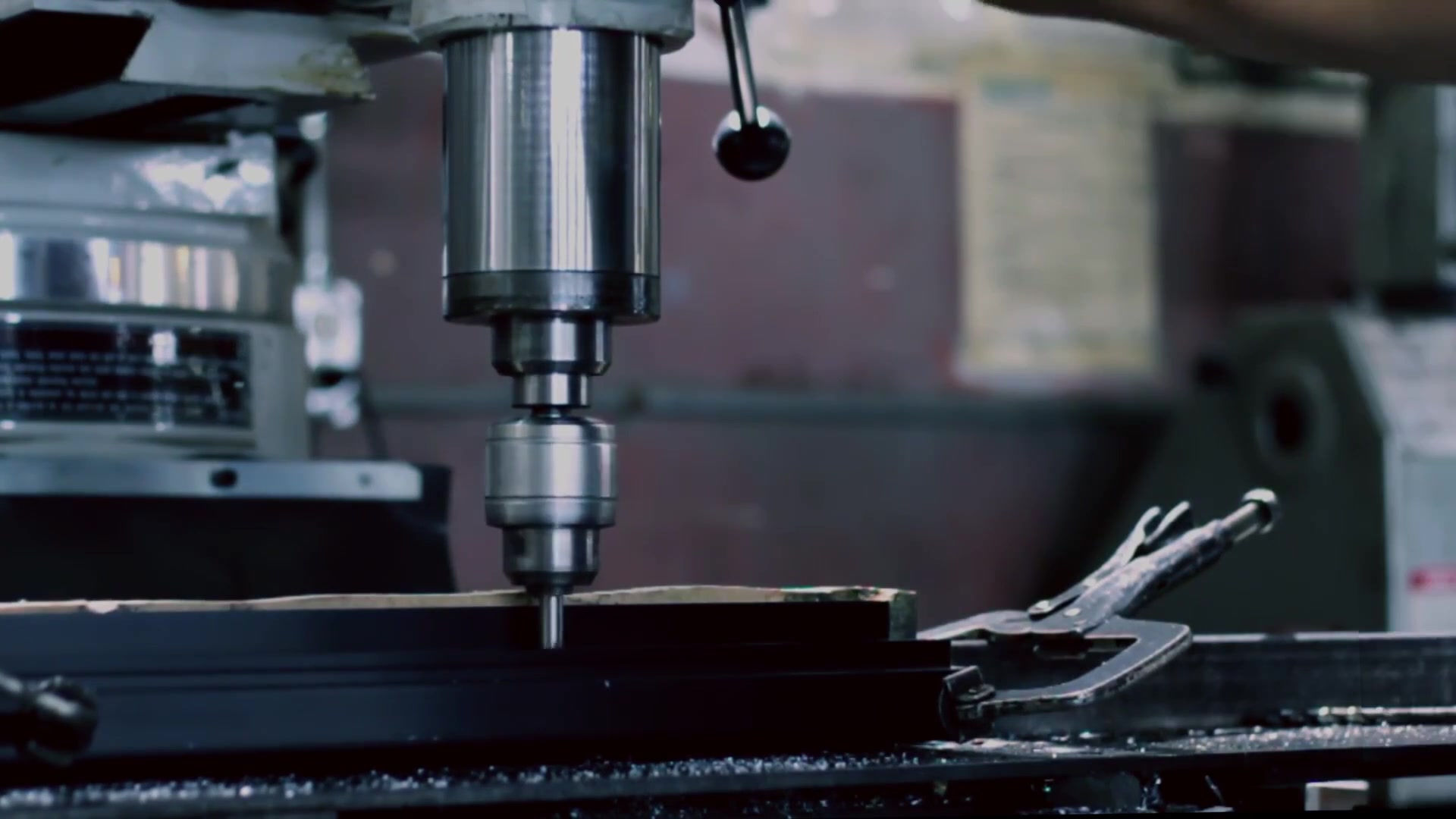
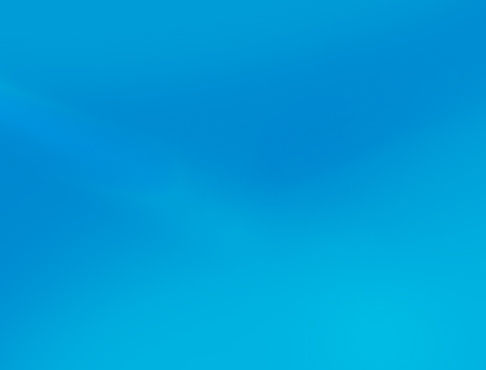
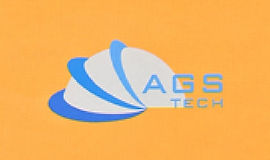
さまざまな製品とサービスのグローバル カスタム メーカー、インテグレーター、コンソリデーター、アウトソーシング パートナー。
私たちは、製造、製造、エンジニアリング、統合、統合、カスタム製造および既製の製品とサービスのアウトソーシングのワンストップ ソースです。
Choose your Language
-
カスタム製造
-
国内およびグローバルな受託製造
-
製造アウトソーシング
-
国内およびグローバル調達
-
連結
-
エンジニアリング統合
-
エンジニアリングサービス
製造された部品を結合、組み立て、固定し、溶接、ろう付け、はんだ付け、焼結、接着剤結合、固定、圧入を使用して完成品または半完成品に変えます。最も一般的な溶接プロセスには、アーク、酸素燃焼ガス、抵抗、プロジェクション、シーム、アプセット、パーカッション、ソリッド ステート、電子ビーム、レーザー、サーミット、誘導溶接などがあります。当社の一般的なろう付けプロセスは、トーチ、誘導、炉、浸漬ろう付けです。当社のはんだ付け方法は、アイロン、ホット プレート、オーブン、IH、ディップ、ウェーブ、リフロー、超音波はんだ付けです。接着には、熱可塑性樹脂、熱硬化性樹脂、エポキシ樹脂、フェノール樹脂、ポリウレタン、接着合金、その他の化学薬品やテープを頻繁に使用します。最後に、当社の締結プロセスは、釘付け、ねじ込み、ナットとボルト、リベット留め、クリンチング、ピン留め、ステッチとステープル留め、圧入で構成されています。
• 溶接 : 溶接には、ワークピースを溶融し、溶加材を導入することによる材料の接合が含まれます。これは、溶融溶融プールにも接合します。その部分が冷えると、強い接合部が得られます。場合によっては圧力をかけます。ロウ付けやハンダ付けは、溶接とは異なり、ワーク同士で融点の低い材料を溶かすだけで、ワーク同士は溶けません。ここをクリックすることをお勧めしますAGS-TECH Inc.による溶接プロセスの概略図をダウンロードしてください。
これは、以下で提供する情報をよりよく理解するのに役立ちます.
アーク溶接では、電源と電極を使用して、金属を溶かす電気アークを作成します。溶接点は、シールドガスまたは蒸気またはその他の物質によって保護されています。このプロセスは、自動車部品や鉄骨構造の溶接に人気があります。シェルデッド メタル アーク溶接 (SMAW) または棒溶接としても知られる方法では、電極棒を母材に近づけ、それらの間に電気アークを発生させます。電極棒が溶けて、フィラー材として機能します。電極には、スラグの層として機能し、シールドガスとして機能する蒸気を放出するフラックスも含まれています。これらは環境汚染から溶接領域を保護します。他のフィラーは使用されていません。このプロセスの欠点は、時間がかかること、電極を頻繁に交換する必要があること、フラックスに由来する残留スラグを削り取る必要があることです。鉄、鋼、ニッケル、アルミニウム、銅などの多くの金属。溶接可能。その利点は、安価なツールと使いやすさです。金属不活性ガス (MIG) としても知られるガス メタル アーク溶接 (GMAW) では、消耗する電極ワイヤー フィラーと、溶接領域の環境汚染に対してワイヤーの周りを流れる不活性ガスまたは部分的に不活性なガスを連続的に供給しています。鋼、アルミニウム、その他の非鉄金属の溶接が可能です。 MIG の利点は、高い溶接速度と優れた品質です。不利な点は、装置が複雑であることと、溶接エリアの周囲のシールド ガスを安定に維持する必要があるため、風の強い屋外環境で直面する課題です。 GMAW のバリエーションはフラックス入りアーク溶接 (FCAW) で、フラックス材料で満たされた細い金属管で構成されています。場合によっては、チューブ内のフラックスが環境汚染から保護するのに十分な場合があります。サブマージ アーク溶接 (SAW) は広く自動化されたプロセスであり、連続的なワイヤ供給と、フラックス カバーの層の下で発生するアークが含まれます。生産率と品質が高く、溶接スラグが落ちやすく、煙の出ない作業環境です。欠点は、特定の位置で parts を溶接するためにしか使用できないことです。ガス タングステン アーク溶接 (GTAW) またはタングステン - 不活性ガス溶接 (TIG) では、別のフィラーおよび不活性ガスまたは不活性ガスに近いガスと共にタングステン電極を使用します。私たちが知っているように、タングステンは融点が高く、非常に高温に適した金属です。上記で説明した他の方法とは異なり、TIG のタングステンは消費されません。薄い材料の溶接において、他の技術よりも有利な低速ですが高品質の溶接技術。多くの金属に適しています。プラズマ アーク溶接は似ていますが、プラズマ ガスを使用してアークを生成します。プラズマ アーク溶接のアークは、GTAW に比べて比較的集中しており、はるかに高速で幅広い範囲の金属厚に使用できます。 GTAW とプラズマ アーク溶接は、ほぼ同じ材料に適用できます。
OXY-FUEL / OXYFUEL WELDING オキシアセチレン溶接、オキシ溶接、ガス溶接とも呼ばれ、ガス燃料と酸素を使用して溶接を行います。電源を使用しないので持ち運びが可能で、電源のない場所でも使用できます。溶接トーチを使用して、ピースとフィラー材料を加熱し、共有の溶融金属プールを生成します。アセチレン、ガソリン、水素、プロパン、ブタンなど、さまざまな燃料を使用できます。酸素燃料溶接では、燃料用と酸素用の 2 つの容器を使用します。酸素は燃料を酸化(燃焼)させます。
抵抗溶接:ジュール熱を利用した溶接で、一定時間電流を流した箇所に熱が発生します。金属には大電流が流れます。この場所に溶融金属のプールが形成されます。抵抗溶接法は、効率が良く、汚染の可能性が少ないため、人気があります。しかし、不利な点は、機器のコストが比較的高いことと、比較的薄いワークピースに固有の制限があることです。スポット溶接は、抵抗溶接の主要なタイプの 1 つです。ここでは、2 つの銅電極を使用してシートを一緒にクランプし、それらに高電流を通すことによって、2 つ以上の重なり合うシートまたはワークピースを接合します。銅電極間の材料が加熱され、その場所に溶融プールが生成されます。その後、電流が停止し、電極が水冷されるため、銅電極の先端が溶接位置を冷却します。適切な材料と厚さに適切な量の熱を加えることがこの技術の鍵となります。誤って適用すると接合部が弱くなるためです。スポット溶接には、ワークピースに大きな変形を引き起こさない、エネルギー効率が高い、自動化が容易で生産速度が優れている、フィラーを必要としないなどの利点があります。欠点は、連続した継ぎ目を形成するのではなく、スポットで溶接が行われるため、全体的な強度が他の溶接方法と比較して相対的に低くなる可能性があることです。一方、SEAM WELDING は、類似材料の接合面で溶接を行います。継ぎ目は、突合せまたはオーバーラップ ジョイントにすることができます。シーム溶接は一方の端から始まり、徐々に他方の端に移動します。この方法では、銅製の 2 つの電極を使用して、溶接領域に圧力と電流を加えます。円盤状の電極がシーム ラインに沿って常に接触しながら回転し、連続的な溶接を行います。ここでも、電極は水で冷却されます。溶接は非常に強く、信頼性があります。他の方法は、プロジェクション、フラッシュ、アプセット溶接技術です。
SOLID-STATE WELDING は、上記で説明した以前の方法とは少し異なります。合体は、金属フィラーを使用せずに、接合された金属の溶融温度より低い温度で行われます。一部のプロセスでは圧力が使用される場合があります。さまざまな方法には、異種金属が同じ金型から押し出される共押出溶接、軟質合金を融点未満で接合する冷間圧接、溶接線が見えない技術の拡散溶接、異種材料を接合する爆発溶接などがあります。電磁力でチューブやシートを加速する電磁パルス溶接、金属を高温に加熱して叩き合わせる鍛造溶接、十分な摩擦圧接を行う摩擦溶接、非回転式の摩擦攪拌溶接などがあります。接合線を横切る消耗工具、真空または不活性ガス中で溶融温度よりも低い温度で金属を一緒にプレスする熱間圧力溶接、容器内で不活性ガスを使用して圧力を加えるプロセスである熱間静水圧溶接、接合するロール溶接間にそれらを強制することによって異なる材料2 つの回転ホイール、高周波振動エネルギーを使用して薄い金属またはプラスチック シートを溶接する ULTRASONIC WELDING。
当社の他の溶接プロセスは、深い浸透と高速処理を伴う電子ビーム溶接ですが、特別な場合には高価な方法であると考えています。導電性または強磁性のワークピースを加熱するレーザービーム溶接も、深い浸透と高速処理を備えていますが、高価な方法です同じ溶接ヘッドでLBWとGMAWを組み合わせ、プレート間の2 mmのギャップを埋めることができるレーザーハイブリッド溶接、放電に続いて圧力を加えて材料を鍛造するサーミット溶接、アルミニウムと酸化鉄粉末間の発熱反応を伴うサーミット溶接、消耗電極を使用し、垂直位置でスチールのみを使用するエレクトロガス溶接、最後にスタッドをベースに接合するスタッドアーク溶接熱と圧力のある材料。
ここをクリックすることをお勧めしますAGS-TECH Incによるろう付け、はんだ付け、および接着剤接合プロセスの回路図をダウンロードしてください
これは、以下で提供する情報をよりよく理解するのに役立ちます.
• ろう付け : 2 つ以上の金属を接合します。フィラー金属をそれらの融点以上に加熱し、毛細管現象を利用して広げます。プロセスははんだ付けに似ていますが、ろう付けではフィラーを溶かすための温度が高くなります。溶接と同様に、フラックスは溶加材を大気汚染から保護します。冷却後、ワークピースは一緒に結合されます。このプロセスには、次の重要なステップが含まれます。良好な嵌合とクリアランス、母材の適切な洗浄、適切な固定具、適切なフラックスと雰囲気の選択、アセンブリの加熱、最後にろう付けされたアセンブリの洗浄。当社のろう付けプロセスには、手動または自動で行われる一般的な方法である TORCH BRAZING があります。 少量生産の注文や特殊なケースに適しています。ろう付けする接合部の近くでガス炎を使用して熱を加えます。炉ろう付けは、オペレーターのスキルをあまり必要とせず、工業的大量生産に適した半自動プロセスです。炉内の温度制御と雰囲気の制御の両方がこの技術の利点です。前者は熱サイクルを制御し、トーチろう付けの場合のように局所的な加熱を排除することを可能にし、後者は部品を酸化から保護するからです。ジギングを使用することで、製造コストを最小限に抑えることができます。欠点は、消費電力が高く、機器のコストが高く、設計上の考慮事項がより困難なことです。真空ろう付けは、真空の炉で行われます。温度の均一性が維持され、残留応力がほとんどない、フラックスフリーの非常にきれいな接合部が得られます。加熱と冷却のサイクルが遅い間に存在する残留応力が低いため、真空ろう付け中に熱処理を行うことができます。主な欠点は、真空環境の作成が高価なプロセスであるため、コストが高いことです。さらに別の技術 DIP BRAZING は、接合面にろう付け化合物が塗布された固定部品を接合します。その後、 fixtured 部品は、熱伝達媒体およびフラックスとして機能する塩化ナトリウム (食卓塩) などの溶融塩の槽に浸されます。空気が排除されるため、酸化物の形成は起こりません。インダクションブレージングでは、母材より融点の低い溶加材で接合します。誘導コイルからの交流電流は、主に鉄系の磁性材料に誘導加熱を誘発する電磁界を生成します。この方法は、選択的な加熱、必要な領域にのみ流れるフィラーとの良好な接合、炎が存在せず冷却が速いため酸化がほとんどない、高速加熱、一貫性、および大量生産への適合性を提供します。プロセスをスピードアップし、一貫性を確保するために、プリフォームを頻繁に使用します。セラミックと金属の継手、ハーメチック シーリング、真空フィードスルー、高真空と超高真空、および流体制御コンポーネントを製造する当社のろう付け施設に関する情報 は、次の場所にあります: ろう付け工場のパンフレット
• はんだ付け : はんだ付けでは、ワークピースを溶かすのではなく、接合部分よりも融点の低い溶加材を接合部に流し込みます。はんだ付けのフィラー金属は、ろう付けよりも低い温度で溶融します。ハンダ付けには鉛フリー合金を使用し、RoHS に準拠しています。さまざまな用途や要件に対応するために、銀合金などのさまざまな適切な合金を用意しています。はんだ付けは、気密性と液密性を備えた接合を提供します。ソフトはんだ付けでは、溶加材の融点は摂氏 400 度未満ですが、銀のはんだ付けとろう付けでは、より高い温度が必要です。ソフトはんだ付けは低温を使用しますが、高温での要求の厳しい用途では強力な接合にはなりません。一方、銀はんだ付けは、トーチによって提供される高温を必要とし、高温用途に適した強力な接合部を提供します。ろう付けには最高の温度が必要で、通常はトーチが使用されます。ろう付け接合部は非常に強いため、重い鉄の物体の修理に適しています。当社の製造ラインでは、手作業によるはんだ付けと自動はんだ付けラインの両方を使用しています。 INDUCTION はんだ付けでは、銅コイルに高周波 AC 電流を使用して誘導加熱を促進します。はんだ付け部分に電流が誘導され、その結果、高抵抗 jointで熱が発生します。この熱で溶加材が溶けます。フラックスも使用。誘導はんだ付けは、コイルをそれらの周りに巻き付けることにより、連続プロセスでシリンダーとパイプをはんだ付けするのに適した方法です。グラファイトやセラミックなどの一部の材料のはんだ付けは、はんだ付けの前に適切な金属でワークピースをメッキする必要があるため、より困難です。これにより、界面結合が促進されます。特に気密パッケージ用途向けに、このような材料のはんだ付けを行っています。当社は、主にウェーブはんだ付けを使用して、プリント回路基板 (PCB) を大量に製造しています。少量のプロトタイピングの目的でのみ、はんだごてを使用した手はんだを使用します。スルーホールと表面実装 PCB アセンブリ (PCBA) の両方にウェーブはんだ付けを使用します。一時的な接着剤がコンポーネントを回路基板に取り付けたままにし、アセンブリをコンベアに載せて、溶融はんだを含む装置の中を移動させます。最初に PCB はフラックス処理され、次に予熱ゾーンに入ります。溶融はんだは鍋にあり、その表面には定在波のパターンがあります。 PCB がこれらの波の上を移動すると、これらの波が PCB の底面に接触し、はんだ付けパッドに付着します。はんだはピンとパッドのみに残り、PCB 自体には残りません。溶融はんだの波は、飛散がなく、波の頂点がボードの望ましくない領域に触れて汚染しないように、適切に制御する必要があります。リフローはんだ付けでは、粘着性のはんだペーストを使用して電子部品を基板に仮付けします。次に、基板を温度制御付きのリフロー オーブンに入れます。ここでは、はんだが溶けてコンポーネントを永久的に接続します。この技術は、表面実装コンポーネントとスルーホール コンポーネントの両方に使用されます。適切な温度制御とオーブン温度の調整は、最大温度制限を超えて過熱してボード上の電子部品が破壊されるのを防ぐために不可欠です。リフローはんだ付けのプロセスでは、予熱ステップ、熱浸漬ステップ、リフローおよび冷却ステップなど、それぞれが異なる熱プロファイルを持ついくつかの領域または段階が実際にあります。これらのさまざまな手順は、プリント回路基板アセンブリ (PCBA) の損傷のないリフローはんだ付けに不可欠です。 ULTRASONIC SOLDERING は、独自の機能を備えたもう 1 つの頻繁に使用される技術です。ガラス、セラミック、および非金属材料のはんだ付けに使用できます。例えば、非金属である光起電力パネルは、この技術を使用して取り付けることができる電極を必要とする。超音波はんだ付けでは、超音波振動も放射する加熱されたはんだこて先を展開します。これらの振動は、基板と溶融はんだ材料との界面にキャビテーション気泡を生成します。キャビテーションの爆縮エネルギーが酸化物表面を変化させ、汚れや酸化物を取り除きます。この間に合金層も形成されます。接合面のはんだには酸素が含まれており、ガラスとはんだの間に強力な共有結合を形成することができます。 DIP SOLDERING は、小規模生産のみに適したウェーブはんだ付けの単純なバージョンと見なすことができます。最初の洗浄フラックスは、他のプロセスと同様に適用されます。コンポーネントが実装された PCB は、溶融はんだを含むタンクに手動または半自動で浸漬されます。溶融はんだは、基板上のはんだマスクで保護されていない露出した金属領域にくっつきます。設備はシンプルで安価です。
• 接着剤による接合 : これもよく使用される一般的な手法で、接着剤、エポキシ、プラスチック剤、その他の化学薬品を使用して表面を接合します。結合は、溶媒の蒸発、熱硬化、UV 光硬化、圧力硬化、または一定時間の待機のいずれかによって行われます。当社の生産ラインでは、さまざまな高性能接着剤が使用されています。適切に設計されたアプリケーションと硬化プロセスにより、接着剤による接着は、強く信頼性の高い非常に低い応力の接着を実現できます。接着剤結合は、湿気、汚染物質、腐食性物質、振動などの環境要因に対する優れた保護機能となります。接着接合の利点は次のとおりです。他の方法でははんだ付け、溶接、またはろう付けが困難な材料に適用できます。また、溶接やその他の高温プロセスによって損傷を受ける熱に弱い材料にも適しています。接着剤のその他の利点は、不規則な形状の表面に塗布できることと、他の方法と比較してアセンブリの重量が非常にわずかに増加することです。また、部品の寸法変化も非常に少ないです。一部の接着剤には屈折率整合特性があり、光や光信号の強度を大幅に低下させることなく、光学部品間で使用できます。一方、短所は硬化時間が長くなり、製造ラインが遅くなる可能性があること、固定具の要件、表面処理の要件、および再加工が必要な場合の分解の難しさです。当社の接着接合作業のほとんどには、次の手順が含まれます。
-表面処理: 脱イオン水洗浄、アルコール洗浄、プラズマまたはコロナ洗浄などの特殊な洗浄手順が一般的です。洗浄後、接着促進剤を表面に塗布して、可能な限り最良の接合を保証します。
-部品固定具: 接着剤塗布と硬化の両方で、カスタム固定具を設計して使用します。
-接着剤の塗布: 手動を使用することもあれば、場合によってはロボット工学、サーボモーター、リニアアクチュエーターなどの自動システムを使用して接着剤を適切な場所に配送し、ディスペンサーを使用して適切な量と量で配送します。
・硬化:接着剤によっては、単純な乾燥硬化だけでなく、UVライトを触媒として硬化させたり、オーブンで加熱硬化させたり、治具や治具に取り付けた抵抗発熱体を使用して硬化させたりする場合もあります。
ここをクリックすることをお勧めしますAGS-TECH Inc.による締結プロセスの概略図をダウンロードしてください。
これは、以下で提供する情報をよりよく理解するのに役立ちます.
• ファスニング プロセス : 当社の機械的接合プロセスは、ファスナーとインテグラル ジョイントの 2 つのカテゴリに分類されます。当社が使用するファスナーの例は、ねじ、ピン、ナット、ボルト、リベットです。当社が使用する一体型ジョイントの例は、スナップおよびシュリンク フィット、シーム、クリンプです。さまざまな固定方法を使用して、当社の機械的ジョイントが長年の使用に対して強力で信頼性が高いことを確認します。ねじとボルトは、物体をまとめて位置決めするために最も一般的に使用される留め具の一部です。当社のネジとボルトは ASME 規格を満たしています。六角キャップ スクリューと六角ボルト、ラグ スクリューとボルト、両頭スクリュー、ダウエル スクリュー、アイ スクリュー、ミラー スクリュー、板金スクリュー、微調整スクリュー、セルフ ドリルおよびセルフ タッピング スクリューなど、さまざまなタイプのスクリューとボルトが展開されています。 、止めねじ、ワッシャ内蔵ねじなど。皿頭、ドーム、丸、フランジ付きヘッドなどのさまざまなネジ頭タイプと、スロット、プラス、四角、六角ソケットなどのさまざまなネジ駆動タイプがあります。一方、 RIVET は、滑らかな円筒形のシャフトとヘッドで構成される永久的な機械的ファスナーです。挿入後、リベットのもう一方の端を変形させ、その直径を広げて固定します。つまり、リベットの頭は取り付け前は 1 つですが、取り付け後は 2 つになります。中実/丸頭リベット、構造用、半管状、ブラインド、オスカー、ドライブ、フラッシュ、フリクションロック、セルフピアスリベットなど、用途、強度、アクセスしやすさ、コストに応じて、さまざまなタイプのリベットを取り付けます。溶接熱による熱変形や材料特性の変化を避ける必要がある場合は、リベット留めが適しています。リベットはまた、軽量で、特に優れた強度とせん断力に対する耐久性を提供します。ただし、引張り荷重に対しては、ねじ、ナット、およびボルトの方が適している場合があります。クリンチング プロセスでは、特殊なパンチとダイを使用して、接合されるシート メタル間に機械的なインターロックを形成します。パンチはシートメタルの層をダイキャビティに押し込み、恒久的な接合部を形成します。クリンチングには加熱も冷却も必要なく、冷間加工プロセスです。場合によってはスポット溶接に代わる経済的な工法です。ピンニングでは、機械部品の位置を相互に固定するために使用される機械要素であるピンを使用します。主な種類はクレビスピン、コッターピン、スプリングピン、ダウエルピン、 、割りピンです。 STAPLING では、材料を接合または結合するために使用される 2 本の突起のある留め具であるステープル ガンとステープルを使用します。ステープル留めには次のような利点があります: 経済的で、簡単かつ迅速に使用できます。ステープルのクラウンは、突き合わせた材料をブリッジするために使用できます。ステープルのクラウンは、ケーブルのようなピースをブリッジし、穴を開けたりせずに表面に留めたりするのを容易にします。ダメージを与えますが、比較的簡単に除去できます。圧入は、部品同士を押し付けることで行われ、部品間の摩擦によって部品が固定されます。オーバーサイズのシャフトとアンダーサイズの穴で構成される圧入部品は、通常、力を加えるか、部品の熱膨張または収縮を利用するという 2 つの方法のいずれかで組み立てられます。 力を加えて圧入する場合は、油圧プレスまたは手動プレスを使用します。一方、熱膨張による圧入の場合は、包む部品を加熱し、熱いうちに組み付けます。冷えると収縮し、通常の寸法に戻ります。これにより、良好な圧入が得られます。これをシュリンクフィッティングと呼びます。これを行うもう 1 つの方法は、組み立てる前に包囲された部品を冷却してから、それらを嵌合部品に滑り込ませることです。アセンブリが温まると膨張し、ぴったりとフィットします。この後者の方法は、加熱によって材料特性が変化する危険性がある場合に適しています。そのような場合は、冷却する方が安全です。
空気圧および油圧コンポーネントおよびアセンブリ
• バルブ、O リング、ワッシャー、シール、ガスケット、リング、シムなどの油圧および空圧コンポーネント。
バルブや空圧機器は多種多様なため、ここにすべてを掲載することはできません。アプリケーションの物理的および化学的環境に応じて、特別な製品を用意しています。用途、コンポーネントの種類、仕様、圧力、温度、バルブや空気圧コンポーネントと接触する液体または気体などの環境条件を指定してください。お客様に最適な製品を選択するか、お客様の用途に合わせて特別に製造します。