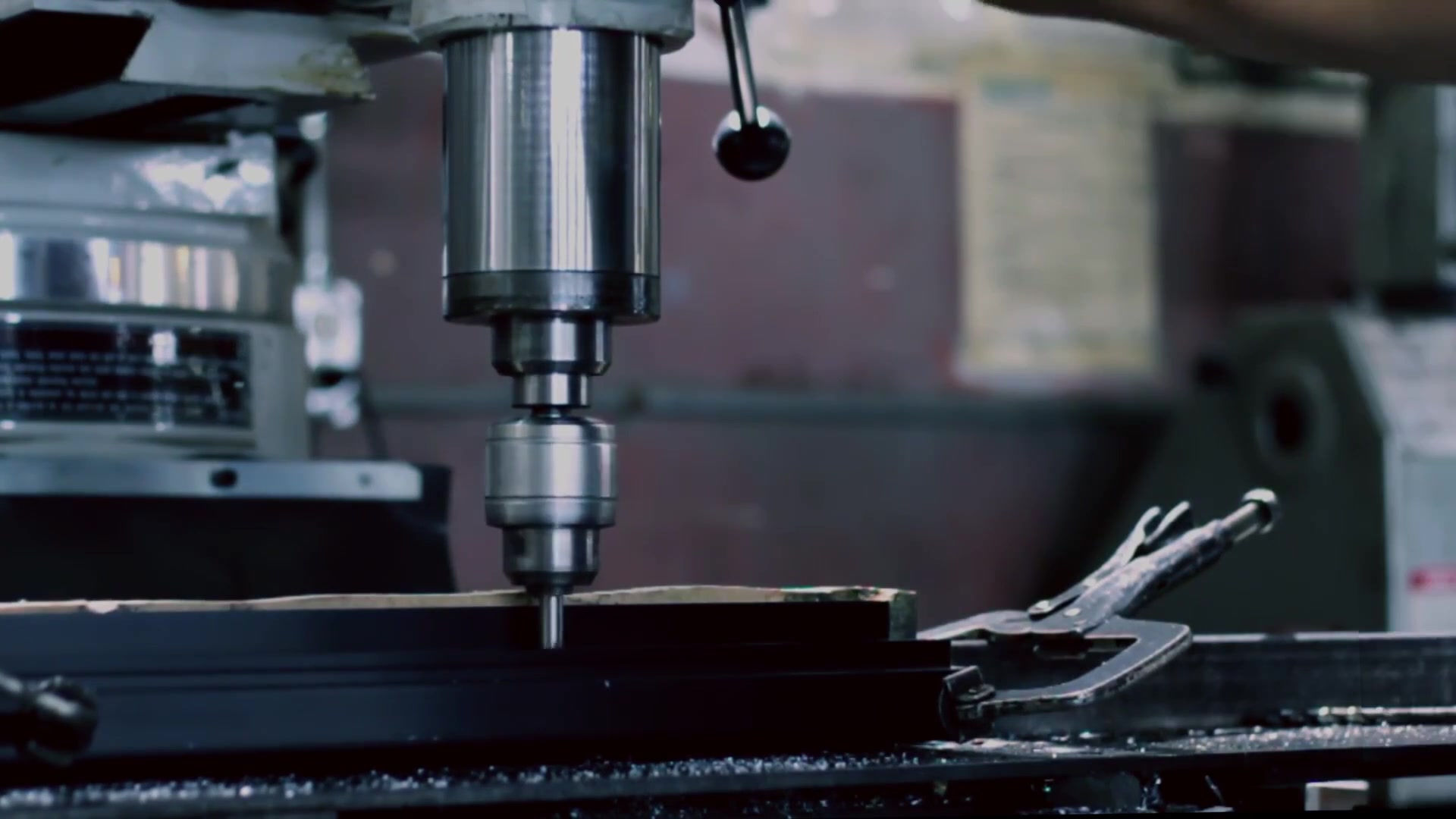
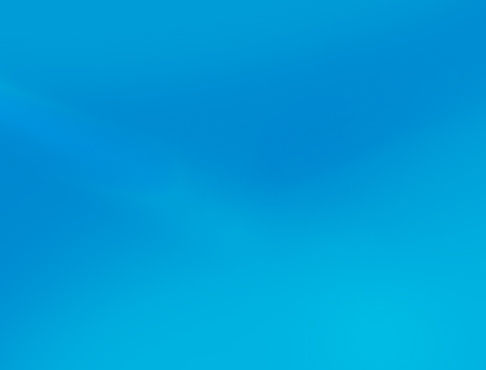
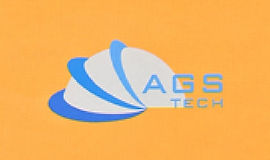
Globalny producent na zamówienie, integrator, konsolidator, partner outsourcingowy w zakresie szerokiej gamy produktów i usług.
Jesteśmy Twoim źródłem kompleksowej obsługi w zakresie produkcji, wytwarzania, inżynierii, konsolidacji, integracji, outsourcingu produktów i usług produkowanych na zamówienie oraz gotowych.
Choose your Language
-
Produkcja na zamówienie
-
Produkcja kontraktowa w kraju i na świecie
-
Outsourcing produkcji
-
Zamówienia krajowe i globalne
-
Konsolidacja
-
Integracja inżynierska
-
Usługi inżynieryjne
Nasze niestandardowe techniki odlewania i obróbki to odlewy jednorazowe i jednorazowe, odlewy żelazne i nieżelazne, piasek, matryca, odśrodkowa, ciągła, ceramiczna forma, inwestycja, tracona pianka, kształt zbliżony do netto, stała forma (odlewanie ciśnieniowe grawitacyjne), gips odlewy formowe (odlewy gipsowe) i łupinowe, części obrabiane metodą frezowania i toczenia przy użyciu urządzeń konwencjonalnych i CNC, obróbka szwajcarska zapewniająca dużą przepustowość niedrogich drobnych elementów precyzyjnych, obróbka śrub pod elementy złączne, obróbka niekonwencjonalna. Należy pamiętać, że oprócz metali i stopów metali obrabiamy elementy ceramiczne, szklane i plastikowe, a także w niektórych przypadkach, gdy wykonanie formy nie jest atrakcyjne lub nie jest możliwe. Obróbka materiałów polimerowych wymaga specjalistycznego doświadczenia, które posiadamy ze względu na wyzwania, jakie stawiają tworzywa sztuczne i guma ze względu na ich miękkość, brak sztywności... itd. Informacje na temat obróbki ceramiki i szkła można znaleźć na naszej stronie poświęconej obróbce niekonwencjonalnej. AGS-TECH Inc. produkuje i dostarcza zarówno lekkie, jak i ciężkie odlewy. Dostarczamy odlewy metalowe i obrabiane części do kotłów, wymienników ciepła, samochodów, mikrosilników, turbin wiatrowych, urządzeń do pakowania żywności i innych. Zalecamy kliknięcie tutaj, aby POBIERZ nasze schematyczne ilustracje procesów obróbki i odlewania opracowane przez firmę AGS-TECH Inc.
Pomoże to lepiej zrozumieć informacje, które przekazujemy poniżej. Przyjrzyjmy się szczegółowo niektórym z różnych technik, które oferujemy:
• ODLEWANIE EKSPLOATACYJNYCH FORM: Ta szeroka kategoria odnosi się do metod, które obejmują formy tymczasowe i jednorazowe. Przykładami są piasek, gips, muszla, inwestycja (zwana również woskiem traconym) i odlewanie gipsu.
• ODLEWANIE PIASKOWE: proces, w którym jako materiał formy używany jest piasek. Metoda bardzo stara i wciąż bardzo popularna do tego stopnia, że większość produkowanych odlewów metalowych jest wykonywana tą techniką. Niski koszt nawet przy produkcji małoseryjnej. Nadaje się do produkcji małych i dużych części. Technikę tę można wykorzystać do produkcji części w ciągu dni lub tygodni przy bardzo niewielkich nakładach inwestycyjnych. Wilgotny piasek jest spajany gliną, spoiwami lub specjalnymi olejami. Piasek jest zwykle zawarty w skrzynkach formierskich, a system wnęki i bramy jest tworzony przez zagęszczanie piasku wokół modeli. Procesy to:
1.) Umieszczenie modelu w piasku w celu wykonania formy
2.) Włączenie modelu i piasku do systemu bramkowania
3.) Usunięcie modelu
4.) Wypełnienie wnęki formy stopionym metalem
5.) Chłodzenie metalu
6.) Łamanie formy piaskowej i usuwanie odlewu
• ODLEWANIE W FORMIE TYNKOWEJ: Podobnie jak w przypadku odlewania piaskowego, zamiast piasku, jako materiał formy stosuje się gips modelarski. Krótkie czasy realizacji produkcji, takie jak odlewanie w piasku i niedrogie. Dobre tolerancje wymiarowe i wykończenie powierzchni. Jego główną wadą jest to, że może być stosowany tylko z metalami o niskiej temperaturze topnienia, takimi jak aluminium i cynk.
• ODLEWANIE W FORMIE POWŁOKI: Podobnie jak w przypadku odlewania w formach piaskowych. Gniazdo formy uzyskane przez utwardzoną skorupę z piasku i spoiwa z żywicy termoutwardzalnej zamiast kolby wypełnionej piaskiem jak w procesie odlewania w piasku. Prawie każdy metal nadający się do odlewania w piasku można odlewać metodą skorupową. Proces można podsumować jako:
1.) Produkcja formy skorupowej. Zastosowany piasek ma znacznie mniejszy rozmiar ziarna w porównaniu z piaskiem używanym do odlewania w piasku. Drobny piasek miesza się z żywicą termoutwardzalną. Metalowy wzór jest pokryty środkiem antyadhezyjnym, aby ułatwić zdejmowanie skorupy. Następnie model metalowy jest podgrzewany i mieszanina piasku jest porowata lub nadmuchana na model odlewania na gorąco. Na powierzchni wzoru tworzy się cienka powłoka. Grubość tej skorupy można regulować, zmieniając czas, w którym mieszanina piasku i żywicy styka się z metalowym wzorem. Luźny piasek jest następnie usuwany z pozostawionym wzorem pokrytym muszlą.
2.) Następnie skorupa i wzór są podgrzewane w piecu, aby skorupa stwardniała. Po całkowitym utwardzeniu skorupa jest wyrzucana z wzoru za pomocą szpilek wbudowanych we wzór.
3.) Dwie takie skorupy są łączone ze sobą przez sklejenie lub zaciśnięcie i tworzą kompletną formę. Teraz forma skorupowa jest wkładana do pojemnika, w którym podczas procesu odlewania jest podtrzymywana piaskiem lub śrutem metalowym.
4.) Teraz gorący metal można wlać do formy skorupowej.
Zaletami odlewania skorupowego są produkty o bardzo dobrym wykończeniu powierzchni, możliwość wykonania skomplikowanych części z dużą dokładnością wymiarową, łatwość automatyzacji procesu, ekonomiczność przy produkcji wielkoseryjnej.
Wadą jest to, że formy wymagają dobrej wentylacji ze względu na gazy, które powstają, gdy stopiony metal styka się ze spoiwem chemicznym, żywice termoutwardzalne i metalowe modele są drogie. Ze względu na koszt wzorów metalowych, technika ta może nie pasować do małych serii produkcyjnych.
• ODLEWANIE INWESTYCYJNE (znane również jako ODLEWANIE LOST-WAX): Również bardzo stara technika, odpowiednia do wytwarzania wysokiej jakości części z dużą dokładnością, powtarzalnością, wszechstronnością i integralnością z wielu metali, materiałów ogniotrwałych i specjalnych stopów o wysokiej wydajności. Można wytwarzać zarówno małe, jak i duże części. Jest to kosztowny proces w porównaniu z niektórymi innymi metodami, ale główną zaletą jest możliwość wytwarzania części o zbliżonym kształcie, skomplikowanych konturach i szczegółach. Tak więc koszt jest w pewnym stopniu równoważony przez eliminację poprawek i obróbki w niektórych przypadkach. Chociaż mogą występować różnice, oto podsumowanie ogólnego procesu odlewania metodą traconego wosku:
1.) Tworzenie oryginalnego wzorca z wosku lub plastiku. Każdy odlew wymaga jednego wzoru, ponieważ są one niszczone w procesie. Potrzebna jest również forma, z której wykonywane są wzory i przez większość czasu forma jest odlewana lub obrabiana. Ponieważ forma nie musi być otwierana, można uzyskać skomplikowane odlewy, wiele modeli woskowych można połączyć jak gałęzie drzewa i zlać razem, umożliwiając w ten sposób produkcję wielu części z jednego wylania metalu lub stopu metalu.
2.) Następnie model zanurza się lub wylewa ogniotrwałą zawiesiną składającą się z bardzo drobnoziarnistej krzemionki, wody, spoiw. Powoduje to powstanie warstwy ceramicznej na powierzchni wzoru. Powłokę ogniotrwałą na wzorze pozostawia się do wyschnięcia i utwardzenia. Od tego etapu pochodzi nazwa odlewania metodą traconego wosku: Zawiesina ogniotrwała jest nakładana na wzór woskowy.
3.) Na tym etapie utwardzona forma ceramiczna jest odwracana do góry nogami i podgrzewana, aby wosk stopił się i wylał z formy. Pozostawia się wnękę do odlewania metalu.
4.) Po wyjęciu wosku forma ceramiczna jest podgrzewana do jeszcze wyższej temperatury, co powoduje jej wzmocnienie.
5.) Odlew metalu wlewa się do gorącej formy wypełniającej wszystkie skomplikowane sekcje.
6.) Odlew może się zestalić
7.) Na koniec forma ceramiczna jest łamana, a wyprodukowane części są wycinane z drzewa.
Oto link do Broszury Odlewnictwa Inwestycyjnego
• ODLEWANIE WZORÓW ODPAROWANYCH: Proces wykorzystuje wzór wykonany z materiału takiego jak pianka polistyrenowa, który odparowuje, gdy gorący stopiony metal jest wlewany do formy. Istnieją dwa rodzaje tego procesu: LOST FOAM CASTING, który wykorzystuje piasek niezwiązany oraz FULL MOLD CASTING, który wykorzystuje piasek związany. Oto ogólne etapy procesu:
1.) Wyprodukuj wzór z materiału takiego jak polistyren. Gdy będą produkowane duże ilości, wzór jest formowany. Jeżeli część ma złożony kształt, może być konieczne sklejenie kilku odcinków takiego materiału piankowego w celu utworzenia wzoru. Często pokrywamy wzór masą ogniotrwałą, aby uzyskać dobre wykończenie powierzchni odlewu.
2.) Wzór jest następnie umieszczany w piasku formierskim.
3.) Stopiony metal jest wlewany do formy, odparowując wzór piankowy, tj. w większości przypadków polistyren przepływający przez gniazdo formy.
4.) Stopiony metal pozostaje w formie piaskowej do stwardnienia.
5.) Po stwardnieniu usuwamy odlew.
W niektórych przypadkach wytwarzany przez nas produkt wymaga rdzenia we wzorze. W odlewaniu wyparnym nie ma potrzeby umieszczania i zabezpieczania rdzenia we wnęce formy. Technika ta jest odpowiednia do wytwarzania bardzo złożonych geometrii, można ją łatwo zautomatyzować do produkcji wielkoseryjnej, a w odlewie nie ma linii podziału. Podstawowy proces jest prosty i ekonomiczny w realizacji. W przypadku produkcji wielkoseryjnej, ponieważ do wytworzenia wzorów z polistyrenu potrzebna jest matryca lub forma, może to być nieco kosztowne.
• ODLEWANIE FORM NIEROZPRĘŻALNYCH: Ta szeroka kategoria odnosi się do metod, w których forma nie musi być ponownie przetwarzana po każdym cyklu produkcyjnym. Przykładami są odlewanie trwałe, ciśnieniowe, ciągłe i odśrodkowe. Uzyskuje się powtarzalność, a części można scharakteryzować jako KSZTAŁT BLISKO NETTO.
• TRWAŁE ODLEWANIE FORM: Formy wielokrotnego użytku wykonane z metalu są używane do odlewania wielokrotnego. Forma stała może być używana dziesiątki tysięcy razy, zanim się zużyje. Do napełniania formy stosuje się zwykle grawitację, ciśnienie gazu lub próżnię. Formy (zwane również matrycami) są zwykle wykonane z żelaza, stali, ceramiki lub innych metali. Ogólny proces to:
1.) Obrabiaj i stwórz formę. Formę często wykonuje się z dwóch pasujących do siebie metalowych bloków, które można otwierać i zamykać. Zarówno elementy części, jak i system bramkowania są zazwyczaj obrabiane w formie odlewniczej.
2.) Wewnętrzne powierzchnie formy są pokryte zawiesiną zawierającą materiały ogniotrwałe. Pomaga to kontrolować przepływ ciepła i działa jak smar ułatwiający usuwanie odlewu.
3.) Następnie stałe połówki formy są zamykane i forma jest podgrzewana.
4.) Stopiony metal wlewa się do formy i pozostawia do zestalenia.
5.) Zanim nastąpi duże schłodzenie, wyjmujemy część z formy stałej za pomocą wypychaczy, gdy połówki formy są otwarte.
Często stosujemy odlewanie w formach trwałych do metali o niskiej temperaturze topnienia, takich jak cynk i aluminium. Do odlewów staliwnych używamy grafitu jako materiału do formowania. Niekiedy uzyskujemy złożone geometrie za pomocą rdzeni w formach trwałych. Zaletami tej techniki są odlewy o dobrych właściwościach mechanicznych uzyskiwanych dzięki szybkiemu chłodzeniu, jednorodność właściwości, dobra dokładność i wykończenie powierzchni, niskie współczynniki odrzutów, możliwość automatyzacji procesu i ekonomiczne wytwarzanie dużych ilości. Wadą są wysokie koszty początkowej konfiguracji, które sprawiają, że nie nadaje się do operacji o małej objętości oraz ograniczenia wielkości produkowanych części.
• ODLEWANIE MATRYC: Matryca jest obrabiana maszynowo, a stopiony metal jest wpychany pod wysokim ciśnieniem do wnęk formy. Możliwe są zarówno odlewy ciśnieniowe z metali nieżelaznych, jak i metali żelaznych. Proces nadaje się do dużych serii produkcyjnych małych i średnich części z detalami, wyjątkowo cienkimi ściankami, spójnością wymiarową i dobrym wykończeniem powierzchni. AGS-TECH Inc. jest w stanie wyprodukować tą techniką ściany o grubości nawet 0,5 mm. Podobnie jak w przypadku odlewania w formach trwałych, forma musi składać się z dwóch połówek, które mogą się otwierać i zamykać w celu usunięcia wyprodukowanej części. Forma odlewnicza może mieć wiele wnęk, aby umożliwić produkcję wielu odlewów w każdym cyklu. Formy do odlewania ciśnieniowego są bardzo ciężkie i znacznie większe niż produkowane przez nie części, a zatem również drogie. Bezpłatnie naprawiamy i wymieniamy zużyte matryce dla naszych klientów, o ile ponownie zamówią u nas swoje części. Nasze matryce mają długą żywotność w zakresie kilkuset tysięcy cykli.
Oto podstawowe uproszczone etapy procesu:
1.) Produkcja formy ogólnie ze stali
2.) Forma zainstalowana na maszynie do odlewania ciśnieniowego
3.) Tłok wymusza przepływ stopionego metalu w zagłębieniach matrycy, wypełniając zawiłe rysy i cienkie ścianki
4.) Po napełnieniu formy stopionym metalem odlew pozostawia się do utwardzenia pod ciśnieniem
5.) Forma jest otwierana, a odlew usuwany za pomocą kołków wypychaczy.
6.) Teraz pusta matryca jest ponownie nasmarowana i zaciśnięta do następnego cyklu.
W odlewaniu ciśnieniowym często stosujemy formowanie wkładek, w którym do formy wbudowujemy dodatkową część i odlewamy wokół niej metal. Po zestaleniu części te stają się częścią odlewanego produktu. Zaletami odlewania ciśnieniowego są dobre właściwości mechaniczne części, możliwość tworzenia skomplikowanych detali, drobne szczegóły i dobre wykończenie powierzchni, wysokie tempo produkcji, łatwa automatyzacja. Wady to: Niezbyt odpowiednia dla małych objętości ze względu na wysoki koszt matrycy i sprzętu, ograniczenia w kształtach, które można odlewać, małe okrągłe ślady na odlewanych częściach wynikające ze styku kołków wypychaczy, cienka wypływka metalu wyciskanego na linii podziału, potrzeba w przypadku otworów wentylacyjnych wzdłuż linii podziału między matrycą, konieczność utrzymania niskiej temperatury formy przy użyciu cyrkulacji wody.
• ODLEWANIE ODŚRODKOWE: Stopiony metal jest wlewany do środka formy obrotowej na osi obrotu. Siły odśrodkowe wyrzucają metal w kierunku obrzeża i pozwala na krzepnięcie, gdy forma nadal się obraca. Można stosować zarówno obroty osi poziomej, jak i pionowej. Odlewane mogą być zarówno części o okrągłych powierzchniach wewnętrznych, jak i inne nieokrągłe kształty. Proces można podsumować jako:
1.) Stopiony metal wlewa się do formy odśrodkowej. Metal jest następnie dociskany do ścian zewnętrznych w wyniku wirowania formy.
2.) Gdy forma się obraca, odlew metalu twardnieje
Odlewanie odśrodkowe jest odpowiednią techniką do produkcji wydrążonych części cylindrycznych, takich jak rury, nie ma potrzeby stosowania wlewów, pionów i elementów zamykających, dobre wykończenie powierzchni i szczegółowe cechy, brak problemów ze skurczem, możliwość produkcji długich rur o bardzo dużych średnicach, wysoka wydajność produkcyjna .
• ODLEWANIE CIĄGŁE (ODLEWANIE PASEM): Stosowane do odlewania ciągłej długości metalu. Zasadniczo stopiony metal jest odlewany w dwuwymiarowy profil formy, ale jego długość jest nieokreślona. Nowy stopiony metal jest stale podawany do formy, gdy odlew przesuwa się w dół, a jego długość wzrasta wraz z upływem czasu. Metale takie jak miedź, stal, aluminium odlewane są w długie pasma w procesie ciągłego odlewania. Proces może mieć różne konfiguracje, ale wspólną można uprościć jako:
1.) Stopiony metal jest wlewany do pojemnika znajdującego się wysoko nad formą w dobrze obliczonych ilościach i szybkościach przepływu i przepływa przez formę chłodzoną wodą. Metalowy odlew wlany do formy krzepnie do listwy startowej umieszczonej na dnie formy. Ta listwa startowa daje rolkom coś, za co mogą się początkowo chwycić.
2.) Długie metalowe pasmo jest przenoszone na rolkach ze stałą prędkością. Rolki zmieniają również kierunek przepływu metalowego pasma z pionowego na poziomy.
3.) Po przebyciu pewnej odległości przez odlewanie ciągłe, palnik lub piła poruszająca się wraz z odlewem szybko przycina go do żądanej długości.
Proces ciągłego odlewania można zintegrować z ROLLING PROCESS, w którym metal odlewany w sposób ciągły może być podawany bezpośrednio do walcarki w celu wytworzenia belek dwuteowych, belek teowych… itd. Odlewanie ciągłe zapewnia jednolite właściwości w całym produkcie, charakteryzuje się wysokim stopniem krzepnięcia, zmniejsza koszty ze względu na bardzo niskie straty materiału, oferuje proces, w którym ładowanie metalu, wylewanie, krzepnięcie, cięcie i usuwanie odlewu odbywa się w trybie ciągłym i co skutkuje wysoką wydajnością i wysoką jakością. Głównym czynnikiem jest jednak wysoka inwestycja początkowa, koszty instalacji i wymagania przestrzenne.
• USŁUGI OBRÓBCZE : Oferujemy obróbkę trzy-, cztero- i pięcioosiową. Rodzaje stosowanych przez nas procesów obróbki to TOCZENIE, FREZOWANIE, WIERCENIE, WYTACZANIE, PRZECIĄGANIE, STRUGANIE, PIŁOWANIE, SZLIFOWANIE, DOCIERANIE, POLEROWANIE i OBRÓBKA NIETRADYCYJNA, która jest dalej rozwijana w innym menu naszej strony internetowej. Do większości naszej produkcji używamy maszyn CNC. Jednak w przypadku niektórych operacji konwencjonalne techniki są lepiej dopasowane i dlatego również na nich polegamy. Nasze możliwości obróbki osiągają najwyższy możliwy poziom, a niektóre najbardziej wymagające części są produkowane w zakładzie posiadającym certyfikat AS9100. Łopatki do silników odrzutowych wymagają wysoce specjalistycznego doświadczenia produkcyjnego i odpowiedniego sprzętu. Przemysł lotniczy ma bardzo surowe standardy. Niektóre elementy o złożonej strukturze geometrycznej najłatwiej wytwarza się za pomocą obróbki pięcioosiowej, która występuje tylko w niektórych zakładach obróbczych, w tym w naszej. Nasz certyfikowany zakład lotniczy posiada niezbędne doświadczenie spełniające obszerne wymagania dotyczące dokumentacji przemysłu lotniczego.
W operacjach TOCZENIA przedmiot obrabiany jest obracany i przesuwany względem narzędzia skrawającego. Do tego procesu używana jest maszyna zwana tokarką.
W FREZOWANIU maszyna zwana frezarką ma obrotowe narzędzie, które powoduje, że krawędzie tnące opierają się o obrabiany przedmiot.
Operacje WIERCENIA obejmują obrotowy nóż z krawędziami tnącymi, który wytwarza otwory w kontakcie z obrabianym przedmiotem. Zwykle stosuje się wiertarki, tokarki lub młyny.
W operacjach WYTACZANIA narzędzie z pojedynczą zagiętą, spiczastą końcówką jest przesuwane do zgrubnego otworu w obracającym się przedmiocie obrabianym, aby nieznacznie powiększyć otwór i poprawić dokładność. Służy do precyzyjnego wykańczania.
PRZECIĄGANIE polega na użyciu narzędzia zębatego do usuwania materiału z przedmiotu obrabianego w jednym przejściu przeciągania (narzędzie zębate). W przeciąganiu liniowym przeciąganie przebiega liniowo po powierzchni przedmiotu obrabianego, aby wykonać cięcie, podczas gdy w przeciąganiu obrotowym przeciąganie jest obracane i wciskane w przedmiot obrabiany, aby wyciąć kształt symetryczny względem osi.
OBRÓBKA TYPU SZWAJCARSKIEGO jest jedną z naszych cennych technik, których używamy do wielkoseryjnej produkcji małych, precyzyjnych części. Na tokarce typu szwajcarskiego niedrogo toczymy małe, złożone, precyzyjne części. W przeciwieństwie do konwencjonalnych tokarek, w których przedmiot obrabiany jest nieruchomy, a narzędzie jest w ruchu, w centrach tokarskich typu Swiss przedmiot obrabiany może poruszać się w osi Z, a narzędzie jest nieruchome. W obróbce typu szwajcarskiego półfabrykat jest utrzymywany w maszynie i przesuwany przez tuleję prowadzącą w osi Z, odsłaniając tylko część do obróbki. W ten sposób zapewniony jest mocny chwyt i bardzo wysoka dokładność. Dostępność narzędzi pod napięciem umożliwia frezowanie i wiercenie w miarę przesuwania się materiału z tulei prowadzącej. Oś Y urządzeń typu szwajcarskiego zapewnia pełne możliwości frezowania i oszczędza dużą ilość czasu w produkcji. Ponadto nasze maszyny posiadają wiertła i narzędzia wytaczarskie, które działają na części, gdy jest ona trzymana we wrzecionie pomocniczym. Nasze możliwości obróbki Swiss-Type dają nam w pełni zautomatyzowaną, kompletną obróbkę w jednej operacji.
Obróbka skrawaniem jest jednym z największych segmentów działalności AGS-TECH Inc. Używamy go jako operacji podstawowej lub operacji drugorzędnej po odlewaniu lub wytłaczaniu części, aby wszystkie specyfikacje rysunkowe były spełnione.
• USŁUGI WYKOŃCZENIA POWIERZCHNI: Oferujemy szeroką gamę obróbki powierzchni i wykańczania powierzchni, takich jak kondycjonowanie powierzchni w celu zwiększenia przyczepności, osadzanie cienkiej warstwy tlenku w celu zwiększenia przyczepności powłoki, piaskowanie, chem-film, anodowanie, azotowanie, malowanie proszkowe, powlekanie natryskowe , różne zaawansowane techniki metalizacji i powlekania, w tym rozpylanie, wiązka elektronów, odparowanie, powlekanie, twarde powłoki, takie jak diamentopodobny węgiel (DLC) lub powłoka tytanowa do narzędzi wiertniczych i skrawających.
• USŁUGI ZNAKOWANIA I ETYKIETOWANIA PRODUKTÓW: Wielu naszych klientów wymaga znakowania i etykietowania, znakowania laserowego, grawerowania na częściach metalowych. Jeśli masz taką potrzebę, porozmawiajmy, która opcja będzie dla Ciebie najlepsza.
Oto niektóre z powszechnie stosowanych produktów odlewanych z metalu. Ponieważ są one gotowe, możesz zaoszczędzić na kosztach form, jeśli którykolwiek z nich spełni Twoje wymagania: