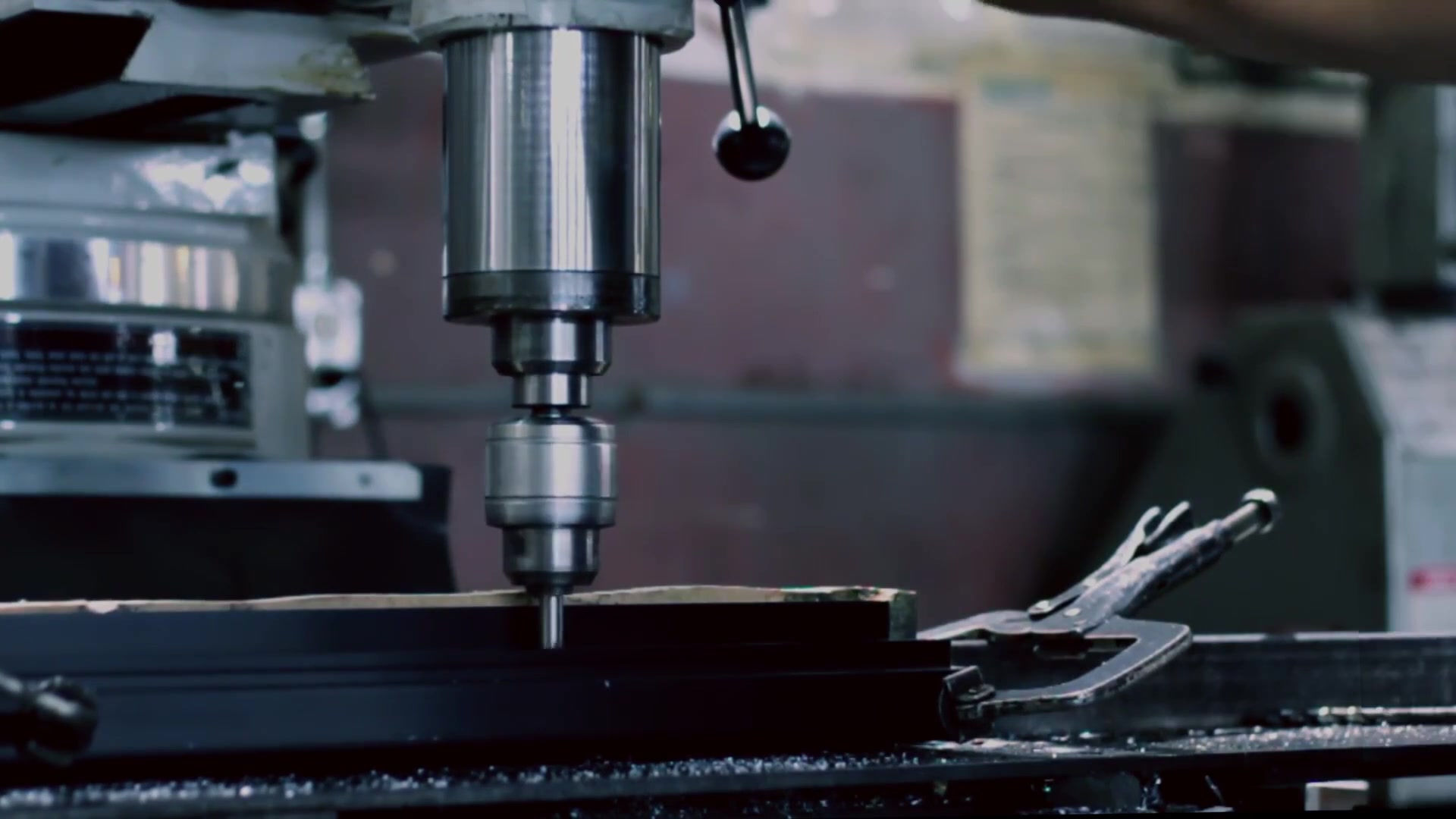
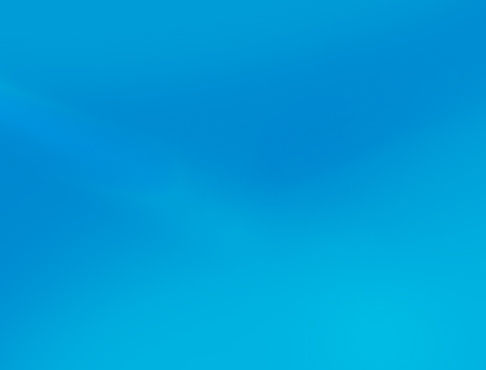
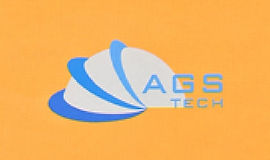
Globalny producent na zamówienie, integrator, konsolidator, partner outsourcingowy w zakresie szerokiej gamy produktów i usług.
Jesteśmy Twoim źródłem kompleksowej obsługi w zakresie produkcji, wytwarzania, inżynierii, konsolidacji, integracji, outsourcingu produktów i usług produkowanych na zamówienie oraz gotowych.
Choose your Language
-
Produkcja na zamówienie
-
Produkcja kontraktowa w kraju i na świecie
-
Outsourcing produkcji
-
Zamówienia krajowe i globalne
-
Konsolidacja
-
Integracja inżynierska
-
Usługi inżynieryjne
Łączymy, montujemy i mocujemy wyprodukowane przez Państwa części i przekształcamy je w gotowe lub półfabrykaty za pomocą SPAWANIA, LUTOWANIA, LUTOWANIA, SPIEKANIA, KLEJENIA KLEJEM, ŁĄCZENIA, ZACISKANIA. Niektóre z naszych najpopularniejszych procesów spawalniczych to spawanie łukowe, gazowo-tlenowe, oporowe, rzutowe, spawowe, spęczane, udarowe, półprzewodnikowe, wiązką elektronów, laserowe, termitowe, indukcyjne. Nasze popularne procesy lutowania to lutowanie palnikowe, indukcyjne, piecowe i zanurzeniowe. Nasze metody lutowania to lutowanie żelazne, płytowe, piecowe, indukcyjne, zanurzeniowe, falowe, rozpływowe i ultradźwiękowe. Do klejenia często używamy tworzyw termoplastycznych i termoutwardzalnych, epoksydów, fenoli, poliuretanów, stopów klejących oraz niektórych innych chemikaliów i taśm. Wreszcie nasze procesy mocowania obejmują wbijanie gwoździ, wkręcanie, nakrętki i śruby, nitowanie, zaciskanie, przypinanie, zszywanie i zszywanie oraz pasowanie wtłaczane.
• SPAWANIE: Spawanie obejmuje łączenie materiałów poprzez topienie obrabianych elementów i wprowadzanie materiałów wypełniających, które również łączą się ze stopionym jeziorkiem spawalniczym. Gdy okolica się ochłodzi, uzyskujemy mocne połączenie. W niektórych przypadkach stosowany jest nacisk. W przeciwieństwie do spawania, operacje lutowania i lutowania polegają jedynie na topieniu materiału o niższej temperaturze topnienia pomiędzy detalami, a detale nie topią się. Zalecamy kliknięcie tutaj, abyPOBIERZ nasze schematyczne ilustracje procesów spawania opracowane przez AGS-TECH Inc.
Pomoże Ci to lepiej zrozumieć informacje, które udostępniamy poniżej.
W spawaniu łukowym używamy zasilacza i elektrody do wytworzenia łuku elektrycznego, który topi metale. Miejsce spawania jest chronione gazem osłonowym lub parą lub innym materiałem. Proces ten jest popularny przy spawaniu części samochodowych i konstrukcji stalowych. W spawaniu łukowym w osłonie metalowej (SMAW) lub znanym również jako spawanie kijem, pałeczka elektrody jest zbliżana do materiału podstawowego, a między nimi powstaje łuk elektryczny. Pręt elektrody topi się i działa jako materiał wypełniający. Elektroda zawiera również topnik, który działa jak warstwa żużla i wydziela opary, które działają jak gaz osłonowy. Chronią one obszar spawania przed zanieczyszczeniem środowiska. Żadne inne wypełniacze nie są używane. Wadą tego procesu jest jego powolność, konieczność częstej wymiany elektrod, konieczność rozdrobnienia resztkowego żużla pochodzącego z topnika. Szereg metali, takich jak żelazo, stal, nikiel, aluminium, miedź… itd. Możliwość spawania. Jego zaletami są niedrogie narzędzia i łatwość obsługi. Spawanie łukiem metalowym w osłonie gazu (GMAW), znane również jako gaz obojętny metal (MIG), mamy ciągłe podawanie zużywalnego wypełniacza drutu elektrodowego i gazu obojętnego lub częściowo obojętnego, który przepływa wokół drutu, chroniąc przed zanieczyszczeniem środowiska w obszarze spawania. Można spawać stal, aluminium i inne metale nieżelazne. Zaletami MIG są wysokie prędkości spawania i dobra jakość. Wadą jest skomplikowany sprzęt i wyzwania, z jakimi mierzy się w wietrznych środowiskach zewnętrznych, ponieważ musimy utrzymywać stabilny gaz osłonowy wokół obszaru spawania. Odmianą GMAW jest spawanie łukowe z rdzeniem topnikowym (FCAW), które składa się z cienkiej metalowej rury wypełnionej materiałami topnikowymi. Czasami strumień wewnątrz rurki wystarcza do ochrony przed zanieczyszczeniem środowiska. Spawanie łukiem krytym (SAW) jest szeroko zautomatyzowanym procesem, obejmującym ciągłe podawanie drutu i zajarzenie łuku pod warstwą otuliny topnika. Szybkość produkcji i jakość są wysokie, żużel spawalniczy łatwo schodzi, a środowisko pracy jest wolne od dymu. Wadą jest to, że można go używać tylko do spawania parts w określonych pozycjach. W spawaniu łukiem wolframowym (GTAW) lub spawaniu wolframowym w gazie obojętnym (TIG) używamy elektrody wolframowej wraz z oddzielnym wypełniaczem i gazami obojętnymi lub zbliżonymi do obojętnych. Jak wiemy, wolfram ma wysoką temperaturę topnienia i jest bardzo odpowiednim metalem do bardzo wysokich temperatur. Wolfram w TIG nie jest zużywany w przeciwieństwie do innych metod wyjaśnionych powyżej. Powolna, ale wysokiej jakości technika spawania, przewyższająca inne techniki spawania cienkich materiałów. Nadaje się do wielu metali. Spawanie łukiem plazmowym jest podobne, ale do tworzenia łuku wykorzystuje się gaz plazmowy. Łuk podczas spawania łukiem plazmowym jest stosunkowo bardziej skoncentrowany w porównaniu do spawania metodą GTAW i może być stosowany do szerszego zakresu grubości metalu przy znacznie wyższych prędkościach. Spawanie metodą GTAW i łukiem plazmowym może być stosowane do mniej więcej takich samych materiałów.
SPAWANIE TLENOWE / TLENOWE zwane również spawaniem tlenowo-acetylenowym, spawanie tlenowe, spawanie gazowe odbywa się przy użyciu paliw gazowych i tlenu do spawania. Ponieważ nie jest używana energia elektryczna, jest przenośny i może być używany tam, gdzie nie ma elektryczności. Za pomocą palnika spawalniczego podgrzewamy elementy i materiał wypełniający, aby wytworzyć wspólny basen stopionego metalu. Można stosować różne paliwa, takie jak acetylen, benzyna, wodór, propan, butan… itd. W spawaniu tlenowo-paliwowym używamy dwóch zbiorników, jednego na paliwo, a drugiego na tlen. Tlen utlenia paliwo (spala je).
ZGRZEWANIE REZYSTANCYJNE: Ten rodzaj zgrzewania wykorzystuje ogrzewanie Joule'a, a ciepło jest wytwarzane w miejscu, w którym przez określony czas działa prąd elektryczny. Przez metal przechodzą wysokie prądy. W tym miejscu tworzą się kałuże stopionego metalu. Metody zgrzewania oporowego są popularne ze względu na ich wydajność, niewielki potencjał zanieczyszczeń. Wadami są jednak stosunkowo znaczne koszty sprzętu i nieodłączne ograniczenie stosunkowo cienkich elementów obrabianych. ZGRZEWANIE PUNKTOWE jest jednym z głównych rodzajów zgrzewania oporowego. Tutaj łączymy dwa lub więcej zachodzących na siebie arkuszy lub elementów roboczych, używając dwóch miedzianych elektrod do zaciskania arkuszy i przepuszczania przez nie wysokiego prądu. Materiał pomiędzy miedzianymi elektrodami nagrzewa się i w tym miejscu powstaje roztopiona kałuża. Prąd jest następnie zatrzymywany, a miedziane końcówki elektrod chłodzą miejsce spoiny, ponieważ elektrody są chłodzone wodą. Doprowadzenie odpowiedniej ilości ciepła do właściwego materiału i odpowiedniej grubości jest kluczowe dla tej techniki, ponieważ w przypadku niewłaściwego zastosowania połączenie będzie słabe. Zgrzewanie punktowe ma tę zaletę, że nie powoduje znaczących odkształceń elementów obrabianych, jest energooszczędne, łatwość automatyzacji i doskonałe tempo produkcji oraz nie wymaga żadnych wypełniaczy. Wadą jest to, że ponieważ spawanie odbywa się punktowo, a nie tworzy ciągły szew, całkowita wytrzymałość może być stosunkowo niższa w porównaniu z innymi metodami spawania. Z kolei SEAM WELDING tworzy spoiny na stykających się powierzchniach podobnych materiałów. Szew może być łączony na styk lub na zakładkę. Spawanie spoin zaczyna się na jednym końcu i przesuwa się stopniowo do drugiego. W tej metodzie stosuje się również dwie elektrody miedziane do przykładania ciśnienia i prądu do obszaru spoiny. Elektrody w kształcie tarczy obracają się ze stałym kontaktem wzdłuż linii szwu i wykonują ciągłą spoinę. Tutaj również elektrody są chłodzone wodą. Spoiny są bardzo mocne i niezawodne. Inne metody to spawanie rzutowe, błyskowe i spęczające.
SPAWANIE SOLIDNE jest nieco inne niż poprzednie metody wyjaśnione powyżej. Koalescencja zachodzi w temperaturach poniżej temperatury topnienia łączonych metali i bez użycia wypełniacza metalowego. W niektórych procesach może być stosowane ciśnienie. Różne metody to ZGRZEWANIE KOEKTRUZYJNE gdzie różne metale są wytłaczane przez tę samą matrycę, ZGRZEWANIE NA ZIMNO gdzie łączymy miękkie stopy poniżej ich temperatury topnienia, ZGRZEWANIE DYFUZYJNE techniką bez widocznych linii zgrzewów, ZGRZEWANIE WYBUCHOWE do łączenia materiałów odmiennych, np. stopów odpornych na korozję z konstrukcją. stali, ZGRZEWANIA IMPULSOWEGO ELEKTROMAGNETYCZNEGO, w którym przyspieszamy rury i blachy siłami elektromagnetycznymi, ZGRZEWANIA KUŻOWEGO polegającego na podgrzaniu metali do wysokich temperatur i zbijaniu ich ze sobą młotkiem, ZGRZEWANIA TARCIOWEGO, w którym wykonuje się odpowiednie zgrzewanie tarciowe, ZGRZEWANIA TARCZOWEGO Z PRZESYŁANIEM, które polega na narzędzie zużywalne przechodzące przez linię złącza, ZGRZEWANIE NA GORĄCO, gdzie ściskamy metale w podwyższonych temperaturach poniżej temperatury topnienia w próżni lub w gazach obojętnych, ZGRZEWANIE NA GORĄCO IZOSTATYCZNE ZGRZEWANIE CIŚNIENIOWE proces, w którym stosujemy ciśnienie za pomocą gazów obojętnych wewnątrz naczynia, ZGRZEWANIE WALCOWE, w którym łączymy odmiennych materiałów, wymuszając je między dwa obrotowe koła, ZGRZEW ULTRADŹWIĘKOWY, gdzie cienkie arkusze metalu lub tworzywa sztucznego są spawane przy użyciu energii wibracyjnej o wysokiej częstotliwości.
Inne nasze procesy spawalnicze to SPAWANIE WIĄZKAMI ELEKTRONICZNYMI z głębokim wtopieniem i szybką obróbką, ale jako metodą kosztowną, uważamy ją za szczególną w szczególnych przypadkach, SPAWANIE ELEKTROŻUŻOWE metodą odpowiednią tylko dla grubych blach i elementów stalowych, SPAWANIE INDUKCYJNE gdzie stosujemy indukcję elektromagnetyczną oraz nagrzewanie naszych elementów przewodzących prąd elektryczny lub ferromagnetycznych, SPAWANIE WIĄZKAMI LASEROWYMI również z głębokim wtopieniem i szybką obróbką, ale kosztowną metodą, SPAWANIE HYBRYDOWE LASEROWE, które łączy LBW z GMAW w tej samej głowicy spawalniczej i jest w stanie wypełnić szczeliny 2 mm między płytami, ZGRZEWANIE PERKUSYJNE, które polega na wyładowaniu elektrycznym, po którym następuje kucie materiałów pod przyłożonym ciśnieniem, ZGRZEWANIE TERMITOWE polegające na reakcji egzotermicznej pomiędzy proszkami aluminium i tlenku żelaza, ZGRZEWANIE ELEKTROGAZOWE z użyciem elektrod topliwych i stosowane wyłącznie ze stali w pozycji pionowej, a na koniec ZGRZEWANIE ŁUKOWE DO ŁĄCZENIA kołka z podstawą materiał z ciepłem i ciśnieniem.
Zalecamy kliknięcie tutaj, abyPOBIERZ nasze schematyczne ilustracje procesów lutowania, lutowania i klejenia opracowane przez AGS-TECH Inc
Pomoże Ci to lepiej zrozumieć informacje, które udostępniamy poniżej.
• LUTOWANIE: Łączymy dwa lub więcej metali przez podgrzewanie spoiw pomiędzy nimi powyżej ich temperatur topnienia i rozprowadzanie metodą kapilarną. Proces jest podobny do lutowania, ale temperatury potrzebne do stopienia wypełniacza są wyższe podczas lutowania. Podobnie jak w przypadku spawania, topnik chroni materiał wypełniający przed zanieczyszczeniami atmosferycznymi. Po schłodzeniu detale są łączone. Proces obejmuje następujące kluczowe etapy: dobre dopasowanie i luz, właściwe czyszczenie materiałów bazowych, właściwe mocowanie, właściwy dobór topnika i atmosfery, podgrzewanie zespołu i wreszcie czyszczenie zespołu lutowanego. Niektóre z naszych procesów lutowania to TORCH BRAZING, popularna metoda wykonywana ręcznie lub w sposób zautomatyzowany. Nadaje się do małych zleceń produkcyjnych i specjalistycznych przypadków. Ciepło jest dostarczane za pomocą płomieni gazowych w pobliżu lutowanego złącza. LUTOWANIE PIECE wymaga mniejszych umiejętności operatora i jest procesem półautomatycznym, nadającym się do masowej produkcji przemysłowej. Zaletą tej techniki jest zarówno kontrola temperatury, jak i atmosfery w piecu, ponieważ ta pierwsza umożliwia nam kontrolowanie cykli cieplnych i eliminację miejscowego nagrzewania, jak ma to miejsce w przypadku lutowania palnikowego, a ta druga chroni część przed utlenianiem. Stosując jigging jesteśmy w stanie zredukować koszty produkcji do minimum. Wadami są wysokie zużycie energii, koszty sprzętu i trudniejsze względy projektowe. LUTOWANIE PRÓŻNIOWE odbywa się w piecu próżniowym. Utrzymuje się równomierność temperatury i uzyskujemy wolne od topników, bardzo czyste połączenia z bardzo małymi naprężeniami szczątkowymi. Obróbka cieplna może odbywać się podczas lutowania próżniowego ze względu na niewielkie naprężenia szczątkowe występujące podczas powolnych cykli ogrzewania i chłodzenia. Główną wadą jest wysoki koszt, ponieważ tworzenie środowiska próżniowego jest procesem kosztownym. Jeszcze inna technika DIP BRAZING łączy mocowane części, w których masa lutownicza jest nakładana na współpracujące powierzchnie. Następnie zamocowane części są zanurzane w kąpieli ze stopionej soli, takiej jak chlorek sodu (sól kuchenna), która działa jako nośnik ciepła i topnik. Powietrze jest wykluczone i dlatego nie dochodzi do tworzenia się tlenków. W LUTOWANIU INDUKCYJNYM łączymy materiały spoiwem o niższej temperaturze topnienia niż materiały bazowe. Prąd przemienny z cewki indukcyjnej wytwarza pole elektromagnetyczne, które indukuje nagrzewanie indukcyjne na przeważnie żelaznych materiałach magnetycznych. Metoda zapewnia selektywne ogrzewanie, dobre połączenia z wypełniaczami płynącymi tylko w pożądanych obszarach, niewielkie utlenianie, ponieważ nie ma płomienia, a chłodzenie jest szybkie, szybkie nagrzewanie, konsystencja i przydatność do produkcji wielkoseryjnej. Aby przyspieszyć nasze procesy i zapewnić spójność, często korzystamy z preform. Informacje na temat naszego zakładu produkującego złączki ceramiczne do metalowych, hermetyczne uszczelnienia, przepusty próżniowe, komponenty do kontroli wysokiego i ultrawysokiego podciśnienia i płynów można znaleźć tutaj: Broszura dotycząca fabryki lutów twardych
• LUTOWANIE : W lutowaniu nie mamy do czynienia z topieniem się elementów obrabianych, ale ze spoiwem o niższej temperaturze topnienia niż części łączące, które wpływają do złącza. Spoiwo w lutowaniu topi się w niższej temperaturze niż w lutowaniu. Do lutowania używamy stopów bezołowiowych i spełniamy wymagania RoHS, a dla różnych zastosowań i wymagań mamy różne i odpowiednie stopy, takie jak stop srebra. Lutowanie oferuje nam złącza, które są gazo i cieczoszczelne. W LUTOWANIU MIĘKKIM nasz lut ma temperaturę topnienia poniżej 400 stopni Celsjusza, podczas gdy w LUTOWANIU SREBRNYM i LUTOWANIU LUTYMOWYM potrzebujemy wyższych temperatur. Lutowanie miękkie wykorzystuje niższe temperatury, ale nie daje mocnych połączeń w wymagających zastosowaniach w podwyższonych temperaturach. Z drugiej strony lutowanie srebrem wymaga wysokich temperatur zapewnianych przez palnik i daje nam mocne połączenia odpowiednie do zastosowań w wysokich temperaturach. Lutowanie wymaga najwyższych temperatur i zwykle używa się palnika. Ponieważ połączenia lutowane są bardzo mocne, są dobrymi kandydatami do naprawy ciężkich przedmiotów żelaznych. W naszych liniach produkcyjnych stosujemy zarówno ręczne lutowanie ręczne, jak i automatyczne linie lutownicze. INDUCTION LUDERING wykorzystuje prąd przemienny wysokiej częstotliwości w cewce miedzianej w celu ułatwienia nagrzewania indukcyjnego. W części lutowanej indukowane są prądy, w wyniku czego na złączu o dużej rezystancji joint generowane jest ciepło. To ciepło topi metal wypełniający. Stosowany jest również topnik. Lutowanie indukcyjne jest dobrą metodą do lutowania cylindrów i rur w procesie ciągłym poprzez owijanie cewek wokół nich. Lutowanie niektórych materiałów, takich jak grafit i ceramika, jest trudniejsze, ponieważ przed lutowaniem wymaga powlekania elementów odpowiednim metalem. Ułatwia to wiązanie międzyfazowe. Lutujemy takie materiały specjalnie do zastosowań w opakowaniach hermetycznych. Nasze płytki drukowane (PCB) produkujemy w dużych ilościach, głównie przy użyciu LUTY WAVE. Tylko dla niewielkich ilości celów prototypowych stosujemy lutowanie ręczne za pomocą lutownicy lutowniczej. Używamy lutowania na fali zarówno do montażu przewlekanego, jak i montażu powierzchniowego PCB (PCBA). Tymczasowy klej utrzymuje komponenty przymocowane do płytki drukowanej, a zespół jest umieszczany na przenośniku i przechodzi przez sprzęt zawierający stopiony lut. Najpierw PCB jest topiony, a następnie wchodzi do strefy podgrzewania. Stopiony lut znajduje się na patelni i ma na swojej powierzchni wzór fal stojących. Kiedy PCB porusza się po tych falach, fale te stykają się z dnem PCB i przyklejają się do pól lutowniczych. Lut pozostaje tylko na pinach i padach, a nie na samej płytce drukowanej. Fale w stopionym lutowiu muszą być dobrze kontrolowane, aby nie było rozpryskiwania, a wierzchołki fal nie dotykały i nie zanieczyszczały niepożądanych obszarów płytek. W lutowaniu rozpływowym używamy lepkiej pasty lutowniczej, aby tymczasowo przymocować elementy elektroniczne do płytek. Następnie deski trafiają do pieca rozpływowego z kontrolą temperatury. Tutaj lut topi się i trwale łączy elementy. Stosujemy tę technikę zarówno w przypadku elementów do montażu powierzchniowego, jak i elementów przewlekanych. Właściwa kontrola temperatury i dostosowanie temperatury piekarnika jest niezbędne, aby uniknąć zniszczenia elementów elektronicznych na płycie poprzez przegrzanie ich powyżej maksymalnych limitów temperatury. W procesie lutowania rozpływowego mamy w rzeczywistości kilka obszarów lub etapów, z których każdy ma odrębny profil termiczny, taki jak etap podgrzewania, etap wygrzewania termicznego, etapy ponownego rozpływu i chłodzenia. Te różne etapy są niezbędne do bezawaryjnego lutowania rozpływowego zespołów obwodów drukowanych (PCBA). LUTOWANIE ULTRADŹWIĘKOWE to kolejna często stosowana technika o wyjątkowych możliwościach – może być stosowana do lutowania materiałów szklanych, ceramicznych i niemetalicznych. Na przykład panele fotowoltaiczne, które są niemetalowe, wymagają elektrod, które można przymocować tą techniką. W lutowaniu ultradźwiękowym stosujemy podgrzewany grot lutowniczy, który również emituje wibracje ultradźwiękowe. Wibracje te wytwarzają pęcherzyki kawitacyjne na styku podłoża ze stopionym materiałem lutowniczym. Implozyjna energia kawitacji modyfikuje powierzchnię tlenku i usuwa brud i tlenki. W tym czasie tworzy się również warstwa stopu. Lut na powierzchni łączenia zawiera tlen i umożliwia tworzenie silnego wspólnego wiązania między szkłem a lutowiem. DIP SOLDERING można uznać za prostszą wersję lutowania na fali, odpowiednią tylko do produkcji na małą skalę. Pierwszy topnik czyszczący nakładany jest podobnie jak w innych procesach. Obwody drukowane z zamontowanymi elementami są zanurzane ręcznie lub w sposób półautomatyczny w zbiorniku zawierającym stopiony lut. Stopiony lut przykleja się do odsłoniętych obszarów metalowych niezabezpieczonych maską lutowniczą na płytce. Sprzęt jest prosty i niedrogi.
• KLEJENIE KLEJEM : Jest to kolejna popularna technika, którą często stosujemy i polega na sklejaniu powierzchni za pomocą klejów, żywic epoksydowych, środków plastycznych lub innych chemikaliów. Klejenie uzyskuje się przez odparowanie rozpuszczalnika, utwardzanie na gorąco, utwardzanie światłem UV, utwardzanie ciśnieniowe lub odczekanie przez pewien czas. W naszych liniach produkcyjnych stosowane są różne kleje o wysokiej wydajności. Przy odpowiednio zaprojektowanych procesach nakładania i utwardzania, łączenie adhezyjne może skutkować bardzo niskimi naprężeniami, które są mocne i niezawodne. Wiązania klejowe mogą być dobrą ochroną przed czynnikami środowiskowymi, takimi jak wilgoć, zanieczyszczenia, korozje, wibracje… itp. Zaletami klejenia są: można je nakładać na materiały, które w innym przypadku byłyby trudne do lutowania, spawania lub lutowania. Może być również preferowane w przypadku materiałów wrażliwych na ciepło, które zostałyby uszkodzone przez spawanie lub inne procesy wysokotemperaturowe. Inne zalety klejów to możliwość ich nakładania na powierzchnie o nieregularnych kształtach i bardzo niewielkie zwiększenie ciężaru montażu w porównaniu z innymi metodami. Również zmiany wymiarowe części są bardzo minimalne. Niektóre kleje mają właściwości dopasowania indeksu i mogą być stosowane pomiędzy elementami optycznymi bez znacznego zmniejszania siły światła lub sygnału optycznego. Z drugiej strony wadami są dłuższe czasy utwardzania, które mogą spowolnić linie produkcyjne, wymagania dotyczące mocowania, wymagania dotyczące przygotowania powierzchni i trudności z demontażem, gdy konieczna jest przeróbka. Większość naszych operacji klejenia obejmuje następujące etapy:
-Obróbka powierzchni: Powszechne są specjalne procedury czyszczenia, takie jak czyszczenie wodą dejonizowaną, czyszczenie alkoholem, czyszczenie plazmowe lub koronowe. Po oczyszczeniu możemy nanieść na powierzchnie promotory przyczepności, aby zapewnić jak najlepsze połączenia.
- Mocowanie części: zarówno do aplikacji kleju, jak i do utwardzania projektujemy i stosujemy niestandardowe mocowania.
-Nakładanie kleju: Czasami używamy ręcznych, a czasami, w zależności od przypadku, zautomatyzowanych systemów, takich jak robotyka, serwomotory, siłowniki liniowe w celu dostarczenia kleju we właściwe miejsce i używamy dozowników, aby dostarczyć go w odpowiedniej objętości i ilości.
-Utwardzanie: W zależności od kleju możemy zastosować proste suszenie i utwardzanie, a także utwardzanie pod lampami UV, które działają jako katalizator lub utwardzanie na gorąco w piecu lub przy użyciu oporowych elementów grzejnych montowanych na przyrządach i uchwytach.
Zalecamy kliknięcie tutaj, abyPOBIERZ nasze schematyczne ilustracje procesów mocowania autorstwa AGS-TECH Inc.
Pomoże Ci to lepiej zrozumieć informacje, które udostępniamy poniżej.
• PROCESY ŁĄCZENIA: Nasze procesy łączenia mechanicznego dzielą się na dwie kategorie: MOCOWANIA i POŁĄCZENIA INTEGRALNE. Przykładami stosowanych przez nas elementów złącznych są śruby, kołki, nakrętki, śruby, nity. Przykładami stosowanych przez nas połączeń integralnych są połączenia zatrzaskowe i skurczowe, szwy, zaciski. Stosując różnorodne metody mocowania zapewniamy, że nasze połączenia mechaniczne są mocne i niezawodne przez wiele lat użytkowania. ŚRUBY i ŚRUBY to jedne z najczęściej używanych elementów złącznych do trzymania przedmiotów razem i pozycjonowania. Nasze śruby i wkręty spełniają normy ASME. Stosowane są różne rodzaje śrub i śrub, w tym śruby z łbem sześciokątnym i śruby z łbem sześciokątnym, śruby i śruby do drewna, śruba dwustronna, śruba kołkowa, śruba oczkowa, śruba lustrzana, śruba do blachy, śruba do precyzyjnej regulacji, śruby samowiercące i samogwintujące , wkręt dociskowy, wkręty z wbudowanymi podkładkami,… i nie tylko. Posiadamy różne typy łbów śrub, takie jak łeb stożkowy, kopułkowy, okrągły, kołnierzowy oraz różne typy napędów śrubowych, takie jak rowek, krzyżakowy, kwadratowy, sześciokątny. Z drugiej strony RIVET jest trwałym łącznikiem mechanicznym składającym się z gładkiego cylindrycznego wału i łba z jednej strony. Po włożeniu drugi koniec nitu ulega deformacji, a jego średnica jest rozszerzana tak, aby pozostał na swoim miejscu. Innymi słowy, przed montażem nit ma jeden łeb, a po montażu dwa. Montujemy różne rodzaje nitów w zależności od zastosowania, wytrzymałości, dostępności i kosztu, takie jak nity z łbem pełnym/okrągłym, konstrukcyjne, półrurowe, zrywalne, oscarowe, wbijane, wpuszczane, samozaciskowe, samowtłaczające. Nitowanie może być preferowane w przypadkach, w których należy unikać odkształceń termicznych i zmian właściwości materiału spowodowanych ciepłem spawania. Nitowanie zapewnia również niewielką wagę oraz szczególnie dobrą wytrzymałość i odporność na siły ścinające. Jednak w przypadku obciążeń rozciągających bardziej odpowiednie mogą być śruby, nakrętki i śruby. W procesie CLINCHING wykorzystujemy specjalne stemple i matryce, które tworzą mechaniczną blokadę pomiędzy łączonymi blachami. Stempel wpycha warstwy blachy do wnęki matrycy i powoduje powstanie trwałego połączenia. W klinczowaniu nie jest wymagane ogrzewanie ani chłodzenie i jest to proces obróbki na zimno. Jest to ekonomiczny proces, który w niektórych przypadkach może zastąpić zgrzewanie punktowe. W PINNING wykorzystujemy kołki, które są elementami maszyn służącymi do zabezpieczenia położenia części maszyny względem siebie. Główne typy to zawleczki, zawleczki, zawleczki, zawleczki, i zawleczka. W ZSZYWANIU używamy zszywaczy i zszywek, które są dwuzębnymi łącznikami służącymi do łączenia lub wiązania materiałów. Zszywanie ma następujące zalety: ekonomiczne, proste i szybkie w użyciu, korona zszywek może być używana do łączenia materiałów połączonych ze sobą, korona zszywki może ułatwić połączenie elementu jak kabel i przymocowanie go do powierzchni bez przebijania lub szkodliwe, stosunkowo łatwe usuwanie. ZŁĄCZANIE ZACISKOWE odbywa się poprzez dociskanie części do siebie, a tarcie między nimi mocuje części. Części pasowane wtłaczane składające się z nadwymiarowego wałka i podwymiarowego otworu są zazwyczaj montowane jedną z dwóch metod: albo poprzez przyłożenie siły, albo wykorzystanie rozszerzalności lub kurczenia się części pod wpływem temperatury. Gdy złączka zaciskowa jest ustalana przez przyłożenie siły, używamy prasy hydraulicznej lub prasy ręcznej. Z drugiej strony, gdy pasowanie wtłaczane jest ustalane przez rozszerzalność cieplną, podgrzewamy części otaczające i montujemy je na swoje miejsce na gorąco. Kiedy ostygną, kurczą się i wracają do swoich normalnych wymiarów. Daje to dobre pasowanie wtłaczane. Nazywamy to alternatywnie DOPASOWANIEM KURCZLIWYM. Innym sposobem na zrobienie tego jest schłodzenie owiniętych części przed montażem, a następnie wsunięcie ich w ich współpracujące części. Gdy montaż się rozgrzeje, rozszerzają się i uzyskujemy ciasne dopasowanie. Ta ostatnia metoda może być preferowana w przypadkach, gdy ogrzewanie stwarza ryzyko zmiany właściwości materiału. W takich przypadkach chłodzenie jest bezpieczniejsze.
Podzespoły i zespoły pneumatyczne i hydrauliczne
• Zawory, elementy hydrauliczne i pneumatyczne takie jak O-ring, podkładka, uszczelki, uszczelka, pierścień, podkładka.
Ponieważ zawory i elementy pneumatyczne są bardzo różnorodne, nie możemy tutaj wszystkiego wymienić. W zależności od środowiska fizycznego i chemicznego Twojej aplikacji mamy dla Ciebie specjalne produkty. Proszę podać nam zastosowanie, rodzaj komponentu, specyfikacje, warunki środowiskowe, takie jak ciśnienie, temperatura, ciecze lub gazy, które będą miały kontakt z Państwa zaworami i komponentami pneumatycznymi; a my dobierzemy dla Ciebie najbardziej odpowiedni produkt lub wyprodukujemy go specjalnie do Twojego zastosowania.