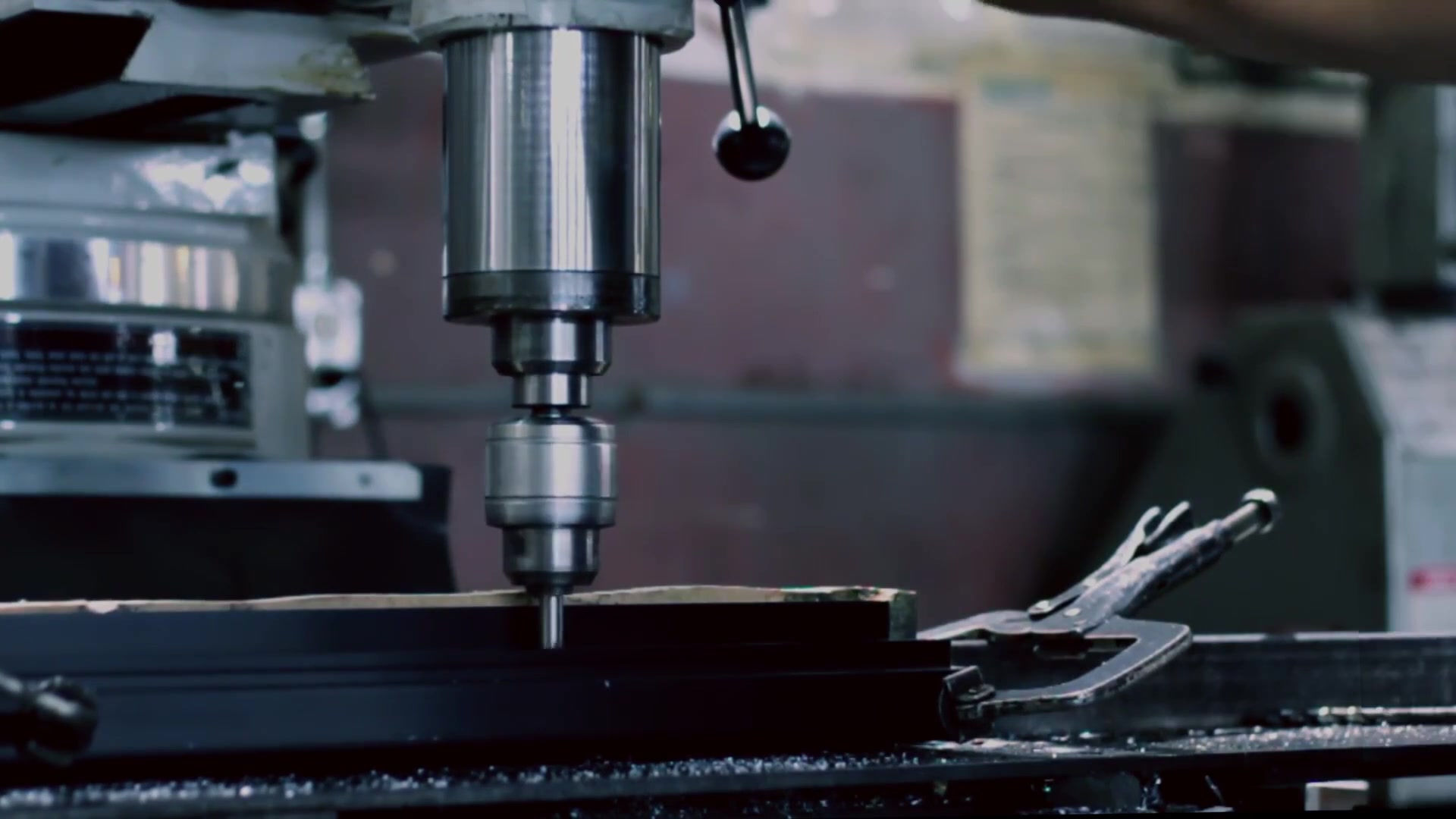
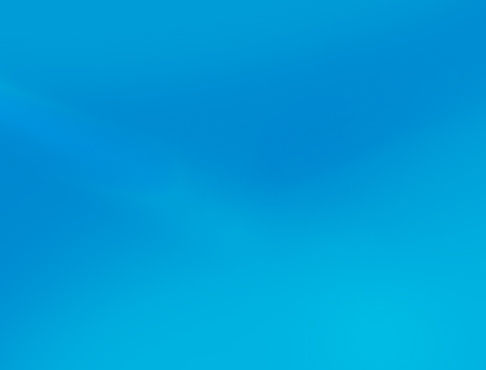
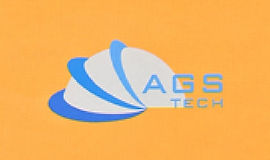
Producător global personalizat, integrator, consolidator, partener de outsourcing pentru o gamă largă de produse și servicii.
Suntem sursa dvs. unică pentru producția, fabricarea, inginerie, consolidare, integrare, externalizare a produselor și serviciilor fabricate la comandă și de pe raft.
Choose your Language
-
Fabricare la comandă
-
Producție pe bază de contract intern și global
-
Externalizarea producției
-
Achiziții interne și globale
-
Consolidation
-
Integrare inginerie
-
Servicii de inginerie
Tipurile de producție de sticlă pe care le oferim sunt sticlă pentru containere, sticlă suflată, fibră de sticlă și tuburi și tijă, sticlă casnică și industrială, lămpi și becuri, turnare de precizie din sticlă, componente și ansambluri optice, sticlă plată și tablă și float. Executăm atât modelarea manuală, cât și modelarea la mașină.
Procesele noastre populare de fabricare a ceramicii tehnice sunt presarea cu matriță, presarea izostatică, presarea izostatică la cald, presarea la cald, turnarea cu alunecare, turnarea cu bandă, extrudarea, turnarea prin injecție, prelucrarea verde, sinterizarea sau arderea, șlefuirea cu diamant, ansamblurile ermetice.
Vă recomandăm să faceți clic aici pentru
DESCARCĂ Ilustrațiile noastre schematice ale proceselor de formare și modelare a sticlei de la AGS-TECH Inc.
Aceste fișiere descărcabile cu fotografii și schițe vă vor ajuta să înțelegeți mai bine informațiile pe care vi le oferim mai jos.
• FABRICAȚIE DE STICLĂ DE RECIPIENTĂ: Avem linii automate de PRESARE ȘI SUFLARE, precum și linii de suflare și suflare pentru producție. În procesul de suflare și suflare aruncăm o gură în matriță goală și formăm gâtul aplicând o lovitură de aer comprimat de sus. Imediat după aceasta, aer comprimat este suflat a doua oară din cealaltă direcție prin gâtul recipientului pentru a forma preforma sticlei. Această preformă este apoi transferată în matrița propriu-zisă, reîncălzită pentru a se înmuia și se aplică aer comprimat pentru a da preformei forma finală a recipientului. Mai explicit, este presurizat și împins pe pereții cavității matriței de suflare pentru a lua forma dorită. În cele din urmă, recipientul din sticlă fabricat este transferat într-un cuptor de recoacere pentru reîncălzirea ulterioară și îndepărtarea tensiunilor produse în timpul turnării și este răcit într-un mod controlat. În metoda prin presare și suflare, bucățile topite sunt introduse într-o matriță paraison (forma semifabricată) și presate în forma paraison (forma semifabricată). Semifabricatele sunt apoi transferate în matrițe de suflare și suflate similar cu procesul descris mai sus în „Procesul de suflare și suflare”. Etapele ulterioare, cum ar fi recoacerea și eliberarea tensiunii, sunt similare sau la fel.
• SUFLARE STICLĂ: Producem produse din sticlă folosind suflarea manuală convențională, precum și aer comprimat cu echipamente automate. Pentru unele comenzi este necesară suflarea convențională, cum ar fi proiectele care implică lucrări de artă pe sticlă sau proiecte care necesită un număr mai mic de piese cu toleranțe slabe, proiecte de prototipare/demo….etc. Suflarea convențională a sticlei implică scufundarea unei țevi metalice goale într-un vas de sticlă topită și rotirea țevii pentru colectarea unei cantități de material din sticlă. Sticla colectată pe vârful țevii este rulată pe fier plat, modelată după dorință, alungită, reîncălzită și suflată cu aer. Când este gata, se introduce într-o matriță și se sufla aer. Cavitatea matriței este umedă pentru a evita contactul sticlei cu metalul. Pelicula de apă acționează ca o pernă între ele. Suflarea manuală este un proces lent care necesită multă muncă și este potrivit doar pentru prototipare sau articole de mare valoare, nu este potrivit pentru comenzi de volum mare ieftine pe bucată.
• PRODUCEREA DE STICLURII DOMESTICE ȘI INDUSTRIALE: Folosind diferite tipuri de materiale din sticlă se produce o mare varietate de articole din sticlă. Unele pahare sunt rezistente la căldură și sunt potrivite pentru sticlăria de laborator, în timp ce unele sunt suficient de bune pentru a rezista la mașinile de spălat vase de mai multe ori și sunt potrivite pentru fabricarea produselor casnice. Utilizând aparatele Westlake, se produc zeci de mii de bucăți de pahare pe zi. Pentru a simplifica, sticla topită este colectată prin vid și introdusă în matrițe pentru a face preformele. Apoi aerul este suflat în matrițe, acestea sunt transferate într-o altă matriță și aerul este suflat din nou și sticla capătă forma finală. Ca și în suflarea manuală, aceste matrițe sunt ținute umede cu apă. Întinderea ulterioară face parte din operația de finisare în care se formează gâtul. Excesul de sticlă este ars. După aceea, urmează procesul controlat de reîncălzire și răcire descris mai sus.
• FORMAREA TUBILOR DE STICLĂ ȘI TIGELOR: Principalele procese pe care le folosim pentru fabricarea tuburilor de sticlă sunt procesele DANNER și VELLO. În procesul Danner, sticla dintr-un cuptor curge și cade pe un manșon înclinat din materiale refractare. Manșonul este transportat pe un arbore tubular rotativ sau suflantă. Sticla este apoi înfășurată în jurul manșonului și formează un strat neted care curge în jos pe manșon și peste vârful tijei. În cazul formării tuburilor, aerul este suflat printr-o suflantă cu vârf gol, iar în cazul formării tijei folosim vârfuri solide pe arbore. Tuburile sau tijele sunt apoi trase peste role de transport. Dimensiunile precum grosimea peretelui și diametrul tuburilor de sticlă sunt ajustate la valorile dorite prin setarea diametrului manșonului și suflarea presiunii aerului la o valoare dorită, ajustând temperatura, viteza de curgere a sticlei și viteza de tragere. Procesul de fabricare a tubului de sticlă Vello, pe de altă parte, implică sticlă care se deplasează dintr-un cuptor și într-un vas cu un dorn sau un clopot gol. Sticla trece apoi prin spațiul de aer dintre dorn și bol și ia forma unui tub. După aceea, se deplasează peste role la o mașină de desenat și este răcită. La sfârșitul liniei de răcire are loc tăierea și prelucrarea finală. Dimensiunile tubului pot fi ajustate la fel ca în procesul Danner. Când comparăm procesul Danner cu procesul Vello, putem spune că procesul Vello se potrivește mai bine pentru producția în cantități mari, în timp ce procesul Danner poate fi mai potrivit pentru comenzi precise de tuburi de volum mai mic.
• PRELUCRARE PLĂCI ȘI STICLĂ PLATĂ și FLOTĂ: Avem cantități mari de sticlă plată în grosimi variind de la grosimi submilimetrice până la câțiva centimetri. Ochelarii noștri plati sunt aproape de perfecțiune optică. Oferim sticlă cu acoperiri speciale, cum ar fi acoperiri optice, în care tehnica de depunere chimică a vaporilor este utilizată pentru a pune acoperiri precum acoperirea antireflex sau oglindă. De asemenea, sunt comune acoperirile conductoare transparente. De asemenea, sunt disponibile acoperiri hidrofobe sau hidrofile pe sticlă și acoperiri care fac sticla auto-curățată. Ochelarii căliți, antiglonț și laminati sunt încă alte articole populare. Tăiem sticla în forma dorită cu toleranțele dorite. Sunt disponibile și alte operațiuni secundare, cum ar fi curbarea sau îndoirea sticlei plane.
• MULTARE DE PRECIZIE A STICLEI: Folosim aceasta tehnica mai ales pentru fabricarea componentelor optice de precizie, fara a fi nevoie de tehnici mai costisitoare si consumatoare de timp, cum ar fi slefuirea, slefuirea si lustruirea. Această tehnică nu este întotdeauna suficientă pentru a obține cele mai bune optice, dar în unele cazuri, cum ar fi produsele de larg consum, camerele digitale, optica medicală, poate fi o opțiune bună mai puțin costisitoare pentru producția de volum mare. De asemenea, are un avantaj față de celelalte tehnici de formare a sticlei în care sunt necesare geometrii complexe, cum ar fi în cazul asferelor. Procesul de bază presupune încărcarea părții inferioare a matriței noastre cu semifabricatul de sticlă, evacuarea camerei de proces pentru îndepărtarea oxigenului, aproape închiderea matriței, încălzirea rapidă și izotermă a matriței și a sticlei cu lumină infraroșie, închiderea ulterioară a jumătăților de matriță. se presează încet sticla înmuiată, într-un mod controlat, până la grosimea dorită și, în final, se răcește sticla și se umple camera cu azot și se îndepărtează produsul. Controlul precis al temperaturii, distanța de închidere a matriței, forța de închidere a matriței, potrivirea coeficienților de expansiune a matriței și a materialului din sticlă sunt cheia în acest proces.
• FABRICAREA COMPONENTELOR ȘI ASAMBLELOR OPTICE STICLĂ: Pe lângă turnarea de precizie a sticlei, există o serie de procese valoroase pe care le folosim pentru a realiza componente și ansambluri optice de înaltă calitate pentru aplicații solicitante. Slefuirea, șlefuirea și lustruirea sticlelor de calitate optică în șlamuri abrazive speciale fine este o artă și o știință pentru realizarea de lentile optice, prisme, plate și multe altele. Planeitatea suprafeței, ondularea, netezimea și suprafețele optice fără defecte necesită multă experiență în astfel de procese. Micile modificări ale mediului pot duce la produse care nu corespund specificațiilor și pot opri linia de producție. Există cazuri în care o singură ștergere pe suprafața optică cu o cârpă curată poate face ca un produs să îndeplinească specificațiile sau să eșueze testul. Unele materiale populare din sticlă utilizate sunt silice topită, cuarț, BK7. De asemenea, asamblarea unor astfel de componente necesită experiență de nișă specializată. Uneori se folosesc cleiuri speciale. Cu toate acestea, uneori, o tehnică numită contact optic este cea mai bună alegere și nu implică niciun material între ochelarii optici atașați. Constă în contactul fizic cu suprafețe plane pentru a se atașa între ele fără adeziv. În unele cazuri, distanțiere mecanice, tije sau bile de sticlă de precizie, cleme sau componente metalice prelucrate sunt folosite pentru a asambla componentele optice la anumite distanțe și cu anumite orientări geometrice unele față de altele. Să examinăm câteva dintre tehnicile noastre populare pentru fabricarea opticii de înaltă calitate.
Șlefuire, șlefuire și lustruire: Forma brută a componentei optice este obținută prin șlefuirea unui semifabricat de sticlă. După aceea, șlefuirea și lustruirea sunt efectuate prin rotirea și frecarea suprafețelor aspre ale componentelor optice de unelte cu formele de suprafață dorite. Suspensii cu particule abrazive minuscule și fluide sunt turnate între optică și instrumentele de modelare. Dimensiunile particulelor abrazive din astfel de suspensii pot fi alese în funcție de gradul de planeitate dorit. Abaterile suprafețelor optice critice de la formele dorite sunt exprimate în termeni de lungimi de undă ale luminii utilizate. Optica noastră de înaltă precizie are toleranțe ale unei zecimi de lungime de undă (lungime de undă/10) sau chiar mai strâns este posibil. Pe lângă profilul suprafeței, suprafețele critice sunt scanate și evaluate pentru alte caracteristici și defecte ale suprafeței, cum ar fi dimensiuni, zgârieturi, așchii, gropi, pete... etc. Controlul strict al condițiilor de mediu în producția optică și cerințele extinse de metrologie și testare cu echipamente de ultimă generație fac din aceasta o ramură provocatoare a industriei.
• PROCESE SECUNDARE ÎN FABRICAREA STICLEI: Din nou, suntem limitați doar cu imaginația dumneavoastră atunci când vine vorba de procesele secundare și de finisare ale sticlei. Iată câteva dintre ele:
-Acoperiri pe sticla (optice, electrice, tribologice, termice, functionale, mecanice...). De exemplu, putem modifica proprietățile suprafeței sticlei făcându-l, de exemplu, să reflecte căldura, astfel încât să mențină răcoare interioarele clădirii, sau să facem ca o parte să absoarbă infraroșu folosind nanotehnologia. Acest lucru ajută la menținerea caldă a interiorului clădirilor, deoarece stratul exterior de sticlă va absorbi radiația infraroșie din interiorul clădirii și o va radia înapoi în interior.
-Gravare pe sticla
-Etichetare ceramică aplicată (ACL)
-Gravare
-Lustruire cu flacără
-Lustruire chimica
-Patarea
FABRICAREA CERAMICII TEHNICE
• PRESARE CU STILĂ: Constă în compactarea uniaxială a pulberilor granulare limitate într-o matriță
• PRESARE LA CALDE: Similar cu presarea cu matriță, dar cu adăugare de temperatură pentru a îmbunătăți densificarea. Pulberea sau preforma compactată este plasată în matriță de grafit și se aplică presiune uniaxială în timp ce matrița este menținută la temperaturi ridicate, cum ar fi 2000 C. Temperaturile pot fi diferite în funcție de tipul de pulbere ceramică care este prelucrată. Pentru forme și geometrii complicate pot fi necesare alte procesări ulterioare, cum ar fi șlefuirea cu diamant.
• PRESARE ISOSTATICĂ: Pulbere granulară sau compacte presate cu matriță sunt plasate în recipiente etanșe și apoi într-un vas sub presiune închis, cu lichid în interior. După aceea, acestea sunt compactate prin creșterea presiunii vasului sub presiune. Lichidul din interiorul vasului transferă forțele de presiune în mod uniform pe întreaga suprafață a recipientului etanș. Materialul este astfel compactat uniform și ia forma recipientului său flexibil și profilul și caracteristicile sale interne.
• PRESARE ISOSTATICĂ LA CALDE: Similar cu presarea izostatică, dar pe lângă atmosfera de gaz sub presiune, sinterăm compactul la temperatură ridicată. Presarea izostatică la cald are ca rezultat o densificare suplimentară și o rezistență crescută.
• turnare cu alunecare / turnare cu scurgere: umplem matrița cu o suspensie de particule ceramice de dimensiuni micrometrice și lichid purtător. Acest amestec se numește „alunecare”. Forma are pori și, prin urmare, lichidul din amestec este filtrat în matriță. Ca rezultat, se formează o turnare pe suprafețele interioare ale matriței. După sinterizare, piesele pot fi scoase din matriță.
• TURNAREA BANDELOR: Producem benzi ceramice prin turnarea suspensiilor ceramice pe suprafete plane mobile. Suspensiile conțin pulberi ceramice amestecate cu alte substanțe chimice pentru legare și transport. Pe măsură ce solvenții se evaporă, se lasă în urmă foi dense și flexibile de ceramică care pot fi tăiate sau rulate după cum se dorește.
• FORMARE prin extrudare: Ca și în alte procese de extrudare, un amestec moale de pulbere ceramică cu lianți și alte substanțe chimice este trecut printr-o matriță pentru a dobândi forma în secțiune transversală și apoi este tăiat la lungimile dorite. Procesul se realizează cu amestecuri ceramice reci sau încălzite.
• MULTARE CU INJECȚIE LA PRESIUNE JUSĂ: Pregătim un amestec de pulbere ceramică cu lianți și solvenți și îl încălzim la o temperatură în care poate fi ușor presat și forțat în cavitatea sculei. Odată ce ciclul de turnare este complet, piesa este ejectată și substanța chimică de legare este arsă. Utilizând turnarea prin injecție, putem obține piese complicate la volume mari din punct de vedere economic. Sunt posibile găuri care sunt o mică fracțiune de milimetru pe un perete de 10 mm grosime, sunt posibile filete fără prelucrare ulterioară, toleranțe cât de strânse de +/- 0,5% sunt posibile și chiar mai mici atunci când piesele sunt prelucrate. , sunt posibile grosimi de perete de ordinul de la 0,5 mm la o lungime de 12,5 mm, precum și grosimi de perete de la 6,5 mm la o lungime de 150 mm.
• PRELUCRARE VERDE: Folosind aceleași scule de prelucrare a metalelor, putem prelucra materiale ceramice presate cât timp sunt încă moi ca creta. Sunt posibile toleranțe de +/- 1%. Pentru toleranțe mai bune folosim șlefuirea cu diamant.
• SINTERIZAREA sau ARDEREA: Sinterizarea face posibilă densificarea completă. Pe piesele compacte verzi apare o contracție semnificativă, dar aceasta nu este o problemă mare, deoarece luăm în considerare aceste modificări dimensionale atunci când proiectăm piesa și sculele. Particulele de pulbere sunt legate între ele și porozitatea indusă de procesul de compactare este îndepărtată în mare măsură.
• Șlefuirea cu diamante: Cel mai dur material „diamant” din lume este folosit pentru șlefuirea materialelor dure precum ceramica și se obțin piese de precizie. Se realizează toleranțe în intervalul micrometric și suprafețe foarte netede. Datorită costului ei, luăm în considerare această tehnică doar atunci când avem cu adevărat nevoie de ea.
• ANSAMBLE ERMETICE sunt cele care practic nu permit nici un schimb de materie, solide, lichide sau gaze intre interfete. Etanșarea ermetică este etanșă. De exemplu, carcasele electronice ermetice sunt cele care păstrează conținutul interior sensibil al unui dispozitiv ambalat nevătămat de umiditate, contaminanți sau gaze. Nimic nu este 100% ermetic, dar atunci când vorbim de ermeticitate ne referim la faptul că în termeni practici, că există ermeticitate în măsura în care rata de scurgere este atât de scăzută încât dispozitivele sunt sigure în condiții normale de mediu timp foarte lung. Ansamblurile noastre ermetice constau din componente metalice, sticla si ceramica, metal-ceramica, ceramica-metal-ceramica, metal-ceramica-metal, metal pe metal, metal-sticlă, metal-sticlă-metal, sticlă-metal-sticlă, sticlă- metal și sticlă la sticlă și toate celelalte combinații de lipire metal-sticlă-ceramică. De exemplu, putem acoperi componentele ceramice cu metal, astfel încât acestea să poată fi lipite puternic de alte componente ale ansamblului și să aibă o capacitate excelentă de etanșare. Avem cunoștințele de a acoperi fibrele optice sau traversele cu metal și de a le lipi sau lipi pe carcase, astfel încât să nu treacă sau să nu se scurgă gaze în carcase. Prin urmare, ele sunt utilizate pentru fabricarea carcasei electronice pentru a încapsula dispozitive sensibile și pentru a le proteja de atmosfera exterioară. Pe langa caracteristicile lor excelente de etansare, alte proprietati precum coeficientul de dilatare termica, rezistenta la deformare, natura fara gazare, durata de viata foarte lunga, natura neconductiva, proprietati de izolare termica, natura antistatica...etc. face din materialele din sticlă și ceramică alegerea pentru anumite aplicații. Informații despre unitatea noastră de producție de fitinguri ceramice până la metal, etanșare ermetică, treceri de vid, vid înalt și ultraînalt și componente de control al fluidelor pot fi găsite aici:Broșura fabricii de componente ermetice