および工業用ガラス製品、ランプおよび電球、精密ガラス成形、光学部品およびアセンブリ、フラット & シート & フロート ガラスです。手成形と機械成形の両方を行います.
当社の一般的なテクニカル セラミック製造プロセスは、ダイ プレス、静水圧プレス、熱間静水圧プレス、ホット プレス、スリップ キャスティング、テープ キャスティング、押出成形、射出成形、グリーン加工、焼結または焼成、ダイヤモンド研削、気密アセンブリです。
ここをクリックすることをお勧めします
AGS-TECH Inc. によるガラス成形および成形プロセスの概略図をダウンロードしてください。
AGS-TECH Inc. による技術的なセラミック製造プロセスの概略図をダウンロードしてください。
写真とスケッチを含むこれらのダウンロード可能なファイルは、以下で提供する情報をよりよく理解するのに役立ちます.
• コンテナ ガラスの製造: プレス アンド ブローおよび製造用のブロー アンド ブロー ラインを自動化しています。ブローアンドブロー工程では、ゴブをブランクモールドに落とし、上から圧縮空気を吹き付けてネックを形成します。この直後に、圧縮空気が容器の首を通して反対方向から 2 回吹き込まれ、ボトルのプリフォームが形成されます。次に、このプリフォームを実際の金型に移し、再加熱して柔らかくし、圧縮空気を加えてプリフォームに最終的な容器の形状を与えます。より明確に言えば、それは加圧され、ブロー金型キャビティの壁に押し付けられて、望ましい形状になります。最後に、製造されたガラス容器は、その後の再加熱および成形中に発生した応力の除去のためにアニーリングオーブンに移され、制御された方法で冷却されます。プレスアンドブロー法では、溶融ゴブをパリソン型(ブランクモールド)に入れ、パリソン形状(ブランク形状)にプレスします。次に、ブランクをブロー金型に移し、「ブロー アンド ブロー プロセス」で説明したプロセスと同様にブローします。アニーリングや応力緩和などの後続の手順は、類似または同じです。
• GLASS BLOWING : 従来の手吹きと自動設備による圧縮空気を使用してガラス製品を製造してきました。一部の注文では、ガラス アート作品を含むプロジェクト、公差の緩い少数の部品を必要とするプロジェクト、プロトタイピング / デモ プロジェクトなど、従来の吹き込みが必要です。従来の吹きガラスでは、中空の金属パイプを溶融ガラスのポットに浸し、パイプを回転させてガラス材料をある程度集めます。パイプの先端に溜まったガラスを平らな鉄の上で転がし、好きな形に伸ばし、再加熱し、空気を吹き込みます。出来上がったら型に入れて空気を吹き込みます。金型キャビティは、ガラスと金属の接触を避けるために湿っています。水膜はそれらの間のクッションのように機能します。手作業による吹き込みは、労働集約的で時間のかかるプロセスであり、プロトタイピングや高価なアイテムにのみ適しており、安価な大量注文には適していません。
• 家庭用および工業用ガラス製品の製造 : さまざまなタイプのガラス材料を使用して、多種多様なガラス製品が製造されています。ガラスの中には、耐熱性があり実験用ガラス器具に適しているものもあれば、食器洗い機に何度も耐えられ、家庭用製品の製造に適しているものもあります。 Westlake の機械を使用して、1 日あたり何万個ものグラスが生産されています。簡単にするために、溶融ガラスを真空で集め、金型に挿入してプリフォームを作ります。その後、型に空気を吹き込み、別の型に移し、再び空気を吹き込み、ガラスが最終的な形になります。手吹きのように、これらの型は水で湿らせたままにします。さらに伸ばすことは、ネックが形成される仕上げ作業の一部です。余分なガラスは焼き払います。その後、上述の制御された再加熱および冷却プロセスが続く。
• GLASS TUBE & ROD FORMING : ガラス管の製造に使用する主なプロセスは、DANNER プロセスと VELLO プロセスです。ダナー プロセスでは、炉からのガラスが流れ、耐火材料で作られた傾斜したスリーブに落下します。スリーブは、回転する中空シャフトまたはブローパイプに取り付けられています。次に、ガラスがスリーブの周りに巻き付けられ、スリーブを流れてシャフトの先端を覆う滑らかな層を形成します。チューブ成形の場合は先端が中空のブローパイプに空気を吹き込み、ロッド成形の場合はシャフトに中実の先端を使用します。次に、チューブまたはロッドはキャリングローラー上に引き出されます。ガラス管の肉厚や直径などの寸法は、スリーブの直径とブローエアの圧力を所望の値に設定し、温度、ガラスの流速、延伸速度を調整することによって、所望の値に調整されます。一方、Vello ガラス管の製造プロセスでは、ガラスが炉から出て、中空のマンドレルまたはベルを備えたボウルに移動します。ガラスはマンドレルとボウルの間の空間を通過し、チューブの形をとります。その後、ローラーを介して延伸機に移動し、冷却されます。冷却ラインの最後に切断と最終加工が行われます。チューブの寸法は、ダナー プロセスと同じように調整できます。 Danner と Vello プロセスを比較すると、Vello プロセスは大量生産に適しているのに対し、Danner プロセスは正確な少量のチューブ注文に適していると言えます.
• 板ガラス、フラットガラス、フロートガラスの処理 : サブミリ厚から数センチメートルまでの厚さの板ガラスを大量に取り扱っています。当社のフラット グラスは、光学的にほぼ完璧です。化学蒸着技術を用いて反射防止やミラーコーティングなどのコーティングを施す光学コーティングなどの特殊コーティングを施したガラスを提供しています。また、透明な導電性コーティングも一般的です。ガラスの疎水性または親水性コーティング、およびガラスのセルフクリーニングを行うコーティングも利用できます。強化ガラス、防弾ガラス、合わせガラスも人気商品です。ガラスをご希望の形状、ご希望の公差でカットいたします。板ガラスの湾曲や曲げ加工などの二次加工も可能です。
• 精密ガラス成形 : この技術は主に精密光学部品の製造に使用され、研削、ラッピング、研磨などのより高価で時間のかかる技術は必要ありません。この技術は、最高の光学部品を最大限に活用するには必ずしも十分ではありませんが、消費者向け製品、デジタル カメラ、医療用光学部品などの場合には、大量生産のための安価で優れた選択肢となる可能性があります。 また、非球面の場合など、複雑な形状が必要な他のガラス成形技術よりも優れています。基本的なプロセスには、金型の下側にガラス ブランクを装填し、酸素を除去するためにプロセス チャンバーを排気し、金型をほぼ閉じ、金型とガラスを赤外光で高速かつ等温加熱し、金型の半分をさらに閉じることが含まれます。軟化したガラスを制御された方法でゆっくりと所望の厚さにプレスし、最後にガラスを冷却し、チャンバーを窒素で満たし、製品を取り出します。このプロセスでは、正確な温度制御、金型閉鎖距離、金型閉鎖力、金型とガラス材料の膨張係数の一致が重要です。
• ガラス光学部品およびアセンブリの製造 : 精密なガラス成形に加えて、要求の厳しい用途向けの高品質の光学部品およびアセンブリを製造するために使用する貴重なプロセスが数多くあります。細かい特殊な研磨剤スラリーで光学グレードのガラスを研削、ラッピング、研磨することは、光学レンズ、プリズム、フラットなどを製造するための技術と科学です。表面の平坦さ、うねり、滑らかさ、および欠陥のない光学表面には、このようなプロセスに関する多くの経験が必要です。環境のわずかな変化が規格外の製品を生み出し、製造ラインを停止させる可能性があります。きれいな布で光学面を 1 回拭くだけで、製品が仕様を満たしているか、テストに不合格になる場合があります。使用される一般的なガラス材料には、石英ガラス、石英、BK7 などがあります。また、そのようなコンポーネントの組み立てには、専門的なニッチな経験が必要です。特殊な接着剤を使用する場合もあります。ただし、オプティカルコンタクトと呼ばれる技術が最良の選択である場合があり、取り付けられた光学ガラスの間に材料を使用しません。物理的に接触する平らな表面で構成され、接着剤なしで互いに取り付けられます。場合によっては、機械的スペーサー、精密なガラス棒またはボール、クランプ、または機械加工された金属部品を使用して、光学部品を特定の距離で相互に特定の幾何学的方向に組み立てます。ハイエンド光学部品を製造するための当社の一般的な技術のいくつかを調べてみましょう。
GRINDING & LAPPING & POLISHING : 光学部品の大まかな形状は、ガラス ブランクを研磨して得られます。その後、光学部品の粗い表面を所望の表面形状を有する工具に回転させてこすることにより、ラッピングおよび研磨が行われる。小さな研磨粒子と流体を含むスラリーが、光学部品と成形ツールの間に注がれています。そのようなスラリー中の砥粒サイズは、所望の平坦度に従って選択することができる。必要な形状からの重要な光学面の偏差は、使用されている光の波長で表されます。当社の高精度光学部品は、波長の 10 分の 1 (波長/10) の公差を持っています。表面プロファイルに加えて、重要な表面がスキャンされ、寸法、傷、欠け、穴、斑点などの他の表面特徴や欠陥について評価されます。光学製造フロアの環境条件の厳密な管理と、最先端の機器を使用した広範な計測およびテスト要件により、これは業界の挑戦的な分野になっています.
• ガラス製造の二次工程: 繰り返しになりますが、ガラスの二次工程および仕上げ工程に関しては、お客様の想像力に制限されます。ここにそれらのいくつかをリストします:
-ガラスのコーティング (光学、電気、トライボロジー、熱、機能、機械など)。一例として、ガラスの表面特性を変更して、例えば熱を反射させて建物の内部を涼しく保つようにしたり、ナノテクノロジーを使用して片面に赤外線を吸収させたりすることができます。これは、ガラスの最外層が建物内部の赤外線放射を吸収し、内部に放射するため、建物の内部を暖かく保つのに役立ちます.
-エッチング on ガラス
-応用セラミックラベリング (ACL)
-彫刻
・火炎研磨
-化学研磨
-染色
テクニカルセラミックスの製造
• DIE PRESSING : ダイに閉じ込められた粒状粉末の一軸圧縮で構成されます。
• HOT PRESSING : ダイ プレスに似ていますが、密度を高めるために温度を加えます。粉末または圧縮プリフォームをグラファイト ダイに入れ、ダイを 2000 ℃ などの高温に保ちながら一軸圧力をかけます。温度は、処理するセラミック粉末の種類によって異なります。複雑な形状や形状の場合、ダイヤモンド研削などの他の後続処理が必要になる場合があります。
• 静水圧プレス : 粒状粉末またはダイ プレス成形体を気密容器に入れ、液体が入った密閉圧力容器に入れます。その後、圧力容器の圧力を上げて圧縮します。容器内の液体は、気密容器の表面積全体に均一に圧力を伝達します。このように、材料は均一に圧縮され、フレキシブル コンテナの形状と内部プロファイルおよび機能を備えています。
• 熱間静水圧プレス : 静水圧プレスに似ていますが、加圧ガス雰囲気に加えて、成形体を高温で焼結します。熱間静水圧プレスにより、高密度化が進み、強度が向上します。
• スリップキャスティング / ドレンキャスティング : マイクロメートルサイズのセラミック粒子とキャリア液の懸濁液を金型に充填します。この混合物は「スリップ」と呼ばれます。型には細孔があるため、混合物中の液体が型にろ過されます。その結果、金型の内面に鋳物が形成されます。焼結後、部品を金型から取り出すことができます。
• テープキャスティング : セラミックスラリーを平らな可動キャリア表面にキャスティングすることにより、セラミックテープを製造しています。スラリーには、結合および運搬の目的で他の化学物質と混合されたセラミック粉末が含まれています。溶媒が蒸発すると、セラミックの緻密で柔軟なシートが残り、必要に応じてカットまたはロールすることができます。
• 押出成形 : 他の押出プロセスと同様に、セラミック粉末と結合剤およびその他の化学物質の柔らかい混合物を金型に通して断面形状を取得し、その後、必要な長さに切断します。このプロセスは、低温または加熱されたセラミック混合物を使用して実行されます.
• 低圧射出成形 : セラミック粉末と結合剤および溶剤の混合物を準備し、容易にプレスして金型キャビティに押し込める温度まで加熱します。成形サイクルが完了すると、部品が取り出され、結合剤が燃焼されます。射出成形を使用すると、複雑な部品を大量に経済的に入手できます。厚さ 10 mm の壁に 1 ミリのごくわずかな穴 が可能であり、追加の機械加工なしでねじ山が可能であり、+/- 0.5% の厳しい公差が可能であり、部品が機械加工される場合はさらに低くなります。 0.5mm から長さ 12.5mm のオーダーの壁厚、および 6.5mm から長さ 150mm の壁厚が可能です。
• GREEN MACHINING : 同じ金属加工ツールを使用して、プレスされたセラミック材料をチョークのように柔らかいうちに機械加工できます。 +/- 1% の公差が可能です。公差を改善するために、ダイヤモンド研削を使用しています。
• SINTERING または FIRING : 焼結により、完全な高密度化が可能になります。グリーン コンパクト パーツには大きな収縮が発生しますが、パーツとツールを設計する際にこれらの寸法変化を考慮しているため、これは大きな問題ではありません。粉末粒子は互いに結合され、圧縮プロセスによって引き起こされる気孔が大幅に除去されます。
• DIAMOND GRINDING : 世界で最も硬い材料「ダイヤモンド」を使用して、セラミックスなどの硬い材料を研削し、精密部品を得ています。マイクロメートル範囲の公差と非常に滑らかな表面が達成されています。費用がかかるため、この手法は本当に必要な場合にのみ検討します。
• HERMETIC ASSEMBLIES とは、実質的に言えば、界面間で物質、固体、液体、または気体の交換を許可しないものです。気密シールは気密です。例えば、ハーメチック電子筐体は、パッケージ化されたデバイスの機密性の高い内部内容物を、湿気、汚染物質、またはガスによって損なわれないように保つものです。 100% の気密性はありませんが、気密性について話すときは、実際には、漏れ率が非常に低く、デバイスが通常の環境条件下で非常に長期間安全であるという程度の気密性があることを意味します。当社のハーメチック アセンブリは、金属、ガラス、セラミック コンポーネント、金属 - セラミック、セラミック - 金属 - セラミック、金属 - セラミック - 金属、金属 - 金属、金属 - ガラス、金属 - ガラス - 金属、ガラス - 金属 - ガラス、ガラス - で構成されています。金属とガラスとガラス、および金属 - ガラス - セラミック結合の他のすべての組み合わせ。たとえば、セラミック部品を金属コーティングして、アセンブリ内の他の部品と強力に結合し、優れたシーリング機能を持たせることができます。光ファイバーやフィードスルーを金属でコーティングし、エンクロージャーにはんだ付けまたはろう付けするノウハウがあるため、エンクロージャー内にガスが通過したり漏れたりすることはありません。したがって、これらは、敏感なデバイスをカプセル化し、外気から保護する電子エンクロージャの製造に使用されます。優れたシール特性に加えて、熱膨張係数、変形抵抗、非ガス放出性、非常に長い寿命、非導電性、断熱性、帯電防止性などの特性があります。ガラスとセラミック材料を特定の用途に選択できるようにします。セラミックと金属の継手、ハーメチック シーリング、真空フィードスルー、高真空と超高真空、および流体制御コンポーネントを製造する当社の施設に関する情報 は、次の場所にあります。気密部品工場のパンフレット