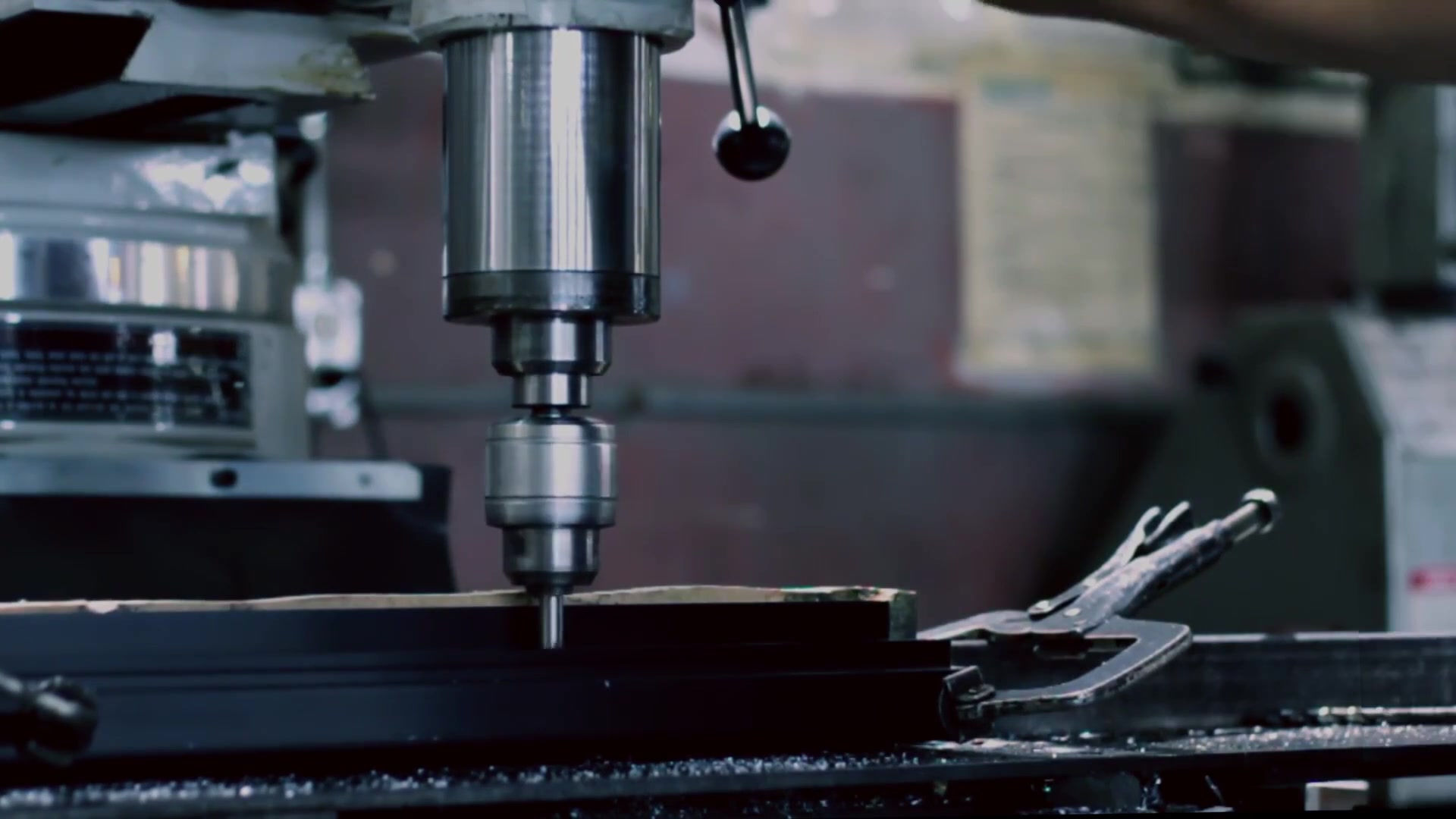
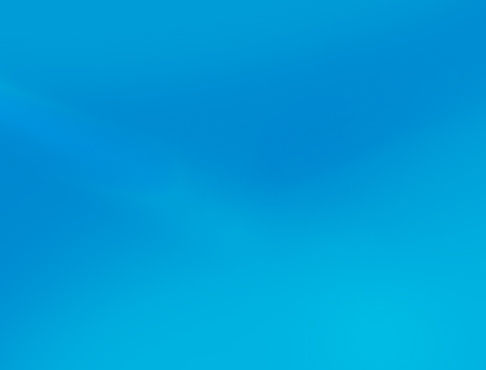
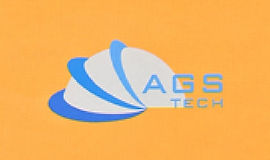
Глобальный производитель на заказ, интегратор, консолидатор, партнер по аутсорсингу широкого спектра продуктов и услуг.
Мы являемся вашим универсальным источником для производства, изготовления, проектирования, консолидации, интеграции, аутсорсинга изготовленных на заказ и готовых продуктов и услуг.
Choose your Language
-
Изготовление на заказ
-
Внутреннее и глобальное контрактное производство
-
Производственный аутсорсинг
-
Внутренние и глобальные закупки
-
Консолидация
-
Инженерная интеграция
-
Инженерные услуги
Наши нестандартные методы литья и механической обработки включают одноразовое и многоразовое литье, литье черных и цветных металлов, песчаное, штампованное, центробежное, непрерывное, керамическое литье, инвестиционную форму, выплавляемую пену, форму, близкую к чистой, постоянную форму (литье под давлением), гипс. отливки в формы (гипсовое литье) и отливки в оболочки, обработанные детали, изготовленные фрезерованием и точением на обычном оборудовании, а также на оборудовании с ЧПУ, швейцарская обработка для высокопроизводительных недорогих мелких прецизионных деталей, обработка винтов для крепежа, нетрадиционная обработка. Пожалуйста, имейте в виду, что помимо металлов и металлических сплавов мы также обрабатываем керамические, стеклянные и пластиковые компоненты, а также в некоторых случаях, когда изготовление пресс-формы нецелесообразно или не представляется возможным. Механическая обработка полимерных материалов требует специального опыта, который у нас есть из-за проблем, связанных с пластиками и резиной из-за их мягкости, нежесткости и т. д. Информацию о механической обработке керамики и стекла см. на нашей странице, посвященной нетрадиционному производству. AGS-TECH Inc. производит и поставляет как легкие, так и тяжелые отливки. Мы поставляем металлические отливки и обработанные детали для котлов, теплообменников, автомобилей, микромоторов, ветряных турбин, оборудования для упаковки пищевых продуктов и многого другого. Мы рекомендуем вам нажать здесь to СКАЧАТЬ наши схематические иллюстрации процессов обработки и литья от AGS-TECH Inc.
Это поможет вам лучше понять информацию, которую мы предоставляем вам ниже. Давайте подробно рассмотрим некоторые из различных методов, которые мы предлагаем:
• ЛИТЬЕ В РАЗНООБРАЗНЫЕ ФОРМЫ: Эта широкая категория относится к методам, в которых используются временные и одноразовые формы. Примерами являются песок, гипс, ракушка, паковочная масса (также называемая выплавляемым воском) и гипсовое литье.
• ЛИТЬЕ В ПЕСКИ: Процесс, при котором в качестве материала формы используется песок. Очень старый метод, который до сих пор очень популярен, так как большинство производимых металлических отливок изготавливается по этому методу. Низкая себестоимость даже при небольших объемах производства. Подходит для изготовления мелких и крупных деталей. Этот метод можно использовать для изготовления деталей в течение нескольких дней или недель с очень небольшими инвестициями. Влажный песок связывают вместе с помощью глины, связующих веществ или специальных масел. Песок обычно содержится в ящиках для форм, а система полостей и литников создается путем уплотнения песка вокруг моделей. Процессы:
1.) Помещение модели в песок для изготовления формы.
2.) Включение модели и песка в литниковую систему
3.) Удаление модели
4.) Заполнение полости формы расплавленным металлом
5.) Охлаждение металла
6.) Разбивание песчаной формы и снятие отливки
• ЛИТЬЕ В ГИПСОВУЮ ФОРМУ: аналогично литью в песчаные формы, но вместо песка в качестве материала формы используется гипс. Короткие сроки производства, такие как литье в песчаные формы и недорого. Хорошие допуски на размеры и качество поверхности. Его основным недостатком является то, что его можно использовать только с металлами с низкой температурой плавления, такими как алюминий и цинк.
• ЛИТЬЕ В ОБОЛОЧКУ: Также похоже на литье в песчаные формы. Полость формы, полученная за счет затвердевшей оболочки из песка и связующего из термореактивной смолы вместо опоки, заполненной песком, как в процессе литья в песчаные формы. Почти любой металл, пригодный для литья в песок, может быть отлит методом оболочкового литья. Процесс можно обобщить следующим образом:
1.) Изготовление оболочковой формы. Используемый песок имеет гораздо меньший размер зерна по сравнению с песком, используемым при литье в песчаные формы. Мелкий песок смешивается с термореактивной смолой. Металлический узор покрыт разделительным составом, чтобы облегчить снятие оболочки. После этого металлическая модель нагревается, и песчаная смесь наносится или выдувается на горячую модель отливки. На поверхности узора образуется тонкая оболочка. Толщину этой оболочки можно регулировать, изменяя продолжительность контакта смеси песка и смолы с металлическим рисунком. Затем рыхлый песок удаляется, а рисунок, покрытый ракушкой, остается.
2.) Далее скорлупу и выкройку прогревают в печи, чтобы скорлупа затвердела. После завершения затвердевания оболочка выталкивается из шаблона с помощью штифтов, встроенных в шаблон.
3.) Две такие оболочки собираются вместе путем склеивания или зажима и составляют полную форму. Теперь оболочковая форма вставляется в емкость, в которой она поддерживается песком или металлической дробью в процессе литья.
4.) Теперь горячий металл можно заливать в форму.
Преимущества оболочечного литья – изделия с очень хорошей отделкой поверхности, возможность изготовления сложных деталей с высокой точностью размеров, легкость автоматизации процесса, экономичность при крупносерийном производстве.
Недостатки заключаются в том, что формы требуют хорошей вентиляции из-за газов, которые образуются при контакте расплавленного металла со связующим химическим веществом, термореактивные смолы и металлические модели дороги. Из-за стоимости металлических моделей этот метод может не подходить для мелкосерийного производства.
• ЛИТЬЕ ПО ИНВЕСТИЦИОННЫМ ОБРАЗЦАМ (также известное как ЛИТЬЕ ПО ВОСКАМ): также очень старая технология, подходящая для изготовления качественных деталей с высокой точностью, повторяемостью, универсальностью и целостностью из многих металлов, тугоплавких материалов и специальных сплавов с высокими эксплуатационными характеристиками. Возможно изготовление как мелких, так и крупногабаритных деталей. Дорогостоящий процесс по сравнению с некоторыми другими методами, но основным преимуществом является возможность изготовления деталей с почти заданной формой, сложными контурами и деталями. Таким образом, стоимость несколько компенсируется устранением переделок и механической обработки в некоторых случаях. Несмотря на то, что могут быть вариации, вот краткое изложение общего процесса литья по выплавляемым моделям:
1.) Создание оригинальной мастер-модели из воска или пластика. Для каждой отливки требуется один шаблон, так как они разрушаются в процессе. Форма, из которой изготавливаются модели, также необходима, и большую часть времени форму отливают или обрабатывают. Поскольку форму открывать не нужно, можно получить сложные отливки, многие восковые модели можно соединить, как ветви дерева, и залить вместе, что позволяет производить несколько деталей из одной заливки металла или металлического сплава.
2.) Затем модель окунают или заливают огнеупорной суспензией, состоящей из очень мелкозернистого кремнезема, воды, связующих. Это приводит к керамическому слою на поверхности рисунка. Огнеупорный слой на шаблоне оставляют сохнуть и затвердевать. Именно на этом этапе происходит название «литье по выплавляемым моделям»: огнеупорная суспензия наносится на восковую модель.
3.) На этом этапе затвердевшую керамическую форму переворачивают вверх дном и нагревают, чтобы воск расплавился и вылился из формы. Оставляют полость для металлической отливки.
4.) После удаления воска керамическая форма нагревается до еще более высокой температуры, что приводит к упрочнению формы.
5.) Металлическая отливка заливается в горячую форму, заполняя все сложные участки.
6.) Отливке дают затвердеть
7.) Наконец, керамическая форма разбивается, а изготовленные детали вырезаются из дерева.
Вот ссылка на Брошюру завода литья по выплавляемым моделям
• ЛИТЬЕ МОДЕЛИ ИСПАРЕНИЯ: В процессе используется модель, изготовленная из такого материала, как пенополистирол, который испаряется при заливке горячего расплавленного металла в форму. Существует два типа этого процесса: ЛИТЬЕ ПО ПОТЕРЯМ, в котором используется несвязанный песок, и ЛИТЬЕ ПОЛНОЙ ФОРМЫ, в котором используется связанный песок. Вот общие этапы процесса:
1.) Изготовьте выкройку из такого материала, как полистирол. Когда будет производиться большое количество, выкройка формуется. Если деталь имеет сложную форму, может потребоваться склеивание нескольких секций такого вспененного материала для формирования рисунка. Мы часто покрываем шаблон огнеупорным составом, чтобы создать хорошую поверхность отливки.
2.) Затем шаблон помещается в формовочную смесь.
3.) Расплавленный металл заливается в форму, испаряя пенопласт, т.е. в большинстве случаев полистирол, при протекании через полость формы.
4.) Расплавленный металл оставляют в песчаной форме для затвердевания.
5.) После затвердевания снимаем отливку.
В некоторых случаях продукт, который мы производим, требует сердцевины в шаблоне. При испарительном литье нет необходимости размещать и закреплять стержень в полости формы. Метод подходит для изготовления деталей очень сложной геометрии, легко автоматизируется для крупносерийного производства, в отливке отсутствуют линии разъема. Основной процесс прост и экономичен в реализации. Для крупносерийного производства, поскольку для изготовления моделей из полистирола требуется штамп или форма, это может быть несколько дорогостоящим.
• ЛИТЬЕ В НЕРАСШИРЯЕМУЮ ФОРМУ: Эта широкая категория относится к методам, при которых форму не нужно переделывать после каждого производственного цикла. Примерами являются непрерывное литье, литье под давлением, непрерывное и центробежное литье. Достигается повторяемость, и детали можно охарактеризовать как ПОЧТИ РЕЗУЛЬТАТНУЮ ФОРМУ.
• ПОСТОЯННАЯ ОТЛИВКА В ФОРМЫ: Многоразовые формы из металла используются для многократного литья. Как правило, постоянную форму можно использовать десятки тысяч раз, прежде чем она изнашивается. Для заполнения формы обычно используются сила тяжести, давление газа или вакуум. Формы (также называемые штампами) обычно изготавливаются из железа, стали, керамики или других металлов. Общий процесс таков:
1.) Обработайте и создайте форму. Обычно форму изготавливают из двух металлических блоков, которые подходят друг к другу и могут открываться и закрываться. Как детали, так и литниковая система обычно изготавливаются в литейной форме.
2.) Внутренние поверхности формы покрыты суспензией, содержащей огнеупорные материалы. Это помогает контролировать поток тепла и действует как смазка для легкого удаления литой детали.
3.) Затем постоянные половинки пресс-формы закрываются и пресс-форма нагревается.
4.) Расплавленный металл заливают в форму и оставляют до затвердевания.
5.) До того, как произойдет значительное охлаждение, мы извлекаем деталь из постоянной формы с помощью эжекторов, когда половинки формы открыты.
Мы часто используем литье в постоянные формы для металлов с низкой температурой плавления, таких как цинк и алюминий. Для стальных отливок мы используем графит в качестве материала формы. Иногда мы получаем сложную геометрию, используя стержни в постоянных формах. Преимуществами этого метода являются отливки с хорошими механическими свойствами, полученными путем быстрого охлаждения, однородность свойств, хорошая точность и чистота поверхности, низкий процент брака, возможность автоматизации процесса и экономичное производство больших объемов. Недостатками являются высокие первоначальные затраты на настройку, которые делают его непригодным для операций с небольшим объемом, и ограничения по размеру изготавливаемых деталей.
• ЛИТЬЕ ПОД ДАВЛЕНИЕМ: Обрабатывается форма, и расплавленный металл под высоким давлением вдавливается в полости формы. Возможно литье под давлением как цветных, так и черных металлов. Этот процесс подходит для крупносерийного производства деталей малого и среднего размера с деталями, чрезвычайно тонкими стенками, стабильностью размеров и хорошим качеством поверхности. Компания AGS-TECH Inc. способна производить с использованием этой технологии стенки толщиной всего 0,5 мм. Как и при литье в постоянные формы, форма должна состоять из двух половин, которые могут открываться и закрываться для извлечения изготавливаемой детали. Форма для литья под давлением может иметь несколько полостей, что позволяет производить несколько отливок за каждый цикл. Формы для литья под давлением очень тяжелые и намного больше, чем детали, которые они производят, поэтому они также дороги. Мы бесплатно ремонтируем и заменяем изношенные штампы для наших клиентов, если они повторно заказывают у нас свои детали. Срок службы наших штампов составляет несколько сотен тысяч циклов.
Вот основные упрощенные этапы процесса:
1.) Изготовление пресс-формы в основном из стали
2.) Пресс-форма, установленная на машине для литья под давлением
3.) Поршень заставляет расплавленный металл течь в полости матрицы, заполняя сложные элементы и тонкие стенки.
4.) После заполнения формы расплавленным металлом отливка подвергается закалке под давлением.
5.) Форма открывается и отливка удаляется с помощью выталкивающих штифтов.
6.) Теперь пустая матрица снова смазывается и зажимается для следующего цикла.
При литье под давлением мы часто используем формование со вставкой, когда мы вставляем дополнительную деталь в форму и отливаем вокруг нее металл. После затвердевания эти детали становятся частью отлитого изделия. Преимуществами литья под давлением являются хорошие механические свойства деталей, возможность получения сложных элементов, мелких деталей и хорошей чистоты поверхности, высокая производительность, простота автоматизации. Недостатки: не очень подходит для небольших объемов из-за высокой стоимости штампа и оборудования, ограничения по формам, которые можно отливать, небольшие круглые следы на литых деталях, возникающие в результате контакта выталкивающих штифтов, тонкий налет металла, выдавленный на линии разъема, необходимость для вентиляционных отверстий вдоль линии разъема между матрицами, необходимость поддержания низкой температуры пресс-формы за счет циркуляции воды.
• ЦЕНТРОБЕЖНАЯ ЛИТЬЕ: Расплавленный металл заливается в центр вращающейся формы на оси вращения. Центробежные силы отбрасывают металл к периферии, и он затвердевает, пока форма продолжает вращаться. Можно использовать как горизонтальное, так и вертикальное вращение осей. Можно отливать детали с круглыми внутренними поверхностями, а также другие некруглые формы. Процесс можно обобщить следующим образом:
1.) Расплавленный металл заливают в центробежную форму. Затем металл прижимается к внешним стенкам из-за вращения формы.
2.) Когда форма вращается, металлическая отливка затвердевает.
Центробежное литье является подходящим методом для производства полых цилиндрических деталей, таких как трубы, отсутствие необходимости в литниках, стояках и литниковых элементах, хорошее качество поверхности и подробные характеристики, отсутствие проблем с усадкой, возможность производства длинных труб очень большого диаметра, высокая производительность .
• НЕПРЕРЫВНАЯ ЛИТЬЕ (МЕТАЛЛИЧЕСКАЯ ЛИТКА): Используется для непрерывной разливки металла. В основном расплавленный металл заливается в двухмерный профиль формы, но его длина не определена. Новый расплавленный металл постоянно подается в форму по мере того, как отливка движется вниз, и ее длина со временем увеличивается. Металлы, такие как медь, сталь, алюминий, отливают в длинные нити с использованием процесса непрерывного литья. Процесс может иметь различные конфигурации, но общий можно упростить следующим образом:
1.) Расплавленный металл заливается в емкость, расположенную высоко над формой, в точно рассчитанных количествах и расходах и течет через форму с водяным охлаждением. Металлическая отливка, залитая в форму, затвердевает до стартового стержня, расположенного на дне формы. Эта стартовая планка дает роликам что-то, за что можно зацепиться изначально.
2.) Длинная металлическая заготовка перемещается роликами с постоянной скоростью. Ролики также меняют направление потока металлической заготовки с вертикального на горизонтальное.
3.) После того, как непрерывная отливка прошла определенное расстояние по горизонтали, горелка или пила, которые перемещаются вместе с отливкой, быстро отрезают ее до нужной длины.
Процесс непрерывной разливки можно интегрировать с ПРОЦЕССОМ ПРОКАТКИ, при котором непрерывно разливаемый металл можно подавать непосредственно в прокатный стан для производства двутавровых балок, тавровых балок и т. д. Непрерывное литье обеспечивает однородные свойства всего продукта, имеет высокую скорость затвердевания, снижает стоимость из-за очень низких потерь материала, предлагает процесс, в котором загрузка металла, заливка, затвердевание, резка и удаление отливки происходят в непрерывном режиме и что приводит к высокой производительности и высокому качеству. Однако основным соображением являются высокие первоначальные инвестиции, затраты на установку и требования к пространству.
• УСЛУГИ ПО ОБРАБОТКЕ: Мы предлагаем трех-, четырех- и пятиосевую обработку. Используемые нами процессы обработки: ТОКАРНАЯ, ФРЕЗЕРОВАЛЬНАЯ, СВЕРЛИТЕЛЬНАЯ, РАСТОЧНАЯ, ПРОШИВКА, СТРОГООБРАБОТКА, ПИЛКА, ШЛИФОВКА, ПРИТРОЙКА, ПОЛИРОВКА и НЕТРАДИЦИОННАЯ ОБРАБОТКА, которая более подробно описана в другом меню нашего веб-сайта. Для большей части нашего производства мы используем станки с ЧПУ. Однако для некоторых операций лучше подходят традиционные методы, поэтому мы также полагаемся на них. Наши возможности обработки достигают максимально возможного уровня, и некоторые наиболее требовательные детали производятся на заводе, сертифицированном AS9100. Лопасти реактивных двигателей требуют узкоспециализированного производственного опыта и подходящего оборудования. В аэрокосмической отрасли действуют очень строгие стандарты. Некоторые детали со сложной геометрической структурой проще всего изготавливать пятикоординатной обработкой, которая есть только на некоторых механообрабатывающих предприятиях, в том числе и на нашем. Наш завод, сертифицированный для аэрокосмической отрасли, имеет необходимый опыт в соответствии с обширными требованиями документации аэрокосмической отрасли.
В токарных операциях заготовка вращается и перемещается относительно режущего инструмента. Для этого процесса используется машина, называемая токарным станком.
В ФРЕЗЕРОВАНИИ станок, называемый фрезерным станком, имеет вращающийся инструмент, который прижимает режущие кромки к заготовке.
Операции СВЕРЛЕНИЯ включают вращающуюся фрезу с режущими кромками, которая создает отверстия при контакте с заготовкой. Обычно используются сверлильные станки, токарные станки или мельницы.
При РАСТОЧНОЙ операции инструмент с одним изогнутым заостренным концом перемещается в черновое отверстие во вращающейся заготовке, чтобы немного увеличить отверстие и повысить точность. Используется для чистовой отделки.
ПРОШИВКА включает в себя зубчатый инструмент для удаления материала с заготовки за один проход протяжки (зубчатый инструмент). При линейной протяжке протяжка проходит линейно по поверхности заготовки, чтобы произвести рез, тогда как при вращательной протяжке протяжка вращается и вдавливается в заготовку, чтобы вырезать осесимметричную форму.
SWISS TYPE MACHINING — одна из наших ценных технологий, которые мы используем для крупносерийного производства небольших высокоточных деталей. На токарном станке швейцарского типа мы недорого вытачиваем мелкие, сложные, прецизионные детали. В отличие от обычных токарных станков, где заготовка остается неподвижной, а инструмент движется, в токарных центрах швейцарского типа заготовка может перемещаться по оси Z, а инструмент неподвижен. При обработке по швейцарскому типу прутковый материал удерживается в станке и продвигается через направляющую втулку по оси Z, обнажая только часть, подлежащую обработке. Таким образом обеспечивается плотный захват и очень высокая точность. Наличие приводных инструментов обеспечивает возможность фрезерования и сверления по мере продвижения материала из направляющей втулки. Ось Y оборудования швейцарского типа обеспечивает полные возможности фрезерования и значительно экономит время производства. Кроме того, наши станки имеют сверла и расточные инструменты, которые воздействуют на деталь, удерживаемую во вспомогательном шпинделе. Наши возможности обработки швейцарского типа дают нам возможность полностью автоматизированной полной обработки за одну операцию.
Механическая обработка является одним из крупнейших сегментов бизнеса AGS-TECH Inc. Мы используем его либо в качестве основной операции, либо в качестве дополнительной операции после литья или выдавливания детали, чтобы были соблюдены все спецификации чертежа.
• УСЛУГИ ПО ОБРАБОТКЕ ПОВЕРХНОСТИ: Мы предлагаем широкий спектр услуг по обработке и отделке поверхности, таких как подготовка поверхности для улучшения адгезии, нанесение тонкого оксидного слоя для улучшения адгезии покрытия, пескоструйная обработка, химическая пленка, анодирование, азотирование, порошковое покрытие, напыление. , различные передовые методы металлизации и нанесения покрытий, включая напыление, электронно-лучевое напыление, нанесение покрытия, твердые покрытия, такие как алмазоподобный углерод (DLC) или титановое покрытие для сверлильных и режущих инструментов.
• УСЛУГИ ПО МАРКИРОВКЕ И МАРКИРОВКЕ ПРОДУКЦИИ: Многим нашим клиентам требуется маркировка и маркировка, лазерная маркировка, гравировка на металлических деталях. Если у вас есть такая потребность, давайте обсудим, какой вариант будет лучшим для вас.
Вот некоторые из наиболее часто используемых металлических литых изделий. Поскольку они есть в наличии, вы можете сэкономить на затратах на пресс-формы, если какой-либо из них соответствует вашим требованиям:
НАЖМИТЕ ЗДЕСЬ, ЧТОБЫ СКАЧАТЬ наши литые алюминиевые коробки серии 11 от AGS-Electronics