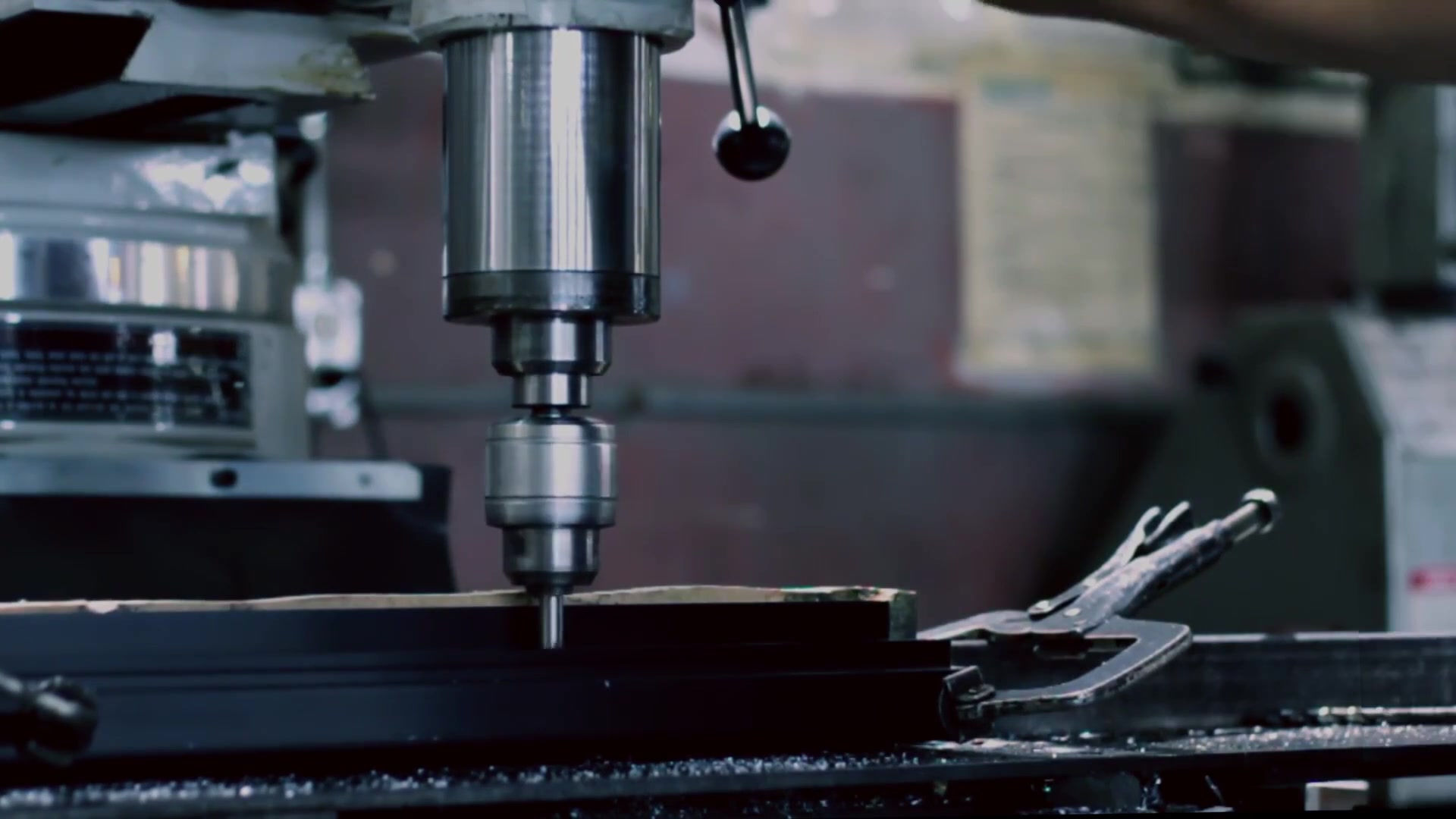
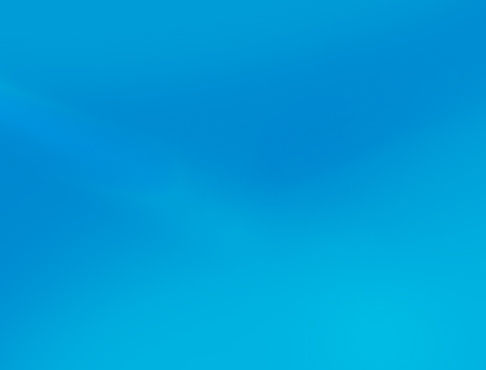
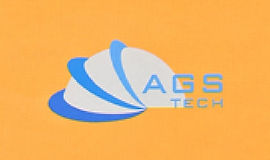
Producător global personalizat, integrator, consolidator, partener de outsourcing pentru o gamă largă de produse și servicii.
Suntem sursa dvs. unică pentru producția, fabricarea, inginerie, consolidare, integrare, externalizare a produselor și serviciilor fabricate la comandă și de pe raft.
Choose your Language
-
Fabricare la comandă
-
Producție pe bază de contract intern și global
-
Externalizarea producției
-
Achiziții interne și globale
-
Consolidation
-
Integrare inginerie
-
Servicii de inginerie
Îmbinăm, asamblam și fixăm piesele dumneavoastră fabricate și le transformăm în produse finite sau semifabricate folosind SUDARE, BRAZARE, LIPIERE, SINTERIZARE, LIERE ADEZIVĂ, FIXARE, MONTARE PRESĂ. Unele dintre cele mai populare procese de sudare ale noastre sunt arc, gaz oxicombustibil, rezistență, proiecție, cusătură, supărare, percuție, stare solidă, fascicul de electroni, laser, termit, sudare prin inducție. Procesele noastre populare de lipire sunt pistolul, inducția, cuptorul și lipirea prin scufundare. Metodele noastre de lipit sunt fierul, plita fierbinte, cuptorul, inducția, scufundarea, unda, reflow și lipirea cu ultrasunete. Pentru lipirea cu adeziv folosim frecvent materiale termoplastice și termostabilizate, epoxidici, fenolici, poliuretan, aliaje adezive, precum și alte substanțe chimice și benzi. În cele din urmă, procesele noastre de fixare constau în cuie, înșurubare, piulițe și șuruburi, nituire, strângere, prindere, cusătură și capsare și montare prin presare.
• SUDARE: Sudarea implică îmbinarea materialelor prin topirea pieselor de prelucrat și introducerea de materiale de umplutură, care se îmbină și la bazinul de sudură topit. Când zona se răcește, obținem o îmbinare puternică. În unele cazuri se aplică presiune. Spre deosebire de sudare, operațiunile de lipire și lipire implică doar topirea unui material cu punct de topire mai mic între piesele de prelucrat, iar piesele de prelucrat nu se topesc. Vă recomandăm să faceți clic aici pentruDESCARCĂ Ilustrațiile noastre schematice ale proceselor de sudare de la AGS-TECH Inc.
Acest lucru vă va ajuta să înțelegeți mai bine informațiile pe care vi le oferim mai jos.
În SUDAREA ARC, folosim o sursă de alimentare și un electrod pentru a crea un arc electric care topește metalele. Punctul de sudare este protejat de un gaz de protecție sau vapori sau alt material. Acest proces este popular pentru sudarea pieselor auto și a structurilor din oțel. În sudarea cu arc metalic acoperit (SMAW) sau cunoscută și sub denumirea de sudare cu stick, un stick de electrod este adus aproape de materialul de bază și se generează un arc electric între ele. Tija electrodului se topește și acționează ca material de umplutură. Electrodul conține, de asemenea, flux care acționează ca un strat de zgură și emite vapori care acționează ca gaz de protecție. Acestea protejează zona de sudură de contaminarea mediului. Nu se folosesc alte materiale de umplutură. Dezavantajele acestui proces sunt încetineala, necesitatea înlocuirii frecvente a electrozilor, nevoia de a ciobi zgura reziduală provenită din flux. Un număr de metale precum fier, oțel, nichel, aluminiu, cupru etc. Poate fi sudat. Avantajele sale sunt instrumentele sale ieftine și ușurința în utilizare. Sudarea cu arc metalic cu gaz (GMAW), cunoscută și sub denumirea de gaz metal-inert (MIG), avem alimentare continuă cu un umplutură de sârmă cu electrod consumabil și un gaz inert sau parțial inert care curge în jurul firului împotriva contaminării mediului înconjurător a regiunii de sudare. Oțelul, aluminiul și alte metale neferoase pot fi sudate. Avantajele MIG sunt viteze mari de sudare și calitate bună. Dezavantajele sunt echipamentele sale complicate și provocările cu care se confruntă în mediile exterioare cu vânt, deoarece trebuie să menținem stabil gazul de protecție din jurul zonei de sudare. O variație a GMAW este sudarea cu arc cu miez de flux (FCAW) care constă dintr-un tub de metal fin umplut cu materiale de flux. Uneori, fluxul din interiorul tubului este suficient pentru a proteja împotriva contaminării mediului. Sudarea cu arc submers (SAW) este un proces automatizat, care implică alimentarea continuă a firului și arcul care este lovit sub un strat de acoperire de flux. Ratele de producție și calitatea sunt ridicate, zgura de sudură se desprinde ușor și avem un mediu de lucru fără fum. Dezavantajul este că poate fi folosit doar pentru a suda parts în anumite poziții. În sudarea cu arc de tungsten cu gaz (GTAW) sau sudarea cu gaz tungsten-inert (TIG) folosim un electrod de tungsten împreună cu o umplutură separată și gaze inerte sau aproape inerte. După cum știm, tungstenul are un punct de topire ridicat și este un metal foarte potrivit pentru temperaturi foarte ridicate. Tungstenul din TIG nu se consumă spre deosebire de celelalte metode explicate mai sus. O tehnică de sudare lentă, dar de înaltă calitate, avantajoasă față de alte tehnici de sudare a materialelor subțiri. Potrivit pentru multe metale. Sudarea cu arc cu plasmă este similară, dar utilizează gaz cu plasmă pentru a crea arcul. Arcul în sudarea cu arc cu plasmă este relativ mai concentrat în comparație cu GTAW și poate fi utilizat pentru o gamă mai largă de grosimi de metal la viteze mult mai mari. Sudarea cu arc GTAW și cu plasmă poate fi aplicată mai mult sau mai puțin pe aceleași materiale.
SUDAREA OXY-FUEL / OXYFUEL numită și sudare oxiacetilenă, sudarea oxi, sudarea cu gaz se realizează folosind combustibili gazosi și oxigen pentru sudare. Deoarece nu se utilizează energie electrică, este portabil și poate fi folosit acolo unde nu există energie electrică. Folosind o pistoletă de sudură încălzim piesele și materialul de umplutură pentru a produce un bazin de metal topit comun. Pot fi utilizați diferiți combustibili, cum ar fi acetilena, benzina, hidrogenul, propanul, butanul etc. În sudarea oxi-combustibil folosim două recipiente, unul pentru combustibil și celălalt pentru oxigen. Oxigenul oxidează combustibilul (îl arde).
SUDARE CU REZISTENTA: Acest tip de sudare profita de incalzirea in joule si caldura este generata in locul in care se aplica curentul electric pentru un anumit timp. Curenții mari trec prin metal. În această locație se formează bazine de metal topit. Metodele de sudare prin rezistență sunt populare datorită eficienței lor, potențialului mic de poluare. Cu toate acestea, dezavantajele sunt costurile echipamentelor relativ semnificative și limitarea inerentă la piesele de lucru relativ subțiri. SUDAREA PUNTURILOR este un tip major de sudare prin rezistență. Aici unim două sau mai multe foi suprapuse sau piese de lucru folosind doi electrozi de cupru pentru a fixa foile împreună și a trece un curent mare prin ele. Materialul dintre electrozii de cupru se încălzește și se generează un bazin topit în acea locație. Curentul este apoi oprit, iar vârfurile electrodului de cupru răcesc locul sudării, deoarece electrozii sunt răciți cu apă. Aplicarea cantității potrivite de căldură pe materialul și grosimea potrivite este cheia pentru această tehnică, deoarece dacă este aplicată greșit îmbinarea va fi slabă. Sudarea prin puncte are avantajele că nu provoacă deformare semnificativă a pieselor de prelucrat, eficiență energetică, ușurință de automatizare și rate de producție remarcabile și nu necesită umpluturi. Dezavantajul este că, deoarece sudarea are loc mai degrabă în puncte decât să formeze o cusătură continuă, rezistența totală poate fi relativ mai mică în comparație cu alte metode de sudare. SUDAREA CUSATURĂ, pe de altă parte, produce suduri la suprafețele de contact ale materialelor similare. Cusătura poate fi cap la cap sau îmbinare suprapusă. Sudarea cusăturii începe de la un capăt și trece progresiv la celălalt. Această metodă folosește și doi electrozi din cupru pentru a aplica presiune și curent în regiunea de sudare. Electrozii în formă de disc se rotesc cu contact constant de-a lungul liniei de cusătură și realizează o sudură continuă. Și aici, electrozii sunt răciți cu apă. Sudurile sunt foarte puternice și fiabile. Alte metode sunt tehnicile de sudură prin proiecție, flash și sudură.
SUDAREA în stare solidă este puțin diferită de metodele anterioare explicate mai sus. Coalescența are loc la temperaturi sub temperatura de topire a metalelor îmbinate și fără utilizarea umpluturii metalice. Presiunea poate fi utilizată în unele procese. Diverse metode sunt SUDAREA COEXTRUZIUNE în care metalele diferite sunt extrudate prin aceeași matriță, SUDAREA LA PRESIUNE LA RECE în care îmbinăm aliajele moi sub punctele lor de topire, SUDAREA prin difuzie o tehnică fără linii vizibile de sudură, SUDAREA prin explozie pentru îmbinarea materialelor diferite, de exemplu aliaje rezistente la coroziune la structura oteluri, SUDAREA ELECTROMAGNETICA IMPULS in care se accelereaza tuburile si tablele prin forte electromagnetice, SUDURA FORJA care consta in incalzirea metalelor la temperaturi ridicate si ciocanarea lor intre ele, SUDAREA CU FRACTARE unde se executa cu suficienta sudura cu frecare, SUDAREA FRICTION STIR care presupune o rotatie non- unealtă consumabilă care traversează linia de îmbinare, SUDARE LA PRESIUNE LA CALDE unde presăm metalele împreună la temperaturi ridicate sub temperatura de topire în vid sau gaze inerte, SUDARE LA PRESIUNE ISOSTATICĂ LA CALDE un proces în care aplicăm presiune folosind gaze inerte în interiorul unui vas, SUDARE LA ROLL unde îmbinăm materiale diferite prin forțarea lor între două roți rotative, SUDARE ULTRASONIC la care sunt sudate foi subțiri de metal sau plastic folosind energie vibrațională de înaltă frecvență.
Celelalte procedee ale noastre de sudare sunt SUDURA CU GRAND ELECTRONIC cu penetrare profundă și procesare rapidă, dar fiind o metodă costisitoare o considerăm pentru cazuri speciale, SUDURA ELECTROZĂRĂ o metodă potrivită numai pentru plăci groase și piese de oțel de prelucrat, SUDURĂ prin INDUCȚIE unde folosim inducția electromagnetică și încălzește piesele noastre electric conductoare sau feromagnetice, SUDARE LASER FACEȚI, de asemenea, cu penetrare adâncă și procesare rapidă, dar o metodă costisitoare, SUDARE HIBRIDĂ LASER care combină LBW cu GMAW în același cap de sudură și capabilă să depășească golurile de 2 mm între plăci, SUDARE prin percuție care presupune o descărcare electrică urmată de forjarea materialelor cu presiune aplicată, SUDAREA TERMITĂ care implică reacție exotermă între pulberile de oxid de aluminiu și fier., SUDAREA ELECTROGAZ cu electrozi consumabili și utilizată numai cu oțel în poziție verticală, iar în final SUDARE ARC STUD pentru îmbinarea știftului la bază material cu căldură și presiune.
Vă recomandăm să faceți clic aici pentruDESCARCĂ Ilustrațiile noastre schematice ale proceselor de lipire, lipire și lipire cu adeziv de la AGS-TECH Inc
Acest lucru vă va ajuta să înțelegeți mai bine informațiile pe care vi le oferim mai jos.
• BRAZARE: Unim două sau mai multe metale prin încălzirea metalelor de adaos între ele deasupra punctelor de topire și folosind acțiunea capilară pentru a se răspândi. Procesul este similar cu lipirea, dar temperaturile implicate pentru topirea umpluturii sunt mai mari la lipire. Ca și în cazul sudării, fluxul protejează materialul de umplutură de contaminarea atmosferică. După răcire, piesele de prelucrat sunt îmbinate. Procesul implică următorii pași cheie: potrivire și degajare bună, curățarea corespunzătoare a materialelor de bază, fixarea corespunzătoare, selectarea corespunzătoare a fluxului și a atmosferei, încălzirea ansamblului și, în final, curățarea ansamblului lipit. Unele dintre procesele noastre de lipire sunt BRAZARE LA TORȚĂ, o metodă populară efectuată manual sau automat. Este potrivit pentru comenzi de producție cu volum redus și cazuri specializate. Căldura este aplicată folosind flăcări de gaz în apropierea îmbinării care este brazată. BRAZAREA LA FUNNER necesită mai puțină abilități de operator și este un proces semi-automat potrivit pentru producția industrială în masă. Atât controlul temperaturii, cât și controlul atmosferei din cuptor sunt avantaje ale acestei tehnici, deoarece prima ne permite să avem cicluri de căldură controlate și să eliminăm încălzirea locală, așa cum este cazul în cazul lipirii cu torță, iar cea din urmă protejează piesa de oxidare. Folosind jigging, suntem capabili să reducem costurile de producție la minimum. Dezavantajele sunt consumul mare de energie, costurile echipamentelor și considerații de proiectare mai dificile. BRAZAREA ÎN VID are loc într-un cuptor cu vid. Se menține uniformitatea temperaturii și obținem îmbinări fără flux, foarte curate, cu tensiuni reziduale foarte mici. Tratamentele termice pot avea loc în timpul lipirii în vid, din cauza tensiunilor reziduale scăzute prezente în timpul ciclurilor lente de încălzire și răcire. Dezavantajul major este costul său ridicat deoarece crearea unui mediu de vid este un proces costisitor. O altă tehnică DIP BRAZING îmbină părțile fixate în care compusul de lipire este aplicat pe suprafețele de îmbinare. După aceea, piesele fixate fixtured sunt scufundate într-o baie de sare topită, cum ar fi clorura de sodiu (sare de masă), care acționează ca mediu de transfer de căldură și flux. Aerul este exclus și, prin urmare, nu are loc formarea de oxid. La BRAZARE prin INDUCȚIE îmbinăm materialele printr-un metal de umplutură care are un punct de topire mai scăzut decât materialele de bază. Curentul alternativ de la bobina de inducție creează un câmp electromagnetic care induce încălzirea prin inducție pe materialele magnetice mai ales feroase. Metoda oferă încălzire selectivă, îmbinări bune cu materiale de umplutură care curg numai în zonele dorite, oxidare redusă deoarece nu sunt prezente flăcări și răcirea este rapidă, încălzire rapidă, consistență și adecvare pentru producția de volum mare. Pentru a ne accelera procesele și pentru a asigura coerența, folosim frecvent preforme. Informații despre instalația noastră de lipire care produce fitinguri din ceramică pe metal, etanșare ermetică, treceri de vid, vid înalt și ultraînalt și componente de control al fluidelor pot fi găsite aici:_cc781905-5cde-bb319836_bb31944Broșura Fabrica de lipire
• LIPIREA: La lipire nu avem topirea pieselor de prelucrat, ci un metal de adaos cu un punct de topire mai mic decât piesele de îmbinare care se varsă în îmbinare. Metalul de umplutură în lipire se topește la temperatură mai scăzută decât în lipire. Folosim aliaje fără plumb pentru lipire și respectăm RoHS și pentru diferite aplicații și cerințe avem aliaje diferite și adecvate, cum ar fi aliajul de argint. Lipirea ne oferă îmbinări care sunt etanșe la gaz și lichide. În lipirea moale, metalul nostru de adaos are un punct de topire sub 400 de grade Celsius, în timp ce în lipirea și lipirea cu argint avem nevoie de temperaturi mai ridicate. Lipirea moale folosește temperaturi mai scăzute, dar nu are ca rezultat îmbinări puternice pentru aplicații solicitante la temperaturi ridicate. Lipirea cu argint, pe de altă parte, necesită temperaturi ridicate furnizate de torță și ne oferă îmbinări puternice, potrivite pentru aplicații la temperaturi înalte. Lipirea necesită cele mai ridicate temperaturi și, de obicei, se folosește o torță. Deoarece îmbinările de lipire sunt foarte puternice, acestea sunt un bun candidat pentru repararea obiectelor grele de fier. În liniile noastre de producție folosim atât lipirea manuală, cât și liniile automate de lipit. LIPIREA INDUCȚIE folosește curent alternativ de înaltă frecvență într-o bobină de cupru pentru a facilita încălzirea prin inducție. Curenții sunt induși în partea lipită și ca rezultat se generează căldură la rezistența mare joint. Această căldură topește metalul de umplutură. Se folosește și flux. Lipirea prin inducție este o metodă bună pentru lipirea cilindrilor și țevilor într-un proces continuu prin înfășurarea bobinelor în jurul lor. Lipirea unor materiale precum grafitul și ceramica este mai dificilă deoarece necesită placarea pieselor de prelucrat cu un metal adecvat înainte de lipire. Acest lucru facilitează legarea interfacială. Lipim astfel de materiale în special pentru aplicații de ambalare ermetică. Producem plăcile noastre de circuite imprimate (PCB) în volum mare, în principal folosind lipirea cu valuri. Numai pentru cantități mici de prototipuri folosim lipirea manuală cu fier de lipit. Folosim lipirea prin val atât pentru ansambluri PCB cu găuri traversante, cât și pentru montare la suprafață (PCBA). Un adeziv temporar menține componentele atașate la placa de circuite, iar ansamblul este plasat pe un transportor și se deplasează printr-un echipament care conține lipire topită. Mai întâi, PCB-ul este fluxat și apoi intră în zona de preîncălzire. Lipitura topită este într-o tigaie și are un model de valuri staționare pe suprafața sa. Când PCB-ul se deplasează peste aceste unde, aceste unde contactează partea inferioară a PCB-ului și se lipesc de plăcuțele de lipit. Lipirea rămâne doar pe pini și plăcuțe și nu pe PCB în sine. Valurile din lipirea topită trebuie să fie bine controlate, astfel încât să nu existe stropire, iar vârfurile undelor să nu atingă și să contamineze zonele nedorite ale plăcilor. În REFLOW SOLDERING, folosim o pastă de lipit lipicioasă pentru a atașa temporar componentele electronice de plăci. Apoi plăcile sunt trecute printr-un cuptor de reflow cu control al temperaturii. Aici lipitura se topește și conectează permanent componentele. Folosim această tehnică atât pentru componentele de montare pe suprafață, cât și pentru componentele cu orificii traversante. Controlul adecvat al temperaturii și reglarea temperaturii cuptorului este esențială pentru a evita distrugerea componentelor electronice de pe placă prin supraîncălzirea acestora peste limitele lor maxime de temperatură. În procesul de lipire prin reflux avem de fapt mai multe regiuni sau etape fiecare cu un profil termic distinct, cum ar fi etapa de preîncălzire, etapa de înmuiere termică, etapa de refluxare și etapa de răcire. Acești pași diferiți sunt esențiali pentru o lipire prin reflow fără deteriorare a ansamblurilor de plăci de circuit imprimat (PCBA). LIPIREA ULTRASONICĂ este o altă tehnică frecvent utilizată cu capacități unice - Poate fi folosită pentru a lipi sticlă, ceramică și materiale nemetalice. De exemplu, panourile fotovoltaice care sunt nemetalice au nevoie de electrozi care pot fi fixați folosind această tehnică. În lipirea cu ultrasunete, implementăm un vârf de lipit încălzit care emite și vibrații ultrasonice. Aceste vibrații produc bule de cavitație la interfața substratului cu materialul de lipit topit. Energia implozivă a cavitației modifică suprafața oxidului și îndepărtează murdăria și oxizii. În acest timp se formează și un strat de aliaj. Lipitura de la suprafața de lipire încorporează oxigen și permite formarea unei legături comune puternice între sticlă și lipire. Lipirea prin scufundare poate fi privită ca o versiune mai simplă a lipirii prin valuri, potrivită numai pentru producția la scară mică. Primul flux de curățare este aplicat ca în alte procese. PCB-urile cu componente montate sunt scufundate manual sau semi-automat într-un rezervor care conține lipitură topită. Lipitura topită se lipește de zonele metalice expuse neprotejate de masca de lipit de pe placă. Echipamentul este simplu și ieftin.
• LIPIREA ADEZIVĂ: Aceasta este o altă tehnică populară pe care o folosim frecvent și implică lipirea suprafețelor folosind cleiuri, epoxidici, agenți plastici sau alte substanțe chimice. Lipirea se realizează fie prin evaporarea solventului, prin întărire la căldură, prin polimerizare cu lumină UV, prin întărire sub presiune sau prin așteptare pentru un anumit timp. În liniile noastre de producție sunt utilizați diverse adezivi de înaltă performanță. Cu procese de aplicare și întărire concepute corespunzător, lipirea adeziv poate avea ca rezultat legături de stres foarte scăzute, care sunt puternice și de încredere. Legăturile adezive pot fi buni protectori împotriva factorilor de mediu, cum ar fi umiditatea, contaminanții, corozivii, vibrațiile etc. Avantajele lipirii adezive sunt: pot fi aplicate pe materiale care altfel ar fi greu de lipit, sudat sau lipit. De asemenea, poate fi de preferat pentru materialele sensibile la căldură care ar fi deteriorate prin sudare sau alte procese la temperaturi ridicate. Alte avantaje ale adezivilor sunt că pot fi aplicați pe suprafețe de formă neregulată și pot crește greutatea ansamblului în cantități foarte mici în comparație cu alte metode. De asemenea, modificările dimensionale ale pieselor sunt foarte minime. Unele cleiuri au proprietăți de potrivire a indicelui și pot fi utilizate între componentele optice fără a scădea în mod semnificativ puterea luminii sau a semnalului optic. Pe de altă parte, dezavantajele sunt timpii de întărire mai lungi care pot încetini liniile de producție, cerințele de fixare, cerințele de pregătire a suprafeței și dificultatea de a dezasambla atunci când este nevoie de reprelucrare. Majoritatea operațiunilor noastre de lipire cu adeziv implică următorii pași:
-Tratamentul suprafeței: procedurile speciale de curățare, cum ar fi curățarea cu apă deionizată, curățarea cu alcool, curățarea cu plasmă sau corona sunt frecvente. După curățare, putem aplica promotori de aderență pe suprafețe pentru a asigura cele mai bune îmbinări posibile.
- Fixarea pieselor: atât pentru aplicarea adezivilor, cât și pentru întărire, proiectăm și folosim dispozitive personalizate.
-Aplicare adeziv: Folosim uneori sisteme manuale, iar uneori, in functie de caz, automate precum robotica, servomotoare, actuatoare liniare pentru a livra adezivii la locul potrivit si folosim dozatoare pentru a-i livra la volumul si cantitatea potrivita.
- Întărire: În funcție de adeziv, putem folosi uscare și întărire simplă, precum și întărire sub lumini UV care acționează ca catalizator sau întărire la căldură într-un cuptor sau folosind elemente de încălzire rezistive montate pe dispozitive și dispozitive de fixare.
Vă recomandăm să faceți clic aici pentruDESCARCĂ Ilustrațiile noastre schematice ale proceselor de fixare de la AGS-TECH Inc.
Acest lucru vă va ajuta să înțelegeți mai bine informațiile pe care vi le oferim mai jos.
• PROCESE DE FIXARE: Procesele noastre mecanice de îmbinare se încadrează în două categorii de brad: FASTENERS și INTEGRAL JOINTS. Exemple de elemente de fixare pe care le folosim sunt șuruburi, știfturi, piulițe, șuruburi, nituri. Exemple de îmbinări integrale pe care le folosim sunt snap and shrink fits, cusături, sertizare. Folosind o varietate de metode de fixare, ne asigurăm că îmbinările noastre mecanice sunt puternice și fiabile pentru mulți ani de utilizare. Șuruburile și șuruburile sunt unele dintre cele mai utilizate elemente de fixare pentru ținerea și poziționarea obiectelor împreună. Șuruburile și șuruburile noastre respectă standardele ASME. Sunt utilizate diferite tipuri de șuruburi și șuruburi, inclusiv șuruburi hexagonale și șuruburi hexagonale, șuruburi și șuruburi autoblocante, șuruburi cu două capete, șuruburi cu cap, șurub cu ochi, șurub oglindă, șurub pentru tablă, șurub de reglare fină, șuruburi autoforante și autofiletante. , șurub de fixare, șuruburi cu șaibe încorporate și multe altele. Avem diferite tipuri de cap de șurub, cum ar fi cap înecat, cupolă, rotund, cu flanșă și diferite tipuri de șuruburi, cum ar fi slot, Phillips, pătrat, hexagonal. Pe de altă parte, un RIVET este un dispozitiv de fixare mecanic permanent format dintr-un ax cilindric neted și un cap pe de o parte. După introducere, celălalt capăt al nitului este deformat și diametrul acestuia este extins astfel încât să rămână pe loc. Cu alte cuvinte, înainte de instalare un nit are un singur cap, iar după instalare are două. Instalăm diferite tipuri de nituri în funcție de aplicație, rezistență, accesibilitate și cost, cum ar fi nituri cu cap solid/rotund, nituri structurale, semitubulare, oarbe, oscar, drive, flush, cu blocare prin frecare, nituri autoperforante. Nituirea poate fi preferată în cazurile în care trebuie evitată deformarea termică și modificarea proprietăților materialului din cauza căldurii de sudare. Nituirea oferă, de asemenea, greutate redusă și în special rezistență și rezistență bună împotriva forțelor de forfecare. Cu toate acestea, împotriva sarcinilor de tracțiune, șuruburile, piulițele și șuruburile pot fi mai potrivite. În procesul de CLINCHARE folosim poanson și matrițe speciale pentru a forma o interblocare mecanică între foile de metal care se îmbină. Poansonul împinge straturile de tablă în cavitatea matriței și are ca rezultat formarea unei îmbinări permanente. Nu este necesară nicio încălzire și nicio răcire în clinch și este un proces de lucru la rece. Este un proces economic care poate înlocui sudarea în puncte în unele cazuri. În PINNING folosim știfturi care sunt elemente ale mașinii utilizate pentru a asigura pozițiile pieselor mașinii unele față de altele. Tipurile majore sunt știfturi, știfturi, știfturi cu arc, știfturi, și știftul despicat. În CAPSARE folosim pistoale de capsare și capse care sunt elemente de fixare cu două capete folosite pentru a îmbina sau lega materiale. Capsarea are următoarele avantaje: Economică, simplă și rapidă de utilizat, coroana capselor poate fi folosită pentru a lega materialele îmbinate între ele, Coroana capsei poate facilita unirea unei piese ca un cablu și fixarea acesteia pe o suprafață fără perforare sau dăunătoare, îndepărtare relativ ușoară. PRESAREA se realizează prin împingerea pieselor împreună, iar frecarea dintre ele fixează piesele. Piesele de fixare prin presare constând dintr-un arbore supradimensionat și un orificiu subdimensionat sunt, în general, asamblate prin una din două metode: fie prin aplicarea forței, fie profitând de dilatarea sau contracția termică a pieselor. Când se stabilește o racordare prin presare prin aplicarea unei forțe, folosim fie o presă hidraulică, fie o presă manuală. Pe de altă parte, atunci când montarea prin presare este stabilită prin dilatare termică, încălzim părțile învelitoare și le asamblam la locul lor cât timp sunt fierbinți. Când se răcesc, se contractă și revin la dimensiunile lor normale. Acest lucru are ca rezultat o potrivire bună prin presare. Numim asta alternativ MONTARE RETRACTĂ. Cealaltă modalitate de a face acest lucru este răcirea pieselor învelite înainte de asamblare și apoi glisarea lor în părțile lor de împerechere. Când ansamblul se încălzește, se extind și obținem o potrivire strânsă. Această ultimă metodă poate fi de preferat în cazurile în care încălzirea prezintă riscul de modificare a proprietăților materialului. Răcirea este mai sigură în aceste cazuri.
Componente și ansambluri pneumatice și hidraulice
• Supape, componente hidraulice și pneumatice, cum ar fi inele O, șaibă, garnituri, garnitură, inel, lame.
Deoarece supapele și componentele pneumatice vin într-o mare varietate, nu putem enumera totul aici. În funcție de mediile fizice și chimice ale aplicației dvs., avem produse speciale pentru dvs. Vă rugăm să ne specificați aplicația, tipul de componentă, specificațiile, condițiile de mediu precum presiunea, temperatura, lichidele sau gazele care vor intra în contact cu supapele și componentele pneumatice dvs.; și vom alege cel mai potrivit produs pentru dvs. sau îl vom fabrica special pentru aplicația dvs.